半固态触变注射成型镁合金组织性能分析定稿版
半固态成型加热工艺对镁合金组织与耐腐蚀性能影响

调研报告1.课题来源及意义镁是地壳中含量最丰富的元素之一,其丰度居第8位,约占地壳组成2.5%,主要以白云石(碳酸镁钙)、菱镁矿存在,此外,海水中含镁约0.13%,可谓取之不尽[1]。
镁合金密度小、比强度高、弹性模量大、减振、抗冲击性能好,成为21世纪材料体系中的重要组成部分,在航空、航天、汽车等众多领域得到广泛应用[2,3]。
然而镁合金仍暴露出力学性能偏低和耐蚀性能差等问题。
本次课题研究了半固态重熔工艺对镁合金组织与耐腐蚀性能的影响。
半固态等温热处理是20世纪90年代中期发展起来的一种半固态合金的制备方法,该方法将合金加热到固液两相区并保温以获得特殊的组织形态,是一种消除铸件中枝晶粗大的有效方法。
本课题的主要意义是通过加强镁的力学性能、耐蚀性的相关研究,积极探索增强镁合金强度、耐蚀性的途径,推动镁合金作为结构材料的应用。
2.镁合金的发展概况2.1国内外镁合金材料应用的现状(1)通讯电子行业镁合金在电子行业中的应用以3C产品(手机、笔记本电脑、数码相机) 为主导, 用镁合金制造的壳罩与传统塑胶壳罩相比, 具有如下优缺点。
优点: 1)强度、刚度高, 镁合金强度比塑胶的大4~ 5倍、刚度大20倍, 用作外壳, 可以做得更薄、更轻; 2)散热性好, 镁合金的散热性是塑胶的200倍~ 300倍, 比热也比塑胶的大, 不易过热; 3)镁合金导电性能佳, 有电磁屏蔽作用, 可防止电磁干扰和对人体的伤害, 不必另作导电处理。
缺点: 1)制造周期长, 镁合金制品制造工序冗长, 开模耗时长, 成型后还需二次加工和后续处理;2)生产成本高, 原料贵, 制造工序多, 产品的良品率低, 使镁合金制品成本偏高; 3)色彩变化少, 镁合金本身为银灰色, 只能用涂装印刷变色, 无法如塑料壳那样混色出多种色彩与纹路。
综上所述, 镁合金与塑胶各有所长, 但随着镁合金制件加工方式的改进, 镁合金具有越来越强的竞争力。
(2)汽车行业为减轻汽车重量以降低油耗, 以及“环保型汽车”对材料可回收性的要求, 镁合金在汽车工业中的应用日益广泛。
镁合金半固态压铸触变成形技术的研究

《热加工工艺》2005年第10期综述近年来镁合金作为一种新型绿色环保合金适应了汽车结构件和3C产品对环保方面的要求[1 ̄3],使镁合金不但在航空航天而且在计算机、通讯设备、汽车上得到了广泛的应用。
镁合金产量在全球的年增长率高达20%,显示出了极大的应用前景[4,5],但与铝合金相比,镁合金产量只有铝合金产量的1%。
制约镁合金广泛应用的主要问题是,传统压铸成形工艺在熔炼和加工过程中,镁合金极易氧化燃烧,使得镁合金的生产难度较大,反映出镁合金成形技术的不完善,有待进一步发展。
20世纪70年代初期美国麻省理工学院的Flem-ngs等发明了半固态金属成形技术[6,7]。
该技术是将金属或合金在固相线与液相线温度区间进行加工,其实是一种近净成形工艺。
半固态成形技术的出现为解决镁合金成形中的氧化燃烧等问题提供了条件。
他将传统压铸技术与塑料注射成形技术结合起来,因而无需熔化设备,并避免了镁合金熔化的危险性[8],可用于传统压铸技术不能解决的镁合金的应用问题。
目前,镁合金半固态成形工艺主要分为:流变压铸、触变成形和注射成形。
然而在实际工业生产中主要采用第二种工艺即触变成形工艺。
该工艺是将半固态金属浆料冷却凝固成坯料后,根据产品尺寸下料,再重新加热到半固态温度,然后放入模具型腔中进行压铸成形。
此工艺中涉及到三个非常重要的环节:非枝晶坯料的制备、坯料的二次重熔加热、半固态触变成形。
如图1所示。
1非枝晶组织半固态浆料的制备制备具有非枝晶组织的优质坯料是半固态成形技术的基础和关键。
之所以这样讲是因为这种无枝晶组织的半固态浆料具有独特的流变学特性,即触变性和伪塑性[9,10]。
具有这种组织的材料力学性能优异,因而它的制备方法也是倍受关注的。
根据原材料的状态不同,可将其制备方法分为液态法、固相法和其他方法[11]。
液态法,像机械搅拌和电磁搅拌等都属于液态法范围。
主要是在外场的作用下对熔体进行处理,破碎出生的固相组织使其形成球状颗粒。
注射成形增强半固态AZ91D镁合金的组织及性能

注射成形增强半固态AZ91D镁合金的组织及性能宇文江涛;赵雄;董璐;牛立斌;胡宇阳【期刊名称】《热加工工艺》【年(卷),期】2024(53)6【摘要】为了研究半固态注射成形技术对AZ91D镁合金显微组织、力学性能以及腐蚀行为的影响,通过对半固态注射成形镁合金进行热处理及电化学腐蚀分析,研究了镁合金成形件在注射成形中与热处理后的组织及性能变化。
结果表明,相对于压铸镁合金,半固态注射成形镁合金的组织均匀、力学性能优良、晶粒细小且平均晶粒尺寸为20~30μm,能获得质量良好的显微组织。
镁合金的热处理对晶界第二相的数量和分布有较大影响,能作用于材料性能。
经时效处理后,镁合金硬度从63.47 HV提高到74.05 HV,抗拉强度从125.56 MPa提高到150.91 MPa,抗拉强度提高了20.2%。
在质量分数为3.5%的NaCl溶液的电化学腐蚀中,合金的自腐蚀电位为-959.56 m V,经固溶+时效处理后,自腐蚀电位先升高到-927.55 m V后下降至-988.94 m V,耐腐蚀性能先增高后降低。
【总页数】6页(P122-127)【作者】宇文江涛;赵雄;董璐;牛立斌;胡宇阳【作者单位】中国船舶集团有限公司第七O五研究所;中国船舶集团有限公司第十二研究所;西安科技大学材料科学与工程学院【正文语种】中文【中图分类】TG146.2【相关文献】1.半固态AZ91D镁合金触变注射成形过程数值模拟及参数优化2.等温热处理工艺对AZ91D镁合金半固态组织演变和成形性的影响3.AZ91D铸造镁合金的固溶处理与半固态等温处理后组织与性能变化的比较分析4.形变率对AZ91D镁合金半固态成形组织及流动性的影响5.多段半固态触变成形与半固态流变成形、半固态触变成形工艺对Mg-Y-Gd-Zn-Zr系合金的组织性能影响研究因版权原因,仅展示原文概要,查看原文内容请购买。
