陶瓷烧成缺陷及原因分析
陶瓷烧成缺陷及原因分析

陶瓷烧成缺陷及原因分析(一)变形:产品烧成变形是陶瓷行业最常见、最严重的缺陷,如口径歪扭不圆,几何形状有不规则的改变等。
主要原因是装窑方法不当。
如匣钵柱行不正,匣钵底或垫片不平,使窑车运行发生震动,影响到产品的变形。
另外,产品在烧成中坯体预热与升温快时,温差大易发生变形。
烧成温度过高或保温时间太长也会造成大量的变形缺陷。
使用的匣钵高温强度差、或涂料抹不平时也会造成烧成品的变形。
(二)开裂:开裂指制品上有大小不同的裂纹。
其原因是坯体入窑水分太高(大于2%以上),预热升温和冷却太快,导致制品内外收缩不匀。
有的是坯体在装钵前已受到碰撞有内伤。
坯体厚薄不匀,配件(如壶把、咀等)重量过大或粘结不良也会造成制品开裂。
防止的办法是:(1)入窑坯体水分小于2%,车速适当减少冷却量。
(2)装窑时套装操作谨慎,垫片与坯体配方一致。
配件大小、重量与粘接位置恰当。
有的在粘接泥浆中加入10-15%的釉料,可以使咀、把与主体牢固熔接一体,如此可克服开裂缺陷。
(三)起泡:烧制品起泡有坯泡与釉泡两种。
坯泡分为氧化泡与还原泡两种。
氧化泡指坯泡外面覆盖釉层,断面呈灰黑色,多形成于窑内低温部位。
主要是瓷胎与釉料中的分解物未能充分氧化,烧失物未完全排除所致。
予热升温快,氧化分解阶段时间短、氧化结束时窑内温度过低,上下温度差过大。
在坯釉料中,碳酸盐。
硫酸盐及有机杂质含量较多等都是造成产品起泡的主因。
此外时装车密度不当、入窑水份高等原因亦须注意。
还原泡又称过火泡,断而发黄,多发生于高温近喷火口处的制品。
主要由于坯体内硫酸盐与高价铁还原不足,强还原气氛不足及烧成温度过高造成。
釉泡系沉积炭及分解物在釉熔前未能烧尽挥发,气体被阻于釉面层中形成。
若延长釉熔时间或适当平烧即可解决。
(四)阴黄:制品表面发黄或斑状发黄,有的断面也有发黄现象,多出现在高火位处。
主要原因是升温太快,釉熔融过早,还原气氛不足、而使瓷胎中的fe2o3未能还原成feo。
此外,装钵柱太低,窑顶局部产品温度偏高而还原不足也会形成阴黄缺陷。
陶瓷生产过程中缺陷及解决

陶瓷生产过程中缺陷及解决色差导致色差的原因也各种各样,原料、坯料加工、成形和烧成等各个环节,控制不好都会产生色差。
两批或两块之间色差1、进厂坯用原料质量波动2、颜料加入量为准确3、球磨细度变化4、色料颗粒大小及级配变化5、白料及色料的比例发生变化6、压制成形7、透明釉施加量发生变化8、烧成制度单块砖上的色差1、无规律的色差:A混料器工作状态不佳,B、白料及色料的颗粒尺寸及颗粒级配相差悬殊2、规律性色差产生这种色差的主要原因是由于推料器安装不当或发生变形等导致它与平台配合不良,喂料时将平台上粉料来回搓细后推入模腔造成。
二、夹层夹层又叫起层、层裂、分层和重皮。
出现夹层现象的根本原因是由于模内粉料中的气体排除不畅造成的。
其影响的因素很多,归结起来为二方面的原因:一、是粉料性能方面的原因,另一个是压机方面的原因1、粉料性能对夹层缺陷的影响①粉料水份对夹层缺陷的影响②陈腐时间对夹层缺陷的影响③粉料颗料级配对夹层缺陷的影响④粉料结块对夹层缺陷的影响⑤粉料表面质量对夹层缺陷的影响2、冲压制度不合理导致夹层缺陷3、模具问题导致夹层缺陷三、变形影响变形的因素很多,如坯体配方、成形、干燥制度等都会导致变形的产生。
对瓷质砖来说,影响最大的还是烧成制度,主要是辊道上下温差设定不合理所致。
烧成对变形的影响1、翘角这种变形的特点是坯体的四角都上翘,长度约为30mm,其余表面是平直或只有少许下凹,这种缺陷发生于窑的中间与两侧。
它是由于烧成后期辊道平面上下温差过大所致。
一般多发生在烧成过程的最后2-5分钟。
解决的办法:①、如果出窑尺寸正确,降低烧成带最后2—3组(箱)辊棒上部的温度(5—10℃或更高,视调试效果确定)并对等升高辊道下面的温度。
②、如果烧成后产品尺寸偏大,则仅升高辊道下面的温度5—10℃度或更多,(视调试效果确定)③、如果烧成后产品尺寸偏小,则仅升高辊道上面的温度5—10℃度或更多,(视调试效果确定)2、角下弯角下弯下好与翘角缺陷相反,它是坯体的四周都下弯,长度约30mm,其余表面是平直或只有少许下凸。
陶瓷质量缺陷修补记录

陶瓷质量缺陷修补记录
概述
本文档记录了陶瓷制品在生产过程中出现的质量缺陷情况,并列出了相应的修补措施和结果。
缺陷一:裂纹
- 缺陷描述:陶瓷制品表面出现明显的裂纹。
- 原因分析:制造过程中温度变化不均匀,导致陶瓷材料出现应力集中。
- 修补措施:使用高温烧结修复技术对裂纹进行修补。
- 修补结果:修补后的陶瓷制品表面裂纹得到有效修复,质量恢复良好。
缺陷二:气泡
- 缺陷描述:陶瓷制品表面存在气泡。
- 原因分析:制造过程中陶瓷材料中的气体未能完全排出,导致气泡形成。
- 修补措施:使用局部烧结修复技术填补气泡。
- 修补结果:经过修补后,陶瓷制品表面的气泡完全被填补,质量得到有效改善。
缺陷三:颜色不均匀
- 缺陷描述:陶瓷制品表面颜色出现明显的不均匀情况。
- 原因分析:制造过程中添加的颜料分散不均匀,导致陶瓷颜色出现不均匀。
- 修补措施:使用特殊配方的颜料进行局部涂抹修复。
- 修补结果:经过修补后,陶瓷制品表面颜色恢复均匀,质量得到有效改善。
结论
通过以上的修补措施,陶瓷质量缺陷得到了有效修复,陶瓷制品的质量得到了明显提升。
我们将继续改进生产工艺,确保陶瓷制品的质量达到最高水平。
卫生陶瓷缺陷分析

