连铸结晶器工作原理
钢铁冶炼中的连铸结晶器设计分析
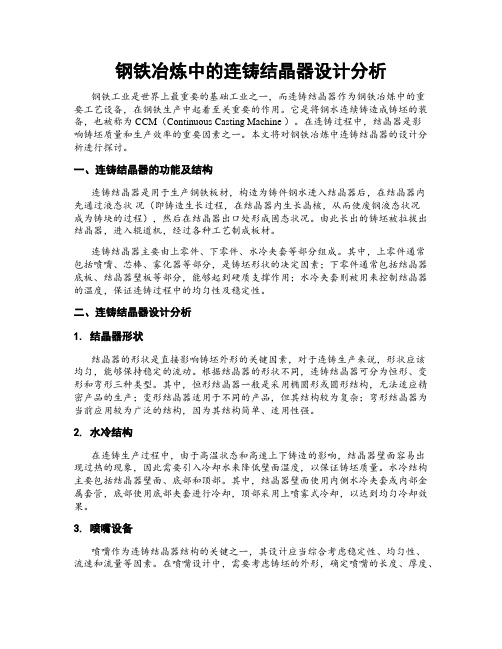
钢铁冶炼中的连铸结晶器设计分析钢铁工业是世界上最重要的基础工业之一,而连铸结晶器作为钢铁冶炼中的重要工艺设备,在钢铁生产中起着至关重要的作用。
它是将钢水连续铸造成铸坯的装备,也被称为CCM(Continuous Casting Machine )。
在连铸过程中,结晶器是影响铸坯质量和生产效率的重要因素之一。
本文将对钢铁冶炼中连铸结晶器的设计分析进行探讨。
一、连铸结晶器的功能及结构连铸结晶器是用于生产钢铁板材,构造为铸件钢水进入结晶器后,在结晶器内先通过液态状况(即铸造生长过程,在结晶器内生长晶核,从而使废钢液态状况成为铸块的过程),然后在结晶器出口处形成固态状况。
由此长出的铸坯被拉拔出结晶器,进入辊道机,经过各种工艺制成板材。
连铸结晶器主要由上零件、下零件、水冷夹套等部分组成。
其中,上零件通常包括喷嘴、芯棒、雾化器等部分,是铸坯形状的决定因素;下零件通常包括结晶器底板、结晶器壁板等部分,能够起到硬质支撑作用;水冷夹套则被用来控制结晶器的温度,保证连铸过程中的均匀性及稳定性。
二、连铸结晶器设计分析1. 结晶器形状结晶器的形状是直接影响铸坯外形的关键因素,对于连铸生产来说,形状应该均匀,能够保持稳定的流动。
根据结晶器的形状不同,连铸结晶器可分为恒形、变形和弯形三种类型。
其中,恒形结晶器一般是采用椭圆形或圆形结构,无法适应精密产品的生产;变形结晶器适用于不同的产品,但其结构较为复杂;弯形结晶器为当前应用较为广泛的结构,因为其结构简单、适用性强。
2. 水冷结构在连铸生产过程中,由于高温状态和高速上下铸造的影响,结晶器壁面容易出现过热的现象,因此需要引入冷却水来降低壁面温度,以保证铸坯质量。
水冷结构主要包括结晶器壁面、底部和顶部。
其中,结晶器壁面使用内侧水冷夹套或内部金属套管,底部使用底部夹套进行冷却,顶部采用上喷雾式冷却,以达到均匀冷却效果。
3. 喷嘴设备喷嘴作为连铸结晶器结构的关键之一,其设计应当综合考虑稳定性、均匀性、流速和流量等因素。
连铸的原理

连铸的原理
连铸是一种先进的铸造工艺,它通过在同一设备上连续进行浇铸和凝固,实现了铸坯的一次成型,大大提高了生产效率和产品质量。
连铸的原理主要包括连续浇铸、连续凝固和连续切割三个方面。
首先,连续浇铸是指在连铸设备上通过连续浇注熔融金属,使金属液不间断地流入结晶器中。
这样可以避免浇注过程中的温度变化和氧化,保证了金属液的纯净度和温度稳定性。
同时,连续浇铸还可以减少浇注过程中的气体夹杂和金属液的氧化,提高了产品的内部质量。
其次,连续凝固是指在结晶器中,熔融金属通过连续往复的凝固过程,逐渐形成固态铸坯。
在这个过程中,结晶器内部的冷却系统不断地将热量带走,使金属液逐渐凝固成固态金属。
通过控制结晶器的温度和冷却速度,可以实现对铸坯组织和性能的精确控制,从而获得更高质量的产品。
最后,连续切割是指在连铸设备的出口处,通过连续的切割装置将凝固成型的铸坯切割成所需长度的产品。
这样可以避免传统浇铸中的冷却等待时间,提高了生产效率。
同时,连续切割还可以减少铸坯表面的氧化和变形,保证了产品的表面质量和尺寸精度。
总的来说,连铸的原理是通过连续浇铸、连续凝固和连续切割,实现了铸坯的一次成型,大大提高了生产效率和产品质量。
这种先进的铸造工艺在现代工业生产中得到了广泛应用,为各种金属制品的生产提供了可靠的技术保障。
344-其他资源-连铸机的结晶器

2.6 结晶器☐结晶器是连铸机非常重要的部件,称之为连铸设备的“心脏”。
钢液在结晶器内冷却初步凝固成一定坯壳厚度的铸坯外形,并被连续地从结晶器下口拉出,进入二冷区。
结晶器应具有良好的导热性和刚性,不易变形和内表面耐磨等优点,而且结构要简单,便于制造和维护。
☐按结晶器外形可分为直结晶器和弧形结晶器。
直结晶器用于立式、立弯式及直弧形连铸机,而弧形结晶器用在全弧形和椭圆形连铸机上。
☐从结构来看,有管式结晶器和组合式结晶器。
小方坯及矩形多采用管式结晶器,而大型方坯、矩型坯和板坯多采用组合式结晶器。
管式结晶器的结构如图所示。
其内管为冷拔异形无缝铜管,外面套有钢质外壳,钢管与铜套之间留有约7mm的缝隙通以冷却水,即冷却水缝。
铜管与钢套可以制成弧形或直形。
铜管的上口通过法兰用螺钉固定在钢质的外壳上,铜管的下口一般为自由端,允许热胀冷缩,但上下口都必须密封。
结晶器外套是圆形的。
外套中部有底脚板,将结晶器固定在振动框架上。
结晶器铜制壁厚10-15mm,磨损后可加工修复,但最薄不能小于3-6mm。
1-O形密封圈;2-润滑法兰;3-O形密封圈;4-铜管;5-压紧法兰;6-压紧弹簧;7-排水管;8-足辊组合式结晶器是由4块复合壁板组合而成。
每块复合壁板都是由铜质内壁和钢质外壳组成。
在与钢壳接触的铜板面上铣出许多沟槽形成中间水缝。
复合壁板用双螺栓连接固定,冷却水从下部进入,流经水缝后从上部排出。
