薄板坯连铸机低碳钢塞棒上涨原因探讨(炼钢生产技术会议))
板坯连铸机粘结漏钢的原因分析及预防 刘雷锋

板坯连铸机粘结漏钢的原因分析及预防刘雷锋摘要:随着连铸技术的发展和广泛应用,连铸坯的质量和品质受到了人们的广泛关注,提高连铸坯的质量成为连铸生产中重点关注的问题之一。
连铸过程开始广泛运用于有色金属行业,尤其是铜和铝。
连铸技术迅速发展起来。
本文对此进行了分析研究。
关键词:坯;连铸;连铸工艺连铸漏钢是个常见现象。
钢水在结晶器内形成坯壳,连铸坯出结晶器后,薄弱的坯壳抵抗不住钢水静压力,出现断裂而漏钢。
对于薄板坯连铸来说更易发生漏钢事故。
漏钢对连铸生产危害很大。
即影响了连铸车间的产量,又影响了连铸坯的质量,更危及操作者的安全。
因此,降低薄板坯连铸漏钢率是提高生产效率,提高产量,提高产品质量,降低成本的重要途径。
现对某厂自2008~2013年薄板坯漏钢率进行统计。
2008年漏钢率达0.56%;2009年漏钢率达0.19%;2010年漏钢率达0.19%;2011年漏钢率达0.19%;2012年漏钢率达0.15%;2013年漏钢率达0.07。
1 工艺流程某厂第一钢轧厂工艺流程为:鱼雷罐供应铁水/混铁炉供应铁水→铁水预处理→转炉炼钢→氩站→精炼→薄板坯连铸2 薄板坯漏钢类型某厂薄板坯连铸漏钢主要有:粘结漏钢、裂纹漏钢、卷渣漏钢、开浇漏钢、鼓肚漏钢五个类型。
3 薄板坯漏钢特征、原因及预防措施3.1 粘结漏钢粘结漏钢是指钢水直接与结晶器铜板接触形成粘结点,粘结点处坯壳与结晶器壁之间发生粘结,此处在结晶器振动和拉坯的双重作用下被撕裂,并向下和两侧扩展,形成倒“V”形破裂线,钢水补充后又形成新的粘结点,这一过程反复进行,粘结点随坯壳运动不断下移,此处坯壳较薄,出结晶器后,坯壳不能承受上部钢水的静压力,便会发生漏钢事故。
据统计,粘结漏钢发生率最高,高达50%以上。
(1)铸坯粘结漏钢后特征。
粘结漏钢后铸坯特征。
坯壳呈“V”字型或“倒三角”状,粘结点明显。
(2)粘结漏钢的原因:1)保护渣性能不好。
保护渣在结晶器铜板与凝固坯壳之间起润滑的效果。
薄板坯连铸连轧设备生产热轧薄板的缺陷分析与改进

薄板坯连铸连轧设备生产热轧薄板的缺陷分析与改进热轧薄板广泛应用于许多行业,包括建筑、汽车制造和航空航天等领域。
然而,在生产过程中,薄板坯连铸连轧设备生产热轧薄板时可能会出现一些缺陷,这些缺陷会对产品质量和性能造成影响。
因此,及时进行缺陷分析和改进是至关重要的。
首先,我们将对薄板坯连铸连轧设备生产热轧薄板的常见缺陷进行分析。
在生产过程中,以下几种常见缺陷可能会出现:1. 表面缺陷:这是最常见的缺陷之一,包括锈蚀、划痕、斑点和凹凸等。
这些缺陷可能是由于设备不良或操作不当导致的。
2. 内部缺陷:内部缺陷主要包括夹杂物、气泡和裂纹等。
夹杂物通常是由原材料中的杂质引起的,如硅、锰、钢水中的氧化物等。
气泡则是由于薄板坯连铸过程中,气体在坯料中的溶解度下降而引起的。
裂纹则主要是由于过高的轧制温度、轧制力过大或轧制参数设置不当等原因引起的。
3. 带杂质缺陷:这种缺陷通常是由于设备设备不良或操作不当导致的。
例如,如果轧机辊子表面不平整或有划痕,则会导致薄板表面出现糙痕。
其次,我们需要进行缺陷改进的工作。
以下是一些建议和方法:1. 优化设备和工艺参数:我们可以通过改进设备和调整工艺参数来减少缺陷的发生。
例如,定期检查和维修设备,确保其正常运行。
在设备运行过程中,根据产品要求和材料特性,适时调整轧制温度、轧制力和轧制速度等参数,以提高产品质量并减少缺陷的发生。
2. 加强原材料质量控制:原材料的质量对产品质量有着重要影响。
因此,我们应该加强原材料的质量控制,确保其符合要求。
例如,定期检测原材料中的杂质含量,采取相应措施减少杂质对产品的不良影响。
3. 强化操作培训和管理:员工的操作技能和工作态度对于产品质量的控制和缺陷改进至关重要。
因此,我们应该加强操作培训,提高员工的技能水平。
同时,加强对生产过程的管理,制定标准作业流程,确保操作规范和一致性。
4. 建立完善的质量管理体系:建立完善的质量管理体系是确保产品质量和缺陷改进的基础。
中国薄板坯连铸连轧技术的现状和发展

中国薄板坯连铸连轧技术的现状和发展中国薄板坯连铸连轧技术是指将熔化的金属经过连铸机连续铸造成坯料,然后通过连续轧制、切割等工艺过程,制成各种规格的薄板材料的生产技术。
目前,中国的薄板坯连铸连轧技术已经取得了较大的进步和发展。
主要体现在以下几个方面:
一、品种规格的增加
随着市场需求的不断增加,中国的薄板坯连铸连轧技术已经实现了从单一规格向多品种、小批量和高品质的发展。
目前,我国已经能够生产厚度为0.8mm以下、宽度在800mm以上的薄板产品,满足了市场对多种产品的需求。
二、技术水平的提高
随着技术的不断发展,中国的薄板坯连铸连轧技术逐步实现了数控化、自动化和智能化。
同时,新的轧制工艺和设备的应用,也使得产品的质量和生产效率得到了大幅提升。
三、环保意识的加强
在当前环保意识不断提高的背景下,中国的薄板坯连铸连轧技术也在不断推进环境保护措施。
例如,在生产过程中采用了新型的净化技术和设备,有效降低了环境污染和能源消耗。
未来,中国薄板坯连铸连轧技术还将继续发展和完善。
我们有理由相信,在技术革新和环保要求的推动下,中国的薄板坯连铸连轧技术将会更加先进、更加高效、更加环保、也更加适应市场需求。
- 1 -。
板坯拉速提高对铸坯质量的影响

