7.63m焦炉炉体结构
7.63m焦炉的环保设施及运行分析

7.63m焦炉的环保设施及运行分析王洪兴李守成马卫华(山西太钢不锈钢股份有限公司焦化厂,太原030003)焦炉在炼焦过程中所产生的大量烟尘和有害气体严重污染了环境。
20世纪70年代以来,这种状况逐渐被人们重视,国内外专家在焦炉污染物控制方面做了大量的研究和试验工作,很多方法已经得到了实际应用。
太钢7. 63m焦炉是国内首次从德国引进的,也是目前中国炭化室高度最高、单孔炭化室容积最大的焦炉,具有全球先进的炼焦工艺技术,其独特的工艺技术和装备设施确保其优秀的环保优势。
1 装煤过程的消烟除尘7. 63m焦炉的装煤采用PROven (Pressure Regulated Oven System)技术,即炭化室压力调节系统,主要由固定杯、皇冠管、密封锥型体、连杆、气缸、定位器和压缩空气控制系统等构成,如图1所示。
PROven系统取代了国内常规焦炉的桥管阀体,通过气动机构调节固定杯内的液位,可以完成导通上升管与集气管、切断上升管与集气管和调节上升管流向集气管的荒煤气量等工作。
由于集气管在负压(-300Pa) 状态下操作,在装煤过程中产生的吸力可以满足消烟除尘的要求。
装煤时,PROven系统将集气管与上升管连通,由于集气管采用负压操作,使炭化室产生负压,可以确保装煤操作过程无烟尘和煤气溢散。
在装煤过程中,PROven系统的快速冲洗管关闭,密封锥型体提起,使固定杯出口打开,荒煤气可以无干扰地通过PROven装置进入集气管,各部件的状态见图2。
图1 PROven系统结构示意图图2 PROven系统处理装煤气流操作状态2 推焦时的防尘措施(1)焦炉机侧摘门、推焦、平煤、尾焦、清门和清框产生的烟尘由推焦机车载除尘器收集。
在推焦、平煤作业时,推焦车上的旋转烟罩已经打开,可以收集摘门、推焦、清框、尾焦、平煤产生的烟尘,在清门机顶部专门的导烟罩可以收集清门过程产生的烟尘。
(2)焦炉焦侧摘门、导焦、尾焦、清门和清框产生的烟尘由地面除尘站方式收集。
7.63米焦炉调火汇编(一)
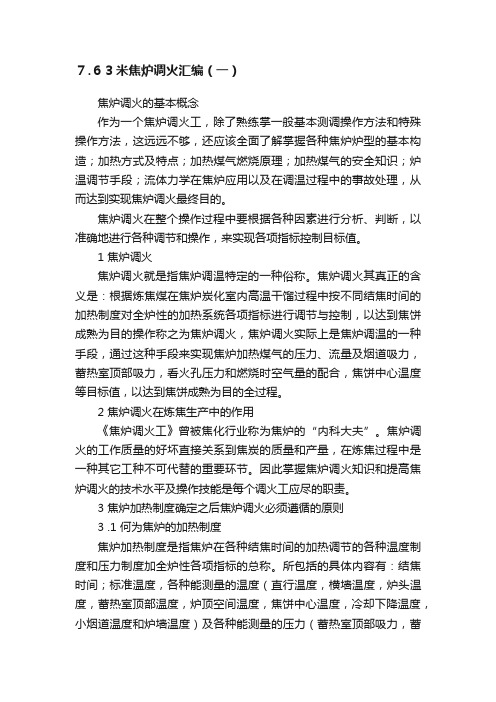
7.63米焦炉调火汇编(一)焦炉调火的基本概念作为一个焦炉调火工,除了熟练掌一般基本测调操作方法和特殊操作方法,这远远不够,还应该全面了解掌握各种焦炉炉型的基本构造;加热方式及特点;加热煤气燃烧原理;加热煤气的安全知识;炉温调节手段;流体力学在焦炉应用以及在调温过程中的事故处理,从而达到实现焦炉调火最终目的。
焦炉调火在整个操作过程中要根据各种因素进行分析、判断,以准确地进行各种调节和操作,来实现各项指标控制目标值。
1 焦炉调火焦炉调火就是指焦炉调温特定的一种俗称。
焦炉调火其真正的含义是:根据炼焦煤在焦炉炭化室内高温干馏过程中按不同结焦时间的加热制度对全炉性的加热系统各项指标进行调节与控制,以达到焦饼成熟为目的操作称之为焦炉调火,焦炉调火实际上是焦炉调温的一种手段,通过这种手段来实现焦炉加热煤气的压力、流量及烟道吸力,蓄热室顶部吸力,看火孔压力和燃烧时空气量的配合,焦饼中心温度等目标值,以达到焦饼成熟为目的全过程。
2 焦炉调火在炼焦生产中的作用《焦炉调火工》曾被焦化行业称为焦炉的“内科大夫”。
焦炉调火的工作质量的好坏直接关系到焦炭的质量和产量,在炼焦过程中是一种其它工种不可代替的重要环节。
因此掌握焦炉调火知识和提高焦炉调火的技术水平及操作技能是每个调火工应尽的职责。
3 焦炉加热制度确定之后焦炉调火必须遵循的原则3 .1 何为焦炉的加热制度焦炉加热制度是指焦炉在各种结焦时间的加热调节的各种温度制度和压力制度加全炉性各项指标的总称。
所包括的具体内容有:结焦时间;标准温度,各种能测量的温度(直行温度,横墙温度,炉头温度,蓄热室顶部温度,炉顶空间温度,焦饼中心温度,冷却下降温度,小烟道温度和炉墙温度)及各种能测量的压力(蓄热室顶部吸力,蓄热室阻力,看火孔压力,炭化室底部压力,燃烧系统五点压力)以及全炉的机、焦侧煤气流量和支管压力、横管压力、孔板直径、进行风门开度的尺寸和空气过剩系数a值等。
3.2 温度制度确定后要遵循的原则温度制度是加热制度的一部分,是指在规定的结焦时间内保证焦饼成熟的主要温度指标的控制值,这个主要温度指标就是指焦炉燃烧室机、焦侧火道平均温度的控制值,也称为标准温度。
7.63m焦炉格子砖施工技术

7.63m焦炉格子砖施工技术摘要:XX焦化公司2×60孔7.63m焦炉,是国内首家最早从德国引进的新型炉型,并且所有工艺设备都是从德国原装引进。
和国内传统炉型相比,该焦炉设计满足焦炉煤气和高炉煤气均可燃烧的要求,蓄热室结构复杂,分格蓄热,砖号多,胀缝多,施工难度大。
本文全面、系统阐述7.63m焦炉蓄热室格子砖施工作业技术措施。
关键词:格子砖隔墙膨胀缝1 工程概况XX焦化焦炉改造是由中冶焦耐工程技术有限公司设计的2×60孔7.63米大型焦炉改造项目。
该焦炉为双联火道、分段加热、废气循环、焦炉煤气下喷、空气侧入,蓄热室分格的超大型焦炉,满足了当前国家发展所倡导的节能环保发展理念。
该焦炉炉体全长103.5m,宽18.56m,共用异型耐火砖号1065个,标型耐火砖号37个,耐材总量达25751.8吨。
