流态化技术在世界熔融还原工艺中的应用
流态固化再生混合料、制备方法及其在坑槽回填中的应用
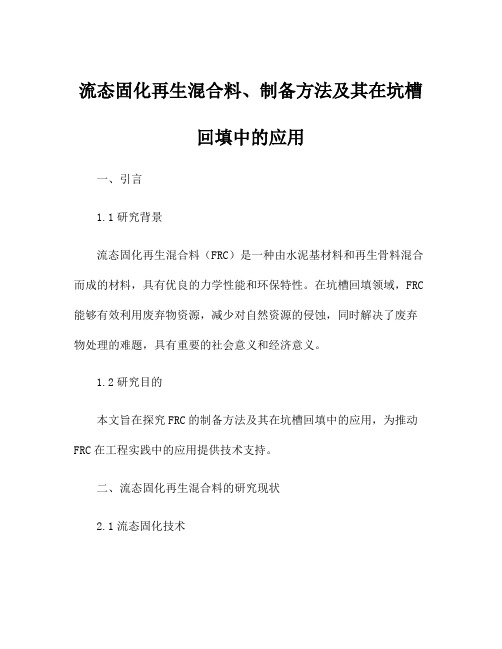
流态固化再生混合料、制备方法及其在坑槽回填中的应用一、引言1.1研究背景流态固化再生混合料(FRC)是一种由水泥基材料和再生骨料混合而成的材料,具有优良的力学性能和环保特性。
在坑槽回填领域,FRC 能够有效利用废弃物资源,减少对自然资源的侵蚀,同时解决了废弃物处理的难题,具有重要的社会意义和经济意义。
1.2研究目的本文旨在探究FRC的制备方法及其在坑槽回填中的应用,为推动FRC在工程实践中的应用提供技术支持。
二、流态固化再生混合料的研究现状2.1流态固化技术流态固化是一种通过控制颗粒材料在流态状态下进行混合和固化的技术,它具有良好的工艺适应性和高效的固化效果,是FRC制备的关键技术。
2.2再生骨料再生骨料是指通过废弃物资源进行再生加工得到的骨料,其来源广泛,可以是建筑废弃材料、废旧混凝土、废弃玻璃等,能够有效减少对原始资源的需求。
2.3 FRC的应用领域FRC在道路工程、地基工程、坑槽回填等领域具有广泛的应用前景,已经在一些工程实践中得到了应用。
三、流态固化再生混合料的制备方法3.1再生骨料处理通过筛分、清洗等方式将再生骨料进行预处理,去除其中的杂质和附着物,提高其质量和稳定性。
3.2流态固化剂的选择选择适宜的水泥基材料和固化剂,并进行配比设计,以保证FRC 具有良好的坚固性和耐久性。
3.3流态固化混合将经过处理的再生骨料和流态固化剂进行混合,并在适宜的条件下进行流态固化,形成FRC产品。
3.4 FRC的养护对制成的FRC产品进行合理的养护,以保证其力学性能和耐久性能。
四、流态固化再生混合料在坑槽回填中的应用4.1 FRC的优势FRC具有优良的力学性能和环保特性,能够有效利用再生资源,减少对原始资源的需求。
4.2坑槽回填的要求坑槽回填是指利用废弃物填埋填方体,其中填方体需要具有一定的强度和稳定性,以保证填埋的安全和效果。
4.3 FRC的应用实例将FRC用于坑槽回填,具有节省成本、减少对原材料需求、环保等显著优势,已经在一些工程实践中得到应用。
直接还原铁工艺技术的对比分析论述

直接还原铁工艺技术的对比分析论述张建国【期刊名称】《资源再生》【年(卷),期】2018(000)002【总页数】5页(P57-61)【作者】张建国【作者单位】北京瀚川鑫冶工程技术有限公司【正文语种】中文在低于矿石融化状态下,通过固态还原,把铁矿石炼制成铁的工艺称作直接还原法,用这种方法生产出的铁也叫作直接还原铁(DRI),由于这种铁保留了失去氧时形成的大量微小气孔,在显微镜下观察形似海绵,所以直接还原铁也称为海绵铁。
直接还原铁是精铁粉在炉内经低温还原形成的低碳多孔状物质,其化学成分稳定,杂质含量少,主要用作电炉炼钢的原料,也可作为转炉炼钢的冷却剂,如果经过二次还原还可供给粉末冶金用。
从上世纪80年代末以来,我国一直宣传推广使用直接还原技术,并对直接还原技术进行了广泛的开发研究,取得了众多成果,为直接还原技术发展奠定了基础。
但是,因铁矿、煤炭、气源等原燃料条件限制,中国直接还原发展的实际成效不大,与钢材、生铁等行业相比还有相当差距。
一、直接还原铁的应用优势直接还原铁生产是指在低于熔化温度之下将铁矿石还原成海绵铁的过程,与传统高炉炼铁方法相比取消了焦炉、烧结等工序,具有流程短、污染小、消耗少,不受炼焦煤短缺影响等优点。
同时海绵铁中硫、磷、硅等有害杂质含量低,有利于电炉冶炼优质纯净钢种。
近年来,由于钢铁产品向小型轻量化、功能高级化、复合化方向发展,因此钢材产品中的非金属材料和有色金属的使用比例在增加,在废钢的破碎分拣过程中,又不能完全有效的剔除非金属和有色金属材料,况且,即使是纯粹完全的黑色废钢料,由于来源不同,化学成分波动也是较大的。
致使加工后的成品入炉废钢的质量很难掌握控制,给电炉炼钢作业带来一定的困难。
如果用一定比例的直接还原铁(30~50%)作为稀释剂与废钢搭配使用,不仅可增加钢的均匀性,还可以改善和提高钢的物理性质,从而达到生产优质钢的目的。
因此,直接还原铁不仅仅是优质废钢的替代品,还是生产优质钢必不可少的高级原料(如天津无缝钢管公司的国外产品设计中就明确要求,必须配置50%的直接还原铁)。
碳吸附赤铁矿粉流态化预还原过程中物性、结构变化规律的研究
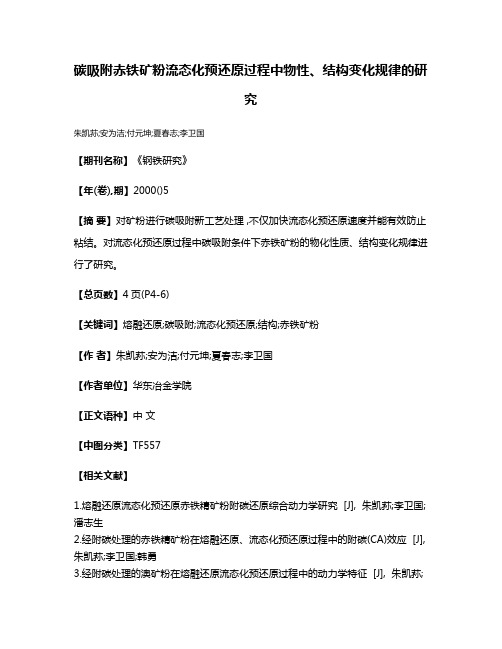
碳吸附赤铁矿粉流态化预还原过程中物性、结构变化规律的研
究
朱凯荪;安为洁;付元坤;夏春志;李卫国
【期刊名称】《钢铁研究》
【年(卷),期】2000()5
【摘要】对矿粉进行碳吸附新工艺处理 ,不仅加快流态化预还原速度并能有效防止粘结。
对流态化预还原过程中碳吸附条件下赤铁矿粉的物化性质、结构变化规律进行了研究。
【总页数】4页(P4-6)
【关键词】熔融还原;碳吸附;流态化预还原;结构;赤铁矿粉
【作者】朱凯荪;安为洁;付元坤;夏春志;李卫国
【作者单位】华东冶金学院
【正文语种】中文
【中图分类】TF557
【相关文献】
1.熔融还原流态化预还原赤铁精矿粉附碳还原综合动力学研究 [J], 朱凯荪;李卫国;潘志生
2.经附碳处理的赤铁精矿粉在熔融还原、流态化预还原过程中的附碳(CA)效应 [J], 朱凯荪;李卫国;韩勇
3.经附碳处理的澳矿粉在熔融还原流态化预还原过程中的动力学特征 [J], 朱凯荪;
李卫国;罗浩
4.熔融还原流态化预还原附碳铁精矿粉的热力学研究 [J], 朱凯荪;陆克从;李卫国
5.熔融还原流态化预还原附碳铁精矿粉的动力学研究 [J], 朱凯荪;陆克从;李卫国因版权原因,仅展示原文概要,查看原文内容请购买。
流态化还原炼铁技术

流态化还原炼铁技术流态化(fluidization)是一种由于流体向上流过固体颗粒堆积的床层而使得固体颗粒具有一般流体性质的物理现象,是现代多相相际接触的工程技术。
使用流态化技术的流化床反应器因具有相际接触面积大,温度、浓度均匀,传热传质条件好,运行效率高等优点而应用于现代工业生产。
高炉炼铁技术在矿产资源受限和环保压力增大等形势下,将面临着前所未有的挑战。
铁矿石对外依存度过高、铁矿石粒度越来越小和焦炭资源枯竭等状况,迫使人们加快步伐探索改进或替代高炉工艺的非高炉型炼铁工艺。
以气固流态化还原技术为代表的非高炉炼铁工艺逐步受到重视。
新工艺的建立和发展需要理论研究作为支撑。