表 5 保护渣现场试用结果
保 护 渣
1
拉速为 1 . 8 而I m 时 n
耗 量 / 兹 ・ m 一 2
>0. 3
表 面缺陷
尤
流人均匀性
好
技 术讲座 6v C 提高对结晶器液面起伏的影响 v C 提高时, 液面起伏加剧, 铸坯表面容易裹渣,
如果浸人式水口浸人深度不足, 将使裹渣加剧。薄
板坯连铸从浸人式水 口侧孔出来的向下流股的下倾 角应当大一些, 以便将钢流分散到结晶器深处。电 磁制动可使液面平稳和液面温度高。当液面起伏偏 离最佳值时, 可用电磁制动进行调节。
c 提高后, V 结晶器热面温度升高, 为了防止粘
结, 结晶器铜板厚度应当减薄, 见表 2 。
表Z v C 提高对结晶器铜板厚度的影响
板坯连铸机 伯利恒
<14 >1 . 4
热 流> 2 . S M W / 扩时, 将产生宽面 纵裂。 该厂在v c
提高时, 为了减少宽面纵裂, 使用了C a o / 5 1 仇 高和 含有2 政 的保护渣, 见表3 。 C o/ a 1 5 仇高和含有2 0 1 2 时, 可以提高保护渣的 结晶温度T c, e可以 T 使热流减少。
而 n [ 2 ] 。
高碳钢因 为容易粘结漏钢和容易内 裂, 所以v c
7V C 提高对板坯内部质量的影响 卢肯斯钢铁公司V c 提高后, 板坯内 部质量( 中心
裂纹、 三重点裂纹、 经向裂纹) 有所下降。该公司经过 研究得出: 降低中间罐钢水过热度和增加铸机下部组 件( n x 对 l u )的夹紧力对改进内部质量有好处。 e
表 4 保护渣的性能( 用于低碳铝镇静钢)
化学成分/ %
1 5 仇 月2 场F 伪 场 临( ) 凡O F 固定
[连铸机,板坯,技术]提高板坯连铸机中间包连浇炉数的技术优化与实践
![[连铸机,板坯,技术]提高板坯连铸机中间包连浇炉数的技术优化与实践](https://img.taocdn.com/s3/m/302929ea0912a21615792924.png)
提高板坯连铸机中间包连浇炉数的技术优化与实践摘要:分析认为,影响济钢板坯连铸机中间包连浇炉数的因素很多,除了与耐材质量、铸机设备有关外,还受到生产组织、市场因素、操作水平和生产工艺的影响。
通过对影响因素的系统分析和改进,使单中间包的连浇炉数较之前有所提高,降低了生产成本,取得了良好的效果。
关键词:连铸机;连浇炉数;使用寿命;生产组织目前,随着国内钢铁市场形势的急剧恶化,各大型钢铁企业均面临着急剧亏损的状态,企业转型以及不断降低生产成本的压力不可避免。
因此,优化板坯连铸机中间包使用寿命,成为济钢炼钢厂连铸工序降成本直接有效的关键措施之一。
1 板坯连铸机中间包使用现状2 影响板坯连铸机中间包连浇炉数的主要因素分析2.1 优化功能耐火材料质量中间包的功能耐火材料有塞棒、套管、浸入式水口,这3种耐火材料能否与中间包包衬寿命同步,直接影响中间包包龄的提高,合理的选用耐材对提高中间包连浇炉数起重要作用。
针对这3种耐火材料对中间包包龄的影响进行了针对性的研究与改进。
2.1.1 提高浸入式水口的使用寿命(1)增强浸入式水口渣线部位的侵蚀性,提高浸入式水口的寿命。
采用高纯度铝碳质材料的整体水口,渣线部分复合锆质,提高渣线部位抗热震性和抗侵蚀性。
优化浸入式水口形状,降低水口堵塞的几率。
(2)改善水口烘烤效果,防止开浇时水口炸裂。
原有水口烘烤装置为烘烤小车,后制作水口烘烤装置,具体见下图1,并对水口烘烤时间和煤气用量的控制,烘烤均匀,有效的防止了开浇或者换水口时的水口炸裂。
(3)优化保护渣成分,减少对水口的侵蚀。
积极与保护渣厂家协调优化保护渣的成分,使用含F和碱金属较低的保护渣,减少了水口C质的氧化和釉质的烧损。
4台板坯连铸机均采用中间包整体塞棒,且带有液位控制装置。
但在生产过程中,时常出现浇铸后期棒头不耐侵蚀、棒身渣线部位抗侵蚀效果差、以及棒头易脱落的现象。
针对以上问题,我们采取如下措施:(1)棒头由镁碳材质改为铝碳材质,保证了塞棒吹氩效果的同时减少了棒头的侵蚀;(2)棒身由铝碳质改为复合锆质材料,减少了棒身渣线部位侵蚀;(3)改进棒头与棒身的结合方式,杜绝了棒头脱落现象;(4)优化装塞棒操作,保证在热态情况下对中良好;(5)细化开浇前对塞棒的检查,观察塞棒本体及头部是否有脱落及裂纹。
薄板坯连铸连轧设备生产热轧薄板的轧辊磨损分析与改进
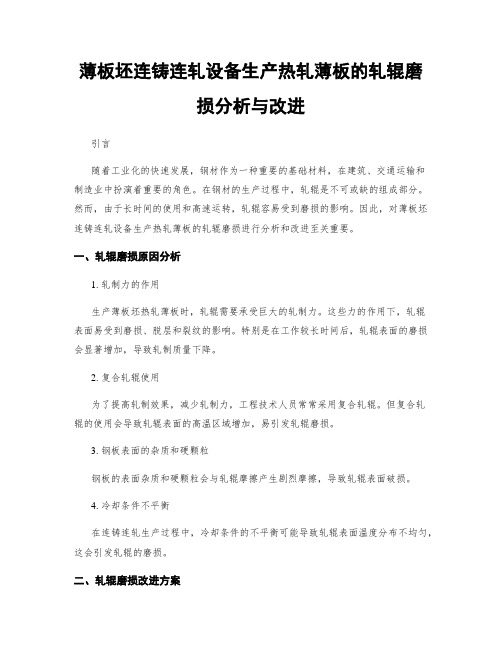
薄板坯连铸连轧设备生产热轧薄板的轧辊磨损分析与改进引言随着工业化的快速发展,钢材作为一种重要的基础材料,在建筑、交通运输和制造业中扮演着重要的角色。
在钢材的生产过程中,轧辊是不可或缺的组成部分。
然而,由于长时间的使用和高速运转,轧辊容易受到磨损的影响。
因此,对薄板坯连铸连轧设备生产热轧薄板的轧辊磨损进行分析和改进至关重要。
一、轧辊磨损原因分析1. 轧制力的作用生产薄板坯热轧薄板时,轧辊需要承受巨大的轧制力。
这些力的作用下,轧辊表面易受到磨损、脱层和裂纹的影响。
特别是在工作较长时间后,轧辊表面的磨损会显著增加,导致轧制质量下降。
2. 复合轧辊使用为了提高轧制效果,减少轧制力,工程技术人员常常采用复合轧辊。
但复合轧辊的使用会导致轧辊表面的高温区域增加,易引发轧辊磨损。
3. 钢板表面的杂质和硬颗粒钢板的表面杂质和硬颗粒会与轧辊摩擦产生剧烈摩擦,导致轧辊表面破损。
4. 冷却条件不平衡在连铸连轧生产过程中,冷却条件的不平衡可能导致轧辊表面温度分布不均匀,这会引发轧辊的磨损。
二、轧辊磨损改进方案1. 提高轧辊材料的性能选择高性能的轧辊材料可以有效提高轧辊的抗磨性能。
例如,采用高硬度、高耐热的合金材料可以减少轧辊表面的磨损。
2. 优化轧辊表面涂层技术采用涂层技术可以有效改善轧辊的抗磨性能。
常用的涂层材料包括液体纳米材料、尖晶石材料等。
这些涂层可以形成坚硬的保护层,降低轧辊与钢坯之间的摩擦和磨损。
3. 控制轧制力合理控制轧制力的大小,可以减少轧辊表面的磨损。
通过优化传动系统和辊系设计,减小轧制力的大小,对轧辊的寿命和性能有着显著的改善作用。
4. 加强轧辊的维护管理定期进行轧辊的维护保养是减少磨损的重要措施。
清洁轧辊表面的杂质和硬颗粒,控制轧辊的温度分布,防止轧辊因过热而受损。
5. 定期更换轧辊根据轧辊使用寿命和磨损情况,定期更换轧辊是降低轧辊磨损的有效方式。
及时更换轧辊可以避免轧辊磨损过度,影响生产质量和效率。
QC-减少中薄板连铸机开浇第一炉生产事故的工艺措施优化.ppt

