FMEA在QC小组活动中的应用
101-FMEA应用指导书

FMEA使用指导书WI304-1011目的FMEA是一组系统化的活动,它的目的是:1.1发现、评价产品/过程中潜在的失效及其后果1.2找到能够避免或减少这些潜在失效发生的措施1.3书面总结上述过程2使用要求和原则2.1FMEA由研发部项目负责人、横向协调小组采用并制定。
2.2在有要求新设计、新技术或新过程时,要求全面实施FMEA;对设计或过程更改的,要求FMEA集中于对设计或过程的修改、由于修改可能产生的影响;将现有的设计或过程用于新的环境、场所时,FMEA应集中于新环境、场所对现有设计或过程的影响。
2.3在使用PFMEA过程中应充分利用以下几个基本的原则:2.3.1在FMEA准备过程中,每项职责必须明确到人。
2.3.2进行FMEA必须依靠集体协作,综合各部门和每一个人的智慧。
2.3.3为达到最佳效益,FMEA应产品设计、过程设计开始之前。
2.3.4FMEA是一份动态文件,适当地应用FMEA是一个相互作用的过程,永无止境。
3设计FMEA3.1设计FMEA建立的步骤3.1.1DFMEA的开发在制订DFMEA之前,应针对每一系统、子系统或零部件,由小组进行风险评估,只对于高风险的系统、子系统或零部件才做DFMEA分析,并将这个风险评估图的复印件伴随到DFMEA制订全过程。
3.1.2评价失效对顾客的潜在影响。
3.1.3确定在设计中的潜在失效起因,确定减少失效发生或找出失效条件的设计控制变量。
3.1.4编制潜在失效模式分级表,然后建立考虑纠正措施的优选体系。
3.1.5将设计过程的结果编制成文件。
3.2为确认DFMEA制定的是否完善和有效,可以使用《DFMEA检查清单》进行检查和补充。
3.3DFMEA栏目填写说明和要求3.3.1FMEA编号填入FMEA文件编号,以便查询。
3.3.2项目名称填入所分析的系统、子系统或零件的名称、编号。
3.3.3设计责任部门填入整车厂、部门和横向协调小组。
如果知道,还应包括供方的名称。
多方论证(APQPFMEA)小组管理办法

多方论证(APQPFMEA)小组管理办法第一篇:多方论证(APQPFMEA)小组管理办法多方论证(APQP/FMEA)小组管理办法多方论证(APQP/FMEA)小组管理办法目的为满足产品质量先期策划和潜在失效模式及后果分析的要求,有效地实施APQP和FMEA各阶段的工作,使多方论证小组组成有统一的工作规范,特制定本办法。
适应范围适用于本公司多方论证小组开展APQP和FMEA工作和确定活动范围。
职责技术中心是多方论证小组管理的牵头部门,负责针对开发产品或项目组织适时成立多方论证小组。
工作程序4.1 多方论证小组的成立4.1.1 当决定承接某项新产品或较复杂的换型产品时,由技术中心根据所开发的产品的复杂程度和技术含量等客观要求,组织相关部门中的合适人员成立多方论证小组。
4.1.2 多方论证小组这个动态机构是永远存在的,但是小组中的成员是根据不同产品、不同项目由不同的人员组成的。
4.1.3 多方论证小组随新产品开发或改型产品开始时成立,并随新产品转入量产和换型产品完成而自动解散,当新的产品或项目开始时,新的多方论证小组又随着成立。
4.2 多方论证小组的构成4.2.1 按“产品质量先期策划进度表”组成多方论证小组。
4.2.2 多方论证小组成员应视开发产品或换型产品的实际情况和工作酌情增加或减少。
4.3 多方论证小组活动范围4.3.1 每项开发产品或换型产品应选出小组长。
4.3.2 应确定每位组员的职责、承担的任务。
4.3.3 小组长召集组员共同讨论,识别顾客的要求。
4.3.4 确定顾客的特殊要求。
4.3.5 选择必须加入的分承包方和顾客代表。
4.3.6 消化顾客的期望和要求。
4.3.7 设计、工艺可行性的评审。
4.3.8 确定成本、时间安排。
4.3.9 确定来自顾客的帮助,建立与顾客的联络和小组内的沟通。
4.3.10 确定应提供的文件和记录。
4.4 多方论证小组的工作任务。
4.4.1 多方论证小组的成员都是项目的设计及先期质量策划的执行者,具体在自已分担的职责范围内做到:a)认真填写“控制计划表” ;b)找出并控制全部“特殊特性” ;c)尽量预见潜在的失效模式,并对后果进行分析;d)制定优先减少不合格品计划;e)参与项目相应阶段的验证与评审。
QC七大手法 ——FMEA
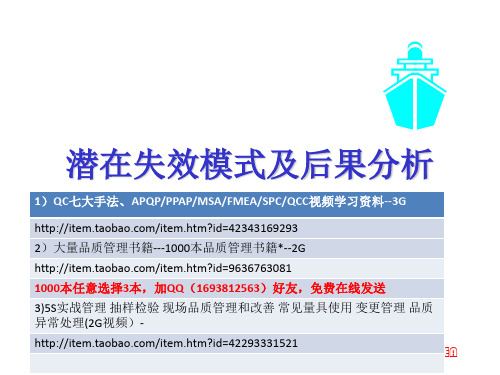
P-FMEA 简介:
过程 FMEA 是一份动态文件, 应该起始于: • 在可行性分析阶段或之前开 始; • 在为生产的工装准备之前; • 要考虑从个别零组件到总成 的所有制造作业。
ISO/TS16949 系列培训
FMEA
P-FMEA 简介:
过程 FMEA 应该从整个过程的 流程图开始。 还应从相应的设计 FMEA 来确 定某些产品影响后果。
1)QC七大手法、APQP/PPAP/MSA/FMEA/SPC/QCC视频学习资料--3G /item.htm?id=42343169293 2)大量品质管理书籍---1000本品质管理书籍*--2G /item.htm?id=9636763081 1000本任意选择3本,加QQ(1693812563)好友,免费在线发送
FMEA
D-FMEA 简介:
设计FMEA应该从系统、子系统或 零部件的框图开始分析。 框图说明了分析中包括的各项目之 间的主要关系,并建立了分析的 逻辑顺序。
ISO/TS16949 系列培训
FMEA
D-FMEA 设计框图:
系统名称:闪光灯
工作环境:温度:湿度:振动:等指标
代表不同的联接 关系。
3 4 开关 C 2 灯泡总成 D 灯罩 A
ISO/TS16949 系列培训
•
FMEA
FMEA 类别: D-FMEA 设计FMEA
P-FMEA 过程FMEA
ISO/TS16949 系列培训
FMEA
D-FMEA 简介:
由设计主管工程师/小组早期采 用的一种分析技术,用来在最大 范围内保证已充分地考虑到和指 明各种潜在的失效模式及其相关 的起因/机理。
责任和目标
分 类
潜在失效 起因/机理
在哪些情况下我们需要导入FMEA?

