麻花钻钻孔中常见问题的原因和解决办法
钻孔过程中易出现的故障及处理

钻孔过程中易出现的故障及处理A、钻孔偏斜这是在施工中最为常见的一种,偏斜原因有好种:1)桩架不稳,钻杆导架不垂直,钻机磨耗,部件松动。
故此在开钻前一定要检查钻机的稳定性与垂直度,在钻进过程中要随时复核,如有偏差及时处理。
2)土层软硬不均,致使钻头受力不均。
在地层分层处要注意控制钻速,不要过快,同时要采用减压钻进。
3)钻进中遇有较大孤石,探头石。
此时宜用钻机钻透。
用冲孔机时,用低速将石打碎;有倾斜基岩时,可用混凝土填平,待混凝土凝固后再钻。
4)扩孔较大处,钻头摆动偏向一方。
在容易扩孔处低速减压钻进。
5)钻杆弯曲,接头不正。
为了防止出现成孔偏斜,可在施工中采用加扶正圈导正,全孔减压钻进的防斜措施。
扶正圈直径比设计桩径小20厘米,扶正圈的位臵放在离钻头5-6米处,必要时可每钻进20―30米加一扶正圈,以加强钻具的导向性。
B、塌孔其表征是孔内水位突然上升又下降,孔口冒细密的水泡,出渣量明显增加而不见进尺,钻机负荷显著增加。
塌孔原因主要有:1)护筒埋臵过浅,周围封填不密,漏水;2)操作不当,如提升钻头,冲击锥(抓)或掏渣筒倾倒,或放钢筋骨架是碰撞孔壁;3)泥浆稠度小,起不到护壁作用;4)泥浆水位高度不够,对孔壁压力小;5)向孔内加水时流速过大,直接冲刷孔壁;6)在松软砂层中钻进时进尺过快。
预防措施:汛期或潮汐地区水位变化过大时,采取升高护筒,增加水头或用虹吸管等措施保持水头相对稳定;提升钻头,下放钢筋骨架时应保持垂直,不要碰撞孔壁。
处理措施:事故发生后应查明塌孔位臵后进行处理。
塌孔位臵不深时,可采取深埋护筒,穿过塌孔处。
塌孔位臵深时,塌孔不严重时,可回填到塌孔位臵以上,并采取改善泥浆性能,加高水头措施,继续钻进。
塌孔严重时,应立即将钻孔用砂类土或砾石土回填,无此类土时可采用粘质土并掺入5%-8%的水泥砂浆,观察数日后重新开钻。
C、扩孔与缩径扩孔多系孔壁小塌孔或钻锥摆动过大,应针对原因采取措施。
缩径常因地层中含有遇水能膨胀的软塑性土或泥质叶岩造成;钻锥磨损过甚也可造成孔径偏小。
麻花钻头的磨法:麻花钻头刃磨方法与技巧【图解】
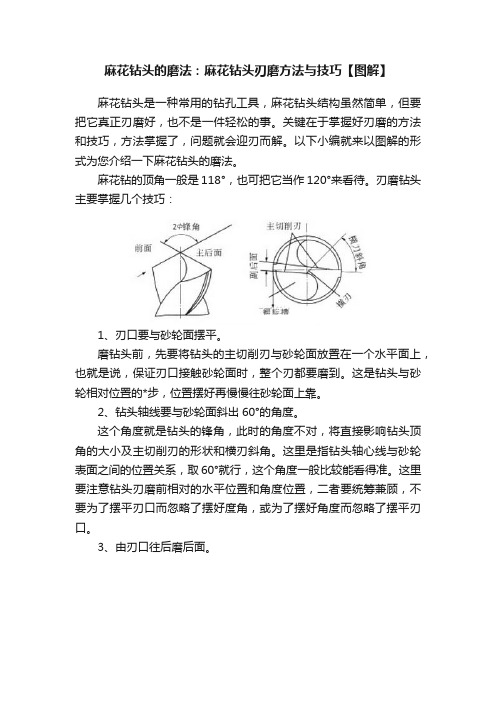
麻花钻头的磨法:麻花钻头刃磨方法与技巧【图解】麻花钻头是一种常用的钻孔工具,麻花钻头结构虽然简单,但要把它真正刃磨好,也不是一件轻松的事。
关键在于掌握好刃磨的方法和技巧,方法掌握了,问题就会迎刃而解。
以下小编就来以图解的形式为您介绍一下麻花钻头的磨法。
麻花钻的顶角一般是118°,也可把它当作120°来看待。
刃磨钻头主要掌握几个技巧:1、刃口要与砂轮面摆平。
磨钻头前,先要将钻头的主切削刃与砂轮面放置在一个水平面上,也就是说,保证刃口接触砂轮面时,整个刃都要磨到。
这是钻头与砂轮相对位置的*步,位置摆好再慢慢往砂轮面上靠。
2、钻头轴线要与砂轮面斜出60°的角度。
这个角度就是钻头的锋角,此时的角度不对,将直接影响钻头顶角的大小及主切削刃的形状和横刃斜角。
这里是指钻头轴心线与砂轮表面之间的位置关系,取60°就行,这个角度一般比较能看得准。
这里要注意钻头刃磨前相对的水平位置和角度位置,二者要统筹兼顾,不要为了摆平刃口而忽略了摆好度角,或为了摆好角度而忽略了摆平刃口。
3、由刃口往后磨后面。
刃口接触砂轮后,要从主切削刃往后面磨,也就是从钻头的刃口先开始接触砂轮,而后沿着整个后刀面缓慢往下磨。
钻头切入时可轻轻接触砂轮,先进行较少量的刃磨,并注意观察火花的均匀性,及时调整手上压力大小,还要注意钻头的冷却,不能让其磨过火,造成刃口变色,而至刃口退火。
发现刃口温度高时,要及时将钻头冷却。
4、钻头的刃口要上下摆动,钻头尾部不能起翘。
这是一个标准的钻头磨削动作,主切削刃在砂轮上要上下摆动,也就是握钻头前部的手要均匀地将钻头在砂轮面上上下摆动。
而握柄部的手却不能摆动,还要防止后柄往上翘,即钻头的尾部不能高翘于砂轮水平中心线以上,否则会使刃口磨钝,无法切削。
这是*关键的一步,钻头磨得好与坏,与此有很大的关系。
在磨得差不多时,要从刃口开始,往后角再轻轻蹭一下,让刃后面更光洁一些。
5、保证刃尖对轴线,两边对称慢慢修。
常见钻孔过程中容易发生的质量问题
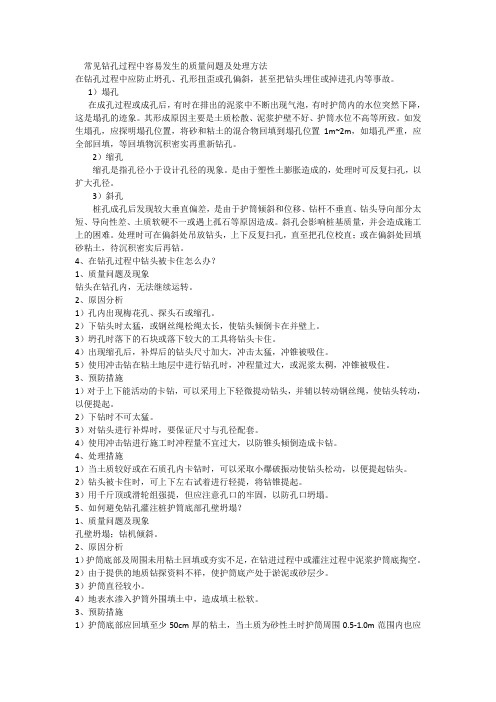
常见钻孔过程中容易发生的质量问题及处理方法在钻孔过程中应防止坍孔、孔形扭歪或孔偏斜,甚至把钻头埋住或掉进孔内等事故。
1)塌孔在成孔过程或成孔后,有时在排出的泥浆中不断出现气泡,有时护筒内的水位突然下降,这是塌孔的迹象。
其形成原因主要是土质松散、泥浆护壁不好、护筒水位不高等所致。
如发生塌孔,应探明塌孔位置,将砂和粘土的混合物回填到塌孔位置1m~2m,如塌孔严重,应全部回填,等回填物沉积密实再重新钻孔。
2)缩孔缩孔是指孔径小于设计孔径的现象。
是由于塑性土膨胀造成的,处理时可反复扫孔,以扩大孔径。
3)斜孔桩孔成孔后发现较大垂直偏差,是由于护筒倾斜和位移、钻杆不垂直、钻头导向部分太短、导向性差、土质软硬不一或遇上孤石等原因造成。
斜孔会影响桩基质量,并会造成施工上的困难。
处理时可在偏斜处吊放钻头,上下反复扫孔,直至把孔位校直;或在偏斜处回填砂粘土,待沉积密实后再钻。
4、在钻孔过程中钻头被卡住怎么办?1、质量问题及现象钻头在钻孔内,无法继续运转。
2、原因分析1)孔内出现梅花孔、探头石或缩孔。
2)下钻头时太猛,或钢丝绳松绳太长,使钻头倾倒卡在并壁上。
3)坍孔时落下的石块或落下较大的工具将钻头卡住。
4)出现缩孔后,补焊后的钻头尺寸加大,冲击太猛,冲锥被吸住。
5)使用冲击钻在粘土地层中进行钻孔时,冲程量过大,或泥浆太稠,冲锥被吸住。
3、预防措施1)对于上下能活动的卡钻,可以采用上下轻微提动钻头,并辅以转动钢丝绳,使钻头转动,以便提起。
2)下钻时不可太猛。
3)对钻头进行补焊时,要保证尺寸与孔径配套。
4)使用冲击钻进行施工时冲程量不宜过大,以防锥头倾倒造成卡钻。
4、处理措施1)当土质较好或在石质孔内卡钻时,可以采取小爆破振动使钻头松动,以便提起钻头。
2)钻头被卡住时,可上下左右试着进行轻提,将钻锥提起。
3)用千斤顶或滑轮组强提,但应注意孔口的牢固,以防孔口坍塌。
5、如何避免钻孔灌注桩护筒底部孔壁坍塌?1、质量问题及现象孔壁坍塌;钻机倾斜。
麻花钻钻孔中常见问题和解决办法
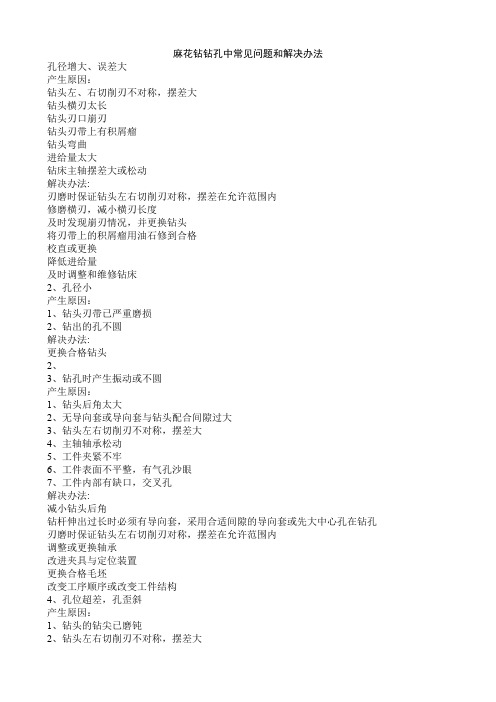
