免硬化解决分层水玻璃精密铸造制壳面层、过渡层新工艺
水玻璃精密铸造制壳工艺新型配方与传统配方比较

水玻璃精密铸造制壳工艺新型配方与传统配方比较一:大幅度提高表面质量..传统配方下;特别是在生产单件二十公斤以上的铸件;表面质量难以保证;表面毛刺、粘砂、表面癞蛤蟆皮、桔子皮及分层引起的缺陷难以避免..在生产厚大件时;表面几乎都要靠打磨才能满足要求..新型配方则完全解决了上述问题;几乎所有材质除了含锰大于4%的材质外的铸件达到甚至超过了复合型型壳的水平..二:大幅度提高内在质量..采用传统配方;由于表面层强度低;在型壳焙烧后;用手在型壳内壁上摸;经常会发现掉白灰的情况;还有采用传统配方;表面层制壳工艺复杂;影响因素很多;导致表面型壳质量很不稳定;型壳分层时有发生;这些因素导致传统的水玻璃型壳的铸件内部质量得不到保证;特别是在要求高的加工面上;时常因为加工出砂孔等缺陷导致铸件报废;这其中有相当部分是型壳质量差造成的;而新型配方很好的解决了这一难题;使铸件内在质量得到大幅度的提升..三:提高成品率;特别是大幅度提高优良品率..采用传统的配方;由于表面和内在质量得不到可靠的控制;废品率比较高;采用新型配方;由于表面质量和内在质量得到大幅度的提高;成品率也相应的提高;特别是不需要修补和打磨优良品率大幅度提高..四:大幅度降低后处理的工作量..采用传统配方;由于表面质量差;后处理工作量相当大;在劳动力日趋紧缺的今天;工作环境很差的后处理招工越来越难;采用新型配方后;后处理的工作量大幅度降低;特别是厚大件;后处理的工作量可以降低80%以上..五:大幅度改善制壳车间的工作环境..传统配方;大多数面层和过渡层采用氯化铵硬化;硬化过程中会产生氨气;氨气严重污染环境的同时;还腐蚀设备..新型配方在制壳过程中没有氨气产生;很好的解决了这一问题..六:降低生产成本..实践表明;采用新型配方比传统配方在制壳成本上每吨铸件高出30——80元;但是;大幅度降低了后处理成本..七:大大提高了传统水玻璃型壳生产大件的能力..对于传统水玻璃型壳;越大的件;出问题越多;生产难度越大..采用新型配方;许多问题迎刃而解;大大提高了传统水玻璃型壳生产大件甚至超大件的能力..总之;新型配方相比传统配方而言;是革命性的进步..谁先使用;谁将引领潮流..本人还有一篇文章免硬化水玻璃精密铸造制壳面层、过渡层划时代的技术革新;在百度文库里同样可以下载;如需要的;请直接下载..如有对新工艺感兴趣的业内专家或者同行需要进一步了解新配方和新工艺的使用情况;请联系我们;谢谢联系方式:。
水玻璃铸造工艺守则

水玻璃铸造工艺守则文件编号:RMZZ/QG-JS-01版本: A修改状态:O受控状态:编制:吴光来日期:2004-3-1蜡料制备1.工艺要求:1.1 蜡液温度:70-90℃,严禁超过90℃。
1.2 稀蜡温度:65-80℃。
1.3 蜡膏保温缸水温:48-50℃。
1.4 蜡膏应搅拌均匀呈糊状,温度控制在45-48℃,其中不允许有颗粒状蜡料。
1.5 蜡料配方1.5.2 在生产过程中必须根据蜡模质量分析结果,适量增加或减少硬脂酸量,冬季的酸值取下限,夏季的酸值取上限。
2操作程序2.1 启动设备,检查运转是否正常,是否漏水、漏气、漏蜡,有问题应及时排除。
检查保温缸水温是否符合工艺要求。
2.2 按蜡料配比把石蜡、硬脂酸和回收蜡分别称好,加入化蜡槽内,加热至全熔状态,其温度不得超过90℃。
2.3 把蜡液送到蜡膏搅拌机盛蜡槽内。
2.4 将搅蜡缸内加入三分之二的蜡片,启动搅拌机进行搅蜡直至呈糊状蜡料为止。
3注意事项3.1 稀蜡需用100目筛过滤,去掉杂质后方能使用。
3.2 不允许有影响质量的空气和水分混入蜡膏中。
3.3 化蜡槽和盛蜡槽每月清理两次。
3.4 蜡膏保温缸、搅蜡缸属于压力容器,应定期检查有关紧固件及密封机构的使用情况,发现问题应及时处理,正常工作压力严禁超过0.50MPa。
4检查项目每班必须测量蜡液温度和保温水温度3-4次,控制在工艺要求范围内并做好原始记录。
蜡模制造1 工艺要求1.1 室温:16-28℃(最高不超过30℃)。
1.2 蜡膏压注温度:45~48℃,压力:0.3~0.5 MPa,保压时间:3~10秒。
1.3 压蜡冷却水温,14~24℃,冷却时间:20~100秒。
1.4蜡模冷却水温,14~24℃,冷却时间:10~60min。
1.5蜡模清洗液温度,20~28℃,清洗液中加入0.01% JFC。
