汽车铝合金摆臂锻造工艺仿真分析
关于汽车碰撞吸能铝合金力学性能试验及仿真的分析
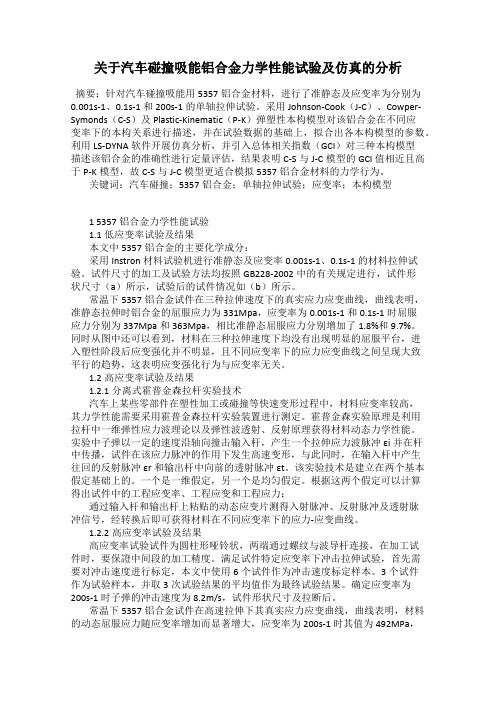
关于汽车碰撞吸能铝合金力学性能试验及仿真的分析摘要:针对汽车碰撞吸能用5357铝合金材料,进行了准静态及应变率为分别为0.001s-1、0.1s-1和200s-1的单轴拉伸试验。
采用Johnson-Cook(J-C)、Cowper-Symonds(C-S)及Plastic-Kinematic(P-K)弹塑性本构模型对该铝合金在不同应变率下的本构关系进行描述,并在试验数据的基础上,拟合出各本构模型的参数。
利用LS-DYNA软件开展仿真分析,并引入总体相关指数(GCI)对三种本构模型描述该铝合金的准确性进行定量评估,结果表明C-S与J-C模型的GCI值相近且高于P-K模型,故C-S与J-C模型更适合模拟5357铝合金材料的力学行为。
关键词:汽车碰撞;5357铝合金;单轴拉伸试验;应变率;本构模型1 5357铝合金力学性能试验1.1低应变率试验及结果本文中5357铝合金的主要化学成分:采用Instron材料试验机进行准静态及应变率0.001s-1、0.1s-1的材料拉伸试验。
试件尺寸的加工及试验方法均按照GB228-2002中的有关规定进行,试件形状尺寸(a)所示,试验后的试件情况如(b)所示。
常温下5357铝合金试件在三种拉伸速度下的真实应力应变曲线,曲线表明,准静态拉伸时铝合金的屈服应力为331Mpa,应变率为0.001s-1和0.1s-1时屈服应力分别为337Mpa和363Mpa,相比准静态屈服应力分别增加了1.8%和9.7%。
同时从图中还可以看到,材料在三种拉伸速度下均没有出现明显的屈服平台,进入塑性阶段后应变强化并不明显,且不同应变率下的应力应变曲线之间呈现大致平行的趋势,这表明应变强化行为与应变率无关。
1.2高应变率试验及结果1.2.1分离式霍普金森拉杆实验技术汽车上某些零部件在塑性加工或碰撞等快速变形过程中,材料应变率较高,其力学性能需要采用霍普金森拉杆实验装置进行测定。
霍普金森实验原理是利用拉杆中一维弹性应力波理论以及弹性波透射、反射原理获得材料动态力学性能。
《2024年7A04高强铝合金轮毂锻造成形工艺研究》范文
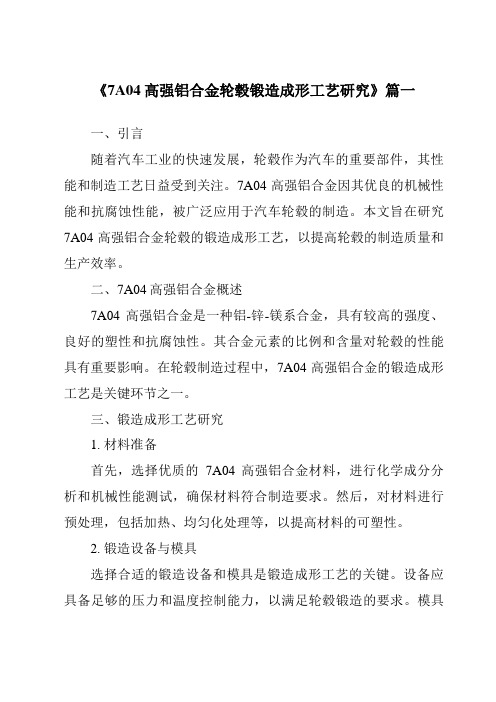
《7A04高强铝合金轮毂锻造成形工艺研究》篇一一、引言随着汽车工业的快速发展,轮毂作为汽车的重要部件,其性能和制造工艺日益受到关注。
7A04高强铝合金因其优良的机械性能和抗腐蚀性能,被广泛应用于汽车轮毂的制造。
本文旨在研究7A04高强铝合金轮毂的锻造成形工艺,以提高轮毂的制造质量和生产效率。
二、7A04高强铝合金概述7A04高强铝合金是一种铝-锌-镁系合金,具有较高的强度、良好的塑性和抗腐蚀性。
其合金元素的比例和含量对轮毂的性能具有重要影响。
在轮毂制造过程中,7A04高强铝合金的锻造成形工艺是关键环节之一。
三、锻造成形工艺研究1. 材料准备首先,选择优质的7A04高强铝合金材料,进行化学成分分析和机械性能测试,确保材料符合制造要求。
然后,对材料进行预处理,包括加热、均匀化处理等,以提高材料的可塑性。
2. 锻造设备与模具选择合适的锻造设备和模具是锻造成形工艺的关键。
设备应具备足够的压力和温度控制能力,以满足轮毂锻造的要求。
模具的设计和制造应考虑轮毂的形状、尺寸和精度要求,确保锻造过程中轮毂的形状和尺寸精度。
3. 锻造过程锻造过程包括加热、锻打、冷却等步骤。
首先,将7A04高强铝合金材料加热至适当的温度,以降低材料的塑性变形抗力。
然后,通过锻打的方式使材料发生塑性变形,形成所需的轮毂形状。
最后,进行冷却处理,使轮毂的内部组织得到充分稳定。
4. 工艺参数优化在锻造过程中,应优化工艺参数,包括加热温度、锻打速度、冷却方式等。
通过实验和仿真分析,确定最佳的工艺参数组合,以提高轮毂的制造质量和生产效率。
同时,要关注模具的使用和维护,以延长模具的使用寿命。
四、研究结果与分析通过对7A04高强铝合金轮毂锻造成形工艺的研究,我们得到了以下结果:1. 优化了材料准备过程,提高了材料的可塑性;2. 选择了合适的锻造设备和模具,提高了轮毂的形状和尺寸精度;3. 通过优化工艺参数,提高了轮毂的制造质量和生产效率;4. 分析了锻造过程中可能出现的缺陷和问题,提出了相应的解决措施。
铝合金铸件凝固过程的宏观及微观模拟仿真研究进展
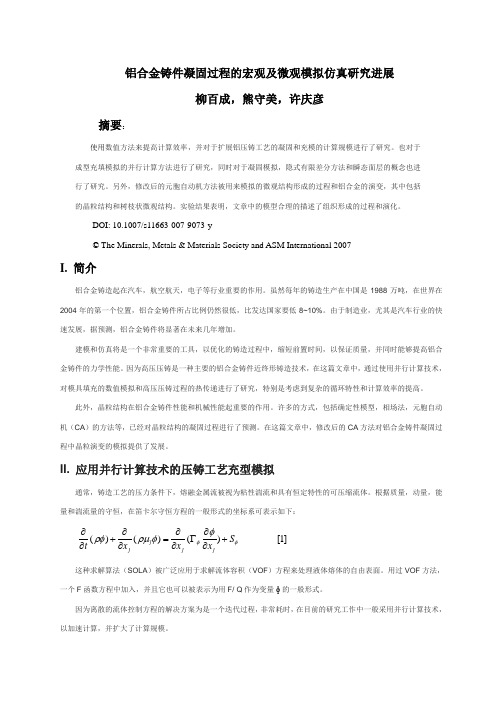
铝合金铸件凝固过程的宏观及微观模拟仿真研究进展柳百成,熊守美,许庆彦摘要:使用数值方法来提高计算效率,并对于扩展铝压铸工艺的凝固和充模的计算规模进行了研究。
也对于成型充填模拟的并行计算方法进行了研究,同时对于凝固模拟,隐式有限差分方法和瞬态面层的概念也进行了研究。
另外,修改后的元胞自动机方法被用来模拟的微观结构形成的过程和铝合金的演变,其中包括的晶粒结构和树枝状微观结构。
实验结果表明,文章中的模型合理的描述了组织形成的过程和演化。
DOI: 10.1007/s11663-007-9073-y© The Minerals, Metals & Materials Society and ASM International 2007I. 简介铝合金铸造起在汽车,航空航天,电子等行业重要的作用。
虽然每年的铸造生产在中国是1988万吨,在世界在2004年的第一个位置,铝合金铸件所占比例仍然很低,比发达国家要低8~10%。
由于制造业,尤其是汽车行业的快速发展,据预测,铝合金铸件将显著在未来几年增加。
建模和仿真将是一个非常重要的工具,以优化的铸造过程中,缩短前置时间,以保证质量,并同时能够提高铝合金铸件的力学性能。
因为高压压铸是一种主要的铝合金铸件近终形铸造技术,在这篇文章中,通过使用并行计算技术,对模具填充的数值模拟和高压压铸过程的热传递进行了研究,特别是考虑到复杂的循环特性和计算效率的提高。
此外,晶粒结构在铝合金铸件性能和机械性能起重要的作用。
