物料平衡管理规程
GMP体系文件物料平衡管理规程

目的:建立一个物料平衡的工作标准,掌握生产过程中物料平衡,进行严格的收率控制,防止发生差错和出现混药现象。
范围:产品生产过程中的各个关键工序
责任人:岗位操作人员、车间管理人员、质量保证部、生产制造部。
内容:
1、在每个关键工序计算收率,进行物料平衡是避免或及时发现差错与混药的有效方法之一,因此,每个品种关键生产工序的批生产记录(批包装记录)都必须明确规定物料平衡的计算方法,以及根据验证结果确定收率范围。
2、物料平衡计算的基本要求
2.1 物料平衡计算公式:物料平衡=(产出量+尾料量)/(总投入量)× 100%
产出量:生产过程中实际产出量,不包括收集的废品量,生产中取得样品量(检品),丢弃的不合格物料。
尾料量:生产过程中产生的药头数量等。
总投入量:生产过程实际投入的数量。
2.2 在生产过程中如有跑料现象,应及时通知车间管理人员及质量保证部质量监督员,并详细记录跑料过程及数量。
跑料量也应计入物料平衡中,加在实际范围之内。
3、物料平衡计算单位
3.1 固体以重量计算。
3.2 液体以体积或重量计算。
4、数据处理
4.1 凡物料平衡在规定范围之内,经质监员审核,可以递交下道工序。
4.2 凡物料平衡高于或低于合格范围,应立即贴“待查”标志,不能递交下道工序,并填写偏差通知单,通知车间管理人员及质监员按“生产过程偏差处理管理规程”进行调查处理,并如实记录。
4.3 质量保证部会同生产制造部定期对各工序收率及产品的总体物料平衡进行
核算,并进行回顾性验证,为工艺改进、技术革新及技术文件的修订提供参考。
物料的平衡管理制度

物料的平衡管理制度一、引言物料管理是企业生产经营活动中非常重要的一环,对于企业来说,有效的物料管理不仅能够提高生产效率、降低成本,还能够确保生产和供应链的顺畅运作。
而物料的平衡管理制度则是物料管理的重要组成部分,旨在通过合理规划和有效控制物料的进出库流动,实现物料的合理利用和最大化价值。
本文将就物料的平衡管理制度进行详细阐述及分析。
二、物料的平衡管理制度概述1. 物料管理的背景和意义物料管理是一项系统性的管理活动,主要涉及物料的采购、入库、库存管理、生产和销售等环节。
在企业生产过程中,物料是生产活动的基础,因此如何有效管理物料,保证其在生产过程中的适时供应和合理利用,对于企业的生产效率和效益至关重要。
物料的平衡管理制度即是一种管理方法,通过对物料的需求、库存、采购及生产等方面进行综合考量和规划,以实现物料的合理配置和最佳利用。
2. 物料的平衡管理制度的定义和内容物料的平衡管理制度是指在物料管理活动中,通过科学、合理的方法对物料的需求、供应、库存和流动等方面进行规划和控制,以达到平衡进出库、合理利用、降低成本和提高效益的管理体系。
其内容主要包括:(1)物料需求的确定:根据生产计划和销售预测,确定物料的需求量和时间节点。
(2)物料采购管理:制定完善的物料采购标准和供应商评估制度,确保物料的质量、价格和供应及时性。
(3)库存管理:建立科学的库存模型,合理控制和优化库存水平,降低过多库存和缺货的风险。
(4)物料流动的控制:通过合理的物料流通路径和库存调度,降低物料的滞留和损耗,提高物料周转率。
(5)物料利用的优化:通过精细化管理和技术创新,提高物料利用率和降低废品率。
(6)风险管理:建立健全的应急预案和风险评估机制,及时应对因物料管理不当而导致的风险和损失。
三、物料的平衡管理制度的设计与实施1. 设计物料平衡管理制度的步骤(1)明确目标和原则:根据企业的发展战略和物料管理的具体需求,明确物料平衡管理制度的目标和原则。
物料平衡的标准管理规程

物料平衡的标准管理规程一、目的:建立物料平衡的标准管理规程,防止发生差错。
二、适用范围:适用于每批产品生产过程中物料平衡的管理。
三、责任者:生产技术部负责人、操作工人、质量监督员。
四、正文:1 在关键工序计算收率,进行物料平衡是避免或及时发现差错的有效方法。
2 收率计算的基本方法:2.1 收率计算收率=实际值/理论值×100%其中:理论值:为按照所用的原料(包装材料)量,在生产中无任何损失或差错的情况下得出的最大数量;实际值:为生产过程中实际产出量包括本工序正品产出量。
2.2 在生产过程中如有跑料、散装后跌落在地上的物料,应及时通知组长及品管监督员,详细记录损失数量及事故过程,其损失数加在实际值之内进行计算。
2.3上工序移交下来的有效物料并经复核的数量,为下工序计算收率的理论值。
2.4各工序物料平衡计算具体方法:2.4.1 过筛打粉预处理:检查与复核原物料品名、数量、以及其质量情况。
