捷达轿车盘式制动器的设计(有全套图纸)
盘式制动器PPT课件

(2)牵引电动机缓速 对于采用电传动系的汽车,可以对电 动驱动轮中的牵引电动机停止供电,使之受驱动轮驱动而 成为发电机,将汽车的部分动能转变成电能,再使之通过 电阻转变为热能而耗散。这时电动机对驱动轮的阻力矩即 是制动力矩。
1.制动盘;2.活塞; 3.摩擦块; 4.进油口;5.制动钳 体; 6.车桥部;
定钳盘式制动器的应用
定钳盘式制动பைடு நூலகம்的缺点
液压缸较多,使制动钳结构复杂; 液压缸分置于制动器的两侧,必须用跨越
制动盘的钳内油道或外部油管来连接; 热负荷大时,液压缸内的油管的制动液容
易汽化; 若要兼用驻车制动时,必须加装一个机械
二、液力缓速式辅助制动系
原上海SH380型汽车采用液力缓速式辅助制动系。 其中的液力缓速器(图23—94)安装在液力机械变 速器的后端。其结构类似于两个并联的液力耦合 器,不过其每一对叶轮中只有一个能转动(即转子 10),而另一个是固定不动的(即带叶片的壳体l和 盖9)。
缓速器壳体用螺钉固定在机械变速器壳体8的后壁 上。转子与其轴6借花键连接,而轴6又用花键套 5与变速器第一轴(输入轴)4相连。
(5) 空气动力缓速 空气动力缓速是采用使车身的 某些活动表面板件伸展,以加大作用于汽车的空 气阻力的办法来起缓速作用。这种方法目前只用 于竞赛汽车。
一、排气缓速式辅助制动系
排气缓速主要用于柴油车,原因是柴油机压缩比较 汽油机压缩比大,作为空压机,其缓速效果优于 汽油机,而且,很容易做到在施行排气缓速时先 切断燃油供给。对汽油机,则需要通过较复杂的 装置方能做到这一点。
图解盘式制动器.

图解盘式制动器1.盘式制动器概述盘式制动器摩擦副中的旋转元件是以端面工作的金属圆盘,被称为制动盘。
其固定元件则有着多种结构型式,大体上可分为两类。
一类是工作面积不大的摩擦块与其金属背板组成的制动块,每个制动器中有2~4个。
这些制动块及其促动装置都装在横跨制动盘两侧的夹钳形支架中,总称为制动钳。
这种由制动盘和制动钳组成的制动器称为钳盘式制动器。
另一类固定元件的金属背板和摩擦片也呈圆盘形,制动盘的全部工作面可同时与摩擦片接触,这种制动器称为全盘式制动器。
钳盘式制动器过去只用作中央制动器,但目前则愈来愈多地被各级轿车和货车用作车轮制动器。
全盘式制动器只有少数汽车(主要是重型汽车)采用为车轮制动器。
这里只介绍钳盘式制动器。
钳盘式制动器又可分为定钳盘式和浮钳盘式两类。
盘式制动器结构图如下图所示2.定钳盘式制动器跨置在制动盘1上的制动钳体5固定安装在车桥6上,它不能旋转也不能沿制动盘轴线方向移动,其内的两个活塞2分别位于制动盘1的两侧。
制动时,制动油液由制动总泵(制动主缸)经进油口4进入钳体中两个相通的液压腔中,将两侧的制动块3压向与车轮固定连接的制动盘1,从而产生制动。
这种制动器存在着以下缺点:油缸较多,使制动钳结构复杂;油缸分置于制动盘两侧,必须用跨越制动盘的钳内油道或外部油管来连通,这使得制动钳的尺寸过大,难以安装在现代化轿车的轮辋内;热负荷大时,油缸和跨越制动盘的油管或油道中的制动液容易受热汽化;若要兼用于驻车制动,则必须加装一个机械促动的驻车制动钳。
定钳盘式制动器示意图1.制动盘2.活塞3.摩擦块4.进油口5.制动钳体6.车桥部3.浮钳盘式制动器制动钳体2通过导向销6与车桥7相连,可以相对于制动盘1轴向移动。
制动钳体只在制动盘的内侧设置油缸,而外侧的制动块则附装在钳体上。
制动时,液压油通过进油口5进入制动油缸,推动活塞4及其上的摩擦块向右移动,并压到制动盘上,并使得油缸连同制动钳体整体沿销钉向左移动,直到制动盘右侧的摩擦块也压到制动盘上夹住制动盘并使其制动。
盘式制动器结构、工作原理盘式制动器图示前桥驱动桥盘式制动器结构
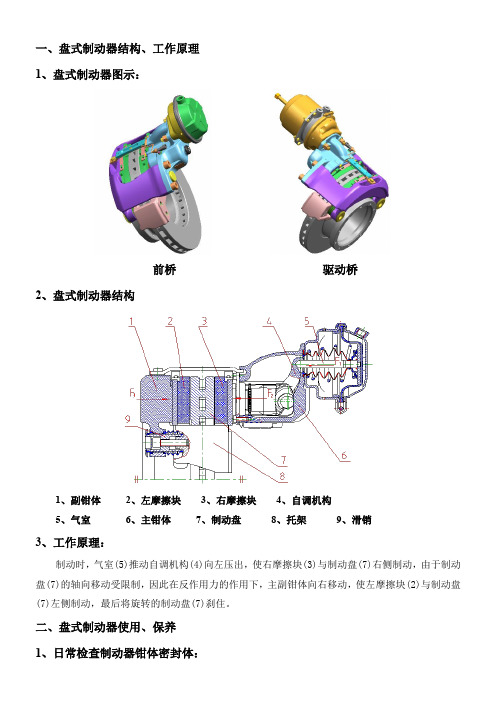
一、盘式制动器结构、工作原理1、盘式制动器图示:前桥驱动桥2、盘式制动器结构1、副钳体2、左摩擦块3、右摩擦块4、自调机构5、气室6、主钳体7、制动盘8、托架9、滑销3、工作原理:制动时,气室(5)推动自调机构(4)向左压出,使右摩擦块(3)与制动盘(7)右侧制动,由于制动盘(7)的轴向移动受限制,因此在反作用力的作用下,主副钳体向右移动,使左摩擦块(2)与制动盘(7)左侧制动,最后将旋转的制动盘(7)刹住。
二、盘式制动器使用、保养1、日常检查制动器钳体密封体:①检查副钳体端2个滑销密封盖,如出现松脱或者遗失及时给予更换或安装;②检查主钳体端2个滑销端盖,如出现松脱或者遗失及时给予更换或安装;③检查主钳体上密封帽,如存在裂纹、损伤或者遗失及时给予更换或安装;④推动主、副钳体滑动检查4个滑销密封圈,如存在裂纹和损伤及时给予更换。
2、定期检查内容:3、制动盘失效判定标准:①尺寸检查:如图:A=制动盘厚度45mm(新),B=制动盘厚度37mm(极限);②裂纹检查:如图所示:检查制动盘上的裂纹和磨损划痕;A1=小裂纹在表面上延伸,此情况允许。
B1=小于0.75a长、1.5mm宽和深的裂纹径向延伸,此情况允许。
C1=小于1.5mm深的环形槽,此情况允许。
D1=径向贯通裂纹是不允许的,制动盘必须更换。
4、摩擦片更换及间隙调整:4.1、摩擦块拆卸4.1.1拨出传感器线束的插座,拿出摩擦块压板总成和摩擦块。
4.1.2一字槽螺钉旋具将弧形弹簧拆卸;用平口螺丝刀将传感器线束的内、外感应头撬出。
取下摩擦块。
注意:撬内、外感应头应避免将绕在感应头上的线束伤断!4.2、摩擦块安装将摩擦块安装在托架内,再用压棒将传感器感应头预先压入摩擦块的U形槽中。
注意:摩擦块安装在托架内后,必须保证摩擦材料与制动盘对应,防止摩擦片装反后出现制动故障;传感器感应头按图示方向装入U形槽,不得装反以及压坏线束。
线束插头按箭头方向拔出内感应头外感应头三、常见故障排查方法:压棒U型槽。
