过程控制实验报告
北京科技大学过程控制实验报告

实验报告课程名称:过程控制系统实验项目名称:被控对象特性测试实验日期与时间: 2022.07 指导教师:班级:姓名:学号:成绩:一、实验目的要求1.了解控制对象特性的基本形式。
2.掌握实验测试对象特性的方法,并求取对象特性参数二、实验内容本节实验内容主要完成测试对象特性,包含以下两部分内容:1.被控对象特性的实验测定本实验采用飞升曲线法(阶跃向应曲线法)测取对象的动特性。
飞升曲线是指输入为阶跃信号时的输出量变化的曲线。
实验时,系统处于开环状态,被控对象在某一状态下稳定一段时间后,输入一阶跃信号,使被控对象达到另一个稳定状态,得到被控对象的飞升曲线。
在实验时应注意以下的一些问题:1)测试前系统应处于正常工作状态,也就是说系统应该是平衡的。
采取一切措施防止其他干扰的发生,否则将影响实验结果。
2)在测试工作中要特别注意工作点与阶跃幅度的选取。
作为测试对象特性的工作点,应该选择正常工作状态,也就是在额定负荷及正常的其他干扰下,因为整个控制过程将在此工作点附近进行。
阶跃作用的取值范围为其额定值的 5-10%。
如果取值太小,由于测量误差及其它干扰的影响,会使实验结果不够准确。
如果取值过大,则非线性影响将扭曲实验结果。
不能获得应有的反应曲线,同时还将使生产长期处于不正常的工作状态,特别是有进入危险区域的可能性,这是生产所不能允许的。
3)实验时,必须特别注意的是,应准确地记录加入阶跃作用的计时起点,注意被调量离开起始点时的情况,以便计算对象滞后的大小,这对以后整定控制器参数具有重要的意义。
4)每次实验应在相同的条件下进行两次以上,如果能够重合才算合格。
为了校验线性,宜作正负两种阶跃进行比较。
也可作不同阶跃量的实验。
2.飞升曲线数据处理在飞升曲线测得以后,可以用多种方法来计算出所测对象的微分方程式,数据处理方法有面积法、图解法、近似法等。
面积法较复杂,计算工作量较大。
近似法误差较大,图解法较方便,误差比近似法小。
过程控制实验报告
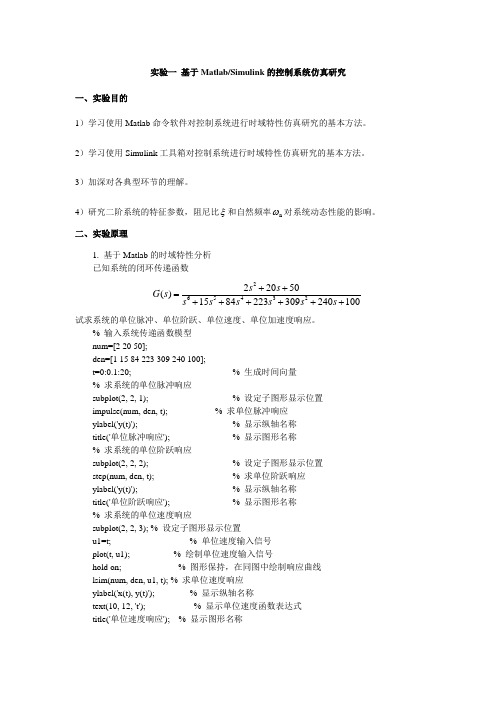
实验一 基于Matlab/Simulink 的控制系统仿真研究一、实验目的1)学习使用Matlab 命令软件对控制系统进行时域特性仿真研究的基本方法。
2)学习使用Simulink 工具箱对控制系统进行时域特性仿真研究的基本方法。
3)加深对各典型环节的理解。
4)研究二阶系统的特征参数,阻尼比ξ和自然频率n ω对系统动态性能的影响。
二、实验原理1. 基于Matlab 的时域特性分析 已知系统的闭环传递函数26543222050()1584223309240100s s G s s s s s s s ++=++++++ 试求系统的单位脉冲、单位阶跃、单位速度、单位加速度响应。
% 输入系统传递函数模型 num=[2 20 50];den=[1 15 84 223 309 240 100];t=0:0.1:20; % 生成时间向量 % 求系统的单位脉冲响应subplot(2, 2, 1); % 设定子图形显示位置 impulse(num, den, t); % 求单位脉冲响应 ylabel('y(t)'); % 显示纵轴名称 title('单位脉冲响应'); % 显示图形名称 % 求系统的单位阶跃响应subplot(2, 2, 2); % 设定子图形显示位置 step(num, den, t); % 求单位阶跃响应 ylabel('y(t)'); % 显示纵轴名称 title('单位阶跃响应'); % 显示图形名称 % 求系统的单位速度响应subplot(2, 2, 3); % 设定子图形显示位置u1=t; % 单位速度输入信号 plot(t, u1); % 绘制单位速度输入信号hold on; % 图形保持,在同图中绘制响应曲线 lsim(num, den, u1, t); % 求单位速度响应 ylabel('x(t), y(t)'); % 显示纵轴名称text(10, 12, 't'); % 显示单位速度函数表达式 title('单位速度响应'); % 显示图形名称 % 求系统的单位加速度响应subplot(2, 2, 4); % 设定子图形显示位置u2=t.*t/2; % 单位加速度输入信号 plot(t, u2); % 绘制单位加速度输入信号hold on; % 图形保持,在同图中绘制响应曲线 lsim(num, den, u2, t); % 求单位加速度响应 ylabel('x(t), y(t)'); % 显示纵轴名称text(11, 100, '1/2*t^2'); % 显示单位加速度函数表达式 title('单位加速度响应'); % 显示图形名称2. 基于Simulink 的时域特性分析按图建立系统的Simulink 模型,对不同的输入信号进行仿真,改变传递函数12325()()s (4)G s G s s s ==+,,观察仿真结果。
过程控制实验报告

过程控制实验报告过程控制实验报告引言:过程控制是一种重要的工程控制方法,广泛应用于工业生产、环境保护、交通运输等各个领域。
本实验旨在通过对过程控制的实际操作,理解和掌握过程控制的基本原理和方法。
一、实验目的本实验的主要目的是通过搭建一个简单的过程控制系统,了解过程控制的基本概念和原理,并通过实际操作掌握过程控制的方法和技巧。
二、实验装置和原理实验所用的装置是一个温度控制系统,由温度传感器、控制器和执行器组成。
温度传感器负责测量温度,控制器根据测量值与设定值的差异来控制执行器的动作,从而实现温度的控制。
三、实验步骤1. 将温度传感器安装在被控温度区域,并连接到控制器上。
2. 设置控制器的参数,包括设定值、比例系数、积分时间和微分时间等。
3. 打开控制器,开始实验。
观察温度的变化过程,并记录实验数据。
4. 根据实验数据分析控制效果,并对控制器的参数进行调整,以达到更好的控制效果。
5. 重复步骤3和4,直到达到满意的控制效果。
四、实验结果与分析在实验过程中,我们观察到温度的变化过程,并记录了实验数据。
通过对实验数据的分析,我们可以评估控制效果的好坏,并对控制器的参数进行调整。
五、实验总结与体会通过本次实验,我们深入了解了过程控制的基本原理和方法。
实践操作使我们更加熟悉了过程控制的过程和技巧。
同时,我们也体会到了过程控制在工程实践中的重要性和应用价值。
六、实验改进与展望本次实验中,我们采用了简单的温度控制系统进行实验。
未来可以进一步扩展实验内容,涉及到其他参数的控制,如压力、流量等,以更全面地了解过程控制的应用。
结语:过程控制是一门重要的工程学科,对于提高生产效率、保护环境、提升产品质量等方面具有重要意义。
通过本次实验,我们对过程控制的原理和方法有了更深入的理解,为今后的工程实践打下了坚实的基础。
希望通过不断学习和实践,我们能够在工程领域中运用过程控制的知识,为社会发展做出更大的贡献。
