数控机床加工的切削用量
浅谈数控车床削切用量的教学方法
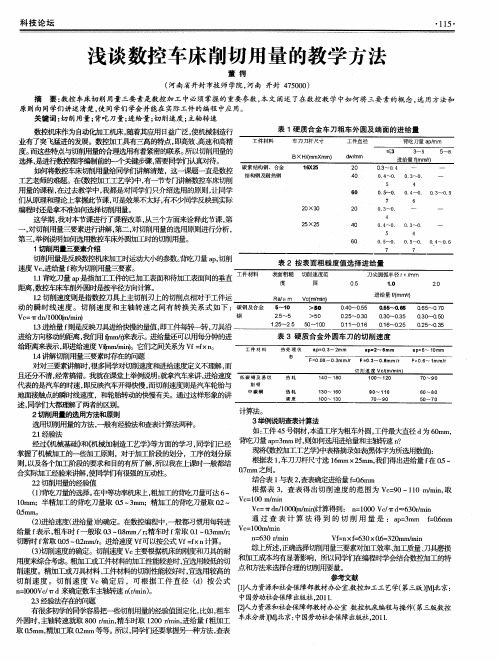
表 1硬质 合金 车刀粗车外圆及端面的进给量 娄 l d 空 【 床作为 自 b 化b 口 】 : 机床, 蓄 日 日 益广泛, 琉 0 造彳 亍 业有了突飞猛进的发展。数控加工具有三高的特点 , 即高效、 高速和高精 度。 而这些特 点与切削用量的 圆左 用有着紧密的联系。 所以切削用量的 选择, 是进行数控程序编制前的— 藩 涉 骤, 需要同学f 『 人 真对待。 碳 素 结构钢 、合金 1 6 X 2 5 2 0 0 3 ~0 . 4 ~ 一 这—课题一直是数控 结构钢 及耐热钢 4 0 0 . 4 ~0 . 0 . 3 - - - - 0 — 工艺老师的难题。在 控加工工艺学》 中, 有—节专门讲解数控车床切削 5 4 用量的课程 , 在过去教学中, 我都是对同学们只介绍选用的原则, 让同学 6 0 0 . 5 ~0 . 0 . 4 ~0 . n 3 ~O . 5 7 6 们从原理和理论 匕 掌握I H , 廿课, 可是效果不太好, 有不少同学反映到实际 20× 3 0 20 0. 3~0. 一 一 编程时还是拿不准如何选择切削用量。 4 这学期 , 我对本节课进行了课程改革, 从三个方面来诠释此节课 , 第 2 5×2 5 4 0 0 . 4 ~0 0 3 " - - - 0 — 对切削用量三要素进行讲解, 第二 , 对切削用量的选用厉 狈0 进行分析, 5 4 第三 , 举例说明如何j 用数控车床外圆加工时的切削用量。 60 0. 5 ~ O. 0. 5 ~0 . n 4~ O . 6 7 7 1 切削用量三要素介绍 切削用量是反映数控机床加工时运动大小的参数。  ̄ ̄ z _ - 3 3 量 印, 切削 表 2 按 表 面 粗 糙 度 值选 择进 给 量 速度 V c , 进给量 f 称为切削用量三要素。 1 . 1 背吃刀量 a p 是指加工工件的已加工表面和待加工表面间的垂直 距离 , 数控车床车削外圆时是按半径方向计算。 l 2切削速度则是指数控刀具上主切削刃上的切削点相对于工件运 O >5 0 0 4 0 ~0 5 5 S 5 ~ 铬 0 6 5 ~0 7 0 动 的瞬时线 速度 。切 削速度 和主轴转 速之 间有转换 关系式 如下 : 碳 钢及 合金 5~1
数控机床加工的切削用量

数控机床加工的切削用量包括切削速度V c (或主轴转速n)、切削深度a p 和进给量f ,其选用原则与普通机床基本相似,合理选择切削用量的原则是:粗加工时,以提高劳动生产率为主,选用较大的切削量;半精加工和精加工时,选用较小的切削量,保证工件的加工质量。
1. 数控车床切削用量 1)切削深度a p在工艺系统刚性和机床功率允许的条件下,尽可能选取较大的切削深度,以减少进给次数。
当工件的精度要求较高时,则应考虑留有精加工余量,一般为0.1~0.5mm 。
切削深度ap 计算公式:a p =式中: d w —待加工表面外圆直径,单位mm d m —已加工表面外圆直径,单位mm. 2)切削速度Vc① 车削光轴切削速度V c 光车切削速度由工件材料、刀具的材料及加工性质等因素所确定,表1为硬质合金外圆车刀切削速度参考表。
切削速度Vc 计算公式: Vc=式中: d —工件或刀尖的回转直径,单位mm n —工件或刀具的转速,单位r/min表1 硬质合金外圆车刀切削速度参考表2mw d d注:表中刀具材料切削钢及灰铸铁时耐用度约为60min。
②车削螺纹主轴转速n切削螺纹时,车床的主轴转速受加工工件的螺距(或导程)大小、驱动电动机升降特性及螺纹插补运算速度等多种因素影响,因此对于不同的数控系统,选择车削螺纹主轴转速n存在一定的差异。
下列为一般数控车床车螺纹时主轴转速计算公式:n≤–k式中:p—工件螺纹的螺距或导程,单位mm。
k—保险系数,一般为80。
3)进给速度进给速度是指单位时间内,刀具沿进给方向移动的距离,单位为mm/min,也可表示为主轴旋转一周刀具的进给量,单位为mm/r。
⑴确定进给速度的原则①当工件的加工质量能得到保证时,为提高生产率可选择较高的进给速度。
②切断、车削深孔或精车时,选择较低的进给速度。
③刀具空行程尽量选用高的进给速度。
④进给速度应与主轴转速和切削深度相适应。
⑵进给速度V f的计算V f = n f式中:n—车床主轴的转速,单位r/min。
数控机床加工的切削用量

单元4数控机床加工的切削用量教学目的1、了解数控机床的运动(主运动、进给运动);2、了解数控机床加工刀具的角度及其作用;3、了解数控机床加工中有关切削层的参数及其作用;4、了解数控机床加工中的切削用量及其选用原则。
5、掌握常用不同材料零件在粗加工、半精加工和精加工时的切削用量选用;教学重点1、数控机床加工刀具的角度及其作用;2、数控加工中粗加工、半精加工和精加工时的切削用量选择;教学难点1、刀具的角度及其作用;2、切削用量选用教学方法讲练结合教学内容一、车削加工与刀具1. 车削加工原理在普通车床和一般数控车床上,可以进行工件的外表面、端面、内表面以及内外螺纹的加工。
对于车削中心,除上述各种加工外,还可进行铳削、钻削等加工。
从上述介绍可以看出:在切削过程中,刀具和工件之间必须具有相对运动,这种相对运动称为切削运动。
根据切削运动在切削过程中的作用不同可以分为主运动、和进给运动。
各种机床的主运动和进给运动参见下表。
主运动是指机床提供的主要运动。
主运动使刀具和工件之间产生相对运动,从而使刀具的前刀面接近工件并对工件进行切削。
在车床上,主运动是机床上主轴的回转运动,即车削加工时工件的旋转运动。
2)进给运动进给运动是指由机床提供的使刀具与工件之间产生的附加相对运动。
进给运动与主运动相配合,可以形成完整的切削加工。
在普通车床上,进给运动是机床刀架(溜板)的直线移动。
它可以是纵向的移动(与机床主轴轴线平行),也可以是横向的移功(与机床主轴轴线垂直),但只能是一亇方向的移动。
