CNC机床钻孔、攻丝切削参数
CNC机床加工中的切削参数选择与优化

CNC机床加工中的切削参数选择与优化在CNC机床加工中,切削参数选择与优化是至关重要的一步。
正确的切削参数可以保证工件的质量,提高加工效率,同时还可以延长刀具的使用寿命。
本文将探讨CNC机床加工中的切削参数选择与优化的要点。
一、切削参数的选择在选择切削参数时,需要考虑以下几个方面:1.工件材料不同的工件材料对切削参数有着不同的要求。
一般来说,硬度较高的材料需要选择较大的进给量和切削速度,以保证切削效果。
而对于较软的材料,则需要选择较小的进给量和切削速度。
2.刀具材料和形状刀具的材料和形状也会影响切削参数的选择。
硬质合金刀具通常适用于高速切削,而高速钢刀具则适用于低速切削。
此外,刀具的形状也会对切削参数产生影响。
例如,球头刀具适合进行曲面加工,而平头刀具适合进行平面加工。
3.加工精度要求不同的加工精度要求也会对切削参数产生影响。
如果要求加工精度较高,就需要选择较小的进给量和切削速度,以提高加工的精度。
而如果加工精度要求较低,可以适当增大切削参数,以提高加工的效率。
二、切削参数的优化切削参数的优化可以通过试切试验和仿真模拟两种方法来进行。
1.试切试验试切试验是一种直接测量和比较不同切削参数效果的方法。
通过试切试验,可以找出切削参数与加工表面粗糙度、切削力等因素的关系。
根据试切试验的结果,可以调整切削参数,从而达到优化加工效果的目的。
2.仿真模拟仿真模拟是通过计算机软件对切削过程进行模拟和分析的方法。
通过仿真模拟,可以在不进行实际加工的情况下对不同的切削参数进行比较和优化。
仿真模拟可以节省时间和成本,并且可以预测加工结果,为切削参数的选择和优化提供依据。
三、切削参数的优化策略在进行切削参数的选择和优化时,可以采用以下几种常用的策略:1.保证切削稳定性切削过程中的稳定性对于保证加工质量和提高加工效率至关重要。
因此,在选择和优化切削参数时,要避免过大或过小的切削速度和进给量,以保证切削过程的稳定性。
2.控制切削温度切削过程中会产生大量的切削热量,如果温度过高,可能会导致刀具磨损加剧和工件变形。
CNC机床钻孔、攻丝切削参数_图文(精)

普通螺纹底孔刀号钻头转速钻头进给丝锥转速丝锥进给细螺纹底孔直径通用管螺纹底孔直径钻头转速钻头进给M4×0.7 3.33950901/4″11.5600160M5×0.8 4.24900904453562/8″15430120M6×155(198501804254251/2″18.7340100M8×1.25 6.76(208002005006253/4″24.2270150M10×1.58.57(21700300500750M12×1.2510.7M12×1.7510.28(22630280500875M16×1.514.5M16×213.99(23460220400800M20×1.518.5M20×2.517.410(24365180320800M20×1.518.5M24×32111(25340160250750M30X3.526.5250125200700M10×1912(26700180500500NPT1/8″8.7147001807、对丝锥:因为孔加工刀具对刀时是以钻尖或丝锥端中心为刀位点,攻螺纹时,由于丝锥切削部分有锥角,端部不能切出完整的牙型,注:若攻不通孔螺纹,底孔深度:D钻=h有效+0.7D+0.3D底孔。
6、对钻头加工倒角,大小采用估算法,手轮进给倒角,切削一定深度后,退出游标卡尺测量,一般比螺纹孔径大3-4mm。
