第十二章-陶瓷烧成
陶瓷工艺原理--烧成与窑具PPT共62页

41、学问是异常珍贵的东西,从任何源泉吸 收都不可耻。——阿卜·日·法拉兹
42、只有在人群中间,才能认识自 己。——德国
43、重复别人所说的话,只需要教育; 而要挑战别人所说的话,则需要头脑。—— 玛丽·佩蒂博恩·普尔
44、卓越的人一大优点是:在不利与艰 难的遭遇里百折不饶。——贝多芬
45、自己们国家的法律中只有某种 神灵, 而不是 殚精竭 虑将神 灵揉进 宪法, 总体上 来说, 法律就 会更好 。—— 马克·吐 温 37、纲纪废弃之日,便是暴政兴起之 时。— —威·皮 物特
38、若是没有公众舆论的支持,法律 是丝毫 没有力 量的。 ——菲 力普斯 39、一个判例造出另一个判例,它们 迅速累 聚,进 而变成 法律。 ——朱 尼厄斯
陶艺 陶瓷烧成课件
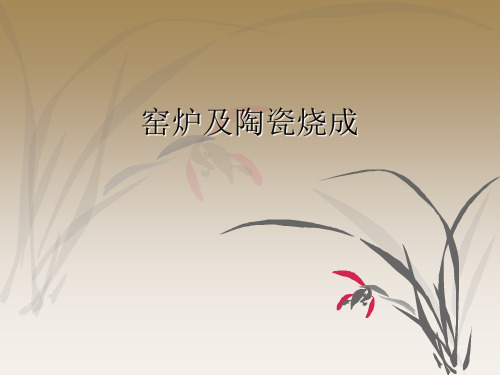
(2).龙窑——一般都是依山坡而建,坡的大 小缓急直接影响烧成时间和产量。
一般窑头坡度大,易上火,窑尾坡度小,易 存火,低的一端为火膛,高的一端有排烟 口。
龙窑的只要特点是升温快、降温也快,维持 火焰和还原时间长。使用的材料为松柴。
在我国南方比较多见。(如浙江龙泉、福建 德化、在景德镇的湖田也多出发现了龙 窑。)
一次烧成和二次烧成
一次烧成:是指经过成型、干燥或施釉后的 生坯,在烧成窑内一次烧成陶瓷产品的工艺 路线。 二次烧成:是指经过成型干燥的生坯,先在 素烧窑内进行第一次烧成(素烧)后的产品, 经拣选,施釉等工序后,再进行第二次烧成 (釉烧)的工艺路线。
设置烧制曲线
釉下烧成曲线
釉上烧成曲线
(三)升温曲线
使之变成“形如覆瓮”的蛋型, 所以也叫瓮形 窑或蛋形窑,景德镇人把这各独具地方特色, 独具技术优势的属于平焰式的窑叫镇窑。
电窑认识
以此款八边形顶 开盖窑炉为例。
此款窑为顶开 盖,小且轻便。 0.07立方、6kw、 220v、接线为4m ㎡以上的全铜 线。
窑炉结构
采用五层不同结构层完美结合。 最里层为高温砖,然后以高保温耐火棉保
150~500℃:坯体可快速升温,比较安全,失去结合 水,碳酸盐、黑云母的分解,气体很容易溢出。
500~700℃:较松散,石英在573℃有突变,膨胀系数 较大。
700~900℃:可快速加热坯体,比较安全,碳化物燃 烧成气体,并排出,坯体气孔增多,可不限制加热速 度,因为坯体很薄,可渗透性强。
• 900~1100℃:在烧成收缩很严重之前要减小制品间 的温差,在900度是升温较慢,盐酸盐分解许多气泡 在釉面玻化之前必须排出,快速升温会导致石膏混入 坯体或已干燥的可溶性盐类集中到一起,坯体炸裂。
(整理)1篇8章3节陶瓷烧成.

(四)生料成球生料成球(raw meal nodule)质量是保证立窑煅烧极其重要的环节。
成球质量好、粒度均匀、大小适宜,才能使窑内通风均匀,煅烧良好,从而保证熟料质量,提高窑的产量,降低消耗。
生料成球质量,首先决定于原料质量,特别是粘土性能及生料细度。
生料细度细时,由于细颗粒生料和水结合较强,料球坚实,强度较大。
其次,生料球大小应适宜,粒度要均匀,有足够的孔隙率,这样既可降低阻力损失,又易于使料球烧透,缩短反应时间,提高煅烧速度。
成球水分与料球大小及强度有密切关系。
用水量多,球径增大;水分过少,物料润湿不充分,形成大量小球,既影响料层透气性,又易炸裂。
通常对生料球有如下要求:(1)粒度:8~15mm,球径大小要均匀;(2)料球含水分:12%~15%;(3)料球强度:从1m高处掉下不破裂;(4)料球孔隙率:30%~35%。
近年来开发推广的“预加水成球”,能显著改善成球质量,提高料层的透气性、通风的均匀性和料球强度,是提高立窑产量、质量,降低消耗的一项新的技术措施。
第三节陶瓷的烧成一、烧成的动力机制及方法从热力学观点来看,烧成(firing)是系统总能量减少的过程。
与块状物料相比,粉末有很大的比表面积,表面原子具有比内部原子高得多的能量。
同时,粉末粒子在制造过程中,内部也存在各种晶格缺陷。
因此,粉体具有比块料高得多的能量。
任何体系都有向最低能量状态转变的趋势,这就是烧成过程的动力。
即粉料坯块转变为烧成制品是系统由介稳状态向稳定状态转变的过程。
但烧成一般不能自动进行,因为它本身具有的能量难以克服能垒,必须加高到一定的温度才能进行。
烧成是一个复杂的物理、化学变化过程。
比如特种陶瓷的烧成,有人认为其烧成机制可归纳为:①粘性流动;②蒸发与凝聚;③体积扩散;④表面扩散;⑤晶界扩散;⑥塑性流动等。
实践说明用任何一种机制去解释某一具体烧成过程都是困难的,烧成是一个复杂的过程,是多种机制作用的结果。
烧成大批量的普通陶瓷一般是在隧道窑、辊道窑或梭式窑等窑炉中进行的。
陶瓷烧成与窑炉热工
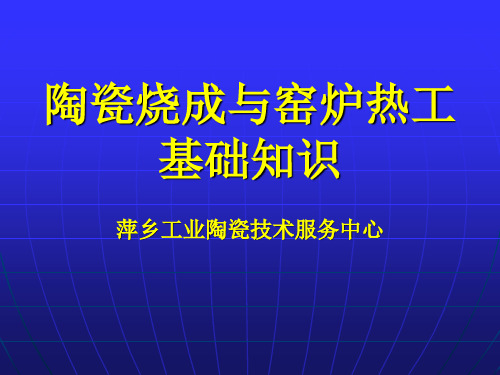
在还原气氛下 CaSO4+CO﹥910℃ CaSO3+CO2↑ CaSO31080~ 1100℃CaO+SO2↑ Fe2O3+CO1000~ 1100℃2Fe+CO2↑ CaO和Fe0促进烧成 致密化,减少泛黄 现象
(3)形成大量液相和莫来石 ①985℃开始出现液相,温度越高,液 985℃ 相越多 液相的作用: A、促使晶体(如莫来石)长大; B、填充坯体孔隙拉紧颗粒,促进坯体致密 化,提高瓷件抗蚀性和机械强度; C、液相会阻碍气体排出,易发生冲泡和变 形。 ②1100℃以上开始形成莫来石. 1100℃以上开始形成莫来石.
