转炉炼钢脱氧技术的现发展状
炼钢转炉冶炼低碳钢脱氧合金化工艺优化
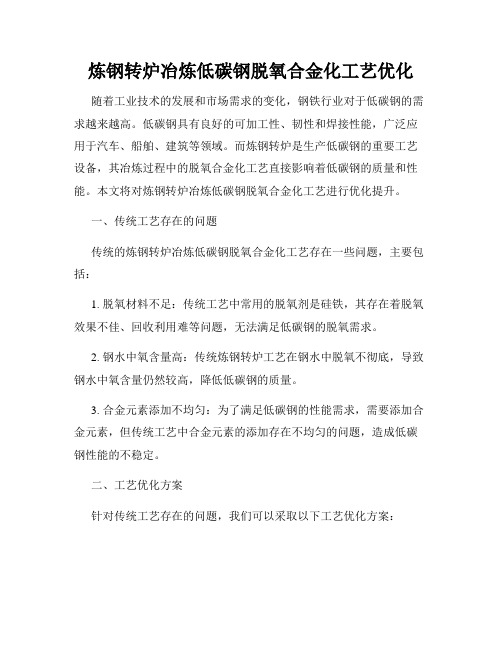
炼钢转炉冶炼低碳钢脱氧合金化工艺优化随着工业技术的发展和市场需求的变化,钢铁行业对于低碳钢的需求越来越高。
低碳钢具有良好的可加工性、韧性和焊接性能,广泛应用于汽车、船舶、建筑等领域。
而炼钢转炉是生产低碳钢的重要工艺设备,其冶炼过程中的脱氧合金化工艺直接影响着低碳钢的质量和性能。
本文将对炼钢转炉冶炼低碳钢脱氧合金化工艺进行优化提升。
一、传统工艺存在的问题传统的炼钢转炉冶炼低碳钢脱氧合金化工艺存在一些问题,主要包括:1. 脱氧材料不足:传统工艺中常用的脱氧剂是硅铁,其存在着脱氧效果不佳、回收利用难等问题,无法满足低碳钢的脱氧需求。
2. 钢水中氧含量高:传统炼钢转炉工艺在钢水中脱氧不彻底,导致钢水中氧含量仍然较高,降低低碳钢的质量。
3. 合金元素添加不均匀:为了满足低碳钢的性能需求,需要添加合金元素,但传统工艺中合金元素的添加存在不均匀的问题,造成低碳钢性能的不稳定。
二、工艺优化方案针对传统工艺存在的问题,我们可以采取以下工艺优化方案:1. 优化脱氧剂的选择:传统的硅铁脱氧剂可以通过其他脱氧剂进行替代,例如铝、锰等。
这些脱氧剂具有良好的脱氧效果和易回收利用的特点,可以提高低碳钢的质量。
2. 加强脱氧过程控制:通过提高脱氧剂的加入量和延长脱氧时间,确保炉料中的氧含量完全脱氧。
可以采用自动控制系统,实时监测钢水中氧含量,调整脱氧剂的加入量,实现钢水的有效脱氧。
3. 合金元素均匀添加:采用先进的合金元素添加技术,确保合金元素的均匀分布。
可以利用真空脱气设备将合金元素均匀加入钢水中,或者采用复合脱氧剂,使脱氧剂和合金元素同时添加,提高低碳钢的合金化效果。
4. 优化工艺参数:通过对炉温、转炉容量、吹氧时间等工艺参数的优化调整,提高低碳钢的冶炼效果。
可以利用计算机模拟技术对工艺参数进行优化设计,以实现低碳钢冶炼过程的最佳效果。
三、优化方案的效果及推广通过实施上述工艺优化方案,可以显著提高炼钢转炉冶炼低碳钢脱氧合金化的效果,进一步提升低碳钢的质量和性能。
试析转炉炼钢技术的发展与展望

试析转炉炼钢技术的发展与展望作者:黄勐来源:《名城绘》2020年第03期摘要:在我国占据主要地位的钢铁生产技术依然是转炉炼钢,这符合我国的国情,即废钢资源紧缺和巨大的人口红利,电费高昂等特点。
诸多因素促使之下,使得转炉炼钢技术在我国进一步发展。
本文主要分析探讨了转炉炼钢技术的发展与展望情况,以供同业者参考。
关键词:转炉炼钢技术;发展;展望转炉是主要用于生产碳钢、合金钢、铜、镍等金属材料的冶炼设备。
其主要原料有铁水、废钢和铁合金等,炼钢过程中的热量来源是靠铁液本身物理热以及铁液各组分间化学反应产生的热量,无需外界附加能源。
我国使用最为普遍的炼钢设备为碱性氧气顶吹和顶底复吹转炉,因其具有成本低、单炉产量高、投资少、生产速度快等优点,被我国钢铁企业所广泛应用。
1我国转炉炼钢技术的应用1.1洁净钢新流程的应用在21世纪的发展形势下,我国钢铁工业中对洁净钢的生产已经成为重点,而洁净钢的生产技术的发展目标就是采取最经济的手段来使生产效率大幅提高,从而形成大规模的生产。
当前我国已经创新出了新的炼钢流程来对洁净钢进行生产,并且已经在部分炼钢企业中得到了初步的应用。
洁净钢新流程能够对钢中的杂质进行有效的“三脱”处理,使其处理比例达到更高,并且转炉日产数也增加了将近一倍,极大提高了洁净钢的生产效率,相比于传统的洁净钢流程,生产成本也要低的多。
1.2转炉脱磷炼钢技术的应用在转炉炼钢生产中,常用脱磷技术方法包括结合铁水三脱预处理和转炉法、转炉双联法、双渣法。
其中双渣法是指操作一台转炉,实行2次造渣,转炉双联法是指操作2台转炉,一台脱磷,完成脱磷之后在另一台脱碳。
大型钢铁厂通过自主研发、应用脱磷脱碳新工艺,促使每一台转炉都可以脱磷、脱碳,应用双联技术炼钢。
一些炼钢厂由于缺乏铁水脱磷预处理的条件与设备,应用双渣法炼钢,但出钢量不高,且磷含量有较大变化,氧气含量较高。
通过不断优化转炉脱磷炼钢技术,提高出钢量与含碳量,保证出钢质量,提高转炉炼钢技术水平。
对炼钢生产中转炉炼钢脱氧工艺的分析

对炼钢生产中转炉炼钢脱氧工艺的分析摘要:随着我国经济的发展和社会的进步,我国的各行各业均均取得了令人瞩目的成就。
在目前的炼钢过程当中,转炉炼钢脱氧方式的应用越来越广泛,作为炼钢过程当中一项重要的内容,钢液脱氧效果控制能够最大限度地保证整个钢产品的质量。
本文主要是分析了炼钢生产中转炉炼钢脱氧工艺,以此为炼钢行业的发展提供些许的借鉴。
关键词:炼钢生产转炉炼钢脱氧工艺分析引言脱氧合金化是在炼钢生产中转炉炼钢过程当中非常重要的一个过程,其能够直接影响到钢产品的质量、产能以及生产成本等重要环节。
同时,脱氧合金化也是冶炼过程最后的一个步骤,通常来讲,脱氧与合金化过程是同步进行的。
一旦出现操作失误的情况,不仅对合金回收率会造成负面影响,还会提高精炼处理的难度,致使钢水混入较多的杂物,影响其可浇性,从而对铸坯的质量造成不利影响,更为严重的情况会产生废品甚至是铸机断浇。
所以,炼钢生产中转炉炼钢脱氧工艺水平的提升是炼钢生产最为关键的环节之一。
1转炉炼钢相关概述1.1转炉炼钢的原理转炉是转炉炼钢操作最为主要的设备。
其形状与鸭梨类似,内部的炉壁是由耐火砖制成,能够实现360°全方位任何角度旋转。
铁水和废钢是炼钢所需要的原材料,整个吹炼过程中的转炉炼钢是氧化反应,脱碳、脱磷、脱硫、脱氧去除有害气体和杂质,提高温度和调整成分是炼钢最基本的任务。
相关操作人员根据铁水的温度和成分和热平衡公式,再加上白灰和轻烧公式等促使炼钢渣的碱度适中,同时有效地去除氧化镁中的碳磷硫等杂物,并且确保在冶炼过程完成之后使得钢温度和成分符合要求。
吹炼过程所产出的钢水含氧量很难达到钢种质量的要求,主要是由于顶吹氧气与铁水、废钢等发生了氧化反应。
因此,在钢产出的过程中必须要加之脱氧工艺,以确保其能够达到钢种质量的要求。
1.2转炉炼钢中氧的产生及其危害钢液当中的氧气主要是以包括非金属杂物和溶解氧气两种形式存在的,而氧气主要产生自炼钢的原材料和吹氧炼钢的工序。
浅析炼钢生产的转炉炼钢脱氧工艺
