金属挤压液压机
锻造设备类别和名称

机
10000 吨以上的有采用契式,我国可பைடு நூலகம்以生产公称力 160MN 以下,质量和 可靠性需要提升。 冷锻压力机 曲柄压力机、楔式压力机、偏心 压力机、肘杆式压力机、多 ( 2/3/4) 工位冷锻压力机、单点 压力机、双点压力机 温锻压力机 曲柄压力机、楔式压力机、偏心 压力机、肘杆式压力机、多 ( 2/3/4) 工位温锻压力机、单点 压力机、双点压力机 冷温锻压力机 曲柄压力机、楔式压力机、偏心 压力机、肘杆式压力机、多 ( 2/3/4) 工位冷温锻压力机、单 点压力机、双点压力机 平锻机 结构类是于热模锻压力机, 但有其特 殊性,刚性、偏载能力、速度等都与 热模锻不同, 国内目前能生产公称力 16MN 以下,但多工位仍然不能生 产。大吨位质量和可靠性差。 与冷锻压力机情况差不多, 国内目前 能生产公称力 10MN 以下, 但多工位 仍然不能生产。 大吨位质量和可靠性 差。 与冷锻压力机情况差不多, 国内目前 能生产公称力 10MN 以下, 但多工位 仍然不能生产。 大吨位质量和可靠性 差。
鳄式平锻机、水平分模平锻机、 结构有鳄式、肘杆式、公称力 20MN 立式分模平锻机、 肘杆式水平分 模平锻机 的鳄式平锻机国内可以提供。 肘杆式 平锻机的垂直打击力较大, 可以进行 复合成形。 当前不再使用立式分模的 平锻机,因为难于实现自动化, 也难 于提升合模打击功能。
挤压压力机
冷(温)挤压机、机械式冷(温) 机械式传动的压力机多是偏心压力 挤压机 机或肘杆压力机, 这种压力机的特点 是形成要求长,也就是压力角大,目 前国内可以生产公称力 12MN 以下 的机械式挤压机。
锻造设备类别和名称
类别 名称 俗称 或其它名称 (锻造)水压机、 (锻造)油压 自由锻液压机 机、快锻机(快速锻造液压机) 、 快锻水压机 简单解释 动力介质有油和水之分;结构有 3 梁 4 柱和 2 柱之分, 单杠和多缸之分; 运动有上压和下拉之分; 国内可以生 产各种规格,只是质量有所差距。 动力介质有油和水之分, 当前以油为 主; 有三梁四柱结构, 也有框架结构, 根据功能, 也就是生产应用的领域不 同,产品不同,有各种类型,如:管 模锻液压机 水压机、油压机 道模锻液压机。 模锻液压机国内基本 能生产各种规格, 可能有一些特种用 途的模锻液压机还不能生产。 当然国 产模锻液压机的可靠性、 精度等与国 外有差距。 小型模锻液压机可以实现 精密锻造或模锻和挤压复合成形。 模锻液压机增加有横向加力系统 (当 多向模锻液压机 液 压 机 等温锻造液压机 等温成形液压机、 多向模锻水压机、 多向模锻液压 机、多向液压机 然不是简单的添加) ,全部规格,国 内多多向模锻工艺不过关,市场有 限。 模锻范畴, 在锻造过程中要实现零件 等温成形机、等温锻造压力机、 加热,国内可以生产公称力 250MN 以下;等温锻速度 0.005~0.5mm/s; 模锻速度 0.5~10mm/s, 其它在攻关。 立式的结构和动力介质类似于模锻, 但挤压要求能持续给能,挤压速度 黑色金属液压挤压机 150 毫米/秒以下国内可以制造。 卧式 黑色挤压机较少。 有的立式挤压机主 要用于生产长轴类或套筒类零件。 结构有立式和卧式之区别, 立式挤压 金属挤压液压机 轻合金液压挤压机 速度 10 毫米/秒以上设备可以制造, 卧室主要用于型材生产, 少加工功能 零部件。 类似于轻合金液压挤压机, 主要用于 原材料坯料制备, 也有直接成形功能 铜合金挤压机、钛合金挤压机 部件的。也生产结构件用型材, 铜合 金挤压机也用于装饰型材挤压, 国内 可以制造各规格。 机 械 压 力 热模锻压力机 曲柄压力机、楔式压力机、偏心 压力机、肘杆式压力机 机械压力机主要有偏心轴、曲轴连 杆、契式、肘杆式结构,1000 吨以 下多为曲轴连杆火肘杆结构, 1000 吨- 10000 吨之间的多为偏心轴,
3150KN专用液压机的液压系统设
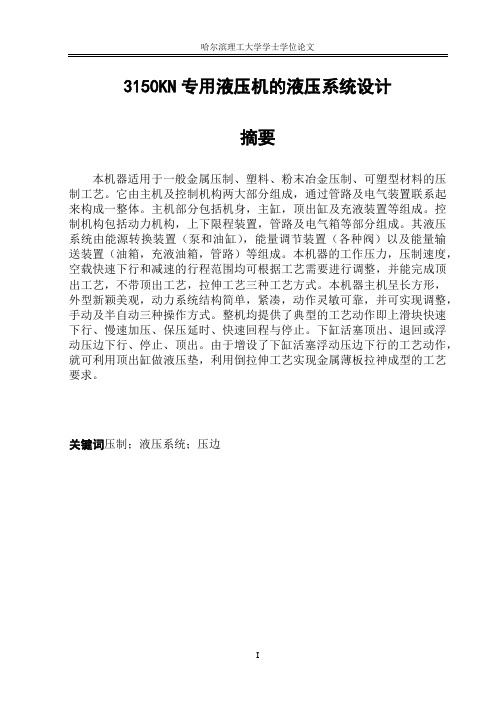
3150KN专用液压机的液压系统设计摘要本机器适用于一般金属压制、塑料、粉末冶金压制、可塑型材料的压制工艺。
它由主机及控制机构两大部分组成,通过管路及电气装置联系起来构成一整体。
主机部分包括机身,主缸,顶出缸及充液装置等组成。
控制机构包括动力机构,上下限程装置,管路及电气箱等部分组成。
其液压系统由能源转换装置(泵和油缸),能量调节装置(各种阀)以及能量输送装置(油箱,充液油箱,管路)等组成。
本机器的工作压力,压制速度,空载快速下行和减速的行程范围均可根据工艺需要进行调整,并能完成顶出工艺,不带顶出工艺,拉伸工艺三种工艺方式。
本机器主机呈长方形,外型新颖美观,动力系统结构简单,紧凑,动作灵敏可靠,并可实现调整,手动及半自动三种操作方式。
整机均提供了典型的工艺动作即上滑块快速下行、慢速加压、保压延时、快速回程与停止。
下缸活塞顶出、退回或浮动压边下行、停止、顶出。
由于增设了下缸活塞浮动压边下行的工艺动作,就可利用顶出缸做液压垫,利用倒拉伸工艺实现金属薄板拉神成型的工艺要求。
关键词压制;液压系统;压边3150KN Special Hydraulic Machine HydraulicSystem DesignAbstractThe machinery for general suppression of metal plastic, powder metallurgy suppression, plastic materials can suppress the process. It consists of host and control most of the two institutions, through pipelines and installations linked to constitute a whole. Including the host part of the fuselage, the main tank, a tank top and liquid-filled devices, and other components. Control agencies, including force, the maximum and minimum levels-devices, pipes and electrical boxes and other components. Its hydraulic system by the energy conversion devices (pumps and fuel tanks), energy-conditioning (all valve) and energy transmission devices (fuel tank, liquid-filled tank, piping) composed. The machines work pressure, the suppression of speed, no-load fast and slow down the scope of the itinerary can be adjusted in accordance with the need for technology and top-out process can be completed, without a roof process, drawing process of three ways. The host was rectangular machines, new aesthetic appearance, the power system used cartridge valve, the structure is simple, compact, sensitive