压缩机缸体的铸造工艺
汽车缸体铸造工艺

汽车缸体铸造工艺一、缸体材料车用发动机缸体缸盖的材质主要有灰铸铁,铝合金,蠕墨铸铁等。
传统的发动机无论是缸体还是缸盖都是采用铸铁的,但是铸铁有着许多先天的不足,例如重量大、散热性差、摩擦系数高等等。
所以,许多发动机厂商都在寻找更适合的材料制造发动机的构成部件,比如密度小的铝。
铝的比重轻,单位体积的铝结构强度要小于铸铁,所以铝缸体通常体积反而大些。
但铝容易和燃烧时产生的水发生化学作用,耐腐蚀性不及铸铁缸体,尤其对温度压强都更高的增压引擎更是如此。
铸铁缸体和铝缸体各有其优缺点,所以所以高增压的引擎很多都采用铸铁缸体,小型车的缸体则更多向铝缸体发展。
金属中的元素组成会对金属材料的性能产生较大的影响,就钢铁而言,钢中含碳量增加,屈服点和抗拉强度升高,但塑性和冲击性降低,当碳量0.23%超过时,钢的焊接性能变坏,因此用于焊接的低合金结构钢,含碳量一般不超过0.20%。
碳量高还会降低钢的耐大气腐蚀能力,在露天料场的高碳钢就易锈蚀;此外,碳能增加钢的冷脆性和时效敏感性。
不同的缸体元素配比也是有差别的。
合肥江淮铸造有限责任公司缸体化学成分要求化学成分(%)C Si Mn P S Cr Cu Ti Sn Pb下限 3.25 1.95 0.60 0.00 0.06 0.25 0.30 0.00 0.06 0.00 0上限 3.40 2.10 0.90 0.06 0.10 0.35 0.50 0.03 0.09 0.00 4二、原材料熔炼熔炼设备选用:中频感应保温电炉:生产效率10t/h,外水冷长炉龄大排距冲天炉:生产效率7t/h。
1、原材料原材料一般为回炉料,废钢和生铁。
回炉料是厂家的常备材料,在使用时必须注意其本身的干净程度。
回炉料的加入量必须严格按一定比例,否则会导致铁水的Si、S含量不易控制。
江淮生产的缸体铸件回炉料使用量一般不超过20%。
在江淮的缸体生产中,废钢的使用量超过50%。
这是由于生铁本身含有粗大石墨,而石墨熔点较高,在2000℃以上,在熔炼中不能熔尽,使得结晶过程中石墨变得粗大。
缸盖铸造工艺的讨论

2008 / 1 现代铸铁 15
[
]
专
S pecial Topic
题
缸
体
缸
盖
铸 造
厚在公差范围内, 且比较均匀。
底注内浇道贴着缸盖的底部进入型腔; 而中注内
技
水套砂芯与气道砂芯最好采用热法覆膜砂 浇道则从分型面进入型腔。若适当增加中、底注
术
芯, 其抗应力变形的能力要强一些, 产生脉纹的 的内浇道数量, 则可减轻内浇道附近局部过热产
基准的设置也要与粗铣加工选取的基准相一致。 纹, 砂型、砂芯间隙处容易泄漏铁液而“跑火”, 并
2 气缸盖的浇注系统与浇注工艺
且在一定程度上还会增大铁液的缩松倾向。因 此, 所谓高温浇注, 是一个相对概念, 是有一个临
2.1 缸盖的浇注系统 浇注系统的截面比例以全封闭式为佳, 即
F 杯>F 直>F 横>F 内。目的是阻止铁液中的熔渣和其 它非金属异物杂质进入型腔, 对防止砂眼、渣孔 缺陷, 避免产生夹杂渗漏, 具有重要作用。
倾向也小一些。底盘芯与盖板芯等则以冷芯为优 生的冲砂、粘砂、缩松等缺陷, 也可以防止因局部
先考虑。但有一点需要注意: 当一型布置两件时, 过热而产生砂芯断裂。由于阶梯注入比单一底注
底盘芯的尺寸会比较大, 呈薄板状; 由于冷芯不 增加设置了中注内浇道, 温度场更趋合理, 铸造
能瞬时建立终强度, 其初始强度较低, 砂芯从芯 应力小, 上部温度较高, 有利于顺序凝固, 也方便
的下方加一与圆柱直径等厚的小方块, 这样可将
气孔位置移至铸件以外, 但此小方块不易清理。
③在一些壁厚比较薄的地方, 采用蓄气冷却
片的方法, 减少所在部位的气孔。以缸盖罩圈处
缸盖铸造工艺的讨论
压缩机零件铸造工艺分析与研究

压缩机零件铸造工艺分析与研究随着现代机械工业的不断发展,压缩机在工业、交通、农业、民用等诸多领域得到了广泛应用并发挥着重要作用。
作为压缩机中的核心部件之一,其零部件铸造工艺对压缩机的性能和质量具有非常重要的影响。
因此,对压缩机零部件的铸造工艺进行分析和研究具有十分重要的意义。
一、压缩机零部件的材质选择了解压缩机零部件的材质选择,对于选择合适的铸造工艺来说是至关重要的。
压缩机零部件主要包括压缩机壳体、气缸、曲轴、连杆、活塞、阀门等。
常用的材质有铸铁、钢、铜、铝合金等。
1、铸铁:铸铁通常用于制造压缩机壳体和气缸等零部件。
铸铁的机械性能稳定可靠,且硬度高、耐磨性好,同时铸造工艺成熟、容易加工,成本相对较低,是制造压缩机零部件的重要材料。
2、钢:钢材具有高强度、高刚性、耐磨性、耐腐蚀等优点。
通常用于制造压缩机的曲轴、连杆等关键零部件。
钢材成本相对较高,加工难度相对铸铁增加,但其机械性能优异,能够满足一些高性能要求的压缩机使用。
3、铜:铜材具有导电性能好、导热性能良好、抗氧化性好等特点。
在制造压缩机阀门、线圈等零部件方面使用较为广泛。
4、铝合金:铝合金具有比重轻、强度高、良好的耐腐蚀性能等特点,在制造压缩机的小型零部件、外壳等方面,往往会选择使用铝合金。
