制程检验作业标准
制程检验作业规范
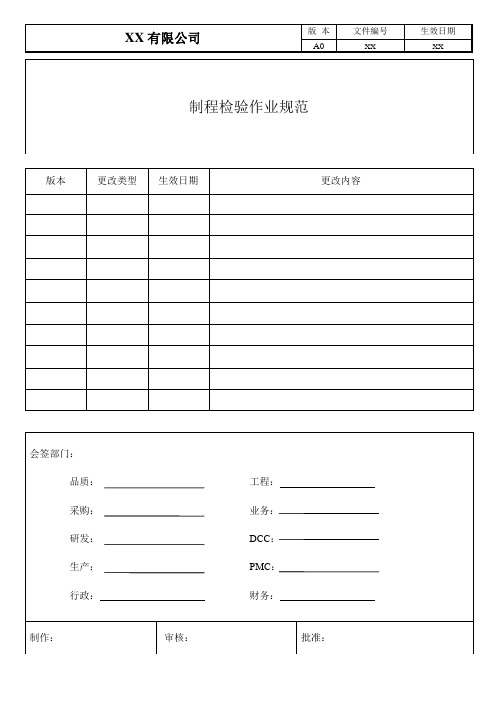
版本
更改类型
生效日期
更改内容
会签部门:
品质:工程:
采购:业务:
研发: DCC:
生产 :PMC:
行政:财务:
制作:
审核:
批准:
1.目的
规范制程检验作业方法,确保产品品质满足客户要求。
2.适用范围
制程检验作业流程。
3.定义
首件:指生产线量产前由生产制作样品的检查。
随机抽样:抽取的样品反映每一个生产时段产品品质。
6.4.3但制程巡检不良率超过3%,IPQC应填写“品质异常矫正单”、连同不良品给个责任部门进行原因分析,责任部门应制定纠正与预防措施,IPQC须加以追踪及效果确认。
6.4.4如产品缺陷无法判断,则应及时呈报班长。
6.4.5不合格品的处理具体依据“不合格品处理程序”作业,纠正与预防措依据“纠正与预防措施控制程序”作业。
品质检验:通过对产品质量进行观察和判断,适当时结合测量、试验进行的符合性评价。
巡检:按一定的时间间隔1H/1次,定期巡回检查:指定专人作在线管制项目定期检查。
抽样:是从要检验的一批产品中,随机抽取一部分产品检验,根据样品的质量,对产品批做出是否合格的判断。
4.作业方法
4.1岗位职责规定如下:
4.1.1工程师或其代理人负责首件确认,不良缺陷确认和判定,预防措施发出及跟进主管指定的其它工作。
8.作业流程图
4.2.4首件检查确认资料: 1) 制造通知单 2) 产品承认书
4.3定期巡回检查:由IPQC巡检人员依规定之点检频率进行抽样检查,巡回检查内容: 依产品管制计划内容检查.
1) 作业指导书是否正确?
2) 作业者是否依作业指导书作业?
3) 机械设备、治工具是否正确使用?
制程检验标准

低
29
表位线
表位留线平齐,长度需符合电表安装要求。
目视
中
30
接线
手试拉不得由松脱或左右晃动的情况。
目视/手试
高
31
线皮、护套
电线安装需有电气防护,但不得压到线皮、护套等。
目视/手试
高
32
配件、附件
塑壳开关绝缘皮、485接线端(柱)等需安装到位。
目视/手试
中
33
全检
元器件
需有确认所有开关、接线盒型号及安装方式的作业步骤。
目视/手试
中
43
箱盖总成
需能与箱底、开关位置配合,符合实际需求。且不得存在脏污等不良。
目视/试装
中
44
敲盖
敲盖
插销、塞子需到位,箱盖能正常开合、开关等均能正常操作。
目视/手试
高
45
铭牌
铭牌需要产品型号配置一致,且需按要求安装(拉铆/黏贴)到位。不得歪斜、偏移。
目视
严重
46
条码、编号
条码(编号)需按生产任务单等单据表述要求操作。
目视/测量
高
6
套端子
端子外端与电线平齐,无铜线外露。
目视
低
7
压端子
压制完成的端子手拉不会脱离电线,端子形状规则并一致。包含485线。
目视/手试
中
8
套铜鼻
电线安插到位。铜鼻与线皮之间的裸露导体长度一致,允许误差±2mm。
目视
中
9
压铜鼻
压制完成后手拉电线不会脱离铜鼻,铜鼻形状需一致。
目视/手试
高
10
工装弯头
工装整套
需核对线与线间的间距是否符合开关间距。
家具厂各种制程作业检验标准

3.1品质部:负责机器加工半成品的品质检验与标识。
3。2机加组:负责不合格品的处理。
4。0品质检验:
4。1检验工具:卡尺、卷尺。
4.2检验方法:工具测量、目视。
4.3品质检验员必须参照限度样板。
4.4品质检验员将结果记录于《巡检记录表》内。
5。0品质要求:
5.1.1工件应与图纸或样品一致(误差为±1 mm)。
5。1.1。4虫柱材必须经过杀虫处理.
5.1.1.5要根据不同的油漆要求选用不同等级的木材。
5。1。1.6端裂或面裂,端裂长度≧10mm不允许,面裂长度≧40mm或宽度≧0。6mm或贯穿者不允许
5。1。1。7。0活节或死节
5.1.1.7。1活节长度≦5cm且在2个以内
不在重要部位者允收
5.1.1。7。2死节长度≦1.5cm且在2个以内
编制/日期
审核/日期
批准/日期
修改/日期
有限公司品质检验标准
标题
机器加工作业品质检验标准
版本
第A版
版次
第0次修改
页码
共2页,第1页
编号
WIQ—017
检验地点
木工车间
检验人员
IPQC
期限
按需要
1。0目的:
为木工组装工序提供符合工程图纸等相关要求的半成品配件.
