机械加工确定加工余量的方法有哪些
机械加工工艺规程的制定 机械制作技术基础复习与测试题

第五章机械加工工艺规程的制定1.生产过程与工艺过程的含义是什么?两者的主要组成部分有哪些?[解]机械的生产过程是指机械从原材料开始直到制成机械产品之间的各个相互联系的劳动过程的总和。
它包括毛坯制造—零件的加工及热处理—机械的装配及检验—油漆及包装过程等直接生产过程.还包括原材料的运输和保管以及设计、工艺装备(刀,夹,量具等)的制造、维修等生产技术准备工作。
工艺过程是生产过程的重要组成部分,包括直接改变工件的形状(铸造,锻造等)、尺寸(机械加工)、位置(装配)和材料性质(热处理)使其成为预期产品的过程。
机械加工的工艺过程一般由工序、安装或工位、工步、走刀等组成。
2.生产纲领的含义是什么?划分生产类型的主要依据有哪些因素?[解]生产纲领即指年产量,它应计入备品和废品的数量。
可按下式计算:N零=N×n×(1+α)(1十β)。
生产类型的划分主要考虑年产量,产品本身的大小和结构的复杂性。
3.经济精度的含义是什么?它在工艺规程设计中起什么作用?[解]经济精度是指在正常的机床、刀具、工人等工作条件下,以合适的工时消耗所能达到的加工精度。
因此,在经济精度的范围内,加工精度和加工成本是互相适应的。
有关资料表格中列出各种加工方法所能达到的经济精度及表面租糙度是拟定零件工艺路线的基础,用以从中选择最合适的加工方法和加工设备。
4.何谓结构工艺性?对机械零件结构工艺性有哪些要求?[解]结构工艺性是指机器和零件的结构是否便于加工,装配和维修。
衡量工艺性的主要依据是能够可靠保证产品质量,且加工劳动量小、生产成本低,材料消耗少。
5.试分析下列加工情况的定位基准:(1)拉齿坯内孔时;(2)珩磨连杆大头孔时;(3)无心磨削活塞销外圆时;(4)磨削床身导轨面时;(5)用浮动镗刀块精镗内孔时;(6)超精加工主轴轴颈时;(7)箱体零件攻螺纹时;(8)用与主轴浮动连接的铰刀铰孔时。
[解]以上都是自为基准的加工例子,即以加工面本身作为定位基准。
加工余量的确定.

图3
由图可看出: 公称加工余量 = 前工序尺寸 - 本工序尺寸 最小加工余量=前工序尺寸的最小值 - 本工序尺寸的最大值 最大加工余量=前工序尺寸的最大值 - 本工序尺寸的最小值 工序加工余量的变动范围(最大加工余量与最小加工余量之差)= 前工序工序尺寸公差+ 本工序的工序尺寸公差
(二)总加工余量:总加工余量是指零件从毛坯变为成品的整个加工过 程中从某一表面所切除金属层的总厚度,也即零件毛坯尺寸与零件图 上设计尺寸之差。总加工余量等于各工序加工余量之和,即
z
zi
总
= zi
i =1
n
式中 n–––某一表面的工序(或工步)数目。
--第i道工序加工余量
图4
二、影响加工余量的因素
(一)前工序的工序尺寸公差(Ta)。
(二)前工序形成的表面粗糙度和表面缺陷层深度(Ra+Da)。
(三)前工序形成的形状误差和位置误差(△x、△w)。
(四)本工序的装夹误差(εb)。
三、确定加工余量的方法
(一)查表修正法 (目前应用最广)
(二)经验估计法 (只适用于单件、小批生产)
(三)分析计算法 (目前应用较少)
余量为单边余量
图1
2、旋转表面:
对于轴:Z=da-db 对于孔:Z=db-da
余量为双边余量
图2
• 工序余量和工序尺寸及其公差的 计算公式: (轴) • Z=Zmin+Ta • Zmax=Z+Tb= Zmin+Ta +Tb • 式中 Zmin——最小工序余量 Zmax——最大工序余量 Ta——上工序尺寸的公差 Tb——本工序尺寸的公差
加工的概念
加工余量:在机械加工过程中,从加工表面切去的金属层厚度。
机械制造工艺学习题及答案填空选择

《机械制造工艺学》习题及答案一填充题1 机械制造工艺学的研究对象主要是机械加工中的三大问题即,,。
2 机械加工工艺系统包括,,,等四个方面。
3 工艺过程划分加工阶段的原因是:,,,。
4 在机械制造中,通常将生产方式划分为、、三种类型。
5 确定毛坯加工余量的方法有三种即、、。
大批量生产用。
6 根据作用的不同,基准通常可分为和两大类,定位基准属于。
7 为了保证加工质量,安排机加工顺序的原则是、、、。
8 选择定位粗基准要考虑(1)使各加工面都有一定的和比较均匀的;(2)保证加工面与非加工面的。