过程控制实验报告
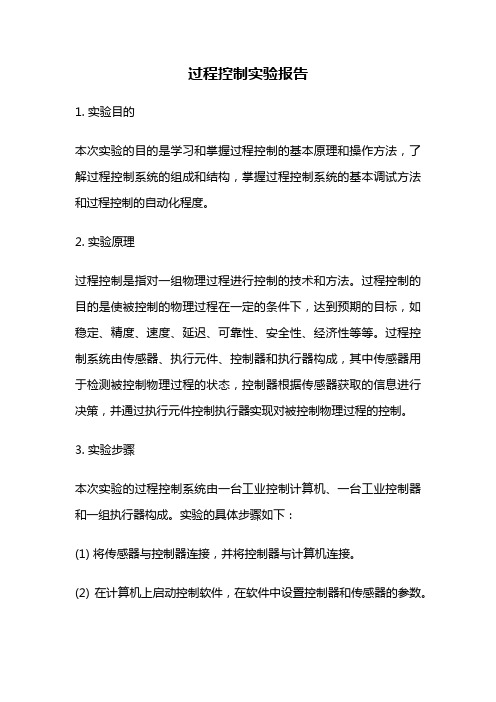
过程控制实验报告1. 实验目的本次实验的目的是学习和掌握过程控制的基本原理和操作方法,了解过程控制系统的组成和结构,掌握过程控制系统的基本调试方法和过程控制的自动化程度。
2. 实验原理过程控制是指对一组物理过程进行控制的技术和方法。
过程控制的目的是使被控制的物理过程在一定的条件下,达到预期的目标,如稳定、精度、速度、延迟、可靠性、安全性、经济性等等。
过程控制系统由传感器、执行元件、控制器和执行器构成,其中传感器用于检测被控制物理过程的状态,控制器根据传感器获取的信息进行决策,并通过执行元件控制执行器实现对被控制物理过程的控制。
3. 实验步骤本次实验的过程控制系统由一台工业控制计算机、一台工业控制器和一组执行器构成。
实验的具体步骤如下:(1) 将传感器与控制器连接,并将控制器与计算机连接。
(2) 在计算机上启动控制软件,在软件中设置控制器和传感器的参数。
(3) 将执行器与控制器连接,并调试执行器的控制参数。
(4) 在控制软件中设置控制策略和控制目标,并启动控制器。
(5) 监测被控制物理过程的状态,并记录相关数据。
(6) 对控制策略和控制参数进行调整,直到被控制物理过程达到预期目标。
4. 实验结果经过多次实验,我们成功地控制了被控制的物理过程,并达到了预期目标。
实验结果表明,过程控制技术可以有效地控制物理过程,并提高物理过程的稳定性、精确性和可靠性。
5. 实验总结本次实验使我们深入了解了过程控制的原理和操作方法,掌握了过程控制系统的基本调试方法和过程控制的自动化程度。
通过实验,我们发现过程控制技术在许多工业领域都具有广泛的应用前景,是提高生产效率和质量的重要手段。
在今后的学习和工作中,我们将继续深入学习和研究过程控制技术,为推动工业自动化和智能化发展做出贡献。
《过程控制系统》实验报告

《过程控制系统》实验报告实验报告:过程控制系统一、引言过程控制系统是指对工业过程中的物理、化学、机械等变量进行监控和调节的系统。
它能够实时采集与处理各种信号,根据设定的控制策略对工业过程进行监控与调节,以达到所需的目标。
在工业生产中,过程控制系统起到了至关重要的作用。
本实验旨在了解过程控制系统的基本原理、组成以及操作。
二、实验内容1.过程控制系统的组成及原理;2.过程控制系统的搭建与调节;3.过程控制系统的优化优化。
三、实验步骤1.复习过程控制系统的原理和基本组成;2.使用PLC等软件和硬件搭建简单的过程控制系统;3.设计一个调节过程,如温度控制或液位控制,调节系统的参数;4.通过修改控制算法和调整参数,优化过程控制系统的性能;5.记录实验数据并进行分析。
四、实验结果与分析在本次实验中,我们搭建了一个温度控制系统,通过控制加热器的功率来调节温度。
在调节过程中,我们使用了PID控制算法,并调整了参数,包括比例、积分和微分。
通过观察实验数据,我们可以看到温度的稳定性随着PID参数的调整而改变。
当PID参数调整合适时,温度能够在设定值附近波动较小,实现了较好的控制效果。
在优化过程中,我们尝试了不同的控制算法和参数,比较了它们的性能差异。
实验结果表明,在一些情况下,改变控制算法和参数可以显著提高过程控制系统的性能。
通过优化,我们实现了更快的响应时间和更小的稳定偏差,提高了系统的稳定性和控制精度。
五、结论与总结通过本次实验,我们了解了过程控制系统的基本原理、组成和操作方法。
我们掌握了搭建过程控制系统、调节参数以及优化性能的技巧。
实验结果表明,合理的控制算法和参数选择可以显著提高过程控制系统的性能,实现更好的控制效果。
然而,本次实验还存在一些不足之处。
首先,在系统搭建过程中,可能由于设备和软件的限制,无法完全模拟实际的工业过程。
其次,实验涉及到的控制算法和参数调节方法较为简单,在实际工程中可能需要更为复杂和精细的控制策略。
《过程控制系统》实验报告

《过程控制系统》实验报告一、实验目的过程控制系统实验旨在通过实际操作和观察,深入理解过程控制系统的组成、工作原理和性能特点,掌握常见的控制算法和参数整定方法,培养学生的工程实践能力和解决实际问题的能力。
二、实验设备1、过程控制实验装置包括水箱、水泵、调节阀、传感器(液位传感器、温度传感器等)、控制器(可编程控制器 PLC 或工业控制计算机)等。
2、计算机及相关软件用于编程、监控和数据采集分析。
三、实验原理过程控制系统是指对工业生产过程中的某个物理量(如温度、压力、液位、流量等)进行自动控制,使其保持在期望的设定值附近。
其基本原理是通过传感器检测被控量的实际值,将其与设定值进行比较,产生偏差信号,控制器根据偏差信号按照一定的控制算法计算出控制量,通过执行机构(如调节阀、电机等)作用于被控对象,从而实现对被控量的控制。
常见的控制算法包括比例(P)控制、积分(I)控制、微分(D)控制及其组合(如 PID 控制)。
四、实验内容及步骤1、单回路液位控制系统实验(1)系统组成及连接将液位传感器安装在水箱上,调节阀与水泵相连,控制器与传感器和调节阀连接,计算机与控制器通信。
(2)参数设置在控制器中设置液位设定值、控制算法(如 PID)的参数等。
(3)系统运行启动水泵,观察液位的变化,通过控制器的调节使液位稳定在设定值附近。
(4)数据采集与分析利用计算机采集液位的实际值和控制量的数据,绘制曲线,分析系统的稳定性、快速性和准确性。
2、温度控制系统实验(1)系统组成与连接类似液位控制系统,将温度传感器安装在加热装置上,调节阀控制加热功率。
设置温度设定值和控制算法参数。
(3)运行与数据采集分析启动加热装置,观察温度变化,采集数据并分析。
五、实验数据及结果分析1、单回路液位控制系统(1)实验数据记录不同时刻的液位实际值和控制量。
(2)结果分析稳定性分析:观察液位是否在设定值附近波动,波动范围是否在允许范围内。
快速性分析:计算液位达到设定值所需的时间。
过程控制实验报告.doc
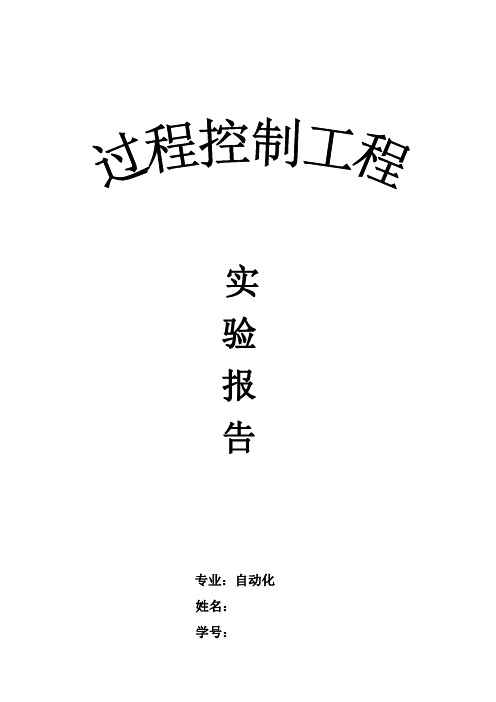
实验报告专业:自动化姓名:学号:实验一、计算机控制系统实验一、实验目的1、了解计算机控制系统的基本构成。
2、掌握本装置计算机实时监控软件的使用3、熟悉计算机控制算法。
4、掌握计算机控制的参数整定方法。
二、实验设备1、THKGK-1过程控制实验装置:GK-02 GK-03 GK-072、计算机及上位机监控软件三、实验原理与常规仪表控制系统相比,计算机控制系统的最大区别就是用微型机和A/D、D/A转换卡来代替常规的调节器。
基本构成框图如下:计算机根据测量值与设定值的偏差,按程序设定的算法进行运算,并将结果经D/A转换器输出。
控制算法有位置式,增量式和速度式。
为了使采样时间间隔内,输出保持在相应的数值,在D/A卡上设有零阶保持器。
四、实验步骤(一)、监控软件的使用及安装说明:1、计算机硬件要求:CPU:486以上。