2.0适用范围:
适用于公司生产用所有机器加工生产过程。
5.2.4产品内部或产品底部等不可见部位,砂光精度为二级:手摸无刺痕、扎手的感觉,无明显崩缺的现象。
编制/日期
审核品质检验标准
标题
砂光作业品质检验标准
版本
第A版
版次
第0次修改
页码
共2页,第2页
制程检验规范
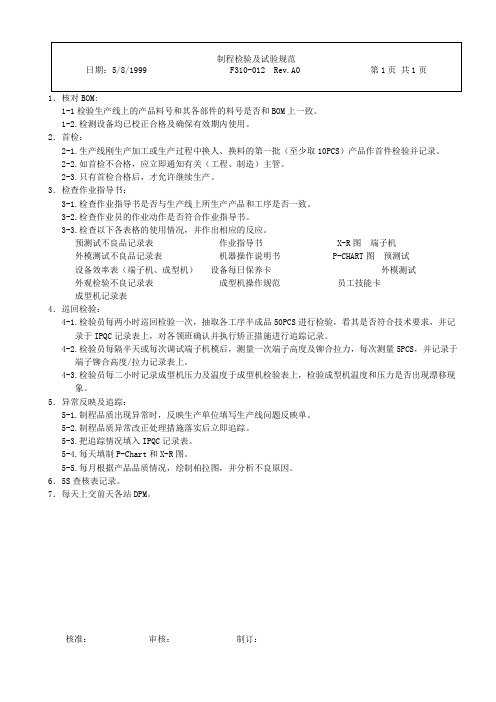
1.核对BOM:1-1检验生产线上的产品料号和其各部件的料号是否和BOM上一致。
1-2.检测设备均已校正合格及确保有效期内使用。
2.首检:2-1.生产线刚生产加工或生产过程中换人、换料的第一批(至少取10PCS)产品作首件检验并记录。
2-2.如首检不合格,应立即通知有关(工程、制造)主管。
2-3.只有首检合格后,才允许继续生产。
3.检查作业指导书:3-1.检查作业指导书是否与生产线上所生产产品和工序是否一致。
3-2.检查作业员的作业动作是否符合作业指导书。
3-3.检查以下各表格的使用情况,并作出相应的反应。
预测试不良品记录表作业指导书 X-R图端子机外模测试不良品记录表机器操作说明书 P-CHART图预测试设备效率表(端子机、成型机)设备每日保养卡外模测试外观检验不良记录表成型机操作规范员工技能卡成型机记录表4.巡回检验:4-1.检验员每两小时巡回检验一次,抽取各工序半成品50PCS进行检验,看其是否符合技术要求,并记录于IPQC记录表上,对各领班确认并执行矫正措施进行追踪记录。
4-2.检验员每隔半天或每次调试端子机模后,测量一次端子高度及铆合拉力,每次测量5PCS,并记录于端子铆合高度/拉力记录表上。
4-3.检验员每二小时记录成型机压力及温度于成型机检验表上,检验成型机温度和压力是否出现漂移现象。
5.异常反映及追踪:5-1.制程品质出现异常时,反映生产单位填写生产线问题反映单。
5-2.制程品质异常改正处理措施落实后立即追踪。
5-3.把追踪情况填入IPQC记录表。
5-4.每天填制P-Chart和X-R图。
5-5.每月根据产品品质情况,绘制柏拉图,并分析不良原因。
6.5S查核表记录。
7.每天上交前天各站DPM。
核准:审核:制订:。
制程检验作业规范

1.目的制程产品的量测与监控,以验证产品符合要求。
2.范围凡本公司制程过程中产品均包括在内。
3.定义(无)4.权责4.1品质部:制程中产品的量测与监控。
4.2生产部:制程中首件产品的送检。
5.作业程序5.1制程产品检验采用首件检验和巡检方式。
5.2 首件检验5.2.1首件检验时机当生产线每日上班开机时、交接班时、不同批换料时、异常处理后。
5.2.1 外观、性能检验首件检验由IPQC按对应《产品工艺流程》中的要求逐一检验。
若发生不合格依《不合格控制程序》处理。
5.2.4检验记录首件检验结果记录于《首检记录表》中,需由IPQC确认结果。
若量测结果符合对应的要求,方可继续生产;若不能符合要求,则须调机或停线,直到符合要求为止。
5.3制程巡检5.3.1巡检时机从生产线开机至产线全部停止生产的整个生产过程,IPQC必须全程在生产线监督指导生产,巡检项目为产线品质记录、量测。
5.3.2外观、性能检验外观、性能检验由IPQC按对应《产品工艺流程图》中的要求逐一检验。
若发现异常时立即通知产线组长和工程师,查找根本原因并改善,若无法当时现场改善需停线处理时巡检人员开立《异常处理报告》查找根本原因,记录于《制程品质检查记录表》巡检报告,并巡检人员及时通知生产与品质主管。
详见《不合格控制程序》。
5.3.3检验记录/频次IPQC每次检验外观抽检10PCS、功能检测5PCS,2小时巡检一次;每2小时在《制程品质检查记录表》记录一次品质状况。
5.4异常管控IPQC在制程巡检过程中发现如有因原材不良或机台、异常导致产品使用功能缺陷或严重影响产品外观时,需开立《异常处理报告》,并及时知会生产现场主管,要求生产人员停止生产进行改善,对己生产不良品要求生产人员进行隔离。
