热喷涂技术修复轴头磨损地局限性
烘缸轴承位磨损无法拆卸-现场5小时快速修复(图文案例)
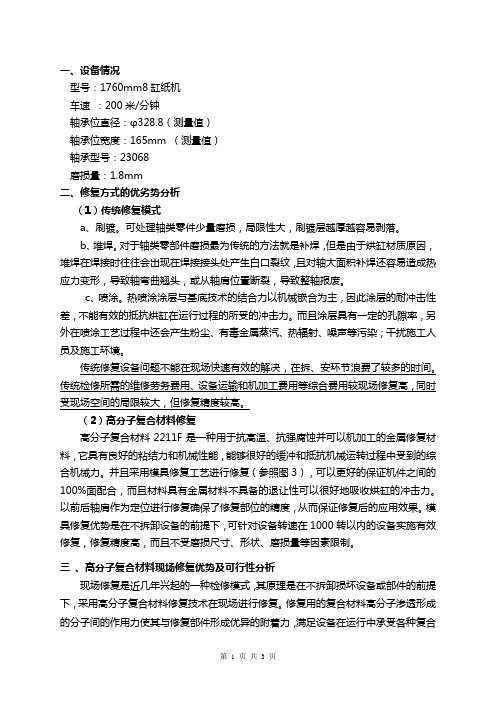
一、设备情况型号:1760mm8缸纸机车速:200米/分钟轴承位直径:φ328.8(测量值)轴承位宽度:165mm (测量值)轴承型号:23068磨损量:1.8mm二、修复方式的优劣势分析(1)传统修复模式a、刷镀。
可处理轴类零件少量磨损,局限性大,刷镀层越厚越容易剥落。
b、堆焊。
对于轴类零部件磨损最为传统的方法就是补焊,但是由于烘缸材质原因,堆焊在焊接时往往会出现在焊接接头处产生白口裂纹,且对轴大面积补焊还容易造成热应力变形,导致轴弯曲翘头,或从轴肩位置断裂,导致整轴报废。
c、喷涂。
热喷涂涂层与基底技术的结合力以机械嵌合为主,因此涂层的耐冲击性差,不能有效的抵抗烘缸在运行过程的所受的冲击力。
而且涂层具有一定的孔隙率,另外在喷涂工艺过程中还会产生粉尘、有毒金属蒸汽、热辐射、噪声等污染;干扰施工人员及施工环境。
传统修复设备问题不能在现场快速有效的解决,在拆、安环节浪费了较多的时间。
传统检修所需的维修劳务费用、设备运输和机加工费用等综合费用较现场修复高,同时受现场空间的局限较大,但修复精度较高。
(2)高分子复合材料修复高分子复合材料2211F是一种用于抗高温、抗强腐蚀并可以机加工的金属修复材料,它具有良好的粘结力和机械性能,能够很好的缓冲和抵抗机械运转过程中受到的综合机械力。
并且采用模具修复工艺进行修复(参照图3),可以更好的保证机件之间的100%面配合,而且材料具有金属材料不具备的退让性可以很好地吸收烘缸的冲击力。
以前后轴肩作为定位进行修复确保了修复部位的精度,从而保证修复后的应用效果。
模具修复优势是在不拆卸设备的前提下,可针对设备转速在1000转以内的设备实施有效修复,修复精度高,而且不受磨损尺寸、形状、磨损量等因素限制。
三、高分子复合材料现场修复优势及可行性分析现场修复是近几年兴起的一种检修模式,其原理是在不拆卸损坏设备或部件的前提下,采用高分子复合材料修复技术在现场进行修复。
修复用的复合材料高分子渗透形成的分子间的作用力使其与修复部件形成优异的附着力,满足设备在运行中承受各种复合力的要求。
选粉机轴承位磨损怎么修复,教你一种现场修复新方法

选粉机轴承位磨损怎么修复,教你一种现场修复新方法选粉机,在新型干法水泥生产线中的煤磨、生料中卸烘干磨及水泥磨系统得到广泛应用。
可分为三分离选粉机、离心式选粉机、旋风式选粉机三大类。
将粉磨的物料进行筛选得到合格的成品。
一、选粉机轴损坏原因设备存在不同程度的震动,紧定套位置容易出现磨损间隙。
一旦出现磨损间隙,紧定套与轴会出现相对摩擦运动,导致短时间内温度升高,金属磨损加剧,间隙加大。
严重时紧定套轴向运动,同时也加剧了轴的磨损。
严重时导致紧定套定位失效,轴承报废。
轴类出现磨损的原因有很多,但是最主要的原因就是用来制造轴的金属特性决定的,金属虽然硬度高,但是退让性差(变形后无法复原),抗冲击性能较差,抗疲劳性能差,因此容易造成粘着磨损、磨料磨损、疲劳磨损、微动磨损等,大部分的轴类磨损不易察觉,只有出现机器高温、跳动幅度大、异响等情况时,才会引起人们的察觉,但到人们发觉时,大部分轴都已磨损,从而造成机器停机。
二、传统修复方法传统修复工艺:针对选粉机轴类的磨损(1)现场电刷镀工艺(2)热喷涂工艺(3)整体拆卸,然后补焊机加工修复(4)更换新部件。
1.电刷镀及热喷涂修复工艺其优点就是可以实现在线修复,其缺点非常明显。
电刷镀镀层不能太厚,所以在修复条件上有局限性,在20丝以内镀层使用效果还能保证,越厚容易脱落,在使用过程中刷镀层容易脱落,使用寿命短。
热喷涂虽然对厚度没有局限性,但是该工艺无法避免热应力的问题,造成轴使用过程中出现裂纹甚至断裂的危险,大大增加生产安全隐患。
2. 补焊机加工修复工艺补焊机加工修复工艺是传统工艺修复工艺中最常见的一种方式,其特点就是修复精度高。
其缺点是对于小型轴类的修复过程中容易造成应力集中或者造成轴的弯曲变形;对于选粉机轴类等大型设备,拆卸和运输将大大增加修复成本和修复周期,且对于机加工设备的要求极高,综合性价比低,大大影响企业的正常生产,增加维修维护成本。
3. 更换新部件对于选粉机轴的磨损,采用更换的方式不仅成本高,且拆装和运输综合成本使企业难以接受,一般不予采用。
[研究]热喷涂法的缺点
![[研究]热喷涂法的缺点](https://img.taocdn.com/s3/m/3276fe0054270722192e453610661ed9ad5155db.png)
热喷涂法的缺陷热喷涂法的缺陷之喷铅、喷铜、喷不锈钢、喷有色金属(1)由于涂层与基体主要是靠机械结合情势(喷焊工艺除外),所以其与基体表面的结合强度,绝对地较低于金属热处理,涂层自身强度一般不可能达到基体金属本身的强度。
(2)涂层存在一定的气孔(喷焊工艺除外),这对于要求耐化学介质腐蚀的环境是不利的。
但有试验表明,当涂层厚度达到一定值时,(比如镍包铝材料的等离子喷涂层,厚度到达0.3~0.5毫米以上时)其气孔已被涂层自身关闭,成为非穿透性气孔。
另外,还可以对涂层进行封孔处理。
然而在某些情况下气孔的存在恰是咱们所需要的。
例如作为隔热涂层、含油轴承和人造骨骼等。
(3)某些喷涂办法(特殊是等离子喷涂和喷焊工艺)要产生多种有害因素,因而在采取这类方法时,必需采用恰当的防护办法。
应该指出,任何一种进步技术都不是万能的,必须根据工作条件剖析其可行性、牢靠性、经济性等诸因素来断定最佳计划。
热喷涂法的长处有哪些?无论那一种热喷涂方法,都是在材料表面形成一层所需功效的表面层。
因此基于这点,热喷涂技术也是一种表面处理技术。
但它与其它表面处理技术比拟,又有许多本身的特点,从而逐步形成一门独破的应用技术。
热喷涂技术的重要优毛病如下:1、热喷涂法的长处-喷铅、喷铜、喷不锈钢、喷有色金属(1)热喷涂法的适应规模广,不仅实用于金属制品,也适用于非金属制品,如陶瓷制品、水泥制品、石膏制品、塑料制品,甚至木材、布匹、纸张等,均能在其表面形成涂层。
(2)能够失掉品种繁多的涂层。
正常来说,凡经加热能呈熔融状态或塑性状况的任何固体工程材料,无论是金属、陶瓷、玻璃或塑材均可作为喷涂材料,而且还可以依据须要将各种材料混杂或制成复合资料,使所得到的涂层满意各类特别请求。
目前已经可能较便利地取得耐磨(包含高硬度、易磨削、低摩擦的各种涂层)、耐腐化、耐高温、隔热、绝缘、导电、防辐射、密封等机能的涂层。
(3)简直不受尺寸和几何外形的限度,只有喷射束能达到的部位,都可以进行喷涂。
热喷涂技术在修复汽车发动机曲轴中的应用

热喷涂技术在修复汽车发动机曲轴中的应用【摘要】热喷涂在铁路上的应用起步较晚,尤其在修复汽车零件中的应用较少。
在修理汽车零部件的过程中,大多采用传统的焊接方法或电刷镀。
【关键词】热喷涂技术;发动机曲轴;焊接方法1.概述热喷涂在修复汽车零件中的应用较少。
在修理汽车零部件的过程中,大多采用传统的焊接方法或电刷镀。
对于发动机曲轴等采用球墨铸铁等含碳量高、受力较大的零件,用CO气体保护焊或手工电弧焊无法满足可靠性的要求,多次试验表明,焊修的曲轴在使用一个中修期(约3年)后,解体时发现均在焊接部位产生裂纹。
每年人厂大修的汽车中至少有一根(价格在30万元)因存在裂纹而无法修复,大部分报废处理。
而热喷涂熔敷焊修能提高曲轴的修复率和可靠性,前期我们对DF8B型汽车发动机所用材质为42CrMo钢的曲轴做过热喷涂熔敷焊修的试验,经检验各项性能指标良好,试样抗拉强度达780MPa,与母体非常接近。