许多的方式,包括确定性模型,相场法,元胞自动机(CA )的方法等,已经对晶粒结构的凝固过程进行了预测。
在这篇文章中,修改后的CA 方法对铝合金铸件凝固过程中晶粒演变的模拟提供了发展。
II. 应用并行计算技术的压铸工艺充型模拟通常,铸造工艺的压力条件下,熔融金属流被视为粘性湍流和具有恒定特性的可压缩流体。
根据质量,动量,能量和湍流量的守恒,在笛卡尔守恒方程的一般形式的坐标系可表示如下:()()()[1]j j j jS t x x x φφφρφρμφ∂∂∂∂+=Γ+∂∂∂∂这种求解算法(SOLA )被广泛应用于求解流体容积(VOF )方程来处理液体熔体的自由表面。
汽车悬架6082铝合金控制臂成形工艺
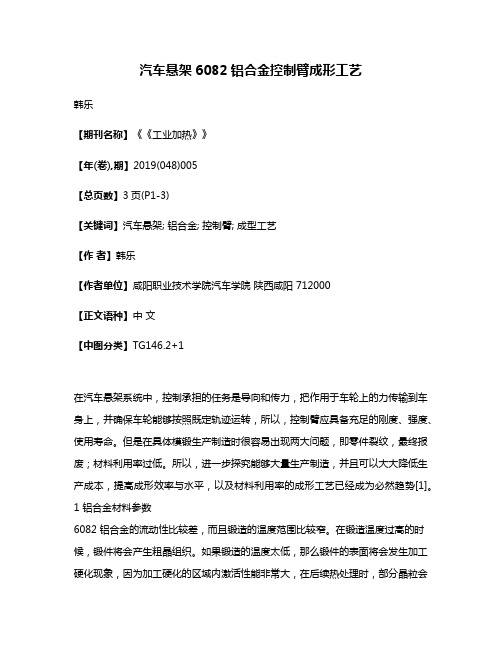
汽车悬架6082铝合金控制臂成形工艺韩乐【期刊名称】《《工业加热》》【年(卷),期】2019(048)005【总页数】3页(P1-3)【关键词】汽车悬架; 铝合金; 控制臂; 成型工艺【作者】韩乐【作者单位】咸阳职业技术学院汽车学院陕西咸阳 712000【正文语种】中文【中图分类】TG146.2+1在汽车悬架系统中,控制承担的任务是导向和传力,把作用于车轮上的力传输到车身上,并确保车轮能够按照既定轨迹运转,所以,控制臂应具备充足的刚度、强度、使用寿命。
但是在具体模锻生产制造时很容易出现两大问题,即零件裂纹,最终报废;材料利用率过低。
所以,进一步探究能够大量生产制造,并且可以大大降低生产成本,提高成形效率与水平,以及材料利用率的成形工艺已经成为必然趋势[1]。
1 铝合金材料参数6082 铝合金的流动性比较差,而且锻造的温度范围比较窄。
在锻造温度过高的时候,锻件将会产生粗晶组织。
如果锻造的温度太低,那么锻件的表面将会发生加工硬化现象,因为加工硬化的区域内激活性能非常大,在后续热处理时,部分晶粒会出现快速增长,然后演变成粗晶,从而使得锻件性能大大下降。
铝合金主要元素是Mg 与Si,以Mg2Si 为主要的强化相轻质合金[2]。
通过挤压工艺能够获取铝棒处于常温状态的力学性能指标,具体如表1所示。
表1 6082铝合金常温状态的力学性能指标抗拉强度Rm/MPa屈服强度ReL/MPa 伸长率A/%数值350 320 9~122 控制臂锻造有限元模拟6082 铝合金控制臂锻造成型是三维非稳态大塑性变形过程,主要包含材料、几何非线性与边界接触条件非线性,弹性变形可以忽略,所以,锻造成型过程模拟会选用刚塑性模型。
在金属塑性成形时,材料塑性变形的物理过程十分繁杂,为了便于进一步计算,将变形的部分过程进行理想化,有助于后续数学处理。
控制臂基本形状为长条形,各个部分的金属体积分布并不均匀。
所以,可以通过辊锻制坯、弯曲预锻、终锻模锻成型等环节加以完成。
铝制车身仿真方法研究及试验对标分析
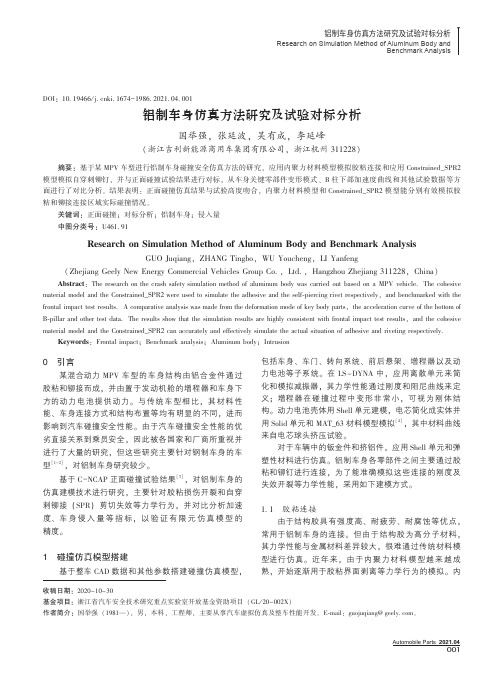
Automobile Parts 2021.04001收稿日期:2020-10-30基金项目:浙江省汽车安全技术研究重点实验室开放基金资助项目(GL /20-002X)作者简介:国举强(1981 ),男,本科,工程师,主要从事汽车虚拟仿真及整车性能开发㊂E-mail:guojuqiang@㊂DOI :10.19466/ki.1674-1986.2021.04.001铝制车身仿真方法研究及试验对标分析国举强,张廷波,吴有成,李延峰(浙江吉利新能源商用车集团有限公司,浙江杭州311228)摘要:基于某MPV 车型进行铝制车身碰撞安全仿真方法的研究,应用内聚力材料模型模拟胶粘连接和应用Constrained_SPR2模型模拟自穿刺铆钉,并与正面碰撞试验结果进行对标,从车身关键零部件变形模式㊁B 柱下部加速度曲线和其他试验数据等方面进行了对比分析㊂结果表明:正面碰撞仿真结果与试验高度吻合,内聚力材料模型和Constrained_SPR2模型能分别有效模拟胶粘和铆接连接区域实际碰撞情况㊂关键词:正面碰撞;对标分析;铝制车身;侵入量中图分类号:U461.91Research on Simulation Method of Aluminum Body and Benchmark AnalysisGUO Juqiang,ZHANG Tingbo,WU Youcheng,LI Yanfeng(Zhejiang Geely New Energy Commercial Vehicles Group Co.,Ltd.,Hangzhou Zhejiang 311228,China)Abstract :The research on the crash safety simulation method of aluminum body was carried out based on a MPV vehicle.The cohesivematerial model and the Constrained_SPR2were used to simulate the adhesive and the self-piercing rivet respectively,and benchmarked with thefrontal impact test results.A comparative analysis was made from the deformation mode of key body parts,the acceleration curve of the bottom ofB-pillar and other test data.The results show that the simulation results are highly consistent with frontal impact test results,and the cohesivematerial model and the Constrained_SPR2can accurately and effectively simulate the actual situation of adhesive and riveting