模具第四章 拉深模
第四章-拉深工艺及拉深模具设计--习题题目练习(附答案)

第四章拉深工艺及拉深模具设计复习题答案一、填空题1.拉深是是利用拉深模将平板毛坯压制成开口空心件或将开口空心件进一步变形的冲压工艺。
2.拉深凸模和凹模与冲裁模不同之处在于,拉深凸、凹模都有一定的圆角而不是锋利的刃口,其间隙一般稍大于板料的厚度。
3.拉深系数m是拉深后的工件直径和拉深前的毛坯直径的比值,m越小,则变形程度越大。
4.拉深过程中,变形区是坯料的凸缘部分。
坯料变形区在切向压应力和径向拉应力的作用下,产生切向压缩和径向伸长的变形。
5.对于直壁类轴对称的拉深件,其主要变形特点有:(1)变形区为凸缘部分;(2)坯料变形区在切向压应力和径向拉应力的作用下,产生切向压缩与径向的伸长,即一向受压、一向收拉的变形;(3)极限变形程度主要受传力区承载能力的限制。
6.拉深时,凸缘变形区的起皱和筒壁传力区的拉裂是拉深工艺能否顺利进行的主要障碍。
7.拉深中,产生起皱的现象是因为该区域内受较大的压应力的作用,导致材料失稳_而引起。
8.拉深件的毛坯尺寸确定依据是面积相等的原则。
9.拉深件的壁厚不均匀。
下部壁厚略有减薄,上部却有所增厚。
10.在拉深过程中,坯料各区的应力与应变是不均匀的。
即使在凸缘变形区也是这样,愈靠近外缘,变形程度愈大,板料增厚也愈大。
11.板料的相对厚度t/D越小,则抵抗失稳能力越愈弱,越容易起皱。
12.因材料性能和模具几何形状等因素的影响,会造成拉深件口部不齐,尤其是经过多次拉深的拉深件,起口部质量更差。
因此在多数情况下采用加大加大工序件高度或凸缘直径的方法,拉深后再经过切边工序以保证零件质量。
13.拉深工艺顺利进行的必要条件是筒壁传力区最大拉应力小于危险断面的抗拉强度。
14.正方形盒形件的坯料形状是圆形;矩形盒形件的坯料形状为长圆形或椭圆形。
15.用理论计算方法确定坯料尺寸不是绝对准确,因此对于形状复杂的拉深件,通常是先做好拉深模,以理论分析方法初步确定的坯料进行试模,经反复试模,直到得到符合要求的冲件时,在将符合要求的坯料形状和尺寸作为制造落料模的依据。
4-1拉深过程分析(模具设计与制造)

2021/1/14
教育部十一五规划教材《模具设计与制造》
第4章 拉深工艺与拉深模具
绪论
用拉深方法来制造薄壁空心件,生产效率 高,材料消耗小,零件的强度和刚度高,而 且工件的精度也较高。拉深件的加工范围非 常广泛,从几毫米的小零件直至轮廓尺寸达2 ~ 3 m,厚度为200 ~ 300 mm的大型零 件。因此,在汽车、拖拉机、航宇航天、国 防、电器、仪表、电子等工业部门以及日常 生活用品生产中,拉深成形占据相当重要的 地位。
2021/1/14
教育部十一五规划教材《模具设计与制造》
第4章 拉深工艺与拉深模具
4.1.2 拉深件与拉深模的分类
(3)在单动压力机上工作的拉深模,按拉深 工序又可分为首次拉深模和再次拉深模。
(4)按有无压边装置可分为有压边装置拉深 模和无压边装置拉深模。
(5)一般板料的拉深要经过数道拉深工序才 能完成,一副拉深模一般只能完成一道拉深 工序,所以拉深模多为单工序模。较复杂拉 深件可采用落料拉深复合模等。
2021/1/14
教育部十一五规划教材《模具设计与制造》
第4章 拉深工艺与拉深模具
4.1.1拉深过程分析 b图表示有压边的拉深过程。
2021/1/14
教育部十一五规划教材《模具设计与制造》