卫生陶瓷缺陷分析着重对其中几种缺陷产生的原因进行分析讨论。
一、变形1、坯料方面①坯料配方不当。
②注浆用的泥浆搭配不合理。
③泥浆成形性能差。
④少于浆速度过慢、中断供浆,会造成坯体塌陷变形。
2、成形及半成品加工方面①注浆模型过干,擦模方法不当;擦模不均匀;模内湿坯收缩不一致,使坯体局部塌陷或局部过早脱模。
②在注浆过程中,由于泥浆表面起皮,或在封闭模型的的漏浆过程中在空腔内产生了负压,形成湿坯塌陷。
③过早脱模,坯体含水率偏高;修坯、粘接操作不当;坯体偏薄或厚薄不一致等。
④模型整体或局部不符合规定要求,失去对坯体的控制作用。
3、烧成方面①装窑方法欠妥。
②烧成制度尤其是烧成温度不合理,烧成温度过高,或局部温度过高等,引起制品变形。
二、裂纹1、原料与坯料方面①原料杂质多,洗、选料不符合要求,有杂质混入坯料。
②坯料配料不准;低可塑性原料用量不当;泥浆细度不合适,过粗或过细;注浆所用泥浆的温度过高。
③泥浆性能不稳定;电解质加入量不当,泥浆过于粘稠;陈腐时间过短;相对密度不合适。
2、成形与半成品加工方面①擦模过程中,用力不均匀或操作方法不当。
②揭模或湿坯脱模过早、过晚。
③模型结构复杂,模型造型或结构本身影响湿坯在模型内均匀地收缩。
④模型对口缝处溢浆,使坯体在对口缝处开裂。
⑤坯体脱模后,在某一部位的重力作用下,使悬空部位接茬处开裂,或某一部位含水率高,受力不均匀,造成坯体开裂。
⑥脱模湿坯与垫托接触部位不相吻合、垫托上有异物,坯体受外力作用而开裂。
⑦修坯粘接时,刀具不锋利,用力不均匀,坯体含水率过高或过低,室内温度高,室外多风等,造成割口与修坯部位开裂。
粘接坯体不实、不牢;各部件与主休含水率不同,收缩不一致,使坯体在干燥时开裂。
⑧打孔眼操作不变,打孔器具不锋利,造成制品眼孔部位开裂。
⑨坯体的底部、凹沟处、漏浆处存浆,或底部模型过干、过湿而造成制品开裂。
⑩坯体在施釉过程中或在存放、搬运、接触等环节不慎磕碰,造成制品开裂。
陶瓷缺陷

生烧[shēng shāo]underfiring制品未达到烧结温度称为生烧。
生烧制品结构疏松、强度较低、收缩小而尺寸不符合要求、密度低、吸水率高、上釉制品釉面无光等缺陷。
引起生烧的原因主要是烧成温度过低或升温速度过快,保温时间太短等。
窑内温度分布不均匀也会引起局部生烧。
可用酒精品红溶液作染色试验进行鉴别。
“北有钧瓷,南有爆花,自然生花,堪称国宝。
”“爆花”实为结晶釉“爆花”为制瓷工艺,不用绘图,烧制中自然在瓶体爆出各种各样的美妙绝伦的逼真图案,令人拍案叫绝。
“‘爆花’科学的说法应该叫结晶釉。
”上世纪六七十年代,“爆花”曾在佛山辉煌一时。
在石湾民间流传着一个故事:曾有日本富商,对“爆花”异常逼真的图案惊叹不已,赞其为世间极品。
商人在购买产品的同时,还要求学习制作技术。
不过,石湾人只出售产品,不“出口”技术。
产品变化导致“爆花”使用减少改革开放以来,这项工艺的使用越来越少了。
因为窑温不容易控制,所以结晶釉出品不稳定,就少用这一工艺了。
不过,结晶釉这项工艺在台湾和江西景德镇仍在应用。
对此,有专家认为,结晶釉工艺使用减少,主要是产品结构和设备结构发生了变化。
目前,佛山生产的多是陶塑艺术品,而结晶釉多用在花瓶等瓷器上。
随着市场需求和产品定位的变化,结晶釉工艺的使用就越来越少了。
另外,结晶釉烧制工艺较复杂,对窑温控制要求很高。
目前,美术陶瓷厂的窑使用的是石油气,这种窑并不适合烧制结晶釉。
而在江西景德镇因为产品以瓷器为主,使用的又是电窑,更利于结晶釉工艺的发挥和保留。
炸釉炸釉由于坯釉的膨胀系数不相适应而造成瓷器釉面炸裂产生裂纹现象。
产生原因(1)配方不当,坯釉之间的膨胀系数差距过大,致使冷却时釉面受到一张应力,此应力超过允许强度,将发生釉裂,反之,当釉的膨胀系数小于坯体时所产生的应力则引起剥釉。
(2)釉料加工过粗或过细,釉层过厚。
(3)产品形状设计不合理,出现釉层厚薄不均。
(4)隐藏在坯体内部的裂纹或应力延及到釉层表面。
建筑陶瓷缺陷成因分析及解决方法

人为因素 、粉料因素 、压机因素 、施釉因素 、 立式干燥器因素、窑炉因素 ♦ 裂纹缺陷产生的具体表征 : 1、人为因素 施釉线受力不均,皮带不水平。集砖器不合理集 砖,左右带速不一致,导致砖坯碰撞较多。补偿器使 用不合理,人工补偿易使坯体存在应力。贮坯车托辊 变形,立式干燥器吊篮托辊弯曲,圆整度不够,装卸 坯车操作不当,光电管设置不合理。车间湿度太大。 翻转器碰撞较多。
♦ 缺陷出现的辅助性原因预防及克服
一般要想达到快烧,那么必须保证较低的入窑 水份。但由于生产中各方面因素影响较多,为 此当出现裂纹缺陷的征兆时,要有足够的预见 性,窑炉及施釉生产线应给予积极配合。 ♦ (1)在保证其流动度和施釉量的前提下,要 尽可能降低面釉水份,以减少砖坯吸湿。 ♦ (2)在保证不粘辊棒的前提下,尽可能少施 底釉。 ♦ (3)在入窑水份大或空气湿度大的情况下, 要降低窑头温度,延长预热带周期,加大排湿 力度。
♦ 3、色差
渗花砖的色差是困扰很多厂家的问题,产生 色差的主要原因是坯料波动和烧成条件变化, 同时生产过程控制不严也易造成色差。 ♦ 原料储存量少,每一批次原料使用时间短, 容易造成原料的化学成分波动大。 ♦ 空窑是造成色差的另一主要原因,空窑会造 成窑炉气氛改变,从而导致坯体色差。 ♦ 窑炉断面温差和烧成气氛也是造成色差的一 个原因。由于坯体温度的变化引起渗花釉流动 性显著变化,影响渗透深度和扩散性,如果波 动大易产生色差。
♦ 4、渗花图案模糊 ♦ 渗花砖抛光后图案很浅或者模糊不清,甚至图案不完
2)通常发生的原因是渗花砖都喷淋了一 定量的助渗剂,由于助渗剂只淋在砖坯 表面,造成表面的水分偏高,入窑时, 如果窑头温度过高,水分急剧蒸发,砖 坯表面收缩量大,就会在砖坯上表面的 边上出现裂纹,由于砖坯底部水分低, 蒸发量少,很少出现裂纹。 3)解决此种缺陷的主要手段是调节入窑 温度:设定一个合理的入窑升温曲线, 降低预热带的升温速度,尤其是预热带 的温度要低。
陶瓷新思维之缺陷分析(含注浆)

大华陶瓷杯类产品缺陷统计
大华陶瓷碟类产品缺陷统计
杯类缺陷分布图
碟类缺陷分布图
大华陶瓷应对措施
预防措施
案例总结
• 在日用陶瓷中陶瓷的装饰缺陷通过提前预防可以 达到较好的改善效果。 • 随着湿度的增大,应加强通风。若温度较低时, 应通过增大湿度以缓和湿度骤减而引起的釉裂等 缺陷的发生。缺陷控制的同时应该结合生产和人 员的管理进行,尤其随着人们环保意识的提高, 会对陶瓷装饰所用的添加剂产生一定的抵触心理 %,会在一定程度上影响产品的合格率,需要结 合一定的生产管理知识进行预防和纠正。
在此录入文字标题
(1)坯体入窑水分过高,加上预热带温度低, 碳素沉积釉中。釉的始熔温度低,釉料玻 化过早,而使沉积在釉层中的碳素不能分 解排出。 (2)坯料中碳酸盐、硫酸盐含量过高. (3)过干过热的坯体施釉,坯体与釉浆温差过 大,不能使釉料被坯体均匀吸收,导致有 些地方釉面过厚,烧成时容易封闭气孔, 使气体无法外逸。
(5)石膏模与模座不吻合
滚压常见缺陷三
产生原因
滚压成型时,滚头转速低,产生下凹花心; 滚压机转速比不合理,转速比过大则产生坯 体底心上凸的花心;滚头与模座停转时间配 合不好;热滚压成型时滚头顶部温度过高; 坯体含水率太低;泥饼在模中放置不正;使 用新模或模型与模座配合太松成型机轴承间 隙过大。
肆 瓷之物语•窑火
解决问题
• 根据结果调整了配方, 烧成有所好转。
• 请问各位问 题解决了吗?
初步结果
• 经过几次调整, 杯把把裂的情况有所好转,但 是生产不过十天又出现反复, 一直没有得到
根治。
• 因此, 技术员就大胆进行新的尝试: 用杯身 泥进行化浆注杯把的试验(行内人称之为:原 泥化浆)。
三.辊道窑常见烧成缺陷的分析