内存:32MB或更多。
硬盘:1GB。
操作系统:Windows98/2000/XP。
显示器:1024×768。
串行口:COM12、软件安装安装过程已经在上位机光盘里面。
(二)、登录后选择PID算法对上水箱液位进行控制1、将计算机与单片机控制屏结合使用,对上水箱液位进行直接数字DDC控制实验。
系统连接图自拟。
(单片机控制屏仅起A/D、D/A转换的作用)2、设置适当的作图时间间隔和给定值,调整PID参数K、、Ti、Td、直到得到较好的过程控制实时曲线。
3、对不同PID参数下的实时控制曲线进行比较,分析各参数变化对控制质量的影响。
4、自行选择其他控制算法进行实验,了解不同算法的控制质量。
五、实验小结1、将上述实验结果整理好,写出参数整定的具体步骤及整定数值,整理出系统的结构图。
Kp=2 Ki=6 K=5 阀门开度为60%2、简述PID参数对系统性能的影响。
PID调节器分别对应比例、积分和微分作用1、比例参数KP的作用是加快系统的响应速度,提高系统的调节精度。
随着KP的增大系统的响应速度越快,系统的调节精度越高,但是系统易产生超调,系统的稳定性变差,甚至会导致系统不稳定。
过程控制控实验报告

过程控制控实验报告实验⼀单容⾃衡⽔箱特性的测试⼀、实验⽬的1. a 根据实验得到的液位阶跃响应曲线,⽤相应的⽅法确定被测对象的特征参数K 、T 和传递函数。
⼆、实验设备1. A3000⾼级过程控制实验系统2. 计算机及相关软件三、实验原理由图2.1可知,对象的被控制量为⽔箱的液位h ,控制量(输⼊量)是流⼊⽔箱中的流量Q 1,Q 2为流出⽔箱的流量。
⼿动阀QV105和闸板QV116的开度(5~10毫⽶)都为定值。
根据物料平衡关系,在平衡状态时:0Q Q 2010=- (1)动态时则有: dtdVQ Q 21=- (2)式中V 为⽔箱的贮⽔容积,dtdV为⽔贮存量的变化率,它与h 的关系为Adh dV =,即:dtdhA dt dV = (3) A 为⽔箱的底⾯积。
把式(3)代⼊式(2)得:QV116V104V103hh QV105QV102P102LT103LICA 103FV101MQ 1Q 2图2.1单容⽔箱特性测试结构图图2.2 单容⽔箱的单调上升指数曲线dtdhA=-21Q Q (4)基于S 2R h Q =,R S 为闸板QV116的液阻,则上式可改写为dtdhA R h Q S =-1,即:或写作:1)()(1+=TS Ks Q s H (5)式中T=AR S ,它与⽔箱的底积A 和V 2的R S 有关;K=R S 。
式(5)就是单容⽔箱的传递函数。
若令SR s Q 01)(=,R 0=常数,则式(5)可改为: TS KR S R K S R T S T K s H 0011/)(0+-=?+= 对上式取拉⽒反变换得: )e -(1KR h(t)t/T0-= (6)当∞→t 时0KR )h(=∞,因⽽有=∞=0R )h(K 阶跃输⼊输出稳态值。
当t=T 时,则)h(KR )e-(1KR h(T) 001∞===-0.6320.632。
式(6)表⽰⼀阶惯性环节的响应曲线是⼀单调上升的指数函数,如图2.2所⽰。
过程控制实验报告

过程控制实验报告1. 背景过程控制是一种控制技术,用于监测和调整工业过程中的变量,以确保产品的质量和效率。
在工业生产中,过程控制对于提高产品质量、降低生产成本和提高生产效率起着至关重要的作用。
本实验旨在通过模拟一个简单的工业过程,了解过程控制的基本原理和方法。
通过对过程中的变量进行监测和调整,我们可以在不同条件下优化过程,并得出相应的结论和建议。
2. 实验设备和方法2.1 实验设备•控制器:使用PID控制器进行过程控制。
•传感器:使用温度传感器、压力传感器和流量传感器等监测过程中的变量。
•执行器:使用阀门、电机等对过程进行调整。
2.2 实验方法1.设定控制目标:根据实验要求,确定需要控制的变量和目标值。
2.连接传感器和执行器:将传感器和执行器与控制器连接,确保数据的传输和命令的执行。
3.数据采集和处理:通过传感器获取过程中的数据,并将其输入到控制器中进行处理。
4.控制策略选择:选择合适的控制策略,如比例控制、积分控制、微分控制等。
5.调整参数:根据实际情况,调整控制器的参数,以达到控制目标。
6.系统监测和优化:实时监测过程中的变量,并根据实验结果进行系统优化。
3. 实验结果经过实验,我们获得了以下结果:•利用PID控制器进行温度控制实验,成功将温度稳定在目标温度范围内,并保持稳定不变。
•利用PID控制器进行压力控制实验,成功将压力稳定在目标压力范围内,并保持稳定不变。
•利用PID控制器进行流量控制实验,成功将流量控制在目标流量范围内,并保持稳定不变。
通过数据分析和结果对比,我们得出以下结论:•PID控制器具有较好的控制性能,能够实现对温度、压力和流量等变量的精确控制。
•过程控制的关键在于选择合适的控制策略和参数调整,通过不断优化可以实现更好的控制效果。
•实时监测对于控制系统的稳定性和可靠性具有至关重要的作用,可以及时发现问题并进行修正。
4. 建议根据实验结果和分析,我们提出以下建议:1.在实际工业生产中,可以采用PID控制器对关键的工艺变量进行控制,以提高产品质量和生产效率。
过程控制实验报告
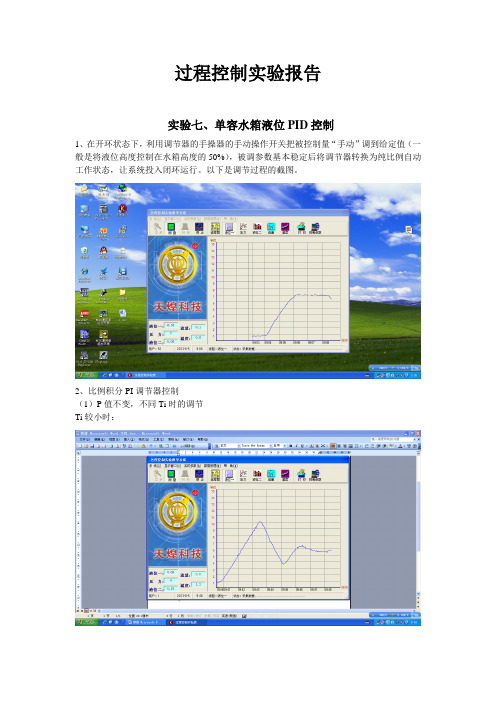
过程控制实验报告实验七、单容水箱液位PID控制1、在开环状态下,利用调节器的手操器的手动操作开关把被控制量“手动”调到给定值(一般是将液位高度控制在水箱高度的50%),被调参数基本稳定后将调节器转换为纯比例自动工作状态,让系统投入闭环运行。
以下是调节过程的截图。
2、比例积分PI调节器控制(1)P值不变,不同Ti时的调节Ti较小时:Ti处于中间位置时:Ti较大时:通过观察不同Ti时的曲线可以发现,当P不变时,Ti越小系统消除余差的能力越强,系统越趋向于不稳定,波动就越大。
这是因为PI环节的幅频特性在低频段为斜率-20的一条斜线,在高频段为斜率为0的直线,相频特性为-90度到0度的一条曲线,因此PI控制器度变化很慢的偏差有很强的调节能力,但之后角度也大,所以当P不变时,Ti越小系统消除余差的能力越强,系统越趋向于不稳定。
(2)Ti值不变,不同P时的调节TI不变P大TI不变P中TI不变P小通过观察不同P时的曲线可以发现,当Ti不变时,比例放大倍数Kc从小到大变化,系统将由稳定想振荡发展,系统的稳定性变差,但Kc增大,控制精度提高,余差减小。
实验参考数据:把上水箱液位作为被控变量,上水箱出水阀开度在70%左右;P:旋钮旋至30%左右;I:0.06X10档;给定电压为1.5V实验八、双容水箱液位PID控制1、同实验七一样,在开环状态下,利用调节器的手操器的手动操作开关把被控制量“手动”调到给定值(一般是将液位高度控制在水箱高度的50%),被调参数基本稳定后将调节器转换为纯比例自动工作状态,让系统投入闭环运行。