respectively.Keywords :Frontal impact;Benchmark analysis;Aluminum body;Intrusion0㊀引言某混合动力MPV 车型的车身结构由铝合金件通过胶粘和铆接而成,并由置于发动机舱的增程器和车身下方的动力电池提供动力㊂与传统车型相比,其材料性能㊁车身连接方式和结构布置等均有明显的不同,进而影响到汽车碰撞安全性能㊂由于汽车碰撞安全性能的优劣直接关系到乘员安全,因此被各国家和厂商所重视并进行了大量的研究,但这些研究主要针对钢制车身的车型[1-2],对铝制车身研究较少㊂基于C -NCAP 正面碰撞试验结果[3],对铝制车身的仿真建模技术进行研究,主要针对胶粘损伤开裂和自穿刺铆接(SPR )剪切失效等力学行为,并对比分析加速度㊁车身侵入量等指标,以验证有限元仿真模型的精度㊂1㊀碰撞仿真模型搭建基于整车CAD 数据和其他参数搭建碰撞仿真模型,包括车身㊁车门㊁转向系统㊁前后悬架㊁增程器以及动力电池等子系统㊂在LS -DYNA 中,应用离散单元来简化和模拟减振器,其力学性能通过刚度和阻尼曲线来定义;增程器在碰撞过程中变形非常小,可视为刚体结构㊂动力电池壳体用Shell 单元建模,电芯简化成实体并用Solid 单元和MAT_63材料模型模拟[4],其中材料曲线来自电芯球头挤压试验㊂对于车辆中的钣金件和挤铝件,应用Shell 单元和弹塑性材料进行仿真㊂铝制车身各零部件之间主要通过胶粘和铆钉进行连接,为了能准确模拟这些连接的刚度及失效开裂等力学性能,采用如下建模方式㊂1.1㊀胶粘连接由于结构胶具有强度高㊁耐疲劳㊁耐腐蚀等优点,常用于铝制车身的连接㊂但由于结构胶为高分子材料,其力学性能与金属材料差异较大,很难通过传统材料模型进行仿真㊂近年来,由于内聚力材料模型越来越成熟,开始逐渐用于胶粘界面剥离等力学行为的模拟㊂内2021.04 Automobile Parts 002合使用,不但可以提高铆接点的刚度,而且使其应力峰值更低,从而提高钣材的疲劳寿命,因此被广泛用于铝制车身的连接㊂在LS-DYNA中,可以应用Constrained_SPR2模型来模拟自穿刺铆接,该模型由HANSSEN和PORCARO等提出[7-8]㊂对于该模型,在纯拉伸和纯剪切载荷作用下,铆钉的力学行为如图2所示㊂力;n㊁ζtη(θ)(3)图3㊀有效位移等值面最后,对于创建的碰撞仿真模型进行检查,参数与设计保持一致,主要包括:零部件厚度㊁各子系统之间的连接方式和输入参数等整车质心和前后轴荷等㊂2 试验对标分析首先对仿真结果进行初步校核,确保系统能量曲线稳定,车辆变形动画符合物理规律,以及其他考察项在有效范围内,最后进行试验对标㊂由于两者总是存在差异,因此仅确保关键指标相互吻合,主要包括:Automobile Parts 2021.04003(1)车辆变形模式:是验证碰撞仿真模型有效性的首要指标;(2)加速度曲线:B 柱下部加速度曲线表征整车刚度性能,与乘员损伤相关性很大;(3)其他测量值:包括侵入量在内的其他考察项,其中侵入量过大会影响乘员生存空间,是衡量车辆碰撞安全性能的重要指标之一㊂2.1㊀变形模式对标在正面碰撞中,吸能盒和前纵梁作为车辆前端主要吸能变形部件,其变形模式是否与试验一致直接关系到仿真模型的有效性㊂图4为整车碰撞后的形状,由图可见仿真与试验状态基本吻合;图5为吸能盒压溃后的有效高度,试验后吸能盒的厚度约为57mm ,仿真测量值为55.1mm ,两者误差很小;图6为前纵梁碰撞后形状,其前部发生了溃缩,有效地吸收了碰撞能量㊂碰撞后前纵梁的长度约为590mm ,仿真值为595.1mm ,两者偏差不到1%㊂通过对比分析可知,该MPV 车型前部结构变形合理,未见明显胶粘失效区域,吸能效率高,对乘员保护起到积极作用㊂图4㊀整车变形模式图5㊀吸能盒压溃变形模式图6㊀前纵梁压溃变形模式2.2㊀加速度曲线对标B 柱下部加速度作为整车加速度响应的表征量,直接关系到假人伤害,是车辆正碰耐撞性的重要评价指标之一㊂图7为驾驶员侧B 柱下部加速度曲线,其中第一个波峰为吸能盒压溃变形,第二个波峰为纵梁初始压溃,后续波峰为纵梁持续溃缩过程㊂通过对比仿真与试验结果可知,曲线整体变化趋势和峰值基本相符,其中前段波形两者基本一致,后段曲线由于涉及到前悬架与车身的连接㊁轮胎模型和增程器悬置失效等因素,使得仿真与试验波形之间存在局部差异㊂积分加速度曲线获得整车速度曲线,如图8所示,由图可见仿真与试验的速度归零时刻基本一致㊂根据结果可见,该MPV 车型B 柱下部加速度波形为理想的矩形波TESW (Tipped Equivalent Square Wave ),即车辆前部区域压溃刚度均匀,有效降低了加速度峰值,为约束系统参数匹配提供了良好的前提条件㊂图7㊀车身B柱下部加速度曲线图8㊀车身B 柱下部速度曲线在正面碰撞过程中,增程器作为质量较大的刚体,其运动状态影响到前围侵入量和B 柱下部加速度曲线㊂由试验结果可知,增程器侧面悬置在碰撞中发生了断裂,如图9所示㊂通过零部件试验测试可知,增程器左右侧悬置的失效力约为45kN ,后部悬置的失效力约为20kN ㊂在仿真分析中,通过离散梁单元Discrete Beam 来模拟悬置,并在材料模型MAT196中设置失效力以模拟悬置断裂情况㊂图10为仿真模型修正后的增程器底部加速度曲线,由图可知仿真与试验结果基本一致,表明增程器运动姿态吻合㊂2021.04 Automobile Parts 004在前防撞上布置多个测点以监测车辆前部碰撞变形如图12所示㊂从表1可见仿真和试验值偏差很说明防撞梁纵向变形两者基本一致㊂图12㊀前防撞梁测点布置[3]2018.[4][5]BARENBLATTbrittle[6]DUGDALEof the Mechanics and Physics of Solids,1960,8(2):100-104.[7]PORCARO R,HANSSEN A G,AALBERG A,et al.Joining of alu-minium using self-piercing riveting:Testing,modelling and analysis [J].International Journal of Crashworthiness,2004,9(2):141-154.[8]HANSSE A G,OLOVSSON L,PORCARO R,et al.A large-scale fi-nite element point connector model for self-piercing rivet connections [J].European Journal of Mechanics-A/Solids,2010,29:484-495.。