(四)、完全燃烧和不完全燃烧 )、完全燃烧和不完全燃烧
完全燃烧:燃料燃烧后完全转变为不 可再燃烧产物的一种燃烧方式 不完全燃烧:燃料燃烧后的烟气中有 可再燃烧产物的一种燃烧方式
(五)、燃料的种类 )、燃料的种类
1、固体燃料:柴、烟煤、无烟煤、煤 粉等 2、液体燃料:重油、柴油、焦油、液 态煤等 3、气体燃料:发生炉煤气、焦炉煤气、 液化石油气、天然气
(三)结构和原理图
七、隧道窑
(一)定义
隧道窑是连续烧成陶瓷制品的热工设备, 它的主体是一条隧道,是一种按逆流原 理工作的横焰式窑。
(二)隧道窑的特点: 隧道窑的特点:
1、利用烟气余热预热坯体,废气排出温度 低,约200℃ 低,约200℃; 2、产品冷却之热加热空气,可助燃或作干 燥介质,产品出窑温度低; 3、连续窑,窑体温度不变,不蓄热,热耗 低; 4、产量大,劳动条件好; 5、较适合产品单一的生产: 6、调控不便,一次投资大
1、水分蒸发期(室温~摄氏300℃) 水分蒸发期(室温~摄氏300℃ 此阶段主要是排出干燥中未除掉的水分。 要求:①入窑坯体水分小于2%否则,坯体 要求:①入窑坯体水分小于2%否则,坯体 有可能因水分蒸发而开裂;或与窑炉SO2 有可能因水分蒸发而开裂;或与窑炉SO2 发生化学反应,造成坯体蒙上一层“白霜” 发生化学反应,造成坯体蒙上一层“白霜” 或产生气泡缺陷;②加强窑内通风,使水 汽及时排除。此阶段坯体强度缓慢提高。 一般升温速度:20~35℃ 一般升温速度:20~35℃/hr
陶瓷烧成过程及影响因素

陶瓷烧成过程及影响因素一。
低温阶段温度低于300℃,为干燥阶段,脱分子水;坯体质量减小,气孔率增大。
对气氛性质无要求二中温阶段温度介于300~950℃1.氧化反应:(1)碳素和有机质氧化;(2)黄铁矿(FeS2)等有害物质氧化。
2.分解反应:(1)结构水脱出;(2)碳酸盐分解;(3)硫酸盐分解3.石英相变和非晶相形成。
影响因素加强通风保持良好氧化气氛,控制升温速度,保证足够氧化反应时间,减少窑内温差。
三。
高温阶段1.氧化保温阶段温度大于950℃,各种反应彻底;2.强还原阶段CO浓度3%~5% 三价铁还原成二价铁之后与二氧化硅反应形成硅酸铁。
3.弱还原阶段非晶态(玻璃相)增多,出现偏高岭石===模来石+ SiO2(非晶态)影响因素,控制升温速度,控制气氛,减小窑内温差四。
高温保温阶段烧成温度下维持一段时间。
物理变化:结构更加均匀致密。
化学变化:液相量增多,晶体增多增大晶体扩散,固液分布均匀五。
冷却阶段液相结晶晶体过冷强度增大急冷(温度大于850℃)→缓冷(850~400℃)→终冷(室温)一次烧成和二次烧成对比一次烧成又称本烧,是经成型,干燥或施釉后的生坯,在烧成窑内一次烧成陶瓷制品的工艺路线。
特点:1 工艺流程简化;2 劳动生产率高;3 成本低,占地少;4 节约能源。
二次烧成是指经过成型干燥的生坯先在素烧池中素烧,即第一次烧成然后拣选施釉在进入釉烧窑内进行釉烧第二次烧成特点:1 避免气泡,增加釉面的白度和光泽度;2 因瓷坯有微孔,易上釉;3 素烧可增加坯体的强度,适应施釉、降低破损率;4 成品变形小,(因素烧已经收缩);5 通过素检可降低次品率。
对批量大,工艺成熟质量要求不是很高的产品,可一次烧成,但一次烧成要求坯釉一起成熟,否则损失大,质量下降,应用二次烧成耐火材料的宏观性质1.气孔:开孔、闭孔和贯通孔;2.气孔率:体积百分比真气孔率Pt=(Vc+V o)/Vb×100%闭气孔率Pc= Vc/Vb×100%显气孔率Pa= V o /Vb×100%Vc---闭孔体积;Vo---开孔+贯通孔;Vb---材料总体积Pt= Pc+ Pa 3.密度(g/cm3)体积密度d=M/V视密度或表观密度da=M/(Vc+Vt)真密度dt=M/Vt Vc---闭孔体积;Vt---除气孔外的材料体积;V---总体积;M—质量4.吸水率(%)是指全部显气孔被水填满时,水的质量与干燥材料的质量之比。
陶瓷烧成技术

第三讲陶瓷烧成技术烧成是将陶瓷坯体在相应的窑炉中进行加热处理,使其发生一系列的物理化学变化,形成预期的矿物组成和显微结构,从而形成固定的外形并获得所要求性能的工序。
烧成时坯体将发生脱水、分解、化合等物理和化学变化,烧成后制品具有一定的机械强度及使用性能。
陶瓷烧成的窑炉主要有隧道窑、辊道窑、梭式窑等。
烧成时的温度制度、气氛制度、压力制度等与产品的质量有直接关系。
因此,烧成过程是陶瓷生产中重要的工序之一。
一、陶瓷坯体的烧成过程(一)烧成过程的阶段划分陶瓷坯体烧成时,根据不同温度区间的主要作用与主要变化反应可分为如下几个阶段(见表3-1)。
在整个烧成过程中,制品在窑内经历了不同的温度变化和气氛变化,既有氧化、分解、新的晶体生成等复杂的化学变化,也伴随有脱水、收缩、以及密度、颜色、强度与硬度的改变等物理变化。
并且这些变化总是相互交错地一起进行。
(二)影响坯体烧成时物理化学变化的主要因素影响坯体烧成时物理化学变化的主要因素主要有坯料的化学组成与矿物组成、坯料的物理状态等。
1.坯料的化学组成与矿物组成根据坯料的化学组成,可以推断坯体在烧成过程中产生膨胀或气泡的可能性,可以估计坯体的耐火度的高低,也可以推断坯体烧后的呈色等。
坯体在烧成过程中的物理化学变化与坯体的化学组成有关,但坯料的化学分析只能提供坯料性质的大致情况,不能完全说明问题的本质,因为化学分析是将泥料的化学组成用氧化物表示出来,实际上泥料的各种成分绝大部分不是以游离氧化物形式存在,而是各式各样的化合物。