麻花钻钻孔中常见问题和解决办法孔径增大、误差大产生原因:钻头左、右切削刃不对称,摆差大钻头横刃太长钻头刃口崩刃钻头刃带上有积屑瘤钻头弯曲进给量太大钻床主轴摆差大或松动解决办法:刃磨时保证钻头左右切削刃对称,摆差在允许范围内修磨横刃,减小横刃长度及时发现崩刃情况,并更换钻头将刃带上的积屑瘤用油石修到合格校直或更换降低进给量及时调整和维修钻床2、孔径小产生原因:1、钻头刃带已严重磨损2、钻出的孔不圆解决办法:更换合格钻头2、3、钻孔时产生振动或不圆产生原因:1、钻头后角太大2、无导向套或导向套与钻头配合间隙过大3、钻头左右切削刃不对称,摆差大4、主轴轴承松动5、工件夹紧不牢6、工件表面不平整,有气孔沙眼7、工件内部有缺口,交叉孔解决办法:减小钻头后角钻杆伸出过长时必须有导向套,采用合适间隙的导向套或先大中心孔在钻孔刃磨时保证钻头左右切削刃对称,摆差在允许范围内调整或更换轴承改进夹具与定位装置更换合格毛坯改变工序顺序或改变工件结构4、孔位超差,孔歪斜产生原因:1、钻头的钻尖已磨钝2、钻头左右切削刃不对称,摆差大3、钻头横刃太长4、钻头与导向套配合间隙过大5、主轴与导向套中心线不同心,主轴与工作台面不垂直6、钻头在切削时振动7、工件表面不平整,有气孔砂眼8、工件内部有缺口、交叉孔9、导向套低端面与工件表面间的距离远,导向套长度短10、工件夹紧不牢11、工件表面倾斜12、进给量不均匀解决办法:重磨钻头刃磨时保证钻头左右切削刃对称,摆差在允许范围内修磨横刃,减小横刃长度采用合适间隙的导向套校正机床夹具位置。
检查钻床主轴的垂直度先打中心孔再钻孔,采用导向套或改为工件回转的方式更换合格毛坯改变工序顺序或改变工件结构加长导向套长度改进夹具与定位装置正确定位安装使进给量均匀5、钻头折断产生原因:切削用量选择不当钻头崩刃钻头横刃太长钻头已钝,刃带严重磨损呈正锥形导向套底端面与工件表面间的距离太近,排屑困难切削液供应不足切屑堵塞钻头的螺旋槽,或切屑卷在钻头与导向套之间导向套磨损或成倒锥形,退刀时,钻屑夹在钻头与导向套之间快速行程终了位置距工件太近,快速行程转向工件进给时误差大孔钻通时,由于进给阻力迅速下降而进给量突然增加工件或夹具刚性不足,钻通孔时弹性恢复,使进给量突然增加进给丝杠磨损,动力头重锤重量不足。
模具钻孔常见问题与解决方法

模具钻孔常见问题与解决方法模具是生产各类产品的基础装备,通常完成一套模具的加工需要很多步骤,钻孔是模具钳工操作中一项基本操作技能,但是要提高钻削精度有一定难度。
本人结合多年钳工操作教学经验,探讨了一些钻孔加工中常见的问题与解决方法。
标签:模具钻孔钳工钻孔精度一、钻孔过程中打滑现象1.打滑现象的危害。
在生产实践中,操作普通钻床的都遇到过这样的情况,在合金工具钢(或者其他高硬度材料)上打孔时,钻床的夹持部分与麻花钻间常出现打滑现象。
出现这样的打滑现象,首先会是钻孔工作无法进行下去,必须停机重新夹紧钻头,降低了工作效率。
其次发生打滑现象之后,钻头尾部的标记有可能会被钻夹磨掉,甚至出现拉伤拉毛痕迹。
这样可能使我们无法识别钻头尾部标注的直径尺寸,必须使用卡尺进行测量,减低了工作效率。
2 .防止麻花钻打滑措施。
根据实际中遇到的这种情况,我经过思考,因为麻花钻尾部是圆柱形,摩擦力比较小,当钻孔遇到切削力比较大的情况时,容易造成钻床夹持部分夹不住的现象,如果把钻头尾部也加工成正六棱柱的形状,可以大大提高抓握力,就能避免打滑的现象。
麻花钻的改造方法比较简单,使用专用夹具在磨床上加工即可。
二、钻孔时控制孔的精度众所周知孔加工精度包括孔的尺寸精度、位置精度和表面粗糙度。
在笔者所接触过的普通模具加工中,多数孔对于表面粗糙及尺寸精度来说没有太高的要求,一般钻、扩、铰加工之后即可满足精度要求,所以这里我们着重讨论如何保证孔的位置精度。
1.控制底孔的精度。
要保证孔的位置精度,在加工底孔时必须做到“ 三个精确”:画线精确、冲眼精确、起钻精确。
第一步:画线精度对于孔位精度有着至关重要的作用。
要检查高度尺的划针脚是否锋利,画线的要求要细而深,最好一气呵成避免重复划线,这对提高样冲眼的位置精度是很有帮助的。
第二步:当孔位十字线划出之后,为了方便钻孔起定心,需要用样冲冲眼。
打样冲眼时,可将样冲沿着一个方向的画线凹槽向十字中心移动,当感觉样冲尖顶有掉在坑里的感觉时,说明样冲已在十字中心了,此时样冲一定要垂直,轻轻敲击样冲,打上冲眼,然后观察冲眼位置是否准确,如果不准确需要及时纠正再用锥度大一些的样冲把样冲眼扩大,然后根据所钻孔用划规划出几个大小不等的同心“检查圆”或“检查方”。
麻花钻怎么磨好排屑

麻花钻怎么磨好排屑你好标准麻花钻刃磨的方法和技巧标准麻花钻是一种非常普通的钻孔工具。
它结构简单,刃磨方便,但要把它真正刃磨好,把刃磨的方法和技巧掌握好,对初学的职校学生来说,也不是一样轻松的事。
工厂里也有这样的情况,工作了十几年的工人,磨不好麻花钻的也不少。
这是什么原因呢?关键是方法和技巧。
方法掌握了,问题就会迎刃而解。
学生在工艺课中都已经学过了标准麻花钻的相关知识,对标准麻花钻的刃磨要求基本上能背下来:①顶角2 为118°±2º ②孔缘处的后角α0为10°-14°③横刃斜角为50°-55°④两主切削刃长度以及和钻头轴心线组成的两个角要相等⑤两个主后刀面要刃磨光滑。
但是光有理论是不够的,一定要让学生站在砂轮机前亲自动手,动手不是盲目刃磨。
如果不是手把手地指导学生刃磨的方法和技巧,那么理论知识再好的学生,你让他第一次去刃磨一个标准麻花钻,十有八九是不能钻削的。
为什么呢?理论还没有对实践起指导作用。
学生还没有掌握刃磨的技能和技巧。
常用的标准麻花钻虽然只刃磨二个主后刀面和修磨横刃,但在刃磨以后要保证顶角、横刃斜角以及两主切削长短相等,左右等高。
而且在修磨横刃以后,使钻头在钻孔过程中切削轻快,排屑正常,确实有一定的难度。
首先要帮助学生树立起信心,信心决定动力。
在掌握了方法和技巧以后,刃磨出一个合格的标准麻花钻也并不是很难的。
其次要明确地告诉他们少磨多看,盲目的刃磨,越磨越盲目,把一支长长的钻头磨完了,还不知其所以然。
只有少磨多看,多分析、多理解,理论才会慢慢地指导实践。
少磨,就是在不得要领时少磨、甚至不磨。
这样可以节约盲目刃磨产生的浪费,也可以潜心研究一番如何磨。
多看,就是看书本上的知识、图解,看教师的刃磨动作,看刃磨好的合格的标准麻花钻,看各种有刃磨缺陷的麻花钻。
静心地看,用心地看,这是非常重要的。
使他们对麻花钻的“好”与“坏”有一个基本的认识。
钻孔缺陷分析

钻孔质量问题分析、快速判断、解决方法

印制板钻孔的质量缺陷通常分为钻孔缺陷和孔内缺陷。
