铸件加工表面的加工余量的确定和说明
确定加工余量的方法

确定加工余量的方法随着现代加工技术的不断发展,加工余量的确定变得越来越重要。
加工余量是指在加工过程中,为了保证加工精度和工件质量而留下的一定量的材料。
加工余量的大小直接影响到工件的精度和质量,因此在加工过程中合理确定加工余量非常重要。
本文将介绍几种常见的确定加工余量的方法。
一、经验法经验法是一种较为简单的方法,可以根据经验和实际情况来确定加工余量。
这种方法通常适用于一些简单的加工工件,如钻孔、车削等。
经验法的确定方式是根据工件的材料、尺寸和形状等因素来确定加工余量。
例如,对于一些硬度较高的材料,应该留下较大的加工余量,以保证工件的精度和质量。
二、计算法计算法是一种较为科学的方法,可以通过计算来确定加工余量。
这种方法通常适用于一些复杂的加工工件,如铸件、锻件等。
计算法的确定方式是根据工件的形状、尺寸、材料和工艺等因素来计算加工余量。
例如,对于一些复杂的铸件,可以通过计算来确定每个加工环节需要留下的加工余量。
三、试验法试验法是一种比较直观的方法,可以通过实际试验来确定加工余量。
这种方法通常适用于一些特殊的加工工件,如高精度零件等。
试验法的确定方式是在实际加工过程中留下一定量的加工余量,然后通过测量和检验来确定加工余量是否合适。
如果加工余量过大或过小,则需要进行相应的调整。
四、仿真法仿真法是一种比较先进的方法,可以通过计算机仿真来确定加工余量。
这种方法通常适用于一些高精度的加工工件,如航空航天零件等。
仿真法的确定方式是通过计算机模拟加工过程,然后根据模拟结果来确定加工余量。
这种方法可以大大提高加工精度和质量,同时也可以减少加工成本和时间。
总之,确定加工余量是加工过程中非常重要的一环。
不同的加工工件和加工要求需要采用不同的方法来确定加工余量。
通过合理确定加工余量可以提高工件的精度和质量,同时也可以减少加工成本和时间。
因此,在加工过程中一定要认真对待加工余量的确定工作。
铸造工艺设计说明书

铸造⼯艺设计说明书铸造⼯艺设计说明书课程设计:机械⼯艺课程设计设计题⽬:底座铸造⼯艺设计班级:机⾃1103设计⼈:学号:指导教师:张锁梅、贾志新前⾔学⽣通过设计能获得综合运⽤过去所学过的全部课程进⾏机械制造⼯艺及结构设计的基本能⼒,为以后做好毕业设计、⾛上⼯作岗位进⾏⼀次综合训练和准备。
它要求学⽣全⾯地综合运⽤本课程及有关选修课程的理论和实践知识,进⾏零件加⼯⼯艺规程的设计和机床夹具的设计。
其⽬的是:(1)培养学⽣综合运⽤机械制造⼯程原理课程及专业课程的理论知识,结合⾦⼯实习、⽣产实习中学到的实践知识,独⽴地分析和解决机械加⼯⼯艺问题,初步具备设计中等复杂程度零件⼯艺规程的能⼒。
(2)培养学⽣能根据被加⼯零件的技术要求,运⽤夹具设计的基本原理和⽅法,学会拟订夹具设计⽅案,完成夹具结构设计,进⼀步提⾼结构设计能⼒。
(3)培养学⽣熟悉并运⽤有关⼿册、图表、规范等有关技术资料的能⼒。
(4)进⼀步培养学⽣识图、制图、运算和编写技术⽂件的基本技能。
(5)培养学⽣独⽴思考和独⽴⼯作的能⼒,为毕业后⾛向社会从事相关技术⼯作打下良好的基础。
⽬录⼀、⼯艺审核 (1)1.数量与材料 (1)2.图样 (1)3.零件的结构性 (1)⼆、成形⼯艺设计 (1)1.确定⼯艺⽅案 (1)(1)浇注位置的选择 (2)(2)分型⾯的选择 (2)2.确定铸造⼯艺参数 (4)(1)机械加⼯余量和铸出孔 (4)(2)浇注位置的选择 (5)(3)拔模斜度 (5)(4)铸造收缩率 (6)3.砂芯设计 (6)4.浇注系统的设计 (6)5. 冷铁的设置 (6)三、⼼得体会 (7)⼀、⼯艺审核1、数量与材料由零件图可知,该零件结构⽐较简单,但是形状不是很规则,⼯作条件⼀般以承受压⼒为主,故要求该零件有良好的刚性和强度。
另外,根据零件图的要求,该底座零件为单件⼩批量⽣产,另外材料选⽤灰铸铁HT200,流动性较好,适于铸造。
2、图样该零件图给出了主视图、左视图、俯视图3个视图。
铸件生产的机加工余量与公差的关系
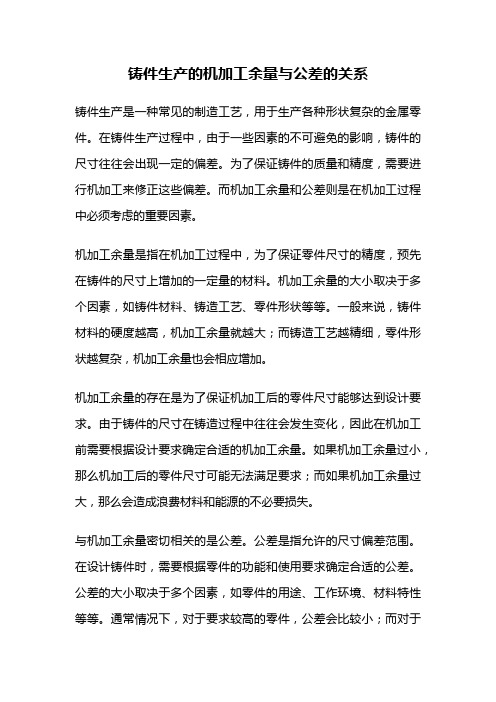
铸件生产的机加工余量与公差的关系铸件生产是一种常见的制造工艺,用于生产各种形状复杂的金属零件。
在铸件生产过程中,由于一些因素的不可避免的影响,铸件的尺寸往往会出现一定的偏差。
为了保证铸件的质量和精度,需要进行机加工来修正这些偏差。