4块壁板有各自独立的冷却水系统。
在4块复合壁板内壁相结合的角部,垫上厚3-5mm并带来45°倒角的铜片,以防止铸坯角裂。
现已广泛采用宽度可调的板坯结晶器。
可用手动、电动或液压驱动调节结晶器的宽度。
内壁铜板厚度在20-50mm,磨损后可加工修复,但最薄不能小于10mm。
随着连铸机拉坯速度的提高,出结晶器下口的铸坯坯壳厚度越来越薄;为了防止铸坯变形或出现漏钢事故,采用多级结晶器技术。
多级结晶器即在结晶器下口安装足辊、铜板或冷却格栅。
炼钢过程中的连铸技术改进与优化

炼钢过程中的连铸技术改进与优化随着现代工业的快速发展,钢铁行业在全球范围内扮演着重要的角色。
炼钢是制造钢材的关键过程之一,而连铸技术在炼钢过程中的应用越来越广泛。
本文将探讨炼钢过程中连铸技术的改进与优化措施,以提高钢材质量和生产效率。
一、连铸技术的基本原理与流程连铸技术是指将炼钢炉中液态钢水直接注入连铸机中,通过结晶器的作用,使其快速凝固为连续坯料。
基本上,连铸技术分为结晶器区、中间区和加热区三个部分。
结晶器区是最重要的部分,其作用是促使钢水迅速凝固形成坯料。
中间区则起到支撑坯料并保持其形状的作用,加热区则用来提供所需的坯料温度。
二、连铸技术改进的原因尽管连铸技术已经成为钢铁生产中主要的浇铸方法,但仍然存在一些问题和潜在的改进空间。
首先,连铸坯料的质量不稳定是一个重要问题。
由于熔铸过程中的各种因素,如温度、流速、结晶器形状等,坯料的结构和性能可能会出现变化。
这导致了产品的不均匀性和不稳定性。
其次,连铸过程中易产生气孔和夹杂物的问题也需要解决。
气孔和夹杂物对钢材的力学性能和外观质量有着显著影响。
此外,传统的连铸技术在能源消耗和生产效率方面也存在一些局限。
例如,冷却设备和传输系统的耗能较高,同时生产线上的工作效率较低。
因此,为了改进钢铁行业的连铸技术,提高生产效率和产品质量,钢铁企业已经采取了一系列的措施。
三、连铸技术改进与优化措施1. 结晶器改进结晶器是连铸技术中最关键的部分,对坯料质量起到决定性的作用。
通过改进结晶器的设计和材料,可以提高坯料的凝固性能和整体质量。
现代连铸技术使用先进的结晶器涂层和陶瓷材料,以减少坯料表面张力和增加热传导率。
此外,优化结晶器的几何形状和冷却系统,可以提高坯料的结晶行为和熔体流动性。
2. 连铸过程控制技术连铸过程中的温度、流速和加热条件等参数对坯料质量有着直接的影响。
通过引入先进的控制技术,如自动化控制系统和实时监测装置,可以实现对连铸过程的精细控制和优化。
自动化系统可以实时监测和调整炉温、浇注速度和结晶器温度等参数,以确保坯料的一致性和质量。
连铸结晶器总成(英)
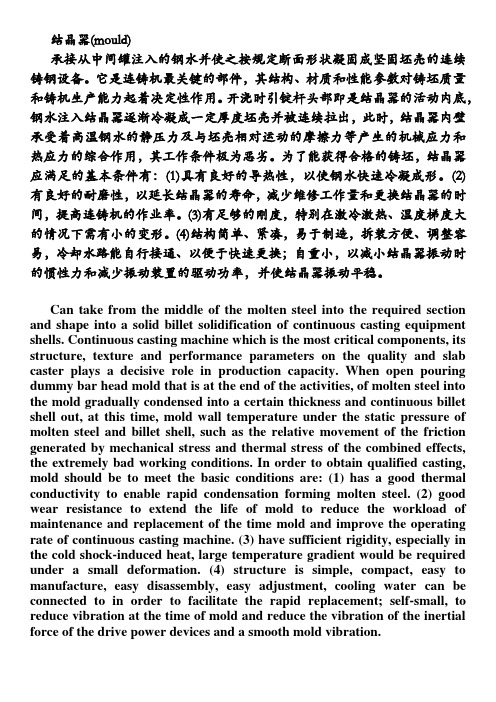
结晶器(mould)承接从中间罐注入的钢水并使之按规定断面形状凝固成坚固坯壳的连续铸钢设备。
它是连铸机最关键的部件,其结构、材质和性能参数对铸坯质量和铸机生产能力起着决定性作用。
开浇时引锭杆头部即是结晶器的活动内底,钢水注入结晶器逐渐冷凝成一定厚度坯壳并被连续拉出,此时,结晶器内壁承受着高温钢水的静压力及与坯壳相对运动的摩擦力等产生的机械应力和热应力的综合作用,其工作条件极为恶劣。
为了能获得合格的铸坯,结晶器应满足的基本条件有:(1)具有良好的导热性,以使钢水快速冷凝成形。
(2)有良好的耐磨性,以延长结晶器的寿命,减少维修工作量和更换结晶器的时间,提高连铸机的作业率。
(3)有足够的刚度,特别在激冷激热、温度梯度大的情况下需有小的变形。
(4)结构简单、紧凑,易于制造,拆装方便、调整容易,冷却水路能自行接通、以便于快速更换;自重小,以减小结晶器振动时的惯性力和减少振动装臵的驱动功率,并使结晶器振动平稳。
Can take from the middle of the molten steel into the required section and shape into a solid billet solidification of continuous casting equipment shells. Continuous casting machine which is the most critical components, its structure, texture and performance parameters on the quality and slab caster plays a decisive role in production capacity. When open pouring dummy bar head mold that is at the end of the activities, of molten steel into the mold gradually condensed into a certain thickness and continuous billet shell out, at this