硅微工艺湿法刻蚀常见材料刻蚀剂和刻蚀速率
微电子制造技术氧化硅的湿法刻蚀_icaredbd
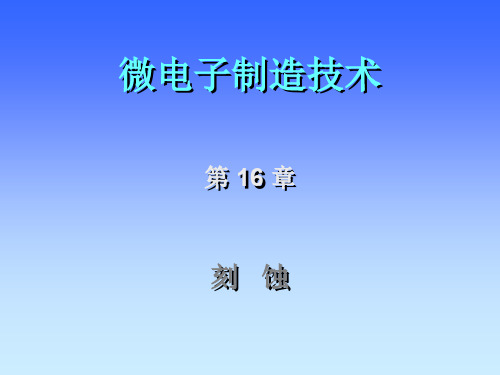
t=刻蚀所用的时间(min)
刻蚀速率通常正比于刻蚀剂的浓度,也与被刻 蚀的图形的几何形状有关。刻蚀的面积越大刻蚀速 率就越慢,因为刻蚀所需要的刻蚀剂气体就越多, 这被称为负载效应。
微电子制造技术
电信学院 微电子学系 7
T = 刻蚀掉的厚度 T
例子; 4. 熟悉湿法刻蚀及其应用; 5. 了解刻蚀检查以及相关的重要的质量测量
方法。
微电子制造技术
电信学院 微电子学系 3
刻蚀原理
刻蚀是利用化学或者物理方法有选择地从硅 片表面去除不需要的材料的过程。刻蚀的基本目标 是在涂胶的硅片上正确地复制掩膜图形。因此,刻 蚀过程中光刻胶层起着有效保护下面的膜层不受浸 蚀的作用。图16.1是常规COMS栅刻蚀工艺示意图。
刻蚀的要求取决于要制作的图形类型。如金 属层、多晶硅栅、隔离槽、通孔等。因为结构的 不同,所以具有大量不同刻蚀参数的材料。
特征尺寸的缩小使刻蚀工艺对尺寸的控制要 求更加严格,也更加难以检测。
微电子制造技术
电信学院 微电蚀参数; 2. 描述干法刻蚀的优点及基本原理; 3. 列举一个介质、硅、金属干法刻蚀的实际
SR =Ef/Er Ef =被刻蚀材料的刻蚀速率 Er =掩膜材料的刻蚀速率
高的选择比可以是100:1
Er
Ef S=
Er
Ef
氮化硅
Oxide
微电子制造技术
Figure 16.8
电信学院 微电子学系 15
刻蚀均匀性
刻蚀均匀性是衡量刻蚀工艺在整个硅片上, 或者整个一批或批与批之间刻蚀能力之间的参数 。均匀性与选择比有密切关系,因为非均匀刻蚀 会产生额外的过刻蚀。保持刻蚀均匀性是保证制 造性能一致的关键。难点在于刻蚀工艺必须在刻 蚀具有不同图形密度的硅片上保证均匀性。
湿法刻蚀工艺技术

湿法刻蚀工艺技术湿法刻蚀是半导体制造工艺中常用的一种加工技术,用于制备微小器件和芯片表面的纹理。
湿法刻蚀工艺技术的基本原理是利用化学反应将半导体表面的材料溶解或腐蚀掉,以形成所需的纹理或结构。
湿法刻蚀的关键是控制刻蚀剂的组成、浓度和刻蚀时间等参数,以实现对半导体材料的精确刻蚀。
常用的刻蚀剂有酸、碱和氧化剂等。
其中,酸性刻蚀剂主要用于硅和多晶硅的刻蚀,碱性刻蚀剂主要用于氮化硅和金属的刻蚀,氧化剂则常用于二氧化硅的刻蚀。
湿法刻蚀工艺技术的步骤通常包括:清洗、预处理、刻蚀和中和等。
首先,需要将待刻蚀的材料进行清洗,以去除表面的杂质和污染物。
然后,进行预处理,包括表面活化和掺杂等步骤,以提高材料的表面质量和电学性能。
接下来,将材料浸泡在刻蚀液中,通过调节刻蚀液的组成和浓度,来控制刻蚀速率和形成的纹理结构。
在刻蚀过程中需要不断搅拌和加热刻蚀液,以保证刻蚀效果的均匀性和稳定性。
最后,对刻蚀后的样品进行中和处理,以去除刻蚀剩余物质的残留。
湿法刻蚀工艺技术在半导体制造中有广泛的应用。
它可以用于制备微细结构,如微孔、微沟槽和微凸起等,用于制备电路和芯片的掩模板。
同时,湿法刻蚀还可以用于改变半导体材料的光学性质和表面形貌,用于制备太阳能电池、光学器件和显示器件等。
湿法刻蚀工艺技术的优点是加工精度高、刻蚀速度快、成本较低,同时具有良好的选择性和均匀性。
然而,湿法刻蚀也存在一些缺点,如对环境的污染、刻蚀剂的废液处理问题等。
在实际应用中,需要注意安全操作,严格控制刻蚀参数,以保证刻蚀效果的稳定性和可靠性。
总的来说,湿法刻蚀工艺技术是半导体制造中常用的一种加工技术,可以实现对半导体材料的精确刻蚀。
它在微电子、光电子和新能源等领域具有重要的应用价值,对推动科技进步和经济发展起到重要作用。
硅体微细加工工艺流程
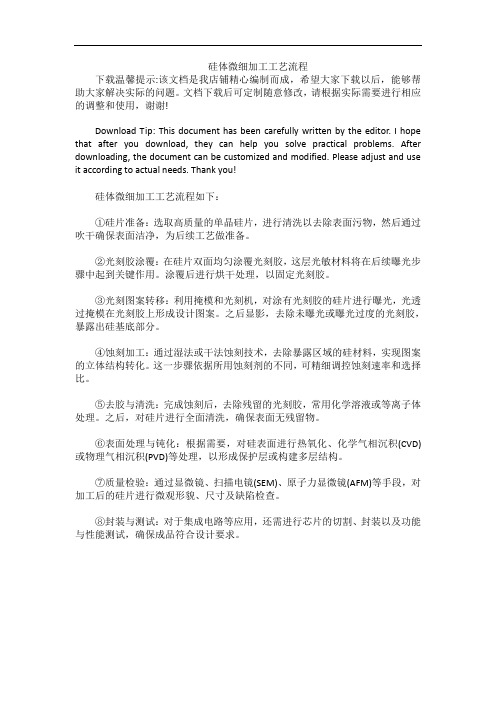
硅体微细加工工艺流程下载温馨提示:该文档是我店铺精心编制而成,希望大家下载以后,能够帮助大家解决实际的问题。
文档下载后可定制随意修改,请根据实际需要进行相应的调整和使用,谢谢!Download Tip: This document has been carefully written by the editor. I hope that after you download, they can help you solve practical problems. After downloading, the document can be customized and modified. Please adjust and use it according to actual needs. Thank you!硅体微细加工工艺流程如下:①硅片准备:选取高质量的单晶硅片,进行清洗以去除表面污物,然后通过吹干确保表面洁净,为后续工艺做准备。
②光刻胶涂覆:在硅片双面均匀涂覆光刻胶,这层光敏材料将在后续曝光步骤中起到关键作用。
涂覆后进行烘干处理,以固定光刻胶。
③光刻图案转移:利用掩模和光刻机,对涂有光刻胶的硅片进行曝光,光透过掩模在光刻胶上形成设计图案。
之后显影,去除未曝光或曝光过度的光刻胶,暴露出硅基底部分。
④蚀刻加工:通过湿法或干法蚀刻技术,去除暴露区域的硅材料,实现图案的立体结构转化。
这一步骤依据所用蚀刻剂的不同,可精细调控蚀刻速率和选择比。
⑤去胶与清洗:完成蚀刻后,去除残留的光刻胶,常用化学溶液或等离子体处理。
之后,对硅片进行全面清洗,确保表面无残留物。
⑥表面处理与钝化:根据需要,对硅表面进行热氧化、化学气相沉积(CVD)或物理气相沉积(PVD)等处理,以形成保护层或构建多层结构。
⑦质量检验:通过显微镜、扫描电镜(SEM)、原子力显微镜(AFM)等手段,对加工后的硅片进行微观形貌、尺寸及缺陷检查。
刻蚀中湿法刻蚀机理

刻蚀中湿法刻蚀机理刻蚀⽅法分为:⼲法刻蚀和湿法刻蚀,湿法刻蚀是将被刻蚀材料浸泡在腐蚀液内进⾏腐蚀的技术,这是各向同性的刻蚀⽅法,利⽤化学反应过程去除待刻蚀区域的薄膜材料,通常SiO2采⽤湿法刻蚀技术,有时⾦属铝也采⽤湿法刻蚀技术,国内的苏州华林科纳在湿法这块做得⽐较好。
下⾯分别介绍各种薄膜的腐蚀⽅法流程:⼆氧化硅腐蚀:在⼆氧化硅硅⽚腐蚀机中进⾏,国内⽬前腐蚀机做的⽐较好的有苏州华林科纳,腐蚀液是由HF、NH4F、与H2O按⼀定⽐例配成的缓冲溶液。
腐蚀温度⼀定时,腐蚀速率取决于腐蚀液的配⽐和SiO2掺杂情况。
掺磷浓度越⾼,腐蚀越快,掺硼则相反。
SiO2腐蚀速率对温度最敏感,温度越⾼,腐蚀越快。
具体步骤为:1、华林科纳设备⼯程师认为将装有待腐蚀硅⽚的⽚架放⼊浸润剂(FUJI FILM DRIWEL)中浸泡10—15S,上下晃动,浸润剂(FUJI FILM DRIWEL)的作⽤是减⼩硅⽚的表⾯张⼒,使得腐蚀液更容易和⼆氧化硅层接触,从⽽达到充分腐蚀;2、将⽚架放⼊装有⼆氧化硅腐蚀液(氟化铵溶液)的槽中浸泡,上下晃动⽚架使得⼆氧化硅腐蚀更充分,腐蚀时间可以调整,直到⼆氧化硅腐蚀⼲净为⽌;3、冲纯⽔;4、甩⼲。
⼆氧化硅腐蚀机理为:H2SiF6(六氟硅酸)是可溶于⽔的络合物,利⽤这个性质可以很容易通过光刻⼯艺实现选择性腐蚀⼆氧化硅。
为了获得稳定的腐蚀速率,腐蚀⼆氧化硅的腐蚀液⼀般⽤HF、NH4F与纯⽔按⼀定⽐例配成缓冲液。
由于基区的氧化层较发射区的厚,以前⼩功率三极管的三次光刻(引线孔光刻)⼀般基极光刻和发射极光刻分步光刻,现在⼤部分都改为⼀步光刻,只有少部分品种还分步光刻,⽐如2XN003,2XN004,2XN013,2XP013等。
但是由于基区的氧化层⼀般⽐发射区的厚,所以刻蚀时容易发⽣氧化区的侵蚀。
⼆氧化硅腐蚀后检查:1、窗⼝内⽆残留SiO2(去胶重新光刻);2、窗⼝内⽆氧化物⼩岛(去胶重新光刻);3、窗⼝边缘⽆过腐蚀(去胶重新光刻);4、窗⼝内⽆染⾊现象(报废);5、氧化膜⽆腐蚀针孔(去胶重新光刻);6、氧化膜⽆划伤等(去胶重新光刻)。
