铝合金精炼解读
铝合金精炼 实验报告
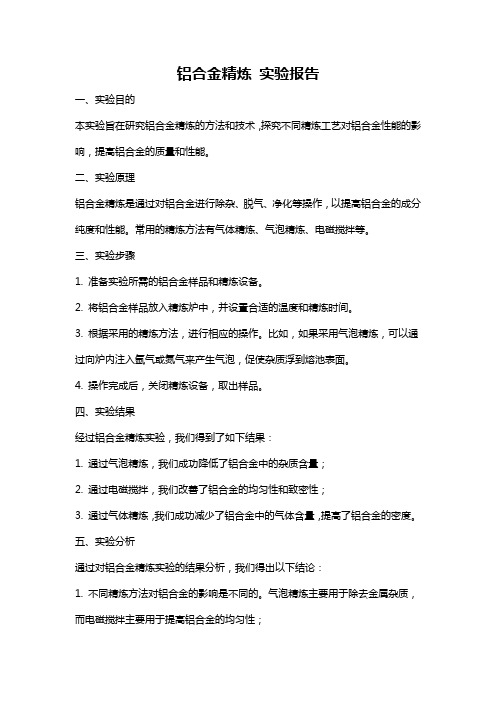
铝合金精炼实验报告一、实验目的本实验旨在研究铝合金精炼的方法和技术,探究不同精炼工艺对铝合金性能的影响,提高铝合金的质量和性能。
二、实验原理铝合金精炼是通过对铝合金进行除杂、脱气、净化等操作,以提高铝合金的成分纯度和性能。
常用的精炼方法有气体精炼、气泡精炼、电磁搅拌等。
三、实验步骤1. 准备实验所需的铝合金样品和精炼设备。
2. 将铝合金样品放入精炼炉中,并设置合适的温度和精炼时间。
3. 根据采用的精炼方法,进行相应的操作。
比如,如果采用气泡精炼,可以通过向炉内注入氩气或氮气来产生气泡,促使杂质浮到熔池表面。
4. 操作完成后,关闭精炼设备,取出样品。
四、实验结果经过铝合金精炼实验,我们得到了如下结果:1. 通过气泡精炼,我们成功降低了铝合金中的杂质含量;2. 通过电磁搅拌,我们改善了铝合金的均匀性和致密性;3. 通过气体精炼,我们成功减少了铝合金中的气体含量,提高了铝合金的密度。
五、实验分析通过对铝合金精炼实验的结果分析,我们得出以下结论:1. 不同精炼方法对铝合金的影响是不同的。
气泡精炼主要用于除去金属杂质,而电磁搅拌主要用于提高铝合金的均匀性;2. 气体精炼有助于减少铝合金中的气体含量,提高铝合金的密度和力学性能;3. 精炼温度和时间的选择也对精炼效果有一定影响,需要根据具体情况进行调整。
六、结论通过铝合金精炼实验,我们成功提高了铝合金的质量和性能,明确了不同精炼方法对铝合金的作用。
这对于铝合金行业的发展具有重要意义,可以为铝合金的生产提供科学依据。
同时,本实验也为进一步研究铝合金精炼技术提供了思路和方向。
七、参考文献1. 王某某. 铝合金精炼技术研究[D]. 上海交通大学, 2015.2. 张某某. 铝合金气体精炼原理及应用研究[J]. 合金, 2020, 7(11): 30-34.八、备注本实验报告仅为实验结果分析和研究结论的简要陈述,并未包含详细的实验步骤和数据。
实验二-铝合金的精炼变质处理
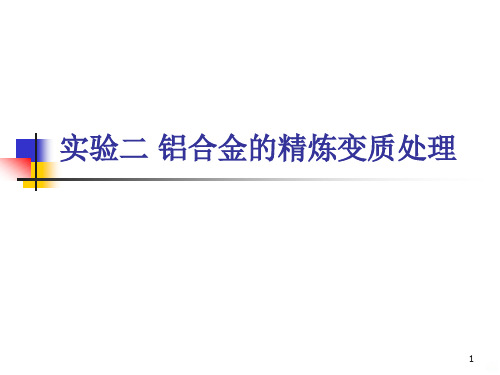
✓应尽量降低铝液表面上的氢分压,为此可采用真空处理。 ✓ 向铝液中吹入惰性气体,以在其内形成氢分压起始为零的气泡来降低含
氢量。
6
铝合金的组织
常温下, Al - Si 二元系仅形成α和β相。 通常把共晶中的β相称为共晶硅, 在
铸态下, 未经变质处理的共晶硅呈粗
大的片状。共晶和过共晶合金组织中 的β相称为初晶硅。铸态下未经变质处
用磷变质 处理能细 化初生硅
变质前初 生硅晶体 长成粗大 厚板片状
Al-Si过共晶合金(含22%Si)铸态组织(金属型)
12
初生硅的变质
变质剂分类
磷变质机制
一类是赤磷或含赤磷的混合变质剂; 另一类是含磷的中间合金(Cu-P)。
形成AlP作为初生硅结晶的异质核心,使初生硅细化。
13
亚共晶铝合金中初生α相的细化
15
四 注意事项
所有用的模具、工具必须烘干 所用的覆盖剂、精炼剂要烘干 千万勿用手直接接触熔炼工具、模具,
先试探,再操作。
16
五 实验报告
根据熔体净化处理的基本原理,讨论有 哪些熔体净化方法。
给出本组实验中观察到合金变质前后的 金相组织,试讨论Al-Sr中间合金变质AlSi合金的机理。
17
2024/1/5
18
氧化夹杂来源: 表面氧化膜、空气、水汽等被搅入铝液中。
5
铝合金的精炼原理
[H ] Ks PH2
气体溶解 度的
Ks A/T B
Sieverts 西华特定
律
式中[H]-溶于铝中氢的浓度;Ks-氢的溶解度系数;T-热力学温
度;A、B-常数,对铝合金而言,不同的合金类和不同的成分,
其数值各不相同。
概念 所谓变质处理是在熔融合金中加入少量的一 种或几种元素(或加化合物起作用而得),改变合 金的结晶组织,共晶体中的硅相由原来的粗大片状 变为细小纤维状,从而改善机械性能。
《汽车轮毂用A356铝合金的精炼及净化》范文
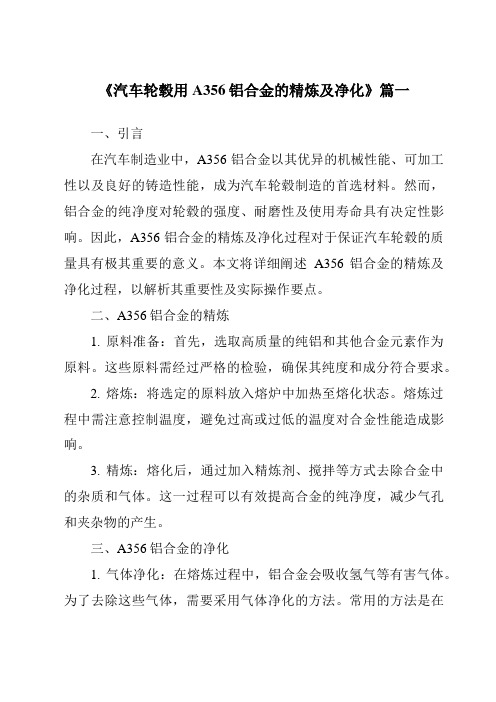
《汽车轮毂用A356铝合金的精炼及净化》篇一一、引言在汽车制造业中,A356铝合金以其优异的机械性能、可加工性以及良好的铸造性能,成为汽车轮毂制造的首选材料。
然而,铝合金的纯净度对轮毂的强度、耐磨性及使用寿命具有决定性影响。
因此,A356铝合金的精炼及净化过程对于保证汽车轮毂的质量具有极其重要的意义。
本文将详细阐述A356铝合金的精炼及净化过程,以解析其重要性及实际操作要点。
二、A356铝合金的精炼1. 原料准备:首先,选取高质量的纯铝和其他合金元素作为原料。
这些原料需经过严格的检验,确保其纯度和成分符合要求。
2. 熔炼:将选定的原料放入熔炉中加热至熔化状态。
熔炼过程中需注意控制温度,避免过高或过低的温度对合金性能造成影响。
3. 精炼:熔化后,通过加入精炼剂、搅拌等方式去除合金中的杂质和气体。
这一过程可以有效提高合金的纯净度,减少气孔和夹杂物的产生。
三、A356铝合金的净化1. 气体净化:在熔炼过程中,铝合金会吸收氢气等有害气体。
为了去除这些气体,需要采用气体净化的方法。
常用的方法是在熔炉中通入惰性气体(如氩气),通过置换熔融金属中的气体,将氢气等有害气体从金属中排出。
2. 机械净化:通过离心分离机等设备对熔融金属进行离心分离,进一步去除杂质和夹杂物。
离心分离可以有效分离密度较大的夹杂物和颗粒物,提高合金的纯净度。
