航煤加氢装置优化操作
基于原油性质变化的航煤加氢装置节能优化经验阐述

基于原油性质变化的航煤加氢装置节能优化经验阐述随着航空运输业的快速发展,航煤成为被广泛使用的燃料之一。
而航煤加氢装置则是航空燃油节能优化的关键设备。
本文将介绍基于原油性质变化的航煤加氢装置的节能优化经验。
一、考虑原油性质变化对航煤加氢的影响航煤加氢的原理是在高温高压下通过加氢反应,将航煤中的芳香烃和烯烃转化为饱和烃,提高其抗爆能力和燃烧效率。
但随着原油性质的变化,航煤中的组分也会发生变化,从而对加氢效果产生影响。
因此,在进行航煤加氢装置的设计和运行时,需要考虑原油性质的变化对加氢效果的影响,从而进行适当的调整和优化。
二、在航煤加氢装置中采用微粒化技术微粒化技术是一种将液态或固态物质通过特殊设备进行细化处理的技术。
在航煤加氢装置中采用微粒化技术,可以使航煤更加均匀地流进反应器中,增加反应面积,提高反应效率。
同时,微粒化技术还可以降低反应温度,减少能量损失,从而达到节能的目的。
三、控制反应器内的氢气流量在航煤加氢反应中,氢气是一种重要的物质。
合理的氢气流量可以提高反应速度和反应效率,但过高的氢气流量也会产生能量浪费。
因此,在航煤加氢装置操作时,需要适当控制反应器内的氢气流量,达到较好的加氢效果和节能效果的平衡。
四、开发多功能催化剂催化剂是航煤加氢装置中起到重要作用的材料。
传统的催化剂以贵金属为主要组分,价格昂贵,难以大规模应用。
因此,近年来,研发一种性能稳定、价格低廉的多功能催化剂成为节能优化的关键。
多功能催化剂不仅可以在加氢反应中发挥较好的催化作用,还可以解决其他废气的治理问题,降低能源损失,具有很高的应用前景。
综上所述,基于原油性质变化的航煤加氢装置节能优化需要针对实际情况进行适当调整和优化。
在航煤加氢装置中,采用微粒化技术、控制反应器内的氢气流量和开发多功能催化剂等措施,可以有效地提高节能效果和加氢效果的质量和稳定性。
加氢裂化装置优化运行生产航煤技术攻关

加氢裂化装置优化运行生产航煤技术攻关【摘要】本文主要围绕加氢裂化装置优化运行生产航煤技术攻关展开探讨。
在分析了研究背景和研究意义。
正文部分首先对加氢裂化装置优化运行技术的现状进行了分析,接着探讨了航煤生产过程中存在的问题,并提出了优化运行的技术路径。
重点介绍了技术攻关的关键技术。
在总结了加氢裂化装置优化运行生产航煤技术攻关的意义,并展望了未来的发展。
通过本文的研究,有望为航煤生产提供更可靠、高效的技术支持,实现生产过程的优化和提高生产效率。
【关键词】关键词:加氢裂化装置、优化运行、生产、航煤、技术攻关、现状分析、问题、技术路径、关键技术、意义、发展展望。
1. 引言1.1 研究背景研究背景部分重点分析了当前加氢裂化装置优化运行技术的现状,包括技术水平、存在的问题和发展趋势。
目前,我国加氢裂化装置的技术水平整体较高,但在运行过程中仍然存在一些问题,例如设备老化、能耗过高、产品质量不稳定等。
这些问题制约了航煤生产的效率和品质,亟待解决。
通过深入研究加氢裂化装置的优化运行技术路径和关键技术,可以有效提升航煤生产的技术水平和经济效益。
加强对加氢裂化装置优化运行生产航煤技术的攻关研究具有重要意义。
通过不断改进技术路径和攻关关键技术,可以更好地适应市场需求和提高产业竞争力。
1.2 研究意义加氢裂化装置在航煤生产过程中扮演着至关重要的角色。
通过优化加氢裂化装置的运行技术,可以有效提高航煤的产量和质量,降低生产成本,提高企业的竞争力。
加氢裂化装置优化运行技术的研究对于航煤生产过程的提升具有重要意义。
加氢裂化装置优化运行生产航煤技术攻关的研究也能够推动相关领域的技术创新和进步。
通过攻克关键技术,不断完善和提升相关技术水平,可以促进航煤生产技术的发展,推动整个行业的繁荣和进步。
这项研究具有重要的实践意义和推动作用。
2. 正文2.1 加氢裂化装置优化运行技术的现状分析加氢裂化装置是航煤生产过程中的关键设备之一,对提高航煤的质量和产量具有重要作用。
基于原油性质变化的航煤加氢装置节能优化经验阐述
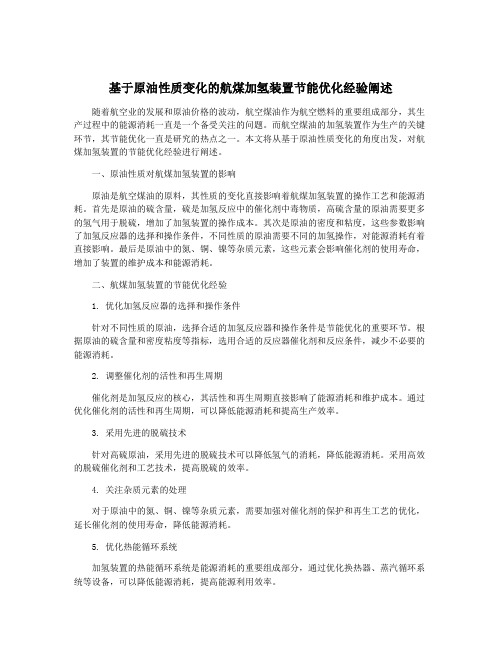
基于原油性质变化的航煤加氢装置节能优化经验阐述随着航空业的发展和原油价格的波动,航空煤油作为航空燃料的重要组成部分,其生产过程中的能源消耗一直是一个备受关注的问题。
而航空煤油的加氢装置作为生产的关键环节,其节能优化一直是研究的热点之一。
本文将从基于原油性质变化的角度出发,对航煤加氢装置的节能优化经验进行阐述。
一、原油性质对航煤加氢装置的影响原油是航空煤油的原料,其性质的变化直接影响着航煤加氢装置的操作工艺和能源消耗。
首先是原油的硫含量,硫是加氢反应中的催化剂中毒物质,高硫含量的原油需要更多的氢气用于脱硫,增加了加氢装置的操作成本。
其次是原油的密度和粘度,这些参数影响了加氢反应器的选择和操作条件,不同性质的原油需要不同的加氢操作,对能源消耗有着直接影响。
最后是原油中的氮、铜、镍等杂质元素,这些元素会影响催化剂的使用寿命,增加了装置的维护成本和能源消耗。
二、航煤加氢装置的节能优化经验1. 优化加氢反应器的选择和操作条件针对不同性质的原油,选择合适的加氢反应器和操作条件是节能优化的重要环节。
根据原油的硫含量和密度粘度等指标,选用合适的反应器催化剂和反应条件,减少不必要的能源消耗。
2. 调整催化剂的活性和再生周期催化剂是加氢反应的核心,其活性和再生周期直接影响了能源消耗和维护成本。
通过优化催化剂的活性和再生周期,可以降低能源消耗和提高生产效率。
3. 采用先进的脱硫技术针对高硫原油,采用先进的脱硫技术可以降低氢气的消耗,降低能源消耗。
采用高效的脱硫催化剂和工艺技术,提高脱硫的效率。
4. 关注杂质元素的处理对于原油中的氮、铜、镍等杂质元素,需要加强对催化剂的保护和再生工艺的优化,延长催化剂的使用寿命,降低能源消耗。
5. 优化热能循环系统加氢装置的热能循环系统是能源消耗的重要组成部分,通过优化换热器、蒸汽循环系统等设备,可以降低能源消耗,提高能源利用效率。
三、结语航煤加氢装置的节能优化是一个复杂的系统工程,需要综合考虑原油性质、工艺技术和设备性能等多个因素。