以下是调节过程的截图。
手动参数:p:大i:0*10 d:0自动参数p:小i:0*10 d:0自动参数p:大i:0*10 d:0P:大I :0.8*10 d:0临界比例度整定:观察实验曲线可知,当比例放大倍数增大时,系统的稳态误差不断减小,响应时间加快,并出现振荡;加入积分作用后虽可消除余差,但加入积分调节可视系统稳定性降低,甚至出现不稳定情况,同时动态响应变慢,调节时间变大。
过程控制综合实验报告

过程控制综合实验报告目录1.流量比值控制系统 (2)2.液位和进口流量串级控制 (5)3.流量-液位前馈反馈控制91 流量比值控制系统1.1 流量比值控制系统描述流量比值控制系统控制流程图如图1.1所示:图1.1 流量比值控制流程图流量比值控制测点清单如表1.1所示:表1.1流量比值控制控制测点清单水介质一路(简称为I路)由泵P101(变频器驱动, 手动控制作为给定值)从水箱V104中加压获得压头, 经电磁阀XV-101进入V103, 水流量可通过变频器或者手阀QV-106来调节;另一路(简称为II路)由泵P102从水箱V104加压获得压头, 经由调节阀FV-101.水箱V103.手阀QV-116回流至水箱V104形成水循环, 通过调节阀FV-101调节此路的水流量;其中, I路水流量通过涡轮流量计FT-101测得, II 路水流量通过电磁流量计FT-102测得。
本题为比值调节系统, 调节阀FV-101为操纵变量, FT-102的测量值与FT-101的测量值经除法器运算后结果作为FTC-101的测量值, FT-102是被控变量。
1.2 控制算法和编程这是一个单闭环流量比值控制系统, 流量计FT-101流量与流量计FT-102成比例控制, 如图1.2所示。
1.3 操作过程和调试编写控制器算法程序, 下装调试;编写测试组态工程, 连接控制器, 进行联合调试。
2.在现场系统上, 打开手阀QV-102.QV-105, QV115, QV106, 电磁阀XV101直接打开(面板上DOCOM接24V, XV101接GND)。
3.在控制系统上, 将支路1流量变送器(FT-101)输出连接到控制器AI1, 将支路2流量变送器(FT-102)输出连接到控制器AI0, 变频器控制端连接到AO0, 调节阀FV-101控制端连接到AO1, 且变频器手动控制。
4.打开设备电源, 包括调节阀电源, 变频器电源, 变频器设为外部信号操作模式。
过程控制实验报告

过程控制实验报告引言过程控制是工程领域中一项重要的技术,其通过监测和控制生产过程中的各种变量,以最大程度地提高生产效率和质量。
本文将介绍一项涉及过程控制的实验,并分析实验结果以及对于工业生产的意义。
实验目的本次实验的目的是通过模拟实际工业生产过程,在实验室环境中对过程控制进行验证和学习。
该实验旨在通过控制设备和监测仪器,了解过程控制在工业生产中的应用,并且掌握相关的理论知识和实际操作经验。
实验设备和材料本次实验使用的设备包括温度传感器、压力传感器、流量计、控制阀和数据采集系统等。
实验所需材料有水、气体和一种特定化学品。
实验步骤1. 实验前准备:清洁实验设备,确保其正常工作状态。
检查传感器和控制阀的准确性和灵敏度。
2. 确定实验参数:选择要监测和控制的变量,比如温度、压力和流量。
根据设计要求设置合理的上限和下限。
3. 运行实验:通过控制阀控制流量和压力,同时记录设备的实际参数。
4. 数据采集:使用数据采集系统实时记录和保存实验过程中的各种参数数据。
5. 数据分析:将实验中收集到的数据进行整理和分析,比较设定值和实际值之间的偏差,并进行统计学处理。
实验结果和讨论根据实验数据的分析,我们可以得出以下结论:1. 过程控制对于维持稳定的生产工艺非常重要。
通过对温度、压力和流量的控制,我们可以确保产品的质量和一致性。
2. 传感器的精确度对过程控制的结果有直接影响。
不准确的传感器可能导致控制误差,从而影响产品的质量。
3. 过程控制需要根据实际情况进行调整和优化。
在实验中,我们可以通过改变控制阀的开度和调整设定值来实现更好的控制效果。
4. 数据采集和分析的重要性不可忽视。
通过收集和分析实验数据,我们可以及时发现问题并采取措施进行调整,从而提高系统的稳定性和可靠性。
总结通过本次实验,我们对过程控制的原理和应用有了更深入的了解。
过程控制在工业生产中起着关键作用,它可以提高生产效率、降低生产成本、改善产品质量,并且减少对环境的影响。
过程控制实验报告

过程控制实验报告液位控制系统参数整定实验概述⼀、PID调节器中各参数对控制结果的影响1 ⽐例作⽤⽐例作⽤即成⽐例的反应控制系统的偏差信号,⼀旦有偏差产⽣,控制器⽴即产⽣控制作⽤,使偏差向减⼩的趋势变化。
⽐例系数的作⽤在于加快系统的响应速度,提⾼系统调节精度。
越⼤,系统的响应速度越快,系统的调节精度越⾼,也就是对偏差的分辨率(重视程度)越⾼,将会产⽣超调,甚⾄导致系统不稳定。
取值过⼩,则会降低调节精度,尤其是使响应速度缓慢,从⽽延长调节时间,使系统静态、动态环节变坏。
2 积分作⽤积分作⽤的强弱取决于积分时间常数。
越⼤,积分作⽤越弱,反之则越强。
积分环节的作⽤在于消除系统的稳态误差,提⾼系统的⽆差度。
积分作⽤系数越⼤,系统静态误差消除越⼤,但积分作⽤系数过⼤,在响应过程的初期会产⽣积分饱和现象,从⽽引起响应过程的较⼤超调。
若积分作⽤系数过⼩,将使系统的静态误差难以消除,影响系统的调节精度。
3 微分作⽤微分环节是响应系统偏差变化的环节,其作⽤主要是在响应过程中抑制偏差向任何⽅向的变化,并能在偏差信号的值变得太⼤之前,在系统中引⼊⼀个有效的早期修正信号,从⽽加快系统的动作速度,减⼩调节时间,对偏差变化进⾏提前预报。
但微分作⽤太强,会引起被控参数⼤幅度变动,使过程产⽣振荡,微分作⽤太弱,导致静差较⼤。
因此,适当的加⼊微分作⽤不但会增加控制过程的稳定性,⽽且能使静差减⼩。
上⾯的分析表明,⽐例、积分、微分三者之间的关系是相互改善⼜相互制约的。
⽐例、积分、微分环节的综合作⽤使PID控制具有结构简单、物理意义明确、鲁棒性强及稳态⽆静差等优点。
因此,PID控制算法在⼯业控制中处于主导地位。
随着科学技术的发展特别是计算机的诞⽣和发展,涌现出许多新的控制⽅式,然⽽直到现在,PID控制仍有⾮常⼴泛的应⽤。
⼆、参数整定实验原理调节器在控制系统中将被调参数的测量值与给定值进⾏⽐较,得到偏差值,根据偏差进⾏逻辑判断和数学运算,产⽣⼀个使偏差减⼩甚⾄为零的控制信号,参数整定的实验⽬的就是根据被控过程的特性确定PID调节器的⽐例度δ,积分时间TI及微分时间TD的⼤⼩,以达到较好的控制效果在简单的过程控制系统中,调节器参数整定通常以系统瞬态响应的衰减率为主要指标,保证系统具有⼀定的稳定裕量。
过程装备控制实验报告

一、实验目的1. 理解过程装备控制的基本原理和概念。
2. 掌握过程装备控制系统的基本组成和结构。
3. 学习过程装备控制系统的调试和优化方法。