综述报告——刻蚀简介

微加工技术——刻蚀简介自从半导体诞生以来,很大程度上改变了人类的生产和生活。
半导体除了在计算机领域应用之外,还广泛地应用于通信、网络、自动遥控及国防科技领域。
本文主要介绍半导体制造工艺中的刻蚀工艺。
随着半导体制造大规模集成电路技术的发展,图形加工线条越来越细,硅片尺寸越来越大,对刻蚀工艺的要求也越来高。
因此,学习了解刻蚀工艺十分必要。
本文将主要从刻蚀简介、刻蚀参数及现象、干法刻蚀和湿法刻蚀四个方面进行论述。
1、刻蚀简介1.1 刻蚀定义及目的刻蚀就是用化学的、物理的或同时使用化学和物理的方法,有选择地把没有被抗蚀剂掩蔽的那一部分薄膜层除去,从而在薄膜上得到和抗蚀剂膜上完全一致的图形。
刻蚀的基本目的,是在涂光刻胶(或有掩膜)的硅片上正确的复制出掩膜图形[1]。
刻蚀,通常是在光刻工艺之后进行。
通过刻蚀,在光刻工艺之后,将想要的图形留在硅片上。
从这一角度而言,刻蚀可以被称之为最终的和最主要的图形转移工艺步骤。
在通常的刻蚀过程中,有图形的光刻胶层〔或掩膜层)将不受到腐蚀源显著的侵蚀或刻蚀,可作为掩蔽膜,保护硅片上的部分特殊区域,而未被光刻胶保护的区域,则被选择性的刻蚀掉。
其工艺流程示意图如下。
1.2 刻蚀的分类从工艺上分类的话,在半导体制造中有两种基本的刻蚀工艺:干法刻蚀和湿法腐蚀。
干法刻蚀,是利用气态中产生的等离子体,通过经光刻而开出的掩蔽层窗口,与暴露于等离子体中的硅片行物理和化学反应,刻蚀掉硅片上暴露的表面材料的一种工艺技术法[1]。
该工艺技术的突出优点在于,是各向异性刻蚀(侧向腐蚀速度远远小于纵向腐蚀速度,侧向几乎不被腐蚀),因此可以获得极其精确的特征图形。
超大规模集成电路的发展,要求微细化加工工艺能够严格的控制加工尺寸,要求在硅片上完成极其精确的图形转移。
任何偏离工艺要求的图形或尺寸,都可能直接影响产品性能或品质,给生产带来无法弥补的损害。
由于干法刻蚀技术在图形转移上的突出表现,己成为亚微米尺寸下器件刻蚀的最主要工艺方法。
1-干法刻蚀和湿法刻蚀

1 干法刻蚀和湿法刻蚀干法刻蚀是把硅片表面暴露于空气中产生的等离子体,等离子体通过光刻胶中开出的窗口,与硅片发生物理或化学反应,从而去掉暴露的表面材料。
湿法腐蚀是以液体化学试剂以化学方式去除硅片表面的材料。
2刻蚀速率是指在刻蚀过程中去除硅片表面材料的速度,通常用。
A/min表示刻蚀速率=T/t(。
A/min)其中T=去掉的材料厚度t=刻蚀所用的时间为了高的产量,希望有高的刻蚀速率。
3刻蚀选择比指的是同一刻蚀条件下一种材料与另一种刻蚀材料相比刻蚀速率快多少。
他定义为被刻蚀材料的刻蚀速率与另一种材料的刻蚀速率的比。
干法刻蚀的选择比低,通常不能提供对下一层材料足够高的刻蚀选择比。
高选择比意味着只刻除想要刻去的那层。
4干法刻蚀的主要目的完整的把掩膜图形复制到硅片表面上。
优点:刻蚀剖面是各向异性,具有非常好的侧壁剖面控制,好的CD控制最小的光刻胶脱落或粘附问题好的片内,片间,批次间的刻蚀均匀性较低的化学制品使用和处理费用不足:对下层材料的差的刻蚀选择比,等离子体带来的器件损伤和昂贵的设备。
5化学机理:等离子体产生的反应元素与硅片表面的物质发生反应,为了获得高的选择比,进入腔体的气体都经过了慎重选择。
等离子体化学刻蚀由于它是各向同性的,因而线宽控制差。
物理机理:等离子体产生的带能粒子在强电场下朝硅片表面加速,这些离子通过溅射刻蚀作用去除未被保护的硅片表面材料。
6基本部件:发生刻蚀反应的反应腔,一个产生等离子体的射频电源,气体流量控制系统,去除刻蚀生成物和气体的真空系统。
氟刻蚀二氧化硅,氯和氟刻蚀铝,氯,氟和溴刻蚀硅,氧去除光刻胶。
7z微波激励源来产生高密度等离子体。
ECR反应器的一个关键点是磁场平行于反映剂的流动方向,这使得自由电子由于磁力的作用做螺旋形运动。
当电子的回旋频率等于所加的微波电场频率时,能有效把电能转移到等离子体中的电子上。
这种振荡增加了电子碰撞的可能性,从而产生高密度的等离子体,获得大的离子流。
MEMS和半导体工艺中的湿法腐蚀配方

MEMS和半导体工艺材料配比苏州能斯达电子科技有限公司的工程师整理了MEMS和半导体工艺中接近50种材料的湿法腐蚀的刻蚀液及配比,趁着新年,给大家送一份豪华大礼包。
1.铝-Aluminum2.砷化铝镓-Aluminum Gallium Arsenide1.1:1:30 –H2SO4:H2O2–60 Å/sec2.8:3:400 –NH3:H2O2:H2O–25 Å/sec3.1:1:10 –HF:H2O2:H2o–80 Å/sec3.三氧化二铝/铝/蓝宝石-Aluminum Trioxide / Alumina /Sapphire1.1:1:3 –NH4OH:H2O2:H2O–80 ℃2.10% Br2:MeOH3.7ml:4g –H3PO:Cr2O34.锑-Antimony1.1:1:1 –HCl:HNO3:H2O2.90:10:1 –H2O:HNO3:HF3.3:3:1:1 –H3PO4:HNO3:CH3COOH:H2O <<3min/1000A 50℃5.铋-Bismuth1.10:1 –H2O:HCl6.黄铜-Brass1.FeCl32.20% NHSO57.青铜-Bronze1.1% CrO38.碳-Carbon1.H3PO4:CrO3:NaCN2.50% KOH (or NaOH)–boiling3.HNO3 concentrated4.H2SO4 concentrated5.3:1 –H2SO4:H2O29.铬 -Chromium1.2:3:12 KMnO4:NaOH:H2O2.3:1 –H2O:H2O23.HCl concentrated and dilute4.3:1 –HCl:H2O25.2:1 –FeCl:HCl6.Cyantek CR-7s (Perchloric based) 7 min/micron (24A/s new)7.1:1 –HCl:glycerine 12min/micron after depassivation8.1:3 –[50gNaOH+100mlH2O]:[30gK3Fe(CN)6+100mlH2O] 1hr/micron10.钴-Cobalt1.1:1 H2O:HNO32.3:1 HCl:H2O211.铜-Copper1.30% FeCl3 saturated solution2.20% KCN3.1:5 –H2O:HNO34.HNO3 concentrated and dilute5.1:1 –NH4OH:H2O26.1:20 –HNO3:H2O27.4:1 –NH3:H2O28.1:1:1 –H3PO4:HNO3:HAc9.5ml:5ml:4g:1:90ml –HNO3:H2SO4:CrO3:NH4Cl:H2O10.4:1:5 –HCL:FeCl3:H2O12.环氧树脂-Epoxies1.General Polymer Etch2.5:1 –NH4OH:H2O2–120 ℃3.Gold Epoxy4.3:1:10 HNO3:HCl:H2O5.Silver Epoxy6.1:3 –HF:HNO37.Aluminum Epoxy8.H2SO4 –hot9.SU8 cured10.3:1 –H2SO4:H2O2–hot13.砷化镓-Gallium Arsenide1. 1.5%-7.5% –Br2 in CH3OH2.1:1 –NH4OH:H2O23.20:7:973 –NH4OH:H2O2:H2O4.40:1:40 –H3PO4:H2O2:H2O5.3:1:50 –H3PO4:H2O2:H2O6.33-66% –HNO3–red fuming etches more rapidly than whitefuming7.1:1 –HF:HNO38.1:1 –H2SO4:H2O29.1:1:30 –H2SO4:H2O2–60 Ås/sec10.8:3:400 –NH3:H2O2:H2O–30 Ås/sec, isotropic11.1:1:10 –HF:H2O2:H2o–80 Ås/sec14.