基于原油性质变化的航煤加氢装置节能优化经验阐述

基于原油性质变化的航煤加氢装置节能优化经验阐述航煤加氢装置是一种重要的石油加工设备,用于将原油中的硫、氮等杂质去除,提高燃料的质量,在航空燃料领域起着关键作用。
在这个装置中,原油的性质变化对节能优化具有重要意义。
原油的性质变化对加氢装置的能耗有直接影响。
随着原油中硫化物和氮化物等杂质的含量增加,加氢装置需要消耗更多的氢气来进行反应。
为了降低能耗,可以采用更先进的催化剂和工艺流程,提高反应效率。
对原油进行预处理,如酸除硫、脱腥等,可以减少催化剂的负荷,降低能耗。
原油的性质变化还会影响加氢装置的热工条件。
不同性质的原油在加氢过程中需要不同的反应温度和压力。
针对原油的性质变化,可以调整加氢装置的运行参数,使其处于最佳工况下,提高热工效率。
还可以利用余热回收技术,对加氢装置的废热进行回收利用,降低能耗。
原油的性质变化还会对催化剂的选择和使用条件产生影响。
不同的原油性质对催化剂的选择有一定的要求,催化剂选择不当会降低反应效率和催化剂的使用寿命。
为了优化节能效果,可以根据原油性质变化的特点来选择合适的催化剂,提高催化剂的活性和稳定性。
还可以优化催化剂的再生和循环利用过程,延长催化剂的使用寿命,减少能耗。
原油性质变化对航煤加氢装置的操作和维护也会产生影响。
不同性质的原油在运行过程中会产生不同的反应产物和副产物,可能会对设备的性能和设备的寿命产生影响。
在操作和维护过程中,需要注意对原油性质变化的监测和分析,及时调整操作参数,保证设备的正常运行和长期稳定。
基于原油性质变化的航煤加氢装置节能优化经验包括调整加氢装置的运行参数、利用余热回收技术、选择合适的催化剂、优化催化剂的再生和循环利用过程以及对设备的操作和维护等方面。
通过这些优化措施,可以提高加氢装置的能耗效率,降低燃料生产过程的能耗,为航空燃料的生产和使用节能减排提供技术支持。
加氢裂化装置优化运行生产航煤技术攻关
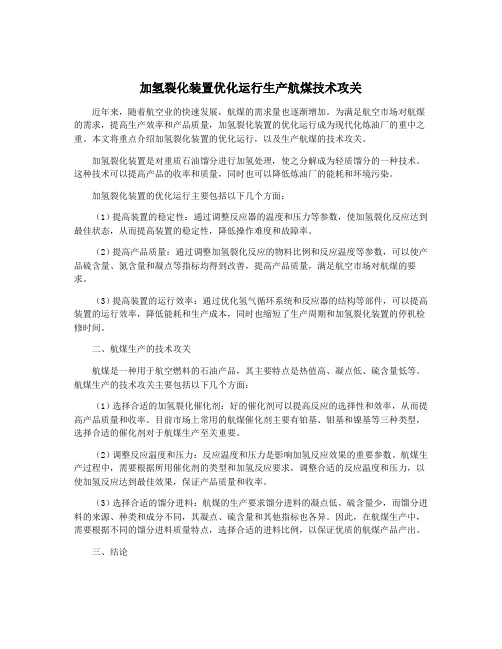
加氢裂化装置优化运行生产航煤技术攻关近年来,随着航空业的快速发展,航煤的需求量也逐渐增加。
为满足航空市场对航煤的需求,提高生产效率和产品质量,加氢裂化装置的优化运行成为现代化炼油厂的重中之重。
本文将重点介绍加氢裂化装置的优化运行,以及生产航煤的技术攻关。
加氢裂化装置是对重质石油馏分进行加氢处理,使之分解成为轻质馏分的一种技术。
这种技术可以提高产品的收率和质量,同时也可以降低炼油厂的能耗和环境污染。
加氢裂化装置的优化运行主要包括以下几个方面:(1)提高装置的稳定性:通过调整反应器的温度和压力等参数,使加氢裂化反应达到最佳状态,从而提高装置的稳定性,降低操作难度和故障率。
(2)提高产品质量:通过调整加氢裂化反应的物料比例和反应温度等参数,可以使产品硫含量、氮含量和凝点等指标均得到改善,提高产品质量,满足航空市场对航煤的要求。
(3)提高装置的运行效率:通过优化氢气循环系统和反应器的结构等部件,可以提高装置的运行效率,降低能耗和生产成本,同时也缩短了生产周期和加氢裂化装置的停机检修时间。
二、航煤生产的技术攻关航煤是一种用于航空燃料的石油产品,其主要特点是热值高、凝点低、硫含量低等。
航煤生产的技术攻关主要包括以下几个方面:(1)选择合适的加氢裂化催化剂:好的催化剂可以提高反应的选择性和效率,从而提高产品质量和收率。
目前市场上常用的航煤催化剂主要有铂基、钼基和镍基等三种类型,选择合适的催化剂对于航煤生产至关重要。
(2)调整反应温度和压力:反应温度和压力是影响加氢反应效果的重要参数。
航煤生产过程中,需要根据所用催化剂的类型和加氢反应要求,调整合适的反应温度和压力,以使加氢反应达到最佳效果,保证产品质量和收率。
(3)选择合适的馏分进料:航煤的生产要求馏分进料的凝点低、硫含量少,而馏分进料的来源、种类和成分不同,其凝点、硫含量和其他指标也各异。
因此,在航煤生产中,需要根据不同的馏分进料质量特点,选择合适的进料比例,以保证优质的航煤产品产出。
航煤加氢装置空气预热器运行优化

航煤加氢装置空气预热器运行优化摘要:2021年,随着我国经济稳步回升,航空煤油市场需求也在不断增长[1]。
煤油加氢技术是生产清洁航煤的关键工艺,占据煤油加氢的主流[2]。
其中加热炉是加氢装置的关键设备,也是能耗的主要来源,因此,优化加热炉运行操作,提高加热炉热效率,以达到节约燃料气降低能耗的目的,是目前炼厂争取效益的有利途径。
近期济南炼化航煤加氢装置分馏塔重沸炉投用了空气预热器,并进行了优化分析,数据表明空气预热器的投用大大降低了燃料气消耗,加热炉排烟温度也大幅降低,热效率平均在90%以上[3],取得了较为理想的节能降耗效果。
关键词:航煤;加热炉;空气预热器;热效率;排烟温度;节能1.引言近期济南炼化航煤加氢装置分馏塔重沸炉投用了空气预热器,并进行了优化分析,数据表明空气预热器的投用大大降低了燃料气消耗,加热炉排烟温度也大幅降低,热效率平均在90%以上,达到了较为理想的节能降耗效果。
2.空气预热器工作原理表1空气预热器技术参数表表2.鼓、引风机参数加热炉F-301、F-302、F-102三炉公用一套空气余热回收系统,三炉烟气通过现有联合烟道进入空气预热器,与空气换热后通过冷烟道进入加热炉F-301烟囱排大气;被加热空气通过主风道进入加热炉F-302炉底,加热炉F-301底部通风为自然通风。
本空气余热回收系统包括空气预热器、鼓风机、引风机,新建吸风口、主风道、炉底风道、风道旁路、冷烟道、热烟道及支烟道。
3.投用过程2020年6月3日10:30,启鼓风机向F-302环形风道并风。
10:45,鼓风机变频提至30%,空气预热器出口空气压力达到280Pa,关闭环形风道快开风门XSV335,XSV336;11:25,现场启引风机,将F-302烟气引入空气预热器,逐步关小F-302烟道挡板HC315并提高引风机变频,直至F-302烟气全部并入空气预热器。
整个过程F-302保持平稳操作,炉膛负压及氧含量均未产生大的波动。
