PLC高速计数器功能应用在定位控制上的案例
PLC高速脉冲输出PTO
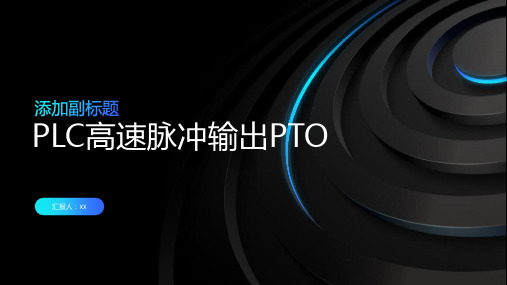
PLC高速脉冲输 出PTO的性能测 试与优化
性能测试的方法与工具
测试方法:使用专业的测试设备对PLC高速脉冲输出PTO进行性能测试,包括脉冲频 率、脉冲宽度、脉冲精度等参数的测量和校准。
测试工具:使用PLC编程软件、示波器、计数器等工具进行性能测试,确保测试结果 的准确性和可靠性。
测试环境:在符合PLC高速脉冲输出PTO技术规格的环境下进行性能测试,包括温度、 湿度、气压等环境因素的考虑和控制。
与传统的模拟量输出相比,PLC高速脉冲输出PTO具有更高的精度和更广泛的应 用范围。
PLC高速脉冲输出PTO的原理
高速脉冲输出PTO的工作原理是通过PLC控制器产生高速脉冲信号,控制电机等执行机构的运动。 PLC高速脉冲输出PTO的脉冲频率、脉冲宽度和脉冲极性等参数可以通过编程进行精确控制。 高速脉冲输出PTO在自动化控制系统中广泛应用于位置控制、速度控制和张力控制等领域。 PLC高速脉冲输出PTO的可靠性高,稳定性好,能够适应各种复杂环境下的工业控制需求。
添加标题
添加标题
配置脉冲输出模块
添加标题
添加标题
调试和测试脉冲输出功能
编程实例及解析
编程环境:使用PLC厂商提供 的编程软件或集成开发环境 (IDE)
编程语言:使用C++或 Python等高级语言进行编 程
编程步骤:编写程序逻辑,配 置脉冲参数,测试和调试等
实例解析:以实际应用为例, 分析编程实现的过程和技巧
感谢您的观看
汇报人:XX
PLC高速脉冲输出PTO的应用场景
自动化生产线 控制
机器人关节驱 动
伺服电机定位 控制
高速计数与测 量
PLC高速脉冲输 出PTO的参数设 置
手轮在三菱FXPLC定位控制系统中的应用
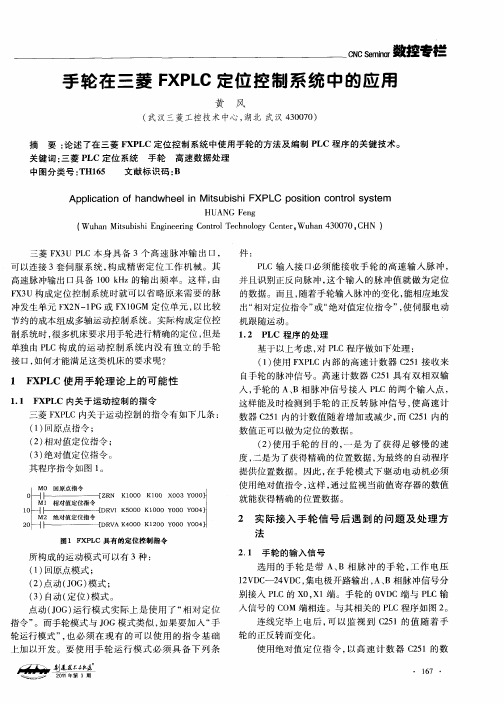
出“ 相对 定 位指令 ” “ 或 绝对值 定 位指 令 ” 使伺 服 电 动 ,
机 跟 随运 动。 1 2 P C 程序 的处 理 . L
基 于 以上考 虑 , P C程序 做如 下处 理 : 对 L () 1 使用 F P C内部 的高 速计 数 器 C 5 XL 2 1接 收来
使用绝 对 值 定 位 指 令 , 高 速 计 数 器 C 5 以 2 1的 数
;
ZU I I
点动 (O ) J G 运行 模 式 实 际上 是 使 用 了 “ 对 定 位 相
指令 ” 。而手轮模 式 与 J G模 式 类似 , O 如果 要 加入 “ 手
轮 运行模 式 ” 也 必 须 在 现 有 的可 以使 用 的指 令 基 础 , 上加 以开 发 。要 使 用 手 轮 运行 模 式 必 须 具 备 下 列 条
数 值正 可 以做 为 定位 的数据 。 () 2 使用 手 轮 的 目的 , 是 为 了获 得 足 够 慢 的速 一 度, 二是 为 了获得 精确 的位 置数据 , 最终 的 自动 程序 为 提 供位 置数据 。因此 , 手 轮模 式 下 驱 动 电动 机必 须 在
,
三菱 F P C内关 于运动 控制 的指令 有如 下几 条 : XL
手轮 在 三 菱 F P C定 位 控 制 系统 中 的应 用 X L
黄 风
( 汉 三菱工 控技术 中心 , 武 湖北 武汉 4 0 7 ) 300
摘
要 : 论述 了在 三菱 F P C定位 控制 系统 中使 用手轮 的方 法及编 制 P C程 序 的关键 技术 。 X L L 手轮 高速数 据处理
() 1 回原 点指令 ; () 2 相对 值定位 指令 ;
PLC高速计数器在传送带位置控制中的应用
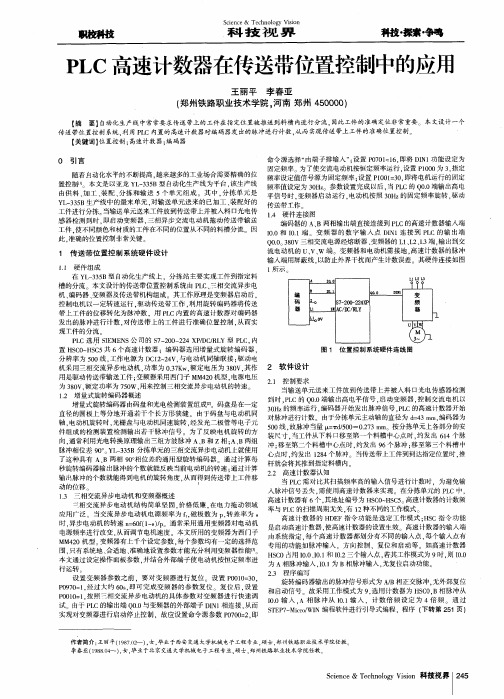
输 出脉 冲的个数就能得到 电机 的旋转角度 .从而得到传 送带上工件移
动 的位 移
’
当 PLC需 对比其扫描频率高的输入信号进行计数时 .为避免输
入脉 冲信号丢失 .需使用 高速计数器来 实现 在分拣单元 的 PLC中.
