槽液各成分分析方法
三 酸 抛 光 槽 硝 酸 浓 度 分 析
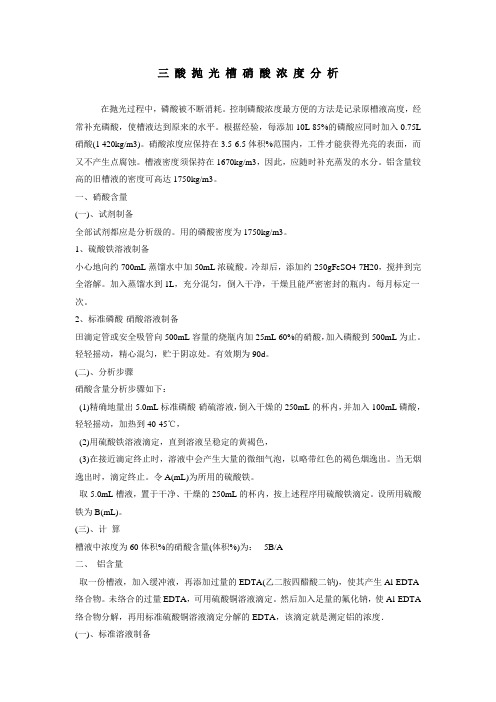
三酸抛光槽硝酸浓度分析在抛光过程中,磷酸被不断消耗。
控制磷酸浓度最方便的方法是记录原槽液高度,经常补充磷酸,使槽液达到原来的水平。
根据经验,每添加10L 85%的磷酸应同时加入0.75L 硝酸(1 420kg/m3)。
硝酸浓度应保持在3.5-6.5体积%范围内,工件才能获得光亮的表面,而又不产生点腐蚀。
槽液密度须保持在1670kg/m3,因此,应随时补充蒸发的水分。
铝含量较高的旧槽液的密度可高达1750kg/m3。
一、硝酸含量(一)、试剂制备全部试剂都应是分析级的。
用的磷酸密度为1750kg/m3。
1、硫酸铁溶液制备小心地向约700mL蒸馏水中加50mL浓硫酸。
冷却后,添加约250gFeSO4·7H20,搅拌到完全溶解。
加入蒸馏水到1L,充分混匀,倒入干净,干燥且能严密密封的瓶内。
每月标定一次。
2、标准磷酸-硝酸溶液制备田滴定管或安全吸管向500mL容量的烧瓶内加25mL 60%的硝酸,加入磷酸到500mL为止。
轻轻摇动,精心混匀,贮于阴凉处。
有效期为90d。
(二)、分析步骤硝酸含量分析步骤如下:(1)精确地量出5.0mL标准磷酸·硝硫溶液,倒入干燥的250mL的杯内,并加入100mL磷酸,轻轻摇动,加热到40-45℃,(2)用硫酸铁溶液滴定,直到溶液呈稳定的黄褐色,(3)在接近滴定终止时,溶液中会产生大量的微细气泡,以略带红色的褐色烟逸出。
当无烟逸出时,滴定终止。
令A(mL)为所用的硫酸铁。
取5.0mL槽液,置于干净、干燥的250mL的杯内,按上述程序用硫酸铁滴定。
设所用硫酸铁为B(mL)。
(三)、计算槽液中浓度为60体积%的硝酸含量(体积%)为: 5B/A二、铝含量取一份槽液,加入缓冲液,再添加过量的EDTA(乙二胺四醋酸二钠),使其产生Al-EDTA 络合物。
未络合的过量EDTA,可用硫酸铜溶液滴定。
然后加入足量的氟化钠,使Al-EDTA 络合物分解,再用标准硫酸铜溶液滴定分解的EDTA,该滴定就是测定铝的浓度.(一)、标准溶液制备所用的全部试剂都应是分析试剂级的。
棕化工艺问题解析指南
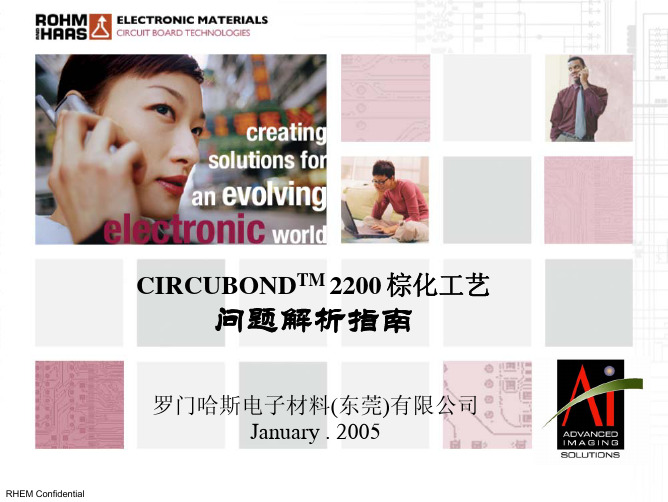
问题解析指南
罗门哈斯电子材料(东莞)有限公司 January . 2005
RHEM Confidential
CIRCUBOND 2200棕化工艺问题解析指南
TM
故障排除步骤
分析所有槽液各成分含量 DES中的退膜液 检查下列条件是否变化 流速 温度 液位 铜箔类型 H2O2浓度或 预浸液中铜含量 层压板周期
TM
轮印
输送轮缺失或被更换 输送轮位置设计不合理 滚轮脏 前工序带来轮印 H2O2浓度低 水平线棕化段流量太 小
RHEM Confidential
检查并清洁 保证输送轮交错排列并且不会阻 碍药水流动 检查并清洁 检查前工序 分析并调整 加大流量
CIRCUBOND 2200棕化工艺问题解析指南
TM
棕化不良
RHEM Confidential
CIRCUBOND 2200棕化工艺问题解析指南
TM
综述
开缸:
• 在开缸时,2218A、2218B中的成份将可能因DI水温度低而沉淀 出来,导致分析结果偏低。如果在此时补加药水,待温度升高 ,成份重新溶解出来就会造成实际浓度偏高。 为了避免以上情况发生,请在配槽时第一步先加入浓H2SO4,再加 入2218A及2218B。 请使用经过处理或浸泡清洗的过滤芯,以免将过滤芯中的粘合剂 和润滑剂带入槽液。未经过处理的过滤芯可能带来大量的泡沫和 发亮的棕化涂层。
CIRCUBOND 2200棕化工艺问题解析指南
TM
金色涂层
没有或2218B浓度低 分析并调整 分析并调整
2218A浓度太高
RHEM Confidential
CIRCUBOND 2200棕化工艺问题解析指南
硫酸亚锡电解着色相关技术内容
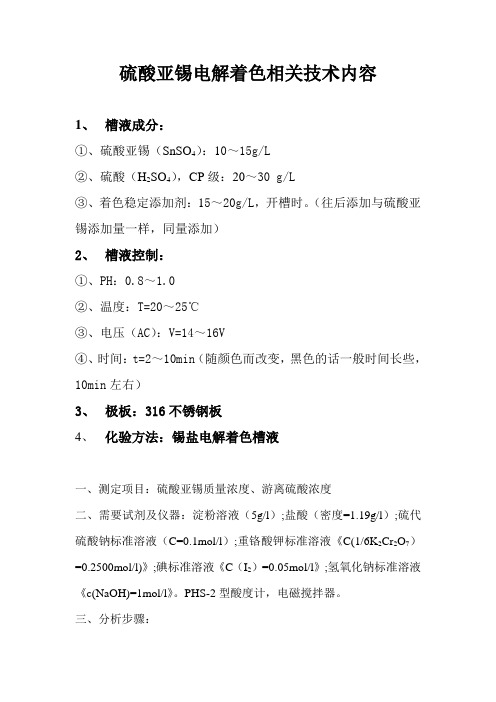
硫酸亚锡电解着色相关技术内容1、槽液成分:①、硫酸亚锡(SnSO4):10~15g/L②、硫酸(H2SO4),CP级:20~30 g/L③、着色稳定添加剂:15~20g/L,开槽时。
(往后添加与硫酸亚锡添加量一样,同量添加)2、槽液控制:①、PH:0.8~1.0②、温度:T=20~25℃③、电压(AC):V=14~16V④、时间:t=2~10min(随颜色而改变,黑色的话一般时间长些,10min左右)3、极板:316不锈钢板4、化验方法:锡盐电解着色槽液一、测定项目:硫酸亚锡质量浓度、游离硫酸浓度二、需要试剂及仪器:淀粉溶液(5g/l);盐酸(密度=1.19g/l);硫代硫酸钠标准溶液(C=0.1mol/l);重铬酸钾标准溶液《C(1/6K2Cr2O7)=0.2500mol/l)》;碘标准溶液《C(I2)=0.05mol/l》;氢氧化钠标准溶液《c(NaOH)=1mol/l》。
PHS-2型酸度计,电磁搅拌器。
三、分析步骤:1、硫酸亚锡质量浓度取10.0ml槽液于250ml锥形瓶中,加入20ml盐酸(密度=1.19g/ml)、50ml水,混匀,滴入数滴淀粉溶液,用经标定的约C(I2)=0.05mol/l的碘标准溶液滴至试液由无色变为蓝色即为终点,读取消耗的碘标准溶液的体积(V1),按下式计算硫酸亚锡质量浓度:C=21.477V1C(I2)g/l式中,C(I2)为碘标准的物质的量浓度。
2、游离硫酸质量浓度。
取50.0ml槽液于400ml锥形瓶中,加200ml水,摇匀。