而机加工余量和公差则是在机加工过程中必须考虑的重要因素。
机加工余量是指在机加工过程中,为了保证零件尺寸的精度,预先在铸件的尺寸上增加的一定量的材料。
机加工余量的大小取决于多个因素,如铸件材料、铸造工艺、零件形状等等。
一般来说,铸件材料的硬度越高,机加工余量就越大;而铸造工艺越精细,零件形状越复杂,机加工余量也会相应增加。
机加工余量的存在是为了保证机加工后的零件尺寸能够达到设计要求。
由于铸件的尺寸在铸造过程中往往会发生变化,因此在机加工前需要根据设计要求确定合适的机加工余量。
如果机加工余量过小,那么机加工后的零件尺寸可能无法满足要求;而如果机加工余量过大,那么会造成浪费材料和能源的不必要损失。
与机加工余量密切相关的是公差。
公差是指允许的尺寸偏差范围。
在设计铸件时,需要根据零件的功能和使用要求确定合适的公差。
公差的大小取决于多个因素,如零件的用途、工作环境、材料特性等等。
通常情况下,对于要求较高的零件,公差会比较小;而对于要求不那么严格的零件,公差可以适当放宽。
机加工余量和公差之间存在密切的关系。
一方面,机加工余量的大小会直接影响到机加工后的尺寸偏差范围。
如果机加工余量过大,那么在机加工过程中可以更好地修正铸件尺寸的偏差,从而使得机加工后的尺寸偏差范围更小;反之,如果机加工余量过小,那么机加工后的尺寸偏差范围可能会比较大。
另一方面,公差的大小也会影响到机加工余量的确定。
如果公差要求比较严格,那么机加工余量需要相应增加,以保证机加工后的尺寸能够在公差范围内。
在实际的铸件生产中,确定合适的机加工余量和公差是十分重要的。
过大的机加工余量和公差会增加生产成本,降低零件的精度;而过小的机加工余量和公差则可能导致机加工后的尺寸无法满足要求。
精密铸造加工余量计算公式

精密铸造加工余量计算公式精密铸造加工余量是指在精密铸造加工过程中为了保证零件尺寸精度和表面质量而留下的一定尺寸的加工余量。
精密铸造加工余量的计算是非常重要的,它直接影响着零件的加工精度和表面质量。
在精密铸造加工中,通常会根据不同的零件要求和加工工艺,采用不同的余量计算公式。
一般来说,精密铸造加工余量的计算公式包括三个方面,缩小余量、加工余量和表面余量。
下面将分别介绍这三个方面的计算公式。
1. 缩小余量的计算公式。
缩小余量是指在模具设计和制造过程中为了弥补熔模收缩、铸件收缩和热变形而设置的一定尺寸的余量。
通常情况下,缩小余量的计算公式为:缩小余量 = 零件尺寸 + 熔模收缩 + 铸件收缩 + 热变形模具尺寸。
其中,熔模收缩是指在金属冷却过程中由于凝固收缩而导致的模具尺寸缩小;铸件收缩是指在金属冷却过程中由于凝固收缩而导致的铸件尺寸缩小;热变形是指在金属冷却过程中由于温度变化而导致的尺寸变化。
通过以上公式计算得到的缩小余量,可以保证在铸造过程中得到满足要求的零件尺寸。
2. 加工余量的计算公式。
加工余量是指在精密铸造加工过程中为了保证零件尺寸精度而设置的一定尺寸的余量。
通常情况下,加工余量的计算公式为:加工余量 = 零件尺寸允许偏差。
其中,允许偏差是指在零件尺寸允许范围内所允许的最大偏差。
通过以上公式计算得到的加工余量,可以保证在加工过程中得到满足要求的零件尺寸精度。
3. 表面余量的计算公式。
表面余量是指在精密铸造加工过程中为了保证零件表面质量而设置的一定尺寸的余量。
通常情况下,表面余量的计算公式为:表面余量 = 表面粗糙度 + 表面处理余量。
其中,表面粗糙度是指零件表面的粗糙度值;表面处理余量是指为了进行表面处理而设置的余量。
通过以上公式计算得到的表面余量,可以保证在加工过程中得到满足要求的零件表面质量。
在精密铸造加工中,根据不同的零件要求和加工工艺,可以根据以上公式计算得到合适的余量。
同时,为了保证零件尺寸精度和表面质量,还需要在实际加工过程中根据具体情况进行适当的调整和修正。
铸件公差及加工余量

国际标准二版ISO8026 第铸件------ 尺差公差和加工留余量1.围此国际标准系统地规定了铸件尺寸公差等级和加工余量要求。
它适用于不同铸造工艺的金属及合金件尺寸[同时请参见介绍g]和第5款]此国际标准适用于图纸上提到的根本公差及/或要求的加工余量,同时也适用于特定尺寸的旁标注的个别公差及/或要求的加工余量(见第11款)。
当铸造厂提供模具或冲模工具,或承受证明责任时,该系统实施。
2.参考标准通过本标准的引用,下述标准构成其条款。