and reliable action, and to achieve adjustment, the three semi-automatic and manual mode of operation.offer of a typical action that is rapidly descending on the slider, slow pressure, Bao calendar, with the rapid return to stop. The cylinder piston to the top, back-pressure or floating down, stop, to the top. As provided under the pressure cylinder piston floating down the side of action, we can make use of hydraulic cylinders to the top pad, using inverted drawing process to achieve sheet metal forming the pull of God demands.Keywords suppressed; hydraulic system; Pressure目录摘要 (I)Abstract (II)第1章绪论 (1)1.1背景 (1)1.2国内外液压机技术发展状况及发展趋势 (1)1.2.1国内外液压机发展状况 (2)1.2.2液压机技术发展趋势 (2)1.2.3国内外液压机的类型 (2)1.3研究的意义 (3)1.4问题的提出和研究的内容 (4)1.4.1问题的提出 (4)1.4.2液压系统设计的步骤 (4)第2章液压系统设计 (6)2.1概述 (6)2.1.1液压传动系统的主要组成 (6)2.1.2液压机的结构形式和工艺方式 (6)2.2明确工作要求,进行工况分析 (7)2.2.1结构概述 (7)2.2.2工作情况 (8)2.2.3 设计参数 (9)2.2.4 负载分析及绘制负载图和速度图 (9)2.3拟订液压系统原理图 (10)2.3.1系统原理图的设计步骤 (11)2.3.2液压系统原理图的问题 (13)2.3.3液压系统的工作原理 (13)2.4液压件的计算与选择 (16)2.4.1 确定缸的有效面积 (16)2.4.2 绘制工况图........................................................ 错误!未定义书签。
液压机安全技术要求

安装稳固性
液压机底座牢固稳定,螺丝和密封垫圈等配件齐全。
12
操作人员培训
操作人员需接受岗前培训,熟悉液压机工作原理、操作流程和安全标准。
13
全面掌握机械性能
操作人员需全面掌握液压机的性能参数,包括稳定性、负载承担能力、压力、流量等。
14
安全防护措施
安装防护罩、紧急停止按钮、拉锁等安全防护设备。
15
4
安全装置功能
滑块运行中,操作者身体任何部分不得进入或停留在工作危险区;意外进入时,滑块应立即停止运行;或手放开操作按钮后,在危险前能停止滑块运行。
5
安全保护控制装置
装有行程转换开关的液压机,除寸动工作规范外,其他动作规范需具备上述安全装置功能之一;可选双手起动式、非接触式等安全保护控制装置。
6
固定栅栏式安全保护装置
液压机安全技术要求
序号
安全技术要求
详细说明
1
设备结构与设计安全
液压机应在设计结构、零部件的强度方面符合安全要求;噪声应符合有关标准规定。
2
主机与附属装置安全
主机及其操纵装置、附属装置所构成的外形和布局均应符合安全要求。
3
安全保护装置
专用液压机(如金属挤压、模膛挤压、高速冲裁等)需采取防碎或防热辐射的护罩、板等安全保护装置;通用工艺性液压机需根据具体安全要求配制安全装置。
开口大小防止手进入工作危险区;栅栏关闭后才能进行工作;滑块运行中不能打开栅栏;需采用平衡装置避免操作者疲劳。
7
双手起动式安全装置
单次操作时,需双手同时操作;中断工作后,需按规定操作才能恢复;单次操作完成滑块自动停止;两按钮间距300mm~600mm;多人操作时,需为每个操作者提供装置。
《液压挤压机的本体结构》课件
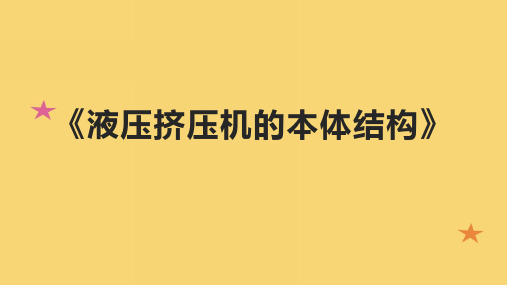
挤压速度:
穿孔速度:铝及合金75-100,铜及合金100-250mm/s 空程:250-350mm/s 回程速度:100-400mm/s
9. 生产能力
小时生产能力:Cs
3600 A
tg t f
Ld
l
Cn Cs T
k
Tt
l
Tx
年产量:
《液压挤压机的本体结构》
1. 挤压力
挤压轴挤出金属所必需的力 别尔林公式:
F F0 F1 F2 F3
抗力 挤压筒 变形区 定径区
卧式挤压机挤压力:3.15~250MN; 立式挤压机挤压力:6~20MN,最大300MN;
2. 液压系统的工作压力
一般介于20~32MPa;
3.
主缸系统参数
主柱塞直径:
6 模座系统
装置模具的部件,承受和传递挤压力
纵向移动模座
0.10)F(接触面上压力要大于工作压力)
松开力:Fts (1.2 1.5)Fty (前梁), Fts (0.6 0.8)Fty(后梁)
内 置 穿 孔 系 统 外 置 穿 孔 系 统
6. 主剪力,辅助剪力
制品与压余分离(0.03F),垫片与压余分离(0.015F)
机架系统
挤
动梁系统
压
主缸系统
机 本
挤压筒系统
体
穿孔系统
模座系统
挤
压余分离装置
压
挤压牵引机构
机
辅
料台与冷床
助 系
剪切装置
统
加热炉
挤压工具
模具,挤压轴, 穿孔针,垫片等
挤压机结构示意图
● 1 机架系统
铝型材挤压机液压系统原理
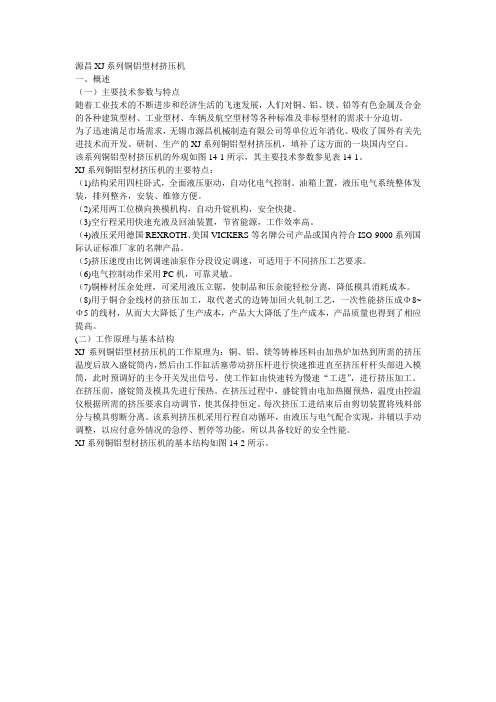
源昌XJ系列铜铝型材挤压机一、概述(一)主要技术参数与特点随着工业技术的不断进步和经济生活的飞速发展,人们对铜、铝、镁、铅等有色金属及合金的各种建筑型材、工业型材、车辆及航空型材等各种标准及非标型材的需求十分迫切。
为了迅速满足市场需求,无锡市源昌机械制造有限公司等单位近年消化、吸收了国外有关先进技术而开发、研制、生产的XJ系列铜铝型材挤压机,填补了这方面的一块国内空白。
该系列铜铝型材挤压机的外观如图14-1所示,其主要技术参数参见表14-1。
XJ系列铜铝型材挤压机的主要特点:(1)结构采用四柱卧式,全面液压驱动,自动化电气控制。
油箱上置,液压电气系统整体发装,排列整齐,安装、维修方便。
(2)采用两工位横向换模机构,自动升锭机构,安全快捷。
(3)空行程采用快速充液及回油装置,节省能源,工作效率高。
(4)液压采用德国REXROTH、美国VICKERS等名牌公司产品或国内符合ISO-9000系列国际认证标准厂家的名牌产品。
(5)挤压速度由比例调速油泵作分段设定调速,可适用于不同挤压工艺要求。
(6)电气控制动作采用PC机,可靠灵敏。
(7)铜棒材压余处理,可采用液压立锯,使制品和压余能轻松分离,降低模具消耗成本。
(8)用于铜合金线材的挤压加工,取代老式的边铸加回火轧制工艺,一次性能挤压成Φ8~Φ5的线材,从而大大降低了生产成本,产品大大降低了生产成本,产品质量也得到了相应提高。
(二)工作原理与基本结构XJ系列铜铝型材挤压机的工作原理为:铜、铝、镁等铸棒坯料由加热炉加热到所需的挤压温度后放入盛锭筒内,然后由工作缸活塞带动挤压杆进行快速推进直至挤压杆杆头部进入模筒,此时预调好的主令开关发出信号,使工作缸由快速转为慢速“工进”,进行挤压加工。
在挤压前,盛锭筒及模具先进行预热。
在挤压过程中,盛锭筒由电加热圈预热,温度由控温仪根据所需的挤压要求自动调节,使其保持恒定。
每次挤压工进结束后由剪切装置将残料部分与模具剪断分离。
锻压工艺标准你了解多少?赶快收藏吧!