四、精炼及净化过程中的注意事项1. 控制温度:在精炼及净化过程中,需严格控制温度。
过高的温度可能导致合金元素挥发,影响合金性能;过低的温度则可能导致精炼及净化效果不佳。
2. 添加适量精炼剂:精炼剂的添加量需根据实际情况进行调整。
过多或过少的精炼剂都会影响精炼及净化效果。
3. 定期检查设备:定期对熔炉、离心分离机等设备进行检查和维护,确保其正常运行和良好的工作状态。
五、结论A356铝合金的精炼及净化过程对于保证汽车轮毂的质量具有至关重要的作用。
通过精炼和净化过程,可以有效去除合金中的杂质和气体,提高合金的纯净度,从而保证汽车轮毂的强度、耐磨性及使用寿命。
《汽车轮毂用A356铝合金的精炼及净化》范文

《汽车轮毂用A356铝合金的精炼及净化》篇一一、引言随着汽车工业的飞速发展,汽车轮毂的制造材料及工艺成为行业关注的焦点。
A356铝合金因其优良的机械性能、铸造性能和抗腐蚀性能,被广泛应用于汽车轮毂的制造。
本文将详细解析A356铝合金的精炼及净化过程,以确保其达到汽车轮毂制造的高标准要求。
二、A356铝合金的基本特性A356铝合金是一种典型的压铸铝合金,具有良好的流动性和抗腐蚀性,能够满足汽车轮毂制造的严格要求。
然而,其成分中的杂质会对合金的性能产生影响,因此需要通过精炼和净化过程来提高其纯度和性能。
三、A356铝合金的精炼过程1. 原料准备:选择优质的A356铝合金原材料,进行预处理,去除表面杂质和氧化皮。
2. 熔炼:将预处理后的原材料放入熔炉中加热至熔化,这一过程需严格控制温度和时间,防止过烧和化学成分的变化。
3. 除气精炼:熔化后的铝液需通过除气机进行除气处理,以去除其中的氢气和其它气体杂质。
这一步骤对于提高合金的纯净度和机械性能至关重要。
4. 熔剂覆盖:在铝液表面覆盖一层熔剂,以防止空气和杂质的侵入,并进一步保护铝液的纯净度。
四、A356铝合金的净化过程1. 机械过滤:利用滤网等设备对铝液进行机械过滤,去除其中的固体杂质和悬浮颗粒。
2. 静置沉降:经过机械过滤后的铝液需静置一段时间,使微小杂质在重力的作用下沉降到底部。
3. 真空净化:采用真空技术对铝液进行进一步净化,通过降低压力使气体和杂质在铝液中上浮至表面,便于去除。
五、精炼及净化后的效果与质量控制经过精炼及净化后的A356铝合金,其纯度和性能得到显著提高,能够满足汽车轮毂制造的高标准要求。
为确保产品质量,需对精炼及净化后的铝合金进行严格的质量检测和控制,包括化学成分分析、机械性能测试等。
此外,还需对生产过程中的关键环节进行监控和记录,确保产品质量可追溯。
六、结论本文详细解析了汽车轮毂用A356铝合金的精炼及净化过程。
通过严格的精炼和净化措施,可以有效提高A356铝合金的纯度和性能,满足汽车轮毂制造的高标准要求。
铝合金的精炼 原理
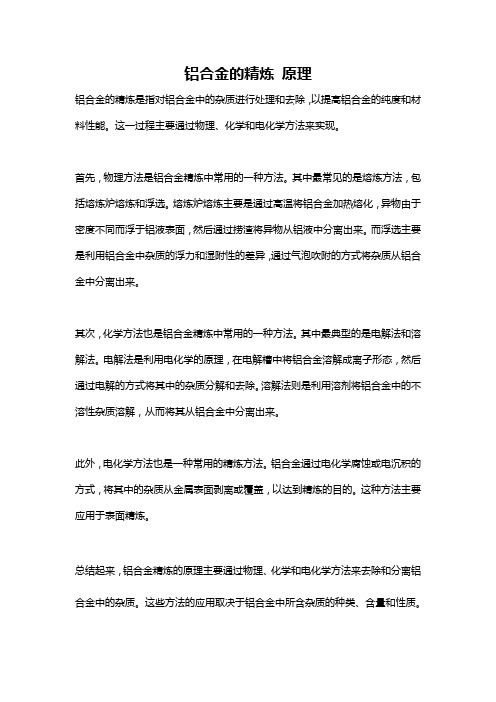
铝合金的精炼原理
铝合金的精炼是指对铝合金中的杂质进行处理和去除,以提高铝合金的纯度和材料性能。
这一过程主要通过物理、化学和电化学方法来实现。
首先,物理方法是铝合金精炼中常用的一种方法。
其中最常见的是熔炼方法,包括熔炼炉熔炼和浮选。
熔炼炉熔炼主要是通过高温将铝合金加热熔化,异物由于密度不同而浮于铝液表面,然后通过捞渣将异物从铝液中分离出来。
而浮选主要是利用铝合金中杂质的浮力和湿附性的差异,通过气泡吹附的方式将杂质从铝合金中分离出来。
其次,化学方法也是铝合金精炼中常用的一种方法。
其中最典型的是电解法和溶解法。
电解法是利用电化学的原理,在电解槽中将铝合金溶解成离子形态,然后通过电解的方式将其中的杂质分解和去除。
溶解法则是利用溶剂将铝合金中的不溶性杂质溶解,从而将其从铝合金中分离出来。
此外,电化学方法也是一种常用的精炼方法。
铝合金通过电化学腐蚀或电沉积的方式,将其中的杂质从金属表面剥离或覆盖,以达到精炼的目的。
这种方法主要应用于表面精炼。
总结起来,铝合金精炼的原理主要通过物理、化学和电化学方法来去除和分离铝合金中的杂质。
这些方法的应用取决于铝合金中所含杂质的种类、含量和性质。
通过精炼处理,可以提高铝合金的质量和性能,使其具备更好的机械性能、耐腐蚀性能和工艺性能,满足不同工业领域对于材料的要求。
铝合金铸造精炼剂
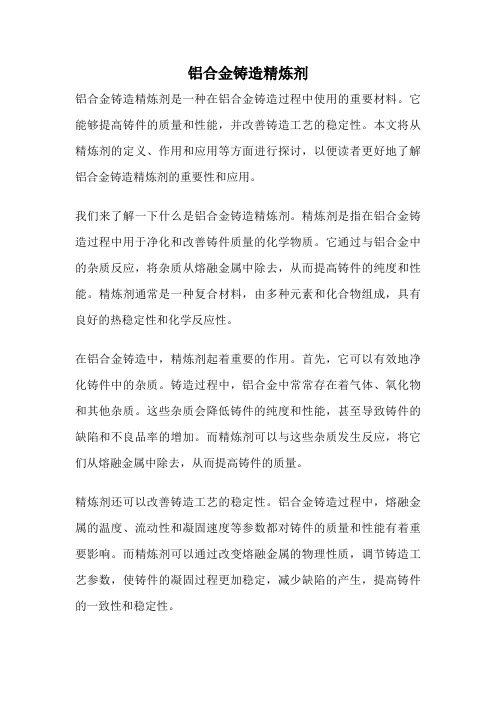
铝合金铸造精炼剂铝合金铸造精炼剂是一种在铝合金铸造过程中使用的重要材料。
它能够提高铸件的质量和性能,并改善铸造工艺的稳定性。
本文将从精炼剂的定义、作用和应用等方面进行探讨,以便读者更好地了解铝合金铸造精炼剂的重要性和应用。
我们来了解一下什么是铝合金铸造精炼剂。
精炼剂是指在铝合金铸造过程中用于净化和改善铸件质量的化学物质。
它通过与铝合金中的杂质反应,将杂质从熔融金属中除去,从而提高铸件的纯度和性能。
精炼剂通常是一种复合材料,由多种元素和化合物组成,具有良好的热稳定性和化学反应性。
在铝合金铸造中,精炼剂起着重要的作用。
首先,它可以有效地净化铸件中的杂质。
铸造过程中,铝合金中常常存在着气体、氧化物和其他杂质。
这些杂质会降低铸件的纯度和性能,甚至导致铸件的缺陷和不良品率的增加。
而精炼剂可以与这些杂质发生反应,将它们从熔融金属中除去,从而提高铸件的质量。
精炼剂还可以改善铸造工艺的稳定性。
铝合金铸造过程中,熔融金属的温度、流动性和凝固速度等参数都对铸件的质量和性能有着重要影响。
而精炼剂可以通过改变熔融金属的物理性质,调节铸造工艺参数,使铸件的凝固过程更加稳定,减少缺陷的产生,提高铸件的一致性和稳定性。