2.热喷涂焊接的特点热喷涂焊接是热喷涂与非透明物质相互作用的过程,通过热喷涂使金属粉末熔化后与所焊接部位结合。
热喷涂焊接有如下特点:(1)热喷涂焊接可使工件产生的变形极小,热影响区也很窄。
(2)可获得深度大的焊缝,焊接厚件时可不开坡口一次成形。
(3)适宜于难熔金属、热敏感性强的金属以及热物理性能差异悬殊、尺寸和体积悬殊工件问的焊接。
通过对球墨铸铁曲轴和锻造曲轴的材质进行分析,先根据其材质做试棒,进行抗拉强度试验和冲击试验,用热喷涂熔敷焊接后的试棒和未焊接的试棒强度进行对比,球墨铸铁曲轴焊接后其强度达到460MPa,达到35号钢在正火加回火状态下的强度。
在这种情况下消除缺陷,采用热喷涂熔敷焊对球墨铸铁曲轴进行修理,可以大大提高曲轴的修复率和可靠性。
3.热喷涂修复汽车发动机球铁曲轴技术方案球铁曲轴的化学成分为:碳3.5%~4.0%,硅2.0%~2.8%,锰0.3%~0.6%,钼0.2%~0.4%,铜0.7%~1.O%,镁0.04%~0.1%,稀土(RxOy)≤0.012%,硫≤0.025%,磷≤0.08%。
热喷涂技术在推力头内孔磨损修复中的应用

寸 ,按 推 力头孔 径 的万 分之 一到万 分 之一点 五 确定 内孔 的配合 过盈 量 。在 喷涂后 的车 削加 工前 .应 根 据推 力 头 外 圆 的 同 心度 ,精 确 调 整 ,误 差 控 制 在
报废 ,稳 定性差 。 电镀 工艺在 电镀过 程 中 ,内孔镀
响涂层 质量 ,这样 对施工 空间要 求就 比较低 ,作业
层 均 匀度很 难控制 ,因为镀层 材料非 常硬 ,金加工
又很 不方便 ,而且 很容 易损伤 推 力头 的外表 。采用 热 喷涂技术 修复推 力头 内孔 ,则 町以完全避免 上述
化后加速 ,形成 高 速熔 滴 射 到经 处 理 的工 件 表 面 ,
收 稿 日期 :2 1 —0 —3 01 8 1
作 者简 介 :罗 金 强 (9 3 ,男 ,电 气 高 级 技 师 ,主 要 从 16 一) 事 水 电 设 备 生 产 管理 工作 。
・
3 推力头 内孔磨损修复
推力 头 内孑 磨损一 般都 呈现 不规则 磨损 ,有椭 L 圆型磨损 、锥 型磨 损 、椭 圆型 和锥 型 复 合 型磨 损 ; 这些 磨损都会 造 成推力 头与 主轴 的松动 ,引起 机组
量和轴 向推力 ,它的工作 状态 直接影 响机组 的稳定
和安全 。
在每 次机组 大修过程 中 ,推力头必 须从 主轴上 拆卸 下来 ,以便整 机解体 维修 、保养 ,因此 ,推力 头磨 损 ( 内孔 磨损 和外 圆磨损 )现象 比较常见 。外
面 。高速燃 气不 但 能使 粉 末 材 料 的颗 粒 加 速运 动 ,
圆磨 损处理起 来 比较 简单 ,采用 金加工 修复工 艺 即
车轴修复用热喷涂层厚度对微动损伤行为的影响
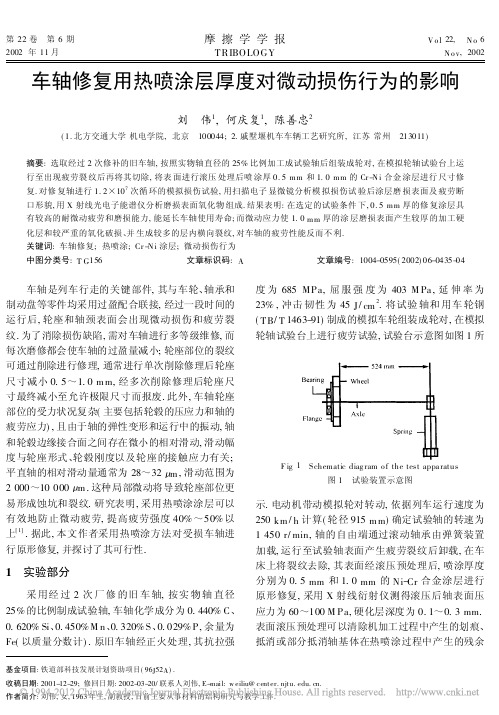
第22卷 第6期摩擦学学报V o l22, N o6 2002年11月TRIBOLOGY N o v,2002车轴修复用热喷涂层厚度对微动损伤行为的影响刘 伟1,何庆复1,陈善忠2(1.北方交通大学机电学院,北京 100044; 2.戚墅堰机车车辆工艺研究所,江苏常州 213011)摘要:选取经过2次修补的旧车轴,按照实物轴直径的25%比例加工成试验轴后组装成轮对,在模拟轮轴试验台上运行至出现疲劳裂纹后再将其切除,将表面进行滚压处理后喷涂厚0.5mm和1.0mm的Cr-N i合金涂层进行尺寸修复.对修复轴进行1.2×107次循环的模拟损伤试验,用扫描电子显微镜分析模拟损伤试验后涂层磨损表面及疲劳断口形貌,用X射线光电子能谱仪分析磨损表面氧化物组成.结果表明:在选定的试验条件下,0.5mm厚的修复涂层具有较高的耐微动疲劳和磨损能力,能延长车轴使用寿命;而微动应力使1.0mm厚的涂层磨损表面产生较厚的加工硬化层和较严重的氧化破损、并生成较多的层内横向裂纹,对车轴的疲劳性能反而不利.关键词:车轴修复;热喷涂;Cr-N i涂层;微动损伤行为中图分类号:T G156文章标识码:A文章编号:1004-0595(2002)06-0435-04 车轴是列车行走的关键部件,其与车轮、轴承和制动盘等零件均采用过盈配合联接,经过一段时间的运行后,轮座和轴颈表面会出现微动损伤和疲劳裂纹.为了消除损伤缺陷,需对车轴进行多等级维修,而每次磨修都会使车轴的过盈量减小;轮座部位的裂纹可通过削除进行修理,通常进行单次削除修理后轮座尺寸减小0.5~1.0m m,经多次削除修理后轮座尺寸最终减小至允许极限尺寸而报废.此外,车轴轮座部位的受力状况复杂(主要包括轮毂的压应力和轴的疲劳应力),且由于轴的弹性变形和运行中的振动,轴和轮毂边缘接合面之间存在微小的相对滑动,滑动幅度与轮座形式、轮毂刚度以及轮座的接触应力有关;平直轴的相对滑动量通常为28~32 m,滑动范围为2000~10000 m.这种局部微动将导致轮座部位更易形成蚀坑和裂纹.研究表明,采用热喷涂涂层可以有效地防止微动疲劳,提高疲劳强度40%~50%以上[1].据此,本文作者采用热喷涂方法对受损车轴进行原形修复,并探讨了其可行性.1 实验部分采用经过2次厂修的旧车轴,按实物轴直径25%的比例制成试验轴,车轴化学成分为0.440%C、0.620%Si、0.450%M n、0.320%S、0.029%P,余量为Fe(以质量分数计).原旧车轴经正火处理,其抗拉强度为685MPa,屈服强度为403M Pa,延伸率为23%,冲击韧性为45J/cm2.将试验轴和用车轮钢(TB/T1463-91)制成的模拟车轮组装成轮对,在模拟轮轴试验台上进行疲劳试验,试验台示意图如图1所 F ig1 Schematic diag ram o f the test appa ratus图1 试验装置示意图示.电动机带动模拟轮对转动,依据列车运行速度为250km/h计算(轮径915m m)确定试验轴的转速为1450r/min,轴的自由端通过滚动轴承由弹簧装置加载,运行至试验轴表面产生疲劳裂纹后卸载,在车床上将裂纹去除,其表面经滚压预处理后,喷涂厚度分别为0.5mm和1.0mm的Ni-Cr合金涂层进行原形修复,采用X射线衍射仪测得滚压后轴表面压应力为60~100M Pa,硬化层深度为0.1~0.3mm.表面滚压预处理可以清除机加工过程中产生的划痕、抵消或部分抵消轴基体在热喷涂过程中产生的残余基金项目:铁道部科技发展计划资助项目(96J52A).收稿日期:2001-12-29;修回日期:2002-03-20/联系人刘伟,E-mail:w eiliu@.作者简介:刘伟,女,1963年生,副教授,目前主要从事材料的结构研究与教学工作.拉应力对试验轴疲劳强度的不利影响.采用注油压装工艺将修复试验轴与模拟车轮组装成试验轮对,该结合为紧密结合,按照铁标(T B/T1463-91)“机车轮对组装技术条件”中的规定,过盈量小于毂孔直径的0.123%,接触面压应力为90~120MPa .将轮对在轮轴模拟试验台上进行微动损伤试验,试验载荷为160M Pa,加载精度控制在0.7%以内,经过1.2×107次循环后卸载.