在哪些情况下我们需要导入FMEA?
FMEA(故障模式与效果分析)是一种常用于产品和过程设计的风险评估工具。
它能够识别、评估和减少潜在故障,从而提高产品和过程的可靠性和安全性。
那么,在哪些情况下我们需要导入FMEA呢?深圳天行健总结如下:
1. 产品设计阶段
在产品设计阶段,FMEA可以帮助设计团队识别潜在的故障模式和效果,并定位其可能的原因和影响。
通过FMEA的分析,设计团队可以识别潜在的风险因素,提前制定相应的措施,从而减少产品在设计、测试和生产过程中的故障率。
2. 生产过程
在生产过程中,FMEA可以用来识别潜在的生产故障,评估其可能的影响和原因,并针对性地采取措施,以减少生产故障出现的概率和影响。
通过FMEA的分析,生产团队可以识别关键和高风险的生产环节,制定相应的控制措施,提高生
产质量和效率。
3. 服务和维护
在服务和维护过程中,FMEA可以用来识别潜在的故障模式和效果,并评估其可能的影响和原因。
通过FMEA的分析,服务和维护团队可以识别关键和高风险的服务和维护环节,制定相应的控制措施,提高服务质量和效率,减少维护成本和时间。
4. 供应链管理
在供应链管理中,FMEA可以用来识别潜在的风险因素,并评估其可能的影响和原因。
通过FMEA的分析,供应链管理团队可以识别关键和高风险的供应链环节,制定相应的控制措施,减少供应链风险,提高供应链效率和可靠性。
综上所述,FMEA是一种常用的风险评估工具,可以在产品设计、生产过程、服务和维护、供应链管理等多个领域中使用。
只有合理运用FMEA,才能提高产品和过程的可靠性和安全性,保证质量和效率的提升。
QC小组活动中常用工具及统计技术合集

QC小组活动中常用工具及统计技术合集在QC(质量控制)小组活动中,常用工具及统计技术是评估和改进质量的重要工具。
本文将介绍几种常用的工具和统计技术,包括直方图、散点图、控制图、Pareto图、故障模式和影响分析(FMEA)以及根因分析等。
一、直方图直方图是一种图形表达方式,可以用于表示数据的分布情况。
在QC小组活动中,直方图通常用于展示数据的频率分布,以便分析数据是否符合正态分布、确定异常值等。
二、散点图散点图用于显示两个变量之间的关系和趋势。
QC小组可以利用散点图观察两个变量是否存在相关性,以及判断是否有异常数据点存在。
三、控制图控制图是一种用于监测过程稳定性和变异性的图表。
在QC小组活动中,常用的控制图有X-Bar和R图、X-Bar和S图,以及P图等。
通过控制图,QC小组可以及时发现过程变异,采取相应措施进行调整和改进。
四、Pareto图Pareto图是一种按照重要性降序排列的柱状图,用于展示问题的优先级和重要性。
在QC小组活动中,Pareto图可以帮助团队确定改进的关键领域,并优先解决最重要的问题。
五、故障模式和影响分析(FMEA)故障模式和影响分析(Failure Mode and Effects Analysis,简称FMEA)是一种系统性的方法,用于分析和评估潜在的故障模式以及其对产品或过程性能的影响。
QC小组通过FMEA可以预防和减少潜在的质量问题,提高产品质量和客户满意度。
六、根因分析根因分析是一种系统性的方法,用于确定问题的根本原因,以便采取相应的纠正和预防措施。
QC小组在活动中常用的根因分析工具包括5W1H、鱼骨图(因果图)和5Why等。
通过根因分析,QC小组能够深入了解问题产生的原因,从而提出有效的改进方案。
除了上述提到的工具和技术,QC小组在活动中还可能运用其他统计方法和工具,如假设检验、回归分析、贝叶斯网络等,以实现对质量进行全面的分析和改进。
总结起来,QC小组活动中常用的工具及统计技术合集包括直方图、散点图、控制图、Pareto图、FMEA以及根因分析等。
FMEA有什么具体的作用?
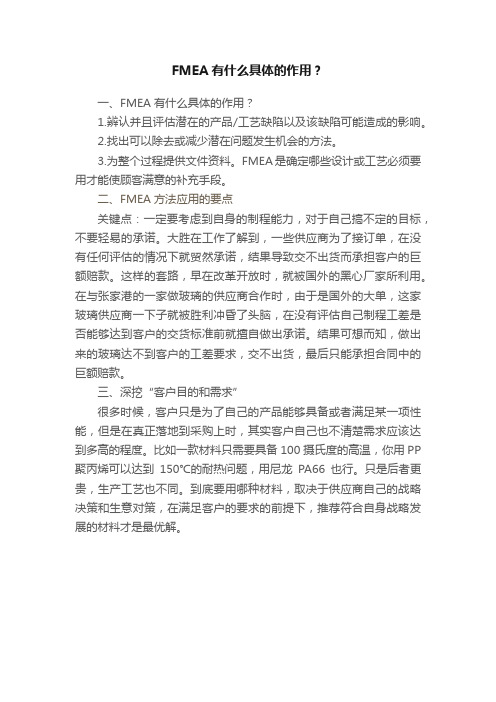
FMEA有什么具体的作用?