2008 赵登报 年6月 郭卫国
《减少中包开浇第一炉生产事故的工艺措施优化》
三炼钢连铸车间QC成果
九、实施对策
依据制定的对策,结合实际生产操作要求,2007年5、6月份, 我们对以上四个方面的改进同时进行实施,具体改进过程如下。
★实施一:采用蓄热式烘烤器★
1、为了降低生产成本,中包烘烤由混合煤气置换成转炉煤气后,热值大大降低,中包温 度达不到要求,为了提高烘烤效果,把烘烤器都改为蓄热式烘烤器,提高了烘烤效果。
《减少中包开浇第一炉生产事故的工艺措施优化》
九、实施对策
★实施四:优化引锭封堵方式★
三炼钢连铸车间QC成果
角部抹硅胶
插入连接钢筋
封堵好的引锭
《减少中包开浇第一炉生产事故的工艺措施优化》
三炼钢连铸车间QC成果
十、效果检查
7月10号开始,进行了全面评估,结果统计如下
序号 调查项目
调查方法
调查结果
1 中包温度
《减少中包开浇第一炉生产事故的工艺措施优化》
九、实施对策
★实施四:优化引锭封堵方式★
三炼钢连铸车间QC成果
纸绳
塞纸绳
《减少中包开浇第一炉生产事故的工艺措施优化》
九、实施对策
★实施四:优化引锭封堵方式★
三炼钢连铸车间QC成果
2、多处增加垫板,规范铁粒铺设方式,防止开浇漏钢和粘引锭头:在浸入 式水口的正中央铺设大垫板,在凹入的燕尾槽斜面处各铺设一个中垫板。然 后在引锭的表面铺设铁粒,铁粒的厚度大约为20mm,保持铁粒铺设均匀。
《减少中包开浇第一炉生产事故的工艺措施优化》
三炼钢连铸车间QC成果
四、制定目标
通过分析事故发生的原因,随着职工操作技能水平的提高和工艺 参数的优化,本着“自我加压、争创一流”的精神,我们设定这 次活动的目标为
《改善连铸板坯缺陷的轧制工艺》范文

《改善连铸板坯缺陷的轧制工艺》篇一一、引言随着现代工业的快速发展,钢铁行业作为国民经济的重要支柱,其产品质量和生产效率的提升显得尤为重要。
连铸板坯作为钢铁生产中的重要环节,其质量直接影响到后续轧制工艺的效率和产品质量。
因此,如何有效改善连铸板坯的缺陷,优化轧制工艺,成为了业界关注的焦点。
本文旨在探讨连铸板坯的常见缺陷及原因,并分析轧制工艺的改进措施,以提高钢铁产品的质量和生产效率。
二、连铸板坯常见缺陷及原因分析1. 中心裂纹:中心裂纹是连铸板坯的主要缺陷之一,其形成原因主要是板坯凝固过程中的温度梯度和热应力过大。
此外,铸坯的化学成分、夹杂物、铸机振动等因素也会对中心裂纹的产生造成影响。
2. 表面裂纹:表面裂纹主要出现在板坯的表面,其形成原因包括钢水质量、结晶器振动、二次冷却制度等因素。
此外,钢中合金元素和夹杂物的含量也会对表面裂纹的产生造成影响。
3. 夹渣和夹杂物:夹渣和夹杂物主要来源于钢水的精炼过程和浇注过程中的夹杂物。
此外,铸模的质量、涂料的性能以及连铸机的维护保养也会影响夹渣和夹杂物的产生。
三、轧制工艺的改进措施针对上述连铸板坯的常见缺陷,轧制工艺的改进措施主要包括以下几个方面:1. 优化轧制参数:通过合理设定轧制温度、轧制速度、压下量等参数,使轧制过程更加稳定,减少轧制过程中的变形和裂纹等缺陷的产生。
2. 调整轧辊质量:选用高质量的轧辊,提高轧辊的硬度和耐磨性,减少轧制过程中的磨损和振动,从而降低板坯的表面裂纹和内部缺陷。
3. 强化轧前准备:在轧制前对连铸板坯进行充分的预热和除鳞处理,以去除表面的夹杂物和氧化皮,提高板坯的表面质量。
4. 优化冷却制度:根据板坯的化学成分、尺寸和轧制要求,制定合理的冷却制度,控制板坯的冷却速度和温度分布,以减少中心裂纹和表面裂纹的产生。
5. 引入无损检测技术:在轧制过程中引入无损检测技术,如超声波检测、X射线检测等,对板坯进行实时监测,及时发现并处理缺陷,提高产品的良品率。
薄板坯连铸连轧设备生产热轧薄板的质量损失与损坏分析
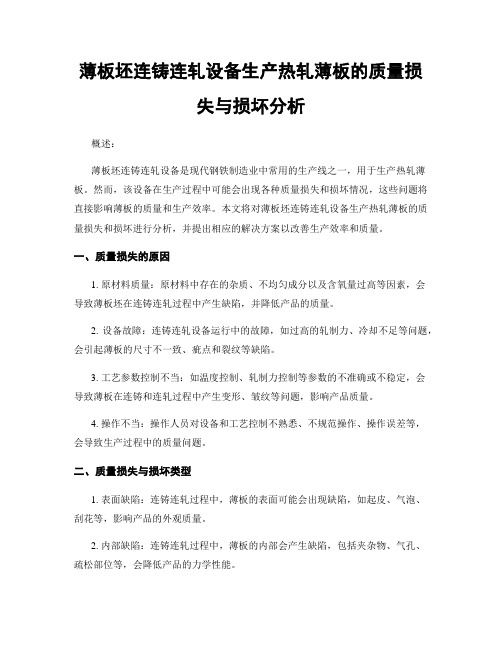
薄板坯连铸连轧设备生产热轧薄板的质量损失与损坏分析概述:薄板坯连铸连轧设备是现代钢铁制造业中常用的生产线之一,用于生产热轧薄板。
然而,该设备在生产过程中可能会出现各种质量损失和损坏情况,这些问题将直接影响薄板的质量和生产效率。
本文将对薄板坯连铸连轧设备生产热轧薄板的质量损失和损坏进行分析,并提出相应的解决方案以改善生产效率和质量。
一、质量损失的原因1. 原材料质量:原材料中存在的杂质、不均匀成分以及含氧量过高等因素,会导致薄板坯在连铸连轧过程中产生缺陷,并降低产品的质量。
2. 设备故障:连铸连轧设备运行中的故障,如过高的轧制力、冷却不足等问题,会引起薄板的尺寸不一致、疵点和裂纹等缺陷。
3. 工艺参数控制不当:如温度控制、轧制力控制等参数的不准确或不稳定,会导致薄板在连铸和连轧过程中产生变形、皱纹等问题,影响产品质量。
4. 操作不当:操作人员对设备和工艺控制不熟悉、不规范操作、操作误差等,会导致生产过程中的质量问题。
二、质量损失与损坏类型1. 表面缺陷:连铸连轧过程中,薄板的表面可能会出现缺陷,如起皮、气泡、刮花等,影响产品的外观质量。
2. 内部缺陷:连铸连轧过程中,薄板的内部会产生缺陷,包括夹杂物、气孔、疏松部位等,会降低产品的力学性能。
3. 宽厚不均:薄板的宽厚不均会导致产品尺寸偏差,甚至无法满足客户的要求。
4. 裂纹:连铸连轧过程中,薄板可能会出现裂纹,降低产品的强度和延展性能。
三、解决方案1. 严格控制原材料质量:了解原材料的成分、杂质含量和氧含量等指标,并加强原材料的筛选和质量检测,确保原材料的稳定性和质量。
2. 定期检查和维护设备:建立设备维护计划,定期对连铸连轧设备进行检查和维护,及时发现故障并进行修复,保证设备的正常运行。
3. 优化工艺参数:通过严格控制温度、轧制力等工艺参数,并应用先进的自动控制技术,确保产品的质量稳定。
4. 加强操作培训和规范化操作:为操作人员提供必要的培训,让他们掌握设备和工艺的操作要点,并制定操作规程,确保操作规范和准确。
板坯连铸低碳铝镇静钢中间包水口堵塞分析及其预防措施