其中蓄热室部位粘土质格子砖1500余吨,半硅质格子砖1000余吨。
2 蓄热室结构特点顾名思义,该部位为空气与煤气在进入燃烧室燃烧前进行预热升温的场所。
由于空气与煤气属于外来介质,温度低,通过预热可以提升进入燃烧室空气的温度,避免燃烧室温度降低,同时可以减少烟气的热损失,提高热效率。
蓄热室分为煤气道和空气道,内部有17道小隔墙,被划分为18个小单元蓄热室。
每个立火道对应两格蓄热室,构成一个加热单元。
为了保证气密性,烘炉过程中有相同的膨胀变化,蓄热室隔墙砖材质跟随主单墙高度变化相同,其中13-21层纵横隔墙均用半硅砖,22-32层横向隔墙采用硅砖,纵向隔墙采用粘土砖。
为了达到良好的蓄热换热效果,格子砖设计从下到上分为粘土砖(AW)、半硅砖(E65)、粘土砖(KA40)三种材质,共18个砖号,总砖量达到429536块,总重量达到2570.7吨。
3 施工难点及重点传统国内焦炉蓄热室无隔墙砌筑,无胀缝留设,格子砖材质单一、型号单一的特点。
而该焦炉具有以下特点:1、该焦炉蓄热室采用分隔式,煤气蓄热室设计有横向隔墙,空气蓄热室更是设计有纵横隔墙,并且在隔墙与主单墙接触位置留有膨胀缝,其中砼基础顶板胀缝对应位置处的蓄热室隔墙胀缝与其他蓄热室胀缝所使用填充物有所不同;2、该焦炉格子砖拥有3种材质,18个砖号,并且存在部分利旧格子砖使用情况,容易造成材质、砖号的混淆;3、该焦炉炉体宽度达到18.56m,蓄热室长,单孔煤气蓄热室和空气蓄热室所使用格子砖总块数均达到3464块,大约为17个托盘砖量。
7.63m焦炉炉体结构
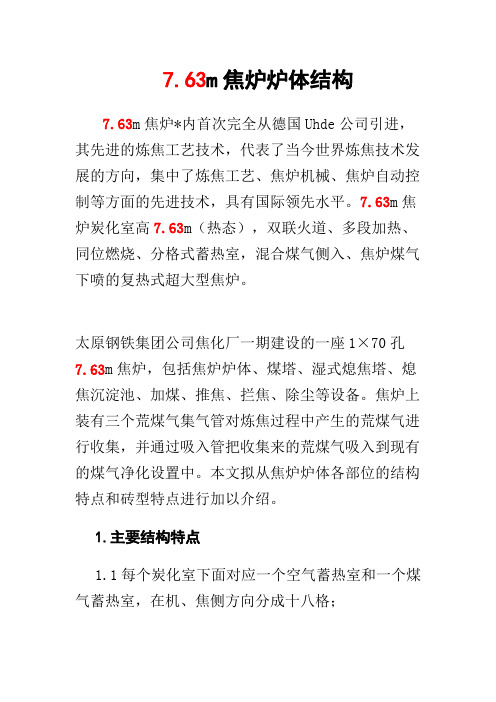
7.63m焦炉炉体结构7.63m焦炉*内首次完全从德国Uhde公司引进,其先进的炼焦工艺技术,代表了当今世界炼焦技术发展的方向,集中了炼焦工艺、焦炉机械、焦炉自动控制等方面的先进技术,具有国际领先水平。
7.63m焦炉炭化室高7.63m(热态),双联火道、多段加热、同位燃烧、分格式蓄热室,混合煤气侧入、焦炉煤气下喷的复热式超大型焦炉。
太原钢铁集团公司焦化厂一期建设的一座1×70孔7.63m焦炉,包括焦炉炉体、煤塔、湿式熄焦塔、熄焦沉淀池、加煤、推焦、拦焦、除尘等设备。
焦炉上装有三个荒煤气集气管对炼焦过程中产生的荒煤气进行收集,并通过吸入管把收集来的荒煤气吸入到现有的煤气净化设置中。
本文拟从焦炉炉体各部位的结构特点和砖型特点进行加以介绍。
1.主要结构特点1.1每个炭化室下面对应一个空气蓄热室和一个煤气蓄热室,在机、焦侧方向分成十八格;1.2分段加热使斜道结构复杂,砖型多。
通道内无胀缝使斜道严密,防止斜道区上部高温事故的产生;1.3燃烧室由36个共18对双联火道组成,同位燃烧,三段加热结构。
在每对火道隔墙间下部设循环孔,将下降火道的废气吸入上升火道的可燃气体中,用此两种方式拉长火焰,达到高向加热均匀的目的;1.4蓄热室无中心隔墙,仅在焦侧设置烟道,由于3段燃烧加热和废气循环,煤气燃烧充分,炉体高向加热均匀,废气中氮氧化物含量低≤500mg/Nm3,达到国家环保标准控制要求;1.5炉体材质全按照德国DIN标准,多达19种,全炉共设置六次满铺滑动层。
蓄热室机、焦侧方向分成十八格,煤气蓄热室与空气蓄热室相间配置,其下部配备两个与其相同的水平烟道,每个水平烟道又通过格子砖支撑墙沿炭化室长度方向分成两格,作为供空气、混合煤气、排废气用,水平烟道不设置衬砖。
因而要求互相之间严密不串漏,因水平烟道存在着气体交换,温度变化,而蓄热室下部温度较低,整个蓄热室下部(1-21层)采用耐急冷急热的半硅砖(E65)砌筑,上部使用硅砖(SI-KN),接缝位置设置滑动层。
7.63米大型焦炉技术文档_一章节

第一节现代焦炉整体结构 (2)1.1、焦炉炉型的分类 (2)1.2、现代焦炉的结构: (2)1.2.1 炭化室 (3)1.2.2 燃烧室 (4)1.2.3 斜道区 (5)1.2.4 蓄热室 (5)1.2.5 小烟道 (6)1.2.6 炉顶区 (6)1.2.7 分烟道、总烟道、烟囱、焦炉基础平台 (6)第二节炼焦炉的机械与设备 (7)2.1 护炉铁件 (7)2.1.1 护炉设备的作用 (7)2.1.2 保护板 (8)2.1.3弹簧 (9)2.1.4 炉柱 (10)2.1.5横拉条 (10)2.1.6 纵拉条 (10)2.1.7 炉门与炉门框 (11)2.2 焦炉加热设备 (12)2.2.1 煤气预热器 (12)2.2.2 交换设备 (13)2.2.3 废气盘 (13)2.3荒煤气导出设备 (14)2.3.1 高压氮水及水封上升管盖装置 (15)2.3.2 上升管和桥管 (16)2.3.3 集气管和吸气管 (16)2.4焦炉机械 (18)2.4.1 装煤车 (19)2.4.2 拦焦车 (19)2.4.3 推焦机 (19)2.4.4 熄焦车和电机车 (20)2.5 附属设备和修理装置 (21)2.5.1 炉门修理站 (21)2.5.2 余煤单斗机和埋刮板提升机 (21)2.5.3 悬臂式起重机和电动葫芦 (21)2.5.4推焦杆更换装置 (21)2.5.5砂轮机及排水泵 (21)第一节现代焦炉整体结构1.1、焦炉炉型的分类现代焦炉因火道结构,加热煤气种类及其入炉方式,实现高向加热均匀性的方法不同等分成许多型式。