在数控车床上,数控车床可以同时实现两亇方向的进给,从而加工出各种具有复杂母线的回转体工件。
在数控车床中,主运动和进给运动是由不同的电机来驱动的,分别称为主轴电机和坐标轴伺服电机。
它们由机床的控制系统进行控制,自动完成切削加工。
2. 切削用量切削用量是指机床在切削加工时的状态参数。
不同类型的机床对切削用量参数的表述也略有不同,但其基本的含义都是一致的,如下图所示。
4.4切削用量的选择数控车削加工中的切削用量包括背吃刀量
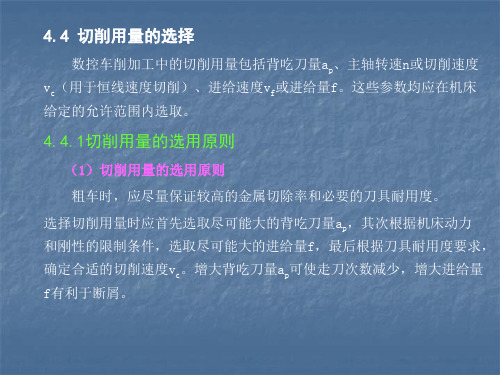
图4-24为车圆弧的阶梯走刀路线。
图4-25(a)为车圆弧的同心圆弧走刀路线。
图4-24 阶梯走刀路线车圆弧
图4-25
同心圆弧走刀路线车圆弧
图4-27为车圆弧的车锥法切削路线
即先车一个圆锥,再车圆弧。
图4-27 车锥法走刀路线车圆弧
(2)车圆锥的走刀路线分析
图4-26 车圆锥走刀路线
(3)车螺纹时轴向进给距离的分析
(4)按安装次数划分工序 以一次安装完成的那一部分工艺过程为一道工序。这种方法适
用于工件的加工内容不多的工件,加工完成后就能达到待检状态。
如图4-21所示工件,工序一:以毛坯的粗基准定位加工左端轮廓; 工序二:以加工好的外圆表面定位加工右端轮廓。
图4-21 轴类零件分析
4.5.3加工顺序的确定
在对零件图进行认真和仔细的分析后,制定加工方案应遵循以 下基本原则——先粗后精,先近后远,内外交叉,程序段最少,走
表4-4 常用切削用量推荐表
工件材料
加工内容
背吃刀量 ap/mm 5-7
切削速度 vc/m· min-1 60~80
进给量 f/mm· r-lσb>600MPa
粗加工
精加工 钻中心孔
2-3
2-6
80~120
120~150 500~800r· min-1
0.2~0.4
表4-3 硬质合金刀具切削用量推荐表
粗 加 工 刀具 材料 工件材料 切削速度 (m/min) 220 180 120 80 80 40 120 100 1600 进给量 (mm/r) 0.2 0.2 0.2 0.2 0.2 0.2 0.2 背吃刀量 mm 3 3 3 3 3 3 2 切削速度 (m/min) 260 220 220 160 140 · 140 120 精 加 工 进给量 (mm/r) 0.l 0.l 0.1 0.l 0.l 0.1 0.l 背吃刀量 mm 0.4 0.4 0.4 0.4 0.4 0.4 0.5 0.5 0.5
数控加工的切削用量

数控加工的切削用量2009-6-11 9:42:00 来源:作者:余英良,于辉阅读:1418次我要收藏1 切削用量选择1.1 数控加工花键轴的切削用量为了保证零件的加工精度,零件分为粗车加工和精车加工。
在粗、精车零件装夹方式与刀具选择的基础上,选定零件数控加工的切削参数如下:在数控精车车削加工中,零件轮廓轨迹的加工余量为0.8÷2=0.4 mm。
主轴转速、背吃刀量等的选择参见表1。
表1 数控加工花键轴工序卡及切削用量1.2 数控加工轴承座的切削用量为了保证零件的加工精度,零件分为粗车加工和精车加工。
在粗、精车零件装夹方式与刀具选择的基础上,选定零件数控加工的切削参数如下:在数控精车车削加工中,零件轮廓轨迹的加工余量为0.8÷2=0.4 mm。
主轴转速、背吃刀量等的选择参见表2。
表2 数控加工轴承座工序卡及切削用量2 相关内容概述金属切削加工的目的,就是用各种类型的金属切削刀具把J:件毛坯上的多余部分从毛坯上剥离开来,得到图样所要求的零件形状和尺寸。
图1 车削加工中切削用量nextpage 2.1 切削用量切削用量是指机床在切削加工时的状态参数。
切削用量包括切削速度、进给速度和背吃刀量。
参见图1。
2.1.1 切削速度切削刃上的切削点相对于工件运动的瞬时速度称为切削速度。
切削速度的单位为m/min。
切削速度与机床主轴转速之问进行转换的关系为:(1)2.1.2 进给速度是刀具在单位时间内沿进给方向上相对于工件的位移量,单位为mm/min。
2.1.3 背吃刀量己加工表面和待加工表面之问的垂直距离。
背吃刀量的计算公式为:(2)式(1)、式(2)中n为主轴(工件)转速,d为工件直径,dω、dm见图1。
在切削加工中,切削速度、进给速度和背吃刀量3个参数是相互关联的。
粗加工中,为提高效率,一般采用较大的背吃刀量。
此时切削速度和进给速度相对较小;在半精加工和精加工阶段,一般采用较大的切削速度、较小的进给量和背吃刀量,以获得较好的加工质量。
切削用量的确定

总之,切削用量的具体数值应根机床性 能、相关的手册并结合实际经验用类比方 法确定。同时,使主轴转速、切削深度及 进给速度三者能相互适应,以形成最佳切 削用量。
2.进给速度的确定 进给速度是数控机 床切削用量中的重要参数,主要根据零件 的加工精度和表面粗糙度要求以及刀具、 工件的材料性质选取。最大进给速度受机 床刚度和进给系统的性能限制。确定进给 速度的原则:
1)当工件的质量要求能够得到保证时, 为提高生产效率,可选择较高的进给速度。 一般在100200mm/min范围内选取。
1.主轴转速的确定主轴转速应根据允许的 切削速度和工件(或刀具)直径来选择。 其计算公式为: n=1000v/πD 式中 v---切削速度,单位为m/min,由刀具的耐用 度决定;n-- -主轴转速,单位为 r/min; D----工件直径或刀具直径,单位为mm。 计算的主轴转速n最后要根据机床说明书选 取机床有的或较接近的转速。
2)在切断、加工深孔或用高速钢刀具加 工时,宜选择较低的进给速度,一般在 20~50mm/min范围内选取。
高时,进给速度应选小些,一般在20~ 50mm/min范围内选取。
3)刀具空行程时,特别是远距离“回零” 时,可以设定该机床数控系统设定的最高 进给速度。
3.背吃刀量确定 背吃刀量根据机床、 工件和刀具的刚度来决定,在刚度允许的 条件下,应尽可能使背吃刀量等于工件的
切削用量的确定