板坯连铸低碳铝镇静钢中间包水口堵塞分析及其预防措施摘要:对攀钢炼钢厂板坯铸机浇铸低碳铝镇静钢过程中出现的中间包水口堵塞进行分析,在实施一系列工艺控制和预防措施后连铸生产逐步顺行,技术经济指标显著改善。
关键词:板坯连铸低碳铝镇静钢水口堵塞1 前言低碳铝镇静钢由于具有冲压性能良好和可以冷态成型的特性,因此成为冷轧板材的必备原料。
攀钢炼钢厂从2003年5月开始试制低碳铝镇静钢板坯,钢种要求C≤O.08%。
Als为0.020~0.080%,低碳易造成钢水过氧化,而较高的Als又很容易导致连铸中间包结水口。
一年多来的试制生产表明,最大的难题是中包水口堵塞使铸机提前停浇。
为此,钢厂在板坯铸机上采取了一系列工艺控制和预防措施,使低碳铝镇静钢的浇注工艺逐步顺行,技术经济指标明显改善。
2 中包水口堵塞原因分析2.1 水口堵塞物来源通过对水口堵塞物的检测和分析。
确定中包钢流通道堵塞原因主要是由于高熔点的化合物A1203(熔点2050℃)、CaS(熔点2450℃)或A1203·MgO等粘附在水口内壁上造成。
对堵塞沉积物作化学分析,成份见表1。
表1 堵塞沉积物化学成分由表1可见,堵塞沉积物的主要成分是A1203,它的来源主要有3个方面:(1)低碳铝镇静钢,在冶炼过程中采用两步脱氧法脱氧,用铝锰铁和铝铁作为脱氧合金,其中的铝将由脱氧反应(1)、(2)形成A1203。
2[Al]+3[0]=( A1203) (1)(Fe203)+2[A1]=( A1203)+2[Fe] (2)(2)大包及中间包水口为A1203-C质水口,在高温下,水口中的Si02被C还原为SiO及CO。
当SiO和CO 接触到钢液时,增加了水口内壁氧的活度,使钢液中的溶解铝被氧化,反应式为(3)、(4)、(5),总反应为(6):(Si02)+(C)={SiO}+{CO} (3)3SiO+2[A1]=( A1203)+3[Si] (4)3C0+2[A1]=(A1203)+3[C] (5)总反应为:3(Si02)+3(C)+4[A1]=2(A1203)+3[Si]+[C] (6)(3)水口密封性不够,钢液二次氧化发生(7)式反应,产生A1203:302+4[A1]=2(A1203) (7)2.2 中包水口结构及堵塞过程板坯连铸机中包水口从上到下由三部分组成:与塞棒配合可实现控流和防堵的透气上水口:由三块滑板组成的可实现自动控流的VSVC71SE滑板机构;可快换的浸入式下水口。
薄板坯连铸机低碳钢塞棒上涨原因探讨(炼钢生产技术会议))

2010年炼钢-连铸生产技术会议薄板坯连铸机低碳钢塞棒上涨原因探讨郑伟栋黄文杰唐志军郝强(河北钢铁集团邯钢公司河北邯郸 056015)摘要:结合邯钢生产实践,对CSP连铸机低碳钢塞棒上涨原因进行了分析并提出了预防措施,有效减少了事故停浇次数。
关键词:CSP,低碳钢,塞棒上涨Discussion and Analysis for Stopping Rising onLow Carbon Steel of Thin Slab CasterZHENG Wei-dong HUANG Wen-jie TANG Zhi-jun HAO Qiang(Hebei Iron & Steel Group HanGang Company, Handan, Hebei, 056015)Abstract: Through the causes analysis put forward prevent measures for stopping rising on low carbon steel of Handan CSP caster. The accident can be reduced effectively.Key Words: CSP,low carbon steel,stopping rising1 前言邯钢CSP薄板坯连铸机主要生产低碳钢、SS400、Q345A/B等铝镇静钢种,其中低碳钢占总产量的60%以上,低碳钢主要为冷轧备料。
在CSP连铸机生产低碳钢过程中,多次出现塞棒上涨事故停浇,甚至开浇不成功,对正常生产组织造成了很大影响,给公司造成了巨大的经济损失。
本文结合邯钢生产实践,通过大量实际生产数据,对CSP薄板坯连铸机生产低碳钢塞棒上涨原因进行了分析,并提出了预防措施,目前塞棒上涨事故停浇已得到有效控制,为公司生产稳定顺行创造了良好条件。
2 薄板坯低碳钢塞棒上涨的机理邯钢CSP薄板坯连铸机通过塞棒机构控制塞棒的开度,实现结晶器液位控制系统稳定地控制钢水从中包到结晶器中,当液位控制系统检测到结晶器中的钢水液位后,将实际值和设定值进行比较,如果实际液位与设定液位有偏差,控制系统将自动进行补偿调节:当结晶器钢水液位高于设定值,塞棒将下压减小开度;当结晶器钢水液位低于设定值,塞棒将上抬增加开度。
湛江炼钢2150mm连铸超低碳钢液面波动的改善