9 零件的加工精度包括三方面的内容即、、。
10 零件表层的机械物理性质包括、、。
11 刀具磨损属于误差,可以通过计算后输入来补偿。
12 零件的表面质量包括、、、。
13 工艺系统的振动分为两大类即与,其中振幅随切削用量而变的是。
14 切削加工后,引起表面残余应力的主要原因有、、。
15 精密机床加工精度零件为了减少热变形,加工前应具备两条:、。
15 弯曲的轴进行冷校直后,原来凸出处会产生应力,原来凹下处产生应力。
16 磨削长薄片状工件时若在长度方向两端顶住,在热影响下工件发生的变形,冷后具有的形状误差。
17 解释自激振动的原理主要有两条、。
18 在普通车床上用两顶尖装夹长轴外圆,若机床刚度较低,则工件产生的形状误差;若工件刚度较低,则工件产生的误差。
19 普通车床上对加工精度影响较大的导轨误差是及。
20 切削加工中,若同时用几把刀具加工零件的几个表面则称这种工步为,若一把刀具同时加工几个表面则称这种刀具为。
21 十大原始误差中、、、属于动误差。
22 主轴轴承外环滚道有形状误差则对类机床的加工精度影响较大;内环滚道有形状误差则对类机床的加工精度影响较大。
25 机械加工过程所产生的加工误差,根据性质可分为两大类与。
机床的制造误差属于,刀具尺寸磨损属于,工件材料硬度变化导致的误差为。
26 车床主轴轴向窜动使被加工零件端面产误差,加工螺纹时将造成工件误差。
机械制造工艺学复习题
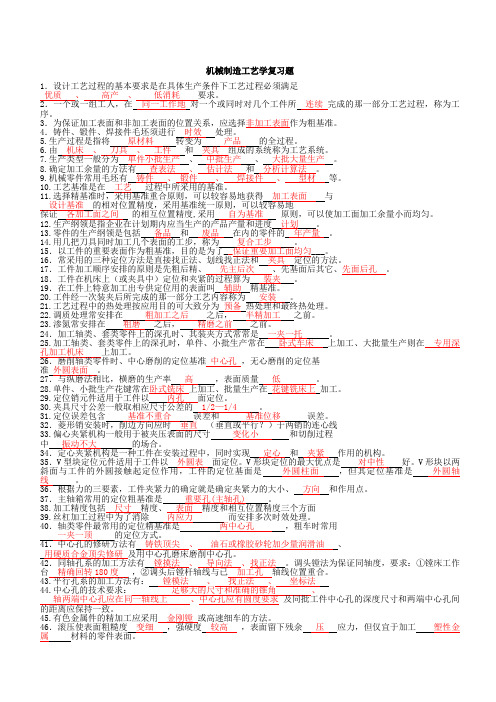
机械制造工艺学复习题1.设计工艺过程的基本要求是在具体生产条件下工艺过程必须满足优质、高产、低消耗要求。
2.一个或一组工人,在同一工作地对一个或同时对几个工件所连续完成的那一部分工艺过程,称为工序。
3.为保证加工表面和非加工表面的位置关系,应选择非加工表面作为粗基准。
4.铸件、锻件、焊接件毛坯须进行时效处理。
5.生产过程是指将原材料转变为产品的全过程。
6.由机床、刀具、工件和夹具组成的系统称为工艺系统。
7.生产类型一般分为单件小批生产、中批生产、大批大量生产。
8.确定加工余量的方法有查表法、估计法和分析计算法。
9.机械零件常用毛坯有铸件、锻件、焊接件、型材等。
10.工艺基准是在工艺过程中所采用的基准。
11.选择精基准时,采用基准重合原则,可以较容易地获得加工表面与设计基准的相对位置精度,采用基准统一原则,可以较容易地保证各加工面之间的相互位置精度,采用自为基准原则,可以使加工面加工余量小而均匀。
12.生产纲领是指企业在计划期内应当生产的产品产量和进度计划。
13.零件的生产纲领是包括备品和废品在内的零件的年产量。
14.用几把刀具同时加工几个表面的工步,称为复合工步。
15.以工件的重要表面作为粗基准,目的是为了__保证重要加工面均匀___。
16.常采用的三种定位方法是直接找正法、划线找正法和夹具定位的方法。
17.工件加工顺序安排的原则是先粗后精、先主后次、先基面后其它、先面后孔。
18.工件在机床上(或夹具中)定位和夹紧的过程算为装夹。
19.在工件上特意加工出专供定位用的表面叫辅助精基准。
20.工件经一次装夹后所完成的那一部分工艺内容称为安装。
21.工艺过程中的热处理按应用目的可大致分为预备热处理和最终热处理。
22.调质处理常安排在粗加工之后之后,半精加工之前。
23.渗氮常安排在粗磨之后,精磨之前之前。
24.加工轴类、套类零件上的深孔时、其装夹方式常常是一夹一托。
25.加工轴类、套类零件上的深孔时,单件、小批生产常在卧式车床上加工、大批量生产则在专用深孔加工机床上加工。
机械加工余量

机械加工余量机械加工余量,通常指零件在加工过程中留下的一定尺寸或形状偏差,它是为了确保零件在加工完成后符合设计要求,以便进行后续的装配、检测,防止零件因加工尺寸不足或过大而无法使用。
机械加工余量是一个重要的概念,对于机械加工工艺的控制和零部件设计起着十分关键的作用。
具体而言,机械加工余量有以下几个方面:1.设计时的余量在机械设计时,就要为加工余量留出一定的设计空间。
这主要包括对零件的几何形状、加工工艺、加工设备等进行考虑。
通常情况下,对于普通的零件,其形状偏差应控制在0.1mm以内,对于精密零件则要在0.01mm以内。