镁合金半固态成型用模具

镁合金半固态成型用模具一、镁合金半固态成型用模具的设计1. 成型零件的特点镁合金半固态成型工艺的特点是成型零件具有较高的强度和硬度,同时还具有优异的成型精度和表面质量。
因此,模具的设计需要考虑成型零件的特点,在保证成型零件精度和表面质量的基础上,尽可能地降低设备成本和生产成本。
2. 模具结构设计模具结构设计是模具设计的关键环节,其设计需要考虑到材料的选择和成型零件的结构特点。
对于镁合金半固态成型,通常采用的模具结构包括上模、下模和模具芯。
上模用于固定模具,下模用于支撑工件,而模具芯则用于成型工件的内部空腔。
3. 模具材料选择模具材料的选择对模具的寿命、使用性能和成本都有着直接的影响。
对于镁合金半固态成型,需要选择耐磨性好、热膨胀系数低、导热性能好的材料。
常用的模具材料包括优质合金钢、硬质合金和陶瓷材料等。
4. 模具温控系统设计模具在半固态成型过程中需要保持一定的温度,以保证工件成型时的温度控制和成型质量。
因此,对于镁合金半固态成型用模具,需要设计相应的温控系统,以实现对模具的恒温控制和稳定工作温度。
二、镁合金半固态成型用模具的制造1. 模具加工工艺模具加工工艺通常包括数控加工、线切割、磨削和装配等环节。
数控加工通常用于模具的大型结构部件加工,如上模和下模等;线切割用于模具的小孔和内部复杂结构的加工;磨削则用于模具的表面精加工,以提高模具的表面质量和精度;最后进行模具的装配和调试,以保证模具的成型精度和稳定性。
2. 表面处理工艺模具的表面处理通常包括热处理、表面涂层等。
热处理可以提高模具的耐磨性和使用寿命,同时还可以改善模具的机械性能;表面涂层可以提高模具的表面硬度和耐磨性,从而提高模具的表面质量和成型精度。
3. 模具检测与质量控制模具的质量控制通常包括模具的检测和试模等。
模具的检测主要包括外观检测、尺寸检测和材料检测等,以保证模具的质量和使用性能;试模则用于验证模具的成型工艺和成型零件的质量,以保证模具能够正常运行和生产出合格的工件。
AZ91D镁合金半固态成型

LOGO
感谢观赏
枝晶臂发生熔断示意图
LOGO
3、枝晶臂弯曲机制。 此机制认为,位错的产生并积累导致塑性变形。 在两相区,位错间发生攀移并结成晶界,当相邻晶 粒的倾角超过20°时,界面能超过固液界面能的两 倍,液相将侵入晶界并迅速渗入,从而使枝晶臂从 主干分离。
LOGO
镁合金半固态流变行为:
等温稳态流变行为: 流体组织随剪切历程、时间变化 较小时的流变规律即为半固态合 金的稳态流变性能。 动态流变行为:冷却速率、固相分数和剪切速率
二、半固态成形技术
LOGO
半固态(semi-solid)成形技术: 金属在凝固过程中,对其进行剧烈搅拌, 或控制固-液态的温度区间,得到一种母液中 均匀地悬浮着一定固相成分的固-液混合浆料, 这种半固态金属浆料具有流变特性,即具有 很好的流动性,易于通过普通加工方法制成 产品。
LOGO
半固态浆料(semi-solid Slurry)的制备技术: (1)机械搅拌法
镁合金半固态成形工艺路线及示意图
LOGO
(枝晶)
(固相)
半固态合金中形成的常规枝晶
经搅拌法得到的半固态合金触变结构
三、镁合金半固态理论
半固态金属组织形成机制
LOGO
1、枝晶臂根部断裂机制。因剪切力的作用使枝晶臂 在根部断裂
(a)
(b)
(c)
(d)
枝晶断裂机制示意图
LOGO
2、枝晶臂根部熔断机制: 晶体长大过程中,表面积逐渐减小,由于受到 流体的快速扩散、温度涨落引起的热振动及在根部 产生的应力的作用,有利于枝晶臂熔断,同时由于 固相中根部溶质含量较高,这也降低了熔点,促进 了该机制的作用。
有两个带齿的同心圆筒组成,其中内筒保持静止, 浆料放置内外筒之间,搅拌通过外筒旋转进行。 直接将搅拌棒插入熔 融的金属中进行搅拌 连续搅拌 非连续搅拌
固溶处理对触变成形AZ63镁合金组织和力学性能的影响的开题报告
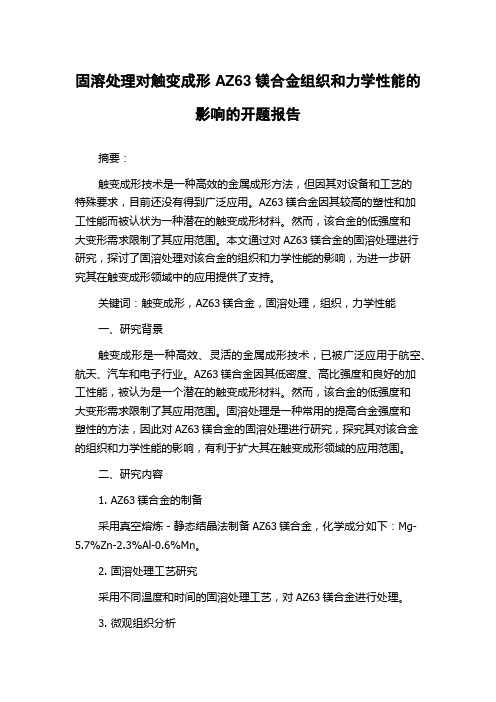
固溶处理对触变成形AZ63镁合金组织和力学性能的影响的开题报告摘要:触变成形技术是一种高效的金属成形方法,但因其对设备和工艺的特殊要求,目前还没有得到广泛应用。
AZ63镁合金因其较高的塑性和加工性能而被认状为一种潜在的触变成形材料。
然而,该合金的低强度和大变形需求限制了其应用范围。
本文通过对AZ63镁合金的固溶处理进行研究,探讨了固溶处理对该合金的组织和力学性能的影响,为进一步研究其在触变成形领域中的应用提供了支持。
关键词:触变成形,AZ63镁合金,固溶处理,组织,力学性能一、研究背景触变成形是一种高效、灵活的金属成形技术,已被广泛应用于航空、航天、汽车和电子行业。
AZ63镁合金因其低密度、高比强度和良好的加工性能,被认为是一个潜在的触变成形材料。
然而,该合金的低强度和大变形需求限制了其应用范围。
固溶处理是一种常用的提高合金强度和塑性的方法,因此对AZ63镁合金的固溶处理进行研究,探究其对该合金的组织和力学性能的影响,有利于扩大其在触变成形领域的应用范围。
二、研究内容1. AZ63镁合金的制备采用真空熔炼 - 静态结晶法制备AZ63镁合金,化学成分如下:Mg-5.7%Zn-2.3%Al-0.6%Mn。
2. 固溶处理工艺研究采用不同温度和时间的固溶处理工艺,对AZ63镁合金进行处理。
3. 微观组织分析采用金相显微镜和扫描电子显微镜对AZ63镁合金的微观组织进行分析。
4. 力学性能测试采用万能材料试验机对不同处理后的AZ63镁合金的拉伸强度和伸长率进行测试。
三、研究意义1. 研究AZ63镁合金的固溶处理对其组织和力学性能的影响,为进一步研究其在触变成形领域中的应用提供支持。
2. 拓展固溶处理方法在镁合金中的应用,促进了镁合金材料的发展和应用。
3. 对于理解镁合金的组织和性能变化机理,有一定的理论意义。
四、研究方案1. 制备AZ63镁合金样品。