CNC机床常用普通螺纹钻孔参数表丝锥钻入深度应大于螺纹有效深度。
一般可取:H丝=h有效+0.7D。
D为螺纹大径。
8、中心钻应短,有良好的刚度。
1、先铣削上表面,再加工螺纹,若表面无要求,则可不铣面。
加工过程:2、加工螺纹的方法:先用中心钻加工底孔的中心孔,再钻底孔,然后对底孔倒角,最后攻丝。
公司为提高效率,在点孔时,点的稍大些,连倒角一起做了。
各类数控刀具转速进给切削量吃刀量参数

各类数控刀具转速进给切削量吃刀量参数数控刀具的转速、进给和切削量是刀具切削加工的重要参数,对加工质量、效率和刀具寿命等方面均有影响。
下面将介绍不同类型的数控刀具的转速、进给和切削量。
1. 铣削参数:数控铣削是常见的数控加工方法之一,常用的铣削刀具包括立铣刀、面铣刀和无心线焊接铣刀等。
铣削刀具的转速范围较大,一般在500-8000转/分之间。
对于高硬度材料的加工,转速一般较低,对于切削困难的材料,可以适当降低转速。
进给量受到刀具直径和材料硬度的影响,通常在0.1-1mm/齿之间。
切削深度也受到切削稳定性的限制,一般在刀具直径的1/2左右。
2. 钻削参数:数控钻削是通过旋转的钻削刀具对工件进行钻孔加工。
钻削刀具的转速一般较高,取决于刀具材料、刃数和切削物材料等因素,通常在200-8000转/分之间。
进给量一般为0.05-0.5mm/转,可以根据材料硬度和孔径大小进行调整。
吃刀量一般为刀具直径的1/4-1/23. 镗削参数:数控镗削是通过旋转的镗刀对孔加工进行切削的一种方法。
镗削刀具的转速较低,一般在100-1000转/分之间。
进给量和切削速度的关系较大,进给量一般为0.1-1mm/转,可以根据材料硬度和切削稳定性进行调整。
镗刀一般为刀具直径的1/4-1/24.螺纹加工参数:螺纹加工是通过数控车削或数控铣削进行的。
螺纹加工的刀具转速一般较低,取决于螺纹规格和材料硬度等因素。
进给量一般为螺距的1/2-2倍之间。
切削深度一般为刀具螺纹高度的1/2左右。
总的来说,数控刀具的转速、进给和切削量等参数需要根据具体的加工要求和材料性质进行调整。
在实际生产中,需要根据材料硬度、刀具材料、切削稳定性和切削效率等因素进行综合考虑,以获得最佳的加工效果。
CNC机床加工中的钻削工艺参数优化与控制
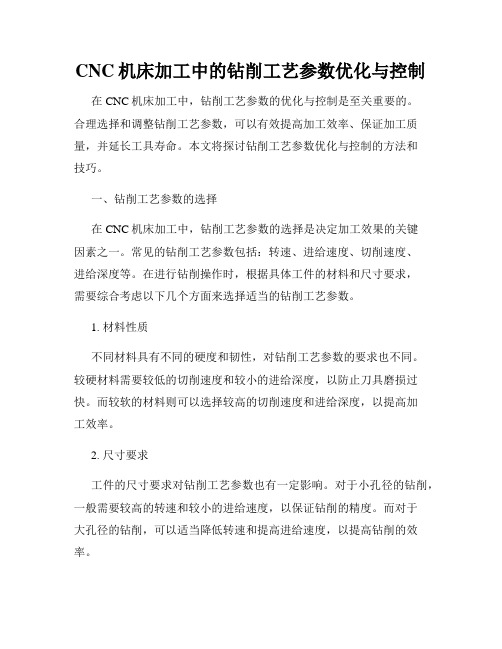
CNC机床加工中的钻削工艺参数优化与控制在CNC机床加工中,钻削工艺参数的优化与控制是至关重要的。
合理选择和调整钻削工艺参数,可以有效提高加工效率、保证加工质量,并延长工具寿命。
本文将探讨钻削工艺参数优化与控制的方法和技巧。
一、钻削工艺参数的选择在CNC机床加工中,钻削工艺参数的选择是决定加工效果的关键因素之一。
常见的钻削工艺参数包括:转速、进给速度、切削速度、进给深度等。
在进行钻削操作时,根据具体工件的材料和尺寸要求,需要综合考虑以下几个方面来选择适当的钻削工艺参数。
1. 材料性质不同材料具有不同的硬度和韧性,对钻削工艺参数的要求也不同。
较硬材料需要较低的切削速度和较小的进给深度,以防止刀具磨损过快。
而较软的材料则可以选择较高的切削速度和进给深度,以提高加工效率。
2. 尺寸要求工件的尺寸要求对钻削工艺参数也有一定影响。
对于小孔径的钻削,一般需要较高的转速和较小的进给速度,以保证钻削的精度。
而对于大孔径的钻削,可以适当降低转速和提高进给速度,以提高钻削的效率。