2.加工技术中的余量加工技术中的余量主要指在机床上进行切削或磨削过程中,由于刀具磨损、机床刚度等因素的影响,所导致的零件加工尺寸与设计尺寸的偏差。
在实际操作中,加工技术中的余量可以通过调整刀具切削角度或者加工速度等措施来进行控制。
3.热变形对加工余量的影响在加工加热敏感的金属材料时,由于加热时材料发生热膨胀,会导致加工余量发生偏差。
这时,加工人员可以通过调整加工参数、减少加热时间、加强冷却等方法来调整加工余量。
机械加工余量的控制非常重要,一定程度上,它也是衡量机械加工技术水平的重要标准。
而在实际应用过程中,如何掌握机械加工余量的大小和控制方法,影响着机械零件的质量和生产效率。
以下是一些有关机械加工余量控制的方法:1.合理选择切削工艺参数在进行机械加工时,加工人员应该合理选择切削工艺参数,包括切削速度、进给量、切削深度等方面,以达到减少加工余量的目的。
2.优化刀具设计优化刀具设计也是减小机械加工余量的重要方面。
合理的切削角度可以减少切削力和变形,从而控制加工余量。
此外,刀具的刃磨加工精度也需要达到精度级别,从而减小加工余量。
3.控制机床几何精度机床几何精度是影响加工余量的重要因素之一。
因为机床精度的影响,加工出来的零件在尺寸、直线度、平行度、垂直度等方面都会受到不同程度的影响,进而导致加工余量的产生。
机械加工工序间余量

3.2机械加工工序间余量本章规定的常见工序间加工留量作为本公司编制机械加工工序及有关单位确定加工余量的依据,如有特殊情况可由工艺部门另作规定。
3.2.1切料头时留芯部安全尺寸如图3.2-1所示,当工件材料σs=400~450MPa时,切料头留芯部安全尺寸d按表3.2-1选取。
表3.2-1 中数据用公式d3≈5Q l/σs计算,式中的σs材料屈服极限。
如为其它材料时,应根据其σs大小将安全尺寸d应乘上修正系数K,K值按表3.2-2选取。
表3.2-1 mm注:①、切料头安全尺寸d应按h13级精度加工。
②、切料头当接近安全尺寸时严禁啃刀。
③、切料头前床面上必须垫适当数量的枕木,在架中心架或托辊切断时,直径可以适当缩小。
表3.2-23.2.2 各类锯片及铣刀切口宽度及切割规格各类锯片及铣刀宽度及切割规格见表3.2-3。
表3.2-3 mm注:圆锯能切割方料的最大尺寸为圆料的70%。
3.2.3 车床切断刀及插床切口刀的切口宽度及切割深度车床切断刀及插床切口刀的切口宽度及切割深度见表3.2-4。
表3.2-4 mm注:车床、插床的刀具宽度可以适当磨小。
如果设计专用切断刀时宽度可以适当减少。
3.2.4箱体、架体零件粗加工后人工时效余量箱体、架体零件粗加工后人工时效余量见表3.2-5 。
表3.2-5 mm注:①、适用于铸铁件粗加工后人工时效及粗精加工分开如床身、立柱、工作台、箱体等,不适用于容易变形的薄板。
②、自然时效余量为表中数值的0.5~0.6倍。
③、铸钢件可按表中数值增加1~2mm。
3.2.5 平键修配余量平键修配余量见表3.2-6。
表3.2-6 mm注:①、间隙配合的导向键及切向键不留修配余量。
②、斜健的两侧不留修配余量,斜面上一般情况设计时已留有0.3~0.5mm的修配量,如图纸上未留量时,工艺上应留量。
3.2.6 孔的钻、扩、铰余量孔的钻、扩、铰余量见表3.2-7.表3.2-7 mm注:①、大于Φ30mm的孔,可在二次走刀中钻出,先用较小钻头预钻孔。
机械加工余量选择方法

机械加工余量选择方法1.基本余量法基本余量法是机械加工中最常用的一种方法。
根据经验和相关的机械加工标准,确定不同材料或零件类型应有的基本余量值。
例如,在车削加工中,对外圆进行车削时,可选择的基本余量为0.5-1.5mm;而对内圆进行车削时,可选择的基本余量为0.1-0.3mm。
根据实际情况,合理选择基本余量值,以确保零件尺寸的精度和质量。
2.递减余量法递减余量法是根据机械加工过程中的实际情况,逐步减小加工余量的方法。
根据零件尺寸的精度要求和加工工艺的特点,通过试验和实践,逐渐调整和减小加工余量,以满足零件的尺寸要求。
这种方法在一些对尺寸精度要求较高的零件加工中比较常用,可以尽量减小加工余量,提高加工精度。
3.检测修正法检测修正法是一种基于实际测量结果的余量选择方法。