在出版期间,提到的版本有效。
标准都是有可能要进展修订的,建议承受本标准的各方使用以下标准的最新版本。
IEC和ISO的成员拥有当前有效的国际标准。
ISO286-1:1998,ISO体系极限与适用---第一局部:公差与适用根底ISO1302:1992,技术图纸---外表构造标注方法.3.定义就本标准,采用下述定义:3.1 根本尺寸:加工前毛坯件的尺寸〔见图一〕,包括必要加工余量〔见图二〕图1:图纸标识(见第四款) 图2:公差极限3.2 尺寸公差[见ISO 286-1]3.3 要求的加工余量,RMA:对于未加工铸件,产品余量允许铸件外表后续加工影响的去除,到达希望的外表构成和必要尺寸准确度。
对柱形或双面加工,RMA要考虑两次〔见图5和6〕3.4 移位:由于多个型板要素的失误,会造成铸件外表的相对移位。
〔见图3〕图3:最大的移位3.5 斜度角(锥角):成形因素〔例如:在包围面上〕额外的倾斜,对于把铸件从铸模和压模,或模具从砂型,或永久模具上的零件间相互挪动都是很有必要。
4 标尺寸除了给壁厚标尺寸〔它可能存在两种尺寸〕,需要防止连续的尺寸。
5 公差等级铸件公差等级分16级,从CT1到CT16〔见图表1〕对根本公差不适用的尺寸,应该被归类为个别公差。
对为获得永久金属模(高压与低压),压模铸件和熔模铸件等特殊的操作,其它更准确的公差标准,比方国标,可以采用.6 移位除非另有说明,移位必须控制在如表1〔见图3〕的公差围之。
铸造工艺参数及在工艺图中的表示方法
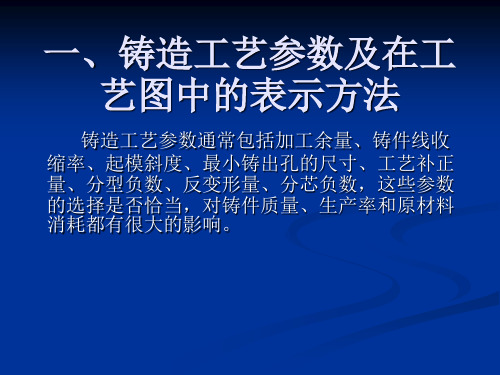
工艺补正量在工艺图中的表示方法:
6、分型负数
因起模后的修型和烘干引起砂型变形,致使分型 面凹凸不平,使合型不严密。为防止浇注时从分型 面跑火,合型时需在分型面上放耐火泥条或石棉绳, 这就增高了型腔的高度。为了保证铸件尺寸合图样 尺寸要求,模样上必须减去相应的高度,减去的数 值称为分型负数。
1)、若模样分为两半,且上、下两半是对称的, 则分型负数在上、下模样上各取一半,否则,分型 负数应在截面大的一侧模样上取。
起模斜度的设置方法:常采用增加壁厚法,对于加
工面一般采用增加壁厚的方法获得起模斜度,起模斜度 在加工余量后做出;加减厚度法,一般用各种铸筋,也 用于壁厚较小的模样侧面的起模斜度;减小壁厚法,一 般用于铸件壁厚较大的模样的起模斜度。
4、最小铸出孔
机械零件上往往有很多孔、槽和台阶,一般应尽 可能在铸造时铸出。这样既可以节约金属,减少机 械加工的工作量、降低成本,又可使铸件壁厚比较 均匀,减少形成缩孔、缩松等铸造缺陷的倾向。但 是,当铸件上的孔、槽尺寸太小,而铸件的壁厚又 较厚和金属压力较高时,反而会使铸件产生粘砂, 造成清理和机械加工困难。有的孔、槽必须采用复 杂而且难度较大的工艺措施才能铸出,而实现这些 措施还不如用机械加工方法制出更为方便和经济。 有时由于孔距要求很精确,铸出的孔如有偏心,就 很难保证加工精度。因此在确定零件上的孔和槽是 否铸出时,必须既考虑到铸出这些孔或槽的可能性, 又要考虑到铸出这些孔或槽的必要性和经济性。
一、铸造工艺参数及在工 艺图中பைடு நூலகம்表示方法
铸造工艺参数通常包括加工余量、铸件线收 缩率、起模斜度、最小铸出孔的尺寸、工艺补正 量、分型负数、反变形量、分芯负数,这些参数 的选择是否恰当,对铸件质量、生产率和原材料 消耗都有很大的影响。
机械加工余量手册

机械加工余量手册1 标准概况GB/T 6414—2017《铸件尺寸公差、几何公差与机械加工余量》是铸造基础性标准之一。
本标准使用重新起草法,修改采用ISO8062-3: 2007《产品几何量技术规范(GPS)模制件尺寸和几何公差第3部分:铸件一般尺寸、几何公差和机械加工余量》。
本标准代替GB/T 6414—1999《铸件尺寸公差与机械加工余量》。
2 标准的主要内容2.1 标准的范围本标准适用于由各种铸造方法生产的铸件[1]。
2.2 术语和定义2.2.1 铸件公称尺寸机械加工前的毛坯铸件的设计尺寸,包括必要的机械加工余量。
2.2.2 铸件尺寸公差铸件允许尺寸的变动量。
公差等于最大极限尺寸与最小极限尺寸之差的绝对值,也等于上偏差与下偏差之差的绝对值。
2.2.3 错型(错箱)由于合型时错位,铸件的一部分与另一部分在分型面处相互错开。
2.2.4 机械加工余量在毛坯铸件上为了随后可用机械加工方法去除铸造对金属表面的影响,并使之达到所要求的表面特征和必要的尺寸精度而留出的金属余量。