因火道结构形式的不同,焦炉可分为二分式焦炉,双联火道焦炉及少数的过顶式焦炉。
根据加热煤气种类的不同,焦炉可分为单热式焦炉和复热式焦炉。
根据煤气入炉的方式不同,焦炉可分为下喷式焦炉和侧入式焦炉。
1.2、现代焦炉的结构:(一)、现代焦炉虽有多种炉型,但都有共同的基本要求:1)焦并长向和高向加热均匀,加热水平适当,以减轻化学产品的裂解损失。
7.63米焦炉上升管气控箱结构说明(工程师培训)
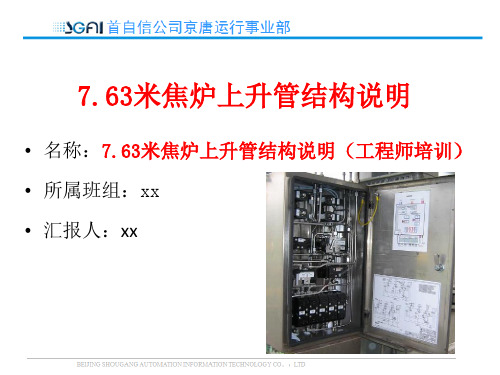
• 名称:7.63米焦炉上升管结构说明(工程师培训) • 所属班组:xx • 汇报人:xx
2*2*1.5 ZRDJYVP
11 +
12-
83 +
84-
2*1.5 ZR-
DJYVP
1+ 2-
设备自带 10米线
上升 上升 管盖 管盖
4*1.5 ZR-KFFP
AI
DI
DO
1 2 3 4 5 6 7 8 9 10 11 12 13 14 15 16 17 18 19 20 21 22 23 24 25 26 27 28 29 30
DCS压 力调节
AO
DCS活 塞杆位 置反馈
AI
10*1.5 ZR-KFFP
10*1.5 ZR-KFFP
10*1.5 ZR-KFFP
5OPห้องสมุดไป่ตู้21106
54-70#
48-70#
5OPR21107
注意:2AI和AO同用10X1.5的线缆,因AI部分点不在同一柜内,因此接线应注意 此线部分需分开接至不同柜内
201x年x月于xx班
10X1.5mm²
10X1.5mm² 10X1.5mm²
2AI
AO
4DO
4DI
柜子号
1-6#
1-23#
1-23#
5OPR21102
7-23#
1-23#
5OPR21103
24-29# 24-47#
24-47#
5OPR21104
30-47#
24-47#
5OPR21105
48-53# 48-70#
48-70#
设备已接好 设备已接好
7.63米大型焦炉技术文档_三章节
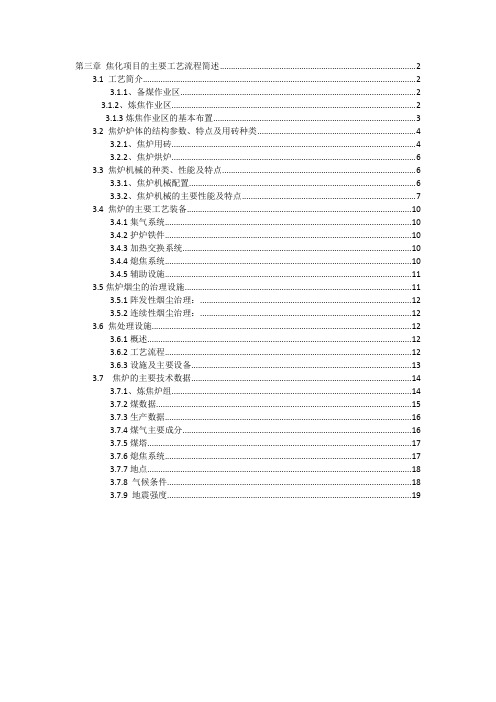
第三章焦化项目的主要工艺流程简述 (2)3.1 工艺简介 (2)3.1.1、备煤作业区 (2)3.1.2、炼焦作业区 (2)3.1.3炼焦作业区的基本布置 (3)3.2 焦炉炉体的结构参数、特点及用砖种类 (4)3.2.1、焦炉用砖 (4)3.2.2、焦炉烘炉 (5)3.3 焦炉机械的种类、性能及特点 (6)3.3.1、焦炉机械配置 (6)3.3.2、焦炉机械的主要性能及特点 (6)3.4 焦炉的主要工艺装备 (9)3.4.1集气系统 (9)3.4.2护炉铁件 (9)3.4.3加热交换系统 (9)3.4.4熄焦系统 (10)3.4.5辅助设施 (10)3.5焦炉烟尘的治理设施 (10)3.5.1阵发性烟尘治理: (11)3.5.2连续性烟尘治理: (11)3.6 焦处理设施 (11)3.6.1概述 (11)3.6.2工艺流程 (12)3.6.3设施及主要设备 (12)3.7 焦炉的主要技术数据 (14)3.7.1、炼焦炉组 (14)3.7.2煤数据 (15)3.7.3生产数据 (15)3.7.4煤气主要成分 (16)3.7.5煤塔 (16)3.7.6熄焦系统 (16)3.7.7地点 (17)3.7.8 气候条件 (17)3.7.9 地震强度 (18)第三章焦化项目的主要工艺流程简述3.1 工艺简介3.1.1备煤作业区备煤作业区采用带预粉碎的先配煤后分组粉碎的工艺流程。
贮煤场来的原料煤经预粉碎后送至配煤室配煤,再运至粉碎机室分组粉碎后送混合站混合均匀,最后通过通廊及转运站由带式输送机输送至贮煤塔,准备入焦炉。
3.1.2炼焦作业区贮煤塔中的配合煤经计量后由装煤车装入焦炉炭化室中。
焦炉在煤气加热条件下对煤进行干馏,炭化室中的煤干馏成焦后由推焦机推出。
装煤采用先进的系统,以控制、调节每个炭化室压力,实现无烟装煤;出焦产生的烟尘通过拦焦机上的集气罩收集起来,经集尘管道送至焦炉出焦除尘地面站除尘。
熄焦主要采用干法熄焦(由首钢院设计),湿法熄焦作为备用。
7.63米大型焦炉新技术介绍

焦炉本体机侧焦炉炉顶焦炉加热系统前言伴随着中国钢铁产业的快速发展,炼焦行业的产能规模和装备水平发生了历史性变化,目前我国炼焦企业已有1300多家,“十五”期间,我国焦炭产量以每年21.7%的速度增长,约占世界焦炭贸易额的47%.首钢一期共建设投产7.63米的大型焦炉4座, .整个焦炉本体由德国公司提供全套技术支持,年产冶金焦炭420万吨,焦炭质量世界第一。
焦化维检作为焦化区域的自动化设备维护单位,肩负着焦化各区域所有自动化系统的维护工作,尤其是焦炉本体作业区,其稳产顺产直接影响着转炉、高炉、炼钢等主生产流程的焦炭供应,所以充分的消化、吸收其先进的核心控制技术和各连锁关系,快速掌握故障处理能力,是出色完成焦炉本体维护任务、保障焦炉生产稳定运行的关键。
本文旨在详细介绍德国公司成套系统组成、工艺结构特点、控制系统要点及其相关知识,通过参阅此文档可对焦炉系统有一个较为全面的了解。