1_3 三相交流异步 电动机和变频器概述
高速计数器有 6个 .其地址编号为 HSC0~HSC5。高速计数器 的计数频
当输送单元送来工件放 到传送带上并被人料 口光电传感器检测
1.2 增 量式旋转编码器概述
到时 .PLC的 QO.0端输 出高电平信号 .启动变频 器 .控制交 流电机 以
增量式旋转编码器 由码盘和光电检测装 置组成 码盘是 在一定 30H 的频率运行 .编码 器开始发出脉冲信 号 .PLC的高速计数器开始
脉 冲相位差 90。。YL一335B分拣单元 的三相交流异步 电动机上就使 用 心点时 .约发出 1284个脉冲。当传送带上工件I!Iiii达指定位置时 ,推
了这种具有 A、B两相 90。相位差 的通用 型旋转编码器 。通过计算 每 杆就会将其推到指定料槽 内
秒 旋转编码器输 出脉 冲的个数就能反映当前电动机的转 速 :通过计 算 2.2 高速计数器认 知
相 交流异步电动机结构简单 坚固 .价格低廉 .在 电力拖 动领域 率与 PLC的扫描周期无关 .有 12种 不同的工作模式。
编 B 尬.1
码 王_。 器 Ll
S7—2Oo-224XP IPLC选 用 SIEMENS公 司 的 s7—200—224 XP/DC/RLY 型 PLC.内
置 HSC0~HSC5共 6个高速计数器 :编码器选用增 量式旋转编码 器 .
图 1 位 置 控 制 系统 硬 件 连 线 图
S7-200系列PLC编程器的高速计数器使用示例

S7-200系列PLC编程器的使用示例Siemens编程器S7-200系列用在中小型设备上的自动系统的控制单元,适用于各行各业,各种场合中的检测,监测及控制。
在这里,和大家一起来讨论S7-200几个使用方面的情况。
1.步进,伺服脉冲定位控制。
在设备的控制系统中,有关运动控制是很重要的,下面我们来看一看西门子S7-200系列PLC怎样来实现这个功能。
首先,确定使用哪个端口来发脉冲,如采用Q0.0发脉冲,则它的控制字为SMB67,脉冲同期为SMW68,脉冲个数存放在SMD72中,下面是控制字节的说明:Q0.0 Q0.1 控制字节说明SM67.0 SM77.0 PTO/PWM更新周期值 0=不更新,1=更新周期值SM67.1 SM77.1 PWM更新脉冲宽度值 0=不更新,1=脉冲宽度值SM67.2 SM77.2 PTO更新脉冲数 0=不更新,1=更新脉冲数SM67.3 SM77.3 PTO/PWM时间基准选择 0=1微秒值,1=1毫秒值SM67.4 SM77.4 PWM更新方法 0=异步更新,1=同步更新SM67.5 SM77.5 PTO操作 0=单段操作,1=多段操作SM67.6 SM77.6 PTO/PWM模式选择 0=选择PTO,1=选择PWMSM67.7 SM77.7 PTO/PWM允许 0=禁止PTO/PWM,1=允许这样根据以上表格,我们得出Q0.0控制字:SMB67为:10000101采用PTO输出,微妙级周期,发脉冲的周期(也就是频率)与脉冲个数都要重新输入。
10000101转化为16进制为85,有了控制字以后,我们来写这一段程序:根据上面这段程序,我们知道了控制字的使用,同时也知道步进电机的脉冲周期与冲个数的存放位置(对Q0.0来说是SMW68与SMD72)。
当然,VW100与VD102内的数据不同的话,步进电机的转速和转动圈数就不一样。
还有一点需要说明得是:M0.0导通---PLC捕捉到上升沿发动脉冲输出后,想停止的话,只须改变端口脉冲的控制字,再启动PLS即可,程序如下:2.高速计数功能。
PLC控制伺服电机实现定位控制
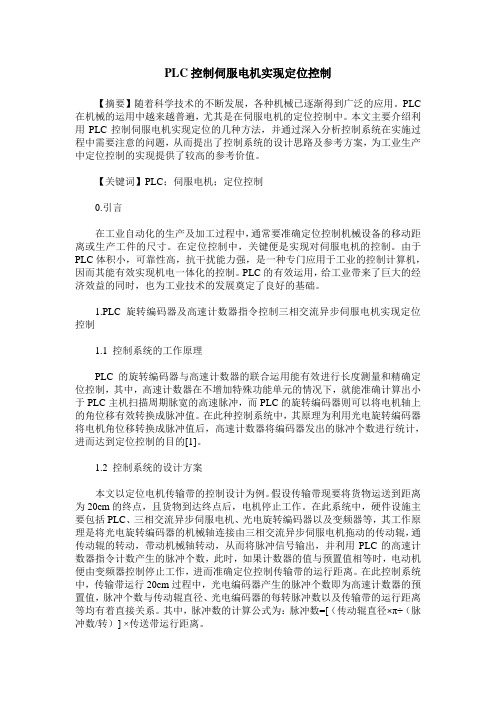
PLC控制伺服电机实现定位控制【摘要】随着科学技术的不断发展,各种机械已逐渐得到广泛的应用。
PLC 在机械的运用中越来越普遍,尤其是在伺服电机的定位控制中。
本文主要介绍利用PLC控制伺服电机实现定位的几种方法,并通过深入分析控制系统在实施过程中需要注意的问题,从而提出了控制系统的设计思路及参考方案,为工业生产中定位控制的实现提供了较高的参考价值。
【关键词】PLC;伺服电机;定位控制0.引言在工业自动化的生产及加工过程中,通常要准确定位控制机械设备的移动距离或生产工件的尺寸。