一、FMEA有什么具体的作用?
1.辨认并且评估潜在的产品/工艺缺陷以及该缺陷可能造成的影响。
2.找出可以除去或减少潜在问题发生机会的方法。
3.为整个过程提供文件资料。
FMEA是确定哪些设计或工艺必须要用才能使顾客满意的补充手段。
二、FMEA方法应用的要点
关键点:一定要考虑到自身的制程能力,对于自己搞不定的目标,不要轻易的承诺。
大胜在工作了解到,一些供应商为了接订单,在没有任何评估的情况下就贸然承诺,结果导致交不出货而承担客户的巨额赔款。
这样的套路,早在改革开放时,就被国外的黑心厂家所利用。
在与张家港的一家做玻璃的供应商合作时,由于是国外的大单,这家玻璃供应商一下子就被胜利冲昏了头脑,在没有评估自己制程工差是否能够达到客户的交货标准前就擅自做出承诺。
结果可想而知,做出来的玻璃达不到客户的工差要求,交不出货,最后只能承担合同中的巨额赔款。
三、深挖“客户目的和需求”
很多时候,客户只是为了自己的产品能够具备或者满足某一项性能,但是在真正落地到采购上时,其实客户自己也不清楚需求应该达到多高的程度。
比如一款材料只需要具备100摄氏度的高温,你用PP 聚丙烯可以达到150℃的耐热问题,用尼龙PA66也行。
只是后者更贵,生产工艺也不同。
到底要用哪种材料,取决于供应商自己的战略决策和生意对策,在满足客户的要求的前提下,推荐符合自身战略发展的材料才是最优解。
FMEA到底有哪些应用?

FMEA到底有哪些应用?
要想搞明白FMEA都有哪些应用,就必须了解FMEA发展历史,从中我们可以发现一些端倪。
从FMEA近70年的发展历程来看,其一直在对产品可靠性有着极高要求的行业大面积推广和使用,并且成为了非常重要的可靠性保证和提升工具。
2019年6月发布的AIAG&VDA FMEA手册明确的将其定义为技术风险分析工具,基于风险管理的过程(ISO31000风险管理将其定义为风险识别、风险分析、风险评价和风险控制),用事前预防(设计开始前)的思维,系统分析产品以及工艺过程控制所存在的风险,并加以系统评价和控制。
所以,从上述来看,FMEA的应用其实非常的明确,就是将FMEA开发的结果应用于设计以及设计控制活动中,以增强设计结果可靠性的保证。
这个解释有点学术了,我给大家列举一些简单、直接的例子就很容易理解了:
DFMEA应用举例:
图纸上的尺寸及特性定义;
产品的结构及材料选择;
特殊特性清单;
设计评审的对象(如特性的定义等);
CAE分析的对象;
设计验证计划(DVP)的开发;
……
PFMEA应用举例:
开发控制计划;
标准化作业的内容;
设备工装点检维护内容;
SPC管理对象;
防错控制;
防错装置清单;
……
除了上面这些应用,还有别的吗?你可以再想一想!其实FMEA 能带给我们的远远不止这些!。
质量故障模式与影响分析(FMEA)在质量改进中的应用案例
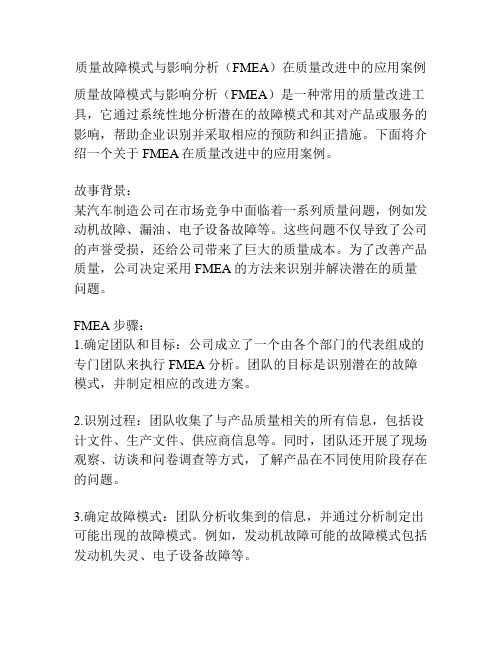
质量故障模式与影响分析(FMEA)在质量改进中的应用案例质量故障模式与影响分析(FMEA)是一种常用的质量改进工具,它通过系统性地分析潜在的故障模式和其对产品或服务的影响,帮助企业识别并采取相应的预防和纠正措施。
下面将介绍一个关于FMEA在质量改进中的应用案例。
故事背景:某汽车制造公司在市场竞争中面临着一系列质量问题,例如发动机故障、漏油、电子设备故障等。
这些问题不仅导致了公司的声誉受损,还给公司带来了巨大的质量成本。
为了改善产品质量,公司决定采用FMEA的方法来识别并解决潜在的质量问题。
FMEA步骤:1.确定团队和目标:公司成立了一个由各个部门的代表组成的专门团队来执行FMEA分析。
团队的目标是识别潜在的故障模式,并制定相应的改进方案。
2.识别过程:团队收集了与产品质量相关的所有信息,包括设计文件、生产文件、供应商信息等。
同时,团队还开展了现场观察、访谈和问卷调查等方式,了解产品在不同使用阶段存在的问题。
3.确定故障模式:团队分析收集到的信息,并通过分析制定出可能出现的故障模式。
例如,发动机故障可能的故障模式包括发动机失灵、电子设备故障等。
4.确定影响:团队评估每个故障模式对产品质量和客户满意度的影响程度。
例如,发动机故障会导致车辆停机,严重影响客户满意度。
5.确定原因:团队分析每个故障模式产生的原因,并列出可能的原因。
例如,发动机故障的原因可能是设计缺陷、生产工艺问题或供应商质量不稳定。
6.确定控制措施:团队制定针对每个故障模式的控制措施,以降低故障发生的可能性或减轻故障对产品的影响。
例如,针对发动机故障,可以加强设计验证、改进生产工艺和加强供应商质量管理等。
7.实施改进:团队将制定的控制措施落实到实际操作中,包括调整设计、改进生产工艺和提高供应商管理等。
同时,团队也要设立有效的跟踪和监控机制,以确保改进方案的有效性。
改进效果:通过FMEA的分析,该汽车制造公司发现了多个潜在的质量问题,并制定了相应的改进措施。
fmea工具的运用
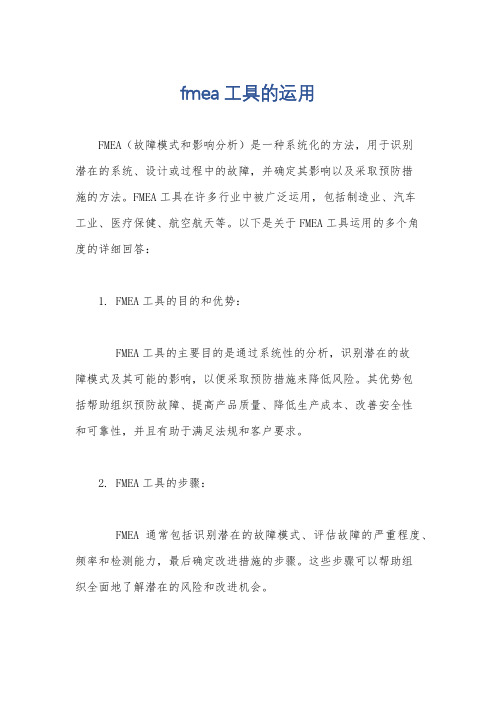
fmea工具的运用FMEA(故障模式和影响分析)是一种系统化的方法,用于识别潜在的系统、设计或过程中的故障,并确定其影响以及采取预防措施的方法。
FMEA工具在许多行业中被广泛运用,包括制造业、汽车工业、医疗保健、航空航天等。
以下是关于FMEA工具运用的多个角度的详细回答:1. FMEA工具的目的和优势:FMEA工具的主要目的是通过系统性的分析,识别潜在的故障模式及其可能的影响,以便采取预防措施来降低风险。
