高炉炼铁影响铁水含硫量因素的分析_赵亮
顶底复吹转炉冶炼双相不锈钢的试验研究
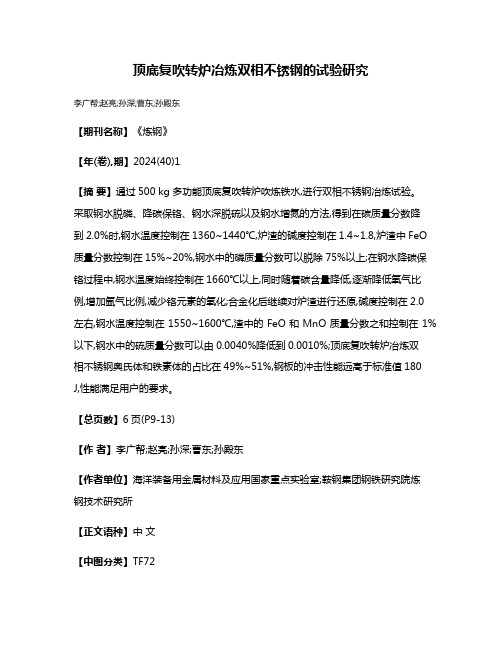
顶底复吹转炉冶炼双相不锈钢的试验研究
李广帮;赵亮;孙深;曹东;孙殿东
【期刊名称】《炼钢》
【年(卷),期】2024(40)1
【摘要】通过500 kg多功能顶底复吹转炉吹炼铁水,进行双相不锈钢冶炼试验。
采取钢水脱磷、降碳保铬、钢水深脱硫以及钢水增氮的方法,得到在碳质量分数降
到2.0%时,钢水温度控制在1360~1440℃,炉渣的碱度控制在1.4~1.8,炉渣中FeO 质量分数控制在15%~20%,钢水中的磷质量分数可以脱除75%以上;在钢水降碳保铬过程中,钢水温度始终控制在1660℃以上,同时随着碳含量降低,逐渐降低氧气比例,增加氩气比例,减少铬元素的氧化;合金化后继续对炉渣进行还原,碱度控制在2.0左右,钢水温度控制在1550~1600℃,渣中的FeO和MnO质量分数之和控制在1%以下,钢水中的硫质量分数可以由0.0040%降低到0.0010%;顶底复吹转炉冶炼双
相不锈钢奥氏体和铁素体的占比在49%~51%,钢板的冲击性能远高于标准值180 J,性能满足用户的要求。
【总页数】6页(P9-13)
【作者】李广帮;赵亮;孙深;曹东;孙殿东
【作者单位】海洋装备用金属材料及应用国家重点实验室;鞍钢集团钢铁研究院炼
钢技术研究所
【正文语种】中文
【中图分类】TF72
【相关文献】
1.100 t顶底复吹转炉冶炼过程的水力学模拟研究
2.氧气顶底复吹转炉冶炼中碳锰铁的试验研究
3.150t顶底复吹转炉全程底吹氮的试验研究
4.顶底复吹转炉冶炼不锈钢还原期行为研究
因版权原因,仅展示原文概要,查看原文内容请购买。
高炉炼铁中脱硫技术研究降低铁水中的硫含量

高炉炼铁中脱硫技术研究降低铁水中的硫含量高炉炼铁是一种重要的冶金过程,其目的是将矿石转化为高品质的铁水。
然而,在炼铁过程中,铁水中的硫含量是一个关键的指标。
过高的硫含量不仅会影响最终产品的质量,还会对环境造成污染。
因此,研究和开发高效的脱硫技术成为了炼铁行业的重要课题。
本文将探讨几种常见的高炉炼铁中脱硫技术,并分析其优缺点。
一、喷射脱硫技术喷射脱硫技术是目前常用的一种高炉炼铁中脱硫方法。
其原理是通过向高炉内部喷射含碱性物质的溶液,让溶液中的碱金属与炉内的硫元素反应,生成易挥发的硫化物,从而实现脱硫的目的。
这种技术操作简单,成本相对较低,可以实现连续的脱硫过程。
但是,喷射脱硫技术不能完全去除铁水中的硫,对于硫含量较高的铁水效果有限。
二、石灰脱硫技术石灰脱硫技术是另一种常见的高炉炼铁中脱硫方法。
这种方法通过加入石灰石(氧化钙)或生石灰(氢氧化钙)等石灰性物质到高炉中,使石灰中的碱金属与铁水中的硫反应生成硫化物,从而实现脱硫的效果。
石灰脱硫技术可以有效地降低铁水中的硫含量,对于高硫铁矿石的脱硫效果尤为显著。
然而,这种方法的缺点是石灰在高炉中的溶解速度相对较慢,需要更长的时间来实现脱硫。
三、钙镁脱硫技术钙镁脱硫技术是一种比较新颖的高炉炼铁中脱硫方法。
该方法通过加入含有碱性金属氧化物的钙镁废渣到高炉中进行脱硫。
废渣中的氧化物可以与硫元素发生反应生成硫化物,从而实现脱硫的效果。
相比于其他脱硫技术,钙镁脱硫技术具有以下优点:脱硫效果好,对硫含量较高的铁水也有较好的处理能力;操作简单,无需引入其他化学药剂;充分利用废渣资源,具有环保效益。
四、电渣重熔技术电渣重熔技术是一种应用于高炉炼铁中的先进脱硫方法。
通过将铁水转移到电渣炉中进行二次冶炼和脱硫,可以有效地降低铁水中的硫含量。
这种方法具有以下优势:可以在绝热状态下进行,脱硫效果好;炉内温度可控,有利于脱硫反应的进行;处理量大,适用于大型高炉。
五、微生物脱硫技术微生物脱硫技术是一种新兴的高炉炼铁中脱硫方法。
高[S]铁水冶炼工艺指导
![高[S]铁水冶炼工艺指导](https://img.taocdn.com/s3/m/f6a195df4128915f804d2b160b4e767f5acf80e9.png)
高[S]铁水冶炼工艺指导一、定义高[S]铁水是指炼铁高炉在非正常情况下生产的超标铁水,铁水[S]含量大于0.070%。
二.硫对钢性能的影响硫在钢中以[FeS]的形式存在,钢中含锰高时也有[MnS]存在。
1、使钢的热加工性能变坏。
硫在液态铁中,硫能无限溶解,而在固态铁中溶解的很少(溶解度仅为0.015-0.020%)钢液在凝故时,随着钢液的温度下降,硫在尚未凝固的钢液逐渐浓聚。
这种被隔离于枝晶间的钢液最后冷却时就会析出FeS,FeS溶点仅1190℃。
当钢在热加工加热过程中,只要超过1100℃时,富集于晶界处的低熔点硫化物夹杂会使晶粒边界处呈脆性或熔融状态,钢坯在轧制或锻造过程中出现裂纹甚至开裂,这种现象称为“热脆”。
严重影响钢的热加工性能。
如果当钢液含氧量高时,在钢液凝故过程中,以FeO形式析出的氧会与FeS形成溶点更低的FeS-FeO共晶体(940℃)在加工时也容易引起“热脆”现象,从而加剧了硫的有害作用。
2、对钢的机械性能产生不良影响。
钢中含硫量高时,塑性硫化物(MnS、FeS、MgS等)的夹杂物增加,热加工时,这种夹杂物沿受力方向延伸,因而使钢材的横向机械性能降低,即横向延伸率和断面收缩率下降。
3、钢的焊接性能变坏。
含硫高的钢材,焊接时往往会出现高温龟裂。
影响程度随钢中的碳、磷的存在而加大。
同时焊接过程中硫易于氧化,生成SO2气体而逸出,导致在焊缝金属中产生很多气孔和疏松,降低了焊接部位的机械强度。
4、当钢中含硫量超过0.06%时,钢的耐腐蚀性能显著恶化。
5、在纯铁和硅钢中随着含硫量含量的提高,磁滞损失增加。
总之,硫对钢材的性能有很多不良影响,在一定条件下,这种不良影响也能得到抑制,锰能抑制硫的有害作用,因为锰能与硫形成较稳定的MnS,溶点(1620℃)远高于热加工温度,因而可以消除“热脆”现象。
三.脱硫的过程及基本反应1、脱硫的基本反应硫在钢液中主要以[FeS]形式存在,在炉渣中可以以(FeS)形式存在。
重钢五高炉炉渣脱硫能力影响因素的浅析

33 铁水 成分 -
铁水 中的非金属元素 ( C S、 元素 ) 如 、 iP 由于 要影响硫的活度 ,从而也会对炉渣的脱硫反应产生
一
般来讲 ,高炉利用系数越高 , 日 或 产量越高,则
定 的影 响 。
34 炉渣 粘度 .