目前国内对于流态化还原炼铁过程中的气固两相流规律的认识还不够深入,特别是对不同属性铁矿粉的流态化特性、不同操作条件下的流态化还原特性,以及反应器结构对流态化还原过程的影响等相关研究还不够充分,基于流态化还原技术的新工艺要成熟应用于大规模工业生产还有明显距离。
发展流态化技术须重视基础研究流态化技术可以把固体散料悬浮于运动的流体之中,使颗粒与颗粒之间脱离接触,从而消除颗粒间的内摩擦现象,使固体颗粒具有一般流体的特性,以期得到良好的物理化学条件。
流态化技术很早就被引入冶金行业,成为非高炉炼铁技术气基还原流程中的一类重要工艺。
流态化技术在直接还原炼铁过程中主要有铁矿粉磁化焙烧、粉铁矿预热和低度预还原、生产直接还原铁的冶金功能。
我国从上世纪50年代后期开始流态化炼铁技术的研究。
1973年~1982年,为了开发攀枝花资源,我国进行了3次流态化还原综合回收钒钛铁的试验研究。
中国科学院结合资源特点对贫铁矿、多金属共生矿的综合利用,开展了流态化还原过程和设备的研究;钢铁研究总院于2004年提出低温快速预还原炼铁方法(FROL TS),并随后对工艺流程进行了探索,取得一定效果。
除此之外,还有针对铁矿及铁氧化物微粉的低温还原特性的研究,探索了小粒径矿粉进行流态化还原的技术特点。
熔融还原工艺

熔融还原工艺熔融还原工艺是一种常用于金属冶炼和废物处理的技术。
它通过在高温下将金属或废物加热至熔点,然后添加还原剂,使有害物质被还原为无害物质,同时将目标金属分离出来。
这种工艺有助于资源的回收利用和环境的保护。
熔融还原工艺的基本原理是利用高温下物质的熔融性和还原性。
在高温下,金属或废物中的有害物质可以被还原为无害物质。
为了实现这个过程,通常需要添加还原剂。
还原剂是一种能够将有害物质还原为无害物质的物质,常用的还原剂有焦炭、燃料和还原气体等。
熔融还原工艺的应用非常广泛,主要包括金属冶炼和废物处理两个方面。
在金属冶炼中,熔融还原工艺可以用来分离出目标金属,并去除杂质。
例如,熔融还原工艺可以用于从废旧电子产品中提取有价金属,如金、银和铜等。
同时,这种工艺还可以用于冶炼废旧钢铁,将其还原为可再利用的原材料。
在废物处理方面,熔融还原工艺可以将废物中的有害物质转化为无害物质,并分离出有价值的物质。
例如,废电池中的有害重金属可以通过熔融还原工艺被还原为无害的物质,并可以回收利用。
另外,熔融还原工艺还可以用于处理含有有机物的废物,将有机物还原为无害的气体和灰渣。
熔融还原工艺的优点是可以高效地分离出目标金属,并处理废物中的有害物质。
与传统的冶炼和废物处理方法相比,熔融还原工艺具有以下优势:1. 高效性:熔融还原工艺可以在较短的时间内将金属分离出来,并将有害物质转化为无害物质,提高了资源的回收利用率和废物处理效率。
2. 环保性:熔融还原工艺能够有效地处理废物中的有害物质,减少对环境的污染。
3. 经济性:熔融还原工艺可以回收有价值的金属,并将废物转化为可再利用的原材料,节约了资源和能源。
然而,熔融还原工艺也存在一些挑战和限制。
首先,高温下的操作需要耗能,并且对设备的要求较高,增加了成本。
其次,熔融还原过程中产生的废气和废渣需要进行处理和处置,否则可能对环境造成污染。
此外,对于一些特殊的废物,熔融还原工艺可能无法完全将其转化为无害物质,仍然需要其他处理方法。
钢铁脱碳——氢基流态化粉矿还原(HYFOR)
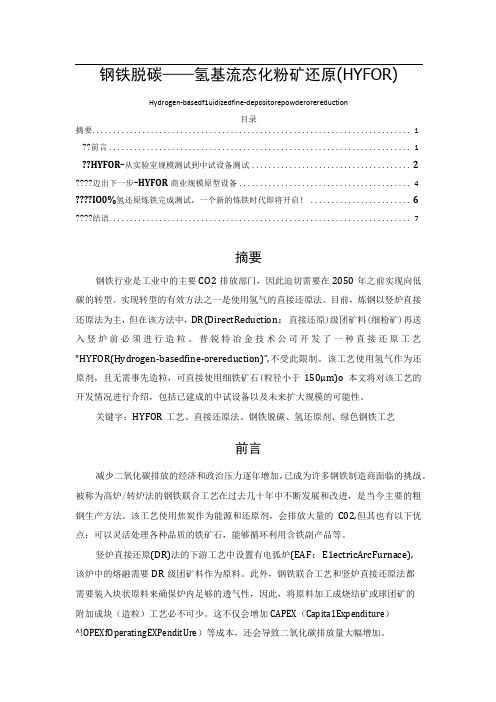
钢铁脱碳——氢基流态化粉矿还原(HYFOR)Hydrogen-basedf1uidizedfine-depositorepowderorereduction目录摘要 (1)前言 (1)HYFOR-从实验室规模测试到中试设备测试 (2)迈出下一步-HYFOR商业规模原型设备 (4)IO0%氢还原炼铁完成测试,一个新的炼铁时代即将开启! (6)结语 (7)摘要钢铁行业是工业中的主要CO2排放部门,因此迫切需要在2050年之前实现向低碳的转型。
实现转型的有效方法之一是使用氢气的直接还原法。
目前,炼钢以竖炉直接还原法为主,但在该方法中,DR(DirectReduction:直接还原)级团矿料(细粉矿)再送入竖炉前必须进行造粒。
普锐特冶金技术公司开发了一种直接还原工艺"HYFOR(Hydrogen-basedfine-orereduction)”,不受此限制。
该工艺使用氢气作为还原剂,且无需事先造粒,可直接使用细铁矿石(粒径小于150μm)o本文将对该工艺的开发情况进行介绍,包括已建成的中试设备以及未来扩大规模的可能性。
关键字:HYFOR工艺、直接还原法、钢铁脱碳、氢还原剂、绿色钢铁工艺前言减少二氧化碳排放的经济和政治压力逐年增加,已成为许多钢铁制造商面临的挑战。
被称为高炉/转炉法的钢铁联合工艺在过去几十年中不断发展和改进,是当今主要的粗钢生产方法。
该工艺使用焦炭作为能源和还原剂,会排放大量的C02,但其也有以下优点:可以灵活处理各种品质的铁矿石,能够循环利用含铁副产品等。
竖炉直接还原(DR)法的下游工艺中设置有电弧炉(EAF:E1ectricArcFurnace),该炉中的熔融需要DR级团矿料作为原料。
此外,钢铁联合工艺和竖炉直接还原法都需要装入块状原料来确保炉内足够的透气性,因此,将原料加工成烧结矿或球团矿的附加成块(造粒)工艺必不可少。
这不仅会增加CAPEX(Capita1Expenditure)^!OPEXfOperatingEXPenditUre)等成本,还会导致二氧化碳排放量大幅增加。
还原精炼条件下炉渣的泡沫化
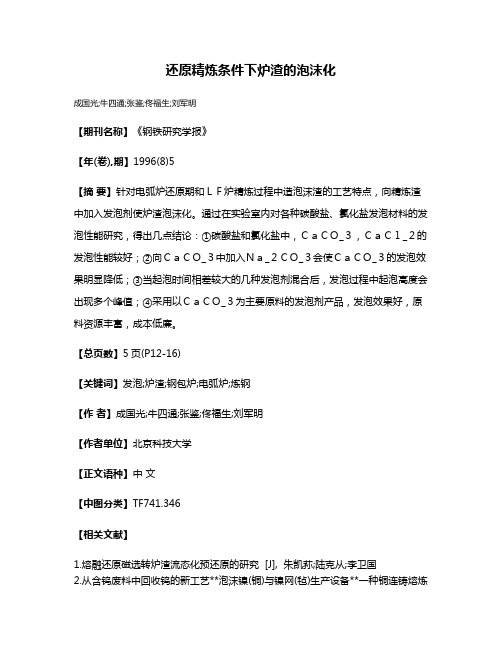
还原精炼条件下炉渣的泡沫化
成国光;牛四通;张鉴;佟福生;刘军明
【期刊名称】《钢铁研究学报》
【年(卷),期】1996(8)5
【摘要】针对电弧炉还原期和LF炉精炼过程中造泡沫渣的工艺特点,向精炼渣中加入发泡剂使炉渣泡沫化。
通过在实验室内对各种碳酸盐、氯化盐发泡材料的发泡性能研究,得出几点结论:①碳酸盐和氯化盐中,CaCO_3,CaCl_2的发泡性能较好;②向CaCO_3中加入Na_2CO_3会使CaCO_3的发泡效果明显降低;③当起泡时间相差较大的几种发泡剂混合后,发泡过程中起泡高度会出现多个峰值;④采用以CaCO_3为主要原料的发泡剂产品,发泡效果好,原料资源丰富,成本低廉。
【总页数】5页(P12-16)
【关键词】发泡;炉渣;钢包炉;电弧炉;炼钢
【作者】成国光;牛四通;张鉴;佟福生;刘军明
【作者单位】北京科技大学
【正文语种】中文
【中图分类】TF741.346
【相关文献】
1.熔融还原磁选转炉渣流态化预还原的研究 [J], 朱凯荪;陆克从;李卫国