4. 培养动手能力和实验技能。
二、实验原理过程装备控制是研究过程工业中使用的装备及其装备的控制。
它涉及到过程工业中的温度、压力、流量、液位等变量的自动化控制。
本实验主要研究一阶、二阶单回路控制系统的结构与组成,以及调节器参数的整定。
三、实验仪器与设备1. 实验台:包含水箱、锅炉、压力容器、手动阀、闸板等。
2. 仪表:智能调节仪、上位机监控软件(MCGS工控组态软件)。
3. 传感器:液位传感器、压力传感器、温度传感器、流量传感器。
4. 控制器:PLC控制器、DCS控制器。
四、实验步骤1. 实验装置连接:按照设计要求完成系统的接线,连接传感器、控制器、执行器等。
2. 系统上电:接通总电源和相关仪表的电源,启动计算机,运行MCGS组态软件,进入本实验系统。
3. 参数整定:选用单回路控制系统所述的某种调节器参数的整定方法整定好调节器的参数。
4. 系统运行:设置系统给定值SV,手动操作调节器的输出,使被控制量接近给定值且基本稳定不变,切换调节器为自动运行。
5. 实验测试:(1)阶跃扰动实验:在系统稳定运行后,突加阶跃扰动(将给定量增加5%~15%),观察并记录系统的输出响应曲线。
(2)扰动实验:待系统进入稳定后,适量打开另一个阀,以作为系统的扰动,观察并记录在阶跃扰动作用下液位的变化过程。
(3)参数变化实验:适量改变PI的参数,用计算机记录不同参数时系统的响应曲线。
五、实验结果与分析1. 阶跃扰动实验结果:在阶跃扰动作用下,系统输出响应曲线呈现出典型的二阶系统响应特性,经过一定时间后,被控制量逐渐恢复到稳定状态。
2. 扰动实验结果:在扰动作用下,系统输出响应曲线同样呈现出典型的二阶系统响应特性,经过一定时间后,被控制量逐渐恢复到稳定状态。
3. 参数变化实验结果:通过改变PI参数,可以观察到系统响应曲线的变化。
过程控制系统实验报告

过程控制及检测装置硬件结构组成认识,控制方案的组成及控制系统连接过程控制是指自动控制系统中被控量为温度、压力、流量、液位等变量在工业生产过程中的自动化控制。
本系统设计本着培养工程化、参数化、现代化、开放性、综合性人材为出发点。
实验对象采用当今工业现场常用的对象,如水箱、锅炉等。
仪表采用具有人工智能算法及通讯接口的智能调节仪,上位机监控软件采用MCGS 工控组态软件。
对象系统还留有扩展连接口,扩展信号接口便于控制系统二次开辟,如PLC 控制、DCS 控制开辟等。
学生通过对该系统的了解和使用,进入企业后能很快地适应环境并进入角色。
同时该系统也为教师和研究生提供一个高水平的学习和研究开辟的平台。
本实验装置由过程控制实验对象、智能仪表控制台及上位机PC 三部份组成。
由上、下二个有机玻璃水箱和不锈钢储水箱串接, 4.5 千瓦电加热锅炉(由不锈钢锅炉内胆加温筒和封闭外循环不锈钢锅炉夹套构成),压力容器组成。
用,透明度高,有利于学生直接观察液位的变化和记录结果。
水箱结构新颖,内有三个槽,分别是缓冲槽、工作槽、出水槽,还设有溢流口。
二个水箱可以组成一阶、二阶单回路液位控制实验和双闭环液位定值控制等实验。
锅炉采用不锈钢精致而成,由两层组成:加热层(内胆)和冷却层(夹套)。
做温度定值实验时,可用冷却循环水匡助散热。
加热层和冷却层都有温度传感器检测其温度,可做温度串级控制、前馈-反馈控制、比值控制、解耦控制等实验。
采用不锈钢做成,一大一小两个连通的容器,可以组成一阶、二阶单回路压力控制实验和双闭环串级定值控制等实验。
整个系统管道采用不锈钢管连接而成,彻底避免了管道生锈的可能性。
为了提高实验装置的使用年限,储水箱换水可用箱底的出水阀进行。
检测上、下二个水箱的液位。
其型号:FB0803BAEIR,测量范围:0~1.6KPa,精度:0.5 。
输出信号:4~20mA DC。
LWGY-6A,公称压力:6.3MPa,精度:1.0%,输出信号:4~20mA DC本装置采用了两个铜电阻温度传感器,分别测量锅炉内胆、锅炉夹套的温度。
过程控制实验报告
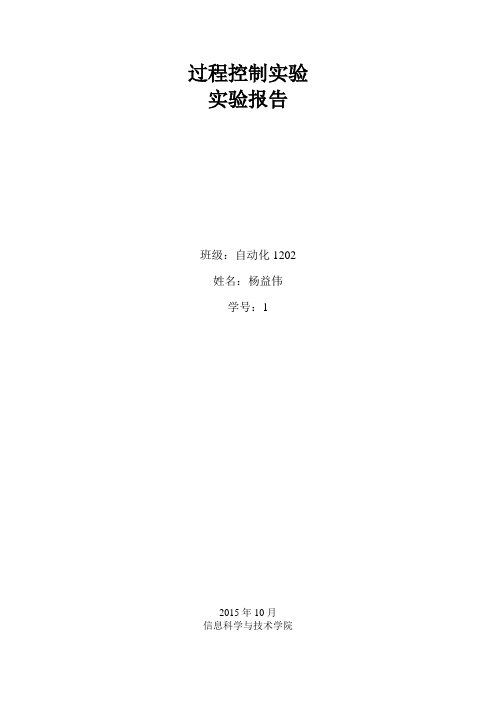
过程控制实验实验报告班级:自动化1202姓名:***学号:12015年10月信息科学与技术学院实验一 过程控制系统建模作业题目一:常见的工业过程动态特性的类型有哪几种通常的模型都有哪些在Simulink 中建立相应模型,并求单位阶跃响应曲线;答:常见的工业过程动态特性的类型有:无自平衡能力的单容对象特性、有自平衡能力的单容对象特性、有相互影响的多容对象的动态特性、无相互影响的多容对象的动态特性等;通常的模型有一阶惯性模型,二阶模型等; 单容过程模型1、无自衡单容过程的阶跃响应实例已知两个无自衡单容过程的模型分别为s s G 5.01)(=和se ss G 55.01)(-=,试在Simulink 中建立模型,并求单位阶跃响应曲线;Simulink 中建立模型如图所示: 得到的单位阶跃响应曲线如图所示:2、自衡单容过程的阶跃响应实例已知两个自衡单容过程的模型分别为122)(+=s s G 和s e s s G 5122)(-+=,试在Simulink 中建立模型,并求单位阶跃响应曲线;Simulink 中建立模型如图所示: 得到的单位阶跃响应曲线如图所示:多容过程模型3、有相互影响的多容过程的阶跃响应实例已知有相互影响的多容过程的模型为121)(22++=Ts s T s G ξ,当参数1=T , 2.1 ,1 ,3.0 ,0=ξ时,试在Simulink 中建立模型,并求单位阶跃响应曲线在Simulink 中建立模型如图所示: 得到的单位阶跃响应曲线如图所示:4、无相互影响的多容过程的阶跃响应实例已知两个无相互影响的多容过程的模型为)1)(12(1)(++=s s s G 多容有自衡能力的对象和)12(1)(+=s s s G 多容无自衡能力的对象,试在Simulink 中建立模型,并求单位阶跃响应曲线;在Simulink 中建立模型如图所示: 得到的单位阶跃响应曲线如图所示:作业题目二:某二阶系统的模型为2() 224nG s s s n nϖζϖϖ=++,二阶系统的性能主要取决于ζ,n ϖ两个参数;试利用Simulink 仿真两个参数的变化对二阶系统输出响应的影响,加深对二阶系统的理解,分别进行下列仿真:(1)2n ϖ=不变时,ζ分别为, , , 时的单位阶跃响应曲线;从上至下ζ分别为,,,(2)0.8ζ=不变时,n ϖ分别为2, 5, 8, 10时的单位阶跃响应曲线;从下到上wn 分别为2,5,8,10实验二PID控制作业题目:建立如下所示Simulink仿真系统图;利用Simulink仿真软件进行如下实验:1.建立如图所示的实验Simulink原理图;2.双击原理图中的PID模块,出现参数设定对话框,将PID控制器的积分增益和微分增益改为0,使其具有比例调节功能,对系统进行纯比例控制;3.