在零件加工结束后,通过测量零件的尺寸,与设计尺寸进行比较。
根据实际测量结果,修正设计尺寸和加工余量,以满足零件尺寸要求。
这种方法相对较为灵活,可以根据实际情况进行调整和修正,适用于对尺寸要求较为严格的零件加工。
4.确定余量法确定余量法是通过实验和计算,根据工艺参数和材料性质,确定加工余量的具体数值。
根据材料的热膨胀系数、强度和硬度等特性,结合机械加工过程中材料的变形和切削刃的磨损等因素,采用数学模型和计算方法,确定合适的加工余量。
这种方法相对较为精细和科学,适用于复杂零件和高精度加工。
在实际机械加工中,选择合适的机械加工余量方法,对于确保零件尺寸的精度和质量至关重要。
工程师和技术人员应根据具体的加工要求、材料特性和加工工艺,合理选择和调整机械加工余量,以获得满足要求的加工结果。
同时,还需要结合实际情况,不断总结和改进机械加工余量的选择方法,提高加工效率和质量。
加工余量与工序尺寸的确定和基准--2011
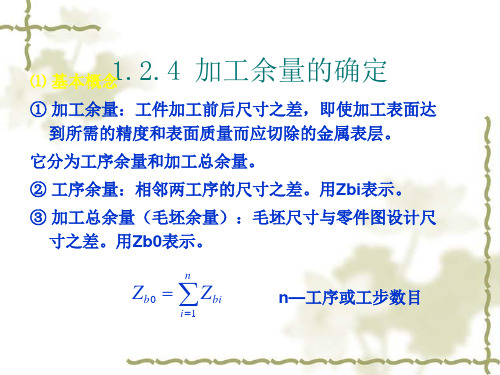
③ 尺寸链的分类 a) 按应用场合来分 工艺尺寸链:全部组成环为同一零件的设 计尺寸所形成的尺寸链,如图2。 特点:所有尺寸都在一个零件上 装配尺寸链:全部组成环为不同零件的工 艺尺寸所形成的尺寸链,如图1。 特点:每一个尺寸都分布在不同的零件上
b) 按各环所处的空间位置来分 直线尺寸链:尺寸链中各环位于同一平面内 且相互平行,最为常规最基本的尺寸链。 平面尺寸链:尺寸链中各环位于同一平面或 几个相互平行平面内,但某些组成环不平行 于封闭环的尺寸链。 空间尺寸链:尺寸链中各环不在同一平面且 互不平行。
极限尺寸的计算:
A0max Az max Aj min
A0min Az min Aj max
⑵ 工序尺寸及其公差的确定 ① 工序基准与设计基准重合,即对同一表面进行多
次加工
这种工序尺寸计算较简单,只需根据各工序的加 工余量就可以算出各工序的基本尺寸。其计算顺 序是由最后一道工序开始逐步向前推算。 例:加工某一个钢制零件上的一个孔,其设计尺 0 寸为 72.50.03 mm,表面粗糙度为Ra0.4。现经过 粗镗、半精镗、精镗、粗磨和精磨五次加工,计 算各次加工的工序尺寸及其公差。
尺寸链中在装配过程或加工过程最后形成 的一环。
c) 组成环:加工或装配时直接影响封闭环 精度的各原始尺寸。
尺寸链中对封闭环有影响的全部环。
增环:尺寸链中的组成环,由于该环的变 动引起封闭环同向变动。 减环:尺寸链中的组成环,由于该环的变 动引起封闭环反向变动。
d) 尺寸链的两个主要功能 公差分配(反计算):已知封闭环基本尺寸 及公差,组成环基本尺寸,求解组成环的公 差。 公差控制(正计算):已知组成环基本尺寸 及公差,核算封闭环尺寸及公差。
机械加工余量和锻件尺寸公差的确定.
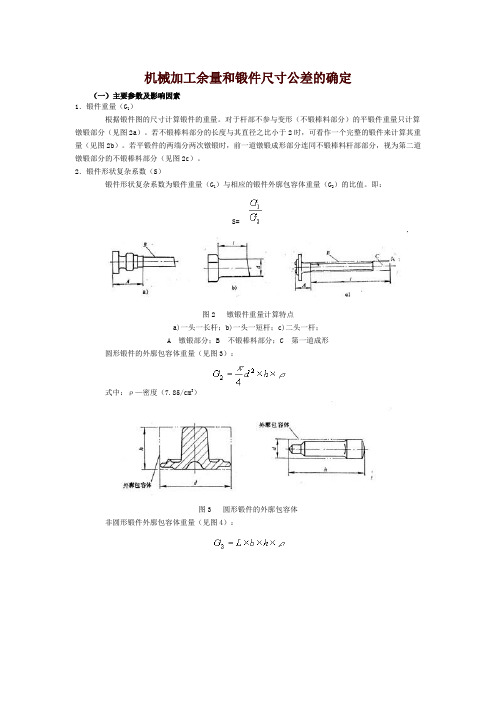
机械加工余量和锻件尺寸公差的确定(一)主要参数及影响因素1.锻件重量(G1)根据锻件图的尺寸计算锻件的重量。
对于杆部不参与变形(不锻棒料部分)的平锻件重量只计算镦锻部分(见图2a)。
若不锻棒料部分的长度与其直径之比小于2时,可看作一个完整的锻件来计算其重量(见图2b)。
若平锻件的两端分两次镦锻时,前一道镦锻成形部分连同不锻棒料杆部部分,视为第二道镦锻部分的不锻棒料部分(见图2c)。
2.锻件形状复杂系数(S)锻件形状复杂系数为锻件重量(G1)与相应的锻件外廓包容体重量(G2)的比值。
即:S=图2 镦锻件重量计算特点a)一头一长杆;b)一头一短杆;c)二头一杆;A 镦锻部分;B 不锻棒料部分;C 第一道成形圆形锻件的外廓包容体重量(见图3):式中:ρ—密度(7.85/cm3)图3 圆形锻件的外廓包容体非圆形锻件外廓包容体重量(见图4):图4 非圆形锻件外廓包容体锻件形状复杂系数分为四级:简单:S1>0.63~1一般:S2>0.32~0.63较复杂:S3>0.16~0.32复杂:S4≤0.16特例:当锻件为薄形圆盘或法兰件(见图5a),其圆盘厚度和直径之比L/d≤0.2时,取形状复杂系数S4。
当L1/d1≤0.2或L2/d2>4时(见图5b),采用形状复杂系数S4。
当冲孔深度大于直径的1.5倍时,形状复杂系数提高一级。