锻压工艺标准你了解多少?赶快收藏吧!现行标准109个,其中国家标准56个,机械行业标准53个(2008年批准发布)。
现行标准109个,其中国家标准56个,机械行业标准53个(2008年批准发布)。
1.锻造、安全、能耗、环保等方面标准锻造GB/T8541-1997锻压术语GB/T9453-2008锻模术语GB/T12361-2003钢质模锻件通用技术条件GB/T12362-2003钢质模锻件公差及机械加工余量GB/T12363-2005锻件功能分类GB/T13320-2007钢质模锻件金相组织评级图及评定方法GB/T20078-2006铜和铜合金锻件GB/T20911-2007锻造用半成品尺寸、形状和质量公差GB/T21469-2008锤上钢质自由锻件机械加工余量与公差一般要求GB/T21470-2008锤上钢质自由锻件机械加工余量与公差盘、柱、环、筒类GB/T21471-2008锤上钢质自由锻件机械加工余量与公差轴类GB/T22131-2008筒形锻件内表面超声波检测方法JB/T4201-1999直齿锥齿轮精密热锻件技术条件JB/T4202-1999钢的锻造余热淬火回火处理JB/T4290-1999高速工具钢锻件技术条件JB/T4385.1-1999锤上自由锻件通用技术条件JB/T4385.2-1999锤上自由锻件复杂程度分类及折合系数JB/T7535-1994锻造工艺质量控制规范JB/T8421-1996钢质自由锻件检验通用规则JB/T8466-1996锻钢件液体渗透检验方法JB/T8467-1996锻钢件超声波探伤方法JB/T8468-1996锻钢件磁粉检验方法:JB/T9174-1999模锻件材料消耗工艺定额编制方法JB/T9177-1999钢质模锻件结构要素JB/T9178.1-1999水压机上自由锻件通用技术条件JB/T9178.2-1999水压机上自由锻件复杂程度分类及折合系数JB/T9179.1-1999水压机上自由锻件机械加工余量与公差一般要求JB/T9179.2-1999水压机上自由锻件机械加工余量与公差圆轴、方轴和矩形截面类JB/T9179.3-1999水压机上自由锻件机械加工余量与公差台阶轴类JB/T9179.4-1999水压机上自由锻件机械加工余量与公差圆盘和冲孔类JB/T9179.5-1999水压机上自由锻件机械加工余量与公差短圆柱类JB/T9179.6-1999水压机上自由锻件机械加工余量与公差模块类JB/T9179.7-1999水压机上自由锻件机械加工余量与公差筒体类JB/T9179.8-1999水压机上自由锻件机械加工余量与公差圆环类JB/T9181-1999直齿锥齿轮精密热锻件结构设计规范安全、环保、能耗JB/T10138-1999渗碳轴承钢锻件安全、能耗、环保GB5083-1999生产设备安全卫生设计总则GB/T8176-1997冲压车间安全生产通则GB12265.1一1997机械安全防止上肢触及危险区的安全距离GB12265.2-2000机械安全防止下肢触及危险区的安全距离GB12265.3-1997机械安全避免人体各部位挤压的最小间距GB/T12801-2008生产过程安全卫生要求总则GB13318-2003锻造生产安全与环保通则GB13887-2008冷冲压安全规程GB/T15319-1994火焰加热炉节能监测方法OB/T19670-2005机械安全防止意外启动JB/T5992.3-1992机械制造工艺方法分类与代码压力加工JB/T50153-1999锻造加热炉能耗分等2. 冲压、金属压力变形试验方法、大型锻件等方面标准冲压GB/T 8845 2006 冲模术语GB/T 13914-2002 冲压件尺寸公差GB/T 13915-2002 冲压件角度公差GB/T 13916-2002 冲压件形状和位置未注公差GB/T 15055-2007 冲压件未注公差尺寸极限偏差GB/T 15825.1-2008 金属薄板成形性能与试验方法第1部分:成形性能和指标GB/T 15825.2-2008 金属薄板成形性能与试验方法第2部分:通用试验规程GB/T 15825.3-2008 金属薄板成形性能与试验方法第3部分:拉深与拉深载荷试验GB/T 15825.4 2008 金属薄板成形性能与试验方法第4部分:扩孔试验GB/T 15825.5-2008 金属薄板成形性能与试验方法第5部分:弯曲试验GB/T 15825.6-2008 金属薄板成形性能与试验方法第6部分:锥杯试验GB/T 15825.7 2008 金属薄板成形性能与试验方法第7部分:凸耳试验GB/T 15825.8 2008 金属薄板成形性能与试验方法第8部分:成形极限图(F1D)测定指南GB/T 16743-1997 冲裁间隙JB/T 4129-1999 冲压件毛刺高度JB/T 4378.1 1999 金属冷冲压件结构要素JB/T 4378.2-1999 金属冷冲压件通用技术条件JB/T 4381-1999 冲压剪切下料未注公差尺寸的极限偏差JB/T 5109-2001 金属板料压弯工艺设计规范JB/T 6054 2001 冷挤压件工艺编制原则JB/T 6058-1992 冲模用钢及其热处理技术条件JB/T 6959 1993 金属板料拉深工艺设计规范JB/T 8930-1999 冲压工艺质量控制规范JB/T 9175.1-1999 精密冲裁件结构工艺性JB/T 9175.2 1999 精密冲裁件质量JB/T 9176-1999 冲压件材料消耗工艺定额编制方法JB/T 9180.1 1999 钢质冷挤压件公差JB/T 9180.2 1999 钢质冷挤压件通用技术条件金属压力变形试验方法GB/T 228-2002 金属材料室温拉伸试验方法GB/T 229-2007 金属材料夏比摆锤冲击试验方法GB/T 232-1999 金属材料弯曲试验方法GB/T 235-1999 金属材料厚度等于或小于3 mm薄板和薄带反复弯曲试验方法GB/T 238-2002 金属材料线材反复弯曲试验方法GB/T 239-1999 金属线材扭转试验方法GB/T 241-2007 金属管液压试验方法GB/T 242-2007 金属管扩口试验方法GB/T 244-2008 金属管弯曲试验方法GB/T 245-2008 金属管卷边试验方法GB/T 246-2007 金属管压扁试验方法GB/T 2039-1997 金属拉伸蠕变及持泵试验方法GB/T 4156-2007 金属材料薄板和薄带埃里克森杯突试验GB/T 4337-2008 金属材料疲劳试验旋转弯曲方法GB/T 4338-2006 金属材料高温拉伸试验方法GB/T 5027-2007 金属材料薄板和薄带塑性应变比(r值)的测定GB/T 5028-1999 金属薄板和薄带拉伸应变硬化指数(n值)试验方法GB/T 7314-2005 金属材料室温压缩试验方法GB/T 10128-2007 金属材料室温扭转试验方法GB/T 13239-2006 金属材料低温拉伸试验方法大型锻件JB/T 6393-1992 大型锻件用合金工具钢JB/T 6394-1992 大型锻件用碳素工具钢JB/T 6395-1992 大型齿轮、齿圈锻件JB/T 6979-1993 大中型钢质锻制模块(超声波和夹杂物)质量分级JB/T 7032-2001 大型全纤维曲轴锻件JB/T 8705-1998 50MW以下汽轮发电机无中心孔转子锻件技术条件JB/T 8706-1998 50~200MW汽轮发电机无中心孔转子锻件技术条件JB/T 8707-1998 300MW以上汽轮机无中心孔转子锻件技术条件JB/T 8708-1998 300 600MW汽轮发电机无中心孔转子锻件技术条件JB/T 8888-1999 环芯法测量汽轮机、汽轮发电机转子锻件残余应力的试验方法JB/T 9020-1999 大型锻造曲轴的超声波检验JB/T 9021-1999 汽轮机主轴和转子锻件的热稳定性试验方法JB/T 10265 2001 水轮发电机用上下圆盘锻件技术条件锻压机械标准现行国家标准和行业标准116个(2009年批准发布)。