2.从含钨废料中回收钨的新工艺**泡沫镍(铜)与镍网(毡)生产设备**一种铜连铸熔炼
炉的保温炉密封炉盖**紫杂铜一步电解生产阴极铜的方法**粗铜无氧化掺氮还原火法精炼工艺 [J],
3.高碱度转炉渣碳热还原时熔渣泡沫化控制及消除技术 [J], 彭绍强;刘铮
4.含钛高炉渣碳热还原时熔渣泡沫化原因分析 [J], 黄家旭;龙盘忠
5.电炉粉尘造泡沫渣过程中FeO的还原与炉渣发泡行为 [J], 王敏;陈伟庆
因版权原因,仅展示原文概要,查看原文内容请购买。
流态化工程原理

流态化工程原理流态化工程原理是指通过控制流体的运动状态和物理特性来实现特定的工艺目标或应用需求的一种技术。
它在化工、石油、能源、环保等领域中广泛应用,为工业生产提供了重要的技术支持和创新方向。
流态化工程原理的基本概念是将固体颗粒悬浮于气体或液体介质中,通过调节流体的速度和流态化剂的添加来改变固体颗粒的运动状态。
在流态化状态下,固体颗粒的运动呈现出流体的特性,具有类似于液体的流动性和类似于气体的均匀性。
这种特性使得流态化工程成为一种高效的物料搬运和反应控制技术。
流态化工程原理的核心是流体的运动和相互作用。
在流态化过程中,流体中的颗粒受到气体或液体的作用力,呈现出不同的运动状态,如床层流动、颗粒间的碰撞和混合等。
这些运动状态对于实现特定的工艺目标至关重要,如颗粒的分离、搬运和反应等。
流态化工程原理的应用范围非常广泛。
在化工领域,流态化工程可以用于固体颗粒的分离、干燥、反应和催化等过程。
例如,在石化工业中,流态化工程可以用于催化剂的制备和石油的加工。
在环保领域,流态化工程可以用于废气和废水的处理和净化。
在能源领域,流态化工程可以用于燃煤和生物质的燃烧,以及核能的利用等。
流态化工程原理的核心是控制流体的运动和相互作用。
通过调节流体的速度和流态化剂的添加,可以改变固体颗粒的运动状态,从而实现特定的工艺目标。
流态化工程既有理论研究,又有实际应用。
在理论研究方面,流态化工程涉及流体力学、热力学和物质传递等多个学科的知识。
在实际应用方面,流态化工程需要考虑工艺流程、设备设计和操作控制等多个方面的问题。
流态化工程原理的研究和应用对于推动工业生产的发展具有重要意义。
它可以提高物料搬运和反应过程的效率,减少能源和原材料的消耗,降低环境污染和废物排放。
同时,流态化工程也为新材料的研发和应用提供了技术支持和创新思路。
通过研究流态化工程原理,我们可以更好地理解和掌握流体的运动规律和相互作用机制,为工业生产的可持续发展做出贡献。
流态化技术在世界熔融还原工艺中的应用
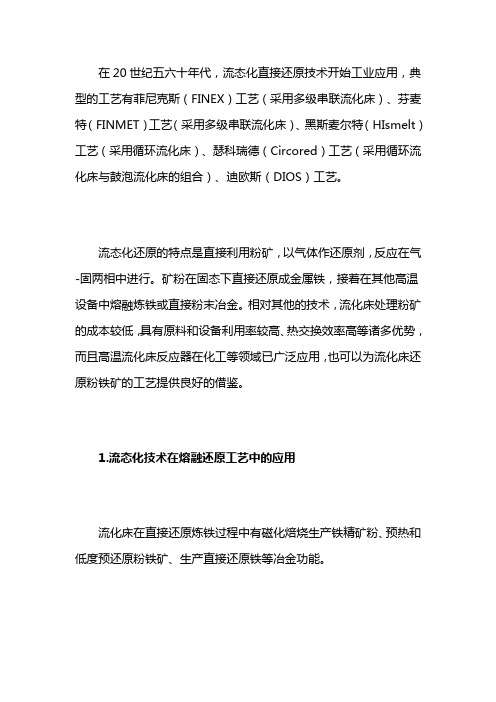
在20世纪五六十年代,流态化直接还原技术开始工业应用,典型的工艺有菲尼克斯(FINEX)工艺(采用多级串联流化床)、芬麦特(FINMET)工艺(采用多级串联流化床)、黑斯麦尔特(HIsmelt)工艺(采用循环流化床)、瑟科瑞德(Circored)工艺(采用循环流化床与鼓泡流化床的组合)、迪欧斯(DIOS)工艺。
流态化还原的特点是直接利用粉矿,以气体作还原剂,反应在气-固两相中进行。
矿粉在固态下直接还原成金属铁,接着在其他高温设备中熔融炼铁或直接粉末冶金。
相对其他的技术,流化床处理粉矿的成本较低,具有原料和设备利用率较高、热交换效率高等诸多优势,而且高温流化床反应器在化工等领域已广泛应用,也可以为流化床还原粉铁矿的工艺提供良好的借鉴。
1.流态化技术在熔融还原工艺中的应用流化床在直接还原炼铁过程中有磁化焙烧生产铁精矿粉、预热和低度预还原粉铁矿、生产直接还原铁等冶金功能。
1)磁化焙烧铁精矿粉磁化焙烧是将Fe2O3在还原气氛中焙烧得到磁化性的Fe3O4,经过磁选使Fe3O4与杂质分离,得到品位高的铁精矿。
1973年~1982年,为了开发攀枝花资源,我国进行了3次流态化还原综合回收钒钛铁的试验研究。
3次的试验结果表明,我国的流态化还原法在理论上是可靠的,工艺上是可行的,主体设备上是成功的,从而为向工业化过渡创造了条件。
2)预热和低度预还原粉铁矿流化床预热和低度预还原粉铁矿工艺中的典型代表是HIsmelt 工艺和DIOS工艺。
HIsmelt工艺正处于工业化开发阶段。
矿粉经过整粒筛分除去大颗粒矿粉后经皮带输送到矿石预热器中进行预热和初级预还原。
整粒筛分后的粒度小于6mm,预热后的矿粉温度可达700℃~800℃,预还原度为10%~11%,处理后的热矿粉装入热矿仓等待喷吹。
为了缓解铁浴炉的压力,可提高预热粉铁矿的还原度,但是粉铁矿只经一级循环流化床预热还原,其还原度一般不超过25%。
DIOS工艺的预还原采用快速流化床与沸腾流化床组合的复合型流化床系统。
流态固化再生混合料、制备方法及其在坑槽回填中的应用
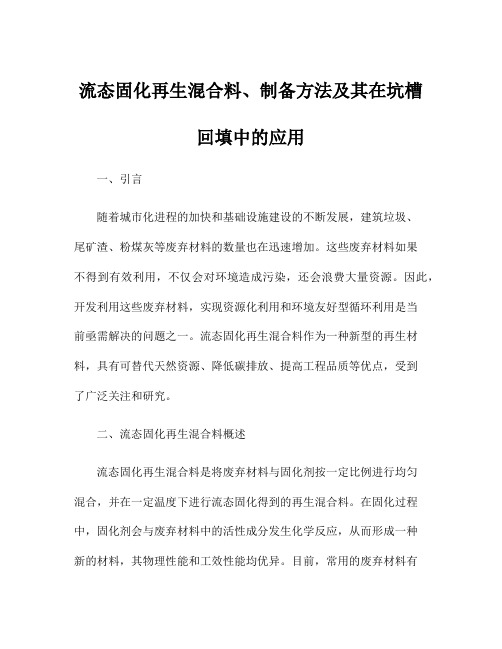
流态固化再生混合料、制备方法及其在坑槽回填中的应用一、引言随着城市化进程的加快和基础设施建设的不断发展,建筑垃圾、尾矿渣、粉煤灰等废弃材料的数量也在迅速增加。
这些废弃材料如果不得到有效利用,不仅会对环境造成污染,还会浪费大量资源。
因此,开发利用这些废弃材料,实现资源化利用和环境友好型循环利用是当前亟需解决的问题之一。
流态固化再生混合料作为一种新型的再生材料,具有可替代天然资源、降低碳排放、提高工程品质等优点,受到了广泛关注和研究。
二、流态固化再生混合料概述流态固化再生混合料是将废弃材料与固化剂按一定比例进行均匀混合,并在一定温度下进行流态固化得到的再生混合料。
在固化过程中,固化剂会与废弃材料中的活性成分发生化学反应,从而形成一种新的材料,其物理性能和工效性能均优异。
目前,常用的废弃材料有建筑垃圾、尾矿渣、粉煤灰等,常用的固化剂有水泥、石灰等。
流态固化再生混合料具有耐久性好、稳定性高、成本低、环保可持续等特点,可广泛应用于基础建设、道路工程、园林绿化等领域。
三、流态固化再生混合料的制备方法流态固化再生混合料的制备方法主要包括废弃材料的选取、预处理、固化剂的选取、混合配比、流态固化和成品混合料的质量控制等环节。
1.废弃材料的选取与预处理首先需要对废弃材料进行选取,通常选用的废弃材料有建筑垃圾、尾矿渣、粉煤灰等。
在选用废弃材料时,一般需要考虑其活性成分含量、颗粒大小和含水量等因素。
对于大颗粒的废弃材料,通常需要进行粉碎处理;对于含水量过大的废弃材料,通常需要进行自然晾晒或机械干燥处理。
预处理后的废弃材料应具有一定的活性成分含量和一定的颗粒大小适应性,以满足与固化剂的混合要求。
2.固化剂的选取与混合配比固化剂是流态固化再生混合料中的关键组成部分,其选取和混合配比直接影响了混合料的品质。