第4章 拉深工艺与拉深模具
4.1.1拉深过程分析
拉深凸模和凹模与冲裁模
不同的是其工作部分没有锋
利的刃口,而是分别有一定
2021/1/14
教育部十一五规划教材《模具设计与制造》
第4章 拉深工艺与拉深模具
4.1.2 拉深件与拉深模的分类
2.拉深工艺分类 拉深工艺可分为不变薄拉深和变薄拉深两
种。后者在拉深后的零件壁部厚度与毛坯厚度 相比较,有明显变薄。生产中主要应用不变薄 拉深。
6拉深模
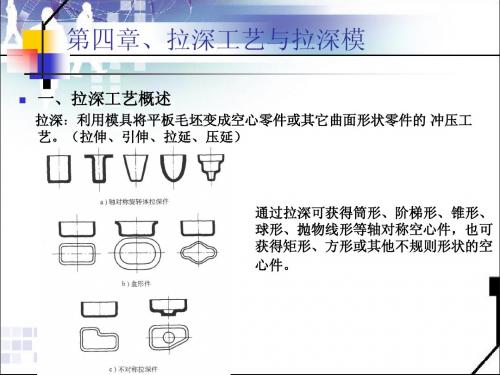
方法一:铣削加工:毛坯加工后,划线,铣型孔,最后钳 工修圆角,淬火后研磨、抛光 方法二:插削加工:毛坯加工后,划线,插型孔,最后钳 工修锉圆角,淬火后研磨、抛光 盒形冲件 方法三:线切割:毛坯加工后,划线,加工安装孔,淬火 后磨安装面等,最后切割型孔。抛光 方法四:电火花:毛坯加工后,划线,加工安装孔,淬火 后磨基面,最后电火花加工型腔,抛光 方法一:仿形铣:毛坯加工后,划线,仿形铣型腔,精修 后淬火、研磨、抛光 方法二:铣削或插削:毛坯加工后,划线, 铣或插型孔,修锉圆角后淬火,研磨抛光 旋转体曲面形冲件 方法三:线切割:毛坯加工后,划线,加工安装孔,淬火 后磨基面,线切割型孔,抛光 方法四:电火花:毛坯加工后,划线,加工安装孔,淬火 后磨基面,用电火花加工型腔。抛光
拉深凹模圆角半径
拉深凸模圆角半径
2、凸、凹模的间隙
拉深模间隙是指单边间隙,即凹模和凸模直径之差 的一半。拉深时凸、凹模之间的间隙对拉深力、工 件质量、模具寿命等都有影响。间隙过大,容易起 皱,工件有锥度,精度差;间隙过小,摩擦加剧, 导致工件变薄严重,甚至拉裂。因此,正确地确定 凸模和凹模之间的间隙是很重要的。
拉深模结构设计注意事项:
1、拉深件高度 拉深中间工序的高度不能算得很准,故模具结构要 考虑安全“留量”,以便工件稍高时仍能适应 2、气 孔 拉深模应有气孔,以便卸下工件 3、限位装置 弹性压边圈要有限位装置,防止被压材料过分变薄 4、控制材料流动 对于矩形或异形拉深件,可利用不等的凹模圆角、 设置拉深筋等方法控制材料流动以达到拉深件质量 要求
2.破裂 随着变形程度的提高,变形力也相应地提高,当变 形力大于传力区(筒形件的壁部)的承载能力时拉深 件则被拉破,筒形件的破裂都发生在壁部凸模圆角 切点稍上一点的位置 。
拉深模具设计

第四章 拉深模具设计 3)各次工序件的高度 在各工序件的直径与圆角半径确定之后,可根据圆筒形件
坯料尺寸计算公式推导出各次工序件高度的计算公式为
D2 r1 H 1 0 .2 5 d 1 0 .4 3 d 1 0 .3 2 r1 d1 d1
次拉出。
第四章 拉深模具设计 用推算法推算各次拉深直径为
d1=m1D=0.50×98.3=49.2mm d2=m2 d1=0.75×49.2=36.9mm d3=m3d2=0.78×36.9=28.8mm d4=m4d3=0.80×28.8=23mm
形程度减小。
第四章 拉深模具设计 因此,为了减小极限拉深系数,凸、凹模圆角半径及模具
间隙应适当取较大值。
但是,凸、凹模圆角半径和模具间隙也不宜取得过大,容 易产生失稳起皱;过大的模具间隙会影响拉深件的精度,使拉 深件的锥度和回弹较大。
第四章 拉深模具设计 ②压边条件。 采用压边圈并加以合理的压边力对拉深有利,可以减小拉
mn