锗-Germanium1.HF:HNO3:H2O2.1:1:1 –HF:HNO3:HAc3.7:1:x HF:HNO3:glycerin 35c 75-100 microns/hour, 100℃775microns/hour4.KF–pH > 65.1:25 NH3OH:H2O21000 Å/min15.金-Gold1.Aqua Regia 3:1 –HCl:HNO3 10-15 microns/min RT, 25-50microns/min 35 ℃2.Chrome Regia 3:10-20% HCl:CrO33.H2SeO4–Temp should be hot, etch is slow4.KCN in H20–good for stripping gold from alumina, quartz, sapphiresubstrates, semiconductor wafers and metal parts5.4g:2g:10ml –KI:I2:H2O Hot (70℃) 280 nm/min6.1:2:3 –HF:HAc:HNO37.30:30:50:0.6 –HF:HNO3:HAc:Br28.NaCN:H2O29.7g:25:g:100ml –KI:Br2:H2O10.9g:1g:50ml –KBr:Br2:H2O 800 nm/min11.9g:1g:50ml –NaBr:Br2:H2O 400nm/min12.400g:100g:400ml –I2:KI:H2O 55℃1270Ås/sec13.1:2:10 –I2:KI:H2O14.Au mask etch 4g:1g:40ml –KI:I2:H2O 1min/micron16.铪-Hafnium1.20:1:1 –H2O:HF:H2O217.铟-Indium1.Aqua Regia 3:1 –HCl:HNO3 hot2.HCl boiling, fast3.IPA4.EOH5.MeOH6.Rare Earth Indium Etchants18.砷化铟镓-Indium Gallium Arsenide1.1:1:20 –H2SO4:H2O2:H2O–30 Ås/sec19.镓铟磷-Indium Gallium Phosphide1.conc HCl–fast20.磷化铟-Indium Phosphide1.1:1 –HCl:H3PO4–fast21.磷化铟氧化物腐蚀剂-Indium Phosphide Oxide Etchants1.NH4OH22.ITO-Indium Tin Oxide1.1:1 –HCl:H2O8 Ås/sec2.1:1:10 –HF:H2O2:H2O125 Ås/sec23.铱-Iridium1.Aqua Regia 3:1 –HCl:HNO3 hot24.铁-Iron1.1:1 –H2O:HCL2.1:1 –H2O:HNO33.1:2:10 –I2:KI:H2O25.铅-Lead1.1:1 –HAc:H2O226.镁-Magnesium1.10ml:1g –H2O:NaOH followed by 5ml:1g –H2O:CrO3 27.钼-Molybendum1.1:1 –HCl:H2O228.镍-Nickel1.1:1:1 –HNO3:HAc:Acetone2.1:1 –HF:HNO33.30% FeCl34.3:1:5:1 –HNO3:H2SO4:HAc:H2O 85 C 10 microns/min5.3:7 –HNO3:H2O6.1:1 –HNO3:HAc7.10% g/ml Ce(NH4)2(NO3)6:H208.HF, concentrated –slow etchant9.H3PO4 –slow etchants10.HNO3 –rapid etchant11.HF:HNO3 –etch rate determined by ratio, the greater the amountof HF the slower the reaction12.4:1 –HCl:HNO3 –increase HNO3 concentration increases etchrate13.30% FeCl314.5g:1ml:150ml –2NH4NO3.Ce(NO3)3.4(H2O):HNO3:H2O –decreasing HNO3 amount increases the etch rate15.3:3:1:1 –H3PO4:HNO3:CH3COOH:H2O ~15min/micron @ RT withair exposure every 15 seconds29.铌-Niobium1.1:1 –HF:HNO330.钯-Palladium1.Aqua Regia 3:1 –HCl:HNO3 hot31.光刻胶-Photoresist (AZ type)1.General Polymer2.5:1 –NH4OH:H2O2 –120 ℃3.5:1 –H2SO4:H2O24.H2SO4:(NH4)2S2O85.Acetone32.铂-Platinum1.Aqua Regia 3:1 –HCl:HNO3 Hot2.Molten Sulfur33.聚合物-Polymer1.5:1 –NH4OH:H2O2 –120 ℃2.3:1 –H2SO4:H2O234.聚合物-Polymer1.1:1 –HF:H2O2.1:1 –HF:HNO33.Sodium Carbonate boiling4.HF conc35.铼、铑和钌-Rhenium, Rhodium and Ruthenium1.Aqua Regia 3:1 –HCl:HNO3 –Hot36.硅-Silicon1.64:3:33 –HNO3:NH4F:H2O 100 Ås/s2.61:11:28 –ethylenediamine:C6H4(OH)2:H2O 78 Ås/s3.108ml:350g:1000ml –HF:NH4F:H2O slow 0.5 Ås/min4.1:1:50 –HF:HNO3:H2O slow etch5.KCl dissolved in H2O6.KOH:H2O:Br2/I27.KOH –see section on KOH etching of silicon8.1:1:1.4:0.15%:0.24% –HF:HNO3:HAc:I2:triton9.1:6:3 –HF:HNO3:HAc and 0.19 g NaI per 100 ml solution10.1:4 –Iodine Etch:HAc11.0.010 N NaI12.NaOH13.HF:HNO314.1:1:1 –HF:HNO3:H2O37.二氧化硅/石英/玻璃-Silicon Dioxide / Quartz / Glass1.BOE 1:5:5 HF:NH4HF:H2O 20 Ås/s2.HF:HNO33.3:2:60 HF:HNO3:H20 2.5 Ås/sec at RT4.BHF 1:10, 1:100, 1:20 HF:NH4F(sat)5.Secco etch 2:1 HF:1.5M K2Cr2O76.5:1 NH4.HF:NaF/L (in grams)7.1g:1ml:10ml:10ml NH4F.HF:HF:H2O:glycerin8.HF –hot9.1:1 1:15, 1:100 HF:H2O10.BOE HF:NH4F:H2O11.1:6 BOE:H2O12.5:43, 1:6 HF:NH4F(40%)13.NaCO3 100 ℃8.8 mm/h14.5% NaOH 100 ℃150 mm/h15.5% HCl 95 ℃0.5mm/day16.KOH see KOH etching of silicon dioxide and silicon nitride38.