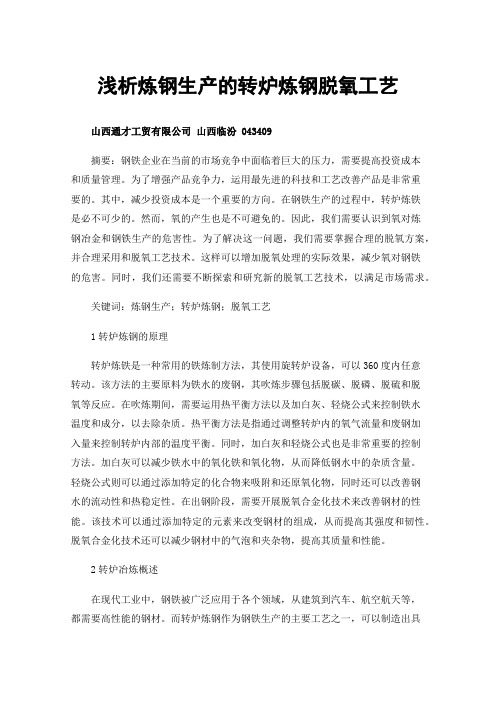
浅析炼钢生产的转炉炼钢脱氧工艺山西通才工贸有限公司山西临汾 043409摘要:钢铁企业在当前的市场竞争中面临着巨大的压力,需要提高投资成本和质量管理。
为了增强产品竞争力,运用最先进的科技和工艺改善产品是非常重要的。
其中,减少投资成本是一个重要的方向。
在钢铁生产的过程中,转炉炼铁是必不可少的。
然而,氧的产生也是不可避免的。
因此,我们需要认识到氧对炼钢冶金和钢铁生产的危害性。
为了解决这一问题,我们需要掌握合理的脱氧方案,并合理采用和脱氧工艺技术。
这样可以增加脱氧处理的实际效果,减少氧对钢铁的危害。
同时,我们还需要不断探索和研究新的脱氧工艺技术,以满足市场需求。
关键词:炼钢生产;转炉炼钢;脱氧工艺1转炉炼钢的原理转炉炼铁是一种常用的铁炼制方法,其使用旋转炉设备,可以360度内任意转动。
该方法的主要原料为铁水的废钢,其吹炼步骤包括脱碳、脱磷、脱硫和脱氧等反应。
在吹炼期间,需要运用热平衡方法以及加白灰、轻烧公式来控制铁水温度和成分,以去除杂质。
热平衡方法是指通过调整转炉内的氧气流量和废钢加入量来控制转炉内部的温度平衡。
同时,加白灰和轻烧公式也是非常重要的控制方法。
加白灰可以减少铁水中的氧化铁和氧化物,从而降低钢水中的杂质含量。
轻烧公式则可以通过添加特定的化合物来吸附和还原氧化物,同时还可以改善钢水的流动性和热稳定性。
在出钢阶段,需要开展脱氧合金化技术来改善钢材的性能。
该技术可以通过添加特定的元素来改变钢材的组成,从而提高其强度和韧性。
脱氧合金化技术还可以减少钢材中的气泡和夹杂物,提高其质量和性能。
2转炉冶炼概述在现代工业中,钢铁被广泛应用于各个领域,从建筑到汽车、航空航天等,都需要高性能的钢材。
而转炉炼钢作为钢铁生产的主要工艺之一,可以制造出具备优良物理性能和化学性能的高性能钢铁,备受业界青睐。
转炉炼钢通过氧化生铁中的碳,制造出高性能钢铁。
其中,碳含量在2.1%范围内可以产生钢铁。
生钢铁中的铁元素和碳元素形成过饱和的固溶体,提高铁、碳含量可以提升钢的韧性和可塑性。
转炉氧枪发展现状

转炉氧枪发展现状转炉氧枪是冶金行业中一种重要的设备,用于向转炉内部喷射氧气,以提高钢水的温度和氧化反应速度,从而实现高效的炼钢过程。
近年来,转炉氧枪在设计和技术上取得了很大的进展,提高了炼钢过程的效率和质量。
在转炉氧枪的设计方面,目前最常见的设计是雾化型氧枪。
这种氧枪通过喷嘴将氧气雾化成细小的气泡,然后喷射到转炉内部。
雾化型氧枪具有喷射稳定、浸润性好、能量利用率高的特点,可以有效地提高转炉内部的温度和氧化速度。
同时,雾化型氧枪还可以根据钢水的质量要求进行自动控制,使得炼钢过程更加智能化。
此外,随着数控技术的发展,目前已经出现了自动化控制的转炉氧枪。
这些自动化控制的氧枪利用传感器感知转炉内部的温度、压力和氧含量等参数,通过计算机控制系统实现对氧枪的操作和调节。
这种自动化控制的转炉氧枪具有响应速度快、控制精度高的特点,能够更好地适应炼钢过程的变化。
另外,为了提高炼钢的能源利用率,目前一些新型的转炉氧枪开始采用燃气雾化技术。
与传统的氧气雾化相比,燃气雾化技术可以将氧气与燃料共同喷射,实现钢水的燃烧和加热。
这种新型的转炉氧枪不仅可以节约能源和氧气,还可以减少炉内的废气排放。
此外,为了改善转炉氧枪的工作环境和使用寿命,目前一些转炉氧枪开始采用耐高温材料和防腐蚀涂层。
这些耐高温材料可以在高温环境下保持良好的强度和稳定性,而防腐蚀涂层可以防止炉内的氧化物和腐蚀性介质对氧枪的侵蚀。
综上所述,转炉氧枪在设计和技术上的不断进步,使得炼钢过程更加高效和智能化。
通过采用雾化型氧枪、自动化控制、燃气雾化技术和耐高温材料等新技术,转炉氧枪能够更好地实现钢水的加热和氧化,从而提高钢水的温度和氧化速度,改善炼钢过程的质量和效率。
随着科技的不断发展,相信转炉氧枪在未来会有更大的突破和应用。
探讨炼钢生产中转炉炼钢脱氧工艺
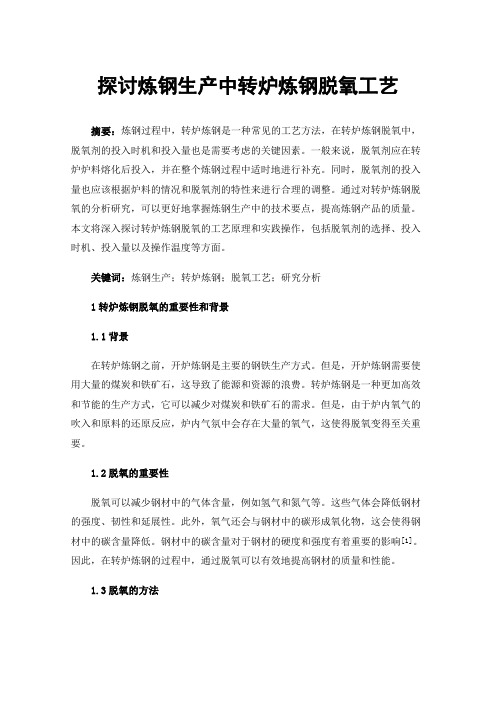
探讨炼钢生产中转炉炼钢脱氧工艺摘要:炼钢过程中,转炉炼钢是一种常见的工艺方法,在转炉炼钢脱氧中,脱氧剂的投入时机和投入量也是需要考虑的关键因素。
一般来说,脱氧剂应在转炉炉料熔化后投入,并在整个炼钢过程中适时地进行补充。
同时,脱氧剂的投入量也应该根据炉料的情况和脱氧剂的特性来进行合理的调整。
通过对转炉炼钢脱氧的分析研究,可以更好地掌握炼钢生产中的技术要点,提高炼钢产品的质量。
本文将深入探讨转炉炼钢脱氧的工艺原理和实践操作,包括脱氧剂的选择、投入时机、投入量以及操作温度等方面。
关键词:炼钢生产;转炉炼钢;脱氧工艺;研究分析1转炉炼钢脱氧的重要性和背景1.1背景在转炉炼钢之前,开炉炼钢是主要的钢铁生产方式。
但是,开炉炼钢需要使用大量的煤炭和铁矿石,这导致了能源和资源的浪费。
转炉炼钢是一种更加高效和节能的生产方式,它可以减少对煤炭和铁矿石的需求。
但是,由于炉内氧气的吹入和原料的还原反应,炉内气氛中会存在大量的氧气,这使得脱氧变得至关重要。
1.2脱氧的重要性脱氧可以减少钢材中的气体含量,例如氢气和氮气等。
这些气体会降低钢材的强度、韧性和延展性。
此外,氧气还会与钢材中的碳形成氧化物,这会使得钢材中的碳含量降低。
钢材中的碳含量对于钢材的硬度和强度有着重要的影响[1]。
因此,在转炉炼钢的过程中,通过脱氧可以有效地提高钢材的质量和性能。
1.3脱氧的方法转炉炼钢中有两种主要的脱氧方法,即硅脱氧和铝脱氧。
硅脱氧是最常用的方法,它通过在炉内加入硅来将氧气与硅反应,从而减少炉内氧气含量。
硅脱氧可以有效地减少氧气含量,但同时也会增加钢材中硅的含量。
铝脱氧则是一种更加高效的脱氧方法,它可以将氧气与铝反应,从而减少氧气含量,同时不会增加钢材中其他元素的含量。
铝脱氧可以生产出更加纯净的钢材。
2氧化铝脱氧法在转炉炼钢中的应用2.1背景在传统的转炉炼钢过程中,气氛中存在大量的氧气,这会使钢中存在过多的气体,如氮气、氧气和氢气等。
这些气体会导致钢中的气孔和夹杂物增多,从而降低钢的质量和性能。
转炉冶炼低碳钢脱氧工艺的改进
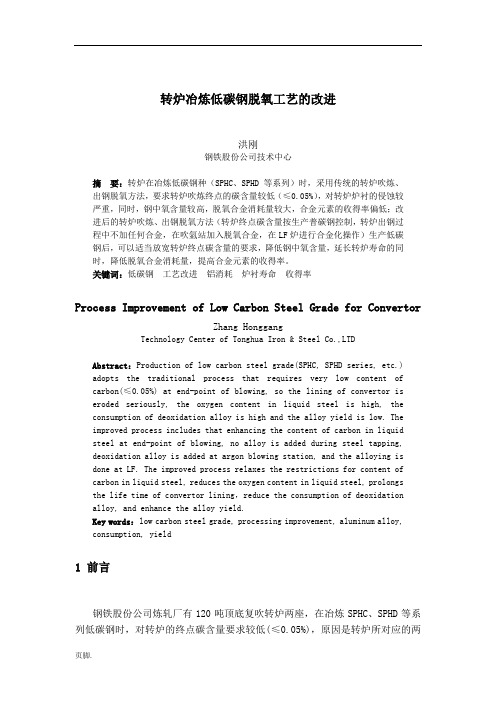