插入玻璃电极(最好在磁力搅拌下),用1mol/l氢氧化钠滴定至试液PH为2.1为终点,读取消耗的氢氧化钠标准溶液的体积(V2).按下式计算游离硫酸的浓度。
C=0.98V2C(NaOH)C(NaOH):氢氧化钠的标准溶液的浓度。
PTH-药水分析与补加计算方法

(控制值-分析值)*V/500
NaOH(g/l)=滴定ml數×4.0
(控制值-分析值)*V/350
H2SO4(%)=滴定ml數×0.133
(控制值-分析值)*V*2
H2O2(%)=滴定ml數×0.312
(控制值-分析值)*V
中和剂-2N(ml/l)=滴定ml數×9.4
(控制值-分析值)*V/1000
H2SO4(ml/L)=滴定ml數×2.7
中和槽
取1ml槽液+100ml D.I水+0.4M NH4Fe(SO4)2 20ml+5N-H2SO4 20ml 中和剂-2N 80~120ml/l 加热至沸腾约5min以0.1N-KMnO4滴 至終點由淡黄色转为淡紫色 硫酸(50%) 35~45ml/l 取1ml槽液+100ml D.I水+3-5D M.O. 指示剂→以0.1N-NaOH滴至黄色
槽名
成分
控制范围
分析方法
取50ml槽液加入100ml烧杯+5g 350~450ml/l NaOH,充分搅拌,倒入50ml滴定管中 冷却,读上层溶液ml数. 膨胀槽 取20ml槽液+D.I水50ml+1M-BaCl2 氢氧化钠 6~10g/l 20ml+3-5滴P.P.指示劑→以0.5MHCl滴至无色 将分光仪器打开预热;取0.1ml槽液 Mn7+ 60~80g/l 加入100ml容量瓶中+0.1NKOH至刻 度,摇匀,将分光光度计波长调至 526nm,以0.1M-KOH将分光光度计归 高锰酸钾槽 零,测试样其吸光度为A;再调至波长 Mn6+ <25g/l 603nm,归零后测其试样吸光度为B 取1ml槽液入250ml烧杯+D.I水 氢氧化钠 35~45g/l 50ml+1M BaCl2 10ml→以0.1M-HCl 滴至PH=8.2为终点 膨胀剂 硫酸(50%) 预中和槽 双氧水 1~3% 取2ml槽液+100ml D.I水+20%H2SO4 20ml→以0.1N-KMnO4滴至粉红色 1~3% 取2ml槽液+100ml D.I水+3-5D M.O. 指示剂→以0.1N-NaOH滴至黄色计算公式添加公式
电镀槽液维护管理标准分析

822022年3月下 第06期 总第378期工艺设计改造及检测检修China Science & Technology Overview0.引言在航空零件制造过程中,电镀工艺是产生有害污染物最多的工序。
电镀工艺中往往含有高浓度的氰化物、重金属等污染物。
以镀镉槽液为例,其氰化物浓度一般在100g/L 以上,是国家标准排放标准的数十万倍,任何槽液调整都可能导致大量的污染物排放。
因此做好电镀槽液维护管理意义重大,不仅可以保障电镀生产的正常进行和电镀零件的加工质量,还可以从源头上大量减少污染物的排放,避免对生态环境的破坏。
本文拟分析国内外电镀槽液管理相关标准对常见的槽液管理方法进行举例介绍,为电镀标准编制与规范化献言献策。
1.电镀槽液维护管理方法1.1槽液配制阶段为延长槽液使用寿命,避免有害污染物的排放,在槽液配制阶段,要根据槽液成分的变化趋势,合理确定各成分的配制浓度,减少溶液的调整或报废。
如在HB/Z 5074《电镀银工艺》中,电镀银槽液中需要添加碳酸钾。
但在后续的电镀过程中会反应生成碳酸钾,当碳酸钾含量达到含量上限时需要添加氰化钡来沉淀碳酸钾,并倒槽去除沉淀。
在这个处理过程中不但需要使用剧毒、昂贵的氰化钡,还会不可避免地会造成有害污染物排放。
因此在配制镀银槽时碳酸钾成分宜采用下限浓度进行配制。
于此类似,所有同时含有氰化物/氢氧化物和碳酸盐的槽液,碳酸盐都可能会因氰化物/氢氧化物存在,造成浓度上升,配制时,碳酸盐宜采用下限浓度进行配制。
在航空产品电镀工艺中,一般对电镀槽液的氢脆性能有严格要求,而光亮剂成分可能造成零件的氢脆性能下降,SAE 标准AMS-QQ-P-416《镀镉》中就禁止在抗拉强度≥180ksi 的零件镀镉中使用光亮剂。
因此在零件外观满足要求的条件下,配制槽液时,光亮剂含量应尽可能低。
配制时光亮剂浓度的确定及后续添加量的确定可以参考JB/T 10339《光亮镀锌添加剂技术条件》、JB/T 7508《光亮镀镍添加剂技术条件》。
蚀刻控制

一、工艺规范1、本碱性蚀刻液分母液和子液,母液是开缸槽液,子液是独立添加液。
其成分指标如下表:2二、操作规范1、净槽使用前先将蚀刻机按常规的碱和酸清洗后,用5﹪的盐酸清洗,再用5﹪的氨水搅拌十分钟后排出洗液.2、加料调速加入母液至液面,升温至48℃以上即开始蚀刻.先以刷磨过的裸铜板测试上下压,调整传动速度,即可正式生产.34三、添加方式1、手动操作l 当比重超过1.21或铜含量超过160g/L时,可除去1/5槽液,并添加子液至液面;.l 因换液后溶液温度会下降,所以须等溶液循环5-10分钟后才能恢复蚀刻;l 长时间不用或抽风太强PH值会降到8.0以下,做板时的铅锡洁白效果会降低,此时可添加20升左右的氨水恢复PH值及板面的洁白度,氨水添加时宜循环慢加,以免破坏成分比例.2、自动添加l 当工作温度达到后,设定比重1.21或铜含量150g/L;l 自动添加开始动作时取槽液测试含铜量和比重,了解与设定值之误差;l 自动添加器必须只有在温度达到后才能启动(铜量一定温度不同比重不同)l 因管路输送的关系,槽液在自动控制器值为150g/L时,槽内的实际含铜量会超过150g/L,通常有±5g/L的误差,要正确掌握.