截取试验轴中产生微动损伤和疲劳裂纹的部位,经丙酮超声波清洗后,用扫描电子显微镜(SEM )分析磨损表面及断口形貌,选用X 射线光电子能谱仪(XPS)分析磨损表面氧化层组成,用HX-200型显微硬度计测定磨损剖面的微区硬度,加载0.49N 、保持时间15s .2 结果及讨论2.1 涂层的组织和性能试验所用2种厚度的涂层均包括底层和工作层,底层由扁平的 -Ni 金属颗粒、少量Al-Fe-Ni 金属间化合物及Al 2O 3组成,以增强涂层与轴基体的结合强度.底层与基体的结合为平滑锯齿面结合,在结合部位的轴基体一侧存在表面细晶层,证明对试验轴进行表面滚压预处理收到了预期的效果,轴基体表面未见熔化痕迹.工作层在涂层中承受微动应力,X 射线衍射测定结果表明,其由扁平的 -Fe 和 -Fe 金属小颗粒以及分布于边界处的杂质组成.涂层的金相组织结构照片见图2.总厚度为0.4~0.5m m 的涂层的底层F ig 2 M etallor gr aphic micro structure o f the coat ing图2 涂层金相组织结构照片厚度约为0.1mm ,工作层厚度为0.3~0.4m m;总厚度为0.9~1.0mm 的涂层的底层厚度约为0.3m m,工作层厚度为0.6~0.7mm.采用喷涂零件标准试样测定的涂层的剪切强度列于表1,涂层与轴结合面的平均剪切强度为73.3M Pa ,涂层的平均剪切强度为136.3MPa,涂层的平均硬度为215H B .2.2 涂层磨损表面及断口形貌图3所示为分别经2种厚度的涂层修复后的轴微动损伤表面形貌SEM 照片.可见:经厚0.5m m 的涂层修复后的轴微动损伤表面无疲劳裂纹,涂层表面氧化膜发生破裂和局部磨损、剥离,磨损部位涂层减薄;而经厚1.0mm 的涂层修复后的轴微动损伤表面出现较长的疲劳裂纹,并呈现较严重的氧化磨损迹表1 涂层的剪切强度Table 1 Shearing strength of the coatingSp ecim en S hearing s trength at the joint of coatin g and ax le /M PaShearing stren gth of the coating /M PaNo .176.8124.0No.259.4141.0No.366.0144.0No.491.1-Average73.3136.3(a)SEM micr og raph of t he fr etted sur faceof 0.5mm coating(b)SEM micr og r aph o f the frett ed surfaceof 1.0mm coatingF ig 3 SEM micr og raph of t he frett ed surface o f0.5mm a nd 1.0mm co ating图3 经厚0.5mm 和1.0mm 涂层修复的试验轴磨损表面SEM 照片象.XPS 分析结果表明,该氧化膜由Fe 2O 3和Cr 2O 3组成,次表层含有FeO [2],其可减轻表面粘着、降低摩擦系数[3].将经厚1.0mm 涂层修复后的轴沿疲劳裂纹敲断,用扫面电子显微镜观察其断口形貌结果示于图4.可以看出,在断口处的涂层内部存在横向裂纹[见图4(a )],而涂层与轴基体结合部位存在有局部剥离迹象[见图4(b)].经厚0.5mm 的涂层修复后的轴磨损截面则未见涂层与轴基体局部分离迹象.2.3 涂层磨损截面微区硬度表2列出了分别经2种厚度的涂层修复后的车轴磨损截面的微区硬度测量结果.可见,厚0.50m m436摩 擦 学 学 报第22卷(a)T rav erse cr acks in coating(b)L ocalized detachment of coat ing fr om ax le substr ateFig4 SEM micro gr aphs o f the fret ted fat ig ue surfa ce o f the ax le r epa ired w ith1.0m m co ating图4 经厚1.0mm的涂层修复后的轴微动疲劳断口形貌SEM照片的涂层的表面加工硬化层厚度约为0.15mm,而厚1.0mm的涂层的表面加工硬化层厚约0.50m m,加表2 涂层磨损截面的微区硬度Table2 Microhardness in the f retted sub-surfaceof the coatingDistan ce from th e fretted s urface/m mM icrohardness H V0.5m m coating 1.0mm coating0.05412-0.10412-0.153814520.25114-0.30153-0.351934370.50-381工硬化层的平均硬度值均在400H V以上.2.4 讨论与厚0.5mm的涂层相比,厚1.0mm的涂层的组织缺陷及非金属夹杂更多,涂层与轴基体的剪切强度和弹性模量的差距更大,在运行过程中车轴的弹性变形和振动的影响也更强.涂层愈厚,其应力愈倾向于3维平面应变状态,由于涂层与轴基体的结合强度73.3MPa低于涂层自身的结合强度136.3MPa,厚1.0m m涂层的整体剥离倾向也更加严重,涂层的裂纹更多、破损几率也更大.涂层中的 -Fe和 -Fe组织在微动应力作用下易于发生较多滑移,从而导致塑性变形和加工硬化.检测结果表明,厚1.0m m的涂层的加工硬化更为显著,致使涂层中的空位和位错等缺陷更多,进而也促进了其表面组织的氧化,加剧了表面破损和开裂的倾向.车轴表面的热喷涂层在轮对运行中可抑制轴表面微动应力的作用,避免微动疲劳过早发生[4].我们的试验结果表明,厚0.5mm的热喷涂层能够有效地实现对轴的保护.若不考虑微动应力的作用,仅从轴的疲劳角度而言,热喷涂会降低轴的疲劳强度.而厚1.0mm的涂层修复后的轴的疲劳强度更低,这可能同热喷涂过程中形成的轴表面应力分布(热喷涂会在轴表面产生残余拉应力)和表面状况有关.另外,修复涂层愈厚,轴的有效直径就愈小,愈不利于保持轴的疲劳性能.综合而言,厚0.5m m的修复涂层比厚1.0mm的涂层更有利于保持车轴原有的高疲劳强度,从而更好地防止微动疲劳.3 结论a. 厚0.5m m的Cr-Ni热喷涂层有利于防止车轴产生的微动疲劳,延长车轴的使用寿命;而厚1.0mm的Cr-Ni热喷涂层不利于保持车轴的疲劳性能.b. 同厚0.5mm的涂层相比,厚1.0mm的涂层在微动应力作用下更易产生塑性变形,形成较厚的加工硬化层,相应的氧化和破损也更为严重.c. 厚1.0mm的涂层的组织缺陷较多,在相同载荷作用下,涂层磨损表面的裂纹亦较多,涂层与轴表面存在局部剥离倾向;因此,采用Cr-N i热喷涂层对受损车轴进行修复时,应严格控制涂层的厚度.参考文献:[1] Zhao S Z(赵锁忠),W an g D Z(王大智).Fretting corrosion ofaxle and coun ter meas ures(车轴的微动磨蚀与对策)[J].Rolling Vehicle(铁道车辆),1995,33(7):10-13.[2] He Qing fu,Liu W ei.An alys is of chemical valence of theelements of th e oxidized su rface layer of a th erm ally sprayedNi-Cr coating under fretting[J].S urface an d CoatingsTechnology,1998,106:91-93.