铝合金铸造精炼剂的应用范围非常广泛。
它适用于各种铝合金材料的铸造,包括铝硅合金、铝铜合金、铝镁合金等。
无论是压铸、重力铸造还是砂型铸造,精炼剂都能发挥重要作用。
它不仅可以提高铸件的质量和性能,还可以降低生产成本,提高生产效率。
铝合金铸造精炼剂在现代铝合金铸造工艺中起着不可替代的作用。
它能够净化铸件、改善铸造工艺的稳定性,提高铸件的质量和性能。
因此,铝合金铸造精炼剂的应用前景非常广阔,对于推动铝合金铸造工艺的发展具有重要意义。
希望通过本文的介绍,读者能够更加深入地了解铝合金铸造精炼剂,并在实际应用中发挥其优势。
铝合金精炼的原理

铝合金精炼的原理铝合金精炼是提高铝合金质量和性能的过程,通过调整铝合金的成分和组织结构,去除杂质和非金属夹杂物,以提升其力学性能、耐热性和耐腐蚀性。
铝合金精炼的原理主要包括氧化物的处理、过滤和除杂、合金组织调整等环节。
首先,铝合金精炼的过程中要处理氧化物。
铝在空气中容易与氧气发生反应生成氧化铝,而氧化铝的存在会影响铝合金的性能。
因此,要通过适当的处理方法将氧化物去除或转化。
常用的方法有气氛调整、熔渣法和焙烧法等。
其中,气氛调整是在熔炼过程中通过调整炉内气氛(如减压、加氢等)来去除氧化物,熔渣法是添加合适的熔渣来吸收和分离氧化物,焙烧法是将氧化物经过高温烘烤使其转化成可溶性的化合物,从而实现去除氧化物。
其次,铝合金精炼的过程中要进行过滤和除杂。
铝合金中常常含有各种杂质和非金属夹杂物,如气泡、夹杂金属、氧化物等。
这些杂质和非金属夹杂物会影响铝合金的力学性能和加工性能,因此需要通过过滤和除杂的方法将其去除。
过滤一般采用陶瓷过滤器,可以通过筛选的方式去除粗大的杂质颗粒;除杂一般采用捞渣(将熔融金属表面的熔渣捞掉)和改变金属的温度和分子结构等方法,以获得较纯净的铝合金。
最后,铝合金精炼的过程中要进行合金组织的调整。
合金组织的好坏直接影响着铝合金的性能。
常用的调整方法包括相成分的改变、相变和再结晶等。
相成分的改变可以通过添加合适的合金元素来改变合金的化学成分,进而改变合金的力学性能和耐腐蚀性能。
相变是指合金中两种或多种相的相互转变,常用的相变有固溶体相变和析出相变等,通过相变可以调整合金的硬度、强度和导热性等性能。
再结晶是指在加热过程中,金属材料的晶粒重新长大,消除变形应力,得到均匀细小的晶粒,从而提高材料的韧性和延展性。
总的来说,铝合金精炼的原理是通过处理氧化物、过滤和除杂、合金组织调整等环节来提高铝合金的质量和性能。
这些环节相互作用,综合运用可以获得高质量的铝合金。
铝合金精炼技术的不断改进和发展,有助于满足不同领域对高性能铝材料的需求,推动着铝合金产业的进步和发展。
第28次课-铸造铝合金熔炼原理讲解学习

铝铸件中气孔的形态及对铸件性能的影响
针孔:分布在整个铸件截面上,因铝液中的气体、夹杂含
量高、精炼效果差、铸件凝固速度低而引起。
点状针孔:呈圆点状轮廓清晰且互不相连,易和缩孔、缩松相区别。由 铸件凝固时析出的气泡所形成,多发生于结晶温度范围小、补缩能力良 好的铸件中。
为消除铝铸件中的气孔,应遵循“除杂为主,除气为辅”、 “除杂是除气的基础”的原则。
Al+O2=Al2O3(γ)---致密氧化膜 > 900 ℃ : Al2O3(γ)→ Al2O3(α)—疏松膜
γ-Al2O3 具有两面性:①和铝液接触的一面是致密的,可阻碍铝液的氧 化和吸气;②和炉气接触的那面却是粗糙、疏松的,其表面小孔吸附 着水汽和氢,搅动铝液时, γ-Al2O3将水汽和氢带入铝液,铝液氧化 生成夹杂物、吸入氢气。
氧化铝的形态、性能及对吸氢的影响(续)
η-Al2O3 、γ-Al2O3 在600-700 ℃范围内吸附水汽和氢的能力 最强,因此,铝液中的氢有两种形式:溶解氢和吸附在氧化 夹杂缝隙中的氢,前者约占90%以上,后者约占10%以下。 故铝液中的氧化夹杂越多,则含氢量也越高。
铝液中卷入Al2O3 夹杂,既增加了含氢量,吸附H2的Al2O3又 是温度下降时气泡形核的基底,容易在铸件中形成气孔。
网状针孔:呈密集相连成网状,伴有少数较大的孔洞。结晶温度范围宽 的合金,铸件缓慢凝固时析出的气体分布在晶界上及发达的枝晶间隙中, 此时结晶骨架已形成,补缩通道被堵,便在晶界上及枝晶间隙中形成网 状针孔。它会割裂合金基体,危害性比前者大。
混合型针孔:由点状针孔和网状针孔混杂在一起,常见于结构复杂、壁 厚不均匀的铸件中。
铝-水气反应(续)
在含硅、铜、锌等元素的铝合金,能较显著地阻缓铝 -水蒸气反应。含镁、钠等元素较多的铝合金,常使 铝-水气反应激烈进行。
铝液精炼的工作原理

铝液精炼的工作原理
铝液精炼是铝合金生产过程中一个重要的工艺环节,它的作用是通过化学反应和物理处理,去除铝液中的杂质和气体,提高铝合金的纯度和品质。
具体来说,铝液精炼的工作原理包括以下几个方面:
1.炉内气体处理:在铝液精炼的过程中,首先要处理炉内的气体,以保证其纯度和稳定性。
一般采用氩气或氮气进行熔炼,在炉内通入高纯度的气体,以保持炉内环境的稳定。
2.添加精炼剂:在铝液中添加一定的精炼剂,如氟化钠、氧化铝等,通过与铝液中的杂质和气体发生反应,使其沉淀到铝液底部,以达到净化和精炼的目的。
3.搅拌铝液:为了让精炼剂充分发挥作用,铝液需要进行充分的搅拌,以促进其混合和反应。
搅拌方式既可以是机械搅拌,也可以是气体搅拌。
4.过滤铝液:在进行铝液精炼时,铝液中的杂质和气体不可能完全沉淀,因此还需要通过过滤器等设备对铝液进行再次净化。