加氢裂化装置优化运行生产航煤技术攻关

加氢裂化装置优化运行生产航煤技术攻关随着我国对航空煤油需求的不断增加,加氢裂化装置的优化运行生产对于航煤技术攻关变得尤为重要。
加氢裂化技术是航煤生产中的关键环节,其优化运行将直接影响航煤质量和产量。
为了提高航煤的质量和产量,降低生产成本,我国科研人员不断进行技术攻关,积极寻求技术创新,推动加氢裂化装置的优化运行生产。
一、加氢裂化技术在航煤生产中的地位加氢裂化技术是将原油或者重质油转化成航空煤油的主要方法之一,也是目前航煤生产中使用最为广泛的技术之一。
加氢裂化技术可以将原油中的重质烃类分子在催化剂的作用下裂解成较轻质的烃类物质,可提高航煤的产量、改善航煤的质量、降低航煤的硫含量、降低航煤的芳烃和烯烃含量,保障航煤的需求。
加氢裂化技术在航煤生产中的地位非常重要。
随着对航煤的需求不断增加,对加氢裂化装置的技术要求也在不断提高,如何实现加氢裂化装置的优化运行已成为当前航煤技术攻关的重要课题。
二、加氢裂化装置存在的问题1. 催化剂的选择问题:催化剂是加氢裂化装置的重要组成部分,直接影响加氢裂化反应的效率和产物的质量。
目前,我国在加氢裂化催化剂研究上与国际先进水平还存在一定差距,催化剂的稳定性和活性需要进一步提高。
2. 操作参数的优化问题:加氢裂化装置的操作参数对于反应效率和产物质量也有着重要的影响,而当前加氢裂化装置在运行过程中,参数调节仍然存在很多困难,导致反应效率和产品质量不能得到最大程度的提高。
3. 能源消耗问题:加氢裂化装置的运行需要耗费大量的能源,目前仍缺乏有效的节能减排技术,导致能源消耗较大。
以上问题的存在导致了加氢裂化装置在航煤生产中的运行存在一定的问题和障碍,严重影响了航煤的产量和质量。
如何解决这些问题,实现加氢裂化装置的优化运行,成为当前航煤技术攻关的重点和难点。
为了解决加氢裂化装置存在的问题,提高航煤的产量和质量,我国科研人员积极开展技术攻关,推动加氢裂化装置的优化运行生产。
主要进行以下几方面的技术攻关:1. 催化剂的研发和优化:加氢裂化装置中的催化剂是影响航煤质量和产量的关键因素之一。
加氢裂化装置优化运行生产航煤技术攻关

加氢裂化装置优化运行生产航煤技术攻关为了提高航煤的品质,同时降低其生产成本,加氢裂化装置的优化运行成为了一项具有重要意义的技术攻关。
针对这一问题,本文将从以下三个方面进行探讨:加氢裂化装置的工艺原理和流程;装置优化运行的必要性和挑战;装置优化运行中的关键技术和应用方法。
一、加氢裂化装置的工艺原理和流程加氢裂化是利用催化剂和氢气使长链烃分子在高温下断裂成短链分子的工艺。
加氢裂化装置的主要部件包括加氢反应器、分馏塔、冷却器等。
其工艺流程如下图所示:[插入图片]在这一工艺中,原料油进入加氢反应器后,在氢气的存在下,经过高温高压的加氢反应,长链烃分子被断裂成短链烃分子。
随着反应的进行,反应器中不断有新的短链分子生成,同时也有短链分子进一步加氢,生成更短的分子。
这时,分馏塔将反应产物分为轻质和重质两部分,轻质部分包含甲烷、乙烷、丙烷等气态产品,重质部分则包含乙烯、丙烯、苯等液态产品。
最后,这些产品经过冷却器冷却,通过分选装置分离出不同产品。
二、装置优化运行的必要性和挑战加氢裂化装置的优化运行主要是为了提高产品的催化裂化效率和产品品质,同时降低生产成本。
具体来说,装置优化运行的必要性体现在以下几个方面:1.提高产品的品质。
通过优化反应的温度、压力、质量比等因素,可以使产物中不同组分的含量得到有效控制,从而提高产品的品质和附加值。
2.降低生产成本。
装置优化运行可以帮助企业在提高产品品质的同时,尽可能降低生产成本,提高经济效益和市场竞争力。
3.优化反应系统的安全性。
优化加氢裂化装置的运行参数,可以有效减少一些不必要的反应失控和事故风险,保证生产过程的稳定性和安全性。
然而,装置优化运行所面临的挑战也不容忽视。
首先,加氢裂化反应机理较为复杂,其反应产物不仅涉及到烃类气体和液体,还可能出现其他非烃类物质,例如硫化物、酸性物等。
其次,不同反应物质的加工条件和要求也不尽相同,因此在不同的工作状态下对不同反应物质进行加工还需要进行针对性的优化。
基于原油性质变化的航煤加氢装置节能优化经验阐述

基于原油性质变化的航煤加氢装置节能优化经验阐述随着经济的发展和人民生活水平的提高,对能源的需求越来越大。
石油是我们生产生活中必不可少的能源,而原油在提炼成各种石油制品的过程中,会产生一些油品残留物。
这些残留物虽然能够应用在航空煤油等方面,但是其能源利用率不高,而且含硫、氮等元素含量也比较高,对环境产生了较大的污染。
近年来,基于原油性质变化的航煤加氢装置成为了炼油厂优化能源的重要手段。
加氢处理技术是将石油加氢,去除其中的硫、氮等含有害物质,提高产品质量的一种方法。
航煤是航空煤油的一种,航空燃料质量优良,性能要求高,航煤生产工艺流程中加氢装置的节能优化就显得尤为重要。
需要对加氢装置的工艺流程进行优化。
传统的加氢装置工艺流程中,会产生一定量的热能消耗以及催化剂的损耗。
在实际生产中,我们需要进行流程优化,使得工艺流程更加平稳、高效。
通过科学的计算和分析,提高原油加氢过程的热效率,减少热损失,提高生产力。
在加氢装置的催化剂选择上也需要进行优化。
选择合适的催化剂是提高加氢装置效率的关键。
催化剂的质量直接影响着加氢反应的速率和效果,而且催化剂的选择也会影响到加氢过程中的能量消耗。
在选择催化剂时,需要根据原油的性质变化来选择合适的催化剂,提高加氢反应的效率,减少能源的消耗。
加氢装置的操作和维护也需要进行节能优化。
在实际的生产过程中,需要对加氢装置进行定期的检查和维护,保证其正常运转。
通过合理的操作和维护,可以减少设备的磨损和损耗,提高设备的使用寿命,减少能源的消耗。
也可以通过对加氢装置操作的规范和标准化,提高生产效率,减少能源的浪费。
需要对加氢装置进行现代化的管理和控制。
在现代化的炼油厂中,加氢装置需要配备先进的自动化控制系统,通过对加氢装置的实时监测和控制,提高设备的运行效率,减少能源的消耗。
通过现代化的管理和控制,可以及时发现设备运行中的问题,提前进行处理,减少能源的损耗。