四、槽液维护和管理1、定期检查自动控制之比重和槽液比重是否相符而适当校正.2、定期分析槽液的PH值,铜含量和氯含量,汇总制成图表以作参考.3、长期不使用时可多加子液以避免氨气的过量损失4、氯化铵添加时应先在槽外溶解再加入槽内,其添加量的计算为:(氯含量单位为g/L)添加量(Kg) = (氯标准-分析值)×槽体升数×0.001515、同样的溶液PH值在50℃时与常温会表现不同的值,换算公式如下:PH(50℃) = PH(T)– 0.021×(50-T)例如T=24℃时, PH(50℃) = PH(24)– 0.021×(50-24)=8.86-0.021×266、溶液PH值的影响因素:温度,校正用的标准液,设备等7、同样的溶液比重在50℃时与常温会表现不同的值,差约0.01,比重差0.01表现的铜含量约差10g/L.五、分析1、C U 的含量测定方法: 吸取10毫升槽液于250毫升的锥形瓶中,加水100毫升,加入50%硫酸至溶液兰色消失为止;加入50%的KCNS 10毫升,KI 1克,淀粉指示剂5毫升;用0.1N 的Na2S2O3标准液滴至兰色刚好消失为终点,记下所耗用的Na2S2O3滴定ml数.计算: 铜含量g/L = 6.4×NV式中: N -- Na2S2O3标准液的实际当量浓度V --- 所耗用的Na2S2O3滴定ml数.2、氯含量的测定需要试剂•0.5M AgNO3溶液•25% HNO3溶液•K2CrO4指示剂分析方法:①取1.0ml样品到一个250ml烧杯中,加30ml DI水;②若样品为无铜的子液则加1ml5%的硫酸铜溶液使其变为兰色,含铜的槽液不需添加;③用25% HNO3溶液加入样品中以调整溶液颜色至透明,微带浅兰色的状态(须小心不可过量,否则要滴加氨水还原成深色后再重复操作);④加入数滴K2CrO4指示剂(注意溶液加入后须仍为清澈透明,否则可滴加25% HNO3调整,此时溶液微带浅绿色);⑤用0.5M AgNO3溶液滴定,同时搅拌被滴定溶液,不可有大颗粒的沉淀产生,溶液沉淀物由粉白转为出现褐色颗粒时即为终点,记下所耗用的AgNO3溶液体积.计算: 氯含量(g/L) = 17.75×V或 (M) = 0.5×V式中: V --- 所耗用的AgNO3溶液滴定ml数.六、问题与对策。
电镀铜锡锌三元合金应用探讨
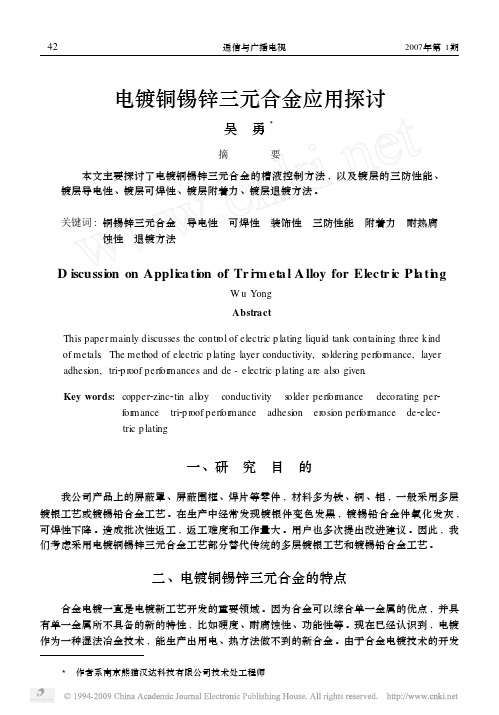
V试 ———试样的体积 , mL。 ③游离氰化钾的测定
1) 试剂
2007年第 1期 通信与广播电视
45
a) 10% KI溶液 ;
b) 011mol/L AgNO3 标准溶液 。 2) 分析方法
用移液管吸取镀液 2mL 于 250mL 锥形瓶中 , 加水 50mL , 加 10% KI溶液 10 mL , 用
formance tri2p roof perform ance adhesion erosion performance de2elec2 tric p lating
一 、研 究 目 的
我公司产品上的屏蔽罩 、屏蔽围框 、焊片等零件 , 材料多为铁 、铜 、铝 , 一般采用多层 镀银工艺或镀锡铅合金工艺 。在生产中经常发现镀银件变色发黑 , 镀锡铅合金件氧化发灰 , 可焊性下降 。造成批次性返工 , 返工难度和工作量大 。用户也多次提出改进建议 。因此 , 我 们考虑采用电镀铜锡锌三元合金工艺部分替代传统的多层镀银工艺和镀锡铅合金工艺 。
二 、电镀铜锡锌三元合金的特点
合金电镀一直是电镀新工艺开发的重要领域 。因为合金可以综合单一金属的优点 , 并具 有单一金属所不具备的新的特性 , 比如硬度 、耐腐蚀性 、功能性等 。现在已经认识到 , 电镀 作为一种湿法冶金技术 , 能生产出用电 、热方法做不到的新合金 。由于合金电镀技术的开发3 作者系源自京熊猫汉达科技有限公司技术处工程师
V试 ———试样的体积 , mL。 ②锡含量的测定
1) 试剂
a) 浓盐酸 ;
b) 双氧水 ;
c) 10%氯化钾溶液 ;
d) 30%六次甲基四胺溶液 ;
e) 二甲酚橙指示剂 ;
f) 氟化铵 ;
g) 0105mol/L EDTA 标准溶液 ;
锌系磷化液配方成分分析、技术研发、磷化机理及工艺流程

锌系磷化液成分分析、配方研发、磷化机理及工艺流程导读:本文详细介绍了锌系磷化液的研究背景,理论基础,参考配方等,本文中的配方数据经过修改,如需更详细资料,可咨询我们的技术工程师。
锌系磷化液广泛应用于金属表面处理,禾川化学引进国外配方破译技术,专业从事金属表面脱漆剂成分分析、配方还原、研发外包服务,为金属表面处理相关企业提供一整套配方技术解决方案。
一、背景磷化是金属材料防腐蚀的重要方法之一,其目的在于给基体金属提供防腐蚀保护、用于喷漆前打底、提高覆膜层的附着力与防腐蚀能力及在金属加工中起减摩润滑作用等。
磷化是常用的前处理技术,原理上应属于化学转化膜处理。
工程上应用主要是钢铁件表面磷化,但有色金属如铝、锌件也可应用磷化。
钢铁表面涂装前处理工艺指脱脂(除油)、除锈、表调、磷化。
然而由于工件表面的状况不同,则生产工艺也有所不同,有的工艺中没有脱脂或没有除锈工序,有的工艺则没有表面调整工序,但磷化工序是绝对不可缺少的。
在涂装处理过程中,如果不清除油脂、氧化皮和锈层,不进行磷化处理,直接进行涂漆和静电喷涂,就会使钢铁表面的涂层产生脱落,失去了涂装的意义。
目前,国内外的金属加工业、薄板加工业、石油行业及汽车、自行车、高低压开关柜、防盗门、铁路等制造业普遍采用的是中、高温磷化,存在着操作不方便、能源和材料消耗大、调整频繁、成膜不均、成本高等问题。
为解决以上问题,常温磷化已成为国际磷化行业的必然和研究课题。