需要提醒的是有时在实际的操作过程中,会发生数控机床运行的实际转速和下速与软件中的设置不符合的情况。
因一般的判断故障的前提是认为设备完好的情况下。
所以设备的完好对工艺人员判断产品的质量问题有十分重要的作用。
下面是一种快速故障诊断的方法。
判断的方法从1到后面逐步排除找出问题。
1.检查所设置钻头的钻孔参数是否正确,主要是转速和下速。
确诊是否是设置和程序上的问题。
2.如钻孔参数正确,将线路板放到两台机床上(注:机床型号需相同,一般的厂都有条件)采用同样或不同样的设置进行钻孔,确诊是否是机床上的问题或程序上的问题(注意如采用中央吸尘的要考虑吸尘真空度的因素)。
因同时二台机床出同样的问题概率较少,可分析出是否是设备或程序上的问题。
3.如问题仍然存在,更换原材料及上下垫板的材料进行试验(采用更换材料批号和生产厂家二种),有时由于各种原因一时无法更换可采用烘板的方式(150度2-3小时自然冷却后再钻孔)。
4.如问题仍然存在,更换钻头进行试验(采用更换材料批号和生产厂家二种),一般名牌厂商的钻头问题较少。
(关闭本窗口)。
标准麻花钻的修磨方法

标准麻花钻的修磨方法
麻花钻是一种常用的金属加工刀具,广泛应用于机械加工、汽车制造、航空航
天等领域。
然而,由于长时间使用和不当操作,麻花钻往往会出现磨损、变形等问题,影响加工质量和效率。
因此,正确的修磨方法对于延长麻花钻的使用寿命、提高加工质量至关重要。
首先,我们需要准备一些必要的工具,包括磨床、砂轮、砂轮架、卡盘等。
在
进行修磨之前,需要对麻花钻进行仔细的检查,确保没有明显的裂纹、变形等缺陷。
接下来,我们可以按照以下步骤进行修磨:
第一步,修整刃部。
将麻花钻夹紧在卡盘上,通过砂轮架将刃部修整成所需的
形状和角度。
在修整刃部时,需要注意保持刃部的对称性和平整度,避免出现刃部不均匀、刃口不锐利等问题。
第二步,修磨刃口。
使用合适的砂轮对麻花钻的刃口进行修磨,确保刃口的锋
利度和光洁度。
在修磨刃口时,需要控制好修磨的力度和速度,避免过度修磨导致刃口变钝或者产生裂纹。
第三步,清洁和涂抹。
修磨完成后,需要用清洁剂将麻花钻进行清洁,去除表
面的金属屑和油污。
然后,可以在刃部和刃口上涂抹一层薄薄的润滑油,以防止麻花钻在使用过程中产生过多的摩擦和磨损。
最后,进行质量检验。
修磨完成后,需要对麻花钻进行质量检验,包括刃部的
形状和角度、刃口的锋利度和光洁度等方面。
只有通过了质量检验,麻花钻才能够重新投入使用。
总之,标准麻花钻的修磨方法是一项需要技术和经验的工作。
通过正确的修磨
方法,可以有效地延长麻花钻的使用寿命,提高加工质量和效率。
希望本文所述的修磨方法对于大家有所帮助。
浅谈修磨麻花钻提高生产效率
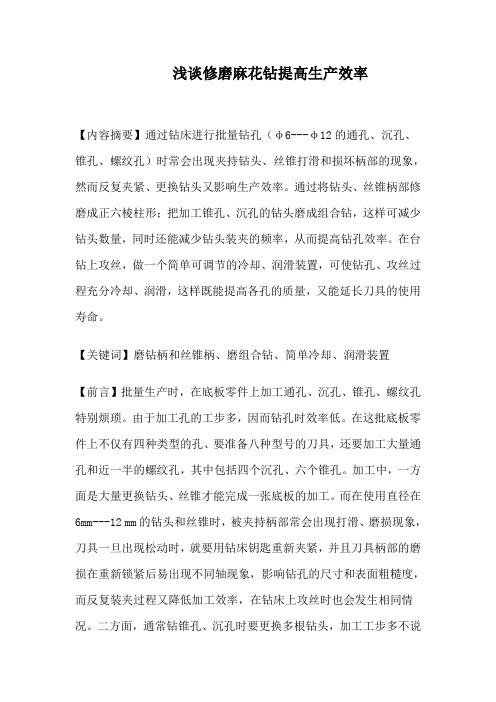
浅谈修磨麻花钻提高生产效率【内容摘要】通过钻床进行批量钻孔(φ6---φ12的通孔、沉孔、锥孔、螺纹孔)时常会出现夹持钻头、丝锥打滑和损坏柄部的现象,然而反复夹紧、更换钻头又影响生产效率。
通过将钻头、丝锥柄部修磨成正六棱柱形;把加工锥孔、沉孔的钻头磨成组合钻,这样可减少钻头数量,同时还能减少钻头装夹的频率,从而提高钻孔效率。
在台钻上攻丝,做一个简单可调节的冷却、润滑装置,可使钻孔、攻丝过程充分冷却、润滑,这样既能提高各孔的质量,又能延长刀具的使用寿命。
【关键词】磨钻柄和丝锥柄、磨组合钻、简单冷却、润滑装置【前言】批量生产时,在底板零件上加工通孔、沉孔、锥孔、螺纹孔特别烦琐。
由于加工孔的工步多,因而钻孔时效率低。
在这批底板零件上不仅有四种类型的孔、要准备八种型号的刀具,还要加工大量通孔和近一半的螺纹孔,其中包括四个沉孔、六个锥孔。
加工中,一方面是大量更换钻头、丝锥才能完成一张底板的加工。
而在使用直径在6mm---12 mm的钻头和丝锥时,被夹持柄部常会出现打滑、磨损现象,刀具一旦出现松动时,就要用钻床钥匙重新夹紧,并且刀具柄部的磨损在重新锁紧后易出现不同轴现象,影响钻孔的尺寸和表面粗糙度,而反复装夹过程又降低加工效率,在钻床上攻丝时也会发生相同情况。
二方面,通常钻锥孔、沉孔时要更换多根钻头,加工工步多不说还会出现孔不同轴现象,钻孔时振动大、孔的表面质量差,且沉孔、锥孔深度也不均匀。
三方面,在攻丝时,用毛刷往底板上孔内加冷却润滑液,效率低又浪费而且还容易遗漏加工的孔。
四方面,冷却、润滑不充分在攻丝时也容易导致丝锥折断,也会加快刀具的磨损而失效,从而影响丝锥寿命增加加工成本。
【正文】在长期的钳工实践中我发现,钻孔不仅在零件加工方面占有重要的地位,而且在大批量生产中提高加工效率显得更为重要。
经过自己的摸索和实践,最终找到了这批产品的问题所在,采用修磨麻花钻、改善冷却液的供给来提高钻孔的效率。
一、在这批生产加工中 (孔直径在6mm---12 mm),我发现钻头柄部夹持部位经常会出现打滑的现象,并导致钻夹头把钻头柄部的标记磨掉,甚至在柄部划出拉伤的痕迹。
标准麻花钻的缺点
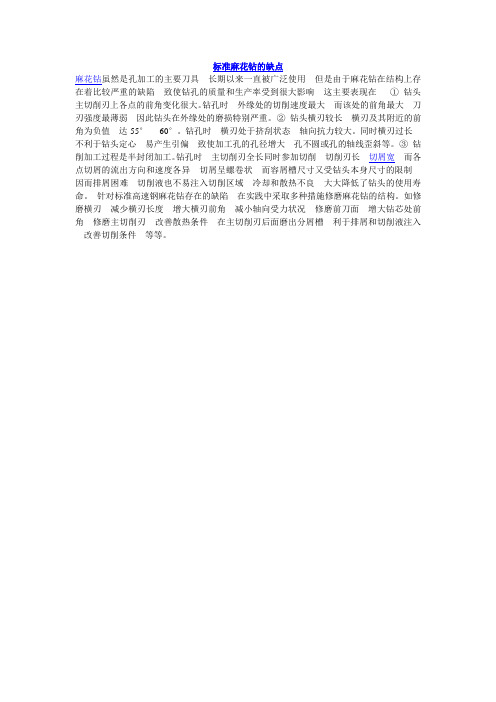
标准麻花钻的缺点
麻花钻虽然是孔加工的主要刀具长期以来一直被广泛使用但是由于麻花钻在结构上存在着比较严重的缺陷致使钻孔的质量和生产率受到很大影响这主要表现在①钻头主切削刃上各点的前角变化很大。
钻孔时外缘处的切削速度最大而该处的前角最大刀刃强度最薄弱因此钻头在外缘处的磨损特别严重。
②钻头横刃较长横刃及其附近的前角为负值达-55°-60°。
钻孔时横刃处于挤刮状态轴向抗力较大。
同时横刃过长不利于钻头定心易产生引偏致使加工孔的孔径增大孔不圆或孔的轴线歪斜等。
③钻削加工过程是半封闭加工。
钻孔时主切削刃全长同时参加切削切削刃长切屑宽而各点切屑的流出方向和速度各异切屑呈螺卷状而容屑槽尺寸又受钻头本身尺寸的限制因而排屑困难切削液也不易注入切削区域冷却和散热不良大大降低了钻头的使用寿命。
针对标准高速钢麻花钻存在的缺陷在实践中采取多种措施修磨麻花钻的结构。
如修磨横刃减少横刃长度增大横刃前角减小轴向受力状况修磨前刀面增大钻芯处前角修磨主切削刃改善散热条件在主切削刃后面磨出分屑槽利于排屑和切削液注入改善切削条件等等。
麻花钻钻孔中常见问题的原因和解决办法
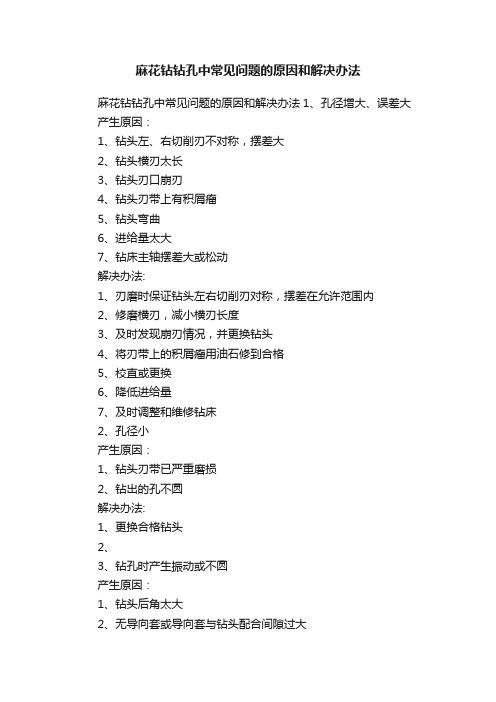