[3] Overz M P,Harris S J,W aterhouse R B.Developm ent ofcoating s b as ed on Fe-Cr-Ni-Al for res isting fretting wear inth e temperature range20-700℃[J].Wear,1981-1982,74:315-338.[4] Liu Wei(刘伟),He Q F(何庆复),C hen S Z(陈善忠).Study on the effect of thermally sprayed coating on resistingfretting fatigue of axle(热喷涂层抗车轴微动疲劳的研究)[J].437第6期刘 伟等: 车轴修复用热喷涂层厚度对微动损伤行为的影响T ribology(摩擦学学报),1999,19(3):234-238.[5] Waterh ou se R B.Fretting wear and fretting fatigue(微动磨损与微动疲劳)[M].T ran slated by Zhou Z R(周仲荣译).Chen gdu(成都):Southw est Jiaotong U nivers ity Pres s(西南交通大学出版社),1999.Fretting Damage Behavior of Rail Vehicle Axle Repaired withThermally Sprayed Cr-Ni CoatingsLIU Wei1,HE Qing-fu1,CHEN Shan-zhong2(1.College of M echanical&E lectr ical Eng ineer ing,N or ther n J iaotong Univ er sity,Beij ing100044,China;2.Qishu y an L ocomotive&Rolling S tock T echnology I nstitute,Changz hou213011,China)Abstract:T he specimens of tw ice-repaired ax les w ith diameter of about25%of that of the real lo com otive axles w ere prepared.T he fretting fatigue tests of the r esulting specimens were carried out on a w heel-ax le-sim ulating test r ig under lo ading conditio n until the fatigue cr acks were o bser ved o n the ax les.T hen the specimens w er e dissembled and coated with thermally sprayed Ni-Cr alloy coating s o f0.5mm and1.0mm thick to r ecover their primary sizes,after cutting away the fatigue cracks.The fr etting tests of the co ated specimens were carried out on the same test rig under a lo ad of160M Pa for a cycle of1.2×107.T he fretted surface m orpho logy and the appearance of the fatigue fr actur e w er e observed w ith a scanning electr on microscope,and the co mpo sition of the ox ide o n fretted surface determ ined w ith an X-ray pho toelectr on spectroscope.T he r esults sho wed that fretting led to the formation of a thicker w o rk hardened layer and ox ides thereon.The Ni-Cr alloy coating of1.0mm thick on the ax le sur face w as liable to g ener ating mo re cr acks and to detaching,w hile that o f0.5mm thick w as m ore beneficial in pro tecting the ax le fr om fretting fatigue.Key words:vehicle ax le reco ver ing;ther mally spraying;Ni-Cr coating;fretting damage behav io rAuthor:LIU Wei,fem ale,born in1963,Associate Professor,E-m ail:w eiliu@.438摩 擦 学 学 报第22卷。
热喷涂技术在零件修复中的应用研究
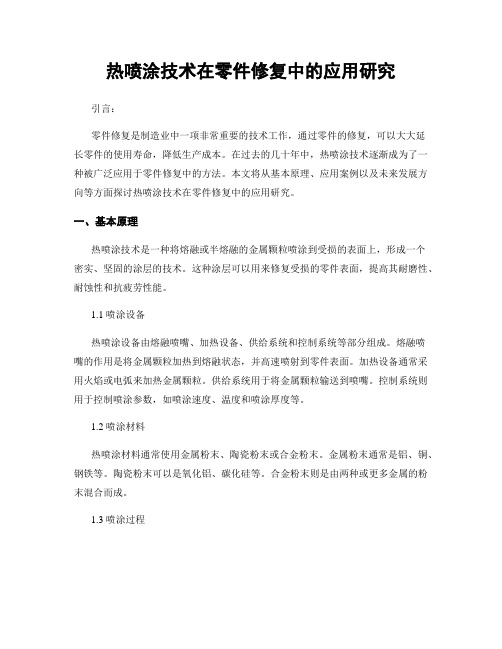
热喷涂技术在零件修复中的应用研究引言:零件修复是制造业中一项非常重要的技术工作,通过零件的修复,可以大大延长零件的使用寿命,降低生产成本。
在过去的几十年中,热喷涂技术逐渐成为了一种被广泛应用于零件修复中的方法。
本文将从基本原理、应用案例以及未来发展方向等方面探讨热喷涂技术在零件修复中的应用研究。
一、基本原理热喷涂技术是一种将熔融或半熔融的金属颗粒喷涂到受损的表面上,形成一个密实、坚固的涂层的技术。
这种涂层可以用来修复受损的零件表面,提高其耐磨性、耐蚀性和抗疲劳性能。
1.1 喷涂设备热喷涂设备由熔融喷嘴、加热设备、供给系统和控制系统等部分组成。
熔融喷嘴的作用是将金属颗粒加热到熔融状态,并高速喷射到零件表面。
加热设备通常采用火焰或电弧来加热金属颗粒。
供给系统用于将金属颗粒输送到喷嘴。
控制系统则用于控制喷涂参数,如喷涂速度、温度和喷涂厚度等。
1.2 喷涂材料热喷涂材料通常使用金属粉末、陶瓷粉末或合金粉末。
金属粉末通常是铝、铜、钢铁等。
陶瓷粉末可以是氧化铝、碳化硅等。
合金粉末则是由两种或更多金属的粉末混合而成。
1.3 喷涂过程热喷涂的过程包括金属颗粒的加热、喷嘴的喷射、颗粒的冷凝和涂层的形成。
首先,金属颗粒通过加热设备被加热到熔点以上,然后喷射到零件表面。
颗粒冷却时会与空气中的氧发生反应形成氧化物,从而形成一层坚固的涂层。
二、应用案例热喷涂技术在零件修复中有着广泛的应用,以下将列举几个典型的案例来说明其应用价值。
2.1 航空发动机叶片修复航空发动机叶片经常遭受高温和高速气流的冲击,导致叶片表面损伤严重。
热喷涂技术可以用来修复这些受损的叶片表面。
通过喷涂耐磨、耐蚀的材料,可以有效地修复叶片表面,延长其使用寿命,提高发动机的性能。
2.2 汽车发动机缸套修复发动机缸套是发动机中非常重要的部件,承受着高温和高压的工作环境。
由于使用寿命的原因,缸套表面经常会受到磨损和腐蚀。
利用热喷涂技术,可以在缸套表面喷涂耐磨、耐蚀的材料,使其表面恢复到理想的状态,提高发动机的工作效率。
飞机轮毂轴承孔修理中热喷涂技术的运用论文