2. 设计不同温度和时间的固溶处理工艺,并进行处理。
3. 对固溶处理后的样品进行金相显微镜和扫描电子显微镜分析,了解其微观组织变化。
触变成形az91d镁合金的固溶和时效热处理研究
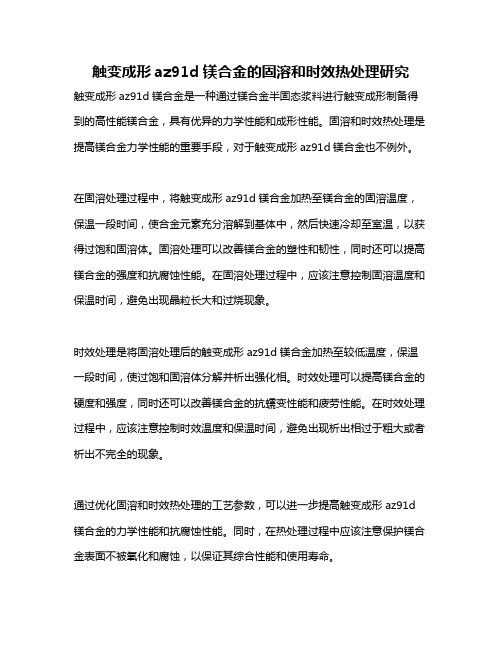
触变成形az91d镁合金的固溶和时效热处理研究触变成形az91d镁合金是一种通过镁合金半固态浆料进行触变成形制备得到的高性能镁合金,具有优异的力学性能和成形性能。
固溶和时效热处理是提高镁合金力学性能的重要手段,对于触变成形az91d镁合金也不例外。
在固溶处理过程中,将触变成形az91d镁合金加热至镁合金的固溶温度,保温一段时间,使合金元素充分溶解到基体中,然后快速冷却至室温,以获得过饱和固溶体。
固溶处理可以改善镁合金的塑性和韧性,同时还可以提高镁合金的强度和抗腐蚀性能。
在固溶处理过程中,应该注意控制固溶温度和保温时间,避免出现晶粒长大和过烧现象。
时效处理是将固溶处理后的触变成形az91d镁合金加热至较低温度,保温一段时间,使过饱和固溶体分解并析出强化相。
时效处理可以提高镁合金的硬度和强度,同时还可以改善镁合金的抗蠕变性能和疲劳性能。
在时效处理过程中,应该注意控制时效温度和保温时间,避免出现析出相过于粗大或者析出不完全的现象。
通过优化固溶和时效热处理的工艺参数,可以进一步提高触变成形az91d 镁合金的力学性能和抗腐蚀性能。
同时,在热处理过程中应该注意保护镁合金表面不被氧化和腐蚀,以保证其综合性能和使用寿命。
AZ91D镁合金半固态触变成形的数值模拟
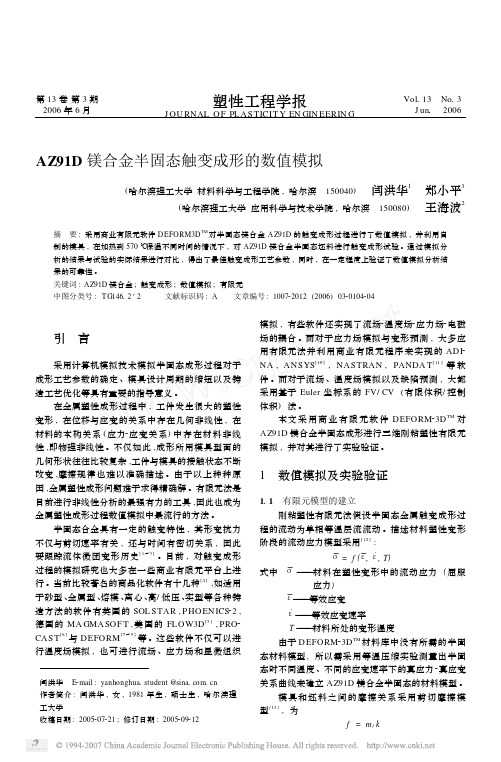
摘 要 : 采用商业有限元软件 D EFORM3DTM 对半固态镁合金 AZ91D 的触变成形过程进行了数值模拟 , 并利用自 制的模具 , 在加热到 570 ℃保温不同时间的情况下 , 对 AZ91D 镁合金半固态坯料进行触变成形试验 。通过模拟分 析的结果与试验的实际结果进行对比 , 得出了最佳触变成形工艺参数 , 同时 , 在一定程度上验证了数值模拟分析结 果的可靠性 。 关键词 : A Z91D 镁合金 ; 触变成形 ; 数值模拟 ; 有限元 中图分类号 : T G1461 2 + 2 文献标识码 : A 文章编号 : 100722012 (2006) 0320104204
106
塑性工程学报
第 13 卷
2 结 论
1) 对 A Z91D 镁合金半固态成形进行了三维刚 粘塑性有限元数值模拟 , 通过试验结果与模拟结果 对比 , 得出充型模拟结果和试验结果基本吻合 。
2) A Z91D 镁合金半固态流动成形在 570 ℃成型 时 , 随着半固态等温时间的增加 , 成形件的组织将 越来越细化 、均匀 , 固相颗粒也会更加球化 , 液相 增加 ; 存在临界成形力和最大成形力随着半固态等 温时间的延长而减小 ; 最佳的半固态等温时间为 30min~45min 。
[ 6 ] Dominique Bouchard ,Jo sée Colbert , Frédéric Pineau. Characterization of co ntact heat t ransfer coefficient s and mat hematical modeling of a semi2solid aluminium die casting. The 8t h S2 P International Conferences , 2004 ,Limassol ,Cyp rus ,2004
半固态触变注射成型镁合金组织性能分析

半固态触变注射成型镁合金组织性能分析半固态挤压注射成型(Semi-Solid Extrusion Injection Molding,简称SSEIM)是一种将半固态合金通过挤压注射成型机进行成型的先进工艺。
在SSEIM过程中,半固态合金的固相含量通常在50%到70%之间,具有较高的流动性和可塑性。
因此,半固态合金在成型过程中能够产生高度复杂的形状,并具有良好的工艺性能和机械性能。
半固态镁合金是一种重要的结构材料,具有低密度、高比强度和良好的热导性能等优点。
然而,由于其熔点低、氧化性强等特性,传统的成型方法难以实现半固态镁合金的高质量制造。
相比之下,SSEIM可以在较低的温度和压力下进行成型,减少了合金的氧化和变质的风险,并且可以实现快速冷却和高强度的组织性能。
在SSEIM过程中,半固态镁合金的组织性能受到多个因素的影响。
首先是合金的成分。
镁合金通常含有铝、锌、锰等合金元素,这些元素能够影响合金的晶体结构和固溶强化效果。
其次是合金的处理工艺。
SSEIM过程中,合金必须通过预热、保温和快速冷却等工艺步骤来控制合金的半固态状态。
这些工艺参数的选择和控制将直接影响合金的晶粒尺寸、形貌和分布。
最后是成型工艺。
SSEIM过程中,合金需要通过挤出和注射两个步骤来实现成型。
这两个步骤中的温度、压力和速度等参数将影响合金的流动性和成型质量。
半固态镁合金的组织性能主要可以通过金相显微镜观察来研究。
通过金相显微镜的断面观察,可以得到合金中晶粒的尺寸、形貌和分布等信息,进而分析合金的晶体结构和固溶强化效果。
此外,通过扫描电子显微镜(SEM)和透射电子显微镜(TEM)的观察,还可以进一步研究合金的细微组织变化和相变情况。
同时,还可以通过显微硬度测试和拉伸测试等力学性能测试来评估合金的力学性能。
在半固态挤压注射成型镁合金的组织性能研究中,需要考虑到合金的成分、处理工艺和成型工艺等因素的综合影响,并结合金相显微镜观察和力学性能测试等手段来全面分析合金的组织性能。
半固态成型镁合金组织与耐腐蚀性能影响
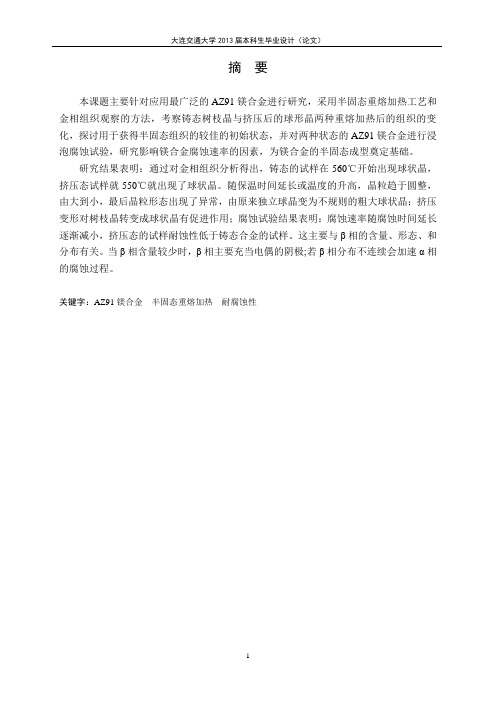
摘要本课题主要针对应用最广泛的AZ91镁合金进行研究,采用半固态重熔加热工艺和金相组织观察的方法,考察铸态树枝晶与挤压后的球形晶两种重熔加热后的组织的变化,探讨用于获得半固态组织的较佳的初始状态,并对两种状态的AZ91镁合金进行浸泡腐蚀试验,研究影响镁合金腐蚀速率的因素,为镁合金的半固态成型奠定基础。