每一个物料,打粉过筛后称重量,并将上述每一种物料经打粉后的损耗率记录在工艺原始记录上。
计算:物料损耗率=(打粉过筛前总重-打粉过筛后总重)/打粉过筛前总重×100%2.4.2制颗粒:检查与复核领入原物料的品名、批号、数量以及质量情况,如发现有异常情况,及时报告品管监督员同意后退回中间站。
颗粒制好后,称重量、抽样测含量,必要时可增加测水分。
2.4.2.1 计算总收率:预处理后物料总重量及制粘合剂的固体料(不含配粘合剂所用的液体溶媒)之和为理论值,颗粒干燥后总重量及捕尘器中废料和收集的残料之和为实际值,颗粒总收率=实际干颗粒共重/(本批配料后的总共重量+外加辅料)×100%颗粒损耗率=(制料前总重-实际干颗粒共重)/制粒前总重×100%2.4.2.2 损耗率太大或有问题时,必须查明原因,如检查工序内地面上积粉等可收集部分称重后,再复核计算是否相符,要求将损耗率降低。
如果损耗率是负值,很可能颗粒中水分太高。
005-物料平衡管理规定 GMP工艺规程及标准操作程序的制订与审核规定
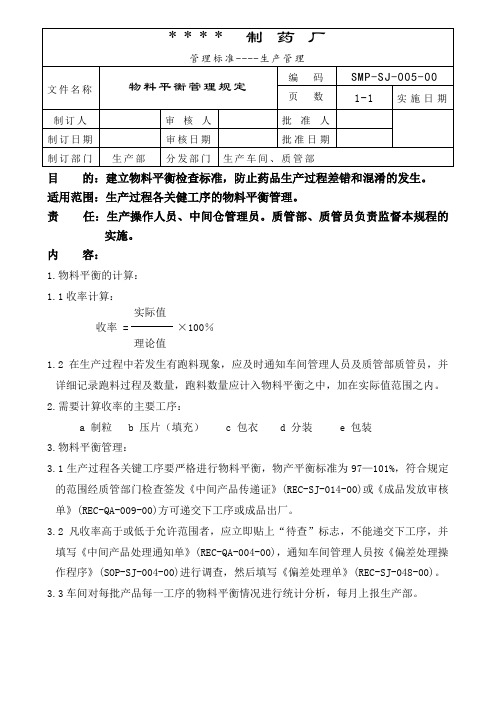
目的:建立物料平衡检查标准,防止药品生产过程差错和混淆的发生。
适用范围:生产过程各关健工序的物料平衡管理。
责任:生产操作人员、中间仓管理员。
质管部、质管员负责监督本规程的实施。
内容:
1.物料平衡的计算:
1.1收率计算:
实际值
收率 = ×100%
理论值
1.2在生产过程中若发生有跑料现象,应及时通知车间管理人员及质管部质管员,并详细记录跑料过程及数量,跑料数量应计入物料平衡之中,加在实际值范围之内。
2.需要计算收率的主要工序:
a 制粒
b 压片(填充)
c 包衣
d 分装
e 包装
3.物料平衡管理:
3.1生产过程各关键工序要严格进行物料平衡,物产平衡标准为97—101%,符合规定的范围经质管部门检查签发《中间产品传递证》(REC-SJ-014-00)或《成品发放审核单》(REC-QA-009-00)方可递交下工序或成品出厂。
3.2凡收率高于或低于允许范围者,应立即贴上“待查”标志,不能递交下工序,并填写《中间产品处理通知单》(REC-QA-004-00),通知车间管理人员按《偏差处理操作程序》(SOP-SJ-004-00)进行调查,然后填写《偏差处理单》(REC-SJ-048-00)。
3.3车间对每批产品每一工序的物料平衡情况进行统计分析,每月上报生产部。
GMP物料平衡管理规程
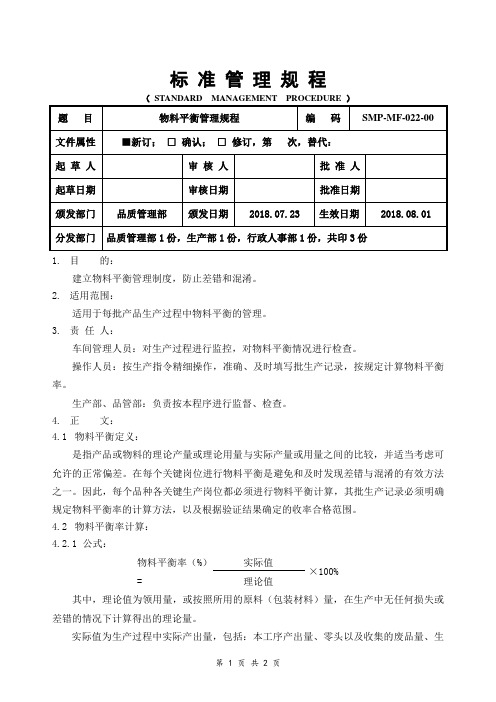
标准管理规程(STANDARD MANAGEMENT PROCEDURE )1.目的:建立物料平衡管理制度,防止差错和混淆。
2.适用范围:适用于每批产品生产过程中物料平衡的管理。
3.责任人:车间管理人员:对生产过程进行监控,对物料平衡情况进行检查。
操作人员:按生产指令精细操作,准确、及时填写批生产记录,按规定计算物料平衡率。
生产部、品管部:负责按本程序进行监督、检查。
4.正文:4.1物料平衡定义:是指产品或物料的理论产量或理论用量与实际产量或用量之间的比较,并适当考虑可允许的正常偏差。
在每个关键岗位进行物料平衡是避免和及时发现差错与混淆的有效方法之一。
因此,每个品种各关键生产岗位都必须进行物料平衡计算,其批生产记录必须明确规定物料平衡率的计算方法,以及根据验证结果确定的收率合格范围。
4.2物料平衡率计算:4.2.1公式:物料平衡率(%)= 实际值×100% 理论值其中,理论值为领用量,或按照所用的原料(包装材料)量,在生产中无任何损失或差错的情况下计算得出的理论量。
实际值为生产过程中实际产出量,包括:本工序产出量、零头以及收集的废品量、生产中取样量(检品)、不合格品量等。
无法收集的不合格物料(如捕尘系统、真空系统、管道系统中的残余物等)除外。
1.1.1在生产过程中如有跑料、散袋后跌落在地上的物料,应及时通知车间主任及QA,并详细记录损失数量和过程。
其损失数量加在实际值的范围之内计算。
4.2.2上工序移交下来的有效物料并经复核的数量,为下工序计算的理论值。
4.2.3需进行物料平衡率计算的主要岗位:称量、配料、压片、包衣、铝塑、包装。
4.2.4物料平衡计算单位:4.2.5制剂成品:以万瓶、万罐、万片/万粒计算。
4.2.6固体用铝箔、PVC以重量(kg)计算,其他内包材和外包装材料以张、只计算。
4.3制定物料平衡限度方法:采用根据设备、设施情况估计一定范围,再积累一定数量批次产品的物料平衡率数据,对数据进行统计计算而得出平衡限度。
4-物料平衡管理规程