基于原油性质变化的航煤加氢装置节能优化是当前炼油厂优化能源的重要手段。
加氢裂化装置优化运行生产航煤技术攻关
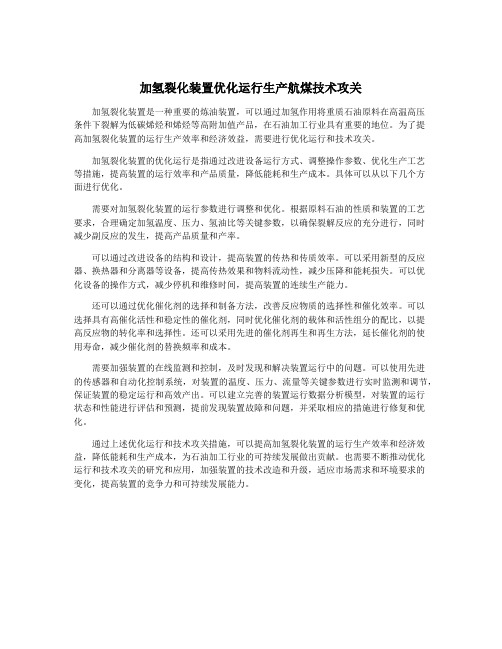
加氢裂化装置优化运行生产航煤技术攻关加氢裂化装置是一种重要的炼油装置,可以通过加氢作用将重质石油原料在高温高压条件下裂解为低碳烯烃和烯烃等高附加值产品,在石油加工行业具有重要的地位。
为了提高加氢裂化装置的运行生产效率和经济效益,需要进行优化运行和技术攻关。
加氢裂化装置的优化运行是指通过改进设备运行方式、调整操作参数、优化生产工艺等措施,提高装置的运行效率和产品质量,降低能耗和生产成本。
具体可以从以下几个方面进行优化。
需要对加氢裂化装置的运行参数进行调整和优化。
根据原料石油的性质和装置的工艺要求,合理确定加氢温度、压力、氢油比等关键参数,以确保裂解反应的充分进行,同时减少副反应的发生,提高产品质量和产率。
可以通过改进设备的结构和设计,提高装置的传热和传质效率。
可以采用新型的反应器、换热器和分离器等设备,提高传热效果和物料流动性,减少压降和能耗损失。
可以优化设备的操作方式,减少停机和维修时间,提高装置的连续生产能力。
还可以通过优化催化剂的选择和制备方法,改善反应物质的选择性和催化效率。
可以选择具有高催化活性和稳定性的催化剂,同时优化催化剂的载体和活性组分的配比,以提高反应物的转化率和选择性。
还可以采用先进的催化剂再生和再生方法,延长催化剂的使用寿命,减少催化剂的替换频率和成本。
需要加强装置的在线监测和控制,及时发现和解决装置运行中的问题。
可以使用先进的传感器和自动化控制系统,对装置的温度、压力、流量等关键参数进行实时监测和调节,保证装置的稳定运行和高效产出。
可以建立完善的装置运行数据分析模型,对装置的运行状态和性能进行评估和预测,提前发现装置故障和问题,并采取相应的措施进行修复和优化。
通过上述优化运行和技术攻关措施,可以提高加氢裂化装置的运行生产效率和经济效益,降低能耗和生产成本,为石油加工行业的可持续发展做出贡献。
也需要不断推动优化运行和技术攻关的研究和应用,加强装置的技术改造和升级,适应市场需求和环境要求的变化,提高装置的竞争力和可持续发展能力。
加氢裂化装置优化运行生产航煤技术攻关
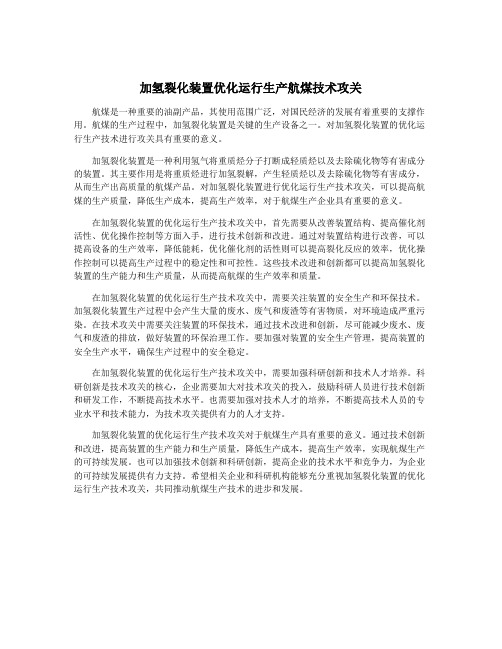
加氢裂化装置优化运行生产航煤技术攻关航煤是一种重要的油副产品,其使用范围广泛,对国民经济的发展有着重要的支撑作用。
航煤的生产过程中,加氢裂化装置是关键的生产设备之一。
对加氢裂化装置的优化运行生产技术进行攻关具有重要的意义。
加氢裂化装置是一种利用氢气将重质烃分子打断成轻质烃以及去除硫化物等有害成分的装置。
其主要作用是将重质烃进行加氢裂解,产生轻质烃以及去除硫化物等有害成分,从而生产出高质量的航煤产品。
对加氢裂化装置进行优化运行生产技术攻关,可以提高航煤的生产质量,降低生产成本,提高生产效率,对于航煤生产企业具有重要的意义。
在加氢裂化装置的优化运行生产技术攻关中,首先需要从改善装置结构、提高催化剂活性、优化操作控制等方面入手,进行技术创新和改进。
通过对装置结构进行改善,可以提高设备的生产效率,降低能耗,优化催化剂的活性则可以提高裂化反应的效率,优化操作控制可以提高生产过程中的稳定性和可控性。
这些技术改进和创新都可以提高加氢裂化装置的生产能力和生产质量,从而提高航煤的生产效率和质量。
在加氢裂化装置的优化运行生产技术攻关中,需要关注装置的安全生产和环保技术。
加氢裂化装置生产过程中会产生大量的废水、废气和废渣等有害物质,对环境造成严重污染。
在技术攻关中需要关注装置的环保技术,通过技术改进和创新,尽可能减少废水、废气和废渣的排放,做好装置的环保治理工作。
要加强对装置的安全生产管理,提高装置的安全生产水平,确保生产过程中的安全稳定。
在加氢裂化装置的优化运行生产技术攻关中,需要加强科研创新和技术人才培养。
科研创新是技术攻关的核心,企业需要加大对技术攻关的投入,鼓励科研人员进行技术创新和研发工作,不断提高技术水平。
也需要加强对技术人才的培养,不断提高技术人员的专业水平和技术能力,为技术攻关提供有力的人才支持。
加氢裂化装置的优化运行生产技术攻关对于航煤生产具有重要的意义。
通过技术创新和改进,提高装置的生产能力和生产质量,降低生产成本,提高生产效率,实现航煤生产的可持续发展。
基于原油性质变化的航煤加氢装置节能优化经验阐述

基于原油性质变化的航煤加氢装置节能优化经验阐述随着航空业的快速发展和对环保要求的日益提高,航空煤油(航煤)作为航空燃料的重要组成部分,其质量要求也越来越高。
为了满足航燃产品质量的提升要求和减少能源消耗,航煤加氢装置的节能优化成为了关注的焦点。
本文将从航煤加氢装置的原理、节能优化的必要性和关键技术等方面进行阐述,希望能够为相关行业的工程师和研究人员提供一些参考。
一、航煤加氢装置的原理航煤加氢装置是将原油等原材料通过加氢技术进行精制,使得航煤的硫含量、芳烃含量、密度等性质得到调整和提高,从而使得最终产品符合航空燃料的质量要求。
通常航煤加氢装置是采用催化加氢技术,通过催化剂的作用将原料中的硫化合物、芳香烃和双键等不饱和物质加氢成饱和的烷烃或环烷烃,来达到分子结构的变化,从而提高产品的质量。
二、航煤加氢装置节能优化的必要性在航煤加氢装置的运行过程中,消耗大量的能源,尤其是氢气、天然气等。
如何降低能源消耗,提高装置的运行效率成为了目前亟待解决的问题。
随着原油资源的逐渐枯竭和环保要求的提高,降低加氢过程中的废气排放量,减少对环境的影响,也成为了行业关注的焦点。
三、航煤加氢装置节能优化的关键技术1. 催化剂的选择和改良:催化剂是航煤加氢装置中至关重要的组成部分,其质量和性能对加氢过程的效率和产品质量有着直接的影响。
目前,针对航煤加氢装置的特性,一些研究机构已经开始研究开发新型催化剂,提高其硫抑制能力、活性和稳定性,从而降低氢气的用量,提高航煤的加氢率。
2. 装置的热工结构优化:通过对航煤加氢装置的热力平衡、传热传质和流体力学等方面进行优化设计,可以减少能量的损失,提高能源的利用率。