其优势包括帮助组织预防故障、提高产品质量、降低生产成本、改善安全性和可靠性,并且有助于满足法规和客户要求。
2. FMEA工具的步骤:FMEA通常包括识别潜在的故障模式、评估故障的严重程度、频率和检测能力,最后确定改进措施的步骤。
这些步骤可以帮助组织全面地了解潜在的风险和改进机会。
3. FMEA工具的应用领域:FMEA工具可以应用于产品设计阶段、制造过程、服务业务等多个领域。
在产品设计阶段,FMEA可用于识别设计缺陷和改进设计。
在制造过程中,FMEA可用于识别生产线上的潜在故障和改进生产流程。
在服务业务中,FMEA可用于识别服务过程中的潜在问题并改进服务质量。
4. FMEA工具的实际案例:举例来说,汽车制造商可以使用FMEA工具来分析汽车零部件的潜在故障模式,以确保汽车在使用过程中的安全性和可靠性。
另外,医疗保健行业也可以使用FMEA工具来分析手术流程中的潜在风险,以提高手术的成功率和患者安全性。
总之,FMEA工具是一种强大的分析工具,可以帮助组织识别和管理潜在的风险,改进产品质量和流程效率。
通过全面运用FMEA工具,组织可以更好地预防故障,提高客户满意度,并在竞争激烈的市场中保持竞争优势。
FMEA的应用及分析
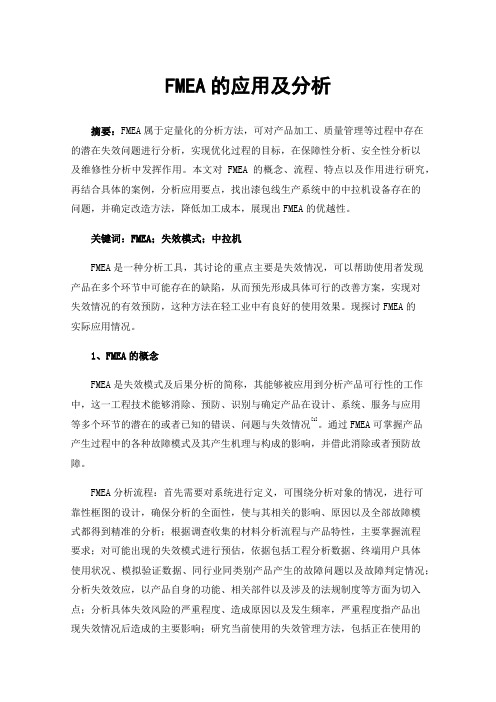
FMEA的应用及分析摘要:FMEA属于定量化的分析方法,可对产品加工、质量管理等过程中存在的潜在失效问题进行分析,实现优化过程的目标,在保障性分析、安全性分析以及维修性分析中发挥作用。
本文对FMEA的概念、流程、特点以及作用进行研究,再结合具体的案例,分析应用要点,找出漆包线生产系统中的中拉机设备存在的问题,并确定改造方法,降低加工成本,展现出FMEA的优越性。
关键词:FMEA;失效模式;中拉机FMEA是一种分析工具,其讨论的重点主要是失效情况,可以帮助使用者发现产品在多个环节中可能存在的缺陷,从而预先形成具体可行的改善方案,实现对失效情况的有效预防,这种方法在轻工业中有良好的使用效果。
现探讨FMEA的实际应用情况。
1、FMEA的概念FMEA是失效模式及后果分析的简称,其能够被应用到分析产品可行性的工作中,这一工程技术能够消除、预防、识别与确定产品在设计、系统、服务与应用等多个环节的潜在的或者已知的错误、问题与失效情况[1]。
通过FMEA可掌握产品产生过程中的各种故障模式及其产生机理与构成的影响,并借此消除或者预防故障。
FMEA分析流程:首先需要对系统进行定义,可围绕分析对象的情况,进行可靠性框图的设计,确保分析的全面性,使与其相关的影响、原因以及全部故障模式都得到精准的分析;根据调查收集的材料分析流程与产品特性,主要掌握流程要求;对可能出现的失效模式进行预估,依据包括工程分析数据、终端用户具体使用状况、模拟验证数据、同行业同类别产品产生的故障问题以及故障判定情况;分析失效效应,以产品自身的功能、相关部件以及涉及的法规制度等方面为切入点;分析具体失效风险的严重程度、造成原因以及发生频率,严重程度指产品出现失效情况后造成的主要影响;研究当前使用的失效管理方法,包括正在使用的可行性评审、安全与失效设计与设计评审等方法,展开难检度分析与关键性分析;确定改进措施,确保检测度、发生度与严重度都得到控制;最后对失效模式的严重度、难检度、发生率与改善情况等数据进行汇总。
FMEA在质量管理中的应用与实践

FMEA在质量管理中的应用与实践质量管理是现代企业发展中的重要环节,它涉及到产品设计、生产制造、供应链管理以及售后服务等多个方面。
为了确保产品和服务的质量稳定和可靠,企业需要采取一系列措施来进行质量管理,而FMEA(故障模式与效应分析)是其中一种重要的方法。
本文将探讨FMEA在质量管理中的应用与实践。
一、FMEA简介FMEA是一种系统性的分析方法,旨在识别和评估潜在的故障、缺陷或问题,并采取相应的措施来预防或减少它们的发生。
它通过分析故障模式、故障原因、故障后果以及现有控制措施的有效性,确定关键问题,制定改善和预防计划,从而提高产品和服务的质量水平。
二、FMEA在质量管理中的应用1. 产品设计阶段的应用在产品设计阶段,通过FMEA可以识别和分析潜在的设计缺陷和故障模式,从而在产品正式投产之前就进行纠正和改进。
FMEA可以帮助设计团队确定关键特征、功能和设计参数,评估各种设计变量的影响,并制定相应的控制措施,以确保产品在使用过程中能够满足客户的需求和期望。
2. 生产制造阶段的应用在生产制造阶段,FMEA可以用于识别和评估潜在的生产过程问题和风险,以及相应的控制方案。
通过分析生产过程中的潜在故障模式和故障原因,FMEA可以帮助企业确定关键的控制点和控制措施,以预防和减少质量问题的发生。
同时,FMEA还可以优化生产工艺流程,提高产品制造的效率和稳定性。
3. 供应链管理阶段的应用在供应链管理中,FMEA可以用于评估和管理供应商的质量风险。
通过对供应链中潜在的故障模式和故障原因进行分析和评估,企业可以识别高风险的供应商,并采取相应的措施进行改进或风险缓解。
这有助于确保供应链的稳定性和可靠性,减少供应链中的质量问题和风险。
4. 售后服务阶段的应用在售后服务阶段,FMEA可以用于评估和改进产品的可靠性和维修性。
通过对已发生故障的产品进行FMEA分析,可以识别主要故障模式和故障原因,并制定相应的改进计划。