二、常用的压缩机零部件铸造工艺压缩机零部件的制造一般通过铸造工艺完成,常见的压缩机零部件铸造工艺有几种:1、砂型铸造:砂型铸造是常用的铸造工艺之一,其流程简单,而且成本低。
在砂模铸造方面,常见的技术有石膏砂芯、石墨砂芯、无碱玻璃砂等砂芯技术。
这种铸造工艺可以非常精确地制造出零部件,同时可以适应多种材质。
2、失重铸造:失重铸造也是一种常见的铸造工艺,它利用熔模的特性,使得工件具有较高精度和表面质量优异的特点。
钢、不锈钢零部件的铸造,往往采用失重铸造方法,是一种适应性非常广泛的铸造工艺。
3、压铸:压铸是一种高效率、高产量、低浪费的铸造工艺,常用于制造小型精密零部件,如压缩机的阀门、泵体和飞轮等零部件。
东风汽车铸造三厂缸体铸造工艺流程(一)

东风汽车铸造三厂缸体铸造工艺流程(一)
东风汽车铸造三厂缸体铸造工艺流程
工艺概述
•工艺名称:东风汽车铸造三厂缸体铸造工艺流程
•目标:生产高质量的汽车发动机缸体
流程步骤
1.原料准备
–选择高品质的铸造材料,如铸铁等
–对原料进行质检,检测其化学成分和力学性能2.模具制备
–设计并制作合适的缸体模具
–确保模具材料和工艺能满足生产要求
3.模具预处理
–清洗和除锈模具,确保表面光洁
–进行模具涂覆,保护模具表面,方便后续操作4.浇注过程
–熔炼铸造材料,保证熔体的均匀性和温度
–使用浇注设备,将熔体倒入模具中
–控制浇注速度和压力,避免产生缺陷
5.硬化
–等待熔体冷却和凝固
–使用冷却介质或冷却水辅助加速凝固过程
6.模具拆卸
–小心地拆卸模具,不损坏缸体
–仔细检查缸体表面是否有破损或缺陷
7.后处理
–进行缺陷修复和表面处理,如打磨、喷涂等
–进行最终的质量检测,并记录检测结果
8.包装和出厂
–对合格的缸体进行包装,以防损坏
–准备出厂文件和运输安排,确保产品安全送达工艺优势
•高质量:严格质检和控制确保缸体的质量稳定性
•高效率:流程的合理设计和设备的优化提高了生产效率
•环保可持续:对原料和能源的合理利用,降低环境影响
结论
这份文章详细介绍了东风汽车铸造三厂缸体铸造工艺流程的各个步骤。
该工艺以高质量、高效率和环保可持续为目标,通过严格质检和控制,以及流程的合理设计和设备的优化,确保生产出高质量的汽车发动机缸体。
汽车发动机缸体铸造工艺流程
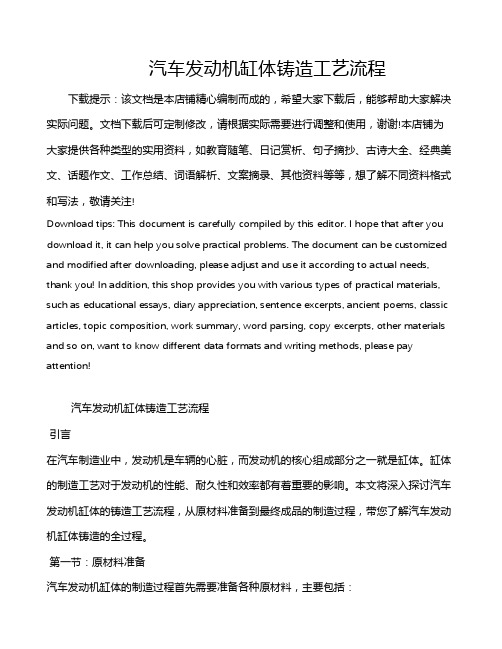
汽车发动机缸体铸造工艺流程下载提示:该文档是本店铺精心编制而成的,希望大家下载后,能够帮助大家解决实际问题。
文档下载后可定制修改,请根据实际需要进行调整和使用,谢谢!本店铺为大家提供各种类型的实用资料,如教育随笔、日记赏析、句子摘抄、古诗大全、经典美文、话题作文、工作总结、词语解析、文案摘录、其他资料等等,想了解不同资料格式和写法,敬请关注!Download tips: This document is carefully compiled by this editor. I hope that after you download it, it can help you solve practical problems. The document can be customized and modified after downloading, please adjust and use it according to actual needs, thank you! In addition, this shop provides you with various types of practical materials, such as educational essays, diary appreciation, sentence excerpts, ancient poems, classic articles, topic composition, work summary, word parsing, copy excerpts, other materials and so on, want to know different data formats and writing methods, please pay attention!汽车发动机缸体铸造工艺流程引言在汽车制造业中,发动机是车辆的心脏,而发动机的核心组成部分之一就是缸体。
铸造工艺的概念
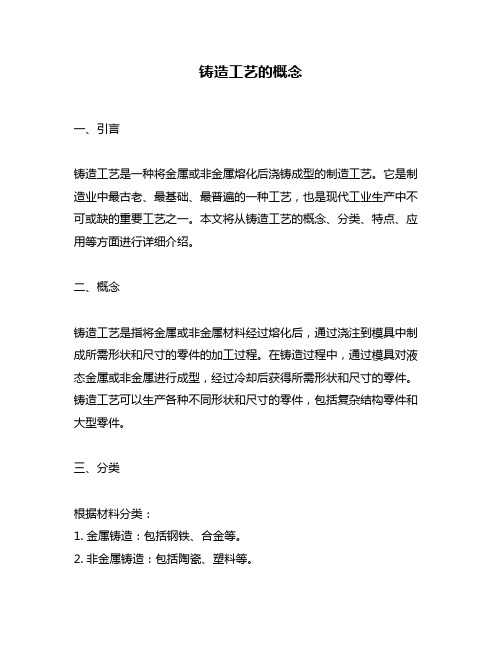
铸造工艺的概念一、引言铸造工艺是一种将金属或非金属熔化后浇铸成型的制造工艺。
它是制造业中最古老、最基础、最普遍的一种工艺,也是现代工业生产中不可或缺的重要工艺之一。
本文将从铸造工艺的概念、分类、特点、应用等方面进行详细介绍。
二、概念铸造工艺是指将金属或非金属材料经过熔化后,通过浇注到模具中制成所需形状和尺寸的零件的加工过程。
在铸造过程中,通过模具对液态金属或非金属进行成型,经过冷却后获得所需形状和尺寸的零件。
铸造工艺可以生产各种不同形状和尺寸的零件,包括复杂结构零件和大型零件。