高炉放铁放渣就越勤 , 炉渣与铁水接触时间就越短 , 就越不利于高炉脱硫。因此可以用 日 产量除时间, 即用单位生铁在炉内停 留时间来近似表示炉渣与铁
据高炉解剖研究证实,铁水进入炉缸前的含硫 量 比出炉铁水含硫量高得多 ,由此认为 ,正常操作
中主要 的脱硫 反应 是在铁 水滴 穿过炉 缸 时的渣层 和 炉 缸 中渣 铁相 互接 触 时发生 的 。
脱硫 反应 方程 式 : 【e](a )C (a)C +F ]19 k F S+C O + =C S+ O [e- 0 J 41 4 或 :【】( C ( )C S+O =S 十 O
括 :炉渣粘度以及渣铁接触条件 。 31温度 . 温度的升高有利于吸热反应 ,温度的降低有利 于放热反应。在高炉冶炼过程中 ,由于 s 和 T 的 i i
还原 都 是 吸热 反应 , 【 s [ ] i】与 L=S/ ) i( S 【 n[iT 】 L= ] i 与炉温具有很强 的相关性 ,而炉料 T/ ) ( 结构的变化可能会影响到生铁中【i s 和 i 】 】 的含量 ,
・
l ・ l
维普资讯
《 重钢五高炉炉渣脱硫能力影响因素的浅析 》
I = - 2 .4 + 9 .5 Xl 2 6 7 + 3 2 8 _ 6 4 40 0 0 + 6 .4 X2 3 . 6 X3
一
定系数 R= . , 2 6 调整后的决定系数 R= . , = . 00 0 6 F 3 9 4 9 > o ( ,1 = . ,表明上式在一定程度上 能解 F 8 ) 22 2 4 释硫在高炉渣铁间的分配 系数 I 与各因素之间比 _ 6
《高炉炼铁技术》项目8任务8.4生铁去硫

冶金工程系
张丰红制作
3
8.4.2硫在煤气、渣、铁中的分配
冶金工程系
张丰红制作
13
三、炉渣的脱硫能力
高炉中的硫除一部分挥发外,其余的硫都经过反应变成 CaS和FeS。CaS不溶于生铁而进入炉渣中。FeS则溶于 生铁,成为生铁的有害组成部分。生铁脱硫主要就是使 FeS和CaO作用生成CaS,使硫由生铁转入到炉渣中。 由于炉渣和铁水互不溶解,所以脱硫只能在渣铁接触面 进行。在渣铁界面上的脱硫反应是:
海南矿:500×O.545=273
锰矿:170×0.12=20.4
合计:
3853.4
每批料出铁量:
3853.4/0.94=4099公斤(0.94为生铁含铁量)
冶金工程系
张丰红制作
9
②硫负荷
7000×0.O28%=1.96 500×0.148%=0.725 2420×0.74%=17.908 合计:20.593 硫负荷=20.593/4099=0.005O2公斤/公斤铁=5.O2(公斤/ 吨·铁)
分解生成的FeS在高炉上部,会有少量的被Fe203或H20氧化。 FeS+10Fe203=7Fe304+SO2 一Q
3FeS+4H2O=Fe304+3H2S↑ +H2↑一Q
冶金工程系
ቤተ መጻሕፍቲ ባይዱ
张丰红制作
11
影响硫挥发的因素主要有:
(1)焦比和炉温 焦比和炉温高,生成煤气量也增多,煤气流速随之 加快,因而煤气在炉内的停留时间缩短,减少了 被吸收的硫量,增加了随煤气挥发的硫量。
准确获取铁水中硫含量的方法
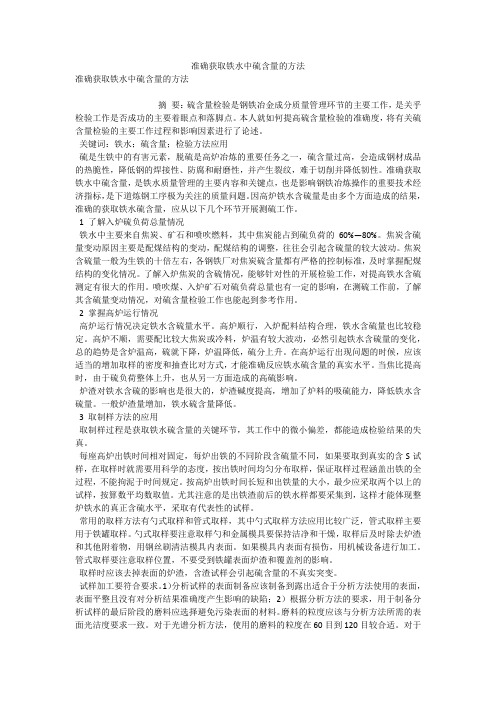
准确获取铁水中硫含量的方法准确获取铁水中硫含量的方法摘要:硫含量检验是钢铁冶金成分质量管理环节的主要工作,是关乎检验工作是否成功的主要着眼点和落脚点。
本人就如何提高硫含量检验的准确度,将有关硫含量检验的主要工作过程和影响因素进行了论述。
关键词:铁水;硫含量;检验方法应用硫是生铁中的有害元素,脱硫是高炉冶炼的重要任务之一,硫含量过高,会造成钢材成品的热脆性,降低钢的焊接性、防腐和耐磨性,并产生裂纹,难于切削并降低韧性。
准确获取铁水中硫含量,是铁水质量管理的主要内容和关键点,也是影响钢铁冶炼操作的重要技术经济指标,是下道炼钢工序极为关注的质量问题。
因高炉铁水含硫量是由多个方面造成的结果,准确的获取铁水硫含量,应从以下几个环节开展测硫工作。
1 了解入炉硫负荷总量情况铁水中主要来自焦炭、矿石和喷吹燃料,其中焦炭能占到硫负荷的60%―80%。
焦炭含硫量变动原因主要是配煤结构的变动,配煤结构的调整,往往会引起含硫量的较大波动。
焦炭含硫量一般为生铁的十倍左右,各钢铁厂对焦炭硫含量都有严格的控制标准,及时掌握配煤结构的变化情况。
了解入炉焦炭的含硫情况,能够针对性的开展检验工作,对提高铁水含硫测定有很大的作用。
喷吹煤、入炉矿石对硫负荷总量也有一定的影响,在测硫工作前,了解其含硫量变动情况,对硫含量检验工作也能起到参考作用。
2 掌握高炉运行情况高炉运行情况决定铁水含硫量水平。
高炉顺行,入炉配料结构合理,铁水含硫量也比较稳定。
高炉不顺,需要配比较大焦炭或冷料,炉温有较大波动,必然引起铁水含硫量的变化,总的趋势是含炉温高,硫就下降,炉温降低,硫分上升。
在高炉运行出现问题的时候,应该适当的增加取样的密度和抽查比对方式,才能准确反应铁水硫含量的真实水平。
当焦比提高时,由于硫负荷整体上升,也从另一方面造成的高硫影响。
炉渣对铁水含硫的影响也是很大的,炉渣碱度提高,增加了炉料的吸硫能力,降低铁水含硫量。
一般炉渣量增加,铁水硫含量降低。
高炉铁合金制备中的含硫物质处理与去除

高炉铁合金制备中的含硫物质处理与去除随着钢铁行业的不断发展,高炉铁合金制备作为关键环节之一,对于钢铁生产的质量和效率具有重要影响。
然而,在高炉铁合金制备过程中,常常会出现含有硫的物质,如硫化铁等,不仅会影响产品质量,还会对环境造成污染。
因此,正确处理和去除含硫物质成为高炉铁合金制备过程中的关键问题。
含硫物质对高炉铁合金制备的影响主要体现在以下几个方面。
首先,含硫物质会对钢铁产品的质量产生负面影响。
硫化铁等含硫物质在高温条件下会与钢铁中的氧化铁反应生成硫酸铁,导致钢铁中的硫含量升高。
高硫含量会使钢铁产品的强度降低,延展性变差,同时还会增加钢铁的脆性。
这不仅降低了钢铁产品的质量,还可能导致产品在使用过程中出现断裂等安全隐患。
其次,含硫物质还会对高炉系统产生不良影响。
硫在高炉燃烧过程中会生成二氧化硫等气体,这些气体在高温状况下会导致高炉炉内的腐蚀,降低炉体的寿命。
同时,高硫含量还会对炉渣性能产生不利影响,降低了炉渣的碱度和可容受硫的能力,从而进一步影响整个高炉的稳定运行。
针对高炉铁合金制备中的含硫物质问题,有以下几种处理和去除方法。