图5 锻件形状复杂特例3.锻件的材质系数锻件的材质系数分为二级:M1:钢的含碳量小于0.65%的碳钢,或合金元素总含量小于3.0%的合金钢。
M2:钢的含碳量大于或等于0.65%的碳钢,或合金元素总含量大于或等于3.0%的合金钢。
4.零件的机械加工精度零件表面粗糙度低于R a1.6,机械加工余量从余量表查得;粗糙度高于R a1.6,加工余量要适当加大;对扁薄截面或在锻件相邻部位截面变化较大的零件(如图6),在长度L范围内应适当加大局部的余量。
图6 应局部增大余量的零件5.加热条件采用煤气或油炉加热钢坯时,机械加工余量和公差从余量表和公差表查得;当采用煤加热钢坯,或经二火进行加热时,适当增大加工余量和公差。
机械加工技术题库 3

《机械加工技术》试题库项目一机械加工的基本概念知识要点:基本概念一、填空1、工艺过程是指生产过程中直接改变生产对象的、、和等,使之成为成品或半成品的过程。
2、一个或一组工人,在一个工作地或一台机床上对于一个或同时对几个工件所连续完成的那一部分工艺过程称为。
*3、工件在机床上或夹具中完成定位并夹紧的过程称为。
车削轴类零件,调头一次,次安装。
4、工件相对于机床或刀具每占据一个加工位置,称为。
5、加工余量大时,刀具对工件每一次切削称为一次。
6、企业在计划期内的产品产量,称为。
7、生产类型是企业生产专业化程度的分类。
根据生产的特点,企业的生产可分为三种基本类型:、和及。
二、判断()1、原材料的组织、运输、保管等属于工艺过程的内容。
()2、工件调头加工时,因加工不连续,应算两道工序。
()3、工件先找正位置再夹紧算作一次安装。
()4、工件在工作台上每占据一个加工位置,就算作一个工位。
()*5、单件小批生产采用金属模机器造型,毛坯精度高,加工余量小。
()*6、大批大量生产中,对操作工人的技术要求也提高。
()*7、大批大量生产往往生产对象的生产成本较高。
三、解释名词*1、工艺过程2、工序3、工步4、安装四、简答题1、什么是工序划分工序的依据是什么**2、大批大量生产可设计采用专用工夹量具,而中小批生产往往采用通用设备,说明理由。
知识要点;机械加工的生产率一、填空1、时间定额是在一定生产技术组织条件下,规定生产所需的时间。
2、目前,多数企业采用这一劳动定额形式。
3、单件时间包括、辅助时间、布置工作地时间、休息生理需要时间。
二、判断()1、减小或重合行程长度可以缩减基本时间,提高生产率。
()2、采用平行或顺序多件加工可缩短加工时间,提高生产率。
项目二金属切削基础知识知识要点:切削运动与切削要素一、填空1、切削运动按在切削加工中所起作用不同分为:和。
2、切削运动中切削速度最高、消耗功率最大的运动是。
如车削加工中的运动。
机械加工工艺-加工余量、工序尺寸及公差
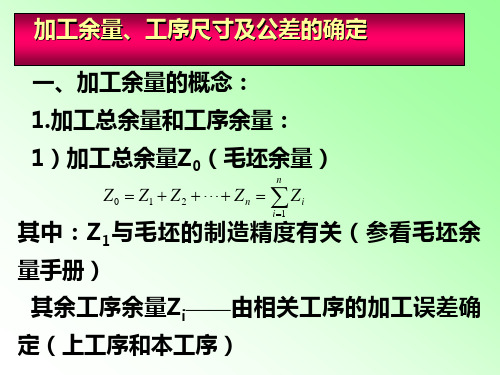
(一)设计 1、合理的结构工艺性、加工精度、表面
粗糙等。 2、零件、部件、产品的三化程度(通用、
标准、系列) (二)先进的工艺及设备
1、毛坯 2、机加工 3、装配
(三)先进的管理:计划、准备、服务、技术、
质量、经济分析等。
提高机加工生产率的工艺途径:
(一)缩短t基 1、(V、F、ap)↑。 2、多刀、多刃、及单刀多件等。
加工余量、工序尺寸及公差的确定
一、加工余量的概念: 1.加工总余量和工序余量: 1)加工总余量Z0(毛坯余量)
n
Z0 Z1 Z2 Zn Zi i 1
其中:Z1与毛坯的制造精度有关(参看毛坯余 量手册)
其余工序余量Zi——由相关工序的加工误差确 定(上工序和本工序)
2)工序余量Zi——相邻两工序基本尺寸之差;
求:本工序工序尺寸L2(渗碳深度) 分析:渗碳层保留深度L0 —单边值(图面尺寸)
渗碳深度L2—单边值。 按尺寸链图,代入公式求解得:L2=0.7+0.025
+0.008
(四)、余量校核 各工序中加工余量由查表及经验确定。 因为各工序尺寸的公差存在,实际余量是变化 的。 例图1-49,
1、工艺路线 1)精车A面,由B处切断。 2)以A面定位,精车B面。 3)以B面定位,磨A面。 4)以A面定位,磨B面。
三、用图表法确定工序尺寸及余量 适用于当零件同一方向尺寸较多的复杂情况。 如:工序多,工序基准转换多,工序中基准不 重合需用尺寸链计算,公差,余量确定复杂。 步骤: (一)绘制加工过程尺寸联系图