延长前温区域(多开烧咀)适当升高温度,中前温区的挡火板适当升高;另外视助燃风风量可否通过加大助燃风来提
高前温区的温度。
适当提高中温区温度 (上下同升);中高温区交接挡火板适当升高来升温,同时检查上下枪油压偏差是否正常,因上下油压偏差过大,形成面温是" 虚温"(下油压明显高于上油压)。如底温高是下弯拱的,那么降低底温,降低末段1~2组底温,保持面温,注意尺寸变化,必要时适当升高面温,在温度不变的情况下;将面枪油压适当升高,底枪油压适当降低。
烧成温度发生大的变化,会影响烧后坯体的白度,而烧后坯体呈色不正常,在色点和底色的相互衬托下,必将影响色点装饰效果,产生色差。
通常情况下,瓷质砖是氧化气氛烧成,如果助燃空气的送风量、排烟风机的抽风量等发生变化,都有可能造成还原气氛,会使砖面发青或发暗,从而产生色差。
窑压的波动,会改变原来设定的烧成制度,使预热带、烧成带和冷却带的长度发生变化而影响烧成,从而造成色差。
适当加大窑炉负压。适当加大抽烟总风量。
注意砖的运行是否整齐?一排砖各块砖走快慢,形状如何?进行机械性调整,检查走砖疏密;适当调节中高温区上下,平衡上、下温度。
3.2.3磨边、抛光的影响
仿古砖、抛光砖等瓷质砖,出窑经过磨边、抛光(半抛)之后,会变的很翘,只要坯、釉膨胀系数匹配,成品还是会变直的。
1)釉料配方
抛光砖不施釉,不存在坯釉膨胀系数不匹配引起的砖形变化。而仿古砖则存在这样的问题。其面釉膨胀系数正常情况下都能和坯体相适应;但做浅色、白砖(特别对白度有特殊要求的砖)时,由于其膨胀系数小,砖烧出来一般很拱。另外,有时由于效果需要(如凸釉等)釉料会调的很高温,膨胀系数很小,也存在这样的问题。
陶瓷工艺学--8 烧成-09.10

这些碳素和有机物加热即发生氧化反应:
C(有机物)+O2
350º C
CO2
C(碳素)+O2
2H2 + O2
600º C
CO2
2H2O
250~ 920º C
S + O2
2CO+O2
SO2
2CO2
这些反应要在釉面熔融和坯体显气孔封闭前
结束。否则,就会产生烟熏、起泡等缺陷。
2. 硫化铁的氧化 FeS2+O2
1. 升温速度的确定
A.低温阶段:升温速度主要取决于坯体入窑时的 水分。
如果坯体进窑水分高、坯件较厚或装窑量大,则升
温过快将引起坯件内部水蒸气压力增高,可能产生开 裂现象; 对于入窑水分不大于1%~2%的坯体,一般强度也 大,在120℃前快速升温是合理的;对于致密坯或厚胎
坯体,水分排除困难,加热过程中,内外温差也较大,
3MgO4SiO2H2O
600~ 970º 3(MgOSiO )(原顽火辉石)+ SiO +H O C 2 2 2
蒙脱石脱水:
Al2O34SiO2nH2O
Al2O34SiO2+nH2O
5. 晶型转变
石英在573℃时, -石英迅速地转变为 -石英, 体积膨胀0.82%;在870℃-石英缓慢地转变为 -鳞石 英,体积膨胀16%。石英晶型转变造成的体积膨胀, 一部分会被本阶段的氧化和分解所引起的体积收缩所 抵消。如果操作得当,特别是保持窑内温度均匀,这 种晶型转变对制品不会带来多大的影响。 由粘土脱水分解生成的无定形Al2O3,在950℃时 转化为-Al2O3。随着温度的升高,-Al2O3与SiO2反应 生成莫来石晶体。
(三)高温玻化成瓷阶段 (从950℃到最高烧成温度)
陶瓷烧结内部缺陷

陶瓷烧结内部缺陷
陶瓷烧结内部缺陷是指在陶瓷材料烧结过程中,出现的不完全烧结、气孔、裂纹、包裹物等不良现象。
这些缺陷会降低陶瓷材料的强度、导热性能、气密性等物理性能,严重影响其使用效果。
造成陶瓷烧结内部缺陷的原因有多种,主要包括以下几个方面:
1. 原料质量不过关:原料中含有杂质、颗粒不均匀、颗粒聚集等问题,会导致烧结过程中出现不良缺陷。
2. 烧结温度不适宜:烧结温度过高或过低都容易引起缺陷。
温度过高会导致颗粒烧结不充分,出现气孔和裂纹;温度过低则会导致颗粒无法烧结在一起,形成脆弱的材料。
3. 烧结时间不足:烧结时间不足无法达到完全烧结的效果,会导致内部缺陷。
4. 烧结过程中的气氛不合适:烧结中的气氛对陶瓷材料的质量有很大影响。
若氧气含量过高,会导致氧化反应过剧烈,形成气孔和裂纹;若氢气含量过高,会造成还原反应不充分,使材料质量下降。
为了减少陶瓷烧结内部缺陷的发生,可以采取以下措施:
1. 严格控制原料质量,避免杂质和不均匀颗粒的存在。
2. 控制烧结温度和时间,确保烧结充分而不过度。
3. 优化烧结气氛,使之适应具体陶瓷材料的烧结要求。
4. 加入助烧剂或增稠剂,改善烧结性能,减少缺陷的发生。
5. 增加烧结压力,可以提高瓷体的致密性,减少气孔和裂纹的发生。
卫生陶瓷烧成缺陷分析及对策方法探讨