氮化硅-Silicon Nitride1.1:60 or 1:20 HF:H2O 1000-2000 Ås/min2.BHF 1:2:2 HF:NH4F:H2O slow attack –but faster for siliconoxynitride3.1:5 or 1:9 HF:NH4F (40%)0.01-0.02 microns/second4.3:25 HF:NH4F.HF(sat)5.50ml:50g:100ml:50ml HF:NH4F.HF:H2O:glycerin –glycerinprovides more uniform removal6.BOE HF:NH4F:H2O7.18g:5g:100ml NaOH:KHC8H4O4:H2O boiling 160 Ås/min, betterwith silicon oxynitride8.9:g25ml NaOH:H20 –boiling 160Ås/min9.18g:5g:100ml NaOH:(NH4)2S2O8:H2O –boiling 160 Ås/min10.A) 5g:100ml NH4F.HF:H2O B)1g:50ml:50ml I2:H2O:glycerin –mixA andB 1:1 when ready to use. RT 180 A/min39.银-Silver1.1:1 NH4OH:H2O22.3:3:23:1 H3PO4:HNO3:CH3COOH:H2O ~10min/100Ås3.1:1:4 NH4OH:H2O2:CH3OH .36micron/min resist5.1-8:1HNO3:H2O6. 1 M HNO3 + light40.不锈钢-Stainless Steel1.1:1 HF:HNO341.钽-Tantalum1.1:1 HF:HNO342.锡-Tin1.1:1 HF:HCL2.1:1 HF:HNO33.1:1 HF:H2O4.2:7 HClO4:HAc43.钛-Titanium1.50:1:1 H2O:HF:HNO32.20:1:1 H2O:HF:H2O23.RCA-1 ~100 min/micron4.x%Br2:ethyl acetate –HOT5.x%I2:MeOH –HOT6.HF:CuSO47.1:2 NH4OH:H2O28.1:2:7, 1:5:4, 1:4:5(18 microns/min), 1:1:50 HF:HNO3:H2O9.COOHCOOH:H2O –any concentration11.1:9 HF:H2O –12 Ås/min12.HF:HCL:H2O13.HCL –conc14.%KOH –conc15.%NaOH- conc16.20% H2SO4 1 micron/minl3COOC2H518.25%HCOOH19.20%H3PO420.HF44.钨-Tungsten1.1:1 HF:HNO32.1:1 HF:HNO3 –thin films3.3:7 HF:HNO34.4:1 HF:HNO3 –rapid attack5.1:2 NH4OH:H2O2 –thin films good for etching tungsten fromstainless steel, glass, copper and ceramics. Will etch titanium aswell.6.305g:44.5g:1000ml K3Fe(CN)6:NaOH:H2O –rapid etch7.HCl –slow etch (dilute or concentrated)8.HNO3 –very slow etch (dilute or concentrated)9.H2SO4 –slow etch (dilute or concentrated)10.HF –slow etch (dilute or concentrated)11.H2O212.1:1, 30%:70%, or 4:1 HF:HNO313.1:2 NH4OH:H2O214.4:4:3 HF HNO3:HAc15.CBrF3 RIE etch16.305g:44.5g:1000ml K3Fe(CN)6:NaOH:H2O –very rapid etch17.HCl solutions –slow attack18.HNO3 –slight attack19.Aqua Regia 3:1 HCL:HNO3 –slow attack when hot or warm20.H2SO4 dilute and concentrated –slow etch21.HF dilute and concentrated –slow etch22.Alkali with oxidizers (KNO3 and PbO2) –rapid etch23.H2O245.钒-Vanadium1.1:1 H2O:HNO32.1:1 HF:HNO346.锌-Zinc1.1:1 HCl:H2O2.1:1 HNO3:H2O47.锆-Zirconium1.50:1:1 H2O:HF:HNO32.20:1:1 H2O:HF:H2O2更多精彩内容欢迎关注MEMSVIEW微视界。
MEMS中硅的深度湿法刻蚀研究

用 F r ay uf 4 o m T ls r ¥ C型 台阶仪 测试 刻蚀 深 度 ,S 7 0 J M6 0 F型 扫描 电子 显 微 镜 ( E 表 征 刻 蚀后 S M)
关键 词 : 机 电 系 统 ; 法 刻蚀 ;深 度 刻 蚀 ; 蚀 速 率 ; 面 粗 糙 度 微 湿 刻 表
.
中 图 分 类 号 : N4 5 T 0
文献 标 志 码 : A
随着 电子元 器件 的小 型化发 展 , 机 电系统 ( MS 已成 为制 作微 机 械 、 感 器 、 制 电路 等微 器 微 ME ) 传 控 件 及其 集成 于芯 片的关 键技 术. 由于芯 片 的集成 和制 造多 以硅 为基体 , 为硅 基体加 工 中关键 技 术 的硅 作 深度湿 法刻蚀 被广 泛应 用于 实际 生产 中 , 用它 可制 作薄 膜 腔声 谐振 器 ( B 利 F AR) 的空 腔 、 导体 激光 器 半 的谐振 腔等硅 微机 械结 构口 ]硅 的刻蚀质 量 , . 包括 刻蚀 的各 向异 性 、 率 和表 面 平 整度 , 诸 多 因素 的 速 受 影响 , : 如 腐蚀 液 的浓度 、 温度 和各 种添 加剂 等口 ] 本文 对硅 湿 法 刻蚀 中可 能存 在 的众 多影 响 因 素作 了 “. 详细 的探讨 , 综合 得到 了最佳 工艺 条件 , 其结 果可 直接 应用 于 ME MS工艺生 产 中.
1 实验
采 用 P型 (0 ) 面抛 光硅 片 , 10双 用标 准 R A 工艺 对其 清洗 , C 然后 两 面都用 P - VD沉 积 ss 1 0 EC i ( 0 N n / i 1 0n 作 为掩 膜层 . 用 光刻 工 艺 制 作 出 一 系列 的方 孔 图形 , CHF m) SO (0 m) 利 以 。和 O 的混 合 气 体
硅微工艺湿法刻蚀常见材料刻蚀剂和刻蚀速率

35
Si3N41/min
SiO22-5/min
掺杂浓度>5X1010cm-3时,刻蚀速率降低到1/50
有毒性,易失效,需与氧气隔离,很少氢气,硅酸盐沉淀
四甲基氢氧化氨TMAH/水/90℃
SiO2刻蚀速率比100硅低四个数量级
掺杂浓度>4X1020cm-3时,刻蚀速率降低到1/40
与IC兼容,易操作,表面光滑,研究不充分
铜
H2O 70mL+FeCl330g,50℃