目前常用的固化剂有水泥、石灰等。
在进行固化剂的选取和混合配比时,通常需要考虑固化剂的品种、含量、硬化速度和耐久性等因素。
【doc】DIOS熔融还原工业试验情况
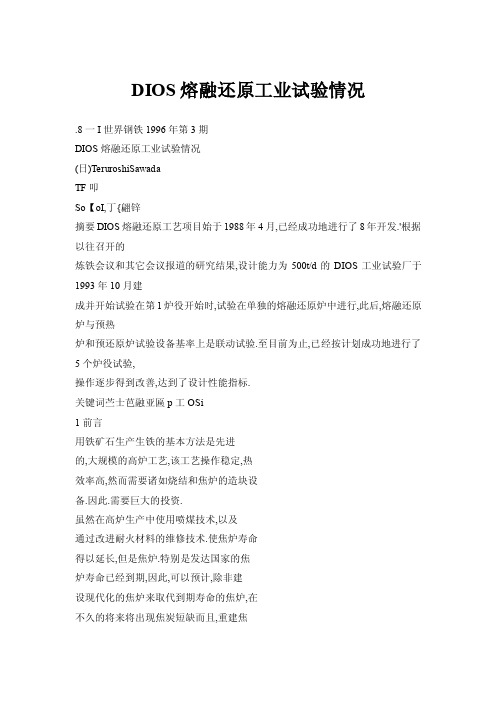
DIOS熔融还原工业试验情况.8一I世界钢铁1996年第3期DIOS熔融还原工业试验情况(日)TeruroshiSawadaTF叩So【oI,丁{翩锌摘要DIOS熔融还原工艺项目始于1988年4月,已经成功地进行了8年开发.'根据以往召开的炼铁会议和其它会议报道的研究结果,设计能力为500t/d的DIOS工业试验厂于1993年10月建成并开始试验在第1炉役开始时,试验在单独的熔融还原炉中进行,此后,熔融还原炉与预热炉和预还原炉试验设备基率上是联动试验.至目前为止,已经按计划成功地进行了5个炉役试验,操作逐步得到改善,达到了设计性能指标.关键词苎士芭融亚匾p工OSi1前言用铁矿石生产生铁的基本方法是先进的,大规模的高炉工艺,该工艺操作稳定,热效率高,然而需要诸如烧结和焦炉的造块设备.因此.需要巨大的投资.虽然在高炉生产中使用喷煤技术,以及通过改进耐火材料的维修技术.使焦炉寿命得以延长,但是焦炉.特别是发达国家的焦炉寿命已经到期,因此,可以预计,除非建设现代化的焦炉来取代到期寿命的焦炉,在不久的将来将出现焦炭短缺而且,重建焦炉要符合未来的环保排放标准.预计将发展投资更小,效率更高的炼铁工艺,以取代依赖优质烧结矿和焦炭的高炉生产工艺.一种替代工艺是南非比勒陀利亚厂的用煤生产铁水的Corex熔融还原工艺,且已证实具有商业价值.对更有效地使用煤的下一代熔融还原的工艺一直在进行研究,并取得进展.新工艺的目标是直接使用煤和铁矿粉, 不仅要取消对环境有影响的焦炉,而且想取消球团厂和烧结厂.目前熔融还原工艺研究最有进展的有日本的DIOS,美国的AISI和澳大利亚的Hlsmelt工艺.D】Os熔融还原工艺是在日本自然资源和能源部的支持下,8个最大的钢铁公司参与,由日本煤利用中心和日本钢铁联盟共同进行的煤实用技术研究项目,始于1988年4 月,计划进行8年(图1略)头三年在日本5个最大的钢铁厂进行基础研究,以得到工业试验厂的基本条件,在此基础上,于1990 年在日本钢管公司京滨厂建造一座500t/d (180,000t/a)的工业试验厂,并于1993年9月建成.1993年10月进行操作试验,至1994年I1月成功地按计划进行了5个炉役的试验.本文描述D1Os工业试验厂设备的特点及取得的试验结果.2DIOS熔融还原工业试验厂的特点图2是DIOS熔融还原工业试验厂简要流程图.DIOS工艺主要由预热和预还原两段炉子,一座熔融还原炉和煤气改质系统组成.预热和预还原炉都是流态化床,在预还原炉中被废气带走的铁矿细料可以循环,以增加预还原度,熔融还原炉是一个内容积为95m的铁浴型炉,中心位置装有氧枪,配有与高炉类似的出铁设备.熔融还原炉工作压力(表压)可增至I9.6×10Pa.粉煤可通过煤气改质系统喷入熔融还原炉.烧结使用的铁矿原料干燥至水分少于2后,装入预热炉.加热至500C左右,然世界钢铁?9?固2DIOS熔融还原工业试验厂流程四后选至预还原炉,在高于700rc下还原至约2o,被分成粗,细两种粒级.细粒级铁矿与热旋风除尘器粉尘一道喷入熔融还原炉粗粒级铁矿通过风动给料阀加至熔融还原炉,干燥至水份小于6的煤与熔荆一道直接加入熔融还原炉.在熔融还原炉中,预还原铁矿熔化,并在厚渣层中直接还原成铁水从底部喷嘴喷入氮气进行搅拌,每隔2~3h出铁一次. DIOs熔融还原工业试验厂主要设备规格见表l.虽然生产率目标为21t/b但工厂铁水最大生产能力按25t/h进行设计表1DIOS工业试验主要设备规格设备规格工厂规楗原料供料预{正原炉熔融还原炉煤气政质出铁设备生产率5oo~/d(ZLt,h)铁矿最犬45t/h煤25t/h焙剂4.6t/h类型流态化床内径x高度Z700nm~×8∞0…能力最犬39t/h类型铁搭炉内径×高度$700mm×9$0Onm~护内压力<19.6×lO'(表压)添加细煤最大4tm类型开口机一怩炮3工业试验操作情况自l993年10月开始进行工业试验,至l994年l1月,成功地进行了5个炉役试验.3.1工业试验步骤图3列出了工业试验步骤.首先整个工业试验系统用氯气吹扫,然后将一定量的铁水加入熔融还原炉,通过中心氧枪吹氧.熔化高炉渣形成初渣,在吹氧后1~2h,工业EH◇:嚣◇:◇挽t.J●焙融蕞矿供料建崖I高妒檀I证原护:l原矿l_吐矿煤供料遵廑广ml.悻矿供枉运崖I;璜热矿幅i王原炉铁矿捌采量:/铁科建厦;I!I贰矿顶热炉:?铁矿瘌泉量/<》加^初始饿水>出畦圈3I)IOS工业试骚步骤10?1996年第3期试验操作即能达到稳定.同时,预热炉和预还原炉中流态化的铁矿量保持不变.3.2操作进程昌-Z_f皂一曲莲●*三最初3个炉役的基本操作数据变化情况示于图4.在第1炉役进行了15炉试验.目的是对所有设备进行运转试验.确定基本操:蝴.i一o'0每炉平均值I吣一:s妖一0每妒平均墟'i—鼹t●●—●lll'.短I辩I[值Il『lIIlIllltI};B9"i'23412345^7S第护槛圈4DIOS工业试验操作指标变化情况作条件.虽然在工业试验开始时,在单独的熔融还原炉中进行试验.但从第8炉开始,熔融还原炉与预热炉和预还原炉连结在一道(即联动操作)进行试验.第2炉役于1994-年1月开始,目的是取得基本操作方法并完成主要技术项目的研究.进行了6炉试验,特别是第2炉连续操作了6天.第3炉役于1994年4月开始,在第】,2炉役建立的操作技术基础上,进行了8炉试验.联动操作氧气流量范围为10000~13000m./h,炉内尽可能保持较高压力,最大可达19.6×10Pa(表压)随着操作技术的改进,试验操作情况大为改善,达到了工业试验目标.4试验结果与讨论4.1铁矿在预热炉和预还原炉内的行为如前所述.铁矿首先加入至预热炉.然后送至预还原炉,两座炉子均为流态化炉.铁矿在两座炉子中的停留时间分剐为2o和60min.铁矿在两座炉子中用熔融还原炉来的热煤气预热和预还原,同时.铁矿粒度细化,并被分为粗,细两级.铁矿在流化床中的粉化行为一般认为是流态化条件的影响如矿石的特性(还原粉化指标和热裂性能等),随着煤气流的上升还原和外来能量使矿石结构变弱在工业试验中.认为在预热炉中矿石粉化的主要原因是陕速加热至500C引起热裂,而在预还原炉中是还原使矿石结构变弱.根据炉内煤气速度及矿石的粒度分布,粉化矿石进一步分成粗,细两级,这种分级对形成稳定的流化床是必要的.