目的:建立物料平衡管理规程,掌握生产过程中物料收率变化,进行严格的收率控制,防止差错和混药。
范围:适用于每个批次产品生产过程的关键工序的物料平衡。
职责:车间管理人员、操作工、质量管理部QA检查员对本规程的实施负责。
依据:《药品生产和质量管理规范》(1998年修订)
规程:
1物料平衡是指产品或物料的理论产量或理论用量与实际产量或用量之间的比较,并适当考虑可允许的正常偏差。
2每个品种各关键生产工序的批生产记录(批包装记录)都必须明确规定物料平衡的计算方法,包含根据检验结果确定的正常偏差。
3实际产量或用量应包括:工序中间产品、取样量、不合格品、回收品之和。
4物料平衡超出规程限度,应查明原因,在得出合理解释、确认无潜在质量事故后,方可按正常产品处理。
第 1 页共1 页。
GMP物料平衡管理规程

页码:文件编号:生效日期: 再版日期:第1页/共2页SMP-PM-01003-1标准管理规程STANDARD MANAGEMENT PROCEDURESubject题目:物料平衡管理规程Issued by颁发部门:质量部Written by起草人:Date日期:Dept. Head Approval 部门主管审核:Date日期:QA Director Approval QA 主管审核:Date日期:Approved by批准:Date日期:Dispense分发:总经理、质量部、生产部、商务部、行政人事部1.目的建立物料平衡的管理规程,严格物料管理,防止物料流失,控制成品率;防止差错和混药事故的发生。
2.适用范围适用于每批产品生产过程中物料平衡的管理。
3.责任者生产部、各生产车间、商务部、质量部相关人员。
4.内容4.1.在每个关键工序计算收率、进行物料平衡,是避免和及时发现差错与混料的有效方法之一。
因此,每个品种各关键生产工序的批生产记录(批包装记录)都必须明确规定收率的计算方法,以及根据验证结果确定的收率合格范围。
4.2.收率计算的基本要求:4.2.1.收率计算:实际值收率=─────────×100%理论值其中:理论值:按照所用的原料(包装材料)量,在生产中无任何损失或差错的情况下得出的最大数量。
实际值:生产过程中实际产出量,包括:本工序产出量、生产中取得样品量(检品)4.2.2.在生产过程中如有跑料现象和可见损耗,应及时通知车间管理人员及QA部门QA检查员,并详细记录跑料可见损耗过程及数量。
跑料和可见损耗数量也应计入物料平衡之中,加在实际值的范围之内。
页码:文件编号:生效日期: 再版日期:第2页/共2页SMP-PM-01003-1标准管理规程STANDARD MANAGEMENT PROCEDURESubject题目:物料平衡管理规程Issued by颁发部门:质量部4.2.3.如若实际收率在规定的收率范围内,即视为物料平衡合格,一般收率应在97%-101%之间。
物料平衡管理规程

目 的:建立物料平衡的工作标准,控制物料的误用或非正常流失,避免差错和混淆。
范 围:每个批次产品生产过程的关键工序。
责 任 人:操作员、车间主管、生产部部长、QA 员。
内 容:1在每个关键工序进行物料平衡是避免或及时发现差错与混淆的有效方法之一。
因此,每个品种各关键生产工序的批生产记录、批包装记录都必须明确规定物料平衡的计算方法,依据各品种工艺规程达到规定的限度范围。
1.1产品(或物料)的理论产量(或理论用量)与实际产量(或用量)之间的比值应有可允许的正常偏差。
1.2 每批产品应在生产完成后,立刻做物料平衡检查。
2物料平衡检查的基本要求2.1计算公式物料平衡 = ×100%其中:理论值:为按照所用的原料(包装材料)量,在生产中无任何损失或差错的情况下得出的最大数量。
实际值:为生产过程中实际产出量,包括:本工序合格产品;不合格产品;生产中抽检样品量(检品);收集的废弃物料(如捕尘系统,地面,设备表面收集物)。
2.2 在生产过程中如有跑料现象,应及时通知车间主管及QA 员,按《生产过程偏差处理管理规程》处理,并详细记录跑料过程及数量。
跑料也应计入物料平衡之中,加在实际值的范围之内。
3各关键工序进行物料平衡或收率的计算方法3.1 提取浓缩浓缩液量实际值理论值临夏龙康制药厂物料平衡管理规程编号SC-G-009版次:01第 2 页共 2 页出膏率=——————————×100%投料量3.2内包装3.2.1按生产指令领出的中间产品量为理论值;灌装合格产品数量、挑出的不合格产品数量、取样数量加上收集未灌装残留数量之和,为实际值。
3.3外包装3.3.1标签、说明书、中盒:领用数量为理论值,使用数量加上挑出的残损数量、剩余数量之和为实际值,物料平衡100%为合格。