第一,采取物理方法去除含硫物质。
物理方法一般是通过物质分离或分解的方式,将含硫物质与钢铁分离。
例如,可以通过热力学原理,利用物质的挥发性差异,实现含硫物质与钢铁的分离。
另外,也可以考虑利用物质的密度差异,通过重力分离或离心分离的方式,将含硫物质从钢铁中去除。
第二,采用化学方法对含硫物质进行处理。
化学方法主要是通过反应或中和的方式,将含硫物质转化为易于处理或去除的物质。
例如,可以利用氧化剂将硫化铁氧化为硫酸铁,然后通过加碱中和的方式将硫酸铁从钢铁中去除。
另外,还可以考虑使用还原剂将硫酸铁还原为硫化物,然后通过物理方法将硫化物与钢铁分离。
第三,采取预处理的方式降低含硫物质的含量。
在高炉铁合金制备过程中,可以在原料的预处理阶段对含硫物质进行降解或转化。
一种常见的方法是在原料中加入适量的脱硫剂,将硫化物转化为易于处理的化合物。
攀钢西昌钢钒高炉铁水适宜硫含量分析

攀钢西昌钢钒高炉铁水适宜硫含量分析饶家庭;王敦旭;谢洪恩【摘要】为了寻求炼铁、炼钢工序经济适宜的铁水硫含量,通过对生产数据的统计,分析了攀钢西昌钢钒1号高炉铁水硫含量与技术经济指标的关系,得到了攀钢西昌钢钒高炉铁水钛含量与铁水硫含量及焦比的回归公式;并依据高炉冶炼过程中实际的矿焦比与铁水钛含量的经验数据,计算分析了不同铁水硫含量与炼铁的原、燃料成本的关系,综合考虑炼钢脱硫成本的变化,得出当前硫负荷条件下铁水适宜的硫含量(质量分数)应控制在0.085%左右.【期刊名称】《材料与冶金学报》【年(卷),期】2014(013)001【总页数】4页(P11-14)【关键词】硫负荷;铁水硫含量;成本;炼钢脱硫【作者】饶家庭;王敦旭;谢洪恩【作者单位】攀钢集团研究有限公司钒钛资源综合利用国家重点实验室,四川攀枝花617000;攀钢集团西昌钢钒有限公司技术质量部,四川西昌615000;攀钢集团研究有限公司钒钛资源综合利用国家重点实验室,四川攀枝花617000【正文语种】中文【中图分类】TF821钢铁厂为了降低生产成本,有时不得不降低原燃料质量以适应市场需求.攀钢西昌钢钒因煤资源紧张,高硫煤配比增加,焦炭含硫量上升,2012年12月份以来,高炉入炉硫负荷由原来的4.2 kg/t上升至4.7 kg/t以上.加之炉渣TiO2含量上升,冶炼温度降低,炉渣脱硫能力下降,致使铁水平均w[S]由0.065%左右上升至0.075%甚至0.10%,从而增加了炼钢铁水脱硫工序的负荷与成本.普通矿高炉冶炼实践表明[1,2],高炉温和强还原气氛是脱硫的良好条件,铁水w[S]一般可达到0.030%左右甚至更低.但是,由于高钛型钒钛磁铁矿高炉冶炼的特殊性,需采用低炉温冶炼,如提高冶炼温度以降低铁水硫含量,则将导致高钛型高炉渣与铁水的分离困难,金属铁损失增加,焦比上升,技术经济指标变差.生产实践表明,通过提高冶炼温度来降低铁水硫含量是不经济的.因此,分析目前冶炼条件下实现适宜铁水硫含量,兼顾炼钢脱硫工序成本,具有重要意义.对西昌钢钒1号高炉2012年10-12月份的日均技术经济指标按铁水硫含量分别统计,见表1.从表1可知,随着铁水硫含量上升,高炉利用系数升高,焦比下降,燃料比下降,金属铁损失降低明显.可见,在一定范围内放宽对铁水硫含量的要求,高炉技术经济指标改善明显.通常,高炉中的硫主要来自于入炉燃料,焦炭带入的硫占总入炉硫量的70%左右.西昌钢钒1号高炉的硫分布见表2.表2表明,随焦炭硫含量升高,焦炭带入硫增加,高炉的硫负荷上升,硫在渣铁间的分配系数Ls下降,进入铁水硫比例略有上升.由此可知,西昌1号高炉铁水硫含量升高的主要原因是焦炭硫含量上升,导致入炉硫负荷上升,以及硫分配系数Ls降低.选取西昌钢钒1号高炉10-12月炉况稳定的每个铁次铁水的沟样成分,以及日平均数据,分析铁水中w[S]与w[Ti]、w[Ti]与焦比Ck的关系,见回归公式(1)、(2).式中:R,N分别表示为相关系数及样本数量.由式(1)、式(2)可知,w[S]与w[Ti]、w[Ti]与焦比关系显著,随着w[Ti]升高,w[S]含量下降,焦比上升.根据回归公式(1)、(2),计算不同[Ti]含量条件下的[S]及焦比,根据矿石与焦炭批重的对应关系(矿焦比范围3.8~4.7 t/t),计算出不同铁水硫含量下的焦比、矿石消耗量及吨铁的原、燃料成本(矿耗+焦比)见图1.实践表明,高炉工序提高脱硫能力的主要措施之一是提高炉温,由图1可知,随着铁水[S]含量降低,焦比升高,随之矿耗增加,原燃料成本增加.从图2可知,随着铁水[S]含量放宽,原燃料成本下降.虚线表示入炉硫负荷上升,如果要维持相同的铁水[S],则原燃料成本增加.由图2可计算出不同铁水硫含量范围条件下焦比、矿耗及成本的变动,结果见表3.从表3可知,随着铁水硫含量增加,焦比+矿耗的成本增加,但变动幅度逐渐减小. 铁水[S]含量(质量分数)与铁水预处理用脱硫剂成本的关系见图3.由图3可见,铁水硫含量升高,脱硫剂成本大幅度上升.铁水中 w[S]由 0.050%上升至0.075%后,脱硫剂成本由 12.21元/t升到17.73元/t;如果铁水硫含量上升到0.10%,脱硫剂成本上升至24.93元/t.在不考虑LF脱硫增加成本和钢种兑现率下降等因素情况下,通过对不同铁水硫含量区间的炼钢脱硫过程中的成本统计计算见表4.从表4可以看出,随铁水硫含量增加,炼钢成本增加,铁水硫含量愈高,炼钢成本增幅愈大.由上分析可知,随着铁水硫含量上升,炼铁原燃料成本逐渐降低,降低幅度逐渐减小,而炼钢成本逐渐增加,且增加幅度逐渐加大,它们之间的关系呈抛物线关系.综合铁水[S]含量对炼铁原燃料和炼钢脱硫总成本的影响见图4.根据抛物线的最小取值点可得,适宜铁水[S]含量(质量分数)约0.085%时,总成本最低,即铁水硫的质量分数超过或低于0.085%时,炼铁炼钢脱硫总成本将上升.(1)目前原料条件下西昌钢钒高炉硫分配系数Ls为7~9,进入高炉后总硫的13%~14%进入铁水.铁水硫含量升高的主要原因是高炉硫负荷升高以及炉渣脱硫能力降低.(2)随着铁水[Ti]含量下降,铁水硫含量增加,焦比降低,炼铁原燃料成本降低,但降低幅度逐渐减小(3)随着铁水硫含量增加,炼钢脱硫成本逐渐增加,且增加幅度逐渐增大.(4)随着铁水硫含量增加,炼铁炼钢脱硫总成本呈抛物线下降,而后上升.在目前的生产条件下,适宜铁水硫含量(质量分数)为0.085%左右.【相关文献】[1]王筱留.钢铁冶金学(炼铁部分)[M].北京:冶金工业出版社,2008.(Wang Xiaoliu.Metallurgy of iron and steel(iron part)[M].Beijing:Metallurgical Industry Press,2008.)[2]梁利生.宝钢3号高炉低硅低硫冶炼[J].炼铁,2005,24 (增):41-45.(Liang Lisheng.No.3 BF low silicon and sulfur smelting at No.3 blast furnace in Baosteel [J].Iron-making 2005,24 (supp.):41-45.)。