数控编程时,编程人员必须确定每道 工序的切削用量,并以指令的形式写入程 序中。切削用量包括主轴转速、背吃刀量 及进给速度等。对于不同的加工方法,需 要选用不同的切削用量。切削用量的选择 原则是:保证零件加工精度和表面粗糙度, 充分发挥刀具切削性能,保证合理的刀具 耐用度;并充分发挥机床的性能,最大限 度提高生产率,降低成本。
浅谈数控加工工艺中切削用量的选择

技 术 应 用
浅谈数控 加工工艺中切 削用量的选择
周靖 明 刘 凡( 铁山 中 桥集团 高级技工 学校, 河北 秦皇岛 060 625 )
摘 要 : 削用量是控制 数控机 床 加工质 量好坏 的关键性 因素, 切 而切 削用量 由背吃 刀量、 削速 度 和进 给 量这 三个要 素组 成 , 切 因此 刀具 的
进给量 是切削用量 中的第二要素, 进给量 的大小就决定了 度 的前 提是选择合 理的切削用量 , 理的切 削用量可以将刀具 零件的加工精度和表面粗糙度, 合 而工件材料和刀具 的耐磨度又 切削性能和机床性能发挥到极致 , 如此就降低了加工成 本还提 决定了进给 量的范围。 多齿刀具中, 在 刀具转速 n 、进给 速度 高了切削效率。 不同的加工种类 , 切削用量的选 择也不相 同, 当 v 、 f每齿进给量 f 和刀具齿数 z之 间有这样 一个 关系式:。 z 加工 的工件为粗 加工时, 在保证加 工成 本的前提下尽量提高生 粗加工对工件表面质量 的要求不高, 在切削中刀杆、 床、 机 产 效率。因此在 背吃刀量的选择上要尽可能的加大, 进给量 的 刀片、 工件 等工具的刚度就决 定了走 刀的进 给量 , 因此进 给量
精确度和 自动化程 度都 比较高, 属于机 电一体化 的加工设备 。
在进行粗 加工时, 在保证精加工和半精加工所 需加工余量
数控加工需要把加工零件的图纸作为加工依据来设置相应 的工 的前 提下, 用走 刀一次性将 多余余 量削除, 当余量过 大或者 背 艺, 程序员将工 艺参数编织 为加工程序 输入 程序控 制系统, 控 吃刀量超 出了工艺系统 刚性范围时, 刀切除尽可能的由大 到 走 制 系统会控 制相应 的工件、工具对 零件进行加 工。 但是 , 控 小, 别是第_刀应该让刀 口尽量靠近 里层 , 数 特 这样可以提高工件 机 床加工中的数控编程仍然 是个 急需解决 的问题 , 程序 员根据 表面的平整度 , 同时也可 以减 少接触硬 皮铸 锻件。 若工艺系 统 工艺要求 编写加工程序 时需要处于人机交互 的状态, 这样确定 的刚度较差或者冲 击载荷较大, 作者可降低背吃刀量 从而减 操 的切削用量才 能将误差 降至最低 。 以编程员在数 控编程 中起 小切 削力 。 所 着关键性 的作用, 必须具有一定的实践经验和 切削用量 的确定 当零 件需要进行精加工时, 背吃刀量 选择是根 据粗加工后 原则 , 数控机床 的应 用不仅保证了加工质量 且保证了加工 的效 的加 工余量确定的, 在加工过 程中可逐渐 降低背 吃刀量 , 样 这 率, 是促进数控机床 的产业化实现企业 生产水平和经济效益提 不仅可以提高加工质量还可 以提高加工精度。 在进 行精加工时
数控加工中切削用量的合理选择

数控加工中切削用量的合理选择【摘要】文章介绍了切削用量的三要素,并对数控机床加工时切削用量的合理选择进行了详细阐述,为数控机床编程与操作人员提供参考。
关键词】切削用量;加工质量;刀具耐用度;选择原则前言:数控加工中切削用量的原则是,粗加工时,一般以提高生产率为主,但也应考虑经济和加工成本;半精加工和精加工时,应在保证加工质量的前提下,兼顾切削效率、经济性和加工成本。
具体数值应根据机床说明书、切削用量手册,并结合经验而定。
切削用量是表示机床主运动和进给运动大小的重要参数。
切削用量的确定是数控加工工艺中的重要内容,切削用量的大小对加工效率、加工质量、刀具磨损和加工成本均有显著影响一、切削用量的选择原则数控加工中选择切削用量,就是在保证加工质量和刀具耐用度的前提下,充分发挥机床性能和刀具切削性能,使切削效率最高,加工成本最低。
(一)加工质量:加工质量分为加工精度和加工表面质量。
1•加工精度是指零件加工后实际几何参数(尺寸、形状和位置)与理想几何参数相符的程度。
符合程度愈高,加工精度愈高。
实际值与理想值之差称为加工误差,所谓保证加工精度,即指控制加工误差。
⑴尺寸精度:加工表面的实际尺寸与设计尺寸的尺寸误差不超过一定的尺寸公差范围。
在国标中尺寸公差分20级(IT01、ITO、IT1〜IT18 )。
尺寸精度的获得方法:①试切法:试切一一测量一一调整一一再试切。
用于单件小批生产。
②调整法:通过预调好的机床、夹具、刀具、工件,在加工中自行获得尺寸精度。
用于成批大量生产。
③尺寸刀具法:用一定形状和尺寸的刀具加工获得。
生产率高,但刀具制造复杂。
④自动控制法:用一定装置,边加工边自动测量控制加工。
切削测量补偿调整。
⑵几何形状精度:加工表面的实际几何要素对理想几何要素的变动量不超过一定公差范围。
在国标中形状公差有六项:直线度、平面度、圆度、圆柱度、线轮廓度、面轮廓度。
几何形状精度的获得方法:成形运动法①轨迹法:利用刀具与工件间的相对运动轨迹来获得形状。
数控机床加工的切削用量

数控机床加工的切削用量包括切削速度V c (或主轴转速n)、切削深度a p 和进给量f ,其选用原则与普通机床基本相似,合理选择切削用量的原则是:粗加工时,以提高劳动生产率为主,选用较大的切削量;半精加工和精加工时,选用较小的切削量,保证工件的加工质量。
1. 数控车床切削用量 1)切削深度a p在工艺系统刚性和机床功率允许的条件下,尽可能选取较大的切削深度,以减少进给次数。
当工件的精度要求较高时,则应考虑留有精加工余量,一般为0.1~0.5mm 。
切削深度ap计算公式:a p =式中: d w —待加工表面外圆直径,单位mm d m —已加工表面外圆直径,单位mm. 2)切削速度Vc① 车削光轴切削速度V c 光车切削速度由工件材料、刀具的材料及加工性质等因素所确定,表1为硬质合金外圆车刀切削速度参考表。