汽车底盘构造与维修9 捷达汽车盘式制动器拆装
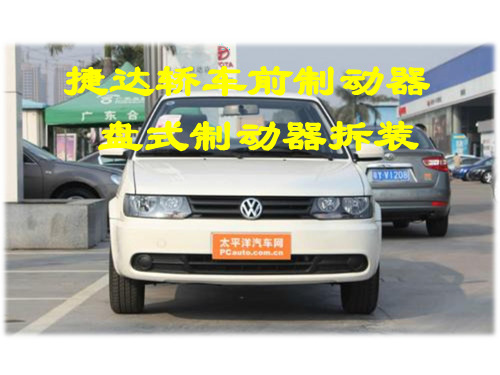
拆 装 盘 式
轮制动器的 拆装; 2、轿车车
正 确 进 行 轿车1辆,块衬层的厚度
10分
轿车车轮 制动器的
2工、具拆1套装,3制、动拧分松泵制动分泵下部装配螺栓,1吊0分起
制 轮制动器的 拆 装 与 调 3、撬棍,4、拆出块制动器摩擦衬块等 15分
动 检查与调整;整。
器 更 换
3、职业素 质的养成。
捷达轿车前制动器 盘式制动器拆装
一、盘式制动器的认知
1、基本结构
制动蹄片一般由铁衬板和 摩擦材料两部分组成,一
定不要等摩擦材料部分都 磨没了才更换蹄片。例如 捷达车的前制动蹄片,新
片的厚度为14毫米,而更 换的极限厚度是7毫米.一 些车辆带有制动蹄片报警
功能,一旦达到了磨损极 限,仪表会报警提示更换 蹄片。达到了使用极限的
制 满 分 ( 100
动 分)
4、螺丝 5、正确清洁检查新的摩擦衬块;10分
刀,5、 6、装配新的摩擦衬块;
专用工 具,6、
7、安装固定制动钳壳体螺栓
15分 15分
清 洁 工 8、正确安装车轮;
10分
块
具。 9、清理现场
5分
10、规定时间15min每超过1min扣10分
考核评语:
7、固定制动钳壳体螺栓
8、正确安装车轮;
使用举升机将汽车降下适当高度,安装前轮 力矩:103N·m
9、清理现场
落车
收举升机垫块
整理工具、清 洁工作场地
操作具体要求
考核 考核内容 操作要求 器材 项目 及 分 值 与 方 法 设备
评分标准
扣分
1、正确拆卸车轮;
10分
1、轿车车
1 、 能 1、捷达 2、通过泵体上的检测孔,检查摩擦衬
捷达轿车后轮制动器_设计说明书
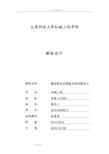
太原科技大学机械工程学院课程设计课程名称:捷达轿车后轮鼓式制动器设计专业:车辆工程班级:车辆121202 姓名:梁开心学号:201212040212 指导教师:赵富强学期:2014-2015 日期:2015/12/28摘要近年来我国汽车市场迅速发展,特别是轿车汽车发展的方向。
然而随着汽车数量的增加,带来的安全问题也越来越引起人们的注意,而制动系统则是汽车主动安全的重要系统之一。
因此,如何开发出高性能的制动系统,为安全行驶提供保障是我们要解决的主要问题。
另外,随着汽车市场竞争的加剧,如何缩短产品开发周期、提高设计效率,降低成本等,提高产品的市场竞争力,已经成为企业成功的关键。
本说明书主要介绍了捷达轿车后轮鼓式制动系统的设计。
首先介绍了汽车制动系统的发展、结构、分类,并对鼓式制动器和盘式制动器的结构及优缺点进行分析。
设计计算确定前盘、后鼓式制动器、制动主缸的主要尺寸和结构形式。
绘制出了后制动器装配图、制动鼓零件图以及制动蹄零件图等。
最终对设计出的制动系统的各项指标进行评价分析。
另外在设计的同时考虑了其结构简单、工作可靠、成本低等因素。
通过本次设计的计算结果表明设计出的制动系统是合理的、符合标准的。
其满足结构简单、成本低、工作可靠等要求。
关键字:汽车;制动;鼓式制动器AbstractIn recent years the rapid development of China's auto market, especially cars car development. However, with the increase in car ownership, safety problems are increasingly attracted attention, and the braking system is an important vehicle active safety systems in the world. Therefore, how to develop high-performance braking system, to provide protection for the safe driving is the main problem we have to solve. In addition, with increased competition in the automotive market, how to shorten the product development cycle, improve design efficiency, reduce costs, increase market competitiveness has become the key to business success.This manual describes the Jetta sedan rear drum brake system design. The first describes the development of automotive braking systems, structure, classification, and by drum brakes and disc brakes on the structure and analyze the advantages and disadvantages. Design calculations to determine the front disk, rear drum brakes, brake master cylinder of the main dimensions and structure. Drawn out of the rear brake assembly diagram, brake drum and brake shoe parts diagram