麻花钻钻孔中常见问题的原因和解决办法麻花钻钻孔中常见问题的原因和解决办法1、孔径增大、误差大产生原因:1、钻头左、右切削刃不对称,摆差大2、钻头横刃太长3、钻头刃口崩刃4、钻头刃带上有积屑瘤5、钻头弯曲6、进给量太大7、钻床主轴摆差大或松动解决办法:1、刃磨时保证钻头左右切削刃对称,摆差在允许范围内2、修磨横刃,减小横刃长度3、及时发现崩刃情况,并更换钻头4、将刃带上的积屑瘤用油石修到合格5、校直或更换6、降低进给量7、及时调整和维修钻床2、孔径小产生原因:1、钻头刃带已严重磨损2、钻出的孔不圆解决办法:1、更换合格钻头2、3、钻孔时产生振动或不圆产生原因:1、钻头后角太大2、无导向套或导向套与钻头配合间隙过大3、钻头左右切削刃不对称,摆差大4、主轴轴承松动5、工件夹紧不牢6、工件表面不平整,有气孔沙眼7、工件内部有缺口,交叉孔解决办法:1、减小钻头后角2、钻杆伸出过长时必须有导向套,采用合适间隙的导向套或先大中心孔在钻孔3、刃磨时保证钻头左右切削刃对称,摆差在允许范围内4、调整或更换轴承5、改进夹具与定位装置6、更换合格毛坯7、改变工序顺序或改变工件结构4、孔位超差,孔歪斜产生原因:1、钻头的钻尖已磨钝2、钻头左右切削刃不对称,摆差大3、钻头横刃太长4、钻头与导向套配合间隙过大5、主轴与导向套中心线不同心,主轴与工作台面不垂直6、钻头在切削时振动7、工件表面不平整,有气孔砂眼8、工件内部有缺口、交叉孔9、导向套低端面与工件表面间的距离远,导向套长度短10、工件夹紧不牢11、工件表面倾斜12、进给量不均匀解决办法:1、重磨钻头2、刃磨时保证钻头左右切削刃对称,摆差在允许范围内3、修磨横刃,减小横刃长度4、采用合适间隙的导向套5、校正机床夹具位置。
检查钻床主轴的垂直度6、先打中心孔再钻孔,采用导向套或改为工件回转的方式7、更换合格毛坯8、改变工序顺序或改变工件结构9、加长导向套长度10、改进夹具与定位装置11、正确定位安装12、使进给量均匀5、钻头折断产生原因:1、切削用量选择不当2、钻头崩刃3、钻头横刃太长4、钻头已钝,刃带严重磨损呈正锥形5、导向套底端面与工件表面间的距离太近,排屑困难6、切削液供应不足7、切屑堵塞钻头的螺旋槽,或切屑卷在钻头与导向套之间8、导向套磨损或成倒锥形,退刀时,钻屑夹在钻头与导向套之间9、快速行程终了位置距工件太近,快速行程转向工件进给时误差大10、孔钻通时,由于进给阻力迅速下降而进给量突然增加11、工件或夹具刚性不足,钻通孔时弹性恢复,使进给量突然增加12、进给丝杠磨损,动力头重锤重量不足。
麻花钻轧制常见的问题及解决办法

麻花钻轧制常见的问题及解决办法刘莉【摘要】针对麻花钻轧制过程中出现的打滑、轧裂、刃带充不满、翘背等问题,文中进行了原因分析,并提出了相应的解决办法.【期刊名称】《机械工程师》【年(卷),期】2012(000)004【总页数】2页(P131-132)【关键词】轧制打滑;刃瓣差;飞边;翘背;裂纹【作者】刘莉【作者单位】哈尔滨量具刃具集团有限责任公司,哈尔滨150040【正文语种】中文【中图分类】TG3351 四辊轧制麻花钻头工艺方法图1四辊轧制麻花钻头工艺方法,是利用两对倾斜安装的扇形板形,成一个麻花钻头截形的封闭孔形,使加热后的毛坯在扇形板旋转压力的作用下,在轧制区产生径向展宽和轴向的延伸,同时做旋转运动。
使得毛坯从封闭孔型中通过,从而产生出麻花钻的螺旋外形,即钻形毛坯(见图1、图2)。
图2这种热变形的辊轧方法加工钻头,在调整和轧制过程中变化的掌握上,不像冷加工铣制方法那样简单直观,要在一次变形中辊轧出几个尺寸和技术要求都合格的钻形毛坯,必须掌握机床设备的结构性能、工艺特点及变形的规律,特别是要掌握正常变形影响的诸多因素,除了受机床本身的精度、辊轧速度、材料性质、加热温度等条件的影响外,必需保证的条件是:(1)扇形板的截形要准确,一副扇形板的截形对应位置上的误差要求不超过0.01mm,且表面粗糙度也要一致;(2)孔形要对称,保证封闭孔形对中心的对称性;(3)孔形中心、送料导套中心、接料到导套中心要同心。
2 轧制过程中存在的问题及解决方法在轧制过程中,由于机床和扇形板精度的影响,扇形板截形的正确性、机床调整的准确度、毛坯料的质量和加热温度等因素的影响,经常出现一些如打滑、轧裂、刃带充不满、翘背等问题,通过几年的工作经历,总结出一些经验,现简单介绍如下。
2.1 轧制时打滑(1)产生的主要原因:(a)开始轧制时扇形板温度低。
(b)扇形板工作表面有油污等脏物。
(c)坯料表面不洁净。
(d)坯料加热温度低或加热速度快,未热透。
打孔机常见故障和排除方法

打孔机常见故障和排除方法1.电源故障电源故障是打孔机故障的常见原因之一、解决方法如下:-检查电源插座和插头是否完好无损,并确保插座正常供电。
-检查电源线是否有线路断裂或短路现象,如有需要及时更换电源线。
-检查电源开关是否处于正常工作状态,尝试多次开关电源,或重启打孔机。
2.钻头卡住或磨损钻头卡住或磨损是打孔机常见的故障之一,可能导致打孔效果不佳。
排除方法如下:-首先检查钻头是否正确安装,如若不正确,则重新安装钻头。
-检查钻头是否有严重磨损的情况,如有需要及时更换钻头。
-有时打孔机使用时间过长,打孔机内部的润滑油可能已经干涸,导致钻头卡住或磨损。
此时需要给打孔机加润滑油,或者对打孔机进行清洁和维护。
3.纸张卡住纸张卡住是打孔机常见的故障之一,可能导致打孔机无法正常工作。
排除方法如下:-首先断电,然后轻轻拔出被卡住的纸张,尽量不要使用力过大,以免将纸张撕裂。
-如果纸张比较紧密卡住,可以试着把打孔机的排针位置调整到打孔机底部,这样纸张就会自动松开。
-检查打孔机的皮带是否松弛或断裂,如有需要及时更换皮带。
4.打孔结果不令人满意打孔结果不令人满意是打孔机常见的故障之一,可能是因为操作不当或打孔机本身问题。
排除方法如下:-首先检查打孔机的导向器是否正确调整,如果导向器位置不准确,可能会导致打孔位置有偏差。
-检查打孔机的钻头是否磨损,如果钻头磨损严重,可能会导致打孔效果不佳。
-检查打孔机的速度控制是否合适,如果速度过快或过慢,会影响打孔的效果。
-检查打孔机的质量控制,如果打孔机本身质量不好,可能会导致打孔结果不理想。
钻孔中产生的问题
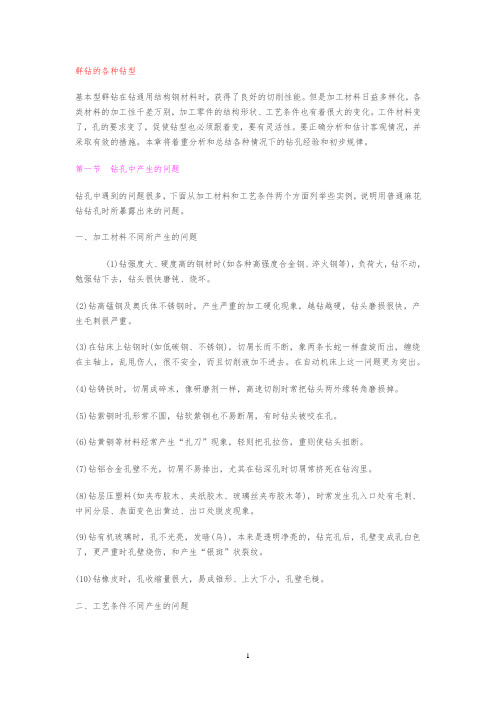
群钻的各种钻型基本型群钻在钻通用结构钢材料时,获得了良好的切削性能。
但是加工材料日益多样化,各类材料的加工性千差万别,加工零件的结构形状、工艺条件也有着很大的变化。
工件材料变了,孔的要求变了,促使钻型也必须跟着变,要有灵活性。
要正确分析和估计客观情况,并采取有效的措施。
本章将着重分析和总结各种情况下的钻孔经验和初步规律。
第一节钻孔中产生的问题钻孔中遇到的问题很多,下面从加工材料和工艺条件两个方面列举些实例,说明用普通麻花钻钻孔时所暴露出来的问题。