time, mold wall temperature under the static pressure of molten steel and billet shell, such as the relative movement of the friction generated by mechanical stress and thermal stress of the combined effects, the extremely bad working conditions. In order to obtain qualified casting, mold should be to meet the basic conditions are: (1) has a good thermal conductivity to enable rapid condensation forming molten steel. (2) good wear resistance to extend the life of mold to reduce the workload of maintenance and replacement of the time mold and improve the operating rate of continuous casting machine. (3) have sufficient rigidity, especially in the cold shock-induced heat, large temperature gradient would be required under a small deformation. (4) structure is simple, compact, easy to manufacture, easy disassembly, easy adjustment, cooling water can be connected to in order to facilitate the rapid replacement; self-small, to reduce vibration at the time of mold and reduce the vibration of the inertial force of the drive power devices and a smooth mold vibration.分类按拉坯方向上断面内壁的线型分结晶器的型式有弧形和直形两种;按其总体结构,不论弧形或直形均有套管式和组合式两种。
连铸机结晶器液位控制系统数学模型及其仿真

连铸机结晶器液位控制系统数学模型及其仿真连铸机结晶器液位控制系统是一个复杂的系统,它的性能直接影响到连铸机的生产效率,因此,对连铸机结晶器液位控制系统的研究是非常重要的。
本文首先简要介绍了连铸机结晶器液位控制系统的结构及工作原理,然后探讨了基于结构参数分析的数学模型,最后对模型进行仿真,得出了连铸机结晶器液位控制系统的数学模型及其仿真的结论。
1.连铸机结晶器液位控制系统简介连铸机结晶器液位控制系统是一种多参数控制系统,它是由连铸机结晶器、液位传感器、控制器、调节阀和电动蝶阀组成的(图1)。
图1铸机结晶器液位控制系统连铸机结晶器是一种机械设备,它将液体转化为固体,由于结晶过程的特点,液位变化会影响结晶质量,因此,需要对结晶器的液位进行控制。
液位传感器检测结晶器液位信号,控制器根据液位检测信号进行控制,调节阀和电动蝶阀调节结晶器的液位,从而实现对液位的控制。
2.数学模型为了研究连铸机结晶器液位控制系统,首先分析控制系统结构,建立系统数学模型,根据结构参数推导出如下数学模型:ttttt Vm = Kp*(|S|-S0)tttt(1)其中Kp为控制器参数,S0为液位参考值,|S|为液位测量值,Vm为控制器输出值。
3.仿真针对连铸机结晶器液位控制系统,结合数学模型,使用Matlab/Simulink环境建立了仿真模型,根据实际情况,设置参数如下:Kp=0.5,S0=2,液位变化范围为0~4。
图2铸机结晶器液位控制系统仿真模型根据仿真模型,控制器输出值Vm与液位|S|的变化曲线如图3所示:图3位及控制器输出值的变化曲线从上图可以看到,随着液位|S|的变化,控制器输出值Vm也随之变化,并且同步变化,Vm和|S|的变化幅度接近,这表明,控制器对液位的控制是有效的。
4.结论本文针对连铸机结晶器液位控制系统,根据结构参数推导出了数学模型,并且基于 Matlab/Simulink环境建立了仿真模型,仿真结果显示,控制器输出值Vm能有效地控制液位|S|,表明数学模型具有较强的可靠性和实际应用价值。
连铸圆坯结晶器

连铸机结晶器总成1、结晶器总成组合式结晶器由结晶器本体、支撑框架以及足锟等部件组成。
结晶器本体由4块铜板及支撑板组合而成,用螺栓连接为一体;支撑框架带有定位、固定装置和冷却水通道;足锟包括支架、锟子、轴承、水管和喷嘴等。