废气从流化床中带走的矿石粒级取决于各种粒级的最终速度.工业试验中煤气速度是2—3m/s,相应世界钢铁地,分成两部分的临界粒度约为0.3ram,图5示出试验矿石的粒度分布圆5加入铁矿的粒廑分市流化床中铁矿的还原行为一般认为是受煤气成份,还原温度,煤气量,停留时间及矿石的还原能力等操作因素的影响图6表明了流化床温度与铁矿还原度的关系以及福图6康层温度对预热炉和强还原炉中铁矿还原度的群响(()D=气化度RT一停留时间)山和干叶厂得到的基础研究结果.随着料层温度升高,特别是在650~750C范围内,铁矿还原度升高,但是,超过750C时,还原度增加变慢.这与基础研究得到的数据相一致, 结果解释如下.由于从Fe0.至Fea0还原率高,料层温度对还原反应影响很小,在较低温度下还原反应进行平稳,而从Fe0至富氏体,还原反应受料层温度影响很大,因此.随着料层温度增至750C,还原度增加{B 快,超过750c后,由于煤气成份接近化学平衡,料层温度对还原度的影响减小.此外,图6还表明,从流化床中带走的细粒矿,虽然矿石一煤气反应时间短,但能够还原至与粗粒矿相同的程度.粗粒矿在流化床中停留时间更长,在预还原炉中不循环.4.2熔融还原炉中煤的反应性能如图4所示,在联动操作下,在产量大于20t/h时.单位煤耗可降至78O~950kg/t. 虽然对挥发份含量为15~33的4种煤进行了测试,但基本上是使用高挥发份煤.开发DIOs工艺的目的之一是得到与高炉工艺相当的燃料比.DIOS工艺的主要热源是由煤的二次燃烧获得,因此,DIOS必须获得较高的二次燃烧率,并同时获得较高的传热效率.在基础研究中发现.厚渣层,铁涪搅拌和炉内加压等操作技术对获得较高的二次燃烧率和传热效率都是有效的.∞0t'..操作条件嚷气鼍北度:oI)38%恃音}I啦率:99%吨靛攥韩:94~lkB/靛木产量:21t/-h●环蛰生16』精^碳捧出2日挥发姆碱燃烧239嗣定碱撼烧163矿迁265培^蛙木0礁硝韩图f碳平衡示例(VMC~挥发物中的碳Fc固定碳)图7表示在铁水设计生产能力下使用高挥发份煤的一种碳平衡示例.其二次燃烧率121996年第3期为38.比福山厂基础研究的4O~55要低,而传热效率达99.比基础研究的85~90要高.煤气氧化度较低,传热效率较高是工业试验操作的特点,这种趋势说明离开熔渣表面的煤气部分与挥发份中的碳发生了反应,因此使炉子上部气体混合物中富含CO和H.假定热交换效率为90.与基础研究结果相同,鄢么,离开熔渣表面的气体氧化度估计大于43.图8表明单位煤耗与铁水生产率间的关系图中的曲线是假设传热效率为90时的囤8单位煤耗与铁水生产率的关系计算结果.随着生产率的提高,二次燃烧率得到改善,由于炉子的热损失相对较低,单位煤耗降低同时说明,与高挥发份煤相比,低挥发份煤对获得高的二次燃烧率效果更好高挥发份煤的单位煤耗为950kg/t.但是低挥发份煤的单位煤耗可能降到780kg/t.4.3炉料畋出如前所叙.铁矿在预还原炉中预还原并分成粗细两级,粗粒矿靠重力加入熔融还原炉中,而细粒矿用氮气从炉顶喷凡.煤和其它炉料靠重力直接装入熔融还原炉从熔融还原炉中吹出的粉尘用旋风除尘器收集,与细粒矿一道喷凡熔融还原炉.在工业试验中,在1.5~3.0m/s的试验的速度范围内,随着熔融还原炉内煤气速度升高.炉料吹出量增加.此外.还发现吹出粉尘主要由较细的铁矿和煤粉组成,而且,随着炉科吹出量增加,其碳含量增加.而铁含量降低.上述现象在图9中得到证实.图9表明,熔融还原炉中煤气速度对煤吹出量的影响,囤9煤气速度与蜞吹出量的关系(HV=高挥发份MV一中挥发份I,V等低挥发份煤畎出量取决于离开炉子的煤气速度.中挥发份煤中,粒度大于]mm与大于3ram的煤相比,细粒煤似乎比粗粒煤更容易被废气带走,可是,使用大于3mm的低挥发份煤LV2,煤吹出量却比使用其它煤要高.已经知道,当煤迅速加热时,低挥发份煤比中,高挥发份煤更易受热冲击而粉化.与此相应,可以假定在熔融还原炉中低挥发份煤发生了热爆裂.图10表明铁矿装入量与铁吹出量的关系.尽管装入铁矿量增加.其中粉矿量达60~70,但吹出铁量并不增加.由此可以证明,炉顶喷吹粉矿技术可以用于商业规模的生产厂中.4.4硫平衡图¨表明熔人渣和铁水中的硫含量与操作时间的关系.铁水中的硫含量开始时增大.但是在试验进行10~]5h后.硫含量达到稳定状态.世界钢铁?13?圈1o棱矿装入量与铁吹出量的关丰DIOs工业试验硫平衡示于图】2.加入熔融还原炉中的硫,大部分由加入的煤带入, 保留在獯热炉和(缸宇单位:sk~/h}迁原炉中的髂矿442矿惦剂2S蹦12DIOS工业试验中硫平衡图一部分通过气化反应脱除.一部分溶入熔渣和铁水.几乎所有的气态硫被熔融还原炉中吹出的粉尘吸收,或者被预热炉和预还原炉中吹出的粉尘吸收,被吸收的硫有一大半循环进入熔融还原炉,剩余部分通过预热炉旋F..II??1??Is结论截至1994年1】月,已按计划成功地进行了5个炉役的DIOS熔融还原工业试验虽然本文仅叙述了第1至第3炉役的试验结果,但是在此期间,设备性能逐步改善,达到了设计目标.而且还弄清了DlOS工艺中的反应行为.DIOs试验项目将进行至1996年3月,在工业试验的剩余炉役中将主要测试熔融还原炉的水冷系统,并评价其水冷效果.最后,1995年将完成商业规模的DIOS熔融还原厂的可行性研究.徐国群译自~IronmakingConferencePro—ceedings》,1995,499~506周渝生校(收稿日期1996年4月10日)。
流化现象的原理和应用
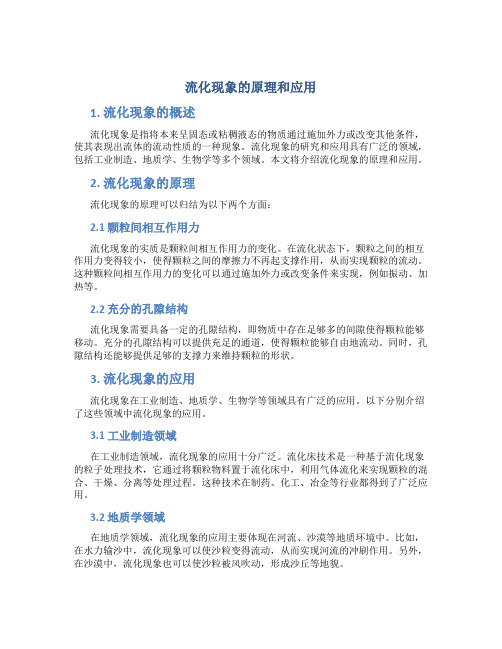
流化现象的原理和应用1. 流化现象的概述流化现象是指将本来呈固态或粘稠液态的物质通过施加外力或改变其他条件,使其表现出流体的流动性质的一种现象。
流化现象的研究和应用具有广泛的领域,包括工业制造、地质学、生物学等多个领域。
本文将介绍流化现象的原理和应用。
2. 流化现象的原理流化现象的原理可以归结为以下两个方面:2.1 颗粒间相互作用力流化现象的实质是颗粒间相互作用力的变化。
在流化状态下,颗粒之间的相互作用力变得较小,使得颗粒之间的摩擦力不再起支撑作用,从而实现颗粒的流动。
这种颗粒间相互作用力的变化可以通过施加外力或改变条件来实现,例如振动、加热等。
2.2 充分的孔隙结构流化现象需要具备一定的孔隙结构,即物质中存在足够多的间隙使得颗粒能够移动。
充分的孔隙结构可以提供充足的通道,使得颗粒能够自由地流动。
同时,孔隙结构还能够提供足够的支撑力来维持颗粒的形状。
3. 流化现象的应用流化现象在工业制造、地质学、生物学等领域具有广泛的应用。