采用高效的换热设备、增加热回收装置等方式可以在一定程度上实现能源的节约。
3. 操作技术的改进:加氢装置的操作人员对装置的操作方式、参数调控等方面的技术水平也对节能优化有着重要的影响。
培养专业的操作技术人员、建立科学的操作管理体系,提高操作技术水平,可以有效地降低能源的消耗。
加氢裂化装置优化运行生产航煤技术攻关

加氢裂化装置优化运行生产航煤技术攻关加氢裂化装置是一种重要的炼油装置,能够将重质石油馏分转化为高附加值产品,如航空煤油。
在当前严峻的能源形势下,航煤技术攻关变得尤为重要。
优化加氢裂化装置的运行生产,是提高航煤产量和品质的重要途径。
本文将就加氢裂化装置优化运行生产航煤技术攻关进行探讨。
加氢裂化装置通常由多个单元组成,包括加氢单元、裂化单元和产品升级单元。
在运行生产中,加氢裂化装置面临着一系列技术难题,如催化剂选择、操作参数控制、热积问题等,这些问题直接影响着装置的生产效率和产品质量。
当前,加氢裂化装置的运行生产存在以下问题:1. 催化剂选择问题。
加氢裂化装置的催化剂是其关键设备,对其选择要求严格。
目前,市场上存在着质量不稳定、性能差异大的催化剂,导致装置性能不稳定,生产效率低下。
2. 操作参数控制问题。
加氢裂化装置需要对多个操作参数进行精密控制,如温度、压力、流速等,而目前操作人员对这些参数的控制理解不深,导致生产过程中出现波动,影响产品质量。
3. 热积问题。
加氢裂化装置在运行过程中会产生大量热积,导致设备温度升高,影响装置的正常运行和寿命。
为了解决上述问题,需要从以下几个方面进行技术攻关:1. 催化剂选择技术攻关。
针对催化剂的质量和性能不稳定的问题,可以通过研发新型催化剂或者改进现有催化剂的制备工艺,提高催化剂的稳定性和活性。
2. 操作参数控制技术攻关。
可以通过引入先进的自动化控制系统,优化装置控制策略,实现对操作参数的精密控制,从而提高装置的稳定性和生产效率。
3. 热积问题技术攻关。
可以通过改进装置内部的传热结构,增加换热器数量,采用先进的冷却技术等手段,降低热积对装置的影响,提高装置的运行稳定性。
以上技术攻关需要结合现有的实际情况,进行详细的研究和试验,才能够有效解决加氢裂化装置优化运行生产的问题。
三、加氢裂化装置优化运行生产的意义和前景加氢裂化装置优化运行生产的技术攻关,不仅可以提高航煤的产量和品质,还可以提高石油资源的综合利用率,降低能源消耗和环境污染,具有重要的经济和社会意义。
加氢裂化装置优化运行生产航煤技术攻关

加氢裂化装置优化运行生产航煤技术攻关随着全球能源需求的不断增长,石油是目前全球主要的能源之一。
而随着石油资源的不断枯竭,对于开发更多的石油资源和提高石油加工技术已成为当今石油行业的重要议题。
在炼油工艺中,加氢裂化装置是一种常用的重整技术,可用于生产高质量的航煤。
加氢裂化装置的优化运行和生产航煤技术仍然存在许多技术难题,需要进行攻关研究。
一、加氢裂化装置的优化运行加氢裂化装置是一种通过加氢作用对重质烃进行裂化得到高质量轻质烃产品的重整技术。
在加氢裂化装置的运行过程中,如何优化控制操作参数,提高产品质量和产量,是目前亟需解决的技术难题。
需要优化选择合适的催化剂。
催化剂是加氢裂化装置中起关键作用的组成部分,对产品质量和产量有着重要影响。
目前,虽然市场上已有多种催化剂可供选择,但如何选择适合特定工艺条件的催化剂,以提高产品质量和产量,仍然是一个需要攻关的问题。
需要加强装置的在线监测技术。
随着工业自动化技术的不断发展,加强装置的在线监测技术,对装置的运行状态进行实时监测和分析,可以及时发现问题,并进行及时的调整和优化,提高装置的运行效率和产品质量。
二、生产航煤技术攻关航煤是一种用途广泛的航空燃料,具有高热值、低凝点、低硫含量等优点,广泛应用于航空工业。
如何通过加氢裂化装置优化运行,提高航煤的品质和产量,是需要攻关的技术难题。
需要优化选择合适的原料。
航煤生产的原料主要来自炼油产品,具有不同的烃组成和物理性质。
如何选择合适的原料,通过合理的原料配方,提高航煤的品质和产量,是亟需攻关的问题。
通过选择高质量的炼油产品,降低含硫量和凝点,提高航煤的品质。
需要优化加氢裂化装置的工艺条件。
通过优化工艺条件,提高裂化产物的选择性,减少不良副产物的生成,提高航煤的品质和产量。
调整加氢裂化装置的反应温度、压力、催化剂种类和催化剂用量等工艺参数,以提高航煤的产品质量和产量。
需要研究航煤的处理和升级技术。
航煤具有较高的凝点和含硫量,如何通过处理和升级技术,降低其凝点和含硫量,提高航煤的品质和适用性,是一个重要的攻关方向。
基于原油性质变化的航煤加氢装置节能优化经验阐述

基于原油性质变化的航煤加氢装置节能优化经验阐述随着航空业的蓬勃发展,航空煤油(航煤)需求日益增加,为了满足航空运输的需求,航空煤油的生产也在不断增加。
在航煤的生产过程中,加氢装置是非常重要的一环,它可以通过加氢使得原油中的硫、氮和重金属等元素得到脱除,从而保证航空煤油的质量,同时也降低了燃油的环境污染。
随着原油性质的变化,加氢装置在节能方面也面临着一些挑战。
本文将从原油性质变化的角度出发,结合实际案例,探讨航煤加氢装置的节能优化经验。
1. 航煤加氢装置的工作原理航煤加氢装置是利用氢气与原油中的硫、氮和重金属等元素进行反应,生成较为洁净的燃料。
在加氢的过程中,首先将含硫、含氮和重金属的原油通过加热器升温至加氢反应的最佳温度区间,然后送入加氢反应器中与氢气进行反应。
接着,通过冷却器将反应后的产物进行冷却,最后通过分离器将产生的硫、氮和重金属的化合物进行分离,从而得到较为洁净的航煤。
整个加氢过程需要消耗大量的能量,因此如何优化加氢装置的节能效果成为了工程师们的关注焦点。
2. 原油性质变化对加氢装置的影响原油的性质受多种因素影响,如地质条件、原油产地等。
而原油中的硫含量、氮含量等指标则直接影响加氢过程的能耗。
通常情况下,硫含量高的原油需要更多的氢气参与加氢反应,因此能耗也会相应增加。
而随着原油资源的逐渐枯竭,更多的是深度加工含硫、难处理的原油,这使得加氢装置的工作条件更加苛刻,能耗也大大增加。