多工步锻造仿真分析
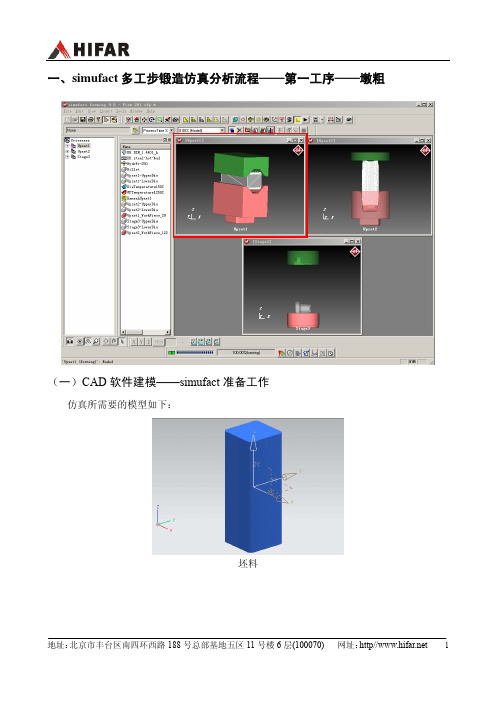
一、simufact多工步锻造仿真分析流程——第一工序——墩粗(一)CAD软件建模——simufact准备工作仿真所需要的模型如下:坯料上模下模(二)simufact墩粗工艺仿真流程在Simufact 中整个锻件的锻造过程按下述求解步骤进行:1)生成开式模锻的分析项目2)导入工件及模具几何模型3)工件及模具位置定义4)定义工件及模具材料5)定义模具运动方式6)定义模具和工件的热参数7)定义摩擦系数8)工件网格划分9)工艺分析条件设置10)分析11)分析结果后处理具体分析过程如下:1)生成开式模锻的分析项目a)点击桌面sfForming 9.0快捷方式启动simufact软件,或者Windows开始菜单中击simufact forming 9.0。
(Windows 开始菜单simufact forming 9.0启动方式) b)选择并按下File→New Project菜单。
c)弹出分析项目向导对话框,按下图进行设置:d)设置完成后,按下“OK”按钮,生成开式模锻工艺仿真分析项目,整个sfForming窗体如下图所示:e)设定单位,点击菜单栏tools-option。
2)导入工件及模具几何模型a)在simufact界面的目标存放区域点击鼠标右键,弹出菜单,选择并按下“Model→Fromfile”菜单。
b)弹出对话框,选择用于墩粗工艺仿真的stl格式模型文件,在导入模型时注意选择合适的单位(m/cm/mm/ft/in)。
3)工件及模具位置定义a)将目标存放区域刚刚导入的上模Upper拖到对应的Process——“UpperDie”(上模)分支上,如下图所示:b)将目标存放区域导入的下模lower拖到对应的Process——“LowerDie”(下模)分支上,如下图所示:c)将目标存放区域导入的工件模型Preform拖到对应的Process——“WorkPiece”(工件)分支上,如下图所示:d)导入模型后,simufact界面显示如下:e)模型定位将整个模型绕x轴旋转90°,保证z轴为上模的运动方向。
《2024年低压铸造铝合金轮毂的数值模拟与工艺优化》范文

《低压铸造铝合金轮毂的数值模拟与工艺优化》篇一一、引言低压铸造技术是铝合金轮毂制造过程中广泛应用的一种铸造工艺。
它结合了计算机技术和精密铸造设备,为制造业提供了更加精确、高效率的制造方式。
通过数值模拟与工艺优化的研究,我们不仅可以对生产流程进行仿真分析,还可以优化工艺参数,提高产品质量和降低生产成本。
本文将就低压铸造铝合金轮毂的数值模拟与工艺优化进行详细探讨。
二、低压铸造铝合金轮毂的数值模拟1. 模型建立在数值模拟过程中,首先需要建立铝合金轮毂的几何模型。
通过CAD软件进行建模,并导入到有限元分析软件中。
在模型中,需要考虑到轮毂的几何形状、尺寸、材料属性等因素。
2. 材料属性设定设定材料属性是数值模拟的重要环节。
根据铝合金的材料性能,设定好材料的密度、导热系数、热膨胀系数等物理参数。
这些参数将直接影响数值模拟的结果。
3. 数值模拟过程在设定好模型和材料属性后,进行数值模拟过程。
这个过程包括填充、凝固和收缩等阶段。
通过模拟填充过程,可以观察到金属液在模具中的流动情况;通过模拟凝固和收缩过程,可以预测产品的质量和可能出现的缺陷。
三、工艺优化1. 填充速度优化在低压铸造过程中,填充速度对产品的质量和性能具有重要影响。
通过数值模拟,可以分析不同填充速度下金属液的流动情况,找到最佳的填充速度,从而提高产品的质量。
2. 温度制度优化温度制度是低压铸造过程中的重要参数之一。
通过优化温度制度,可以控制金属液的凝固过程,减少产品缺陷的产生。
通过数值模拟,可以分析不同温度制度下产品的质量和性能,从而找到最佳的温度制度。
3. 模具设计优化模具设计对产品的质量和性能具有重要影响。
通过优化模具的设计,可以提高产品的质量和降低生产成本。
在模具设计中,需要考虑到模具的材质、结构、冷却系统等因素。
通过数值模拟,可以分析不同模具设计对产品的影响,从而找到最佳的设计方案。
四、结论通过数值模拟与工艺优化的研究,我们可以对低压铸造铝合金轮毂的生产过程进行仿真分析,优化工艺参数,提高产品质量和降低生产成本。
汽车用铝合金控制臂锻造工艺研究
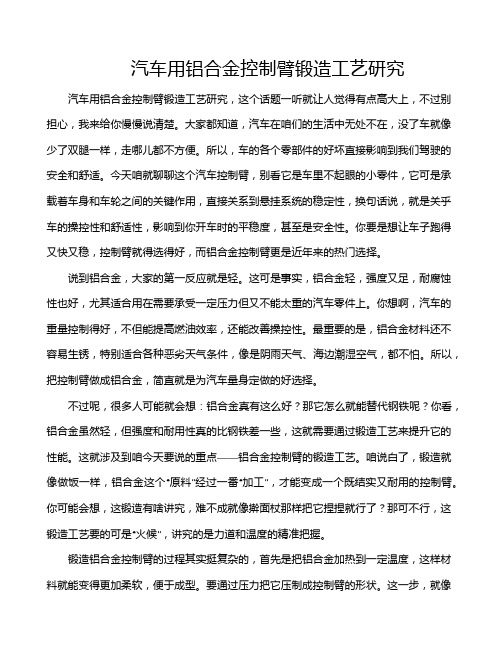
汽车用铝合金控制臂锻造工艺研究汽车用铝合金控制臂锻造工艺研究,这个话题一听就让人觉得有点高大上,不过别担心,我来给你慢慢说清楚。
大家都知道,汽车在咱们的生活中无处不在,没了车就像少了双腿一样,走哪儿都不方便。
所以,车的各个零部件的好坏直接影响到我们驾驶的安全和舒适。
今天咱就聊聊这个汽车控制臂,别看它是车里不起眼的小零件,它可是承载着车身和车轮之间的关键作用,直接关系到悬挂系统的稳定性,换句话说,就是关乎车的操控性和舒适性,影响到你开车时的平稳度,甚至是安全性。
你要是想让车子跑得又快又稳,控制臂就得选得好,而铝合金控制臂更是近年来的热门选择。
说到铝合金,大家的第一反应就是轻。
这可是事实,铝合金轻,强度又足,耐腐蚀性也好,尤其适合用在需要承受一定压力但又不能太重的汽车零件上。
你想啊,汽车的重量控制得好,不但能提高燃油效率,还能改善操控性。
最重要的是,铝合金材料还不容易生锈,特别适合各种恶劣天气条件,像是阴雨天气、海边潮湿空气,都不怕。
所以,把控制臂做成铝合金,简直就是为汽车量身定做的好选择。