进行 分析探 讨 。
《 代 建筑卫 生陶瓷 工程 师手册 》坯 体温 差 : 现 ,
△ t: 一 / 2Ⅱ
l 烧 成 缺 陷分析
烧成制度 包括 温度制 度 、 力制 度和气 氛 制度 , 压 其 中压力制 度决 定 了温 度 制度 , 即好 的 压力 制 度 是实 现 温度 曲线 的保 证 , 而烧成气 氛 决定 了物理 、 化学反应 的
预热 带坯体 处 于膨 胀 过 程 , 温度 曲线 的 调整 婴 参 考泥 浆的热膨胀 曲线 , 即热膨胀 曲线斜 率大 的温度 段 , 升温速度 要缓慢 。 若 坐便 器 结 构复 杂 ,{ 差 产 勺 _温 ! 『 I 】
维普资讯
20 . o 1 0 6 N .2
维普资讯
・
2 ・ 6
陶 瓷
卫生 陶 瓷 烧 成缺 陷 分 析 及又 策 方 法捻 讨 J 1
杨 纪 岩
( 陶机 器( 京) 限公 司 北 京 10 9 ) 东 北 有 0 0 6
摘 要 简 述 了隧 道 窑 在 氧 化气 氛 条件 下 卫 生 陶瓷 的 部 分 烧 成 缺 陷 , 并对 缺 陷 产 生 的 原 因 及 对 策 方 法 进 行 丁 探 讨 分 析 。 关键 词 预热带 烧成带 冷却 带 M值
程度 , 卫生 陶瓷烧 成一般 都选用 氧化 气氛 。 从窑头 到制 品开 始烧 结 前 的 升温 段 称 为 预热 带 。 在此 阶段 , 坯体 、 层会 经历 一系列 物理 、 学 变化( 釉 化 包 括 自由水 、 构水 排 出 、 结 石英 的晶型转 化 、 素 的氧化 、 碳 白云石分 解 、 化 物分 解 及体 积 的膨 胀收 缩 等 过稚 ) 硫 , 烧成 开裂 、 化物 落 脏 主要 发 生 在这 一 阶 段 。渊整 好 硫 一 此 阶段 的温度 曲线对 解决 生产 的实 际问题具 有 相 当重
陶瓷缺陷分析
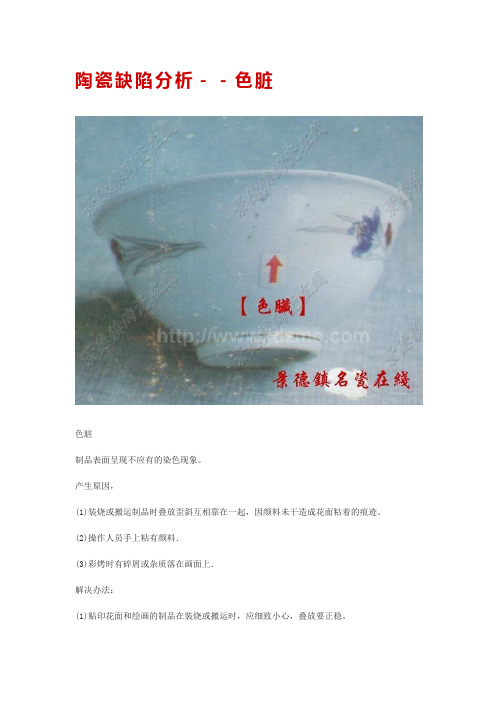
陶瓷缺陷分析--色脏色脏制品表面呈现不应有的染色现象。
产生原因,(1)装烧或搬运制品时叠放歪斜互相靠在一起,因颜料未干造成花面粘着的痕迹。
(2)操作人员手上粘有颜料.(3)彩烤时有碎屑或杂质落在画面上.解决办法:(1)贴印花面和绘画的制品在装烧或搬运时,应细致小心,叠放要正稳。
(2)操作人员工作时手上要保持干净,勿粘颜料。
(3)防止彩烤碎屑、杂质落在画面上。
陶瓷缺陷分析--画面彩色不正画面彩色不正(1)画面缺陷--面面残缺和色泽不正的现象.(2)彩色不正--同一花纹色彩浓淡不匀或由于欠火而产生不光亮的现象。
产生原因:I.釉下装饰(1)分水时,水色、浓淡、厚薄不统一。
(2)施釉时,釉层厚薄不一或画面不干净.(3)花纸上的料没有全部贴坯上,或使用了不符合要求的花纸,以及纸上料色有浓淡不匀的现象。
(4)烧成温度低或烧成气氛不当,使釉面没有充分玻化,花纹色彩不易进出.(5)烧成时由于吸烟或者是欠釉影响产品的呈色效果.2.釉上装饰(1)花纸质量不好或存放时间过长而变质.(2)操作技术不熟练,贴花时未贴妥,而鼓有空气,随着彩烤时温度上升,气泡胀破,导致爆花,或花纸正反面贴错,会造成严重爆花.(3)贴薄膜花纸时,所用酒精配制不当.(4)彩烤时,从色料中或花纸中所产生的气体会对其它产品上的色料发生反应,从而出现呈色不良.(5)所使用的燃料其含硫量过高,使气氛中的二氧化硫与釉料或色料中氧化钙及其它化合物生成硫酸盐,从而使彩色失去光泽。
(6)装烤方式或装载量不当。
(7)彩烤温度过高或过低,使彩色不正。
解决办法:1。
釉下装饰(1)熟悉釉下贴花的操作技术,以及手工工艺,掌握釉下花面的色彩浓淡要求,调好料浆水份.(2)保管好花纸,防止受潮或过干,产生贴花的问题。
(3)掌握釉下贴花产品的施釉厚度,防止过厚或过薄。
(4)制定合理的烧成制度,防止吸烟和烧成气氛不良的现象。
2.釉上装饰(1)妥善保管好花纸,勿使其受潮变质,注意先进厂的先用,保管时间不超过两年,若时间过久将会自然老化变质。
卫生陶瓷开裂缺陷的种类成因和克服方法

卫生陶瓷开裂缺陷的种类成因和克服方法卫生陶瓷是一种常见的建筑材料,被广泛应用于厨房和卫生间等环境中。
然而,卫生陶瓷常常会出现开裂缺陷,可能会降低其使用寿命和美观度。
本文将讨论卫生陶瓷开裂缺陷的种类、成因和克服方法。
首先,烧结缺陷是指卫生陶瓷在生产过程中,由于烧结不均匀或烧结温度不正确等原因,导致整体或局部瓷块存在缺陷。
烧结缺陷常常表现为开裂、气孔等。
开裂可以分为开板裂纹、冷却裂纹和热应力裂纹等。
开板裂纹是指瓷块在烧结过程中由于板坯在收缩时遇到阻力,导致瓷块表面出现裂纹。
冷却裂纹是指瓷块在从高温状态冷却到室温时,由于温度变化引起的开裂。
热应力裂纹是指瓷块在受到外界温度变化或热应力的作用下,产生的表面和内部开裂。
其次,晶粒生长不良是指陶瓷中晶粒的尺寸和分布不均匀,导致瓷表面产生缺陷。
晶粒生长不良是由于原材料的成分和烧结工艺等因素引起的。
晶粒生长不良可能导致瓷表面出现凹凸不平、斑点等问题。
最后,应力缺陷是指瓷块在使用过程中由于外界压力引起的开裂。
应力缺陷可能是由于装配、变形等原因引起的。
应力缺陷可能导致瓷块表面和内部出现裂纹。
针对卫生陶瓷开裂缺陷的成因,可以采取以下方法加以克服。
首先,改进生产工艺和控制烧结温度。
提高生产工艺的精确性,确保瓷块的烧结温度均匀。
同时,要严格控制烧结温度的范围,以确保瓷块达到最佳的烧结效果,减少烧结缺陷的发生。
其次,优化原材料配比。
通过调整原材料的成分,可以改变瓷块的物理性质,提高其抗开裂性能。
特别是要注意控制瓷块的氧化物含量,避免过多的氧化物对瓷块的烧结效果产生不良影响。
此外,增加材料结构的均匀性。
可以通过优化瓷块的结构和形状,增加瓷块材料的均匀性。
这可以降低瓷块受到外界作用时的应力集中,减少开裂缺陷的发生。
最后,加强检测和质量控制。
在生产过程中,应增加对瓷块的检测步骤,及时发现和修复存在的缺陷。
此外,要加强与供应商和客户的沟通,了解其对产品质量的要求,以便在生产过程中进行相应的调整。
113烧成气氛对产品缺陷的影响