飞机轮毂轴承孔修理中热喷涂技术的运用论文引言热喷涂是利用热源将喷涂材料加热到熔化或半熔化状态,依靠热源自身或外加的压缩气流,将其以一定的速度喷射到经预处理的基体表面,形成具有足够结合强度和特定性能的涂层。
热喷涂涂层具有耐磨损和耐腐蚀等优良性能,并能对工件因磨损和腐蚀等引起的尺寸变化进行修复,在航空航天、机械制造、交通等领域得到了广泛应用。
飞机轮毂长时间使用后,轮毂轴承安装孔会出现腐蚀或磨损。
对于严重腐蚀和磨损,通常采用加装钢衬套来修理轮毂轴承安装孔。
每次加装钢衬套修理,需要加工去除轮毂基体上的损伤和腐蚀。
钢材料较硬,并且钢衬套外径表面若有损伤,容易损伤轮毂轴承安装孔。
轮毂轴承安装孔修理有一定的极限尺寸,加装钢衬套修理轮毂轴承安装孔会缩短半轮毂的使用寿命。
从修理飞机轮毂轴承安装孔的热喷涂涂层性能要求出发,分析可应用的热喷涂技术,介绍轮毂轴承安装孔热喷涂修理流程,分析轮毂轴承安装孔热喷涂修理的质量控制。
1飞机轮毂轴承安装孔的热喷涂涂层性能要求飞机机轮主要用于在地面支撑飞机并使飞机能够在地面滑行。
在使用过程中,机轮会承受较大的静载荷、动载荷和冲击载荷。
机轮主要是由轮毂和轮胎组成。
轮毂上安装有内、外侧轴承。
机轮通过轴承与起落架轮轴配合。
施加在飞机轮毂轴承安装孔上的热喷涂涂层会承受较大的静载荷、动载荷和冲击载荷。
飞机轮毂材料是铝合金。
热喷涂涂层与轮毂铝合金基体要有较高的结合强度,涂层应有较高的硬度,涂层应具备较好的耐磨损及耐腐蚀性能。
如霍尼韦尔公司标准施工手册规定,热喷涂涂层与轮毂铝基体的结合强度应不小于34.5MPa,涂层硬度应为70-90HRB,涂层孔隙率应不大于10%,氧化物含量应不大于40%[1].2飞机轮毂轴承安装孔修理应用的热喷涂技术飞机轮毂轴承安装孔基体材料为铝合金。
热喷涂涂层材料应与铝合金基体有较好的浸润性和兼容性。
常用的喷涂材料为镍铝合金(95%镍,5%铝)、铝硅合金(5%-12%硅)。
热喷涂修复法剖析

2020/4/27
12
机械设备维修工程学
2020/4/27
13
机械设备维修工程学
• ⑵喷涂层的性能
• ①喷涂层硬度
•
喷涂层的硬度取决于喷涂材料和喷枪规范。一般
为HB150 ~350左右。喷涂材料、喷射距离、压缩空
气压力和喷涂层厚度对涂层硬度都有影响。
• 金属喷涂层的硬度高于所用的金属丝的硬度,这是 因为金属微粒喷射到零件表面上后迅冷却而产生了淬
时,被撞扁而贴在工件表面上。此时,颗粒与工件表面之
间有如下连接过程:
2020/4/27
9
机械设备维修工程学
• (1)机械粘合 ——工件表面通常都要进行粗糙加工(例 如喷砂、拉毛等),表面上的不平凸起对涂层有一种 钩锚作用,微粒既和工件金属又和后到的微粒产生机 械结合而形成覆盖层。发生这种情况的前提是金属微 粒达到工件表面时,其温度应很高,处于塑性状态。 喷涂时微粒运动速度近似等于空气流的速度,且微粒 从喷枪口飞到工件表面的时间很短(不超过0.003s), 金属微粒不会剧烈地冷却。
需喷涂的零件表面上。这样,半塑性金属颗粒以高速
度撞击变形并填塞在粗糙的零件表面上,就逐渐地形
成覆盖层。金属丝不断地向前输送,同时不断地被熔
化,熔化的金属又不断地吹向工件表面,从而保证了
喷涂过程的连续进行。
2020/4/27
6
机械设备维修工程学
• 电弧喷涂过程由下列四个循环阶段组成:
• ①两电极接触,钢丝的尖端短路被熔化;
表面结合起来,后到的颗粒又与先到的颗粒结合,如此连
续进行,便逐形成了喷涂层,如图5-41所示。微粒在飞行
过程中,高温的液态金属与空气接触,在凝固的同时,产
轴头磨损原因及解决办法
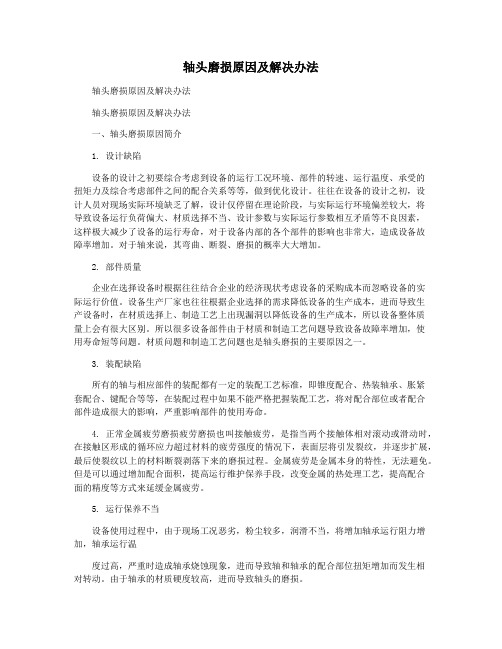
轴头磨损原因及解决办法轴头磨损原因及解决办法轴头磨损原因及解决办法一、轴头磨损原因简介1. 设计缺陷设备的设计之初要综合考虑到设备的运行工况环境、部件的转速、运行温度、承受的扭矩力及综合考虑部件之间的配合关系等等,做到优化设计。
往往在设备的设计之初,设计人员对现场实际环境缺乏了解,设计仅停留在理论阶段,与实际运行环境偏差较大,将导致设备运行负荷偏大、材质选择不当、设计参数与实际运行参数相互矛盾等不良因素,这样极大减少了设备的运行寿命,对于设备内部的各个部件的影响也非常大,造成设备故障率增加。
对于轴来说,其弯曲、断裂、磨损的概率大大增加。
2. 部件质量企业在选择设备时根据往往结合企业的经济现状考虑设备的采购成本而忽略设备的实际运行价值。
设备生产厂家也往往根据企业选择的需求降低设备的生产成本,进而导致生产设备时,在材质选择上、制造工艺上出现漏洞以降低设备的生产成本,所以设备整体质量上会有很大区别。
所以很多设备部件由于材质和制造工艺问题导致设备故障率增加,使用寿命短等问题。
材质问题和制造工艺问题也是轴头磨损的主要原因之一。
3. 装配缺陷所有的轴与相应部件的装配都有一定的装配工艺标准,即锥度配合、热装轴承、胀紧套配合、键配合等等,在装配过程中如果不能严格把握装配工艺,将对配合部位或者配合部件造成很大的影响,严重影响部件的使用寿命。
4. 正常金属疲劳磨损疲劳磨损也叫接触疲劳,是指当两个接触体相对滚动或滑动时,在接触区形成的循环应力超过材料的疲劳强度的情况下,表面层将引发裂纹,并逐步扩展,最后使裂纹以上的材料断裂剥落下来的磨损过程。
金属疲劳是金属本身的特性,无法避免。
但是可以通过增加配合面积,提高运行维护保养手段,改变金属的热处理工艺,提高配合面的精度等方式来延缓金属疲劳。
5. 运行保养不当设备使用过程中,由于现场工况恶劣,粉尘较多,润滑不当,将增加轴承运行阻力增加,轴承运行温度过高,严重时造成轴承烧蚀现象,进而导致轴和轴承的配合部位扭矩增加而发生相对转动。
热喷涂涂层工艺的耐磨性与耐蚀性改进

热喷涂涂层工艺的耐磨性与耐蚀性改进热喷涂涂层是一种常用的表面修复和改性材料技术,广泛应用于航空航天、能源、化工、机械制造等领域。
然而,由于工艺和材料的局限性,热喷涂涂层在耐磨性和耐蚀性方面存在一定的问题。
为了提高热喷涂涂层的耐磨性和耐蚀性,需要从工艺和材料两个方面入手进行改进。
首先,从工艺方面来说,热喷涂涂层的耐磨性和耐蚀性受到热喷涂工艺参数的影响。
例如,喷涂温度、喷涂速度、气体流量等参数的选择直接影响了涂层的致密性和附着力,从而影响耐磨性和耐蚀性。
因此,需要通过优化工艺参数,使涂层能够获得更高的致密性和附着力。
同时,还可以采用预处理技术来提高热喷涂涂层的耐磨性和耐蚀性。
例如,通过喷丸、化学处理和表面活性剂处理等方法,可以有效地清除表面的污染物和氧化层,提供更好的附着力和致密性。
此外,还可以采用多层涂层的方法,在基础涂层上覆盖保护涂层,进一步提高耐磨性和耐蚀性。
在材料方面,热喷涂涂层的材料选择至关重要。
常用的热喷涂涂层材料包括金属、陶瓷和聚合物等,各具特点,用途不同。
例如,金属涂层具有良好的导热性和导电性,适用于提高材料耐热性;陶瓷涂层具有优异的耐磨性和耐蚀性,适用于提高涂层的耐磨性和耐蚀性;聚合物涂层具有良好的耐化学性和耐热性,适用于提高涂层的耐蚀性和耐热性。
因此,根据具体应用需求,选择合适的热喷涂涂层材料是提高耐磨性和耐蚀性的关键。
此外,还可以采用复合涂层的方法,将不同性能的材料组合在一起,形成具有多种优点的涂层结构。
例如,可以在基础涂层上覆盖一层耐磨性较高的陶瓷涂层,形成高硬度的涂层;或者在表面涂覆一层具有耐蚀性的聚合物涂层,提高涂层的耐蚀性。