不同的原油特性也会导致加氢装置的操作参数取值不同。
这包括了反应温度、压力等参数的设定,而这些参数的变化会直接影响到加氢过程的能耗。
3. 航煤加氢装置的节能优化经验(1)合理选择原油在实际生产中,根据原油的性质进行选择,优先选择含硫含量低、易处理的原油,这可以有效降低加氢装置的能耗。
还可以考虑对原油进行混合,通过控制不同原油的比例来达到降低加氢能耗的效果。
(2)优化加氢反应条件根据原油的性质和厂家实际情况,对加氢反应条件进行优化。
航煤加氢装置的运行优化及问题处理

航煤加氢装置的运行优化及问题处理摘要:航煤加氢装置运行近12年,通过采取降低分馏塔顶回流、投用汽提氮气、更换塔底泵叶轮及降低塔压等措施,使装置塔底热源消耗降低;通过调整柴油热源温度和流量、调整航煤原料初馏点,并调整航煤操作参数,使装置实现了满负荷运行;通过对分馏塔底再沸器检修,解决了航煤产品色度不合格的问题。
关键词:航煤加氢喷气燃料能耗银腐色度1 航煤加氢装置概述中石化股份天津分公司航煤加氢装置原设计加工能力80万吨/年,于2009年12月17日首次开工,在2012年8月扩能改造为100万吨/年。
装置采用石油化工科学研究院开发的航煤临氢脱硫醇RHSS技术,加工常减压装置的直馏航煤,生产满足国家标准GB6537-2018要求的3号喷气燃料。
近期,装置采取措施降低分馏塔热源消耗,实现装置满负荷运行,并解决了航煤产品色度不合格的问题。
2 优化降低航煤加氢分馏塔热源消耗2.1 攻关目标通过采取攻关措施,降低航煤加氢分馏塔热源消耗。
2.2 攻关采取主要措施2.2.1 降低分馏塔顶回流和外采量通过降低分馏塔顶回流,使分馏塔底热源消耗减少;经过攻关发现,分馏塔顶回流过小,会影响塔顶、塔底物料传质,造成塔底物料中的硫化氢不能充分脱除,使航煤产品银片腐蚀不合格。
硫化氢对银片腐蚀的影响是很大的,只要在喷气燃料中硫化氢硫化氢含量超过1ppm,银片腐蚀就会不合格[1]。
通过攻关摸索得出结论,航煤塔顶回流量不低于1.9t/h(回流阀位不小于35%),可以保证航煤产品银片腐蚀合格。
2.2.2 投用分馏塔汽提氮气通过攻关摸索看出,在航煤原料轻组分含量偏少时(航煤原料初馏点高于140℃),投用分馏塔汽提氮气,有助于分馏塔物料向上流动,保证塔顶有足够的回流量和外采量,进而保证航煤产品银片腐蚀合格。
2.2.3 更换分馏塔底泵P-202B叶轮为避免在降低分馏塔压力后,分馏塔底泵出现气蚀和振动偏大情况,将分馏塔底泵P-202B的叶轮进行了更换。
基于原油性质变化的航煤加氢装置节能优化经验阐述

基于原油性质变化的航煤加氢装置节能优化经验阐述随着全球能源需求的增长,航空煤油(航煤)作为航空运输领域最重要的燃料之一,受到了越来越多的关注。
航煤的加氢装置是炼油厂的关键设备之一,其主要作用是将原油中的硫、氮等杂质去除,提高航煤的质量,同时还能通过适当的操作和改造,实现节能降耗的效果。
1. 增加加氢装置的柔性和适应性。
由于原油中的硫含量逐渐降低,加氢装置在运行时可以适当降低加氢剂的投入量,减少废氢的产生,从而降低能源的消耗。
在设备设计和焦炭燃烧过程中,应充分考虑适应不同原油质量的变化,提高设备的适应性和柔性。
2. 优化加氢装置的操作方式。
根据不同原油的特性,合理选择加氢温度、压力、催化剂的使用量等操作参数,以达到最佳的去硫效果和最低的能耗。
要做好进料质量的监测和控制,避免运行中的异常情况导致能耗增加。
3. 提高加氢装置的热能利用效率。
炉排冷却器是加氢装置的重要组成部分,通过优化炉排冷却器的结构和操作方式,可以最大程度地回收废热,提高热能利用效率,减少能源的消耗。
还可以采用其他热能回收技术,如余热发电等,进一步提高能源利用效率。
4. 开展节能技术研发和推广。
针对航煤加氢装置存在的能耗问题,需要加大节能技术的研发力度,并将其推广应用到实际生产中。
可以研究新型催化剂的开发和应用,以提高反应活性和选择性,减少加氢剂的使用量,降低能耗。
利用先进的自动化控制技术,实现对加氢装置的精确控制和优化调节,也是节能降耗的重要手段。
基于原油性质变化的航煤加氢装置节能优化经验是一个持续完善和创新的过程。
通过合理选择操作参数,提高能量利用效率,开展节能技术研发和推广,可以实现航煤加氢装置的节能降耗,为航空运输领域的可持续发展做出贡献。
加氢裂化装置优化运行生产航煤技术攻关

加氢裂化装置优化运行生产航煤技术攻关近年来,随着航空业的发展和煤化工技术的不断成熟,航空煤油(即航煤)作为航空燃料的重要来源,受到了广泛关注。
而在生产航煤的关键环节中,加氢裂化装置的优化运行技术攻关显得尤为重要。
加氢裂化技术是一种将重质石油馏分加氢裂化制取轻质石油产品的重要工艺,其技术和工艺参数的优化将直接影响到航煤产品的质量和产量。
加氢裂化技术的优化运行,不仅需要充分考虑原料性质、反应条件、催化剂性能等因素,同时也需要结合现代化控制技术,实现对加氢裂化装置的全面精细化管理。
为此,国内外的研究机构和企业纷纷投入到加氢裂化装置优化运行生产航煤技术攻关中,不断探索更加高效、节能、环保的加氢裂化技术。
加氢裂化装置的优化运行需要充分考虑原料的性质。
由于原料不同、质量不同,对于加氢裂化工艺参数的要求也各有不同。
在生产实践中,需要开展多方面的原料研究,确定最佳的原料组合和质量指标,以确保加氢裂化反应的高效进行。
也需要引入先进的原料预处理技术,对原料进行预处理,提高其稳定性和纯净度,从而更好地满足反应的要求。
加氢裂化装置的优化运行还需要重点考虑反应条件的优化。
在加氢裂化过程中,反应条件的设定对于产品产率和产品质量有着至关重要的影响。
包括反应温度、压力、催化剂种类和性能等参数的选择和调整,都需要进行深入研究和综合考量。
通过合理的反应条件优化,可以提高产品的产量和质量,同时还能够降低生产过程中的能耗和排放,实现资源的高效利用和环境的友好保护。
加氢裂化装置的优化运行也需要考虑催化剂的性能和使用寿命。
催化剂是加氢裂化反应的关键,其选择和使用对于反应的进行有着至关重要的作用。
需要对催化剂的性能进行深入研究,包括活性、稳定性、抗中毒性等指标的优化。