研究结果表明:通过对金相组织分析得出,铸态的试样在560℃开始出现球状晶,挤压态试样就550℃就出现了球状晶。
随保温时间延长或温度的升高,晶粒趋于圆整,由大到小,最后晶粒形态出现了异常,由原来独立球晶变为不规则的粗大球状晶;挤压变形对树枝晶转变成球状晶有促进作用;腐蚀试验结果表明:腐蚀速率随腐蚀时间延长逐渐减小,挤压态的试样耐蚀性低于铸态合金的试样。
这主要与β相的含量、形态、和分布有关。
当β相含量较少时,β相主要充当电偶的阴极;若β相分布不连续会加速α相的腐蚀过程。
关键字:AZ91镁合金半固态重熔加热耐腐蚀性ABSTRACTThe main subject of the study for the most widely used AZ91 magnesium alloy,with Semi-solid remelting heating process and microstructure observation,inspected changes in the organizations investigated cast dendrites and squeeze both spherical crystal remelting heated and explored better initial state for semi-solid structure.AZ91 magnesium alloy of two states for immersion corrosion was tested,studying factors affecting the corrosion rate of magnesium alloys,which laid the foundation for the semi-solid forming of magnesium alloy.The results showed that, spherical crystal was found in the cast of the specimen at 560 ℃while extruded samples at 550 ℃ by analysis of the microstructure.With the holding time or temperature increases, the grain tended rounded, descending,and the last grain morphology appeared abnormal, irregular coarse spherical crystal from the original independent Spherulite ;The organization from dendrite into spherical crystal was promoted by compressional deformation.The corrosion test results showed that: the corrosion rate gradually decreased with the etching time extending, while the specimen corrosion resistance of squeezed state was lower than the cast alloy specimens.This mainly depended on the content of the β phase, morphology and distribution.When β phase content was small, the β phase mainly acte d as a galvanic cathode;The β phase discontinuous distribution would accelerate the corrosion process of the α-phase.Key words: AZ91Magnesium alloy semi-solid remelting heating corrosion resistance目录第一章绪论 (1)1.1课题来源及意义 (1)1.2镁及其合金发展与应用 (1)1.3半固态加工的概念与发展 (3)1.3.1半固态加工的概念 (3)1.3.2半固态加工的发展 (3)1.4半固态金属浆料或坯料的制备 (5)1.4.1机械搅拌法 (5)1.4.2电磁搅拌法 (5)1.4.3应变诱发熔化激活法 (6)1.4.4半固态等温热处理法 (6)1.4.5注射成形 (6)1.5镁合金表面防腐处理 (6)1.6课题的主要内容 (10)第二章试验材料、设备及试验过程 (11)2.1试验材料 (11)2.2试验设备 (11)2.3试验过程 (14)2.3.1等温热处理试验 (14)2.3.2 金相试样制备 (14)2.3.3 金相显微组织观察 (16)2.3.4 镁合金的耐腐蚀性能实验 (16)第三章试验结果讨论与分析 (18)3.1铸态半固态等温处理显微组织 (18)3.2挤压态半固态等温处理显微组织 (21)3.3耐腐蚀性能分析 (25)第四章结论 (27)谢辞 (28)参考文献 (29)第一章绪论1.1课题来源及意义镁合金作为最轻的工程金属材料,被誉为“21世纪的绿色工程材料”。
半固态流变压铸AZ91D镁合金的组织与性能

Ke wor - ma es u a ly;s mis i y e d gn i m l o e - ol d;r e o y;s r c r h ol g tu t e u
镁 合金 作 为 最 轻 的 金属 结 构 材 料 ,具 有 密 度 小 、
1 试 验 方 法
1 1 试 验 材料 .