dn d n 1
第四章 拉深模具设计 2)影响极限拉深系数的因素
(1)材料方面。
①材料的力学性能。
材料的屈强比σ s/σ b越小、伸长率δ 越大,对拉深越有利。
②材料的相对厚度(t/D)。 材料的相对厚度大时,凸缘抵抗失稳起皱的能力增强,因而 所需压边力减小(甚至不需要),这就减小了因压边力而引起的 摩擦阻力,从而使总的变形抗力减少,故极限拉深系数可减小。
H2
D2 r2 0 .2 5 d 2 0 .4 3 d 2 0 .3 2 r2 d2 d2
(4-4)
Hn
D2 rn 0 .2 5 d n 0 .4 3 d n 0 .3 2 rn dn dn
4.5拉深模具设计

深度拉深件或落料拉深复合模:
应使工艺力曲线位于压力机滑块 的许用压力曲线之下,还需对压力机 的电机功率进行校核
三. 压力机的选择
深度拉深件或落料拉深复合模:
1 F1 max h1
1000
① 计算拉深功A
首次拉深:
以后各次拉深:
凸、凹模工作部分形状
带压边圈的拉深
:
a:用于直径d≤100mm的拉深件
b:用于直径d>100mm的拉深件
五. 拉深工艺的辅助工序
润滑
热处理
目的:消除加工硬化及残余应力
对于普通硬化金属(如08钢、10钢、15钢等), 若工艺过程正确,模具设计合理,一般可不要进行中 间热处理。 对高度硬化金属(如不锈钢、耐热钢等),一般 一、二道工序后就要进行中间热处理。
凸模圆角的影响
:
凸模圆角rp↓↓→rp处弯曲变形程度 ↑→“危险断面”受拉力大→工件易产生局部变薄; 凸模圆角rp↑↑→凸模与毛坯的接触面↓→ 易产生底部变薄和内皱
四. 凸、凹模工作部分的尺寸设计
凹模圆角半径rd的计算
:
首次拉深: d r
1
0.8 ( D d )t
以后各次拉深: d n
r (0.6 ~ 0.8)rdn1
式中:rd1、rdn-1、rdn——首次、第(n-1)次和第n 次拉深模的凹模圆角半径 D——毛坯直径;d——中径;t——工件厚度。
有平面凸缘拉深件,最后一次拉深时:
凹模圆角半径应和拉深件的一致,即rdn=r。
四. 凸、凹模工作部分的尺寸设计
凸模圆角半径rd的计算
四. 凸、凹模工作部分的尺寸设计
模具第四章拉深模设计
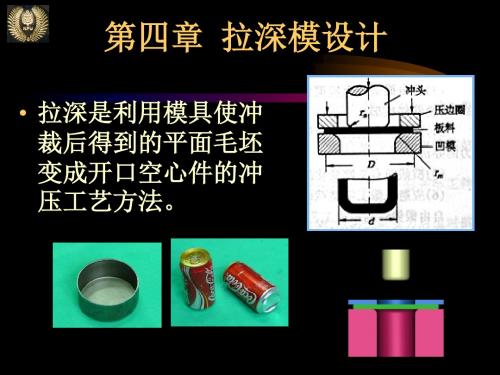
7)确定各次拉深半成品的高度:
h10.2(5 D d1 2d1)0.4d r 3 1 1(d10.3r1 2 ) h20.2(5 D d2 2d2)0.4d r3 2 2(d20.3r2 2 )
hn0.2(5 D dn 2dn)0.4d r3 n n(dn0.3rn 2 )
D0max 的拉深系数——极限拉深系数 (圆角部分不破裂,周边变形区坯料不 失稳起皱)
mc
d D0 m ax
3、影响极限拉深系数的因素
– 板料的力学性能 – 板料的相对厚度:t/D; t/D大,抗失
稳能力强,不易起皱。 – 模具结构及其参数:有无压边圈、凹
模圆角半径、凸模圆角半径。 – 拉深工艺条件:拉深次数、压边条件、
C=(1.1-1.20)t
用压边的一次拉深 光洁拉深
C=(1.0-1.15)t
C=(0.95-1.05)t
二、凸凹模结构形式
无压料一次拉深成形的凹模结构
a)圆弧形 b)锥形 c)渐开线形 d)等切面形
无压料多次拉深的凸、凹模结构
有压料多次拉深的凸、凹模结构
四、凸凹模刃口尺寸及公差(1)