1、画出工件简图,标注相关设计尺寸。 2、按加工工序列表填写工艺过程,画加工符 号(箭头等)。 (二)工艺尺寸链查找
尺寸链中封闭环只有一个,用L0表示。 工艺尺寸链中的封闭环的定义见P.53倒10行。
加工余量的确定
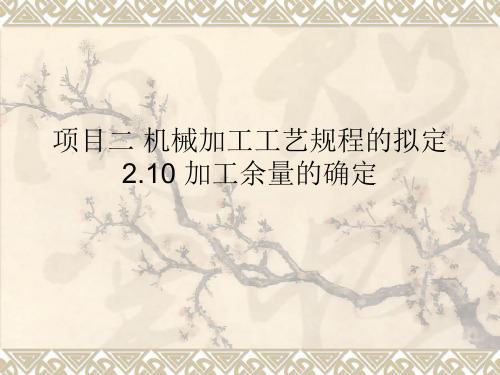
加工顺序的安排 (1)切削加工顺序安排原则 1)先粗后精
粗精加工分开,按照粗加工—半精加工—精加 工—光整加工顺序。 2)先主后次 ①主要表面加工容易出废品,减少工时浪费。 ②次要表面安排在半精加工之后。 3)先面后孔 平面大而平整容易定位,利于保证相互位置精度。 4)先基面后其它 第一工序首先加工基面,再用精基面加工其它。
简单的工序(或工步)尺寸确定:
根据各工序(或工步)加工余量就可算出各工 序(或工步)的基本尺寸,“由后往前推” 其计算顺序是由最后一道工序(或工步)开始 向前推算。各中间工序(或工步)尺寸的公 差按加工方法的经济精度确定,并按“入体 原则”标注。
1.根据该表面的经济精度确定加工方法 2.查表确定工序余量和毛坯余量(查工艺手册) 3.查表(同1表)确定各工序尺寸公差等级和表面粗糙 度 4.计算工序尺寸,由后往前推算到毛坯尺寸, 孔的工序尺寸=后道工序尺寸-后道工序余量 轴的工序尺寸=后道工序尺寸+后道工序余量 5.标注工序尺寸,终工序尺寸按照零件图标注,中间
2R 2(R - δ) 2δ
上工序留下的形状误差的影响
δ
R-δ R
轴的弯曲对加工余量的影响
旋转轴中心线 工件中心线
5)本工序加工时的安装误差εb
返回本章目录
e
2e
2.确定加工余量的方法
经验估算法 查表修正法 分析计算法
中间工序尺寸及公差的确定
采用“单向入体原则”来标注 包容面(孔)――单向正偏差标注,基本尺 +0.03 寸等于最小极限尺寸 如孔1000 被包容面(轴)——单向负偏差标注,基本 0 尺寸等于最大极限尺寸。 如轴 20-0.01 中心距离和毛坯尺寸按双向偏差标注 如100±0.5
如何确定铸件加工余量【干货】
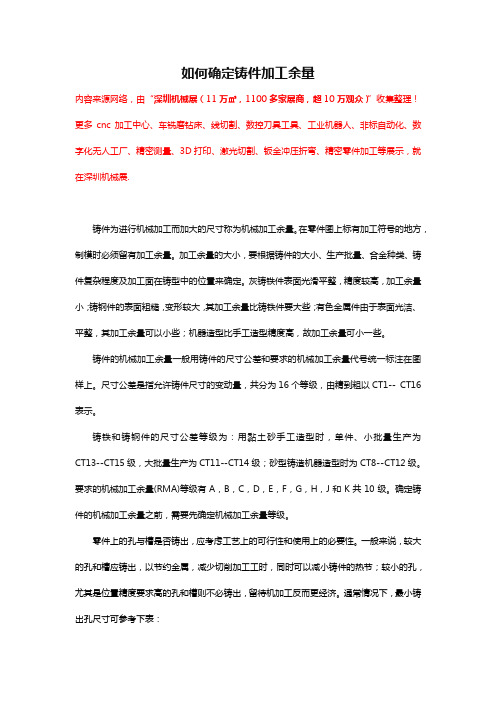
如何确定铸件加工余量内容来源网络,由“深圳机械展(11万㎡,1100多家展商,超10万观众)”收集整理!更多cnc加工中心、车铣磨钻床、线切割、数控刀具工具、工业机器人、非标自动化、数字化无人工厂、精密测量、3D打印、激光切割、钣金冲压折弯、精密零件加工等展示,就在深圳机械展.铸件为进行机械加工而加大的尺寸称为机械加工余量。
在零件图上标有加工符号的地方,制模时必须留有加工余量。
加工余量的大小,要根据铸件的大小、生产批量、合金种类、铸件复杂程度及加工面在铸型中的位置来确定。
灰铸铁件表面光滑平整,精度较高,加工余量小;铸钢件的表面粗糙,变形较大,其加工余量比铸铁件要大些;有色金属件由于表面光洁、平整,其加工余量可以小些;机器造型比手工造型精度高,故加工余量可小一些。
铸件的机械加工余量一般用铸件的尺寸公差和要求的机械加工余量代号统一标注在图样上。
尺寸公差是指允许铸件尺寸的变动量,共分为16个等级,由精到粗以CT1-- CT16表示。
铸铁和铸钢件的尺寸公差等级为:用黏土砂手工造型时,单件、小批量生产为CT13--CT15级,大批量生产为CT11--CT14级;砂型铸造机器造型时为CT8--CT12级。
要求的机械加工余量(RMA)等级有A,B,C,D,E,F,G,H,J和K共10级。
确定铸件的机械加工余量之前,需要先确定机械加工余量等级。
零件上的孔与槽是否铸出,应考虑工艺上的可行性和使用上的必要性。
一般来说,较大的孔和槽应铸出,以节约金属,减少切削加工工时,同时可以减小铸件的热节;较小的孔,尤其是位置精度要求高的孔和槽则不必铸出,留待机加工反而更经济。
通常情况下,最小铸出孔尺寸可参考下表:内容来源网络,由“深圳机械展(11万㎡,1100多家展商,超10万观众)”收集整理!更多cnc加工中心、车铣磨钻床、线切割、数控刀具工具、工业机器人、非标自动化、数字化无人工厂、精密测量、3D打印、激光切割、钣金冲压折弯、精密零件加工等展示,就在深圳机械展.。
机械加工工序余量计算方法