组合式结晶器可以配置液位检测装置、外置式电磁搅拌装置。
2、结晶器结构特点A、结晶器本体两块弧面铜板和两块侧面铜板组合成结晶器内腔,铜板上加工有若干冷却水槽(即水缝),用螺钉将铜板与支承板(也称为背板)连接。
支承板上设有冷却水通道,冷却水从振动台上的供水孔进入支撑框架再进入支承板,再通过支撑框架流回到振动台上的回水孔。
设计时,需要根据冷却水压强核算螺钉连接的受力及强度,并调整连接螺钉数量,直至满足要求。
一般情况下,两排螺钉之间布置5~6条水缝。
结晶器内腔角部的倒角一般采用早弧面和侧面铜板的结合部位垫有带45°斜面的铜质垫板形成;也有直接在侧面铜板上加工出倒斜角斜面的。
铜板厚度一般为45~50mm,主要取决于水缝深度和再加工要求。
可采用的材质有Cu—Ag和Cu—Cr—Zr。
如果连铸机拉速不高,相应铜板热面温度不超过250℃,可以采用Cu—Ag。
随着连铸技术发展和操作水平提高,连铸机拉速也相应提高,结晶器铜板有必要采用Cu—Cr—Zr合金,可以满足热面温度为350℃甚至更高的工况。
目前,国内方坯结晶器铜板次用Cu—Ag和Cu—Cr—Zr的都有,采用Cu—Cr—Zr的日趋增多。
为了提高结晶器使用寿命,铜板都会经过表面处理,即镀层。
典型的镀层材料有Cr、Ni、Ni—Fe、Ni—Co、Co—Ni。
Cr的硬度高,督促呢个化学稳定性好,但Cr与Cu的线膨胀系数差距较大,镀层结合力差,镀层易剥落。
Ni与Cu的结合力好,但其镀层硬度相对较低,高温耐磨性差。
现已很少采用单独镀Cr或Ni得铜板。
Ni—Fe、Ni—Co、Co—Ni都有硬度高、耐磨性好的特点,其中Ni—Fe的化学稳定性较差,其镀层韧性随着硬度增加会降低;Ni—Co的抗热交变性稍差;Co—Ni的材料成本较高。
连铸原理与工艺
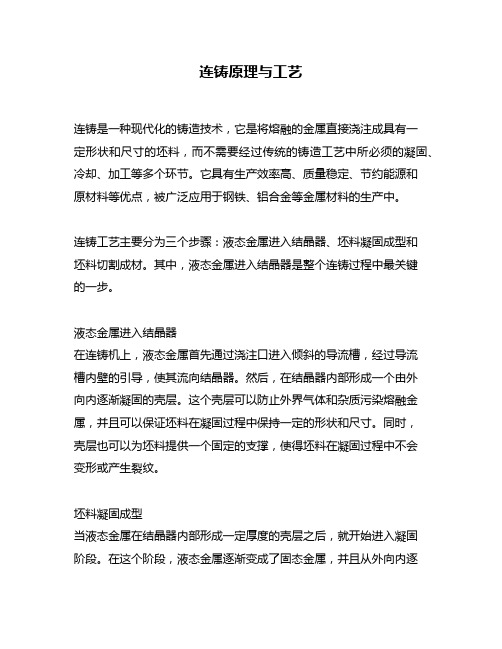
连铸原理与工艺连铸是一种现代化的铸造技术,它是将熔融的金属直接浇注成具有一定形状和尺寸的坯料,而不需要经过传统的铸造工艺中所必须的凝固、冷却、加工等多个环节。
它具有生产效率高、质量稳定、节约能源和原材料等优点,被广泛应用于钢铁、铝合金等金属材料的生产中。
连铸工艺主要分为三个步骤:液态金属进入结晶器、坯料凝固成型和坯料切割成材。
其中,液态金属进入结晶器是整个连铸过程中最关键的一步。
液态金属进入结晶器在连铸机上,液态金属首先通过浇注口进入倾斜的导流槽,经过导流槽内壁的引导,使其流向结晶器。
然后,在结晶器内部形成一个由外向内逐渐凝固的壳层。
这个壳层可以防止外界气体和杂质污染熔融金属,并且可以保证坯料在凝固过程中保持一定的形状和尺寸。
同时,壳层也可以为坯料提供一个固定的支撑,使得坯料在凝固过程中不会变形或产生裂纹。
坯料凝固成型当液态金属在结晶器内部形成一定厚度的壳层之后,就开始进入凝固阶段。
在这个阶段,液态金属逐渐变成了固态金属,并且从外向内逐渐缩小。
同时,由于液态金属的收缩率和晶粒长大率不同,所以在凝固过程中会形成一定数量的热裂纹和气孔。
为了解决这个问题,连铸工艺中采用了多种措施来控制坯料的凝固过程。
例如,在结晶器内部设置冷却水管道来降低壳层温度、使用高效保护气体来防止氧化等。
此外,在连铸工艺中还可以通过调整浇注速度、结晶器倾角、结晶器长度等参数来控制坯料的凝固速度和形状。
坯料切割成材当坯料完全凝固之后,它会被自动切割成一定长度的材料。
在连铸工艺中,切割方式主要分为两种:火焰切割和机械切割。
火焰切割是利用氧炔火焰将坯料加热到一定温度后进行切割,适用于较大尺寸的坯料。
机械切割则是使用钢丝、钢锯等工具将坯料进行切割,适用于较小尺寸的坯料。
总之,连铸工艺是一种高效、节能、环保的现代化铸造技术。
它通过控制液态金属的流动和凝固过程,使得金属材料可以以一种更加稳定和高效的方式生产出来。
同时,在连铸工艺中还可以通过调整参数、优化设备等手段来不断提高产品质量和生产效率,为现代制造业的发展做出了重要贡献。
常规板坯连铸机结晶器技术

常规板坯连铸机结晶器技术【保护视力色】【打印】【进入论坛】【评论】【字号大中小】2006-12-0711-07杨拉道刘洪王永洪刘赵卫邢彩萍田松林 (西安重型机械研究所)结晶器是连铸机中的铸坯成型设备, 是连铸机的核心设备之一。
其作用是将连续不断地注入其内腔的钢液通过水冷铜壁强制冷却,导出钢液的热量,使之逐渐凝固成为具有所要求的断面形状和一定坯壳厚度的铸坯,并使这种芯部仍为液相的铸坯连续不断地从结晶器下口拉出.为其在以后的二冷区域内完全凝固创造条件。
在钢水注入结晶器逐渐形成一定厚度坯壳的凝固过程中.结晶器一直承受着钢水静压力、摩檫力、钢水热量的传递等诸多因素引起的的影响.使结晶器同时处于机械应力和热应力的综合作用之下.工作条件极为恶劣.在此恶劣条件下结晶器长时间地工作.其使用状况直接关系到连铸机的性能.并与铸坯的质量与产量密切相关。
因此.除了规范生产操作、选择合适的保护渣和避免机械损伤外.合理的设计是保证铸坯质量、减小溢漏率、提高其使用寿命的基础和关键。