前言 (3)第一节.炼焦工艺流程介绍 (5)一.炼焦工艺流程介绍 (5)二.焦炉参数列举 (5)三.7.63米超大型焦炉新技术分析 (6)3.1焦炉加热系统 (6)3.1.1蓄热室 (7)3.1.2加热壁 (8)3.1.3不同的加热系统 (9)3.1.4焦炉煤气加热 (9)3.1.5混合气体加热 (10)3.1.6转换设备 (11)3.1.7废气系统 (11)3.2.荒煤气导出系统 (12)3.2.1荒煤气导出系统构成 (12)3.2.2 Proven系统构成 (13)第二节. 7.63米超大型焦炉成套系统工艺流程分析 (14)一:交换机系统(Resevering systm) (14)1.1交换机系统(Resevering systm)概述 (14)1.2交换机动作流程简介 (15)二.PROVEN系统 (16)2.1.PROVEN系统概述 (16)2.2炉压调节的工艺原理 (17)2.3、炉压调节系统的上位监控 (18)三.BLEEDER放散系统 (19)3.1荒煤气点火放散系统的工艺原理 (19)3. 2工艺流程 (20)3.3、荒煤气点火放散系统的自动控制 (21)第三节、CokeMaster系统在焦炉中的应用 (24)一、概述 (24)二:系统功能 (24)三、软硬件配制 (24)3.1硬件配制 (25)3.2软件配制 (25)四、功能系统组成 (25)4.1手动测温系统(ManuTherm) (25)4.2自动测温系统(AutoTherm) (26)4.3炉温控制系统(BatControl) (27)4.4推焦计划自动编制系统(PushSched) (28)第四节、焦炉焦炉工业网络拓扑配置 (29)一、焦炉网络拓扑图 (29)1.1工业以太网拓扑图 (29)二、安全系统概述 (32)2.1、安全系统介绍 (32)第一节.炼焦工艺流程介绍一.炼焦工艺流程介绍由备煤作业区送来的配合好的炼焦用煤装入煤塔。
7.63米大型焦炉技术文档_二章节
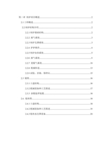
第二章焦炉项目概述 (2)2.1工程概述 (2)2.2焦炉结构介绍 (2)2.2.1焦炉基础结构 (2)2.2.2 废气系统 (3)2.2.3焦炉支撑系统 (3)2.2.4 护炉铁件 (4)2.2.5焦炉加热系统 (5)2.2.6 废气系统 (9)2.2.7 荒煤气系统 (10)2.2.8 机械轨道 (13)2.2.9试验、存储、修理站 (15)2.3 煤塔 (16)2.3.1土建结构 (16)2.3.2机械设备和工艺描述 (17)2.3.3 余煤处理装置 (18)2.4. 熄焦塔 (18)2.4.1土建结构 (18)2.4.2机械设备和工艺描述 (19)2.4.3熄焦水沉降设备 (20)第二章焦炉项目概述2.1 工程概述XX公司位于东北部,焦化项目工程位于钢铁基地内,其北侧为炼铁区,西面为烧结区,南面为焦煤堆场,东面为精品化工区。
XX公司最终建设规模为产钢3000万t/a,工程分三期建设。
焦化一期工程建设4座7.63m特大型焦炉及配套设施,采用XX公司先进的自动化控制系统,使整个焦化厂能够在最佳工况下生产,该系统包括自动测温系统、手动测温系统、炉温控制系统、推焦计划自动编制系统和煤气净化控制系统;采用先进的系统,控制、调节每个炭化室压力,实现无烟装煤。
本工程为XX公司焦化一期工程,建设规模为年产干全焦420万t/a,生产品种为冶金焦,分步实施:第一步建设2×70孔7.63m复热式焦炉;第二步建设2×70孔7.63m复热式焦炉。
并建设与4×70孔7.63m复热式焦炉相配套的备煤作业区、焦处理设施、煤气净化作业区及厂区内供配电、供排水、废水处理和总图运输等生产、公辅设施。
本工程主要产品为冶金焦、焦炉煤气、焦油、轻苯、精重苯、硫酸、硫铵等,净化后焦炉煤气除焦化自用外,其余外供。
2.2 焦炉结构介绍本节着重介绍7.63米焦炉的工程达到的设计目标2.2.1焦炉本体基础结构介绍焦炉基础结构是加强混凝土结构,包括基础钢板,在钢板上排列着炉柱、由支柱和在焦炉端台处的抵抗墙支撑的带有开孔的铺板很坚固的连接到基础板上。
7.63米焦炉调火汇编(一)

7.63米焦炉调火汇编(一)1.7.3炭化室压力调节各炭化室压力的调节是通过一个PROven装置实现的。
如上图,在集气管内对应每孔炭化室桥管末端安装一个形状象皇冠的管,皇冠管上开有多条沟槽,同时桥管下端设有一个“固定杯”,杯内设有由执行机构控制的活塞杆及与其相连的杯口塞,同时在桥管设有压力检测与控制装置。
炭化室压力调节是由调节杯内的水位也就是荒煤气流经该装置的阻力变化实现的。
其操作原理如下:两个喷嘴喷洒的氨水流入杯内,测压压力传感器将检测到上升管部位的压力信号及时传到执行机构的控制器,控制器发出指令执行机构控制活塞杆带动杯口塞升降,调节固定杯出口大小来调节杯内的水位,使炭化室压力永远保持在微正压状态。
水位越高,沟槽开度越小,荒煤气导出所受阻力越大;水位越低,沟槽开度越大,荒煤气导出所受阻力越小。
在装煤和结焦初期,炭化室产生大量荒煤气使压力增高,此时压力控制装置通过执行机构,活塞杆将杯口塞提升,使固定杯下口全开。