4数据处理4.1物料平衡在合格范围之内的,经QA员签字,可以递交下工序或办理入库。
4.2物料平衡超出合格范围的,必须严格按《生产过程偏差处理管理规程》进行调查,采取处理措施,并详细记录。
物料平衡与收率管理规程
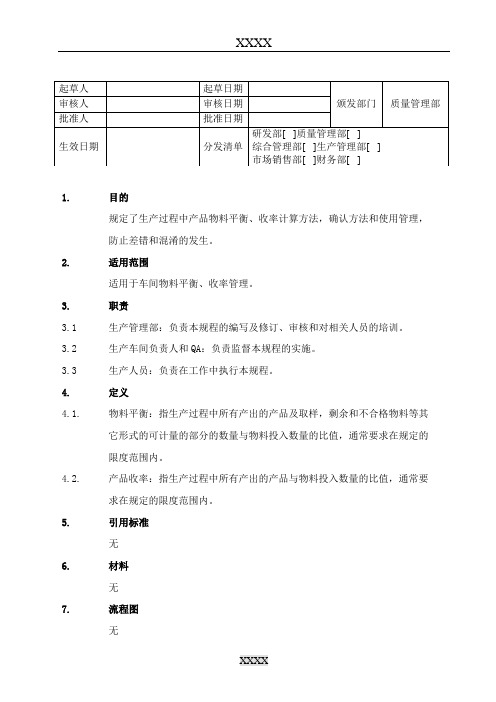
1.目的规定了生产过程中产品物料平衡、收率计算方法,确认方法和使用管理,防止差错和混淆的发生。
2.适用范围适用于车间物料平衡、收率管理。
3.职责3.1 生产管理部:负责本规程的编写及修订、审核和对相关人员的培训。
3.2 生产车间负责人和QA:负责监督本规程的实施。
3.3 生产人员:负责在工作中执行本规程。
4.定义4.1.物料平衡:指生产过程中所有产出的产品及取样,剩余和不合格物料等其它形式的可计量的部分的数量与物料投入数量的比值,通常要求在规定的限度范围内。
4.2.产品收率:指生产过程中所有产出的产品与物料投入数量的比值,通常要求在规定的限度范围内。
5.引用标准无6.材料无7.流程图无8.内容8.1.物料平衡管理8.1.1.物料平衡的计算方法是:本工序产品+取样品+不合格品+剩余物料物料平衡 = ——————————————————×100%本工序投料量8.1.2.物料平衡限度的确定方法8.1.2.1.产品在一批生产结束,统计各工序的物料平衡值,三批确认批生产数据作为临时的物料平衡限度。
8.1.2.2.生产管理部应对同一产品同一岗位上20个正常批次生产的数据进行统计,确定该产品在该工序的物料平衡接受限度。
8.1.2.3.使用20个正常批产品进行统计的方法,可以用于为一个新产品确定物料平衡接受限度,也可以用于对已有的产品物料平衡限度进行检查和修改。
8.1.3.物料平衡限度的确定程序8.1.3.1.生产经理、QA负责共同确定各个产品在各生产工序的物料平衡接受限度。
8.1.3.2.当需要采取对20个正常批产品用统计的方法来确定某一物料接受限度时,生产管理部负责数据的收集和计算,然后由生产经理和QA审核确定。
8.1.3.3.产品在各个生产工序的物料平衡限度,应印在该工序的批记录上。
8.1.4.物料平衡限度的使用当某一生产工序的工作结束后,生产操作人员要按照批记录中的要求,计算物料平衡,并填写在批记录中。
XX公司物料平衡管理规程

XX公司物料平衡管理规程第一章:总则1.1 目的本规程旨在确保XX公司在物料管理方面的高效性和准确性,通过合理调控和监控物料流动,实现物料平衡,提高资源利用效率,降低成本,保障生产运营的顺利进行。
1.2 适用范围本规程适用于XX公司所有部门和岗位,包括采购、生产、仓储、物流等相关人员。
第二章:物料平衡管理流程2.1 数据收集与监控2.1.1 各部门物料流量数据的统计与汇总通过定期收集和统计各部门的物料流量数据,包括原材料采购量、生产过程中的物料损耗、成品出库等数据,并进行汇总。
确保物料流量数据的准确性和实时性。
2.1.2 数据监控与异常预警建立物料流量数据监控系统,定期对物料流量进行分析和监控。
一旦发现物料流量异常,及时预警,并采取相应的措施进行调整,保持物料平衡。
2.2 调控与优化2.2.1 采购计划的制定根据生产需求和市场预测,制定合理的采购计划,确保原材料的及时供应和充足库存,避免生产线因缺料而停产停工的情况发生。
2.2.2 生产过程中的物料控制对每个生产环节的物料使用量进行监控和记录,确保物料的准确投入和控制,避免过量消耗和损耗。
同时,优化生产工艺,降低物料损耗率,提高生产效率。
2.2.3 仓储管理与库存控制通过合理布局和规范的仓储管理,优化物料存储方式,减少物料存储空间占用和损耗,确保库存的准确性和及时性。
同时,定期进行库存盘点和清理,及时处理过期或损坏的物料,避免废品积压。
2.3 监督与审计2.3.1 内部监督制度的建立建立内部监督制度,明确各部门职责和权限,确保各个环节的物料流动监督到位,规范操作。
定期开展内部审计,发现问题并提出改进意见。
2.3.2 外部监督与评估定期邀请第三方进行物料平衡管理方面的评估,对公司物料平衡管理情况进行全面审查,发现问题并提出改进措施。
第三章:责任与义务3.1 部门责任各部门应根据本规程的要求,做好物料流量数据的记录和统计工作,及时上报相关数据,并配合其他部门的调控工作,确保物料平衡和生产运行的正常进行。
物料平衡管理规程

物料平衡管理规程一、目的:建立物料平衡管理标准工作规程,掌握生产过程中物料平衡在控制范围之内,防止差错和混药。
二、范围:每个批次产品生产过程的关键工序都要进行物料平衡计算。