精车,滚压
IT6-7
0.2-1.6
粗车,半精车,粗磨,精磨,镜面磨削
研磨
超精加工
抛光
0.1-0.4
9、螺旋齿轮及双曲线齿轮的精加工余量
10、圆锥齿轮的加工余量
11、蜗轮的精加工余量
12、齿轮孔的磨削加工余量
13、蜗杆的精加工余量
一、适用范围及选择原则
1、适用范围
适用于一般精度、刚性较好,没有相同工序(如:粗车,调质,半精车,淬火,粗磨,油煮定性,半粗磨,研磨)的零件,对于关健性精密零件(如:主轴,丝杆等)或刚性差的零件中关键性精密尺寸,由于需采用多次相同性质的加工,其加工余量应根据具体情况考虑,不能完全搬用
5
D≥100
4.5
5
5.5
6
说明:1、本表摘自《一般工艺规定及指导资料》
2、实体料d=0
3、轴件中心孔切除余量
表4
外径
中心孔d
(GB145)
中心孔切除
余量
外径
中心孔d
(GB145)
中心孔切除
余量
≤25
2
6.5
66-70
5
13.5
26-40
3
10.0
71-100
40-65
4
12.5
101
6
17.0
说明:1、本表摘自《机械加工余量实用手册》[表5-8]
普通车床
20-25
用钢料毛坯制造摩擦片、瓦尔片类零件
普通车床
20-25
同轴度允差小于0.06之精车零件
普通车床
20-25
套类零件
六角车床
30
说明:1、除表列零件类型外均不留卡头
机械加工时加工余量的确定

机械加工时加工余量的确定发布:2011-08-23 | 作者: | 来源: liujiada | 查看:320次| 用户关注:零件加工工艺路线确定后,在进一步安排各个工序的具体内容时,应正确地确定工序的工序尺寸,为确定工序尺寸,首先应确定加工余量。
一、加工余量的概念由于毛坯不能达到零件所要求的精度和表面粗糙度,因此要留有加工余量,以便经过机械加工来达到这些要求。
加工余量是指加工过程中从加工表面切除的金属层厚度。
加工余量分为工序余量和总余量。
(一)工序余量工序余量是指某一表面在一道工序中切除的金属层厚度。
1.工序余量的计算零件加工工艺路线确定后,在进一步安排各个工序的具体内容时,应正确地确定工序的工序尺寸,为确定工序尺寸,首先应确定加工余量。
一、加工余量的概念由于毛坯不能达到零件所要求的精度和表面粗糙度,因此要留有加工余量,以便经过机械加工来达到这些要求。
加工余量是指加工过程中从加工表面切除的金属层厚度。
加工余量分为工序余量和总余量。
(一)工序余量工序余量是指某一表面在一道工序中切除的金属层厚度。
1 .工序余量的计算工序余量等于相邻两工序的工序尺寸之差。
对于外表面(见图 3 -75a )Z=a - b对于内表面(见图3-75b )Z=b — a式中Z ——本工序的工序余量(mm) ;a ——前工序的工序尺寸(mm );b ——本工序的工序尺寸(mm) 。
上述加工余量均为非对称的单边余量,旋转表面的加工余量为双边对称余量。
对于轴(图3 -75 c )Z=d a — d b对于孔(图3-75d )Z=d b — d a式中Z ——直径上的加工余量(mm );d a ——前工序的加工直径(mm );d b ——本工序的加工直径(mm )。
当加工某个表面的工序是分几个工步时,则相邻两工步尺寸之差就是工步余量。
它是某工步在加工表面上切除的金属层厚度。
2 .工序基本余量、最大余量、最小余量及余量公差由于毛坯制造和各个工序尺寸都存在着误差,加工余量也是个变动值。
加工余量、工序尺寸及其公差的确定

2、影响加工余量的因素
1、上道工序加工表面的表面质量 2、上道工序的尺寸公差 Ta
2、影响加工余量的因素
1、上道工序加工表面的表面质量
2、上道工序的尺寸公差 Ta
3、本道工序的安装误差ε b
上述各项误差和缺陷都是上道工序 形成的,为能将其全部切除,还要考虑 本工序的装夹误差ε b的影响。如右图 所示,由于三爪自定心卡盘定心不准, 使工件轴线偏离主轴旋转轴线e值,造 成加工余量不均匀,为确保将前工序的 各项误差和缺陷全部切除,直径上的余 量应增加2e。装夹误差ε b的数量,可 在求出定位误差、夹紧误差和夹具的装 夹误差后求得。
4.工序尺寸及其公差的确定
1)基准重合时,工序尺寸及其公差的计算 生产上绝大部分加工面都是在基准重合(工艺基准和设计