2.2.5 起模斜度为使模样容易从铸型中取出或型芯自芯盒脱出,平行于起模方向在模样或芯盒壁上的斜度。
2.3 尺寸标注除壁厚的尺寸标注(允许存在由两个尺寸组成的尺寸链)外,应避免链式尺寸标注。
2.4 倾斜要素2.4.1 在设计要求有斜度(如有起模斜度)的位置,应采用沿斜面对称分布的公差。
2.4.2 图样上一般应规定斜度是增加材料,还是减去材料,或取平均值,表示为:斜度+;斜度-;斜度±。
2.4.3 与图样上通用的斜度布置不同的特殊表面的斜度,应在该表面上单独标注,标注应符合GB/T 131的规定,例如。
2.4.4 对于要机械加工的尺寸,为了能获得成品尺寸,应采用“斜度+”,而不考虑图样上对斜度的通用技术要求。
2.5 公差等级铸件尺寸公差等级的代号为DCTG,即英文Dimensional Casting Tolerance Grade的缩写,公差等级分为16级,标记为DCTG1~DCTG16,见表1。
制造工艺详解——铸造

制造工艺详解——铸造铸造是人类掌握比较早的一种金属热加工工艺,已有约6000年的历史。
中国约在公元前1700~前1000年之间已进入青铜铸件的全盛期,工艺上已达到相当高的水平。
一、铸造的定义和分类铸造的定义:是将液体金属浇铸到与零件形状相适应的铸造空腔中,待其冷却凝固后,获得具有一定形状、尺寸和性能金属零件毛坯的成型方法。
常见的铸造方法有砂型铸造和精密铸造,详细的分类方法如下表所示。
砂型铸造:砂型铸造——在砂型中生产铸件的铸造方法。
钢、铁和大多数有色合金铸件都可用砂型铸造方法获得。
由于砂型铸造所用的造型材料价廉易得,铸型制造简便,对铸件的单件生产、成批生产和大量生产均能适应,长期以来,一直是铸造生产中的基本工艺。
精密铸造:精密铸造是用精密的造型方法获得精确铸件工艺的总称。
它的产品精密、复杂、接近于零件最后形状,可不加工或很少加工就直接使用,是一种近净形成形的先进工艺。
铸造方法分类二、常用的铸造方法及其优缺点1. 普通砂型铸造制造砂型的基本原材料是铸造砂和型砂粘结剂。
最常用的铸造砂是硅质砂,硅砂的高温性能不能满足使用要求时则使用锆英砂、铬铁矿砂、刚玉砂等特种砂。
应用最广的型砂粘结剂是粘土,也可采用各种干性油或半干性油、水溶性硅酸盐或磷酸盐和各种合成树脂作型砂粘结剂。
砂型铸造中所用的外砂型按型砂所用的粘结剂及其建立强度的方式不同分为粘土湿砂型、粘土干砂型和化学硬化砂型3种。
砂型铸造用的是最流行和最简单类型的铸件已延用几个世纪.砂型铸造是用来制造大型部件,如灰铸铁,球墨铸铁,不锈钢和其它类型钢材等工序的砂型铸造。
其中主要步骤包括绘画,模具,制芯,造型,熔化及浇注,清洁等。
工艺参数的选择加工余量:所谓加工余量,就是铸件上需要切削加工的表面,应预先留出一定的加工余量,其大小取决于铸造合金的种类、造型方法、铸件大小及加工面在铸型中的位置等诸多因素。
起模斜度:为了使模样便于从铸型中取出,垂直于分型面的立壁上所加的斜度称为起模斜度。
铸钢件机械加工余量、尺寸公差及缺陷评定标准

铸钢件机械加工余量、尺寸公差及缺陷评定标准1、范围本标准规定了铸钢件机械加工余量、尺寸公差及缺陷的评定。
本标准适用于起重机械产品铸钢件尺寸公差测量验收及铸造缺陷评定,也适用于外协铸钢件毛坯的检验验收。
2、引用标准GB/T11350-89 铸件机械加工余量GB6414-86 铸件尺寸公差JB/T6392.2-92 起重机车轮技术条件Q/DQ100-80 普通桥式起重机技术条件3、铸件机械加工余量铸件机械加工件,有毛坯图时,加工余量按毛坯图的规定;没有毛坯图时,按公司的产品特点,选用GB/T11350-89《铸件机械加工余量》中H级加工余量(铸件尺寸公差等级按CT13)数值如表1:表1注:表中每栏的加工余量数值是以一测为基准,进行单侧加工的加工余量值,()内数值为进行双侧加工时,每测的加工余量值。
4、铸件尺寸公差4.1 铸件尺寸公差按设计图纸的规定。
4.2 设计图纸未规定的铸件非加工面的尺寸公差及加工面毛坯尺寸公差,按公司的产品特点,选用GB64414-86《铸件尺寸公差》中规定的CT13级,公差带为对称分布,即一半为正值,一半为负值。
公差数值见表2:表25、技术要求5.1 铸件最终热处理应按图纸规定,铸件毛坯应进行正火或退货处理;5.2 铸件表面应整洁,不得留有明显的型砂、斑疤等缺陷。