详见《不合格控制程序》。
6.相关资料6.1不合格控制程序6.2产品工艺流程7.表单7.1首检记录表7.2巡检记录表7.3异常处理报告。
制程检验标准

3.5在巡检过程中发现严重问题时,要求现场马上停机,并将不良品与良品分开摆放做好标识,由巡检人员开具品质异常单,交由部门主管审批处理。
4.0制程检验项目
序号
巡检
工序
检查项目
检查工具
检验标准
1
机加工
外观
目测
外观有无砸伤碰伤。
装配
外观
目测
无披锋无毛刺
规格尺寸
卡尺
装配无松动,尺寸能否满足作业指导书上的要求
5
铆接
外观
目视
外观无批锋,爆裂等
尺寸
卡尺,拉力机
外径,高度及拉力要求能否满足作业指导书上的要求。
6
焊接
外观
目视
外观无焊渣,及焊接有无到位,
尺寸,性能
卡尺,扭力扳手
检查焊接的高度,及螺纹的扭力强度。
批 准
审 核
编 制
尺寸
卡尺
长度,宽度,外径,能否满足:作业指导书上的要求
2
冲压
外观
目测
外观有无压伤碰伤,缺料,及批锋
尺寸
卡尺
长度,宽度,外径,能否满足:作业指导书上的要求
3
注塑
压力
目测
注塑压力是否正常
时间
目测
注塑时间是否正确
温度
目测
注塑温度是否正常
尺寸、性能
卡尺,拉力机
长度,宽度,外径,能否满足:作业指导书上的要求
4
文件编号
版本版次
A/1
制程检验标准
生效日期
页 码
1/1
1.0 目的
为确保车间在制程任意时间段均在受控状态平稳生产,特制订本规范。
制程检验规范
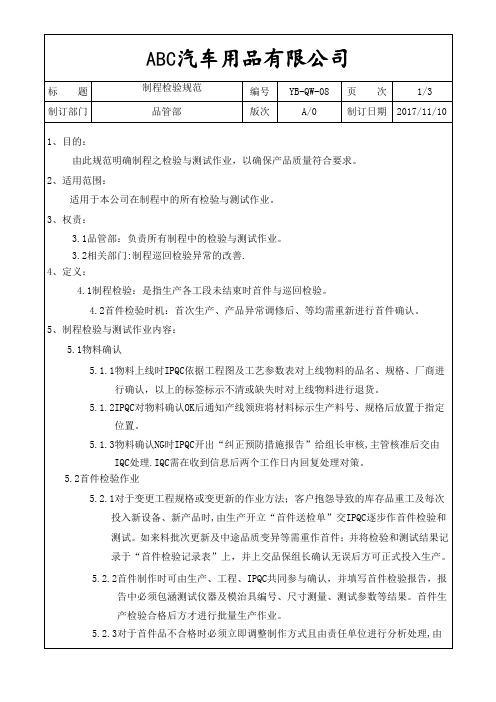
停线时机:
5.4.1新产品未制作首件未经确认而批量投产时。
5.4.2正常生产时不良率超过5%时。
5.4.3无正式发行之工程图、SOP作业时。
5.4.4未依”不合格管制程序”对不合格品及修理品进行标示隔离,未依”产品鉴别与追溯管制程序”和”检验与测试状况管制程序”对产品的状态进行标示和可追溯性进行管制时。
5.4.5客户抱怨的改善对策在生产时未执行时。
5.4.6同一产线同一产品FQC连续批退三次时需开出停线通知单。
6.合格品管制程序
7.表单
7.1首件检验记录表
7.2制程检验记录表
5.2.2首件制作时可由生产、工程、IPQC共同参与确认,并填写首件检验报告,报告中必须包涵测试仪器及模治具编号、尺寸测量、测试参数等结果。首件生产检验合格后方才进行批量生产作业。
5.2.3对于首件品不合格时必须立即调整制作方式且由责任单位进行分析处理,由品保负责确认改善效果,若有相关资料变更时则应重新投入首件制作并重新确认记录。
5、制程检验与测试作业内容:
5.1物料确认
5.1.1物料上线时IPQC依据工程图及工艺参数表对上线物料的品名、规格、厂商进行确认,以上的标签标示不清或缺失时对上线物料进行退货。
制程检验作业规范
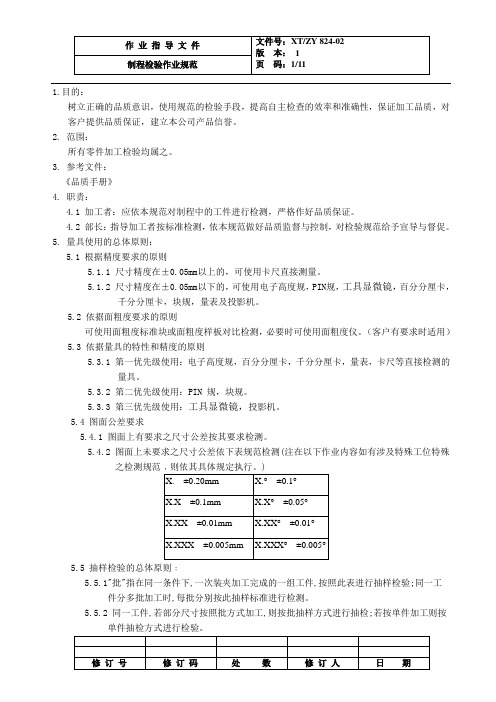
1.目的:树立正确的品质意识,使用规范的检验手段,提高自主检查的效率和准确性,保证加工品质,对客户提供品质保证,建立本公司产品信誉。
2. 范围:所有零件加工检验均属之。
3. 参考文件:《品质手册》4. 职责:4.1 加工者:应依本规范对制程中的工件进行检测,严格作好品质保证。
4.2 部长:指导加工者按标准检测,依本规范做好品质监督与控制,对检验规范给予宣导与督促。
5. 量具使用的总体原则:5.1 根据精度要求的原则5.1.1 尺寸精度在±0.05mm以上的,可使用卡尺直接测量。
5.1.2 尺寸精度在±0.05mm以下的,可使用电子高度规,PIN规,工具显微镜,百分分厘卡,千分分厘卡,块规,量表及投影机。
5.2 依据面粗度要求的原则可使用面粗度标准块或面粗度样板对比检测,必要时可使用面粗度仪。
(客户有要求时适用)5.3 依据量具的特性和精度的原则5.3.1 第一优先级使用:电子高度规,百分分厘卡,千分分厘卡,量表,卡尺等直接检测的量具。