常温磷化不仅可以有效地降低能源消耗,还可以解决操作不方便、材料消耗大、调整频繁、成膜不均、成本高等问题。
禾川化学技术团队具有丰富的分析研发经验,经过多年的技术积累,可以运用尖端的科学仪器、完善的标准图谱库、强大原材料库,彻底解决众多化工企业生产研发过程中遇到的难题,利用其八大服务优势,最终实现企业产品性能改进及新产品研发。
不锈钢管道酸洗钝化(浸泡法)缺陷分析与质控要点
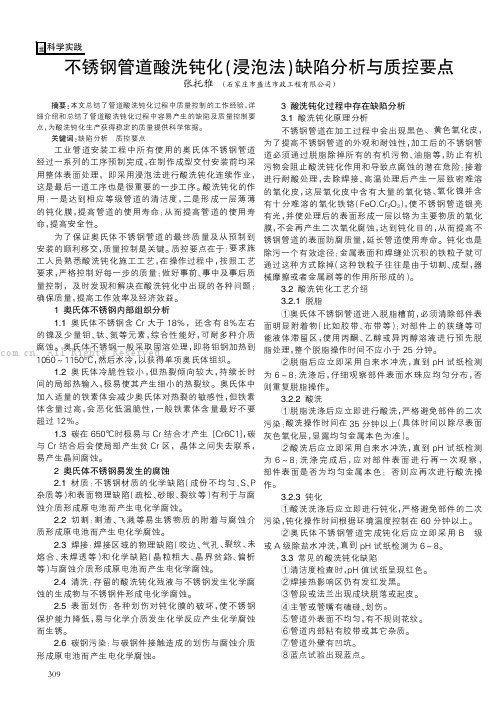
摘要:本文总结了管道酸洗钝化过程中质量控制的工作经验,详细介绍和总结了管道酸洗钝化过程中容易产生的缺陷及质量控制要点,为酸洗钝化生产获得稳定的质量提供科学依据。
关键词:缺陷分析质控要点工业管道安装工程中所有使用的奥氏体不锈钢管道经过一系列的工序预制完成,在制作成型交付安装前均采用整体表面处理,即采用浸泡法进行酸洗钝化连续作业,这是最后一道工序也是很重要的一步工序。
酸洗钝化的作用:一是达到相应等级管道的清洁度,二是形成一层薄薄的钝化膜,提高管道的使用寿命;从而提高管道的使用寿命,提高安全性。
为了保证奥氏体不锈钢管道的最终质量及从预制到安装的顺利移交,质量控制是关键。
质控要点在于:要求施工人员熟悉酸洗钝化施工工艺,在操作过程中,按照工艺要求,严格控制好每一步的质量;做好事前、事中及事后质量控制,及时发现和解决在酸洗钝化中出现的各种问题;确保质量,提高工作效率及经济效益。
1奥氏体不锈钢内部组织分析1.1奥氏体不锈钢含Cr大于18%,还含有8%左右的镍及少量钼、钛、氮等元素,综合性能好,可耐多种介质腐蚀。
奥氏体不锈钢一般采取固溶处理,即将钼钢加热到1050~1150毅C,然后水冷,以获得单项奥氏体组织。
1.2奥氏体冷脆性较小,但热裂倾向较大,持续长时间的局部热输入,极易使其产生细小的热裂纹。
奥氏体中加入适量的铁素体会减少奥氏体对热裂的敏感性,但铁素体含量过高,会恶化低温脆性,一般铁素体含量最好不要超过12%。
1.3碳在650℃时极易与Cr结合才产生[Cr6C1],碳与Cr结合后会使局部产生贫Cr区,晶体之间失去联系,易产生晶间腐蚀。
2奥氏体不锈钢易发生的腐蚀2.1材质:不锈钢材质的化学缺陷(成份不均匀、S、P 杂质等)和表面物理缺陷(疏松、砂眼、裂纹等)有利于与腐蚀介质形成原电池而产生电化学腐蚀。
2.2切割:割渣、飞溅等易生锈物质的附着与腐蚀介质形成原电池而产生电化学腐蚀。
2.3焊接:焊接区域的物理缺陷(咬边、气孔、裂纹、未鉻熔合、未焊透等)和化学缺陷(晶粒粗大、晶界贫、偏析等)与腐蚀介质形成原电池而产生电化学腐蚀。
PTH药液成分的分析方法
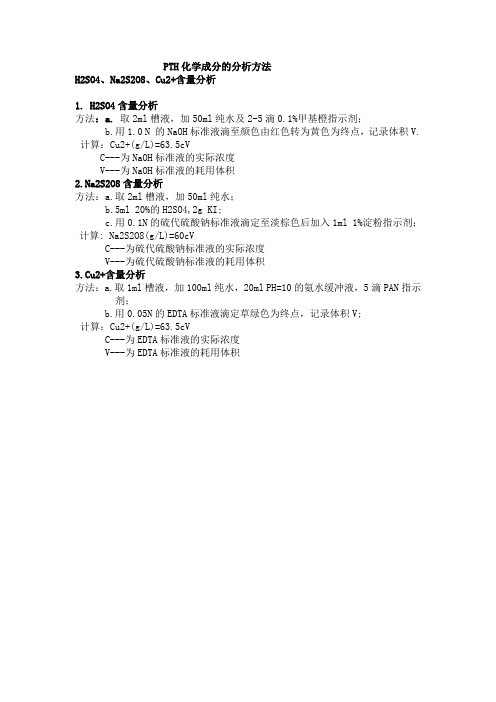
PTH化学成分的分析方法
H2SO4、Na2S2O8、Cu2+含量分析
1.H2SO4含量分析
方法:a.取2ml槽液,加50ml纯水及2-5滴0.1%甲基橙指示剂;
b.用1.0 N 的NaOH标准液滴至颜色由红色转为黄色为终点,记录体积V.计算:Cu2+(g/L)=63.5cV
C---为NaOH标准液的实际浓度
V---为NaOH标准液的耗用体积
2.Na2S2O8含量分析
方法:a.取2ml槽液,加50ml纯水;
b.5ml 20%的H2SO4,2g KI;
c.用0.1N的硫代硫酸钠标准液滴定至淡棕色后加入1ml 1%淀粉指示剂;计算: Na2S2O8(g/L)=60cV
C---为硫代硫酸钠标准液的实际浓度
V---为硫代硫酸钠标准液的耗用体积
3.Cu2+含量分析
方法:a.取1ml槽液,加100ml纯水,20ml PH=10的氨水缓冲液,5滴PAN指示剂;
b.用0.05N的EDTA标准液滴定草绿色为终点,记录体积V;
计算:Cu2+(g/L)=63.5cV
C---为EDTA标准液的实际浓度
V---为EDTA标准液的耗用体积。
ABS电镀资料

ABS电镀流程去应力——化学除油——亲水——化学粗化——回收——中和——预浸——胶体钯活化——回收——解胶——化学镍——活化(5%盐酸)——焦铜——酸铜——亮镍——铬哪些塑料最适合电镀?广泛应用于电镀的塑料是ABS。
ABS是丙烯腈(A),丁二烯(B)和苯乙烯(S)的三元共聚物,是由丙烯腈与苯乙烯形成的树脂相和苯乙烯与丁二烯形成的弹性体相(也称橡胶体相)组成的混合物。
在粗化过程中,橡胶粒子被溶去形成小坑,这是金属镀层抛锚的地方,是镀层结合力的基础。
橡胶粒子太少,粗化后小坑太少,结合力不好。
橡胶粒子太多,粗化后小坑连成大坑,结合力也不好。
因此,电镀用的ABS中,丁二烯(B)的含量要控制在18%——23%。
而且,ABS要接枝共聚的镀层结合力才会好。
符合这样要求的ABS,称电镀级ABS,最适合电镀。
后来,在ABS中加入PC(聚碳酸酯),以改善性能。
加入PC后粗化要难一些,PC加到40%- 45%(质量分数),还可以用ABS 的粗化溶液粗化,不需要用有机溶剂预粗化,只要在68度粗化15分钟即可。
PC再多,要用有机溶剂预粗化。
塑料件是否适合电镀还和塑料件的设计有关。
电镀用塑料件的设计要注意以下几点:1)有可能时用弧面代替大的平面2)避免深的不通孔。
槽和孔不要太近,边要倒圆。
3)不要太薄,厚度不要突变。
4)尽可能不用金属镶件。
5)考虑装挂点塑料镀的结合力由哪些因素决定?主要讨论ABS和ABS+PC的镀层结合力首先,一定要选取电镀级的塑料。
否则,即使一切都做得正确,镀层结合力也不好。
第二,要正确设计电镀用塑料件。
第三,要有正确的注塑工艺。
电镀人员首先要检查塑料件是否有应力集中,如果有要加以消除。