转炉冶炼低碳钢脱氧工艺的改进洪刚钢铁股份公司技术中心摘要:转炉在冶炼低碳钢种(SPHC、SPHD等系列)时,采用传统的转炉吹炼、出钢脱氧方法,要求转炉吹炼终点的碳含量较低(≤0.05%),对转炉炉衬的侵蚀较严重,同时,钢中氧含量较高,脱氧合金消耗量较大,合金元素的收得率偏低;改进后的转炉吹炼、出钢脱氧方法(转炉终点碳含量按生产普碳钢控制,转炉出钢过程中不加任何合金,在吹氩站加入脱氧合金,在LF炉进行合金化操作)生产低碳钢后,可以适当放宽转炉终点碳含量的要求,降低钢中氧含量,延长转炉寿命的同时,降低脱氧合金消耗量,提高合金元素的收得率。
关键词:低碳钢工艺改进铝消耗炉衬寿命收得率Process Improvement of Low Carbon Steel Grade for ConvertorZhang HonggangTechnology Center of Tonghua Iron & Steel Co.,LTDAbstract:Production of low carbon steel grade(SPHC, SPHD series, etc.)adopts the traditional process that requires very low content ofcarbon(≤0.05%) at end-point of blowing, so the lining of convertor iseroded seriously, the oxygen content in liquid steel is high, theconsumption of deoxidation alloy is high and the alloy yield is low. Theimproved process includes that enhancing the content of carbon in liquidsteel at end-point of blowing, no alloy is added during steel tapping,deoxidation alloy is added at argon blowing station, and the alloying isdone at LF. The improved process relaxes the restrictions for content ofcarbon in liquid steel, reduces the oxygen content in liquid steel, prolongsthe life time of convertor lining,reduce the consumption of deoxidationalloy, and enhance the alloy yield.Key words:low carbon steel grade, processing improvement, aluminum alloy,consumption, yield1 前言钢铁股份公司炼轧厂有120吨顶底复吹转炉两座,在冶炼SPHC、SPHD等系列低碳钢时,对转炉的终点碳含量要求较低(≤0.05%),原因是转炉所对应的两台薄板坯连铸机(意大利达涅利公司的FTSC型)对钢水的质量要求较严格,考虑精炼处理过程中的增碳及尽量避开钢种成份的包晶区需要成品钢水的碳含量≤0.06%,这使转炉终点的氧含量偏高,尤其是在转炉炉役的后期,转炉的复吹效果变差,终点的碳氧浓度积较高,一般情况下转炉终点的氧含量要达到800PPm 以上,对转炉炉衬的侵蚀较严重,而且脱氧及合金化所消耗的合金成本较高,我厂的此类钢种产量比例约占薄板坯产量的30%左右,每月约5万吨,因此,需要对现有的冶炼及脱氧合金化工艺进行优化,以降低生产成本。
我国转炉复吹技术的发展和现状

我国转炉复吹技术的发展和现状
转炉复吹技术是指在钢水净化过程中,在转炉内部进行二次喷吹氧气,以增强钢水中的氧化反应,从而提高钢水净化效果的一种技术。
我国的转炉复吹技术始于上世纪80年代,随着技术的发展,该技术已经得到了广泛应用。
目前,我国大多数钢厂都采用了转炉复吹技术,其中大型钢铁企业的复吹技术水平已达到国际先进水平。
转炉复吹技术的发展与现状主要有以下几点:
1. 技术改进:随着科技的不断进步,转炉复吹技术得到了不断改进和完善,特别是在喷吹氧气的位置、角度、流量等方面做出了不少创新,从而提高了钢水净化效果。
2. 技术水平提高:我国大多数钢厂都拥有较为先进的复吹技术设备,能够更好地掌握复吹技术,提高钢水净化效率,降低生产成本,提高钢铁产品质量。
3. 实现绿色环保:转炉复吹技术可有效净化钢水中的杂质,减少废气排放,达到了绿色环保的效果。
我国的钢铁企业也在积极推广清洁生产,不断提高环保水平。
总之,转炉复吹技术在我国的发展和应用已经取得了显著成果,随着科技的不断进步和环保要求的不断提高,该技术将会得到更广泛的应用。
炼钢生产中转炉炼钢脱氧工艺的分析

23
I 行业发展 ndustry development
进一步是钢液中碳、氧发生反应,生成一氧化碳气泡。在真空环 境下,脱氧法产生的 CO 不会对钢液形成污染,并且 CO 气泡逸 出,加强钢液搅拌,让脱氧反应更加充分、彻底,大大节约了脱 氧剂与石灰使用成本。真空脱氧法具备脱氧效果明显,以及投入 成本低的优势在转炉炼钢脱氧过程中获得了较为普遍的使用。3 脱氧工艺的优化 3.1 普碳钢脱氧工艺的优化
解氧气形式两种,炼钢原料与吹氧炼钢环节是产生氧的主要来 源。在实际炼钢过程中,碳、锰、磷、硅等元素以及其他一些化 ห้องสมุดไป่ตู้杂质的去除,都离不开对大量氧气的使用,借助氧化反应使氧 气与杂质有效结合形成氧化物析出,进而获得高纯度的钢。
可见,氧在钢液中存在是必然的,实际吹氧炼钢时,钢液中 需要氧化的杂质含量越大,所需的氧气量也就越大,同时钢液中 的氧含量也会有所增加。若是没有对钢液中的氧进行有效处理, 导致钢液中的氧含量过高,就会在钢液凝固时有充足的氧气与 钢液中的铁发生氧化反应。形成氧化亚铁结晶析出。钢液中的 氧化亚铁会对铸坯造成极大破坏,直接影响钢产品质量响,甚至 还会导致铸坯变形,严重时产生热脆反应进一步催生钢铁的氧 化现象,导致钢液报废。