5.3.2 第二优先级使用:PIN 规,块规。
5.3.3 第三优先级使用:工具显微镜,投影机。
5.4 图面公差要求5.4.1 图面上有要求之尺寸公差按其要求检测。
5.4.2 图面上未要求之尺寸公差依下表规范检测(注在以下作业内容如有涉及特殊工位特殊5.5 抽样检验的总体原则﹕5.5.1"批"指在同一条件下,一次装夹加工完成的一组工件,按照此表进行抽样检验;同一工件分多批加工时,每批分别按此抽样标准进行检测。
5.5.2 同一工件,若部分尺寸按照批方式加工,则按批抽样方式进行抽检;若按单件加工则按单件抽检方式进行检验。
5.5.3 单件加工必须全检所有加工尺寸。
5.5.4 进行抽检时,若发现有一件不合格,须对该批进行全验。
6. 作业内容6.1 切削加工检验标准6.1.3 工件的检测项目6.1.4备注: 1‧表中尺寸公差指切削加工直接成型的工件尺寸。
制程检验规范

5.5.5对于新产品,其生产前三批之首件若经IPQC检验发现不合格时,必须呈交生产经理及以上审核确认,判定检验结果并裁定处理方法。
4.职责:
4.1物料上线时的确认。
4.2首末件确认及制程中的巡回检验。
4.3品质、环保、安全异常时开出异常反馈单,并跟进措施的执行情况。
5.作业程序及内容:
5.1生产前准备;检查检验所需仪器、设备,治、工、夹具的运行情况是否符合检验要求,作好仪器、设备的点检、标识与保养工作,并将结果记录于《仪器日常保养记录表》中。
5.7异常处理:
5.7.1当在巡检过程中,若出现重大品质异常,不良率超过10%,导致大批量不良品或无法生产时,IPQC员必须及时知会生产线现场管理人员和PE/QE工程师予以现场处理,并根据实际情况,提出停拉申请,并知会相关部门责任人员解决;待问题改善后,通知生产线回复产,并跟踪改善效果。
5.8退料检查:
5.8.1良品退料:经过外观及性能检验合格,标识准确无误的良品物料,将贴上“良品退料”的合格标贴后,IPQC员在生产线开具的《退料单》上确认签字后,予以良品退料。
5.8.2不良品退料:经过外观及性能检验不合格,标识准确无误的不良品物料,将贴上“不良品退料”的不合格标贴标识清楚,不同供应商的不良品退料要用不同的外卡通包装,且须分析其不良原因与《不良品退料单》上原因相符,并判定准确无误后, IPQC员在生产线开具的《退料单》上签字(有特殊原因的须在不良原因中作特别注明)后,予以不良品退料。
5.5.6.3为加强品质管控,作业人员除本身需对产品进行“自检”外,还需对上工序流下之产品进行“互检”动作。
制程检验标准

一、目的:为确保制程中各阶段产品品质符合规定标准,必须于制程中规划适当之检验作业,并确保唯有检验合格的产品才能移交下一制程及客户,故制定本程序。
二、范围:1.本程序规定产品于制程中检验中检验的规范,制程检测作业检验结果判定,不合格的处理等等。
2.本标准适用本公司固定电阻器制程中之检测作业。
三、职责:1.品保课负责本程序之制订与维护。
2.生产部各作业员负责首件检验,自主抽验及成品自动全选之检验作业。
3.品保课负责制程品质稽核作业。
四、作业内容:1.品保课与生产部参与制程规划时,即针对产品特性客户之需求,而规划制程中之检验活动,含作业者自主检查,品管稽核抽验等。
2.制程检验中之允收标准。
均达到国家标准,客户标准、出货标准为高,以确保出货成品均获得客户允收。
有关产品品质特性制程中规格列如下表所示:3.自主检验生产中规划作业人员自行确认作业之符合性,以达人人品管自负品质责任之境界,自主检验又分:(1)首件检验:指每日开机时,机台维修后更换规格时作业者调试机台后,作业员及QC应参照下表抽样确认产品特性。
(2)自主检查生产中作业人员必须定时巡回各机台,约1小时1次确认生产状态,检查项目参照各部门外观检查标准及作业标准书实施。
4.焊接制程之[焊点是否牢固]一项,是为确定抗拉力强度为求效率。