3. 加工效率要求加工效率是指单位时间内所能完成的工作量,对于有高效率要求的加工,可以选择较高的转速和进给速度。
但是要注意不能过度提高,否则容易导致刀具磨损严重,影响加工质量。
二、钻削工艺参数的优化方法在选择适当的钻削工艺参数之后,接下来就需要对其进行优化,以提高加工效率和质量。
以下是几种常见的钻削工艺参数优化方法。
1. 实验优化法实验优化法是指通过实际的钻削试验,对各种不同的钻削工艺参数组合进行测试和比较,以找到最佳的参数组合。
在进行实验时,需要根据预先设定的优化目标,如加工精度、加工效率等,来评估各组参数的优劣。
2. 数值模拟优化法数值模拟优化法是指通过利用数值仿真软件,建立钻削过程的数值模型,并对不同参数组合进行仿真分析,以求得最佳参数组合。
数值模拟方法可以节省实验成本和时间,并且可以对复杂情况进行模拟和研究。
3. 统计优化法统计优化法是指利用统计学方法和实验设计理论,对钻削工艺参数进行优化。
各类数控刀具转速进给切削量吃刀量参数

各类数控刀具转速进给切削量吃刀量参数数控刀具在加工过程中,转速、进给、切削量以及吃刀量是非常重要的参数。
这些参数的选择直接影响到加工效率和加工质量。
以下是各类数控刀具转速、进给、切削量和吃刀量的相关参数介绍。
1.钻头的转速、进给和切削量:钻头是一种主要用于钻孔加工的刀具。
在使用钻头进行加工时,转速、进给和切削量是必不可缺的参数。
转速:钻头的转速直接影响到加工的效率和刀具的使用寿命。
转速一般根据材料的硬度和直径大小来选择。
对于较硬的材料和大直径的钻孔,需要选择较低的转速以提高刀具的寿命。
进给:进给是指钻头在加工过程中前进的速度。
进给过大会导致切屑过大,反之则会导致切屑过细。
进给的选择需要根据具体材料来确定。
切削量:切削量是指钻头在一次进刀中切削的材料的厚度。
切削量的选择需要根据材料的硬度、强度和钻头的直径来确定。
过大的切削量容易导致刀具断裂,过小的切削量则会降低加工效率。
吃刀量:吃刀量是指钻头在加工过程中的进给量。
合适的吃刀量可以提高切削效率,但过大的吃刀量容易导致刀具断裂。
吃刀量的选择需要根据具体材料和钻头的直径来确定。
2.铣刀的转速、进给和切削量:铣刀是一种主要用于铣削加工的刀具。
在使用铣刀进行加工时,转速、进给和切削量同样是非常重要的参数。
转速:铣刀的转速需要根据具体材料和刀具的类型来确定。
对于硬度较高的材料,需要选择较低的转速以减少刀具磨损和提高加工质量。
进给:铣刀的进给速度直接影响到加工效率。
进给过大会导致切削力过大,进而影响加工表面质量。
进给过小则会降低加工效率。
进给的选择需要根据具体材料和刀具的直径和齿数来确定。
切削量:铣刀的切削量是指在一次进刀中切削的材料的厚度。
切削量的选择需要根据材料的硬度、强度和铣刀的直径和齿数来确定。
合适的切削量可以提高加工效率,但过大的切削量会导致刀具过载。
吃刀量:吃刀量是指铣刀在进给过程中每次移动的距离。
合适的吃刀量可以提高加工效率,但过大的吃刀量会导致切削力过大,刀具容易损坏。
常用CNC机床钻孔攻丝切削参数

常用CNC机床钻孔攻丝切削参数1. 切削速度(Cutting Speed)切削速度指的是工件表面上一点在单位时间内被切除的长度。
对于钻孔操作来说,切削速度可以用来控制钻头进给速度,通常以每分钟一些距离(mm/min)或每转一些距离(mm/rev)表示。
切削速度的选择应根据工件材料和刀具的硬度来确定。
2. 进给量(Feed Rate)进给量指的是工件和刀具之间相对运动过程中,刀具在单位时间内沿工件轴向移动的距离。