过滤器通常采用陶瓷过滤器或石英过滤器,以过滤残留的杂质和气体。
总的来说,铝液精炼的工作原理是通过添加精炼剂、搅拌铝液、过滤铝液等多个步骤,去除铝液中的杂质和气体,提高铝合金的纯度和品质。
这也是铝合金生产中不可或缺的一个环节。
- 1 -。
铝合金的精炼 原理
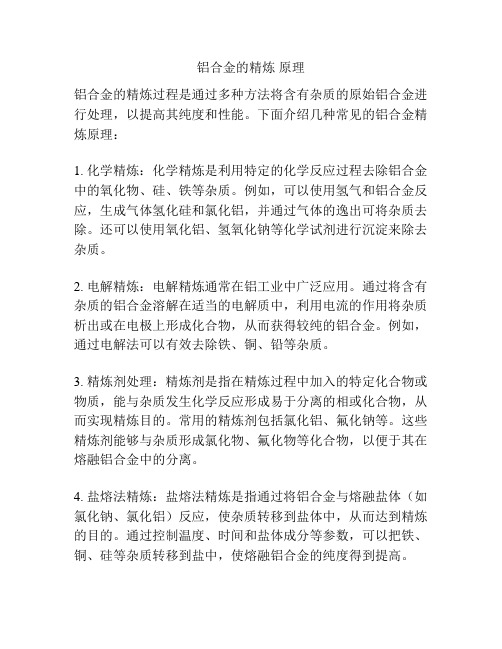
铝合金的精炼原理
铝合金的精炼过程是通过多种方法将含有杂质的原始铝合金进行处理,以提高其纯度和性能。
下面介绍几种常见的铝合金精炼原理:
1. 化学精炼:化学精炼是利用特定的化学反应过程去除铝合金中的氧化物、硅、铁等杂质。
例如,可以使用氢气和铝合金反应,生成气体氢化硅和氯化铝,并通过气体的逸出可将杂质去除。
还可以使用氧化铝、氢氧化钠等化学试剂进行沉淀来除去杂质。
2. 电解精炼:电解精炼通常在铝工业中广泛应用。
通过将含有杂质的铝合金溶解在适当的电解质中,利用电流的作用将杂质析出或在电极上形成化合物,从而获得较纯的铝合金。
例如,通过电解法可以有效去除铁、铜、铅等杂质。
3. 精炼剂处理:精炼剂是指在精炼过程中加入的特定化合物或物质,能与杂质发生化学反应形成易于分离的相或化合物,从而实现精炼目的。
常用的精炼剂包括氯化铝、氟化钠等。
这些精炼剂能够与杂质形成氯化物、氟化物等化合物,以便于其在熔融铝合金中的分离。
4. 盐熔法精炼:盐熔法精炼是指通过将铝合金与熔融盐体(如氯化钠、氯化铝)反应,使杂质转移到盐体中,从而达到精炼的目的。
通过控制温度、时间和盐体成分等参数,可以把铁、铜、硅等杂质转移到盐中,使熔融铝合金的纯度得到提高。
以上所述的铝合金精炼原理并不是完整的,不同的工艺和要求会采用不同的精炼方法。
最终的精炼效果也需要经过多次处理和优化才能达到理想的纯度和性能要求。
铝合金精炼解读

典型铝合金熔炼工艺∙2013-11-19 11:18:57∙来源:中铝网∙我要评论随着科学技术的发展,汽车、造船、航空、航天及其他制造业对铝合金铸件的品质要求也愈来愈高,除了保证化学成分、力学性能和尺寸精度外,不允许铸件有气孔、缩孔等缺陷。
而铝合金的熔炼则是铸件生产过程中的一个很重要的工序。
多年来的生产经验证明,熔炼工艺过程控制不严,铸件很容易产生针孔、氧化夹渣、缩松等缺陷,直接影响铸件质量。
因此,要想获得优质铝合金铸件,必须严格控制熔炼工艺。
一、熔炼前的准备1.严格控制炉料质量。
炉料质量是铸造生产的源头,直接影响到最终铸件的质量,成分不合格导致产品成批性报废。
因此,要高度重视。
必须做到:①严格控制炉料中新旧炉料的比例,回炉料所占炉料质量百分比应小于等于70%;②保证炉料干净,炉料需经吹砂后使用;③三等回炉料枷浇冒口匀使用前应经重熔精炼处理;④炉料应充分预热,去除水分、油污等杂质;⑤由于铭合金有铝硅类、铝铜类、铝镁类等合金,合金牌号较多,使用的元素也比较多,且互相影响,要求严格管理,不可混料;⑥配料、称量要准确,比如ZL104合金,考虑到除气、排渣及变质过程中的损耗,Mg元素应在实际配料时多加炉料质量的0.02%-0.03%,才能保证铸件的化学成分。
2.熔炼工具。
熔炼使用的址涓及熔炼工具须清理干净且涂上涂料,以保证使用时与铝合金有效隔离,减少合金液受到杂质污染,并且需要充分预热,址涓要烘烤至暗红色再加入炉料熔炼,以防水蒸气带入合金中使合金的气体增加、针孔度增加。
3.其他工作。
严格按已制订好的工艺规范作好覆盖剂、精炼剂及变质剂的准备工作。
二、熔炼操作熔炼步骤如下。
①装料。
在预热后的柑A中装入预制合金锭、优质回炉料,再加中fol合金,最后加合金元素。
②温度控制。
严格控制铝合金熔炼的温度,只有合适的温度才能获得高质量的合金液,避免过热。
若温度过高,会加大合金中各种元素的氧化烧损,引起合金中化学成分的变化。
铝合金的精炼目的及分类
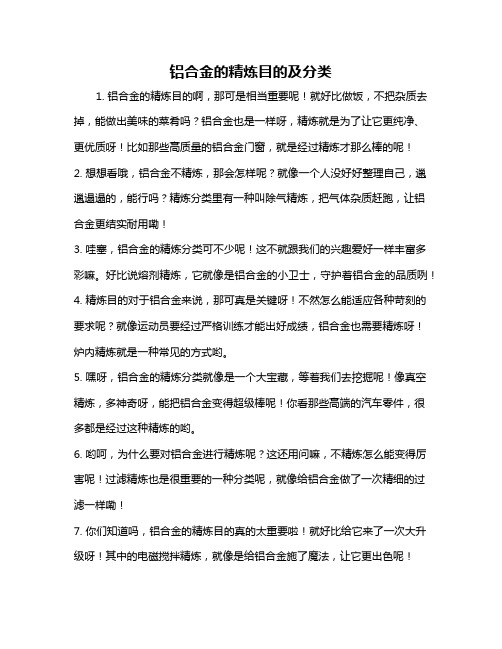
铝合金的精炼目的及分类
1. 铝合金的精炼目的啊,那可是相当重要呢!就好比做饭,不把杂质去掉,能做出美味的菜肴吗?铝合金也是一样呀,精炼就是为了让它更纯净、更优质呀!比如那些高质量的铝合金门窗,就是经过精炼才那么棒的呢!
2. 想想看哦,铝合金不精炼,那会怎样呢?就像一个人没好好整理自己,邋邋遢遢的,能行吗?精炼分类里有一种叫除气精炼,把气体杂质赶跑,让铝合金更结实耐用嘞!
3. 哇塞,铝合金的精炼分类可不少呢!这不就跟我们的兴趣爱好一样丰富多彩嘛。
好比说熔剂精炼,它就像是铝合金的小卫士,守护着铝合金的品质咧!
4. 精炼目的对于铝合金来说,那可真是关键呀!不然怎么能适应各种苛刻的要求呢?就像运动员要经过严格训练才能出好成绩,铝合金也需要精炼呀!炉内精炼就是一种常见的方式哟。
5. 嘿呀,铝合金的精炼分类就像是一个大宝藏,等着我们去挖掘呢!像真空精炼,多神奇呀,能把铝合金变得超级棒呢!你看那些高端的汽车零件,很多都是经过这种精炼的哟。
6. 哟呵,为什么要对铝合金进行精炼呢?这还用问嘛,不精炼怎么能变得厉害呢!过滤精炼也是很重要的一种分类呢,就像给铝合金做了一次精细的过滤一样嘞!
7. 你们知道吗,铝合金的精炼目的真的太重要啦!就好比给它来了一次大升级呀!其中的电磁搅拌精炼,就像是给铝合金施了魔法,让它更出色呢!
8. 哎呀呀,铝合金的精炼分类可真有意思!每一种都像是有特殊本领一样。
比如说吹气精炼,那可是让杂质无处可逃呀!想想那些精致的铝合金制品,这里面可都有精炼的功劳呢!