不过呢,很多人可能就会想:铝合金真有这么好?那它怎么就能替代钢铁呢?你看,铝合金虽然轻,但强度和耐用性真的比钢铁差一些,这就需要通过锻造工艺来提升它的性能。
这就涉及到咱今天要说的重点——铝合金控制臂的锻造工艺。
咱说白了,锻造就像做饭一样,铝合金这个“原料”经过一番“加工”,才能变成一个既结实又耐用的控制臂。
你可能会想,这锻造有啥讲究,难不成就像擀面杖那样把它捏捏就行了?那可不行,这锻造工艺要的可是“火候”,讲究的是力道和温度的精准把握。
锻造铝合金控制臂的过程其实挺复杂的,首先是把铝合金加热到一定温度,这样材料就能变得更加柔软,便于成型。
要通过压力把它压制成控制臂的形状。
这一步,就像打铁匠在炉火前挥锤的那种感觉,锻造出来的铝合金控制臂就会比铸造出来的要坚固很多。
你要是简单地铸造铝合金,它的结构就可能不够紧密,强度就低,容易出现裂纹。
高速列车新型铝合金车体型材的挤压加工与仿真分析
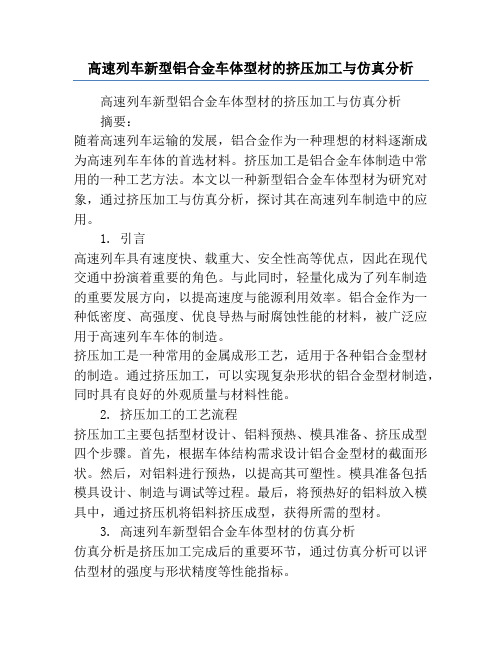
高速列车新型铝合金车体型材的挤压加工与仿真分析高速列车新型铝合金车体型材的挤压加工与仿真分析摘要:随着高速列车运输的发展,铝合金作为一种理想的材料逐渐成为高速列车车体的首选材料。
挤压加工是铝合金车体制造中常用的一种工艺方法。
本文以一种新型铝合金车体型材为研究对象,通过挤压加工与仿真分析,探讨其在高速列车制造中的应用。
1. 引言高速列车具有速度快、载重大、安全性高等优点,因此在现代交通中扮演着重要的角色。
与此同时,轻量化成为了列车制造的重要发展方向,以提高速度与能源利用效率。
铝合金作为一种低密度、高强度、优良导热与耐腐蚀性能的材料,被广泛应用于高速列车车体的制造。
挤压加工是一种常用的金属成形工艺,适用于各种铝合金型材的制造。
通过挤压加工,可以实现复杂形状的铝合金型材制造,同时具有良好的外观质量与材料性能。
2. 挤压加工的工艺流程挤压加工主要包括型材设计、铝料预热、模具准备、挤压成型四个步骤。
首先,根据车体结构需求设计铝合金型材的截面形状。
然后,对铝料进行预热,以提高其可塑性。
模具准备包括模具设计、制造与调试等过程。
最后,将预热好的铝料放入模具中,通过挤压机将铝料挤压成型,获得所需的型材。
3. 高速列车新型铝合金车体型材的仿真分析仿真分析是挤压加工完成后的重要环节,通过仿真分析可以评估型材的强度与形状精度等性能指标。
首先,利用CAD软件建立新型铝合金车体型材的三维模型。
然后,导入模具设计软件进行模具结构设计。
接下来,采用有限元软件对挤压加工过程进行仿真分析,计算各工艺参数对型材形状的影响,以及挤压过程中的应力分布和变形情况。
最后,根据分析结果优化设计参数,以满足型材的强度与精度要求。
4. 实验验证通过实验验证新型铝合金车体型材的挤压加工性能与仿真分析结果的一致性,以确保仿真分析的准确性与可靠性。
首先,进行挤压加工实验,制备一批新型铝合金车体型材。
然后,对实际制备的型材进行物理测试,如强度测试、硬度测试和形状精度测试等。
汽车铝合金转向节锻造成形模拟与试验研究
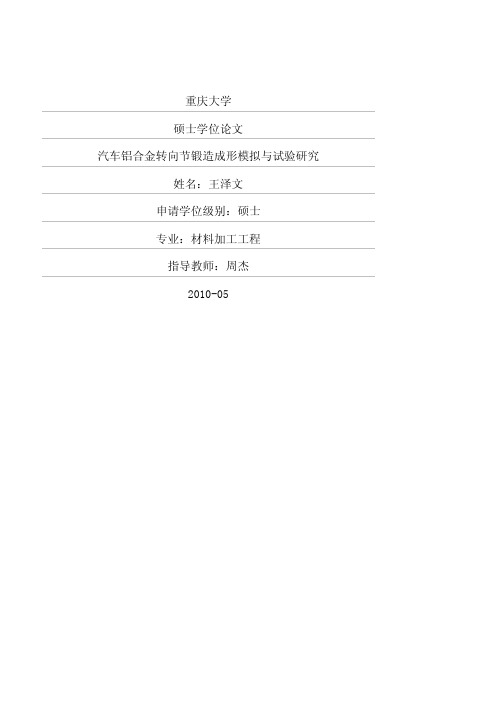
重庆大学硕士学位论文汽车铝合金转向节锻造成形模拟与试验研究姓名:王泽文申请学位级别:硕士专业:材料加工工程指导教师:周杰2010-05摘要随着汽车制造业的高速发展,汽车轻量化和性能要要求越来越严格,汽车零部件生产中,尺寸精度高、外形复杂的锻件所占比重越来越大。
因此,开发材料利用率高并能节约能源的锻造新工艺,对于汽车零件制造业的发展极为重要。
近年来,铝合金结构零件在汽车轻量化要求日益提高的情况下运用越来越广泛。
将铝合金锻件运用到汽车转向系统中,不但可以满足汽车行驶过程中的强度要求,还因为重量的减轻提高其操纵性能。
但是由于铝合金材料本身的特性,如锻造时变形抗力大、流动性差和外摩擦系数较大等导致铝合金锻件的成形困难,阻碍了其在汽车工业中的运用。
转向节是汽车转向系统中的重要零件,既承载一定的车体重量,又在汽车行驶过程中承受交变载荷和刹车时的力矩,是汽车上的重要安全零件之一。
转向节的主要工艺为锻造成形,因此组织性能和外形尺寸的要求非常严格,对于该类锻件锻造方法探索研究将对我国汽车工业的发展产生重要意义。
本文研究的奥迪汽车铝合金转向节,外形极其复杂,主要依靠从国外进口,国内尚无成功的制造经验。
在研究过程中,对该转向节原有的工艺方案进行了分析,运用所建立汽车铝合金转向节弯曲成形制坯过程和终锻成形过程的三维有限元模型,利用三维有限元数值模拟软件DEFORM-3D对汽车转向节锻造成形工艺进行系统分析,模拟其弯曲制坯和终锻成形过程,研究其缺陷产生的原因和演化机理。
找出了影响工厂试制质量的关键因素,提出了既能满足产品精度要求,又能提高材料率、改善弯曲成形质量和终锻模具寿命的优化措施,改进了模锻工艺,使其趋向合理化。
通过模拟验证,给出了二次弯曲成形模具的最优结构参数。
本文的研究工作,结合了模锻工艺、有限元理论、数值模拟仿真技术及模具CAD技术,达到了缩短产品开发周期、提高模具寿命、降低成本等目的。
得到的工作成果解决了奥迪轿车铝合金转向节的锻造成形难题,为同类锻件的生产提供了工艺参考,具有一定的指导意义。
铝合金滚边仿真方法与工艺参数影响分析
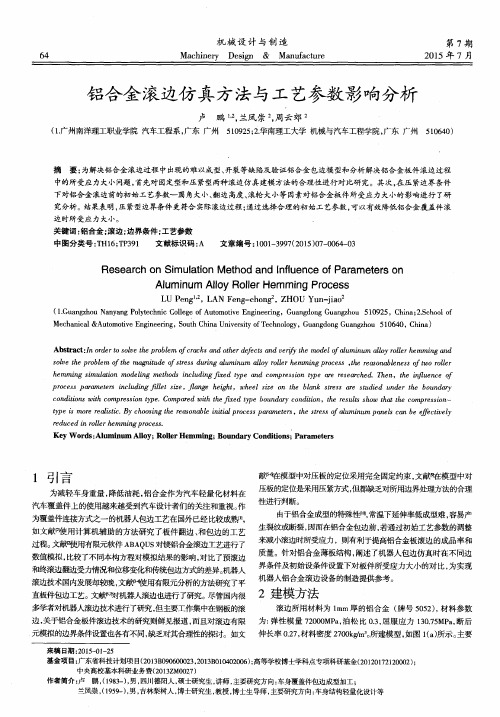
t y p e i s D z o r e r e li a s t i c . B y c h o o s i n g t h e r e a s o n bl a e i n i t i a l p r o c e s s p ra a m e t e r s , t h e s t r e s s f o a l u m i n u m p a n e l s c o n b e e f e c t i v e l y