对于钻孔操作来说,进给量决定了钻孔的深度和速度,通常以每分钟一些距离(mm/min)表示。
进给量的选择应根据工件材料、刀具类型和加工要求来确定。
3. 主轴转速(Spindle Speed)主轴转速指的是主轴每分钟旋转的圈数,通常以转/分钟(rpm)表示。
主轴转速的选择应根据刀具直径、材料硬度和加工要求等因素来确定。
较小的刀具直径可选择较高的主轴转速,而大直径刀具则需要较低的转速。
4. 切削深度(Depth of Cut)切削深度指的是刀具进入工件的深度。
对于钻孔操作来说,切削深度由工件材料和创allenge参数所限制。
在进行钻孔操作时,应确保切削深度不超过钻头长度的80%,以避免过度切削,造成负载过大和刀具损坏。
5. 降刀速度(Plunge Rate)降刀速度指的是刀具从工件表面向下进入工件的速度。
对于钻孔操作来说,降刀速度通常选择较低的数值,以避免切削过快而导致刀具容易折断。
6. 切削液(Cutting Fluid)切削液是进行钻孔、攻丝和切削等操作时必不可少的润滑剂。
切削液的使用可以减少摩擦、冷却刀具、切削表面以及清洁切屑等功能,从而提高加工质量和刀具寿命。
除了上述参数,还有一些与具体机床和刀具相关的参数也需要考虑,例如进给速度、切削角度、切削力等。
在选择这些参数时,需要根据具体的工件和加工要求来进行调整,以保证加工质量和生产效率。
总结起来,CNC机床钻孔、攻丝和切削参数的选择应考虑工件材料、刀具类型、加工要求等因素,并结合实际应用进行合理调整。
CNC加工切削参数表

備註:
1.以上參數主要針對銅材(電極銅)設定,不適合其他材質.
2.球刀加工步距以表面粗糙度作为标准(祥見注解).
3.筋條精加工程序F以正常值的40%为參考,Ap以正常值的50%为參考.
4.標注La\Lb為安全值,如超出安全刃長和刀長則F以正常70%為參考.
5.此參數為永進機床參數,牧野機床S和F可以1.5~2倍的正常值為參考,原則上保證S和F的正比變化.
6.預留給精加工程式的餘量以0.05~0.2mm為宜,如留量過大,須考慮增加中加工或以正常F的70%為參考.
7.以上粗加工參數以等高加工模式為依據,精加工標注"側刃〞以側面加工模式為依據,標注〞平面〞以平面加工模式為依據 球刀以投影加工模式為依據,其他則以等高加工為依據.。
加工中心攻丝回退参数
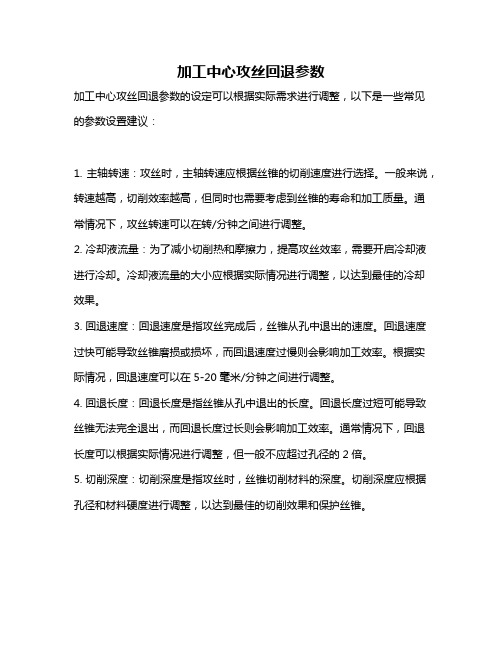
加工中心攻丝回退参数
加工中心攻丝回退参数的设定可以根据实际需求进行调整,以下是一些常见的参数设置建议:
1. 主轴转速:攻丝时,主轴转速应根据丝锥的切削速度进行选择。
一般来说,转速越高,切削效率越高,但同时也需要考虑到丝锥的寿命和加工质量。
通常情况下,攻丝转速可以在转/分钟之间进行调整。
2. 冷却液流量:为了减小切削热和摩擦力,提高攻丝效率,需要开启冷却液进行冷却。
冷却液流量的大小应根据实际情况进行调整,以达到最佳的冷却效果。
3. 回退速度:回退速度是指攻丝完成后,丝锥从孔中退出的速度。
回退速度过快可能导致丝锥磨损或损坏,而回退速度过慢则会影响加工效率。
根据实际情况,回退速度可以在5-20毫米/分钟之间进行调整。
4. 回退长度:回退长度是指丝锥从孔中退出的长度。
回退长度过短可能导致丝锥无法完全退出,而回退长度过长则会影响加工效率。
通常情况下,回退长度可以根据实际情况进行调整,但一般不应超过孔径的2倍。
5. 切削深度:切削深度是指攻丝时,丝锥切削材料的深度。