还需要研究催化剂的再生技术,延长催化剂的使用寿命,降低生产成本,提高装置的经济效益。
加氢裂化装置的优化运行还需要结合现代化控制技术,实现对装置的全面精细化管理。
通过引入先进的自动化设备和技术,对加氢裂化装置进行全过程的在线监测和控制,实时调整各项工艺参数,保证装置的安全稳定运行。
加氢裂化装置优化运行生产航煤技术攻关
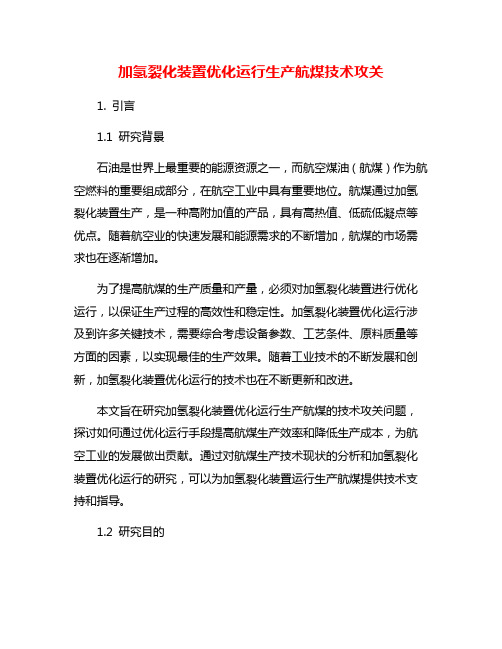
加氢裂化装置优化运行生产航煤技术攻关1. 引言1.1 研究背景石油是世界上最重要的能源资源之一,而航空煤油(航煤)作为航空燃料的重要组成部分,在航空工业中具有重要地位。
航煤通过加氢裂化装置生产,是一种高附加值的产品,具有高热值、低硫低凝点等优点。
随着航空业的快速发展和能源需求的不断增加,航煤的市场需求也在逐渐增加。
为了提高航煤的生产质量和产量,必须对加氢裂化装置进行优化运行,以保证生产过程的高效性和稳定性。
加氢裂化装置优化运行涉及到许多关键技术,需要综合考虑设备参数、工艺条件、原料质量等方面的因素,以实现最佳的生产效果。
随着工业技术的不断发展和创新,加氢裂化装置优化运行的技术也在不断更新和改进。
本文旨在研究加氢裂化装置优化运行生产航煤的技术攻关问题,探讨如何通过优化运行手段提高航煤生产效率和降低生产成本,为航空工业的发展做出贡献。
通过对航煤生产技术现状的分析和加氢裂化装置优化运行的研究,可以为加氢裂化装置运行生产航煤提供技术支持和指导。
1.2 研究目的本文的研究目的旨在通过对加氢裂化装置优化运行生产航煤技术进行深入探讨和研究,提高航煤生产效率和质量,实现航煤生产过程的优化和提升,进一步推动我国航煤产业的发展和提升。
具体来说,本研究旨在探索加氢裂化装置优化运行的关键技术,明确实施方案,并验证其实施效果,为加氢裂化装置运行生产航煤技术攻关提供有效支撑和指导。
通过本次研究,我们希望能够为航煤生产行业的技术改进和优化提供有益的经验和启示,为我国航煤产业的可持续发展和提升做出积极贡献。
2. 正文2.1 加氢裂化装置优化运行的重要性加氢裂化装置是航煤生产中非常重要的设备,其优化运行对于提高航煤生产效率、降低生产成本具有重要意义。
加氢裂化装置的优化运行可以有效提高燃料油和柴油的产量,同时降低焦油和其他副产物的生成量,提高产品质量和市场竞争力。
通过加氢裂化装置的优化运行,还可以降低能耗、减少环境污染,实现经济效益与环保效益的双赢。
加氢裂化装置优化运行生产航煤技术攻关
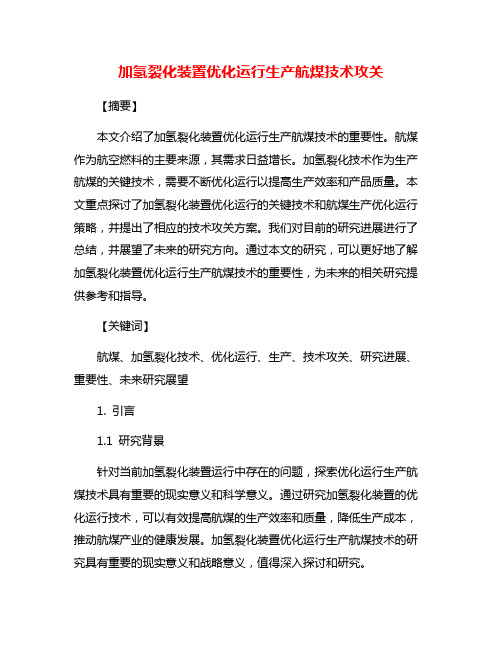
加氢裂化装置优化运行生产航煤技术攻关【摘要】本文介绍了加氢裂化装置优化运行生产航煤技术的重要性。
航煤作为航空燃料的主要来源,其需求日益增长。
加氢裂化技术作为生产航煤的关键技术,需要不断优化运行以提高生产效率和产品质量。
本文重点探讨了加氢裂化装置优化运行的关键技术和航煤生产优化运行策略,并提出了相应的技术攻关方案。
我们对目前的研究进展进行了总结,并展望了未来的研究方向。
通过本文的研究,可以更好地了解加氢裂化装置优化运行生产航煤技术的重要性,为未来的相关研究提供参考和指导。
【关键词】航煤、加氢裂化技术、优化运行、生产、技术攻关、研究进展、重要性、未来研究展望1. 引言1.1 研究背景针对当前加氢裂化装置运行中存在的问题,探索优化运行生产航煤技术具有重要的现实意义和科学意义。
通过研究加氢裂化装置的优化运行技术,可以有效提高航煤的生产效率和质量,降低生产成本,推动航煤产业的健康发展。
加氢裂化装置优化运行生产航煤技术的研究具有重要的现实意义和战略意义,值得深入探讨和研究。
1.2 研究意义研究意义:加氢裂化装置在航煤生产中扮演着至关重要的角色。
通过优化其运行和生产技术,可以提高航煤的产量和质量,降低生产成本,从而促进航煤产业的健康发展。
加氢裂化技术的优化也可以降低对环境的影响,减少废弃物的产生,达到资源节约和环境保护的效果。
对加氢裂化装置优化运行生产航煤技术的研究具有重要的意义。
2. 正文2.1 航煤需求与加氢裂化技术航煤是一种重要的航空燃料,具有良好的燃烧性能和高能量密度,广泛应用于民航、军航和舰船等领域。
随着航空产业的快速发展,航煤需求量逐年增加。
为了满足对航煤的需求,加氢裂化技术成为重要的生产方式。
加氢裂化技术是一种高效的油品加工技术,能够将较重的石油馏分转化为轻质产品,包括航煤。
通过加氢裂化,可以提高航煤的产率和质量,满足不同飞行条件下航空发动机的需求。
加氢裂化技术还可以实现资源的充分利用,减少环境污染。
- 1、下载文档前请自行甄别文档内容的完整性,平台不提供额外的编辑、内容补充、找答案等附加服务。
- 2、"仅部分预览"的文档,不可在线预览部分如存在完整性等问题,可反馈申请退款(可完整预览的文档不适用该条件!)。
- 3、如文档侵犯您的权益,请联系客服反馈,我们会尽快为您处理(人工客服工作时间:9:00-18:30)。
航煤加氢装置优化操作
摘要:针对镇海炼化炼油四部航煤加氢装置的实际生产情况,分析装置生产存在的问题,并采取相应的对策。
经过相应措施的实施,达到装置的长周期运行及全面达标。
关键词:航煤加氢压降达标
一、概述
航煤加氢装置2001年5月建成投产,该装置采用北京石油化工科学研究院开发的新一代航煤精制技术RHSS技术,它包括新型加氢脱硫醇催化剂RSS—1A以及与之相适应的临氢脱硫醇工艺,集合了非临氢及加氢两种工艺的特点,选用低温活性好的催化剂,操作费用较低,经济效益好,生产的高附加值航煤产品量占公司航煤成品出厂量的大头。
但航煤装置生产也存在不少难点。
首先航煤质量指标多、要求严,操作条件苛刻,操作上稍有疏忽就会导致馏出口不合格并污染成品大罐,而且不能进行调和成为合格产品;其次装置开工周期短,投产时间不长,操作人员经验不足,操作条件有待变化;再次航煤原料/精制航煤换热器管程压降上升较快,影响到装置的处理量,相关管线振动幅度较大,甚至有可能造成装置非计划停工。
本文试图通过对航煤加氢装置操作特点的分析并采取相应措施,以达到克服各种不利因素,确保装置平稳长周期运行和全面达标的目的。