• 当工件要求外形尺寸 (D) 时:
二、常用拉深模
无压边装置的以后各次拉深模
1-推件板 2-拉深凹模 3-拉深凸模 4-压边圈 5-顶杆 6-弹簧
有压边装置的以后各次拉深模
§4-7凸凹模工作部分的设计
一、拉深模间隙:间隙太大时,拉深件壁不 直或成锥形;间隙太小,模具磨损加剧, 工件易拉裂。
不用压边的浅拉深 多次拉深
C=(1.0-1.05)t
§4-5拉深件的起皱与破裂
一、起皱 拉深件的起皱: 受切向压应力失 稳而起皱。
第4章拉深模具设计过程

项目四、拉深模具设计过程任务1:根据设计任务,选择图4.1零件,设计拉深模具。
1.分析拉深件工艺性并拟定拉深工艺方案零件为一无凸缘圆筒形件,材料为08F,拉深性能较好,尺寸为未注公差,可作IT14级精度,壁厚1mm,高度尺寸不大,整体拉深工艺性较好,采用普通的拉深工艺应该能满足要求。
图4.1圆盖,20万件/年2.确定冲压模具类型采用正装拉深模。
3.拉深工艺计算(1)确定修边余量Δh;零件的相对高度h/d=59/48=1.21,经查得修边余量Δh=2.5(查表4-3)所以,修正后拉深件的总高应为48+2.5=50.5mm。
(2)计算毛坯直径D;确定坯料尺寸由无凸缘筒形拉深件坯料尺寸计算公式(4-5)D=(3)计算板料相对厚度(t/D)×100,并判断是否采用压边圈t/D×100=1/121.31×100=0.82<1.5,查表4-8,要压边圈(4)拉深系数计算,确定拉深次数,求出工序件尺寸d/D=59/121.31=0.49<[m1]=0.55,不能一次过拉深成形,需要多次拉深。
根据t/D=0.82,查表4-4得各次拉深的极限拉深系数为[m]=0.55,[m2]=0.78,1[m3]=0.80。
d1=[m1]D=0.55×121.31=66.72mm (4-10)d1=[m2]D=0.78×67.55=52.04mm因d2=52.04mm<59mm,所以需采用2次拉深成形。
计算各次拉深工序件尺寸,为了使第2次拉深的直径与零件要求一致,需对极限拉深系数进行调整。
调整后取各次拉深的实际拉深系数为m1=0.57,m2=0.84重新计算各次工序件直径为:d1=m1D=0.57×121.31=69mm (4-10)d2=m2d1=0.85×70=59mm根据公式(4-27和4-28),给出工序件圆角r 1=7,r 2=6.5,计算出各工序件的高度尺寸:()211111110.250.430.3239.2r D h d d r mm d d ⎛⎫=-++= ⎪⎝⎭(4-12) ()222222220.250.430.3250.5r D h d d r mm d d ⎛⎫=-++= ⎪⎝⎭画出工序草图,如图1工序件草图。
第四章 拉深工艺及模具设计

拉深过程中影响起皱的主要因素
板料的相对厚度 t/D
t dt d
t/D 越小,拉深变形区抗失稳的能力越差,越易起皱。
拉深系数 m(切向压应力的大小)
m 越小,拉深变形程度越大,切向压应力的数值越大;另外, 变形区的宽度越大,抗失稳的能力变小,越易起皱。
模具工作部分几何形状
用锥形凹模拉深时,由于毛坯的 过渡形状使拉深变形区有较大的抗失 稳能力,与平端面凹模相比可允许用 相对厚度较小的毛坯而不致起皱。
划分为五个区: I 凸缘部分 II 凹模圆角部分 III 筒壁部分 IV 凸模圆角部分 V 筒底部分