更准确地说,坯体在烧成过程中的物理化学变化是取决于泥料的矿物组成。
例如高岭土和多水高岭土,它们的晶体结构基本相似,但在加热过程中的脱水反应是不相同的。
即使是同一氧化物,在两种不同的矿物组成中所起的作用也不一定相同,例如游离石英与黏土或长石中的氧化硅,其所起作用的性质就不一样。
同样是氧化硅,在以不同的晶态(石英、鳞石英、方石英)存在时,会表现出不同的特性。
[整理]陶瓷烧成缺陷及原因分析
![[整理]陶瓷烧成缺陷及原因分析](https://img.taocdn.com/s3/m/cadf1d35abea998fcc22bcd126fff705cc175c4b.png)
陶瓷烧成缺陷及原因分析发布时间:2008-8-4 15:07:14 阅读:52 次新闻来源:作者:(一)变形:产品烧成变形是陶瓷行业最常见、最严重的缺陷,如口径歪扭不圆,几何形状有不规则的改变等。
主要原因是装窑方法不当。
如匣钵柱行不正,匣钵底或垫片不平,使窑车运行发生震动,影响到产品的变形。
另外,产品在烧成中坯体预热与升温快时,温差大易发生变形。
烧成温度过高或保温时间太长也会造成大量的变形缺陷。
使用的匣钵高温强度差、或涂料抹不平时也会造成烧成品的变形。
(二)开裂:开裂指制品上有大小不同的裂纹。
其原因是坯体入窑水分太高(大于2%以上),预热升温和冷却太快,导致制品内外收缩不匀。
有的是坯体在装钵前已受到碰撞有内伤。
坯体厚薄不匀,配件(如壶把、咀等)重量过大或粘结不良也会造成制品开裂。
防止的办法是:(1)入窑坯体水分小于2%,车速适当减少冷却量。
(2)装窑时套装操作谨慎,垫片与坯体配方一致。
配件大小、重量与粘接位置恰当。
有的在粘接泥浆中加入10-15%的釉料,可以使咀、把与主体牢固熔接一体,如此可克服开裂缺陷。
(三)起泡:烧制品起泡有"坯泡"与"釉泡"两种。
坯泡分为"氧化泡"与"还原泡"两种。
氧化泡指坯泡外面覆盖釉层,断面呈灰黑色,多形成于窑内低温部位。
主要是瓷胎与釉料中的分解物未能充分氧化,烧失物未完全排除所致。
予热升温快,氧化分解阶段时间短、氧化结束时窑内温度过低,上下温度差过大。
在坯釉料中,碳酸盐。
硫酸盐及有机杂质含量较多等都是造成产品起泡的主因。
此外时装车密度不当、入窑水份高等原因亦须注意。
还原泡又称过火泡,断而发黄,多发生于高温近喷火口处的制品。
主要由于坯体内硫酸盐与高价铁还原不足,强还原气氛不足及烧成温度过高造成。
釉泡系沉积炭及分解物在釉熔前未能烧尽挥发,气体被阻于釉面层中形成。
若延长釉熔时间或适当平烧即可解决。
陶瓷烧窑小作文

陶瓷烧窑小作文篇一《陶瓷烧窑:一场奇妙的土与火之歌》我和陶瓷烧窑的缘分,还得从一次乡间旅行说起。
那是个宁静的小村子,路边有个小小的陶瓷作坊,一进去就像进入了一个泥土的魔法世界。
在作坊里,我看到了尚未烧制的陶瓷坯体,它们看起来普普通通的,就像被揉好面人却还没上过色的样子。
有个老师傅正把一摞摞的坯拿进窑里。
那窑看起来就像一个大大的嘴巴,坯体就像是要被吞进去的食物。
我好奇极了,凑上去想一探究竟。
只见老师傅小心翼翼地摆放着每一个坯体,像是摆弄着一件件稀世珍宝。
他说这些坯体摆放可不能马虎,如果不小心碰到或者放置的间距不对,烧出来的陶瓷可就全毁了。
我看着他那专注的神情,就像在对待自己刚出生的孩子。
我在旁边也想帮忙,老师傅笑着让我拿一个小坯体试试。
我紧张兮兮地拿起,那坯体在我手上就像个脆弱的蛋壳,我都不敢用力呼吸,颤颤巍巍地放到指定位置。
一切准备就绪后,就是点火环节了。
老师傅像个神秘的魔法师,轻轻一点,那火焰就呼地一下蹿起来。
窑里一下子亮堂堂的,像个被点燃激情的小宇宙。
我能透过窑的小窗口看到里面的坯体在火焰中微微晃动,好像在接受一场神圣的洗礼。
接下来的几个小时,我就像个虔诚的守护者一样,守在窑边。
随着温度的上升,窑壁也变得滚烫滚烫的。
我时不时去看看那火焰的颜色,老师傅说火焰的颜色能大概反映窑内的温度呢。
刚开始是那种暗暗的红色,就像晚霞的尾巴不小心被塞进了窑里,过了一会儿就变成了明亮的橙色,像个热情奔放的橘子精在窑里撒欢。
我眼睛都不敢眨,生怕错过这奇妙的变化。
这一窑烧完后,当看到那些原本灰扑扑的坯体变成了色彩斑斓、质地光滑的陶瓷,我整个人都惊呆了。
就像目睹了一群丑小鸭瞬间变成了白天鹅。
我拿起一个小小的陶瓷茶杯,那触感、那色泽,无不诉说着这一场土与火共舞的奇妙经历。
这小小的烧窑过程,却像一场盛大而又神秘的庆典,让人回味无穷。
篇二《陶瓷烧窑:从土到宝的神秘之旅》我一直对陶瓷烧窑充满了好奇,就像只好奇的小老鼠想要探寻宝库的秘密。
陶瓷制造工艺烧成
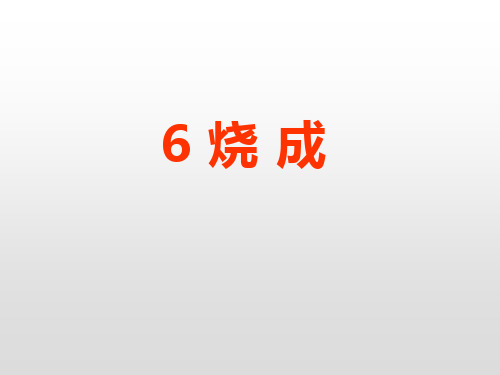
烧结现象示意图 a-晶粒重排; b1-疏松堆积的颗粒系 统中颗粒中心靠近; b2-紧密堆积的系统中, 颗粒中心的靠近。
固相烧结传质机理 (1)蒸发-凝聚
烧结时颈部区域的扩大,球的形状逐步变为椭圆,气孔形状发生了变化 两个球形颗粒中心间的距离不变。 不导致坯体的收缩和气孔率的降低
烧结温度TS和熔融温度Tm之间的关系: 金属粉末TS≈(0.3~0.4) Tm, 盐类TS≈0.57Tm, 硅酸盐TS ≈(0.3~0.4) Tm。
烧结的推动力
1、能量差 粉状物料的表面能大于多晶烧结体的晶界能,即能量差是烧结的推 动力,但较小。烧结不能自发进行,必须对粉料加以高温,才能促 使粉末体转变为烧结体。 例如:
球形颗粒间颈部长大改变气孔形状与中心距