1.6 脱模剂:ZF201.1.7蜡模表面光洁度,形状完整,轮廓清洗,尺寸合格,不允许有缩陷,凸包裂纹等缺陷。
熔模铸造表面和内部缺陷总结经验

熔模铸造表面和内部缺陷总结经验A.浇不到(欠铸):液体金属未充满型腔造成铸件缺肉B 冷隔: 铸件上有未完全融合的缝隙,其交接边缘圆滑原因分析:1.浇注温度和型壳退度低,流动性差2..金属液含气最大,氧化严重以致流动性下降3.铸件壁厚薄4.浇注系统大小和设置位置不合理,直浇道高度不够5.型壳焙烧不充分或型壳透气性差,在铸型中形成气袋6.浇注速度过慢或浇注时金属液断流7.浇注量不足防止办法:1.适当提高浇注温度和型壳温度2.采用正确的熔炼工艺,减少金属液的含气量和非金属杂质3.对于薄壁件应注意浇注系统设计,减少流动阻力和流程,增加直浇道高度4 .焙烧要充分,提高型壳透气性5.适当提高浇注速度,并避免浇注过程断流6 .保证必须的浇注量C 结疤(夹砂):铸件表面上有大小不等,形状不规则的疤片状突起物由于型壳内层局部分层剥离,浇注时金属液充填已剥离的型壳部位,致使铸件表面局部突起1.撒砂时浮砂太多或砂拉中粉尘、细砂多,在砂粒之间产生分层2.涂料粘度大,局部堆积,硬化不透,在涂料之间产生分层3.气温高或涂料与撤砂间隔时间长,撤砂时涂料表面已结成硬皮,涂料与砂粒之间产生分层4.第二层或加固层涂料粘度大、流动性差,涂料不能很好渗入前层细砂间隙,在后层涂料与前层砂粒之间产生分层5.型壳前层残留硬化剂过多,后层涂料不能很好渗入前层间隙。
在后层涂料和前层砂粒之间产生分层6.硬化温度大大高出工作室温度,硬化后骤冷收缩造成型壳局部开裂剥离7.易熔模与面层涂料的润湿性差,在型壳层和易熔模之间形成空隙8.型壳焙烧、浇注时膨胀收缩变化大造成内层开裂剥离9.涂料粘度小,料层过薄或撒砂不足,造成型壳硬化过度,开裂剥离10.面层和加固层耐火材料差异太大,膨胀收缩不一致,便面层分层剥离防止办法:1.撒砂砂粒不可过细且要尽里均匀,粉尘要少,湿度不宜过高,撒砂时要抖去浮砂2.严格控制涂料粘度,涂料要涂均匀,力求减少局部堆积,并应合理选择硬化工艺参数3.缩短涂料与撒砂的间隔时闻4.适当减小第二层或加固层涂料的粘度,采用低粘度的过渡层涂料5.干燥时间要控制适当。
精密铸造各工序操作规程及注意事项

精密铸造各⼯序操作规程及注意事项精密铸造各⼯序操作规程及注意事项压蜡⼯序⼯艺操作规程及注意事项⼀.⼯艺要求:室温:24±2℃,蜡缸温度:54±2℃射蜡嘴温度: 54±2℃压射压⼒:3.5-4.0mpa保压时间:视蜡模⼤⼩,壁厚⽽定(⼀般为6-8秒)冷却⽔温度:≤20℃⼆.操作程序:1.检查压蜡机油压,保温温度,操作按钮是否正常,按照技术规定调整压蜡机压射压⼒,射蜡嘴温度,保压时间,冷却时间等。
2.从保温箱中取出蜡缸,装在压蜡机上,挤出上部混有空⽓的蜡料。
3.将模具放在压蜡机⼯作台⾯上,调整射蜡嘴使之与模具注蜡⼝⾼度⼀致,检查模具所有芯⼦,活块位置是否正确,模具开合是否顺利。
4.打开模具,喷薄薄⼀层分型剂,合型,对准射蜡嘴。
5.双⼿按动⼯作按钮,压制蜡模。
6.抽出芯⼦,打开模具,⼩⼼取出蜡模,放在⼯作台⼀侧,合上模具开始压下⼀件,同时对该件粗略检查⽆缺陷后按要求放⼊冷却⽔中或放⼊存放盘中冷却,冷却时间为4⼩时,注意有以下缺陷的蜡模应报废:(1)因模料中卷⼊空⽓,蜡模局部有⿎起的;(2)蜡模任何部位有缺陷的;(3)蜡模有变形不能简单修复的;(4)尺⼨不符合规定的。
7.清除模具上残留的模料,注意只能⽤⽵⼑,不可⽤⾦属⼑⽚清除残留模料,防⽌模具型腔及分型⾯受损,⽤压缩空⽓⽓嘴吹净模具分型⾯。
芯⼦上的蜡屑等,视模具结构及使⽤情况每2-10件喷⼀次分型剂。
8.及时将蜡模从冷却⽔中轻轻取出,⽤压缩空⽓吹净蜡屑及⽔珠,并进⾏⾃检,将合。
放⼊存放盘中。
9.每班下班或模具使⽤完毕后,应⽤软布或棉棒清理模具,如发现模具有损伤或不正常,应⽴即报告领班,由领班处理。
并清扫压蜡机,⼯具及现场,做到清洁、整齐。
三.注意事项:1.压制蜡模时,⾸先必须进⾏检查,确认合格后,⽅可进⾏操作,压蜡模过程中不能轻易变动压制参数。
2.模具型腔不要喷过多的分型剂,并要均匀,必要时可⽤压缩空⽓⽓嘴辅助将分型剂吹均匀。
水玻璃铸造工艺
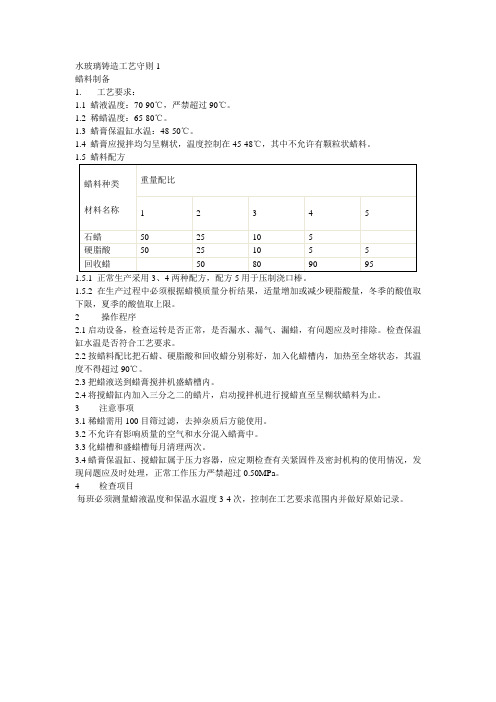