均以尖咀钳代替拉力计,每一次取样5PCS/台,试验方法如下:以尖咀钳夹住导线焊接点处,向本体弯曲90度,焊接点不得有脱落情形。
(1)焊接端子拉力强度判断标准:《使用工具东京120拉力计》1/2W:4kg以上1/4W:3kg以上1/6W:2.5kg以上1W : 4.5kg以上2W : 5kg以上5.有关自主检验各制程检查项目品质判定标准,参考工作区外观检查标准及各站作业标准书。
五、自动全数筛选:电阻器产品于加电压(短时间过负荷)后及涂装完成后,必须经阻值100%自动选别测试,将阻值误差高于设定标准的检出予以剔除。
六、品管稽核抽验1.除以上检验与筛选外,制程中又安排品管人员执行品管稽核抽验对切割作业,焊接作业及涂装作业等三个重要制程作抽样检验。
制程检验规范
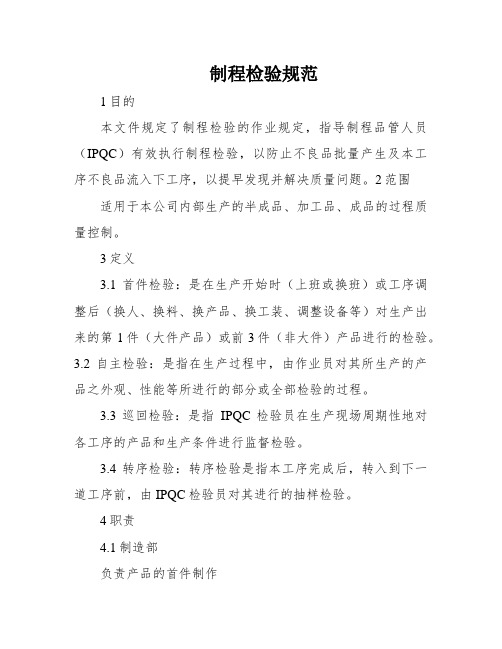
制程检验规范1目的本文件规定了制程检验的作业规定,指导制程品管人员(IPQC)有效执行制程检验,以防止不良品批量产生及本工序不良品流入下工序,以提早发现并解决质量问题。
2范围适用于本公司内部生产的半成品、加工品、成品的过程质量控制。
3定义3.1首件检验:是在生产开始时(上班或换班)或工序调整后(换人、换料、换产品、换工装、调整设备等)对生产出来的第1件(大件产品)或前3件(非大件)产品进行的检验。
3.2自主检验:是指在生产过程中,由作业员对其所生产的产品之外观、性能等所进行的部分或全部检验的过程。
3.3巡回检验:是指IPQC检验员在生产现场周期性地对各工序的产品和生产条件进行监督检验。
3.4转序检验:转序检验是指本工序完成后,转入到下一道工序前,由IPQC检验员对其进行的抽样检验。
4职责4.1制造部负责产品的首件制作负责生产进程中每工序产品的自主检验负责参与不及格品的评审和处理4.2品管部负责首件检验和记录负责制程巡检和转序检验负责参与不及格品的评审和监督处理情形5作业内容5.1检验前准备:检验员于物料上线前依据周生产计划表、派工单,相识当日生产之产品,需事先掌握下列状况:A.订单要求B.客户特殊要求C.紧急上线,未经进料检验之物料D.是否有特采物料E.是否有新进员工F.是否为新产品G.是否有设计变更H.是否发生客诉之产品I.是否有上次生产呈现过质量异常之产品5.2首件生产及检验5.2.1首件确认时机A.每日刚入手下手生产时;B.换人、换机、换料、换产品生产时;C.修机、异常处理后重新生产时5.2.2生产部门遵照《生产管理程序》在正式生产前先做首件加工。
5.2.3操纵员在加工好第一个产品时,首先按图纸或工艺文件的要求举行自主检查,自检及格后交品管检验员,检验员依样品、图纸、工艺文件举行重要尺寸、外观等检验,及格由检验员在首件产品上作“首件及格“标示,放置于生产线旁做封样参照,并做好《首件检查记录表》。
制程检验作业规范

√
压接
端子
外观
目视/端子铆压规范
/
1.无半包,全包,铜丝伸入功能区,外被铆伤,铆断铜丝等不良
20PCS/H
√
尺寸
端子铆压规范
卡尺
1.尺寸须符合工程图面要求
2.内外铆的高宽度及基端子拉力须符合端子铆压规范要求
20PCS/H
√
插HOUSING
外观
目视
/
1.确认产线作业人员在作业过程中在端子插入housing后是否有一个端子回拉的动作。
20PCS/2H
√
理线
外观
目视
/
理线后无铜丝断股,铜丝散乱,飞丝等不良现象
20PCS/2H
√
剥芯线
外观
目视
/
1.前后两端的剥线的切口部位须平齐,无线皮未剥净现象
2.剥被无伤铜丝及铜丝剥断现象(7/0.12不允许有断铜丝,7支以上允许断1根)
3.一般剥芯线尺寸须控制在1.5~2mm
20PCS/2H
√
尺寸
5.3.2巡回檢驗發現外观不良超过3%以上,功能不良超过0.5%时,IPQC须開出《異常通知單》,知会给制造,工程,生管,并通知生产线停线,待不良
完全改善至此范围之内(外观不良3%以内,功能不良0.5%以内)时方可重新生产。