以下分别介绍了这些领域中流化现象的应用。
3.1 工业制造领域在工业制造领域,流化现象的应用十分广泛。
流化床技术是一种基于流化现象的粒子处理技术,它通过将颗粒物料置于流化床中,利用气体流化来实现颗粒的混合、干燥、分离等处理过程。
这种技术在制药、化工、冶金等行业都得到了广泛应用。
3.2 地质学领域在地质学领域,流化现象的应用主要体现在河流、沙漠等地质环境中。
比如,在水力输沙中,流化现象可以使沙粒变得流动,从而实现河流的冲刷作用。
另外,在沙漠中,流化现象也可以使沙粒被风吹动,形成沙丘等地貌。
3.3 生物学领域在生物学领域,流化现象的应用主要体现在生物流体中。
例如,在人体血液循环中,流体的流化性质使血液能够顺利地流动到全身各处,实现物质的输送和代谢。
另外,在细胞生物学中,细胞内的细胞质也表现出一定的流化性质,使得细胞内各种物质可以流动和交换。
4. 总结流化现象是一种将固态或粘稠液态物质转变为流体的现象,其原理是颗粒间相互作用力的变化和充分的孔隙结构的存在。
2024年度流态化工程原理PDF版PPT大纲
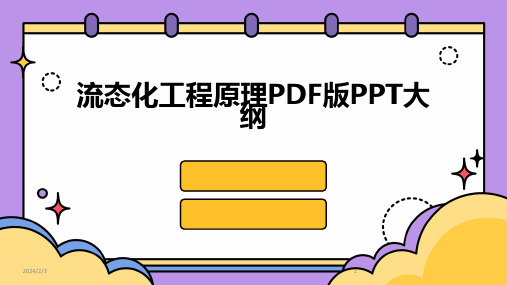
流态化技术也用于熔融还原过程,如铁浴熔融还 原等,以实现高效、环保的冶金生产。
挑战与问题
3
冶金行业流态化技术应用面临高温、高压、高粘 度等极端条件挑战,以及物料粘结、设备磨损等 问题。
2024/2/3
29
环保领域应用前景展望
废气处理
流态化技术在环保领域具有广阔应用前景,如用于废气处理中的 脱硫、脱硝等过程。
态化。
散式流态化特征
聚式流态化特征
颗粒均匀分散,床层膨 胀均匀,颗粒间相对运
动小。
8
颗粒聚集成团簇,床层 膨胀不均匀,颗粒间相
对运动大。
流态化基本方程与参数
01
02
03
04
流态化基本方程
描述流态化过程中颗粒受力与 运动关系的方程。
重要参数
包括颗粒密度、流体密度、操 作速度、床层空隙率等。
颗粒受力分析
2024/2/3
循环流化床反应器
通过气体循环使床内颗粒 保持快速流动状态,床层 温度均匀,适用于小颗粒 物料和高温、高压反应。
振动流化床反应器
通过振动使床层颗粒保持 流动状态,可强化传热、 传质过程,适用于易结块 、粘性物料。
13
流化床反应器设计原则与方法
设计原则
满足工艺要求,保证操作稳定、可靠;实现高效传热、传质;降低能耗,减少 环境污染。
颗粒团聚成因
颗粒间作用力导致颗粒聚集,影响流态化效果。
处理措施
优化颗粒形状和大小分布,减少颗粒间作用力;加入适量细粉或液体,改善颗粒 流动性;采用振动或搅拌等外部力场破坏团聚。
2024/2/3
24
堵塞现象预防与处理方法
2024/2/3
堵塞现象成因
非高炉炼铁工艺发展现状

保证其高的还原速 率。
M e 技 术和 H L I irx d Y — 技术 具 有 污 染较 小 ,能耗 低 I I
的特 点,但都 只解 决了不使用焦炭这一个 问题 ,仍 必 须使用球 团矿 ,另外 我国天然气资源严重缺乏 ,这两
基直接还原有着 自己的特 点,我 国煤 资源丰 富,此 工
2 1 .1o 中闯 新技 企 0 o 1 高 术 业 5 7
艺在 我 国有 着 一 定 的发 展前 景 。
烟道燧奄
料 进 行 一 定 程 度 的还 原 后 入 炉 , 同时 可 以减 小终 还 原 炉 生 产 成 品铁 的 压 力 。 因此 二 步 法 熔 融 已经 成 为 熔 融 还 原工 艺 的主 要 发展 方 向 。
术还原温度为80 0 ℃~9 0 0 ℃),另外 ,H L I I Y — I 反应器
内压 力 > . 5 P ,其 高温 、 高 压 、 高 氢气 浓 度 的条 件 0 5M a
公 司 开 发 的一 种 用 粉 矿 和 煤 生 产 优 质 海 绵 铁 的 工艺 ,
工艺原理 :采用转底炉 ,将煤层和铁矿粉交替铺在炉 床上 ,通过煤气烧嘴加热 。这样 的混合物可使温度 很 快上升到1 0 ℃ 以上 。此工艺可 以使用粉矿 ,但煤 层 30 和铁矿粉 的交替铺层必然 导致其 生产率低 的弱点。煤
高炉炼铁发展至今,因其必须使用储量有限的焦炭
为 主 要 燃 料 ,冶 炼
种工艺难 以适应我 国国情。
¨斗
等原 因,面 临着 能源 、环境、投资等方面 的困扰 。近 几十年来世界各 国的冶金 工作 者们 一直致力于研究和 改进各种非高炉炼铁技术 。
E 交流园 地
xeha nge Fi l e d
熔融还原处理-概述说明以及解释

熔融还原处理-概述说明以及解释1.引言1.1 概述熔融还原处理是一种重要的工艺和技术,通过在高温和还原气氛下,使废弃物或回收材料经过熔融加热后发生物理和化学变化,从而实现废弃物的资源化利用和回收再利用。
这种处理方法广泛应用于废弃物处理、金属回收和资源循环利用等领域。
熔融还原处理的原理是利用高温条件下物质的熔融性和还原性。
通过在高温环境中,加入适量的还原剂,使废弃物或回收材料发生熔融反应,通过还原剂与废弃物中的化合物发生化学反应,从而得到可再利用的金属和其他有价值的物质。
熔融还原处理具有许多优点。
首先,它可以实现废弃物的无害化处理和资源化利用,大大减少了废弃物对环境的污染。
其次,通过熔融还原处理,废弃物中的有价值物质可以得到有效回收和利用,具有很高的经济价值。
此外,熔融还原处理还能降低对原材料的需求,实现资源的循环利用,有助于推动可持续发展。
然而,熔融还原处理也存在一些局限性。
首先,熔融还原处理需要耗费大量的能源和设备投入,造成一定的经济成本。
其次,废弃物中可能存在有害物质,在处理过程中需要采取措施防止其对环境和人体健康造成危害。
此外,熔融还原处理的技术和设备仍然存在一些技术难题和待解决的问题,限制了其在某些领域的应用。
综上所述,熔融还原处理是一种具有潜力和前景的技术,能够实现废弃物的资源化利用和回收再利用。
虽然存在一些局限性,但随着科技的不断进步和创新,相信熔融还原处理在未来会有更广泛的应用。
1.2 文章结构文章结构部分的内容可以按照以下方式进行编写:文章结构部分主要介绍本篇文章的章节组成和内容安排。
通过清晰的结构安排,读者可以更好地理解和掌握文章的主题和内容。
本篇文章分为引言、正文和结论三个部分。
在引言部分,我们将首先对熔融还原处理进行概述,简要介绍该技术的定义和原理。
接下来,我们将介绍本篇文章的结构,即各个章节的内容安排。
最后,我们将明确本篇文章的目的,即通过对熔融还原处理进行深入研究,探讨其应用领域、方法,以及优势和局限性,以期为未来的发展提供展望。
熔融还原法

熔融还原法