在采取了消除应力措施之后,还有明显的应力集中,就不要电镀。
第二要做好脱脂。
但是塑料表面是不能通过脱脂达到亲水的,因此严格遵照工艺要求就更显重要。
抛光后的零件不应存放,尽快脱脂为好,要用超声波强化脱脂效果。
第三,粗化是影响结合力的关键因素。
槽液分析报告

槽液分析报告1. 引言槽液是指工业生产过程中使用的液体,由于长期使用和各种因素的影响,槽液的性能和质量可能会发生变化。
槽液分析是一种通过检测槽液中的成分和性能来评估其质量和有效性的方法。
本报告旨在对样本槽液进行全面的分析和评估,并提出相应的建议,以便进一步改进槽液的性能和质量。
2. 实验目的本次槽液分析的主要目的是:•检测槽液的物理性质,包括密度、粘度等。
•分析槽液的化学成分,确定含有的主要元素和杂质。
•评估槽液的性能,如温度稳定性、抗氧化性等。
3. 方法3.1 样本采集从生产现场随机选取一定量的槽液样本,并进行适当的保存和封存,以确保样本的原始性和准确性。
3.2 物理性质测试使用密度计和粘度计对槽液样本进行测试,记录并比较不同样本之间的差异。
3.3 化学成分分析使用化学分析仪器,如红外光谱仪、质谱仪等,对槽液样本进行分析,以确定主要元素和可能的杂质。
3.4 性能评估对槽液样本进行温度稳定性测试和抗氧化性测试,评估其在不同条件下的稳定性和耐受性。
4. 实验结果4.1 物理性质测试结果对于样本A,其密度为1.05 g/cm³,粘度为20 mPa·s。
而样本B的密度为1.08 g/cm³,粘度为25 mPa·s。
说明在密度和粘度方面,样本B相对于样本A来说更加稠密和黏滞。
4.2 化学成分分析结果通过红外光谱分析,我们发现槽液样本中含有苯乙烯、乙烯和一些杂质。
质谱仪的结果显示主要元素为碳、氢和氧,但也检测到了微量的其他元素。
4.3 性能评估结果在温度稳定性测试中,样本A在高温环境下表现出较好的稳定性,而样本B在低温环境下表现更好。
在抗氧化性测试中,样本A和样本B均显示出较好的抗氧化能力。
5. 结论通过对槽液样本的分析,我们得出以下结论:•样本B相对于样本A在密度和粘度方面更加稠密和黏滞。
•槽液样本中主要含有苯乙烯、乙烯等化学成分。
•槽液样本表现出良好的温度稳定性和抗氧化性能。
电镀线槽液浓度异常处理操作指引
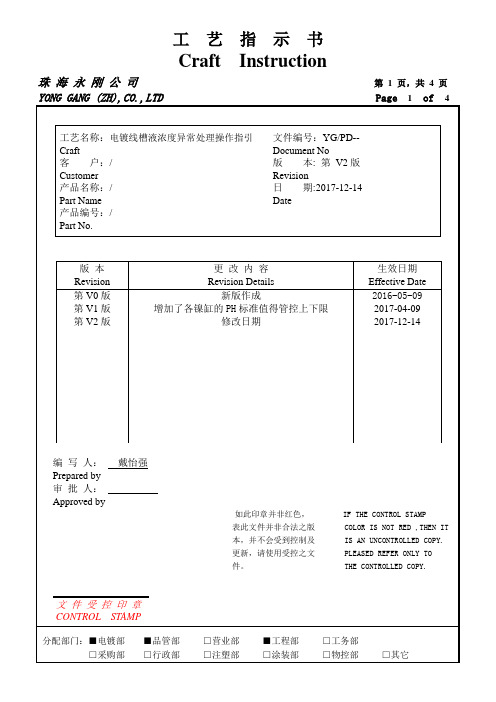
HCl
是
260-320ml/L
269-307mL/L
290mL/L
中和
还原剂
否
45-55mL/L
50mL/L
A线
槽名
成分
是否管控
规格上下限
控制上下限
控制值
解胶
H2SO4
否
40-45g/L
42.5g/L
加速剂
否
60-80g/L
70g/L
化学镍
LFS1
是
25-35ml/L
26-33ml/L
30mL/L
H2SO4
是
60-75g/L
62-72.5g/L
67.5g/L
Cl-
是
60-120ppm
70-105g/L
90ppm
半光镍
NiSO4
是
300-340g/L
305-334g/L
320g/L
NiCl2
是
40-50g/L
41-48g/L
45g/L
H3BO3
是
40-50g/L
41-48g/L
45g/L
光镍
NiSO4
5.2 《电镀线物料添加记录表》
六、备注:由于造成电镀线槽液浓度异常一般是有清缸、倒槽、药水的更换所导制的,电镀线处于停
产状态,不对产品造成影响,其分析结果无需填入到所要管控的SPC中。
52.5g/L
H3BO3
是
40-45g/L
40.7-44.3g/L
42.5g/L
光铬
CrO3
是
250-300g/L
257-290g/L
275g/L
H2SO4
电泳漆液成分及工艺条件对膜层的影响

电泳漆液成分及工艺条件对膜层的影响一、固体分含量固体分含量过低时,电解作剧烈,漆膜薄,气泡多,易产生针孔;过高时则膜层比较粗糙,易起桔皮。
因此稳定固体分含量是保证电泳质量的一个关键,对于EC-3000金色电泳漆来说,每电泳15一20M2的零件需补充1L浓缩液。
二、溶剂电泳漆液刚配制时,其溶剂含量稍高。
但随着漆液使用时间的延长和超滤的使用,溶剂不断挥发和滤出,其含量会逐渐下降,影响漆膜质量。
严重时,漆膜会在烘烤前脱落。
因此,应及时添加调整,一般每滤出100L超滤渗透液,应补充1.2L溶剂。
三、电压极间电压升高,电场作用加强,漆液中带电粒子泳动,沉积速度加快,使泳透力提高,膜层增厚。
电泳操作时,应根据零件形状与大小,槽液温度高低,所需膜的厚薄,选择最佳电压。
当电泳漆槽刚配制时,其溶剂含量及导电度均高,则电压应适当降低。
四、PH值由于阳极采用隔膜控制,电泳漆液的PH值较为稳定,当超滤液排出太多或隔膜液漏出进入电泳漆液时,使电泳漆液PH值发生变化,可用有机酸调整。
PH值过低时,漆膜再溶解增加,膜层变薄,且对设备腐蚀严重。
五、电导率电导率是控制电泳漆膜层质量的关键指标之一。
新配溶液时电导率可能较高,因此需要通地超滤排出渗液以降低电导率。
电导率过高,则膜厚易产生桔皮和表面粗糙等现象。
电导率过低,则容易产生针孔和麻点。
因此当电导率的高低不同时需要采用不同的电压和槽液温度,以便获得良好的膜层。
电导率较高时,可采用较低的电压和温度;反之则要相应提高电压和温度。
六、温度电泳漆液的温度一般控制在26度左右。
温度过低,必需使用较高的电压以达到电泳的目的;温度过高,则加剧溶剂的挥发,不利于电导率的稳定和控制。
七、电泳时间电泳时间的长短会影响漆膜外观及膜层的厚薄。
当电泳时间过长时,膜厚色深,透明性变差。
电泳时间过短,则膜层不完整。