这有助于提高产品的可靠性和寿命,并减少维修成本和客户投诉。
FMEA的作用及分析方法

可以做什么? —设计变更 —过程变更 —特别的控制 —标准、程序或
指南的更改
采取措施后的 效果验证
3.5 PFMEA分析要素——过程步骤/功能
➢ 过程步骤:指工序
✓ 在编号过程和术语的基础上,填入识别的所需分析过程步骤或操作 (可填入编号或名称。名称方面如车削、钻孔、功丝、焊接、装配 等)。
✓ 使用的过程编号体制、先后排序和术语应与那些用于过程流程图的 文件(控制计划、作业指导书)保持一致,以确保可追溯性和联系。
•DFMEA---设计FMEA,在产品设计前对产品的每一个模块和软件 系统进行各自的DFEMA分析,如结构安装、安全设计、机芯配合、 外部接口等,也可细化到各个元器件。分析对象:以系统、子系 统或零部件为分析对象
•PFMEA---过程FMEA(制造/装配FMEA),针对产品的生产制造过程 进行的分析。分析这些生产过程中可能会产生什么样的失效模式 以及带来怎么样的影响后果,最终导致产品的失效的。分析对象 :以生产工艺过程的每道工序为分析对象;
➢ 产品生产之前,设计阶段,由设计缺陷产生 的故障模式
➢ 在生产之前,针对生产和组装过程缺陷的故 障模式
➢ 在产品使用之前,对系统或过程产生的缺陷 引起的故障模式的分析
➢ 对设备系统(一般机械)、分系统(电子、机 械、控制)、组件(工装夹具、物料输送、驱 动)、部件的潜在失效模式的分析
1.4 FMEA的分类
措施结果
建议 措施
责任和目标
完成日期
采取措施及 生效日期
S
O
D
R P
N
3.3 PFMEA表头信息
➢ 项目名称:
填入所需分析过程的系统、子系统或零部件的名称
➢ 过程责任:
FMEA的概念和运用时机

书山有路勤为径, 学海无涯苦作舟
•32
RPN 流程
•探测度D •探测度D
•严重度S •严重度S
•来自经验和数据 •DFMEA
•来自预测
•频度O
•级别
•项目/功能•失•潜效在模式•失•潜效在后果
•潜在失效
•现行
•的起因/机理 •设计控制
•RPN
•PFMEA
•级别
•项目/功能•失•潜效在模式•失•潜效在后果
频 度 数
现行设 计控制
预探 防测
不 易 探 测 度 数
D
风 险 顺 序 数 R
P
N
建议 措施
责任 和目 标完 成日
期
•后 果是 什么
•会有什么问题 •无功能 •部分功能 •功能过强 •功能降级 •功能间歇 •非预期功能
•有 多糟 糕
•起 因是 什么
•发 生频
率如 何
•怎样 预防
和探 测
•能做些什么 •设计更改 •过程更改 •特殊控制 •采用新程序 或指南的更 改
•28
过程FMEA 小组成员
• 过程工程师—通常的小组领导 • 生产操作者 • 工艺工程师 • 设计工程师 • 可靠性工程师 • 加工工程师 • 维修工程师 • 项目经理 • 质量工程师 • 其他,包括:销售、供应商、QA/QC等
书山有路勤为径, 学海无涯苦作舟
•29
定义顾客
DFMEA的顾客 • 最终使用者:使用产品的人 PFMEA的顾客 • 后序的操作者 • 最终使用者:使用产品的人
书山有路勤为径, 学海无涯苦作舟
•27
设计FMEA 小组成员
• 在筹备样件期间开始 • 设计工程师—通常的小组领导 • 检验工程师 • 可靠性工程师 • 制造工程师 • 最终服务工程师 • 项目经理 • 质量工程师 • 顾客联系人 • 其他,包括:销售、开发、过程、QA/QC等
FMEA分析与应用研究

FMEA分析与应用研究FMEA(Failure Mode and Effects Analysis)是一种常用的风险管理工具,用于识别和评估设计或工艺过程中的潜在故障模式及其潜在影响,以制定适当的预防措施。
FMEA分析可以帮助组织预测潜在故障、减少失误、提高产品质量、降低成本,并提高客户满意度。
1.识别潜在故障模式:通过系统地审查设计、工艺或过程,以确定可能的故障模式,并将其列入FMEA表格中。
故障模式可以是由设计、设备或操作人员引起的。
2.评估故障影响:对于每个故障模式,对其潜在影响进行评估。
这包括考虑故障对安全、质量、生产效率和客户满意度的影响。
3.评估故障发生的可能性:根据以往的经验和专业知识,评估每个故障模式发生的可能性。
这可以帮助判断哪些故障模式具有较高的风险,并设定优先级。
4.制定预防措施:根据故障模式和其潜在影响的优先级,制定相应的预防措施。
这可以包括加强培训、更改设计、改进工艺等。
5.执行预防措施并监控效果:实施预防措施并监控其效果。
如果预防措施有效,可以减少故障的发生和潜在影响。
FMEA分析可以应用于各个领域,例如制造业、医疗设备、航空航天、汽车工业等。
它可以帮助组织发现并解决设计或工艺中的潜在问题,从而提高产品安全性和质量水平。
通过在产品开发的早期阶段应用FMEA分析,组织可以避免在后期进行昂贵的修复工作。
1.方法改进:不断改进FMEA分析方法,使其更好地适用于特定行业和领域。
例如,开发新的工具和模型,以帮助自动化和标准化FMEA分析。
2.效果评估:评估FMEA分析对产品质量和生产效率的影响。
比较使用FMEA分析和未使用FMEA分析的组织,评估其在故障预防和风险管理方面的差异。
3.教育与培训:开发培训课程和教学材料,以帮助组织有效地使用FMEA分析。
培训可以涵盖FMEA分析的概念、方法和工具的使用。
4.案例研究:研究通过应用FMEA分析成功解决问题的实际案例。