4、烧成气氛的控制
烧成气氛的控制受到窑炉结构和设备配置的限制,比如风机风量的大小,风管直径的大小,排烟口、抽热口、抽湿口位置的设置等,都会影响到烧成气氛的控制。但是,最关键的还是稳定压力制度和合理操作燃烧器。
4.1稳定压力制度压力变化会影响到气体的流动状态,因此窑内压力制度的波动会引起气氛的波动,要控制好气氛,就必须稳定好压力制度,而稳定压力制度的关键在于控制好零压面。在窑炉预热带,因要排走水分和燃烧时产生的烟气,故压力相对比窑外环境的低,对比之下窑内气压处于负压状态;在冷却带要鼓入冷空气使制品冷却,压力相对比窑外环境的高,对比之下窑内气压处于正压状态;在正负压之间有一零压面,烧成带就处在预热带和冷却带之间,因而零压面的移动就会引起烧成带气氛的变化。当零压面位于烧成带前段,处于烧成带与预热带之间时,烧成带的气压为微正压状态,气氛为还原气氛;当零压面位于烧成带的后端时,烧成带处于微负压状态,气氛为氧化气氛。
3、烧成气氛对产品缺陷的影响
陶瓷产品在烧成过程中会发生一系列的物理化学反应,如水分的蒸发,盐类的分解,有机物、碳和硫化物的氧化,晶型的转变,晶相的形成等。这些物理化学反应的速度,除了受温度影响之外,气氛对其也有很大的影响,如果控制不当,就会使陶瓷产品产生各种缺陷,下面介绍最常见的几种缺陷。
4.2合理操作燃烧器烧成的燃料是否完全燃烧将会影响到窑炉气氛,特别是烧成带的气氛。因此合理地操作燃烧器,控制好燃料的燃烧程度,是控制窑内气氛的重要手段。在燃料完全燃烧的情况下,燃料中的全部可燃成分在空气充足时能完全氧化,燃烧产物中没有游离C及CO、H2、CH4等可燃成分,保证氧化气氛的实现;当燃料不完全燃烧时,燃烧产物中存在一些游离C及CO、H2、CH4等,使窑内气氛呈还原性。要使燃料完全燃烧,须注意以下三点:①确保燃料与空气充分,均匀地混合;②保证充足的空气供给,并保持一定的过剩空气量;③确保燃烧过程在较高的温度下进行。
陶瓷砖圆弧形“掉角”缺陷的成因及解决
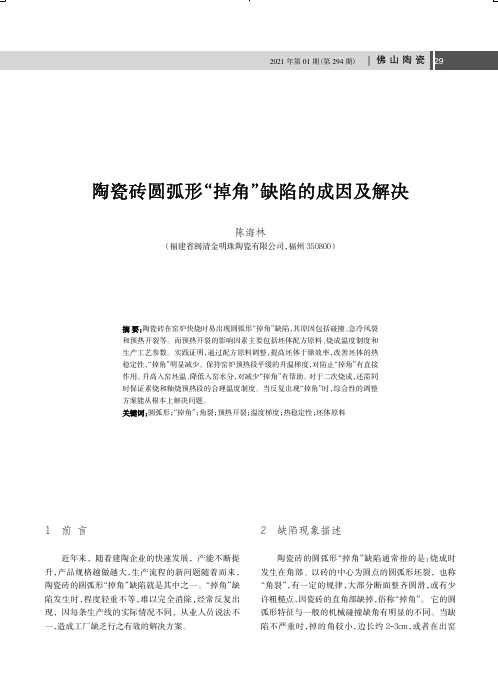
1前言近年来,随着建陶企业的快速发展,产能不断提升,产品规格越做越大,生产流程的新问题随着而来,陶瓷砖的圆弧形“掉角”缺陷就是其中之一。
“掉角”缺陷发生时,程度轻重不等,难以完全消除,经常反复出现,因每条生产线的实际情况不同,从业人员说法不一,造成工厂缺乏行之有效的解决方案。
2缺陷现象描述陶瓷砖的圆弧形“掉角”缺陷通常指的是:烧成时发生在角部、以砖的中心为圆点的圆弧形坯裂,也称“角裂”,有一定的规律,大部分断面整齐圆滑,或有少许粗糙点,因瓷砖的直角部缺掉,俗称“掉角”。
它的圆弧形特征与一般的机械碰撞缺角有明显的不同。
当缺陷不严重时,掉的角较小,边长约2~3cm,或者在出窑陈海林(福建省闽清金明珠陶瓷有限公司,福州350800)“掉角”缺陷,其原因包括碰撞、急冷风裂和预热开裂等。
而预热开裂的影响因素主要包括坯体配方原料、烧成温度制度和生产工艺参数。
实践证明,通过配方原料调整,提高坯体干燥效率,改善坯体的热稳定性,“掉角”明显减少。
保持窑炉预热段平缓的升温梯度,对防止“掉角”有直接作用。
升高入窑坯温、降低入窑水分,对减少“掉角”有帮助。
对于二次烧成,还需同时保证素烧和釉烧预热段的合理温度制度。
当反复出现“掉角”时,综合性的调整方案能从根本上解决问题。
“掉角”;角裂;预热开裂;温度梯度;热稳定性;坯体原料图1预热开裂口砖的角部已出现圆弧形裂纹,然后在平台滚动过程中掉去。
而缺陷严重时,少则一个砖角缺掉,多则四个砖角全部缺掉,且掉的角较大,边长可达到10cm 或以上,甚至类似于窑炉冷却不当引起的弧形开裂。
3缺陷的形成原因及解决方法笔者查阅了近年来一些同行解决“掉角”缺陷的宝贵经验,结合自己在日常生产中的调试实践,将圆弧形“掉角”缺陷按形成原因及解决方法分为三类,列举如下:由于粉料的颗粒级配不合理,流动性差,或模具的设计存在一定缺陷,造成砖坯的角部致密度(强度)低,如果发生机械碰撞,有可能会产生圆弧形“掉角”。
陶瓷烧制中常见的釉面缺陷及处理方法

陶瓷烧制中常见的釉面缺陷及处理方法陶瓷作为一种古老而又广泛应用的材料,其独特的质感和美观的外观使其在建筑、餐具、装饰等领域得到了广泛的应用。
然而,在陶瓷的烧制过程中,常常会出现一些釉面缺陷,影响了其质量和美观度。
本文将介绍几种常见的釉面缺陷及其处理方法。
首先,我们来讨论一下釉面开裂这一常见的缺陷。
釉面开裂可能是由于釉料与胎体的热胀冷缩系数不匹配所引起的。
在烧制过程中,釉料和胎体会因为温度变化而产生不同程度的膨胀和收缩,如果两者之间的差异过大,就会导致釉面开裂。
为了解决这个问题,可以采取一些措施,如调整釉料的成分,增加胎体的强度等。
此外,适当控制烧制温度和速度也是防止釉面开裂的有效方法。
另一个常见的釉面缺陷是釉面流挂。
釉面流挂是指在烧制过程中,釉料在陶瓷表面形成一层厚重的流挂,影响了陶瓷的外观和质感。
釉面流挂的原因有很多,例如釉料的粘度过高、烧制温度过高等。
为了解决这个问题,可以通过调整釉料的成分和粘度来控制釉面的流动性,同时适当降低烧制温度,避免釉面流挂的发生。
除了釉面开裂和釉面流挂,还有一种常见的釉面缺陷是釉面气泡。
釉面气泡是指在烧制过程中,釉料中的气体无法完全排出,形成的气泡在釉面上留下了不美观的痕迹。
釉面气泡的形成与釉料的成分、烧制温度等因素有关。
为了避免釉面气泡的产生,可以采取一些措施,如调整釉料的成分、控制烧制温度和时间等。
此外,还可以在釉料中添加一些消泡剂来减少气泡的形成。
此外,在陶瓷烧制过程中,还会出现一些其他的釉面缺陷,如釉面色斑、釉面剥落等。
这些缺陷的产生原因各不相同,处理方法也各有不同。
对于釉面色斑,可以通过调整釉料的成分和配比来解决。
对于釉面剥落,可以采取一些措施,如增加釉料的附着力、增加胎体的强度等。
总之,陶瓷烧制中常见的釉面缺陷给陶瓷的质量和美观度带来了一定的影响。
通过对釉面缺陷的原因进行分析,我们可以采取相应的处理方法来解决这些问题。
调整釉料的成分、控制烧制温度和时间、增加胎体的强度等都是有效的方法。
卫生陶瓷开裂缺陷的种类成因和克服方法