9. 总之呢,铝合金的精炼目的就是为了让它更好,精炼分类也是各有各的妙处。
我们在生活中用到的各种铝合金制品,都离不开这些精炼呢!。
铝合金的精炼
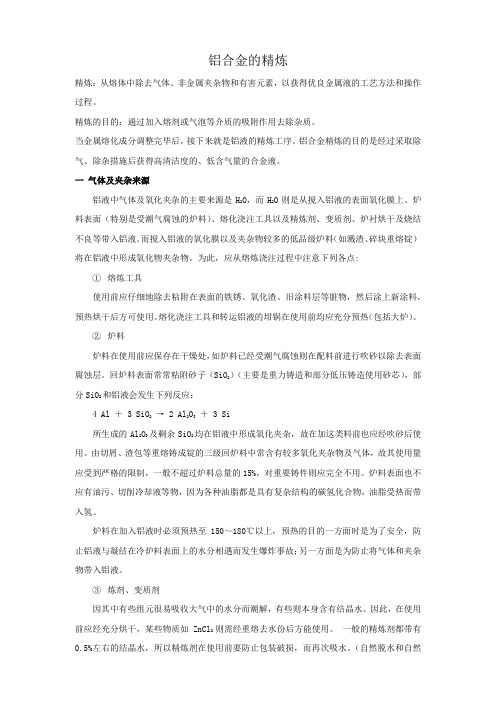
铝合金的精炼精炼:从熔体中除去气体、非金属夹杂物和有害元素,以获得优良金属液的工艺方法和操作过程。
精炼的目的:通过加入熔剂或气泡等介质的吸附作用去除杂质。
当金属熔化成分调整完毕后,接下来就是铝液的精炼工序。
铝合金精炼的目的是经过采取除气、除杂措施后获得高清洁度的、低含气量的合金液。
一气体及夹杂来源铝液中气体及氧化夹杂的主要来源是H2O,而H2O则是从搅入铝液的表面氧化膜上、炉料表面(特别是受潮气腐蚀的炉料)、熔化浇注工具以及精炼剂、变质剂、炉衬烘干及烧结不良等带入铝液。
而搅入铝液的氧化膜以及夹杂物较多的低品级炉料(如溅渣、碎块重熔锭)将在铝液中形成氧化物夹杂物。
为此,应从熔炼浇注过程中注意下列各点:①熔炼工具使用前应仔细地除去粘附在表面的铁锈、氧化渣、旧涂料层等脏物,然后涂上新涂料,预热烘干后方可使用。
熔化浇注工具和转运铝液的坩锅在使用前均应充分预热(包括大炉)。
②炉料炉料在使用前应保存在干燥处,如炉料已经受潮气腐蚀则在配料前进行吹砂以除去表面腐蚀层。
回炉料表面常常粘附砂子(SiO2)(主要是重力铸造和部分低压铸造使用砂芯),部分SiO2和铝液会发生下列反应:4 Al + 3 SiO2→ 2 Al2O3+ 3 Si所生成的Al2O3及剩余SiO2均在铝液中形成氧化夹杂,故在加这类料前也应经吹砂后使用。
由切屑、渣包等重熔铸成锭的三级回炉料中常含有较多氧化夹杂物及气体,故其使用量应受到严格的限制,一般不超过炉料总量的15%,对重要铸件则应完全不用。
炉料表面也不应有油污、切削冷却液等物,因为各种油脂都是具有复杂结构的碳氢化合物,油脂受热而带入氢。
炉料在加入铝液时必须预热至150~180℃以上,预热的目的一方面时是为了安全,防止铝液与凝结在冷炉料表面上的水分相遇而发生爆炸事故;另一方面是为防止将气体和夹杂物带入铝液。
③炼剂、变质剂因其中有些组元很易吸收大气中的水分而潮解,有些则本身含有结晶水。
因此,在使用前应经充分烘干,某些物质如ZnCl2则需经重熔去水份后方能使用。
铝合金的精炼方法
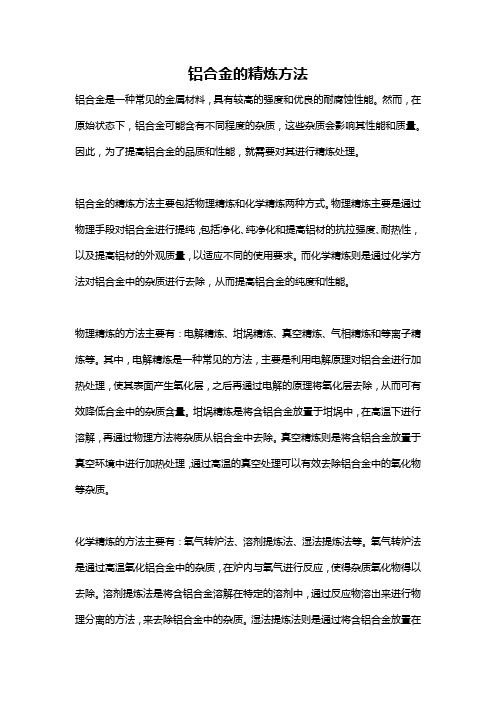
铝合金的精炼方法铝合金是一种常见的金属材料,具有较高的强度和优良的耐腐蚀性能。
然而,在原始状态下,铝合金可能含有不同程度的杂质,这些杂质会影响其性能和质量。
因此,为了提高铝合金的品质和性能,就需要对其进行精炼处理。
铝合金的精炼方法主要包括物理精炼和化学精炼两种方式。
物理精炼主要是通过物理手段对铝合金进行提纯,包括净化、纯净化和提高铝材的抗拉强度、耐热性,以及提高铝材的外观质量,以适应不同的使用要求。
而化学精炼则是通过化学方法对铝合金中的杂质进行去除,从而提高铝合金的纯度和性能。
物理精炼的方法主要有:电解精炼、坩埚精炼、真空精炼、气相精炼和等离子精炼等。
其中,电解精炼是一种常见的方法,主要是利用电解原理对铝合金进行加热处理,使其表面产生氧化层,之后再通过电解的原理将氧化层去除,从而可有效降低合金中的杂质含量。
坩埚精炼是将含铝合金放置于坩埚中,在高温下进行溶解,再通过物理方法将杂质从铝合金中去除。
真空精炼则是将含铝合金放置于真空环境中进行加热处理,通过高温的真空处理可以有效去除铝合金中的氧化物等杂质。
化学精炼的方法主要有:氧气转炉法、溶剂提炼法、湿法提炼法等。
氧气转炉法是通过高温氧化铝合金中的杂质,在炉内与氧气进行反应,使得杂质氧化物得以去除。
溶剂提炼法是将含铝合金溶解在特定的溶剂中,通过反应物溶出来进行物理分离的方法,来去除铝合金中的杂质。
湿法提炼法则是通过将含铝合金放置在盐酸和硫酸溶液中,使得杂质得以溶解和分离。
总的来说,铝合金的精炼方法是多种多样的,通过物理和化学手段的结合,可以对铝合金进行充分的提纯和清洁。
这不仅可以提高铝合金的纯度和性能,也可以扩大其应用范围和市场需求。
因此,在铝合金的生产过程中,精炼处理是非常重要的环节,能够有效提高铝合金的品质和市场竞争力。
铝合金冶炼工艺流程

铝合金冶炼工艺流程
铝合金冶炼是指通过冶炼铝矿石,将其转化为铝合金的过程。
以下是一种铝合金冶炼工艺流程的简要介绍:
1. 原料准备:首先需要选取适合冶炼的铝矿石,并进行矿石的粉碎和筛分,将其矿粉与矿石分开。
同时,还需要进行矿石中的杂质去除,例如氧化铁和硅酸盐等。
2. 熔炼和精炼:将经过准备的铝矿石加入到熔炼炉中,与炉子内预先加热的底渣反应,将铝矿石还原为金属铝。
在此过程中,控制熔炼温度、翻搅速度和反应时间,以确保还原反应可以高效进行。
3. 合金化:熔炼得到的金属铝中可能含有杂质元素,需要通过合金化来提高其力学性能和化学性能。
合金化可以通过添加合金元素的方式实现,常用的合金元素包括硅、镁、铜和锌等。
合金化程度的控制和合金元素的选取,决定了最终铝合金的性质。
4. 精炼:合金化后的铝合金还可能有一些不纯物质存在,需要进行进一步的精炼。
常用的精炼方法包括湿法和电解精炼两种。
湿法精炼主要通过将含有杂质的铝合金浸泡在盐溶液中,让不纯物质溶解,然后通过沉淀或过滤得到纯净的铝合金。
电解精炼则是通过电流的作用,将有害杂质转移到阴极上,使阴极上积聚的是纯净的铝合金。
5. 深加工:经过精炼后的铝合金可以用于制造各种产品。
通过
压铸、挤压、轧制、冷却、加工等工艺,可以将铝合金加工成所需的形状和尺寸。
以上是铝合金冶炼的基本工艺流程。
当然,不同的冶炼厂和产品需求可能会有所差异,具体的冶炼工艺流程还需要根据实际情况来进行调整和优化。
铝合金冶炼是一种复杂的过程,在操作过程中需要严格控制各个参数,以确保铝合金的质量,并达到预期的性能要求。
《汽车轮毂用A356铝合金的精炼及净化》范文
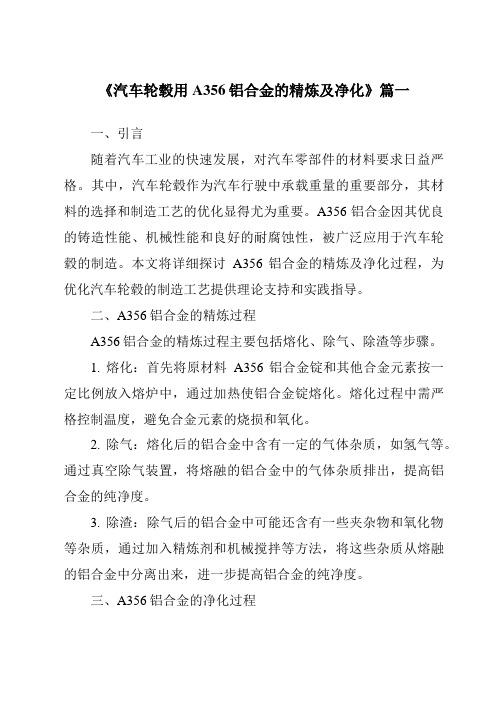
《汽车轮毂用A356铝合金的精炼及净化》篇一一、引言随着汽车工业的快速发展,对汽车零部件的材料要求日益严格。
其中,汽车轮毂作为汽车行驶中承载重量的重要部分,其材料的选择和制造工艺的优化显得尤为重要。
A356铝合金因其优良的铸造性能、机械性能和良好的耐腐蚀性,被广泛应用于汽车轮毂的制造。
本文将详细探讨A356铝合金的精炼及净化过程,为优化汽车轮毂的制造工艺提供理论支持和实践指导。
二、A356铝合金的精炼过程A356铝合金的精炼过程主要包括熔化、除气、除渣等步骤。