水玻璃铸造工艺守则1蜡料制备1. 工艺要求:1.1 蜡液温度:70-90℃,严禁超过90℃。
1.2 稀蜡温度:65-80℃。
1.3 蜡膏保温缸水温:48-50℃。
1.4 蜡膏应搅拌均匀呈糊状,温度控制在45-48℃,其中不允许有颗粒状蜡料。
1.5.1 正常生产采用3、4两种配方,配方5用于压制浇口棒。
1.5.2 在生产过程中必须根据蜡模质量分析结果,适量增加或减少硬脂酸量,冬季的酸值取下限,夏季的酸值取上限。
2 操作程序2.1 启动设备,检查运转是否正常,是否漏水、漏气、漏蜡,有问题应及时排除。
检查保温缸水温是否符合工艺要求。
2.2 按蜡料配比把石蜡、硬脂酸和回收蜡分别称好,加入化蜡槽内,加热至全熔状态,其温度不得超过90℃。
2.3 把蜡液送到蜡膏搅拌机盛蜡槽内。
2.4 将搅蜡缸内加入三分之二的蜡片,启动搅拌机进行搅蜡直至呈糊状蜡料为止。
3 注意事项3.1 稀蜡需用100目筛过滤,去掉杂质后方能使用。
3.2 不允许有影响质量的空气和水分混入蜡膏中。
3.3 化蜡槽和盛蜡槽每月清理两次。
3.4 蜡膏保温缸、搅蜡缸属于压力容器,应定期检查有关紧固件及密封机构的使用情况,发现问题应及时处理,正常工作压力严禁超过0.50MPa。
4 检查项目每班必须测量蜡液温度和保温水温度3-4次,控制在工艺要求范围内并做好原始记录。
蜡模制造1 工艺要求1.1 室温:16-28℃(最高不超过30℃)。
1.2 蜡膏压注温度:45~48℃,压力:0.3~0.5 MPa,保压时间:3~10秒。
1.3 压蜡冷却水温,14~24℃,冷却时间:20~100秒。
1.4蜡模冷却水温,14~24℃,冷却时间:10~60min。
1.5蜡模清洗液温度,20~28℃,清洗液中加入0.01% JFC。
1.6 脱模剂:ZF201.1.7蜡模表面光洁度,形状完整,轮廓清洗,尺寸合格,不允许有缩陷,凸包裂纹等缺陷。
2 操作程序2.1 手工制模2.1.1检查压型的分型面、型腔、脱模机构、定位销、紧固件应完整清洁。
精密铸造工艺规程

精密铸造工艺规程编制:审核:批准:日期:1 / 23文件目录2 / 23蜡型工艺规程一、工艺参数1.蜡料的配置(﹪)2.蜡料使用的温度3.压缩空气工作压力0.25—0.4 MPa4.搅料用碎蜡块加入量占蜡液的30%(碎蜡块30%蜡液70%)5.新蜡与硬脂酸的比例1∶16.作业环境温度0-30℃3 / 231.按配比称料、加温熔化。
2.在蜡液中加碎蜡块,搅拌成糊状(碎蜡块只许一次加成)。
3.装料调整好水温、压蜡。
4.冷凝、折模、蜡模水冷。
5.清理型腔、涂分型剂。
6.合型锁紧、重复压蜡。
7.修刮飞边、毛刺、修补缺陷。
8.用洗涤剂洗涤油迹,并用清水清洗一遍。
9.擦干水迹,分类入库。
4 / 23浇口棒蜡模工艺规程1.清擦模具,涂分型剂。
2.自由浇注蜡液。
3.将木棒擦入半凝固蜡液中,木棒擦入深度距离底部不能少于5-10㎜。
4.冷却取出,清擦合模。
5.修刮飞边毛刺,修补少量缺陷的蜡模。
5 / 23蜡模组焊工艺规程一、工艺参数二、操作规程1.将合格的蜡模依次焊上。
2.修刮蜡豆,插入车上。
3.组焊后应吹净蜡屑。
6 / 23制壳工艺规程一、配涂料用水玻璃的技术要求二、涂料配比7 / 23四、制壳工艺规范参数(比重氯化镁1.24-1.28,PH值5.5-5.6)五、操作规程1.按照工艺参数,配制好各种生产用料;2.每班检查涂料粘度、氯化镁浓度、氯化铵浓度;3.涂挂表面层涂料撒砂硬化干燥2遍;4.涂挂过度层涂料撒砂硬化干燥1遍;5.涂挂加强层涂料撒砂硬化干燥4-9遍;6.其余各层可直接硬化;7.铸件重量大于20kg,加强层不少于7.5层;8 / 239.若需铁丝加固,需在第3层硬化后,采用18#铁丝;10.铸件重量小于0.05kg,表面层2遍,加强层3遍;11.粘度计采用容量100ml,出口径φ6mm,蒸馏水标准4±0.5秒。
脱蜡工艺规程一、工艺参数1、脱蜡水氯化铵浓度4-8%。
2、水温大于95摄氏度。
3、热水脱蜡时间小于1小时,随着铸件重量的增加,可适当延长时间。
精密铸造4种制壳工艺特点分析及改进方向探讨
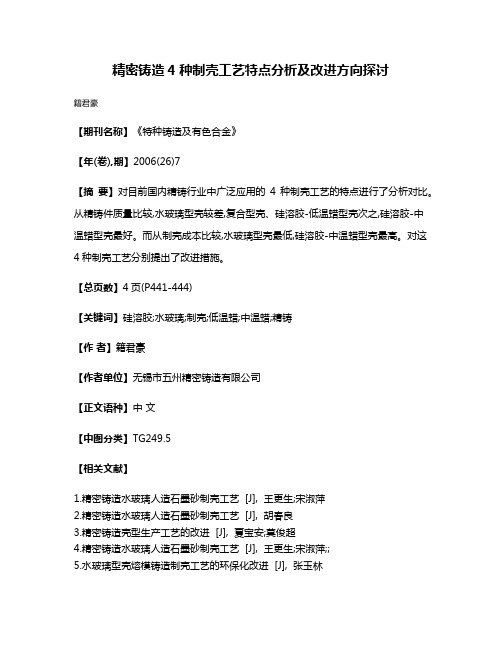
精密铸造4种制壳工艺特点分析及改进方向探讨
籍君豪
【期刊名称】《特种铸造及有色合金》
【年(卷),期】2006(26)7
【摘要】对目前国内精铸行业中广泛应用的4种制壳工艺的特点进行了分析对比。