基准重合)的情况下进行加工的,基准重合情况下工序尺寸与 公差的确定过程如下:
(1)确定毛坯总余量和各加工工序的工序余量 (2)确定工序基本尺寸
(3)确定工序公差 (4)标注工序尺寸公差 最终加工工序尺寸的公差按设计尺寸标注,其余工序尺寸 公差按“入体原则”标注。
56 2
工序尺寸及其公差的确定实例2
某轴直径为ф 60mm,其尺寸精度要求为IT5,表面粗 糙度要求为Ra0.04μ m,并要求高频淬火,毛坯为锻件。其 工艺路线为:粗车—半精车——高频淬火—粗磨——精 磨——研磨。现在来计算各工序的工序尺寸及公差。
各工序的工序尺寸及公差的确定
工序 名称
研磨
4.工序尺寸及其公差的确定
1)基准重合时,工序尺寸及其公差的计算 生产上绝大部分加工面都是在基准重合(工艺基准和设计
基准重合)的情况下进行加工的,基准重合情况下工序尺寸与 公差的确定过程如下:
机械加工余量标准

3.2机械加工余量标准25EQY —19-19991.主题内容与适用范围本标准规定了磨削加工的加工余量。
本标准适用于磨削各类材料时的加工余量。
2. 技术内容加工余量表(一)厚度4以上的平面磨削余量(单面)说明:1.二次平面磨削余量乘系数1.52.三次平面磨削余量乘系数23.厚度4以上者单面余量不小于0.5-0.84.橡胶模平板单面余量不小于0.7毛坯加工余量表(二)I:园棒类:(1)工件的最大外径无公差要求,光洁度在▽以下,例:不磨外圆的凹模带台肩的凸模、凹模、凸凹模以及推1.63.2杆、推销、限制器、托杆、各种螺钉、螺栓、螺塞、螺帽外径必须滚花者。
(毫米)当D <36时并不适应于调头夹加工,在加工单个工件时,应在L 上加夹头量10-15。
(2)工件的最大外径有公差配合要求,光洁度在▽以上,例如:外圆须磨加工的凹模,挡料销、肩台须磨加工的凸模或凸凹模等。
(毫米)当D <36时,不适合调头加工,在加工单个零件时,应加夹头量10-15。
毛坯加工余量表(三)Ⅱ:圆形锻件类(不需锻件图)(1)不淬火钢表面粗糙度在▽以下无公差配合要求者,例如:固定板、退料板等。
(毫米)注:表中的加工余量为最小余量,其最大余量不得超过厂规定标准。
毛坯加工余量表(四)Ⅲ:矩形锻件类:表内的加工余量为最小余量,其最大余量不得超过厂规定标准。
3.2 平面、端面磨削加工余量表(五)一、平面平面每面磨量二、端面端面每面磨量注:本表适用于淬火零件,不淬火零件应适当减少20-40%粗加工的表面粗糙度不应低于▽如需磨两次的零件,其磨量应适当增加10-20%环形工件磨削加工余量表(六)6.4 1.6 注:φ50以下,壁厚10以上者,或长度为100-300者,用上限φ50-φ100,壁厚20以下者,或长度为200-500者,用上限φ100以上者,壁厚30以下者,或长度为300-600者,用上限长度超过以上界线者,上限乘以系数1.3 加工粗糙度不低于▽,端面留磨量0.5φ6以下小孔研磨量表(七)注:本表只适用于淬火件应按孔的最小极限尺寸来留研磨量 淬火前小孔需占铰粗糙度▽以上当长度e 小于15毫米时,表内数值应加大20-30%导柱衬套磨削加工余量表(八)镗孔加工余量表(九)附注:当一次镗削时,加工余量应该是粗加工余量加工精加工余量。
- 1、下载文档前请自行甄别文档内容的完整性,平台不提供额外的编辑、内容补充、找答案等附加服务。
- 2、"仅部分预览"的文档,不可在线预览部分如存在完整性等问题,可反馈申请退款(可完整预览的文档不适用该条件!)。
- 3、如文档侵犯您的权益,请联系客服反馈,我们会尽快为您处理(人工客服工作时间:9:00-18:30)。
精密零件加工确定加工余量的方法有哪些
精密零件加工在实际工作中,确定加工余量的方法有哪些?下面小编来为您讲解:
1、经验估计法。
根据工艺人员本身积累的经验确定加工余量。
一般为了防止余量过小而产生废品,所估计的余量总是偏大。
常用于单件、小批量生产。
2、查表法。
根据有关手册提供的加工余量数据,再结合本厂生产实际情况加以修正后确定加工余量。
这是各工厂广泛的,采用的方法。
3、分析计算法。
根据理论公式和一定的试验资料,对影响零件加工余量的各因素进行分析、计算来确定加工余量。
这种方法较合理,但需要全面可靠的试验资料,计算也较复杂。
一般只在材料十分贵重或少数大批、大量生产的工厂中采用。