卫生陶瓷开裂缺陷的种类成因和克服方法卫生陶瓷是一种常用于卫生洁具和浴室装饰的材料,其质量直接关系着人们的生活品质和安全。
然而,卫生陶瓷在生产和使用过程中,常常会出现开裂缺陷,严重影响产品的使用寿命和安全性。
本文将分析卫生陶瓷开裂缺陷的种类、成因和克服方法。
卫生陶瓷开裂缺陷的种类可以分为内部开裂和外部开裂两大类。
内部开裂一般发生在卫生陶瓷的结构内部,如坯体和釉面的界面,常见的有晶粒开裂、浸透性裂纹、烧结缺陷引起的气孔等;外部开裂则是指卫生陶瓷表面产生的开裂缺陷,如釉面开裂、抛光开裂等。
1.原材料质量问题:卫生陶瓷生产常用的原材料有陶瓷粉体、釉料、填料等,如果原材料质量不合格,其中含有杂质或未经充分混合,容易导致开裂缺陷。
2.烧成工艺控制问题:卫生陶瓷的烧成是一个关键的制造工艺,烧成温度、时间和气氛的控制与开裂缺陷密切相关。
例如,烧成温度过高或过低、升温速率不合适等都会引起瓷体的开裂。
3.设计和制造工艺问题:卫生陶瓷产品的设计和制造工艺也是开裂缺陷的重要原因。
例如,产品设计中存在结构不合理的地方,容易出现应力集中,从而引起开裂。
制造工艺中,包括浇注、降温、研磨抛光等环节的控制不当也会导致开裂。
针对卫生陶瓷开裂缺陷,可以采取以下方法进行克服:1.提高原材料质量:加强原材料的筛选和质检工作,确保原材料无杂质、粒度均匀,并进行充分混合。
材料的质量直接关系着最终制品的质量。
2.优化烧成工艺:通过调整烧成温度、时间和气氛等参数,确保瓷体能够均匀烧结、收缩均匀,并避免过度烧结导致开裂。
此外,还可以采用预烧降温等特殊工艺方法来减小烧结产生的应力和开裂风险。
3.优化设计和制造工艺:在产品设计阶段,加强力学性能分析,避免应力集中;在制造工艺中,加强工艺控制,确保每一个环节的严格把关,特别是涂料施工、研磨抛光等环节,避免过程中引入新的缺陷。
4.加强质量管理和监控:建立完善的质量管理体系,加强对卫生陶瓷生产过程中各环节的监控和检测,及时发现和解决问题,确保产品质量的稳定和可靠。
陶瓷在烧结过程中的误差分析