T cn l y e h oo ,Wua 3 0 4 u e,Ch a g h n4 0 7 ,H b i i ) n
A sr c : T e p o e s so b ia ino e .o i lry a d mirsrcu e a d p o e t so e . oi bt t a h rc s e ff r t f mi l su r n c o tu t r n r p ri f mi l a c o s . d s e s . d s
t e ba r It p at r ft e m a ie. t e Iw ert e S i h e fa to n t e em is i m ir s r c r h r e em er u e o h chn h o h OI p as r c in i h s d - ol d c o tu t e. u
t sl te gt n o g in o h am pes m a e y s en i s r n h a d eln ato ft e s e l d b em is l h - o i r eo- e c s ig pr c s e c gh d di a tn o e sar mu h hi - e h h s o h s m pls mad rt an t o e ft e a e e by mel di s ig. t e ca tn
半固态

半固态触变注射成形技术在Mg合金铸造中的应用前言:近年来,随着对环保等方面要求的提高,镁合金以其质量轻、比强度高、比刚度高、减震性好、耐电磁屏蔽和易回收等特点而从众多金属材料中脱颖而出,广泛应用于航空、航天、电子和汽车等行业。
特别是目前正在用于笔记本电脑和手机壳体的制造,有逐渐取代可回收性较差的塑料壳体的趋势,成为目前研究及应用的热点。
常用的镁合金成形方法主要有压铸、半固态铸造、挤压铸造等,其中压铸法是国内外广泛采用的镁合金成形方法。
但同压铸镁合金产品相比,半固态成形产品的铸造缺陷少,产品的力学性能及表面和内在质量高,此外还有节约能源、安全性好和近净成形性好等优点,因此镁合金的半固态成形受到了广泛的关注。
而镁合金半固态触变注射成形技术是目前半固态铸造技术的最新发展方向半固态浆料的内部特征是固液两相共存,在晶粒边界存在液态金属"半固态浆料主要有以下特点(1) 表观粘度半固态浆料组织特性的客观反映就是表观粘度"研究表明,半固态浆料的表观粘度与固相率密切,随着固相率的增加而增加"当浆料的固相率超过临界值时,粘度值迅速增加"(2)流变性半固态浆料的固相率为50%时,仍具有很好的流动性"这是因为金属液中的固相具有球状或类球状结构,导致半固态浆料的粘度降低"半固态浆料的流变性可分为稳态流变性和非稳态流变性"稳态流变性是指恒温恒剪切速率条件下的流变性,非稳态流变性是指连续冷却或者剪切速率变化条件下的流变性" (3) 触变性半固态金属的触变性是指表观粘度对剪切时间的依赖关系,反映了半固态浆料的依时行为"半固态浆料的表观粘度在一定的剪切速率下,随着时间的延长而逐步下降,具有可逆性"(4) 球状未熔固相颗粒半固态浆料中存在着一定分数的未熔球状或类球状固相颗粒,因此在凝固过程导致收缩减小,偏析减少"可以说正是因为球状未熔固相颗粒的存在,才使半固态浆料具有一系列的独特优点"流变成形是将金属液在从液相向固相的冷却过程中进行强烈搅拌,在一定的固相体积分数下通过压铸或是挤压的方式来成形(一步法);触变成形则是将由搅动设备所制备的半固态铸锭重新加热至半固态进行压铸挤压成形(二步法)。
半固态触变压铸AZ91D镁合金组织与性能的研究的开题报告

半固态触变压铸AZ91D镁合金组织与性能的研究的开题报告一、研究背景与意义随着轻量化技术的迅速发展,轻合金材料在汽车、航空航天、电子等领域得到了广泛应用。
其中,镁合金由于具有轻质、高强、耐腐蚀性好等优点,成为了轻量化领域的热门材料之一。
然而,固化过程中会出现缩孔、热裂等问题,对铸件的完整性和质量产生不利影响。
因此,在解决热处理时产生的问题方面,半固态铸造技术正在成为一种备受关注的技术。
半固态触变压铸技术具有高生产效率、低成本、铸造质量优异等优点,特别适用于生产轻质铸件。
二、研究内容及拟解决的问题本文将以AZ91D镁合金为研究对象,通过半固态触变压铸技术,控制材料的变形、温度等工艺参数,以期获得高强度、高塑性、低收缩率的铸件。
同时,本文还将研究半固态铸造过程中的组织演变规律、力学性能和断口形貌等问题,并进一步分析半固态触变压铸AZ91D镁合金的可行性和其未来的应用前景。
三、研究方法本文将采用实验方法,首先将AZ91D镁合金加热到固态和半固态状态,并通过触变压铸的方式制备铸件。
然后,分别进行金相、显微组织分析、力学性能测试和断口形貌分析,并将结果与常规铸造方式(如重力铸造、低压铸造等)进行对比分析。
最后,结合实验结果,探讨半固态触变压铸AZ91D镁合金的优缺点和未来的应用前景。
四、研究计划及预期成果本文的研究计划分为三个阶段。
第一阶段:通过材料选用和实验设计,确定半固态触变压铸工艺参数和试验方案。
第二阶段:采用实验与分析相结合的方法,研究半固态触变压铸AZ91D镁合金的组织演变规律和力学性能,并分析其断口形貌。
第三阶段:总结实验结果,探讨半固态触变压铸AZ91D镁合金的优缺点和应用前景。