三、责任者:车间主任、工艺员、操作工、QA。
四、内容:1在生产关键工序需要计算物料平衡情况,避免差错,混药事故的发生,生产工序批生产记录要明确规定物料平衡的计算方法,以及根据验证结果确定物料平衡合格范围。
2物料平衡计算:物料平衡=实际值/理论值×100%其中:理论值:为按照所用的原料量,在生产中无任何损失或差错的情况下得出的最大数量。
实际值:为生产过程中实际产出量。
包括:产出的合格品量;生产中抽取的检品量和留样量。
3物料平衡检查:生产必须按照处方量的100%投料,制定物料平衡率时适当考虑允许的正常偏差,正常偏差是根据同品种的行业水平和本厂历史水平、技术条件进行制定。
下列项目需进行物料平衡计算:3.1各种原料;3.2各种包装材料、标签、说明书等;3.3制剂生产中关键工序中间体、成品。
3.4原料药生产中所用溶剂3.5 原料药生产中关键工序中间体、成品,成品需根据化学反应计算总收率。
4生产过程中物料平衡偏差处理:4.1偏差发现人在采取措施仍不能将偏差控制在规定范围内时,立即停止生产并报告车间主任;4.2发现偏差时,车间管理人员进行调查,根据调查结果提出处理措施,使偏差控制在规定的范围内;4.3车间管理人员进行调查,根据调查结果提出处理措施:4.3.1确认不影响产品最终质量的情况下可继续加工;4.3.2确认不影响产品质量的情况下进行返工,或采取补救措施;4.3.3确认影响产品质量,则报废或销毁。
5 物料平衡计算的关键工序5.1原料药车间5.1.1化学合成部分酰化反应:溶剂回收率,产品收率,;5.1.2还原反应:溶剂回收率,产品收率;5.1.3脱水反应:溶剂回收率,产品收率;5.1.4溶解脱色:湿品收率,溶剂回收率,干产品收率;5.1.5化学合成主原料总收率5.1.6 标签,说明书,印刷包装材料计算领用数与使用数,剩余数,销毁数之和相符。
18物料平衡管理规程

物料平衡管理规程一、目的:规范物料平衡的管理,掌握生产过程中物料收率变化,进行严格的收率控制,防止差错和混药。
二、范围:每个批次产品生产过程的关键工序都要进行物料平衡。
三、责任人:质量部长、生产部长、车间主任、质量管理员。
四、内容:1.在每个关键工序进行物料平衡是避免或及时发现差错与混淆的有效方法之一。
因此,每个品种各关键生产工序的批生产记录(批包装记录)都必须明确规定物料平衡的计算方法,以及根据验证结果确定各工序物料平衡的合格范围。
2.物料平衡计算的基本要求物料平衡:产品或物料实际产量或实际用量及收集到的损耗之和与理论产量或理论用量之间的比较,并考虑可允许的偏差范围。
2.1计算 物料平衡=理论产量或理论用量损耗量实际产量或实际用量 ×100% 2.2在生产过程中如有跑料现象,应及时通知车间管理人员及质量管理员,并详细记录跑料过程及数量。
跑料数量也应计入物料平衡之中,加在实际值的范围之内。
2.3确定需进行物料平衡计算的主要工序:口服液体车间:配制(料液)、灌封(料液、内包材)、包装(产品瓶数、包装材料)。
口服固体车间:制粒总混、压片、内包、外包。
2.4物料平衡计算单位。
灌装前以体积计算。
灌装后用“瓶”计算。
瓶= 平均装量分装药液体积2.5数据处理2.5.1凡物料平衡在合格范围之内,经车间质量管理员检查后,才可以递交下工序。
2.5.2凡物料平衡高于或低于合格范围,应立即停止生产,不能递交下工序,并填写偏差通知单,通知车间管理人员及质量管理员按《偏差处理管理规程》进行调查,采取处理措施,并详细记录。
2.5.3质量部应定期对各工序物料平衡及产品的总体物料平衡进行回顾性验证,为工艺改进,技术创新及技术标准文件的修订提供参考。
3.物料平衡的审核3.1需进行物料平衡审核的物料、工序配制、灌封中间产品、包装品在加工处理包装后。
生产所用的外包装材料在包装完毕后。
成品入库前。
其它平衡审核。
3.2每批产品在生产作业完成后,操作人员应根据物料的领用量、结存量、污损量等实际数量(计量必须准确)进行平衡计算,经车间质量管理员复核无误、确认平衡在规定限度内、签字认可后,方可将产品移交下工序或入库,如平衡超出限度的合格范围,应按《偏差处理管理规程》进行处理。
物料平衡审核及管理规程

文件制修订记录1.0目的建立物料平衡的审核及管理规程,掌握生产过程中物料平衡及收率变化,进行严格的物料平衡及收率控制,防止差错和混药。
2.0范围关键岗位的物料平衡计算及审核3.0责任技术开发部部长、车间主任、质量管理部监控员、技术员、班长、操作工4.0管理内容4.1 在每个关键岗位计算收率、进行物料平衡计算是避免或及时发现差错与混药的有效方法之一。