进行仿真,观测系统的响应曲线,分析系统性能;然后调整比例增益,观察响应曲线的变化,分析系统性能的变化;由以上三组响应曲线可以看出,纯比例控制对系统性能的影响为:比例调节的余差随着比例带的加大而加大,减小比例带就等于加大调节系统的开环增益,其后果是导致系统真激烈震荡甚至不稳定,比例带很大时,被调量可以没有超调,但余差很大,调节时间也很长,减小比例带就引起被调量的来回波动,但系统仍可能是稳定的,余差相应减少;4.重复步骤2,3,将控制器的功能改为比例微分控制,观测系统的响应曲线,分析比例微分的作用;由以上四组响应曲线可以看出,比例微分控制对系统性能的影响为:可以提高系统的稳定性,引入适当的微分动作可以减小余差,并且减小了短期最大偏大,提高了振荡频率5.重复步骤2,3,将控制器的功能改为比例积分控制,观测系统的响应曲线,分析比例积分的作用;由以上响应曲线可以看出,比例积分控制对系统性能的影响为:消除了系统余差,但降低了稳定性,PI调节在比例带不变的情况下,减小积分时间TI增大积分增益I,将使控制系统稳定性降低、振荡加剧、调节过程加快、振荡频率升高6.重复步骤2,3,将控制器的功能改为比例积分微分控制,观测系统的响应曲线,分析比例积分微分的作用;由以上几组响应曲线可以看出,比例积分微分控制对系统性能的影响为:提高系统稳定性,抑制动态偏差,减小余差,提高响应速度,当微分时间较小时,提高微分时间可以减小余差,提高响应速度并减小振荡,当微分时间较大时,提高微分时间,振荡会加剧;7.将PID控制器的积分微分增益改为0,对系统进行纯比例控制;不断修改比例增益,使系统输出的过度过程曲线的衰减比n=4,记下此时的比例增益值;经过调整,当比例P=1时,终值r=,第一个波峰值y1=,第二个波峰值y2=,衰减比约为4,如下图所示8.修改比例增益,使系统输出的过度过程曲线的衰减比n=2,记下此时的比例增益值;经过调整,当比例P=12时,终值r=,第一个波峰值y1=,第二个波峰值y2=衰减比约为2,如下图所示9.修改比例增益,使系统输出呈现临界振荡波形,记下此时的比例增益;P=100 p=1000由图可知,Kp值越大,系统的衰减比越小;故要使系统呈现临界波形,可使Kp趋于无穷大10.将PID控制器的比例、积分增益进行修改,对系统进行比例积分控制;不断修改比例、积分增益,使系统输出的过渡过程曲线的衰减比n=2,4,10,记下此时比例和积分增益;将PID控制器的比例、积分、微分增益进行修改,对系统进行比例积分控制;不断修改比例、积分、微分增益,使系统输出的过度过程曲线的衰减比n=2,4,10,记下此时比例、积分、微分增益;对系统进行比例积分控制:n=2经过调整,当比例P=2,I=时终值r=1,第一个波峰值y1=,第二个波峰值y2=,衰减比约为2,如下图所示n=4经过调整,当比例P=,I=时终值r=,第一个波峰值y1=,第二个波峰值y2=,衰减比约为4n=10经过调整,当比例P=,I=时终值r=,第一个波峰值y1=,第二个波峰值y2=,衰减比约为10对系统进行比例积分微分控制n=2经过调整,当比例P=6,I=1,D=时终值r=1,第一个波峰值y1=,第二个波峰值y2=,衰减比约为2n=4经过调整,当比例P=6,I=,D=时终值r=,第一个波峰值y1=,第二个波峰值y2=,衰减比约为4,如下图所示n=10经过调整,当比例P=11,I=,D=2时终值r=,第一个波峰值y1=,第二个波峰值y2=,衰减比约为10,如下图所示实验三串级控制作业题目:串级控制系统仿真;已知某串级控制系统的主副对象的传递函数G o1,G o2分别为:1211(),1001101o o G s G s s ==++,副回路干扰通道的传递函数为:221()201d G s s s =++; (1) 画出串级控制系统的方框图及相同控制对象下的单回路控制系统方框图; (2) 用Simulink 画出上述两个系统的仿真框图串级控制系统的方框图如下所示:单回路控制系统方框图如下所示:(3) 选用PID 调节器,整定主副控制器的参数,使该串级控制系统性能良好,并绘制相应的单位阶跃响应曲线;经过不断试验,当PID C1为主控制器输入比例系数为360,积分系数为30,微分系数为60时;当PID C2为副控制器输入比例系数为5,积分系数为0,微分系数为0时;系统阶跃响应达到比较满意的效果,系统阶跃响应如下图所示:采用这套PID 参数时二次扰动作用下的阶跃响应: 一次扰动下的阶跃响应:(4) 比较单回路控制系统及串级控制系统在相同的副扰动下的单位阶跃响应曲线,并说明原因;单回路控制系统在相同的副扰动下的单位阶跃响应曲线:二次扰动作用下的阶跃响应:一次扰动下的阶跃响应:串级控制系统在相同的副扰动下的单位阶跃响应曲线:二次扰动作用下的阶跃响应:一次扰动下的阶跃响应:比较上图故可知串级系统由于副回路的存在对扰动的抑制能力更强;因扰动经干扰通道进入回路后首先影响副回路的输出,副回路反馈后引起副控制器立即动作,力图消弱干扰影响,使得干扰经过副回路的抑制后再进入主回路,对主回路的输出影响大为减弱实验四 比值控制作业题目:在例一中如系统传递函数为43()151s G s e s -=+,其他参数不变,试对其进行单闭环比值控制系统仿真分析,并讨论43()151s G s e s -=+分母中“15”变化10%±时控制系统的鲁棒性;1分析从动量无调节器的开环系统稳定性;由控制理论知,开环稳定性分析是系统校正的前提;系统稳定性的分析可利用Bode 图进行,编制MA TLAB Bode 图绘制程序M-dile 如下:clear all close all T=15;K0=3;tao=4; num=K0;den=T,1;G=tfnum,den,'inputdelay',tao;marginG执行该程序得系统的Bode 图如图所示,可见系统是稳定的;幅值裕量为,对应增益为2选择从动量控制器形式及整定其参数;根据工程整定的论述,选择PI 形式的控制器,即() Ip K G s K s=+; 本处采用稳定边界法整定系统;先让I K =0,调整p K 使系统等幅振荡由稳定性分析图知在p K =附近时系统震荡,即使系统处于临界稳定状态;系统Simulink 框图如下所示调节0.3,0.02p I K K ==时,系统响应图如下所示,基本达到了振荡临界要求3系统过程仿真;单闭环比值控制过程相当于从动量变化的随动控制过程;假定主动量由一常值10加幅度为的随机扰动构成,从动量受均值为0、方差为1的随机干扰;主动量和从动量的比值根据工艺要求及测量仪表假定为3;系统的控制过程Simulink 仿真框图如图所示;其中控制常量及随机扰动采用封装形式;主动控制量的封装结构如下:运行结果如下所示图中曲线从上往下分别为从动量跟踪结果、主动量给定值和随机干扰:可见除初始时间延时外,从动量较好地跟随主动量变化而变化,并且基本维持比值3,有效地克服了主动量和从动量的扰动;4单闭环比值控制系统鲁棒性分析要求分母中“15”变化10%,即积分时间为~,分析系统鲁棒性;系统仿真框图如下图所示延时选择模块Subsystem的展开图如下所示改变积分时间常数为,……共11个值;经过运行后在工作空间绘图使用语句:plottout,simout;hold