A b s t r a c t : I n o r d e r t o s o l v e t h e p r o b l e m o f c r a c k s a n d o t h e r d e f e c t s a n d v e r f i y t h e m o d e l fa o l u mi n u m a l l o y r o l l e r h e m mi n g nd a S o l v e t h e p r o b l e m f o t h e m a g n i t u d e f o s t r e s s d u r i n g l a u m i n u m l a l o y r o l l e r h e m mi n g p r o c e s s, t h e r e a s o n a b l e n e s s f o t w o r o l l e r h e mm i n g s i m u l a t i o n mo d e l i n g m e t h o d s i n c l u d i n g ix f e d t y p e a n d c o m p r e s s i o n t y p e o , F e r e s e a r c h e d .T h e n ,t h e i n lu f e n c e f o p r o c e s s p ra a m e t e r s i n c l di u n gf il l e t s i z e , la f ng e h e i g h t ,w h e e l s z i e o n t h e b l nk a s t r e s s a r e s t u d i e d u n d e r t h e b o u da n r y
7050铝合金大锻件锻造工艺仿真与再结晶组织模拟
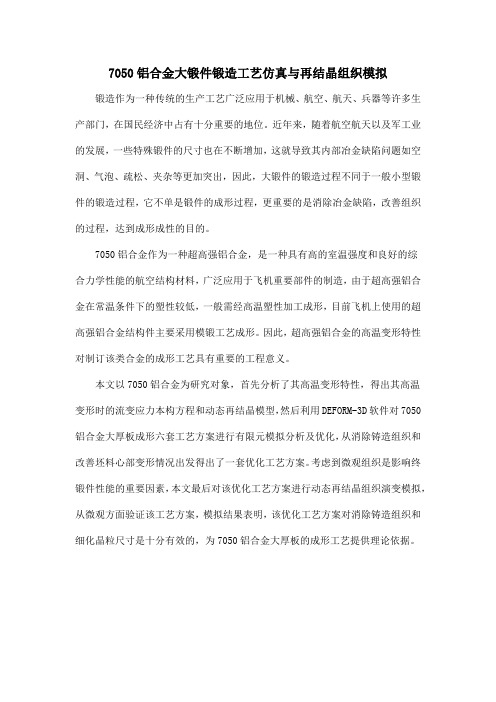
7050铝合金大锻件锻造工艺仿真与再结晶组织模拟锻造作为一种传统的生产工艺广泛应用于机械、航空、航天、兵器等许多生产部门,在国民经济中占有十分重要的地位。
近年来,随着航空航天以及军工业的发展,一些特殊锻件的尺寸也在不断增加,这就导致其内部冶金缺陷问题如空洞、气泡、疏松、夹杂等更加突出,因此,大锻件的锻造过程不同于一般小型锻件的锻造过程,它不单是锻件的成形过程,更重要的是消除冶金缺陷,改善组织的过程,达到成形成性的目的。
7050铝合金作为一种超高强铝合金,是一种具有高的室温强度和良好的综
合力学性能的航空结构材料,广泛应用于飞机重要部件的制造,由于超高强铝合金在常温条件下的塑性较低,一般需经高温塑性加工成形,目前飞机上使用的超高强铝合金结构件主要采用模锻工艺成形。
因此,超高强铝合金的高温变形特性对制订该类合金的成形工艺具有重要的工程意义。
本文以7050铝合金为研究对象,首先分析了其高温变形特性,得出其高温变形时的流变应力本构方程和动态再结晶模型,然后利用DEFORM-3D软件对7050铝合金大厚板成形六套工艺方案进行有限元模拟分析及优化,从消除铸造组织和改善坯料心部变形情况出发得出了一套优化工艺方案。
考虑到微观组织是影响终锻件性能的重要因素,本文最后对该优化工艺方案进行动态再结晶组织演变模拟,从微观方面验证该工艺方案,模拟结果表明,该优化工艺方案对消除铸造组织和细化晶粒尺寸是十分有效的,为7050铝合金大厚板的成形工艺提供理论依据。
铝合金车身件的成形模拟仿真与优化设计
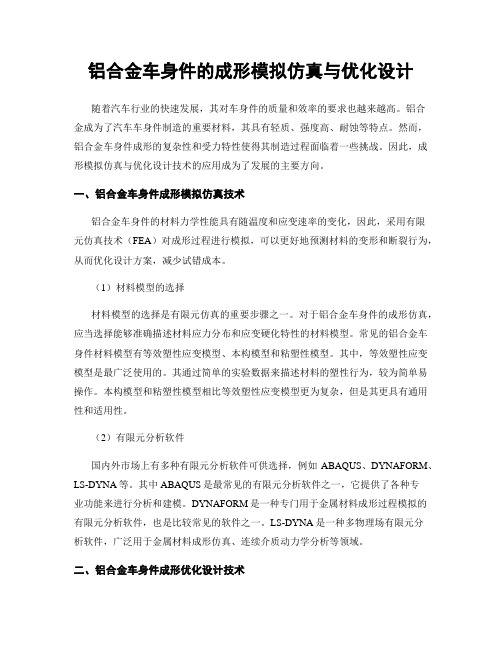
铝合金车身件的成形模拟仿真与优化设计随着汽车行业的快速发展,其对车身件的质量和效率的要求也越来越高。
铝合金成为了汽车车身件制造的重要材料,其具有轻质、强度高、耐蚀等特点。
然而,铝合金车身件成形的复杂性和受力特性使得其制造过程面临着一些挑战。
因此,成形模拟仿真与优化设计技术的应用成为了发展的主要方向。
一、铝合金车身件成形模拟仿真技术铝合金车身件的材料力学性能具有随温度和应变速率的变化,因此,采用有限元仿真技术(FEA)对成形过程进行模拟,可以更好地预测材料的变形和断裂行为,从而优化设计方案,减少试错成本。
(1)材料模型的选择材料模型的选择是有限元仿真的重要步骤之一。
对于铝合金车身件的成形仿真,应当选择能够准确描述材料应力分布和应变硬化特性的材料模型。
常见的铝合金车身件材料模型有等效塑性应变模型、本构模型和粘塑性模型。
其中,等效塑性应变模型是最广泛使用的。
其通过简单的实验数据来描述材料的塑性行为,较为简单易操作。
本构模型和粘塑性模型相比等效塑性应变模型更为复杂,但是其更具有通用性和适用性。
(2)有限元分析软件国内外市场上有多种有限元分析软件可供选择,例如ABAQUS、DYNAFORM、LS-DYNA等。
其中ABAQUS是最常见的有限元分析软件之一,它提供了各种专业功能来进行分析和建模。
DYNAFORM是一种专门用于金属材料成形过程模拟的有限元分析软件,也是比较常见的软件之一。
LS-DYNA是一种多物理场有限元分析软件,广泛用于金属材料成形仿真、连续介质动力学分析等领域。
二、铝合金车身件成形优化设计技术成形模拟仿真的主要目的是为了实现设计、制造、材料选择、操作调整等所需的优化目的。
成形优化的目标可以是提高组件质量、减少成本、改善成形时间和降低零件价值等。
其依靠有限元仿真分析来分析影响成形过程的因素,并寻找最优解。
(1)设计变量优化设计变量优化是一种基于算法的方法,用于确定工程目标和条件下的最优设计参数。
汽车用6016铝合金板材预时效工艺研究及冲压成形数值模拟

摘要6016铝合金板材主要制造汽车覆盖件,特别是乘用车内外罩、后行李箱和门框等汽车外板,是汽车轻量化的关键材料。
而目前国内的铝合金板材仍存在着成形性、抗凹性及零件成形后质量差等问题,无法满足使用要求。
因此开展6016铝合金板材关键的预时效工艺和冲压成形工艺研究,对提高板材的成形质量十分重要。
本文将545 o C固溶30 min的6016铝合金(Al-0.55%Mg-1.0%Si-0.18%Cu)板材水淬后,经60 o C~160 o C×5 min~30 min预时效,室温停放25天后,进行185 o C×20 min的模拟烤漆处理。