因此,每个品种各关键生产岗位的批生产记录都必须明确规定收率和物料平衡计算方法,以及根据验证结果确定的合格范围限度。
4.2收率及物料平衡计算的基本要求:4.2.1 收率计算:实际值收率= ×100%理论值其中:理论值:按照所用的原料(包装材料)量,在生产中无任何损失或差错的情况下得出的最大数量。
实际值:生产过程中实际产出量。
收率是进行成本核算的重要基础数据。
4.2.2 物料平衡计算:产成品+不合格品+取样量物料平衡率= ×100%理论产品数物料平衡是指生产过程中所有产出可见产品(或中间产品)及其它形式产出与初始物料投入数量的比值。
4.2.3 在生产过程中如有跑料现象,应及时通知车间技术员及质量管理部监控员,并详细记录跑料过程及数量。
4.3 各岗位收率及物料衡算4.3.1 提取工艺各岗位收率及物料衡算4.3.1.1 中药材前处理收率及物料平衡4.3.1.1.1 收率净药材重量中药材前处理收率= ×100%投料总重量4.3.1.2 净药材粉碎岗位:4.3.1.2.1 收率粉碎后药粉重量粉碎收率= ×100%净药材投料量4.3.1.2.2 物料衡算粉碎后药粉重量+废弃量物料平衡率= ×100%净药材投料量4.3.1.3 净药材提取、浓缩岗位:4.3.1.3.1 收率清膏重量收率= ×100%净药材投料量4.3.1.4 膏粉混合岗位:4.3.1.4.1 收率混合后膏粉重量混合收率= ×100%膏粉总投料量4.3.1.4.2 物料衡算混合后膏粉重量+废弃量物料平衡率= ×100%膏粉总投料量4.3.1.5 膏粉干燥岗位:4.3.1.5.1 收率干燥后干粉重量干燥收率= ×100%膏粉总投料量4.3.1.5.2 物料衡算干燥后干粉重量+废弃量物料平衡率= ×100%膏粉总投料量4.3.1.6 粉碎岗位:4.3.1.6.1 收率粉碎后药粉重量粉碎收率= ×100%领入药粉重量4.3.1.6.2 物料衡算粉碎后药粉重量+废弃量物料平衡率= ×100%领入药粉重量4.3.2 制剂各岗位收率及物料衡算4.3.2.1 制粒、干燥岗位:4.3.2.1.1 收率干颗粒重量干颗粒收率= ×100%投料重量4.3.2.1.2 物料衡算干颗粒重量+废弃量物料平衡率= ×100%投料重量4.3.2.2 整粒岗位:4.3.2.2.1 收率整粒后颗粒重量整粒收率= ×100%干燥后颗粒重量4.3.2.2.2 物料衡算整粒后颗粒重量+废弃量物料平衡率= ×100%干燥后颗粒重量4.3.2.3 批混岗位:4.3.2.3.1 收率批混后重量收率= ×100%领入重量4.3.2.3.2 物料衡算批混后重量+废弃量+取样量物料平衡率= ×100%领入重量4.3.2.4 压片4.3.2.4.1 收率压片后合格素片重量压片收率= ×100%领入颗粒重量4.3.2.4.2 物料衡算压片后合格素片重量+取样量+废弃量物料平衡率= ×100%领入颗粒总重量4.3.2.5 包衣岗位:4.3.2.5.1 收率糖衣片总重量×片芯系数包衣收率= ×100%领入片芯总重量4.3.2.5.2 物料衡算糖衣片总重量×片芯系数+废弃量物料平衡率= ×100%领入片芯总重量片芯平均重量片芯系数= ×100%糖衣片平均重量4.3.2.6 胶囊充填岗位:4.3.2.6.1 收率充填后胶囊总重量(1—空心胶囊系数)+尾料量胶囊充填收率= ×100%领入药粉重量4.3.2.6.2 物料衡算充填后胶囊总重量(1—空心胶囊系数)+废弃量+尾料量物料平衡率= ×100%领入药粉重量空胶囊平均重量空心胶囊系数= ×100%充填后胶囊平均重量4.3.2.7 灌封岗位:4.3.2.7.1 收率合格品数量灌封收率= ×100%理论灌封数量4.3.2.7.2 物料衡算合格品数量+不合格品数量+取样量物料平衡率= ×100%理论灌封数量配制量理论灌封数量=理论装量4.3.2.8 灯检岗位4.3.2.8.1 收率合格品数量灯检收率= ×100%领入数量4.3.2.8.2 物料衡算合格品数量+废弃量物料平衡率= ×100%领入数量4.3.2.9 铝塑包装4.3.2.9.1 收率热合后总重量(1—空铝塑板系数)铝塑包装收率= ×100%充填后胶囊重量或糖衣片重量4.3.2.9.2 物料衡算热合后总重量(1—空铝塑板系数)+废弃量物料平衡率= ×100%充填后胶囊重量或糖衣片重量空铝塑板平均重量空铝塑板系数= ×100%成品板平均重量4.3.2.10 成品包装4.3.2.10.1 收率包装产出量成品包装收率= ×100%成品包装理论产量投料量成品包装理论产量=规格4.3.2.10.2 物料衡算产出量+取样量+不合格品数量物料平衡率= ×100%成品包装理论产量4.3.2.11 标签物料衡算使用数+废品数+剩余数物料平衡率= ×100%领用数注:废品数包括已打印批号且未使用的数量。