预期成果为:对半固态触变压铸AZ91D镁合金进行深入探究,为轻量化材料的研究提供新的思路和方法,并为优化半固态铸造工艺提供理论和实验依据。
Mg-6Zn-xZr镁合金半固态组织及性能研究的开题报告

Mg-6Zn-xZr镁合金半固态组织及性能研究的开题报告题目:Mg-6Zn-xZr镁合金半固态组织及性能研究1. 研究背景镁合金是一种性能优异的轻质材料,具有高比强度、高比刚度和耐腐蚀性等优点,被广泛应用于航空、汽车、电子等领域。
但是,镁合金的应用受到其低的塑性和焊接性能的限制,这是由于其晶粒尺寸和形状的限制造成的。
半固态成形技术是一种有效的工艺手段,可以通过控制热处理参数和加工压力,获得精细、均匀的组织,提高镁合金的塑性和焊接性能。
Mg-6Zn合金是一种具有良好综合性能的镁合金,但其在半固态成形过程中的变形行为和组织演化规律尚不清楚。
Zr元素是常用的微合金化元素,具有强化晶界和提高塑性的作用。
因此,研究Mg-6Zn-xZr镁合金半固态组织及性能,对于扩大镁合金的应用范围、提高其性能具有重要的意义。
2. 研究目的本研究旨在探究Mg-6Zn-xZr镁合金在半固态成形过程中的变形行为和组织演化规律,分析添加Zr元素对其力学性能的影响,并对其应用前景进行初步探讨。
3. 研究内容3.1 Mg-6Zn-xZr镁合金的制备采用真空熔炼和等体积法制备Mg-6Zn-xZr合金。
3.2 半固态成形工艺的制备通过调节热处理参数和加工压力等参数,制备出不同形貌和尺寸的半固态合金试样。
3.3 材料组织和性能的表征使用金相显微镜、扫描电镜、X射线衍射仪、拉伸试验机等仪器对半固态试样的组织和力学性能进行分析和表征。
4. 预期成果本研究预计获得以下成果:4.1 掌握Mg-6Zn-xZr镁合金的制备方法和半固态成形工艺;4.2 研究Mg-6Zn-xZr镁合金在半固态成形过程中的变形行为和组织演化规律;4.3 分析不同Zr含量对Mg-6Zn合金力学性能的影响;4.4 探讨Mg-6Zn-xZr镁合金的应用前景。
5. 研究意义本研究的意义在于探索Mg-6Zn-xZr镁合金半固态成形技术的应用,扩大镁合金的应用范围,提高其力学性能和焊接性能,进一步推动轻质材料的研究和应用。
半固态触变注射成型镁合金

半固态触变注射成型镁合金内容摘要:摘要:本文对半固态触变注射成型镁合金AZ91D 的组织与性能进行了分析,结果表明,该成形法所生产的镁合金产品的组织及力学性能均优于压铸产品,从而为应用半固态触变注射成型法进行镁合金汽车零部件的生产奠定基础。
关键词:触变注射成型镁合金组织力学性能1 引言近年来,随着对绿色、环保等方面要求的提高,镁合金以其重量轻、比强度高、比刚度高、减震性好、耐电磁屏蔽、易回收等特点从众多金属材料中脱颖而出,广泛的应用于航空、航天、电子和汽车等行业。
目前,镁合金应用的两大热点产业是电子业和汽车业。
另一方面,作为实际应用中最轻的结构金属,镁合金能够满足交通运输业日益严格的节能和尾气排放要求,从而生产出重量轻、耗油少、环保的新一代交通工具。
摘要:本文对半固态触变注射成型镁合金AZ91D 的组织与性能进行了分析,结果表明,该成形法所生产的镁合金产品的组织及力学性能均优于压铸产品,从而为应用半固态触变注射成型法进行镁合金汽车零部件的生产奠定基础。
关键词:触变注射成型镁合金组织力学性能1 引言近年来,随着对绿色、环保等方面要求的提高,镁合金以其重量轻、比强度高、比刚度高、减震性好、耐电磁屏蔽、易回收等特点从众多金属材料中脱颖而出,广泛的应用于航空、航天、电子和汽车等行业。
目前,镁合金应用的两大热点产业是电子业和汽车业。
一方面,用于“3C” (Computer、Communication、Con sumption Electronics Products)产品的壳体,有逐渐取代可回收性较差的塑料壳体的趋势;另一方面,作为实际应用中最轻的结构金属,镁合金能够满足交通运输业日益严格的节能和尾气排放要求,从而生产出重量轻、耗油少、环保的新一代交通工具。
国内外广泛采用的镁合金成形方法为压铸法。
压铸镁合金产品具有尺寸稳定性好、生产率高等优点,但也具有夹杂多、气孔多、成形后难热处理、尺寸近净成形差等不足。
Mg-Zn-Al新型镁合金开发及半固态触变成形的开题报告
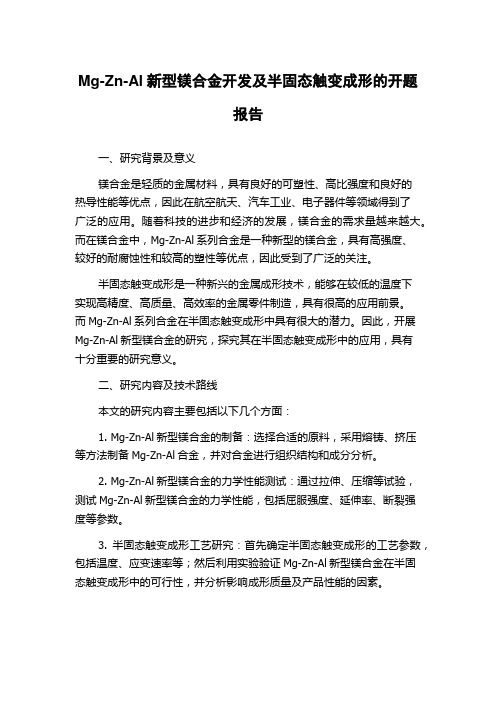
Mg-Zn-Al新型镁合金开发及半固态触变成形的开题报告一、研究背景及意义镁合金是轻质的金属材料,具有良好的可塑性、高比强度和良好的热导性能等优点,因此在航空航天、汽车工业、电子器件等领域得到了广泛的应用。
随着科技的进步和经济的发展,镁合金的需求量越来越大。
而在镁合金中,Mg-Zn-Al系列合金是一种新型的镁合金,具有高强度、较好的耐腐蚀性和较高的塑性等优点,因此受到了广泛的关注。
半固态触变成形是一种新兴的金属成形技术,能够在较低的温度下实现高精度、高质量、高效率的金属零件制造,具有很高的应用前景。
而Mg-Zn-Al系列合金在半固态触变成形中具有很大的潜力。
因此,开展Mg-Zn-Al新型镁合金的研究,探究其在半固态触变成形中的应用,具有十分重要的研究意义。
二、研究内容及技术路线本文的研究内容主要包括以下几个方面:1. Mg-Zn-Al新型镁合金的制备:选择合适的原料,采用熔铸、挤压等方法制备Mg-Zn-Al合金,并对合金进行组织结构和成分分析。
2. Mg-Zn-Al新型镁合金的力学性能测试:通过拉伸、压缩等试验,测试Mg-Zn-Al新型镁合金的力学性能,包括屈服强度、延伸率、断裂强度等参数。