在球形颗粒表面有一正曲率半径,在二个颗粒连接处有一小的负曲率半径 的颈部。
根据开尔文公式:
ln P 2M P0 dRTr
x r
凸表面蒸气压>平表面蒸气压>凹表面蒸气压 质点从凸表面蒸发向凹表面(颈部)迁移、凝 聚,使颈部逐渐被填充。
蒸发-凝聚传质
球形颗粒连接处曲率半径ρ和接触颈部半径x之间的开尔文公式:
粒度为1m的材料烧结后,G降低约8.3J/g(无机材料等效于0.5 1.5 KJ/mol);
α-石英与β-石英之间的多晶转变时,G为1.7 KJ/mol; 一般化学反应前后能量变化超过200 KJ/mol。
烧结的难易可以用GB晶界能/SV表面能比值来衡量: GB/SV越大,烧结越困难
2、压力差:颗粒的弯曲表面上存在有压力差
目前我国日用陶瓷工业广泛采用隧道窑、辊道窑和推板窑,并 保留少量的倒焰窑继续用于生产。
烧结定义: 经过成型的粉末在加热到一定温度后开始收缩,在低于物质
陶瓷艺术的烧成方法

陶瓷艺术的烧成方法陶瓷品制作完成后,还要经过烧制才能最终成为成品。
那么,你知道陶艺的烧成方法有哪些吗?以下是有我为大家整理的,希望能帮到你。
陶瓷的烧成方法1、素烧法:表面不上釉的作品,直接烧成称为素烧。
素烧可以保留陶瓷作品上的手工痕迹,显现材质的自然和本质的美。
陶的素烧温度为900~1150℃。
瓷的素烧温度为1100~1310℃。
2、本烧法:陶瓷作品坯体表面上釉后,用高温一次性烧成,使坯体完全烧结,釉料完全融化,称为本烧。
烧成温度为1100~1350℃。
3、釉烧法:釉烧分两次烧成,陶瓷坯体经过一次素烧后再上釉,用低温二次烧成,使釉完全融化,烧成温度为900~1000℃。
4、氧化焰法:调整烟道阀门,保证窑内空气充足,定时添加燃料,使燃料在空气中彻底烧尽,由于窑炉氧气充足,则形成氧化焰气氛5、还原焰法:当温度加速升温至高温阶段,放低烟道阀门,使窑炉供养不足,炉内碳素增加,形成还原焰气氛。
6、乐烧法:乐烧采用二次烧成的工艺技术。
第一次素烧,温度为700~900℃。
再上釉,用低温二次烧成。
7、盐烧法:坯体在高温时,将氯化钠直接撒入在燃烧的窑炉中,氯化钠开始挥发,产生纳蒸气,这种纳蒸汽同陶瓷坯体表面的铝与硅产生反应,熔融成釉形成带有肌理的透明釉。
8、熏烧法:熏烧采用素烧和烟熏二次完成的工艺技术。
在素烧完成后再选用木屑、树枝、报纸等作燃料产生浓烟,通过坯体表面的缝隙使碳素附着于作品表面,形成自然的斑迹效果。
9、柴烧法:一种用木柴直接烧陶的方法。
因柴火直接在体坯上留下自然的“火痕”和木柴燃烧后的灰烬落在作品表面形成的“落灰釉”,使得作品色泽温润且有变化。
烧制陶瓷工艺流程烧制陶瓷的关键因素是:泥、釉、火。
为什么有些陶、瓷器会莫明其妙的出现裂纹呢?为什么有时甚至会掉皮釉呢?这不外是在一定温度条件下泥和釉的收缩系数又称膨胀系数不相一致的结果。
有时人们亦会对这种缺陷特意加以利用,传统的开片釉及现代陶艺的一些肌理追求就是利用釉和泥收缩系数不相一致的原理配制出来的。
烧成
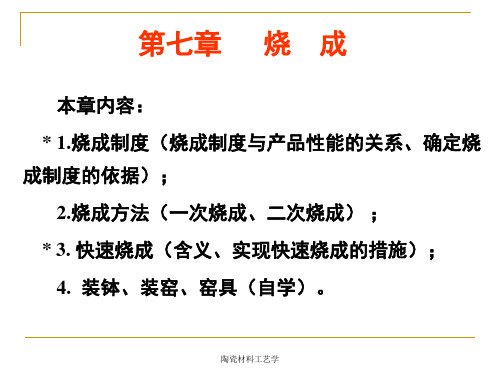
陶瓷材料工艺学
K2O-Al2O3-SiO2相图低共熔点985±20℃,烧
结温度范围宽50~60℃;
MgO-Al2O3-SiO2相图低共熔点1355℃,烧结
温度范围窄10~20℃;
热分析曲线DTA、 TE 、ITE拟定烧成制度。
P379 图10-9 ,10-10
陶瓷材料工艺学
方石英
1300~1400℃
3Al2O3 • 2SiO2+SiO2
陶瓷材料工艺学
第二种看法:
Al2O3•2SiO2
Al2O3+SiO2
约950℃
Al2O3(无定形) 3γ -Al2O3 +2SiO2
γ -Al2O3 3Al2O3 • 2SiO2
>1000℃
陶瓷材料工艺学
4、冷却阶段
①. 液相析晶,玻璃相物质凝固; ②. 游离石英晶型转变。
2. 坯体形状、厚度和入窑水分
陶瓷制品由于形状、厚度和含水率不同,升温速 度和烧成周期都有所不同。 薄壁小制品入窑水分易于控制,一般可采取短周 期烧成。对大件厚壁制品,则升温不能过快,周期不 能过短。如果坯体含有大量高可塑性粘土,则由于排 水困难、升温速度更应放慢。
陶瓷材料工艺学
3. 窑炉结构、燃料类型和装窑密度
3、高温玻化成瓷阶段(950℃~最高烧成温度) ①.1050℃以前继续氧化分解反应及排除少量残余 结构水; ②.硫酸盐分解和高价铁的还原与分解; ③.形成大量液相和莫来石新相; ④.新相的重结晶和坯体的烧结; ⑤.釉料熔融成玻璃体。 制品强度增加,气孔率减少,坯体急剧收缩。
陶瓷材料工艺学
980~1000℃
陶瓷材料工艺学
二、烧成制度的确定
1. 温度制度:
陶瓷的生产工艺
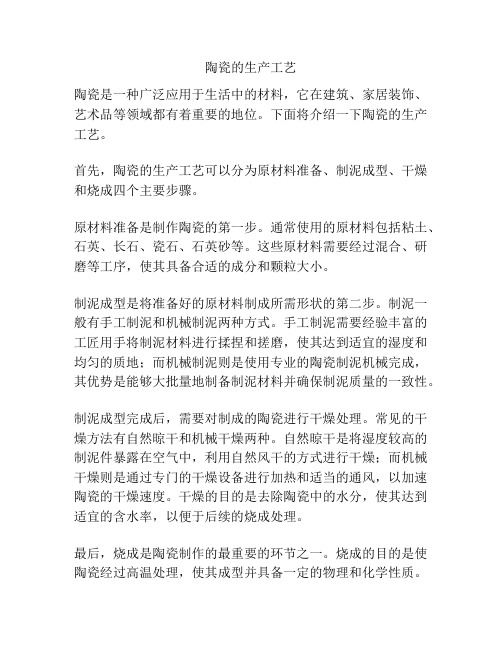
陶瓷的生产工艺陶瓷是一种广泛应用于生活中的材料,它在建筑、家居装饰、艺术品等领域都有着重要的地位。
下面将介绍一下陶瓷的生产工艺。
首先,陶瓷的生产工艺可以分为原材料准备、制泥成型、干燥和烧成四个主要步骤。
原材料准备是制作陶瓷的第一步。
通常使用的原材料包括粘土、石英、长石、瓷石、石英砂等。
这些原材料需要经过混合、研磨等工序,使其具备合适的成分和颗粒大小。
制泥成型是将准备好的原材料制成所需形状的第二步。
制泥一般有手工制泥和机械制泥两种方式。
手工制泥需要经验丰富的工匠用手将制泥材料进行揉捏和搓磨,使其达到适宜的湿度和均匀的质地;而机械制泥则是使用专业的陶瓷制泥机械完成,其优势是能够大批量地制备制泥材料并确保制泥质量的一致性。