1. 熔化:首先将原材料A356铝合金锭和其他合金元素按一定比例放入熔炉中,通过加热使铝合金锭熔化。
熔化过程中需严格控制温度,避免合金元素的烧损和氧化。
2. 除气:熔化后的铝合金中含有一定的气体杂质,如氢气等。
通过真空除气装置,将熔融的铝合金中的气体杂质排出,提高铝合金的纯净度。
3. 除渣:除气后的铝合金中可能还含有一些夹杂物和氧化物等杂质,通过加入精炼剂和机械搅拌等方法,将这些杂质从熔融的铝合金中分离出来,进一步提高铝合金的纯净度。
三、A356铝合金的净化过程A356铝合金的净化过程主要包括滤渣、均匀化处理和铸造等步骤。
1. 滤渣:精炼后的铝合金通过滤渣装置,将剩余的杂质和夹杂物进一步去除,保证铸造出的轮毂表面光滑、无缺陷。
2. 均匀化处理:滤渣后的铝合金需要进行均匀化处理,使合金元素在熔体中均匀分布,提高合金的性能。
均匀化处理的温度和时间需严格控制,避免合金元素的过烧和氧化。
3. 铸造:均匀化处理后的铝合金即可进行铸造。
铸造过程中需控制好铸造温度、铸造速度和冷却速度等参数,以保证轮毂的尺寸精度和机械性能。
四、结论通过对A356铝合金的精炼及净化过程的探讨,我们可以得出以下结论:1. 精炼过程能有效去除铝合金中的气体杂质和夹杂物,提高铝合金的纯净度,为后续的铸造过程提供良好的原材料。
2. 净化过程通过滤渣、均匀化处理和铸造等步骤,进一步保证轮毂的尺寸精度和机械性能,提高轮毂的使用寿命和安全性。
铝合金精炼
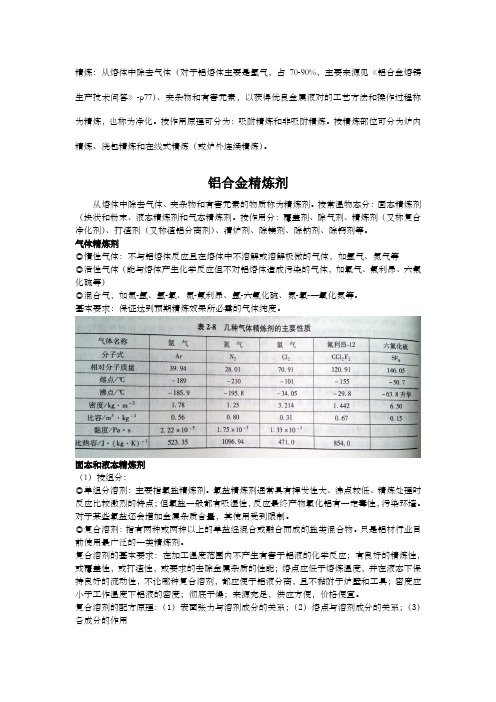
精炼:从熔体中除去气体(对于铝熔体主要是氢气,占70-90%,主要来源见《铝合金熔铸生产技术问答》-p77)、夹杂物和有害元素,以获得优良金属液对的工艺方法和操作过程称为精炼,也称为净化。
按作用原理可分为:吸附精炼和非吸附精炼。
按精炼部位可分为炉内精炼、浇包精炼和在线式精炼(或炉外连续精炼)。
铝合金精炼剂从熔体中除去气体、夹杂物和有害元素的物质称为精炼剂。
按常温物态分:固态精炼剂(块状和粉末、液态精炼剂和气态精炼剂。
按作用分:覆盖剂、除气剂、精炼剂(又称复合净化剂)、打渣剂(又称渣铝分离剂)、清炉剂、除镁剂、除钠剂、除钙剂等。
气体精炼剂◎惰性气体:不与铝熔体反应且在熔体中不溶解或溶解极微的气体,如氩气、氮气等◎活性气体(能与熔体产生化学反应但不对铝熔体造成污染的气体,如氯气、氟利昂、六氟化硫等)◎混合气,如氮-氩、氩-氯、氮-氟利昂、氩-六氟化硫、氮-氯-一氧化氮等。
基本要求:保证达到预期精炼效果所必需的气体纯度。
固态和液态精炼剂(1)按组分:◎单组分溶剂:主要指氯盐精炼剂。
氯盐精炼剂通常具有挥发性大、沸点较低、精炼处理时反应比较激烈的特点;但氯盐一般都有吸湿性,反应最终产物氯化铝有一定毒性,污染环境。
对于某些氯盐还会增加金属杂质含量,其使用受到限制。
◎复合溶剂:指有两种或两种以上的单盐经混合或融合而成的盐类混合物。
只是铝材行业目前使用最广泛的一类精炼剂。
复合溶剂的基本要求:在加工温度范围内不产生有害于铝液的化学反应;有良好的精炼性,或覆盖性,或打渣性,或要求的去除金属杂质的性能;熔点应低于熔炼温度,并在液态下保持良好的流动性,不论哪种复合溶剂,都应便于铝液分离,且不黏附于炉壁和工具;密度应小于工作温度下铝液的密度;彻底干燥;来源充足,供应方便,价格便宜。
复合溶剂的配方原理:(1)表面张力与溶剂成分的关系;(2)熔点与溶剂成分的关系;(3)各成分的作用(2)按使用目的:◎防止氧化和吸气用的覆盖剂(要求小的表面张力和低的熔点)◎除氢脱气的除气剂◎除去氧化物夹杂用的净化剂◎除去钠、镁、钾、钙等杂质元素的元素清除剂◎清炉分离铝液用的除渣剂(对铝液有大的表面张力而对氧化渣要有较小的表面张力)◎细化变质用的变质剂铝及其合金中气体的来源氢在液态铝合金和固态铝合金的饱和溶解度相差近17倍,因此即使合金液含氢量很低,凝固时也会有大量的氢析出,在铸件中形成针孔和夹杂等缺陷。
铝合金的精炼与净化技术
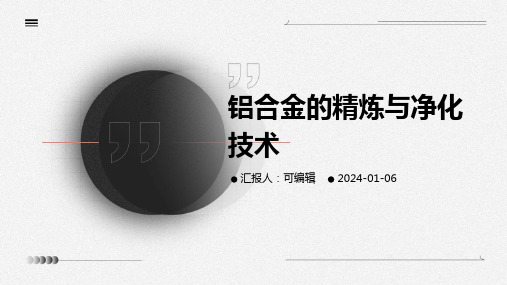
晶粒细化技术
铝合金的晶粒大小对其力学性能和加工性能有重要影响。通 过晶粒细化技术可以减小铝合金的晶粒尺寸,提高其力学性 能和加工性能。常用的晶粒细化剂包括铝钛硼、铝钛碳等。
细化原理:晶粒细化剂在铝合金熔体中形成大量弥散的质点 ,这些质点可作为非自发形核的基底,促使熔体形核,从而 细化晶粒。
微量元素控制技术
铝合金的精炼与净化 技术
汇报人:可编辑 2024-01-06
• 铝合金精炼与净化的重要性 • 铝合金的精炼技术 • 铝合金的净化技术 • 铝合金精炼与净化的未来发展 • 铝合金精炼与净化的实际应用案
例
目录
01
铝合金精炼与净化的重要性
铝合金的应用领域
航空航天
铝合金因其轻质、高强 度特性广泛应用于航空
精炼与净化有助于降低铝合金的 夹杂物含量,提高其加工性能和 表面质量。
02
铝合金的精炼技术
熔剂精炼
总结词
熔剂精炼是一种通过在铝液中加入一定量的熔剂,以去除杂质和气体的方法。
详细描述
熔剂精炼的原理是利用熔剂与铝液中的杂质发生化学反应,生成不溶于铝液的 化合物,从而将杂质从铝液中分离出来。常用的熔剂包括氯化物、氟化物和硫 化物等。
建筑行业的应用
铝合金在建筑行业中被广泛用于门窗、幕墙、支架等。铝合金的精炼与净化技术可以提高其抗风压、 抗水压和耐久性,确保建筑的安全性和美观性。
例如,某建筑公司采用铝合金精炼与净化技术,成功建造了一座高层写字楼。该建筑的外墙采用高强 度铝合金材料,不仅美观耐用,而且提高了建筑物的抗震性能和节能性能。
微量元素对铝合金的性能具有重要影 响,如铁、硅、铜等元素会影响铝合 金的强度、塑性和耐腐蚀性等。通过 微量元素控制技术可以精确调控这些 元素的含量,提高铝合金的性能。
铝合金的精炼处理
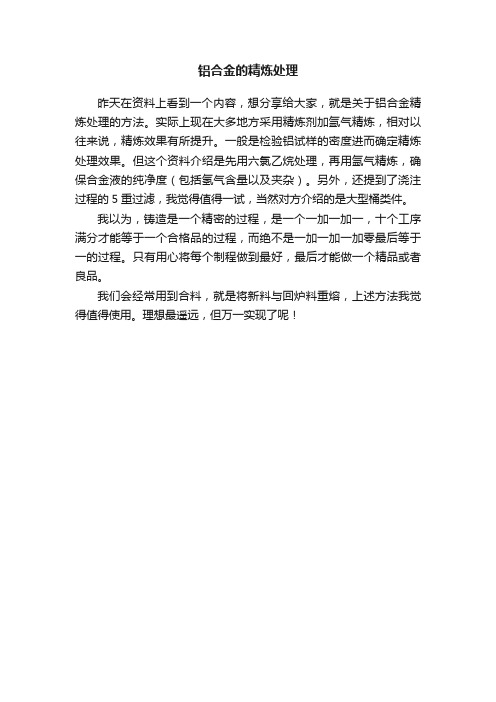
铝合金的精炼处理
昨天在资料上看到一个内容,想分享给大家,就是关于铝合金精炼处理的方法。
实际上现在大多地方采用精炼剂加氩气精炼,相对以往来说,精炼效果有所提升。
一般是检验铝试样的密度进而确定精炼处理效果。
但这个资料介绍是先用六氯乙烷处理,再用氩气精炼,确保合金液的纯净度(包括氢气含量以及夹杂)。
另外,还提到了浇注过程的5重过滤,我觉得值得一试,当然对方介绍的是大型桶类件。
我以为,铸造是一个精密的过程,是一个一加一加一,十个工序满分才能等于一个合格品的过程,而绝不是一加一加一加零最后等于一的过程。
只有用心将每个制程做到最好,最后才能做一个精品或者良品。