国内外大型铝挤压机的技术现状
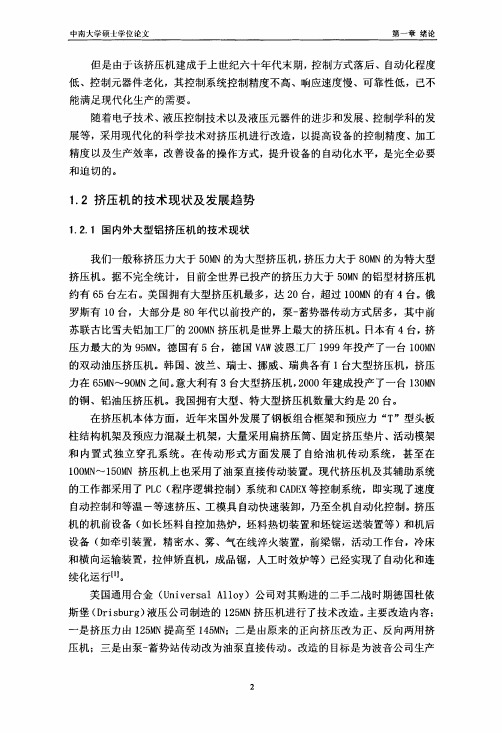
75MN铝挤压机机后区分成三个相对独立的控制区,采用三台PLC对其进行 控制,可独立工作,互不依赖,同时应用网络技术将PLC联网,实现集中监督、
管理。PLC选用高可靠性的SIMATIC S7系列产品,配置为1套S7—400PLC、2套
4
中南大学硕士学位论文
第一章绪论
S7—300PLC以及分布式i/o和人机界面TDl7、0P27,通过PROFIBUS-DP网络连接
中南大学硕士学位论文
第一章绪论
但是由于该挤压机建成于上世纪六十年代末期,控制方式落后、自动化程度 低、控制元器件老化,其控制系统控制精度不高、响应速度慢、可靠性低,已不 能满足现代化生产的需要。
随着电子技术、液压控制技术以及液压元器件的进步和发展、控制学科的发
展等,采用现代化的科学技术对挤压机进行改造,以提高设备的控制精度、加工 精度以及生产效率,改善设备的操作方式,提升设备的自动化水平,是完全必要
中间主缸的柱塞直径达2m,为确保高速空程前进的缸内充液和回程时大流 量的排液,要避免主缸吸空,西重所自行开发设计了国内卧式液压机最大口径 DN400的充液阀【9】’在主缸后部三只并联使用【10】。 125MN挤压机选用预卸压阀和比例溢流阀两种卸压元件来实现挤压机的卸
压。通过电控系统控制的比例溢流阀在卸压初始阶段有良好的卸压性能,但当压
中南大学硕士学位论文
第一章绪论
按3s卸压时间计算,瞬时排出的流量高达3600L/min,相当于7台500L/min流
量的大泵在同时排放,容易产生大的振动,给系统造成大的危害的情况,应用了
西重所的专利技术“带阻尼卸压、排液用三级插装阀"17J,使系统能按理想的卸
压曲线进行快速卸压、振动小、挤压机工作平稳。
自动控制等【15J。
液压机的工作原理、特点与分类

3
图4-2 液压机工作原理
1、小柱塞 2、大柱塞
2021/7/5
如图,两个充满工 作液体的具有柱塞或活 塞的容腔由管道连接, 当小柱塞上作用的力为 F1 时,在大柱塞上将产 生向上的作用力 F2,迫 使制件变形,且:
F2=F1×A2/A1
A1、A2 分别为小柱塞和 大柱塞的工作面积。
4
图4-3 液压机工作过程
980rpm
型号
Y160L-4
额定转速
1440rpm
型号
160YCY14-1B
公称排量
160ml/r
型号
63YCY14-1B
公称排量
63ml/r
设备总重×103kg
约65秒
额定功率 30KW
数量
1台
额定功率 15KW
数量
1台
额定压力 31.5MPa
数量
1台
额定压力 31.5MPa
数量
1台
~8.2
续表4-2 Y81Q-2000金属打包液压机主要技术参数
(2) 整体框架式液压机:机身由铸造或型钢焊接而成,一 般为空心箱形结构,抗弯性能较好,立柱部分做成矩形 截面,便于安装平面可调导向装置。活动横梁运动精度 较高,在塑料制品和粉末冶金、薄板冲压液压机中获得 广泛应用。
2021/7/5
18
四、按传动形式分类
(1) 泵直接传动液压机:每台液压机单独配备高压泵, 中小型液压机多为这种传动形式。
工作台尺寸(前后×左右×距地面高)
工作行程速度(mm/s) 活动横梁至工作台最大距离/mm 液体工作压力/MPa
3000 800 300 1140×1210×700 4.3 1240 2000
金属挤压液压机控制系统仿真设计说明书
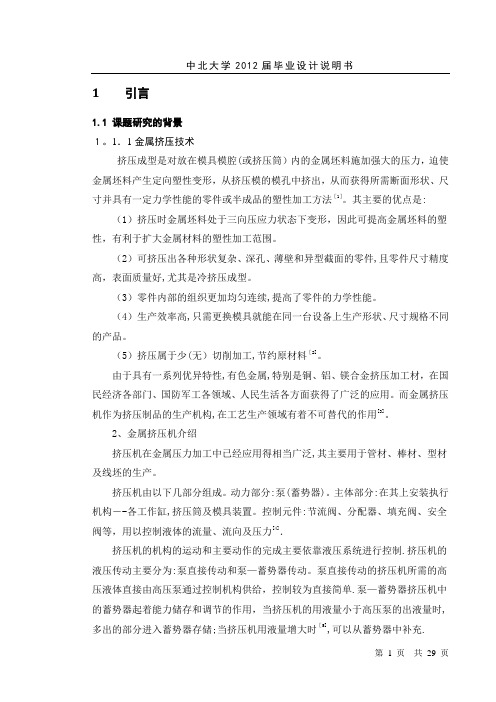
1引言1.1 课题研究的背景1。
1.1金属挤压技术挤压成型是对放在模具模腔(或挤压筒)内的金属坯料施加强大的压力,迫使金属坯料产生定向塑性变形,从挤压模的模孔中挤出,从而获得所需断面形状、尺寸并具有一定力学性能的零件或半成品的塑性加工方法[1]。
其主要的优点是: (1)挤压时金属坯料处于三向压应力状态下变形,因此可提高金属坯料的塑性,有利于扩大金属材料的塑性加工范围。
(2)可挤压出各种形状复杂、深孔、薄壁和异型截面的零件,且零件尺寸精度高,表面质量好,尤其是冷挤压成型。
(3)零件内部的组织更加均匀连续,提高了零件的力学性能。
(4)生产效率高,只需更换模具就能在同一台设备上生产形状、尺寸规格不同的产品。
(5)挤压属于少(无)切削加工,节约原材料[2]。
由于具有一系列优异特性,有色金属,特别是铜、铝、镁合金挤压加工材,在国民经济各部门、国防军工各领域、人民生活各方面获得了广泛的应用。
而金属挤压机作为挤压制品的生产机构,在工艺生产领域有着不可替代的作用[3]。
2、金属挤压机介绍挤压机在金属压力加工中已经应用得相当广泛,其主要用于管材、棒材、型材及线坯的生产。
挤压机由以下几部分组成。
动力部分:泵(蓄势器)。
主体部分:在其上安装执行机构--各工作缸,挤压筒及模具装置。
控制元件:节流阀、分配器、填充阀、安全阀等,用以控制液体的流量、流向及压力[4].挤压机的机构的运动和主要动作的完成主要依靠液压系统进行控制.挤压机的液压传动主要分为:泵直接传动和泵—蓄势器传动。
泵直接传动的挤压机所需的高压液体直接由高压泵通过控制机构供给,控制较为直接简单.泵—蓄势器挤压机中的蓄势器起着能力储存和调节的作用,当挤压机的用液量小于高压泵的出液量时,多出的部分进入蓄势器存储;当挤压机用液量增大时[5],可以从蓄势器中补充.1.1。
2国内外挤压机发展现状由于挤压机的整机结构方面,已经比较成熟,国外挤压机技术发展主要体现在电液控制系统方面.在电气控制系统方面,挤压机可分为三大类[6]:(1)继电器控制控制系统以继电器为主控元件,这种控制方式是电气控制中发展最早的一种,是延续了几十年的传统控制方式,电路结构简单、技术要求不高、成本较低、控制功能简单、适应性不强[7].其适用于单机工作、加工产品精度要求不高的大批量生产(如餐具、厨具产品等),也可组成简单的生产线[8],但由于电路的限制,压机工作稳定性、柔性差。
锻造设备类别和名称
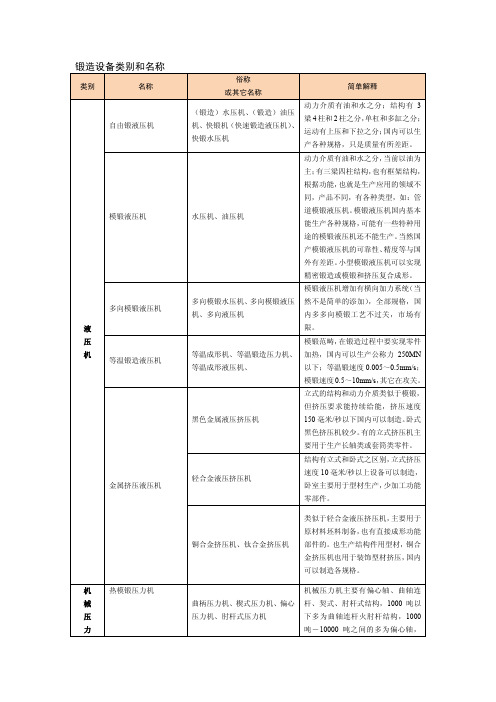
摩擦螺旋压力机
螺
电动螺旋压力机
旋
压
力 液压螺旋压力机
机
双盘摩擦螺旋压力机,模压机
电动程控螺旋压力机、高能螺旋 压力机、电动数控螺旋压力机
两个摩擦盘与中间的飞轮交替接触 而实现提升和打击,公称力 100MN 以下全部可以生产,但在数控和精巧 方面与国外有差距。 电机直接驱动飞轮和螺杆,电机正转 打击,反转回程。国内目前可以生产 公称力 80MN 以下的压力机,但可靠 行不足。 公称力 25MN 以下可以生产,电机直 接驱动下行打击,液压提升回程。
轻合金液压挤压机
速度 10 毫米/秒以上设备可以制造, 卧室主要用于型材生产,少加工功能
零部件。
铜合金挤压机、钛合金挤压机
类似于轻合金液压挤压机,主要用于 原材料坯料制备,也有直接成形功能 部件的。也生产结构件用型材,铜合 金挤压机也用于装饰型材挤压,国内 可以制造各规格。
曲柄压力机、楔式压力机、偏心 压力机、肘杆式压力机