桥管内喷洒的氨水全流入集气管,在杯内不形成任何水封,使大量荒煤气以最小阻力导入集气管,炭化室内压力不致过大。
而在结焦末期,压力控制装置通过执行机构,活塞杆使杯口关闭,大量氨水迅速充满固定杯,形成阻断桥管与集气管的水封,以维持炭化室的正压。
在结焦过程中则可通过压力控制装置自动调节固定杯内的水封高度,从而实现对炭化室内煤气压力的自动调节,防止因超压而造成的炉门泄漏。
推焦时,炭化室需要与集气管隔绝,以免将空气吸入集气管,这时活塞达到最低位置,大量氨水迅速将固定杯充满,同时关闭皇冠管的沟槽,切断了荒煤气的通道。
为了减少冲满固定杯的时间,或在风、电中断时达到完全隔绝的目的,应快速打开注水阀,与此同时,上升管打开装置自动打开上升管盖,将多余荒煤气放散。
要求用冲洗液冲洗固定杯,以关闭“皇冠”管中的沟槽,活塞达到最低位置即可完成此项任务,为减少冲入固定杯时间,也为防止停风、停电,需要打开快速注水阀。
人工操作:使用气动控制操作面板,把气缸停止在最低极限位置,打开快速注水管,将固定杯注满,可使集气管与炭化室隔绝。
7.63米焦炉炉体参数
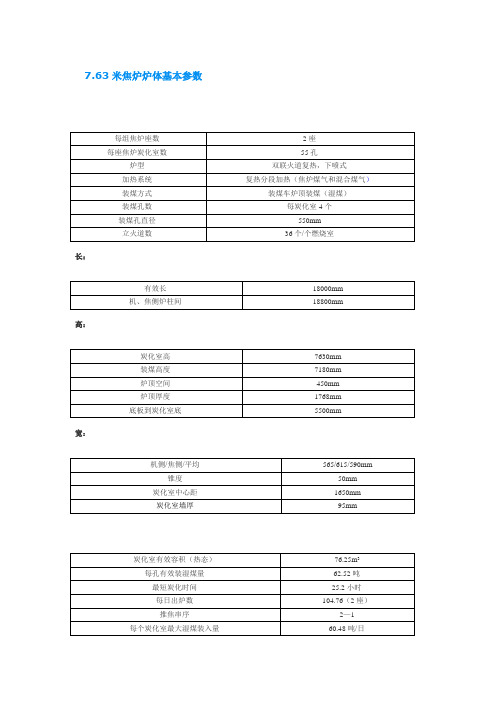
7.63米焦炉炉体基本参数长:高:宽:2.1.2焦炉炉体结构及特点 a)7.63m焦炉炉体为双联火道、分段供空气加热及废气循环,焦炉煤气下喷、低热值混合煤气及空气均侧入,蓄热室分格及单侧烟道的复热式超大型焦炉。
此焦炉具有结构先进、严密、功能性强、加热均匀、热工效率高、环保优秀等特点。
b)在分格蓄热室中,每个立火道单独对应1格蓄热室构成1个加热单元。
用焦炉煤气加热时,在地下室用设有孔板的喷嘴调节煤气,孔板调节方便,准确;空气是通过小烟道顶部的金属调节板调节。
用低热值混合煤气加热时,煤气和空气均用小烟道顶部的金属调节板调节,使得加热煤气和空气在蓄热室长向上分布合理,均匀。
c)蓄热室主墙,单墙和隔墙结构严密,用异型砖错缝砌筑,保证了各部分砌体之间不互相串漏。
主墙和单墙下部采用半硅砖,上部采用硅砖砌筑,半硅砖砌体和硅砖砌体之间设有滑动缝。
d)蓄热室的小烟道采用单侧烟道。
e)分段加热使斜道结构复杂,砖型多。
但斜道的通道内无膨胀缝的设计使斜道严密,防止了斜道区上部高温事故的发生。
f)燃烧室由36个共18对双联火道组成。
分3段供给空气进行分段燃烧;并在每对火道隔墙间下部设循环孔,将下降火道的废气吸入上升火道的可燃气体中,用此两种方式拉长火焰,达到高向加热均匀的目地。
当用高炉煤气和焦炉煤气的低热值混合煤气加热时,空气通过燃烧室底部斜道出口,距燃烧室底部1/3和2/3处的立火道隔墙出口分别喷出,与燃烧室底部斜道另一个出口喷出的低热值混合煤气形成3点燃烧加热;当焦炉单用焦炉煤气加热时,混合煤气通道也和空气通道一样走空气,空气通过燃烧室底部两个斜道出口,距燃烧室底部1/3和2/3处的立火道隔墙出口分别喷出。
焦炉煤气由燃烧室底部煤气喷嘴喷出,形成3点燃烧加热。
由于3段燃烧加热和废气循环,炉体高向加热均匀,且废气中的氮氧化物含量低,可以达到先进国家的环保标准。
g)炉顶设有4个装煤孔和1个水封式上升管。
7.63米焦炉主工艺介绍
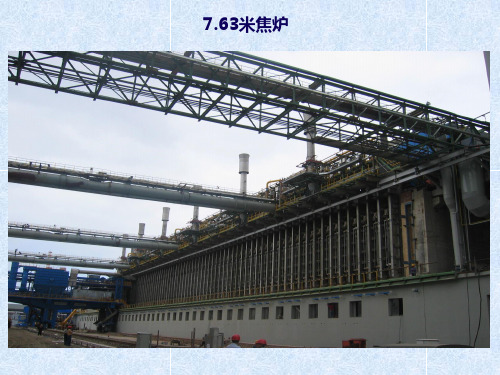
液压交换机系统概述
• 交换机系统是焦炉的心脏,负责整个焦炉的供热。 7.63米焦炉为复热式超大型焦炉,既可以用焦炉煤 气加热,又可以用混合煤气加热。整套设备都由德 国UHDE公司供货,并提供技术支持。 • 这套系统由液压缸、液压泵、蓄能器、油箱、油路 控制台、限位开关、电磁阀、压力表、液位计、电 液执行器等设备构成,主要动力源是液压油。
上升管系统
上升管系统
上升管系统
炉压调节的工艺
• • • •
炉压调节分三个过程 1:炼焦过程 2:推焦过程 3:装煤过程
1.炼焦过程
• Fast flooding pipe is closed • Stand pipe lid is closed • Piston in control position between 0 und 260mm (064%) • Oven = pressure • GCM = suction
3.装煤过程
• Fast flooding pipe is closed • Stand pipe lid is closed • Piston near in retracted position • Oven pressure = GCM-pressure
3.装煤过程
•
在推焦过程结束后,推焦车给出推焦完毕信号 ,PROven系统关上上升管盖,进入装煤阶段, 为了不产生烟尘放散,要将炭化室和集气管完全 连通,这需要将活塞打到全开模式,活塞的位置在 100%,并借助鼓风机产生的吸力,使炭化室产生 负压(-350Pa),从而实现无烟装煤。
2.放散系统
• 京唐钢铁公司焦化作业部的7.63米大型焦炉 的上升管通过鹅型管与集气管相连,集气 管则通过三段吸气管连接到鼓风机,由鼓 风机产生吸力将炼焦时产生的荒煤气吸到 煤气净化区域进行相应处理。每段吸气管 上装有一个电液执行器,其对应的集气管 上的装有三块压力表,每段集气管上配有 两套Bleeder放散系统,每套系统包括现场 控制面板、声光报警器、点火电极、气缸 、热电偶、气动阀、电磁阀等设备构成。