制泥成型完成后,需要对制成的陶瓷进行干燥处理。
常见的干燥方法有自然晾干和机械干燥两种。
自然晾干是将湿度较高的制泥件暴露在空气中,利用自然风干的方式进行干燥;而机械干燥则是通过专门的干燥设备进行加热和适当的通风,以加速陶瓷的干燥速度。
干燥的目的是去除陶瓷中的水分,使其达到适宜的含水率,以便于后续的烧成处理。
最后,烧成是陶瓷制作的最重要的环节之一。
烧成的目的是使陶瓷经过高温处理,使其成型并具备一定的物理和化学性质。
根据烧成温度的不同,可以将烧成分为低温烧成、中温烧成和高温烧成三种类型。
低温烧成通常在800-1000℃之间进行,适用于一些日常用的陶瓷制品;中温烧成一般在1000-1300℃之间,适用于一些建筑和装饰领域的陶瓷制品;而高温烧成则可以在1300℃以上,适用于一些特殊陶瓷制品,如瓷砖、瓷器等。
总的来说,陶瓷的生产工艺包括原材料准备、制泥成型、干燥和烧成四个主要步骤。
在每个步骤中,都需要经过一系列的操作和处理才能最终制成高质量的陶瓷制品。
随着科技的进步,现代陶瓷制造工艺已经逐渐实现了机械化和自动化,大大提高了生产效率和制品质量。
陶瓷材料烧成制度
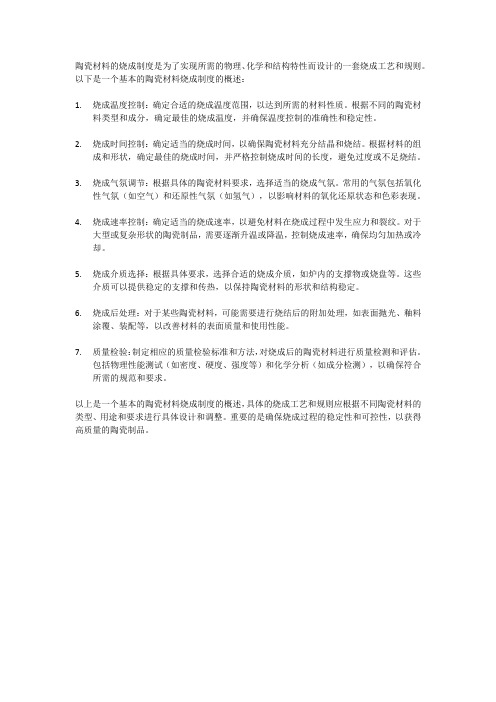
陶瓷材料的烧成制度是为了实现所需的物理、化学和结构特性而设计的一套烧成工艺和规则。
以下是一个基本的陶瓷材料烧成制度的概述:1.烧成温度控制:确定合适的烧成温度范围,以达到所需的材料性质。
根据不同的陶瓷材料类型和成分,确定最佳的烧成温度,并确保温度控制的准确性和稳定性。
2.烧成时间控制:确定适当的烧成时间,以确保陶瓷材料充分结晶和烧结。
根据材料的组成和形状,确定最佳的烧成时间,并严格控制烧成时间的长度,避免过度或不足烧结。
3.烧成气氛调节:根据具体的陶瓷材料要求,选择适当的烧成气氛。
常用的气氛包括氧化性气氛(如空气)和还原性气氛(如氢气),以影响材料的氧化还原状态和色彩表现。
4.烧成速率控制:确定适当的烧成速率,以避免材料在烧成过程中发生应力和裂纹。
对于大型或复杂形状的陶瓷制品,需要逐渐升温或降温,控制烧成速率,确保均匀加热或冷却。
5.烧成介质选择:根据具体要求,选择合适的烧成介质,如炉内的支撑物或烧盘等。
这些介质可以提供稳定的支撑和传热,以保持陶瓷材料的形状和结构稳定。
6.烧成后处理:对于某些陶瓷材料,可能需要进行烧结后的附加处理,如表面抛光、釉料涂覆、装配等,以改善材料的表面质量和使用性能。
7.质量检验:制定相应的质量检验标准和方法,对烧成后的陶瓷材料进行质量检测和评估。
包括物理性能测试(如密度、硬度、强度等)和化学分析(如成分检测),以确保符合所需的规范和要求。
以上是一个基本的陶瓷材料烧成制度的概述,具体的烧成工艺和规则应根据不同陶瓷材料的类型、用途和要求进行具体设计和调整。
重要的是确保烧成过程的稳定性和可控性,以获得高质量的陶瓷制品。
陶瓷重点

陶瓷工艺学重点1.传统上,陶瓷的概念是指所有以黏土为主要原料与其它天然矿物经过适当的配比、粉碎、成型并在高温培烧情况下经过一系列的物理化学反应后,形成的坚硬物质。
2.釉下彩绘是在素烧或未烧的坯体上进行彩绘,然后施上一层透明釉在高温下烧制而成。
釉中彩是在陶瓷釉上进行彩绘后,在1060-1250C 温度下快速烤烧而成。
在高温条件下,制品釉面软化熔融,使陶瓷颜料渗透到釉层中内部,冷却后釉面封闭,颜料自然沉入釉中。
3.等静压成型是将待压试样置于高压容器中,利用液体介质不可压缩的性质和均匀传递的压力的性质,从各个方向对试样进行均匀加压,使瘠性物料成型致密坯体,也称为等静压法。
第一章原料1.原料的分类方法有以下几类:(1)按工艺特性分为:可塑性原料,非可塑性原料,和熔剂性原料。
(2)按原料的用途:瓷坯原料,瓷釉原料、色料及彩料原料。
(3)按矿物组成可分为:黏土质原料,硅质原料,长石质原料,钙质原料,镁质原料。
(4)按原料的获得方式可分为:矿物原料和化工原料。
2.黏土的分类:按成因分可分为:(1)原生黏土:又称一次黏土,残留黏土,是母岩风化崩解在原地残留下来的黏土;(2)次生黏土,又称二次黏土、沉积黏土,是由风化形成的黏土,经雨水河流的冲刷与漂流及有时外加风力的作用以后,迁移至盆地或水流缓慢的湖泊沼泽地沉积下来,而形成黏土层。
3.按耐火度分类:耐火黏土(耐火度在1580C以上);难熔黏土(耐火度在1350--1580C)易熔黏土(耐火度在1380C以下)4.高岭石(Al2O3.2SiO2.2H2O)5.蒙脱石也叫膨润土(Al2O3.4si2O.nH2O)6.黏土的组成包括:矿物组成。
化学组成,颗粒组成。
7.可塑性:是指泥团在一定外力作用下产生形变但不开裂,当外力去掉以后,仍能保持形状不变,黏土的这种性质称为可塑性。
8.可塑性指数是指黏土的液限含水率与塑性含水率之差。
9.可塑性指标系是指在工作水分下,黏土泥团受外力作用最初出现裂纹时应力与应变的乘积。
烧结的概念——精选推荐

第十二章烧结(Sinter)第一节基本概念一、烧结1、烧结的意义烧结是粉末冶金、陶瓷、耐火材料、超高温材料等部门的一个重要工序。
烧结的目的是把粉状物料转变为致密体。
这种烧结致密体是一种多晶材料,其显微结构由晶体、玻璃相和气孔组成,烧结过程直接影响显微结构中晶粒尺寸和分布,气孔尺寸和分布以及晶界体积分数….。
烧结过程可以通过控制晶界移动而抑制晶粒的异常生长或通过控制表面扩散、晶界扩散和晶格扩散而充填气孔,用改变显微结构方法使材料性能改善。