273氧枪喷头空气动力学模拟研究
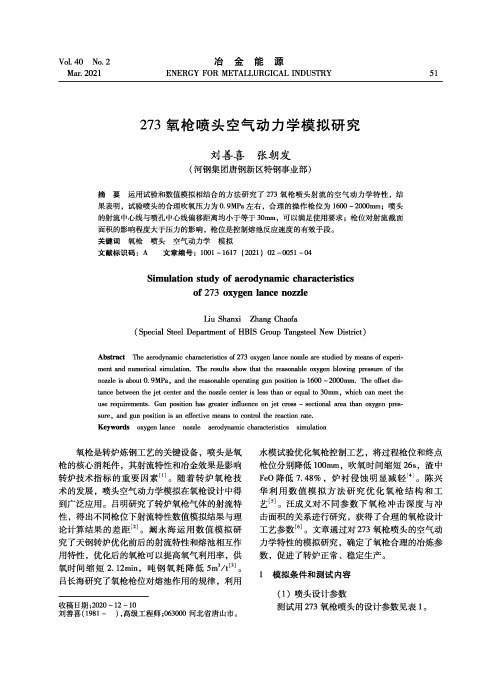
ENERGY FOR METALLURGICAL INDUSTRYMar. 202151氧枪是转炉炼钢工艺的关键设备,喷头是氧枪的核心消耗件,其射流特性和冶金效果是影响 转炉技术指标的重要因素⑴。
随着转炉氧枪技 术的发展,喷头空气动力学模拟在氧枪设计中得到广泛应用。
吕明研究了转炉氧枪气体的射流特 性,得出不同枪位下射流特性数值模拟结果与理 论计算结果的差距闵。
阚永海运用数值模拟研究了天钢转炉优化前后的射流特性和熔池相互作用特性,优化后的氧枪可以提高氧气利用率,供 氧时间缩短2. 12min,吨钢氧耗降低5m 3/t [3]。
吕长海研究了氧枪枪位对熔池作用的规律,利用273氧枪喷头空气动力学模拟研究刘善喜张朝发(河钢集团唐钢新区特钢事业部)摘要运用试验和数值模拟相结合的方法研究了 273氧枪喷头射流的空气动力学特性,结 果表明,试验喷头的合理吹氧压力为0. 9MPa 左右,合理的操作枪位为1600 ~ 2000mm ;喷头的射流中心线与喷孔中心线偏移距离均小于等于30mm,可以满足使用要求;枪位对射流截面 面积的影响程度大于压力的影响,枪位是控制熔池反应速度的有效手段。
关键词氧枪喷头空气动力学模拟文献标识码:A文章编号:1001 -1617 (2021) 02-0051 -04Simulation study of aerodynamic characteristicsof 273 oxygen lance nozzleLiu Shanxi Zhang Chaofa(Special Steel Department of HBIS Group Tangsteel New District)Abstract The aerodynamic characteristics of 273 oxygen lance nozzle are studied by means of experi ment and numerical simulation. The results show that the reasonable oxygen blowing pressure of thenozzle is about 0. 9MPa, and the reasonable operating gun position is 1600 ~2000mm. The offset dis tance between the jet center and the nozzle center is less than or equal to 30mm , which can meet the use requirements. Gun position has greater influence on jet cross - sectional area than oxygen pres sure, and gun position is an effective means to control the reaction rate.Keywords oxygen lance nozzle aerodynamic characteristics simulation水模试验优化氧枪控制工艺,将过程枪位和终点枪位分别降低100mm,吹氧时间缩短26s,渣中 FeO « 7. 48% ,炉衬侵蚀明显减轻⑷。
首钢京唐1号高炉铁水含硫高的分析
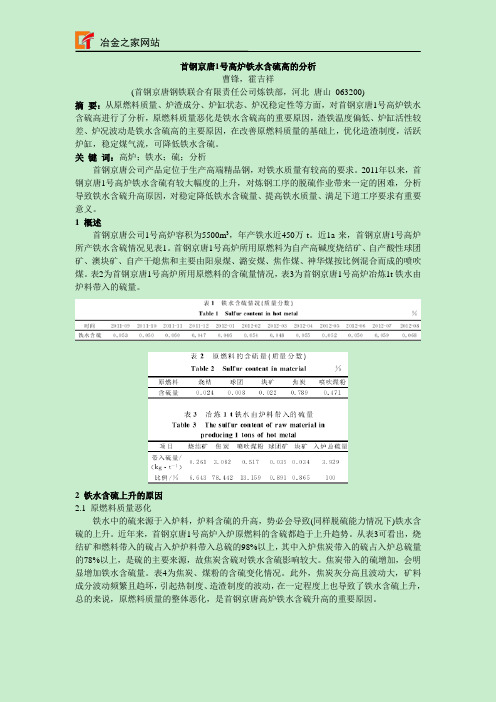
首钢京唐1号高炉铁水含硫高的分析曹锋,霍吉祥(首钢京唐钢铁联合有限责任公司炼铁部,河北唐山063200)摘要:从原燃料质量、炉渣成分、炉缸状态、炉况稳定性等方面,对首钢京唐1号高炉铁水含硫高进行了分析,原燃料质量恶化是铁水含硫高的重要原因,渣铁温度偏低、炉缸活性较差、炉况波动是铁水含硫高的主要原因,在改善原燃料质量的基础上,优化造渣制度,活跃炉缸,稳定煤气流,可降低铁水含硫。
关键词:高炉;铁水;硫;分析首钢京唐公司产品定位于生产高端精品钢,对铁水质量有较高的要求。
2011年以来,首钢京唐1号高炉铁水含硫有较大幅度的上升,对炼钢工序的脱硫作业带来一定的困难,分析导致铁水含硫升高原因,对稳定降低铁水含硫量、提高铁水质量、满足下道工序要求有重要意义。
1 概述首钢京唐公司1号高炉容积为5500m3,年产铁水近450万t。
近1a来,首钢京唐1号高炉所产铁水含硫情况见表1。
首钢京唐1号高炉所用原燃料为自产高碱度烧结矿、自产酸性球团矿、澳块矿、自产干熄焦和主要由阳泉煤、潞安煤、焦作煤、神华煤按比例混合而成的喷吹煤。
表2为首钢京唐1号高炉所用原燃料的含硫量情况,表3为首钢京唐1号高炉冶炼1t铁水由炉料带入的硫量。
2 铁水含硫上升的原因2.1 原燃料质量恶化铁水中的硫来源于入炉料,炉料含硫的升高,势必会导致(同样脱硫能力情况下)铁水含硫的上升。
近年来,首钢京唐1号高炉入炉原燃料的含硫都趋于上升趋势。
从表3可看出,烧结矿和燃料带入的硫占入炉炉料带入总硫的98%以上,其中入炉焦炭带入的硫占入炉总硫量的78%以上,是硫的主要来源,故焦炭含硫对铁水含硫影响较大。
焦炭带入的硫增加,会明显增加铁水含硫量。
表4为焦炭、煤粉的含硫变化情况。
此外,焦炭灰分高且波动大,矿料成分波动频繁且趋坏,引起热制度、造渣制度的波动,在一定程度上也导致了铁水含硫上升,总的来说,原燃料质量的整体恶化,是首钢京唐高炉铁水含硫升高的重要原因。
2.2 炉渣对铁水含硫的影响在原燃料含硫高的条件下,炉渣脱硫能力是直接影响铁水质量的重要因素之一。
高炉铁水有害元素分析与控制
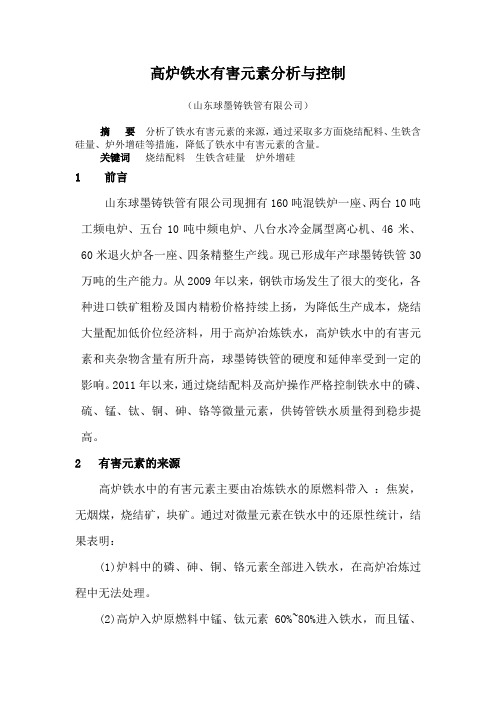