焦化公司7.63m焦炉耐材砌筑施工方案

7米63焦炉耐火材料砌筑施工作业设计方案目录1、编制依据2、工程概况3、施工条件4、施工部署5、施工方案6、劳动组织7、工期计划8、工程质量保证措施9、施工机械、机具计划10、安全保证措施11、文明施工及环保措施12、冬季施工13、附图(施工平面图布置)1、编制依据1.1、某焦化公司7.63m焦炉耐材砌筑施工图;1.2、相关的施工规范和技术规程《工业炉砌筑工程质量检验评定标准》GB50309-92《工业炉砌筑工程施工及验收规范》GB50211-20041.3、按GB/T19001-2000 idt ISO 9001:2000、GB/T24001-2004 idt ISO14001:2004、GB/T28001-2001 idt OHSAS18001:2001标准建立的公司《质量、环境、职业健康安全程序管理手册》CFMCC/QEOM/2005(B版)和《质量、环境、职业健康安全程序文件》CFMCC/MSP/2005(B版),以及公司颁布实施的有关企业技术质量标准和操作规程;1.4、业主对质量、安全、文明施工的有关规定;1.5、国家现行安全生产法规等。
2、工程概况某焦化7.63m焦炉工程是建设节能经济,扩大生产规模,提高焦化装备水平的大型工程项目,是从德国引进炉型,经转化设计。
该厂2座70孔焦炉采用炭化室高7.63m的大容积焦炉,其2×70孔的焦炭产量超过了目前国内6m焦炉3×70孔的产量,具有生产效率高,占地面积小,环境性能好等特点。
加热采用分段加热系统保证了焦炉垂直高度方向加热均匀性和焦炭成熟度。
先进的特殊结构的弹性炉门,保证了炉门优良的密封性,完善的护炉铁件系统,保证了炉体严密性和使用寿命。
2.1、 70孔7.63m焦炉炉型基本尺寸:炉型焦炉冷态尺寸备注总尺寸(㎜)有效尺寸全炉长119790 70孔小烟道高1535 蓄热室高2505 斜道高1155 炉顶高1750炭化室尺寸全长18560全高7540 冷态尺寸机侧宽578焦侧宽628平均宽603中心距1650立火道个数36个立火道中心距498炭化室锥度502.2、焦炉主要构造组成焦炉主要由小烟道、蓄热室、斜道、燃烧室、炉顶部位等组成。
7。63焦炉的优点
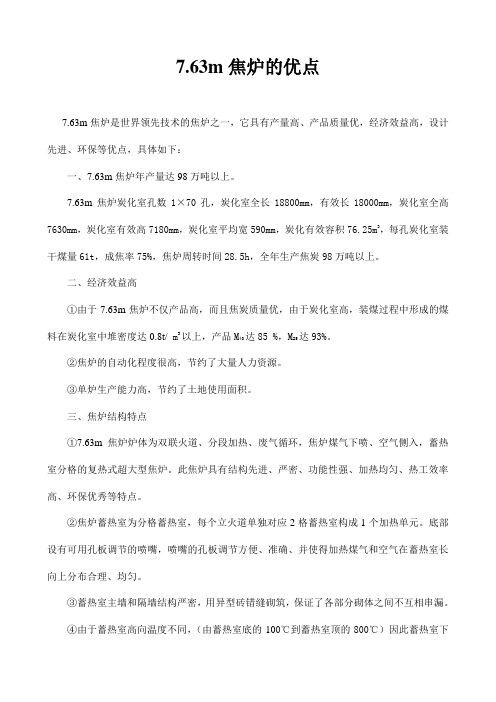
7.63m焦炉的优点7.63m焦炉是世界领先技术的焦炉之一,它具有产量高、产品质量优,经济效益高,设计先进、环保等优点,具体如下:一、7.63m焦炉年产量达98万吨以上。
7.63m焦炉炭化室孔数1×70孔,炭化室全长18800mm,有效长18000mm,炭化室全高7630mm,炭化室有效高7180mm,炭化室平均宽590mm,炭化有效容积76.25m3,每孔炭化室装干煤量61t,成焦率75%,焦炉周转时间28.5h,全年生产焦炭98万吨以上。
二、经济效益高①由于7.63m焦炉不仅产品高,而且焦炭质量优,由于炭化室高,装煤过程中形成的煤料在炭化室中堆密度达0.8t/ m3以上,产品M40达85 %,M25达93%。
②焦炉的自动化程度很高,节约了大量人力资源。
③单炉生产能力高,节约了土地使用面积。
三、焦炉结构特点①7.63m焦炉炉体为双联火道、分段加热、废气循环,焦炉煤气下喷、空气侧入,蓄热室分格的复热式超大型焦炉。
此焦炉具有结构先进、严密、功能性强、加热均匀、热工效率高、环保优秀等特点。
②焦炉蓄热室为分格蓄热室,每个立火道单独对应2格蓄热室构成1个加热单元。
底部设有可用孔板调节的喷嘴,喷嘴的孔板调节方便、准确、并使得加热煤气和空气在蓄热室长向上分布合理、均匀。
③蓄热室主墙和隔墙结构严密,用异型砖错缝砌筑,保证了各部分砌体之间不互相串漏。
④由于蓄热室高向温度不同,(由蓄热室底的100℃到蓄热室顶的800℃)因此蓄热室下部采用粘土砖砌筑,而蓄热室上部(接近蓄热室高度的65%)采用硅砖砌筑。
从而保证了主墙和各分隔墙之间的紧密结合。
⑤分段加热使斜道结构复杂,砖型多。
但通道内无膨胀缝使斜道严密,防止了斜道区上部高温事故的产生。
四、工艺设计先进,实用、可靠、低成本1、焦炉采用焦炉煤气加热,各项参数的测量显示记录调节和低压报均有自动抗利仪表来完成,废气系统的废气导出烟道为单侧烟道,布置在焦侧这样废气交换开闭器较常规设计的双侧烟道就减少了一半,既节约了投资又优化了焦炉操作环境。
国内常见大容积焦炉的比较与选型建议

国内常见大容积焦炉的比较与选型建议贾建成刘少阳(邯钢集团邯宝公司焦化厂)1.前言随着炼焦工业的发展,焦炉日趋大型化和现代化,焦炉炭化室的高度从4m左右增加到6m、7m 、7.63m,甚至达到8m或8.65m,长度从13m增加到17m, 18m, 个别达到20.8m,容积从25m3左右增加到40 m3, 50m3,80m3, ,最大可达100m3,以上;建设大容积焦炉,也就是建设大型焦炉,可降低基建投资和操作费用,增加焦炭产量,提高生产效率,同时,随着煤炭资源日趋紧张,炼焦煤价格的大幅上扬,高炉的大型化与富氧喷吹技术的发展对焦炭的机械性能和高温反应性和反应后强度提出了更高要求,也促使焦炉向大型化和自动化方向发展,结合目前国内占主导的炭化室高6m焦炉,新近建设的7m焦炉和我国马钢、太钢、武钢和兖州矿业从德国引进的7.63m焦炉,本文从焦炉炉体结构、机械配置,车辆自动化水平和环境保护和投资等方面对不同炉型焦炉的优缺点作一对比,提出一条较为可行的焦炉选型方法和原则。