下标1、2、3分别代表 坯料径向、厚向、切 向的应力和应变
坯料各区的应力与应变是很不均匀的。
24.10.2023
IV
24.10.2023
I II
III V
三、拉深变形过程中凸缘变形区的应力分布
拉深至某一瞬时 R t
使
max 1 max
出现在
R t0.7~0.9R 0
即拉深早期。
24.10.2023
四、筒壁传力区的受力分析
(1)压边力Q 引起的摩擦应力
M
2 Q dt
(2)材料流过凹模圆角半径产生弯 曲变形的阻力
W 14b
rd
t t
2
(3)材料流过凹模圆角后又被拉直 成筒壁的反向弯曲力
'WW14b
t rdt
2
24.10.2023
§4-3 直壁旋转体零件的拉深
一、拉深毛坯尺寸的确定
拉深毛坯尺寸的确定原则: 体积不变原则: 若拉深前后料厚不变,拉深前坯料表面积与拉深后
冲件表面积近似相等,得到坯料尺寸。
第4章 拉深

四川信息职业技术学院机电工程系
13
4.3.2 影响极限拉深系数的因素
极限拉深系数的数值取决于筒壁传力区最大拉应力与危险断面的抗拉 强度。因此,凡是影响筒壁传力区的最大拉应力和危险断面的抗拉强度 的因素都会影响极限拉深系数。 1、材料的力学性能 一般来说,材料组织均匀,晶粒大小适当,屈强比小,材料的伸长 率大,塑性好,拉深性能好,极限拉深系数较小。 2、材料相对厚度 t/D 相对厚度t/D愈大,拉深时抵抗失稳起皱的能力愈大,因而可减小 压料力,减小摩擦阻力,有利于减小拉深系数。
第一次拉深系数 第二1
mn =
式中: D—毛坯直径:d1,d2 ,dn—各次拉深后的直径(中径)
四川信息职业技术学院机电工程系 12
dn d n −1
图4-7
4.3.1 拉深系数及其极限
m称为拉深系数,它可以表示拉深变形程度的大小, m愈小,拉深 称为拉深系数,它可以表示拉深变形程度的大小, 愈小 愈小, 称为拉深系数 变形程度愈大, 愈大 拉深变形程度愈小。 愈大, 变形程度愈大, m愈大,拉深变形程度愈小。 从拉深时凸缘变形区的应力分布与起皱和筒壁传力区的受力情况与 拉裂的分析中已经知道,拉深变形程度对凸缘区的径向拉应力和切 向压应力以及对筒壁传力区拉应力影响极大,为了防止在拉深过程中 产生起皱和拉裂的缺陷,就应减小拉深变形程度,即增大拉深系数, 从而减小切向压应力和径向拉应力,减小起皱和拉裂的可能性。 为保证拉深工艺的顺利进行,就必须使拉深系数大于一定值, 为保证拉深工艺的顺利进行,就必须使拉深系数大于一定值,这个 一定的数值即为在一定条件下的极限拉深系数 极限拉深系数。 一定的数值即为在一定条件下的极限拉深系数。拉深系数小于极限 拉深系数,就会使拉深件起皱,破裂或严重变薄。 拉深系数,就会使拉深件起皱,破裂或严重变薄。
第四章 拉深工艺与模具设计
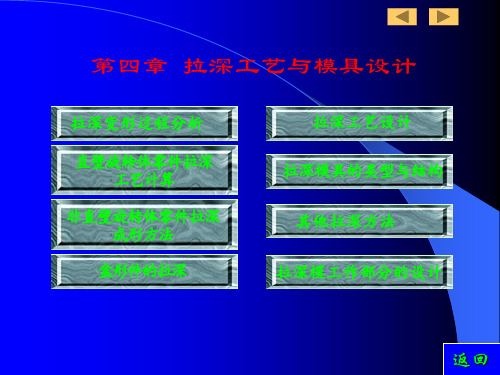
t D
Ky (1
m1 )
以后各次拉深中制件不起皱的条件是: 实践证明:
t di1
K
y
(
1 m1
1)
直壁圆筒形件的首次拉深中起皱最易发生的时刻:拉深的初期
(二)拉裂 当筒壁拉应力超过筒壁材料的抗拉强度时,拉深件就会在底部圆角与 筒壁相切处——“危险断面”产生破裂。
为防止拉裂,可以从以下几方面考虑: (1)根据板材成形性能,采用适当的拉深比和压边力; (2)增加凸模表面粗糙度;改善凸缘部分的润滑条件; (3)合理设计模具工作部分形状;选用拉深性能好的材料等。