生产过程物料平衡管理规程

目的:本程序依据《药品生产质量管理规范》(2010修订版)规定了生产过程物料平衡的管理。
范围:本程序适用于每个批次产品生产过程的关键工序。
职责:质量管理部、生产部内容:1计算平衡收率的主要工序:粉碎、混合、包装。
2车间主任或工艺员按工艺规程中物料平衡的计算规定对关键工序中间产品物料平衡收率进行计算。
3平衡收率的计算方法必须按工艺规程规定的计算方法计算,并核对是否符合规定范围,如确认符合规定,则签字转下道工序;如出现偏差,则按8项下规定进行。
4在生产过程中如有跑料现象,应及时通知车间负责人,并详细记录跑料过程及数量,跑料数量应计入物料平衡收率的计算中。
5偏差处理5.1凡收率高于或低于规定范围,应在状态标识中注明“待查”,不能递交下工序。
5.2由工艺员或工序班组长填写偏差处理单,写明品名、批次或批号、•规格、数量、工序偏差内容、发生的过程及原因、填表人签字、注明日期,将偏差处理单交分厂负责人,并报生产部和质量管理部。
5.3车间主任会同生产部和质量管理部进行调查,根据调查结果提出处理意见和措施。
a) 确认不影响产品最终质量的情况下继续加工。
b) 确认不影响产品质量的情况下进行返工,或采取补救措施。
c) 确认不影响产品质量的情况下,采取再回收、再利用措施。
d) 确认影响产品质量,按不合格产品处理程序进行处理。
5.4车间主任将调查结果及需采取的措施,写出书面报告附偏差处理单之后,上报质量管理部,经质量管理部经理审核,签字批准后送车间。
5.6车间生产工序按批准的措施组织实施,并做好详细记录。
5.7偏差处理单附批生产记录。
6若调查发现有可能与本批次前后生产批次的产品相关联,必须立即采取措施停止相关批次的放行,直至确认与之无关方可放行。
如有放行市场产品,必要时按产品收回管理程序处理。
物料平衡管理规程

XXXXXXXXX有限公司一、目的:为防止混淆和差错制定本规程。
二、范围:本规定适用于在公司生产产品。
三、责任:操作人员、技术人员、QA人员、车间管理人员。
四、内容:1.物料平衡:产品或物料的理论产量或理论用量与实际产量或用量之间的比较,并适当考虑允许正常的偏差,正常偏差值是根据同品种的行业水平和本厂历史水平、技术条件制订的。
2.物料平衡是及时发现或避免差错与混药的有效方法之一。
因此,每个品种各关键生产工序的批生产记录都必须明确规定物料平衡率的计算方法,以及根据验证结果确定的物料平衡率合格范围。
3.物料平衡与收率的区别3.1物料平衡的计算是为了防止物料误用或非正常流失。
3.2收率是合格品与投入的比值。
4.物料平衡率计算4.1物料平衡率=实际值/理论值×100%4.2理论值:按照所用的原料、辅料、包装材料量,在生产中无任何损失或差错下得到的最大数量的值。
4.3实际值:生产过程中实际产出量,包括:本工序产出量、收集的残品量、取样量(检品)、丢弃的不合格物料。
5.生产过程中如有跑料现象应及时通知工序负责人、QA检查员或车间主任,并详细记录跑料原因及数量。
跑料数量应记入物料平衡之中,加在实际值的范围之内。
6.上工序移交下来的有效物料并经复核的数量,为下工序计算物料平衡率的理论值,而下道工序所产出的数量为实际值。
7.进行物料平衡率计算的工序应包含但不限于下列工序::7.1片剂:制粒工序,总混工序,压片工序、包衣工序、内包装工序,外包装工序。
7.2胶囊剂:制粒工序,总混工序,胶囊充填工序,内包装工序,外包装工序。
7.3颗粒剂:制粒工序,总混工序,内包装工序,外包装工序。
7.4丸剂:总混工序,制丸工序,包衣工序,内包装工序,外包装工序。
7.5口服液体制剂:灌装工序、灯检工序、内包装工序、外包装工序。
7.6散剂:总混工序,散剂分装工序,外包装工序。
7.7酊、酒剂:灌封工序,外包装工序。
7.8软膏剂:灌封工序,外包装工序。
- 1、下载文档前请自行甄别文档内容的完整性,平台不提供额外的编辑、内容补充、找答案等附加服务。
- 2、"仅部分预览"的文档,不可在线预览部分如存在完整性等问题,可反馈申请退款(可完整预览的文档不适用该条件!)。
- 3、如文档侵犯您的权益,请联系客服反馈,我们会尽快为您处理(人工客服工作时间:9:00-18:30)。
物料平衡管理规程
目的:建立物料平衡的工作标准,控制物料的误用或非正常流失,避免差错和混淆。
范围:每个批次产品生产过程的关键工序。