因此,当配方、原料粒度、成型等工序完成以后,烧结是使材料获得预期的显微结构以使材料性能充分发挥的关键工序。
2、烧结的定义宏观定义:一种或多种固体(金属、氧化物、氮化物等)粉末经过成型,在加热到一定温度后开始收缩,在低于熔点温度下变成致密、坚硬的烧结体,这种过程称为烧结。
微观定义:由于固态中分子(或原子)的相互吸引,通过加热,使粉末体产生颗粒粘结,经过物质迁移使粉末体产生强度并导致致密化和再结晶的过程。
由于烧结体宏观上出现体积收缩,致密度提高和强度增加,因此烧结程度可以用坯体收缩率、气孔率、吸水率或烧结体密度与理论密度之比(相对密度)等指标来衡量。
3、与烧结有关的一些概念A.烧结与烧成(firing):烧成:包括多种物理和化学变化。
例如脱水、坯体内气体分解、多相反应和熔融、溶解、烧结等。
而烧结仅仅指粉料经加热而致密化的简单物理过程,烧结仅仅是烧成过程的一个重要部分。
B.烧结和熔融(Melt):烧结是在远低于固态物质的熔融温度进行的。
泰曼发现烧结温度(T S)和熔融温度(T M)的关系有一定规律:金属粉末 T S=(0.3~0.4)T M盐类 T S=0.57T M硅酸盐 T S=(0.8~0.9)T M烧结和熔融这两个过程都是由原子热振动而引起的,但熔融时全部组元都为液相,而烧结时至少有一组元是处于固态。
C.烧结与固相反应:两个过程均在低于材料熔点或熔融温度之下进行的。
陶瓷的烧成详细分析
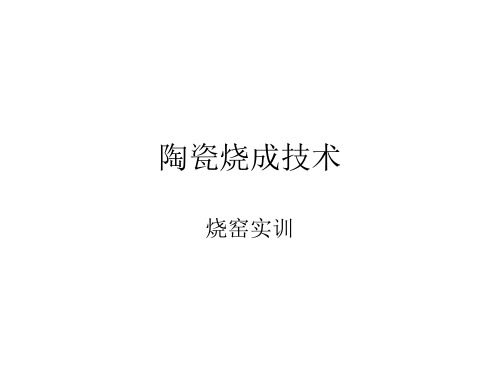
坯体处于弹性状态时,如果加热或冷却过快,则造成坯体内外温 差过大,膨胀不一致,由此引起的热力效应达到了极限值,或因坯体 内外晶型转化不一致而产生的应力达到了极限值,(最常见的是石英 在573的晶型转化),就会使坯体开裂而变成废品。在残余物化结合 水排除阶段,因坯体水分一般都在临界水分以下,不会产生干燥收缩。 但如水分较多,升温过快,水分蒸发过急,则会使坯体炸裂。 坯体在塑性状态时,上述应力受到液相缓冲可能减小或消失。但 当存在较大重力负荷,或因坯体烧成收缩不一致时,坯体就会变形而 成废品,坯体温度愈高,其中液相粘度愈低,就越容易变形。由于烧 成温度不够高或过高,保温时间不足或过长,会导致产品生烧或过烧。 生烧表现为坯体烧结不够,坯体内物理化学变化不充分;过烧则表现 为坯体烧结过分,或发生不希望出现的变化,并常伴随有变形。
陶瓷烧成技术
烧窑实训
陶瓷烧成
• 陶瓷烧成 陶瓷烧成是生产陶瓷制品的主要工序之一。 将生坯或半成品在高温下处理,使其发生 物理、化学变化而得产品的过程。 • 陶瓷的出现离不开窑炉。陶器的烧成温度 约800~1000℃,瓷器的烧成温度约 1200~1300℃。瓷器出现远远晚于陶瓷, 其中一个重要原因就是窑炉技术水平低, 窑炉温度不能达到瓷器烧成要求的温度。
在不过烧的情况下,随着烧成温度的的升高,瓷坯的体积密度增大, 吸水率和显气孔率逐渐减小,釉面的光泽度不断提高,釉面的显微硬 度也随着温度的升高而不断增大。 在烧成温度范围内,适当提高烧成温度,有利于电瓷的机电性能 和细瓷的透光度的提高。 保温是指烧成过程中,达到最高烧成温度范围后,保持一段时间, 或在较低温度下保持一段时间,这段时间称为保温时间,随后进入冷 却阶段。在生产实践中,适当降低烧成温度,延长保温时间,有利于 提高产品品质,降低烧成损失率。保温时间及保温温度对希望釉面析 晶的产品(如结晶釉等艺术釉产品)更为重要。为了控制釉层中析出 晶核的速度、尺寸和数量,这类产品的保温温度往往比烧成温度低得 多,百问世间直接关系到晶体的形成率。 烧成过程中的升降温速度是否恰当,较直观地是看其对制品在烧 成过程中体积热胀冷缩带来的影响(有无变形、开裂)。
陶瓷鉴赏第12章彩绘装饰鉴赏PPT课件

40
一、珐 琅 彩
• 珐琅彩瓷创始于清康熙年间,是在明代一种工 艺品“景泰蓝”的制作工艺的影响下移植、演 化而成的彩瓷装饰技术。
• பைடு நூலகம்泰蓝工艺品是在铜胎上掐以铜丝、再填上蓝、 红、黄、白等色,釉烧而成。其蓝色在景泰年 间最稳定、最鲜艳,由此被称为“景泰蓝”。
第 十 二章
不同彩绘装饰 名瓷鉴赏
1
• 在陶瓷装饰中,除艺术釉装饰外,还有一类为 彩绘装饰。 彩绘装饰主要包括釉上彩绘、釉下彩绘和斗彩 等几大类,它是将我国传统的绘画技术运用到 瓷器中的新工艺。
2
\
第一节 釉下彩绘及鉴赏
釉下彩绘装饰是用釉下颜料,在生瓷胎或素烧瓷 胎表面进行彩绘后,再覆盖一层透明釉,经过高
4、 烧成 :青花在还原焰下1300~1320的温度 中烧成
6
青 花 瓷
7
元代青花瓷
• 色彩鲜艳纯净, 层次分明、浓深 浅淡不同层次的 渲染完全由于工 匠运用色料的技 巧,这类技法使 青花画更接近和 达到国画题材的 表现手法。
8
青 花 罐(人物)
9
青 花 罐(山水)
10
青 花 执 壶
—
明 弘 治
4
一、青 花 瓷
• 青花瓷是以钴矿作为颜料绘于生胎表面,施以透 明釉,在高温下一次烧成的蓝色彩施的釉下彩瓷 器。
• 我国早在唐、宋时期就开始制作青花瓷器。
1、青花瓷特色
是以含钴的兰色颜料作为单一色彩的绘画。由
于白地兰花巧妙配合,相互映辉,画面明快清晰、 雅致大。
彩料的浓淡深浅、线条的粗细疏密、图案大小等
耐火材料重点