气,锤头抬起,突然释放下腔油压, 上腔压缩氮气膨胀推动活塞下行实 现打击。目前国内可以生产模锻 16T 以下,自由锻 8T 以下的锻锤。国外 自由锻没有,很好生产这类锻锤了。 对于大吨位锻锤,采用对击,其中主 锤头的打击与放油打击一样,目前下 锤头打击是依靠机械联接实现,国内 完全可以制造。 油缸中,上下腔全部充满高压油,由 于上腔面积大而形成推动,推动活塞 下行实现打击。模锻 125KJ 以下,对 击 400KJ 以下可以生产,但可靠性和 可控性与国外有差距。大吨位锻锤, 采用对击,上锤头运行于模锻一致, 下锤头有的是机械联接,有的是液压 驱动,国内目前的结构为机械联接。
国内可以生产。
材料竖向被咬入,完成聚料成形,全
部规格国产。但目前国内还不能生产
挤压机主要技术参数确定
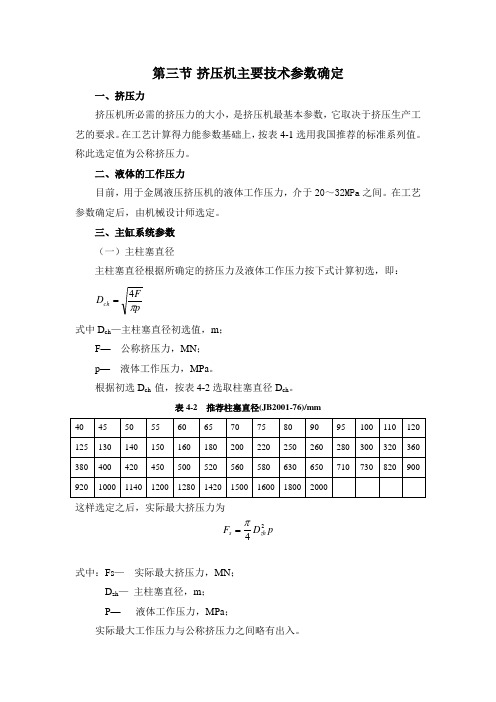
第三节 挤压机主要技术参数确定一、挤压力挤压机所必需的挤压力的大小,是挤压机最基本参数,它取决于挤压生产工艺的要求。
在工艺计算得力能参数基础上,按表4-1选用我国推荐的标准系列值。
称此选定值为公称挤压力。
二、液体的工作压力目前,用于金属液压挤压机的液体工作压力,介于20~32MPa 之间。
在工艺参数确定后,由机械设计师选定。
三、主缸系统参数 (一)主柱塞直径主柱塞直径根据所确定的挤压力及液体工作压力按下式计算初选,即:pFD ch π4=式中D ch —主柱塞直径初选值,m ;F — 公称挤压力,MN ; p — 液体工作压力,MPa 。
根据初选D ch 值,按表4-2选取柱塞直径D ch 。
表4-2 推荐柱塞直径(JB2001-76)/mm这样选定之后,实际最大挤压力为p D F zh s 24π=式中:Fs — 实际最大挤压力,MN ; D zh — 主柱塞直径,m ;P —液体工作压力,MPa ;实际最大工作压力与公称挤压力之间略有出入。
(二)主柱塞行程主柱塞行程取决于挤压机装入锭坯的方式,主柱塞行程有长行程和短行程之分。
行程长短与装锭方式的关系如图4-2所示。
当锭坯在挤压筒和挤压轴之间装入时,主柱塞行程至少要大于挤压筒长度、锭坯长度、锭片厚度三者之和。
称为长行程,其值按下式选取,即:t zh L S )3.22.2(-=式中:S zh —主柱塞行程,mm Lt — 挤压筒长度,mm短行程挤压机分两种情况,锭坯在挤压筒(可移动)和模座间装入;挤压筒可移出挤压中心线外装入锭坯。
此时主柱塞行程为短行程,一般取为t zh L S )3.12.1(-=(三)主柱塞回程力主柱塞回程力F h ,一般按经验公式确定,即 F h =(0.05~0.08)F 式中 F h —主柱塞回程力,MN ;F — 公称挤压力,MN 。
对于小型挤压机,系数取上限值,否则反之。
(四)快速前进力对于泵-蓄势器传动的挤压机,主柱塞空程前进是靠低压罐中的液体(0.8~1.2MPa )推动,不存在快速前进力。
铅条液压挤压机的工作原理
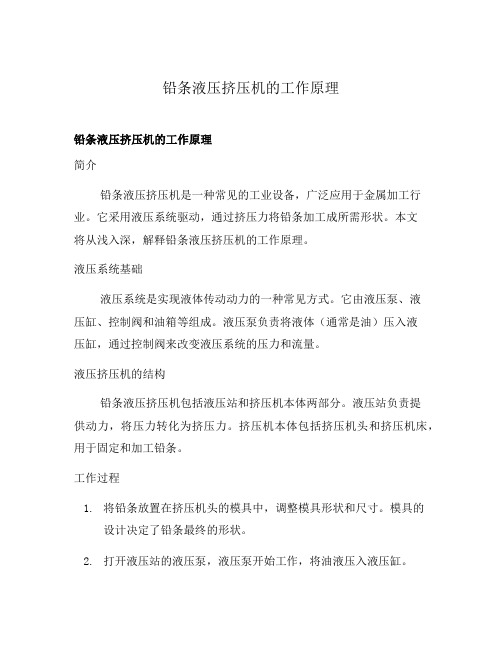
铅条液压挤压机的工作原理铅条液压挤压机的工作原理简介铅条液压挤压机是一种常见的工业设备,广泛应用于金属加工行业。
它采用液压系统驱动,通过挤压力将铅条加工成所需形状。
本文将从浅入深,解释铅条液压挤压机的工作原理。
液压系统基础液压系统是实现液体传动动力的一种常见方式。
它由液压泵、液压缸、控制阀和油箱等组成。
液压泵负责将液体(通常是油)压入液压缸,通过控制阀来改变液压系统的压力和流量。
液压挤压机的结构铅条液压挤压机包括液压站和挤压机本体两部分。
液压站负责提供动力,将压力转化为挤压力。
挤压机本体包括挤压机头和挤压机床,用于固定和加工铅条。
工作过程1.将铅条放置在挤压机头的模具中,调整模具形状和尺寸。
模具的设计决定了铅条最终的形状。
2.打开液压站的液压泵,液压泵开始工作,将油液压入液压缸。
3.通过控制阀,调整液压系统的压力和流量,使得挤压力达到所需的数值。
4.液压缸产生的挤压力传递给挤压机头,挤压机头将挤压力传导到铅条上。
5.铅条在挤压力的作用下发生塑性变形,逐渐形成所需的形状。
6.当达到设定的挤压时间或达到设定的铅条长度时,关闭液压泵,停止挤压过程。
7.打开模具,取出已经加工好的铅条。
工作原理解析液压挤压机的工作原理基于液压系统的传动方式和力的作用。
通过液压泵提供的压力和流量,液压缸产生的挤压力可以精确控制。
挤压机头接收到挤压力后,将力传导给铅条,使其发生塑性变形。
应用领域铅条液压挤压机在金属加工行业具有广泛的应用。
例如,用于制作铅管、铅线、铅板等各种形状的铅制品。
其应用领域涉及建筑、电气、化工等多个行业。
结论铅条液压挤压机是一种基于液压系统工作的设备。
通过准确控制液压系统的压力和流量,将铅条加工成所需形状。
深入了解挤压机的工作原理,可以帮助我们更好地理解其应用和操作方法。
液压系统优势铅条液压挤压机采用液压系统作为动力传动方式,相比于机械传动和电动传动具有以下优势: - 动力输出平稳:液压系统的传动是通过液体传递力的方式,具有平稳的动力输出特点,可以避免机械传动中的冲击和振动问题。
液压金属压块机设计

摘要工业化初期由于盲目扩大生产,金属浪费现象严重,而回收利用较少,废金属对环境的污染与日剧增。
随着我国经济增长方式由粗放型向集约型的转变和人们环保意识的增强,市场对废金属处理的设备需求将越来越大。
为了实现对废金属的有效回收,以及再利用,对有效处理废金属的压块机研究已引起了众多人的兴趣。
该液压废金属压块机用于常态下冷压各种厚度在3mm以下的废金属边角料,废钢屑,废油箱,解体汽车壳等金属废料。
冷压成块状,便于储运或投炉。
本机带有快送装置,大幅度提高工效。
该液压废金属压块机是集液压控制和电气控制为一体,液压缸在侧压板上的按照均布对称布置,以此实现了液压缸推动压板做圆弧形轨迹的运动。
并且整个压块机由液压缸顺序动作推动压板、压头,提升门,实现了动作的一贯连续性。
该压块机的设计参数:料箱尺寸:2000*1000*500mm压块尺寸:500*500*300公称压力:1000KN液压系统压力:25MPa该液压废金属压块机体积小,操作方便,不但具备多种使用要求,而且大大提高了废金属回收的效率。
关键词:液压,废金属,压块机,回收AbstractSince the early industrialization blind expansion of production, metal waste are serious and less recycling, scrap metal pollution to the environment become more and more serious. As China's economic growth mode from extensive to intensive changes and the enhancement of environmental awareness among the people, the market for scrap metal processing equipment demand will grow. In order to achieve the effective recovery of scrap metal and re-use, effective handling of scrap metal on the Press has aroused the interest of