三、分类根据材料分类:1. 金属铸造:包括钢铁、合金等。
2. 非金属铸造:包括陶瓷、塑料等。
根据模具分类:1. 砂型铸造:采用砂型作为模具。
2. 金属型铸造:采用金属型作为模具。
3. 石膏型铸造:采用石膏型作为模具。
4. 混凝土型铸造:采用混凝土型作为模具。
5. 精密铸造:采用特殊的精密模具进行铸造。
根据生产方式分类:1. 手工铸造:手工操作制作零件。
2. 自动化铸造:利用机器设备进行生产。
四、特点1. 生产成本低。
相对于其他制造工艺,铸造工艺的生产成本较低,因为它可以使用废旧金属或非金属材料进行生产,同时也可以利用回收再利用的原材料。
2. 生产效率高。
相对于其他制造工艺,铸造工艺的生产效率较高,因为它可以一次性生产多个零件,并且可以同时进行多个生产线。
3. 产品质量好。
相对于其他制造工艺,铸造工艺的产品质量较好,因为它可以通过调整材料比例和温度等参数来控制产品质量。
4. 应用范围广。
由于其可适应性强,所以被广泛应用于各种领域,包括汽车制造、机械制造、建筑业等。
五、应用1. 汽车制造。
铸造工艺被广泛应用于汽车制造领域,生产汽车发动机缸体、缸盖、曲轴箱等零部件。
2. 机械制造。
铸造工艺被广泛应用于机械制造领域,生产各种机械零部件。
3. 建筑业。
铸造工艺被广泛应用于建筑业领域,生产各种建筑材料和装饰品。
4. 航空航天。
铸造工艺被广泛应用于航空航天领域,生产各种飞行器零件和发动机零部件。
压铸成型工艺

压铸成型工艺汇报人:2023-12-24•压铸成型工艺简介•压铸成型原理与设备•压铸成型材料目录•压铸成型工艺流程•压铸成型质量控制•压铸成型新技术与发展趋势•压铸成型工艺案例分析01压铸成型工艺简介特点高效率:压铸成型工艺可以实现快速、连续的生产,提高生产效率。
可加工复杂零件:压铸模具可以设计得非常复杂,因此可以用于生产各种形状和结构的铸件。
精度高:由于液态金属在高压下注入模具,因此铸件尺寸精度高,表面光洁度好。
定义:压铸成型是一种金属铸造工艺,通过高压将液态金属注入模具中,冷却后得到铸件。
定义与特点汽车工业家电行业建筑行业其他行业压铸成型的应用领域01020304汽车发动机、底盘、刹车系统等零部件的制造。
各种金属外壳、支架等部件的制造。
建筑五金、门窗等部件的制造。
航空航天、电子、医疗器械等领域的零部件制造。
压铸成型技术起源于18世纪的欧洲,最初用于小型精密零件的制造。
随着技术的不断发展,压铸成型工艺逐渐应用于更广泛的领域。
近年来,随着新材料、新工艺的不断涌现,压铸成型技术也在不断创新和进步。
未来,压铸成型工艺将继续向着高效、精密、环保的方向发展。
压铸成型的历史与发展发展历史02压铸成型原理与设备0102压铸成型能够生产出形状复杂、精度高、表面质量好的金属零件,广泛应用于汽车、电子、通讯等领域。
压铸成型是一种金属铸造工艺,利用高压将液态金属快速充填到模具型腔内,并在压力下凝固成型。
压铸机按照结构可分为冷室压铸机和热室压铸机,按照功能可分为单动压铸机和双动压铸机。
金属液在模具外冷却凝固,多用于大型、复杂零件的生产。
冷室压铸机金属液在模具内冷却凝固,多用于小型、简单零件的生产。
热室压铸机压铸机分类压铸模具是实现压铸成型的关键工具,由动模和定模两部分组成。
模具设计需考虑零件形状、尺寸、精度、浇注系统、排溢系统等因素,以确保生产出合格的金属零件。
压铸模具03压铸成型材料流动性好压铸材料应具有良好的流动性,以便在高压下填充模具的各个角落。
缸体缸盖铸造过程的工艺流程
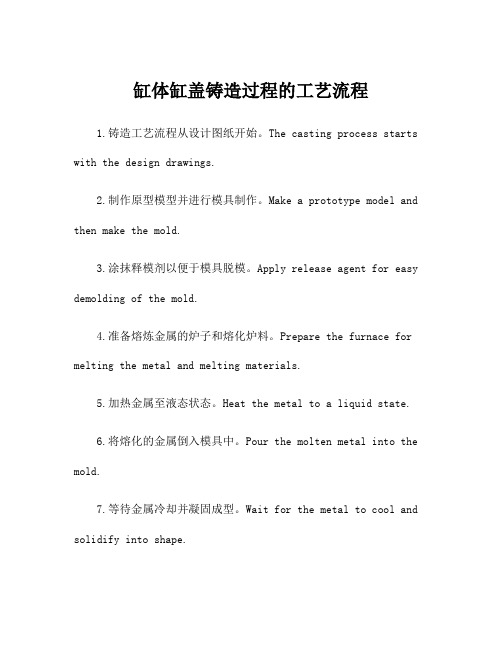
缸体缸盖铸造过程的工艺流程1.铸造工艺流程从设计图纸开始。
The casting process starts with the design drawings.2.制作原型模型并进行模具制作。
Make a prototype model and then make the mold.3.涂抹释模剂以便于模具脱模。
Apply release agent for easy demolding of the mold.4.准备熔炼金属的炉子和熔化炉料。
Prepare the furnace for melting the metal and melting materials.5.加热金属至液态状态。
Heat the metal to a liquid state.6.将熔化的金属倒入模具中。
Pour the molten metal into the mold.7.等待金属冷却并凝固成型。
Wait for the metal to cool and solidify into shape.8.取出铸造件并进行去毛刺处理。
Remove the castings and deburr.9.进行加工处理以达到精度要求。
Process the castings to meet the accuracy requirements.10.进行表面处理以提高光洁度。