一、加工材料不同所产生的问题(1)钻强度大、硬度高的钢材时(如各种高强度合金钢、淬火钢等),负荷大,钻不动,勉强钻下去,钻头很快磨钝、烧坏。
(2)钻高锰钢及奥氏体不锈钢时,产生严重的加工硬化现象,越钻越硬,钻头磨损很快,产生毛刺很严重。
(3)在钻床上钻钢时(如低碳钢、不锈钢),切屑长而不断,象两条长蛇一样盘旋而出,缠绕在主轴上,乱甩伤人,很不安全,而且切削液加不进去。
在自动机床上这一问题更为突出。
(4)钻铸铁时,切屑成碎末,像研磨剂一样,高速切削时常把钻头两外缘转角磨损掉。
(5)钻紫铜时孔形常不圆,钻软紫铜也不易断屑,有时钻头被咬在孔。
(6)钻黄铜等材料经常产生“扎刀”现象,轻则把孔拉伤,重则使钻头扭断。
(7)钻铝合金孔壁不光,切屑不易排出,尤其在钻深孔时切屑常挤死在钻沟里。
(8)钻层压塑料(如夹布胶木、夹纸胶木、玻璃丝夹布胶木等),时常发生孔入口处有毛刺、中间分层、表面变色出黄边、出口处脱皮现象。
(9)钻有机玻璃时,孔不光亮,发暗(乌),本来是透明净亮的,钻完孔后,孔壁变成乳白色了,更严重时孔壁烧伤,和产生“银斑”状裂纹。
(10)钻橡皮时,孔收缩量很大,易成锥形、上大下小,孔壁毛糙。
二、工艺条件不同产生的问题(1)钻薄板孔,有时工件不便于压紧,人们多采用手扶,但当钻头刚要钻出工件时,手就扶不住工件了,发生抖动,很容易出工伤事故。
另外,孔易产生多角形、毛刺和变形。
麻花钻钻孔常见问题有哪些?原因及解决办法汇总
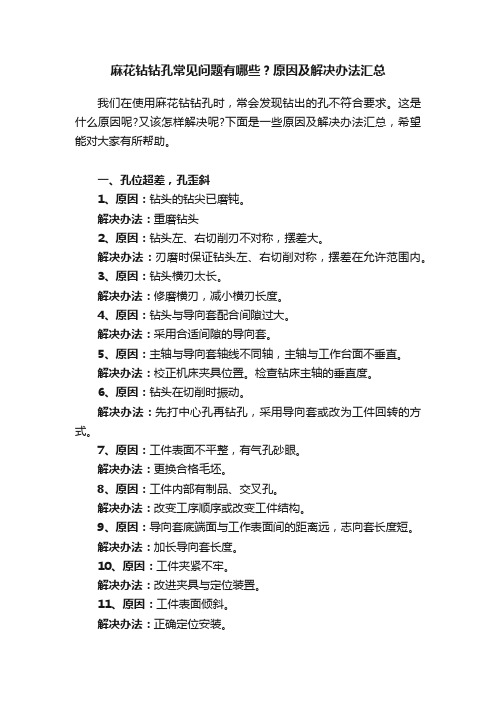
麻花钻钻孔常见问题有哪些?原因及解决办法汇总我们在使用麻花钻钻孔时,常会发现钻出的孔不符合要求。
这是什么原因呢?又该怎样解决呢?下面是一些原因及解决办法汇总,希望能对大家有所帮助。
一、孔位超差,孔歪斜1、原因:钻头的钻尖已磨钝。
解决办法:重磨钻头2、原因:钻头左、右切削刃不对称,摆差大。
解决办法:刃磨时保证钻头左、右切削对称,摆差在允许范围内。
3、原因:钻头横刃太长。
解决办法:修磨横刃,减小横刃长度。
4、原因:钻头与导向套配合间隙过大。
解决办法:采用合适间隙的导向套。
5、原因:主轴与导向套轴线不同轴,主轴与工作台面不垂直。
解决办法:校正机床夹具位置。
检查钻床主轴的垂直度。
6、原因:钻头在切削时振动。
解决办法:先打中心孔再钻孔,采用导向套或改为工件回转的方式。
7、原因:工件表面不平整,有气孔砂眼。
解决办法:更换合格毛坯。
8、原因:工件内部有制品、交叉孔。
解决办法:改变工序顺序或改变工件结构。
9、原因:导向套底端面与工作表面间的距离远,志向套长度短。
解决办法:加长导向套长度。
10、原因:工件夹紧不牢。
解决办法:改进夹具与定位装置。
11、原因:工件表面倾斜。
解决办法:正确定位安装。
12、原因:进给量不均匀。
解决办法:使进给量均匀。
二、孔径增大、误差大1、原因:钻头左、右切削刃不对称,摆差大。
解决办法:刃磨时保证钻头左、右切削刃对称,摆差在允许范围内。
2、原因:钻头横刃太长。
解决办法:修磨横刃,减小横刃长度。
3、原因:钻头刃口崩刃。
解决办法:及时发现崩刃情况,并更换钻头。
4、原因:钻头刃带上有积屑瘤。
解决办法:将刃带上的积屑瘤用油石修整到合格。
5、原因:钻头弯曲。
解决办法:校直或更换。
6、原因:进给量太大。
解决办法:降低进给量。
7、原因:钻床主轴摆差大或松动。
解决办法:及时调整和维修钻床。
三、孔径小1、原因:钻头后角太大。
解决办法:减小钻头后角。
2、原因:无导向套或导向套与钻头配合间隙过大。
解决办法:钻杆伸出过长时必须有导向套,采用合适的间隙的导向套或先打中心孔再钻孔。
钻孔过程中常见问题原因分析及处理措施

钻孔过程中常见问题原因分析及处理措施关键词:钻孔问题预防措施处理方法前言:桩基础是工业与民用建筑工程一种常用的基础形式。
桩基础作为一种深基础,具有承载力高、稳定性好、沉降量小而均匀、沉降稳定快、良好的抗震性能等特性,因此在各类建筑工程中得到广泛应用,尤其适用于建造在软弱地基上的各类建(构)筑物。
桩按材料可分为钢筋混凝土桩、钢桩、木桩等,按受力分类为摩擦桩和端承桩,按桩的入土方法可分为打入桩、压入桩和灌注桩等。
建筑工程桩基础不论采用何种类型的桩,实际施工过程中保证桩基质量,使桩基符合设计要求,是基础工程施工中经常遇到的问题。
1塌孔1.1塌孔原因分析塌孔是一种最常见的事故,在钻孔过程中或在成孔后都有可能发生,究其原因如下。
(1)泥浆稠度小,护壁效果差,出现漏水;或护筒埋置较浅,周围封堵不密实而出现漏水;或护筒底部土层厚度不足,护筒底部出现漏水,造成泥浆水头高度不足,对孔壁压力小。
(2)泥浆相对密度过小,水头对孔壁的压力较小。
(3)在松软的砂层中进尺过快,泥浆护壁形成较慢,孔壁渗水。
(4)钻进时中途停钻时间较长,孔内水头未能保持在孔外水位或地下水位线以上2.0m,降低了水头对孔壁的压力。
(5)提升钻头或掉放钢筋笼时碰撞孔壁。
(6)钻孔附近有大型设备或车辆振动。
(7)孔内水流失造成水头高度不够。
(8)清孔后未能及时灌注混凝土,放置时间过长。
1.2塌孔的预防措施(1)根据设计部门提供的地质勘探资料,对于不同的地质情况,选用适宜的泥浆比重,泥浆粘度和不同的钻进速度。
如在砂层中,应选用较好的造浆材料,加大泥浆稠度提高泥浆粘度以加强护壁,并适当降低进尺速度。
(2)在陆地上埋置护筒时,底部应夯填密实,护筒周围也要回填密实。
(3)水中振动沉入护筒时,根据地质资料,将护筒穿过淤泥及透水层,护筒衔接严密不漏水。
(4)由于汛期或潮汐水位变化大时,采取升高护筒,增加水头保证水头压力相对稳定。
(5)钻孔无特殊原因应尽量连续作业。
麻花钻头的磨法麻花钻头磨法图解

麻花钻头的磨法麻花钻头磨法图解.标准麻花钻的修磨方法1、修磨横刃(1)磨去横刃,形成新的切削刃(鱼嘴形)。
修磨后加大该处前角,使轴向力大大降低。
但这种刃形切削时定心不好,钻孔精度差;且钻心强度减弱,易崩刃。
只用于钻铸铁等强度低的材料,一般少用。
(2)十字形刃磨,横刃长度不变,修磨处加大横刃前角,但钻心强度减弱,不宜加工硬质材料,主要用于钻深孔。
它须用专用夹具刃磨。
法。
麻花钻头的磨法:1.“刃口摆平轮面靠。
”这是钻头与砂轮相对位置的第一步,往往有学生还没有把刃口摆平就靠在砂轮上开始刃磨了。
这样肯定是磨不好的。
这里的“刃口”是主切削刃,“摆平”是指被刃磨部分的主切削刃处于水平位置。
“轮面”是指砂轮的表面。
“靠”是慢慢靠拢的意思。
此时钻头还不能接触砂轮。
2.“钻轴斜放出锋角。
”这里是指钻头轴心线与砂轮表面之间的位置关系。