many people.The Hydraulic Press for scrap metal under the norm in the 3mm thickness of cold-pressing all kinds of the following bits and pieces of scrap metal, steel scrap, waste oil tanks and the disintegration of the shell and other metal scrap car. Cold into a massive, easy storage and transportation or to vote furnace. Local delivery devices with a fast, substantial increase in work efficiency.Hydraulic Press scrap metal made metal-hydraulic control and electrical control as one. The hydraulic cylinder in the side clips on the uniform in accordance with the symmetrical layout, to achieve a hydraulic cylinder clips to promote the arc-shaped path of movement. and the entire sequence by the hydraulic cylinder action to promote clips, the pressure head, doors make the movement's continuity.The Press of the design parameters: feed box size: 2000*1000*500mm Press Size: 500*500*300Nominal pressure: 1000KN Hydraulic system pressure: 25MPaThis hydraulic scrap metal Press has small size, it is easy to operate, not only meets the requirements of multiple use, but also greatly improves the efficiency of recycling scrap metal. Keywords:Hydraulic,Scrap metal,Press,Recycling目录摘要 (I)Abstract(英文摘要) (Ⅱ)目录 (Ⅲ)第一章引言 (1)第二章液压废金属压块机结构设计 (3)2.1 压块机的工作原理设计 (3)2.2 确定压块机的设计原则 (3)2.3 压块机的总体结构 (3)2.4 压块机的压板设计 (3)2.5 压块机的机身设计 (4)2.6 压块机各零部件设计 (4)2.6.1 门的设计 (4)2.6.2机架设计的准则 (4)第三章液压控制系统设计 (5)3.1根据压块机动作原理设计液压控制系统原理图 (5)3.1.1 设计思路 (5)3.1.2 液压控制系统原理图 (6)3.1.3 液压控制系统回路 (7)3.2根据给定的参数及使用要求选取液压元件的型号,规格 (8)3.3液压泵的选择 (9)3.3.1 确定液压泵的最大工作压力 (9)3.3.2确定液压泵的流量 (9)3.3.3选择液压泵的规格 (10)3.3.4 确定液压泵的驱动功率 (11)3.4 电动机的选取 (11)3.5 油箱的设计 (12)3.6联轴器的选取 (13)3.7液压阀,压力表的安装 (13)3.8管子内径的计算 (13)3.9 液压泵站的设计 (15)第四章液压缸的安装布局及设计 (16)4.1 四个通过支架联接在压板上测液压缸的设计及其计算 (16)4.1.1 在压板上液压缸的布局设计 (16)4.1.2 压力P (17)4.1.3缸筒设计及计算 (17)4.1.4缸筒壁厚σ的计算 (18)4.1.5缸筒外径的计算1D (18)4.1.6缸筒壁厚的验算 (18)4.1.7活塞杆的设计及其计算 (19)4.1.8H为最小导向长度的确定 (20)4.1.9支承环的选用 (21)4.1.10活塞设计 (22)4.1.11液压缸进出油口采用螺纹连接 (23)4.1.12密封件的选用 (23)4.1.13防尘圈的选用 (25)4.2 通过压头进行推压的主液压缸的设计及其计算 (26)4.2.1主液压缸的设计 (26)4.2.2压力P (26)4.2.3缸筒设计及其计算 (26)4.2.4缸筒壁厚σ的计算 (27)4.2.5缸筒外径的计算1D (27)4.2.6缸筒壁厚的验算 (27)4.2.7活塞杆的设计及其计算 (28)4.2.8H为最小导向长度的确定 (29)4.2.9支承环的选用 (30)4.2.10活塞设计 (31)4.2.11液压缸进出油口采用螺纹连接 (31)4.2.12密封件的选用 (31)4.2.13防尘圈的选用 (34)4.3 提升门的两个开门液压缸的设计及其计算 (35)4.3.1开门液压缸的设计 (35)4.3.2压力P (35)4.3.3缸筒设计及其计算 (36)4.3.4缸筒壁厚σ的计算 (36)4.3.5缸筒外径的计算1D (37)4.3.6缸筒壁厚的验算 (37)4.3.7 活塞杆的设计及其计算 (37)4.3.8H为最小导向长度的确定 (38)4.3.9支承环选用 (39)4.3.10 活塞设计 (40)4.3.11 液压缸进出油口采用螺纹连接 (40)4.3.12 密封件的选用 (41)4.3.13防尘圈的选用 (44)第五章电气控制系统设计 (45)5.1 选起动电路 (45)5.2 压块机电气控制系统图 (46)5.2.1 设计要点 (46)5.2.2电气控制系统图 (46)5.3 电磁铁线圈的得电顺序 (47)5.4 电磁铁得失电,液压缸动作过程 (47)5.5 PLC语句表 (50)总结 (51)参考文献 (53)致谢及声明 (54)第一章引言工业化初期由于盲目扩大生产,金属浪费现象严重,金属回收利用较少,废金属对环境的污染与日剧增。
卧式液压金属打包机技术参数
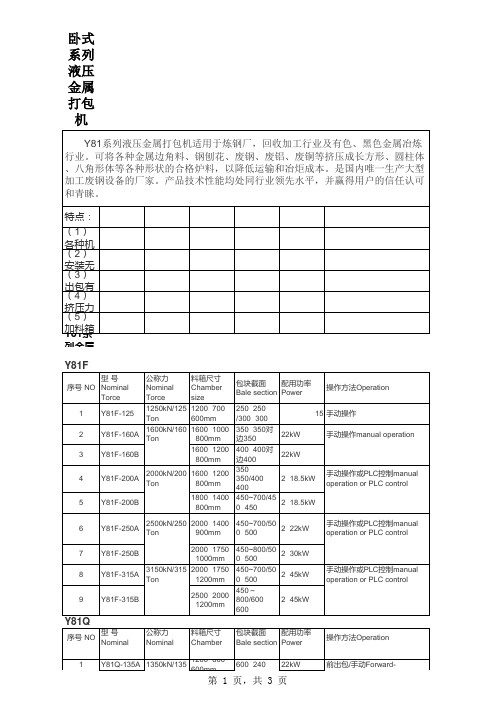
推包/PLC控制Push-out/PLC control
江阴市宏晟液压科技有限公司 :云亭街道澄杨路松桥堍 > 电话:0510-86151229 > 电话:0510-86151310 > 传真:0510-86016118
· Feed opening size加料箱尺寸L x W x H · Wrap Size包块尺寸L x W · Single work time单次工作时间 · Nominal Force公称推力(KN) · Working capacity工作能力(KG/H) · Power 功率(KW) · manual operation操作方式 · package翻包 equipment出包方式 of 产品说明 · 本系列金属液压打包机,可将各种金属边角料、钢刨花、废铝、废铜等挤压成型,便于运输、冶炼 · 采用缓速启动形式,换向时平稳,分流,减少系统冲击 · 结构坚固耐用,安装时无需底脚螺丝,移动方便 · 出包有翻包和推包两种形式 · 加料箱尺寸和包块形状尺寸可根据用户原料规格设计定制 1200-1800 380V /15KW 手动阀操作 1000x700x600 300x300 120 135A 1350kN/135 1200×600× 600×240 600mm 1400×600× Y81Q-135B Ton 1400×700× 700×280 Y81Q-160 1600kN/160 600mm 600mm Ton 2000kN/200 1400×700× 700×280 600mm To YR81Q-230 2300kN/230 1800×750× 750×350 700mm To Y81Q-200