因此需要根据漆液的电导率,固体分含量等因素的变化,在确定溶液温度和电压的前提下,选择最佳的电泳时间,以确保膜层的质量。
航空电镀槽液检测标准

航空电镀槽液检测标准包括了对电镀液成分、浓度、pH值等关键参数的规范要求。
在进行电镀槽液检测时,需要遵循一定的标准和方法,以确保电镀过程的稳定性和镀层的质量。
以下是一些相关的标准和方法:
1. 取样规范性:在取样过程中,必须遵守规范的操作流程,以避免因操作失误或取样不规范而影响检测结果的准确性。
2. 分析方法的选择:电镀槽液的分析方法多样,选择合适的分析方法是确保检测结果准确的关键。
例如,可以使用滴定法、分光光度法、原子吸收光谱法等进行分析。
3. 记录管理:在分析过程中,应详细记录每一步的操作和结果,以便于后续的质量控制和问题追溯。
4. 标准参考:可以参考国内外的相关标准,如GB/T 8184-2004《铑电镀液》、HG/T 4319-2012《铁镍钨合金电镀液》等,这些标准规定了电镀液的具体成分和质量要求。
5. 环保要求:电镀企业在生产过程中还需遵守环保要求,如废水、废气、固体废物和噪声污染防治等,确保生产过程的环境友好性。
6. 行业规范:根据《电镀行业规范条件》,电镀企业需加强重金属污染防治,推进产业结构调整和转型升级,促进行业的可持续健康发展。
综上所述,航空电镀槽液检测标准不仅涉及电镀液本身的质量控制,还包括了环保、安全和行业规范等多个方面。
因此,电镀企业在进行槽液检测时,应综合考虑各种因素,确保检测工作的全面性和准确性。
瓦特镀镍液槽液成分分析

瓦特镀镍液槽液成分分析
瓦特镀镍液槽液主要由镍盐、氢氧化钠、硼酸、氯化钠和其他助剂组成。
其中,镍盐通常是硫酸镍或氯化镍,氢氧化钠用于调节液槽液的pH值,硼酸用于提高液槽液的工作温度和镀液液层的厚度,氯化钠是控制镀液电导率的重要因素。
此外,液槽液中常加入一些助剂,如表面活性剂、缓蚀剂、着色剂、防泡剂等,以更好地调节液槽液的性能和提高镀层质量。
但具体液槽液成分比例和助剂种类在不同厂家和生产工艺中可能会有所不同。
废槽液主要成分

废槽液主要成分介绍废槽液是一种在工业生产过程中产生的废弃液体,它包含了许多有害物质和化学成分。
本文将对废槽液的主要成分进行探讨,包括其组成、特征、对环境和人体的影响等方面。
废槽液的定义废槽液是指工业生产过程中产生的废弃液体,它包括了许多来自于生产过程中使用的化学物质和工业废弃物的残留物。
废槽液的成分复杂多样,其中的化学物质可能对环境和人体健康产生不利影响。
废槽液的来源废槽液的来源多种多样,主要包括工业生产过程中的废弃物排放、洗涤剂和清洁剂的使用、废水处理系统中的残留物等。
这些废弃物通常会进入废水处理系统,但由于处理不当或处理系统故障,废槽液中的有害物质有可能被释放到环境中。
废槽液的组成废槽液的组成主要取决于工业生产过程中使用的化学物质和废弃物。
下面是一些常见的废槽液成分:有机物废槽液中常含有各种有机物,包括有机溶剂、石油化学物质、塑料添加剂等。
这些有机物通常具有高挥发性,易溶于水,并且具有一定的毒性。
它们可能对环境产生污染,也有可能对人体健康造成危害。
重金属废槽液中的重金属主要来自于工业生产过程中的废弃物。
常见的重金属包括铅、汞、镉、铬等。
这些重金属对环境和人体健康具有很高的毒性,它们可能积累在生物体内,造成慢性中毒或其他健康问题。
废槽液中常含有酸性或碱性物质,这些物质可能来自于工业生产过程中使用的化学试剂、中和剂等。
酸碱物质的存在可能导致废槽液的酸碱度失衡,进而对生态系统产生负面影响。
其他成分废槽液中还可能含有其他化学物质,比如有害气体、放射性物质以及各种工业废弃物的残留物等。
这些成分的特性和影响需要根据具体情况进行详细分析。
废槽液的特征废槽液具有以下特征:混浊性废槽液通常呈混浊状,其中可能悬浮着固体颗粒。
这些固体颗粒可能是废弃物的残留物或其他沉淀物。
异味废槽液通常具有刺激性的异味,这些异味可能来自于废弃物的分解产物或化学反应产生的气体。
酸碱度失衡废槽液的酸碱度可能失衡,这可能会影响水体的酸碱性,并对生态系统产生不利影响。
油含量的检测方法

双击鼠标自动滚屏脱脂槽液中含油量现场测定方法的研究浏览次数:52〔摘要〕油漆尤其电泳漆对油污非常敏感,除油不尽或脱脂槽液含油量高会造成漆膜缩孔、不均、附着力下降和防腐性能下降。
因此脱脂槽液中含油量的现场测定就异常重要,本文采用称重方法对脱脂槽液中含油量测定进行了研究,并就pH值在1-13、活性剂浓度在0.5-8.0g/L范围内,各因素对测定结果的影响进行了探讨分析,得出较适合涂装现场使用的测试方法。
〔关键词〕脱脂槽液重量法含油量测定0 前言钢材在生产过程中要使用防锈油,加工过程中要使用拉延油、润滑油等,在搬运过程中还有可能会沾上操作者手上的汗迹和油迹。
在涂装生产中,脱脂槽内会累积大量的油污,而脱脂槽中含油量的高低会直接影响除油效果和涂装质量。
目前含油量检测方法很多[1]:重量法、比重瓶法、比浊(变换溶剂)法、比浊(超声波)法、气相色谱法、电阻法、热解法、紫外分光光度法、萤光法、非分散红外法、三波数红外光度法等。
中华人民共和国标准《污水综合排放标准》(GB 8978-1996)中将红外光度法作为检测油类物质的标准方法;中华人民共和国城镇建设行业标准《污水排入城市下水道水质标准》(CJ 3082-1999)中分别将重量法和红外光度法作为检测油类物质的标准方法。
中华人民共和国标准《工业锅炉水质》(GB 1576-2001)规定采用重量法。
其中红外光度法具有灵敏度高,适用于各种油品,选择性强,但此方法设备投资较大,设备日常维护烦琐。