在定位控制中,关键便是实现对伺服电机的控制。
由于PLC体积小,可靠性高,抗干扰能力强,是一种专门应用于工业的控制计算机,因而其能有效实现机电一体化的控制。
PLC的有效运用,给工业带来了巨大的经济效益的同时,也为工业技术的发展奠定了良好的基础。
1.PLC旋转编码器及高速计数器指令控制三相交流异步伺服电机实现定位控制1.1 控制系统的工作原理PLC的旋转编码器与高速计数器的联合运用能有效进行长度测量和精确定位控制,其中,高速计数器在不增加特殊功能单元的情况下,就能准确计算出小于PLC主机扫描周期脉宽的高速脉冲,而PLC的旋转编码器则可以将电机轴上的角位移有效转换成脉冲值。
在此种控制系统中,其原理为利用光电旋转编码器将电机角位移转换成脉冲值后,高速计数器将编码器发出的脉冲个数进行统计,进而达到定位控制的目的[1]。
1.2 控制系统的设计方案本文以定位电机传输带的控制设计为例。
假设传输带现要将货物运送到距离为20cm的终点,且货物到达终点后,电机停止工作。
在此系统中,硬件设施主要包括PLC、三相交流异步伺服电机、光电旋转编码器以及变频器等,其工作原理是将光电旋转编码器的机械轴连接由三相交流异步伺服电机拖动的传动辊,通传动辊的转动,带动机械轴转动,从而将脉冲信号输出,并利用PLC的高速计数器指令计数产生的脉冲个数,此时,如果计数器的值与预置值相等时,电动机便由变频器控制停止工作,进而准确定位控制传输带的运行距离。
PLC高速计数器在龙门刨床位控中的应用
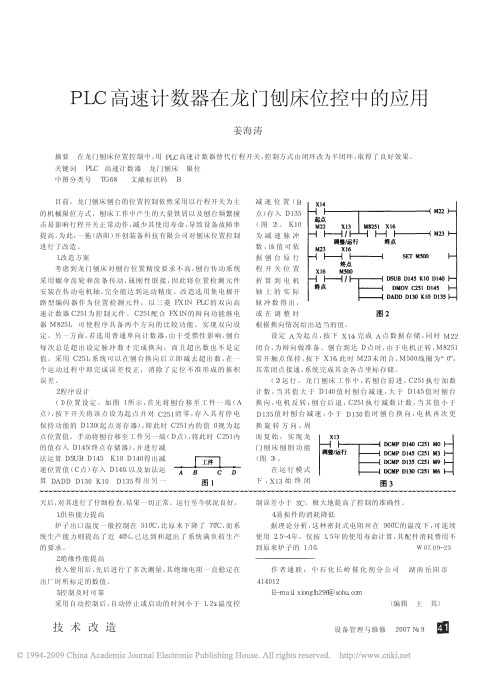
目前,龙门刨床刨台的位置控制依然采用以行程开关为主的机械限位方式,刨床工作中产生的大量铁屑以及刨台频繁撞击易影响行程开关正常动作,减少其使用寿命,导致设备故障率提高。
为此,一拖(洛阳)开创装备科技有限公司对刨床位置控制进行了改造。
1.改造方案考虑到龙门刨床对刨台位置精度要求不高,刨台传动系统采用螺伞齿轮和齿条传动,属刚性联接,因此将位置检测元件安装在传动电机轴,完全能达到运动精度。
改造选用集电极开路型编码器作为位置检测元件,以三菱FX1NPLC的双向高速计数器C251为控制元件。
C251配合FX1N的辩向功能继电器M8251,可使程序具备两个方向的比较功能,实现双向设定。
另一方面,若选用普通单向计数器,由于受惯性影响,刨台每次总是超出设定脉冲数才完成换向,而且超出数也不是定值。
采用C251,系统可以在刨台换向后立即减去超出数,在一个运动过程中即完成误差校正,消除了定位不准形成的累积误差。
2.程序设计(1)位置设定。
如图1所示,首先将刨台移至工件一端(A点),按下开关将该点设为起点并对C251清零,存入具有停电保持功能的D130(起点寄存器),即此时C251内的值0视为起点位置值。
手动将刨台移至工件另一端(D点),将此时C251内的值存入D145(终点存储器),并进行减法运算DSUBD145K10D140得出减速位置值(C点)存入D140,以及加法运算DADDD130K10D135得出另一减速位置(B点)存入D135(图2)。
K10为减速脉冲数,该值可依据刨台原行程开关位置折算到电机轴上的实际脉冲数得出,或在调整时根据换向情况给出适当的值。
设定A为起点,按下X14,完成A点数据存储,同时M22闭合,为辩向做准备。
刨台到达D点时,由于电机正转,M8251常开触点保持,按下X16,此时M23未闭合,M500线圈为“0”,其常闭点接通,系统完成其余各点坐标存储。
(2)运行。
龙门刨床工作中,若刨台前进,C251执行加数计数,当其值大于D140值时刨台减速,大于D145值时刨台换向,电机反转;刨台后退,C251执行减数计数,当其值小于D135值时刨台减速,小于D130值时刨台换向,电机再次更换旋转方向,周而复始,实现龙门刨床刨削功能(图3)。
三菱plc高速计数器使用实例三菱plc

三菱plc高速计数器使用实例 - 三菱plc 高速计数器是指能计算比一般扫描频率更快的脉冲信号,它的工作原
理与一般计数器类似,只是计数通道的响应时间更短。
在越来越多的
把握过程中需要对高速脉冲信号进行处理,而一般的计数方式远远不
能满足要求。
为此需要用到高速计数器。
计数器是plc内部重要的软
元件之一,高速计数器是plc计数器中常用的一种,PLC 内部有两种