切削深度应根据孔径和材料硬度进行调整,以达到最佳的切削效果和保护丝锥。
这些参数的设置应根据具体设备和加工需求进行相应的调整。
建议在生产过程中对参数进行不断的优化和调整,以达到最佳的加工效果和保护设备。
CNC加工中心切削参数表

粗加工参数指材料 硬度在HRC30-50, 对于低0-50, 对于低于此硬度的 材料,切深可增大
刀长在200以下 刀长在200以下 刀长在200以下 刀长在200以下 刀长在200以下 刀长在200以下 刀长在160以下 刀长在160以下 刀长在160以下 刀长在160以下 刀长在160以下 刀长在160以下 刀长160-250 刀长160-250 刀长160-250 刀长160-250 刀长160-250 刀长160-250 刀长250-350 刀长250-350 刀长250-350 刀长250-350 刀长250-350 刀长250-350
0.8-2 36 1800 700-1000 4800 72 0.6 36 1800 1000 4800 72 0.5 36 800 1000 4800 72
0.3 0.5 1400 1400 600 0.225 0.3 0.5 1400 1200 600 0.225 0.3 0.5 1000 1200 600 0.225
E25R0.8 E25R0.8 E25R0.8 E25R0.8 E25R0.8 E25R0.8 E32R0.8 E32R0.8 E32R0.8 E32R0.8 E32R0.8 E32R0.8 E25R5 E25R5 E25R5 E25R5 E25R5 E25R5 E32R6 E32R6 E32R6 E32R6 E32R6 E32R6
普通 普通 普通 普通 普通 普通 普通 普通 普通 普通 普通 普通 普通 普通 普通 普通 普通 普通
aa(mm) ar(mm) F(mm/min) S(转/min) 寿命(min) 金属去除率 aa(mm) ar(mm) F(mm/min) S(转/min) 寿命(min) 金属去除率 aa(mm) ar(mm) F(mm/min) S(转/min) 寿命(min) 金属去除率
CNC加工中心精加工切削参数计算表

以下仅供参考
1.一般的选择原则是中等的每刃进给量,较小的轴向切深
p ,适当的径向切深
e
,高的切
削速度。
2.使用球刀的切削速度要高于平刀的切削速度。
3.刀具的伸出长度不能超过直径的4倍,刀具过长切削参数需往下调整
4.适用刀具直径:D4-D12
高速铣削加工用量的确定主要考虑加工效率、加工表面质量、刀具磨损以及加工成本。
不同刀具加工不同工件材料时,加工用量会有很大差异,目前尚无完整的加工数据,可根据实际选用的刀具和加工对象参考刀具厂商提供的加工用量选择。
二、切削速度的计算
Vc=(π*D*S)/1000
Vc:线速度(m/min) π:圆周率(3.14159) D:刀具直径(mm)
S:转速(rpm)
例题. 使用Φ25的铣刀Vc为(m/min)25 求S=?rpm
Vc=πds/1000
25=π*25*S/1000
S=1000*25/ π*25
S=320rpm
三、进给量(F值)的计算
F=S*Z*Fz
F:进给量(mm/min) S:转速(rpm) Z:刃数
Fz:(实际每刃进给)
例题.一标准2刃立铣刀以2000rpm)速度切削工件,求进给量(F
值)为多少?(Fz=0.25mm)
F=S*Z*Fz
F=2000*2*0.25
F=1000(mm/min)。
cnc攻丝