第四章 拉深工艺与模具设计
拉深变形过程分析
直壁旋转体零件拉深 工艺计算
非直壁旋转体零件拉深 成形方法
盒形件的拉深
拉深工艺设计 拉深模具的类型与结构
其他拉深方法 拉深模工作部分的设计
返回
拉伸:
拉深是利用拉深模具将冲裁好的平板毛坯压制成各种开口的空心工 件,或将已制成的开口空心件加工成其它形状空心件的一种冲压加 工方法。拉深也叫拉延。
(二)筒壁传力区的受力分析
1.压边力Q引起的摩擦力:
m
2Q dt
2.材料流过凹模圆角半径产生弯曲变形的阻力
w
1 4
b
rd
t t
/
2
3.材料流过凹模圆角后又被拉直成筒壁的反向弯曲w 力 仍按上式进行计
算,拉深初期凸模圆角处的弯曲应力也按上式计算
w
w
1 4
b
rd
t t
2)筒底圆角半径rn
筒底圆角半径rn即是本道拉深凸模的圆角半径rp,确定方法如下:
r r 一般情况下,除末道拉深工序外,可取 pi = di。 对于末道拉深工序:
第四章拉深工艺及拉深模具设计复习题答案(可编辑修改word版)

第四章拉深工艺及拉深模具设计复习题答案一、填空题1.拉深是是利用拉深模将平板毛坯压制成开口空心件或将开口空心件进一步变形的冲压工艺。
2.拉深凸模和凹模与冲裁模不同之处在于,拉深凸、凹模都有一定的圆角而不是锋利的刃口,其间隙一般稍大于板料的厚度。
3.拉深系数m 是拉深后的工件直径和拉深前的毛坯直径的比值,m 越小,则变形程度越大。
4.拉深过程中,变形区是坯料的凸缘部分。
坯料变形区在切向压应力和径向拉应力的作用下,产生切向压缩和径向伸长的变形。
5.对于直壁类轴对称的拉深件,其主要变形特点有:(1)变形区为凸缘部分;(2)坯料变形区在切向压应力和径向拉应力的作用下,产生切向压缩与径向的伸长,即一向受压、一向收拉的变形;(3)极限变形程度主要受传力区承载能力的限制。
6.拉深时,凸缘变形区的起皱和筒壁传力区的拉裂是拉深工艺能否顺利进行的主要障碍。
7.拉深中,产生起皱的现象是因为该区域内受较大的压应力的作用,导致材料失稳_而引起。
8.拉深件的毛坯尺寸确定依据是面积相等的原则。
9.拉深件的壁厚不均匀。
下部壁厚略有减薄,上部却有所增厚。
10.在拉深过程中,坯料各区的应力与应变是不均匀的。
即使在凸缘变形区也是这样,愈靠近外缘,变形程度愈大,板料增厚也愈大。
11.板料的相对厚度t/D 越小,则抵抗失稳能力越愈弱,越容易起皱。
12.因材料性能和模具几何形状等因素的影响,会造成拉深件口部不齐,尤其是经过多次拉深的拉深件,起口部质量更差。
因此在多数情况下采用加大加大工序件高度或凸缘直径的方法,拉深后再经过切边工序以保证零件质量。
13.拉深工艺顺利进行的必要条件是筒壁传力区最大拉应力小于危险断面的抗拉强度。
14.正方形盒形件的坯料形状是圆形;矩形盒形件的坯料形状为长圆形或椭圆形。
15.用理论计算方法确定坯料尺寸不是绝对准确,因此对于形状复杂的拉深件,通常是先做好拉深模,以理论分析方法初步确定的坯料进行试模,经反复试模,直到得到符合要求的冲件时,在将符合要求的坯料形状和尺寸作为制造落料模的依据。
模具设计 演示文稿第4章
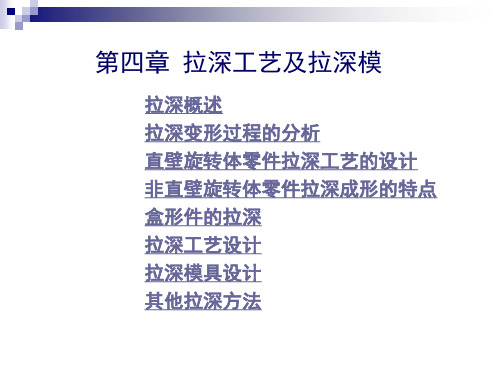
表面拉伤:
材料表面无锈蚀、铁屑等异物和及时修磨模具.
毛坯边缘无裂纹和毛刺:易损伤模具和拉裂零件, 钳工去刺或小零件滚抛.