parts chart. End of the braking system designed to evaluate the analysis of the indicators. Also taking into account in the design of its structure is simple, reliable, low cost factor.Through this design results show that the design of the braking system is reasonable, standards-compliant. Meet its simple structure, low cost, reliable requirements.Key words: car;braking;brake drum目录第1章绪论1.1制动器设计的意义 (5)1.2制动器研究现状 (5)1.3 鼓式制动器的简介 (5)1.4 鼓式制动器的组成固件 (6)1.5 鼓式制动器的工作原理 (6)1.6 鼓式制动器的产品特性 (7)1.7设计基本要求和整车性能参数 (7)第2章鼓式制动器的选择2.1鼓式制动器形式方案分析 (8)2.2鼓式制动器 (8)2.3制动驱动机构的结构形式选择 (9)2.4简单制动系 (9)2.5动力制动系 (10)2.5.1气压制动系 (10)2.5.2气顶液式制动系 (10)2.5.3全液压动力制动系 (10)2.6鼓式制动器主要零部件的结构设计 (10)2.6.1制动蹄 (10)2.6.2制动底板 (11)2.6.3制动蹄的支承 (11)2.6.4制动轮缸 (11)2.7鼓式制动器整体方案分析 (11)2.8鼓式制动器装配注意事项 (13)第3章鼓式制动器的设计计算3.1捷达轿车的主要参数数值 (14)3.2车辆前后轮制动力的分析 (14)3.3前、后轮制动力分配系数 的确定 (17)3.4制动器受力分析及最大制动力的确定 (18)3.4.1制动器受力分析 (18)3.4.2制动器最大制动力矩 (18)3.5制动鼓内径R及制动鼓壁厚度的选取 (19)3.5.1制动鼓壁厚的确定 (19)3.5.2.制动蹄摩擦衬片的包角β和宽度b (20)β (21)3.5.3.摩擦衬片起始角3.5.4.张开力P的作用线至制动器中心的距离α (21)3.5.5.制动蹄支销中心的坐标位置是k与c (21)3.5.6摩擦片摩擦系数f (21)第4章制动器主要零部件的结构设计4.1 制动鼓 (23)4.2 制动蹄 (23)4.3 制动底板 (23)4.4 制动蹄的支承 (23)4.5 制动轮缸 (24)4.6 制动器间隙 (24)第5章校核5.1制动器的热容量和温升的核算 (25)5.2 制动器的校核 (26)5.2.1摩擦衬片所受力的校核 (26)5.3驻车制动的计算 (26)5.3.1汽车可能停驻的极限上坡路倾斜角α (26)5.3.2汽车可能停驻的极限下坡路倾斜角'α (27)结论 (28)致谢 (29)参考文献30第1章绪论1.1制动器设计的意义现代交通工具中用得最多,最普遍,也是最方便的交通运输工具就是汽车。
1.6升汽车盘式制动器的总体设计
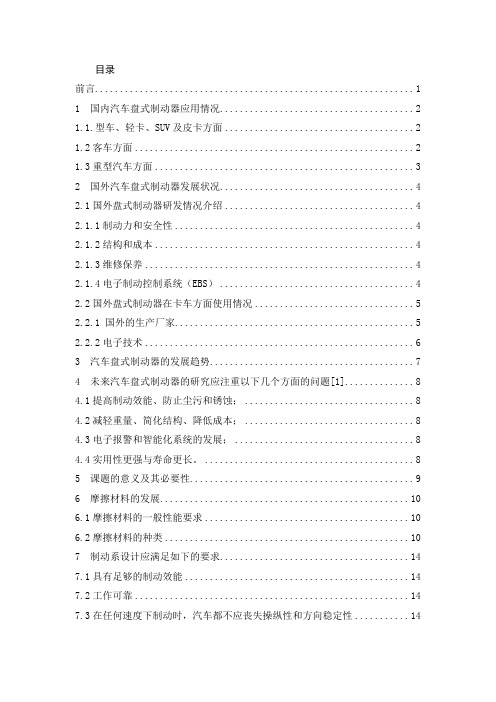
目录前言 (1)1 国内汽车盘式制动器应用情况 (2)1.1.型车、轻卡、SUV及皮卡方面 (2)1.2客车方面 (2)1.3重型汽车方面 (3)2 国外汽车盘式制动器发展状况 (4)2.1国外盘式制动器研发情况介绍 (4)2.1.1制动力和安全性 (4)2.1.2结构和成本 (4)2.1.3维修保养 (4)2.1.4电子制动控制系统(EBS) (4)2.2国外盘式制动器在卡车方面使用情况 (5)2.2.1 国外的生产厂家 (5)2.2.2电子技术 (6)3 汽车盘式制动器的发展趋势 (7)4 未来汽车盘式制动器的研究应注重以下几个方面的问题[1] (8)4.1提高制动效能、防止尘污和锈蚀; (8)4.2减轻重量、简化结构、降低成本; (8)4.3电子报警和智能化系统的发展; (8)4.4实用性更强与寿命更长。
(8)5 课题的意义及其必要性 (9)6 摩擦材料的发展 (10)6.1摩擦材料的一般性能要求 (10)6.2摩擦材料的种类 (10)7 制动系设计应满足如下的要求 (14)7.1具有足够的制动效能 (14)7.2工作可靠 (14)7.3在任何速度下制动时,汽车都不应丧失操纵性和方向稳定性 (14)7.3防止水和污泥进入制动器工作表面,保证制动效能的水稳定性好 (14)7.4制动能力的热稳定性良好 (14)7.5操纵轻便,并具有良好的随动性 (15)7.6作用滞后性应尽可能好 (15)7.7摩擦衬块应有足够的使用寿命 (15)7.8与悬架、转向装置不产生运动干涉,在车轮跳动或汽车转向时不会引起自行制动 (15)7.9能全天候使用,气温高时液压制动管路不应有气阻现象;气温低时气制动管路不应出现结冰 (15)8 在本次设计中以1.6升轻型汽车为标准,来设计前轮的制动器 (16)8.1鼓式和盘式制动器的结构形式有多种: (16)8.1.1不同的鼓式制动器的主要区别有[3]: (16)8.1.2按摩擦副中固定元件的结构不同,盘式制动器的种类有以下几种 (16)9 盘式制动器的工作原理 (17)10 盘式制动器的分类 (18)10.1固定钳式 (18)10.2浮动钳式: (19)10.2.1滑动钳式 (19)10.2.2摆动钳式 (19)10.2.3摆动钳式与固定钳式相比有以下优点 (19)10.2.4另外盘式制动器还有以下优点 (19)10.2.5盘式制动器的主要缺点是 (20)11 盘式制动器主要参数的初步确定 (21)11.1.设计的原始数据 (21)11.2.确定制动衬块的工作面积A (21)11.3.