“锋角”即顶角118°±2o的一半,约为60°这个位置很重要,直接影响钻头顶角大小及主切削刃形状和横刃斜角。
要提示学生记忆常用的一块30°、60°、90°三角板中60°的角度,学生便于掌握。
口诀一和口诀二都是指钻头刃磨前的相对位置,二者要统筹兼顾,不要为了摆平刃口而忽略了摆好斜角,或为了摆好斜放轴线而忽略了摆平刃口。
在实际操作中往往很会出这些错误。
此时钻头在位置正确的情况下准备接触砂轮。
3.“由刃向背磨后面。
”这里是指从钻头的刃口开始沿着整个后刀面缓慢刃磨。
这样便于散热和刃磨。
在稳定巩固口诀一、二的基础上,此时钻头可轻轻接触砂轮,进行较少量的刃磨,刃磨时要观察火花的均匀性,要及时调整压力大小,并注意钻头的冷却。
当冷却后重新开始刃磨时,要继续摆好口诀一、二的位置,这一点往往在初学时不易掌握,常常会不由自主地改变其位置的正确性。
4.“上下摆动尾别翘。
”这个动作在钻头刃磨过程中也很重要,往往有学生在刃磨时把“上下摆动”变成了“上下转动”,使钻头的另一主刀刃被破坏。
钻孔中的常见问题及处理
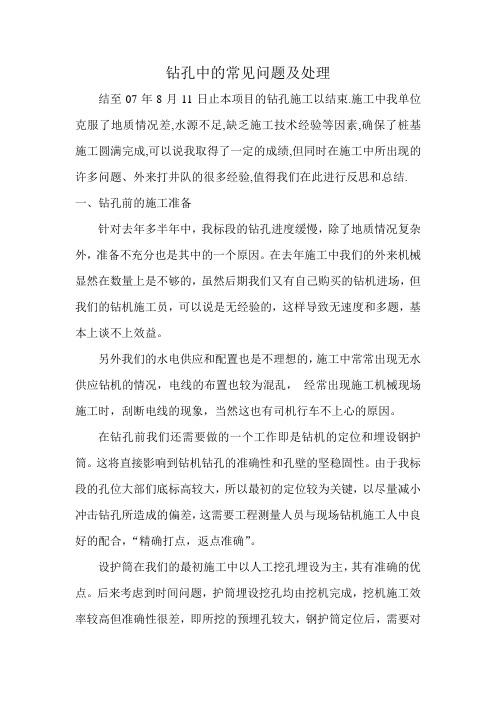
钻孔中的常见问题及处理结至07年8月11日止本项目的钻孔施工以结束.施工中我单位克服了地质情况差,水源不足,缺乏施工技术经验等因素,确保了桩基施工圆满完成,可以说我取得了一定的成绩,但同时在施工中所出现的许多问题、外来打井队的很多经验,值得我们在此进行反思和总结.一、钻孔前的施工准备针对去年多半年中,我标段的钻孔进度缓慢,除了地质情况复杂外,准备不充分也是其中的一个原因。
在去年施工中我们的外来机械显然在数量上是不够的,虽然后期我们又有自己购买的钻机进场,但我们的钻机施工员,可以说是无经验的,这样导致无速度和多题,基本上谈不上效益。
另外我们的水电供应和配置也是不理想的,施工中常常出现无水供应钻机的情况,电线的布置也较为混乱,经常出现施工机械现场施工时,刮断电线的现象,当然这也有司机行车不上心的原因。
在钻孔前我们还需要做的一个工作即是钻机的定位和埋设钢护筒。
这将直接影响到钻机钻孔的准确性和孔壁的坚稳固性。
由于我标段的孔位大部们底标高较大,所以最初的定位较为关键,以尽量减小冲击钻孔所造成的偏差,这需要工程测量人员与现场钻机施工人中良好的配合,“精确打点,返点准确”。
设护筒在我们的最初施工中以人工挖孔埋设为主,其有准确的优点。
后来考虑到时间问题,护筒埋设挖孔均由挖机完成,挖机施工效率较高但准确性很差,即所挖的预埋孔较大,钢护筒定位后,需要对其四周的回填土进仔细压实,以防止孔内泥浆渗透周围土层造成护筒塌陷,影响施工。
我们也可以采取用沙袋四周堆砌的方法来确保护筒稳定。
另外护筒自身长度,对于护筒稳定也较为重要,其也是防止漏浆塌也的一项措施。
二、漏浆及塌孔的处理。
漏浆问题一直是我标段钻机施工中一项较为棘手的问题之一。
在06年的大半年中,此问题严重影响了我们的钻孔施工进度并造成了许多不必要的经济的损失。
漏浆主要是孔位下有溶洞造成的。
针对此问题我们所采取的措施一是,根据地质报告所反应的溶洞情况深埋护筒,从根本上防止漏止漏浆,此方法较为安全有效,但需要较大的投入和专业的护筒埋设队伍。
3.5钻孔过程中容易出现的问题
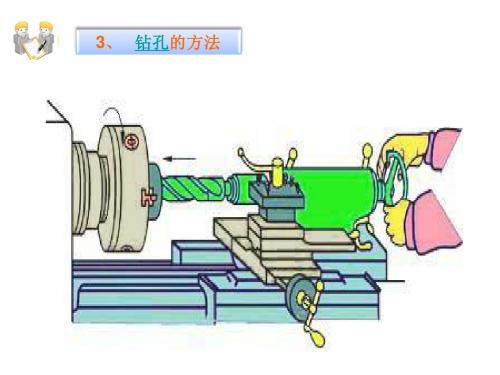
4 钻头直径小于5㎜时,先用中心钻钻出中心孔, 再用麻花钻钻孔。
1.钻孔应车端面,防止钻头摆动折断钻头。
2.尾座应和主轴同心,防止钻削时孔径扩大。
3.钻头将要钻透工件时(进给手感轻松)进给量要小。
4.钻头钻进1~2mm时要停车测量孔径,防止孔径超差。
5.钻削前要检查钻头是否弯曲,钻头、钻夹头柄部及钻
钻削前要检查钻头是否弯曲钻头钻夹头柄部及钻套是否干净套是否干净防止钻削时孔径扩大或钻柄在尾座筒内打滑防止钻削时孔径扩大或钻柄在尾座筒内打滑钻孔时应注意问题钻孔时产生的废品分析作业要求
3、 钻孔的方法
1 2
钻孔前工件的端面要平,中心部位不许有凸台。 找正尾座
3.小直径钻头刚性差,钻头横刃接触端面时 钻头产生摆动,容易使钻头折断。可用装 在刀架上的挡铁挡住钻头头部防止摆动, 然后慢进给钻削。
套是否干净,防止钻削时孔径扩大或钻柄在尾座筒内打滑
钻孔时应注意问题
钻孔时产生的废品分析
作业
要求: 独立完成,书写认真,保质保量 习题册: 课题二 时间: 晚自习
- 1、下载文档前请自行甄别文档内容的完整性,平台不提供额外的编辑、内容补充、找答案等附加服务。
- 2、"仅部分预览"的文档,不可在线预览部分如存在完整性等问题,可反馈申请退款(可完整预览的文档不适用该条件!)。
- 3、如文档侵犯您的权益,请联系客服反馈,我们会尽快为您处理(人工客服工作时间:9:00-18:30)。
麻花钻钻孔中常见问题的原因和解决办法1、孔径增大、误差大产生原因:1、钻头左、右切削刃不对称,摆差大2、钻头横刃太长3、钻头刃口崩刃4、钻头刃带上有积屑瘤5、钻头弯曲6、进给量太大7、钻床主轴摆差大或松动解决办法:1、刃磨时保证钻头左右切削刃对称,摆差在允许围2、修磨横刃,减小横刃长度3、及时发现崩刃情况,并更换钻头4、将刃带上的积屑瘤用油石修到合格5、校直或更换6、降低进给量7、及时调整和维修钻床2、孔径小产生原因:1、钻头刃带已严重磨损2、钻出的孔不圆解决办法:1、更换合格钻头2、3、钻孔时产生振动或不圆产生原因:1、钻头后角太大2、无导向套或导向套与钻头配合间隙过大3、钻头左右切削刃不对称,摆差大4、主轴轴承松动5、工件夹紧不牢6、工件表面不平整,有气孔沙眼7、工件部有缺口,交叉孔解决办法:1、减小钻头后角2、钻杆伸出过长时必须有导向套,采用合适间隙的导向套或先大中心孔在钻孔3、刃磨时保证钻头左右切削刃对称,摆差在允许围4、调整或更换轴承5、改进夹具与定位装置6、更换合格毛坯7、改变工序顺序或改变工件结构4、孔位超差,孔歪斜产生原因:1、钻头的钻尖已磨钝2、钻头左右切削刃不对称,摆差大3、钻头横刃太长4、钻头与导向套配合间隙过大5、主轴与导向套中心线不同心,主轴与工作台面不垂直6、钻头在切削时振动7、工件表面不平整,有气孔砂眼8、工件部有缺口、交叉孔9、导向套低端面与工件表面间的距离远,导向套长度短10、工件夹紧不牢11、工件表面倾斜12、进给量不均匀解决办法:1、重磨钻头2、刃磨时保证钻头左右切削刃对称,摆差在允许围3、修磨横刃,减小横刃长度4、采用合适间隙的导向套5、校正机床夹具位置。