湛江炼钢 2150mm连铸超低碳钢液面波动的改善摘要:介绍了湛江炼钢2150mm板坯连铸,从投产到2019年超低碳钢液面波动的改善情况,主要从控流系统的改造、钢水纯净度的提高、不同耐材透气型式的组合和连铸过热度、通钢量等工艺参数的范围制定,到人员操作技能水平的提高五个方面进行了总结。
通过采取以上措施,2150mm板坯连铸超低碳钢的液面波动合格率得到显著改善。
关键词:连铸;超低碳;液面波动湛江炼钢一期共建设两台2150mm连铸机,于2015年9月28日投产;投产后5个月,即开始生产超低碳钢(超低碳钢绝大多数都是汽车板)。
超低碳钢由于碳低氧高的特性,且采用铝脱氧,钢水中不可避免残留一些Al2O3,在浇注过程中粘附在水口或塞棒表面,导致结晶器液面波动增大[1];而湛江2150mm连铸机由于生产超低碳汽车板时需采用结晶器电磁搅拌,更加剧了液面波动[2]。
而连铸过程中要求将结晶器液面波动控制在一定范围内( 一般为±5 mm),液面波动过大将会影响结晶器保护渣的三层结构,破坏其润滑和传热平衡,导致铸坯表面产生缺陷;同时也会增加结晶器钢水的卷渣风险,致使铸坯内夹杂物含量超标,严重影响铸坯和最终产品的质量,甚至会造成铸坯夹渣漏钢的恶性生产事故[3,4]。
湛江2150连铸超低碳钢经过长期生产实践统计发现,随着液面波动增大,热轧夹渣临时封锁率随之上升,液面波动10mm时的热轧夹渣临时封锁率比液面波动6mm时高40%,是液面波动3mm时的2倍。
超低碳汽车板,由于轧制厚度薄,在用户端冲压时变形量大减薄率高,对表面和内部质量要求较高。
为减小夹渣概率,减少用户端发生质量问题次数,对液面波动超过10mm的板坯,一般需要进行机清或手清处理,严重的要进行改钢降级、甚至报废,影响连铸收得率、热装热送率和合同完成率[5,6]。
因此不断提高超低碳钢水的纯净度和液面波动合格率,生产出无缺陷板坯,是湛江炼钢厂坚持不懈追求的目标。
钢材原材料上涨调研报告

钢材原材料上涨调研报告钢材原材料上涨调研报告报告摘要:近年来,钢材原材料价格持续上涨,给钢铁行业带来了巨大的影响。
本报告通过调研和数据分析,总结了导致钢材原材料上涨的主要原因,同时分析了这种趋势对钢铁行业的影响和应对措施。
一、引言钢材是现代社会重要的基础材料,广泛应用于建筑、机械制造、汽车制造等领域。
钢材原材料价格的上涨对钢铁企业和终端消费者的经济运行产生了深远的影响。
因此,研究钢材原材料价格上涨的原因及其应对策略具有重要的理论和实践意义。
二、主要原因分析1. 原材料供应不足:对于钢铁行业来说,铁矿石和焦炭是主要的原材料,供应不足导致价格上涨。
近年来,原材料供应紧张的主要原因包括矿山停产、政策调控和环保限产等。
2. 原材料价格上涨:全球原材料价格的上涨是导致钢材原材料价格上涨的另一个重要因素。
国际市场价格的上涨会直接传导至国内市场,带动国内价格上涨。
3. 运输成本增加:原材料的运输成本也对钢材原材料价格上涨起到一定的推动作用。
油价上涨、运输费用增加等因素都对运输成本形成一定的压力,这部分成本会转嫁到钢材原材料价格上。
三、对钢铁行业的影响1. 成本上升:钢材原材料价格上涨导致钢铁企业的生产成本上升,进而影响到企业的盈利能力。
特别是中小型钢铁企业在面对原材料价格上涨时更为薄弱。
2. 全球竞争力下降:由于原材料价格上涨,中国的钢铁企业的成本优势受到削弱,进一步降低了企业的国际竞争力。
3. 终端消费者受压:钢材原材料价格的上涨会进一步推高钢铁产品的价格,给终端消费者带来经济压力。
特别是建筑业、汽车制造业等依赖钢材的行业将面临较大的挑战。
四、应对措施1. 多元化采购:钢铁企业应该建立多元化原材料采购渠道,降低对单一原材料的依赖程度,减少供应链风险。
2. 提高自主创新能力:通过技术创新和工艺改进,降低生产成本,提高核心竞争力,从而缓解原材料价格上涨对企业利润的冲击。
3. 国际合作:加强与国际市场的合作与对话,寻求资源共享和合作发展,缓解原材料供应不足的问题。
连铸参数对低碳钢圆坯凝固组织形态的影响

连铸参数对低碳钢圆坯凝固组织形态的影响
连铸参数对低碳钢圆坯凝固组织形态的影响是一个重要的研究课题。
凝固组织形态的构造决定了圆坯的性能及加工表现,而连铸参数则是影响凝固组织构造的重要因素之一。
本文将从两个方面讨论连铸参数对低碳钢圆坯凝固组织形态的影响。
首先,连铸参数对凝固组织构造有很重要的作用。
凝固组织构造是由凝固温度、时间、温升率、冷却速率、连铸界面状态等影响的,其中连铸参数如温度、时间、温升速率等是影响凝固组织构造的最重要的参数。
正确的温度和温升速率将有助于凝固时间的延长,并促进·细晶粒的生成;如果连铸参数设置不当,将导致晚凝固细晶粒的形成,影响圆坯的性能。
其次,连铸参数也会影响圆坯内部组织的合金元素分布。
当添加合金元素时,凝固组织受到合金元素的影响也会改变,这可能会导致细晶粒的不均匀分布和完整性的降低,从而对圆坯的加工性能产生影响。
此外,连铸参数的变化可能会影响合金元素在冷却过程中的移动,从而使它们在凝固体系中均匀分布。
总之,连铸参数对低碳钢圆坯凝固组织形态是不可忽视的影响因素,正确设置连铸参数有助于合理控制凝固温度和时间,有效促进细晶粒生成,确保凝固体系中合金元素的均匀分布,从而有效提高低碳钢圆坯的性能及加工表现。
因此,在设计和改进连铸钢圆坯的凝固组织形态时,应根据不同钢的特性采用特定的连铸参数,以保证该钢的可靠性和性能。
板坯连铸机“滞坯”原因分析与控制
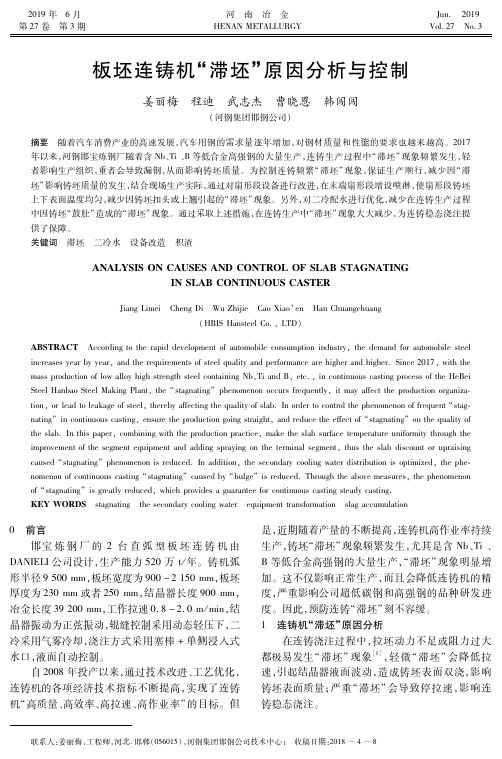
0 前言 邯宝 炼 钢 厂 的 2台 直 弧 型 板 坯 连 铸 机 由
DANIELI公司设计,生产能力 520万 t/年。铸机弧 形半径 9500mm,板坯宽度为 900~2150mm,板坯 厚度为 230mm或者 250mm,结晶器长度 900mm, 冶金长度 39200mm,工作拉速 0.8~2.0m/min,结 晶器振动为正弦振动,辊缝控制采用动态轻压下,二 冷采用气雾冷却,浇注方式采用塞棒 +单侧浸入式 水口,液面自动控制。
2019年第 3期 河 南 冶 金 · 4 1·
1.1 二冷水配水工艺制度对“滞坯”的影响
0.47L/kg),对其冷坯下线铸坯宽面鼓肚情况进行
在连铸浇注过程中,拉坯动力不足或阻力过大 都极易发生“滞坯”现象[1],轻微 “滞坯”会降低拉 速,引起结晶器液面波动,造成铸坯表面双浇,影响 铸坯表面质 量;严 重 “滞 坯 ”会 导 致 停 拉 速,影 响 连 铸稳态浇注。
联系人:姜丽梅,工程师,河北.邯郸(056015),河钢集团邯钢公司技术中心; 收稿日期:2018 4 8
自 2008年投产以来,通过技术改进、工艺优化, 连铸机的各项经济技术指标不断提高,实现了连铸 机“高质量、高效率、高拉速、高作业率”的目标。但
是,近期随着产量的不断提高,连铸机高作业率持续 生产,铸坯“滞坯”现象频繁发生,尤其是含 Nb、Ti、 B等低合金高强钢的大量生产,“滞坯”现象明显增 加。这不仅影响正常生产,而且会降低连铸机的精 度,严重影响公司超低碳钢和高强钢的品种研发进 度。因此,预防连铸“滞坯”刻不容缓。 1 连铸机“滞坯”原因分析
ANALYSISON CAUSESAND CONTROLOFSLABSTAGNATING IN SLABCONTINUOUSCASTER
中国薄板坯连铸连轧技术的现状和发展