通过合理设计复合涂层结构,可以综合利用不同材料的优点,进一步提高热喷涂涂层的耐磨性和耐蚀性。
总结来说,提高热喷涂涂层的耐磨性和耐蚀性需要从工艺和材料两个方面入手。
通过优化工艺参数,采用预处理技术和合理选择涂层材料,可以提高涂层的致密性、附着力和耐磨性、耐蚀性。
热喷涂技术使曲轴“死而复生”

热喷涂技术使曲轴“死而复生”热喷涂技术能直接针对许多贵重零部件的失效原因,实行局部表面强化、修复、预保护,以达到延长使用寿命或重新恢复使用价值的目的。
石油钻机等设备中一些大功率曲轴,曲轴轴颈表面的磨损是不均匀的,主轴颈与连杆轴颈的径向磨损主要呈椭圆形,且其最大磨损部位相互对应,即各主轴颈的最大磨损处靠近连杆轴颈一侧;而连杆轴颈的最大磨损处也是靠近主轴颈一侧。
曲轴轴颈沿轴向还有锥形磨损。
油田使用的各种重型车辆、拖拉机、柴油机的曲轴等均因上述磨损而失效,但均可采用热喷涂技术进行修复。
如:可采用电弧喷涂3Cr13 涂层或等离子喷涂陶瓷涂层来修复。
这样既可显著降低成本,又能延长设备使用寿命,其是可有效解决进口设备的修复问题。
还可采用热喷涂方法恢复加工超差零部件或强化耐磨件表层。
1984年美国“技术评论”提倡旧品翻新或再生,并称为“重新制造”。
重新制造所需能源约为制造新品的20%~60%,价格只有新品的40%~60%。
许多采用热喷涂技术处理过的旧零部件,其性能要优于新品。
油田使用的各类泵的柱塞、缸套、叶轮等零件均可采用多种热喷涂方法进行修复。
如可采用超音速火焰喷涂WC-12Co 或等离子喷涂Al2O3等来修复和强化,也可采用电弧喷涂1Cr13 钢丝进行修复。
采用热喷涂技术修复后的柱塞使用寿命高于表面淬火柱塞,略低于工作表面喷焊镍基合金的柱塞。
对于一些大直径柱塞,由于变形而无法采用喷焊进行修复时,热喷涂则不失为一种无变形、低成本的最佳修复方法。
国内曾修复一个12 吨的柱塞,喷涂层重达33公斤,涂层作封孔处理后,使用性能优于新柱塞,而成本只有新柱塞的1/4。
热喷涂法修复缸体主轴承座孔

载货汽车经常满载在山区道路 行 驶 时 ,由 于 发 动 机 负 荷 大 ,工 作 时主轴瓦与主轴承座孔内表面沿 圆 周 方 向 相 对 运 动 ,导 致 轴 承 瓦 背 和 座 孔 磨 损 ,其 圆 度 、圆 柱 度 误 差 超 差 ,严 重 时 ,还 会 发 生“ 抱 轴 ”故 障 ,使 缸 体 报 废 。针 对 这 种 情 况 ,我 们对磨损量较大的轴承座孔采用 热 喷 涂 工 艺 ,通 过 加 工 使 之 恢 复 到 标 准 尺 寸 。 检 验 记 录 表 明 ,采 用 该 方法修复的缸体使用寿命可达 ’(& 万 )*,每台节约成本 " 万元。现将 该工艺规程介绍给大家,以供参 考。
汽车维修 !##$%&
!"
必须对涂层质量进行认真检验。可 用半圆形小铜锤敲击工作层表面, 如响声清脆,表明涂层与座孔表面 结 合 良 好 ;如 响 声 嘶 哑 ,表 明 涂 层 与 座 孔 表 面 结 合 不 牢 ,应 刮 除 后ቤተ መጻሕፍቲ ባይዱ重 喷 。
.%镗削座孔 ")仍 采 用 清 除 氧 化 层 时 选 好 的 座孔作定位基准。 !)对 中 镗 杆 :在 镗 杆 上 安 装 专 用划针,使镗杆在定位基准孔内转 动 ,划 针 在 座 孔 内 壁 的 间 隙 应 一 致 , 且 镗 杆 能 在 支 架 孔 内 灵 活 转 动 ,然 后紧固可调支架。 $)镗 削 座 孔 :粗 镗 时 ,切 削 速 度 应 为 "/# (!/#: 9 *;<, 进 刀 量 为 #%#/(#%"#**, 吃 刀 深 度 应 选 择 适 当 ,避 免 引 起 镗 杆 振 动 。 精 镗 时 ,切 削 速 度 可 相 应 提 高 ,进 刀 量 可 减 小 , 直到座孔内径达到标准尺寸为止。 精镗后,表面粗糙度 =8 的最大允许 值为 $%!(’%$! *。 .)镗 削 完 毕 ,用 手 提 式 微 型 软 轴砂轮将油道孔边缘磨成一定倒角 并去除毛刺,以减少该处的应力集 中 ,避 免 涂 层 剥 落 。 另 外 ,在 装 复 发 动机前,必须再次清除座孔表面和 油道内的金属屑及杂物,并对座孔 涂层进行浸油处理,使涂层表面微 孔晶粒间渗足润滑油,形成良好的 润滑油膜。!
机械设备维修中热喷涂技术的应用

机械设备维修中热喷涂技术的应用摘要:机械设备在工作的过程中,由于工作环境的恶劣,长时间的使用会产生一定的磨损和腐蚀问题,缩短其使用寿命,造成资源的不必要浪费,本文正是基于这一背景,对机械设备维修中最常见的技术——热喷涂技术进行了分析,从其基本原理、分类、特点和作用过程入手,确定热喷涂技术的可行性,然后具体阐述了热喷涂技术在机械设备维修中的应用,热喷涂技术在机械设备维修中应用前景广阔,希望对相关工作提高帮助。
关键词:机械设备维修;热喷涂技术;应用前言:随着机械设备的利用率增加,资源利用的不断深入,社会的负担越来越大,在机械设备应用的过程中,大都是高温、高压、高腐蚀的环境,对机械设备的磨损和腐蚀十分严重,已经造成了大量的资源浪费,而对机械设备的维修工作势在必行,同时提高维修的成效也迫在眉睫,热喷涂技术在机械设备维修上能有效的解决这一问题,取得了较好的效果。
一、热喷涂技术简介(一)热喷涂技术的原理热喷涂技术是机械设备维修中常用的技术,其基本原理为:利用高温将喷涂材料加热到熔融状态,然后借助外力推动将熔融状喷涂材料喷射到机械设备的表面,通过机械咬合作用形成一层致密的保护层,完成对损坏的机械设备的维修工作。
(二)热喷涂技术的分类1.火焰喷涂火焰喷涂是利用气体燃烧产生的高温融化喷涂材料,从喷枪中喷出至机械设备上,形成保护层。
火焰喷涂在操作中工艺简单,不需要复杂的仪器,而且对环境的要求不高,不过在喷涂效果上没有其他热喷涂技术有效,例如塑料类涂层。
2.电弧喷涂电弧喷涂是将金属材料作为两个电极,然后通电高温在点击两端产生电弧,能融化喷涂材料,将喷涂材料喷涂到机械设备表面。
电弧喷涂技术在应用时工艺简单,对设备的要求低,成本较小,而且喷涂效果较好,不过在喷涂材料的选择上有一定的局限性,需要采用丝状材料。
3.等离子喷涂等离子喷涂通过喷嘴和电极之间的电弧将喷涂材料变成等离子状态,然后喷出离子焰,喷涂到机械设备表面,如图1所示。
轴瓦磨损热喷涂修复

轴瓦磨损热喷涂修复
轴瓦是滑动轴承和轴颈接触的部分,形状为瓦状的半圆柱面,非常光滑,是支承轴转动的重要机械零件,轴瓦的硬度大大低于轴颈的硬度,在其工作的过程中,由于轴瓦承受着轴的冲击和压力,而且瓦面与轴颈产生相对的滑动,因此导致了轴瓦的磨损。
严重时,轴瓦与轴径发生咬合现象,在轴瓦面拉出深的沟槽,影响了传动的平稳性和准确性。
对于一些局部被磨损的轴瓦,长青金属采用热喷涂法进行修复,热喷涂修复轴瓦,不仅施工方便,实用性强,而且可以节约修复成本。
一般热喷涂修复轴瓦分为以下八个工艺流程,包括工件的清洗除油、表面的制备、非工作面的保护、预热、喷涂合金、冷却、修整和检验。
本信息由长青金属张忠霞搜集整理。
应用热喷涂技术修复发动机曲轴
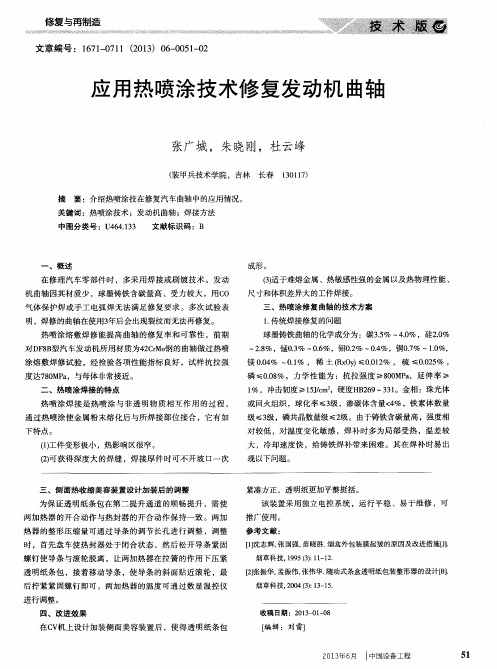
推广使用 。
参考文献 :
[ 1 ] 沈 志辉, 张国强, 苗晓胜 . 烟盒外包装膜起 皱的原 因及改进措施 【 J 】 . 烟草科技, 1 9 9 5 ( 3 ) : 1 1 - 1 2 . [ 2 ] 张振华, 孟振伟 , 张伟华. 随动式条盒透明纸包装整形器 的设计 [ B ] . 烟草科技 , 2 0 0 4 ( 3 ) : 1 3 — 1 5 .