切削速度Vc 计算公式: Vc=式中: d —工件或刀尖的回转直径,单位mm n —工件或刀具的转速,单位r/min表1 硬质合金外圆车刀切削速度参考表2mw d d注:表中刀具材料切削钢及灰铸铁时耐用度约为60min。
②车削螺纹主轴转速n切削螺纹时,车床的主轴转速受加工工件的螺距(或导程)大小、驱动电动机升降特性及螺纹插补运算速度等多种因素影响,因此对于不同的数控系统,选择车削螺纹主轴转速n存在一定的差异。
下列为一般数控车床车螺纹时主轴转速计算公式:n≤–k式中:p—工件螺纹的螺距或导程,单位mm。
k—保险系数,一般为80。
3)进给速度进给速度是指单位时间内,刀具沿进给方向移动的距离,单位为mm/min,也可表示为主轴旋转一周刀具的进给量,单位为mm/r。
⑴确定进给速度的原则①当工件的加工质量能得到保证时,为提高生产率可选择较高的进给速度。
②切断、车削深孔或精车时,选择较低的进给速度。
③刀具空行程尽量选用高的进给速度。
④进给速度应与主轴转速和切削深度相适应。
⑵进给速度V f的计算 V f = n f式中:n—车床主轴的转速,单位r/min。
关于数控加工中的刀具和切削用量的探讨

粗加工时 , 在留下精 加工 、 半精加工 的余量后 , 尽可能一次走刀将 剩下 的余量切除 :若工艺系统 刚性不足或余量过大不能一次切除 . 也 1刀 具 的选 择 . 应按先多后少的不等余量法加工 第一刀的 a 应尽可能大些 . 口 p 使刀 数控铣 加工刀具种类很 多 . 了适应数控机床 高速、 为 高效和 自 动 在 里层切 削. 避免工件表面不平及有硬皮 的铸锻件 化程度高的特点 . 所用刀具 正朝 着标准化 、 用化和模块化的方 向发 通 当冲击载荷较 大 ( 如断续 表面) 或工艺系统刚度 较差 ( 如细长轴 、 展. 主要包括铣 削刀具和孑 加工刀具两大类 为 了满足高效和特殊 的 镗刀杆、 L 机床陈 旧) , 时 可适当降低 a , p使切削力减小 。 铣 削要求 . 又发展 了各种特殊用途 的专用刀具 数控铣刀具 的分类有 精加工时 . 应根 据粗加工 留下的余量确定 。 a p 采用逐渐降低 a p的 多种方法 。 根据刀具结构可分为 : 整体式 : ① ②镶嵌式 , 采用焊接或机 方法 .逐步提高加工精度 和表面质量 一般精加 工时 .取 a = . ~ p 0 5 0 夹 式连接 , 机夹式又可分为不转位 和可转位两种 : ③特殊型式 , 如复合 O8 半精 加工 时. a= .~ .m . mm: 取 p 1 3O m 0
至可以决定着机床 功效 的发挥和安全生产的顺利进行 。 所以, 编制加 工程序 时, 在 选择合 理的刀具和切 削用量 , 是编制高质 量加 工程序的前提 。 文章对数控机床加 工时切 削用量的合理选择进行 了详细 阐述 . 【 关键词】 刀具; 高速加工; 数控 要求; ; 削用量 选择 切
车削加工切削用量的选择

数控机床加生产效率为主,但也应考 率加工成本;半精加工和精加工的切削用量应以保证加工质量 为前提,并兼顾切削效率和加工成本。粗车和半精车切削用量 的具体选择方法介绍如下: (1)粗车切削用量选择
数控机床加工的切削用量
2)进给量f
当背吃刀量确定后,再选出进给量f ,就能计算切削力。 该力作用在工件、机床和刀具上,应为它们的刚度和强度所 允许。也就是说,应在不损坏刀片和刀杆、不损坏机床进给 机构、不顶弯工件和不产生振动的条件下,选取一个最大的 进给量f 值。或者利用确定的和f ,求出主切削力Fz,来校验 刀片和刀杆的强度;根据计算出的切深抗力Fy来校验工件的 刚度;根据计算出的进给抗力Fx来校验机床进给机构薄弱环 节的强度等。
数控机床编程与操作
半精车和精车的背吃刀量较小,产生的切削力不大,所
以增大进给量主要受到表面粗糙度限制。在已知的切削速度v
(预先假设)和刀尖圆弧半径条件下,根据加工要求达到的 表面粗糙度,可利用计算的方法或手册资料确定进给量。
数控机床加工的切削用量
3)切削速度Vc
半精车、精车的背吃刀量和进给量f 较小,切削力对工艺系 统强度和刚度影响较小,消耗功率较少,故切削速度Vc主要受 刀具耐用度限制。需要注意的是,交流变频调速的数控车床低 速输出力矩较小,因此切削速度不能太低。
按上述原则,可利用计算的方法或查手册资料来确定进 给量f 值。 3)切削速度v
在背吃刀量和进给量选定后,根据规定达到的合理耐用度 值,就可确定切削速度v。
数控机床加工的切削用量
1.切削用量选择原则
a 要提高生产效率应尽量增大背吃刀量 p、进给量f 和切
削速度 v 。事实上,在提高切削用量时会受到切削力、切削
浅谈数控车床加工中切削用量的选择

在 数 控 车 床 加 工 中 , 削 用 量 的 合 理 切 选择 , 接 影 响 工 件 的 加 工 质量 、 响 刀具 直 影
2 切 削用量选择原则
的 使 用 寿 命 、 响零 件 的 加 工成 本 , 终 影 影 最 响 整 个 产 品 的 质量 和 成 本 。 文 针 对 数 控 式输 入 到 程 序 中 , 削 用 量 的 合 理选 择 是 后 的 的零 件 , 量 很 少 , 是 要求 通 过 加 工 本 切 余 但 车 床 中切 削 用 量 选 择 原 则 及 方 法 加 以 论 零 件 表 面 质量 、 寸 精 度 , 位 公 差 、 工 后 对 其表 面 质量 、 寸 精 度 、 尺 形 加 尺 形位 公差 等 符
下 综 合 因素 的 影 响 : 1 刀 具 差 异 的 影 响—— 不 同 的 刀具 厂 ) 于表 面质量 的要 求不 严格 , 在加 工 过 家 生 产 的 刀 具 质量 差 异 很 大 , 以 切 削 用 所
反 而 会 影 响 生 产效 率 。 因此 , 理 地 选 择 切 合 削 用量 , 数控 编 程人 员和 操作 人 员在 进 行 是 编 程 中 必 须 要 考 虑 的 一个 重 要 问题 。