中国薄板坯连铸连轧技术的现状和发展
薄板坯连铸连轧技术是近年来国内钢铁工业快速发展的一项关键技术,该技术是在连铸技术和轧制技术的基础上发展而来。
目前,国内主要的薄板坯连铸连轧工艺有双流炉连铸双机、连铸机联轧机等几种,各钢厂也积极推广和应用该技术。
该技术的特点是高效、低耗、高质、低成本。
其生产效率比传统热轧技术高出一倍以上,并且产品质量稳定可靠,成品率高。
另外,该技术实现了原始资料的高效利用,降低了资源消耗和耗能量,使钢铁生产更加环保。
目前,国内钢铁行业正在不断探索和推广该技术。
我国大型钢铁企业,在不断优化工艺流程,提高品质的同时,还在推广绿色环保型钢材,以适应市场的不断变化和发展。
随着技术的不断进步和应用,薄板坯连铸连轧技术在国内的应用前景将会更加广阔,并为钢铁行业的可持续发展注入新的动力。
钢铁冶炼中的连铸加速技术

钢铁冶炼中的连铸加速技术钢铁冶炼是现代工业中至关重要的一环,而连铸加速技术则是其中一项关键的创新。
通过连铸加速技术,钢铁生产过程中的效率得以大幅提升,同时还能够改善产品的质量和减少资源的浪费。
本文将深入探讨钢铁冶炼中的连铸加速技术,分析其原理、应用以及对钢铁行业的影响。
连铸加速技术的基本原理是在钢铁冶炼过程中,通过连续铸造的方式将熔化的金属直接浇铸成坯料。
相较于传统的铸造工艺,连铸加速技术不需要等待整个熔化金属液体浇铸完成后才进行下一次生产,而是可以连续不断地进行,从而大大提高了生产效率。
这一技术的关键在于高效的连续铸造设备和精密的控制系统,能够确保坯料的质量和尺寸稳定性。
在连铸加速技术的应用方面,其在钢铁行业中已经得到了广泛的采用。
首先,它可以大幅缩短生产周期,提高了钢铁生产的效率。
传统的铸造工艺需要等待每一次浇铸完成后进行冷却固化,而连铸加速技术可以实现连续不断的生产,减少了等待时间,从而缩短了整个生产周期。
其次,连铸加速技术还可以改善产品的质量。
由于连铸过程中金属液体的流动更加均匀稳定,因此可以减少气孔和夹杂等缺陷的产生,提高了产品的密度和均匀性。
此外,连铸加速技术还可以减少资源的浪费。
相较于传统的铸造工艺,它需要的能源和原材料更少,因此具有更高的资源利用率。
钢铁行业的发展离不开技术的创新,而连铸加速技术的出现无疑为该行业带来了巨大的变革。
首先,它提高了钢铁生产的效率和产能,使得钢铁企业能够更好地满足市场需求。
随着全球经济的发展和工业化进程的加速,对钢铁产品的需求不断增长,而连铸加速技术的应用可以帮助钢铁企业更好地应对市场变化,保持竞争优势。
其次,连铸加速技术的推广应用还有助于减少环境污染。
传统的钢铁生产工艺往往会产生大量的废气和废水,对环境造成严重的污染,而连铸加速技术的应用可以减少这些污染物的排放,降低了钢铁行业对环境的负面影响,符合可持续发展的要求。
然而,值得注意的是,连铸加速技术的推广应用还面临着一些挑战和障碍。
张尹

连铸塞棒上涨原因分析及应对措施自210转炉厂投产以来,我厂的生产逐渐走向稳定,但在浇注低碳钢时,时常发生塞棒上涨和中间包水口堵塞的现象,尤其是在每浇次前两炉,上涨机率达到90%,严重时造成生产中断,使生产非常的被动。
根据连铸生产实际情况,试对塞棒上涨的原因以及应采取的预防措施进行分析。
一.塞棒上涨的现象在塞棒上涨前期,开口度缓慢增大,大约维持在10~15分钟;后期上涨速度增快,3~5分钟塞棒开口度达到最大值,这时钢流变小不能及时的填充到结晶器,液位开始急剧下降,当液位超过检测的范围就会被迫停机,严重的影响了生产的稳定。
二.塞棒上涨原因分析1.首先是中间包的烘烤。
我们现在中间包的烘烤由于压风不足和盖板变形,烘烤臂压不紧致使火焰都冒了出来,大部分都是烤在盖板和烤包臂上,影响中间包的烘烤效果。
如果大火烘烤时间过长,中间包耐材强度降低;耐材表面的防氧化涂层被氧化疏松。
因此在开浇第一炉就有很多的杂质和脱落的耐材与钢水混和,凝聚在塞棒的周围,促使塞棒上涨和水口的堵塞。
2.钢水质量差。
现在转炉下渣和钢水的过氧化增加了精炼脱氧难度,钢水中活度[O]含量过高,势必增加Al2O3夹杂物,堵塞中间包水口。
Ca-Al比控制不合理。
冶炼周期达不到要求。
3.保护浇注不够。
钢水上台后停留时间长,大包长水口氩封流量控制不合理。
在中间包的覆盖不到位,钢水裸露导致钢水被二次氧化,氧化夹杂物增多;致使开浇塞棒上涨。
三.塞棒上涨预防措施1.针对塞棒上涨和水口堵塞这一严重的问题,我们连铸工烘烤中间包总的要求是要在开浇前1-2h内,快速烘烤到1000-1100℃为好,这样可以节省能源,也便于使用。
在烤大火的时候,尽量把压风开到最大,煤气只能根据火焰大小调节,不是开的越大越好。
确保中包底部也能得到有效的烘烤。
但往往由于烘烤时间不够或太长,操作人员就要根据实际情况开浇,当钢水在中间包温度偏低或中包有异常时,可以实现低位开浇,适当提前到15T左右开浇,起步时间比平时快10S左右,防止钢水在中间包里结冷钢。
本钢薄板坯连铸连轧生产线卡钢_堆钢事故原因分析