从精铸件质量比较,水玻璃型壳较差,复合型壳、硅溶胶-低温蜡型壳次之,硅溶胶-中温蜡型壳最好。
而从制壳成本比较,水玻璃型壳最低,硅溶胶-中温蜡型壳最高。
对这4种制壳工艺分别提出了改进措施。
【总页数】4页(P441-444)
【关键词】硅溶胶;水玻璃;制壳;低温蜡;中温蜡;精铸
【作者】籍君豪
【作者单位】无锡市五州精密铸造有限公司
【正文语种】中文
【中图分类】TG249.5
【相关文献】
1.精密铸造水玻璃人造石墨砂制壳工艺 [J], 王更生;宋淑萍
2.精密铸造水玻璃人造石墨砂制壳工艺 [J], 胡春良
3.精密铸造壳型生产工艺的改进 [J], 夏宝安;莫俊超
4.精密铸造水玻璃人造石墨砂制壳工艺 [J], 王更生;宋淑萍;;
5.水玻璃型壳熔模铸造制壳工艺的环保化改进 [J], 张玉林
因版权原因,仅展示原文概要,查看原文内容请购买。
面层制壳工艺研究

涂料干燥工艺:自干1.5~2h;风干1.5~2h;氨干0.5 h,氨气流量:表面层10~15 L/min; 加固层10~20 L/min。
采用中国标准杯体积测定粘度。
再将电熔刚玉的主要成分及杂质与锆英砂作一个比较,见表2:
电熔刚玉 Al2O3≥98.5 Fe2O3≤0.10 1级锆砂 ZrO2≥65 Fe2O3≤0.30 2级锆砂 ZrO2≥63 Fe2O3≤0.70 3级锆砂 ZrO2≥60 Fe2O3≤1.00 表2 电熔刚玉与锆英砂成分比较表
2.1 锆英粉-熔融石英粉混合浆-撒锆英砂
面层配浆工艺如下:
锆英粉:熔融石英粉 = 85%:15%
粉液比: 1:3.2
粘度值(詹氏4#):42~45s
润湿剂:10kg面层硅溶胶加30ml
消泡剂:10kg面层硅溶胶加22ml
面层撒砂:100~120目锆英砂
面层干燥时间:6~7h
环境条件:温度22~25℃;湿度22~25%
该工艺适用于生产汽车零件和精密机械零件,面层制壳成本比全锆英粉降低约25%左右。
图3A左 锆英粉+熔融石英粉混合浆,撒锆英砂
Fig.3 Left Zircon-powder + Melting Quartz Powder Admixture pulp,Caesar Zircon-Sand
1.2莫来砂做面层撒砂材料
锆英石与高岭石这两种耐火材料有着良好的兼容性和复合性,所以,面层砂采用以莫来砂替代锆英砂。
面层配浆工艺如下:
粉液比(325目锆英粉): 1:3.3~3.4
粘度值(詹氏4#):42~45s
润湿剂:10kg面层硅溶胶加28ml
水玻璃精铸工艺流程

水玻璃精铸工艺流程下载温馨提示:该文档是我店铺精心编制而成,希望大家下载以后,能够帮助大家解决实际的问题。
文档下载后可定制随意修改,请根据实际需要进行相应的调整和使用,谢谢!并且,本店铺为大家提供各种各样类型的实用资料,如教育随笔、日记赏析、句子摘抄、古诗大全、经典美文、话题作文、工作总结、词语解析、文案摘录、其他资料等等,如想了解不同资料格式和写法,敬请关注!Download tips: This document is carefully compiled by theeditor. I hope that after you download them,they can help yousolve practical problems. The document can be customized andmodified after downloading,please adjust and use it according toactual needs, thank you!In addition, our shop provides you with various types ofpractical materials,such as educational essays, diaryappreciation,sentence excerpts,ancient poems,classic articles,topic composition,work summary,word parsing,copy excerpts,other materials and so on,want to know different data formats andwriting methods,please pay attention!水玻璃精铸工艺流程一、蜡模制作阶段。