计数器,一种是对PLC内部信号进行计数的计数器,另一种是对外部
大事信号进行计数的计数器。
一:高速计数器种类和软元件编号1、高速计数的种类基本单元内置了32位增减计数器的高速计数器(单
相计数/单相双计数/双相双计数),依据计数方法的不同可以分为硬
件计数器和软件计数器两种在高速计数器中,供应了可以选择外部复
位输入端子和外部启动输入端子开头计数的功能。
2、高速计数器的
区分硬件计数器:这种计数器是通过硬件进行计数。
软件计数器:
这种计数器是通过CPU中断处理进行计数,每个计数器需要在最大响
应频率和综合频率的两个限制条件下使用。
3、高速计数器的种类和
输入信号的形式 4、高速计数器软元件一览
二:高速计数器输入安排对应各个高速计数器的编号,X000-X007
安排表如下
三、高速计数器使用1、单相单计数的输入
2、单相双计数的输入
3、双相双计数的输入。
电气控制与PLC(案例教程)教学课件第11章 S7-200PLC高速计数和脉冲输出指令及应用——以

• (4)切割刀回程触发BG2限位开关后,回程结束。 • (5)设备再次运行进行下一次物料进给切割,循环往复,将材料切分成长度相同的成品。
11.2 步进电动机及驱动器
• (4)在启动中断程序之前,必须使中断事件与发生此事件时希望执行的程序段建立联系,使用ATCH指令建 立中断事件与程序段之间的联系。将中断事件连接到中断程序时,该中断自动被启动。根据指定事件优先 级组,PLC按照先来先服务的顺序对中断提供服务。
• (5)中断调用即调用中断程序,使系统对特殊的内部事件产生响应。系统响应中断时自动保存逻辑堆栈、 累加器和某些特殊标志存储器位,即保护现场。中断处理完成时又自动恢复这些单元原来的状态,即恢复 现场。
• 当把中断程序连接到定时中断事件上,如果该定时中断被允许,则开始计时,定时中断就连续 地运行,每当达到定时时间值,执行中断程序。通常可用定时中断以固定的时间间隔对模拟量输 入进行采样或者执行PID控制回路。
• 2)定时器T32/T96中断允许对定时时间间隔产生中断。这类中断只支持1ms分辨率的定时器 T32和T96。当定时器的当前值等于预设值时,响应中断,在CPU的正常1ms定时刷新中,执行 中断程序。
• CPU响应中断的原则:当不同优先级别的中断事件同时向CPU发出中断请求时,CPU总是 按照优先级别由高到低的顺序响应中断。在任何时刻,CPU只执行一个中断程序。一旦中断程 序开始执行,它要一直执行到结束,而且不会被别的中断程序,甚至是更高优先级的中断程序所 打断。中断程序执行中,新出现的中断请求按优先级和到来时间的先后顺序进行排队等候处理。
如何实现台达PLC和变频器的位置控制
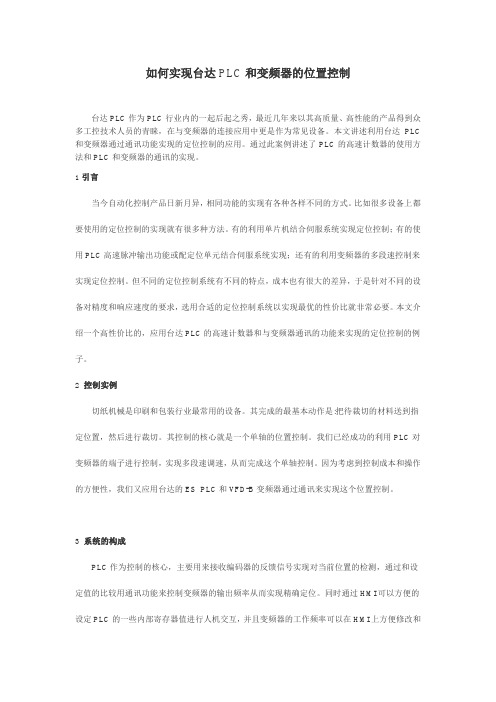
如何实现台达PLC和变频器的位置控制台达PLC作为PLC行业内的一起后起之秀,最近几年来以其高质量、高性能的产品得到众多工控技术人员的青睐,在与变频器的连接应用中更是作为常见设备。
本文讲述利用台达PLC 和变频器通过通讯功能实现的定位控制的应用。
通过此案例讲述了PLC的高速计数器的使用方法和PLC和变频器的通讯的实现。
1引言当今自动化控制产品日新月异,相同功能的实现有各种各样不同的方式。
比如很多设备上都要使用的定位控制的实现就有很多种方法。
有的利用单片机结合伺服系统实现定位控制;有的使用PLC高速脉冲输出功能或配定位单元结合伺服系统实现;还有的利用变频器的多段速控制来实现定位控制。
但不同的定位控制系统有不同的特点,成本也有很大的差异,于是针对不同的设备对精度和响应速度的要求,选用合适的定位控制系统以实现最优的性价比就非常必要。
本文介绍一个高性价比的,应用台达PLC的高速计数器和与变频器通讯的功能来实现的定位控制的例子。
2 控制实例切纸机械是印刷和包装行业最常用的设备。
其完成的最基本动作是:把待裁切的材料送到指定位置,然后进行裁切。
其控制的核心就是一个单轴的位置控制。
我们已经成功的利用PLC对变频器的端子进行控制,实现多段速调速,从而完成这个单轴控制。
因为考虑到控制成本和操作的方便性,我们又应用台达的ES PLC和VFD-B变频器通过通讯来实现这个位置控制。