3. 半固态触变成形工艺研究:首先确定半固态触变成形的工艺参数,包括温度、应变速率等;然后利用实验验证Mg-Zn-Al新型镁合金在半固态触变成形中的可行性,并分析影响成形质量及产品性能的因素。
4. 复合成形技术研究:将半固态触变成形技术与其他成形技术结合,如注射成形技术、挤压成形技术等,形成多种复合成形技术,并对其进行比较分析。
技术路线如下:三、预期研究成果1. 成功制备出Mg-Zn-Al新型镁合金,并对其组织结构和成分进行了分析。
2. 测试出Mg-Zn-Al新型镁合金在拉伸、压缩等试验中的力学性能。
3. 确定了Mg-Zn-Al新型镁合金在半固态触变成形中的工艺参数,并对其成形性能进行了分析。
4. 研究出了Mg-Zn-Al新型镁合金的多种复合成形技术,并进行了比较分析。
镁合金半固态注射成型技术
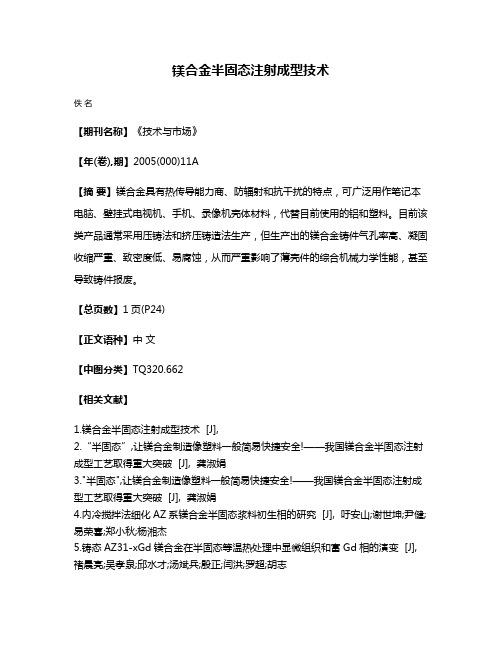
镁合金半固态注射成型技术
佚名
【期刊名称】《技术与市场》
【年(卷),期】2005(000)11A
【摘要】镁合金具有热传导能力商、防辐射和抗干扰的特点,可广泛用作笔记本电脑、壁挂式电视机、手机、录像机壳体材料,代替目前使用的铝和塑料。
目前该类产品通常采用压铸法和挤压铸造法生产,但生产出的镁合金铸件气孔率高、凝固收缩严重、致密度低、易腐蚀,从而严重影响了薄壳件的综合机械力学性能,甚至导致铸件报废。
【总页数】1页(P24)
【正文语种】中文
【中图分类】TQ320.662
【相关文献】
1.镁合金半固态注射成型技术 [J],
2.“半固态”,让镁合金制造像塑料一般简易快捷安全!——我国镁合金半固态注射成型工艺取得重大突破 [J], 龚淑娟
3."半固态",让镁合金制造像塑料一般简易快捷安全!——我国镁合金半固态注射成型工艺取得重大突破 [J], 龚淑娟
4.内冷搅拌法细化AZ系镁合金半固态浆料初生相的研究 [J], 吁安山;谢世坤;尹健;易荣喜;郑小秋;杨湘杰
5.铸态AZ31-xGd镁合金在半固态等温热处理中显微组织和富Gd相的演变 [J], 褚晨亮;吴孝泉;邱水才;汤斌兵;殷正;闫洪;罗超;胡志
因版权原因,仅展示原文概要,查看原文内容请购买。
- 1、下载文档前请自行甄别文档内容的完整性,平台不提供额外的编辑、内容补充、找答案等附加服务。
- 2、"仅部分预览"的文档,不可在线预览部分如存在完整性等问题,可反馈申请退款(可完整预览的文档不适用该条件!)。
- 3、如文档侵犯您的权益,请联系客服反馈,我们会尽快为您处理(人工客服工作时间:9:00-18:30)。
半固态触变注射成型镁
合金组织性能分析
HUA system office room 【HUA16H-TTMS2A-HUAS8Q8-HUAH1688】
半固态触变注射成型镁合金组织性能分析
摘要:本文对半固态触变注射成型镁合金AZ91D 的组织与性能进行了分析,结果表明,该成形法所生产的镁合金产品的组织及力学性能均优于压铸产品,从而为应用半固态触变注射成型法进行镁合金汽车零部件的生产奠定基础。
关键词:触变注射成型镁合金组织力学性能
1 引言
近年来,随着对绿色、环保等方面要求的提高,镁合金以其重量轻、比强度高、比刚度高、减震性好、耐电磁屏蔽、易回收等特点从众多金属材料中脱颖而出,广泛的应用于航空、航天、电子和汽车等行业。
目前,镁合金应用的两大热点产业是电子业和汽车业。
一方面,用于“3C” (Computer、Communication、Consumption Electronics Products)产品的壳体,有逐渐取代可回收性较差的塑料壳体的趋势;另一方面,作为实际应用中最轻的结构金属,镁合金能够满足交通运输业日益严格的节能和尾气排放要求,从而生产出重量轻、耗油少、环保的新一代交通工具。
国内外广泛采用的镁合金成形方法为压铸法。
压铸镁合金产品具有尺寸稳定性好、生产率高等优点,但也具有夹杂多、气孔多、成形后难热处理、尺寸近净成形差等不足。
采用压铸法制造的零件很难满足诸如用于“ 3C”产品中所广泛使用的薄壁壳体类零件以及用于汽车工业中的高性能镁合金零部件的要求。
同压铸法相比,半固态方法制造的产品具有铸造缺陷少,产品的力学性能、尺寸精度、表面和内在质量高等优点,此外还有节约能源、安全性好、近净成形性好等优点。
目前世界上已经成功工业化的镁合金半固态成型技术是触变注射成型技术[1]。
长春华禹镁业有限公司是我国最早引进此项技术的厂家,本文利用该公司的触变注射成型机制备试样,对触变注射成型镁合金的组织及力学性能进行了分析,从而为公司下一步进行汽车用高性能镁合金的研究开发作适当的技术储备。
2 半固态触变注射成型技术的原理及工艺过程
2.1 半固态触变注射成型技术的原理
在普通铸造过程中,初晶以枝晶方式长大,当固相率达到0.2 左右时,枝晶就形成连续网络骨架,失去宏观流动性。
半固态成形是在液态金属从液相到固相冷却过程中进行强烈搅拌,使普通铸造成形时易于形成的树枝晶网络骨架被打碎而保留分散的颗粒状组织形态,悬浮于剩余液相中。
这种颗粒状非枝晶的显微组织,在固相率达0.5~0.6 时仍具有一定的流变性,从而可利用常规的成形工艺如压铸、挤压,模锻等实现金属的成形[2~4]。
半固态触变注射成形法是近些年来开发的一种新工艺,源于美国DOW化学公司,美国THI XOMAT公司将其商业化。