第一章:1耐火材料的定义;耐火度不小于1580℃的无机非金属材料分类:按化学成份、矿物组成分类1)氧化硅质2)硅酸铝质3)氧化镁质4)刚玉质5)白云石质MgCa(CO3)2 6)尖晶石质Fe2MgO4 7)橄榄石质Mg2SiO4 8)碳质9)含锆质10)特殊耐火材料按化学性质分类;1)酸性耐火材料2)中性耐火材料3)碱性耐火材料3、按制造方法分类块状耐火材料;不定形耐火材料;烧制耐火材料;熔铸耐火材料。
4、按耐火度分类普通耐火材料(1580~1770℃);高级耐火材料(1770~2000℃);特级耐火材料(大于2000℃)。
按密度分:轻质(气孔率45%-85%)、重质生产过程中的基本知识,如一般生产工艺流程:原料加工→配料→混练→(成型)→干燥→烧成(熔制)→(成型)→检验→成品,配料(颗粒级配又称(粒度)级配,由不同粒度组成的物料中各级粒度所占的数量,用百分数表示。
)混料使两种以上不均匀物料的成分和颗粒均匀化,促进颗粒接触和塑化的操作过程称为混练。
等内容;耐火材料行业存在的问题1)钢铁行业竞争激烈,面临更大的成本压力2洁净钢的生产对耐火材料提出更高要求,除了要求长寿还要对钢水无污染3)研发有待加强,4)应注意可持续发展战略。
存在的差距:1、通常用耐火材料综合消耗指标来衡量一个国家的钢铁工业与耐火材料的发展水平,我国吨钢消耗水还较高。
(见下表)2、耐火材料生产装备落后,新技术推广慢3、原料不精,高纯原料的生产有困难。
,发展趋势:当今耐火材料的发展,一极是不定形化,而另一极则是定形耐火材料的高级化,概括起来就是朝着高纯化、精密化、致密化和大型化。
着重开发氧化物和非氧化物复合的耐火材料。
等。
问题:1合计可用作耐火原料总数为4000余种,其中常用于工业生产的耐火原料只有100种。
why?除了考虑熔点外,还要看它在自然界中存在的数量及分布情况,即作为耐火原料还应该具有来源广,成本低廉。
在地球岩石层中,硅酸盐+铝酸盐数量最大占%。
- 1、下载文档前请自行甄别文档内容的完整性,平台不提供额外的编辑、内容补充、找答案等附加服务。
- 2、"仅部分预览"的文档,不可在线预览部分如存在完整性等问题,可反馈申请退款(可完整预览的文档不适用该条件!)。
- 3、如文档侵犯您的权益,请联系客服反馈,我们会尽快为您处理(人工客服工作时间:9:00-18:30)。
问题1、坯体在烧成过程中有那些物理变化?
五、 强度与硬度的变化
低温阶段随着机械吸附水的消失,强度略 有提高结晶水排除阶段则无明显变化。到了 570℃石英转变时,强度则有所下降750℃以后 强度才逐渐增加,此时应控制好烧成温度防止 过烧。
坯体在750℃以前是非常脆弱的,750℃以后, 由于长石-石英玻璃质及莫来石晶体开始形成, 硬度逐渐增加,在良好的烧成温度下冷却后, 陶瓷器的硬度一般可达莫氏7-8级
然掌握烧窑的科学规律,闯过最后关键工序--烧窑。
2.烧结过程
在烧结过程中,烧结坯发生一系列物理、 化学变化,坯块由粉末颗粒聚集体变成晶 粒结合体,多孔体变成致密体,从而得到 具有所需物理、机械性能的产品。
烧成工序是陶瓷生产过程中最重要的工序 之一,制定科学合理的烧成制度,并准确 执行是产品质量的重要保证。
坯体在烧结过程中会发生哪些宏观上的变 化呢?
陶瓷的烧成
—— “土”与“火”的艺术—— 主讲人:吴任平 教授
思考题
1、何谓氧化气氛烧成,何谓还原气氛烧 成,试述不同气氛烧成的产品外观有什么 不同?原因何在? 2、坯体在烧成过程中有那些物理变化? 烧结程度可用哪些指标来衡量? 3、为什么说在陶瓷生产中烧窑是关键? 4、制定烧成制度的依据有哪些?
2.烧结过程
坯体宏观上的变化: 体积收缩、气孔减少、致密度提高,强度增
加,颜色改变; 烧结程度可以用坯体的: 收缩率、气孔率、体积密度和机械强度 等指标来衡量; 烧结是一个不可逆的过程。
烧结是一个复杂的物理、化学变化过程;
2.烧结与烧成
烧成温度:为了达到产品的性能要求,应该 烧到的最高温度。
4.4制定烧成制度的依据4
四、釉烧方法
1、釉料的熔化温度与坯料的氧化分解温度相适应,中 火保温防止针孔、橘釉、黑心、鼓泡等缺陷。 2、冷却初期依据釉料要求确定冷却速度
光泽釉——快速冷却 结晶釉——结晶温度保温处理 3、二次烧成 高温素烧低温釉烧:釉烧时可以不考虑坯体的脱结 构水及氧化分解排气,素烧时不考虑釉的作用。 低温素烧高温釉烧:釉烧时可以不考虑坯体的脱结 构水,素烧时不考虑釉的作用。 二次烧成其它优点:
2)烧成制度对产品性能的影响
⑤ 压力制度 是实现气氛制度的保障,二者相辅相
成; 参见热压烧结。
问题2:何谓氧化气氛烧成,何谓还原气氛烧成,试述不 同气氛烧成的产品外观有什么不同?原因何在?
在烧窑时火焰在不同时期有不同的性质。火焰的性质大致可 分为三种:氧化焰、还原焰和中性焰,不同性质的火焰有不 同的作用。
1)减少缺陷,提高合格率,避免浪费。 2)坯体强度提高,有利于施釉、装饰 3)工序的机械化。
4.5-4.6 制定烧成制度的依据
五、根据坯料中氧化钛和氧化铁的含量确定气氛制度 低铁高钛坯料(北方)常用氧化气氛烧成; 高铁低钛坯料(南方)常用还原气氛烧成。
六、窑炉结构、容量、燃料和装窑密度
窑炉结构——窑内温度的均匀性,升温速度,烧成 温度。 燃料种类——装烧方法,升温速度,烧成温度。 容量和装窑密度——窑内温度的均匀性,升温速度 。
问题1、坯体在烧成过程中有那些物理变化?
三、 气孔率的变化 气孔率由低温阶段逐渐增加,到氧化阶段末期 达最高峰。以后由于液相的形成和体积的收缩 而逐步降低,到达烧成温度时为最低。如温度 持续升高(即发生过烧现象时)气孔率又随着 坯体的膨胀而增加。
问题1、坯体在烧成过程中有那些物理变化?