文章编号 :11-5004(2019)09-0023-2
由于在固态铁中氧的溶解度非常低,最后形成的氧化物夹 杂会导致钢材的机械性能降低,尤其是会导致钢材的冲击韧性 以及疲劳强度下降,所以必须要采取有效的工艺方法来进行转 炉炼钢的脱氧。
对炼钢生产中转炉炼钢脱氧工艺的探讨

对炼钢生产中转炉炼钢脱氧工艺的探讨摘要:随着中国钢铁企业竞争的加剧,钢铁企业加强了成本和质量管理。
因此,如何利用新技术提高产品质量,降低投资成本,已成为现阶段中国钢铁企业提高产品竞争力的关键。
在转炉炼钢的实际制造过程中,氧气的大量存在是不可避免的,因此企业必须首先了解氧气对炼钢产品和钢铁生产的影响,同时了解有效的除氧方法,进而合理利用和改进除氧技术,在保证钢铁质量的前提下,进一步降低投资成本,更加安全有效地实现炼钢生产。
转炉炼钢脱氧工艺广泛应用于炼钢生产中,能有效提高钢材质量。
同时,为了保证应用效果,必须加强对该工艺的应用研究,特别是加强对转炉氧含量的控制。
关键词:炼钢生产;转炉炼钢;脱氧工艺;氧化处理引言:中国工业发展比较快,在冶炼钢铁材料时,对各种工艺和技术的应用有很高的要求。
转炉炼钢的脱氧处理是生产转炉炼钢产品过程中的关键环节,因为钢水脱氧的效率直接关系到炼铁生产和炼钢产品的质量。
如果钢液含氧量高,钢材的热成型性会减弱,内部气孔会扩大,组织疏松,容易形成热脆性,影响钢材的生产质量。
在转炉炼钢过程中,需要结合实际生产情况,提高对氧的危害性的认识。
通过脱氧技术的合理使用,可以有效提高钢材质量,有效提高钢厂生产能力,为钢厂持续稳定发展奠定坚实基础,加强转炉炼钢的脱氧管理已成为提高炼钢生产质量的关键原因。
目前,转炉炼钢脱氧工艺是我国最重要的炼钢技术,在应用中取得了良好的效果。
因为转炉炼钢形成的氧气会在一定程度上影响钢材质量,进而降低生产效率,制约和阻碍钢厂的经营和发展。
与其他炼钢技术相比,转炉炼钢自动化生产水平相对较高,可以提高生产质量和效率,因此,该技术在钢铁企业生产中得到了广泛应用。
但在工艺应用中仍存在一些不足,需要在现有工艺的基础上进行创新和优化,以提高综合生产水平。
1氧气在炼钢生产中的影响及危害分析在转炉炼钢中,需要分离生铁中的碳和杂质,通过氧化处理可以生产出强度更高、性能更好的材料。
在生产过程中,生铁中的碳和铁元素会反应生成碳化铁。
炼钢转炉脱氧工艺分析

炼钢转炉脱氧工艺分析2.河北省半钢水冶炼高洁净高品质特殊钢重点实验室, 河北省承德市067000摘要:炼钢生产中,钢液脱氧效果的优劣成为影响钢产品质量的关键因素。
首先我们应当认清氧气究竟会给钢产品带来什么样的危害,熟悉炼钢不同的脱氧工艺,尝试优化、改进,以提升脱氧效果。
为此,本文介绍了脱氧技术现状,分析了氧的危害,并探讨转炉炼钢脱氧工艺与优化措施,旨在节省成本,推动钢铁行业的持续发展。
关键词:转炉;炼钢;脱氧工艺引言伴随行业竞争的白热化,钢铁企业陆续从质量、生产成本上予以控制。
在转炉炼钢生产活动中,氧的产生在所难免。
我们要意识到氧对钢产品的危害,灵活运用多元的脱氧方法,逐步改良脱氧处理工艺,提高脱氧处理效果。
在不影响钢产品质量的基础上,节省生产成本,推动钢铁行业的发展。
1脱氧技术现状炼钢过程中,最开始看到的脱氧物,就是硅。
硅脱氧有它自身的不足:脱氧不完全、钢材皮下可见大量的气泡;钢中熔合大量的硅盐酸,这些对于钢材质量均是不利的。
脱氧产生的SiO2为酸性物质,能够使钢水快速回磷或是回硫。
1930年代,人类就大范围地推广电解铝技术。
由于那时候的铝价便宜,铝脱氧技术作为一支新秀,很快成为炼钢脱氧行业的领头军。
在脱氧方面,铝有出色的表现,美国早在很多年前就开始将铝充当炼钢中的脱氧剂,相较于硅脱氧,铝脱氧有助于提高脱氧效率,降低钢中的SiO2。
氧化铝是一种典型的中性物质,对钢渣碱度并无太大的影响,不会导致钢水回磷或是回硫。
在炼钢厂中,铝至今仍是最核心的脱氧剂。
由于铝的比重小,回收率相对偏低(约10%~25%),耗费的炼钢成本相对偏大。
为促进铝的高效利用,有些钢厂开始研发铝系复合脱氧剂,如硅铝钡。
这类铝系脱氧剂,在密度方面要比纯铝高出不少。
将它置于钢液中,不易下沉。
另外,熔点相对偏低的复合氧化物,很大程度上也可以对脱氧产物进行全面地清除。
铝脱氧后生成一种氧化铝,使钢材本身的疲劳性能发生变化。
而非铝系复合脱氧剂,恰巧就会转变夹杂物最初的这种形态。
转炉炼钢技术的发展与展望
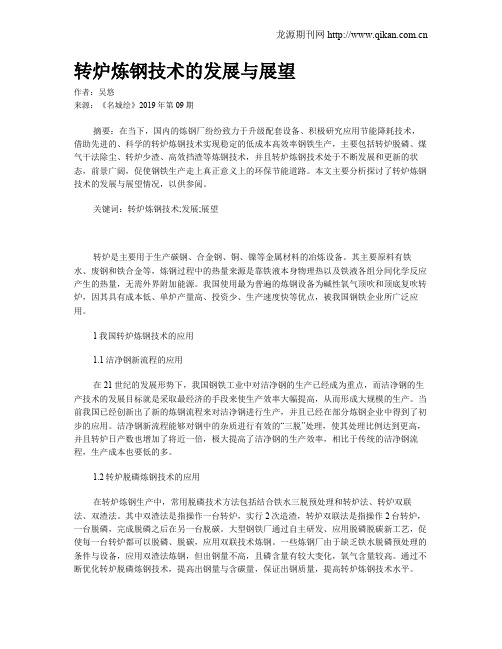
转炉炼钢技术的发展与展望作者:吴悠来源:《名城绘》2019年第09期摘要:在当下,国内的炼钢厂纷纷致力于升级配套设备、积极研究应用节能降耗技术,借助先进的、科学的转炉炼钢技术实现稳定的低成本高效率钢铁生产,主要包括转炉脱磷、煤气干法除尘、转炉少渣、高效挡渣等炼钢技术,并且转炉炼钢技术处于不断发展和更新的状态,前景广阔,促使钢铁生产走上真正意义上的环保节能道路。
本文主要分析探讨了转炉炼钢技术的发展与展望情况,以供参阅。
关键词:转炉炼钢技术;发展;展望转炉是主要用于生产碳钢、合金钢、铜、镍等金属材料的冶炼设备。
其主要原料有铁水、废钢和铁合金等,炼钢过程中的热量来源是靠铁液本身物理热以及铁液各组分间化学反应产生的热量,无需外界附加能源。
我国使用最为普遍的炼钢设备为碱性氧气顶吹和顶底复吹转炉,因其具有成本低、单炉产量高、投资少、生产速度快等优点,被我国钢铁企业所广泛应用。
1我国转炉炼钢技术的应用1.1洁净钢新流程的应用在21世纪的发展形势下,我国钢铁工业中对洁净钢的生产已经成为重点,而洁净钢的生产技术的发展目标就是采取最经济的手段来使生产效率大幅提高,从而形成大规模的生产。
当前我国已经创新出了新的炼钢流程来对洁净钢进行生产,并且已经在部分炼钢企业中得到了初步的应用。
洁净钢新流程能够对钢中的杂质进行有效的“三脱”处理,使其处理比例达到更高,并且转炉日产数也增加了将近一倍,极大提高了洁净钢的生产效率,相比于传统的洁净钢流程,生产成本也要低的多。
1.2转炉脱磷炼钢技术的应用在转炉炼钢生产中,常用脱磷技术方法包括结合铁水三脱预处理和转炉法、转炉双联法、双渣法。