我们会经常用到合料,就是将新料与回炉料重熔,上述方法我觉得值得使用。
理想最遥远,但万一实现了呢!。
铝合金精炼步骤

铝合金精炼步骤哎呀,说起铝合金精炼,这事儿可真不是一两句能说清楚的。
你想想,那铝锭子,硬邦邦的,得经过多少道工序才能变成我们手里那些轻巧的铝合金产品啊。
我跟你说,这过程,可比咱们平时做饭复杂多了。
首先啊,得从那铝土矿开始。
这玩意儿,就是铝的老家,里面含有氧化铝。
你别小看它,这氧化铝可是个硬骨头,得经过高温煅烧,才能变成氧化铝。
这个过程,就像是把生米煮成熟饭,得有耐心,慢慢来。
煅烧完了,氧化铝就出来了,但这玩意儿还不能直接用,得电解。
电解你知道吧?就是把氧化铝溶解在冰晶石里,然后通电,让铝离子游到阴极去。
这个过程,就像是把面团发酵,得等着,不能急。
电解出来的铝,还不是我们想要的铝合金。
这时候,就得加入一些其他金属,比如铜啊、镁啊、硅啊,这些。
这就像是炒菜,得放点调料,才能做出好味道。
加入这些金属,铝就变得不一样了,有了不同的性能,比如硬度啊、韧性啊,都能按照我们的需求来调整。
接下来,就是熔炼。
把铝和这些金属混合在一起,加热到高温,让它们完全融合。
这个过程,就像是把各种食材混合在一起,做成一锅大杂烩。
得掌握好火候,不然做出来的东西,要么太硬,要么太软。
熔炼好了,就得冷却成型。
这就像是把面团压成面饼,得有一定的形状,才好用。
冷却成型后,铝合金就初具雏形了。
最后,就是精加工。
这就像是把面饼切成面条,得精细操作,才能做出好产品。
精加工包括切割、打磨、抛光等等,每一步都得小心翼翼,不然就前功尽弃了。
你看,这铝合金精炼,是不是跟咱们做饭一样,得一步步来,不能急。
每一步都得精心操作,才能做出好的产品。
这过程,虽然听起来枯燥,但你要是真的去工厂看看,那热火朝天的场面,那机器的轰鸣声,那工人的汗水,都让人感受到工业的魅力。
这不仅仅是生产,更是一种艺术,一种人类智慧的结晶。
所以啊,下次你手里拿着铝合金制品的时候,不妨想想,这背后有多少人的汗水和智慧。
这不仅仅是一块金属,这是人类文明进步的见证。
- 1、下载文档前请自行甄别文档内容的完整性,平台不提供额外的编辑、内容补充、找答案等附加服务。
- 2、"仅部分预览"的文档,不可在线预览部分如存在完整性等问题,可反馈申请退款(可完整预览的文档不适用该条件!)。
- 3、如文档侵犯您的权益,请联系客服反馈,我们会尽快为您处理(人工客服工作时间:9:00-18:30)。
典型铝合金熔炼工艺∙2013-11-19 11:18:57∙来源:中铝网∙我要评论随着科学技术的发展,汽车、造船、航空、航天及其他制造业对铝合金铸件的品质要求也愈来愈高,除了保证化学成分、力学性能和尺寸精度外,不允许铸件有气孔、缩孔等缺陷。
而铝合金的熔炼则是铸件生产过程中的一个很重要的工序。
多年来的生产经验证明,熔炼工艺过程控制不严,铸件很容易产生针孔、氧化夹渣、缩松等缺陷,直接影响铸件质量。
因此,要想获得优质铝合金铸件,必须严格控制熔炼工艺。
一、熔炼前的准备1.严格控制炉料质量。
炉料质量是铸造生产的源头,直接影响到最终铸件的质量,成分不合格导致产品成批性报废。
因此,要高度重视。
必须做到:①严格控制炉料中新旧炉料的比例,回炉料所占炉料质量百分比应小于等于70%;②保证炉料干净,炉料需经吹砂后使用;③三等回炉料枷浇冒口匀使用前应经重熔精炼处理;④炉料应充分预热,去除水分、油污等杂质;⑤由于铭合金有铝硅类、铝铜类、铝镁类等合金,合金牌号较多,使用的元素也比较多,且互相影响,要求严格管理,不可混料;⑥配料、称量要准确,比如ZL104合金,考虑到除气、排渣及变质过程中的损耗,Mg元素应在实际配料时多加炉料质量的0.02%-0.03%,才能保证铸件的化学成分。
2.熔炼工具。
熔炼使用的址涓及熔炼工具须清理干净且涂上涂料,以保证使用时与铝合金有效隔离,减少合金液受到杂质污染,并且需要充分预热,址涓要烘烤至暗红色再加入炉料熔炼,以防水蒸气带入合金中使合金的气体增加、针孔度增加。
3.其他工作。
严格按已制订好的工艺规范作好覆盖剂、精炼剂及变质剂的准备工作。
二、熔炼操作熔炼步骤如下。
①装料。
在预热后的柑A中装入预制合金锭、优质回炉料,再加中fol合金,最后加合金元素。
②温度控制。
严格控制铝合金熔炼的温度,只有合适的温度才能获得高质量的合金液,避免过热。
若温度过高,会加大合金中各种元素的氧化烧损,引起合金中化学成分的变化。
温度过低,会使合金的化学成分不均匀,合金中的氧化夹杂物、气体等不易排出,合金的理化性能下降,影响铸造性能。
③时间控制。
严格控制熔炼时间,操作要迅速,减少合金吸气和氧化夹杂,增加合金元素的烧损,影响合金化学成分。
④精炼操作。
铝合金精炼的主要目的是清除熔液内的气体和非金属夹杂物、均匀合金成分。
精炼是熔炼中极为重要的一个工艺过程。
应正确选用精炼剂、控制好加入量份般加入合金质量的0.5%-0.7%)及把握好精炼温度,精炼温度一般控制在700-7200C。
在精炼的过程中,用钟罩将精炼剂分批压入熔液面下约2/3处怀要压入柑A底韵,均匀缓慢做顺时针转动,速度要缓、动作要平稳,避免金属液大幅度搅动,以防增加氢含量和卷入夹杂。
⑤变质处理。
铭合金变质的目的是细化晶粒,提高铸件性能。
变质剂应先预热,控制要点是:①变质温度,一般不超过7400C ;②变质时间,一般为10min ;③变质剂的加入量,使用双色变质剂的用量一般为合金液质量的1.0%-1.2%;④操作方法要到位。
合金精炼后要尽快浇注完毕,砂型铸造一般应控制在40min内,金属型铸造应控制在2h内,否则,要重新进行精炼、变质,再次精炼时加入的精炼剂为合金质量的0.2%左右。
(注意事项。
为防止发生铝合金飞溅,熔炼场地应保持干燥;操作人员应戴防辐射眼镜、工作帽、手套,着工作服。
)三、两个关键问题①单铸试棒的力学性能,不能完全反映熔炼质量的好坏。
单铸试棒的性能只能代表熔炼质量和热处理质量的一部分。
铝液中含气量的多少、产生缩松和氧化倾向的大小、夹渣物含量的多少,不能完全根据单铸试棒的力学性能全部反映出来。
②几种元素对铝合金组织和性能的影响。
在实际生产中发现,铝合金中Mg元素的含量在接近标准的下限时,可能引起铸件硬度降低,而接近标准上限时,可能引起延伸率降低;Ti元素是铝合金中最常用的细化剂,对合金熔炼有益;Fe元素是合金中主要的有害杂质,会降低合金的机械性能,它来自柑涓、熔炼工具和炉料,应严格控制;Mn 元素能有效地减弱Fe元素对铝合金的有害影响,但Mn的加入量不宜过多,否则易产生粗大脆性化合物,还可能产生偏析,影响铸件性能。