7um/min
铬
HCl 1mL
甘油1mL
min
HCl 1mL
饱和CeSO49mL
min
NaOH 1g+H2O 2mL 1mL
K3FeCN61g+H2O 3mL 3mL
钼
H3PO45mL
HNO33mL
H2O 2mL
抛光腐蚀
K3FeCN611g
KOH 10g
H2O 150mL
1um/min
钨
KH2PO434g
KOH
K3FeCN633g
用水稀释至1L
min
铂
HCl 3mL
HNO31mL
20um/min,腐蚀之前在HF中浸泡30S
HCl 7mL
HNO31mL
H2O 8mL
85℃
钯
HCl 1mL
HNO310mL
CH3COOH 10mL
KI 4g
I21g
H2O 40mL
min
硅常见各向异性刻蚀
硅微工艺湿法刻蚀常见材料刻蚀剂和刻蚀速率
各种材料的腐蚀剂和腐蚀速率
材料
半导体材料单晶硅刻蚀方法
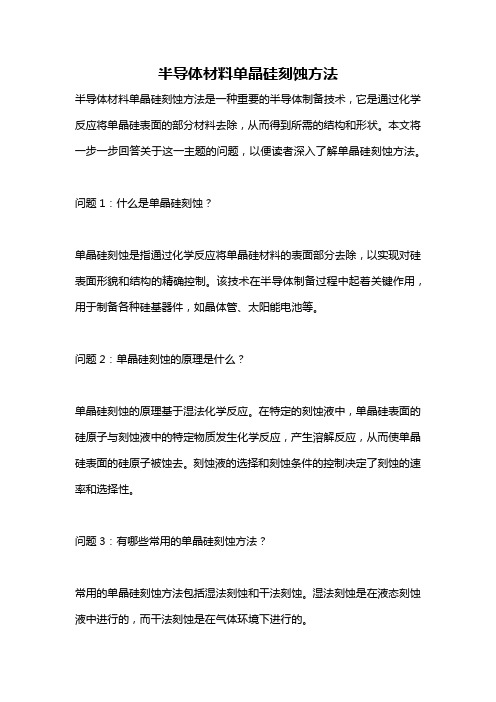
半导体材料单晶硅刻蚀方法半导体材料单晶硅刻蚀方法是一种重要的半导体制备技术,它是通过化学反应将单晶硅表面的部分材料去除,从而得到所需的结构和形状。
本文将一步一步回答关于这一主题的问题,以便读者深入了解单晶硅刻蚀方法。
问题1:什么是单晶硅刻蚀?单晶硅刻蚀是指通过化学反应将单晶硅材料的表面部分去除,以实现对硅表面形貌和结构的精确控制。
该技术在半导体制备过程中起着关键作用,用于制备各种硅基器件,如晶体管、太阳能电池等。
问题2:单晶硅刻蚀的原理是什么?单晶硅刻蚀的原理基于湿法化学反应。
在特定的刻蚀液中,单晶硅表面的硅原子与刻蚀液中的特定物质发生化学反应,产生溶解反应,从而使单晶硅表面的硅原子被蚀去。
刻蚀液的选择和刻蚀条件的控制决定了刻蚀的速率和选择性。
问题3:有哪些常用的单晶硅刻蚀方法?常用的单晶硅刻蚀方法包括湿法刻蚀和干法刻蚀。
湿法刻蚀是在液态刻蚀液中进行的,而干法刻蚀是在气体环境下进行的。
问题4:湿法刻蚀有哪些常见方法?湿法刻蚀的常见方法包括浸没刻蚀、喷射刻蚀和微影刻蚀。
浸没刻蚀是将单晶硅材料浸泡在特定刻蚀液中,通过溶解反应将硅表面蚀去。
这种方法适用于制备平面硅晶圆。
喷射刻蚀是将刻蚀液以高速喷射到单晶硅表面,通过物理冲击和化学反应共同作用,实现刻蚀。
这种方法适用于制备具有复杂结构的硅器件。
微影刻蚀是将光刻胶覆盖在单晶硅表面,然后使用光刻技术形成所需的图形,在特定刻蚀液中进行刻蚀。
这种方法通常用于制备微电子器件。
问题5:干法刻蚀有哪些常见方法?干法刻蚀的常见方法包括物理刻蚀和化学气相刻蚀。
物理刻蚀是利用高能粒子(如离子束)或高能光束对单晶硅表面进行刻蚀。
这种方法具有高速、高精度的特点,适用于制备微纳米器件。
化学气相刻蚀是将刻蚀气体在高温条件下与单晶硅表面进行化学反应,产生刻蚀。
这种方法具有高选择性和均匀性,适用于制备复杂结构的硅器件。
问题6:单晶硅刻蚀的关键参数和影响因素有哪些?单晶硅刻蚀的关键参数包括刻蚀速率、刻蚀选择性、表面粗糙度和侧壁质量。
各向同性湿法腐蚀

例2:Si采用HNO3和HF腐蚀(HNA)
首先 然后 所以,总方程式是
在该腐蚀剂中加入醋酸,可以限制硝酸的离解。
各向同性湿法腐蚀
例3:Si采用KOH腐蚀
各向异性
Si + 2OH- + 4H2O Si(OH)2++ + 2H2 + 4OH-
硅湿法腐蚀由于晶向而产生的各向异性腐蚀
各向异性湿法腐蚀
微透镜
优点: 其体积小、重量轻、便于集成化、阵列化等
应用: 微透镜阵列在微光学系统中有着重要而广泛 的应用,如可用于光信息处理、光计算、光 互连、光数据传输、生成二维点光源,也可 用于复印机、图像扫描仪、传真机、照相机, 以及医疗卫生器械中。
硅晶圆模具(wafer-scale mold)的制备
5. K. Furuya, K. Nakanishi, R. Takei, E. Omoda, M. Suzuki et al. Nanometer-scale thickness control of amorphous silicon using isotropic wet-etching and low loss wire waveguide fabrication with the etched material . Appl. Phys. Lett..2012, 100, 251108
8. M. Baranski, J. Albero, R. Kasztelanic,C. Goreckia. A numerical model of wet isotropic etching of silicon molds for microlenses fabrication [J]. Journal of The Electrochemical Society,.2011, 158(11):681~688
硅微工艺湿法刻蚀常见材料刻蚀剂和刻蚀速率
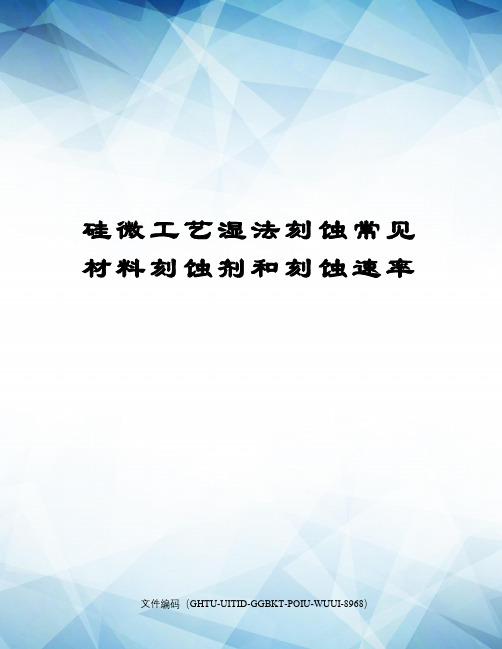
用水稀释至1L
160.0nm/min
铂
HCl3mL
HNO31mL
20um/min,腐蚀之前在HF中浸泡30S
HCl7mL
HNO31mL
H2O8mL
40.0-50.0nm/min,85℃
钯
HCl1mL
HNO310mL
CH3COOH10mL
KI4g
I21g
H2O40mL
100.0nm/min
1.0
12.5-50
SiO2刻蚀速率比(100)硅低四个数量级
掺杂浓度>4X1020cm-3时,刻蚀速率降低到1/40
与IC兼容,易操作,表面光滑,研究不充g+H2O2mL)1mL
(K3Fe(CN)61g+H2O3mL)3mL
25.0-100.0nm/min
钼
H3PO45mL
HNO33mL
H2O2mL
抛光腐蚀
K3Fe(CN)611g
KOH10g
H2O150mL
1um/min
钨
KH2PO434g
KOH13.4g
金
HCl3mL
HNO31mL
25-50um/min
KI4g
I21g
H2O40mL
0.5-1um/min
银
NH4OH1mL
H2O21mL
CH3OH4mL
360.0nm/min,腐蚀后快速清洗
铜
H2O70mL+FeCl330g,50℃
7um/min
铬
HCl1mL
甘油1mL
80.0nm/min
HCl1mL
硅微工艺湿法刻蚀常见材料刻蚀剂和刻蚀速率
微电子加工中的湿法蚀刻技术

微电子加工中的湿法蚀刻技术在微电子加工中,人们通常使用蚀刻技术来制造微电子元器件。
蚀刻技术是一种在表面覆盖涂层的基板或硅片上通过化学反应从上面腐蚀掉一部分薄膜的工艺。
蚀刻技术分为干法和湿法两种,而本文将重点介绍一种常见的湿法蚀刻技术。
一、湿法蚀刻技术简介湿法蚀刻技术是一种利用溶剂和氧化剂等化学液体溶解材料的方法,从而在光刻工艺后将表面覆盖的光刻胶或金属掩模起模后的所需槽口或者图形刻写到基板表面的过程。
在微电子加工中,湿法蚀刻技术被广泛应用于制作电路板,芯片和其他微电子器件。
二、湿法蚀刻技术的优势与干法蚀刻技术相比,湿法蚀刻技术具有许多优势。
首先,它可以实现亚微米级高分辨率,可以在非常小的表面区域内进行刻写。
其次,湿法蚀刻技术可以准确地控制腐蚀速度,从而实现所需的形状和尺寸,提高制造效率和良率。
第三,相对于干法蚀刻技术,湿法蚀刻技术更加适用于大规模生产,且可选择多种不同的湿法溶液以获得合适的蚀刻速率和剖面特征。
三、湿法蚀刻技术的步骤湿法蚀刻技术通常包含以下几个步骤:1.基板清洗 - 清洗基板以确保表面没有灰尘和污垢,从而保证成品质量。
2.光刻制备 - 将光刻胶或其他掩膜材料盖在基板上。
3.曝光 - 利用掩膜进行曝光处理,并通过曝光方式使掩膜达到所需形状。
4.腐蚀 - 放入湿法溶液进行腐蚀刻蚀。
5.去除光刻胶 - 溶解光刻胶以使后续步骤成为可能。
6.清洗 - 清洗基板以暴露所需形状。