on;grid on 即可见到下图的仿真结果;仿真结果可见,随着延时环节的变化,从动量跟随主动量的规律有较小变化,但并未改变系统稳定性及精度,说明系统在积分时间发生10%变化时仍能正常工作,系统的鲁棒性较强;实验五解耦控制系统作业题目:在例题中若输入输出之间传递关系改为1122110.5()()7131 ()50.3()13151Y s X s s s Y s X s s s ⎡⎤⎢⎥⎡⎤⎡⎤++=⎢⎥⎢⎥⎢⎥-⎣⎦⎣⎦⎢⎥⎢⎥++⎣⎦,其他参数不变,试利用对角阵解耦方法实现系统的过程控制;(1) 求系统相对增益以及系统耦合分析 由题得系统静态放大系数矩阵为⎥⎦⎤⎢⎣⎡22211211k k k k =⎥⎦⎤⎢⎣⎡3.05-5.011 即系统的第一放大系数矩阵为:⎥⎦⎤⎢⎣⎡-=⎥⎦⎤⎢⎣⎡=⎥⎦⎤⎢⎣⎡=3.055.0112221121122211211k k k k p p p p P系统的相对增益矩阵为:⎥⎦⎤⎢⎣⎡=Λ57.043.043.057.0由相对增益矩阵可以得知,控制系统输入、输出的配对选择是正确的;通道间存在较强的相互耦合,应对系统进行解耦分析;系统的输入、输出结构如下图所示2确定解耦调节器根据解耦数学公式求解对角矩阵,即=⎥⎦⎤⎢⎣⎡---=⎥⎦⎤⎢⎣⎡)(11)(21)(12)(22)(21)(12)(22)(111)(22)(21)(12)(11s Gp s Gp s Gp s Gp s Gp s Gp s Gp s Gp s N s N s N s N ⎥⎦⎤⎢⎣⎡++++---++++=3.38.527.1285544082515.0365.133.38.527.1288.58.822.2161222222S S S S S S S S S S 采用对角矩阵解耦后,系统的结构如下图所示:解耦前后系统的simulink 阶跃仿真框图及结果如下:1.不存在耦合时的仿真框图和结果图a2.系统耦合Simulink仿真框图和结果图b3.对角矩阵解耦后的仿真框图和结果图c对比图a和图b可知,本系统的耦合影响主要体现在幅值变化和响应速度上,但影响不显著;其实不进行解耦通过闭环控制仍有可能获得要求品质;对比图a和图c可知,采用对角解耦器后系统的响应和不存在耦合结果一样,采用对角实现了系统解耦;解耦后系统可按两个独立的系统进行分析和控制;3.控制器形式选择与参数整定通过解耦,原系统已可看成两个独立的单输入输出系统;考虑到PID应用的广泛性和系统无静差要求,控制器形式采用PI形式;PI参数整定通过解耦的两个单输入输出系统进行,整定采取试误法进行; 当x1y1通道Kp=20,Ki=3时系统的阶跃响应如图:当x2y2通道Kp=35,Ki=5时系统阶跃响应如图:4系统仿真采用对角矩阵解耦时,控制系统如下图所示:为了比较解耦和不解耦两种情况,分别列出两种情况的Simulink框图和仿真结果; 解耦时系统的Simulink仿真框图及结果第二幅图中的响应曲线从上往下依次是通道x2y2的输入波形和响应波形、通道x1y1的输入波形和响应波形以及随机扰动波形:不解耦时系统的Simulink仿真框图及结果第二幅图中的响应曲线在t=1s处从上往下依次是通道x2y2的输入波形和响应波形、通道x1y1的输入波形和响应波形以及随机扰动波形:由图对比结果可知,系统解耦后系统的动态响应有一定改善,但改善不大,这是由于耦合较弱所致;因此当要求不高时,系统可以不采取解耦措施;。
过程控制系统实验报告

过程控制系统实验报告
控制系统是指自动地完成规定的工作,用来保证生产过程的安全、正常进行。
它包括检测设备、反馈装置以及输入信号和操纵控制阀门等部件组成。
现代化的生产设备越来越多采用自动化仪表及设施,并由此发展成为一个自动控制系统。
因此,人们将这些自动控制装置称之为“自动控制系统”。
一般地说,凡是具有确切的被控变量、测量值、反馈值和控制值(即控制对象)的独立的随动系统,都可看做是控制系统。
本次实验课是以 PID 控制系统为例,对 PID 控制系统做深入探讨,从而使学生能够理论联系实际,真正提高分析问题和解决问题的能力,培养严谨求实的科学态度。
过程控制系统中主要有:1、被控对象参数测量单元2、控制器3、执行器4、检测装置与反馈装置5、通讯网络与计算机控制系统分为
闭环控制和开环控制两大类。
开环控制系统只依靠输出量测量结果来校正偏差,然后利用调节手段去修正被控量,直到满足给定值。
开环控制适应性强,但抗干扰能力弱;闭环控制则相反。
最简单的闭环控制方法就是比例-积分控制( P—微分—比例+积分)。
也叫 PID 控制或比例-积分式控制。
- 1 -。
过程控制实验报告
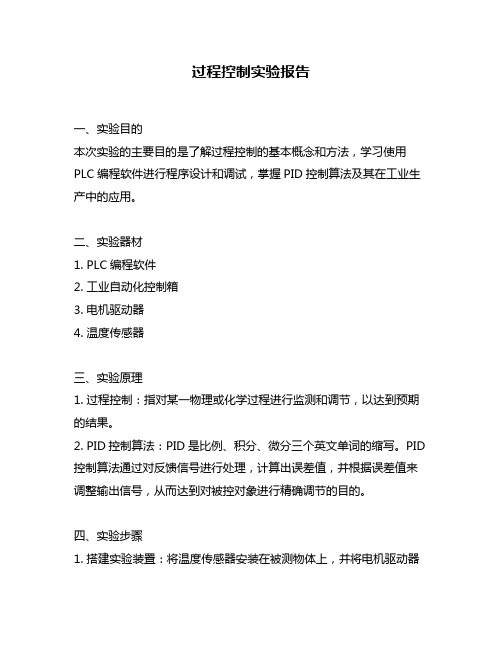
过程控制实验报告一、实验目的本次实验的主要目的是了解过程控制的基本概念和方法,学习使用PLC编程软件进行程序设计和调试,掌握PID控制算法及其在工业生产中的应用。
二、实验器材1. PLC编程软件2. 工业自动化控制箱3. 电机驱动器4. 温度传感器三、实验原理1. 过程控制:指对某一物理或化学过程进行监测和调节,以达到预期的结果。
2. PID控制算法:PID是比例、积分、微分三个英文单词的缩写。
PID 控制算法通过对反馈信号进行处理,计算出误差值,并根据误差值来调整输出信号,从而达到对被控对象进行精确调节的目的。
四、实验步骤1. 搭建实验装置:将温度传感器安装在被测物体上,并将电机驱动器与被测物体相连。
2. 编写PLC程序:使用PLC编程软件编写程序,对温度传感器采集到的数据进行处理并输出给电机驱动器。
3. 调试程序:在调试模式下运行程序,观察温度变化情况,并根据实际情况进行调整,使温度保持在设定值范围内。
4. 记录实验数据:记录温度传感器采集到的数据及程序调试过程中的各种参数和结果。
五、实验结果分析通过本次实验,我们成功地搭建了一个过程控制装置,并使用PID控制算法对被测物体进行了精确控制。
在调试程序的过程中,我们发现PID控制算法具有较高的精度和稳定性,在工业生产中得到了广泛的应用。
六、实验总结本次实验通过对过程控制和PID控制算法的学习,让我们更加深入地了解了工业自动化生产中的相关知识。
同时,也让我们对PLC编程软件有了更深入的认识,并学会了如何使用它来进行程序设计和调试。
通过本次实验,我们不仅获得了理论知识,还锻炼了动手能力和分析问题能力。
- 1、下载文档前请自行甄别文档内容的完整性,平台不提供额外的编辑、内容补充、找答案等附加服务。
- 2、"仅部分预览"的文档,不可在线预览部分如存在完整性等问题,可反馈申请退款(可完整预览的文档不适用该条件!)。
- 3、如文档侵犯您的权益,请联系客服反馈,我们会尽快为您处理(人工客服工作时间:9:00-18:30)。
过程控制系统实验