四、 颜色的变化
未烧前生坯的颜色取决于坯体中的杂质。有多 量有机物存在时呈灰色,有铁质存在时呈浅黄 色。烧成过程中至中温阶段结束,由于有机物 都已挥发,只有铁质被氧化为Fe2O3,所以一般 呈粉红色。以后经高温烧成后,如是氧化焰则 呈 为浅Fe黄O并色生或成红硅色酸如亚是铁还,原所焰以则呈由泛于青Fe或2O白3被色还,原而 发 发黄生。过日烧用则瓷Fe中O再因次坯被料氧含化铁成量F一e2般O在3而0造.6%成以制下品, 所以无论用氧化焰或还原焰烧成都能得到较高 的白度。
液相的组成和数量以及气孔的形貌和 数量;
过高的烧成温度使新型陶瓷的晶粒过 大或少数晶粒猛增,破坏组织结构的 均匀性,使制品的机电等性能劣化。
2)烧成制度对产品性能的影响
③ 保温时间 使窑炉内部各处温度均匀; 使产品(大件)内部温度均匀,同时
烧结; 保温能促进新型陶瓷的扩散和重结晶,
烧结温度:材料加热过程达到气孔率最小、 密度最大时的温度。
3、烧成制度
1)烧成制度包括的内容:
温度制度:指升温速度、烧成温度、 保温时间及冷却速度;
气氛制度:氧化、还原、中性或其他 气氛;
压力制度:窑炉内气体的压力大小; 实际生产中还要考虑窑炉加热类型、
内部结构和装窑方式等因素。
问题1、坯体在烧成过程中有那些物理变化?
二、 体积的收缩
在低温阶段,由于机械吸附水的蒸发,体积有 微小收缩。当到570℃时,β--石英转化为α --石 英,到870℃时,a--石英又转化为a--鳞石英,这 些多晶转变会使石英比重降低,从而影响到坯 体的收缩,但因日用瓷中坯料石英的含量不多, 因而此阶段体积变化也不大。到了900℃以后, 坯体内液相逐渐形成,结晶颗料由于表面张力 而互相靠拢,收缩逐渐加剧,一直烧结时收缩 最大,一般日用瓷器烧成收缩在8~14%左右。
2)烧成制度对产品性能的影响
① 升、降温速度 坯体慢速升温(24~48h加热至1300℃),其
抗张强度比快速升温(18h内加热到1300℃) 的坯体约增加30%,并且气孔率为1.5%, 快速升温则为3.0%;
缓慢冷却收缩率大,相对气孔率小。
2)烧成制度对产品性能的影响
②烧成温度 Hale Waihona Puke 烧成温度的高低直接影响晶粒尺寸、
烧成
1、概述 :
烧成是陶瓷工艺的第三个重要工序。烧结是 把粉末坯块加热到低于其基本组元的熔点温 度以下进行保温,然后冷却到室温的热处理 工艺。
定义:通过高温处理,使坯体发生一系列物 理化学变化,形成预期的矿物组成和显微结 构,从而达到固定外形并获得所要求效果的 工序。
烧 结 现 象 示 意 图
1、氧化焰:是指燃料完全燃烧的火焰,火焰完全燃烧必须有 大量空气供给,这时窑中的氧气充足,CO较少。为了使坯中 水分及一切有机物都蒸发和挥发排出,使坯体得到正常的收 缩,所以在烧窑过程中必须有氧化焰阶段。
2、还原焰:还原焰是不完全燃烧的火焰。这时窑中所产生的 一氧化碳和氢气多,没有或者极少游离氧的存在。由于还原 焰(能Fe使O)坯,体而内变的成高青价色铁,(消Fe灭2O瓷3)色得发到黄充的分现还象原,变因为此氧在化日亚用铁瓷 的烧窑过程中,多采用还原焰烧成。
4.1 制定烧成制度的依据
一、坯料组分在加热过程中的性状变化
1)相图(晶型转变)和热分析资料(差热曲线DTA、失重曲
线TG、热膨胀曲线TE、ITE)。是确定升、降温速度的依
据之一。
热分析综合图谱
粘土
石英
线膨胀
ITE TE
长石
DTA
4.1 制定烧成制度的依据
利用热分析综合图谱绘制理论烧成曲线
1400 ITE
过长时间的保温可使晶体过分长大或 发生二次重结晶。
2)烧成制度对产品性能的影响
④ 气氛制度
还原气氛对氧化物陶瓷的烧结有促进作用, 在氧分压低的气氛中,如在氢气、一氧化 碳、惰性气体或真空中烧成的,可得到良 好的氧化物陶瓷烧结体;
气氛中存在的水蒸气能促进氧化镁陶瓷坯 体的初期烧结;
在还原性(如氢气)、中性(如氮气)和惰性(如 氩气)气氛中烧成都有利于BaTiO3陶瓷的半 导体化,即有利于陶瓷材料室温阻值的降 低。
3、中性焰:烧中性焰时,窑内所产生的一氧化碳加氢气与进 入窑中的空气化合量几乎相等,处于平衡状态,其作用是使 氧化亚铁不再受氧化作用而恢复成高价铁,最后使坯体达到 完全玻化的目的。但控制中性焰非常困难,常用弱还原焰代 替它。
4 制定烧成制度的依据
4.1 坯料在加热过程中的性状变化 4.2 烧结曲线和高温物相分析 4.3 制品的大小和形状 4.4 釉烧方法 4.5 坯料中氧化钛和氧化铁的含量 4.6 窑炉结构、容量、燃料和装窑密度
小结:为什么说在陶瓷生产过程中烧窑是关键 ?
陶瓷在制造上,最重要的操作就是烧窑。因为陶瓷的制造,从 选择原料到制成成品的工序很多,古人说过手七十二,方克成 器,现在大概也有二十到六十左右的工序。在这些工序中,当 然都各有相当的重要性,尤其是最后的烧窑操作更为重要,稍 不注意就会前功尽弃,既浪费了原材料和燃料,又浪费了大量 人力,在陶瓷工艺方面,就重要性来说,可以分为一烧,二土, 三制作,烧窑是关键之关键。 陶瓷生产上,一般的破损率及合 格率大多数是在烧窑方面,由于烧窑的操作及烧成气氛不合理, 造成破损而降低等级的产品百分率非常多。尤其是颜色釉的烧 成,更要强调烧窑,颜色釉的烧成火焰性质、温度、烧成时间 及燃料种类对颜色的呈色变化有重要影响,有人说颜色釉的烧 成是一门火的艺术,也确有其道理。 要最后得到陶瓷珍品,必
问题1、坯体在烧成过程中有那些物理变化?
陶瓷生产是一个复杂的过程,其中以由泥坯烧 成至瓷器这一环节最为重要。随着温度的不断 升高,坯体内部会发生一系列的物理、化学反 应。其中物理反应的大小主要取决于泥料的各 种组分含量,其物理反应大致有如下几种:
一、 重量的变化
在低温阶段,坯体的失重等于排出的机械吸附 水的重量,至中温阶段由于化学结晶水的排除 而使坯体急剧失重。此外,由于有机物和矿物 杂质的氧化与分解,也会失去一定的重量。而 这些失重的多少视各种坯体的组成不同而不同, 一般变化在3%~8%之间。
1.烧结范围宽、液相粘度大、且随温度变化小 的坯料,烧成温度可以确定在烧结范围上限附 近(T2); 2.烧结范围窄、液相粘度小、且随温度变化大 的坯料,烧成温度只能定在烧结范围下限附近 (T1)