责任人:操作员、车间工艺员、车间主任、生产部部长、QA员。
内容:
1产品(或物料)的理论产量(或理论用量)与实际产量(或实际用量)之间的比值应有可允许的正常偏差。
1.1在每个关键工序进行物料平衡是避免或及时发现差错与混淆的有效方法之一。
因此,每个品种各关键生产工序的批生产记录、批包装记录都必须明确规定物料平衡的计算方法,以及根据验证结果确定的物料平衡允许范围(控制指标详见各产品工艺规程)。
1.2 每批产品应在生产完成后,立刻做物料平衡检查。
2物料平衡检查的基本要求
2.1计算公式
实际值
×100%
理论值
其中:
理论值:为按照所用的原料(包装材料)量,在生产中无任何损失或差错的情况下得出的最大数量。
实际值:为生产过程中实际产出量,包括:本工序产出量;收集的废品量;生产中取样量(检品);
2.2 在生产过程中如有跑料现象,应及时通知车间主任及QA员,按《生产过程偏差处理管理规程》(编号SMP-SC-SG-011)处理,并详细记录跑料过程及数量。
跑料数量也应计入物料平衡之中,加在实际值的范围之内。
3各关键工序进行物料平衡的计算方法
3.1粉碎工序:
细粉总量
----------------------------------- ×100%
净药材重量(或干膏重量)
3.2制粒工序:
颗粒总量+本批尾料量-上批尾料量
--------------------------------------------------------×100%
投料量
3.3批混工序:
批混后细粉重量+取样量
------------------------------------------------------ ×100%
投料量
3.4压片工序:
素片量+本批尾料量
-----------------------------------------×100%
领用颗粒量
3.5包衣工序:
包衣片量+本批尾料量
---------------------------------------×100%
领用素片重量+辅料重量
3.6胶囊充填工序:
充填后胶囊重量×(1-0.17)+本批尾料量
----------------------------------------------------------------×100%
领用细粉总量
3.7颗粒分装工序:
分装后颗粒数量(袋)×规格(g)+本批尾料量
---------------------------------------------------------------------------×100%
颗粒总量
3.8内包装工序:
铝塑板数量(板)×每板粒数(片数)+未包装量(片)
-------------------------------------------------------------------------------×100%
领用素片重量×1000÷规格(g)
3.9外包装工序:
3.9.1片剂、胶囊剂:
成品量(粒)+取样量(粒)
------------------------------------------------------×100%
领用待包装品(铝塑板)数量×粒/板
3.9.2颗粒剂:
成品量(袋)+取样量(袋)
------------------------------------------×100%
领用待包装品(复合膜袋)数量
3.9.3按批包装指令领出的待包装品量为理论值;包装成品数量加上取样(包括检验、留样观察)数量,未完成包装数量,收集的半成品、成品残损数量,挑出的不合格成品数量为实际值,物料平衡100%为合格。
3.9.4标签、说明书:标签、说明书实际领用数量为理论值,说明书实际使用数量加上挑出的不合格数量、剩余数量为实际值,物料平衡100%为合格。
4计算结果评价及中间品、半成品、成品处理
4.1物料平衡在允许范围之内的,经QA员审核签字,可以递交下工序或办理入库。
4.2物料平衡超出允许范围的,必须严格按《生产过程偏差处理管理规程》(编号
SMP-SC-SG-008)进行调查,采取处理措施,并详细记录。
5备注
5.1成品量:已内包装(外包装)完毕的包装品(充填后胶囊、素片、包衣片、充填后颗粒)的数量。
5.2未包装量:尚未内包装(外包装)的合格半成品(充填后胶囊、素片、包衣片、充填后颗粒)的数量。
5.3上批尾料量:上一批该品种生产结束后剩余的质量合格的中间品、半成品总量。
5.5本批尾料量:该工序在本批品种生产结束后剩余的质量合格的中间品、半成品的数量。
5.6取样量:从该工序取走的用于检验的中间品、半成品、成品的数量。