摘 要: 在数 控 车床 加 工 中, 削用量 的合理选择 , 切 直接 影响 工件 的加工 质量 , 影响 刀具的使 用寿命 . 影响零件 的加工 成本 , 最终 影响 整 个 产品 的质量和 成本 。 IF N C 0 系统 的数控 车床 为倒 , 绍数控 车床 粗加 工时切 削用量 的选 择 原则 . 加工时 切削 用量 的选择 原 现 , A U i  ̄ 介 精
Sci ence an Techn o I novaton d ol gy n i He al r d
数控车床切削用量的选择
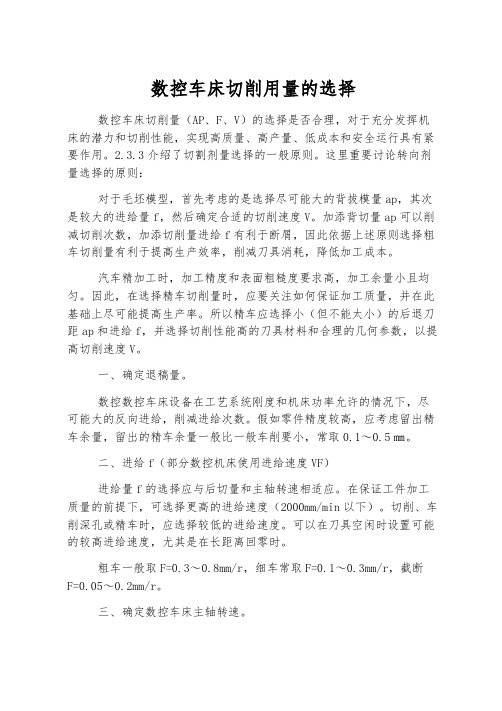
数控车床切削用量的选择数控车床切削量(AP、F、V)的选择是否合理,对于充分发挥机床的潜力和切削性能,实现高质量、高产量、低成本和安全运行具有紧要作用。
2.3.3介绍了切割剂量选择的一般原则。
这里重要讨论转向剂量选择的原则:对于毛坯模型,首先考虑的是选择尽可能大的背拔模量ap,其次是较大的进给量f,然后确定合适的切削速度V。
加添背切量ap可以削减切削次数,加添切削量进给f有利于断屑,因此依据上述原则选择粗车切削量有利于提高生产效率,削减刀具消耗,降低加工成本。
汽车精加工时,加工精度和表面粗糙度要求高,加工余量小且均匀。
因此,在选择精车切削量时,应要关注如何保证加工质量,并在此基础上尽可能提高生产率。
所以精车应选择小(但不能太小)的后退刀距ap和进给f,并选择切削性能高的刀具材料和合理的几何参数,以提高切削速度V。
一、确定退稿量。
数控数控车床设备在工艺系统刚度和机床功率允许的情况下,尽可能大的反向进给,削减进给次数。
假如零件精度较高,应考虑留出精车余量,留出的精车余量一般比一般车削要小,常取0.1~0.5㎜。
二、进给f(部分数控机床使用进给速度VF)进给量f的选择应与后切量和主轴转速相适应。
在保证工件加工质量的前提下,可选择更高的进给速度(2000mm/min以下)。
切削、车削深孔或精车时,应选择较低的进给速度。
可以在刀具空闲时设置可能的较高进给速度,尤其是在长距离回零时。
粗车一般取F=0.3~0.8mm/r,细车常取F=0.1~0.3mm/r,截断F=0.05~0.2mm/r。
三、确定数控车床主轴转速。
1)轻车在圆外时的主轴转速。
轻型车圆时,应依据加工零件的直径和零件、刀具材料和加工性能所允许的切削速度来确定主轴转速。
除计算和选表外,还可依据实际阅历确定切割速度。
需要注意的是,交流变频数控车床低速输出扭矩小,切削速度不能太低。
确定切削速度后,采纳公式n=1000vc/πd计算主轴转速N(r/min)。
数控车削中切削用量的选择
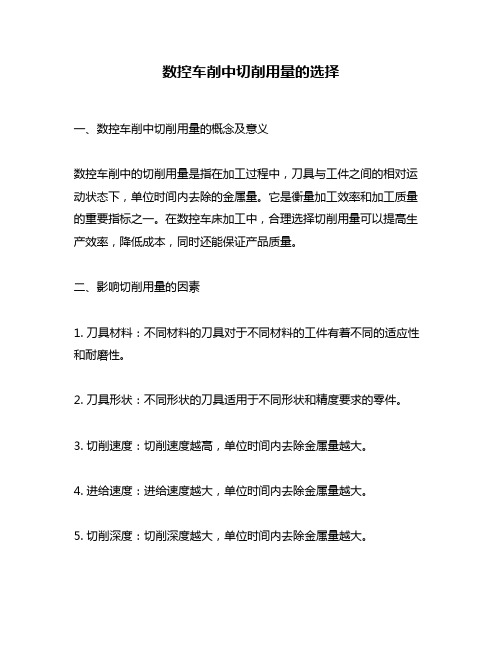
数控车削中切削用量的选择一、数控车削中切削用量的概念及意义数控车削中的切削用量是指在加工过程中,刀具与工件之间的相对运动状态下,单位时间内去除的金属量。
它是衡量加工效率和加工质量的重要指标之一。
在数控车床加工中,合理选择切削用量可以提高生产效率,降低成本,同时还能保证产品质量。
二、影响切削用量的因素1. 刀具材料:不同材料的刀具对于不同材料的工件有着不同的适应性和耐磨性。
2. 刀具形状:不同形状的刀具适用于不同形状和精度要求的零件。
3. 切削速度:切削速度越高,单位时间内去除金属量越大。
4. 进给速度:进给速度越大,单位时间内去除金属量越大。
5. 切削深度:切削深度越大,单位时间内去除金属量越大。
6. 工件硬度:硬度较高的工件需要使用更耐磨损的刀具以及更小而深入地进行切割以提高切削用量。
三、如何选择合适的切削用量1. 根据工件材料和形状选择刀具:不同材料和形状的工件需要使用不同的刀具,以达到最佳加工效果。
2. 根据加工要求选择切削速度和进给速度:根据加工要求确定切削速度和进给速度,以达到最佳的加工效率和质量。
3. 根据机床性能选择最佳切削深度:根据机床性能选择最佳的切削深度,以达到最佳的加工效率和质量。
4. 根据刀具磨损情况及时更换:定期检查并更换磨损严重的刀具,以保证加工质量。
5. 选择合适的冷却液:根据不同材料和形状的工件,选择合适的冷却液以降低温度、减少摩擦、延长刀具寿命等。
四、常见问题及解决方法1. 切屑太长或太细怎么办?答:调整进给速度或者增大/减小齿数可以改变每个齿面上去除金属量,从而改变切屑形状。
2. 切削力过大怎么办?答:减小切削深度或者降低切削速度可以减小切削力,同时也可以延长刀具寿命。
3. 刀具磨损过快怎么办?答:增加冷却液的流量或者更换更耐磨的刀具可以延长刀具寿命。
4. 加工表面粗糙度过大怎么办?答:调整进给速度或者增大/减小齿数可以改变每个齿面上去除金属量,从而改善表面质量。
数控机床加工的切削用量
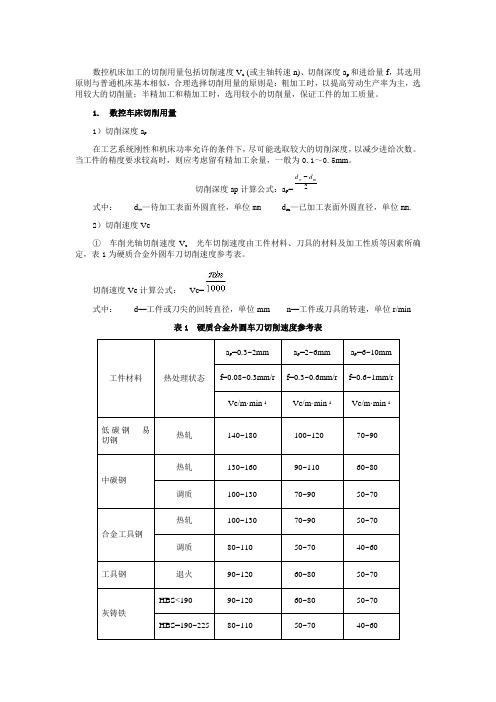
数控机床加工的切削用量包括切削速度V c (或主轴转速n)、切削深度a p 和进给量f ,其选用原则与普通机床基本相似,合理选择切削用量的原则是:粗加工时,以提高劳动生产率为主,选用较大的切削量;半精加工和精加工时,选用较小的切削量,保证工件的加工质量。
1. 数控车床切削用量 1)切削深度a p在工艺系统刚性和机床功率允许的条件下,尽可能选取较大的切削深度,以减少进给次数。
当工件的精度要求较高时,则应考虑留有精加工余量,一般为0.1~0.5mm 。
切削深度ap计算公式:a p =式中: d w —待加工表面外圆直径,单位mm d m —已加工表面外圆直径,单位mm. 2)切削速度Vc① 车削光轴切削速度V c 光车切削速度由工件材料、刀具的材料及加工性质等因素所确定,表1为硬质合金外圆车刀切削速度参考表。
切削速度Vc 计算公式: Vc=式中: d —工件或刀尖的回转直径,单位mm n —工件或刀具的转速,单位r/min表1 硬质合金外圆车刀切削速度参考表2mw d d注:表中刀具材料切削钢及灰铸铁时耐用度约为60min。
②车削螺纹主轴转速n切削螺纹时,车床的主轴转速受加工工件的螺距(或导程)大小、驱动电动机升降特性及螺纹插补运算速度等多种因素影响,因此对于不同的数控系统,选择车削螺纹主轴转速n存在一定的差异。