4-2 直壁旋转体零件拉深工艺的设计 1.拉深毛坯尺寸的确定
拉深毛坯尺寸的确定原则: 体积不变原理(拉深前毛坯表面积等于拉深后 零件的表面积)、相似性原理。 毛坯的计算方法:
拉深件的壁厚和硬度的变化
实际上多是凸模园角处拉裂
筒 壁 的 拉 裂
---应从压Leabharlann 力大、未按零件形状计算 展开尺寸、凹模园 角、过小和凹模润 滑综合分析
• 防止拉裂的措施: ①.可根据板材的成形性能,采用适当的拉深比 和压边力; ②.增加凸模的表面粗糙度(有时在凸模园角与 零件处垫砂布); ③.改善凸缘部分变形材料的润滑条件; ④.适当合理设计模具工作部分的形状; ⑤.适当合理的毛料展开尺寸; ⑥.选用拉深性能好的材料。 ⑦.如果是多次拉深,尤其表面会产生冷作硬化 现象,用中间退火来消除。
1).拉深系数(重要概念)
拉深系数是表示拉深后圆筒形件的直径与拉深
前毛坯(或半成品)的直径之比。 (如图4.2.2)
m1 d1 D m2 d 2 d1 .......... ... mn 1 d n 1 d n 2 mn d n d n 1
工件的直径与毛坯直径之比称为总拉深系数,
举例2:
试确定如下图所示零件(材料08钢, 材料厚度=2mm)的拉深次数和各拉深工 序尺寸。 计算步骤如下: 1).确定切边余量 h 根据 h 200, h / d 200/ 88 2.28 ,查教材 表4-2,并取:h 7 mm 。 2).按公式计算毛坯直径 2 2 展开计算公式 D d 2 2d 2 H 1.72rd 2 0.56r
- 1、下载文档前请自行甄别文档内容的完整性,平台不提供额外的编辑、内容补充、找答案等附加服务。
- 2、"仅部分预览"的文档,不可在线预览部分如存在完整性等问题,可反馈申请退款(可完整预览的文档不适用该条件!)。
- 3、如文档侵犯您的权益,请联系客服反馈,我们会尽快为您处理(人工客服工作时间:9:00-18:30)。
图4-3所示的扇形chef是从板料圆环上截 取的单元,经过拉深后变成了矩形c´h´e´f´。
扇形单元体变形是切
线方向受压缩,径向方向
受拉伸,材料向凹模口流
动,多余的材料(图中阴
影部分)由于流动填补了
双点划线部分。设扇形面
积为A1,拉深后矩形面积
综合起来看,平板毛坯在凸模压力的 作用下,凸模底部的材料变形很小,
一、拉深变形过程
的分析
1、拉深变形过程及特点
圆筒形件的拉深过程如图4-1所示。 直径为D的圆形平板毛坯2被凸模1拉 入凸、凹模的间隙里,形成直径为d 高为H的空心圆柱体4。在这一过程 中,板料金属是如何流动的呢?
如图4-2所示,把直径为D的圆板料 分成两部分:一部分是直径为d的圆 板,另一部分是直径为(D-d)的 圆环部分,把这块板料拉深成直径为 d的空心圆筒。在这个拉伸试验完成 后,发现板料的第一部分变化不大, 即直径为d的圆板仍保持原形状作为 空心圆筒的底,板料的圆环部分变化 相当大,变成了圆柱体的筒壁,这一 部分的金属发生了流动。
3)拉深后工件在各个部分的厚 度是不同的如图4-6所示。
2)在底部圆角与直壁相 接部分工件最薄,最易发生 拉裂,如图4-7所示。
拉深使材料发生塑性变形,所以必然伴随着 加工硬化,如果工件需多次拉深才能成形, 或工件是硬化效应强的金属,则应合理安排 退火工序以恢复材料的塑性,降低其硬度和 强度。
2、影响极限拉深因数的因数 在制定拉深工艺时,拉深次
数愈少愈好.亦即希望尽可能的降低极限拉深因数.在不同的条件下极 限拉深因数是不同的,影响极限拉深因数的因数有以下几个方面:
变形程度是有限的,也就是存在极 限拉深因数,它是由危险截面的强 度来决定的。极限拉深因数是使拉 伸工件不破裂的最小拉深因数。
注:当总拉深因数<极限拉深因数,就必 须进行多次拉深。合理的分配每次 拉深因数是很关键的,一般希望在 保证极限拉深因数的前提下,尽可 能取小的拉深因数,这样就可以减 少拉深次数,提高经济效益。