确定摩擦衬块外半径R2与内半径R1 (21)11.4.确定制动盘直径D (21)11.5.确定制动盘厚度h (21)12 制动器的设计和计算[12] (22)12.1制动力与制动力分配系数 (22)12.2同步附着系数 (26)12.3制动强度和附着系数利用率 (28)12.4制动器最大制动力矩 (30)12.5制动力矩的计算 (32)12.6驻车制动计算 (33)12.7摩擦衬块的磨损特性计算 (34)12.7.1比能量耗散率 (34)L f (35)12.7.2.比滑磨功13 制动器的热容量和温升校核 (37)参考文献 (38)致谢 (39)前言汽车在当今社会生产和生活中是极其重要的交通工具,随着社会要求的不断增长和科学技术的飞速发展、车辆的高速化都有了很大的提高,许多的交通事故也不断的增长,制动性能的要求日益成为一个迫切的问题。
轿车盘式制动器结构设计 【汽车专业毕业论文】【答辩通过】

摘要汽车的设计与生产涉及到许多的领域,其独有的安全性、经济性、舒适性等众多指标,也对设计提出了更高的要求。
汽车制动系统是汽车行驶的一个重要主动安全系统,其性能的好坏对汽车的行驶安全有着重要影响。
随着汽车的行驶速度和路面情况复杂程度的提高,更加需要高性能,长寿命的制动系统。
鉴于制动系统的重要性,本次设计的主要内容就是运输车辆中的制动器,从制动系的功用及设计的要求出发,依据给定的设计参数,进行了方案论证。
对各种形式的制动器的优缺点进行了比较后,在前盘后鼓得基础上改为前后都是盘式制动器,保持制动力分配系数的稳定,改善了汽车的制动稳定性,简化了汽车的制动装置,减轻了整车质量,从而提高了汽车在行驶过程中的安全性与稳定性。
选择了简单液压驱动机构和双管路系统,选用了间隙自动调节装置,采用比例阀作为制动力的调节装置。
关键词:制动钳; 制动盘; 制动轮缸;制动衬片本论文材料仅供参考学习,疑问可咨询文档贡献者。
AbstractAutomobile design and production are involved in many fields, its unique safety, economy, comfort and so many indicators, also raised taller requirement to the design. Automobile braking system is an important vehicle active safety system, and its performance depends on car has an important influence on road safety. As the vehicle of the speed and pavement situation was complex degree rise, more require high-performance, long life of brake system.In view of the importance of brake system, the design of the main content is a transport vehicles, the brake from brake system function and design, according to the requirement of design parameters, given the scheme comparison. On all forms of brake their advantages and disadvantages are discussed, based on HouGu have in QianPan instead of before and after are disc brakes, maintain braking force distribution coefficient, improves the stability of the braking stability and simplify the automobile braking device, reduce the vehicle quality, thereby improving the car while driving in the process of security and stability. Choose a simple hydraulic driving mechanism and double pipeline system, chose clearance automatic adjusting device, proportional valve as brake force adjusting device Keywords:brake disc; Brake wheel cylinder; Brake caliper; Braking facings formulations本论文材料仅供参考学习,疑问可咨询文档贡献者。
盘式制动器
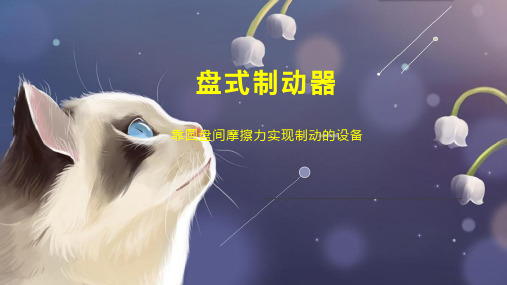
2.制动盘厚度
制动盘厚度对制动盘质量和工作时的温升有影响。为使质量小些,制动盘厚度不宜取得很大;为了降低温度, 制动盘厚度又不宜取得过小。制动盘可以做成实心的,或者为了散热通风的需要在制动盘中间铸出通风孔道。一 般实心制动盘厚度可取为10—20mm,通风式制动盘厚度取为20~50mm,采用较多的是20—30mm。在高速运动下 紧急制动,制动盘会形成热变形,产生颤抖。为提高制动盘摩擦面的散热性能,大多把制动盘做成中间空洞的通风 式制动盘,这样可使制动盘温度降低20 %~30%。