下列为一般数控车床车螺纹时主轴转速计算公式:n≤–k式中:p—工件螺纹的螺距或导程,单位mm。
k—保险系数,一般为80。
3)进给速度进给速度是指单位时间内,刀具沿进给方向移动的距离,单位为mm/min,也可表示为主轴旋转一周刀具的进给量,单位为mm/r。
⑴确定进给速度的原则①当工件的加工质量能得到保证时,为提高生产率可选择较高的进给速度。
②切断、车削深孔或精车时,选择较低的进给速度。
③刀具空行程尽量选用高的进给速度。
④进给速度应与主轴转速和切削深度相适应。
⑵进给速度V f的计算 V f = n f式中:n—车床主轴的转速,单位r/min。
数控车削加工中的切削用量包括背吃刀量ap
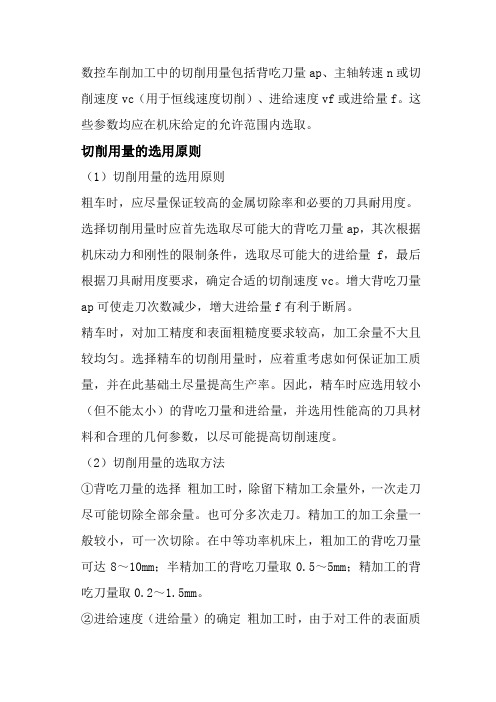
数控车削加工中的切削用量包括背吃刀量ap、主轴转速n或切削速度vc(用于恒线速度切削)、进给速度vf或进给量f。
这些参数均应在机床给定的允许范围内选取。
切削用量的选用原则(1)切削用量的选用原则粗车时,应尽量保证较高的金属切除率和必要的刀具耐用度。
选择切削用量时应首先选取尽可能大的背吃刀量ap,其次根据机床动力和刚性的限制条件,选取尽可能大的进给量f,最后根据刀具耐用度要求,确定合适的切削速度vc。
增大背吃刀量ap可使走刀次数减少,增大进给量f有利于断屑。
精车时,对加工精度和表面粗糙度要求较高,加工余量不大且较均匀。
选择精车的切削用量时,应着重考虑如何保证加工质量,并在此基础土尽量提高生产率。
因此,精车时应选用较小(但不能太小)的背吃刀量和进给量,并选用性能高的刀具材料和合理的几何参数,以尽可能提高切削速度。
(2)切削用量的选取方法①背吃刀量的选择粗加工时,除留下精加工余量外,一次走刀尽可能切除全部余量。
也可分多次走刀。
精加工的加工余量一般较小,可一次切除。
在中等功率机床上,粗加工的背吃刀量可达8~10mm;半精加工的背吃刀量取0.5~5mm;精加工的背吃刀量取0.2~1.5mm。
②进给速度(进给量)的确定粗加工时,由于对工件的表面质量没有太高的要求,这时主要根据机床进给机构的强度和刚性、刀杆的强度和刚性、刀具材料、刀杆和工件尺寸以及已选定的背吃刀量等因素来选取进给速度。
精加工时,则按表面粗糙度要求、刀具及工件材料等因素来选取进给速度。
进给速度νf 可以按公式ν f =f×n计算,式中f表示每转进给量,粗车时一般取0.3~0.8mm/r;精车时常取0.1~0.3mm/r;切断时常取0.05~0.2mm/r。
③切削速度的确定切削速度vc可根据己经选定的背吃刀量、进给量及刀具耐用度进行选取。
实际加工过程中,也可根据生产实践经验和查表的方法来选取。
粗加工或工件材料的加工性能较差时,宜选用较低的切削速度。
数控车床切削用量的选择及其如何确定
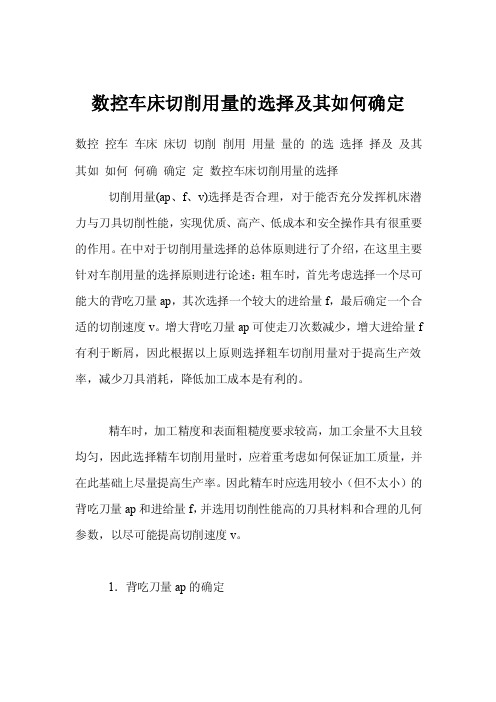
数控车床切削用量的选择及其如何确定数控控车车床床切切削削用用量量的的选选择择及及其其如如何何确确定定数控车床切削用量的选择切削用量(ap、f、v)选择是否合理,对于能否充分发挥机床潜力与刀具切削性能,实现优质、高产、低成本和安全操作具有很重要的作用。
在中对于切削用量选择的总体原则进行了介绍,在这里主要针对车削用量的选择原则进行论述:粗车时,首先考虑选择一个尽可能大的背吃刀量ap,其次选择一个较大的进给量f,最后确定一个合适的切削速度v。
增大背吃刀量ap可使走刀次数减少,增大进给量f 有利于断屑,因此根据以上原则选择粗车切削用量对于提高生产效率,减少刀具消耗,降低加工成本是有利的。
精车时,加工精度和表面粗糙度要求较高,加工余量不大且较均匀,因此选择精车切削用量时,应着重考虑如何保证加工质量,并在此基础上尽量提高生产率。
因此精车时应选用较小(但不太小)的背吃刀量ap和进给量f,并选用切削性能高的刀具材料和合理的几何参数,以尽可能提高切削速度v。
1.背吃刀量ap的确定在工艺系统刚度和机床功率允许的情况下,尽可能选取较大的背吃刀量,以减少进给次数。
当零件精度要求较高时,则应考虑留出精车余量,其所留的精车余量一般比普通车削时所留余量小,常取~㎜。
2.进给量f(有些数控机床用进给速度Vf)进给量f的选取应该与背吃刀量和主轴转速相适应。
在保证工件加工质量的前提下,可以选择较高的进给速度(2000㎜/min以下)。
在切断、车削深孔或精车时,应选择较低的进给速度。
当刀具空行程特别是远距离“回零”时,可以设定尽量高的进给速度。
粗车时,一般取f=~㎜/r,精车时常取f=~㎜/r,切断时f=~㎜/r。
3.主轴转速的确定(1)光车外圆时主轴转速光车外圆时主轴转速应根据零件上被加工部位的直径,并按零件和刀具材料以及加工性质等条件所允许的切削速度来确定。
切削速度除了计算和查表选取外,还可以根据实践经验确定。
需要注意的是,交流变频调速的数控车床低速输出力矩小,因而切削速度不能太低。
数控加工中刀具的选择与切削用量的确定

具 虽 然 增 加 了 成 本 , 但 由此 带 来 的 加 工 质 量 和 加 工 效 率
的 提 高 , 则 可 以使 整 个 加 工 成 本 大 大 降 低 。
在 经 济 型 数 控 加 工 中 , 由 于 刀 具 的 刃 磨 、 测 量 和 更 换 多 为 人 工 进 行 , 辅 助 时 间较 长 , 因 此 , 必 须 合 理 安 排 刀 具 的 排 列 顺 序 。 一 般 应 遵 循 以 下 原 则 : 尽 量 减 少 刀 具
化 和 系列 化 。 数控 刀 具 根据 刀 具 结 构可 分 为 :整 体 式 和镶 嵌 进 行 自 由 曲面 加 工 时 , 为 保 证 加 工 精 度 , 切 削 行 距 一 般
式 。镶嵌 式 又 可分 为焊 接 或机 夹 式 ,机 夹 式 又 可分 为 不 转位 取 得 很 精 密 。 由 于 球 头 刀 具 的 端 部 切 削 速 度 为 零 , 故 球 和 可 转位 两 种 ;还 有 减 振 式 、 内冷 式和 特 殊 形式 ( 复 合刀 如