采用硬度、拉伸试验,结合示差扫描量热法(DSC)、扫描电子显微镜(SEM)等分析技术,研究预时效工艺对合金的力学性能及微观组织的影响规律。
通过数值模拟仿真实际的冲压过程,并预估零件成形后可能出现的质量缺陷,优化关键成形工艺参数。
结果表明:①固溶淬火后立即进行预时效可以抑制自然时效过程,T4P态合金的成形性和烘烤硬化性能都得到改善。
烤漆前后的硬度随着预时效温度升高,出现先缓慢增加后迅速增加的趋势。
预时效温度为100 o C,预时效时间为20 min合金烘烤前屈服强度低于120 MPa,延伸率在25%左右;烘烤后屈服强度高于180 MPa(预变形2%合金烘烤硬化值达到104 MPa),烘烤后的延伸率在22%左右,综合比较优于其他预时效工艺。
②结合DSC曲线对β”析出温度和激活能进行计算,研究发现,随预时效温度升高,β”析出峰左移,激活能也降低。
说明预时效可以抑制合金自然时效过程,提高合金T4P态成形性能,而且促进烘烤过程中β”的析出,增强烘烤硬化效果。
③以铝制汽车发动机罩内板为对象,建立冲压CAE模型,对板料冲压过程仿真,研究了不同成形工艺对成形后最大减薄率、最大增厚率及最大回弹量的影响规律。
④对多因素的优化问题,首先通过灰色关联分析法,获得较优的工艺参数为:压边力500 KN,摩擦系数0.1,凹凸模间隙1.1t(1.32 mm)、凸模速度3 m/s,仿真试验后出现了少量拉裂缺陷。
汽车下摆臂成形工艺研究

方案 12
后期很大的工作量,同时也为设计人员提供了更好
2.25
2.15
结束语
通过稳健性设计使目标响应的预测值均值由确定性优化的 13.075 减小到了 12.869,降低了目标响
应对设计变量随机波动的敏感性,即提高了制件质
量,从而保证了冲压件在生产中成形的质量,得到了
基于正交试验的最佳工艺参数组合,可以减少开发
用[J]. 集美大学学报,
2013,
(1):
111~114
第一作者简介:王屹峰,男,1976 年生,从事汽车
手白车身焊装技术及冲压件工艺开发。
(收稿日期:
2014-01-23)
《模具制造》2014 年第 3 期
Copyright©博看网 . All Rights Reserved.
简化,这无疑是一种无奈之举,和进口汽车相比,出现
了明显的差距,档次骤然下降。因此,研究复杂结构
(2)模具间隔很小,无法单副安装,要求用垫板按
2~3 副模具一组组装起来,若垫板为铸件,厚度≥
200mm,用钢板时,厚度≥80mm,垫板、U 型槽要符合
压力机工作台并快速装夹。
(3)模具要考虑使用普通压力机的安装需要,此
introduces the main technical points, process parameters and die structure, it has some
popularization value.
Key words: hem arm; in closed. transfer die
3制件生产批量很大要求采用thansfer传递模具进行生产制件加工除开卷落料模之外其余6工序成形模具要布置在一台自动大型冲压机工作台上每副模具长度以及模具之间的间隙都将受到限制特别是左右件共模后模具的导向粗精二次定位制件检测机构浮料装置和送料抓手等都不好布置模具的安装定位滑料也十分闲难设计中常常会出现捉襟见肘的状况结构设计很费思考
一种汽车铝合金控制臂的锻造方法与流程
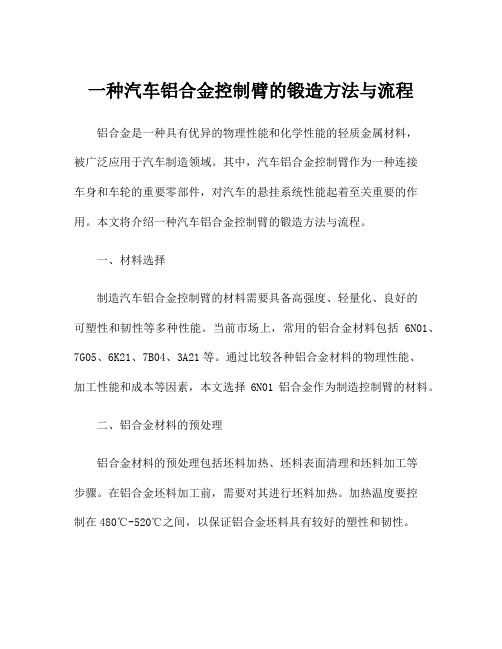
一种汽车铝合金控制臂的锻造方法与流程铝合金是一种具有优异的物理性能和化学性能的轻质金属材料,被广泛应用于汽车制造领域。
其中,汽车铝合金控制臂作为一种连接车身和车轮的重要零部件,对汽车的悬挂系统性能起着至关重要的作用。
本文将介绍一种汽车铝合金控制臂的锻造方法与流程。
一、材料选择制造汽车铝合金控制臂的材料需要具备高强度、轻量化、良好的可塑性和韧性等多种性能。
当前市场上,常用的铝合金材料包括6N01、7G05、6K21、7B04、3A21等。
通过比较各种铝合金材料的物理性能、加工性能和成本等因素,本文选择6N01铝合金作为制造控制臂的材料。
二、铝合金材料的预处理铝合金材料的预处理包括坯料加热、坯料表面清理和坯料加工等步骤。
在铝合金坯料加工前,需要对其进行坯料加热。
加热温度要控制在480℃-520℃之间,以保证铝合金坯料具有较好的塑性和韧性。
接下来,需要对铝合金坯料表面进行清理。
清理过程中,应采用喷砂或振动研磨等表面处理方式,以保证坯料表面光洁,并去除表面的氧化物等杂质。
三、铝合金控制臂的锻造工艺铝合金控制臂的锻造工艺主要包括坯料定型、精密坯料加工、成形、热处理和精加工等环节。
具体步骤如下:(1)坯料定型将铝合金坯料放入定型模具中,利用坯料加工产生的温度和压力等因素,将坯料锻造成要求尺寸和形状的预成型件。
(2)精密坯料加工将预成型件放入数控铣床等加工设备中,进行精密加工。
具体加工方式包括铣削、钻孔、攻丝等,以确保预成型件的尺寸精度和表面质量符合要求。
(3)成形将精密加工后的预成型件放入锻压模具中,进行成形加工。
利用锻压模具的压力,将预成型件锻造成为形状、尺寸更加精确的控制臂件。
(4)热处理将成形后的控制臂件进行热处理。
热处理温度一般在500℃左右,热处理时间需要根据具体情况而定。
通过热处理,可以提高铝合金件的强度和韧性。
(5)精加工热处理后的控制臂件需要进行精加工。
具体加工方式包括铣削、打孔、抛光等,以确保控制臂件的尺寸和表面质量满足设计要求。
- 1、下载文档前请自行甄别文档内容的完整性,平台不提供额外的编辑、内容补充、找答案等附加服务。
- 2、"仅部分预览"的文档,不可在线预览部分如存在完整性等问题,可反馈申请退款(可完整预览的文档不适用该条件!)。
- 3、如文档侵犯您的权益,请联系客服反馈,我们会尽快为您处理(人工客服工作时间:9:00-18:30)。
本 文选用 的摆臂 材料 是 6 X X X 系 铝 合 金 中 的 6 0 8 2铝合 金 , 其工艺 性较 好 , 主要 应用 于辊 锻 、 轧制 、 锻造 、 冲压 成型 等 …。 同时 该 铝合 金 具备 较 好 的 延展 性、 抗 腐蚀性 及优 良的可 焊接性 , 因此 6 0 8 2铝合 金是