熔融还原法(fusionreductivemethod)是一种用于制备高纯度
金属、稀土和半导体材料的制备技术。
它同时包含了熔融和还原两个步骤。
熔融还原法是以金属氢化物或硝酸盐为原料进行熔融,然后经过还原处理,以获得高纯度的金属、稀土和半导体材料。
熔融还原法的使用得到了广泛的认可,因为它比其他制备技术更加容易操作,也更具经济效益,而且生产过程中也不需要污染物。
此外,它还可以用于制备高纯度少结晶材料,而其他制备技术无法满足这个需求。
一般来说,熔融还原法可以分为以下几个主要步骤:
1.融:熔融还原法的应用需要将金属氢化物或硝酸盐以最低温度,最低压力的条件下熔融;
2.原:当熔融物质的温度降至某一低点,一定剂量的还原剂必须添加,以降低金属氢化物或硝酸盐的氧化性,将金属原子还原成金属状态;
3.却:当金属氢化物或硝酸盐的氧化性降低后,需要以适当的冷却速率将其冷却至室温;
4.化:当金属处于非晶状态时,需要以恒定的温度和适当温度梯度,使金属进入晶体状态,以获得更高的纯度;
5.涤:在这个步骤中,将金属浸泡在合适的洗涤液中,去除可能残留在表面的污染物,以达到高纯度的要求。
由于熔融还原法具有简单、安全、高效率、低污染等优势,因此
它已经在工业中得到了广泛的应用,比如在获得高纯度金属、稀土和半导体材料方面,都使用到了熔融还原法。
此外,由于熔融还原法能够制备出少结晶材料,以获得最佳性能,因此熔融还原法也被广泛应用于临界温度和高压的研究中,以及在超导领域的研究中。
综上所述,熔融还原法是一种可靠、经济高效的制备技术,它可以用来制备高纯度金属、稀土和半导体材料,也可以用于临界温度和高压的研究以及超导领域的研究,具有广泛的应用前景。
FINEX熔融还原炼铁技术简介

FINEX熔融还原炼铁技术简介近代高炉炼铁工艺经过150多年的发展,在生产效率、工艺技术、装备大型化等方面日臻成熟,各项潜力得以较为充分的发挥,为人类文明和经济发展做出了巨大贡献。
但高炉生产依赖的焦煤资源供应不足,加之烧结及焦化工序污染严重,其可持续发展面临巨大挑战。
因此,基于不用焦炭的非高炉炼铁技术,成为近30多年来世界钢铁业着力研究和发展的前沿技术之一。
其中,熔融还原炼铁技术得到广泛关注,这项技术以非焦煤为能源,在高温熔态下还原铁氧化物得到铁水,主要包括COREX和FINEX两种工艺。
FINEX起源于COREX,但针对COREX 存在的问题进行了集成创新,形成特有的技术如流态化还原炉、煤压块、还原铁压块等,已成为目前世界上技术相对成熟、工业生产适应性较好的熔融还原炼铁工艺。
自1992年起,韩国浦项与奥钢联合作启动FINEX技术基础研究,历经20余年的研发,先后建成60万t/a的示范厂、150万t/a的工业化生产厂,2011年已开工建设200万t/a的FINEX工厂。
2013年,我国重庆钢铁集团与POSCO正式签署了建设年产300万吨规模“FINEX 一贯制铁所”合作协议,标志着该项技术首次引入国内。
一、FINEX工艺概述FINEX工艺是在COREX工艺基础上开发的一种新的熔融还原工艺。
其工艺主要由3个工序组成:流化床预还原装置、DRI粉压块装置和熔融气化炉装置。
第一步是流化床反应装置,可以把铁矿粉进行预还原,其所使用的还原性气体是由熔融气化炉的煤经燃烧和高温分解而产生的;第二步,经流化床预还原后进入压块工序,变成热压块铁。
非焦煤经过压块变成压块煤,加入到熔融气化炉中;第三步,压块煤在熔融气化炉中燃烧产生热量,把经流化床中还原过的热压块铁熔化成铁水和炉渣[1]。
其工艺流程图见图1所示。
图1FINEX工艺流程图二、FINEX工艺的优势[2]FINEX工艺具有几个方面的优势:1.可采用资源丰富、廉价的铁粉矿。
- 1、下载文档前请自行甄别文档内容的完整性,平台不提供额外的编辑、内容补充、找答案等附加服务。
- 2、"仅部分预览"的文档,不可在线预览部分如存在完整性等问题,可反馈申请退款(可完整预览的文档不适用该条件!)。
- 3、如文档侵犯您的权益,请联系客服反馈,我们会尽快为您处理(人工客服工作时间:9:00-18:30)。
在20世纪五六十年代,流态化直接还原技术开始工业应用,典型的工艺有菲尼克斯(FINEX)工艺(采用多级串联流化床)、芬麦特(FINMET)工艺(采用多级串联流化床)、黑斯麦尔特(HIsmelt)工艺(采用循环流化床)、瑟科瑞德(Circored)工艺(采用循环流化床与鼓泡流化床的组合)、迪欧斯(DIOS)工艺。
流态化还原的特点是直接利用粉矿,以气体作还原剂,反应在气-固两相中进行。
矿粉在固态下直接还原成金属铁,接着在其他高温设备中熔融炼铁或直接粉末冶金。
相对其他的技术,流化床处理粉矿的成本较低,具有原料和设备利用率较高、热交换效率高等诸多优势,而且高温流化床反应器在化工等领域已广泛应用,也可以为流化床还原粉铁矿的工艺提供良好的借鉴。
1.流态化技术在熔融还原工艺中的应用
流化床在直接还原炼铁过程中有磁化焙烧生产铁精矿粉、预热和低度预还原粉铁矿、生产直接还原铁等冶金功能。
1)磁化焙烧铁精矿粉
磁化焙烧是将Fe2O3在还原气氛中焙烧得到磁化性的Fe3O4,经过磁选使Fe3O4与杂质分离,得到品位高的铁精矿。
1973年~1982年,为了开发攀枝花资源,我国进行了3次流态化还原综合回收钒钛铁的试验研究。
3次的试验结果表明,我国的流态化还原法在理论上是可靠的,工艺上是可行的,主体设备上是成功的,从而为向工业化过渡创造了条件。
2)预热和低度预还原粉铁矿
流化床预热和低度预还原粉铁矿工艺中的典型代表是HIsmelt 工艺和DIOS工艺。
HIsmelt工艺正处于工业化开发阶段。
矿粉经过整粒筛分除去大颗粒矿粉后经皮带输送到矿石预热器中进行预热和初级预还原。
整粒筛分后的粒度小于6mm,预热后的矿粉温度可达700℃~800℃,预还原度为10%~11%,处理后的热矿粉装入热矿仓等待喷吹。
为了缓解铁浴炉的压力,可提高预热粉铁矿的还原度,但是粉铁矿只经一级循环流化床预热还原,其还原度一般不超过25%。
DIOS工艺的预还原采用快速流化床与沸腾流化床组合的复合型流化床系统。
粉铁矿在一级预热流化床中预热到500℃~600℃,预还原度达到8%~9%;在二级流化床中粉铁矿温度升高到约780℃,还原度约为27%。
粗粉还原以沸腾床为主,细粉还原则在循环床中进行,且细粉还原炉在较高的炉压下工作,煤气流速相对缓慢,预还原仍在浮氏体范围内。
实践结果表明,低度预还原的DIOS未获得成功,也未实现工业应用。
3)直接还原生产DRI或HBI
目前,最常用的优质废钢的替代料是直接还原铁(DRI)和热压块铁(HBI)。