拉深的变形区比较大,金属流动性大, 拉深过程中容易发生起皱、拉裂而失 败。因此,有必要分析拉深时的应力 状态和变形特点,找出发生起皱、拉 裂的根本原因,在制订工艺和设计模 具时注意它,以提高拉深件的质量。
设在拉深过程的某一时刻,毛坯处于 如图4-4所示情况,分析各部分的 应力状态。
1)平面凸缘部分(A区)_主变形区
终保持平圆形状,它受两向拉应力σ1和σ3的作用。变形是三向的,
ε1和ε3是拉伸,ε2是压缩。由于拉伸变形受到凸模摩擦力的阻止,
故变薄很小,可忽略不计。
见图4-4
图4-4
返回
3、拉深变形的特点
综合对拉伸过程的应力和变形的分析可以看到,拉深会产 生一些特定的现象,即起皱、拉裂和硬化。
1)起皱发生在圆筒形凸缘部分,如图4-5所示,是由切向压应力引起 的。起皱的危害很大,首先,起皱变厚的板料不易被拉入凸、凹模的间 隙里,使拉深件底部圆角部分受力过大而被拉裂。即使勉强拉入也会使 工件留下皱痕,影响工件的质量。它还会使材料与模具之间的摩擦与磨 损加剧,损害磨具的寿命。
由于凸模向下压,迫使板料进入
凹模,故在凸缘产生径向拉应力σ1, 小单元体互相挤压产生切向压应力 σ3,由于压边圈提供的压边力产生 法向压应力σ2,在这3个主应力中
σ2的绝对值比σ1 、σ3的绝对值小 得多。凸缘上σ1 、σ3是变化的,是 凸缘外到内, σ1是由小变大,而σ3 的绝对值则是由大变小,在凸缘的最 外缘σ3的压应力是最大的,则材料 在切向上必然是压缩变形。如果被拉 深的材料厚度较薄,压边力太小,就 有可能是凸缘部分的材料失稳而产生 起皱现象。
2)凸缘圆角部分(B区)_过渡区 这部分的材料受到径向拉应力σ1, 切向压应力σ3,以及凹模圆角的压力和弯曲受压作用共同产生法
向压应力σ2,,此处的σ1值的绝对值最大,则材料会在径向上发生拉 伸变形,材料有变薄的倾向。
3)筒壁部分(C区)_传力区 该部分受到凸模传来的拉应力σ1和凸模 阻碍材料切向自由压缩而产生的拉应力σ3,显然, σ1的绝对值大,径 向是拉伸变形,径向的拉伸是靠壁厚的变薄来实现的,故筒壁上厚下 薄。
总之,了解拉深工艺的这些特点后,在制订 工艺、设计模具时,应考虑如何在保证最大 变形程度下避免毛坯起皱和工件被拉裂。
二、拉深因数
1、拉深因数的概念和意义
对于旋转类工件来说,拉深因数是指 拉深后工件的直径与拉伸前毛坯(或 半成品)的直径之比,拉深因数用m 表示。如图4-8中:
第一次拉深因数m1为:m1=d1/ D;
第四章 拉深模
第一节 拉深模的设计基础 第二节 拉深模的设计示范
第一节 拉深模的设计基础
拉深是把一定形状的平板毛坯或空心件通过拉 深模制成各种空心零件的工序。在冲压生产中 拉深是一种广泛使用的工序,用拉深工序可得 到的制件一般可分为三类:
1、旋转体零件:如搪瓷脸盆、铝锅等。 2、方形零件:如饭盒、汽车油箱等。 3、复杂形状零件:如汽车覆盖件等。
4)底部圆角部分(D区)_过渡区 该部分受到径向拉应力σ1和切向拉应 力σ3的作用,厚度方向上受到凸模的弯曲作用而产生压应力σ2 。材 料变形为平面应变状态,径向拉伸变形,是靠壁厚变薄来实现的,这 部分材料变薄最为严重,最易出现拉裂,此处称为危险断面。
5)圆筒底部(E区)_不变形区 这部分材料一开始就被拉入凹模中,始
为A2,由于拉深时厚度变
而毛坯(D-d)的环形区的金属在
化很小,可认为拉深前后
凸模压力的作用下,要受到拉应力和
面积相等,即A1= A2,所 以,H> (D-d)/2。
压应力的作用,径向伸长、切向缩短, 依次流入凸、凹模的间隙里成为筒壁, 最后,使平板毛坯完全变成圆筒形工
件为止。
2、拉深时的应力 状态和变形情况
第二次拉深因数m2为:m2=d2/d1;
……第n次拉深因数mn=dn/dn-1。
工件直径dn与毛坯直径D之比称为总 拉深因数,即:工件成形所需要的拉 深因数。总的拉深因数:
m总= dn/ D=m1·m2·····mn
若工件是非圆形件,则总的拉深因数 m总=工件周长/毛坯周长
显然,拉深因数永远小于1,且m越小, 变形程度越大。