5.4压接产品类:
工序名称
检验项目
检验方法
/依据
检验工具
检验要求
抽样数量
异常类别
7.使用表单
7.1《首件记录表》
7.2《IPQC巡检报表》
7.3《端子测量记录表》
2.检查外包装箱无破损、压伤现象。
3.检查外包装箱之印字/写字内容是否正确。
家具厂各种制程作业检验实用标准
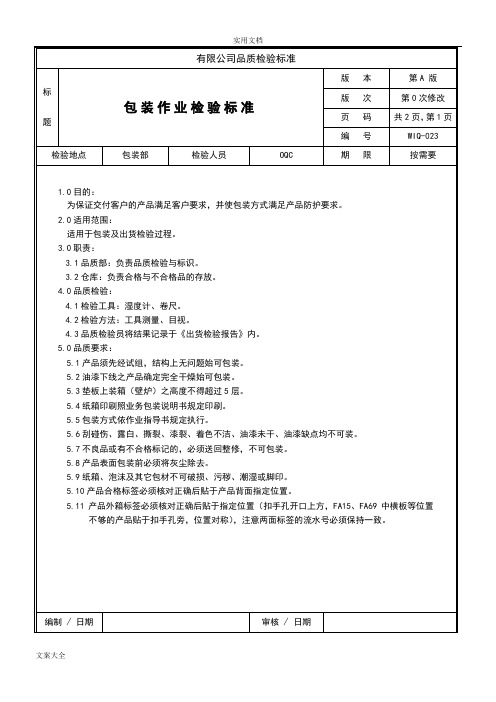
5.1. 3水胶带或胶水印应砂除
5.2.0手砂
5.2.1砂光精度四级,浅色透木纹类:表面应无任何毛刺、跳刀痕、雕痕、胶水印、补灰痕、刮痕、粗砂痕及凹凸不平等现象,砂光细腻,手感柔滑。不允许砂变形(特别注意雕刻部位和工艺线),边角不可锋利,倒角柔畅、均匀。
5.2.6实木嵌补不能有明显色差、断痕、胶痕和修补痕迹。
5.2.7清漆、浅色产品严禁用502胶水修补。补土颜色需调制与木材颜色接近。
5.2.8宽≥1mm,长≥10mm的缝隙由木工砂光人员修补。宽<1mm,长<10mm(结构性)的缝隙由油漆部打磨修补,但非结构性缝隙,如开裂、崩缺、撕裂等应由木工部处理。
成型
宽深度
±0.5
±0.5
±0.5
凸榫
直线度
0.3
0.3
长宽厚
0.1
-0.3
凹榫
长宽厚
0.1
+0.2
车床
直径
0.5
注:①单件之间公差:批量生产中部件与部件之间的不等尺寸公差。
②批量性同时尺寸公差:批量各部位尺寸同时与图纸或样品之间的实际公差范围。
编制/日期
审核/日期
批准/日期
修改/日期
有限公司品质检验标准
编制/日期
审核/日期
批准/日期
修改/日期
有限公司品质检验标准
标 题
机器加工作业品质检验标准
版 本
第A版
版 次
第0次修改
页 码
共2页,第1页
编 号
WIQ-017
检验地点
木工车间
检验人员
制程检验标准

广津机电设备有限公司备注:以上各道工序不允许出现碰伤现象6.3.2尺寸检验本公司尺寸及零配件加工尺寸检验按公司技术图纸或客户图纸要求执行。
编制审核批准7、抽样计划7.1产品批量上线前,要求质检员做好首检、日常巡检工作由质检员填写《首件确认记录表》进行检测,如首检确认不合格必须采取相应措施解决问题,整改合格后重新确认直至合格后方可进行批量生产。
7.2对于生产批量小于10件的产品或客户对质量有特殊要求的产品公司规定必须全检。
7.3对于批量大于10件,且生产能力满足精度要求的实施抽样检验。
7.4制程检验过程中出现不合格品时,必须按要求做好待处理或不合格品、返工、返修,报废件的状态标识牌,并进行隔离。
7.5巡检按每隔1—2小时抽检1件~5件,如出现异常情况可加大抽检比例,并填写《巡检记录表》。
7.6半成品入库抽样计划依据抽样标准,正常检验单次抽样计划,并填写《成品检验报告单》。
7.7公司规定半成品入库检验标准,重要缺失及主要缺失AQL按0.65级,次要缺失AQL按4.0级,检验按照II级检验标准。
8、检验记录8.1检验员将检验结果填写在《首件确认记录表》、《巡检记录表》、《成品(零部件)检验报告单》、《成品(支架)》与《成品(主驱动)自检表》上。
8.2《首件确认记录表》、《巡检记录表》、《成品(零部件)检验报告单》、《成品(支架)》与《成品(主驱动)自检表》,每月底汇总交品质部品质保存,限期1年。
8.3制程检验过程中出现不合格时,经车间质量主管确认后按《不合格控制程序》执行。
9、相关文件9.1《监视和测量控制程序》9.2《不合格品控制程序》9.3国标及其它标准9.4抽样计划按抽样标准正常检验单次抽样计划。
编制审核批准。
制程检验规范
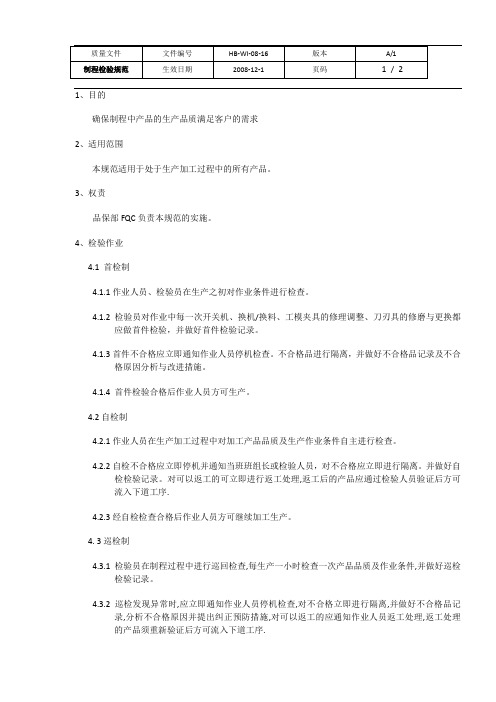
1、目的确保制程中产品的生产品质满足客户的需求2、适用范围本规范适用于处于生产加工过程中的所有产品。
3、权责品保部FQC负责本规范的实施。
4、检验作业4.1 首检制4.1.1作业人员、检验员在生产之初对作业条件进行检查。