蜡模制作是水玻璃精铸的起始环节,对后续的工艺有着重要影响。
水玻璃铸造工艺全过程

水玻璃铸造工艺守则文件编号:RMZZ/QG-JS-01版本:A修改状态:O受控状态:蜡料制备1. 工艺要求:1.1 蜡液温度:70-90℃,严禁超过90℃。
1.2 稀蜡温度:65-80℃。
1.3 蜡膏保温缸水温:48-50℃。
1.4 蜡膏应搅拌均匀呈糊状,温度控制在45-48℃,其中不允许有颗粒状蜡料。
1.5 蜡料配方1.5.2 在生产过程中必须根据蜡模质量分析结果,适量增加或减少硬脂酸量,冬季的酸值取下限,夏季的酸值取上限。
2 操作程序2.1 启动设备,检查运转是否正常,是否漏水、漏气、漏蜡,有问题应及时排除。
检查保温缸水温是否符合工艺要求。
2.2 按蜡料配比把石蜡、硬脂酸和回收蜡分别称好,加入化蜡槽内,加热至全熔状态,其温度不得超过90℃。
2.3 把蜡液送到制膏机内。
2.4启动制膏机进行打蜡制膏直至呈糊状蜡料为止。
3 注意事项3.1 稀蜡需用100目筛过滤,去掉杂质后方能使用。
3.2 不允许有影响质量的空气和水分混入蜡膏中。
3.3 化蜡槽和盛蜡槽每月清理两次。
3.4 蜡膏保温缸、搅蜡缸属于压力容器,应定期检查有关紧固件及密封机构的使用情况,发现问题应及时处理,正常工作压力严禁超过0.50MPa。
4 检查项目每班必须测量蜡液温度和保温水温度3-4次,控制在工艺要求范围内并做好原始记录。
蜡模制造1 工艺要求1.1 室温:16-28℃(最高不超过30℃)。
1.2 蜡膏压注温度:45~48℃,压力:0.3~0.5 MPa,保压时间:3~10秒。
1.3 压蜡冷却水温,14~24℃,冷却时间:20~100秒。
1.4蜡模冷却水温,14~24℃,冷却时间:10~60min。
1.5蜡模清洗液温度,20~28℃,清洗液中加入0.01% JFC。
1.6 脱模剂:ZF201.1.7蜡模表面光洁度,形状完整,轮廓清洗,尺寸合格,不允许有缩陷,凸包裂纹等缺陷。
2 操作程序2.1 手工制模2.1.1检查压型的分型面、型腔、脱模机构、定位销、紧固件应完整清洁。
(整理)熔模铸造水玻璃工艺
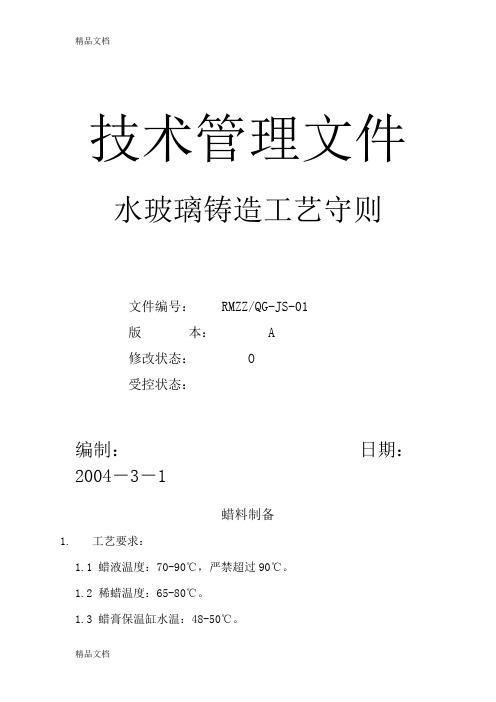
技术管理文件水玻璃铸造工艺守则文件编号:RMZZ/QG-JS-01版本:A修改状态:O受控状态:编制:日期:2004-3-1蜡料制备1.工艺要求:1.1 蜡液温度:70-90℃,严禁超过90℃。
1.2 稀蜡温度:65-80℃。
1.3 蜡膏保温缸水温:48-50℃。
1.4 蜡膏应搅拌均匀呈糊状,温度控制在45-48℃,其中不允许有颗粒状蜡料。
1.5 蜡料配方1.5.1 正常生产采用3、4两种配方,配方5用于压制浇口棒。
1.5.2 在生产过程中必须根据蜡模质量分析结果,适量增加或减少硬脂酸量,冬季的酸值取下限,夏季的酸值取上限。
2操作程序2.1 启动设备,检查运转是否正常,是否漏水、漏气、漏蜡,有问题应及时排除。
检查保温缸水温是否符合工艺要求。
2.2 按蜡料配比把石蜡、硬脂酸和回收蜡分别称好,加入化蜡槽内,加热至全熔状态,其温度不得超过90℃。
2.3 把蜡液送到蜡膏搅拌机盛蜡槽内。
2.4 将搅蜡缸内加入三分之二的蜡片,启动搅拌机进行搅蜡直至呈糊状蜡料为止。
3注意事项3.1 稀蜡需用100目筛过滤,去掉杂质后方能使用。
3.2 不允许有影响质量的空气和水分混入蜡膏中。
3.3 化蜡槽和盛蜡槽每月清理两次。
3.4 蜡膏保温缸、搅蜡缸属于压力容器,应定期检查有关紧固件及密封机构的使用情况,发现问题应及时处理,正常工作压力严禁超过0.50MPa。
4检查项目每班必须测量蜡液温度和保温水温度3-4次,控制在工艺要求范围内并做好原始记录。
蜡模制造1 工艺要求1.1 室温:16-28℃(最高不超过30℃)。
1.2 蜡膏压注温度:45~48℃,压力:0.3~0.5 MPa,保压时间:3~10秒。
1.3 压蜡冷却水温,14~24℃,冷却时间:20~100秒。
1.4蜡模冷却水温,14~24℃,冷却时间:10~60min。
1.5蜡模清洗液温度,20~28℃,清洗液中加入0.01% JFC。
1.6 脱模剂:ZF201.1.7蜡模表面光洁度,形状完整,轮廓清洗,尺寸合格,不允许有缩陷,凸包裂纹等缺陷。