四、熔炼导致的缺陷分析及防止1.针孔铝合金针孔缺陷产生的原因:①炉料及熔炼工具烘烤不充分;②熔化温度过高或熔炼时间太长;③变质后铝液停留的时间过长;④合金精炼不好;⑤工作场地太潮湿。
防止办法:①炉料及工具应彻底烘干;②控制熔化温度,一般不超过7400C、不超过浇注温度,还要防止合金在熔化过程中的局部过热;③操作迅速,尽量缩短熔炼时间;④精炼操作要细心,精炼是防止气孔的最好办法;⑤变质后合金液静置8-15min应及时浇注;⑥保持熔炼场地干燥。
2.氧化夹渣铝合金氧化夹渣缺陷产生的原因:①炉料不清洁,回炉料使用量过多;②合金液中的熔渣未清除干净;③变质处理后,静置时间不够。
防止办法:炉料经吹砂后,回炉料控制在炉料质量的70%以内;除气排渣要彻底;变质后,保证足够的静置时间,以便熔渣有充分的时间下沉或上浮。
3.缩孔及缩松缺陷铝合金缩孔和缩松缺陷产生的原因:①合金晶粒粗大;②招合金浇注温度过高;③铸件浇注系统设计不合理。
防止办法:①合金液精炼、变质操作的效果对该类缺陷影响很大,因此要做到位;②严格控制铝液温度,防止过热,在保证铸件不产生浇不足的情况下,应尽可能采用低的浇注温度,浇注温度一般不超过7300C ;③合理设计浇注系统,使金属液能够平稳充型;④适当调整成分,控制适宜的杂质含量对增强金属液的流动性也有效果。
五、Z L 104合金熔炼过程中Mg元素的控制措施熔炼的过程中,防止合金元素的烧损显得特别重要,ZL104铝合金在熔炼过程中,Mg的损耗比其他组元损耗要难于控制,为减少Mg元素的烧损,就要加强熔炼工艺的控制。
本节重点以ZL104为例详细探讨铝合金熔炼工艺控制,特别是铝合金在高温状态及精炼、变质阶段的控制。
ZL104铝合金属于Al-Si二元共晶合金中添加Mg的AI-Mg-Si铸造合金,在国防工业及民用产品中,铸造铝合金ZL104应用广泛,其成分为(质量分数)Si8.0% -10.5% " M四.17%-0.3%MnO.2%-0.5%,其余为Al o ZL104合金铸件一般在T6状态下使用,由于Mg的加入与Si 形成硬而脆的M护i强化相,它对合金的热处理效果影响最为敏感。
当合金经固溶再在150-180℃时效处理后,自铭a固熔体中析出弥散的Mg2Si质点,从而引起晶格发生了崎变,阻碍位错运动,起到强化作用,因而合金的抗拉强度有较大提高,甚至达到峰值。
但少量的Mg起不到强化作用,而过量的Mg将会有大量的Mg2Si形成,影响合金的塑性。
在实际中发现,当Mg含量接近材料标准下限时,一般硬度低、延伸高;而当Mg含量接近材料标准上限时,一般延伸率低,可能达不到要求。
多年的生产实践说明,熔炼工序是该类材质铸件生产流程中的关键工序。
这道工序是理化性能的保证,稍有疏忽就可能导致整炉零件因化学成分不合格而报废,而其中起关键作用的元素就是成分中的Mg元素。
多次的实践证明,由于Mg元素比较活泼,再加上各方面的烧损因素,在生产中不易控制。
因此,在熔炼过程中如何来提高ZL104合金的质量是生产ZL104合金铸件很关键的问题。
影响ZL104中的Mg元素的因素比较多。
Mg是活泼元素,其熔点为650℃且与氧的亲和力很强。
处在液态时氧化速度大大加强。
在精炼及变质的过程中,Mg元素的烧损都会增加,保温浇注的时间过长,Mg元素的损耗要增加。
1.配料在新料及回炉料的配比上,要特别重视Mg元素的含量。
在炉料的配比量上,要采取“去尾数”的方法。
例如:如果回炉中Mg含量为0.1484%,我们通常的算法是保留小数点后两位数,第三位数采用“四舍五入’,的办法,这时,0.1484%就算做0.15%。
这样计算就等于在回炉料中多算了0.0016%的Mg,在配比中就要少算0.0016%的Mg质量。
但是我们考虑到Mg在熔炼过程中大量的损耗,就不管第三位数字了,以实际分析出的第二位数字为准,即为0.14%来计算其Mg含量。
事实说明,用这种方法计算的炉料熔炼的效果是合格的。
2.精炼工序精炼的目的是清除合金液中的非金属夹杂物他包括气哟I精炼的方法有多种,其中用六氯乙烷(C2CQ除气精炼比较常用。
在700-720℃时用钟罩将精炼剂C厂16分批压入熔液面下约2/3处,均匀缓慢做顺时针转动,待C2Ch充分反应,将熔液中的夹杂、气体带出。
要点是搅动的速度要缓慢,如果搅动的频率过大,C2CL6在铝液中反应激烈,熔液不停地翻滚,熔液中的镁与氧大量接触,产生燃烧,这样就增加了烧损量,可能造成镁量的急剧减少。
C2CI。
的用量与合金成分及原铸锭质量有关,也与Mg含量有关,一般用量为炉料质量的0.5%-0.7%。
在柑涓电阻炉内熔化,精炼时间在10min以内时,经过测定,这个环节Mg的损失量为炉料质量的0.02%-0.05%。
3.除渣当使用C2CL充分精炼后,将钟罩取出,清理掉残留的氧化物,将熔液表面的夹杂物用打渣勺捞出。
在温度为680-700℃时再将Mg装入钟罩,压入熔液下部怀要压入柑涓底韵,静置3-.5min。
待Mg在熔液中完全熔化,然后缓慢做顺时针搅动,使之均匀分布在合金中,不能让翻滚的熔液冲破液面,以免让Mg漂浮在液面产生氧化燃烧,降低Mg的实际含量。
整个操作过程要小心、稳重。
4.变质工序根据合金熔炼工艺,Al-Si合金中含Si量质量比在6%-11%的合金浇注后易产生粗晶硅,在砂型铸造或金属型铸造时都应在精炼后进行变质处理。
为细化晶粒,在使用钠基四元变质剂时,用量一般约为炉料质量比的2.5%,应该先在炉边预热5-10min使其挥发尽吸入的水蒸气。
当合金温度达到720-740℃时,将变质剂压入合金液面,逐渐熔化使其产生变质效果,然后静置。
整个操作时间为8-12min。
在浇注过程中,不需要把变质剂的渣料取出,只需把变质剂推向一旁即可,舀取合金液进行浇注,确保自始至终的变质效果。
这个过程中Mg元素的烧损比精炼阶段要大,Mg的损失量为炉料质量比的0.13%-0.18%。
合金液温度比较高且大量和钠盐接触,遇到活泼的钠元素助长了Mg元素的远速氧化,因此,变质过程是Mg元素损失的主要阶段。
5.浇注工艺合金变质处理后4-10min应立即进行浇注。
浇注温度一般要求为730-745℃之间。
实践证明,当温度在750℃以上时,会加速铝的氧化,镁的烧损也加速,因此,要严格控制浇注温度,根据该铸件的生产特点,在开始浇注时把温度控制在740750℃之间,因为此时砂型或金属型温度较低,避免最后浇注的零件产生浇不足等缺陷。
不能随意延长静置时间,这会增加镁元素的烧损,造成化学成分不合格,一般砂型铸造要求40min内浇完,金属型铸造在2h内浇完。