四、湿法蚀刻技术的注意事项在使用湿法蚀刻技术时,有一些需要注意的事项。
例如,湿法蚀刻技术中需要频繁使用化学物质,特别需要注意对化学品的安全管理充分,需要在严格的实验室条件下进行操作。
此外,由于微小的误差可能会导致整个制造过程失败,湿法蚀刻技术需要高度精确的控制,需要使用高质量的设备和材料。
总之,湿法蚀刻技术是制造微电子器件中极其重要的工艺之一,其优点包括了高准确度、可大规模生产等,但需要注意安全管理及高度精确的控制等问题。
硅微工艺湿法刻蚀常见材料刻蚀剂和刻蚀速率
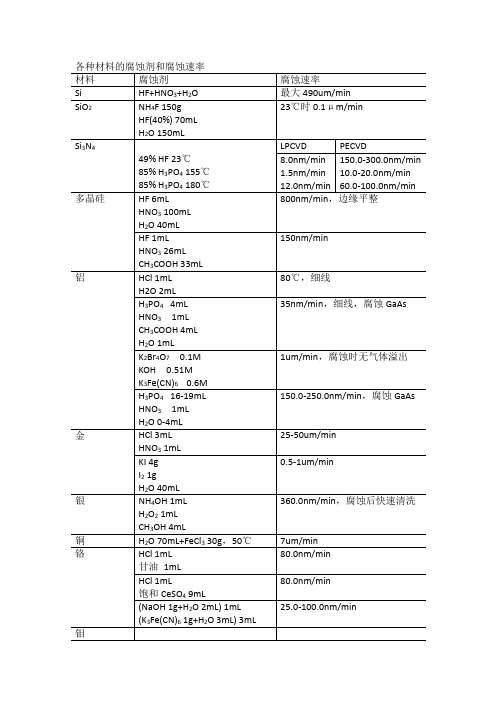
材料
腐蚀剂
腐蚀速率
Si
HF+HNO3+H2O
最大490um/min
SiO2
NH4F 150g
HF(40%) 70mL
H2O 150mL
23℃时0.1μm/min
Si3N4
49% HF 23℃
85% H3PO4155℃
85% H3PO4180℃
LPCVD
PECVD
8.0nm/min
1.5nm/min
12.0nm/min
150.0-300.0nm/min
10.0-20.0nm/min
60.0-100.0nm/min
多晶硅
HF 6mL
HNO3100mL
H2O 40mL
800nm/min,边缘平整
HF 1mL
HNO326mL
CH3COOH 33mL
150nm/min
铝
HCl 1mL
金
HCl 3mL
HNO31mL
25-50um/min
KI 4g
I21g
H2O 40mL
0.5-1um/min
银
NH4OH 1mL
H2O21mL
CH3OH 4mL
360.0nm/min,腐蚀后快速清洗
铜
H2O 70mL+FeCl330g,50℃
7um/min
铬
HCl 1mL
甘油1mL
80.0nm/min
掺杂浓度>1020cm-3时,刻蚀速率降低到1/20
与IC不兼容,对氧化层腐蚀过快,大量H2气泡
邻苯二酚,乙二胺,水(EDP)/Pyrazine/115℃
1.25
sio2湿法刻蚀工艺

sio2湿法刻蚀工艺Sio2湿法刻蚀工艺引言:Sio2湿法刻蚀工艺是一种常用的微纳加工技术,广泛应用于半导体器件制造和微电子技术领域。
本文将就Sio2湿法刻蚀工艺的原理、步骤和应用进行详细阐述,以便读者对该工艺有更深入的了解。
一、Sio2湿法刻蚀工艺的原理Sio2湿法刻蚀工艺是通过将硅基片浸泡在含有化学溶液的反应槽中,利用化学反应来去除硅基片上的Sio2膜。
该工艺的刻蚀速率可通过调节溶液中的温度、浓度和搅拌等因素来控制。
二、Sio2湿法刻蚀工艺的步骤Sio2湿法刻蚀工艺包括预处理、刻蚀和清洗等步骤。
1. 预处理:在进行Sio2湿法刻蚀前,需要对硅基片进行预处理。
首先,将硅基片放入去离子水或酸性溶液中进行清洗,去除表面的杂质和有机物。
然后,将硅基片放入HF酸中进行去氧化处理,以去除硅基片表面的氧化层。
2. 刻蚀:预处理后的硅基片放入含有刻蚀溶液的反应槽中进行刻蚀。
刻蚀溶液通常由HF酸和H2O2氧化剂组成。
刻蚀过程中,HF酸起到去除Sio2膜的作用,而H2O2氧化剂则提供刻蚀反应所需的氧气。
3. 清洗:刻蚀完成后,需要对硅基片进行清洗,以去除残留的刻蚀溶液和产生的杂质。
一般采用纯水或酸性溶液进行清洗,然后用氮气吹干硅基片。
三、Sio2湿法刻蚀工艺的应用Sio2湿法刻蚀工艺在半导体器件制造和微电子技术领域具有广泛的应用。
1. 刻蚀掩膜制备:Sio2湿法刻蚀可用于制备掩膜。
在制备半导体器件中,需要在硅基片表面涂覆一层Sio2膜作为掩膜,然后通过刻蚀去除掩膜上不需要的部分,从而形成所需的器件结构。
2. 制备微纳结构:Sio2湿法刻蚀还可用于制备微纳结构。
通过在硅基片上涂覆一层Sio2膜,并利用刻蚀工艺去除不需要的部分,可以制备出微纳米尺度的结构,如微通道、微孔等。
3. 表面处理:Sio2湿法刻蚀还可用于表面处理。
通过刻蚀硅基片表面的Sio2膜,可以改变硅基片的表面性质,如增加表面粗糙度、改变表面能等,从而实现对硅基片的功能改善。
干法刻蚀和湿法刻蚀制备硅微尖的比较

干法刻蚀和湿法刻蚀制备硅微尖的比较王维彪 金长春 赵海峰王永珍 殷秀华 范希武(中国科学院长春物理研究所,长春 130021)梁静秋 姚劲松(中国科学院长春光学精密机械研究所,长春 130022)摘要 主要研究了用干法刻蚀和各向同性湿法刻蚀的方法在〈100〉晶面和〈111〉晶面的单晶硅衬底上制备硅微尖.结果表明干法刻蚀和〈111〉晶面的硅衬底各向同性湿法腐蚀容易制备出顶端曲率半径比较小的硅微尖,通过实验,最后得到曲率半径10~20nm 的硅微尖.关键词 硅微尖,冷阴极,干法刻蚀,湿法刻蚀1 引 言硅微尖场发射阵列是真空微电子器件的重要电子源,在FED 及微电子器件中有着广泛的应用前景.由于它和微电子集成工艺兼容,硅工艺成熟,从而得到人们的重视.自从H .F .Gray 制备出硅微尖阵列[1],现已发展了多种方法制备硅微尖阵列,比较典型的有干法刻蚀和湿法刻蚀.我们研究了干法刻蚀和湿法刻蚀两种方法对硅微尖的形成及顶端曲率半径的影响,以及用不同直径的图形刻蚀硅微尖时的形状及对硅微尖的纵横比(asp ect 2rati o )的影响.2 硅微尖的制备过程实验选用单面抛光〈111〉和〈100〉晶向的单晶硅衬底,电阻率分别为138 c m 和108c m .衬底经过氧化、光刻腐蚀后进行干法刻蚀和湿法刻蚀.干法刻蚀:采用的设备为磁控反应离子刻蚀机.所用的气体为SF 6和O 2气的混合气体,压强为:13Pa ,功率为:100W ,频率为:13.56M H z.湿法刻蚀:采用的腐蚀剂为H F HNO 3 H 2O =1.5 15 5的混合液.将样品放入溶液中进行刻蚀,时间根据需要确定.刻蚀出的微尖样品用扫描电镜(SE M )进行观察.3 结果和讨论制备硅微尖的毛坯形状对硅微尖的质量有很大的关系,只有凹面的原坯才可以制备出顶端曲率半径比较小的硅微尖.对于干法刻蚀来说,制备具有凹面的硅尖原坯,晶面的选择对原坯的形状影响不大.对于湿法刻蚀,晶面的选择对原坯的形状影响很大.为了用湿法刻蚀制备具有凹面的硅尖原坯,我们选择了〈111〉面单晶硅衬底制备硅微尖.1)干法刻蚀制备硅微尖所用〈100〉晶向的单晶硅作衬底,其工艺过程如下图1所示.干法刻蚀的腐蚀机理比较复杂,它既有化学反应又有物理的过程,纵向反应速率和横向反应速率的选择很重要.如果横向反应速率大了,则刻蚀出的硅尖原坯高度不够,影响其纵横比,而且经氧化腐蚀后制备出的硅尖的曲率也不理想.第19卷 第3期发 光 学 报V o l.19,N o.31998年9月 CH I N ESE JOU RNAL O F LUM I N ESCEN CE Sep t.,1998图1 干法刻蚀制备硅微尖的工艺示意图F ig .1 T he cou rse illu strati on of Si 2ti p s fab ricati on by dry etch ing .我们知道,硅尖高度小,减小了绝缘层厚度,使栅极和衬底之间的电容加大,击穿电压阈值降低,使栅极加电压受到限制.所以选择腐蚀很重要.我们选择纵向腐蚀速率大于横向腐蚀速率,增大硅微尖的原坯高度,以便于提高硅尖的纵横比,如图2所示的硅尖原坯是提高纵向刻蚀速率和减小Si O 2掩膜直径后制备的.图3是硅尖原坯经过氧化、腐蚀后制备出的硅尖照片,尖端曲率半经约为10~20nm .2)各向同性湿法刻蚀制备硅微尖的工艺如图4所示.图2 干法刻蚀制备硅尖原坯的扫描电镜照片F ig .2 T he SE M i m age of Si 2ti p o riginal shapefab ricated by dry etch ing.图3 干法刻蚀制备的硅微尖F ig .3 T he i m age of Si 2ti p fab ricated by dry etch ing.