重量法具有仪器设备投资少、维护简单;药剂价格相对较低、检测成本低;方法简单直观等特点,特别适合涂装生产企业现场检测。
在涂装生产中常见油污主要由矿物油、凡士林、皂类、动植物油脂、脂肪酸等[2]组成,该类物质难溶于水,易溶于石油醚、三氯甲烷、四氯化碳、汽油等有机溶剂。
可采用有机溶剂萃取分液的方法将油从脱脂槽液中分离出来,再通过蒸发除去有机溶剂,称重得到油的重量。
本文通过以下试验确定了一种简单有效的测定脱脂槽液中油含量的方法。
- 1、下载文档前请自行甄别文档内容的完整性,平台不提供额外的编辑、内容补充、找答案等附加服务。
- 2、"仅部分预览"的文档,不可在线预览部分如存在完整性等问题,可反馈申请退款(可完整预览的文档不适用该条件!)。
- 3、如文档侵犯您的权益,请联系客服反馈,我们会尽快为您处理(人工客服工作时间:9:00-18:30)。
温州鸿升集团有限公司电镀各槽液分析方法编制:温在亮鸿升集团化验室为确保电镀产品质量达到要求,需要定期对电镀槽液进行维护以达到工艺要求。
相关人员定期对电镀槽液进行化验分析,及时补充不足的成分,维持槽液性能稳定。
电镀车间综合线:氰化镀铜、焦磷酸铜、打底镍槽、冲击镍槽、光亮酸铜槽、半光镍槽、光亮镍槽、三价铬槽、六价铬槽。
电镀车间自动线:预镀镍、半光亮镍、全光亮镍、镍封以及六价铬槽。
电镀槽液每周分析一次,做好相关记录,并及时上报品保部门。
Cu : ①取氰化镀铜槽液2.0ml 于250ml 锥形瓶②+100ml O H 2③+1g 8224O S NH )(④加热至澄清,溶液呈浅蓝色⑤+10ml1:1O H NH 23⑥+5滴PAN 指示剂⑦用0.1N EDTA 滴定,溶液由深蓝转为绿色到达终点。
CuCN :△×4.48 g/L—CN :①取氰化镀铜槽液10.0ml 于250ml 锥形瓶②+50ml O H 2③+10ml10%KI④用0.1N 3g NO A 滴定,溶液由清澈至刚出现浑浊到达终点。
游离NaCN :△×0.981 g/L722u O P C :①取焦磷酸铜槽液2.0ml 于250ml 锥形瓶②+100ml O H 2③加热至50℃④+10ml1:1O H NH 23⋅⑤+5滴PAN 指示剂⑥用0.1N EDTA 滴定,溶液由紫色转为绿色到达终点。
722u O P C :△×7.53 g/L-472O P : ①取焦磷酸铜槽液1.0ml 于250ml 锥形瓶②+100ml O H 2③+8~10ml1N COOH CH 3 调节PH 至3.8~4.0④+25ml0.2N n )(23Z COO CH⑤加热煮沸3min ,冷却后转移至250ml 容量瓶,加水至刻度线。
⑥过滤,静置后取滤液100ml 至250ml 锥形瓶⑦+10~15ml PH=10缓冲溶液⑧+5滴PAN 指示剂⑨用0.1N EDTA 溶液滴定,溶液由紫色转为黄绿色到达终点。
-472O P :(5-0.25×△)×87.00 g/L724O P K :(-472O P -722u O P C ×0.578)/0.527 g/LO H SO C 245u ⋅:①取光亮酸铜槽液1.0ml 于250ml 锥形瓶②+100ml O H 2③+1:1O H NH 23⋅调节PH 至9.9~10④+5滴PAN 指示剂⑤用0.1N EDTA 滴定,溶液由深蓝转为绿色到达终点。
O H SO C 245u ⋅:△×25.00 g/L42SO H : ①取光亮酸铜槽液1.0ml 于250ml 锥形瓶②+100ml O H 2③+5滴甲基橙指示剂④用0.1N NaOH 滴定,溶液由红色转为黄色到达终点。
42SO H :△×4.90 g/L—l C : ①取光亮酸铜槽液25.0ml 于250ml 锥形瓶②+100ml O H 2③加热至50℃④+3ml 1:13HNO⑤+2滴0.1N 3g NO A 溶液浑浊⑥用0.01N ()23g NO H 滴定,溶液由浑浊转为清澈到达终点。
—l C :△×14.20 g/LO H C N 226l i ⋅:①取冲击镍槽液1.0ml 于250ml 锥形瓶②+100ml O H 2③+10ml 1:1O H NH 23⋅④+0.05g 紫脲酸铵指示剂⑤用0.1N EDTA 滴定,溶液由棕色转为紫色到达终点。
O H C N 226l i ⋅:△×11.90 g/LHCl : ①取冲击镍槽液1.0ml 于250ml 锥形瓶②+100ml O H 2③+10ml 1:1O H NH 23⋅④+5滴甲基橙⑤用0.1N NaOH 滴定,溶液由红色转为黄色到达终点。
HCl :△×3.65 g/L导电盐+3r C : ①取三价铬槽液1.0ml 于250ml 锥形瓶②+30ml O H 2③+10ml 硼酸指示剂 溶液显绿色④用0.1N NaOH 滴定,溶液由绿色转为浅红色到达终点。
+3r C :△×6.20 g/L辅加剂: ①取三价铬槽液50.0ml 于250ml 锥形瓶②+10ml 1:1HCl③+50ml 523H COOC CH 转移至125ml 分液漏斗④摇晃均匀,静置后放出下层溶液⑤+15ml O H 2冲洗上层溶液,放出下层溶液,重复2次。
将剩余液体倒入250ml 锥形瓶⑥+10ml 无水OH CH 3荡洗分液漏斗并倒入装有剩余液体的锥形瓶中⑦+5滴溴甲酚紫指示剂⑧用0.1N NaOH 滴定,溶液由黄色转为蓝色到达终点。
辅加剂:△×1.80 g/L+3r C : ①取三价铬槽液1.0ml 于250ml 锥形瓶②+150ml O H 2③+1g 22a O N 摇晃均匀④加热溶液,保持微沸20~30min 至溶液完全变黄 ⑤+2g 24HF NH⑥+10ml 浓HCl⑦+5ml 10%KI⑧+5滴淀粉指示剂⑨用0.1N 322a O S N 滴定,溶液由棕色转为绿色到达终点。