4.1.2 检验员对作业中每一次开关机、换机/换料、工模夹具的修理调整、刀刃具的修磨与更换都应做首件检验,并做好首件检验记录。
4.1.3首件不合格应立即通知作业人员停机检查。
不合格品进行隔离,并做好不合格品记录及不合格原因分析与改进措施。
4.1.4 首件检验合格后作业人员方可生产。
4.2自检制4.2.1作业人员在生产加工过程中对加工产品品质及生产作业条件自主进行检查。
4.2.2自检不合格应立即停机并通知当班班组长或检验人员,对不合格应立即进行隔离。
并做好自检检验记录。
对可以返工的可立即进行返工处理,返工后的产品应通过检验人员验证后方可流入下道工序.4.2.3经自检检查合格后作业人员方可继续加工生产。
4. 3巡检制4.3.1检验员在制程过程中进行巡回检查,每生产一小时检查一次产品品质及作业条件,并做好巡检检验记录。
4.3.2 巡检发现异常时,应立即通知作业人员停机检查,对不合格立即进行隔离,并做好不合格品记录,分析不合格原因并提出纠正预防措施,对可以返工的应通知作业人员返工处理,返工处理的产品须重新验证后方可流入下道工序.4.3.3 经巡检检验合格后作业人员方可继续加工生产。
4.4转站核查4.4.1在制品转入下一站加工时,品保部检验员应对产品标示卡进行核查,若标示卡填写内容与要求不符,(如产品名称,批次号,数量,日期等)则予以拒收,标识卡与实物相符后方可接收.4.4.2品保部检验员依据抽样检验规范>对中转站在制品进行抽样检验,并做好检验记录。
4.4.3经抽样检验不合格品进行隔离,不合格品按《不合格品控制程序》执行。
4.4.4经检验合格后产品方可转入下一站加工。
相关文件与表格《不合格品控制程序》《首件检验记录》《自检检验记录》《巡检检验记录>。
制程检验标准SIP(线外加工检验工序内容图示)指导培训04
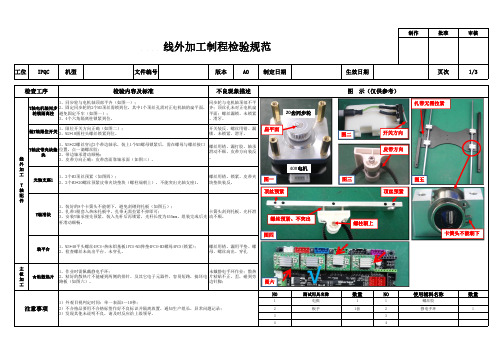
线外加工制程检验规范制作批准审核工位IPQC机型文件编号版本A0制定日期生效日期页次1/3检查工序检验内容及标准不良现象描述图 示(仅供参考)线外加工Y 轴配件Y轴电机装同步轮锁隔离柱1、同步轮与电机轴顶部平齐(如图一);2、固定同步轮的2个M3顶丝需锁到位,其中1个顶丝孔需对正电机轴的扁平面,避免固定不牢(如图一);3、4个六角隔离柱锁紧到位。
同步轮与电机轴顶部不平齐;顶丝孔未对正电机扁平面;螺丝漏锁、未锁紧、滑牙。
装Y轴限位开关1、限位开关方向正确(如图二);2、M2*10圆柱头螺丝锁紧到位。
开关装反、螺丝用错、漏锁、未锁紧、滑牙。
Y轴皮带夹块垫块1、M3*22螺丝穿过2个带边轴承,装上1个M3螺母锁紧后,需在螺母与螺丝接口位置,点一滴螺丝胶;2、带边轴承滑动顺畅;3、皮带方向正确:皮带齿面靠轴承面(如图三)。
螺丝用错、漏打胶、轴承滑动不顺、皮带方向装反。
光轴支座11、2个M3顶丝预紧(如图四);2、2个M3*20螺丝预紧皮带夹块垫块(螺柱端朝上),不能突出光轴支座1。
螺丝用错、锁紧、皮带夹块垫块装反。
Y轴滑块1、装好的8个卡簧头不能朝下,避免刮磳到托板(如图五);2、扎带1根套入热床托板中,扎带无需拉紧不掉即可;3、安装Y轴承座先预紧,装入光杆后再锁紧,光杆长度为455mm,组装完成后光杆滑动顺畅。
卡簧头刮到托板、光杆滑动不顺。
装平台1、M3*40平头螺丝4PCS+热床铝基板1PCS+M3弹垫4PCS+M3螺母4PCS(锁紧);2、检查螺丝未高出平台、未穿孔。
螺丝用错、漏用平垫、螺母、螺丝高出、穿孔主板加工★粘散热片1、作业时需佩戴静电手环;2、粘好的散热片不能碰到两侧的排针、及其它电子元器件,容易短路,搞坏电路板(如图六)。
未戴静电手环作业;散热片粘贴不正、歪,碰到旁边针脚;注意事项1)外观目视判定时间:单一表面5~10秒;2)不合格品要用不合格标签作好不良标识并隔离放置,通知生产组长,异常问题记录;3)发现其他未说明不良,请及时反应给上级领导。