谢谢观看
盘式制动器沿制动盘向施力,制动轴不受弯矩,径向尺寸小。
用途
盘式制动器已广泛应用于轿车,现在大部分轿车用于全部车轮,少数轿车只用作前轮制动器,与后轮的鼓式 制动器配合,以使汽车有较高的制动时的方向稳定性。在商用车中,目前盘式制动器在新车型及高端车型中逐渐 被采用。
主要组成
制动盘
摩擦衬块
1.制动盘直径
制动力疲软,不总的原因有:(a)制动器漏油;(b)制动油路中有空气;(c)轮毂油封破损,钳盘上有油污; (d)制动严重磨损,摩擦面烧损;(e)气路气压调整过低。
解决方法: 1、改变制动衬块材料 可换用稍软的制动衬块材料,使摩擦系数相对得到提高,制动力变大。 2、清除制动衬块排屑槽中的异物 如果制动衬块的排屑槽被异物覆盖,制动时将失却排出尘土、刮去水分的作用,使制动力降低。 制动后跑偏 跑偏的直接原因是两侧车轮的制动力矩不等所致,常见的故障原因:(a)制动钳盘油污严重,摩擦系统数严 重下降,造成制动力矩不平衡,此时应清除制动钳盘上的油污;(b)分泵活塞卡滞不能工作。静车踩制动,观察 分泵工作情况,视情拆检。
捷达轿车制动系统毕业设计说明书
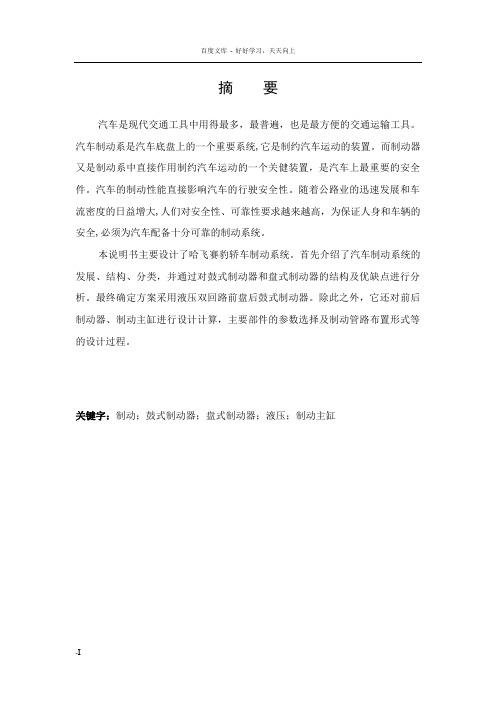
摘要汽车是现代交通工具中用得最多,最普遍,也是最方便的交通运输工具。
汽车制动系是汽车底盘上的一个重要系统,它是制约汽车运动的装置。
而制动器又是制动系中直接作用制约汽车运动的一个关健装置,是汽车上最重要的安全件。
汽车的制动性能直接影响汽车的行驶安全性。
随着公路业的迅速发展和车流密度的日益增大,人们对安全性、可靠性要求越来越高,为保证人身和车辆的安全,必须为汽车配备十分可靠的制动系统。
本说明书主要设计了哈飞赛豹轿车制动系统。
首先介绍了汽车制动系统的发展、结构、分类,并通过对鼓式制动器和盘式制动器的结构及优缺点进行分析。
最终确定方案采用液压双回路前盘后鼓式制动器。
除此之外,它还对前后制动器、制动主缸进行设计计算,主要部件的参数选择及制动管路布置形式等的设计过程。
关键字:制动;鼓式制动器;盘式制动器;液压;制动主缸ABSTRACTAutomobile is the modern traffic tools, the most common used most, also be the most convenient traffic transportation. Automobile brake system is automobile chassis to an important system, it is restricted by the car of the movement of the device. And the brake is brake system directly effect the automobile sport in a restricted key device, is the most important safety car parts. The automobile braking performance directly influence the car driving safety. With the rapid development of the industry and highway traffic density increases day by day, the people to the safety and reliability of the demand is higher and higher, to ensure the safety of the person and vehicles, must be equipped with very reliable car brake system.This manual mainly designed saibao hafei car brake system. First this paper reviewed the automobile braking system development, structure, classification, and through to the drum brake disc brake and the structure of the advantages and disadvantages and analyzed. Ultimately determine the scheme adopts hydraulic double circuit qianpan hougu type brake. In addition, it's still around to brake and brake main cylinder design, calculation of the main parts of parameter selection and brake pipe, the design process of decorate a form, etc.Key words: Braking; Brake drum; Brake disc; Hydroid pressure;Braking cylinder第1章绪论汽车制动系的研究的目的和意义汽车制动系是用于使行驶中的汽车减速或停车,使下坡行驶的汽车车速保持稳定以及使已停止的汽车停在原地(包括在斜坡上)驻留不动的机构,汽车制动系直接影响着汽车行驶的安全性和停车的可靠性。
图解盘式制动器
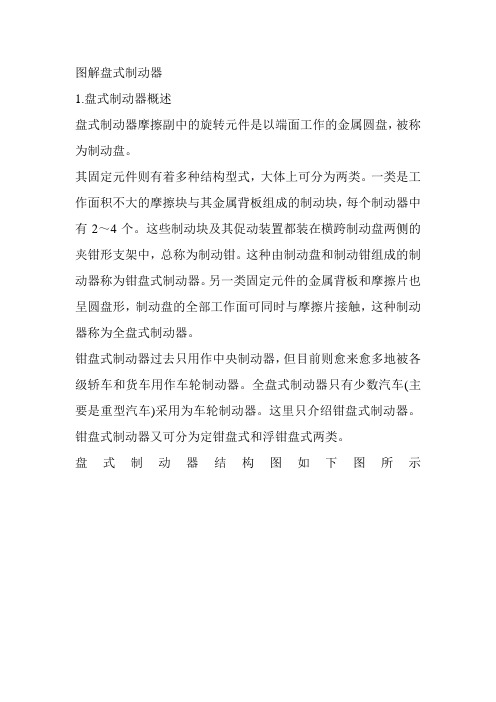
图解盘式制动器1.盘式制动器概述盘式制动器摩擦副中的旋转元件是以端面工作的金属圆盘,被称为制动盘。
其固定元件则有着多种结构型式,大体上可分为两类。