Байду номын сангаас
( 1 ) q - 件变形极小 ,热影 响区很 窄。 ( 2 ) 可 获得深 度大 的焊缝 ,焊接厚 件 时可不 开坡 口一次
三 、侧面 热收缩 美容装置 设计加 装后 的调整
紧凑方正 ,透 明纸更加平整挺括。
该装 置采用独立 电控 系统 ,运 行平稳 、易 于维修 ,可
为保 证透 明纸条包 在第二 提升 通道 的顺 畅提升 ,需使 两加 热器 的开合动 作与热 封器 的开合动 作保持 一致 。两加 热器 的整形 压缩量 可通过 导条 的调节长 孔进行 调整 ,调整 时 ,首先盘 车使热 封器处 于闭合状 态 ,然后松 开导 条紧 固 螺钉使 导条 与滚轮 脱离 ,让两加热 器在 拉簧 的作用 下压 紧 透 明纸条包 ,接着 移动导 条 ,使 导条 的斜 面贴 近滚 轮 ,最 后拧 紧紧 固螺钉 即可 。两 加热器 的温度 可通过 数显 温控仪
收稿 日期 :2 0 1 3 — 0 1 — 0 8
在C V 机上设 计加装侧 面美容装 置后 ,使得透 明纸条包
【 编辑 :刘雷]
2 0 1 3 年6 月 l 中国设备工程
5 1
i 镰≮
0
一
修 复 与 再 制 造
热喷涂技术在机械制造中的应用研究
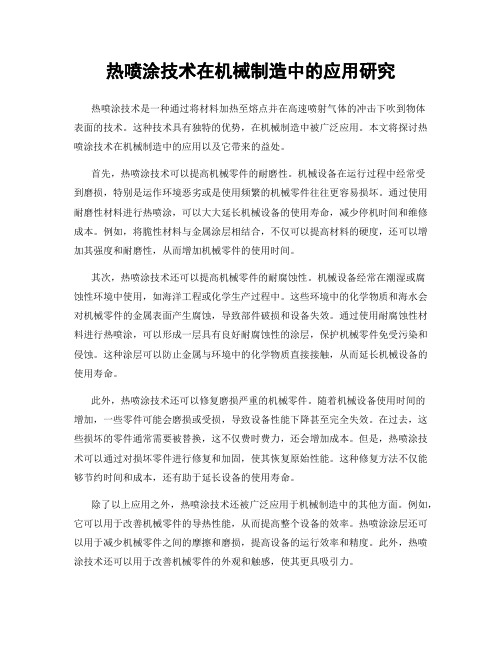
热喷涂技术在机械制造中的应用研究热喷涂技术是一种通过将材料加热至熔点并在高速喷射气体的冲击下吹到物体表面的技术。
这种技术具有独特的优势,在机械制造中被广泛应用。
本文将探讨热喷涂技术在机械制造中的应用以及它带来的益处。
首先,热喷涂技术可以提高机械零件的耐磨性。
机械设备在运行过程中经常受到磨损,特别是运作环境恶劣或是使用频繁的机械零件往往更容易损坏。
通过使用耐磨性材料进行热喷涂,可以大大延长机械设备的使用寿命,减少停机时间和维修成本。
例如,将脆性材料与金属涂层相结合,不仅可以提高材料的硬度,还可以增加其强度和耐磨性,从而增加机械零件的使用时间。
其次,热喷涂技术还可以提高机械零件的耐腐蚀性。
机械设备经常在潮湿或腐蚀性环境中使用,如海洋工程或化学生产过程中。
这些环境中的化学物质和海水会对机械零件的金属表面产生腐蚀,导致部件破损和设备失效。
通过使用耐腐蚀性材料进行热喷涂,可以形成一层具有良好耐腐蚀性的涂层,保护机械零件免受污染和侵蚀。
这种涂层可以防止金属与环境中的化学物质直接接触,从而延长机械设备的使用寿命。
此外,热喷涂技术还可以修复磨损严重的机械零件。
随着机械设备使用时间的增加,一些零件可能会磨损或受损,导致设备性能下降甚至完全失效。
在过去,这些损坏的零件通常需要被替换,这不仅费时费力,还会增加成本。
但是,热喷涂技术可以通过对损坏零件进行修复和加固,使其恢复原始性能。
这种修复方法不仅能够节约时间和成本,还有助于延长设备的使用寿命。
除了以上应用之外,热喷涂技术还被广泛应用于机械制造中的其他方面。
例如,它可以用于改善机械零件的导热性能,从而提高整个设备的效率。
热喷涂涂层还可以用于减少机械零件之间的摩擦和磨损,提高设备的运行效率和精度。
此外,热喷涂技术还可以用于改善机械零件的外观和触感,使其更具吸引力。
需要指出的是,尽管热喷涂技术在机械制造中具有许多优势和应用,但它并非没有局限性。
热喷涂涂层的结合强度可能不够高,容易出现脱落现象。
喷涂技术在修复发动机转轴磨损方面的应用

・
电火 花 法 对 车 削 处 进 行 拉 毛 粗 化 表 面 , 加 吸 附 面 增
积。
发 电机转 子 回水箱 轴颈 密封 处轴套 周 围磨损 ,
①
收稿 日期 : o 一o —1 2 2 3 4 0
作者 筒介 : 文彬 (98 , , 范 16 一)男 毕业 于武 汉大学 , 程师 。 工
摘 要 : 绍 了喷 涂技 术 在修 复发 电机 转轴 磨损 、 治转 子 回水 箱漏 水 方 面的经 验 。 介 根 关键 词 : 喷涂 技术 ; 电机 ; 子 ; 损 ; 漏 ; 复 发 转 磨 泄 修
中 图分 类 号 : TM3 l l 文献 标 识码 : B
Ab ta t Th a e to c st e e p re c h t t e s r y n e h oo y m e d t e fa f e e a o o o ,c r h e k s r c : e p p ri r du e h x e i n e t a h p a i g t c n lg n h r y o n r t rr t r u e t e l n g a o e e t rr t r 。 fg n ro e u n b x. Ke r s p a i g t c n l g y wo d :s r y n e h oo y;g n r t r o o ;{a e e ao ;r t r r y;l k;r p i a e e ar
达 3年 的 运 行 观 察 , 果 证 明 这 种 方 法 在 发 电 机 转 结
长 , 削 宽 度 向 两 侧 延 长 3mm, 削 深 度 为 7mm。 车 切
・ ・
子 修 补 方 面 是 成 功 的 。笔 者 希 望 借 此 文 将 我 们 的 体
大轴磨损在线修复案例(轴颈损伤修复、轴颈修复)

大轴磨损在线修复案例(轴颈损伤修复、轴颈修复)随着生产设备逐渐向大型化、集约化方向发展,大型传动部位越来越多,由于大型传动部位往往传递动力非常大,长期工作的条件下经常导致传动部位磨损。
传统的修复方法有堆焊、热喷涂、电刷渡等,但均存在一定弊端:补焊高温产生的热应力无法完全消除,易造成材质损伤,导致部件出现弯曲或断裂;而热喷涂、电刷镀受涂层厚度限制,容易剥落,且以上方法都是用金属修复金属,无法改变“硬对硬”的配合关系,常常导致修复失效。
对于上述修复技术,在欧美日韩企业已不太常见,发达国家一般采用的是高分子复合材料技术和纳米技术,高分子技术可以现场操作有效提升了维修效率,且降低了维修费用和维修强度,其中应用最为广泛的是福世蓝技术体系。