其中双渣法是指操作一台转炉,实行2次造渣,转炉双联法是指操作2台转炉,一台脱磷,完成脱磷之后在另一台脱碳。
大型钢铁厂通过自主研发、应用脱磷脱碳新工艺,促使每一台转炉都可以脱磷、脱碳,应用双联技术炼钢。
一些炼钢厂由于缺乏铁水脱磷预处理的条件与设备,应用双渣法炼钢,但出钢量不高,且磷含量有较大变化,氧气含量较高。
炼钢生产中脱氧工艺分析

14炼钢生产中脱氧工艺分析梁金鹏(甘肃酒钢集团宏兴钢铁股份有限公司安全环保处,甘肃 嘉峪关 735100)摘 要:钢液脱氧处理是炼钢工艺的重要步骤,其脱氧效果直接决定着钢水的整体质量,因此,需要在炼钢生产中重视脱氧处理。
钢液中氧含量过多,就会降低钢产品的结构质量,增加其热脆概率。
关键词:炼钢生产;转炉炼钢;脱氧工艺中图分类号:TF713.5 文献标识码:A 文章编号:11-5004(2019)09-0014-2收稿日期:2019-09作者简介:梁金鹏,男,生于1977年,汉族,河南平顶山人,本科,中级工程师,研究方向:炼钢工艺及金属冶炼安全。
1 氧的产生与危害在炼钢生产所产生的钢液中,氧一般以非金属夹杂物、溶解氧的形式存在,这种形式主要是由于炼钢生产中原料的特殊性与吹氧炼钢生产等造成的。
在炼钢生产中,无论采用何种生产方式,在去除钢中杂质中,都需要借助于氧气与这些元素的反应来实现,通过氧气与杂质元素的反应,生成氧化反应物,析出杂质。
在吹氧冶炼中,钢液中氧的含量是随着其他杂质元素的含量而变化的,二者成负向变化的关系,杂质含量低,钢液中氧的含量反而较高,一旦没有进行必要的脱氧处理,含氧量较高的钢液在冷凝固中,氧会与钢液产生化学反应,使得其析出FeO,这种反应现象大大降低了钢产品的质量,使得钢的塑性降低,极易出现热脆现象,还会加大其氧化的概率。
如果钢液中含有的氧较多,还会加大硫的危害,使得氧可以与钢液中的其他物质连续发生反应,形成氧化产物,这些氧化产物的出现大大降低了钢产品的物理与化学性能。
2 脱氧技术的现状近年来,炼钢生产中的转炉炼钢脱氧工艺中,铝依然是最常用到的脱氧剂,但是其回收利用率在10%~25%之间,利用效率低,因此,大大提高了炼钢生产企业的生产成本,有些炼钢企业为了有效解决此类问题,逐步研发了一些铝系的复合脱氧剂,比如硅铝铁、铝锰铁等。
一般情况下,这些复合脱氧剂的密度要远远高于纯铝,将其倒入钢液以后,有足够的上浮时间,因此,能够大大提高其回收利用效率,脱氧以后会形成低熔点的复合氧化物,因此,可以达到理想的脱氧效果。
我国转炉炼钢技术发展现状与趋势分析

我国转炉炼钢技术发展现状与趋势1、转炉炼钢技术发展现状目前,转炉炼钢仍是世界上最主要的炼钢方法,其钢产量占世界钢总产量的65%以上。
由于我国废钢资源短缺,电力缺乏,电价偏高,因此电炉钢的产量增长受到一定程度的制约,而随着生铁资源的充裕也给转炉钢产量的增长提供了良好条件。
因此,转炉钢产量近年来获得了快速增长。
2905年我国转炉钢产量为3.14亿吨,到2013年提高到7.65亿吨。
随着转炉钢产量的增加,转炉炼钢生产工艺技术也得到迅速发展。
转炉炼钢技术进步主要体现在以下几个方面。
1.1、转炉装备日趋大型化2001年我国100吨以上大型转炉只有30座,产能为3602万吨。
至2013年增长到345座,产能超过5.08亿吨,13年间大型转炉的生产能力增长了14倍。
其中300吨转炉从3座增加到11座,产能从678万吨增长到2759万吨以上。
从数量上来看,我国现有转炉中以100-199吨的转炉数量最多,而200吨及以上的转炉数量最少,我国仍然保有一定数量的30吨以下的转炉。
因此,淘汰落后产能任务艰巨。
目前,我国100吨及以上转炉的产能约占全部转炉产能的67.5%。
随着淘汰落后产能力度的加大,我国转炉将进一步朝着大型化方向发展。
1.2、转炉生产工艺进一步优化提高钢材洁净度是21世纪钢材质量发展的重大技术方向。
为提高钢材质量且扩大冶炼钢种,我国大、中型转炉炼钢厂都相继增建了铁水脱硫装置和二次精炼装置。
近年来新建的转炉炼钢厂大多配置了铁水脱硫装置,并根据冶炼钢种的要求配置了相应的炉外精炼装置,一般多采用LF精炼,有些转炉炼钢厂还配置了Ⅵ)精炼装置,从而为高附加值钢种的生产提供了有利条件。
我国自主设计建设的京唐公司300吨转炉采用了国际上最先进的脱磷炉与脱碳炉分工、联合生产的工艺,京唐公司是国际上最早采用这一先进工艺的300吨转炉大型炼钢厂。
经过近两年的技术攻关,脱磷炉生产周期28min,脱碳炉32min;单炉班产炉数从7-8炉次提高至16炉次,转炉生产效率提高1倍,出钢温度平均降低20℃。
转炉炼钢脱氧工艺分析

21Metallurgical smelting冶金冶炼转炉炼钢脱氧工艺分析徐 亮(河北钢铁集团宣化钢铁公司,河北 张家口 075100)摘 要:以如今实际的炼钢情况而言,转炉炼钢的应用频次较高,此种炼钢方法的自动化水平普遍高于其他技术,其生产效果相对显著,但是此种炼钢方法在具体应用期间必须关注脱氧技术的良好应用,由于脱氧操作质量能够在一定程度上决定炼钢操作的效果。
总体而言,在炼钢操作期间,转炉炼钢的应用需要重视脱氧技术的操作,因此针对其展开探讨与研究对于炼钢业的发展具有重要的意义。
关键词:转炉炼钢;脱氧工艺;对策分析中图分类号:TF713.5 文献标识码:A 文章编号:11-5004(2020)21-0021-2收稿日期:2020-11作者简介:徐亮,男,生于1987年,汉族,辽宁鞍山人,工程师,研究方向:炼钢冶金。
钢铁企业立足实际,选择合适的转炉炼钢脱氧工艺,通过降低钢中的夹杂物,改善钢水的流动性,提升脱氧效率与效果。
1 转炉炼钢与脱氧工艺的相关概述1.1 转炉炼钢的原理转炉炼钢操作的设备为转炉。
转炉的形态类似于鸭梨,内部为由耐火砖形成的炉壁,炉体能够360度任意角度旋转。
炼钢所需的原料为铁水和废钢,转炉炼钢在整个吹炼过程为氧化反应,炼钢的基本任务包括:脱碳、脱磷、脱硫、脱氧去除有害气体和杂质,提高温度和调整成分。
吹炼过程根据铁水温度和成分操作人员利用热平衡公式和加白灰、轻烧公式使炼钢渣系形成合适的碱度和氧化镁有效的去除C、P、S,并在冶炼结束能够达到合适的出钢温度和成分要求。