高炉铁水有害元素分析与控制(山东球墨铸铁管有限公司)摘要分析了铁水有害元素的来源,通过采取多方面烧结配料、生铁含硅量、炉外增硅等措施,降低了铁水中有害元素的含量。
关键词烧结配料生铁含硅量炉外增硅1 前言山东球墨铸铁管有限公司现拥有160吨混铁炉一座、两台10吨工频电炉、五台10吨中频电炉、八台水冷金属型离心机、46米、60米退火炉各一座、四条精整生产线。
现已形成年产球墨铸铁管30万吨的生产能力。
从2009年以来,钢铁市场发生了很大的变化,各种进口铁矿粗粉及国内精粉价格持续上扬,为降低生产成本,烧结大量配加低价位经济料,用于高炉冶炼铁水,高炉铁水中的有害元素和夹杂物含量有所升高,球墨铸铁管的硬度和延伸率受到一定的影响。
2011年以来,通过烧结配料及高炉操作严格控制铁水中的磷、硫、锰、钛、铜、砷、铬等微量元素,供铸管铁水质量得到稳步提高。
2 有害元素的来源高炉铁水中的有害元素主要由冶炼铁水的原燃料带入:焦炭,无烟煤,烧结矿,块矿。
通过对微量元素在铁水中的还原性统计,结果表明:(1)炉料中的磷、砷、铜、铬元素全部进入铁水,在高炉冶炼过程中无法处理。
(2)高炉入炉原燃料中锰、钛元素60%~80%进入铁水,而且锰、钛元素在铁水中含量与高炉铁水含硅量呈正相关性关系。
原始生铁含硅量的提高有助于有害元素含量的升高。
3 不同元素对铸铁管的危害供铸管铁水中一些元素达到一定值会对铸铁管的退火产生一定的影响,进而降低对铸铁管的产品质量:磷是铸铁中的常存元素,它对球墨铸铁的机械性能,尤其是冲击韧性和塑性有明显的不良影响,因此总是作为有害元素对待。
其主要原因是共晶团晶界产生的磷共晶脆相,磷共晶呈多角状分布于共晶团边界,急剧恶化球墨铸铁的力学性能,使球墨铸铁韧性下降;其次是磷阻碍珠光体的分解,又能固溶于铁素体中,这些都能降低韧性。
磷的质量分数每增加0.01%时,脆性转变温度升高4.0~4.5℃。
当磷的质量分数超过0.16%时,脆性转变温度已在室温以上,冲击断口出现脆性断裂。
高炉炉料质量与结构对炼铁的影响 许亮

高炉炉料质量与结构对炼铁的影响许亮摘要:炼铁工序的成本控制是否科学、合理将直接影响整个企业的效益和竞争力。
在生铁成本中原、燃料占很大比重,精料和炼铁成本的关系密切。
本文分析了影响入炉原、燃料质量的主要因素及其对高炉炼铁的影响,探讨了当前资源环境条件下比较合理的炉料结构形式。
关键词:高炉炼铁;品位;成分;冶金性能;炉料结构1我国炼铁工业的发展现状(1)重点钢铁企业高炉焦比不断减少。
通常焦炭粉末超过规定的标准会造成高炉炉料透气性能变得更差,压差越来越高,风量不断减少。
因此,在喷射媒粉的时候,必须要严格控制其用量。
并且随着焦炭粉末越来越多,也很有可能被高炉煤气带到高炉外面,导致其除尘灰中含碳量越来越多,这样也就使得焦炭的高炉使用期限缩减,焦比上升;焦炭容易分化,会使得高炉缸内焦炭粒度逐渐变小,甚至会有更多的粉末,这会导致高炉缸是不活跃的,直接造成高炉鼓的风吹不会透过炉缸中心,还会导致高炉缸内灰尘易于堆积;很多小型和中型的高炉使用的焦炭量远远超高。
如果出现高炉休风的情况,就难以使风量立即回复,进而发生延长炉况处理时间的现象。
也曾经发生过某个小高炉全部使用土焦炼铁。
在高炉休风结束后,就会发生不能吹进风的现象。
就是因为焦炭粉化后,缸内每个焦炭之间才不会有足够的孔隙。
(2)重点钢铁企业喷比得到大幅度提升。
优化炼铁系统结构的主要环节是提升高炉喷煤比,这也是全球炼铁技术发展的主流趋势。
高炉喷吹煤粉是减少炼铁成本、节省焦炭的主要策略之一,而且能够优化钢铁工业能源结构,使得全国主焦煤资源紧缺的矛盾得到高效及解决。
尽量以采用喷煤为主,而不是过多的采用焦炭,这样就能够少建立焦炉,以便于不仅减少生产运行费用以及炼铁系统的投资成本,并且减少焦炉生产过程中对环境产生的污染程度,还可以大幅度的提高钢铁企业的核心市场竞争力以及劳动生产率。
(3)重点钢铁企业热风温度不断提升。
重点钢铁企业高炉热风温度的是逐年提升,而且增长幅度很大,促使炼铁焦比的日益下降。
高炉炼铁影响铁水含硫量因素的分析_赵亮

高炉炼铁影响铁水含硫量因素的分析赵亮何志军靳晓勤依卓李远游靳恩东(辽宁科技大学,鞍山 114051)摘要本文运用Minitab进行数学分析某炼铁厂高炉生产数据,确定得出影响高炉铁水硫含量的因素有富氧率、铁水温度、焦炭灰分、铁水硅含量以及风温;同时对铁水硫含量以及其影响因素进行回归分析、方差分析和稳定性分析得出高炉铁水硫含量与其影响因素的关系式为:S%=0.3137-0.00018555T-0.002781X-0.031342Y,其中T为高炉铁水温度,℃;X为富氧率;Y为铁水硅含量。
关键词 Minitab 硫含量高炉冶炼Analysis of Blast Furnace Ironmaking Factors Affecting SulphurContent in Hot MetalZhao Liang He Zhijun Jin Xiaoqin Yi Zhuo Li Yuanyou Jin Endong(University of Science and Technology Liaoning, Anshan, 114051)Abstract This paper mathematically analyzed the production data of the iron blast furnace with Minitab, which indicates that the factors affecting the sulfur content in hot metal are the ratio of oxygen enrichment, the molten iron’s temperature, coke ash, the silicon content of molten iron as well as the blast temperature. At the same time, it carried out regression analysis, variance analysis and stability analysis to investigate the sulfur content in hot metal and its influence factors, from which it can conclude the relation of the sulfur content in blast furnace and its influence factors is as following:℃S%=0.3137-0.00018555T-0.002781X-0.03Si%. The T is for the temperature of the molten iron in blast furnace , and the X is for the ratio of oxygen enrichment.Key words Minitab, sulfur content, blast furnace process1 前言随着世界经济的发展,高新技术的广泛应用,各个行业对钢材质量的要求越来越高。