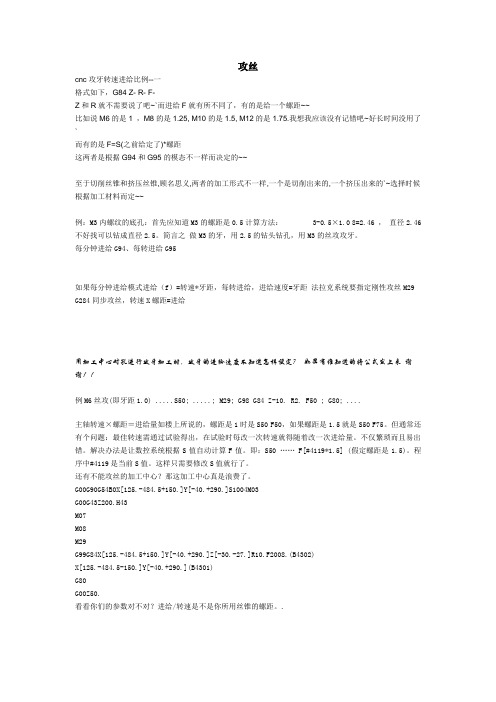
攻丝cnc攻牙转速进给比例--一格式如下,G84 Z- R- F-Z和R就不需要说了吧~`而进给F就有所不同了,有的是给一个螺距~~比如说M6的是1 ,M8的是1.25, M10的是1.5, M12的是1.75.我想我应该没有记错吧~好长时间没用了`而有的是F=S(之前给定了)*螺距这两者是根据G94和G95的模态不一样而决定的~~至于切削丝锥和挤压丝锥,顾名思义,两者的加工形式不一样,一个是切削出来的,一个挤压出来的`~选择时候根据加工材料而定~~例:M3内螺纹的底孔:首先应知道M3的螺距是0.5计算方法: 3-0.5×1.0 8=2.46 ,直径2.46不好找可以钻成直径2.5。
简言之做M3的牙,用2.5的钻头钻孔,用M3的丝攻攻牙。
每分钟进给G94、每转进给G95如果每分钟进给模式进给(f)=转速*牙距,每转进给,进给速度=牙距法拉克系统要指定刚性攻丝M29 G284同步攻丝,转速X螺距=进给用加工中心对孔进行攻牙加工时,攻牙的进给速度不知道怎样设定?如果有谁知道的将公式发上来谢谢!!例M6丝攻(即牙距1.0) .....S50; .....; M29; G98 G84 Z-10. R2. F50 ; G80; ....主轴转速×螺距=进给量如楼上所说的,螺距是1时是S50 F50,如果螺距是1.5就是S50 F75。
但通常还有个问题:最佳转速需通过试验得出,在试验时每改一次转速就得随着改一次进给量。
不仅繁琐而且易出错。
解决办法是让数控系统根据S值自动计算F值。
即:S50 …… F[#4119*1.5] (假定螺距是1.5)。
程序中#4119是当前S值。
这样只需要修改S值就行了。
还有不能攻丝的加工中心?那这加工中心真是浪费了。
G00G90G54B0X[125.-484.5+150.]Y[-40.+290.]S1004M03G00G43Z200.H43M07M08M29G99G84X[125.-484.5+150.]Y[-40.+290.]Z[-30.-27.]R10.F2008.(B4302)X[125.-484.5-150.]Y[-40.+290.](B4301)G80G00Z50.看看你们的参数对不对?进给/转速是不是你所用丝锥的螺距。
cnc攻牙转速对照表【免费下载】

在攻牙机上转速与孔的直径的关系攻牙机转的越慢攻的直径越大,这个与时间有关系,你攻丝的时候如果在里面攻的时间长一些攻的直径就越大,反之就小一些,这个是有限度的,当你速度快慢到一定程度就没什么区别了。
切削速度,受到丝攻材质、种类、吃入的牙数、下孔形状、切削材料及切削油等使用条件所左右,故其选用更有充分注意的必要。
cnc攻牙转速对照表如下:CNC铝材钻孔、攻牙标准参数表规格普通丝攻挤压丝攻底孔直径S F 底孔直径S FM1.0×0.25 0.75~0.78 120 0.25 0.86~0.88 400 0.25M1.2×0.25 0.95~0.98 150 0.25 1.06~1.08 450 0.25M1.4×0.3 1.1~1.14 210 0.3 1.24~1.25 500 0.3M1.6×0.35 1.25~1.32 280 0.35 1.41~1.43 560 0.35M1.5×0.35 1.15~1.2 250 0.35 \ 0.35 M2.0×0.4 1.6~1.68 360 0.4 1.78~1.80 600 0.4M2.5×0.45 2.1~2.14 320 0.45 2.25~2.28 550 0.45M3.0×0.5 2.5~2.6 300 0.5 2.73~2.75 500 0.5注:1、此表参数只限铝材攻牙;2、需氧化的产品,钻孔选择最小底孔直径;3、此表只供参考,加工中应按切削液浓度与攻牙深度适当调整转数;4、此表为G95攻牙模式;5、螺旋丝攻与普通丝攻参数基本一致,攻牙时转数可加倍。