相比传统技术,高分子复合材料既具有金属所要求的强度和硬度,又具有金属所不具备的退让性(变量关系),通过“模具修复”、“部件对应关系”、“机械加工”等工艺,可以最大限度确保修复部位和配合部件的尺寸配合;同时,利用复合材料本身所具有的抗压、抗弯曲、延展率等综合优势,可以有效地吸收外力的冲击,极大化解和抵消轴承对轴的径向冲击力,并避免了间隙出现的可能性,也就避免了设备因间隙增大而造成的二次磨损。
以下是福世蓝技术在各行业大型传动部位磨损的应用案例,仅供参考。
案例一:烧结机胀套配合部件磨损2010年12月,某钢铁企业烧结厂的烧结机胀套配合部件出现磨损,该胀套为烧结机主轴传动胀套,用于连接烧结机传动大齿轮和主轴,转速小于1转/分,轴径280mm,齿轮孔内径355mm,电机功率2×7.5KW,速比1000或500,电机为4极或6极,与胀套配合部位轴径约50%的面出现磨损,能够定位,磨损最深处1.5mm,呈沟状磨损。
为了保证修复部位的使用效果,我们将本次修复分为三个步骤,首先对轴径磨损部位、齿轮内孔进行表面处理,做到干净、干燥、粗糙,并露出金属原色,轴径表面涂抹高分子金属修复材料,用直尺刮平,固化;齿轮内孔表面处理,并涂抹高分子金属修复材料,将磨损痕迹磨平,固化;材料加热固化后,将材料表面打磨平整,用胀套内圈作为模具将轴径表面修复出配合尺寸,并打磨角边,然后测量修复后的尺寸;最后将胀套内外圈涂抹高分子金属修复材料,进行总装配。
车轴修复用热喷涂层厚度对微动损伤行为的影响

车轴修复用热喷涂层厚度对微动损伤行为的影响摘要:本文研究了在车轴修复过程中使用热喷涂层的厚度对微动损伤行为的影响。
在实验中,使用了不同厚度的热喷涂层进行修复,通过微动试验研究了不同厚度的热喷涂层对车轴微动损伤行为的影响。
研究结果表明,热喷涂层的厚度对车轴的微动损伤行为有着重要的影响,较厚的热喷涂层可以有效地降低车轴微动损伤,并提高车轴的寿命。
关键词:车轴修复;热喷涂层;微动损伤;寿命Introduction车轴在长时间使用中会产生一定程度的损伤,特别是微动损伤。
为了延长车轴的使用寿命,常常需要进行修复。
而在车轴修复过程中,常常采用热喷涂层的方法,来修补车轴表面的缺陷。
热喷涂层不仅能够提高车轴的表面硬度和抗磨性,还能够填充车轴表面的缺陷,防止微动损伤的发生。
然而,热喷涂层的厚度对微动损伤行为的影响还没有得到深入的研究。
本文旨在探究热喷涂层的厚度对车轴微动损伤行为的影响,为车轴修复提供参考依据。
Experimental Procedure本实验使用了不同厚度的热喷涂层进行车轴修复,涂层材料为NiCr8020。
在实验中,首先将车轴表面打磨,并清洗干净。
然后使用热喷涂机进行喷涂,分为三组实验,分别是3mm,5mm和7mm厚度的热喷涂层。
实验中采用了微动试验,用于研究不同厚度的热喷涂层对车轴的微动损伤行为的影响。
微动试验中,将车轴用夹具固定,另一端装有负荷,将车轴进行周期性的微动运动,通过测量微动位移和载荷大小,研究车轴的微动损伤情况。
实验中采用了三个不同厚度热喷涂层的车轴进行对比实验,并对实验数据进行统计和分析。
Results and Discussions实验结果表明,热喷涂层的厚度对车轴微动损伤行为有着重要的影响。
在微动试验中,较厚的热喷涂层能够有效地抵抗车轴的微动损伤,而较薄的热喷涂层则会导致车轴微动损伤的加剧。
实验结果显示,较薄的热喷涂层容易产生裂纹,并形成更严重的微动损伤。
而较厚的热喷涂层则能够有效地防止裂纹的产生,并保护车轴表面免受微动损伤的侵害。
- 1、下载文档前请自行甄别文档内容的完整性,平台不提供额外的编辑、内容补充、找答案等附加服务。
- 2、"仅部分预览"的文档,不可在线预览部分如存在完整性等问题,可反馈申请退款(可完整预览的文档不适用该条件!)。
- 3、如文档侵犯您的权益,请联系客服反馈,我们会尽快为您处理(人工客服工作时间:9:00-18:30)。
热喷涂技术修复轴头磨损的局限性
关键词:轴头磨损,热喷涂技术,碳纳米材料技术,修复案例,索雷工业
轴头磨损问题在企业设备运行过程中时有发生,其影响或大或小。
传统解决方法,如补焊、刷镀、喷涂、镶嵌非标套等。
下面,小编重点介绍一下轴头磨损热喷涂修复工艺的利与弊以及索雷工业新型碳纳米材料在轴头磨损方面的应用。
如下:
轴头磨损热喷涂修复技术优点
1.硬度高、抗磨损、耐高温;
2.涂层沉积效率较高,特别适合沉积薄膜涂层。
轴头磨损热喷涂修复技术局限性
1.结合强度不大高,涂层耐冲击和重载性能较差;
2.涂层含有不同程度的孔隙,耐腐蚀、抗氧化等性能差;
3.喷涂小件时,涂层材料的利用率低,经济性差;
4.劳动条件差,噪音、粉尘、有毒金属蒸汽、热和弧光辐射问题严重。
索雷碳纳米聚合物材料技术可替代热喷涂工艺
索雷碳纳米聚合物材料技术是由碳纳米无机材料等高性能材料通过聚合技术生成的双组份复合材料。
该材料最大优点是抗冲击、耐腐蚀、抗磨损、抗压强度高、粘着力强、机加工性能优等特点,可粘着于各种金属、混凝土、玻璃、PVC、橡胶等材料。
目前,该技术自引进以来已经成功服务于水泥、钢铁、造纸、化工、电力、船舶、食品等行业领域的众多工业企业。
下面小编与大家共同分享几个实际案例
1.全球最大水泥集团拉法基水泥国内某分公司HFCG160-140辊压机轴头磨损;轴颈750-
790mm,轴颈1:12锥、磨损尺寸单边2-3mm,磨损宽度487mm、轴承型号232/750CAKF3/C3W33。
采用索雷碳纳米聚合物材料SD7101H现场12小时成功修复。
2.某大型钢铁集团80T转炉主轴因轴承支架损坏造成轴承位出现严重磨损,轴颈900mm;磨损宽度450mm;轴承型号230/900MBD/W33;磨损深处超过7mm;局部坑洞达到10mm;采用索雷碳纳米聚合物材料SD7104现场8小时成功修复。
3.某集团企业造纸分公司2640纸机检修期间发现17条烘缸轴头磨损。
轴承位直径170mm;磨损宽度100mm;磨损直径1-10mm不等;正常工作温度120℃左右。
类似问题企业曾采用加工非标套方法,但由于效果不理想加上此次数量较大,企业经多方咨询比较最终采用索雷SD7104材料现场成功修复。