这些案例可以揭示FMEA分析对质量改进和风险管理的实际效果。
FMEA在质量管理中的应用

FMEA 在质量管理中的应用摘要:在过去的一个世纪里,大规模的产业生产从繁荣过渡到衰退。
前者的生产管理模式不再有利。
如果产业企业想在产业上维持他们的主要地位,他们就必须革新。
为什么这么说呢,因为如果企业一直在做平时做的事情,那就只能得到通常能得到的东西。
激烈的竞争和危机感强的企业总是改变他们的面貌,促进变化的不确定性和风险。
风险管理分析的概念是针对经营风险尽可能地将风险控制在最小限度或最小化。
关键词:质量;预防措施;产品;方法;现状分析AbstractQuality scientists and reliability engineers have been through the operation of the enterprise system to find a comprehensive risk, in order to eliminate the risk, and finally found that the focus of risk control should be put on the prevention of all risks and defects.一、引言随着质量管理科学的逐步改进,质量管理的重点从后疗法到前预防逐渐变化。
预防可以事先带来各种优点:降低生产成本,降低产品的报废率,减少产品风险等。
但是,如何在每一个回合中分析失败模式和原因,以达到有效的预防效果?作为预防程序,PFMEA会给我们解决这个问题。
PFMEA(过程故障模式和影响分析)是1960年代NASA在开发航天飞机的过程中发明的预防程序。
为确保航天飞机的可靠性发挥了重要作用。
此后,pfmea广泛用于非军事领域,并通过持续改进成为有效的质量管理方法。
1.FMEA产生的背景2.1、FMEA的发展历史FMEA技术的应用非常快。
1950年代初期,美国首先将FMEA应用于战斗机操作系统的设计和分析。
1960年代中期,fmea技术在美国航空航天产业中被正式使用。
fmea使用方法

fmea使用方法一、FMEA是啥。
1.1 FMEA啊,就是失效模式与效应分析(Failure Mode and Effects Analysis)。
这可是个好东西呢,就像一个放大镜,能把潜在的问题找出来,防患于未然。
它不是什么高大上、让人摸不着头脑的玩意儿,简单来说,就是提前琢磨可能出岔子的地方,然后想办法解决。
1.2 这就好比你要出门旅行,你得提前想想路上可能遇到啥麻烦事,像车坏了、天气不好之类的。
FMEA在工程或者生产领域,就起着这样的作用。
二、FMEA的使用步骤。
2.1 第一步,得组建个团队。
这团队可不是乌合之众,得是各个方面的行家凑一块儿。
就像盖房子,你得有泥瓦匠、木工、电工这些个专业人士。
大家坐下来,八仙过海,各显神通,把自己懂的那一块可能出现的问题都给抖搂出来。
2.2 第二步,识别潜在的失效模式。
这就像是在鸡蛋里挑骨头,但这骨头不挑出来可不行。
比如说在汽车生产中,发动机启动不了、刹车失灵这些都是非常严重的失效模式。
这一步要把能想到的所有可能出问题的情况都列出来,一个都不能少,可不能做“马大哈”。
2.3 第三步,分析失效的后果。
这后果有轻有重,就像下象棋,一步走错,可能满盘皆输,也可能只是小损失。
比如在电子产品中,屏幕偶尔闪一下可能就是小问题,但要是整个系统崩溃了,那可就是大麻烦了。
要把这些后果都清清楚楚地写出来,让大家心里有数。
三、FMEA的好处。
3.1 首先呢,它能提高产品或者流程的可靠性。
这就好比给你的东西或者做事的方法上了一道保险。
有了FMEA,就像是给产品或者流程打了预防针,能避免很多不必要的麻烦。
就像俗话说的“未雨绸缪”,总比出了问题再去救火要强得多。
3.2 它能节省成本。
你想啊,如果产品到了用户手里才发现问题,那可就麻烦了。
召回啊、维修啊,这都是白花花的银子。
要是提前用FMEA把问题解决了,这钱不就省下来了嘛。
这就叫“吃不穷,穿不穷,算计不到就受穷”,在企业里也是这个理儿。
FMEA在实验室质量管理中的应用

质量管理FMEA在实验室质量管理中的应用■ 黄思嘉 张芳芳* 丁 豪(上海市食品药品包装材料测试所)摘 要:为持续改进质量管理,确保检验检测工作质量,在实验室质量管理中,运用失效模式和效益分析(failure mode and effects analysis,FMEA)进行风险管理。
本文基于FMEA的实验室质量管理方式,以人、机、料、法、环为分类方式,结合近6年内外部评审中所产生的不符合项、原因分析及纠正措施的具体示例进行评估分析。
通过将实验室风险评估后的风险等级结合实验室现有的5S管理体系,提出针对性的应对措施,以期能有效地控制风险,更好地开展实验室质量管理。
FMEA模型在实验室质量管理中的运用,可以清晰分析出实验室当前存在的风险,防止高风险质量问题的发生,有效促进5S 管理体系逐步开展,不断完善实验室质量管理。