3 系统的构成PLC作为控制的核心,主要用来接收编码器的反馈信号实现对当前位置的检测,通过和设定值的比较用通讯功能来控制变频器的输出频率从而实现精确定位。
同时通过HMI可以方便的设定PLC的一些内部寄存器值进行人机交互,并且变频器的工作频率可以在HMI上方便修改和直观显示。
台达的DVP系列PLC都具有两个通讯口,COM1是RS232,COM2是RS485,支持ModBus ASCII/RTU通讯格式,通讯速率最高可达115200bps,两通讯口可以同时使用。
台达PLC高速计数器在位置控靛中的应用
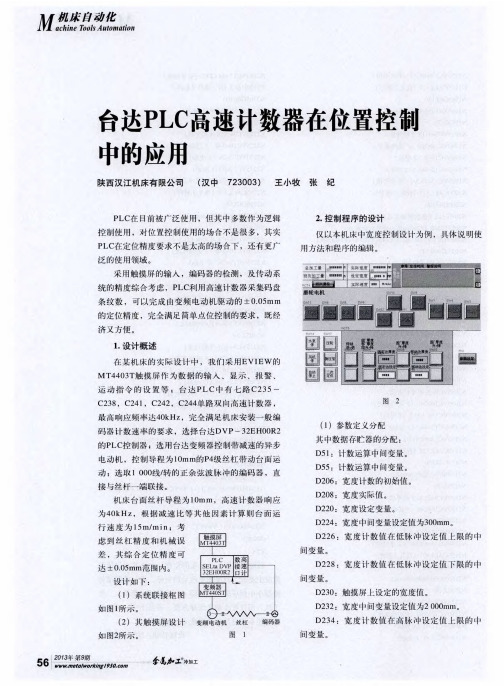
D 2 3 6 ' <D 2 5 3 <D 2 3 4 控 制s 3 变频器 1 高速
MI l
度达 到 ±0 . 0 5 mm范围内 ,完全满足加 工精度的要 求。用户对该使用效果非常满意。 此方 法在木材加工 、玻璃加工 ,以及要求不高 的金属加工的领域都可广泛的使用,拓宽 了P L C 的
控 制s 2 变频器 1 反 转
M8 3
设定 实际宽 度一致
— —
_ 1 / 卜 — — — — ቤተ መጻሕፍቲ ባይዱ — — — — — — —— ' ( M 2 4 0 卜 一
宽度标 志
M2 3 0
M 8 3
设 定实 际宽度一致
设 定实际宽 度一致
M8 3
控 制s 4 变频器 1 低 速
机床 自动化
a c h i n e T o o I s Au t o ma r i o n
D2 3 6 :宽 度计 数值在 高脉冲设定 值下限 的中
间变 量 。
D2 3 8 :宽度设定值与实际值之差变量。
其 中 高速 计 数 器 的分 配 :
C 2 5 3 :宽度脉冲编码器的计数 。 ( 2 )程序流程如图3 所示。
5 8
・参
籼工
图 6
参 曷 冷 加 工
毒 G 7
机 沫 自动 化
速 运 行 ,如 图 1 O 所示 。
DC MP D t 2 2 0 D2 0 8 M 8 3
传机
动输
—
0 M8 3
宽 度设 宽 度 设定实 际 定变 量 实 际值 宽度一 致 :
/ 卜 — — — — — — — — — —— - { M 2 1 0 卜 一
PLC控制伺服电机准确定位的方法

PLC控制伺服电机准确定位的方法在自动化生产、加工和控制过程中,经常要对加工工件的尺寸或机械设备移动的距离进行准确定位控制。
这种定位控制仅仅要求控制对象按指令进入指定的位置,对运动的速度无特殊要求,例如生产过程中的点位控制(比较典型的如卧式镗床、坐标镗床、数控机床等在切削加工前刀具的定位),仓储系统中对传送带的定位控制,机械手的轴定位控制等等。
在定位控制系统中常使用交流异步电机或步进电机等伺服电机作为驱动或控制元件。
实现定位控制的关键则是对伺服电机的控制。
由于可编程控制器(PLC)是专为在工业环境下应用而设计的一种工业控制计算机,具有抗干扰能力强、可靠性极高、体积小等显著优点,是实现机电一体化的理想控制装置。
本文旨在阐述利用PLC控制伺服电机实现准确定位的方法,介绍控制系统在设计与实施中需要认识与解决的若干问题,给出了控制系统参考方案及软硬件结构的设计思路,对于工业生产中定位控制的实现具有较高的实用与参考价值。
1 利用PLC的高速计数器指令和旋转编码器控制三相交流异步电机实现的准确定位1.1 系统工作原理PLC的高速计数器指令和编码器的配合使用,在现代工业生产自动控制中可实现精确定位和测量长度。
目前,大多数PLC都具有高速计数器功能,例如西门子S7-200系列CPU226型PLC有6个高速计数器。
高速计数器可以对脉宽小于PLC主机扫描周期的高速脉冲准确计数,不需要增加特殊功能单元就可以处理频率高达几十或上百kHz的脉冲信号。
旋转编码器则可以将电动机轴上的角位移转换成脉冲值。
利用PLC的高速计数器指令和编码器控制三相交流异步电机实现的准确定位控制系统,其原理是通过与电动机同轴相连的光电旋转编码器将电机角位移转换成脉冲值,经由PLC的高速计数器来统计编码器发出的脉冲个数,从而实现定位控制。
1.2 设计与实施以对传输带的定位控制设计为例加以说明。
现需要用传输带运送货物,从货物运送起点到指定位置(终点)的距离为10 cm。
基于PLC的定位控制功能的实现
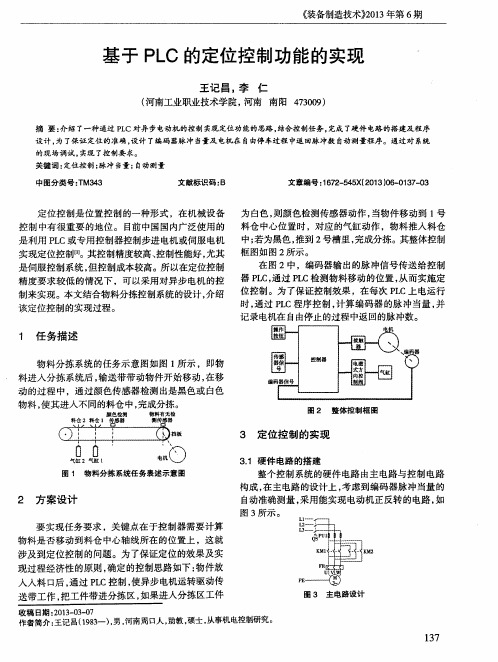