浇口、冒口、毛边应气割清除,飞刺应清除,气割应在铸件毛坯热处理前进行。
浇、冒口气割侯,根部残留高度不大于4mm;5.3 铸件毛坯如有气孔、夹渣、机械伤痕等缺陷,除高锰钢外可焊补;5.4 铸件不加工的次要表面,若缺陷在下述范围内允许存在,可不进行焊补:a、缺陷总面积不超过该表面面积的5%;b、单个缺陷面积的直径不超过5mm,深度不超过其壁厚的10%,且绝对值不超过3mm,每100mm×100mm 面积上不超过2个。
5.5 铸件毛坯焊补,应遵循以下条件:a、焊补应在毛坯热处理前进行;b、缺陷必须清除干净,至呈现良好基体金属;c、所用焊条应能保证焊内的机械性能与铸件本身的机械性能相当。
铸造工艺参数及在工艺图中的表示方法
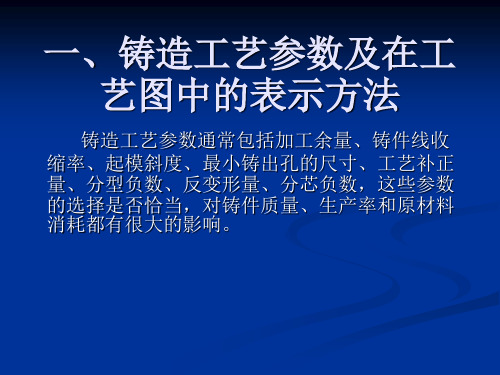
13、冷铁
用蓝色线表示,在需要放置冷铁处画 并 注明冷铁编号(无编号的注明尺寸大小)、 数量
14、浇注系统
工艺图中绘制浇注系统用红色线表示 示例如下:
15、铸造工艺图章
铸件毛重:包含加工余量的铸件重量(首件为计算的理论重 量)
造型方法:手工、手工木底板、手工铁底板、GFA线、气冲 线等
一般中小铸件壁厚差别不大且结构上刚度 较大时,不必留反变形。大的床身类、平台 类等多使用反变形量。
8、分芯负数
对于分段制造的长砂芯或分开制作的大砂
芯,在接缝处应留出分芯间隙量,即在砂芯 的分开处,将砂芯尺寸减去间隙尺寸,被减 去的尺寸称为分芯负数。分芯负数是为了砂 芯拼合及下芯方便而采用的。分芯负数可以 留在相邻的两个砂芯上,每个砂芯各留一半; 也可留在指定的一侧的砂芯上。分芯负数根 据砂芯接合面的大小一般留1-3mm。分芯负 数多用于手工制芯的大砂芯。
编号顺序:芯子编号顺序通常为下芯顺序,如 在其大芯上组装有另外小芯,其小芯的编号是在其 大芯基础上,在阿拉伯数字右下角标小写的汉语拼 音,即表示芯子的编号,如1a#芯、2a#……,如其 芯为覆膜砂芯、钢管芯、耐火管芯、铁芯,则需在 工艺章中注明
芯头边界:砂芯全部用蓝色线表示,其外型芯头 部分用红色线表示;如果是两个互相装配的砂芯边 界应全部用蓝色线表示。
在工艺图中,加工量的表示方法
2、铸件线收缩率
铸件从线收缩起始温度冷却至室温时,线尺 寸的相对收缩量称为铸件线收缩率。以模样与铸 件的长度差占模样长度的百分率表示:铸造收缩 率 K=(L模-L件)/L件X100%
式中 :L模 为模样的尺寸; L件 为铸件的尺寸。
铸件线收缩率受许多因素的影响,例如,合 金的种类及成分、铸件冷却、收缩时受到阻力的 大小、冷却条件的差异等,因些,要十分准确的 给出 铸件的线收缩率是非常困难的。当铸件处于 自由收缩状态时线收缩率较大,当铸件不能自由 收缩时线收缩率较小。
加工余量

加工余量为了加工出合格的零件,必须从毛坯上切去的那层金属的厚度,称为加工余量。
加工余量又可分为工序余量和总余量。
某工序中需要切除的那层金属厚度,称为该工序的加工余量。
从毛坯到成品总共需要切除的余量,称为总余量,等于相应表面各工序余量之和。
在工件上留加工余量的目的是为了切除上一道工序所留下来的加工误差和表面缺陷,如铸件表面冷硬层、气孔、夹砂层,锻件表面的氧化皮、脱碳层、表面裂纹,切削加工后的内应力层和表面粗糙度等。
从而提高工件的精度和表面粗糙度。
加工余量的大小对加工质量和生产效率均有较大影响。
加工余量过大,不仅增加了机械加工的劳动量,降低了生产率,而且增加了材料、工具和电力消耗,提高了加工成本。
若加工余量过小,则既不能消除上道工序的各种缺陷和误差,又不能补偿本工序加工时的装夹误差,造成废品。
其选取原则是在保证质量的前提下,使余量尽可能小。
一般说来,越是精加工,工序余量越小。
编辑本段基准机械零件是由若干个表面组成的,研究零件表面的相对关系,必须确定一个基准,基准是零件上用来确定其它点、线、面的位置所依据的点、线、面。
根据基准的不同功能,基准可分为设计基准和工艺基准两类。
1.设计基准在零件图上用以确定其它点、线、面位置的基准,称为设计基准。
如图32-2所[cc2]示的轴套零件,各外圆和内孔的设计基准是零件的轴心线,端面A是端面B、C的设计基准,内孔的轴线是外圆径向跳动的基准。
2.工艺基准零件在加工和装配过程中所使用的基准,称为工艺基准。
工艺基准按用途不同又分为装配基准、测量基准及定位基准。