图4 湿法刻蚀制备硅微尖的工艺示意图 F ig .4 T he cou rse illu strati on of Si 2ti p fab ricati onby w et etch ing .对于湿法各向同性刻蚀,由于腐蚀速率在纵向和横向比上难以调控,同时也考虑到制备带栅极硅冷阴极的需要,将Si O 2图形的直径设为3微米,比上面干法刻蚀的直径大些.图5是在腐蚀剂H F HNO 3 H 2O =1.5 15 5中一步腐蚀成的硅微尖.用高分辨扫描电镜观察硅微尖的顶端曲率半径约为10~15nm ,高度约为1.4Λm .372第3期王维彪等:干法刻蚀和湿法刻蚀制备硅微尖的比较 图5 湿法刻蚀制备的硅微尖F ig.5 T he SE M i m age of Si2ti p fab ricatedby w et etch ing.从上面的实验可以看出,选择好腐蚀剂和硅衬底的晶向,湿法刻蚀也能制备出顶端曲率半径很小的硅微尖.我们用干法刻蚀和湿法刻蚀的方法,制备出顶端曲率半径都比较小的硅微尖.干法刻蚀具有刻蚀速率可以调控、对晶面方向无要求、Si O2掩膜直径可以较小等优点,可以制备高质量、高密度的硅微尖冷阴极.对于湿法刻蚀制备硅微尖来说,如图中掩膜直径比较大,但这对在硅微尖上覆盖金刚石或其它材料有利.在制备工艺上,湿法刻蚀可以省去中间的氧化过程,直接进一步腐蚀即可制备出顶端曲率半径很小的硅微尖.其缺点是对衬底晶向及Si O2掩膜直径有要求.我们认为,干法刻蚀比湿法刻蚀在制备高质量、高密度带栅极硅冷阴极更有利、更方便.参 考 文 献[1]Gray H F,Camp isi G J,Greene R F.IEDM T ech.D ig.,1986,776.[2]M arcus R B,R avi T S,Gm itter T et al,A pp l.Phys.L ett.,1969,56(3):236.[3]黄庆安.硅微机械加工技术,科学出版社,1995,11.THE COM PAR IS ON OF Si-T IP FABR I CAT I ON M ETHOD S BET W EEN D RY ETCH ING AND W ET ETCH INGW ang W eib iao J in Changcun Zhao H aifengW ang Yongzhen Y in X iuhua Fan X i w u(Chang chun Institu te of P hy sics,Ch inese A cad e my of S ciences,Chang chun130021)L iang J ingqiu Yao J in song(Chang chun Institu te of Op tics and F ine M echanics,Ch inese A cad e my of S ciences,Chang chun130022)AbstractW e fab ricated Si2ti p s by dry etch ing〈100〉Si2sub strate and by one step w et chem i2 cal etch ing〈111〉Si2sub strate in so lu ti on of H F HNO3 H2O=1.5 15 5.T he radii of Si2ti p s’top abou t10~20nm w ere go tten after exp eri m en t.Key word Si2ti p,co ld cathode,dry etch ing,w et etch ing472 发 光 学 报第19卷。
微电子制造技术氧化硅的湿法刻蚀

T = 刻蚀掉的厚度 T
t = 刻蚀时间
刻蚀开始
刻蚀结束
Figure 16.3 刻蚀速率
微电子制造技术 电信学院 微电子学系 8
刻蚀剖面
刻蚀剖面指的是被刻蚀图形的恻壁形状。有 两种基本的刻蚀剖面,分别为各向同性的刻蚀剖 面和各向异性刻蚀剖面。 各向同性刻蚀剖面是指在所有方向以相同的 刻蚀速率进行的刻蚀(见图1.4)。湿法化学腐蚀 就是各向同性刻蚀,因而不能用于亚微米器件制 造中的选择性图形刻蚀。
各向异性刻蚀是仅在一 个方向刻蚀
Resist
Film Substrate Figure 16.5 具有垂直刻蚀剖面的各向异性刻蚀
微电子制造技术
电信学院 微电子学系 10
Table 16.1 湿法刻蚀和干法刻蚀的恻壁剖面
刻蚀类型 湿法刻蚀 恻壁剖面 各向同性 各向同性 (与设备和参数 有关) 各向异性 (与设备和参数 干法刻蚀 有关) 各向异性 – 锥形 硅槽 示意图
各向同性刻蚀是在各个方 向上同样的速率进行刻蚀 Resist
Film Substrate
微电子制造技术
Figure 16.4
湿法各向同性刻蚀
电信学院 微电子学系 9
对于亚微米尺寸的图形来说,希望刻蚀剖面 是各向异性的,即刻蚀只在垂直于硅片表面的方 向进行(见图 16.5 ),只有很少的横向刻蚀。各 向异性刻蚀对于亚微米器件的制作来说非常关键 。各向异性刻蚀大部分是通过干法等离子体刻蚀 来实现的。
Er S= Ef Ef Oxide
氮化硅
Er
微电子制造技术
Figure 16.8
电信学院 微电子学系 15
刻蚀均匀性
刻蚀均匀性是衡量刻蚀工艺在整个硅片上, 或者整个一批或批与批之间刻蚀能力之间的参数 。均匀性与选择比有密切关系,因为非均匀刻蚀 会产生额外的过刻蚀。保持刻蚀均匀性是保证制 造性能一致的关键。难点在于刻蚀工艺必须在刻 蚀具有不同图形密度的硅片上保证均匀性。 刻蚀的不均匀,是因为刻蚀速率与刻蚀剖面 、图形尺寸和宽度有关。因为刻蚀速率在刻蚀小 窗口图形时较慢,甚至在具有高深宽比的小尺寸 图形上刻蚀居然停止。这一现象被称为深宽比相 关刻蚀(ARDE),也被称为微负载效应。为了 提高均匀性,必须把硅片表面的 ARDE效应降到 最小。
微电子制造技术氧化硅的湿法刻蚀
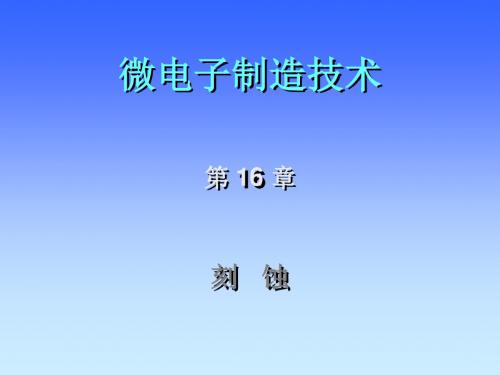
微电子制造技术
电信学院 微电子学系 26
干法刻蚀机比较
类型 园桶式 平行板 (Plasma) 顺流等离子体 Triode Planar Ion Beam Milling Reactive Ion Etch (RIE) Electron Cyclotron Resonance (ECR) Distributed ECR Inductively Coupled Plasma (ICP) Helicon Wave Dual Plasma Source Magnetically Enhanced RIE (MERIE) 刻蚀机理 化学 物理和化 学 化学 Reactive Inert Reactive Reactive Reactive Reactive Reactive Reactive Reactive 压力 (Torr) 10-1 to 1 10-1 to 1 10-1 to 1 10-3 10-4 < 0.1 10-4 to 103
结构设置 Coil or electrodes outside vessel Planar diode (two electrodes) Coil or electrodes outside vessel Triode (three electrodes) Planar triode Planar or cylindrical diode Magnetic field in parallel with plasma flow Magnets distributed around central plasma Spiral coil separated from plasma by dielectric plate Plasma generated by electromagnets and plasma density maintained at wafer by magnetic field Independent plasma and wafer biasing Planar diode with magnetic field confining plasma