一类是工作面积不大的摩擦块与其金属背板组成的制动块,每个制动器中有2~4个。
这些制动块及其促动装置都装在横跨制动盘两侧的夹钳形支架中,总称为制动钳。
这种由制动盘和制动钳组成的制动器称为钳盘式制动器。
另一类固定元件的金属背板和摩擦片也呈圆盘形,制动盘的全部工作面可同时与摩擦片接触,这种制动器称为全盘式制动器。
钳盘式制动器过去只用作中央制动器,但目前则愈来愈多地被各级轿车和货车用作车轮制动器。
全盘式制动器只有少数汽车(主要是重型汽车)采用为车轮制动器。
这里只介绍钳盘式制动器。
钳盘式制动器又可分为定钳盘式和浮钳盘式两类。
盘式制动器结构图如下图所示2.定钳盘式制动器跨置在制动盘1上的制动钳体5固定安装在车桥6上,它不能旋转也不能沿制动盘轴线方向移动,其内的两个活塞2分别位于制动盘1的两侧。
制动时,制动油液由制动总泵(制动主缸)经进油口4进入钳体中两个相通的液压腔中,将两侧的制动块3压向与车轮固定连接的制动盘1,从而产生制动。
这种制动器存在着以下缺点:油缸较多,使制动钳结构复杂;油缸分置于制动盘两侧,必须用跨越制动盘的钳内油道或外部油管来连通,这使得制动钳的尺寸过大,难以安装在现代化轿车的轮辋内;热负荷大时,油缸和跨越制动盘的油管或油道中的制动液容易受热汽化;若要兼用于驻车制动,则必须加装一个机械促动的驻车制动钳。
定钳盘式制动器示意图1.制动盘2.活塞3.摩擦块4.进油口5.制动钳体6.车桥部3.浮钳盘式制动器制动钳体2通过导向销6与车桥7相连,可以相对于制动盘1轴向移动。
制动钳体只在制动盘的内侧设置油缸,而外侧的制动块则附装在钳体上。
制动时,液压油通过进油口5进入制动油缸,推动活塞4及其上的摩擦块向右移动,并压到制动盘上,并使得油缸连同制动钳体整体沿销钉向左移动,直到制动盘右侧的摩擦块也压到制动盘上夹住制动盘并使其制动。
《盘式制动器》PPT课件

精选ppt
2
精选ppt
3
盘式制动器
精选ppt
1
盘式制动器的主要部件包括: □制动衬块 □含有活塞的卡钳 □安装在轮毂上的转子
盘式制动器中,制动衬块挤压的是转子而不是车 轮,并且压力是液压传送而不是线缆传送的。 衬 块和盘片之间的摩擦会降低盘片的速度。
行驶中的汽车具有一定的动能,为了让汽车停止 下来,制动器必须将此能量从汽车中消除。 制动器如何做到这一点呢? 每当您停车时, 制动器都会将动能转化为由衬块与盘片之间的 摩擦产生的热能。大多数汽车的盘式制动器都带 有通风孔。
定钳盘式制动器的CAD图纸-装配-零件图++

定钳盘式制动器的CAD图纸装配零件图目录一、性能与用途 (1)二、结构特征与工作原理 (1)三、安装与调整 (4)四、使用与维护 (9)五、润滑 (12)六、特别警示 (13)七、故障原因及处理方法 (12)附图1:盘式制动器结构图 (15)附图2:盘形闸结构图 (16)附图3: 制动器限位开关结构图 (17)附图4: 盘式制动器的工作原理图 (18)附图5: 盘式制动器安装示意图 (19)附图6: 制动器信号装置安装示意图 (20)一、性能与用途盘式制动器是靠碟形弹簧产生制动力,用油压解除制动,制动力沿轴向作用的制动器。
盘式制动器和液压站、管路系统配套组成一套完整的制动系统。
适用于码头缆车、矿井提升机及其它提升设备,作工作制动和安全制动之用。
其制动力大小、使用维护、制动力调整对整个提升系统安全运行都具有重大的影响,安装、使用单位必须予以重视,确保运行安全。
盘式制动器具有以下特点:1、制动力矩具有良好的可调性;2、惯性小,动作快,灵敏度高;3、可靠性高;4、通用性好,盘式制动器有很多零件是通用的,并且不同的矿井提升机可配不同数量相同型号的盘式制动器;5、结构简单、维修调整方便。
二、结构特征与工作原理1、盘式制动器结构(图1)盘式制动器是由盘形闸(7)、支架(10)、油管(3)、(4)制动器信号装置(8)、螺栓(9)、配油接头(11)等组成。
盘形闸(7)由螺栓(9)成对地把紧在支架(10)上,每个支架上可以同时安装1、2、3、4对甚至更多对盘形闸,盘形闸的规格和对数根据提升机对制动力矩的大小需求来确定。
2、盘形闸结构(图2)盘形闸由制动块〔1〕、压板(2)、螺钉(3)、弹簧垫圈(4)、滑套(5)、碟形弹簧(6)、接头(7)、组合密封垫(8)、支架(9)、调节套(10)、油缸(11)、油缸盖(12)、盖(13)、放气螺栓(17)、放气螺钉(19)、O形密封圈(20)、Yx密封圈(21)、螺塞(22)、Yx密封圈(23)、压环(24)、活塞(25)、套筒(26)、联接螺钉(27)、键(28)及其它副件、标件等组成。
盘式制动器的设计
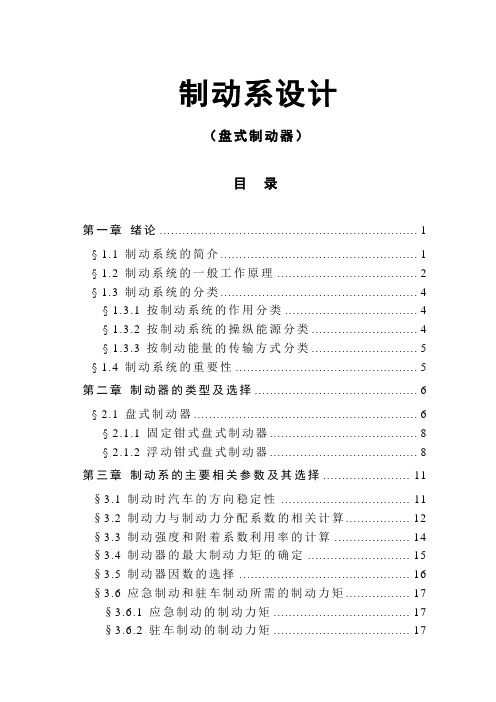
摩擦式制动器按其旋转元件的不同又可分为鼓式制动器和盘式制动器。盘式制动器和鼓式制动器的结构如下:
1.制动踏板 2.推杆 3.主缸活塞 4.制动主缸 5.油管 6.制动轮缸 7.轮缸活塞 8.制动鼓 9.摩擦片 10.制动蹄 11.制动底板 12.支承销 13.制动蹄回位弹簧
一个以内圆面为工作表面的金属制动鼓固定在车轮轮毂上,随车轮一同旋转。在固定不动的制动底板上,有两个支承销,支撑着两个弧形制动蹄的下端。制动蹄的外圆面上装有摩擦片。制动底板上还装有液压制动轮缸,用油管5与装在车架上的液压制动主缸相连通。主缸中的活塞3可由驾驶员通过制动踏板机构来操纵。
图2-1盘式制动器和鼓式制动器
本次设计车型为中档轿车,全部车轮选择盘式制动器,下面对其进行介绍和计算。
§
按摩擦副中固定元件的结构不同,盘式制动器分为钳盘式和全盘式两类。盘式制动器的结构如右图所示:
图2-2盘式制动器安装结构
钳盘式制动器(图2—3)的固定摩擦元件是制动块,装在与车轴连接且不能绕车轴轴线旋转的制动钳中。制动衬块与制动盘接触面很小,