水玻璃熔模精铸新型环保制壳技术改造项目可行性研究报告
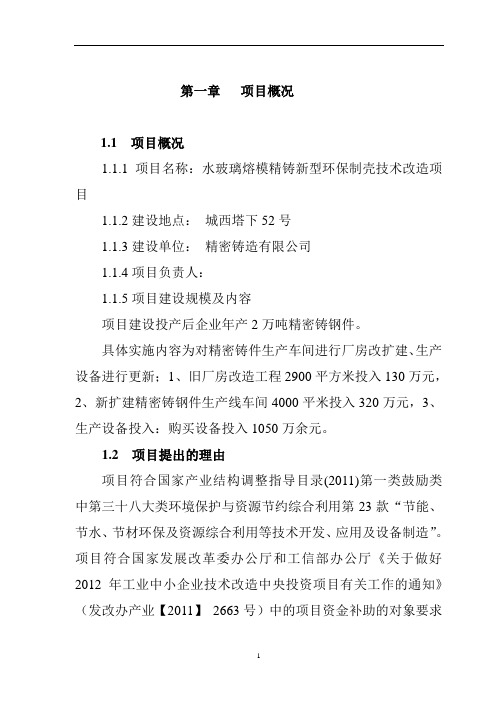
第一章项目概况1.1 项目概况1.1.1项目名称:水玻璃熔模精铸新型环保制壳技术改造项目1.1.2建设地点:城西塔下52号1.1.3建设单位:精密铸造有限公司1.1.4项目负责人:1.1.5项目建设规模及内容项目建设投产后企业年产2万吨精密铸钢件。
具体实施内容为对精密铸件生产车间进行厂房改扩建、生产设备进行更新;1、旧厂房改造工程2900平方米投入130万元,2、新扩建精密铸钢件生产线车间4000平米投入320万元,3、生产设备投入:购买设备投入1050万余元。
1.2 项目提出的理由项目符合国家产业结构调整指导目录(2011)第一类鼓励类中第三十八大类环境保护与资源节约综合利用第23款“节能、节水、节材环保及资源综合利用等技术开发、应用及设备制造”。
项目符合国家发展改革委办公厅和工信部办公厅《关于做好2012年工业中小企业技术改造中央投资项目有关工作的通知》(发改办产业【2011】2663号)中的项目资金补助的对象要求1.3 项目建设规模及技术工艺特点项目完成后可使公司生产能力达到年产2万吨精密铸钢件。
工艺技术:采用水玻璃熔模精铸新型环保制壳技术水玻璃熔模精铸新型环保制壳技术是通过对水玻璃的活性处理、型壳材料性能的优选和独特工艺配方,突破了目前国内外水玻璃熔模精铸所采用的传统制壳工艺技术,创新地解决了行业上有关环保弊端的共性技术难题; 其生产工艺技术路线主要包括;蜡模、制壳、脱蜡、模壳焙烧、溶炼浇注、退火及清理等,主体是水玻璃浆料与新型硬化剂接触后,在涂层界面上迅速产生界面硬化形成硅胶凝膜,随后,硬化剂通过涂层胶膜的间隙和微裂纹由表及里的渗透扩散,胶凝层不断增厚,顺序硬化胶膜中二氧化硅,使凝胶化转变充分,硬化层逐渐顺序形成,固结成精密模壳。
生产线采用新型环保节能先进铸造设备,淘汰了传统烧煤、烧油焙烧炉、传统脱蜡机、传统退火炉等燃煤对环境污染的设备,新型环保节能先进铸造设备:如新型射蜡机、搅拌机、喷沙机、淋沙机、调温机、抛光机、新型电加热蒸汽脱蜡釜、硅碳棒电炉(焙烧炉)、电加热箱式台车(退火)炉、节能快速感应电炉等等设备。
硅溶胶、水玻璃复合工艺规程陈

硅溶胶、水玻璃复合工艺规程陈编制说明本工艺规程共分三部分:第一部分:硅溶胶、水玻璃复合工艺熔模铸特点第二部分:硅溶胶、水玻璃复合工艺熔模铸工艺流程第三部分:硅溶胶、水玻璃复合工艺熔模铸工艺规程其中第三部分又分为一下四项内容:1、材料2、工艺装备3、工艺参数4、工艺要求及操作要点本工艺规程是硅溶胶、水玻璃复合工艺熔模铸通用工艺规程,但其中某些主要参数是结合本公司实际生产而确定。
本工艺规程中的不尽之处,请参阅《产品标准工艺卡》及《工艺技术命令表》硅溶胶、水玻璃复合精铸工艺规程一、特点1、硅溶胶、水玻璃型壳采用面层和过度层恒温恒湿制壳,被层采用化学硬化法,能使型壳迅速硬化而建立湿强度,故工艺周期短、工时消耗少、生产效率高。
2、水波离价廉易购,货源充足,其价格仅相当于其他两种粘结剂的1/20~1/30。
3、水玻璃性能稳定,耐火材料对涂料的稳定性影响小,制壳过程中对生产现场的温湿度的要求也不象其他粘结剂那样严格。
4、水玻璃型壳熔模铸型选的主要问题是铸件尺寸精度较低,表面质量较差,难以满足外观质量高的要求,用硅溶胶工艺做面层和过度层可以很好的互补各自的优缺点,即减低成本又能提高外观质量。
5、硅溶胶、水玻璃复合工艺熔模铸选适用于精铸不锈钢、碳钢、合金钢、球铁、铝合金等精铸件。
二、 1、碳钢工艺流程2、不锈钢工艺流程:蜡处理射蜡修蜡组树清洗焙烧脱蜡制壳浇注振壳切割磨浇口(固熔化处理)抛光钝化焊补修整咬酸喷砂抛丸三、工艺规程(一)蜡处理1、材料1)材料种类:石蜡、低分子聚乙烯蜡(可选用成品模料)2)材料性能:2、工艺装备:脱蜡槽、水洗槽、化蜡桶、搅蜡机、100目过滤网3、工艺参数:1)热水温度:100℃2)加热温度:100℃3)沸腾时间:1h4)搅拌时间:直至模料的白点消失5)关掉蒸汽后静置沉淀时间:1.5~2h6)在蜡桶中静置时间:≥4h7)静置后冷却时间:2h8)水的去除:待蜡冷却后从化蜡桶底阀排出。
4、工艺要求及操作要点1)配制新模料时:①将新蜡料敲成小块放入化蜡桶中。
精密铸造制壳工艺特点及改进方向探讨
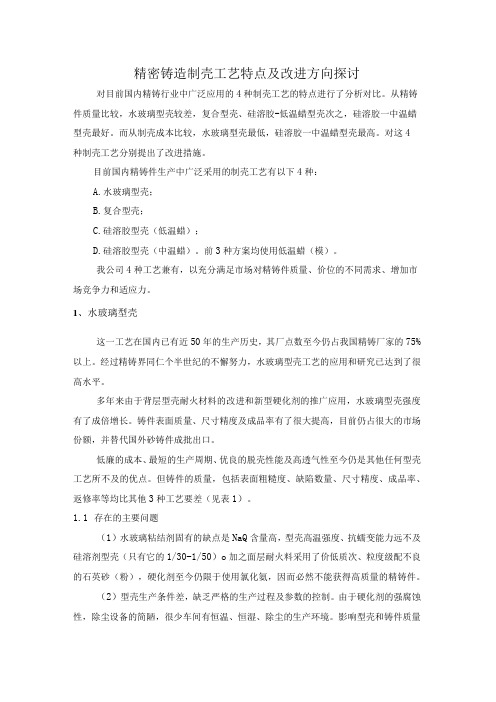