榭
P E ——_ _ ( 图3 主电 路设计
作 霎 者 昙 简 介 : 王 记 昌 ( 1 9 8 3 一 ) . , 男 。 , 河 南 周 口 人 , 助 教 , 硕 士 , 从 事 机 电 控 制 研 究 。
1 3 7
Eq u i p me n t Ma n u f a c t u r i n g T e c h n o l o g y No . 6, 2 0 1 3
1 任务描 述
物料分拣系统 的任务示意图如图 1 所示 ,即物 料进入分拣 系统后 , 输送带带动物件开始移动 , 在移 动 的过程 中 ,通过颜色传感器检测 出是黑色或 白色 物料 , 使其进入不 同的料仓 中, 完成分拣 。
颜色检测 物料 有无检 r 器信号 控制器
图2 整体 控 制 框 图
口,具有 P P I 通讯协议 、 M P I 通讯协议和 自由方式通 讯能力[ 3 1 。编码器选用增量式 光电编码器 , 旋转一周 返回5 0 0 个脉冲。根据 图 3 、 4 完成 主电路及控制线
路 的安 装 。
依据编程思路 , 在S 7 — 2 0 0 对应 的编程 软件中完 成程序 的设计 , 编译成功后 , 通过 P P I 电缆线 下载到 L C控制器中。运行调试表 明, 可实现预定的功能 。 电式接 近开关和光纤式接近开关完成 。在 P L C的选 P 择上 , 需 要考虑 P L C外 围电路 的输入 、 输 出形式 、 技 术参数及 I / O点数 的要求 , 同时要求选择 的控制器具 r — 赢 备高速计数模块的功能 。根据选择的 P L C 及外 围电 路, 确定电源 的形式及 电压高低。编码器选择 了增量 式光电编码器 , 输 出三组方波脉冲 A 、 B和 Z 相, 其中 存 储 蓥 番 罡 雾 翥 器 霉 脉 冲 A、 B两路为正交脉 冲信号 , z相 为每转一个 脉冲 , 用 记 录每 銎 霪 齿 肇 嚣 脉 冲 于基 准 点定 位 。控 制 电路 如 图 4所示 。
PLC高速计数器在传送带位置控制中的应用

0引言随着自动化水平的不断提高,越来越多的工业场合需要精确的位置控制[1]。
本文是以亚龙YL-335B型自动化生产线为平台,该生产线由供料、加工、装配、分拣和输送5个单元组成。
其中,分拣单元是YL-335B生产线中的最末单元,对输送单元送来的已加工、装配好的工件进行分拣。
当输送单元送来工件放到传送带上并被入料口光电传感器检测到时,即启动变频器,三相异步交流电动机拖动传送带输送工件,使不同颜色和材质的工件在不同的位置从不同的料槽分流。
因此,准确的位置控制非常关键。
1传送带位置控制系统硬件设计1.1硬件组成在YL-335B型自动化生产线上,分拣站主要实现工件到指定料槽的分流。
本文设计的传送带位置控制系统由PLC、三相交流异步电机、编码器、变频器及传送带机构组成。
其工作原理是变频器启动后,控制电机以一定转速运行,驱动传送带工作,利用旋转编码器将传送带上工件的位移转化为脉冲数,用PLC内置的高速计数器对编码器发出的脉冲进行计数,对传送带上的工件进行准确位置控制,从而实现工件的分流。
PLC选用SIEMENS公司的S7-200-224XP/DC/RLY型PLC,内置HSC0~HSC5共6个高速计数器;编码器选用增量式旋转编码器,分辨率为500线,工作电源为DC12~24V,与电动机同轴联接;驱动电机采用三相交流异步电动机,功率为0.37Kw,额定电压为380V,其作用是驱动传送带输送工件;变频器采用西门子MM420机型,电源电压为380V,额定功率为750W,用来控制三相交流异步电动机的转速。
1.2增量式旋转编码器概述增量式旋转编码器由码盘和光电检测装置组成[2]。
码盘是在一定直径的圆板上等分地开通若干个长方形狭缝。
由于码盘与电动机同轴,电动机旋转时,光栅盘与电动机同速旋转,经发光二极管等电子元件组成的检测装置检测输出若干脉冲信号。
为了反映电机旋转的方向,通常利用光电转换原理输出三组方波脉冲A、B和Z相;A、B两组脉冲相位差90°。
fx3u定位控制实例

fx3u定位控制实例FX3U是三菱电机推出的一款高性能PLC,可广泛应用于自动化控制系统中。
其中,定位控制是FX3U的一项重要功能,可以实现对机械装置的精确定位和运动控制。