陶瓷在烧结过程中的误差分析烧结是陶瓷烧成中重要的一环。
在高温下伴随烧结过程发生的主要变化是颗粒间接触界面扩大并逐渐形成晶界;连通的气孔逐渐变成孤立的气孔并缩小,最后大部分甚至全部从坯体中排除,使成型体的致密度和强度增加,成为具有一定性能和几何外形的整体。
因此,烧结总是意味着固体粉状成型体在低于其熔点温度下加热,使物质自发地充填颗粒间隙而致密化的过程。
烧结可以发生在单纯的固体之间,也可以在液相参与下进行。
前者称故相烧结;后者称液相烧结。
烧结过程可能包含某些化学反应的作用,但重要的是,烧结并不依赖于化学反应的作用。
它可以在不发生任何化学反应的情况下。
简单地将固体粉料加热,转变成坚实的致密烧结体,这是烧结区别于固相反应的一个重要方面。
因此烧结可代替液态成型方法,在远低于固体物料的熔点温度下,制成接近于理论密度的大件异型无机材料制品,并改善其物理性能。
一、烧结过程烧结前,成型体中有些颗粒彼此之间以点接触,有的则相互分开,保留着较多的空隙。
随着温度的升高和时间的延长,开始产生颗粒间的键合和重排过程,这时粒子因重排而相互靠拢,大空隙逐渐消失,气孔的总体积迅速减小,但颗粒之间仍以点接触为主,总表面积并没有缩小。
当颗粒间由点接触逐渐扩大为面接触,粒界面积增加,固气表面积相应减小,但空隙仍然是连通的,开始有明显的传质过程。
随着传质过程的继续进行,粒界进一步发育扩大,气孔则逐渐缩小和变形,最终转变成孤立的闭气孔。
与此同时颗粒粒界开始移动。
粒子长大,气孔逐渐迁移至Ⅱ粒界而消失,烧结体致密度增高。
二、影响烧结的因素影响烧结的因素很多,大致可归纳为三类,即前段因素(包括母盐的种类、制备条件、分解温度、预烧温度、预烧时间)、内因(晶体结构及变化、大小、分布、形状、表面状态、表面能大小、扩散系数、粘度和杂质的种类、数量、结构缺陷、结构位错变形、状态的安定程度)、外因(加人物的种类、加入量、粉碎处理、爆发冲击处理、高能照射处理、超音波处理、储藏影响、成型方法、成型压力、烧结温度、加热速度、烧结时间、烧结加压、烧结气氛)。
陶瓷缺陷——精选推荐
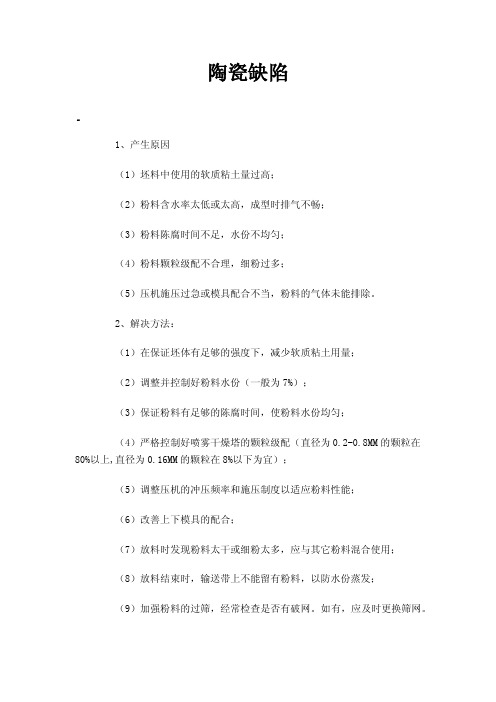
陶瓷缺陷1、产生原因(1)坯料中使用的软质粘土量过高;(2)粉料含水率太低或太高,成型时排气不畅;(3)粉料陈腐时间不足,水份不均匀;(4)粉料颗粒级配不合理,细粉过多;(5)压机施压过急或模具配合不当,粉料的气体未能排除。
2、解决方法:(1)在保证坯体有足够的强度下,减少软质粘土用量;(2)调整并控制好粉料水份(一般为7%);(3)保证粉料有足够的陈腐时间,使粉料水份均匀;(4)严格控制好喷雾干燥塔的颗粒级配(直径为0.2-0.8MM的颗粒在80%以上,直径为0.16MM的颗粒在8%以下为宜);(5)调整压机的冲压频率和施压制度以适应粉料性能;(6)改善上下模具的配合;(7)放料时发现粉料太干或细粉太多,应与其它粉料混合使用;(8)放料结束时,输送带上不能留有粉料,以防水份蒸发;(9)加强粉料的过筛,经常检查是否有破网。
如有,应及时更换筛网。
变形1、产生原因:(1)坯釉膨胀系数不匹配;(2)坯料可塑性原料过多;(3)坯料的颗粒原料过细;(4)粉料陈腐时间不足,水份不均匀;(5)成型时布料和加压不匀,使其收缩不一致;(6)坯体干燥和烧成过程中受热不均匀,使其收缩不一致;(7)承载坯体的辊棒变形或粘有附物不平;(8)辊棒变形、间距过大等,与坯体规格不匹配。
2、解决方法:(1)调整坯釉配方,使之膨胀系数相匹配;(2)减少坯料中可塑原料的用量,以减少坯体中的收缩率(吸水率<0.5%的制品,总收缩率控制在8%以下,吸水率为3-6%的制品,控制在6%以下;(3)适当增大坯料的颗粒;(4)保证粉料有足够的陈腐时间;(5)调整推料框栅结构和压机动作,使推料框与下模的动作匹配,达到布料均匀;(6)调整干燥窑烟气流速、温度等,调整烧成窑挡火墙板等使窑内温度均匀。
(7)大规格砖可采用高静压模具,使坯料受力均匀;(8)更换变形的辊棒并清除辊棒上的附杂物。
碰角产生原因:砖坯与砖坯之间或压机至压机辊台——烧成窑的运输过程中与其它物体发生局部碰撞:即造成破角。
- 1、下载文档前请自行甄别文档内容的完整性,平台不提供额外的编辑、内容补充、找答案等附加服务。
- 2、"仅部分预览"的文档,不可在线预览部分如存在完整性等问题,可反馈申请退款(可完整预览的文档不适用该条件!)。
- 3、如文档侵犯您的权益,请联系客服反馈,我们会尽快为您处理(人工客服工作时间:9:00-18:30)。
陶瓷烧成缺陷及原因分析发布时间:2008-8-4 15:07:14 阅读:52 次新闻来源:作者:(一)变形:产品烧成变形是陶瓷行业最常见、最严重的缺陷,如口径歪扭不圆,几何形状有不规则的改变等。
主要原因是装窑方法不当。
如匣钵柱行不正,匣钵底或垫片不平,使窑车运行发生震动,影响到产品的变形。
另外,产品在烧成中坯体预热与升温快时,温差大易发生变形。
烧成温度过高或保温时间太长也会造成大量的变形缺陷。
使用的匣钵高温强度差、或涂料抹不平时也会造成烧成品的变形。
(二)开裂:开裂指制品上有大小不同的裂纹。
其原因是坯体入窑水分太高(大于2%以上),预热升温和冷却太快,导致制品内外收缩不匀。
有的是坯体在装钵前已受到碰撞有内伤。
坯体厚薄不匀,配件(如壶把、咀等)重量过大或粘结不良也会造成制品开裂。
防止的办法是:(1)入窑坯体水分小于2%,车速适当减少冷却量。
(2)装窑时套装操作谨慎,垫片与坯体配方一致。
配件大小、重量与粘接位置恰当。
有的在粘接泥浆中加入10-15%的釉料,可以使咀、把与主体牢固熔接一体,如此可克服开裂缺陷。
(三)起泡:烧制品起泡有"坯泡"与"釉泡"两种。
坯泡分为"氧化泡"与"还原泡"两种。
氧化泡指坯泡外面覆盖釉层,断面呈灰黑色,多形成于窑内低温部位。
主要是瓷胎与釉料中的分解物未能充分氧化,烧失物未完全排除所致。
予热升温快,氧化分解阶段时间短、氧化结束时窑内温度过低,上下温度差过大。
在坯釉料中,碳酸盐。
硫酸盐及有机杂质含量较多等都是造成产品起泡的主因。
此外时装车密度不当、入窑水份高等原因亦须注意。
还原泡又称过火泡,断而发黄,多发生于高温近喷火口处的制品。
主要由于坯体内硫酸盐与高价铁还原不足,强还原气氛不足及烧成温度过高造成。
釉泡系沉积炭及分解物在釉熔前未能烧尽挥发,气体被阻于釉面层中形成。
若延长釉熔时间或适当平烧即可解决。
(四)阴黄:制品表面发黄或斑状发黄,有的断面也有发黄现象,多出现在高火位处。
主要原因是升温太快,釉熔融过早,还原气氛不足、而使瓷胎中的Fe2O3未能还原成FeO。
此外,装钵柱太低,窑顶局部产品温度偏高而还原不足也会形成阴黄缺陷。
在产品原料中TiO2含量太高,也会导致产品发黄,如若在坯料中加入微量CoO,可遮盖产品的黄色。
(五)烟熏:不论采用何种燃料都会发生烟熏现象。
烟熏指产品表面呈灰色或不纯正的白色。
主要由于坯体氧化不完全或还原过早使坯内炭素、有机物或低温碳未能烧尽在釉层封闭之前。
有时烟气倒流也会熏蚀釉面。
若釉料中钙含量偏高也易形成烟熏缺陷。
(六)针孔:指产品釉面出现微小凹痕或小孔。
形成此类缺陷一是坯料中有机物。
碳素、氧化铁含量较高,当升温快时烧失物未能完全烧尽挥发而到后期高温阶段才逸出釉面,形成宛如微观火山状的针孔。
此外,高温炉还原气氛太弱,喷火口部位产品再次被氧化也会造成针孔。
再者,当釉料流动性差或施釉过薄时也会发生针孔缺陷。
(七)桔釉:制品釉面不平、呈桔皮状。
一般发生于盘、碟类或瓷板砖类制品。