冲天炉熔炼灰铸铁液压件含硫量的控制

冲天炉熔炼灰铸铁液压件含硫量的控制温远明【摘要】本文主要分析影响冲天炉熔炼灰铸铁硫含量的三个主要因素,将实践与化学理论相结合,进行科学的分析调研.为达到液压用灰铸铁件的组织和性能要求,所有参与反应的物质原料均需要按照一定的比例量加入、浇包内加入等一系列专业性的实验操作.本文会对含硫量数据进行具体估算,最后归纳获得合适硫含量的方法.【期刊名称】《现代制造技术与装备》【年(卷),期】2017(000)008【总页数】2页(P112,115)【关键词】冲天炉;灰铸铁液压件;含硫量控制;熔炼【作者】温远明【作者单位】广西机电职业技术学院,南宁530007【正文语种】中文笔者走访铸造工厂,根据厂里的铸造技术和铸造数据,分析铸造工艺中的硫量数据,计算相应估算公式,从实践数据总结,再将最接近完美的估算数据回归到铸造流水线上,以期为铸造业添砖加瓦。
冲天炉熔炼技术繁琐,变化多端,影响含硫量的因素主要有三个。
1.1 炉料因素炉料中废钢配入量越多,铁水增硫率越高。
原因有二。
一是废钢在一定条件下更容易产生铁水,即使其本身的含硫量较低,但在炉内熔化的位置较低时,结合其自身熔点高的特性,加上废钢中碳、硅含量低而产生化学反应,产生较多Fe0,从而加剧了增硫。
二是铁水中含有碳、硅以及锰等元素。
其中,碳和硅能使Fe0还原,从而有助于炉内进行脱硫反应。
然而,锰作用更大,在其特殊性能下能直接引起脱硫反应。
在锰与FeS发生反应后,产生MnS随即转入渣中。
其中,MnS的熔点极高,高达1500℃,决定其产生的是放热反应。
所以,要达到更好的脱硫作用,可以选择较低的温度环境。
1.2 温度因素炉渣碱度决定着硫的分配指数。
在炉渣含碱度较高的条件下,想降低铁水中的终硫量,必须提高温度才能达到一定的效果。
然而,温度只能到达一定程度,持续升温下,锰的脱硫反应2Mn+S2=2MnS,将不利于锰的脱硫。
在这种特殊情况下,为保证成功脱硫,必须要做到高温条件下出炉,且铁水经一段时间静置方可。
赵倩一丹-炼铁工艺的污染预防与治理
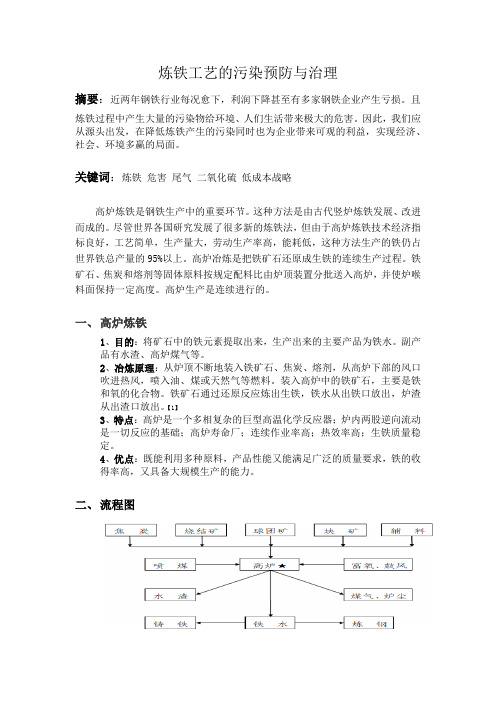
炼铁工艺的污染预防与治理摘要:近两年钢铁行业每况愈下,利润下降甚至有多家钢铁企业产生亏损。
且炼铁过程中产生大量的污染物给环境、人们生活带来极大的危害。
因此,我们应从源头出发,在降低炼铁产生的污染同时也为企业带来可观的利益,实现经济、社会、环境多赢的局面。
关键词:炼铁危害尾气二氧化硫低成本战略高炉炼铁是钢铁生产中的重要环节。
这种方法是由古代竖炉炼铁发展、改进而成的。
尽管世界各国研究发展了很多新的炼铁法,但由于高炉炼铁技术经济指标良好,工艺简单,生产量大,劳动生产率高,能耗低,这种方法生产的铁仍占世界铁总产量的95%以上。
高炉冶炼是把铁矿石还原成生铁的连续生产过程。
铁矿石、焦炭和熔剂等固体原料按规定配料比由炉顶装置分批送入高炉,并使炉喉料面保持一定高度。
高炉生产是连续进行的。
一、高炉炼铁1、目的:将矿石中的铁元素提取出来,生产出来的主要产品为铁水。
副产品有水渣、高炉煤气等。
2、冶炼原理:从炉顶不断地装入铁矿石、焦炭、熔剂,从高炉下部的风口吹进热风,喷入油、煤或天然气等燃料。
装入高炉中的铁矿石,主要是铁和氧的化合物。
铁矿石通过还原反应炼出生铁,铁水从出铁口放出,炉渣从出渣口放出。
【1】3、特点:高炉是一个多相复杂的巨型高温化学反应器;炉内两股逆向流动是一切反应的基础;高炉寿命厂;连续作业率高;热效率高;生铁质量稳定。
4、优点:既能利用多种原料,产品性能又能满足广泛的质量要求,铁的收得率高,又具备大规模生产的能力。
二、流程图高炉炼铁流程图炼铁流程图三、高炉炼铁废弃物高炉炼铁后会产生高炉渣和多种对环境有污染,对人体有危害的气体等多种有害物质。
这些物质产生的同时伴随着大量能源的浪费,因此,对于这些废弃物的回收和利用应加大研究与利用。
在为企业创造价值的同时也给减轻环境自净的负担。
1、高炉渣高炉炉渣是铁矿石中脉石和焦炭中的灰分等与熔剂相互作用生成低熔点的化合物,形成非金属的液相。
高炉渣处理方法分为出干渣和水淬渣。
关于控制好铁水中硫含量的几点建议
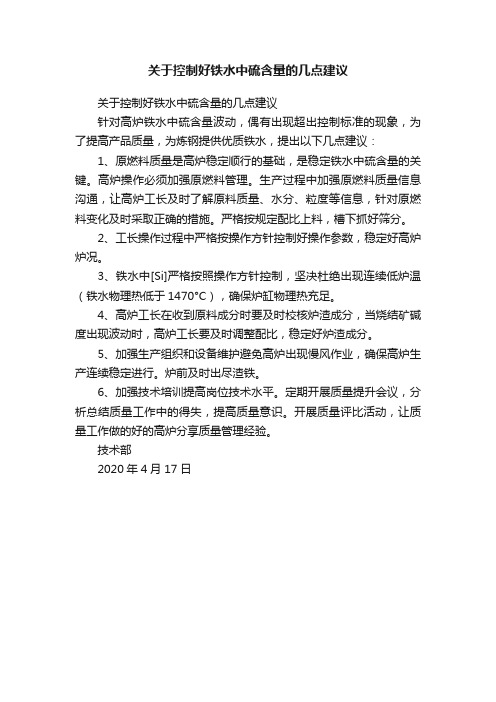
关于控制好铁水中硫含量的几点建议
关于控制好铁水中硫含量的几点建议
针对高炉铁水中硫含量波动,偶有出现超出控制标准的现象,为了提高产品质量,为炼钢提供优质铁水,提出以下几点建议:
1、原燃料质量是高炉稳定顺行的基础,是稳定铁水中硫含量的关键。
高炉操作必须加强原燃料管理。
生产过程中加强原燃料质量信息沟通,让高炉工长及时了解原料质量、水分、粒度等信息,针对原燃料变化及时采取正确的措施。
严格按规定配比上料,槽下抓好筛分。
2、工长操作过程中严格按操作方针控制好操作参数,稳定好高炉炉况。
3、铁水中[Si]严格按照操作方针控制,坚决杜绝出现连续低炉温(铁水物理热低于1470°C),确保炉缸物理热充足。
4、高炉工长在收到原料成分时要及时校核炉渣成分,当烧结矿碱度出现波动时,高炉工长要及时调整配比,稳定好炉渣成分。
5、加强生产组织和设备维护避免高炉出现慢风作业,确保高炉生产连续稳定进行。
炉前及时出尽渣铁。
6、加强技术培训提高岗位技术水平。
定期开展质量提升会议,分析总结质量工作中的得失,提高质量意识。
开展质量评比活动,让质量工作做的好的高炉分享质量管理经验。
技术部
2020年4月17日。
铁水运输时硫含量的变化