本文将以FX3U定位控制实例为主题,介绍其原理和应用。
一、定位控制的原理定位控制是通过控制电机的运动,使得被控制物体精确移动到预定位置的过程。
在FX3U中,定位控制主要依靠PLC的高速计数器和脉冲输出功能来实现。
需要通过高速计数器来接收外部脉冲信号,通常是由编码器或脉冲发生器产生的。
高速计数器能够精确地计算脉冲的数量,从而确定电机的位置。
然后,PLC会根据设定的目标位置和当前位置之间的差值,计算出控制电机需要输出的脉冲数量。
接下来,FX3U通过脉冲输出功能将计算得到的脉冲信号发送给电机驱动器,驱动器会根据接收到的脉冲信号控制电机的转动角度和速度。
通过连续输出脉冲信号,电机可以逐步移动到目标位置,实现定位控制。
二、FX3U定位控制的应用FX3U的定位控制功能广泛应用于各种自动化设备和生产线中,以下以一个简单的装配机器人为例,介绍FX3U定位控制的应用过程。
装配机器人通常由多个电机和传感器组成,通过定位控制实现对零部件的精确装配。
首先,需要将机器人的各个关节与电机相连,并安装编码器用于测量电机的转动角度。
然后,通过编程设置FX3U 的高速计数器和脉冲输出功能,使其能够接收编码器的脉冲信号并控制电机的运动。
在装配过程中,传感器可以感知到待装配零部件的位置和状态,并将信号传输给FX3U。
FX3U根据传感器的信号确定待装配零部件的位置,然后计算出电机需要输出的脉冲数量。
通过控制电机的输出脉冲信号,机器人的各个关节可以精确地移动到目标位置,完成零部件的装配。
除了装配机器人,FX3U定位控制还可以应用于印刷机械、包装设备、数控机床等领域。
在印刷机械中,通过定位控制可以实现印刷品的对位精确度,提高印刷质量。
在包装设备中,定位控制可以使得包装物料准确地进入包装盒中,提高生产效率。
- 1、下载文档前请自行甄别文档内容的完整性,平台不提供额外的编辑、内容补充、找答案等附加服务。
- 2、"仅部分预览"的文档,不可在线预览部分如存在完整性等问题,可反馈申请退款(可完整预览的文档不适用该条件!)。
- 3、如文档侵犯您的权益,请联系客服反馈,我们会尽快为您处理(人工客服工作时间:9:00-18:30)。
PLC高速计数器功能应用在定位控制上的案例
一、概述
切纸机械是印刷和包装行业最常用的设备之一。
切纸机完成的最基本动作是把待裁切的材料送到指定位置,然后进行裁切。
其控制的核心是一个单轴定位控制。
我公司引进欧洲一家公司的两台切纸设备,其推进定位系统的实现是利用单片机控制的。
控制过程是这样的,当接收编码器的脉冲信号达到设定值后,单片机系统输出信号,断开进给电机的接触器,同时电磁离合制动器的离合分离,刹车起作用以消除推进系统的惯性,从而实现精确定位。
由于设备的单片机控制系统老化,造成定位不准,切纸动作紊乱,不能正常生产。
但此控制系统是早期产品,没有合适配件可替换,只能采取改造这一途径。
目前国进行切纸设备进给定位系统改造主要有两种方式,一是利用单片机结合变频器实现,一是利用单片机结合伺服系统实现,不过此两种改造方案成本都在两万元以上。
并且单片机系统是由专业开发公司设计,技术保守,一旦出现故障只能交还原公司维修或更换,维修周期长且成本高,不利于改造后设备的维护和使用。
我们结合自己设备的特点提出了新的改造方案,就是用PLC的高速计数器功能结合变频器的多段速功能实现定位控制,并利用HMI(人机界面HumanMachineInterface)进行裁切参数设定和完成一些手动动作。
二、改造的可行性分析
现在的大多PLC都具有高速计数器功能,不需增加特殊功能单元就可以处理频率高达几十或上百KHz的脉冲信号,而切纸机对进给系统的精度和响应速度要求不是很高。
可以通过对切纸机进给系统相关参数的计算,合理的选用编码器,让脉冲频率即能在PLC处理的围又可以满足进给的精度要求。
在进给过程中,让PLC对所接收的脉冲数与设定数值进行比较,根据比较结果驱动相应的输出点对变频器进行输出频率的控制,实现接近设定值时进给速度变慢,从而减小系统惯性,达到精确定位的目的。
另外当今变频器技术取得了长足的发展,使电机在低速时的转矩大幅度提升,从而也保证了进给定位时低速推进的可行性。
三、主要控制部件的选取
1、PLC的选取
设备需要的输入输出信号如下:
x0脉冲输入
x1脉冲输入
x2前限位
x3后限位y3前进!