(1)装配基准装配时用以确定零件在部件或产品中的位置的基准,称为装配基准。
(2)测量基准用以检验已加工表面的尺寸及位置的基准,称为测量基准。
如图32-2中的零件,内孔轴线是检验外圆径向跳动的测量基准;表面A是检验长度L尺寸l和的测量基准。
(3)定位基准加工时工件定位所用的基准,称为定位基准。
作为定位基准的表面(或线、点),在第一道工序中只能选择未加工的毛坯表面,这种定位表面称粗基准.在以后的各个工序中就可采用已加工表面作为定位基准,这种定位表面称精基准。
铸件加工余量标准大全
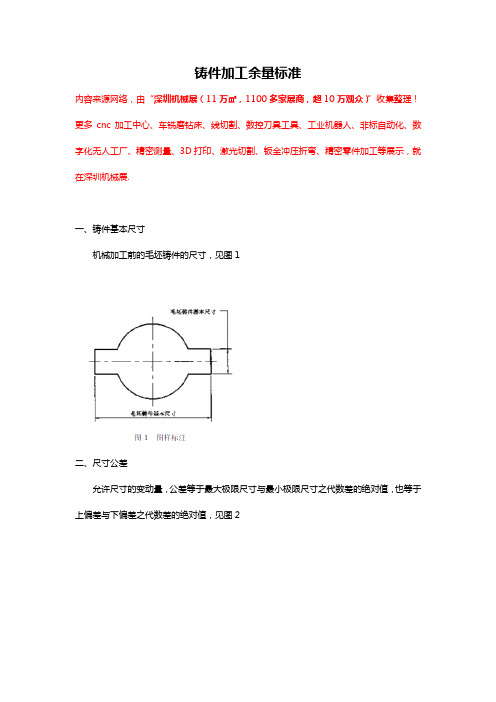
铸件加工余量标准内容来源网络,由“深圳机械展(11万㎡,1100多家展商,超10万观众)”收集整理!更多cnc加工中心、车铣磨钻床、线切割、数控刀具工具、工业机器人、非标自动化、数字化无人工厂、精密测量、3D打印、激光切割、钣金冲压折弯、精密零件加工等展示,就在深圳机械展.一、铸件基本尺寸机械加工前的毛坯铸件的尺寸,见图1二、尺寸公差允许尺寸的变动量,公差等于最大极限尺寸与最小极限尺寸之代数差的绝对值,也等于上偏差与下偏差之代数差的绝对值,见图2三、错型和错箱由于合型时错位铸件的一部分与另一部分在分型面处相互错开,见图三四、起模斜度为使模样容易从铸型中取出或型芯自芯盒脱,出平行于起模方向在模样或芯盒壁上的斜度壁厚,壁厚是指由铸型与铸型、铸型与型、芯型芯与型芯之间构成的铸壁厚度倾斜要素:在设计要求有斜度,例如带有起模斜度的场合应采用沿斜面对称分布的公差,见图4五、要求的机械加工余量(RMA)除非另有规定,要求的机械加工余量适用于整个毛坯铸件,即对所有需机械加工的表面只规定一个值,且该值应根据最终机械加工后成品铸件的最大轮廓尺寸,根据相应的尺寸范围选取,见图5。
铸件某一部位在铸态下的最大尺寸应不超过成品尺寸与要求的加工余量及铸造总公差之和,当采用斜度时,斜度应另外考虑。
图5六、要求的机械加工余量等级要求的机械加工余量等级有10级,称之为A、B、C、D、E、F、G、H、I、J和K级机械加工余量的标注,应在图样上标出需机械加工的表面和要求的机械加工余量值,并在括号内标出要求的机械加工余量等级,当制造模样或金属型装备时应考虑这些要求:A 用公差和要求的机械加工余量代号统一标注B如果需要个别要求的机械加工余量则应标注在图样的特定表面上内容来源网络,由“深圳机械展(11万㎡,1100多家展商,超10万观众)”收集整理!更多cnc加工中心、车铣磨钻床、线切割、数控刀具工具、工业机器人、非标自动化、数字化无人工厂、精密测量、3D打印、激光切割、钣金冲压折弯、精密零件加工等展示,就在深圳机械展.。
如何确定铸件加工余量【干货】
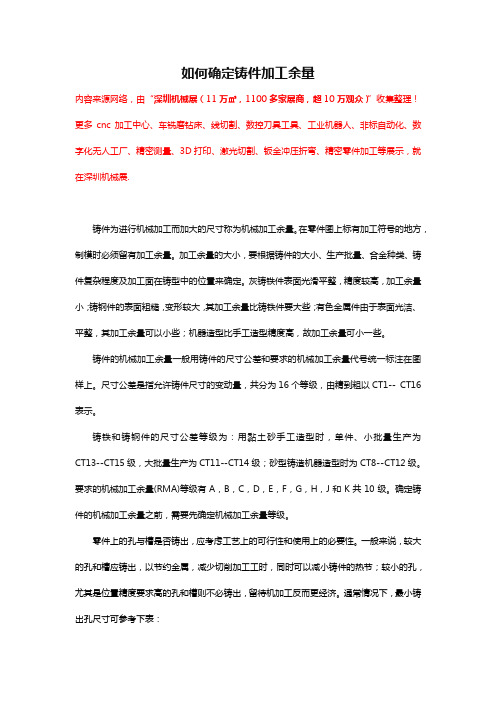
如何确定铸件加工余量内容来源网络,由“深圳机械展(11万㎡,1100多家展商,超10万观众)”收集整理!更多cnc加工中心、车铣磨钻床、线切割、数控刀具工具、工业机器人、非标自动化、数字化无人工厂、精密测量、3D打印、激光切割、钣金冲压折弯、精密零件加工等展示,就在深圳机械展.铸件为进行机械加工而加大的尺寸称为机械加工余量。
在零件图上标有加工符号的地方,制模时必须留有加工余量。
加工余量的大小,要根据铸件的大小、生产批量、合金种类、铸件复杂程度及加工面在铸型中的位置来确定。
灰铸铁件表面光滑平整,精度较高,加工余量小;铸钢件的表面粗糙,变形较大,其加工余量比铸铁件要大些;有色金属件由于表面光洁、平整,其加工余量可以小些;机器造型比手工造型精度高,故加工余量可小一些。
铸件的机械加工余量一般用铸件的尺寸公差和要求的机械加工余量代号统一标注在图样上。
尺寸公差是指允许铸件尺寸的变动量,共分为16个等级,由精到粗以CT1-- CT16表示。
铸铁和铸钢件的尺寸公差等级为:用黏土砂手工造型时,单件、小批量生产为CT13--CT15级,大批量生产为CT11--CT14级;砂型铸造机器造型时为CT8--CT12级。
要求的机械加工余量(RMA)等级有A,B,C,D,E,F,G,H,J和K共10级。
确定铸件的机械加工余量之前,需要先确定机械加工余量等级。
零件上的孔与槽是否铸出,应考虑工艺上的可行性和使用上的必要性。
一般来说,较大的孔和槽应铸出,以节约金属,减少切削加工工时,同时可以减小铸件的热节;较小的孔,尤其是位置精度要求高的孔和槽则不必铸出,留待机加工反而更经济。