板坯连铸机一般采用四壁组合式(亦称板式)结晶器.也有一个结晶器浇多流铸坯的插装式结构。
结晶器主要参数的确定1 结晶器长度H结晶器长度主要根据结晶器出口的坯壳最小厚度确定。
若坯壳过薄.铸坯就会出现鼓肚变形.对于板坯连铸机.要求坯壳厚度大于10~15mm。
结晶器长度也可按下式进行核算:H=(δ/K)2Vc+S1+S2 (mm)式中δ——结晶器出口处坯壳的最小厚度.mmK——凝固系数.一般取K=18~22 mm/min0.5Vc——拉速.mm/minS1——结晶器铜板顶面至液面的距离.多取S1=100 mmS2——安全余量.S=50~100 mm对常规板坯连铸机可参考下述经验:当浇铸速度≤2.0m/min时.结晶器长度可采用900~950mm。
当浇铸速度2.0~3.0m/min时.结晶器长度可采用950~1100mm。
当浇铸速度≥3.0m/min时.结晶器长度可采用1100~1200mm。
常规板坯连铸机结晶器技术

常规板坯连铸机结晶器技术结晶器是连铸机中的铸坯成型设备, 是连铸机的核心设备之一。
其作用是将连续不断地注入其内腔的钢液通过水冷铜壁强制冷却,导出钢液的热量,使之逐渐凝固成为具有所要求的断面形状和一定坯壳厚度的铸坯,并使这种芯部仍为液相的铸坯连续不断地从结晶器下口拉出,为其在以后的二冷区域内完全凝固创造条件。
在钢水注入结晶器逐渐形成一定厚度坯壳的凝固过程中,结晶器一直承受着钢水静压力、摩檫力、钢水热量的传递等诸多因素引起的的影响,使结晶器同时处于机械应力和热应力的综合作用之下,工作条件极为恶劣,在此恶劣条件下结晶器长时间地工作,其使用状况直接关系到连铸机的性能,并与铸坯的质量与产量密切相关。
因此,除了规范生产操作、选择合适的保护渣和避免机械损伤外,合理的设计是保证铸坯质量、减小溢漏率、提高其使用寿命的基础和关键。
板坯连铸机一般采用四壁组合式(亦称板式)结晶器,也有一个结晶器浇多流铸坯的插装式结构。
ﻫ结晶器主要参数的确定ﻫ1 结晶器长度Hﻫ结晶器长度主要根据结晶器出口的坯壳最小厚度确定。
若坯壳过薄,铸坯就会出现鼓肚变形,对于板坯连铸机,要求坯壳厚度大于10~15mm。
结晶器长度也可按下式进行核算:ﻫﻫH=(δ/K)2Vc+S1+S2 (mm)ﻫﻫ式中δ——结晶器出口处坯壳的最小厚度,mmﻫK——凝固系数,一般取K=18~22 mm/min0.5ﻫ Vc——拉速,mm/minS1——结晶器铜板顶面至液面的距离,多取S1=100 mmﻫﻫS2——安全余量,S=50~100 mmﻫﻫ对常规板坯连铸机可参考下述经验:ﻫﻫ当浇铸速度≤2.0m/min时,结晶器长度可采用900~950mm。
ﻫﻫ当浇铸速度2.0~3.0m/min 时,结晶器长度可采用950~1100mm。
当浇铸速度≥3.0m/min时,结晶器长度可采用1100~1200mm。
ﻫﻫ 2 结晶器铜板厚度hﻫﻫ铜板厚度的确定是依据热量传热原理和高温下的使用性能,具体说,与铜板材质、镀层、机械性能、拉速、冷却水量的大小和分布等有关。
连续铸造原理和连铸设备简介
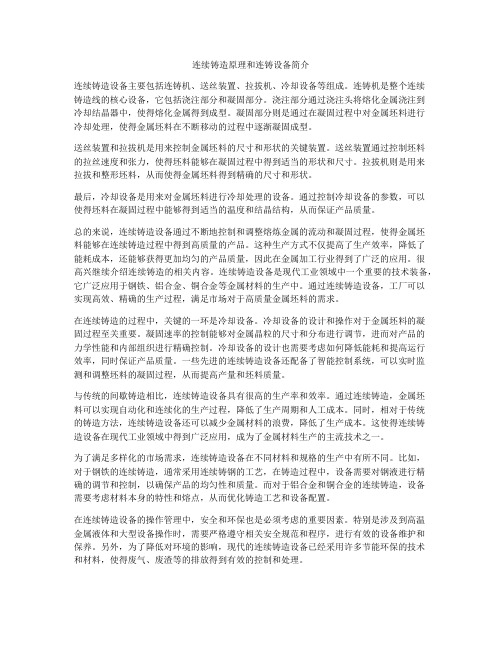
连续铸造原理和连铸设备简介连续铸造设备主要包括连铸机、送丝装置、拉拔机、冷却设备等组成。
连铸机是整个连续铸造线的核心设备,它包括浇注部分和凝固部分。
浇注部分通过浇注头将熔化金属浇注到冷却结晶器中,使得熔化金属得到成型。
凝固部分则是通过在凝固过程中对金属坯料进行冷却处理,使得金属坯料在不断移动的过程中逐渐凝固成型。
送丝装置和拉拔机是用来控制金属坯料的尺寸和形状的关键装置。
送丝装置通过控制坯料的拉丝速度和张力,使得坯料能够在凝固过程中得到适当的形状和尺寸。
拉拔机则是用来拉拔和整形坯料,从而使得金属坯料得到精确的尺寸和形状。
最后,冷却设备是用来对金属坯料进行冷却处理的设备。
通过控制冷却设备的参数,可以使得坯料在凝固过程中能够得到适当的温度和结晶结构,从而保证产品质量。
总的来说,连续铸造设备通过不断地控制和调整熔炼金属的流动和凝固过程,使得金属坯料能够在连续铸造过程中得到高质量的产品。
这种生产方式不仅提高了生产效率,降低了能耗成本,还能够获得更加均匀的产品质量,因此在金属加工行业得到了广泛的应用。
很高兴继续介绍连续铸造的相关内容。
连续铸造设备是现代工业领域中一个重要的技术装备,它广泛应用于钢铁、铝合金、铜合金等金属材料的生产中。
通过连续铸造设备,工厂可以实现高效、精确的生产过程,满足市场对于高质量金属坯料的需求。
在连续铸造的过程中,关键的一环是冷却设备。
冷却设备的设计和操作对于金属坯料的凝固过程至关重要。
凝固速率的控制能够对金属晶粒的尺寸和分布进行调节,进而对产品的力学性能和内部组织进行精确控制。
冷却设备的设计也需要考虑如何降低能耗和提高运行效率,同时保证产品质量。
一些先进的连续铸造设备还配备了智能控制系统,可以实时监测和调整坯料的凝固过程,从而提高产量和坯料质量。