精密铸造制壳工艺特点及改进方向探讨对目前国内精铸行业中广泛应用的4种制壳工艺的特点进行了分析对比。
从精铸件质量比较,水玻璃型壳较差,复合型壳、硅溶胶-低温蜡型壳次之,硅溶胶一中温蜡型壳最好。
而从制壳成本比较,水玻璃型壳最低,硅溶胶一中温蜡型壳最高。
对这4种制壳工艺分别提出了改进措施。
目前国内精铸件生产中广泛采用的制壳工艺有以下4种:A.水玻璃型壳;B.复合型壳;C.硅溶胶型壳(低温蜡);D.硅溶胶型壳(中温蜡)。
前3种方案均使用低温蜡(模)。
我公司4种工艺兼有,以充分满足市场对精铸件质量、价位的不同需求、增加市场竞争力和适应力。
1、水玻璃型壳这一工艺在国内已有近50年的生产历史,其厂点数至今仍占我国精铸厂家的75%以上。
经过精铸界同仁个半世纪的不懈努力,水玻璃型壳工艺的应用和研究已达到了很高水平。
多年来由于背层型壳耐火材料的改进和新型硬化剂的推广应用,水玻璃型壳强度有了成倍增长。
铸件表面质量、尺寸精度及成品率有了很大提高,目前仍占很大的市场份额,并替代国外砂铸件成批出口。
低廉的成本、最短的生产周期、优良的脱壳性能及高透气性至今仍是其他任何型壳工艺所不及的优点。
但铸件的质量,包括表面粗糙度、缺陷数量、尺寸精度、成品率、返修率等均比其他3种工艺要差(见表1)。
1.1存在的主要问题(1)水玻璃粘结剂固有的缺点是NaQ含量高,型壳高温强度、抗蠕变能力远不及硅溶剂型壳(只有它的1/30-1/50)o加之面层耐火料采用了价低质次、粒度级配不良的石英砂(粉),硬化剂至今仍限于使用氯化氨,因而必然不能获得高质量的精铸件。
(2)型壳生产条件差,缺乏严格的生产过程及参数的控制。
由于硬化剂的强腐蚀性,除尘设备的简陋,很少车间有恒温、恒湿、除尘的生产环境。
影响型壳和铸件质量的涂料配制、硬化、风干、脱蜡等工序,极少按行业规定的操作规范严格控制。
如定期检测涂料粘度、涂片重、硬化剂浓度、PH值等。
型壳风干处的温度、湿度、风速等更是不加控制,故常在高、低温或梅雨季节发生批量报废的质量事故。
精密铸造工艺规程

4.过滤网为200目
二、操作程序:
1.设备准备:
a脱蜡用蒸汽发生器压力应达1。0Mpa,最低不得小于0。7Mpa。
b对脱蜡釜进行预热1~2次。
C准备好过滤网,确保干净,整洁,无破损。
2.型壳准备:
A将封浆后已达到干燥时间的陶壳从挂架上取下,执下挂钩,盖板并将浇口杯处多余砂粒清理干净,放于脱蜡小车上,准备脱蜡。
2.蜡件凹陷处的修复:
2.1蜡件的凹陷应用专用修补蜡进行修补,修补后表面要平整。
3.蜡件气泡的修复:
3.1对蜡件上的气泡必须全部挑破,用专用修补蜡进行修补,修补后蜡件需平整无缺。
4.蜡件油纹的修复:
4.1蜡件油纹的修复,需用吸有三氯乙烯或三乙氯烷的棉花团,轻柔的对油纹处进行擦拭,注意不要伤到蜡件本身。
6.涂料基本搅拌均匀后,用4#詹氏杯测其粘度,若粘度过高,则加硅溶胶调整,过低则加耐火粉料调整。
工艺规程
LOQS-C2-S205
涂料配制
第2版共2页第2页
7.面层、二层锆浆,每次新配制后,务必要作好记录,严格按规定日期给予更换,即面层20-25天,二层25-30天。
8.在操作过程中,造成成粘度偏高,应加蒸馏水予以高速特别是真空沾浆机内泥浆更应如此。
4.打开模具,喷涂脱模剂,合模后将模具射蜡口对准射蜡嘴。
5.按动工作按钮,压制蜡模。
6.按拆装顺序,抽出抽芯,打开模具,用压缩空气,小心将蜡件取出,按要求入入冷却水或盘中冷却。
7.模件存在下列缺陷应予以报废。
A因模料卷入空气,使蜡件局部有鼓起的;
B蜡件某一部位有缺陷的;
C蜡件变形且不易修复者;
D尺寸不符合规定者;
8.涂挂二层前,首先将面层多余砂粒抖净,然后在硅溶胶原液中进行预湿2-5S,取出后滴4~7秒。
- 1、下载文档前请自行甄别文档内容的完整性,平台不提供额外的编辑、内容补充、找答案等附加服务。
- 2、"仅部分预览"的文档,不可在线预览部分如存在完整性等问题,可反馈申请退款(可完整预览的文档不适用该条件!)。
- 3、如文档侵犯您的权益,请联系客服反馈,我们会尽快为您处理(人工客服工作时间:9:00-18:30)。
划时代的水玻璃精密铸造制壳工艺
面层、过渡层新型工艺和配方
各位精密铸造行业的专家、企业家们,衷心的请您耐心认真的了解本文介绍的内容,相信您一定可以感受到即将到来的呼之欲出的精铸工艺革命!