2008年第5期本钢技术13本钢薄板坯连铸连轧生产线卡钢、堆钢事故原因分析李毅伟(本钢技术中心,辽宁 本溪 117000)摘 要:针对本钢薄板坯连铸连轧生产线发生的卡钢、堆钢事故进行现场跟踪和取样分析,找出引起卡钢和堆钢事故的主要原因,通过加强设备维护、提高铸坯质量和优化生产工艺来预防卡钢事故的发生,减少由于卡钢和堆钢事故造成的经济损失。
关键词:卡钢;堆钢;铸坯缺陷中图分类号:TG335.5文献标识码:BAnalysis on the Reason for the Hot Rolled Strip Blocked and Piled up ofThin Slab Caster and Hot Mill of BX STEELLI Yiwei(Technology Center,BX STEEL,Benxi Liaoning 117000)Abstract: Analysis on the hot rolled strip blocked and piled up of Thin Slab Caster and Hot Mill of BXSTEEL, find the main reason for caused strip blocked and piled up.Through reinforce maintain of theequipment , improve the quality of slab and optimize product process , prevent the happening of stripblocked and piled up, reduce the economy loss .Keywords: strip blocked;strip piled up;defect of slab1 概述本钢薄板坯连铸连轧生产线于2005年4月投入生产,在投入生产初期,由于生产工艺参数调试、连铸坯质量缺陷、机械或电器故障等原因引起的卡钢、堆钢事故经常出现,每次事故的经济损失都在几万元以上,多时可达10几万元,最多时一个月经济损失近百万元。
板坯连铸机中间包塞棒断裂问题分析与改进措施
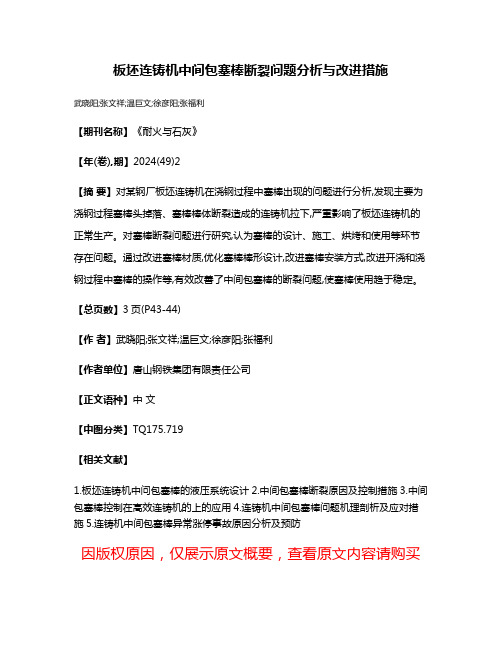
板坯连铸机中间包塞棒断裂问题分析与改进措施
武晓阳;张文祥;温巨文;徐彦阳;张福利
【期刊名称】《耐火与石灰》
【年(卷),期】2024(49)2
【摘要】对某钢厂板坯连铸机在浇钢过程中塞棒出现的问题进行分析,发现主要为浇钢过程塞棒头掉落、塞棒棒体断裂造成的连铸机拉下,严重影响了板坯连铸机的正常生产。
对塞棒断裂问题进行研究,认为塞棒的设计、施工、烘烤和使用等环节存在问题。
通过改进塞棒材质,优化塞棒棒形设计,改进塞棒安装方式,改进开浇和浇钢过程中塞棒的操作等,有效改善了中间包塞棒的断裂问题,使塞棒使用趋于稳定。
【总页数】3页(P43-44)
【作者】武晓阳;张文祥;温巨文;徐彦阳;张福利
【作者单位】唐山钢铁集团有限责任公司
【正文语种】中文
【中图分类】TQ175.719
【相关文献】
1.板坯连铸机中问包塞棒的液压系统设计
2.中间包塞棒断裂原因及控制措施
3.中间包塞棒控制在高效连铸机的上的应用
4.连铸机中间包塞棒问题机理剖析及应对措施
5.连铸机中间包塞棒异常涨停事故原因分析及预防
因版权原因,仅展示原文概要,查看原文内容请购买。
- 1、下载文档前请自行甄别文档内容的完整性,平台不提供额外的编辑、内容补充、找答案等附加服务。
- 2、"仅部分预览"的文档,不可在线预览部分如存在完整性等问题,可反馈申请退款(可完整预览的文档不适用该条件!)。
- 3、如文档侵犯您的权益,请联系客服反馈,我们会尽快为您处理(人工客服工作时间:9:00-18:30)。
2010年炼钢-连铸生产技术会议
薄板坯连铸机低碳钢塞棒上涨原因探讨
郑伟栋黄文杰唐志军郝强
(河北钢铁集团邯钢公司河北邯郸 056015)
摘要:结合邯钢生产实践,对CSP连铸机低碳钢塞棒上涨原因进行了分析并提出了预防措施,有效减少了事故停浇次数。
关键词:CSP,低碳钢,塞棒上涨
Discussion and Analysis for Stopping Rising on
Low Carbon Steel of Thin Slab Caster
ZHENG Wei-dong HUANG Wen-jie TANG Zhi-jun HAO Qiang
(Hebei Iron & Steel Group HanGang Company, Handan, Hebei, 056015)
Abstract: Through the causes analysis put forward prevent measures for stopping rising on low carbon steel of Handan CSP caster. The accident can be reduced effectively.
Key Words: CSP,low carbon steel,stopping rising
1 前言
邯钢CSP薄板坯连铸机主要生产低碳钢、SS400、Q345A/B等铝镇静钢种,其中低碳钢占总产量的60%以上,低碳钢主要为冷轧备料。
在CSP连铸机生产低碳钢过程中,多次出现塞棒上涨事故停浇,甚至开浇不成功,对正常生产组织造成了很大影响,给公司造成了巨大的经济损失。
本文结合邯钢生产实践,通过大量实际生产数据,对CSP薄板坯连铸机生产低碳钢塞棒上涨原因进行了分析,并提出了预防措施,目前塞棒上涨事故停浇已得到有效控制,为公司生产稳定顺行创造了良好条件。
2 薄板坯低碳钢塞棒上涨的机理
邯钢CSP薄板坯连铸机通过塞棒机构控制塞棒的开度,实现结晶器液位控制系统稳定地控制钢水从中包到结晶器中,当液位控制系统检测到结晶器中的钢水液位后,将实际值和设定值进行比较,如果实际液位与设定液位有偏差,控制系统将自动进行补偿调节:当结晶器钢水液位高于设定值,塞棒将下压减小开度;当结晶器钢水液位低于设定值,塞棒将上抬增加开度。
造成塞棒上涨即塞棒持续上抬的直接原因是流入结晶器内的钢水逐渐减少,为满足结晶器钢水液位要求,塞棒逐步上涨。
造成流入结晶器内的钢水逐渐减少的根本原因是高熔点夹杂物逐步附着在侵入式水口下部内壁(一侧或两侧)、水口上部碗部区域,部分附着物被钢水冲刷掉进入结晶器,导致结晶器液面控制曲线在相应点剧烈波动,随着夹杂物的越积越多,塞棒逐步上涨。