2500kN/250 Ton
推包/PLC控制Push-out/PLC control
第三章液压机
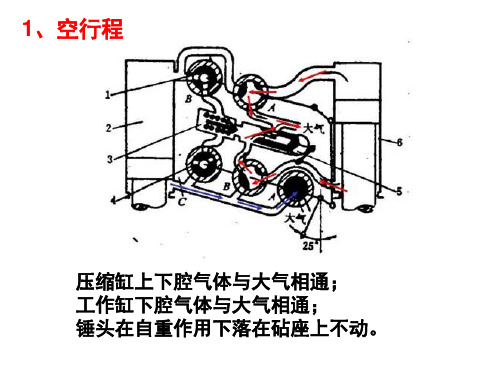
二、液压机的选用
应以在该设备上进行的主要工艺为依据, 确保其主要参数都满足工艺要求,结合使用 条件,投资情况,制造厂情况并参考国内外 同类设备的参数和使用效果来决定。
在选用液压机时还应注意以下几个问题:
(1)关于最大偏心距
液压机的主要技术参数中,除锻造液压机外, 一般不专门列出允许的最大偏心距。但这不等 于可以在任意位置进行加载,相反,成形生产 中所用的大多数液压机如冲压液压机、塑料制 品液压机等都是按较小的偏心距甚至中心载荷 进行设计的,其承受偏心载荷的能力更差。
(0)手动液压机:用于一般压制、压装等工艺。 (1)锻造液压机:用于自由锻、钢锭开坯及金属模锻。 (2)冲压液压机:用于各种薄板、厚板的冲压。 (3)一般用途液压机:用于各种工艺,通常称为万能液压机。 (4)校正压装液压机:用于零件的校正及装配。 (5)层压液压机:用于胶合板、刨花板、纤维板及绝缘材料板 的压制。 (6)挤压液压机:用于挤压各种有色及黑色金属材料。 (7)压制液压机:用于各种粉末制品的压制成形,如粉末冶金、 人造金刚石、耐火材料的压制。 (8)打包、压块液压机:用于将金属碎屑及废料压成块。 (9)其他液压机:包括轮轴压装、冲孔等专门用途的液压机。
立柱与横梁的连接形式
(a)双螺母式(b)锥台式(c)锥台式(d)锥套式(e)锥套式
双 螺 母 式
26
双 螺 母 式
27
3) 立柱的预紧方式 注意:为什么要预紧?何处被预紧? ● 加热预紧 过程:o 立柱、横梁安装到位;
o
o o o
内外螺母冷态拧紧;
加热立柱两端; 拧紧外螺母; 冷却后即产生很大的预紧力。
整个机身的刚性较差,受力时会产生角变形,且
机身上无导轨,运动精度较差,有时为了保证机 身有足够的强度和刚度,结构上做得比较笨重。
铝型材挤压机工作原理及结构
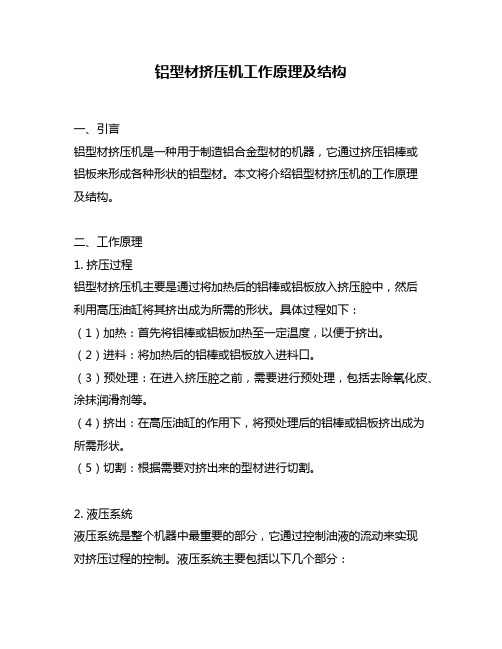
铝型材挤压机工作原理及结构一、引言铝型材挤压机是一种用于制造铝合金型材的机器,它通过挤压铝棒或铝板来形成各种形状的铝型材。
本文将介绍铝型材挤压机的工作原理及结构。
二、工作原理1. 挤压过程铝型材挤压机主要是通过将加热后的铝棒或铝板放入挤压腔中,然后利用高压油缸将其挤出成为所需的形状。
具体过程如下:(1)加热:首先将铝棒或铝板加热至一定温度,以便于挤出。
(2)进料:将加热后的铝棒或铝板放入进料口。
(3)预处理:在进入挤压腔之前,需要进行预处理,包括去除氧化皮、涂抹润滑剂等。
(4)挤出:在高压油缸的作用下,将预处理后的铝棒或铝板挤出成为所需形状。
(5)切割:根据需要对挤出来的型材进行切割。
2. 液压系统液压系统是整个机器中最重要的部分,它通过控制油液的流动来实现对挤压过程的控制。
液压系统主要包括以下几个部分:(1)油箱:存储液压油。
(2)油泵:将液压油送至高压油缸。
(3)高压油缸:产生高压力,用于挤出铝棒或铝板。
(4)低压油缸:产生低压力,用于控制机器的各个部分。
(5)阀门、管路等。
三、结构1. 挤出机头挤出机头是铝型材挤压机中最重要的部分之一,它主要由以下几个部分组成:(1)模具:用于形成所需的型材形状。
(2)加热器:用于加热铝棒或铝板。
(3)预处理装置:用于去除氧化皮、涂抹润滑剂等。
(4)挤出腔体:将预处理后的铝棒或铝板送入模具中。
2. 液压系统如前所述,液压系统是整个机器中最重要的部分之一。
它主要由以下几个部分组成:(1)驱动泵站:产生液压油。
(2)高压油缸:产生高压力,用于挤出铝棒或铝板。
(3)低压油缸:产生低压力,用于控制机器的各个部分。
(4)管路、阀门等。
3. 控制系统控制系统主要用于控制整个机器的运行。
它主要由以下几个部分组成:(1)PLC控制器:用于对机器进行自动化控制。
(2)人机界面:用于操作和监测机器的运行情况。
(3)电气元件:包括传感器、继电器等。
四、结论通过以上介绍,我们可以得出结论:铝型材挤压机是一种利用液压系统将加热后的铝棒或铝板挤出成为所需形状的机器。
铝合金挤压的最新技术和装备
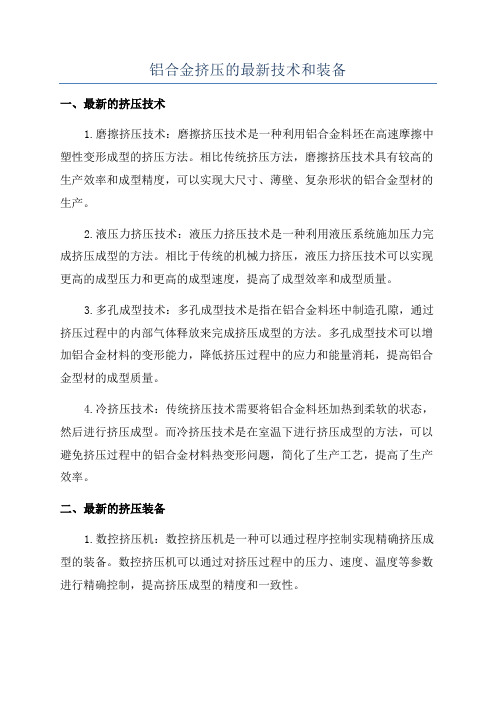
铝合金挤压的最新技术和装备一、最新的挤压技术1.磨擦挤压技术:磨擦挤压技术是一种利用铝合金料坯在高速摩擦中塑性变形成型的挤压方法。
相比传统挤压方法,磨擦挤压技术具有较高的生产效率和成型精度,可以实现大尺寸、薄壁、复杂形状的铝合金型材的生产。
2.液压力挤压技术:液压力挤压技术是一种利用液压系统施加压力完成挤压成型的方法。
相比于传统的机械力挤压,液压力挤压技术可以实现更高的成型压力和更高的成型速度,提高了成型效率和成型质量。
3.多孔成型技术:多孔成型技术是指在铝合金料坯中制造孔隙,通过挤压过程中的内部气体释放来完成挤压成型的方法。
多孔成型技术可以增加铝合金材料的变形能力,降低挤压过程中的应力和能量消耗,提高铝合金型材的成型质量。
4.冷挤压技术:传统挤压技术需要将铝合金料坯加热到柔软的状态,然后进行挤压成型。
而冷挤压技术是在室温下进行挤压成型的方法,可以避免挤压过程中的铝合金材料热变形问题,简化了生产工艺,提高了生产效率。
二、最新的挤压装备1.数控挤压机:数控挤压机是一种可以通过程序控制实现精确挤压成型的装备。
数控挤压机可以通过对挤压过程中的压力、速度、温度等参数进行精确控制,提高挤压成型的精度和一致性。
2.智能挤压模具:智能挤压模具是一种根据工件形状和挤压过程中的力学特性进行优化设计的模具。
智能挤压模具可以通过模具内部的传感器和控制系统实时监测和调整挤压过程中的压力分布,实现均匀的变形和优化的材料利用。
3.真空挤压装备:真空挤压装备是一种在挤压过程中对料坯进行真空处理的装备。
真空挤压可以有效地防止氧化反应和气孔形成,提高挤压成型的表面质量和力学性能。
4.挤压成型模拟仿真装备:挤压成型模拟仿真装备可以通过计算机模拟和分析挤压过程中的力学和热学特性,预测成型过程中的变形情况和应力分布,优化挤压工艺和模具设计,提高挤压成型的效率和质量。
总之,铝合金挤压技术的不断创新和发展,使得铝合金型材的生产更加高效、精确和可靠。
TJ231-1978机械设备安装工程施工及验收规范第三册机械压力机、空气锤、液压机、铸造设备安装

第5条组装组合横梁应符合下列要求:一、结合面的接触应良好,局部间隙不应大于0.1毫米,间隙累计长度不应大于周长的1/5;二、连接螺栓的螺母端面与横梁的接触应良好,局部间隙不应大于0.05毫米,间隙累计长度不应大于周长的1/5;三、热装螺栓时,螺母的旋转角度应符合设备技术文件的规定,无规定时,材料为40号钢或45号钢的螺栓,初拉伸应力可800-1000公斤力/厘米²计算;四、定位凸台和定位的键与键、键与梁的接触应均匀,接触面积应大于75%。