该工艺是将塑料的注塑成形原理与半固态金属成形工艺相结合,集半固态金属浆料的制备、输送、成形等过程于一体,该法较好地解决了半固态金属浆料的保存输送、成形控制困难等问题。
2.2 半固态触变注射成型技术的工艺过程
注射成形法主要工艺过程如下:被制成颗粒的镁合金原料(由枝晶镁合金铸锭制成,其组织仍为枝晶组织)从料斗中加入;在套筒中的镁合金原料通过电加热转变成半固体状态,在螺杆的剪切作用下,在套筒中半固体金属浆料形成了近乎于球形状的固体颗粒,在注射缸的作用下,以相当于塑料注塑机的十倍速率压射到模具内成形。
触变注射成形机的基本结构如图1-1 所示。
图1 触变注射成形机原理图
3 试验设备及方法
3.1 触变注射成形试样的制备
本论文采用日本制钢所的JLM-450MG 型触变注射成型机制备了标准力学性能试样,在不同制备条件下,考察了目前最广泛使用的镁合金AZ91D 组织与性能的变化以及耐腐蚀性能。
该成型机的外观如图2 所示,试样模具由日本制钢所提供,所制备的测试试样如图3所示,成形过程中模具温度为180℃。
图3 中由左至右依次为标准冲击试样,标准蠕变试样,标准拉伸试样和硬度试样,在论文只采用标准拉伸试样进行试验,分别考察不同工艺条件下,半固态镁合金组织与性能的变化。
图2 JLM 450-MG 触变成型机图3 注射成型的半固态镁合金试样
快速腐蚀条件如下:腐蚀介质为0.5%NaCl 或0.1molNaCl 溶液;试验温度:室温(静态)或35±1℃;腐蚀时间:5 昼夜。
4 结果与讨论
4.1 半固态触变注射成型镁合金的组织分析
图4 中组织是取自不同工艺参数制备标准拉伸试棒的中部,其工艺参数的区别主要表现在料筒温度的差别,在图4 中由工艺(a)至工艺(d)料筒温度逐步升高。
图4 触变注射成型AZ91D 组织
由图4 可见,在不同工艺参数条件下,半固态镁合金组织的变化不大,主要差别表现在缺陷的数量和大小方面。
可见,料筒温度对半固态镁合金成型性具有决定性的影响,在料筒温度较低的条件下,半固态浆料的流变性不足,成型性能不足,提高料筒温度可以明显的提高半固态浆料的流变性能,但会明显降低固相率,在工艺d 的条件下,除晶粒细小
外,其组织已经接近普通压铸合金组织。
因此,在实际产品制备中必须控制好料筒温度和组织这两方面的因素,才有可能获得高质量的产品。
图5 为半固态镁合金组织的扫描电镜照片。
由图5a 可见,半固态镁合金试棒的组织细小、均匀,图5b 为放大的晶界相,对晶界相的定点能谱分析表明,其晶界相的主要组成为Mg 和Al,并含有少量的Zn,其定点能谱分析结果如图6 所示。
对半固态镁合金进行线扫描的结果表明,Al 和Zn 主要分布在晶界上,在晶内分布较少,Mg 则主要分布在晶内,在晶界处Mg 含量明显减少,如图7 所示。
以上结果表明半固态触变注射成型镁合金的组织形态及分布基本与压铸组织相同。
(a) 半固态镁合金组织 (b) 半固态镁合金的晶界相
图5 半固态镁合金组织的扫描电镜照片
图6 半固态镁合金晶界相分析
图7 半固态镁合金线扫描结果
4.2 半固态触变注射成型AZ91D 的力学性能分析
4.2.1 触变注射成型AZ91D 的力学性能
图8 中示出了50 根试棒(图4 工艺d 条件下)中随机抽取5 根试棒的力-位移曲线、力-变形曲线以及力学性能的测量数据。
由此可见,半固态触变注射成形试棒已达到了很高的强度,其平均断裂强度可达到270MPa 以上,平均屈服强度可达150MPa 左右(由于镁合金试棒在拉伸过程中没有明显的屈服点,故而以σp0.2 估算屈服强度)。
图8 半固态镁合金的力学性能[6]
4.2.2 盐水快速腐蚀对触变注射成型AZ91D 性能的影响
镁合金的抗腐蚀性能是衡量镁合金性能的一个重要指标,本文采用快速腐蚀试验考察了经快速腐蚀后触变成型镁合金试棒组织与性能的变化。
所采用试棒与前述力学性能试棒相同。
图9 示出了经5 昼夜快速腐蚀后AZ91D 镁合金试棒的力学性能。
可见,腐蚀后镁合金试棒力学性能明显下降,平均断裂强度下降到220MP 左右,屈服强度下降至120MPa 左右。
腐蚀试验结果表明,尽管半固态组织细小、致密,但是其抗腐蚀性能仍然相当差,做为重要结构部件和装饰性壳体类零部件时,仍须采用适当的表面处理工艺,否则将无法满足使用要求。
图9 快速腐蚀后触变注射成型AZ91D 的力学性能[6]
5 结论
近年来,世界各国高度重视镁合金的研究与开发,将镁资源作为21 世纪的重要战略物资,加强了镁合金在汽车、计算机、通讯及航空航天领域的应用开发研究。
美、日、欧等发达国家目前已经投入大量人力和物力,实施多项大型联合研究发展计划,研究汽车用镁
合金零部件,这些研究开发计划加快了国外应用镁合金零部件的步伐。
我国是一个摩托车生产、消费大国和出口大国,也是一个潜在的汽车生产和消费大国。
然而,目前我国的镁合金成型技术还相对落后,镁合金零部件的力学性能及耐腐蚀性能较低是制约汽车用镁合金零部件在我国应用的一个重要因素。
本论文通过对触变注射成型AZ91D 镁合金试棒的显微组织、力学性能分析和快速腐蚀试验,得出如下结论:应用触变注射成型技术可得到组织细小、致密,力学性能相对较高的镁合金部件。
其综合力学性能优于目前广泛采用的压铸镁合金部件。
但是应该看到,触变注射成型设备的高昂费用及所必须支付的专利许可费用,加之成型用原材料——镁粒的成本较高,整体投资比较大。
因而该技术尤其适用于那些具有较高要求和高附加值产品的加工。