2.6m焦炉,7m焦炉和7.63m焦炉的炉体结构特点常见6m焦炉为双联火道、废气循环、焦炉煤气下喷、高炉煤气侧入的复热(或)单热下调式大容积焦炉,7m焦炉炉体采用高低灯头、蓄热室长向分格和空气下调技术, 7.63m焦炉与6m相比炉体采用分段加热、蓄热室长向分格和空气下调技术,具有结构先进、严密,功能性强,加热均匀等特点。
6m,7m和7.63m焦炉的炉体结构和工艺参数比较见下表1。
表1 6m、7m和7.63m焦炉的炉体结构和工艺参数表(以220吨/年为基准)3.6m焦炉,7m焦炉和7.63m焦炉的焦炉机械配置与自动化水平比较随着国内机加工设备的改进和数控加工技术的推广与电子计算机技术的发展,以及新材料和新技术的应用,大容积焦炉机械在总结国内外焦炉机械操作经验的基础上,吸取目前成熟、可靠、先进、实用的焦炉机械的长处,主要从提高焦炉机械效率,降低劳动强度和改善操作环境出发,并以安全、可靠、实用进行和配置的,国内常见6m焦炉,7m焦炉和7.63m焦炉的焦炉机械配置与机车自动化配置水平列表比较见表2。
6m焦炉与7.63m焦炉施工技术对比

一、炉体参数序号项目 6.0m焦炉7.63m焦炉1 焦炉宽度(mm)15980 185602 炭化室长度(mm)15980 185603 炭化室有效长度(mm)15140 180004 炭化室高度(mm)6000 75405 炭化室有效高度(mm)5650 71806 炭化室有效容积(m3/孔) 38.5 76.257 基础平台高度(mm)2408 蓄热室高度(mm)4100 40359 斜道高度(mm)800 112010 炭化室高度(mm)6000 754011 炉顶高度(mm)1200(1250) 175012 全高(mm)12340(12390) 1444513 炉顶坡度(mm)5014 高向膨胀(mm) 140 14515 横向膨胀(mm) 200 24016 炭化室全锥度(mm) 60 5017 燃烧室间距(mm) 1300 165018 立火道间距(mm) 480 498/50219 立火道数量(个) 32 3620 炭化室平均宽度(mm) 450 60321 产量(万t/a孔) 1.00 1.5722 端燃烧室与抵抗墙距离mm2500 297023 全炉砖号(个)452 107324 顶板炉长方向段数(段) 1 8二、主要结构特点序号项目 6.0m焦炉7.63m焦炉1 蓄热室滑动层基础平台红砖砌体表面设置滑动,采用钙基润滑脂+0.5mm镀锌钢板+钙基润滑脂+石油沥青毡基础平台砼表面,采用双层0.5mm石墨纸板;蓄热室21层与22层之间,在21层主、单墙上设置滑动层, 采用石墨糊+石油沥青毡2 斜道区滑动层上下层胀缝之间以、炭化室墙砖与第8层胀缝之间设置滑动层,采用石油沥青纸仅在第35层、36层上表面满铺滑动层,采用石墨糊+石油沥青毡3 炉顶滑动层炭化室过顶砖与燃烧室墙设置滑动层, 采用石油沥青纸炭化室过顶砖与燃烧室墙之间设置滑动层, 炭化室过顶砖表面全炉满铺滑动层, 炉顶缸砖下表面满铺滑动层,均采用石墨糊+石油沥青毡4 箅子砖设置在水平烟道内设置衬砖,在衬砖上放置箅子砖。
焦炉炉体结构课件

03
焦炉内部结构
燃烧室结构
炉墙
燃烧室的两侧由耐火砖砌成的炉 墙,用于隔绝燃烧室和焦炭室,
承受高温烟气冲刷。
燃烧器
位于燃烧室顶部的燃烧器,将煤 气和空气混合后点燃,产生高温
烟气。
拱顶
燃烧室的顶部由耐火材料砌成的 拱形结构,起到支撑和分散烟气
压力的作用。
焦炭室结构
炭化室墙
焦炭室的四周由耐火砖砌成,用于将炼焦煤隔绝成独立的空间, 承受高温和压力。
焦炉发展历程
01
02
03
初创阶段
早期的焦炉结构简单,效 率低下,产量有限。
改进阶段
随着技术的发展,焦炉结 构不断优化,提高了热效 率和产量。
现代化阶段
引入先进的自动化技术和 环保措施,使得焦炉生产 更加高效可分为顶装式焦炉和侧装 式焦炉,主要区别在于装 煤方式的不同。
位于炉顶盖板下方,是燃烧室的一 部分,通常设有看火孔,以供操作 人员观察火焰状况。
炉顶保温层
用于减少热量损失,提高焦炉热效 率。
炉墙结构
耐火砖层
焦炉炉墙主要由耐火砖砌成,承受高温,保证炉 体的稳定性和寿命。
保温层
减少热量损失,提高热效率。
金属结构层
用于支撑和固定耐火砖层,保证炉墙的稳定性。
炉底结构
燃烧不充分
燃烧不充分会导致能源浪费和污染物排放增加。处理方法 为清理燃烧器、喷嘴,调整燃气和空气比例,确保燃烧充 分。
温度控制失灵
温度控制失灵会影响焦炭质量和产量。处理方法为检查温 度控制系统元件,更换损坏部件,重新标定温度探头。
THANKS
感谢观看
根据结构形式分类
可分为单室式焦炉和多室 式焦炉,多室式焦炉又可 进一步分为连续式、半连 续式和间歇式。
7.63米焦炉概述
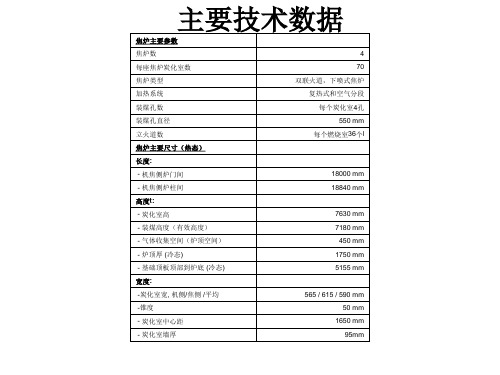