二、装置各项达标指标及难点分析
航煤加氢装置开工一来始终被公司定为二类达标装置,2004年装置的达标项及指标如表—1所示:
表-1:航煤加氢装置达标项目及指标
在实际生产过程中存在以下生产难点。
1、装置操作苛刻度高,馏出口合格率达标为工作难点。
航煤质量指标多、要求严、特别是银片腐蚀指标不合格原因目前还没有明确定论,一般认为航煤银片腐蚀主要是由有机硫、小分子硫醇、单体硫和硫化氢引起的。
从操作经验来看,本装置银片腐蚀不合格由微量硫化氢(均在1PPm以下)引起,但要定量分析,公司没有必要设备。
且银片腐蚀分析时间长达4小时,分析结果严重滞后给操作带来不利影响。
随着公司加工原油的劣质化趋势日益明显,航煤原料油性变化幅度较大,对操作影响较大,稍有疏忽会引起塔201底航煤银片腐蚀大于2级,从而导致精脱硫罐后航煤银片腐蚀在2级以上而不合格。
2、装置含硫污水含油量存在超标问题。
航煤加氢装置含硫污水分级控制合格率是与Ⅰ加氢装置合并考核的。
由于改造不彻底,特别
是Ⅰ加氢高分501及低分容502没有同步扩容,导致处理量提高后,物料在高低分停留时间缩短,油水没有充足时间分离,致使含硫污水分级控制合格率存在连续不合格的现象。
针对这一情况我们对旋流器容502/3进行了改造,将旋流器位置从容502移至容530后(泵513出口),经过容530油水再次分离及污水量增加而达到旋流器压降增加,取得了一定效果,但分离效果不稳定,污水含油量时高时低,分析认为含油污水旋流分离器作用发挥不到位,根据其它装置的经验,旋流器本身没有问题,只是旋流器出入口压差过小引起。
3、航煤原料换热器换201的压降问题。
航煤原料主要是Ⅲ常一线,航煤原料经储运部G401/G402罐缓冲后付装置,由于这两只罐只有5000M3,航煤料在罐内停留沉降时间非常有限,Ⅲ常经常性对常压塔顶系统冲水,加上Ⅲ常腐蚀问题没有得到有效解决,使常一线航煤料经常夹带微小黑色颗粒物质,最后送到航煤加氢装置。
因此航煤原料夹带颗粒物是压降上升的主要原因。
再者缓冲罐、管线以及换热器管束生成的硫化亚铁等杂质堵塞了换热器的管束是次要原因。
换热器管程压降上升较快,影响到装置的处理量,压降上升后相关管线振动幅度较大,甚至有可能造成装置非计划停工。
三、相应的措施
为完成公司制度的达标目标,保证装置长周期运行,经过分析,采取以下几条措施:
1、根据航煤原料油性的变化,适当调整分馏塔进料、塔底、塔顶温度的回流量。
与国内类似装置进行交流,了解兄弟企业的生产情况,并上报大技措对分馏塔进行改造。
平时做好精脱硫剂的使用情况,
保证一罐投用,一罐备用,以确保航煤银腐合格。
根据硫化氢与无色醋酸铅反应生成黑色沉淀的机理,每4小时或遇生产波动即用醋酸铅试纸测航煤产品,发现醋酸铅试纸颜色变深及时调整操作。
2、平时加强容502、50
3、203、204界位控制,并对容502/3,容530相关管线进行改造,做好相关工作。
3、对航煤原料过滤器进行改造,并对航煤原料/精制航煤换热器增加付线,以利于生产中切出清洗,减少非计划停工次数。
四、措施实施
1、用醋酸铅试纸检测航煤产品,及时调整优化操作。
为完成质量馏出口合格率指标,部管理人员从质管中心要来醋酸铅试纸,班组人员每班用醋酸铅试纸定时检测塔201底航煤(1次/4小时)及精脱硫罐后航煤(1次/4小时);较大幅度调整操作、提进料量、提反应温度及压力时增加检测频次,脱前航煤1次/2小时、脱后航煤1次/2小时;当油性明显变化、操作异常及发现醋酸铅试纸颜色变深,不定时增加检测,防止出现银片腐蚀不合格;并利用操作经验及时调整操作,实施分馏炉炉膛温度与瓦斯流量串级控制,提高操作平稳率,从而提高馏出口合格率。
2、加强精细操作
为确保含硫污水分级控制合格率达标,要求含硫污水旋流器投用。
平时加强容203、204、502、503、504界位控制。
检查容502/3后发现其内部的4根旋流管有3根受损,设备人员将设备修复后,并
利用大修时对旋流器污油出口回容530管线扩径,防止污油积存旋流器同时增加污水循环量,增加旋流器压降;容530污油接管线进入新增的闪蒸罐容532,污水污油再次进行沉降,提高污水污油分离效果,确保含硫污水分级控制合格率达标。
定期对容502/3进行水冲洗,以保证油水分离效果,另一方面对容530管线进行改造,增加了容530顶直接至低压瓦斯线,做到方便、安全溢油。
3、实施技术改造项目确保装置安稳长生产
2003年利用停工大检修机会,装置增上的微米原料过滤器201/3,滤芯精度为40um。
由于在运行过程中,滤芯由外至内堵塞程度逐渐加重,并且折叠状滤网深处不易清理,清洗的时间间隔逐渐缩短,运行时间由最初的15天缩短至3天。
由于人工清洗不便,导致滤芯堵塞严重,并有部分滤芯破损,而导致滤芯报废。
为了选择适合生产的滤芯,通过不断调整滤芯精度,先后试用植物纤维滤芯,不锈钢丝网60um、200um、80um,最后选定为80un的不锈钢丝网滤芯;同时上报技措,再新添加1个过滤器,滤芯精度定为40um,采用串联使用,以延长滤芯使用周期。
通过对过滤器的改造,装置受“黑料”、“灰料”冲击明显减少。
2004年9月,利用停工消缺机会,对航煤原料/精制航煤换热器管壳程增加了跨线,换热器压降高时切出进行清洗而不影响生产,达到了预期目的。
使装置安全、平稳生产得以顺利进行。
五、实施效果
经过不断努力,装置运行和达标情况良好,取得了不错的成绩。
2006年达标数据如下表-2所示:
表-2:航煤加氢装置达标统计数据
六、遗留问题
根据金山、高桥石化公司同类航煤加氢装置操作情况,单塔分馏完全可以使塔底航煤银片腐蚀达到成品指标(1级以下),目前航煤加氢装置在低处理量能达到1级,但在大处理量时银片腐蚀只能达到2级,可能是因为塔上部塔径小汽液相负荷卡脖子,操作回流量过小导致分馏精度不够。
设计增上精脱硫罐的本意是抵御生产波动对产品质量的影响,防止短时间不合格航煤对大罐的污染。
但实际操作中必须依赖后精制才能确保航煤产品合格。
因此分馏塔改造的项目仍要进行下去,以解决航煤银腐问题,降低生产成本。
中国石化镇海炼化公司
炼油四部。