Carry out surface treatment to improve the brightness.11.检验铸件的尺寸和质量。
Inspect the dimensions and quality of the castings.12.进行热处理以提高材料性能。
Carry out heat treatment to improve material performance.13.进行喷涂防锈油漆以防止生锈。
Spray anti-rust paint to prevent rust.14.进行最终检验以确保产品质量。
关于高质量汽缸体铸造工艺问题的探讨

摘要 :介绍了现代汽车发动机对汽缸体铸件的技术要求和铸造工艺难点,从铸造工艺设计、铁液成分控制、铸件冷却
大型高压球墨铸铁缸体的研制
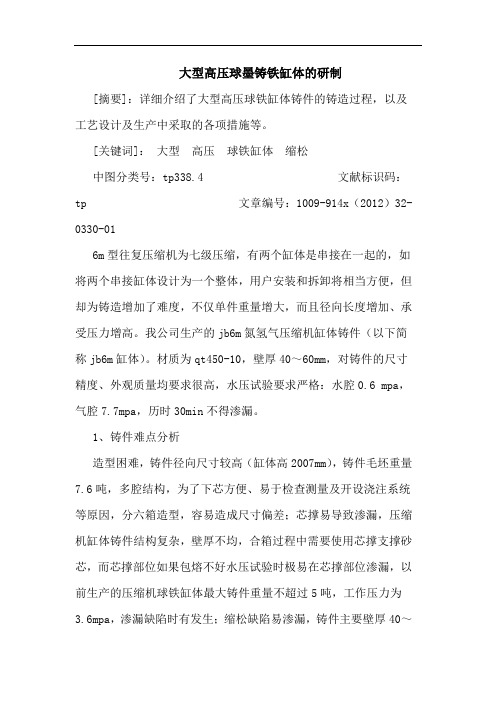
大型高压球墨铸铁缸体的研制[摘要]:详细介绍了大型高压球铁缸体铸件的铸造过程,以及工艺设计及生产中采取的各项措施等。
[关键词]:大型高压球铁缸体缩松中图分类号:tp338.4 文献标识码:tp 文章编号:1009-914x(2012)32- 0330-016m型往复压缩机为七级压缩,有两个缸体是串接在一起的,如将两个串接缸体设计为一个整体,用户安装和拆卸将相当方便,但却为铸造增加了难度,不仅单件重量增大,而且径向长度增加、承受压力增高。
我公司生产的jb6m氮氢气压缩机缸体铸件(以下简称jb6m缸体)。
材质为qt450-10,壁厚40~60mm,对铸件的尺寸精度、外观质量均要求很高,水压试验要求严格:水腔0.6 mpa,气腔7.7mpa,历时30min不得渗漏。
1、铸件难点分析造型困难,铸件径向尺寸较高(缸体高2007mm),铸件毛坯重量7.6吨,多腔结构,为了下芯方便、易于检查测量及开设浇注系统等原因,分六箱造型,容易造成尺寸偏差;芯撑易导致渗漏,压缩机缸体铸件结构复杂,壁厚不均,合箱过程中需要使用芯撑支撑砂芯,而芯撑部位如果包熔不好水压试验时极易在芯撑部位渗漏,以前生产的压缩机球铁缸体最大铸件重量不超过5吨,工作压力为3.6mpa,渗漏缺陷时有发生;缩松缺陷易渗漏,铸件主要壁厚40~60mm,而且大小方门、进排气口、筋板较多,纵横交错形成结构热节,极易产生局部缩孔缩松,影响组织均匀性和致密性,从而导致打压渗漏。
2、工艺方案设计2.1 创新铸造工艺以杜绝因芯撑包熔问题产生的渗漏由于压缩机缸体的复杂结构,几乎都需要用芯撑来固定砂芯,特别是水腔、气腔的上下两端都需要用芯撑来支撑砂芯,但由于芯撑质量、清洁度、浇注温度等因素若与基体熔和不良,打压时水腔气腔芯撑部位容易发生渗漏。
为此,我们决定调整这个缸体的生产工艺,大胆取消铸铁芯撑,15个芯子全部用芯头来固定解决。
(工艺结构如图1)2.2 分析影响缩松的因素及采取措施碳当量:提高碳量,增大了石墨化膨胀,可减少缩孔缩松。
挤压铸造工艺原理、特点、分类

第9章挤压铸造概述挤压铸造,简称挤铸,也称“液态模锻”或“液锻”。
其原理是对进入挤压铸型型腔内的液态(或半固态)金属施加较高的机械压力,使其成形和凝固,从而获得铸件或铸锭的一种工艺方法。
此工艺是一种介于模锻与压铸之间,实施铸锻结合的工艺。
其与模锻不同,置于模具(铸型)中的不是固态坯料,而是液态(或半固态)金属;与普通压铸不同,其液态金属是自下而上缓慢、平稳充型的,并保持在高压力下凝固。
从工艺方法方面,挤压铸造主要分两大类:①直接挤压铸造,简称直接挤铸,包括直接冲头挤铸、柱塞挤铸等,即液态金属在压力推动下充填由冲头与凹型组成的型腔中,且挤压冲头直接挤压在铸件上(见图9-1)。
②间接挤压铸造,简称间接挤铸,包括上压式和下顶式间接挤铸等,即液态金属在压力推动下,充填已闭合锁型的型腔中,挤压压冲头通过内浇道将压力传递到铸件上(见图9-2)。
图9-1典型直接挤压铸造工艺程序示意图a)铸型准备b)浇注c)合挤压压d)开型,取出铸件按挤压铸型的分(合)型方向的不同,挤压铸造也可分为立式挤铸(水平分型,如图9-1所示)和卧式挤铸(垂直分型,如图9-2所示)两大类。
但不论是何种类型,为创造良好的排气条件,挤压冲头对液态金属的挤压力,大都是垂直方向(由上向下或自下而上)施加的。
图9- 2典型间接挤压铸造(下顶式)工艺程序示意图a)铸型准备后浇注 b)合型,挤压料筒摆正e)挤压头和挤压料筒上升 d)挤压头上升挤压挤压铸造的工艺过程一般分为下列步骤(见图9-1,图9-2)。
(1)铸型准备包括对铸型、挤压料简及挤压冲头的清理和喷涂,并将其回复到准备位置上。
(2)浇注将液态(或半固态)金属注入凹型或料筒中。
(3)合型合型并锁型,将料筒、冲头进入待挤压位置。
(4)挤压用挤压冲头将液态(半固态)金属推人型腔,并继续保压直至其完全凝固。
(5)开型推出铸件。
挤压铸造一般在专用挤压铸造机(简称挤铸机)上进行。
但国内外也不少是选普通液压机代用,后者设备投资少,也可行,但生产效率低并会影响产品质量。
挤压铸造工艺简介