第6条组装液压缸和柱塞应符合下列要求:一、立式液压缸柱塞的不铅垂度和卧式液压缸柱塞的不水平度均不应超过0.1/1000;二、液压缸法兰与上、下横梁(或前、后梁)的接触应良好,局部间隙不应大于0.05毫米,间隙累计长度不应大于周长的1/5;三、拧紧液压缸柱塞压套法兰螺栓时,螺母受力应一致,法兰间隙应均匀。
第7条组装立柱(或张力柱)应符合下列要求:一、立柱(或张力柱)螺纹与螺母螺纹的接触应均匀,接触面积应大于60%;二、立柱(或张力柱)螺母与上、下横梁(或前、后梁)的接触应良好,局部间隙不应大于0.05毫米,间隙累计长度不应大于周长的1/5;三、立柱(或张力柱)预紧前,应宁晋立柱(或张力柱)各螺母,其拧紧程度应一致。
第8条液压机立柱(或张力柱)的预紧,应用加热或超压预紧(尽量用加热预紧)。
第9条液压机立柱(或张力柱)采用加热预紧时,其加热温度和螺母的旋转角度应符合设备技术文件的规定,无规定时,可按下列公式计算:一、立柱(或张力柱)被拉紧部分的伸长量:λ(1)EL/=σ•式中λ——立柱(或张力柱)伸长量,厘米;σ——初拉伸应力,一般为1000~1200公斤力/厘米²(锻造、冲压液压机可取高值,卧式液压机可取低值);L——立柱(或张力柱)被拉紧部分的长度,厘米;E——弹性模数,公斤力/厘米²。
二、立柱(或张力柱)受热部分伸长后,螺母的旋转角:•rλ=(2)360S/式中r——螺母旋转角,度;S——立柱(或张力柱)螺纹螺距,厘米;λ——立柱(或张力柱)伸长量,厘米。
铝型材挤压机工作原理及结构
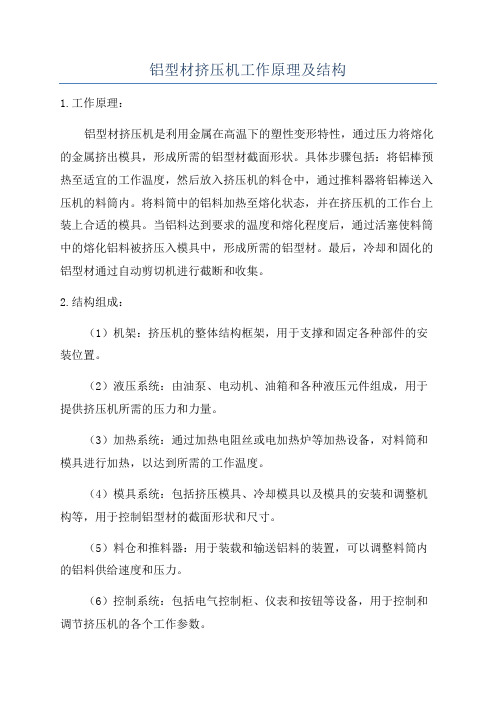
铝型材挤压机工作原理及结构1.工作原理:铝型材挤压机是利用金属在高温下的塑性变形特性,通过压力将熔化的金属挤出模具,形成所需的铝型材截面形状。
具体步骤包括:将铝棒预热至适宜的工作温度,然后放入挤压机的料仓中,通过推料器将铝棒送入压机的料筒内。
将料筒中的铝料加热至熔化状态,并在挤压机的工作台上装上合适的模具。
当铝料达到要求的温度和熔化程度后,通过活塞使料筒中的熔化铝料被挤压入模具中,形成所需的铝型材。
最后,冷却和固化的铝型材通过自动剪切机进行截断和收集。
2.结构组成:(1)机架:挤压机的整体结构框架,用于支撑和固定各种部件的安装位置。
(2)液压系统:由油泵、电动机、油箱和各种液压元件组成,用于提供挤压机所需的压力和力量。
(3)加热系统:通过加热电阻丝或电加热炉等加热设备,对料筒和模具进行加热,以达到所需的工作温度。
(4)模具系统:包括挤压模具、冷却模具以及模具的安装和调整机构等,用于控制铝型材的截面形状和尺寸。
(5)料仓和推料器:用于装载和输送铝料的装置,可以调整料筒内的铝料供给速度和压力。
(6)控制系统:包括电气控制柜、仪表和按钮等设备,用于控制和调节挤压机的各个工作参数。
3.工作过程:(1)启动挤压机,在加热系统预热到设定温度后,打开料仓盖,将铝料放入料仓内。
(2)通过电机驱动液压系统的油泵,产生足够的压力将铝料推入料筒中。
(3)启动加热系统,加热料筒并将铝料熔化。
(4)调整模具的合适位置和形状,确保挤压出来的铝型材截面形状和尺寸符合要求。
(5)启动液压系统的活塞,使熔化的铝料通过模具中的压力腔挤出,形成铝型材。
(6)使用冷却系统对挤压出的铝型材进行冷却和固化。
(7)通过自动剪切机对铝型材进行定尺截断和收集,完成整个工作过程。
总结:。
- 1、下载文档前请自行甄别文档内容的完整性,平台不提供额外的编辑、内容补充、找答案等附加服务。
- 2、"仅部分预览"的文档,不可在线预览部分如存在完整性等问题,可反馈申请退款(可完整预览的文档不适用该条件!)。
- 3、如文档侵犯您的权益,请联系客服反馈,我们会尽快为您处理(人工客服工作时间:9:00-18:30)。
山东威力重工
• 操作步骤: • 1、用氧-乙炔火焰烤划伤部位(掌握温度,避免表面退火),将常年 渗金属表面的油烤出来,烤到没有火花四溅。 • 2、将划伤部位用角磨机表面处理,打磨深度1毫米以上,并沿缸筒外 壁打磨出沟槽,最好是燕尾槽。划伤两端钻孔加深,改变受力情况。 • 3、用脱脂棉蘸丙酮或无水乙醇将表面清洗干净。 • 4、将调和均匀的美嘉华-福世蓝2211F金属修复材料涂抹到划伤表面; 第一层要薄,要均匀且全部覆盖划伤面,以确保材料与金属表面最好 的粘接,再将材料涂至整个修复部位后反复按压,确保材料填实并达 到所需厚度,使之比缸筒外壁表面略高。 • 5、材料在24℃下完全达到各项性能需要24小时,为了节省时间,可 以通过卤钨灯提高温度,温度每提升11℃,固化时间就会缩短一半, 最佳固化温度70℃。 • 6、材料固化后,用细磨石或刮刀,将高出缸筒外壁表面的材料修复 平整,施工完毕。
山东威力重工
3.金属挤压液压机常见故障和处理方案
• 金属挤压液压机运行中,有时会有螺栓脱落,掉入液压缸内对柱塞壁 造成严重划伤。问题出现后,传统方法根本无法实现现场修复,只能 是拆卸后运往生产厂家进行补焊加工或报废更换。由于没有备件更换, 重新生产配件或返厂维修时间无法掌控,长时间停机给企业造成严重 经济损失,同时还要支付高额的加工或修复费用。为了满足企业连续 化生产的要求,需要找到方便快捷、简单有效的维修手段来解决该设 备问题,最大程度减少企业的停机停产时间并降低维修维护费用。目 前可以采用高分子复合材料的方法进行现场修复,应用较为成熟的有 福世蓝体系。采用金属修复2211F高分子复合材料现场修复,其具有 超强的粘着力,极好抗压性、均衡的综合物理化学性能、良好的耐磨 性,通过现场涂抹,固化后研磨出配合尺寸,即可免机加工现场修复 柱塞划伤,避免报废更换,延长设备使用寿命。
山东威力重工
金属挤压液压机
金属挤压液压机由机身、带缸滑块、 侧缸、电气操纵箱、活塞式上打料机 构、工作台垫板、模具移动支架和顶 出缸组成,液压机机身采用钢板焊接 的整体框架式结构,其左、右两侧面 均设计为全开放式开口,在机身上方 设置有由钢板制成的安全装置,其内 安装有液压机动力机构,带缸滑块上 设有滑块垫板,于滑块垫板上开有T 形槽,液压夹紧块嵌装于T形槽内, 气缸安装在工作台垫板上。 目录 1 简介 2 原理及应用 3 金属挤压液压机常见故障和 处理方案
1.简介
• 挤压工艺主要用于生产有色金属和黑色金属的各种管、棒、型材和线 材,可以挤出各种截面形状的材料,包括复杂的带筋壁板。 • 一般适用锻件、汽车、拖拉机、航天等行业金属挤压成形工艺。 • 冲孔拔伸工艺是用于将加热并经高压水除鳞后的钢坯,通过冲孔和多 次拔伸,生产出具有一定壁厚的筒形工件的工艺过程,如高压气瓶、 氧气筒、炮弹弹体及各种容器。冲孔是将冲子压入坯料,形成盂形, 再移至拔伸液压机上,通过一系列直径逐渐减少的模圈(或者通过类 似作用的装置),使坯料拔长、直径减少、壁厚减薄。 • 冲孔和拔伸液压机可以做成一体。也可以分开做成冲孔液压ห้องสมุดไป่ตู้和拔伸 液压机,配套组成冲孔拔伸液压机组。
山东威力重工
2.原理及应用
驱动和控制系统有设置在操纵箱内的控制液压 机工作的控制器PLC以及操纵箱上的控制面板, 与控制器PLC电连接的驱动电路;通过导线与驱 动电路相连的第一移动工作台驱动电机和第二 移动工作台驱动电机;设置在液压机的T型导轨 上的多个起落缸;设置在移动工作台T型导轨的 下端与控制器PLC中的CPU模块相连的检测A位到 位限位开关、检测B位到位限位开关、检测C位 到位限位开关和检测D位到位限位开关。