3 CSP低碳钢塞棒上涨的影响因素
3.1钢水钙含量及钙铝比
作者简介:郑伟栋(1974—),男,钢铁冶金高级工程师,zhtzwd@.
3.1.1 CSP连铸机第一炉钢水Ca含量统计分析
CSP连铸机低碳钢第一炉钢水Ca含量对开浇成功与否有重要影响,通过对CSP薄板坯连铸机开浇成功与开浇不成功(不能起步或起步后塞棒上涨严重)炉次钢水Ca含量情况进行了统计(表1、图1)表明,开浇成功与开浇不成功精炼出站样平均Ca含量分别为65.6ppm、51.2ppm,成品样平均Ca含量分别为27.4ppm、20.6ppm,Ca损失率分别为58.23%、59.77%。
表1 CSP低碳钢开浇第一炉钢水Ca含量统计
类别精炼样Ca含量/ppm 成品样Ca含量/ppm Ca损失率/% 开浇成功65.6 27.4 -58.23 开浇不成功51.2 20.6 -59.77
图1 CSP低碳钢开浇第一炉钢水Ca含量统计(ppm)
由于第一炉开浇,中间包钢水需要一个填充过程。
填充期间,中间包内没有渣层保护,长水口没有浸入熔池,钢水与空气接触,吸N2和O2,发生二次氧化,产生大量夹杂,没有时间上浮。
中间包钢水开浇过程中氧含量和氮含量会明显上升,中间包钢水填充1.5 min,w(N)高达160~170ppm,w(TO)为80ppm左右[1]。
从表1、图2可以看出,开浇成功炉次钢水精炼样及成品样Ca含量均高于开浇不成功炉次,钢水Ca 损失率均在60%左右,故要求CSP低碳钢第一炉钢水精炼出站样Ca含量控制在60ppm左右,确保CSP连铸机开浇成功。
3.1.2 CSP低碳钢连拉炉次钢水Ca含量统计分析
对CSP低碳钢连拉炉次钢水Ca含量进行统计(表2、图2)表明,正常炉次、塞棒上涨炉次精炼出站样平均Ca含量分别为49.4ppm、34.2ppm,成品样平均Ca含量分别为28.0ppm、18.7ppm,Ca损失率分别为43.30%、45.03%。
表2 CSP低碳钢连拉炉次钢水Ca含量统计
类别精炼样Ca含量/ppm 成品样Ca含量/ppm Ca损失率/% 正常炉次49.4 28.0 -43.32 塞棒上涨炉次34.2 18.8 -45.03
图2 CSP低碳钢连拉炉次钢水Ca含量统计(ppm)
从表2、图2可以看出,正常炉次钢水精炼样及成品样Ca含量均高于塞棒上涨炉次,钢水Ca损失率均在45%左右,故要求CSP低碳钢连拉炉次钢水精炼样Ca含量控制在50ppm左右。
3.1.3 CSP低碳钢Ca/Als统计分析
对CSP低碳钢正常炉次、塞棒上涨炉次Ca/Als进行统计(表3)表明,正常炉次精炼出站样Ca/Als、成品样Ca/Als均高于塞棒上涨炉次,为提高钢水可浇性,要求第一炉钢水Ca/Als控制在0.18左右,连浇炉次钢水精炼出站样Ca/Als控制在0.15左右,确保成品样Ca/Als在0.09~0.15。
表3 CSP低碳钢连拉炉次钢水Ca/Als统计
类别精炼样Ca/Als 成品样Ca/Als
正常炉次0.147 0.096
塞棒上涨炉次0.088 0.056
3.2 CSP低碳钢Alin(夹杂铝)含量统计分析
对CSP低碳钢正常炉次、塞棒上涨炉次Alin含量进行统计(表4)表明,正常炉次精炼出站样及成品样平均Alin含量均低于塞棒上涨炉次,成品样比精炼样Alin升高11ppm左右,尤其是第一炉钢水与空气接触机会多,二次氧化严重,Alin含量升高20ppm左右。
故要求加强钢水纯净度控制,保证钢水净吹时间,尽可能保证钢水精炼出站样Alin含量控制在25ppm以下。
表4 CSP低碳钢Alin统计
类别精炼样Alin/ppm 成品样Alin/ppm
正常炉次24 35
塞棒上涨炉次33 45
3.3 CSP低碳钢精炼后期补铝操作
对塞棒上涨炉次精炼过程分析表明,精炼后期补铝操作,极易引起塞棒上涨事故停浇。
精炼后期补铝,产生的Al2O3夹杂尺寸小,不利于夹杂物碰撞长大并且没有充分时间上浮去除[2]。
故要求精炼前期加强钢水过程Als控制,以利于高熔点Al2O3夹杂形成簇状物上浮去除。
如后期必须要进行补铝操作,为了尽可能降低补铝对钢水质量及可浇性造成影响,要保证补铝后到钙处理前的时间至少在10min以上,并保证钢水静吹时间至少在5 min以上,确保夹杂物充分上浮。
3.4 钢水精炼时间
钢液中的夹杂主要靠聚集上浮入渣去除,在有吹氩搅拌的条件下,钢液中全氧的变化与精炼时间呈指数关系,达到一定的精炼时间后,钢液中的全氧达最低,所以,从去除夹杂物的角度,必须保证一定的精炼时间。
但精炼时间过长,钢液在高温下和熔渣、大气以及耐火材料长时间接触,钢水中的Als二次氧化及钢包耐材熔损产生大量小颗粒夹杂,悬浮在钢水中难以去除,极易造成塞棒上涨甚至漏钢事故。
故要求加强生产组织,尽可能避免钢水压站时间过长对钢水质量造成影响。
3.5 钢包烧氧
在生产中多次出现钢包不自开烧氧后塞棒上涨现象,据有关资料介绍,烧氧对中间包钢水w(TO)有显著影响[3],钢包烧氧可以使中间包钢水w(TO)上升15ppm以上。
故要求严格钢包热修操作、选择优质引流砂等措施,提高大包自开率,尤其是连铸第一炉钢水,要求使用包况良好的周转包确保自开,避免诸多不利因素叠加严重影响钢水质量,造成塞棒上涨事故停浇。
4 结论
(1)为减少CSP低碳钢塞棒上涨事故停浇,第一炉钢水精炼出站样Ca含量应控制在60ppm左右,Ca/Als 控制在0.18左右;连浇炉次钢水精炼出站样Ca含量应控制在50ppm左右,Ca/Als控制在0.15左右。
(2)钢水精炼出站样Alin含量尽量控制在25ppm以下。
(3)尽可能避免精炼后期补铝操作,确需补铝则要保证补铝后到钙处理前的时间至少在10min以上。
(4)要保证钢水精炼时间,同时要避免钢水压站时间过长。
(5)钢包烧氧对钢水质量有严重影响,要尽可能避免CSP连铸第一炉钢包烧氧。
参考文献:
[1] 高海潮等. CSP连铸浸入式水口结瘤案例研究.钢铁.2005.11.
[2] 成国光等.《新编钢水精炼暨铁水预处理1500问》.北京:中国科学技术出版社,2007.3.
[3] Hughes P.Improvement in the Internal Quality of Continuously Cast Slabs at Lukens Steel[J].Iron and Steelmaker,1995,22(6):35.。