由于在吹炼过程中顶吹氧气和炉内铁水、废钢发生强有力的化学氧化反应,最终所得钢水所含氧含量不能满足钢种质量要求,所以在出钢过程中要开展脱氧合金化操作来提升钢的品质,达到钢种要求。
1.2 脱氧工艺在炼钢过程中的重要作用转炉炼钢期间脱氧技术主要为了降低钢中氧的数量,防止因为氧含量较多,和别的物质发生不利于生产质量要求的反应。
浅析炼钢生产的转炉炼钢脱氧工艺

浅析炼钢生产的转炉炼钢脱氧工艺摘要:伴随着我国生产与消费的持续增长,我国钢资源数量也呈现出了持续增加的趋势。
在转炉炼钢过程中会产生大量的氧气,影响钢的生产质量和炼钢企业的生产效率,不利于提高企业的竞争力。
因此,要深入研究转炉炼钢脱氧工艺,进一步提高工艺水平,有效保障炼钢质量。
本文主要分析了炼钢生产的转炉炼钢脱氧工艺对生产起到的参考作用,以期推动我国炼钢行业的健康发展。
关键词:炼钢生产;转炉;炼钢;脱氧工艺引言面对世界钢铁企业的剧烈竞争,各钢铁企业不断地逐步提高投资成本和质量管理。
通过运用最先进的科技和工艺改善产品,以减少投资成本,已成为现阶段钢铁企业增强产品竞争力的重点。
在转炉炼铁的实际生产过程中,氧的产生是必然的。
因此,有必要认识氧对炼钢冶金和钢铁生产的危害性,并掌握合理的脱氧方案,进而合理地采用和脱氧工艺技术,以增加脱氧处理的实际效果。
1转炉炼钢的原理及优点转炉炼铁所使用的主要机械是旋转炉设备。
旋转炉的形状近似于鸭梨,里面是由燃料气体混合物所组成的炉壁,炉体能够在360°内任何方向转动。
炼铁所需要的主要原料是铁水的废钢,而转炉炼铁的全部吹炼步骤都是抗氧化反应,主要工作应该分为:脱碳、脱磷、脱硫、脱氧以除去危险空气和杂物等,增加温度和改变成分。
在吹炼期间的铁水温度和成分作业中需要运用热平衡方法和加白灰、轻烧公式,对冶炼钢渣体系生成适当的 pH 值和氧化镁以合理的比例去除C、P、S 等,并使熔炼结果能够获得最理想的出钢温度和成分条件。
因为在吹炼阶段中,顶吹空气与高炉内铁水、废钢等进行了强烈的化学氧化反应,最后产生铁流所充氧量无法达到钢材的品质要求,所以在出钢阶段中必须开展脱氧合金化技术来改善钢材的性能,以满足炼钢的需要。
2脱氧技术的现状在熔炼的情况下,最早出来的脱氧物就是硅,即硅的制造导致镇静钢的出现。
但是,由于硅的脱氧能力降低,易产生不完全脱氧,从而在金属中产生了大量的金属泡沫。
在用脱氧硅时,也会产生大量的硅盐酸并掺入钢材中,这对原材料钢的使用也有重要影响。
转炉炼钢技术的发展与展望
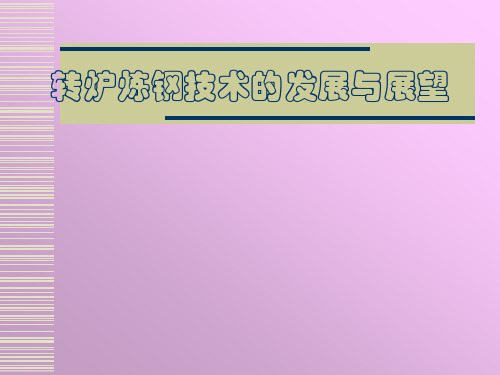
转炉技术完善化时期(1970~1990年)
这一时期,由于连铸技术的迅速发展,出现了全连铸的 炼钢车间。
对转炉炼钢的稳定性和终点控制的准确性,提出更高的 要求。
为了改善转炉吹炼后期钢渣反应远离平衡,实现平稳吹 炼的目标,综合顶吹、底吹转炉的优点,研究开发出各 种顶底复合吹炼工艺,在全世界迅速推广。
国内钢厂采用溅渣护炉工艺后的平均经济效益为4.0元 /t,每年全国可获经济效益l.8亿元。
溅渣护炉的基本原理
是利用高速氮气把成分调整后的剩余炉渣 喷溅在炉衬表面形成溅渣层。
溅渣层固化了镁碳砖表层的脱碳层,抑制 了炉衬表层的氧化,并减轻了高温炉渣对 砖表面的冲刷侵蚀。
溅渣护炉示意图
溅渣护炉技术今后研究工作的重点
控制精度
([IC]±0.03)% (T±15)℃
([IC]±0.02)% (T±12)℃
([IC]±0.03)% (T±15)℃ 对吹炼的控制精 度超过 5 年以上 的熟练操作工人
命中率 ≤50%
80 ~ 90%
≥90%
动态控制采用的两种方法
副枪动态控制技术 在吹炼接近终点时(供O2量85%左右),插入副枪
全自动吹炼控制技术的冶金效果
①提高了终点控制精度,对低碳钢([%C]<0.06%),控制精度为 ±0.015%;对中碳钢([%C]=0.06~0.20%),控制精度为 ±0.02%;高碳钢([%C]>0.20%),控制精度为±0.05%;温 度±10℃,命中率≥95%。
②实现了对终点S、P、Mn的准确预报,精度为:S±0.0009%; P±0.00l4%;Mn±0.009%。
(3)具备容错性,可消除各种系统误差,随机误差和 检测误差;
(4)响应迅速,系统安全可靠。
转炉炼钢脱氧工艺

一、引言钢铁企业管理者无一不希望自家企业的钢材质量可以稳居市场龙头,进而钢铁企业内部竞争不亚于一线城市内房地产行业之间的竞争。
如何利用现存的先进脱氧工艺提升钢材质量,降低脱氧成本变成了各个钢铁企业在行业中获得核心竞争力的重点。
由于在实际转炉炼钢过程中,必然会有氧气的产生,而氧气的存在对于转炉炼钢这个工业起着重要的作用。
因此,钢铁企业管理者需要充分了解氧气的存在对于钢产品来说会产生怎样的危害,并着重掌握脱氧技术的核心内容。
以期达到少资金投入,大幅度脱氧的目的,让炼钢产业可以更快更好的发展起来。
二、转炉石炼钢脱氧工艺的诞生一种成熟的脱氧工艺诞生之前都有无数个稚嫩的脱氧工艺为之铺路,虽然这些稚嫩如今已不被企业所使用,但它们的存在伟大且有意义,值得用纤细的笔杆浓墨重彩地写入历史。
1865年英国工程师贝斯麦通过研究得出了低吹酸性转炉炼钢法,让钢铁变得更易制取,大量而廉价的钢铁从机器中源源不断地生产出来,从而促进了欧洲的工业革命。
1879年,发明的吹碱性转炉炼钢法更大大的提升了钢铁的转化率和质量。
又过百年,奥地利通过研究得到了纯氧顶吹转炉,将前人头痛的祛除有害物质的难题解决掉的同时,也为后期完善而系统的脱氧工艺做出了铺垫。
三、钢材中氧气存在的危害钢铁作为一种满足工程建筑需求的材料,企业一般要求其质量和性能都能够承载住重达千斤的物品。
可生铁或废铁中一般都含有磷、硫、氢、氧、氮等元素,它们的存在让钢铁的性能大打折扣。
其中的氧元素则以非金属物质存在于钢液之中,在炼钢吹氧这步骤中,想除去一些杂质金属氧气必须存在,并且发挥着不可替代的作用。
例如,和杂质结合时形成氧化物沉淀,让金属杂质从钢液中析出。
在整个过程中氧气含量充足时,金属杂质将会被充分化为沉淀,但氧气含量过饱和且不能有效处理后。
会发生下列三种情况。
①过量的氧气会在钢液凝固的途中与之发生化学反应,生成一种名为氧化亚铁的杂质,此种物质的存在极有可能损害铸培,严重者有可能使钢材发生变形这种糟糕的情况,会对钢材质量造成毁灭性打击。