350 拉伸强度 0.2%耐力 [MPa] 300 250 200 150 100 50 0
VSC系列
Vertical-die-clamping Vertical-shot Squeeze Casting machine (纵向合模 纵向挤压铸造机)
1.挤压铸造工艺的概要
UBE挤压铸造设备的类型 挤压铸造设备
有地沟型: 250, 350, 500, 630, 800T 无地沟型: : 350, 800, 1250T
200 180 160 σu=143MPa
应力 [MPa]
140 120 100 80 60 40 20 普通压铸 挤压铸造 σu=67MPa
0
104
105
106
107
108
重复次数(Cycle) [次]
3.挤压铸造工艺的应用实例
3.挤压铸造工艺的应用实例
SQZ sample
Brake caliper
・射出速度:max. 10 m/s
1.挤压铸造工艺的概要
UBE挤压铸造机的出厂数量
SQZ: 410 sets
As of Aug. 2014
Europe:
38 sets China: 10 sets
Japan:
256 sets Korea: 20 sets
North & south America:
5
和普通压铸的比较/充填
压缩机缸体的铸造工艺

HT275,材料检测采用C型 (450 mm)单铸试棒 。本体 硬度要求达到HB228~277,检测部位在两个端面 。毛坯 重量是 1 143 kg,壁厚均匀 ,主要壁厚 为25-40 mm。缸 体的结构简 图如 图1所示 。客户之 前在生产 这个产 品时 常 出现粘 砂现象 ,而且无 法清 理 ; 内腔有 大 面积脉 纹 缺陷 ,致使 产 品的使 用性 能受 到很 大影 响 。我 厂通 过 对 缸体 结构 的分 析 ,设 计 了合理 的工 艺 ,成功 解决 了 铸 件出现 的粘 砂 、脉纹等缺 陷 。
道设置在缸体长度方 向的侧面 ,布置在上箱 ,直浇道设 在横浇道中部 ,铁液从 中间向两边均匀 的引入型腔 。根 据缸体 的结构特点 、铁液的分布情况 ,设计 内浇道数 量 和位置 ,将 内浇道布置在下箱 ,有利于浇注过程 中提高 浇注系统的挡渣效果 。浇注系统全部倒 网角 ,减少由浇 注 系 统 引起 的夹 砂 。 由于采 用 中问 注 入 铁 液 ,采 用 开 放 式的浇 注系统 ,确保铁液充型平稳 。为防止浇 注过程 中 铁液 飞溅产生 的铁豆滚入 型腔产生冷隔缺陷 ,浇注前必
下芯 前用 相应 的砂 芯检具 检测 砂芯 尺寸是 否发 生 变形 ,砂 芯装 配好后 必须 用检具 检 测装 配尺 寸是否 符 合要 求 。由于砂 芯数 量 比较多 ,形状 比较 复杂 ,下 芯 顺 序要 考虑 周 全 ,尤 其是 下箱 的气 腔砂芯 和水 腔砂 芯 须先 组合后 才 能不发 生 干涉 。为此 ,在实 际生 产前 采 用计 算机模拟 砂芯装配过 程可 以起 到很好 的指导作 用 。 所 有砂 芯 ,尤其 是气 腔 和水腔砂 芯在 流涂 完成 后必 须 用 烘烤 的方 式检 测砂 芯 的排气 通道是 否顺 畅 ,如果 有 漏气 的地方必 须进 行修 补 ,确保 排气顺 畅 才能验 收合 格 。合 箱 的关 键 环节是 必须 将缸 径砂 芯 的两端 芯头 密 封好 ,防止浇 注过 程 中铁液 钻入砂 芯 钢管 导致产 品报 废 。另 外一个 关键 环节 就是 气腔 和水 腔砂 芯 的排 气通 道在 装 配砂 芯过程 中采 用铁 屑管 连接并 引 出到铸 型外 面 ,使 浇 注过 程 中砂 芯 产生 的气体 能 迅 速排 出铸 型 。 铁屑 管来 源很 广 ,有一 定 的强度 和可塑 性 ,是 很好 的 排气通道 材料 ,如 图6和图7所示 。 3.3 熔炼 和浇 注过 程
压缩机生产工艺流程
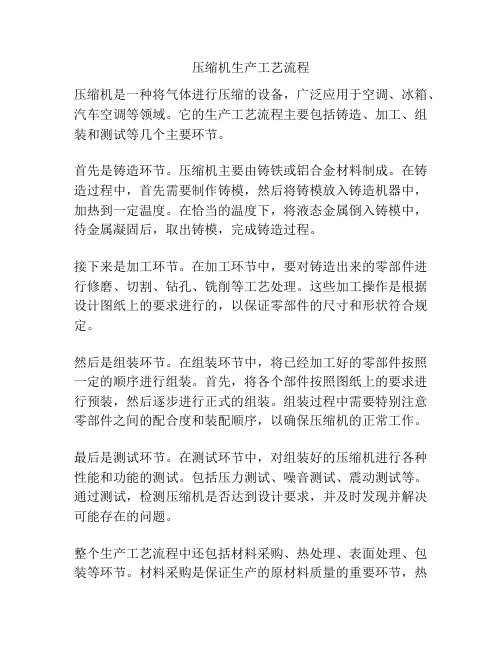
压缩机生产工艺流程
压缩机是一种将气体进行压缩的设备,广泛应用于空调、冰箱、汽车空调等领域。
它的生产工艺流程主要包括铸造、加工、组装和测试等几个主要环节。
首先是铸造环节。
压缩机主要由铸铁或铝合金材料制成。
在铸造过程中,首先需要制作铸模,然后将铸模放入铸造机器中,加热到一定温度。
在恰当的温度下,将液态金属倒入铸模中,待金属凝固后,取出铸模,完成铸造过程。
接下来是加工环节。
在加工环节中,要对铸造出来的零部件进行修磨、切割、钻孔、铣削等工艺处理。
这些加工操作是根据设计图纸上的要求进行的,以保证零部件的尺寸和形状符合规定。
然后是组装环节。
在组装环节中,将已经加工好的零部件按照一定的顺序进行组装。
首先,将各个部件按照图纸上的要求进行预装,然后逐步进行正式的组装。
组装过程中需要特别注意零部件之间的配合度和装配顺序,以确保压缩机的正常工作。
最后是测试环节。
在测试环节中,对组装好的压缩机进行各种性能和功能的测试。
包括压力测试、噪音测试、震动测试等。
通过测试,检测压缩机是否达到设计要求,并及时发现并解决可能存在的问题。