通常情况下,最小铸出孔尺寸可参考下表:内容来源网络,由“深圳机械展(11万㎡,1100多家展商,超10万观众)”收集整理!更多cnc加工中心、车铣磨钻床、线切割、数控刀具工具、工业机器人、非标自动化、数字化无人工厂、精密测量、3D打印、激光切割、钣金冲压折弯、精密零件加工等展示,就在深圳机械展.。
铸造工艺参数及在工艺图中的表示方法
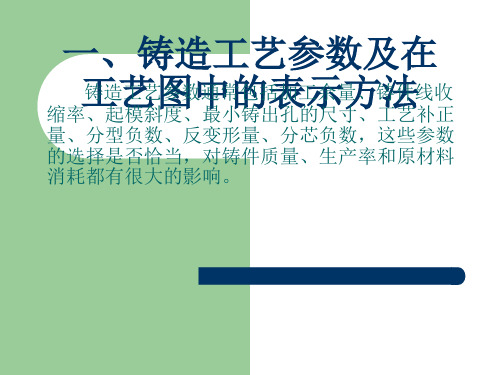
工艺补正量在工艺图中的表示方法 :
6、分型负数
因起模后的修型和烘干引起砂型变形,致使分 型面凹凸不平,使合型不严密。为防止浇注时从分 型面跑火,合型时需在分型面上放耐火泥条或石棉 绳,这就增高了型腔的高度。为了保证铸件尺寸合 图样尺寸要求,模样上必须减去相应的高度,减去 的数值称为分型负数。
1)、若模样分为两半,且上、下两半是对称的 ,则分型负数在上、下模样上各取一半,否则,分 型负数应在截面大的一侧模样上取。
注:(1)、同一铸件,由于结构上的原因,其局部 与整体、纵向与径向或长、宽、高三个方向的铸造 收缩率可能不一致。对于重要铸件长、宽、高应分 别给以不同的铸造收缩率。对于收缩大的方向和部 位取上限值,反之取下限值。
(2)、对于手工造型的灰铸铁件和球墨铸铁小件可 以不留缩尺。
3、起模斜度
为使模样容易从铸型中取出或型芯自芯盒脱出, 平行于起模方向在模样或芯盒壁上的斜度称为起模 斜度。
在工艺图中,加工量的表示方法
2、铸件线收缩率
铸件从线收缩起始温度冷却至室温时,线尺 寸的相对收缩量称为铸件线收缩率。以模样与铸 件的长度差占模样长度的百分率表示:铸造收缩 率 K=(L模-L件)/L件X100%
式中 :L模 为模样的尺寸; L件 为铸件的尺寸。
铸件线收缩率受许多因素的影响,例如,合 金的种类及成分、铸件冷却、收缩时受到阻力的 大小、冷却条件的差异等,因些,要十分准确的 给出 铸件的线收缩率是非常困难的。当铸件处于 自由收缩状态时线收缩率较大,当铸件不能自由 收缩时线收缩率较小。
一般中小铸件壁厚差别不大且结构上刚度较大时
,不必留反变形。大的床身类、平台类等多使用反 变形量。
8、分芯负数
对于分段制造的长砂芯或分开制作的大砂芯, 在接缝处应留出分芯间隙量,即在砂芯的分开处, 将砂芯尺寸减去间隙尺寸,被减去的尺寸称为分芯 负数。分芯负数是为了砂芯拼合及下芯方便而采用 的。分芯负数可以留在相邻的两个砂芯上,每个砂 芯各留一半;也可留在指定的一侧的砂芯上。分芯 负数根据砂芯接合面的大小一般留1-3mm。分芯负 数多用于手工制芯的大砂芯。
DIN1685-1_球墨铸铁件公差和加工余量
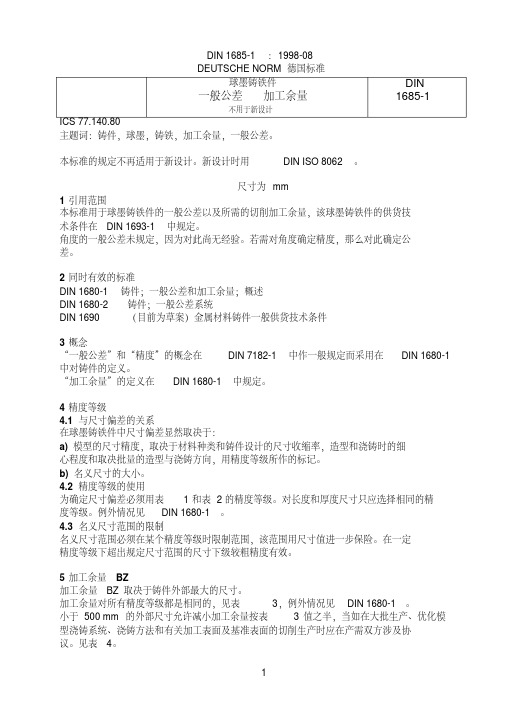
DIN 1685-1:1998-08 DEUTSCHE NORM 德国标准球墨铸铁件一般公差加工余量不用于新设计DIN 1685-1ICS 77.140.80主题词:铸件,球墨,铸铁,加工余量,一般公差。
本标准的规定不再适用于新设计。
新设计时用DIN ISO 8062。
尺寸为 mm1 引用范围本标准用于球墨铸铁件的一般公差以及所需的切削加工余量,该球墨铸铁件的供货技术条件在DIN 1693-1中规定。
角度的一般公差未规定,因为对此尚无经验。
若需对角度确定精度,那么对此确定公差。
2 同时有效的标准DIN 1680-1 铸件;一般公差和加工余量;概述DIN 1680-2 铸件;一般公差系统DIN 1690 (目前为草案)金属材料铸件一般供货技术条件3 概念“一般公差”和“精度”的概念在DIN 7182-1中作一般规定而采用在DIN 1680-1中对铸件的定义。
“加工余量”的定义在DIN 1680-1中规定。
4 精度等级4.1 与尺寸偏差的关系在球墨铸铁件中尺寸偏差显然取决于:a)模型的尺寸精度,取决于材料种类和铸件设计的尺寸收缩率,造型和浇铸时的细心程度和取决批量的造型与浇铸方向,用精度等级所作的标记。
b)名义尺寸的大小。
4.2 精度等级的使用为确定尺寸偏差必须用表1和表2的精度等级。
对长度和厚度尺寸只应选择相同的精度等级。
例外情况见DIN 1680-1。
4.3 名义尺寸范围的限制名义尺寸范围必须在某个精度等级时限制范围,该范围用尺寸值进一步保险。
在一定精度等级下超出规定尺寸范围的尺寸下级较粗精度有效。
5 加工余量BZ加工余量BZ取决于铸件外部最大的尺寸。