学院机电工程学院
班级******
学号********
姓名********
老师韩保君
第一节一阶单容水箱特性的测试
一、实验目的
1. 掌握单容水箱的阶跃响应的测试方法,并记录相应液位的响应曲线。
2. 根据实验得到的液位阶跃响应曲线,用相关的方法确定被测对象的特征参数T和传递函数。
二、实验设备
1. THJ-2型高级过程控制系统实验装置
2. 计算机及相关软件
3. 万用电表一只
三、实验原理
由图2-1可知,对象的被控制量为水箱的液位H,控制量(输入量)
是流入水箱中的流量Q
1,手动阀V
1
和V
2
的开度都为定值,Q
2
为水箱中
流出的流量。
根据物料平衡关系,在平衡状态时
动态时,则有
式中V为水箱的贮水容积,dtdV为水贮存量的变化率,它与H的关系为
A为水箱的底面积。
把式(3)代入式(2)得
基于R
S
为阀V2的液阻,则上式可改写为
式中T=AR
S ,它与水箱的底积A和V
2
的R
S
有关;K=R
S。
式(5)就是单容水箱的传递函数。
若令Q
1(S)=R0/S,R
=常数,则式(5)可改为
对上式取拉氏反变换得
当t—>∞时,h(∞)=KR
,因而有K=h(∞)/R0=输出稳态值/阶跃输入当t=T时,则有
h(T)=KR
0(1-e-1)=0.632KR
=0.632h(∞)
式(6)表示一阶惯性环节的响应曲线是一单调上升的指数函数,如图2-2所示。
当由实验求得图2-2所示的阶跃响应曲线后,该曲线上升到稳态值的63%
所对应的时间,就是水箱的时间常数T 。
该时间常数T 也可以通过坐标原点对响应曲线作切线,切线与稳态值交点所对应的时间就是时间常数T ,由响应曲线求得K 和T 后,就能求得单容水箱的传递函数。
如果对象的阶跃响应曲线为图2-3,则在此曲线的拐点D 处作一切线,它与时间轴交于B 点,与响应稳态值的渐近线交于A 点。
图中OB 即为对象的滞后时间τ,BC 为对象的时间
常数T ,所得的传递函数为
四、实验内容与步骤
1.按图2-1接好实验线路,并把阀V 1和V 2开至某一开度,且使V 1的开度大于V2的开度。
2.接通总电源和相关的仪表电源,并启动磁力驱动泵。
3.把调节器设置于手动操作位置,通过调节器增/减的操作改变其输出量的大小,使水箱的液位处于某一平衡位置。
4.手动操作调节器,使其输出有一个正(或负)阶跃增量的变化(此增量不宜过大,以免水箱中水溢出),于是水箱的液位便离开原平衡状态,经过一定的调节时间后,水箱的液位进入新的平衡状态,如图2-4所示。
5.启动计算机记下水箱液位的历史曲线和阶跃响应曲线。
wentai
五、数据处理
(1) 正向增量:首先设置输出值为50%,使水箱系统达到一个稳定的状态,然后再测量初始稳态时对应的参数,得到初始输出值:
7.7929e001,时间77’92。
再调节手动操作器,给一个正向的变化,待其平衡稳定,测量时间为正无穷对应的参数,稳态输出:1.096e002,时间109’6
所以,在T时间内,液位变化量为两个稳态输出的差值,经计算结果为57*0.632 = 36.024,对应0.632h。
将结果绘制成下表:
参数值测量值
液位h
K T τ
正向输入
0.1792 88
得到传递函数为:
H(s)=K/(s+Ts)=0.1721/(1+84.5s)
这次试验的注意事项有不能任意改变阀门开度的大小;阶跃信号不能取得太大,否则会影响正常运行,也不能太小,以防止对象特性的不真实性;在输入阶跃信号前,过程必须处于平衡状态。
通过这次试验,我们明白了过程控制的相关思想也明白了思考和实践相结合的重要性,也更加注重团队合作能力。
六、思考题
1.做本实验时,为什么不能任意改变出水口阀开度的大小?
答:因为如果一开始进水阀的开度<出水阀的开度,那么系统永远无法达到平衡。
同时出水阀也决定了液位达到设定值所需时间的长短,所以记录数据前,应先调好出水阀开度的大小,才能快速达到平衡。
任意改变出水阀开度大小会对响应曲线造成干扰,从而使实验结果的误差变大。
2.用响应曲线法确定对象的数学模型时,其精度与那些因素有关?答:因为系统用到了仪表,因此与仪表的精度有关,同时与出水阀开度的大小有关。
并和放大系数K、时间常数T以及纯滞后时间有关。
第二节双容水箱特性的测试
一、实验目的
1. 熟悉双容水箱的数学模型及其阶跃响应曲线。
2. 根据由实际测得双容液位的阶跃响应曲线,确定其传递函数。
二、实验设备
1. THJ-2 型高级过程控制系统实验装置
2. 计算机、MCGS 工控组态软件、RS232/485 转换器1 只、串口线1 根
3. 万用表1 只
三、原理说明
由图2-5 所示,被控对象由两个水箱相串联连接,由于有两个贮水的容积,故称其为双容对象。
被控制量是下水箱的液位,当输入量有一阶跃增量变化时,两水箱的液位变化曲线如图2-6 所示。
由图2-6 可见,上水箱液位的响应曲线为一单调的指数函数(图2-6 (a)),而下水箱液位的响应曲线则呈S 形状(图2-6 (b))。
显然,多了一个水箱,液位响应就更加滞后。
由S 形曲线的拐点P 处作一切线,它与时间轴的交点为A,OA 则表示了对象响应的滞后时间。
至于双容对象两个惯性环节的时间常数可按下述方法来确定。
在图2-7 所示的阶跃响应曲线上求取:
(1) h2(t)|t=t1=0.4 h2(∞)时曲线上的点B和对应的时间t1;
(2) h(t)|t=t2=0.8 h2(∞)时曲线上的点C和对应的时间t2。
然后,利用下面的近似公式计算式
由上述两式中解出T1和T2,于是求得双容(二阶)对象的传递函数为
四、实验内容与步骤
1、接通总电源和相关仪表的电源。
2、接好实验线路,打开手动阀,并使它们的开度满足下列关系:
V1的开度>V2的开度>V3的开度
3、把调节器设置于手动位置,按调节器的增/减,改变其手动输出值,使下水箱的液位处于某一平衡位置(一般为水箱的中间位置)。
4、按调节器的增/减按钮,突增/减调节器的手动输出量,使下水箱的液位由原平衡状态开始变化,经过一定的调节时间后,液位h2进入另一个平衡状态。
5、上述实验用计算机实时记录h2的历史曲线和在阶跃扰动后的响应曲线。
6、把由计算机作用的实验曲线进行分析处理,并把结果填表入下表中:
wentai
五、数据处理
G(s)=0.1151/(78.8s+1)(92S+1)
参数经过仔细的调整,最后达到了预期的效果。
六、思考题
1、在本实验中,为什么对出水阀不能任意改变其开度?
如果实验条件中没有水量大小,及水量是恒定的,肯定不能改变水流大小,不然在其他外因发生变化时产生的测试结果就不能完全归结于该外因变化的结果,可能还存在水流大小变化的影响。
2、引起双容对象的滞后特性是什么?
答:由于多了一个容积,水位差h2表现出来的响应特性就不同于单容水箱,响应过程在时间上落后了一步,存在管道上的滞后,干扰引起的传感器反馈信号上的滞后。
这段滞后时间主要是对象容量增加和容积之间存在阻力所造成的。