整个生产工艺流程中还包括材料采购、热处理、表面处理、包装等环节。
材料采购是保证生产的原材料质量的重要环节,热
处理是对零部件进行硬度调节的过程,表面处理是为了防止零部件表面氧化和腐蚀,包装是为了保护压缩机在运输和储存过程中的安全和完整。
以上就是压缩机生产工艺流程的简要介绍。
随着科技的不断进步,压缩机的生产工艺也在不断改进和创新,以提高生产效率和产品质量。
大型压缩机缸体的铸造工艺

关 键 词 :缸体 ;渗漏 ;致密性 ;耐磨性 中 图分 类号 :T 4 . 文献标 识 码 :B 文章 编 号 :10—9 7 (0 9 09— 4 GI35 0 14 7 2 1)0— 8 10 1
Ca t g Pr c s fL r e Sc l mp e s rCyid r si o e s o a g ae Co n rs o l e n
图1 6 0 M5 缸体
F g. M 5 y i d rc s i g i 16 0 c l e a tn n
报 废 ,造成 无法 挽救 的损失 。 因此 ,大 型缸体 铸 件生 产 之前 要对 其 耐压性 能 有充 分 的技术 准备 ,将 渗漏 几
率 降到最低 。
1 缸体铸造 工艺难点分 析
浇注系统设计的原则是 :①铁液大流量快速平稳充
()缸 体熔 炼工 艺 控制难 度大 。铸 件 需要 加工 的 3 部位 多 ,要有 好 的切削 加工性 ,同时缸 径又要 具备 很 好 的耐 磨性 ,铸件 因冷 却缓 慢 ,往往 导致共 晶石 墨粗 大 ,严重影响缸径 的耐磨性 ;缸体 的尺寸精度 要求高 , 铸 件 的 内应 力要 小 ,确 保缸 体尺 寸稳 定性 好 ,保 证 缸
()缸 体 内在质 量要求 严格 。缸 体 工作环境 恶 劣 , 1 工作 时 承 载 高 压 、高 速 的 气 流 冲 击 。 缸 体 壁 厚 3~ 5 10mm,上 下 连接盘 厚 大 ,形 成多处 热 节 ,每 个缸 体 1
收稿 日期 :2 1- 5 0 收到初稿 ,2 1- 6 2 收到修订稿。 0 10 — 9 0 10 — 2
ma u a t r d s c e s ul t i i tt .Th yid rc sig h d g o a hn bly a d we r n f cu e u c s f l a t f s r y s r y e c l e a t a o d m c ia i n a n n i t
挤压铸造在汽车、摩托车上应用

挤压铸造在汽车、摩托车上的应用
中国兵器科学研究院、宁波分院
齐丕骧
“挤压铸造”国内外也称“液态模锻”是一种介于铸造与锻造之间的优质、高效、节能的工艺方法,它既能接近甚至达到同种合金锻件的内部组织和力学性能,又能实现高效率的大批是生产,与普通压铸件相比,可较大程度的提高力学及使用性能,与普通锻件相比,又可节约能源。因此,多年来,国内外厂商,均把此项工艺用做汽车、摩托车高档有色金属铸件的方法之一,并迅速的在发展。
挤压压力/Mpa
浇注温度/℃
模具温度
/℃
保压时间
/s
生产周期/s
铸件质量/kg
成品质量/kg
0.04
110
810
210
45
120
10.5
5.7
表3 用不同方法铸造的铝轮毂规格及力学性能
规格特性
挤压铸造
金属型铸造
铝轮毂设计
碟形
碟形
铝轮毂直径×铝轮毂宽度/mm
330.2×152.4
330.2×139.7
质量/kg
5.2
5.3~6.3
热处理状态
淬火+人工时效
淬火+人工时效
合金种类
A356.0
A356.0
力学
性能
σb/MPa
303~338
155~251
σ0.2/Mpa
237~268
126~212
δ/%
6.0~15.9
2.4~2.8
硬度/HRF
84~90
60~92
2.2 铝合金活塞
解放牌汽车铝活塞毛坯的挤压设备为四柱式160t液压机。模具(图6)采用上冲头14和套筒15加压充型,底柱7反正结晶(动凹型式),两侧芯杆11成形销孔的铸型结构。侧芯杆11由气缸1通过杆2、3实现抽拉和闭锁。凹型13由弹簧9支撑而有4mm的上下活动余量,以实现反压结晶。
- 1、下载文档前请自行甄别文档内容的完整性,平台不提供额外的编辑、内容补充、找答案等附加服务。
- 2、"仅部分预览"的文档,不可在线预览部分如存在完整性等问题,可反馈申请退款(可完整预览的文档不适用该条件!)。
- 3、如文档侵犯您的权益,请联系客服反馈,我们会尽快为您处理(人工客服工作时间:9:00-18:30)。
铸造
张证:压缩机缸体的铸造工艺
·1013·
型,在铸型最低位置的两侧各安放一个溢流槽,堆积 低温脏铁液,同时也能收集合箱过程中的浮砂,如图3 所示。 2.4 其他工艺参数的确定
由于缸体壁厚相对比较厚大,材质牌号比较高,收 缩量相对比较大。浇注温度应遵循低温快浇的原则,同 时也能减少气腔和水腔粘砂,便于清理,提高铸件表面 质量。根据客户以往的生产经验和国内某铸造厂的质量 问题总结,为避免气腔和水腔型砂烧结,无法清理导致 铸件报废,气腔和水腔砂芯采用70~140目的宝珠砂,同 时选用锆英粉醇基涂料等措施来提高铸件的抗粘砂能 力。其余部位仍采用70~140目石英砂和石墨醇基涂料, 以降低生产成本。由于铸件壁厚较大,保温时间要控制 在36 h以上,禁止产品打箱温度超过500 ℃。