我国传统的水玻璃精密铸造工艺,面层、过渡层以水玻璃为粘结剂,辅以石英粉,适当添加消泡剂、渗透剂配浆以后,将蜡模模组进行蘸浆、洒砂、风干,然后用氯化铵、或者氯化铝、氯化铝氯化镁混合作为硬化剂,浸泡,待水玻璃和氯化铵反应以后,起到硬化的作用,硬化以后仍需等待模组干燥,然后再进入到下一层的操作。
多年来,我国一直用氯化铵作水玻璃型壳的硬化剂。
以后又逐步发展为用氯化铝:氯化镁作硬化剂。
无论用何种硬化剂,都免不了需要硬化,都有其不可克服的缺点。
氯化铵虽能在较短时间内硬化型壳,但焙烧后型壳强度差,作高强度型壳的硬化,显然不行,加之硬化时有氨气逸出,散发出刺鼻的气味,故工作环境条件差,导致招工难,留人难。
用氯化铝,还是氯化铝和氯化镁混合溶剂硬化,又有铸件表面质量差,清砂困难等缺点。
为客服上述传统工艺的各种缺陷,我公司技术人员经过多年的生产实践和摸索,经历了无数次的试验失败和不断尝试,研究出一种新型工艺和配方(该工艺和配方已经进入了国家实用型专利的申请流程),利用量身定做的配浆设备、配浆配方、脱蜡装置等重要工艺因素,让水玻璃精密铸造工艺取得飞跃的进步。
本文介绍的新工艺,主要是体现在型壳的面层、过渡层制作彻底告别硬化时代,使铸件的表面质量得到很大的提高,其光洁度甚至可以与硅溶胶精铸工艺生产出来的铸件媲美。
避免了传统的制壳工艺带来的表面分层、表面粘砂,橘子皮等缺陷。
同时,由于没有了氯化铵挥发出来的氨味,工作环境得到明显的改善,同时工艺参数要求、操作要求没有传统的硬化工艺那么复杂和严格,操作简单,一般工人均可上手,减少了由于熟练工流失,新工人上岗时的废品损失,稳定了工厂的正常生产效率。
成本方面,制壳材料成本比传统硬化工艺非但没有增加,而且明显减少了铸件后处理的焊补打磨抛丸处理,大大降低了生产成本,提高了良品率,缩短了生产周期,提升了利润空间的同时,大大提升了客户满意度。
总之,该新型工艺和配方,是水玻璃精密铸造技术革新中一个革命性的进步,对于我国的水玻璃精密铸造工艺有着划时代的意义,影响之深远超乎我们原有的想象。
主要体现在以下几方面:
第一,一旦使用了该新型工艺和配方,我国水玻璃精密铸件表面质量得到根本性的提高,推翻了以往水玻璃精密铸
件表面质量粗糙的传统印象;
第二,该新型工艺和配方的使用,不仅可以碳钢、球铁、灰铁、低合金钢等材质铸件表面质量的提升,对于各类不
锈钢铸件、耐热合金钢、耐磨合金钢、耐腐耐酸钢、
合金铸铁等的表面质量也同样的有很好的提升;
第三,对于很多以前为了获得更好的表面质量,只能选择成本更高的复合型硅溶胶工艺甚至全硅溶胶工艺的铸件,
现在终于可以重新选择水玻璃精密铸造工艺,达到低
成本、高质量效果,为具有中国特色的水玻璃精密铸
造工艺在国际市场提升了竞争力,获得更多的国际市
场认可,为我国的铸件出口创汇做出卓越的贡献;
第四,极大程度的减少了铸件后处理的补焊打磨修环节,一次性良品率提高了80%以上,为企业节省了每吨1000
元左右的成本,缩短了交货周期,提高了企业的获利
能力;
第五,取代了氯化铵硬化工艺,大大改善了铸造企业的操作环境,为环境保护做出了贡献,使得原本脏乱差的铸造
厂,也可以比较容易的获得ISO14000的环境体系的
认证,获得铸件的国际买家的考核和认同,增加了铸
造企业的外贸接单能力;
第六,新型工艺和配方的使用,解决了水玻璃精密铸造制壳操作参数难控制,型壳不稳定、对操作工要求高等难题,
在目前日趋严重的用工荒尴尬局面下,使企业在不增
加工资成本甚至降低工资成本,反而更容易招聘到制
壳操作工,减少了企业对于熟练操作工、铸造工艺工
程师的依赖,掌握了用工的主动权。
该工艺和配方更多的优点,在此不再一一赘述,等待各位铸造界的资深专家和优秀企业家去发掘。
我们希望各位业内有识之士,可以跟我们一起群策群力,为解决精铸行业的难题出谋划策。
巨大的商业机会永远垂青于能抢占先机的企业和企业家,如您想更进一步了解和探讨本工艺和配方,欢迎按以下联系方式联系我们。
由于时间等原因,希望各位暂时以邮件的方式和我们进行联系,必要的时候,我们再进行电话沟通,感谢大家的理解和支持!
联系方式:
赵先生,邮箱:zhaozx168@
王先生,邮箱:wwh78@
-。