头 刀 具 常 用 于 曲面 的 精 加 工 。 而 平 头 刀 具 在 表 面 加 工 质
具 )。根 据 制 造刀 具 所 用 的材 料 可 分 为 :优 质碳 素 工 具 ;合 量 和 切 削 效 率 方 面 都 优 于 球 头 刀 , 因 此 , 在 不 过 切 的 前
金 工 具钢 ;高速 钢 ;硬质 合 金 ;其他 材 料 刀 具 ,如 陶 瓷 、金 提 下 , 无 论 是 曲面 的 粗 加 工 还 是 精 加 工 , 都 应 优 先 选 择
刀 具 的 选 择 和 切 削 用 量 的 选 择 尤 为 重 要 , 它 不 仅 对 被 加 工 零 件 的 质 量 影 响 巨大 ,甚 至 可 以 决 定 机 床 功 效 的 发挥 和 安 全 生 产 的 顺 利 进 行 。 所 以 无 论 是 手 工 鳊 程 或 计 算 机 辅 助 编 程 ,在 编 制 加 工 程 序 时 ,选 择 合 理 的 刀具 和 切 削 用 量 ,都
- 1、下载文档前请自行甄别文档内容的完整性,平台不提供额外的编辑、内容补充、找答案等附加服务。
- 2、"仅部分预览"的文档,不可在线预览部分如存在完整性等问题,可反馈申请退款(可完整预览的文档不适用该条件!)。
- 3、如文档侵犯您的权益,请联系客服反馈,我们会尽快为您处理(人工客服工作时间:9:00-18:30)。
单元4 数控机床加工的切削用量教学目的1、了解数控机床的运动(主运动、进给运动);2、了解数控机床加工刀具的角度及其作用;3、了解数控机床加工中有关切削层的参数及其作用;4、了解数控机床加工中的切削用量及其选用原则。
5、掌握常用不同材料零件在粗加工、半精加工和精加工时的切削用量选用;教学重点1、数控机床加工刀具的角度及其作用;2、数控加工中粗加工、半精加工和精加工时的切削用量选择;教学难点1、刀具的角度及其作用;2、切削用量选用教学方法讲练结合教学内容一、车削加工与刀具1. 车削加工原理在普通车床和一般数控车床上,可以进行工件的外表面、端面、内表面以及内外螺纹的加工。
对于车削中心,除上述各种加工外,还可进行铣削、钻削等加工。
从上述介绍可以看出:在切削过程中,刀具和工件之间必须具有相对运动,这种相对运动称为切削运动。
根据切削运动在切削过程中的作用不同可以分为主运动、和进给运动。
各种机床的主运动和进给运动参见下表。
各种机床的主运动和进给运动主运动是指机床提供的主要运动。
主运动使刀具和工件之间产生相对运动,从而使刀具的前刀面接近工件并对工件进行切削。
在车床上,主运动是机床上主轴的回转运动,即车削加工时工件的旋转运动。
2)进给运动进给运动是指由机床提供的使刀具与工件之间产生的附加相对运动。
进给运动与主运动相配合,可以形成完整的切削加工。
在普通车床上,进给运动是机床刀架(溜板)的直线移动。
它可以是纵向的移动(与机床主轴轴线平行),也可以是横向的移功(与机床主轴轴线垂直),但只能是一亇方向的移动。
在数控车床上,数控车床可以同时实现两亇方向的进给,从而加工出各种具有复杂母线的回转体工件。
在数控车床中,主运动和进给运动是由不同的电机来驱动的,分别称为主轴电机和坐标轴伺服电机。
它们由机床的控制系统进行控制,自动完成切削加工。
2. 切削用量切削用量是指机床在切削加工时的状态参数。
不同类型的机床对切削用量参数的表述也略有不同,但其基本的含义都是一致的,如下图所示。
车削加工中切削用量示意图(1)切削速度(c v ) 切削刃上的切削点相对于工件运动的瞬时速度称为切削速度。
切削速度的单位为(m/min )米/ 分。
在各种金属切削机床中,大多数切削加工的主运动都是机床主轴的运动形成,即都是回转运动。
切削速度与机床主轴转速之间进行转换的关系为:1000dnv c π= ………………… 4-1式中:c v ——切削速度 (m/min)d ——工件直径 (mm)n ——主轴转速 (r/min)(2) 进给量(f ) 不同种类的机床,进给量的单位是不同的。
对于普通车床,进给量为工件(主轴)每转过一转,刀具沿进给方向上相对于工件的移动量,单位为mm/r ;对于数控车床,由于其控制原理与普通车床不同,进给量还可以用进给速度 f v (单位为 mm/min )来表达,即:刀具在单位时间内沿着进给方向上相对于工件的位移量。
其它类型的机床则根据其结构不同,进给量的单位表达还可以为刀具或工件每转的位移量( mm/r ,使用多齿刀具的机床)。
在车削加工时,进给速度f v 是指切削刃上选定点相对于工件进给运动的瞬时速度。
它与进给量之间的关系为:f n v f ⨯= ……………………4-2(3) 切削深度(p a ) 己加工表面和待加工表面之间的垂直距离。
对于车床而言,切削深度p a 的计算公式为: 2m w f d d v -= ……………………4-3 式中: w d ——待加工表面直经 (mm)m d ——己加工表面直经 (mm)切削加工中,切削速度(c v )、进给量(f )和切削深度(p a )这三个参数是相互关联的。
在粗加工中,为了提高效率,一般采用较大的切削深度(p a )。
此时切削速度(c v )和进给量(f )相对较小;而在半精加工和精加工阶段,一般采用较大的切削速度(c v )、较小的进给量(f )和切削深度(p a ),以获得较好的加工质量(包括表面粗糙度、尺寸精度和形状精度)。
(4) 切削时间 m t 切削时间是反映切削效率高低的一种指标。
车削外圆时切削时间可由下式计算: p f m a v lA t =……………………4-4式中:l ——刀具行程长度A ——半径方向加工余量(5)金属切除率(w z ) 金属切除率是指每分钟切下工件材料的体积。
它是衡量切削效率高低的另一个指标,金属切除率w z 由下式计算:f v v z f c w 1000= (单位mm 3/min ) ……………………4-5 (6)合成切削运动和合成切削速度 当主运动与进给运动同时进行时,刀具切削刃上某一点相对于工件的运动称为合成切削运动,其大小与方向用合成速度c v 表示。