+3r C :△×1.73 g/L+3r C 测量方案2:+3r C : ①取三价铬槽液1.0ml 于250ml 锥形瓶②+75ml O H 2③+10ml 1:142SO H④+1ml 85%43PO H⑤+10ml 1%3g NO A⑥+2g ()8224O S NH⑦加热煮沸2min ,冷却⑧+3滴苯代邻氨基苯甲酸⑨用0.1N ()()2424e SO F NH 滴定,溶液由紫红色转为绿色到达终点。
+3r C :△×1.73 g/L六价铬槽(包括综合线和自动线):3r O C : ①取六价铬槽液5.0ml ,稀释至100ml 后取稀释液2ml于250ml 锥形瓶(含原槽液0.1ml )②+75ml O H 2+3r C : ①取六价铬槽液5.0ml ,稀释至100ml 后取稀释液2ml 于250ml 锥形瓶(含原槽液0.1ml )②+75ml O H 2③+10ml 1:142SO H③吸取Vml 六价铬槽液至25ml 比色管中,加水至刻度线,摇匀④放在比色管架上的1号和2号管之间,在日光灯下进行比色,若试样颜色浓于2号比色管,则在2号和3号之间进行比色,依次类推。
然后确定并估计出槽液的三价铬浓度。
附:三价铬的浓度如下表:42SO H : ①用移液管分别取20ml 六价铬槽液于离心管A 及B 中②分别加入5ml 1:1HCl③+10ml 20%2l a C B 于离心管A 中④+10ml O H 2于离心管B 中⑤封盖摇匀并置于离心器中⑥调节离心时间为5min ,转速由0慢慢调节至1400rpm⑦读出离心管A 、B 的读数42SO H :读数A-B g/L镍槽(包括自动线预镀镍、半光亮镍、全光亮镍、镍封以及综合线打底镍、半光亮镍、全光亮镍1和全光亮镍2):+2i N : ①取镍槽液1.0ml 于250ml 锥形瓶②+100ml O H 2③+10ml 1:1O H NH 23⋅④+0.05g 紫脲酸铵指示剂⑤用0.1N EDTA 滴定,溶液由棕色转为紫色到达终点。
+2i N :△×5.87 g/L-l C : ①取镍槽液1.0ml 于250ml 锥形瓶②+100ml O H 2③+3滴10%42r O C K④用0.1N 3g NO A 滴定,溶液由白色浑浊转为刚出现红色浑浊即到达终点。
O H C N 226l i ⋅:△×11.90 g/LO H SO N 247i ⋅:(+2i N -0.25×O H C N 226l i ⋅)×4.78 g/L33BO H : ①取镍槽液1.0ml 于250ml 锥形瓶②+40ml 10%6146O H C (甘露醇)③+10ml 1:1O H NH 23⋅④+3滴BPC 指示剂(溴甲酚紫)⑤用0.1N NaOH 滴定,溶液由黄色转为刚呈淡紫色到达终点。
33BO H :△×6.18 g/L33BO H 测量方案2:33BO H : ①取镍槽液1.0ml 于250ml 锥形瓶②+40ml O H 2③+10ml 10%()O H CN F K 2643e ⋅④+10ml 1:1383O H C (丙三醇)⑤+10滴酚酞指示剂⑥用0.1N NaOH 滴定,溶液由绿色转为乳白色到达终点(过量则呈红色)33BO H :△×6.18 g/L各槽液相关工艺范围综合线:氰化镀铜槽 游离NaCN : 5—15 g/L CuCN : 30—40 g/L打底镍槽 O H SO N 247i ⋅: 200—250 g/L O H C N 226l i ⋅: 10—20 g/L 33BO H : 10—20 g/L冲击镍槽 O H C N 226l i ⋅: 100—200 g/L HCl : 30—80 g/L焦磷酸铜槽 722u O P C : 35—70 g/L724O P K : 170—320 g/L光亮酸铜槽 O H C 245uSO ⋅: 180—210 g/L 42SO H : 55—65 g/L—l C : 60—120 mg/L半光亮镍槽 O H SO N 247i ⋅: 220—280 g/L O H C N 226l i ⋅: 45—55 g/L 33BO H : 40—50 g/L全光亮镍槽 O H SO N 247i ⋅: 220—280 g/L O H C N 226l i ⋅: 45—55 g/L 33BO H : 35—45 g/L三价铬槽 +3r C 10—16 g/L 导电盐 90—120 g/L 辅加剂 6—10 g/L六价铬槽 3r O C : 200—250 g/L+3r C : 2—4 g/L 42SO H : 0.8—1.5 g/L自动线:预镀镍槽 O H SO N 247i ⋅: 180—250 g/L O H C N 226l i ⋅: 45—60 g/L 33BO H : 40—50g/L半光亮镍槽 O H SO N 247i ⋅: 220—280 g/L O H C N 226l i ⋅: 45—55 g/L 33BO H : 40—50 g/L全光亮镍槽 O H SO N 247i ⋅: 230—280 g/L O H C N 226l i ⋅: 50—60 g/L 33BO H : 40—50 g/L镍封槽 O H SO N 247i ⋅: 180—250 g/L O H C N 226l i ⋅: 55—85 g/L 33BO H : 40—50 g/L六价铬槽 3r O C : 200—250 g/L +3r C : 2—4 g/L 42SO H : 0.8—1.5 g/L。