对炼钢生产中转炉炼钢脱氧工艺的探讨
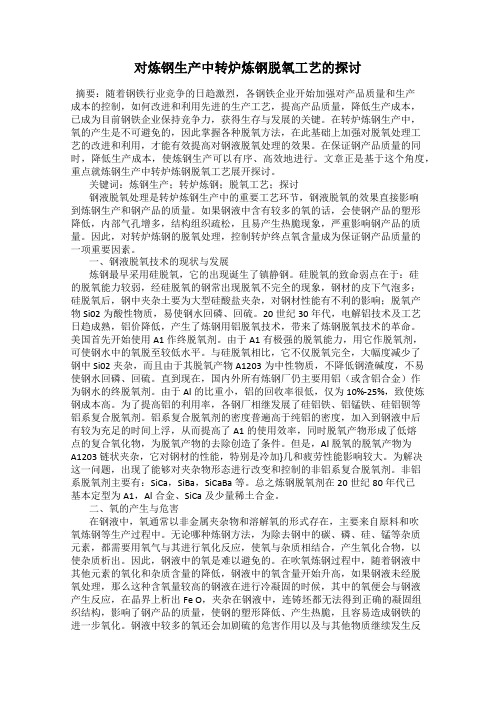
对炼钢生产中转炉炼钢脱氧工艺的探讨摘要:随着钢铁行业竞争的日趋激烈,各钢铁企业开始加强对产品质量和生产成本的控制,如何改进和利用先进的生产工艺,提高产品质量,降低生产成本,已成为目前钢铁企业保持竞争力,获得生存与发展的关键。
在转炉炼钢生产中,氧的产生是不可避免的,因此掌握各种脱氧方法,在此基础上加强对脱氧处理工艺的改进和利用,才能有效提高对钢液脱氧处理的效果。
在保证钢产品质量的同时,降低生产成本,使炼钢生产可以有序、高效地进行。
文章正是基于这个角度,重点就炼钢生产中转炉炼钢脱氧工艺展开探讨。
关键词:炼钢生产;转炉炼钢;脱氧工艺;探讨钢液脱氧处理是转炉炼钢生产中的重要工艺环节,钢液脱氧的效果直接影响到炼钢生产和钢产品的质量。
如果钢液中含有较多的氧的话,会使钢产品的塑形降低,内部气孔增多,结构组织疏松,且易产生热脆现象,严重影响钢产品的质量。
因此,对转炉炼钢的脱氧处理,控制转炉终点氧含量成为保证钢产品质量的一项重要因素。
一、钢液脱氧技术的现状与发展炼钢最早采用硅脱氧,它的出现诞生了镇静钢。
硅脱氧的致命弱点在于:硅的脱氧能力较弱,经硅脱氧的钢常出现脱氧不完全的现象,钢材的皮下气泡多;硅脱氧后,钢中夹杂土要为大型硅酸盐夹杂,对钢材性能有不利的影响;脱氧产物Si02为酸性物质,易使钢水回磷、回硫。
20世纪30年代,电解铝技术及工艺日趋成熟,铝价降低,产生了炼钢用铝脱氧技术,带来了炼钢脱氧技术的革命。
美国首先开始使用A1作终脱氧剂。
由于A1有极强的脱氧能力,用它作脱氧剂,可使钢水中的氧脱至较低水平。
与硅脱氧相比,它不仅脱氧完全,大幅度减少了钢中Si02夹杂,而且由于其脱氧产物A1203为中性物质,不降低钢渣碱度,不易使钢水回磷、回硫。
直到现在,国内外所有炼钢厂仍主要用铝(或含铝合金)作为钢水的终脱氧剂。
由于Al的比重小,铝的回收率很低,仅为10%-25%,致使炼钢成本高。
为了提高铝的利用率,各钢厂相继发展了硅铝铁、铝锰铁、硅铝钡等铝系复合脱氧剂。
- 1、下载文档前请自行甄别文档内容的完整性,平台不提供额外的编辑、内容补充、找答案等附加服务。
- 2、"仅部分预览"的文档,不可在线预览部分如存在完整性等问题,可反馈申请退款(可完整预览的文档不适用该条件!)。
- 3、如文档侵犯您的权益,请联系客服反馈,我们会尽快为您处理(人工客服工作时间:9:00-18:30)。
转炉炼钢脱氧技术的现发展状摘要:介绍了沉淀脱氧、扩散脱氧、真空脱氧和复合脱氧法对钢水脱氧的影响以及各种脱氧工艺效果之间的比较。
关键词:脱氧工艺,效果分析The Present Situation Of BOF Purging ProcessAbstract:The present paper introduces settling purging and spread purging and vacuum purging and composite purging and the comparison to all kinds of purging process.Key word:purging process;effect analyse前言当钢液中大量元素,特别是碳被氧化到较低浓度时,钢液内就存在着较高量的氧(ω[ O ]=0.02%~0.08%)。
这种饱含氧的钢液在冷凝固时,不仅在晶界上析出FeO及FeO-FeS,使钢的塑性降低及发生热脆,而且其中的[ C ]及[ O ]将继续反应,甚至强烈反应。
因为其内的氧在冷却的钢液中溶解度减小,出现偏析时,毗连于凝固层的母体钢液的含氧量增高,超过了ω[ C ]·ω[ O ]平衡值,于是CO 气泡形成,使钢锭饱含气泡,组织疏松,质量下降。
因此,只有在控制沸腾(沸腾钢)或不出现沸腾(镇静钢)时,才可能获得成分及组织合格的优质钢锭或钢坯。
为此,对于沸腾钢,ω[ O ]需降到0.025%~0.030%,对于镇静钢,ω[ O ]应小于0.005%。
【1】2 脱氧原理2.1 钢液的脱氧不管是哪种炼钢方法,都需要在熔池中供氧去除C、Si、Mn、P等杂质元素,氧化精炼结束后,钢液达到了一定成分和温度。
如果钢水不进行脱氧,连铸胚就得不到正确的凝固组织结构。
钢中氧含量高,还会产生皮下气泡、疏松等缺陷,并加剧硫的危害作用。
而且还会生成过多的氧化物杂质,降低钢的塑性、冲击韧性等力学性能。
因此,必须在出钢或浇注过程中,加脱氧剂适当减少钢液含氧量,除去钢中的过剩氧。
2.2 脱氧剂和脱氧能力炼钢常用的脱氧元素有:硅、锰和铝。
硅:硅的脱氧生成物位SiO2或硅酸铁(FeO·SiO2)。
硅脱氧反应式为:[ Si ] + 2[ O ] = SiO2∆G=—576440+218.2T J/molK=在ω[ O ] [Si]<2%,·值接近1,于是可得ω[Si]%·ω≈a Si ·炉渣碱度越高,SiO 2的活度越小,残余量越低,硅的脱氧效果越好。
各种牌号的Fe-Si 是常用的脱氧剂锰:锰是弱脱氧剂,常用于沸腾钢脱氧,其脱氧产物并不是纯的MnO ,而是MnO 与FeO 的熔体。
锰脱氧反应式可表示为:[Mn]+[O] =(MnO)(l) ∆G θ=—244300+107.6T J/mol[Fe]+[O] =(FeO)[Mn]+ (FeO)= (MnO)+Fe (l)实验测得上述反应的平衡常数: lglg =k MnO ][%)(Mn N N W FeO l MnO ∙=T 6440—2.95 k Mn lg =a Mn N o l MnO W ∙][%)(lg =T12760—5.62 当金属含锰增加时,与之平衡的脱氧产物中的N MnO 也是随之增大。
当N MnO 增大到一定的浓度时,脱氧产物开始有固态的FeO ·MnO 出现铝:铝是强脱氧剂,常用于镇静钢的终脱氧,铝脱氧反应为:2[Al]+3[O] =Al2O3 ∆G θ=—1242400+394.93T J /mol复合脱氧剂:使用两种或多种脱氧元素制成的复合脱氧剂,例如硅锰、硅钙、硅锰铝等复合脱氧剂,复合脱氧剂有以下优点:(1)可以提高脱氧元素的脱氧能力;(2)有利于形成液态的脱氧产物,便于产物的分离和上浮;(3)有利于提高易挥发元素在钢中的溶解度,减少元素的损失,提高脱氧元素的脱氧效率。