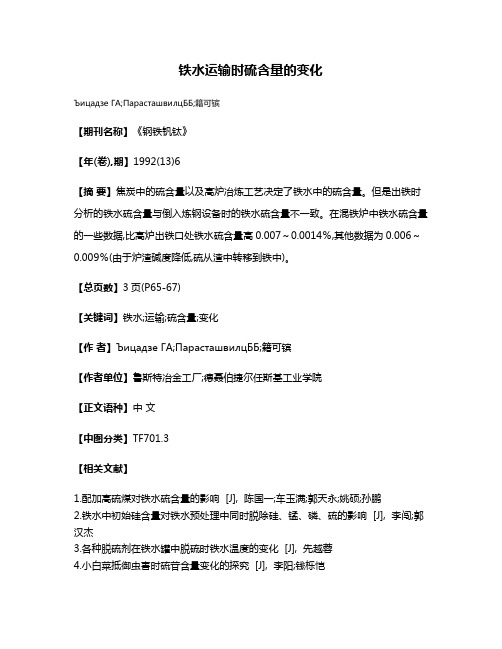
铁水运输时硫含量的变化
Ъицадзе ГА;ПарасташвилцББ;籍可镔
【期刊名称】《钢铁钒钛》
【年(卷),期】1992(13)6
【摘要】焦炭中的硫含量以及高炉冶炼工艺决定了铁水中的硫含量。
但是出铁时分析的铁水硫含量与倒入炼钢设备时的铁水硫含量不一致。
在混铁炉中铁水硫含量的一些数据,比高炉出铁口处铁水硫含量高0.007~0.0014%,其他数据为0.006~0.009%(由于炉渣碱度降低,硫从渣中转移到铁中)。
【总页数】3页(P65-67)
【关键词】铁水;运输;硫含量;变化
【作者】Ъицадзе ГА;ПарасташвилцББ;籍可镔
【作者单位】鲁斯特冶金工厂;德聂伯捷尔任斯基工业学院
【正文语种】中文
【中图分类】TF701.3
【相关文献】
1.配加高硫煤对铁水硫含量的影响 [J], 陈国一;车玉满;郭天永;姚硕;孙鹏
2.铁水中初始硅含量对铁水预处理中同时脱除硅、锰、磷、硫的影响 [J], 李闯;郭汉杰
3.各种脱硫剂在铁水罐中脱硫时铁水温度的变化 [J], 先越蓉
4.小白菜抵御虫害时硫苷含量变化的探究 [J], 李阳;钱栎恺
因版权原因,仅展示原文概要,查看原文内容请购买。
铁钢界面铁水成分差异分析
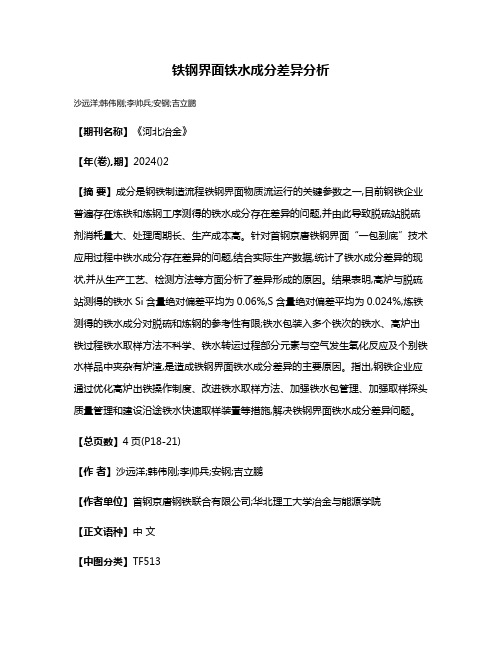
铁钢界面铁水成分差异分析
沙远洋;韩伟刚;李帅兵;安钢;吉立鹏
【期刊名称】《河北冶金》
【年(卷),期】2024()2
【摘要】成分是钢铁制造流程铁钢界面物质流运行的关键参数之一,目前钢铁企业普遍存在炼铁和炼钢工序测得的铁水成分存在差异的问题,并由此导致脱硫站脱硫剂消耗量大、处理周期长、生产成本高。
针对首钢京唐铁钢界面“一包到底”技术应用过程中铁水成分存在差异的问题,结合实际生产数据,统计了铁水成分差异的现状,并从生产工艺、检测方法等方面分析了差异形成的原因。
结果表明,高炉与脱硫站测得的铁水Si含量绝对偏差平均为0.06%,S含量绝对偏差平均为0.024%,炼铁测得的铁水成分对脱硫和炼钢的参考性有限;铁水包装入多个铁次的铁水、高炉出铁过程铁水取样方法不科学、铁水转运过程部分元素与空气发生氧化反应及个别铁水样品中夹杂有炉渣,是造成铁钢界面铁水成分差异的主要原因。
指出,钢铁企业应通过优化高炉出铁操作制度、改进铁水取样方法、加强铁水包管理、加强取样探头质量管理和建设沿途铁水快速取样装置等措施,解决铁钢界面铁水成分差异问题。
【总页数】4页(P18-21)
【作者】沙远洋;韩伟刚;李帅兵;安钢;吉立鹏
【作者单位】首钢京唐钢铁联合有限公司;华北理工大学冶金与能源学院
【正文语种】中文
【中图分类】TF513
【相关文献】
1.大型高炉转炉铁钢界面铁水温降分析
2.GA-BP的铁钢界面铁水温度预测
3.铁钢工序界面铁水温降预测系统的开发与应用
4.数智赋能“铁-钢界面”——铁水智能调度系统研究
5.铁钢界面铁水温降行为的研究现状
因版权原因,仅展示原文概要,查看原文内容请购买。
- 1、下载文档前请自行甄别文档内容的完整性,平台不提供额外的编辑、内容补充、找答案等附加服务。
- 2、"仅部分预览"的文档,不可在线预览部分如存在完整性等问题,可反馈申请退款(可完整预览的文档不适用该条件!)。
- 3、如文档侵犯您的权益,请联系客服反馈,我们会尽快为您处理(人工客服工作时间:9:00-18:30)。
高炉炼铁影响铁水含硫量因素的分析
赵亮何志军靳晓勤依卓李远游靳恩东
(辽宁科技大学,鞍山 114051)
摘要本文运用Minitab进行数学分析某炼铁厂高炉生产数据,确定得出影响高炉铁水硫含量的因素有富氧率、铁水温度、焦炭灰分、铁水硅含量以及风温;同时对铁水硫含量以及其影响因素进行回归分析、方差分析和稳定性分析得出高炉铁水硫含量与其影响因素的关系式为:S%=0.3137-0.00018555T-0.002781X-0.031342Y,其中T为高炉铁水温度,℃;X为富氧率;Y为铁水硅含量。
关键词 Minitab 硫含量高炉冶炼
Analysis of Blast Furnace Ironmaking Factors Affecting Sulphur
Content in Hot Metal
Zhao Liang He Zhijun Jin Xiaoqin Yi Zhuo Li Yuanyou Jin Endong
(University of Science and Technology Liaoning, Anshan, 114051)
Abstract This paper mathematically analyzed the production data of the iron blast furnace with Minitab, which indicates that the factors affecting the sulfur content in hot metal are the ratio of oxygen enrichment, the molten iron’s temperature, coke ash, the silicon content of molten iron as well as the blast temperature. At the same time, it carried out regression analysis, variance analysis and stability analysis to investigate the sulfur content in hot metal and its influence factors, from which it can conclude the relation of the sulfur content in blast furnace and its influence factors is as following:
℃S%=0.3137-0.00018555T-0.002781X-0.03Si%. The T is for the temperature of the molten iron in blast furnace , and the X is for the ratio of oxygen enrichment.