流化床是生产直接还原铁的常用装备,典型的工艺有FINEX (预还原预热炉料)、Circored和FINMET工艺等。
FINMET是工业应用较成功的工业装置,该工艺可直接用粒度小于12mm的粉铁矿,其生产装置由四级流化床顺次串联,逐级预热和还原粉铁矿。
第一级流化床反应器内温度约为550℃,最后一级流化床反应器内温度约为800℃,析碳反应主要发生在此流化床反应器内。
反应器内的压力保持在1.1MPa~1.3MPa。
产品的金属化率为91%~
92% ,碳质量分数为0.5%~3.0% ,产品热压块后外销或替代优质废钢。
流化床反应器顶部煤气与天然气蒸汽重整炉的新鲜煤气混合后作为还原煤气,混合煤气经过一个CO2脱除系统,在还原煤气炉内加热到830℃~850℃之后被送入流化床还原反应器。
新鲜煤气是为了补偿还原过程中消耗的CO和H2。
Circored工艺流程如下:粉铁矿进入初始阶段的循环流化床反应器之前,在循环流化床预热器中被干燥预热到850℃~900℃。
预还原的金属化率约为70%,粉料流入流化床反应器进行终还原,反应后其金属化率为93%~96%。
流化床被分隔以利于控制。
通过加热矿和循环气体为吸热还原反应提供热能。
整个还原工艺的绝对压力为4个大气压,还原温度在630℃~650℃。
预还原阶段的停留时间短,气体流速高;终还原的停留时间长,气体流速低。
从终还原炉产出的还原矿粉在700℃下被压成块(HBI),所以有利于安全贮存和运输。
FINEX工艺由三级流化床反应器串联组成,可以直接使用粒度小于8mm的粉铁矿,生产较高预还原度的DRI供熔化气化炉冶炼铁水。
粉铁矿和粉状熔剂(石灰石和白云石等)以及焦炭粉的混合炉料经干燥后,由垂直传送带和锁斗仓添加到三级流化床反应器系统。
炉顶煤气经除尘净化后约41%通过加压变压吸附去除CO2,使煤气中的CO2
从33%降到3%,然后返回一级反应器作为补充还原气体循环利用,有效地利用工艺内部能量循环,突破了FINMET工艺需要天然气的能源限制,降低了燃料比。
FINEX工艺的金属化率控制在50%~70%,有效地控制了流化床的黏结,扩大了流化床的产能,与有7米厚半焦床的熔化气化炉匹配更佳。
4)几种流化床处理粉铁矿工艺的比较
采用中高预还原度的FINEX、FINMET和Circored工艺都已经工业化,而低预还原度的HIsmelt和DIOS工艺处在半工业化和小规模工厂试验阶段。
上述几种工艺中预热粉矿多采用循环流化床床型,还原粉矿多使用鼓泡流化床。
除HIsmelt工艺外,其他工艺均采用多级流化床匹配运行,以此提高煤气利用率和增强工艺可行性。
2.熔融还原工艺中采用流态化技术的思考
现有的流态化直接还原工艺中FINEX用于熔融还原的工业化最为成功,浦项制铁把FINMET与克瑞克斯(Corex)这两种成熟的工艺
嫁接在一起,对这两种工艺的参数进行了优化。
这一点非常值得参考和借鉴,对开发熔融还原新工艺有重要的现实意义。
HIsmelt和DIOS工艺因预还原度较低而造成终还原炉负担过重,导致耐火材料侵蚀过快、燃料消耗高和仅能够维持间歇式冶炼等问题,难以实现工业化连续生产。
在开发和设计流态化预热预还原系统时,必须考虑合理的铁浴终还原系统的冶炼强度和还原能力。
在两步法熔融还原工艺中,流态化预还原和预热粉铁矿应达到80%左右的预还原度和800℃左右的温度。
高的预还原度虽能减轻铁浴炉的还原压力,但容易使流化床产生黏结和失流,影响流化床的操作稳定性。
流态化预热预还原系统可以直接高效地利用粉铁矿资源,省去造块(球)和烧结工序,减轻了环境污染,降低了生产成本,同时这也是实现高效熔融还原炼铁工艺的有效途径。
流化状态的选择要依据生产工艺的实际要求而定,可以采用同种床型的多级串联或者多种床型的组合系统。
在设计床型时必须考虑高温下粉矿和还原气体的性质及其反应特性。
适度降低粉铁矿的预还原度,能为流化床创造宽松的操作条件,解决或缓解黏结和失流等问题。
另外,将粉铁矿预热,能缓解铁浴终还原炉的热负荷强度,提高整个熔融还原工艺的熔炼效率并降低能耗。
煤气改质的冶金功能定位在调节和变换铁浴终还原炉产出的高
温煤气和流态化预热预还原系统的炉顶煤气。
如何综合利用产生煤气所携带的物理热和炉顶煤气的物理余热,直接关系到能否降低工艺系统的能耗。
煤气改质系统解决了高温煤气物理余热的利用问题。
煤气改质是利用高温煤气携带的物理余热作为改质热源,将物理热转化为煤气的化学能,提高了煤气的还原势和系统能量利用率。
煤气(富氢)改质能为预还原工序提供合格的还原煤气,提高预还原操作的工作效率,更好地匹配二步法熔融还原工艺中预还原和终还原的操作。
另外,循环利用流态化预还原的炉顶煤气的化学能和物理热,能够提高预还原炉料的产能,并进一步降低工艺的燃料消耗,同时也提高了铁浴终还原炉的生产率并延长了其寿命。
选择铁浴炉作为终还原系统的装备,一方面选用非焦煤作为燃料和还原剂,可以扩大冶金工业的能源适用性;另一方面直接使用高温(800℃左右)、较高预还原度(80%)的粉矿为炉料,能省去压块工序,节约成本。
铁浴熔池将熔解喷入的煤粉、矿粉和熔剂,并迅速进行还原反应,产生的气体对熔池进行强烈搅拌,能促进矿粉的快速还原,确保渣中的FeO处于较低的水平,减缓耐火材料的侵蚀,使其达到工业化生产要求。
溶解碳还原FeO比固体碳还原FeO高出1个~2个数量级,可以提高铁浴终还原炉的生产效率。
参考上述工艺,考虑到终还原产生煤气的温度和还原势与预还原工序的匹配,以及终还原炉的冶炼强度等因素,铁浴终还原炉的二次燃烧率控制在20%左右应该可行。
熔融还原工艺的燃料消耗远高于高炉流程,其最终能耗和操作成本在很大程度上依赖于尾气的综合利用。
输出煤气经煤气改质后可用于还原铁矿石生产碳化铁和海绵铁,或作为化工原料生产二甲醚,也可以利用输出煤气直接发电。
经过上述分析和思考,借鉴和参考现有的流态化熔融还原流程,提出一种采用流化床处理粉铁矿的熔融还原炼铁新工艺流程,包括流态化预热预还原系统、煤气改质系统、铁浴终还原系统和综合利用系统4个部分。
3.结语
第一,在炼铁工艺中流态化的应用有磁化焙烧生产铁精矿粉、预热和低度预还原粉铁矿和生产直接还原铁,典型的流化床处理粉铁矿的工艺流程有FINEX、FINMET、Circored和HIsmelt等。
第二,目前主流的熔融还原炼铁工艺流程均为二步法,采用中高预还原度和低二次燃烧率(Corex和FINEX已经工业化)的工艺可行性更佳,开发新的炼铁工艺流程理应遵循这一原则。
第三,新的炼铁流程中设有煤气改制环节,使预还原和终还原工序更加匹配和顺行。