深硅刻蚀工艺原理

深硅刻蚀工艺原理深硅刻蚀(Silicon Deep Etching)是一种用于微纳加工的关键工艺。
它可以在硅片上进行高精度、高深度的刻蚀,用以制造微纳米器件,如微机电系统(MEMS)、传感器、光子器件等。
深硅刻蚀工艺的原理基于湿法刻蚀和干法刻蚀两种方法。
湿法刻蚀是深硅刻蚀的主要原理之一、湿法刻蚀使用一种含有刻蚀剂的溶液,通过溶液与硅表面发生化学反应来刻蚀硅。
湿法刻蚀的刻蚀速度取决于刻蚀剂的浓度、温度、流速等因素。
深硅刻蚀中常用的刻蚀剂有氢氟酸(HF)、氢氧化钾(KOH)和氢氟酸和硝酸(HNO3)的混合物。
在湿法刻蚀过程中,硅表面上的氧化物层会起到保护作用,防止刻蚀剂直接与硅接触。
刻蚀剂通过破坏氧化物层将硅暴露出来,然后溶解硅。
由于刻蚀剂是从硅片的正面和背面进行刻蚀,因此可以实现较大的深度刻蚀。
干法刻蚀是另一种深硅刻蚀的重要原理。
干法刻蚀与湿法刻蚀不同,它不使用溶液来刻蚀硅表面,而是通过气相刻蚀来进行。
干法刻蚀常用的刻蚀气体有氢氟酸、氯化氢和氧化硅等。
干法刻蚀通常利用高能离子束轰击硅表面,将硅表面的原子击碎并氧化,然后通过氧化物在高温下与离子反应生成气体,将离子弹射离开硅表面,从而实现刻蚀作用。
干法刻蚀具有高速度、高精度和高均匀性等优点。
深硅刻蚀的工艺流程一般包括掩膜定义、刻蚀准备、刻蚀、刻蚀终结和清洗等步骤。
首先,通过光刻技术在硅片上定义出掩膜,掩膜上有所需刻蚀的结构。
然后,在刻蚀准备中,对硅片进行表面处理,以去除氧化层和其他杂质。
接下来,进行刻蚀过程,可以采用湿法刻蚀或干法刻蚀,根据需要选择刻蚀剂和刻蚀条件。
刻蚀终结后,通过清洗去除残留的刻蚀剂和刻蚀产物,以便进行下一步的加工或测试。
深硅刻蚀工艺的应用非常广泛。
它可以制造微纳米的光学元件,如光纤阵列、波导、光栅等。
它还广泛用于制造MEMS器件,如惯性传感器、声波传感器、加速度计等。
此外,深硅刻蚀还可以制造微电子器件、太阳能电池组件、生物芯片等。
3.湿法刻蚀

反应方程式如下:
Si 4HNO3 SiO2 4NO2 2H2O
SiO2 4HF SiF4 2H2O
SiF4 2HF H 2 SiF6
工艺流程: 上料→,,混合酸液腐蚀→风刀1→DI水冲洗→KOH腐 蚀→风刀2→DI水冲洗→腐蚀→风刀3→DI水冲洗→ 压缩空气风干→下料 工艺条件: 去离子水压力为4、压缩空气压力为6 环境温度:Байду номын сангаас5±3℃ 相对湿度:40%~60% ,无凝露 腐蚀槽温度:6-9℃ 槽温度:18℃左右
主要控制点:
1、腐蚀深度控制在1.2±0.2之间 2、刻蚀宽度D≤1,每片测量四点,测量点在 每边的中间点,20点(5道)或32点( 8道) 的平均值。 3、绝缘电阻≥1。 以上三个参数在正常生产时至少每隔1小时测 量一次。当更换药液和停产一段时间再生产时 及参数不正常时,要求增加测量次数。
4、腐蚀槽循环流量要求设定在30~35之间。 循环流量过小会导致腐蚀量不够,甚至硅 片边缘 不能完全去除;循环量过大会导致 过腐蚀现象和硅片边缘刻蚀宽度出现阴影 严重引起表面不合格。 5、腐蚀槽温度保证在7±1 ℃,随着温度 的升高,腐蚀速率会加快,但会使药液密 度减小,以致发生过腐蚀现象。所以在温 度未降到工艺控制范围内时禁止生产。
工艺准备: 1、工装工具准备: 备齐用于工艺生产的PVC手套、口罩、防护眼罩、防 护面罩、防护套袖、防护服、防酸碱手套、防酸碱胶 鞋等。 2、设备准备: 确认设备能正常运行,DI水、压缩空气等压力及流量 正常。确认设定的刻蚀工艺,碱洗工艺和HF腐蚀工 艺名称及参数。 3、工艺洁净管理:穿好净化服,戴口罩,操作时戴 洁净PVC手套。 4、原材料准备: 观察外观是否正常。常见的不合格片包括含缺角、裂 纹、手印、孔洞的硅片等。
- 1、下载文档前请自行甄别文档内容的完整性,平台不提供额外的编辑、内容补充、找答案等附加服务。
- 2、"仅部分预览"的文档,不可在线预览部分如存在完整性等问题,可反馈申请退款(可完整预览的文档不适用该条件!)。
- 3、如文档侵犯您的权益,请联系客服反馈,我们会尽快为您处理(人工客服工作时间:9:00-18:30)。
刻蚀剂/稀释剂/添加剂/温度
刻蚀速率(100)/mm/min
刻蚀速率比(100)/(111)
掩膜材料刻蚀速率
刻蚀终止特性
备注
KOH/水/异丙醇/85℃
1.4
400,(110)/(111)是60
Si3N4几乎不刻蚀
SiO228/min
掺杂浓度>1020cm-3时,刻蚀速率降低到1/20
K3Fe(CN)633g
用水稀释至1L
160.0nm/min
铂
HCl3mL
HNO31mL
20um/min,腐蚀之前在HF中浸泡30S
HCl7mL
HNO31mL
H2O8mL
40.0-50.0nm/min,85℃
钯
HCl1mL
HNO310mL
CH3COOH10mL
KI4g
I21g
H2O40mL
100.0nm/min
硅微工艺湿法刻蚀常见材料刻蚀剂和刻蚀速率
各种材料的腐蚀剂和腐蚀速率
材料
腐蚀剂
腐蚀速率
Si
HF+HNO3+H2O
最大490um/min
SiO2
NH4F150g
HF(40%)70mL
H2O150mL
23℃时0.1μm/min
Si3N4
49%HF23℃
85%H3PO4155℃
85%H3PO4180℃
LPCVD
与IC不兼容,对氧化层腐蚀过快,大量H2气泡
邻苯二酚,乙二胺,水(EDP)/Pyrazine/115℃
1.25
35
Si3N41/min
SiO22-5/min
掺杂浓度>5X1010cm-3时,刻蚀速率降低到1/50
有毒性,易失效,需与氧气隔离,很少氢气,硅酸盐沉淀
四甲基氢氧化氨(TMAH)/水/90℃
饱和CeSO49mL
80.0nm/min
(NaOH1g+H2O2mL)1mL
(K3Fe(CN)61g+H2O3mL)3mL
25.0-100.0nm/min
钼
H3PO45mL
HNO33mL
H2O2mL
抛光腐蚀
K3Fe(CN)611g
KOH10g
H2O150mL
1um/min
钨
KH2PO434g
KOH13.4g
金
HCl3mL
HNO31mL
25-50um/min
KI4g
I21g
H2O40mL
0.5-1um/min
银
NH4OH1mL
H2O21mL
CH3OH4mL
360.0nm/min,腐蚀后快速清洗
铜
H2O70mL+FeCl330g,50℃
7um/min
铬
HCl1mL
甘油1mL
80.0nm/min
HCl1mL
PECVD
8.0nm/min
1.5nm/min
12.0nm/min
150.0-300.0nm/min
10.0-20.0nm/min
60.0-100.0nm/min
多晶硅
HF6mL
HNO3100mL
H2O40mL
800nm/min,边缘平整
HF1mL
HNO326mL
CH3COOH33mL
150nm/min
1.0
12.5-50
SiO2刻蚀速率比(100)硅低四个数量级
掺杂浓度>4X1020cm-3时,刻蚀速率降低到1/40
与IC兼容,易操作,表面光滑,研究不充分
铝
HCl1mL
H2O2mL
80℃,细线
H3PO44mL
HNO31mL
CH3COOH4mL
H2O1mL
35nm/min,细线,腐蚀GaAs
K2Br4O70.1M
KOH0.51M
K3Fe(CN)60.6M
1um1mL
H2O0-4mL
150.0-250.0nm/min,腐蚀GaAs