与传统的间歇铸造相比,连续铸造设备具有很高的生产率和效率。
通过连续铸造,金属坯料可以实现自动化和连续化的生产过程,降低了生产周期和人工成本。
连铸结晶器
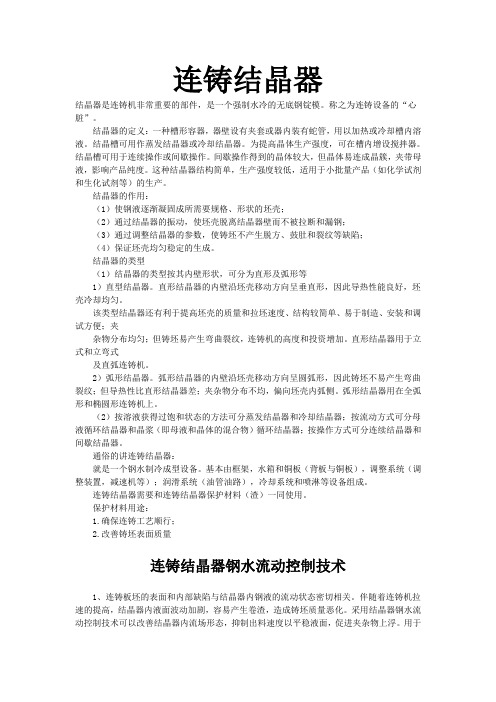
连铸结晶器结晶器是连铸机非常重要的部件,是一个强制水冷的无底钢锭模。
称之为连铸设备的“心脏”。
结晶器的定义:一种槽形容器,器壁设有夹套或器内装有蛇管,用以加热或冷却槽内溶液。
结晶槽可用作蒸发结晶器或冷却结晶器。
为提高晶体生产强度,可在槽内增设搅拌器。
结晶槽可用于连续操作或间歇操作。
间歇操作得到的晶体较大,但晶体易连成晶簇,夹带母液,影响产品纯度。
这种结晶器结构简单,生产强度较低,适用于小批量产品(如化学试剂和生化试剂等)的生产。
结晶器的作用:(1)使钢液逐渐凝固成所需要规格、形状的坯壳;(2)通过结晶器的振动,使坯壳脱离结晶器壁而不被拉断和漏钢;(3)通过调整结晶器的参数,使铸坯不产生脱方、鼓肚和裂纹等缺陷;(4)保证坯壳均匀稳定的生成。
结晶器的类型(1)结晶器的类型按其内壁形状,可分为直形及弧形等1)直型结晶器。
直形结晶器的内壁沿坯壳移动方向呈垂直形,因此导热性能良好,坯壳冷却均匀。
该类型结晶器还有利于提高坯壳的质量和拉坯速度、结构较简单、易于制造、安装和调试方便;夹杂物分布均匀;但铸坯易产生弯曲裂纹,连铸机的高度和投资增加。
直形结晶器用于立式和立弯式及直弧连铸机。
2)弧形结晶器。
弧形结晶器的内壁沿坯壳移动方向呈圆弧形,因此铸坯不易产生弯曲裂纹;但导热性比直形结晶器差;夹杂物分布不均,偏向坯壳内弧侧。
弧形结晶器用在全弧形和椭圆形连铸机上。
(2)按溶液获得过饱和状态的方法可分蒸发结晶器和冷却结晶器;按流动方式可分母液循环结晶器和晶浆(即母液和晶体的混合物)循环结晶器;按操作方式可分连续结晶器和间歇结晶器。
通俗的讲连铸结晶器:就是一个钢水制冷成型设备。
基本由框架,水箱和铜板(背板与铜板),调整系统(调整装置,减速机等);润滑系统(油管油路),冷却系统和喷淋等设备组成。
连铸结晶器需要和连铸结晶器保护材料(渣)一同使用。
保护材料用途:1.确保连铸工艺顺行;2.改善铸坯表面质量连铸结晶器钢水流动控制技术1、连铸板坯的表面和内部缺陷与结晶器内钢液的流动状态密切相关。
上引连铸法

上引连铸法上引连铸是一种连续铸造的方法,其原理是利用金属熔液冷却结晶的机理,从熔融的金属或合金熔液中缓慢连续地抽出具有一定形状的固态金属线材、板材等。
该方法的主要特点是可直接从熔融的金属或合金熔液中制取连续的线材或板材,无需经过铸造、挤压、拉拔、轧制等加工过程,缩短了加工周期,降低了加工过程的污染及损耗;连续生产能力大,单炉生产能力可达500kg,甚至可生产连续的线材、板材;可根据需要生产不同外径的线材和板材。
目前该方法大量应用于无氧铜线、钢材的生产。
2 结构组成上引连铸机主要由熔化系统、熔液液面跟踪系统、熔液冷却结晶系统、牵引系统、收线系统组成[1]。
熔化系统:对金属块进行加热熔化,并对熔液提供保温、保护等。
主要由中频感应电源、熔化坩埚及保温炉组成。
熔液液面跟踪系统:对熔融的金属液面进行跟踪测量,并通过升降机构使熔液冷却结晶系统中的结晶器能够与金属液面因不断地被抽取而发生的高度变化保持同步。
主要由碳化硅浮子、信号处理系统、升降机构组成。
熔液冷却结晶系统:对进入到结晶器内的金属熔液进行冷却凝固成形,从而获得固定形状的线材或板材。
主要由冷却水进出管道、结晶室、石墨定形管、耐火材料保护套、冷却水系统等组成。
牵引系统:对在结晶器内已形成的短小的固态金属线材或板材进行受控牵引,以获得连续的线材或板材。
收线系统:对牵引出的线材或板材进行弯圈收线,方便储存。
3 工作原理是上引连铸结晶器的结构示意图。
结晶器的下端装有耐火材料保护套、石墨定型管等,从结晶器的顶部预先插入一根外径与石墨定型管内径基本一致的金属线材做为引子(铸杆),线材通过石墨定型管并在结晶器的底端露出一小截。
通入流动的冷却水,将结晶器浸入熔液中,熔液液面不能超过耐火材料保护套的上端面。
将结晶器总成固定在牵引系统的导引轨道上。
其工作示意图见图2。
在图2中,当结晶器浸入高温金属熔液中时,原先已预插在结晶器内的线材的外露部分及结晶器h高度以内的部分会因受热而被熔化,而在结晶器内h高度以上的金属线材因受不断流动的冷却水作用而保持固态形状,因此在h高度的区域内形成了一个原始的固-液交界面,这个固-液交界面的实际位置与熔液温度以及受冷却室内流动冷却水的冷却强度有关。
连铸连轧知识点

连铸连轧知识点连铸和连轧是金属工业中常见的两个工艺过程。
连铸是指将液态金属连续铸造成坯料的过程,而连轧是指将坯料经过一系列压制和变形操作,连续地轧制成所需尺寸的金属板、带材或线材的过程。
本文将介绍连铸和连轧的基本概念、工艺流程和主要应用。
一、连铸连铸是一种高效的金属铸造技术,具有生产速度快、坯料质量好等优点。
连铸主要应用于钢铁、铜、铝等金属的生产中。