攻牙机是一种在机件壳体、设备端面、螺母、法兰盘等各种具有不同规格的通孔或盲孔的零件的孔的内侧面加工出内螺纹、螺丝或叫牙扣的机械加工设备。
攻牙机也叫攻丝机、螺纹攻牙机、螺纹攻丝机、自动攻牙机等。
根据驱动动力种类的不同攻攻牙机牙机可以分为手动攻牙机、气动攻牙机、电动攻牙机、模内攻牙机和液压攻牙机等;根据攻牙机主轴数目不同可分为单轴攻牙机、二轴攻牙机、四轴攻牙机、六轴攻牙机、多轴攻牙机等;根据加工零件种类不同攻牙机又可分为模内攻牙机、万能攻牙机、热打螺母攻牙机、法兰螺母攻牙机、圆螺母攻牙机、六角螺母攻牙机、盲孔螺母攻牙机、防盗螺母攻牙机等多种型号;根据攻牙机加工过程的自动化程度不同攻牙机可分为全自动攻牙机、半自动攻牙机和手动攻牙机等;根据攻牙机攻牙时是否同时钻孔攻牙机又分钻孔攻牙机、扩孔攻牙机等。
CNC设备具体参数

12.4kVA
(29.4kVA)
气源
工作气压
0.4MPa~0.6MPa
所需流量
120L/min
机床尺寸
机床高度
mm
2,608mm
所需占地面积(控制装置门打开时)
mm
1,624mm×2,829mm
(2,114mm×2,829mm)
机床重量(包括控制装置和防护罩)
kg
2,300kg (2,400kg)
最大负载(均匀负载)重量
kg
250kg
主轴
主轴旋转速度
min-1
10~10,000
16~16,000
攻丝中主轴转速
min-1
MAX.6,000min-1
锥孔
7/24 No.30号锥度
进给速度
X×Y×Z轴快速移动速度
m/min
50m/min×50m/min×50m/min
切削进给速度
mm/minBiblioteka 1mm/min~10,000mm/min(X、Y)、1mm/min~20,000mm/min(Z)
精度*3
定位精度
mm
0.005mm/300mm
重复定位精度
mm
±0.003mm
正面门参数
1扇门
标准附件
1套操作说明书/4个地脚螺栓/4个水平垫板/1套保险丝
CNC设备具体参数:
机型
TC-S2Cz(TC-S2Cz-O)
10,000min-1
16,000min-1
CNC系统
CNC-B00
移动量
X轴移动量
mm
500mm (700mm)
Y轴移动量
mm
加工中心CNC切削参数表(大全)
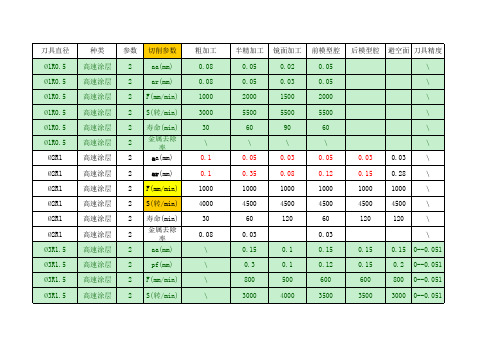
高速涂层 高速涂层 高速涂层 高速涂层 高速涂层 高速涂层 高速涂层 高速涂层 高速涂层 高速涂层 高速涂层 高速涂层 高速涂层 高速涂层 高速涂层
飞刀 飞刀
2 S(转/min)
\
1500
2 寿命(min)
\
60
2
金属去除 率
\
\
2
aa(mm)
\
0.3
2
ar(mm)
\
0.78
2 F(mm/min)
\
参数 切削参数
2
aa(mm)
2
ar(mm)
2 F(mm/min)
2 S(转/min)
2 寿命(min)
2
金属去除 率
2
aa(mm)
2
ar(mm)
2 F(mm/min)
2 S(转/min)
2 寿命(min)
2
金属去除 率
2
aa(mm)
2
pf(mm)