【2】3 三种不同脱氧工艺比较3.1 沉淀脱氧沉淀脱氧法是指将脱氧剂加到钢液中,它直接与钢液中的氧反应生成稳定的氧化物,即直接脱氧。
沉淀脱氧效率高,操作简单,成本低,对冶炼时间无影响,但沉淀脱氧的脱氧程度取决于脱氧剂能力和脱氧产物的排除条件。
向钢液中加人与氧的亲和力比铁大的元素,使溶解于钢液中的氧化铁还原,用公式表示如下:x[ M ] + y[ Fe0 ] = ( M x O y ) + yFe这种脱氧法的缺点是随着氧化铁的还原,在钢液中产生了新的氧化物Fe x0y,因此采用这种方法脱氧时,必须创造夹杂物上浮的良好条件。
【3】图3.1成品钢锭氧含量的趋势图3.2 扩散脱氧扩散脱氧是根据氧分定律建立起来的,一般用于电炉还原期,或钢液的炉外精炼。
随着钢液中氧向炉渣中扩散,炉渣中(FeO)逐渐增多,为了使(FeO)保持在低水平,需在渣中加脱氧剂来还原渣中的(FeO),这样可以保证钢液中的氧不断向渣中扩散。
扩散脱氧的产物存在于熔渣中,这样有利于提高钢液个纯洁度,但扩散脱氧的速度慢,时间长,可以通过吹氩搅拌或钢渣混冲等方式加速脱氧进程。
另外,进行扩散脱氧操作前,需换新榨,以防止回磷。
将脱氧剂加入到炉渣中,直接降低炉渣中的氧化铁含量,借分配定律的作用使钢液中的氧化铁逐渐转移到炉渣中来。
平衡状态下,氧在炉渣和钢液之间的分配服从分配定律为:L FeO=,即[%FeO]= L FeO×a(FeO)由上式可见,如人为降低(Fe0),则钢液中的[Fe0]就会扩散进人炉渣。
因此,决定熔池中氧含量的主要因素不是钢液中的含碳量,而是炉渣中的氧化铁含量。
将含氧化铁较低的合成渣置于盛钢桶内与钢液混合,也能得到相同效果。
【4】表3.2 各种钢扩散脱氧工艺优化前后的技术指标对比从表2可以看出,经扩散脱氧工艺优化后,各钢种Si、Mn等成分的收得率提高,Als 损失量降低了0.005%以上,脱氧合金成本大大降低,平均达到3元/t钢以上。
按年产420万t钢计算,年可创效益1 000万元以上。
3.3 真空脱氧真空脱氧法是将钢包内钢液置于真空条件下,通过抽真空打破原有的碳氧平衡,促使碳与氧的反应,达到通过钢中碳除去氧的目的。
此法的优点为脱氧产物是CO,不会污染钢液;CO气泡具有去气和吸附夹杂的作用;CO气泡逸出时,可起到搅拌钢液的作用。
在根本改善钢的质量方面,应用真空脱氧有很大意义,这是因为采用其他脱氧方法不可能完全去除钢中的夹杂物。
真空碳脱氧服从以下热力学规律:[C] + {O} = COlgK=lg==2.003[%O] =如果根据上式近似评价碳在1873 K下的脱氧能力,则当P CO =10-3 Pa时,碳就具有比铝还强的脱氧能力。
前苏联的研究表明,1873 K时,P CO =0.006687 Pa,[O] =(18.2±2.07)×10-5%,[C]×[O] =1.3×10-10。
在真空碳脱氧的过程中吹入100~200 L/min的氩气进行搅拌,为产生CO气泡创造了条件,真空度达0.5乇时解除真空,可以达到钢中游离氧含量100×10-6以下。
初炼炉出钢不加合金及预脱氧剂,钢水中游离氧在500×10-6左右,大包温度在1580℃以上直接入真空位,根据钢液碳含量增碳至0.13%,然后进行真空碳脱氧处理约8 min,真空度达到0.5乇后解除真空,取样吊至LF炉精炼,根据钢种不同直接加入相应量的硅锰合金,后步工序同正常炉次操作。
每炉钢(120 t/炉)降低脱氧剂及石灰消耗量,见下表:【5】表3.3.1 每炉钢降低脱氧剂及石灰消耗情况表3.3.2 每炉钢增加的成本从表3.3.1和表3.3.2可以看出,采用真空碳脱氧工艺后,非过氧化炉次每炉钢可降低成本2229元,对过氧化炉次,由于铝线用量比此工艺多消耗300 m以上,故每炉钢成本可以降低3000元左右。
3.4 复合脱氧依据钢的电弧炉冶炼原理,经过对铁合金炉渣的筛选再处理,采用“SC复合脱氧剂”,它是铁合金生产中的副产品(炉渣),主要成分正是电石渣所需的成分CaC2。
SC复合脱氧剂的化学成分见表3.4.1。
表3.4.1 SC复合脱氧剂的化学成分(%)其中SiCa脱氧反应的自由能变化远低于C的氧化反应:SiCa+3FeO=3Fe+CaSiO3△G1873K=﹣1032.9 KJ 这样,就可以使用复合脱氧剂的方法解决难以获得电石渣或类似电石渣脱氧剂的问题。
表3.4.2 SC复合脱氧剂与Si-Fe-C脱氧剂脱氧效果比较表3.4.2是在冶炼12Mn和ZG230—450钢中使用SC复合脱氧剂和Si-Fe-C粉两种脱氧剂的脱氧效果比较。
可以看出,与Si-Fe-C相比,SC脱氧剂不仅有横好的脱氧效果,而且脱氧速度快、脱氧率高,每炉可缩短冶炼时间。
【6】4 三种脱氧工艺的对比沉淀脱氧法,是目前应用得最广泛的方法。
相当于扩散脱氧和真空扩散法,设备简单,工艺流程也不复杂。
图4 3种脱氧方法的特点对于扩散脱氧法,由于脱氧剂加在渣层内,脱氧反应在渣钢液界面进行,脱氧产物不进入钢液中,就不会沾污钢液,因而在原则上说是冶炼优质钢最好的脱氧方法。
真空脱氧法,对于机器设备和操作精良有较高的要求,可以得到脱氧效果较好的钢液。
复合脱氧法,相对于单一脱氧剂而言,效率有很大的提升。
5 总结通过比较沉淀脱氧、扩散脱氧、真空脱氧以及复合脱氧法,可见不同的工艺各有其优缺点。
应当在生产实践中,有机的结合这4种脱氧工艺。
有效的将复合脱氧剂应用到沉淀、扩散、真空脱氧工艺中。
这样可以大大减少脱氧剂的使用量,同时能加快脱氧速度,降低工人的劳动强度。
结合各种脱氧工艺生产,还可以减低电能消耗,提升钢液质量。
参考文献:【1】钢铁冶金原理(第三版),黄希古,主编,冶金工业出版社.【2】现代冶金学(钢铁冶金卷),朱苗勇,主编,钢铁工业出版社.【3】沉淀脱氧和柔性吹氩搅拌对于提高钢锭质量的分析,姚国平,太原科技,2008.12.【4】炼钢厂150t转炉出钢过程脱氧工艺研究,范启兴,梅山科技,2008增刊(1).【5】精炼过程中的真空碳脱氧试验,李慧勇,宽厚板,2009.8.【6】复合脱氧粉剂在电炉炼钢扩散脱氧中的应用,吉仁龙,铁合金,1996.7.。