双联火道,下喷式焦炉
复热式和空气分段 每个炭化室4孔 550 mm 每个燃烧室36个l
000 mm 18840 mm
7630 mm 7180 mm 450 mm 1750 mm 5155 mm
565 / 615 / 590 mm 50 mm 1650 mm
- 炭化室墙厚
95mm
生产数据
生产数据 炭化室有效容积(热态) 装煤量 (湿煤) 76.25 m³ 64.66 tons
主要技术数据
焦炉主要参数 焦炉数 每座焦炉炭化室数 4 70
焦炉类型
加热系统 装煤孔数 装煤孔直径 立火道数 焦炉主要尺寸(热态) 长度: - 机焦侧炉门间 - 机焦侧炉柱间 高度t: - 炭化室高 - 装煤高度(有效高度) - 气体收集空间(炉顶空间) - 炉顶厚 (冷态) - 基础顶板顶部到炉底 (冷态) 宽度: -炭化室宽, 机侧/焦侧 /平均 -锥度 - 炭化室中心距
• 京唐公司计划分三期建10 座焦炉,其中一 期建4座,建设规模为年产干全焦约420万 吨,生产品种为冶金焦。建设分两步进行, 一步建2座70孔7.63米焦炉。 • 一期一步建两座7.63m复热式焦炉。焦炉采 用单集气管,三吸气管,干法熄焦,湿熄 焦备用。装煤采用集气系统PROven方式除 尘,出焦除尘采用地面站。
• 配好的煤在常温下装入焦炉的炭化室后, 煤在隔绝空气的条件下受到来自炉墙和炉 底(1000℃~1100℃)的热流加热,逐步 转变为焦炭。 • 炭化室中成熟的焦炭通过焦炉四大机车中 的推焦车推出炭化室,通过导焦车(也叫 拦焦车)导入熄焦车,再由熄焦车将红焦 送到熄焦装置进行熄焦处理。出焦后的空 炭化室立即由装煤车进行定量装煤。
• (6)小烟道:位于蓄热室的下部,主要作 用是 通过箅子砖 在上升气流时分配空气或 高炉煤气,下降气流时集合并排出废气, 箅子砖还起到支撑格子砖的作用。 • (7)烟道:其作用是汇集焦炉加热系统排 出的废气,并引导废气到烟囱排走。 • (8)烟囱:烟囱通过烟道与加热系统相连。 在浮力的作用下,烟囱产生足够的吸力, 使焦炉加热系统 内产生气体流动。
7.63米大型焦炉技术文档_四大机车简介

在所有四个煤斗已装满煤后,最大量的传感器响应动作,煤塔出口再次自动关闭。
(6)时序图:
3.1.3
1主要零部件:
A:接料嘴。B:支架。C:槽。D:驱动电机。E:带轴承的搅拌机。
2布置:
此炉盖泥封系统包括一个固定的储浆罐和两个安装在装煤车上的储浆槽。固定的储浆罐及其相关的阀,管,搅拌器等安装在煤塔里,与称重煤斗高度位置相当。其工作就是把泥封粉末和水混合在一起进行搅拌并将准备好的混合泥浆输送到装煤车上的储浆槽里。
2布置:
这四个装煤孔盖清扫器是安装在主平台下部(平台中心处),由液压缸驱动。主要由下列部件组成:
(1).带左驱动的刮刀框架,导向轮,清扫刮刀
(2).带右驱动的刮刀框架,导向轮,清扫刮刀
炉盖是由一个独立单元来清扫的。炉盖清扫器是自动地摆向炉盖。与装煤孔盖外形匹配的清扫刮刀在提升设备旋转时可以移除任何装煤孔盖上的结块。装煤孔座和孔盖的清扫是在装煤过之前进行的。
4操作工序:
当“取盖”指令发出后,所有四个炉盖提升设备同时由原始位置移至工作位置。到位之后,磁铁线圈通电,同时磁铁开始旋转。达到预设旋转时间后,带减速机的电动机停止。这时炉盖提升设备携带炉盖被提起至原始位置以便导套落下。装煤孔盖的插入过程基本与上述是反序的。但是按从炉盖1到4的顺序依次进行的。
5控制与监视:
第六章
第一节
7.63米焦炉稳定熄焦沉淀池和粉焦起运是采用粉焦刮板机,如下图,它自动沿沉淀池长向做往复运行,将粉焦刮到脱水台上。适应这种粉焦捞出设备的要求,沉淀池采用长条整体形状。
1:刮板机构.2:走行轨道.3:安全指标灯.4:走行台车.5:干油润滑系统.6:安全栏杆.7:直梯.8:电控系统.9:链条.10:电缆线槽.11:电缆卷筒.12:铭牌
- 1、下载文档前请自行甄别文档内容的完整性,平台不提供额外的编辑、内容补充、找答案等附加服务。
- 2、"仅部分预览"的文档,不可在线预览部分如存在完整性等问题,可反馈申请退款(可完整预览的文档不适用该条件!)。
- 3、如文档侵犯您的权益,请联系客服反馈,我们会尽快为您处理(人工客服工作时间:9:00-18:30)。
7.63m焦炉炉体结构
7.63m焦炉*内首次完全从德国Uhde公司引进,其先进的炼焦工艺技术,代表了当今世界炼焦技术发展的方向,集中了炼焦工艺、焦炉机械、焦炉自动控制等方面的先进技术,具有国际领先水平。
7.63m焦炉炭化室高7.63m(热态),双联火道、多段加热、同位燃烧、分格式蓄热室,混合煤气侧入、焦炉煤气下喷的复热式超大型焦炉。
太原钢铁集团公司焦化厂一期建设的一座1×70孔7.63m焦炉,包括焦炉炉体、煤塔、湿式熄焦塔、熄焦沉淀池、加煤、推焦、拦焦、除尘等设备。
焦炉上装有三个荒煤气集气管对炼焦过程中产生的荒煤气进行收集,并通过吸入管把收集来的荒煤气吸入到现有的煤气净化设置中。
本文拟从焦炉炉体各部位的结构特点和砖型特点进行加以介绍。
1.主要结构特点
1.1每个炭化室下面对应一个空气蓄热室和一个煤气蓄热室,在机、焦侧方向分成十八格;。