须将所有冒口用铁板或者报纸遮盖。 2.3 冒口和聚渣结构设计
在铸件的顶部设置排气溢流冒口,便于在浇注过 程中及时排除型腔产生的气体,使铁液能快速充满型 腔,同时将浇注过程中产生的气体、夹渣和低温铁液 通过冒口排出铸型,减少铸型上方的铸件产生铸造缺 陷的几率。考虑到缸径浇注位置的上下部位易吸附脏 铁液,产生气孔、夹砂和夹渣等缺陷,在缸径砂芯的 上下侧各开设铁液溢流槽,储存含有气体、砂和渣的 低温铁液;为将浇注过程中最初的低温脏铁液排出铸
关键词:压缩机缸体;疏松;粘砂;浇注系统;呋喃树脂砂 中图分类号:TG242 文献标识码:B 文章编号:1001-4977 (2011) 10-1011-04
Casting Process of Compressor Cylinder
ZHANG Zheng (Cixi Huili Machinery & Electric Co., Ltd., Cixi 315333, Zhejiang, China)
(a) 上模样
(b) 下模样 图2 缸体上、下模样 Fig. 2 Upper and lower pattern of cylinder
图3 铸造工艺简图 Fig. 3 Sketch of casting process
2.2 浇注系统设计 在分型面设置浇注系统是典型的设计模式。将横浇
道设置在缸体长度方向的侧面,布置在上箱,直浇道设 在横浇道中部,铁液从中间向两边均匀的引入型腔。根 据缸体的结构特点、铁液的分布情况,设计内浇道数量 和位置,将内浇道布置在下箱,有利于浇注过程中提高 浇注系统的挡渣效果。浇注系统全部倒圆角,减少由浇 注系统引起的夹砂。由于采用中间注入铁液,采用开放 式的浇注系统,确保铁液充型平稳。为防止浇注过程中 铁液飞溅产生的铁豆滚入型腔产生冷隔缺陷,浇注前必
图1 压缩机缸体结构简图 Fig. 1 Sketch of the structure of compressor cylinder
收稿日期:2011-05-10收到初稿,2011-06-13收到修订稿。 作者简介:张证 (1970-),男,工程师,主要从事铸造生产管理和工艺设计。E-mail:zhangzheng@
Abstract:The casting structure of the cylinder for compressor was analyzed in this paper, and the casting process was designed. The defects such as burning-on and shrinkage porosity were eliminated through enhancing the procedure control during production. Finally the qualified castings were produced, which can provide the technical support and experience for production of similar cylinder castings. Key words:compressor cylinder; shrinkage porosity; burning-on; gating system; furan resin bonded
Oct. 2011 Vol.60 No.10
图6 气腔和水腔砂芯排气通道连接图 Fig. 6 Sketch of venting channel connecting the gas cavity and water cavity of clay core
图7 铁屑管连接细节 Fig. 7 Connecting details
将铁液的化学成分和温度调整到工艺规定的范围, 采用2 t铁液包盛装铁液1 500 kg。按工艺规定控制浇注 温度 (1 320±10) ℃,采用拔塞式浇口杯,浇注过程中 使浇口杯处于充满状态,浇注时间控制在 (33±2) s, 使浇注过程平稳。浇注过程中用锶硅钡孕育剂进行随流
·1014·
FOUNDRY
·1012·
FOUNDRY
Oct. 2011 Vol.60 No.10
2 铸造工艺设计
2.1 分型面的设计 由于缸体外形是细长型结构,借鉴专业压缩机铸
件类似缸体的生产经验。缸体的控制重点是缸径和两 个端面的质量,这三个部位的质量要均匀稳定,处于 同一质量水平。如果采用垂直造型和浇注,缸径上部 和缸体上端面容易出现气孔、夹渣和疏松等铸造缺陷, 质量将很难保证,且模具需分成三段,造型难度增大。 另外,合箱操作也很困难,缸体的水腔砂芯支撑难度