关键词:FMEA,实验室,质量管理DOI编码:10.3969/j.issn.1002-5944.2024.07.030Application of FMEA in Quality Management of LaboratoriesHUANG Si-jia ZHANG Fang-fang* DING Hao(Shanghai Food and Drug Packaging Material Control Center)Abstract:To continuously promote quality management and ensure the quality of the inspection and testing work, failure mode and effects analysis (FMEA) is used to strengthen the quality management of laboratories. The paper is based on the FMEA laboratory quality management method, and conducts evaluation and analysis on the examples of non-conformity, cause analysis and corrective actions happened in the internal and external review in the past six years, which are classified by man, machine, material, method, environments. Based on the laboratory risk assessment results and the 5S System applied by laboratories, the paper proposes targeted measures to effectively control risks and better carry out the laboratory quality management. The application of FMEA in laboratory quality management can clearly find out the current risks and prevent high-risk quality problems, which effectively promotes the gradual application of the 5S System and continuously improves the quality management in the laboratory.Keywords: FMEA, laboratory, quality management0 引 言近年来,各检验检测实验室对质量管理体系中的风险管理越来越重视[1]。
FMEA在QC小组活动中的应用

FMEA在QC小组活动中的应用摘要:针对QC小组活动过程中如何正确运用QC工具迅速找出问题症结,借助于故障模式及影响分析法(FMEA法)开展了烟丝含水率批次间波动统计分析,准确获得了问题的症结。
不仅提高了QC小组质量,而且为FMEA法在QC小组活动中的应用提供了借鉴。
关键词:QC工具;症结;FMEA法;统计分析QC小组是指企业员工围绕企业经营战略、方针目标和现场存在的问题,以改进质量、降低消耗、提高素质和经济效益为目的组织起来的,运用质量管理理论和方法开展活动的小组[1]。
在企业全面质量管理实施的过程中,QC小组活动的开展起到十分重要的作用,通过QC小组活动的开展,企业不仅解决了实际生产过程中遇到的问题,同时提高了经济效益和员工队伍的素质。
根据“现场型”课题的活动程序,课题选定之后,QC小组成员需要对存在的问题进行剖析,以便进把握问题的严重程度,从而找出问题的症结。
找出症结的关键在于对数据进行科学的处理。
在数据处理过程中,正确应用工具不仅可以提高解决问题的效率,而且也会提高QC小组活动成果的水平,失效模式及影响分析(FMEA,Failure Mode andEffects Analysis)工具具有可操作性强、科学、便捷等特点,如何在QC小组活动中的应用FMEA法是值得探索的问题。
1FMEA 法分析流程过程失效模式与影响分析(FMEA)是通过分析和识别工艺生产或产品制造过程中可能出现的失效模式,以及这些失效模式发生后对产品质量和客户的影响,从而有效针对性地制造控制措施以有效减少工艺生产和产品制造过程中的风险[2]。
目前FMEA 技术在国内航空、机械、电子、医疗等领域均已成功应用[3-4],但在QC小组活动过程中并未多见。
在开展QC小组活动过程中应用FMEA方法实现症结的辨识,对于提高解决问题效率、提高风险辨识的能力具有重要作用。
FMEA作为一种系统化的方法,它采取团队讨论的形式,利用小组成员的经验和理论知识来挖掘系统中潜在的失效模式,评估失效模式的后果及严重程度,找出失效的症结,估计发生度,评估现有过程的控制措施,确定检测度,从而完成FMEA分析[5]。
- 1、下载文档前请自行甄别文档内容的完整性,平台不提供额外的编辑、内容补充、找答案等附加服务。
- 2、"仅部分预览"的文档,不可在线预览部分如存在完整性等问题,可反馈申请退款(可完整预览的文档不适用该条件!)。
- 3、如文档侵犯您的权益,请联系客服反馈,我们会尽快为您处理(人工客服工作时间:9:00-18:30)。
FMEA在QC小组活动中的应用
摘要:针对QC小组活动过程中如何正确运用QC工
具迅速找出问题症结,借助于故障模式及影响分析法(FMEA