( 1 . 安徽工程大学 机械与汽车工程 学院 , 安徽 芜湖 2 4 1 0 0 0 ; 2 . 安徽骆氏升泰汽车零部件有限公 司, 安徽 芜湖 2 4 1 0 0 0 )
摘 要 :为有 效缩 短 产品 研发 周 期 、 节 约开 支及 降低成 本 , 在铝 合金 摆 臂锻 造 工 业生 产 中 , 选 用下料 、 高温热 处理 、 辊 锻 制
第3 4卷 第 9期
V0 1 .3 4 N O.9
新 乡学院学报
J o u r n a l o f Xi n x i a n g Un i v e r s i t y
2 0 1 7年 9月
S e p . 2 0 1 7
汽车铝合金摆臂锻造工艺仿真分析
周 俊。 , 时培 成 , 李 云召
前 悬挂 下 直臂 ( 图 1 ) , 故 将一 般工 艺流 程 中弯 曲环 节
改成 了压扁环节 ,这有 利于锻坯平稳地置 于模锻 下模 具 上 .同时也有利于材 料充分地填充至模具 的各个枝 芽 ,避免 了坯料在模锻 过程 中移动 和填充不充分 现象
的 产 生
a辊 锻 一 道 次 b辊 锻 二 道 次
坯、 压扁、 模锻 成 型 、 余 边去 除 、 锻件 检 测 等工 艺流 程 , 并以 D E F O R M一 3 D软 件 为平 台 , 利 用有 限元 方 法对 铝合 金摆 臂 锻 造 成 形过 程 进行 建 模及 仿 真研 究 , 分析铝 合 金摆 臂 在锻 造 过 程 中冷 挤 压金 属 的 流动 规 律 。结 果表 明 , 此 锻 造 工 艺可 以较 好
料辊锻 。
种应用前景 非常广阔的合金材料 【 2 ] 。 在 实际工业 生产 中 .由于摆臂 形状过 于复杂 , 一
次成型 难度较 大 , 要满 足摆臂质 量 、 强度 、 材料利 用率 等相关 要求 ,设 计 出合 理 的生产T 艺显得 尤为重 要 。 本文所 采用 的T 艺流 程为 : 下 料一 高温 热处 理一 辊锻
一
1 辊锻制坯仿真
本 文初始坯 料选用 的 是半径 2 5 m m、高 2 4 5 m m 的圆柱形棒 料 。相关文献 显示铝 合金 6 0 8 2的最佳锻 造 温度为 4 4 0 ~ 4 9 0℃。在实 际_ T 业生 产中 , 设 置高 温 加热 炉温度 为 4 7 0℃, 下料 、 高温热处理 , 然后进 行坯
选择等操 作 。其 中模具 与夹具材料 分别选择为 2 5 C r —
m o 4 ( Z A ) ( M a c h i n i n g ) 、 1 2 C r _ Ma r t e n s i t i c — S t a i n l e s s _ s t e e l 。
设置上模具动作 沿— z方 向进行 . 为缩 短仿真时间及提 高仿真精度 .本仿真在速度及上下模具间距上做 了相 应的简化处理。设定速度为 1 m m / s 。 根据上下模具 的 距离 7 0 m m, 设置 步数为 6 0 、 模具增量 为 0 . 5 a r m / s t e p 。 然后进行物体间关系定位 ,即设定摩 擦类型为剪切摩 擦, 摩擦系数为 0 . 3 。检查并生成 D B文件和 K E Y文件 。 离开 D e % r m 一 3 D .之后利用 D e  ̄ m 内置求解器进行仿 r
地 成型 锻 件 . 能 为锻 件 的 实际 工业 生 产提供 一定 的理 论依 据 。
关键 词 : 铝 合金 ; 摆臂 : D E F O R M一 3 D; 有 限元 仿 真
中 图分 类 号 : T G 3 1 6 文 献标 识 码 : A 文 章编 号 : 2 0 9 5 — 7 7 2 6 ( 2 0 1 7 ) 0 9 — 0 0 3 4 — 0 4
c辊 锻 一道 次Байду номын сангаас模具
d辊 锻 二 道 次模 具
a 摆臂 正视 图
b摆臂斜视 图
图 2 辊 锻 型 槽 系 及 辊锻 模 具
图 1 前 悬 挂 下直 臂 总成 图
辊锻 仿 真 阶段 主要 分 为坯料 夹 紧和 辊锻 两个 步
收 稿 日期 : 2 0 1 7 - 0 3 — 2 0 基金项 目 : 安 徽 省 科 技 攻 关计 划项 目( 1 6 0 4 a 0 9 0 2 1 5 8 ) 作者简 介 : 周俊 ( 1 9 9 1 一 ) , 男, 安 徽 宣城 人 , 硕 士研 究 生 , 研 究方 向 : 汽 车摆 臂 分 析 。
由于所选初始坯料截 面积与辊 锻毛坯 截面积均 为
圆形 ,为 了达到较为理想 的延展状 态 ,本文采用 了椭
圆一 圆形 型槽 系辊锻制坯的方式 。 其 型槽 系截 面示意 图及辊锻模型 如图 2所示 。
制坯一 压 扁 ( 弯曲) 一 模 锻成 型一 余边 切 除一 锻件 检
测 。 因所选用 的锻 造零 件为帕萨特或奥迪 A 6汽车 的
格式 的压扁模具替换辊锻模具 , 定位模具 、 锻坯及夹具 。 然后对模具及夹具进行 网格划分 、 加载模具及夹具材料
增加 其轴 向延伸率 ,为二 道次辊 锻提供相应 的横 截面
积 做准备 . 以减少及避 免锻 件飞边 的产生 。 二道次辊锻 是为 了得 到具有 合适 长度及合 理 的横 截 面积的锻坯 , 以避 免在模锻过程 中模具 轴向填充不充分 .导致 摆臂 f f J 现 残次品 . 浪费人 力 、 物力、 财力等 。 在模拟 仿真 时 ,先将 C A T I A — V 5 R 2 0绘制 的 三维
通信作者 :时培成 ( 1 9 7 6 一 ) , 男, 安徽 六安人 , 教授 , 博士 , 研 究方向: 汽车振 动。
周 俊, 时培成 , 李云召: 汽车铝合金摆 臂锻造 工艺仿真分析
・3 5・
骤。 其 中一道 次辊锻 目的是减小原 始棒料的横截面积 ,
在D e f o m 前处理中 ,选择辊锻相 应的 K r E Y文件, 打开 D e  ̄ r m 一 2 D / 3 D P r e , 选择 “ 最终” 选项 。用预存为 s t l