主要原因是釉面波化时升温过快,烧成温度过高使釉面产生沸腾现象所致。
另外釉浆厚薄不均、高温流动性差及釉料研磨不细等都是形成桔釉缺陷的症结所在。
(八)惊釉:产品釉面有发丝粗的裂纹。
主要原因是坯、釉膨胀系数相差较大形成。
这就需要重新调整坯。
釉配料配方。
此外烧成温度过高、冷却制度不合理或釉层过厚也会形成惊釉缺陷。
(九)生烧与过烧:生烧的制品外观发黄、吸水率偏高、釉面光泽差而粗糙、强度低、敲打时声音浑浊。
过烧时产品发生变形,釉面起泡或流釉。
主要原因在烧成温度偏高或偏低,高温保温时间控制不当,装车密度不合理或烧成温差大等产生局部过烧或生烧。
(十)无光:亦称消艳。
产生釉面无光的原因是釉面形成微细体和釉层熔融不良,因此形成釉面无光缺陷。
可在冷却初期采取快速冷却,防止釉面层析晶。
提高釉面光泽度。
艺术陶瓷的选购我国的陈设艺术陶瓷,分陶和瓷两大类。
陶主要产地有:以紫砂壶和花盆著称的陶都江苏宜兴;以陶塑人物和动物造型见长的广东石湾;还有生产唐三彩的河南洛阳;生产黑釉陶罐的山西浑源;生产刻花陶器的四川荣昌。
瓷主要产地有:以生产青花、玲珑、粉彩、颜色釉四大传统名瓷的瓷都江西景德镇;以釉下五彩装饰美术瓷而闻名的湖南醴陵;还有生产雨点釉和创新刻瓷艺术的山东淄博;生产花釉和象牙瓷的河北邯郸;生产白瓷的福建德化;生产青瓷的浙江龙泉;以及生产釉上彩花瓷的广东潮州;生产仿南宋官窑艺术瓷的浙江萧山等。
陶瓷]关于发展我国粗瓷产业的思考我国陶瓷历史悠久,制瓷工艺与装饰技艺具有独特的民族风格与地方特色,而名扬海内外。
建国以来我国大江南北建设了许多大型陶瓷产区,为发展陶瓷事业与当地经济建设做出了贡献。
陶瓷业的兴旺还刺激与带动了其他相关产业如矿产、交通、能源及第三产业的发展。
当前国际市场需求结构正发生巨大变化。
欧、德、日、韩等传统陶瓷生产大国,已将密集性劳动行业的陶瓷业逐步放弃,而采取大量从国外进口陶瓷的方针。
为中国陶瓷业的持续、稳步发展提供了很好的机遇。
例如,当前国际市场上美国陶瓷消费者需求纹饰淡雅、明快的美术陶瓷;德国市场很欢迎具有仿古风格的瓷器餐具及咖啡具;法国人喜欢动物造型的瓷器制品;日本人青睐手工风格,造型与釉色丰富、有窑变效果的陶瓷产品;澳大利亚流行铁炻器与铁质感的瓷器产品;意大利青睐紫沙陶壶茶具;西班牙消费者欢迎具有东方色彩的陶瓷产品;俄罗斯则需要大量进口供实验使用的各类化工陶瓷制品等等。
国际市场对陶瓷的需求范围越来越广,这为我国陶瓷的发展壮大提供了难得的机遇。
不过,随着我国及世界各国优质高岭土与细瓷原料日益减少,生产精细瓷器的细瓷原料储量日减,价格也越来越昂贵,增加了产品的成本。
而且也越来越不容易得到。
另一方面,储量非常大的粗陶瓷原料,遍布我国各地,采用当地丰富的陶土资源生产粗陶瓷产品,具有十分广阔的发展前景。
但是多年来粗陶瓷产业不受重视,也是事实。
其实,发展适合本地特色的粗瓷产品,说是粗瓷,但粗瓷并不粗。
关键是将它做好,做细。
将当地的人才优势、技术优势与资源优势三者结合起来,就能成气候。
就能实现"泥土变成金"。
其发展起来将是前途无量。
还能实现大批出口,何乐而不为?为建立循环经济,继续推动我国陶瓷产业持续稳定向前发展,将陶瓷产业这块蛋糕做大,现借《陶城报》就发展粗陶瓷产业问题,提出几点看法。
一:资源优势建国50多年来,国家有关地质部门对陶瓷原料的分布与储藏进行了勘探,得出的数据为优质陶瓷原料储藏均仅为千万吨级。
相比较之下,我国各种粗瓷陶土原料储量品种多,储藏非常丰富,多为亿吨及几亿吨、几十亿吨级。
如北方的大青土、二青土、缸土、碱石、焦宝石等储量都很丰富。
大青土储量有几十亿吨、缸土也有数亿吨。
南方的紫砂土储量十分丰富,有十几亿吨。
此外还有铝矾土、煤矸石等均有千万吨级到亿吨级。
包括各地煤矿废弃的煤矸石山,也可以用做粗瓷原料。
丰富的陶瓷原料与丰富的能源条件是大发展的优势,发展粗瓷产品起码使用几百年没有问题。
历史经验证明,采用地产粗瓷原料可以大批量生产各类陶瓷产品。
可以生产艺术陶瓷、园林陶瓷、建筑陶瓷、卫生陶瓷、日用陶瓷(如沙锅、陶制餐具及茶具等)等各类产品,经过精细加工还可以生产出口国际市场的各种炻器产品。
今后应该下大力气推动粗陶瓷产品的发展。
将来我国陶瓷发展的方向,在保持细瓷产品创高档与品牌的同时,更应该大力发展以当地原料生产的粗陶瓷产品。
其实,陶瓷是一个大概念,也包括含一定比例的当地粗瓷原料生产的陶瓷产品。
粗料通过细作,也可以生产出好产品,创造出较高的经济价值。
它包括有日用瓷、艺术瓷、仿古瓷、园林瓷、工业瓷、电磁等种类的方方面面。
大力发展粗瓷产品还非常符合当前国家要求发展绿色产品、造就循环经济的大政策。
二:可供发展的产品(1)、炻器。
炻器产品位于瓷器与陶器之间,主要是用当地含有铁及各种杂质的劣质原料生产的产品,产品种类有餐具、茶具、咖啡具、酒具、插花具等。
我国陶瓷在20世纪70年代后期已经开始生产炻器产品。
主要产区有山东淄搏、河北彭城、江苏高淳、河南焦作等瓷区。
这样可以抵消由于高档细瓷原料由外地运输,成本不断上涨带来的负面影响,降低产品成本。
炻器产品主要大量出口到国际市场,而且进入美国市场没有那么多的贸易限制。
因此,将来我们应该大力发展炻器产品,加强产品设计与提高装饰艺术,成为世界上最大的炻器生产强国。
(2)、发展"和陶"产品。
和陶产品即具有东方风格的造型丰富、釉色斑斓的陶制餐具产品,由日本最先生产,故称和陶。
和陶产品的特色是注重反映手工制作痕迹,擅长发挥造型的丰富与变换性,重视各种色釉装饰。
其所用原料、釉料与生产技术,在我国任何一个陶瓷产区均可以完全可以满足。
和陶产品可以作为继陶瓷沙锅后未来产品的一个新的发展方向,也是粗陶瓷产品发展的一个方向。
目前,"和陶"产品主要出口到日本、台湾、韩国及东南亚地区,而且每年定单很大。
(3)、美术陶瓷。
我国各地的陶土原料储藏丰富,能够生产各种美术陶瓷,如江苏宜兴生产的紫砂壶、仿钧釉艺瓷;河北彭城瓷区生产的各种仿古瓷、高温花釉动物雕塑、现代陶艺;河南洛阳、禹县生产的唐三彩雕塑、仿古钧瓷;广东石湾生产的瓦脊公仔、人物雕塑等产品都使用了当地的粗瓷原料。
美术陶瓷属于劳动密集型产业,发展美术瓷可以解决大量就业。
也可成为展示地方陶瓷艺术形象的名牌,成为推动陶瓷观光旅游的热门产业。
发展美术陶瓷,目前还不需要大量的投资。
搞一家民间陶瓷作坊,个人投资几万元就可搞起来。
但在他们创业初期时困难很多,政府可在税收及收费上进行扶持,实行优惠政策。
此外,能否帮助其搞到小额贷款。
(4)、园林陶瓷。
目前国家大力发展旅游业与园林事业,对园林陶瓷产品的需求很大。
因此发展园林陶瓷产品很有前途。
如陶瓷花盆、花缸、鱼缸、陶瓷果皮箱、大衣架、瓷桌、绣墩、灯架、灯柱等产品,这些都使用粗瓷原料生产。
关键是在粗瓷的外表挂上一层美丽的釉色,以增加其美感与观赏性。
当然,粗瓷原料也可以用于釉料配制的原料,可谓一举两得。
(5)、紫砂陶瓷。
目前国内园林产业已经形成上千亿元产值的市场,对各类陶瓷花盆需求数量惊人。
我国南北方各地,紫砂土原料储量均十分巨大,也能在生产粗瓷产品方面做出大文章。
如江苏的宜兴瓷区用紫砂土生产琉璃瓦与紫砂壶、园林陶瓷产品。
他们利用粗瓷原料生产陶瓷制品,工作做得非常出色,仅*紫砂土原料资源一项就发了财,做得很好。
不仅紫砂壶能够赚钱。
他们做得紫砂花盆也很不错,产品造型成了系列。
造型有圆形、椭圆形、方形等各种花盆产品,还出口到国外市场。
佛山瓷区生产的人物陶瓷雕塑也使用有大量的紫砂土原料(只是在当地的称呼不同);河南省宝丰瓷区也采用紫砂原料生产供出口的各种紫砂壶茶具、花盆等粗瓷产品。