检查钻床主轴的垂直度6、先打中心孔再钻孔,采用导向套或改为工件回转的方式7、更换合格毛坯8、改变工序顺序或改变工件结构9、加长导向套长度10、改进夹具与定位装置11、正确定位安装12、使进给量均匀5、钻头折断产生原因:1、切削用量选择不当2、钻头崩刃3、钻头横刃太长4、钻头已钝,刃带严重磨损呈正锥形5、导向套底端面与工件表面间的距离太近,排屑困难6、切削液供应不足7、切屑堵塞钻头的螺旋槽,或切屑卷在钻头与导向套之间8、导向套磨损或成倒锥形,退刀时,钻屑夹在钻头与导向套之间9、快速行程终了位置距工件太近,快速行程转向工件进给时误差大10、孔钻通时,由于进给阻力迅速下降而进给量突然增加11、工件或夹具刚性不足,钻通孔时弹性恢复,使进给量突然增加12、进给丝杠磨损,动力头重锤重量不足。
动力液压缸反压力不足,当空钻通时,动力头自动下落,使进给量增大13、钻铸件时遇到缩孔14、锥柄扁尾折断解决办法:1、减少进给量和切削速度2、及时发现崩刃情况,当加工较硬的钢件时,后角要适当减小3、修磨横刃,减小横刃长度4、及时更换钻头,刃磨时将磨损部分全部磨掉5、加大导向套与工件间的距离6、切削液喷嘴对准加工孔,加大切削液流量7、减小切削速度,进给量;采用断屑措施;或采用分级进给方式,使钻头退出数次8、及时更换导向套9、增加工作行程距离10、修磨钻头顶角,尽可能降低钻孔轴向力;孔将要钻通时,改为手动进给,并控制进给量11、减少机床,工件夹具的弹性变形;改进夹紧定位,增加工件,夹具的钢性;增加二次进给12、及时维修机床,增加动力头重锤重量,增加二次进给13、对估计有缩孔的铸件要减少进给量14、更换钻头,并注意擦净锥柄油污6、钻头寿命低产生原因:1、同第五项之1、2、3、4、5、6、72、钻头切削部分几何形状与所加工的材料不适应3、其他解决办法1、同第五项之1、2、3、4、5、6、72、加工铜件时,钻头应选用较小后角,避免钻头自动钻入工件,使进给量突然增加;加工低碳钢时,可适当增大后角,以增加钻头寿命;加工较硬的钢材时,可采用双重钻头顶角,开分屑槽或修磨横刃等,以增加钻头寿命3、改用新型适用的高速钢(铝高速钢、钴高速钢)钻头或采用涂层刀具;消除加工件的夹砂、硬点等不正常情况7、孔壁表面粗糙产生原因:1、钻头不锋利2、后角太大3、进给量太大4、切削液供给不足,切削液性能差5、切屑堵塞钻头的螺旋槽6、夹具的刚性不足7、工件材料硬度过低解决办法:1、将钻头磨锋利2、采用适当后角3、减少进给量4、加大切削液流量,选择性能好的切削液5、见第五项之76、改进夹具7、增加热处理工序,适当提高工件硬度二、枪钻钻孔中常见问题的原因和解决办法8、孔径增大,误差大。
产生原因:1、切屑粘结2、机床主轴与钻套的同轴度不好3、刀具形状不合适解决方法:1、提高切削速度,减小进给量;换用极压性高的切削液;提高切削液的压力,流量;提高工件的硬度。
2、调整机床主轴与钻套的同轴度;采用合适的钻套直径;减小主轴摆差。
3、钻尖位置向侧移动和加大外刃切削角;减小倒锥,加宽刃带;改变导向块的位置;校正枪钻头部的弯曲和摆差。
9、孔不圆常见原因:1、机床主轴与钻套的同轴度不好2、刀尖形状不合适3、刀具形状不合适4、工件加紧不牢解决办法:1、调整机床主轴与钻套的同轴度2、改变钻尖位置,保持平衡3、调整导向块位置4、改进夹具,使工件加紧力均匀10、孔弯曲、歪斜产生原因:1、机床主轴与钻套的同轴度不好2、刀尖形状不合适3、刀具形状不合适4、进给量太大5、工件夹紧不牢6、工件材料组织不均匀解决办法:1、调整机床主轴与钻套的同轴度;采用合适的钻套直径;减小主轴摆差。
校正钻头头部的弯曲与摆差2、改变外刃切削角、刃切削角与钻尖位置3、改变导向块的位置;导向中心架的数量要合适;采用短粗柄部的枪钻4、减小进给量5、改进夹具,使工件夹紧力均匀6、采用材料组织均匀的工件11、孔表面粗糙产生原因:1、切屑粘结2、同轴度不好3、光作用过小4、颤振5、退刀划痕解决办法:1、提高切削速度,减小进给量;换用极压性高的切削液;提高切削液的压力、流量;提高工件硬度2、调整机床主轴与钻套的同轴度;采用合适的钻套直径3、变动导向块的位置、形状;加宽刃边宽度;减小倒锥量;加大外刃切削角4、设置合适的中心架;尽量缩短枪钻长度;降低切削液的压力;控制光作用5、变动导向块的位置;加大倒锥量;调整机床主轴与钻套同轴度;校正枪钻头部的弯曲及摆差;待主轴停止转动后退刀12、枪钻折断产生原因:1、机床主轴与钻套的同轴度不好2、光作用过大3、断屑不好4、切削用量过大5、枪钻过度磨损6、枪钻崩刃7、孔将钻通时,由于进给阻力迅速下降而使进给量突然增加8、主轴松动解决方法:1、调整机床主轴与钻套的同轴度;采用合适的钻套直径;减小主轴摆差。
校正钻头头部的弯曲与摆差2、变动导向块的位置;加大倒锥量3、改变切削刃的角度,使、外切削刃切削平衡;及时发现崩刃情况,并更换;增大导向套与工件间的距离;加大切削液的压力流量;采用材料组织均匀的工件4、降低切削速度与进给量,避免进给量不均匀5、定期更换枪钻,避免过度磨损6、及时发现崩刃情况并更换,后角要合适7、孔将钻通时,减小进给量8、维修机床13、枪钻寿命低产生原因:1、切削用量过大2、枪钻不合适3、切削液不合适解决方法;1、降低切削速度及进给量2、更换刀具材料;加大油孔与油隙;增大后角,降低刃磨面得粗糙度3、换用极压性高的切削液;增大切削液的压力、流量;改善切削液过滤情况三、排屑深孔钻钻孔中常见问题的原因和解决办法1、孔表面粗糙产生原因:1、切屑粘结2、同轴度不好3、切削速度过低,进给量过大或不均匀4、刀具几何形状不合适解决方法:1、降低切削速度;避免崩刃;换用极压性高的切削液,并改善过滤情况;提高切削液的压力、流量2、调整机床主轴与钻套的同轴度;采用合适的钻套直径3、才用合适的切削用量4、改变切削刃几何角度与导向块的形状2、孔口呈喇叭形产生原因:1、同轴度不好解决方法:1、调整机床主轴、钻套与支承套的同轴度;采用合适的钻套直径,及时更换磨损过大的钻套3、钻头折断产生原因:1、断屑不好,切屑排不出2、进给量过大、过小或不均匀3、钻头过度磨损4、切削液不合适解决方法:1、改变断屑槽尺寸,避免过长、过浅;及时发现崩刃情况,并更换;加大切削液的压力、流量;采用材料组织均匀的工件2、采用合适的切削用量3、定期更换钻头,避免过渡磨损4、选用合适的切削液并改善过滤情况4、钻头寿命低产生原因:1、切削速度过高或过低,进给量过大2、钻头不合适3、切削液不合适解决方法:1、采用合适的切削用量2、更换刀具材料;变动导向块的位置、形状3、换用极压性高的切削液,增大切削液的压力、流量;改善切削液过滤情况5、切屑成带状切屑过小切屑过大产生原因:1、断屑槽