1. 连铸的基本原理连铸的基本原理是将熔融的金属通过连续浇注的方式,直接铸造成连续的坯料。
具体原理如下:首先,将金属熔融至液态,并通过加热设备保持在一定温度范围内;然后,通过连续浇注系统,将熔融金属均匀地注入到连铸结晶器中;在连铸结晶器中,通过冷却剂的作用,使金属迅速凝固,并形成坯料;最后,通过一系列传动装置,将连续产生的坯料送往下游的轧制设备或其他后续处理过程中。
2. 连铸的工艺流程连铸的工艺流程一般包括以下几个关键步骤:(1)冶炼:将矿石等原料经过熔炼处理,得到液态的金属合金;(2)调温:通过加热设备将金属保持在一定的液态温度;(3)连续浇注:通过连续浇注系统,将熔融金属注入到连铸结晶器中;(4)结晶与凝固:在连铸结晶器中,通过冷却剂的作用,使金属迅速凝固,并形成坯料;(5)切割和输送:将连续产生的坯料切割成合适的长度,并送往下游的加工设备。
3. 连铸的应用连铸广泛应用于钢铁、铜、铝等金属的生产中。
在钢铁工业中,连铸可以直接将炼钢铁水铸造成连续坯料,用于后续轧制成钢板和钢材。
在有色金属工业中,连铸可以将液态金属铸造成连续的板材、带材和线材,用于制造电线电缆、汽车零部件等产品。
二、连轧连轧是一种将金属坯料经过多道次的压制和变形操作,连续地轧制成所需尺寸的金属板、带材或线材的工艺过程。
连轧具有高效快速、坯料成形完整等特点,广泛应用于钢铁、有色金属等工业领域。
1. 连轧的基本原理连轧的基本原理是通过一系列的压制和变形操作,使金属坯料逐渐减小厚度、增大长度,并达到所需的尺寸要求。
常规板坯连铸机结晶器技术(知识学习)
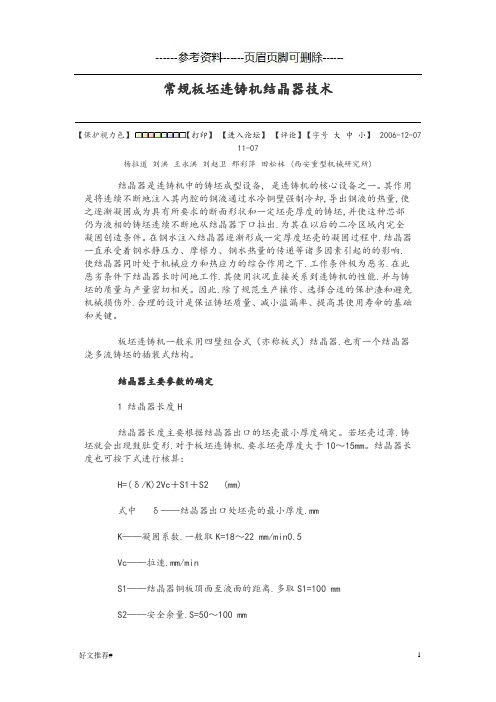
常规板坯连铸机结晶器技术【保护视力色】【打印】【进入论坛】【评论】【字号大中小】2006-12-0711-07杨拉道刘洪王永洪刘赵卫邢彩萍田松林 (西安重型机械研究所)结晶器是连铸机中的铸坯成型设备, 是连铸机的核心设备之一。
其作用是将连续不断地注入其内腔的钢液通过水冷铜壁强制冷却,导出钢液的热量,使之逐渐凝固成为具有所要求的断面形状和一定坯壳厚度的铸坯,并使这种芯部仍为液相的铸坯连续不断地从结晶器下口拉出.为其在以后的二冷区域内完全凝固创造条件。
在钢水注入结晶器逐渐形成一定厚度坯壳的凝固过程中.结晶器一直承受着钢水静压力、摩檫力、钢水热量的传递等诸多因素引起的的影响.使结晶器同时处于机械应力和热应力的综合作用之下.工作条件极为恶劣.在此恶劣条件下结晶器长时间地工作.其使用状况直接关系到连铸机的性能.并与铸坯的质量与产量密切相关。
因此.除了规范生产操作、选择合适的保护渣和避免机械损伤外.合理的设计是保证铸坯质量、减小溢漏率、提高其使用寿命的基础和关键。
板坯连铸机一般采用四壁组合式(亦称板式)结晶器.也有一个结晶器浇多流铸坯的插装式结构。
结晶器主要参数的确定1 结晶器长度H结晶器长度主要根据结晶器出口的坯壳最小厚度确定。
若坯壳过薄.铸坯就会出现鼓肚变形.对于板坯连铸机.要求坯壳厚度大于10~15mm。
结晶器长度也可按下式进行核算:H=(δ/K)2Vc+S1+S2 (mm)式中δ——结晶器出口处坯壳的最小厚度.mmK——凝固系数.一般取K=18~22 mm/min0.5Vc——拉速.mm/minS1——结晶器铜板顶面至液面的距离.多取S1=100 mmS2——安全余量.S=50~100 mm对常规板坯连铸机可参考下述经验:当浇铸速度≤2.0m/min时.结晶器长度可采用900~950mm。
当浇铸速度2.0~3.0m/min时.结晶器长度可采用950~1100mm。
当浇铸速度≥3.0m/min时.结晶器长度可采用1100~1200mm。
连铸工艺设备连铸设备及主要工艺参数
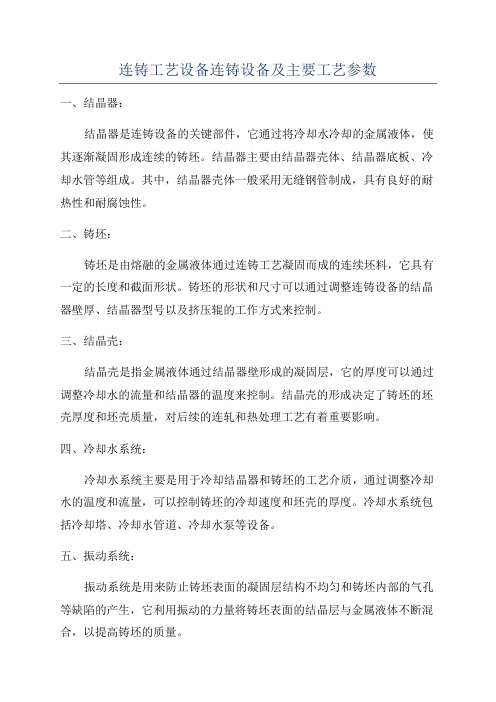
连铸工艺设备连铸设备及主要工艺参数一、结晶器:结晶器是连铸设备的关键部件,它通过将冷却水冷却的金属液体,使其逐渐凝固形成连续的铸坯。
结晶器主要由结晶器壳体、结晶器底板、冷却水管等组成。
其中,结晶器壳体一般采用无缝钢管制成,具有良好的耐热性和耐腐蚀性。
二、铸坯:铸坯是由熔融的金属液体通过连铸工艺凝固而成的连续坯料,它具有一定的长度和截面形状。
铸坯的形状和尺寸可以通过调整连铸设备的结晶器壁厚、结晶器型号以及挤压辊的工作方式来控制。
三、结晶壳:结晶壳是指金属液体通过结晶器壁形成的凝固层,它的厚度可以通过调整冷却水的流量和结晶器的温度来控制。
结晶壳的形成决定了铸坯的坯壳厚度和坯壳质量,对后续的连轧和热处理工艺有着重要影响。
四、冷却水系统:冷却水系统主要是用于冷却结晶器和铸坯的工艺介质,通过调整冷却水的温度和流量,可以控制铸坯的冷却速度和坯壳的厚度。
冷却水系统包括冷却塔、冷却水管道、冷却水泵等设备。
五、振动系统:振动系统是用来防止铸坯表面的凝固层结构不均匀和铸坯内部的气孔等缺陷的产生,它利用振动的力量将铸坯表面的结晶层与金属液体不断混合,以提高铸坯的质量。