Key words Minitab, sulfur content, blast furnace process
1 前言
随着世界经济的发展,高新技术的广泛应用,各个行业对钢材质量的要求越来越高。
一般地说,市场要求钢材具有强度高、低温韧性好、冷成型性能和焊接性能良好等特性。
硫是钢铁产品中的一种有害元素,它对钢的性能存在多方面的影响。
从冶炼角度考虑,要求每道工序都要尽可能地降低产品中的硫含量,从而达到降低成本,增加效益的目的,而高炉炼铁中,无论从动力学还是热力学来讲都有利于硫的脱除。
因此在目前形势下,对高炉炼铁这一工序而言,怎样降低铁水中硫含量是一项重要的课题。
高炉铁水的脱硫是整个钢铁生产中最重要的脱硫环节,也是冶炼优质生铁的首要问题。
所以探究高炉生产因素对高炉铁水硫含量的影响规律就显得尤为重要。
经过相关分析和高炉操作者的经验得到在高炉生产诸多影响因素中铁水硅含量、铁水温度、富氧率、焦炭灰分以及风温对铁水硫含量影响较大,其中硅含量可以影响到硫的活度,使硫可以更辽宁省教育厅基金(L2011041)和辽宁科技大学重点基金(2012CX05)。
赵亮,男,硕士,从事钢铁冶金研究工作,934063251@
好的参与反应,达到脱除的目的;铁水温度影响脱硫的热力学条件,温度高有利于硫的脱除;富氧率的高低影响脱硫的氧化性气氛,氧分压高有利于硫的脱除。
研究这些因素对铁水硫含量的影响规律对高炉生产品质优良铁水以及铁水在后续炼钢降低硫含量方面有指导性的意义。
Minitab软件具有数据分析、数据处理功能,其中包括单因素或多元回归分析、时间序列分析、各种统计模型、神经网络模型等[1]。
利用Minitab数学方法处理高炉生产数据并判定高炉铁水硫含量以及其影响因素的稳定性,从而帮助我们判定高炉生产是否稳定,对实际生产具有指导性的意义。
2实验方法
2.1 影响硫含量因素的确定
从原材料质量、入炉控制、炉内参数、送风操作等方面入手,选取所有可能影响铁水硫含量的因素,由相关性分析、高炉操作者以及大量查阅文献的基础上确定了铁水硫含量的因素有:铁水硅含量、铁水温度、富氧率、风温以及焦炭灰分[2]。
图1为相关分析模型。
图1 铁水硫含量与其影响因素的散点图.
由图1可以得出铁水硫含量随铁水硅含量、铁水温度以及富氧率的升高而降低;随风温和焦炭灰分的升高而升高。
由图可以得出高炉生产中为了达到降低铁水硫含量的目的,可以通过适度增加Si的含量,提高铁水温度,提高富氧率,降低焦炭灰分等手段达到。
二月份散点图富氧率的增加S%降低的不是很明显。
2.2硫含量与其影响因素的回归分析
运用Minitab对铁水硫含量以及它的影响因素进行回归分析,其中自变量风温、焦炭灰分的p值都远远大于0.05,故这两个自变量删除。
表1、表2为回归和方差分析数据。
由方差分析知道P=0.000<0.05,则以上数据有显著的效果,又R-Sq = 66.4% R-Sq(调整)= 62.6%(R-Sq、R-Sq(调整)较大且相近),证明保留这几个变量效果是不错的。
所以得到模型:
=−−−
S T X Y
%0.31370.000185550.0027810.031342
式中T——高炉铁水温度,℃;
X——富氧率;
Y——铁水硅含量。
对硫含量进行残差图分析。
图2为铁水硫含量的四合一残差图以及残差与自变量图。
表1回归分析
自变量系数系数标准误差T P 常量0.3137 0.1068 2.94 0.007 铁水温度−0.00018555 0.00007499 −2.47 0.020
富氧率−0.002781 0.001535 −1.81 0.021
Si% −0.031342 0.008810 −3.56 0.001
表2方差分析
来源自由度SS MS F P
0.00018931 17.76 0.000
回归 3 0.00056792
0.00001066
残差误差27 0.00028776
合计30 0.00085568
图2 残差图以及残差与自变量图
图3 S%的Xbar-R图
首先从概率图可以得出,全部数据点基本在一条直线上,即可以认为残差服从正态分布,残差的直方图也显示了残差的正态性;拟合值,此图正常未见喇叭口形状分布,说明线性模型是可以接受的;数据顺序图正常,没有形成U或倒U的形状,残差对于观测值顺序随机分布。
2.3铁水硫含量的稳定分析
通过Minitab做S%的Xbar-R图,其中将数据分为10组,组容为3。
图3为S%的Xbar-R图。
首先从R图得出一月份极差稳定,没有超出控制线,极差值总体水平波动很小,从X图得出,硫含量稳定在控制线以内,整体水平波动较小,一月份均值控制在为0.02155;二月份极差稳定,没有超过控制线,均值控制在0.02154;一月份、二月份均值相差不大,平均值为0.021545。
由此可见铁水含硫量的高低与富氧率、铁水温度、铁水硅含量等因素是分不开的。
3结语
通过Minitab软件对某炼铁厂高炉高炉生产数据分析得出了以下结论:
(1)影响铁水含硫量的主要因素有富氧率、铁水温度、焦炭灰分、铁水硅含量以及风温。
(2)通过回归分析后得到铁水硫含量与富氧率、铁水温度、铁水贵含量的关系式:S%=0.3137-0.00018555T-0.002781X-0.03Y,其中T为高炉铁水温度,℃;X为富氧率;Y为铁水硅含量。
并且硫含量在控制范围之内,平均值为0.021545。
参考文献
[1] 徐光冰,高齐圣. Minitab在可靠性数据分析中的应用[J]. 电子质量. 2006-12, (20), 1: 1~2.
[2] 俞晓林. 降低高炉铁水硫含量的措施分析[J]. 浙江冶金, 2005, (3): 2~3.。