法)开展了烟丝含水率批次间波动统计分析,准确获得了问题的症结。
不仅提高了QC小组质量,而且为FMEA法在QC
小组活动中的应用提供了借鉴。
关键词:QC工具;症结;FMEA法;统计分析
QC小组是指企业员工围绕企业经营战略、方针目标和现
场存在的问题,以改进质量、降低消耗、提高素质和经济效
益为目的组织起来的,运用质量管理理论和方法开展活动的
小组[1]。
在企业全面质量管理实施的过程中,QC小组活动
的开展起到十分重要的作用,通过QC小组活动的开展,企
业不仅解决了实际生产过程中遇到的问题,同时提高了经济
效益和员工队伍的素质。
根据“现场型”课题的活动程序,课题选定之后,QC
小组成员需要对存在的问题进行剖析,以便进把握问题
的严重程度,从而找出问题的症结。
找出症结的关键在于对
数据进行科学的处理。
在数据处理过程中,正确应用工具不
仅可以提高解决问题的效率,而且也会提高QC小组活动成
果的水平,失效模式及影响分析(FMEA,Failure Mode and
Effects Analysis)工具具有可操作性强、科学、便捷等特点,
如何在QC小组活动中的应用FMEA法是值得探索的问题。
1FMEA 法分析流程过程失效模式与影响分析(FMEA)是通过分析和识别工
艺生产或产品制造过程中可能出现的失效模式,以及这些失效模式发生后对产品质量和客户的影响,从而有效针对性地制造控制措施以有效减少工艺生产和产品制造过程中的风险[2]。
目前FMEA 技术在国内航空、机械、电子、医疗等领域均已成功应用[3-4],但在QC小组活动过程中并未多见。
在开展QC小组活动过程中应用FMEA方法实现症结的辨识,
对于提高解决问题效率、提高风险辨识的能力具有重要作用。
FMEA作为一种系统化的方法,它采取团队讨论的形式,
利用小组成员的经验和理论知识来挖掘系统中潜在的失效
模式,评估失效模式的后果及严重程度,找出失效的症结,
估计发生度,评估现有过程的控制措施,确定检测度,从而
完成FMEA分析[5]。
本文给出的具体FMEA分析流程图见图
1。
2应用案例
2.1定义失效模式烟叶是一种具有吸湿性的物质,其内部一般都含有
一定
数量的水分。
烟草产品的水分主要分为烟草产品的表面吸收的水分、毛细管吸附和凝结的水分以及烟草产品中所含的晶
体水化合物。
烟草产品的表面吸收的水分可通过在线水分仪检测快速获取,而毛细管吸附和凝结的水分以及烟草产品中所含的晶体水化合物则无法测量,且随着一定的空气状态下,会向细胞表面扩散或吸附一定的水分,统称为“烟草产品的内含水”。
产品的内含水的波动无法量化测量,只能通过生
产线施加水量和除去水量的分析去识别波动。
七匹狼 ( 16 支
纯香,厦门)的生产流程,如图 2 所示。
失效模式可以从生产流程的工艺环节中去查找。
通过多
次分析得到可能导致失效模式的工艺环节的量化指标如表所示。
2.2定义SOD 评分准则
2.2.1 严重度严重度S (Severity)分为10级。
在七匹狼(16支纯
香,厦门)的生产流程中对前后道工序的水分差值的严重程度进行分级、评估。
见表2。
2.2.2频度频度0( Occurrence)分为10级。
频度级别主要根据
Cpk
进行判定,见表3.
2.2.3不可探测度不可探测度D( Detectability )分为10 级。
不
可探测度
的级别划分是根据人工或在线检测对产品失效模式的检测,主要从无控制方式或控制完全失效、仅靠事后检测、事前预
防、针对失效模式的原因进行有效控制且失效模式不会发生
4 个方面划分级别。
见表4。
2.3根据SOD评分准则进行RPN打分
依据分级准则从严重度(S)、频度(O)、不易探测度(D)、
风险优先系数(RPN)等方面对七匹狼(16支纯香,厦门)
的工艺生产中可能出现的失效模式进行分析,见表5。
由图3的RPN打分表可以得出:CTD烘丝工序烘丝强度
的批次间波动和松散回潮工序出口片烟含水率的批次间波动的RPN值》
100 ,列为高风险项目。
通过FMEA法的使用,可以得出:松散回潮工序的出口片烟含水率批次间波动和
CTD烘丝工序的烘丝强度的批次间波动是影响加香出口烟丝
批次间水分波动的重要因素。
通过现状调查确定了松散回潮工序的出口片烟含水率
批次间波动和CTD烘丝工序的烘丝强度的批次间波动是影响加香出口烟丝批次间水分波动主要症结之一。
随后,根据活动程序针对前室温度波动大这一问题进行了原因分析,经过要因确认、对策实施等环节,使出口片烟含水率批次间波动值控制在预期范围内。
3结论
FMEA在QC小组现状调查阶段的成功运用,不仅方便、
准确地确定了松散回潮工序的出口片烟含水率批次间波动和CTD烘丝工序的烘丝强度的批次间波动是影响加香出口烟
丝批次间水分波动的重要因素,找出了问题的症结,而且还提升了QC 成果的水平。
参考文献
中国社会
[1]中国质量协会.QC小组基础教材[M].北京:
出版社,2004.
[2]李毅佳,余建星.基于FMEA和模糊理论的海底管道建
造期质量风险分析[J].中国安全科学学报,2012( 1):112-117.
[3]史宪铭,王华伟.基于贝叶斯网络的复杂系统FMEA
模型[J] .兵工自动化,2004,23(2)27-29.
[4]许苹等.FMEA在医疗风险管理中的应用以及局限性
[J].现代预防医学,2007,34(1):51-52.
[5]基于FMEA 和HAZOP 的综合分析方法及应用研究[J].
中国安全生产科学技术,2011 ,06.。