造型难度最大的也是铸件质量最关键的环节是气 腔和水腔砂芯的制备。气腔和水腔砂芯比较薄,质量 要求高,可采用50%的石英砂和50%的宝珠砂混合,为 防止砂芯变形和提高砂芯强度,在砂芯中安放Φ10 mm 钢筋作为芯骨。由于砂芯全部被铁液包围,必须要加 强砂芯的排气,因此在钢筋上拴Φ6 mm的尼龙通气绳, 并通过芯头将排气通道联通到铸型外面。为防止砂 芯变形,脱模后的砂芯立即放在托芯板上进行固化 30 min以上。如图4和图5所示。
大,型腔尺寸不易控制。合箱过程中很难彻底清理浮 砂,缸径在浇注过程中容易形成夹砂,导致产品报废。 因此确定缸体最佳的分型面是对称水平分型,采用水 平造型、合箱和浇注。模具上、下模样如图2所示,上 下铸型采用三个定位销定位,减少铸型尺寸偏差。为 防止合箱过程中发生碰撞,在上下铸型合箱时增加两 个导向销。在型板的四个角增加5 mm的砂箱垫铁,便 于合箱时上下铸型之间软接触,避免上下砂箱之间硬 接触,导致锁箱不紧浇注过程产生跑火现象。工艺简 图如图3所示。
产品的表面质量很差,产品在使用过程中这些缺陷将 逐渐脱落,严重污染气腔的气体和水腔的循环冷却水, 从而影响产品的使用性能。图10是我厂生产的缸体内 腔图片,内腔没有脉纹缺陷,铸件表面质量非常好。 彻底解决了产品在使用过程中存在的质量问题。经客 户加工验证,缸体质量符合图纸要求和使用性能要求。
图9 原缸体铸件 Fig. 9 Original cylinder casting
of scrap pipe
孕育。铁液上升到冒口位置时应降低浇注速度,同时停 止随流孕育,至浇满冒口后停止浇注。浇注开始必须注 意点火排气,以降低型内气体压力,同时防止跑火。
4 铸件质量检验结果
经过去应力热处理和清理打磨,产品进行了性能 检测和尺寸检测,都满足产品要求。由于事先工艺设 计考虑细致和生产准备充分,采取的措施落实有效, 解决了缸体气腔和水腔粘砂无法清理的质量问题,缸 体整体质量得到了很大的提高,铸件外观如图8所示。 图9是客户提供的原缸体铸件图片,内腔脉纹非常严 重,由于内腔无法采用工具进行清理去除脉纹,导致
sand
1 压缩机缸体铸件简介
压缩机缸体是由两层圆环组成的大型压力容器, 铸件质量要求较高,缸体的缸径不允许有疏松、夹砂、 气孔、粘砂等铸造缺陷,其他部位不允许焊补修复; 缸体的水腔需通过4 MPa的压力测试,缸体的气腔需通 过压缩机最大允许工作压力测试。生产的压缩机缸体 铸件的轮廓尺寸为:1 457 mm×816 mm×816 mm,材 质采用ASTM A278标准中的M-40,相当于中国牌号
图8 产品外观图片 Fig. 8 Photo showing the appearance of part
图10 现在生产的缸体铸件 Fig. 10 Cylinder after improvement
(编辑:刘冬梅,ldm@)
Oct. 2011 Vol.60 No.10
铸造
FOUNDRY
·1011·
压缩机缸体的铸造工艺
张证
(慈溪市汇丽机电有限公司,浙江慈溪 315333)
摘要:通过对压缩机缸体铸件结构的分析,进行了合理的工艺设计,并通过加强生产过程控制,解决了生产过程中出
现的粘砂和疏松等质量问题,生产出合格的铸件,为类似缸体的铸造提供了技术支持和成功经验。
图4 气腔砂芯图 Fig. 4 Sand core of gas cavity
图5 水腔砂芯图 Fig. 5 Sand core of water cavity
3.2 合箱及下芯过程 在摆放铸型下箱时事先在地面上平铺一层松软旧
砂,并勾划出排气凹槽,可以防止铸型被地面顶坏, 也可以保证浇注过程中底部排气通畅。还能防止浇注 过程中铁液飞溅。整个装配过程所有砂型和芯子必须 在造型2 h后才能涂刷涂料,涂刷涂料之前对型芯进行 检查和修补,将浮砂吹干净,同时用石棉绳将砂芯的 排气通道封堵,防止涂刷涂料过程中涂料进入,堵塞 通道。为防止烘干过程中砂芯变形,要注意摆放位置。 为防止粘砂,所有砂芯全部用醇基锆英粉涂料。由于 砂芯芯头很小,无法支撑砂芯重量和承受浇注过程铁 液的冲击,采用灰铁芯撑来支撑砂芯,芯撑的尺寸可经 过多次试验来确定,确保芯撑在充型过程中不会熔化, 在凝固过程中部分熔化。将芯撑固定在砂芯或者铸型 上,防止在合箱和浇注过程中芯撑移动导致产品报废。
下芯前用相应的砂芯检具检测砂芯尺寸是否发生 变形,砂芯装配好后必须用检具检测装配尺寸是否符 合要求。由于砂芯数量比较多,形状比较复杂,下芯 顺序要考虑周全,尤其是下箱的气腔砂芯和水腔砂芯 须先组合后才能不发生干涉。为此,在实际生产前采 用计算机模拟砂芯装配过程可以起到很好的指导作用。 所有砂芯,尤其是气腔和水腔砂芯在流涂完成后必须 用烘烤的方式检测砂芯的排气通道是否顺畅,如果有 漏气的地方必须进行修补,确保排气顺畅才能验收合 格。合箱的关键环节是必须将缸径砂芯的两端芯头密 封好,防止浇注过程中铁液钻入砂芯钢管导致产品报 废。另外一个关键环节就是气腔和水腔砂芯的排气通 道在装配砂芯过程中采用铁屑管连接并引出到铸型外 面,使浇注过程中砂芯产生的气体能迅速排出铸型。 铁屑管来源很广,有一定的强度和可塑性,是很好的 排气通道材料,如图6和图7所示。 3.3 熔炼和浇注过程