x4前减速位y4后退
x5电机运转信号y5高速
x6刀上位y6中速
x7滑刀保护y7低速
x10压纸器上位y10
x11光电保护y11
x12小车后位y12进给离合
x13双手下刀按钮y13压板下
x14停止按钮y14刀离合
x15连杆保护y15电机禁启动
x16刀回复到位
针对这些必需的输入点数,选用了FX1s-30MR的PLC,因为选用了人机界面,其它一些手动动作,如前进、后退、换刀等都通过人机界面实现,不需占用PLC输入点,从而为选用低价位的FX1s系列PLC成为可能,因为FX1s系列PLC输入点最多只有16点。
另外此系列PLC
的高速计数器具有处理频率高达60千赫的脉冲的能力,足可以满足切纸机对精度的要求。
2、编码器的选取
编码器的选取要符合两个方面,一是PLC接收的最高脉冲频率,二是进给的精度。
我们选用的是编码器分辨率是500P/R(每转每相输出500个脉冲)的。
通过验正可以知道此分辨率可以满足上面两个条件。
验证所需的参数:电机最高转速是1500转/分(25转/秒)、进给丝杆的导程是10mm/转。
验证如下:
本系统脉冲最高频率=25转/秒×500个/转×2(A/B两相)=25KHz
理论进给分辨率=10mm/500=0.02mm
同时由上面的数据知道进给系统每走1mm编码器发出50(此数据很重要,在PLC程序的数据处理中要用到)个脉冲信号。
由于此工程中对编码器的A/B相脉冲进行了分别计数,使用了两个高速计数器,且在程序中应用了高速定位指令,则此PLC可处理的最高脉冲频率为30千赫,因此满足了第一个条件;我们的切纸机的载切精度要0.2mm,可知理论精度完全满足此要求。
3、变频器和HMI的选取
这两个部件我们都选用了三菱公司的产品,分别是FR-E540-0.75K-CH和F920GOT-BBD-K-C。
四、F920GOT-BBD-K-C的特点
F920GOT是带按键型的HMI,它的使用和编程非常简单方便。
它具有以下特点:1)可以方便的实现和PLC的数据交换;2)通过本身自带的6个功能按键开关,可以控制PLC部的软继电器,从而可以减少PLC输入点的使用;3)具有两个通讯口,一个RS232C(用于和个人电脑通讯)和一个RS422(用于和PLC通讯),利用电脑和F920GOT相连后不仅可以对HMI进行程序的读取和上传,还可以直接对PLC的程序进行上传下载、调整和监控。
五、PLC和HMI程序的编写
此工程中程序的难点主要在于数据的处理上。
在切纸机工作过程中除手动让进给定位机构前进后退外,还要实现等分裁切功能和指定具体位置定位功能,并且HMI上还要即时显示定位机构的当前位置。
我们为了简化程序中的计算,采用了两个高速计数器C235和C236。
C236通过计算前进后退的脉冲数,再进行换算后用于显示进给机构的当前位置;C235用于进行精确定位。
定位过程是这样的,每次进给机构需要定位工作时,通过计算把需要的脉冲数送到C235,不论进给机构前进还是后退C235进行减计数,同时对C235中的数值进行比较,根据比较结果驱动相应的输出点对变频器进行输出频率的控制,实现接近设定值时进给速度变慢,从而达到精确定位。
因为任何系统都有惯性和时间上的迟滞,所以变频器停止输出的时间并不是C235中的计数值减小到0时,而是让C235和一个数据寄存器D130比较,当C235中的值减小到D130中的设定值时PLC控制变频器停止输出。
D130的值可通过人机界面进行修改和设定,在调试时通过修改这个值,以达到定位准确的目的。
显示定位机构当前位置的程序见下图1,
图1 显示定位机构当前位置程序段
实现定位控制的程序段见下图2。
图2 定位程序段
还有一个问题是参数设定时的小数点位问题,实际工作中在设定位置时要精确到0.1mm。
这个问题在一些单片机系统中常会遇到,常见的处理办法是加大一个数量级,就是设定数据时,在人机界面上用1代替0.1mm,10代替1mm。
不过我们在处理此问题时通过HMI中对数据的设置和PLC的程序编写达到了所见即所得的效果。
HMI中主要是对数值的格式要设定好。
HMI 中的设置画面见下图。
图3 HMI中数据设置画面
比如我要等分裁切10.5mm的纸,就可以在HMI上设定为10.5,而不是像我公司其它设备上要设为105,但PLC的寄存器D128的容是105而不是10.5,这样在计算需要的脉冲数时就要用下面一条命令:
MULD128K5D10(此命令中尽管编程时D11不出现但实际上寄存器D11被占用,不能再应用于其它地方,否则会出现问题。
)
而不是用:
MULD128K50D10
编程中其它应注意的问题。
一是双线圈问题。
本工程中利用条件跳转和步进指令避免了双线圈问题。
二是误信号问题。
编码器是一种比较精密的光电产品,受振动时不可避免的会出现误信号,而切纸机在执行裁切动作时会造成很大振动,如果忽视这个现象,定位精度和执行机构当前位置的显示都会不准确。
本工程中处理方法参见上面例子程序图1,只有Y3、Y4接通,即只有进给机构前进和后退时才让C236进行计数,这样就屏蔽了裁切时震动造成的误信号。
六、变频器的参数设置
此工程中需设定的变频器的主要参数见下。
参数号名称设定值
0转矩提升8%(低速时电机转矩不足时可提高此数字)
43速设定(高速)30Hz
53速设定(中速)10Hz
63速设定(低速)2Hz
7加速时间0.5s
8减速时间0.5s
24多段速设定(4速)50Hz
79操作模式2(只执行外部操作)
在调试过程中为了达到定位速度和精度的完美结合,应对三段速设定值,加减速时间和HMI
中D130、D200和D202的数值进行相应调整。
七、结论
通过上述的改造过程,完全恢复了我们切纸机的功能,试用三个月以来运行非常稳定。
由这个应用实例可以看出结合PLC的高速计数器功能,合理的进行应用,在一定场合可以取代高成本的定位控制系统,实现控制系统最优的性价比。
也迎合了我国当前提出的建设节约型社会的宗旨。