制程检验作业标准
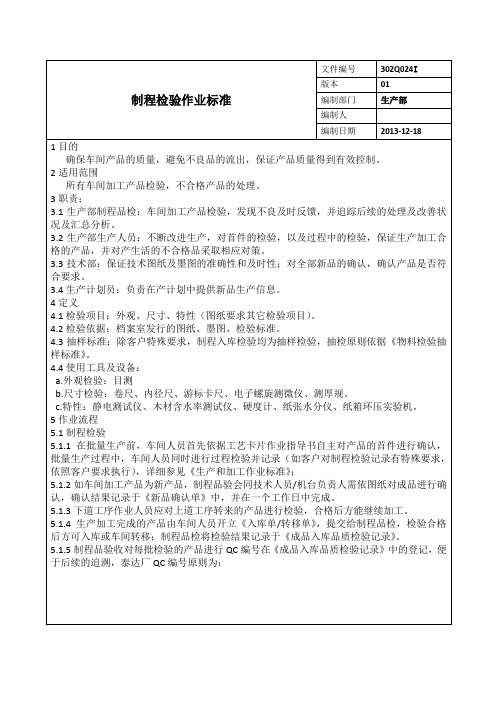
5.1制程检验
5.1.1在批量生产前,车间人员首先依据工艺卡片作业指导书自主对产品的首件进行确认,批量生产过程中,车间人员同时进行过程检验并记录(如客户对制程检验记录有特殊要求,依照客户要求执行),详细参见《生产和加工作业标准》;
5.1.2如车间加工产品为新产品,制程品验会同技术人员/机台负责人需依图纸对成品进行确认,确认结果记录于《新品确认单》中,并在一个工作日中完成。
5.2.6如涉及到交期等异常问题其它部门对生产部的处理结果提出异议时,详见《不合格品管制程序》。
5.3品质问题追溯
制程检验作业标准
文件编号
302Q024I
版本
01
编制部门
生产部
编制人
编制日期
2013-12-18
如厂内任何阶段发现品质出现异常时,可从QC编号或内部订单号、采购订单号追查相关制程检验记录及生产情况记录,并可由此记录追查到来料检验记录,进而分析造成品质异常的制程/来料原因,具体见《QC工程图》之描述。
5.4特殊产品:目测外观干净无破损,有印刷部分则要求印刷清晰,位置准确,不歪斜,不露白等一些印刷问题。
6引用文件
6.1《产品报废作业标准》
6.2《车间退库作业标准》6.3《不合格品管制程序》6.4《生产和加工作业标准》
7相关记录
7.1《成品入库品质检验记录》
7.2《QC工程图》
8流程图
见附页
制程检验作业标准
5.2不合格品的处理:
5.2.1首件检验不合格时,车间人员应立即改善、调整、再次首件检验合格后方可生产。
5.2.2如制程异常对产品品质造成严重不良影响时,经生产主管确认后,车间应立即停止生产,由相关人员进行原因分析提出改善对策,调整直至产品合格方可继续生产。
- 1、下载文档前请自行甄别文档内容的完整性,平台不提供额外的编辑、内容补充、找答案等附加服务。
- 2、"仅部分预览"的文档,不可在线预览部分如存在完整性等问题,可反馈申请退款(可完整预览的文档不适用该条件!)。
- 3、如文档侵犯您的权益,请联系客服反馈,我们会尽快为您处理(人工客服工作时间:9:00-18:30)。
制程检验作业标准
作业文件
WG-QC-013
起草:
审核:
批准:
20 年月日发布 20 年月日实施
一、目的:
为规范IPQC对过程产品品质控制及作业方法,使产品在生产过程中得到有效的控制。
二、适用范围:
适用于本公司的IPQC检验工作。
三、定义:
IPQC:即生产过程品质控制(In process Quality Control)。
四、职责:
4.1首件确认在下列情况下应该进行首检确认:
4.1.1:一批产品开始投产时;
4.1.2:设备重新调整或工艺有重大变化时;
4.1.3:轮班或操作人员变化时;
4.1.4:原材料种类或材料发生变化时。
4.2对制程产品定时进行抽验;
4.3品质异常的回馈及改善追踪。
五、内容:
1.制程检验分首件检验和巡机检验,制程检验流程图如附件一。
2.检验依据
制程检验依《制程检验作业标准》以及《制程检验规范》执行。
3.检验时机
3.1首件和巡检时机依《制程检验规范》执行。
3.2制程检验频率、抽样计划、检验项目、判定标准、量测工具等依各系列
产品《制程检验规范》执行
4. 取样
检验员于检验前核对物料使用的正确性,无误后,再进行取样检验。
5.检验判定
5.1 检验判定合格时,检验员将检验结果记录于《制程检验报告表》
中,通知生产课正常生产:
5.2 检验判定不合格之处理
5.2.1巡机检验判定不合格时,检验员填写制程检验报告表并通知生产课
组长要求停止生产,组长则应要求生技人员作原因分析调查和调修
机台;除手动组装机外,其它机器之停机,应在工程工模/设备维修保养记
录表上填写停机原因、时间以及改善方式;若生产过程中出现重大异常无
法排除急需停线时立即通知品质主管召。