2 F(mm/min)
2 S(转/min)
粗加工 0.08 0.08 1000 3000 30
ar(mm)
\
Ø8R4
高速涂层 2 F(mm/min)
\
40
60
0.2 0.3 1000 3000 50
0.1 0.12 600 3500 70
0.3 0.6 1200 2000 60 \ 0.3 0.69 1100
0.15 0.15 1400 2200 90
\ 0.15 0.17 1300
40
0.1 0.18 800 3200 50
0.2 0.37 1400 1800 90
0.3 0.38
1500 0--0.051 90 0--0.051
- 1、下载文档前请自行甄别文档内容的完整性,平台不提供额外的编辑、内容补充、找答案等附加服务。
- 2、"仅部分预览"的文档,不可在线预览部分如存在完整性等问题,可反馈申请退款(可完整预览的文档不适用该条件!)。
- 3、如文档侵犯您的权益,请联系客服反馈,我们会尽快为您处理(人工客服工作时间:9:00-18:30)。
钻头转速 钻头进给 丝锥转速 丝锥进给 细螺纹 底孔直径 通用管螺 底孔直径 钻头转速 钻头进给 纹 1/4″ 11.5 600 160 2/8″ 15 430 120 1/2″ 18.7 340 100 3/4″ 24.2 270 150
M4×0.7 3.3 3 950 90 M5×0.8 4.2 4 900 90 445 356 M6×1 5 5(19) 850 180 425 425 M8×1.25 6.7 6(20) 800 200 500 625 M10×1.5 8.5 7(21) 700 300 500 750 M12×1.25 10.7 M12×1.75 10.2 8(22) 630 280 500 875 M16×1.5 14.5 M16×2 13.9 9(23) 460 220 400 800 M20×1.5 18.5 M20×2.5 17.4 10(24) 365 180 320 800 M20×1.5 18.5 M24×3 21 11(25) 340 160 250 750 M30X3.5 26.5 250 125 200 700 M10×1 9 12(26) 700 180 500 500 NPT1/8″ 8.7 700 180 14 加工过程: 1、先铣削上表面,再加工螺纹,若表面无要求,则可不铣面。 2、加工螺纹的方法:先用中心钻加工底孔的中心孔,再钻底孔,然后对底孔倒角,最后攻丝。 公司为提高效率,在点孔时,点的稍大些,连倒角一起做了。 3、孔加工循环的选择,中心钻选用G82,底孔加工选用G81,倒角选用G82,螺纹若是右旋,选用G84。 4、孔加工循环的高度平面选择:a:Z向R高度:对G81、G82,为螺纹孔上表面以上3-5mm,对G84应大些,为10mm以上。 b:初始平面高度:为螺纹孔上表面以上20mm。公司选用100mm。 5、孔底面高度:对底孔钻,考虑到钻头角度以及孔是通孔的因素,取螺纹孔下表面下方0.3D底孔。 注:若攻不通孔螺纹,底孔深度:D钻=h有效+0.7D+0.3D底孔。 6、对钻头加工倒角,大小采用估算法,手轮进给倒角,切削一定深度后,退出游标卡尺测量,一般比螺纹孔径大3-4mm。 7、对丝锥:因为孔加工刀具对刀时是以钻尖或丝锥端中心为刀位点,攻螺纹时,由于丝锥切削部分有锥角,端部不能切出完整的牙型, 丝锥钻入深度应大于螺纹有效深度。一般可取:H丝=h有效+0.7D。D为螺纹大径。 8、中心钻应短,有良好的刚度。