2)水稳定性好。制动块对盘的单位压力高,易于将水挤出,因而浸水后效能降低不多;又由于离心力作用及衬块对盘的擦拭作用,出水后只需经一、二次制动即能恢复正常。鼓式制动器则需经十余次制动方能恢复。
3)制动力矩与汽车运动方向无关。
4)易于构成双回路制动系,使系统有较高的可靠性和安全性。
5)尺寸小、质量小、散热良好。
图1-1制动系统简单示意图
- 1、下载文档前请自行甄别文档内容的完整性,平台不提供额外的编辑、内容补充、找答案等附加服务。
- 2、"仅部分预览"的文档,不可在线预览部分如存在完整性等问题,可反馈申请退款(可完整预览的文档不适用该条件!)。
- 3、如文档侵犯您的权益,请联系客服反馈,我们会尽快为您处理(人工客服工作时间:9:00-18:30)。
摘
要
汽车制动系统是汽车各个系统中最为重要的。如果制动系统失灵,那么结果将会是毁 灭性的。制动器实际上是一个能量转化装置,这种转化实际上是把汽车的动能转换为汽车 的热能挥发出去,当制动器制动时,驱动程序来命令十倍于以往的力来使汽车停止下来。 制动系统可以发挥上千磅的压力来分配给四个制动器。 盘式制动器又称为碟式制动器,这种制动器散热快、重量轻、构造简单、调整方便, 特别是高负载时耐高温性能好,制动效果稳定,而且不怕泥水侵袭,在冬季和恶劣路况下 行车,盘式制动比鼓式制动更容易在较短的时间内令车停下。有些盘式制动器的制动盘上 还开了许多小孔,加速通风散热,提高制动效率。由制动器设计的一般原则,综合考虑制 动效能、制动效能稳定性、制动间隙调整简便性、制动器的尺寸和质量及噪声等诸多因素 设计本产品。在设计中涉及到同步系数的选取、制动器效能因素的选取、制动力矩的计算, 以及制动器主要元件选取,最后对设计的制动器进行校核计算。 关键词 :制动系统,盘式制动器(论文)通过答辩
目
录
摘 要··························································································································· I Abstract························································································································ II 第 1 章 绪论···············································································································1 1.1 盘式制动器的介绍与特点··············································································1 1.2 国内汽车盘式制动器应用情况······································································2 第 2 章 制动器的结构与设计原则···········································································4 2.1 汽车盘式制动器···························································································4 2.2 捷达轿车盘式制动器的结构与工作原理···················································5 2.3 制动器设计的一般原则···············································································7 2.3.1 制动驱动机构的选择············································································8 2.3.2 制动管路的选择····················································································8 本章小结··············································································································10 第 3 章 制动器设计·································································································11 3.1 盘式制动器主要元件····················································································11 3.1.1 制动盘··································································································11 3.1.2 制动钳··································································································12 3.1.3 制动块··································································································13 3.1.4 摩擦材料······························································································13 3.1.5 制动器间隙··························································································13 3.2 同步附着系数的选取····················································································14 3.3 制动器效能因数····························································································16 3.4 制动器受力分析与力矩计算········································································16 3.4.1 制动受力分析······················································································16 3.4.2 制动力矩的计算··················································································17 3.5 摩擦衬块的摩擦特性····················································································18 3.6 制动器液压驱动机构的设计计算································································20 本章小结··············································································································21 第 4 章 校核与技术要求·························································································22 4.1 制动器的热容量和温升的核算····································································22 4.2 制动器的调试································································································23 4.2.1 制动盘的技术要求··············································································23 4.2.2 制动钳技术总成要求··········································································23 4.2.3 前轮轮毂总成技术要求······································································24 4.3 总成装配拆卸与检查的技术要求································································25 本章小结··············································································································26 结 论···························································································································27 致 谢···························································································································28 参考文献·····················································································································29 附录 1 译文················································································································30 附录 2 英文参考资料································································································31