合成速度等于主运动与进给速度之和。
即:f c v v v += ……………………4-63. 切削刀具(车刀)以车刀为例介绍刀具的基础知识。
图示为普通外圆车刀的示意图。
车刀由夹持部分和切削部分组成。
夹持部分称为刀柄,用来把刀具装夹在车床的刀架上,一般用45#钢材经锻造加工而成;切削部分俗称为刀头,在车刀上为单刀片。
刀片材料一般有高速钢(俗称白钢刀条)和硬质合金两种,用于切削金属材料。
根据刀具切削部分与夹持部分(即刀片与刀柄)连接方式的不同,车刀分为焊接刀具和机夹刀具两大类。
车刀示意图车刀切削部分的主要构成:1)前刀面(A ) 切削加工中被切下的切屑经过的刀片表面。
γA ) 刀具片上与待加工表面相对的表面。
2)后刀面(α3)副后刀面(α`A)刀具片上与己加工表面相对的表面。
4)主切削刃( S ) 前刀面与后刀面相交处形成的切削刃。
用于切出工件上的过渡表面,完成主要的金属切除。
主切削刃是刀具主要的加工刃。
5)副切削刃( S′)前刀面与副后刀面相交处形成的切削刃。
主要作用是配合主切削刃,完成金属材料的切除,形成工件的己加工表面。
6)刀尖指主切削刃与副切削刃交接处形成的切削点。
根据刀具所使用的场合不同,为使刀尖保持锋利,刀尖有倒棱刀尖和倒圆刀尖两种。
4. 刀具切削部分(刀片)的几何角度确定刀具的几何参数,需要以一定的参考坐标系和参考坐标平面为基准。
以车刀为例,引人一个坐标系,作为刀具几何参数的测量基准,这个坐标系就是刀具角度坐标系。
P)此平面是指通切削刃上的一个选定点而垂直于主运动方向的平面。
(1)基面(r对于车刀,这个选定点就是过刀尖而与刀柄安装平面的平面。
图4-8 刀具角度坐标系图4-9 车刀的角度P)此平面是指通过切削刃上的一个选定而垂直于基面的平面。
(2)切削平面(sP)也称为主截面。
正交平面是指通过切削刃选定点并同时垂直于(3)正交平面(o基面和切削平面的平面。
车刀的主要几何角度见下表。
车刀上的几种重要角度在正交平面(主截面)内测量的角度:1)前角(0γ) 前刀面与基面间的夹角。
当前刀面与基面间夹角小于90度时,前角为正值;前刀面与基面间夹角大于90度时,前角为负值。
前角对于刀具的切削性能有很大的影响。
2)后角(0α) 后刀面与切削平面间的夹角。
当后刀面切削平面间与夹角小于90度时,后角为正值;后刀面与切削平面间夹角大于90度时,后角为负值。
由于后角的存在,后用刀面与加工过渡表面之间的摩擦可以大大减小。
3)楔角(0β) 前刀面与后刀面间的夹角。
)(9000αγβ+-︒=r ……………………4-7在基面r P 内测量的角度:1)主偏角(r k ) 主切削平面与假定运动方向之间的夹角。
主偏角恒定为正值。
2)副偏角(r k ') 副切削平面与假定运动方向之间的夹角。
副偏角恒定为正值。
3)刀尖角(r ε) 主切削平面与副切削平面之间的夹角。
)(180`r r r k k +-︒=ε ……………………4-8在切削平面s P 内测量的角度:1)刃倾角(s λ) 指主切削刃与基面间的夹角。
当刀尖比车刀刀柄的安装面高时,刃倾角为正值;当刀尖比车刀刀柄的安装面低时,刃倾角为负值;当切削刃平行于刀柄安装面时,刃倾角为0°,此时,切削刃位于基面内。
以上是对上主切削刃的分析。
采用同样的方法,也可以定义副切削刃的参考坐标系和参考坐标平面,即定义由副基面(r P `)、副切削平面(s P `)和副正交平面(o P `)构成的参考坐标系,进而对副切削刃的各种角度进行分析。
刀具角度对加工的影响见下表。
刀具角度对加工的影响5. 切削层(1)切削层参数切削层尺寸与切削用量p a 、f 大小有关。
直接影响切削过程的是切削横截面面积及其厚度、宽度尺寸。
它们的符号与定义如下:1)切削厚度c a 垂直于加工表面度量的切削层尺寸。
2)切削宽度w a 平行加工表面度量的切削层尺寸。
3)切削面积c A 切削层在基面投影中的面积。
当刀具刃倾角︒=0s λ时,r c k f a sin = (mm ) ……………………4-9 r pw k a a sin = (mm ) ……………………4-10f a a a A p w c c ==(mm 2) ……………………4-11上述分析可知,切削厚度与切削宽度随主偏角的大小而变化。
当︒=90r k 、f a a c c ==max 、p w w a a a max =时,切削面积c A 由切削用量p a 、f 决定,不受主偏角变化的影响。
但是切削层横截面的形状则与主偏角、刀尖圆弧半径有关。
由于刀尖圆弧、主偏角的不同,引起切削厚度、切削宽度的变化,使得横截面形状的差异很大,对切削过程将产生不同的影响。
(2)正切屑与倒切屑 正切屑与倒切屑的切削层尺寸特征是:正切屑:W G a a ≤倒切屑: r pr k a k f sin sin ≥显然产生倒切屑的情况下,主要切削工作以由原来的副切削刃承担,此时p c a a =, f a w =。
原副切削刃上刀具的副前角 0`γ、副刃倾角s `λ对切削过程的影响,比0γ、s λ角更为重要。
这说明,在刀具切削时判定主切削刃和副切削刃除与切削运动有关外,还与切削层尺寸参数有关。
二、 车削加工切削用量的选择1. 切削用量选择原则根据不同的加工条件和加工要求,又考虑到切削用量各参数对切削过程的不同影响,故切削用量参数p a 、f 和v 增大的次序和程度应有所区别。
可从以下几个方面分析:(1) 生产效率 切削用量p a 、f 和v 增大,会使切削时间m t 减小。
当加工余量一定时,减小切削深度p a 会使走刀次数增多,切削时间增加,生产效率降低。
所以,一般情况下尽量优先增大p a ,以求一次进刀全部切除加工余量。
(2) 机床功率 切削用量对机床功率的影响是由于切削力与切削速度变化造成的。
当切削深度p a 和切削速度v 增大时,均使切削功率成正比增加。
此外,增大切削深度p a 使切削力增加较多,而增大进给量f 使切削力增加较少,消耗功率也较少。