六、铸坯切割系统:铸坯切割系统是将连铸的整坯切割成所需长度的小块铸件,以便后续的加工和使用。
铸坯切割系统包括切割机、切割刀具等设备。
七、传动系统:传动系统主要是将连铸工艺设备的动力传递给各个部件,以确保连铸过程的连续和稳定。
传动系统包括电机、减速机、联轴器等设备。
八、电气控制系统:电气控制系统是连铸设备各个部件之间的信息交流和工艺参数调整的重要手段,它通过传感器、PLC控制器等设备实现对连铸过程的自动控制。
与连铸设备相关的主要工艺参数包括:1.结晶器温度:结晶器温度决定了铸坯的凝固速度和结晶壳的厚度,通常在1000℃-1500℃之间。
2. 冷却水流量:冷却水的流量决定了铸坯的冷却速度和坯壳的厚度,通常在20-100L/min之间。
3. 振动频率和振幅:振动频率和振幅的调节可以改善铸坯的结晶层结构,通常在50-150Hz和0.2-0.5mm之间。
连续铸造简介

连续铸造是一种先进的铸造方法,其原理是将熔融的金属,不断浇入一种叫做结晶器的特殊金属型中,凝固(结壳)了的铸件,连续不断地从结晶器的另一端拉出,它可获得任意长或特定的长度的铸件。
连续铸造的优点连续铸造在国内外已经被广泛采用,如连续铸锭(钢或有色金属锭),连续铸管等。
连续铸造和普通铸造比较有下述优点:[1]1、由于金属被迅速冷却,结晶致密,组织均匀,机械性能较好;2、连续铸造时,铸件上没有浇注系统的冒口,故连续铸锭在轧制时不用切头去尾,节约了金属,提高了收得率;3、简化了工序,免除造型及其它工序,因而减轻了劳动强度;所需生产面积也大为减少;4、连续铸造生产易于实现机械化和自动化,铸锭时还能实现连铸连轧,大大提高了生产效率。
利用贯通的结晶器在一端连续地浇入液态金属,从另一端连续地拔出成型材料的铸造方法。
结晶器一般用导热性较好,具有一定强度的材料,如铜、铸铁、石墨等制成,壁中空,空隙中间通冷却水以增强其冷却作用。
铸出的成型材料有方形、长方形、圆形、平板型、管形或各种异形截面。
连续铸造方法的设想是英国人H.贝塞麦于1857年提出的,在当时的技术条件下未能实际应用,直到20世纪30年代,这种方法才成功地用于铜、铝合金的铸造。
到50年代,连续铸造在各国的钢厂正式用于铸钢。
根据铸造出的成型材料不同,连续铸造有铸锭、铸管、铸板等。
图1为连续铸钢锭示意图,有水平式、垂直式和圆弧式 3种。
结晶器在钢水包下部,钢水通过结晶器被连续地拉出成锭,表面固化的锭材在结晶器下面受到喷射水的二次冷却而完全凝固。
当锭料被拉至一定长度时,由切割机切断成段料,供进一步加工使用。
为了缩小锭材中的柱状晶区域,以便减少锭材轴心区的成分偏析和非金属夹杂,可在结晶器下部装一电磁装置。
70年代出现一种电磁结晶器,即利用成形的电磁场代替结晶器围住液态金属,铸锭在结晶器下部被水强烈冷却。
另外还有一种离心连续铸造方法,工作时结晶图2为铁管连续铸造。
铸造机上安有内、外结晶器。
- 1、下载文档前请自行甄别文档内容的完整性,平台不提供额外的编辑、内容补充、找答案等附加服务。
- 2、"仅部分预览"的文档,不可在线预览部分如存在完整性等问题,可反馈申请退款(可完整预览的文档不适用该条件!)。
- 3、如文档侵犯您的权益,请联系客服反馈,我们会尽快为您处理(人工客服工作时间:9:00-18:30)。
连铸结晶器工作原理
连铸结晶器是连铸生产线中的重要组成部分,其工作原理涉及多种物理和化学过程。
下面将对连铸结晶器的工作原理进行详细解释。
**一、连铸结晶器的作用**
连铸结晶器主要用于在连铸过程中将液态金属逐渐冷却凝固,形成连续的坯料。
通过
结晶器对液态金属进行凝固成形,可以满足不同工艺要求和坯料规格的生产需求,同时也
可以提高产品的质量和性能。
**二、连铸结晶器的工作原理**
1. **结晶器内的冷却系统**
连铸结晶器内部配备了冷却系统,主要包括冷却水管和冷却水。
在连铸过程中,通过
冷却水对结晶器进行冷却,使得液态金属能够迅速被冷却并凝固。
2. **液态金属的注入和分布**
在结晶器上部,液态金属经过预炼炉或其他方式得到均匀温度后,通过喷嘴均匀地注
入到结晶器内,形成一定宽度和深度的液态金属层。
通过振动和控制系统,实现液态金属
在结晶器内的均匀分布和控制厚度。
3. **结晶器外壁和内壁的温度控制**
结晶器外壁设有绝热层以保持结晶器内温度稳定,内壁则通过冷却水保持一定的温度,以控制凝固过程中的结晶器内部温度分布。
4. **凝固过程**
液态金属在结晶器内受到冷却水的冷却,由于受热传导和传热等因素,逐渐凝固成形,形成坯料。
结晶器内部的振动系统也可以对液态金属进行微小的振动,以促进坯料的凝固
和形成。
5. **坯料的后续处理**
连铸结晶器中形成的坯料随后通过后续的冷却、切割和处理工艺,最终成为可加工的
半成品或成品。
通过以上工作原理的分析可以看出,连铸结晶器不仅仅是一个简单的冷却设备,其内
部结构和工作原理涉及了液态金属的凝固过程、温度控制、振动控制等多方面的物理和化
学过程,是连铸生产中至关重要的环节。