加工余量对所有精度等级都是相同的,见表3,例外情况见DIN 1680-1。
小于500 mm的外部尺寸允许减小加工余量按表 3 值之半,当如在大批生产、优化模型浇铸系统、浇铸方法和有关加工表面及基准表面的切削生产时应在产需双方涉及协议。
见表4。
DIN 1685-1:1998-08对铸件重量大于1000kg和/或壁厚大于50mm时加工余量也需在产需双方签订协议。
- 1、下载文档前请自行甄别文档内容的完整性,平台不提供额外的编辑、内容补充、找答案等附加服务。
- 2、"仅部分预览"的文档,不可在线预览部分如存在完整性等问题,可反馈申请退款(可完整预览的文档不适用该条件!)。
- 3、如文档侵犯您的权益,请联系客服反馈,我们会尽快为您处理(人工客服工作时间:9:00-18:30)。
铸件加工表面的加工余量的确定和说明序号基本尺寸/mm 加工余量等级加工余量/mm 选择理由和选择过程说明
1 137 G 双侧余量3.0
根据成批生产的加工余量等级(表2.8)为G级,尺寸公差等级为CT10,查表2-10,双侧加工余量为3mm,即尺寸为143mm,查表2-7,等尺寸公差为3.6mm,该尺寸及公差为(143±1.8)mm
2 Φ65G 双侧余量2.5
根据成批生产的加工余量等级(表2.8)为G级,尺寸公差等级为CT10,查表2-10,双侧加工余量为2.5mm,即尺寸为Φ70mm,查表2-7,等尺寸公差为3.2mm,该尺寸及公差为Φ(70±1.6)mm
3 17 G 单侧余量3.5
根据成批生产的加工余量等级(表2.8)为G级,尺寸公差等级为CT10,查表2-10,单侧加工余量为3.5mm,即尺寸为17+3.0-3.5=16.5mm,查表2-7,等尺寸公差为2.4mm,该尺寸及公差为(16.5±1.2)mm
4 Φ80G 双侧余量2.5
根据成批生产的加工余量等级(表2.8)为G级,尺寸公差等级为CT10,查表2-10,双侧加工余量为2.5mm,即尺寸为Φ85mm,查表2-7,等尺寸公差为3.2mm,该尺寸及公差为Φ(85±1.6)mm
5 30 G 单侧余量3.5
根据成批生产的加工余量等级(表2.8)为G级,尺寸公差等级为CT10,查表2-10,单侧加工余量为3.5mm,即尺寸为30+3.0+3.5=36.5mm,查表2-7,等尺寸公差为3.2mm,该尺寸及公差为(36.5±1.6)mm
6 Φ100G 双侧余量2.5
根据成批生产的加工余量等级(表2.8)为G级,尺寸公差等级为CT10,查表2-10,双侧加工余量为2.5mm,即尺寸为Φ105mm,查表2-7,等尺寸公差为3.6mm,该尺寸及公差为Φ
(105±1.8)mm
7 15 G 单侧余量3.5
根据成批生产的加工余量等级(表2.8)为G级,尺寸公差等级为CT10,查表2-10,单侧加工余量为3.5mm,即尺寸为15+3.0+3.5=21.5mm,查表2-7,等尺寸公差为2.4mm,该尺寸及公差为(21.5±1.2)mm
8 Φ47H 双侧余量3.0
根据成批生产的加工余量等级(表2.8)为H级,尺寸公差等级为CT10,查表2-10,双侧加工余量为3mm,即尺寸为Φ41mm,查表2-7,等尺寸公差为2.8mm,该尺寸及公差为Φ(41±1.4)mm
9 Φ32H 双侧余量3.0
根据成批生产的加工余量等级(表2.8)为H级,尺寸公差等级为CT10,查表2-10,双侧加工余量为3mm,即尺寸为Φ26mm,查表2-7,等尺寸公差为2.6mm,该尺寸及公差为Φ(26±1.3)mm
10 Φ60H 双侧余量3.0
根据成批生产的加工余量等级(表2.8)为H级,尺寸公差等级为CT10,查表2-10,双侧加工余量为3.0mm,即尺寸为Φ54mm,查表2-7,等尺寸公差为2.8mm,该尺寸及公差为Φ(54±1.4)mm
11 78 G 单侧余量3.5
根据成批生产的加工余量等级(表2.8)为G级,尺寸公差等级为CT10,查表2-10,单侧加工余量为3.5mm,即尺寸为78+3.0-3.5=77.5mm,查表2-7,等尺寸公差为3.2mm,该尺寸及公差为(77.5±1.6)mm
12 Φ155G 双侧余量3.0
根据成批生产的加工余量等级(表2.8)为G级,尺寸公差等级为CT10,查表2-10,双侧加工余量为4mm,即尺寸为Φ161mm,查表2-7,等尺寸公差为4.0mm,该尺寸及公差为Φ(161±2.0)mm。