几何形状不合适,切屑刃几何形状不合适,进给量过小;工件材料组织不均匀2、断屑槽过短或过深;断屑槽半径过小3、断屑槽过长或过浅;断屑槽半径过大解决方法:1、变动断屑槽及切削刃的几何形状;增大进给量;才用材料组织均匀的工件2、变动断屑槽的几何形状3、变动断屑槽的几何形状四、扩孔钻扩孔中常见问题的原因和解决方法1、孔径增大产生原因:1、扩孔钻切削刃摆差大2、扩孔钻刃带上有切屑瘤3、安装扩孔钻时,锥柄表面油污未擦干净,或锥面有磕、碰伤解决方法:1、刃磨时保证摆差在允许围2、及时发现崩刃情况,更换刀具3、将刃带上的切屑瘤用油石修整到合格4、安装扩孔钻前必须将扩孔钻锥柄及机床主轴锥孔部油污擦干净,锥面有磕、碰处用油石修光2、孔表面粗糙产生原因:1、切削用量过大2、切削液供给不足3、扩孔钻过度磨损解决方法:1、适当降低切削用量2、切削液喷嘴对准加工孔口;加大切削液流量3、定期更换扩孔钻;刃磨时把磨损区全部磨去3、孔位置精度超差产生原因:1、导向套配合间隙大2、主轴与导向套同轴度误差大3、主轴轴承松动解决方法:1、位置公差要求较高时,导向套与刀具配合要精密些2、校正机床与导向套位置3、调整主轴轴承间隙五、多刃铰刀铰孔中常见问题的原因和解决办法1、孔径增大,误差大产生原因:1、铰刀外径尺寸设计值偏大或铰刀刃口有毛刺2、切削速度过高3、进给量不当或加工余量太大4、铰刀主偏角过大5、铰刀弯曲6、铰刀刃口上粘附着切屑瘤7、刃磨时铰刀刃口摆差超差8、切削液选择不合适9、安装铰刀时,锥柄表面油污未擦干净,或锥面有磕、碰伤10、锥柄的扁尾偏位,装入机床主轴后于锥柄圆锥干涉11、主轴弯曲或主轴轴承过松或损坏12、铰刀浮动不灵活,与工件不同轴13、手铰时两手用力不均匀,使铰刀左右晃动解决方法:1、根据具体情况适当减小铰刀外径;将铰刀刃口毛刺修光2、降低切削速度3、适当调整进给量减少加工余量4、适当减小主偏角5、校直或报废弯曲铰刀6、用油石仔细修整到合格7、控制摆差在允许围8、选择冷却性能较好的切削液9、安装铰刀前必须将铰刀锥柄及机床主轴锥孔部油污擦干净,锥面有磕、碰伤处用油石修光10、修磨铰刀扁尾11、调整或更换主轴轴承12、重新调整浮动卡头,并调整同轴度13、注意正确操作2、孔径小产生原因:1、铰刀外径尺寸设计值偏小2、切削速度过低3、进给量过大4、铰刀主偏角过小5、切削液选择不合适6、铰刀已磨损,刃磨时磨损部分未磨去7、铰薄壁刚件时,铰玩孔后孔弹性恢复使孔径缩小8、铰钢料时,余量太大或铰刀不锋利,亦易产生弹性恢复使孔径缩小9、孔不圆,孔径不合格解决方法:1、更改铰刀外径尺寸2、适当提高切削速度3、适当降低进给量4、适当增大主偏角5、选择润滑性好的油性切削液6、定期更换铰刀,正确刃磨铰刀切削部分7、设计铰刀尺寸时应考虑此因素,或根据实际情况取值8、作实验性切削,取合适余量;将铰刀磨锋利9、见序号三3、孔不圆产生原因:1、铰刀过长,刚性不足,铰削时产生振动2、铰刀主偏角过小3、铰刀刃带窄4、铰孔余量偏5、孔表面有缺口、交叉孔6、孔表面有砂眼、气孔7、主轴轴承松动,无导向套,或铰刀与导向套配合间隙过大8、由于薄壁工件装夹过紧,卸下后工件变形解决方法:1、刚性不足的铰刀可才用不等分齿距地铰刀;铰刀的安装应采用刚性联接2、增大主偏角3、选用合格铰刀4、控制预加工工序的孔位误差5、采用不等分齿距地铰刀,采用较长、较精密的导向套6、选用合格毛坯7、采用等距铰刀铰精密的孔时,对机床主轴间隙与导向套的配合间隙应要求较高8、采用恰当的夹紧方法,减小夹紧力4、孔表面有明显的棱面产生原因:1、铰孔余量过大2、铰刀切削部分后角过大3、铰刀刃带过宽4、工件表面有气孔、砂眼5、主轴摆差大解决方法:1、减小铰孔余量2、减小切削部分后角3、修磨刃带宽度4、选用合格毛坯5、调整机床主轴5、孔表面粗糙产生原因:1、切削速度过高2、切削液选择不合适3、铰刀主偏角过大,铰刀刃口不等4、铰孔余量太大5、铰孔余量不均匀或太小,局部表面未铰到6、铰刀切削部分摆差超差,刃口不锋利,表面粗糙7、铰刀刃带过宽8、铰孔时排屑不良9、铰刀过度磨损10、铰刀碰伤,刃口留有毛刺或崩刃11、刃口有积屑瘤由于材料关系,不适用零度前角或负前角铰刀解决方法:1、降低切削速度2、根据加工材料选择切削液3、适当减小主偏角,正确刃磨铰刀刃口4、适当减小铰孔余量5、提高铰孔前底孔位置精度与质量,或增加铰孔余量6、选用合格铰刀7、修磨刃带宽度8、根据具体情况减少铰刀齿数,加大容屑空间,或采用带刃倾角铰刀,使排屑顺利9、定期更换铰刀,刃磨时把磨损区全部磨去10、铰刀在刃磨、使用及运输过程中应采取保护措施,避免磕、碰伤;对已碰伤的铰刀,应用特细的油石将磕、碰修好,或更换铰刀11、用油石修整到合格12、采用前角为5º-10º的铰刀6、铰刀寿命低产生原因:1、铰刀材料不合适2、铰刀在刃磨时烧伤3、切削液选择不合适切削液未能顺利地流到切削处4、铰刀刃磨后表面粗糙度太粗解决方法:1、根据加工材料选择铰刀材料,可才用硬质合金铰刀或涂层铰刀2、严格控制刃磨切削用量,避免烧伤3、根据加工材料正确选择切削液;经常清除切屑槽的切屑,用足够压力的切削液4、通过精磨或研磨达到要求7、孔位置精度超差产生原因:1、导向套磨损2、导向套底端距工件太远,导向套长度短,精度差3、主轴轴承松动解决方法;1、定期更换导向套2、加长导向套,提高导向套与铰刀间的配合精度3、及时维修机床,调整主轴轴承间隙8、铰刀刀齿崩刃产生原因:1、铰孔余量过大2、工件材料硬度过高3、切削刃摆差过大,切削负荷不均匀4、铰刀主偏角太小,使切削宽度增大5、铰深孔或盲孔时,切削太多,又未及时清除6、刃磨刀齿已磨裂解决方法:1、修改预加工孔的孔径尺寸2、降低材料硬度,或改用负前角铰刀或硬质合金铰刀3、控制摆差在合格围4、加大主偏角5、注意及时清除切屑或采用带刃倾角铰刀6、注意刃磨质量9、铰刀柄部折断产生原因:1、铰孔余量过大2、铰锥孔时,粗、精铰削余量分配及切削用量选择不合适3、铰刀刀齿容屑空间小,切削堵塞解决方法:1、修改预加工的孔径尺寸2、修改余量分配,合理选择切削用量3、减少铰刀齿数,加大容屑空间;或将刀齿间隔磨去一齿10、铰孔后孔的中心线不直产生原因:1、铰孔前的钻孔不直,特别是孔径较小时,由于铰刀刚性较差,不能纠正原有的弯曲度2、铰刀主偏角过大,导向不良,使铰刀在铰削中容易偏差方向3、切削部分倒锥过大4、铰刀在断续孔中部间隙处位移5、手铰孔时,在一个方向上用力过大,迫使铰刀向一边偏斜,破坏了铰孔的垂直度解决方法:1、增加扩孔或镗孔工序校正孔2、减小主偏角3、调换合适的铰刀4、调换有导向部分或加长切削部分的铰刀5、注意正确操作。