2-降低棒材轧辊烧辊频次--轧钢准备作业区(高秋喜)
QC小组成果_轧辊消耗要点

3、找出不合理配辊图图纸,进行修正或重新绘制。
4、将重新绘制的图纸与加工人员一起讨论修正,最终形成新的配辊图集。
2
2、人员技术责任心不强,在轧辊加工和预装及调整方面造成了轧辊的一些不必要浪费和损失
加强检查力度。
利用技术课堂、分析会议等时机,分期分岗位对工作人员进行技术指导和岗位责任意识教育。
否
12、车床设备加工精度低
加工班部分车床使用年限较久,车床的数控水平较低,造成轧辊加工过程中的精度控制不好,孔型尺寸与设计尺寸之间存在较大误差,使得连轧关系调整存在困难。
是
小组对要因逐一进行了确认,找出了7主要要因,并采取了相应对策。
制定对策
序号
要因
对策
目标
措施
完成
时间
负责人
1
1、配辊图图纸不合理
(1)技改前旧图纸与新工艺不合
避免轧机轴承缺油状况,解决8V立轧机常出现轴承烧损问题。
1、厂里成立专门的攻关队对立轧机轴承保护进行攻关研究。
2、建立轧机预装台帐与大修记录,保证预装质量。
7
7、车床加工精度低、车刀硬度不足耐磨性差
引进新车床,制作新的样板,考虑使用新型轧辊加工刀具。
提高孔型加工尺寸精度。
1、购置新的车床,用来车加工大规格轧辊。
2008年下半年以及2010年1月,我厂连续进行两次技改,完成了生产线由半连轧向全连轧的转变,实现了轧制150方并兼容200方的轧制工艺布局,增加了轧制线的适应性。年设计产能由30万吨增加到60万吨,产能扩大一倍,随着我厂产量的不断提高,轧机架次的增加,轧辊的数量、轧辊的总消耗量也随之大幅增加,轧辊消耗成为考核轧钢生产的一个重要技术经济指标,通过与外部优秀同行的辊耗指标进行对比,发现我厂的辊耗偏高,分析原因主要有:
提高冷轧辊的使用率

提高冷轧辊的使用效率摘要:本文介绍了冷轧薄板厂使轧辊的主要失效形式,分析了轧辊的断裂和裂纹产生原因,提出了具体改进措施。
关键词:轧辊失效硬度1 前言随着市场的发展,客户对冷轧薄板的质量要求不断提高,生产厂家必须适应市场的需求,生产更高质量的产品以满足用户的需要。
在轧机所有备件中,轧辊是非常重要的备件。
轧辊在工作中要承受高的轧制力、冲击载荷、疲劳和磨损等,因此冷轧辊的消耗非常大。
统计资料表明,在冷轧生产过程中冷轧辊的消耗在生产成本中所占的比例达25%左右。
冷轧薄板厂要想取得更好的经济效益, 一方面要生产适销对路的高附加值产品,另一方面要降低生产成本。
因此,提高轧辊的使用效率是取得良好经济效益的重要手段之一,也是本文阐述的主要内容。
2 轧辊磨削设备及轧制产品2.1 磨削设备鄂钢采用MK8463/5000-H数控轧辊磨床用于加工冷轧板带生产线中的工作辊、支承辊修磨加工。
机床可磨削圆柱形、具有中凸(凹)要求的任意曲线的辊面以及圆锥形的辊面等。
可磨削正弦及抛物面曲线辊面、辊面端部倒角。
机床总体布局如图1:图 12.1.1 机床主要技术规格参数见表1表1最大磨削直径Ф630 mm最小磨削直径(在最大砂轮情况下)Ф100 mm顶尖距5000 mm工件最大重量6000kg中凸(凹)量(半径方向) 1.5 mm中心架支承直径范围根据工件要求定头架顶尖移动量150 mm尾架顶尖移动量500 mmZ轴—拖板纵向移动速度10~5000 mm/minX轴—砂轮架横向进给速度1~2000 mm/minX1轴—测量臂调整速度0~1000 mm/min数控最小分辨率(U轴)0.00001mm数控最小分辨率(U1轴)0.0001mm数控最小分辨率(X1轴)0.0001mm数控最小分辨率(X轴)0.0001mm数控最小分辨率(Z轴)0.0005mm工件转速(无级) 8~80 r/min砂轮规格Ф750×100×Ф305 mm砂轮最大线速度(恒线速) 50m/s冷却液箱流量300L/min电机总功率约120kW头架电机(西门子)22kW砂轮架电机(西门子)30kW机床总重量55t2.1.2机床工作精度标准1.圆柱面磨削见表2表2圆度≤0.002mm辊形误差≤0.002mm表面粗糙度≤Ra0.32μm圆度≤0.002mm纵截面上直径一致性≤0.002/1000 mm表面粗糙度≤Ra0.2μm2.中凸(凹)面磨削(半径上的中凸(凹)量为0.1mm。
轧钢厂高棒轧钢工岗位安全操作规程
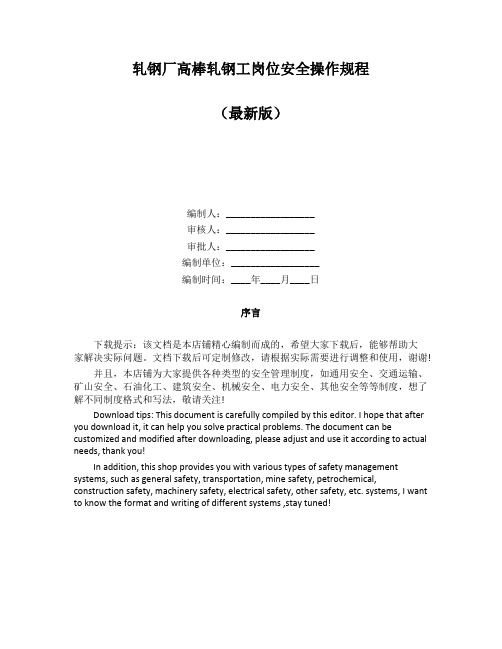
轧钢厂高棒轧钢工岗位安全操作规程(最新版)编制人:__________________审核人:__________________审批人:__________________编制单位:__________________编制时间:____年____月____日序言下载提示:该文档是本店铺精心编制而成的,希望大家下载后,能够帮助大家解决实际问题。
文档下载后可定制修改,请根据实际需要进行调整和使用,谢谢!并且,本店铺为大家提供各种类型的安全管理制度,如通用安全、交通运输、矿山安全、石油化工、建筑安全、机械安全、电力安全、其他安全等等制度,想了解不同制度格式和写法,敬请关注!Download tips: This document is carefully compiled by this editor. I hope that after you download it, it can help you solve practical problems. The document can be customized and modified after downloading, please adjust and use it according to actual needs, thank you!In addition, this shop provides you with various types of safety management systems, such as general safety, transportation, mine safety, petrochemical, construction safety, machinery safety, electrical safety, other safety, etc. systems, I want to know the format and writing of different systems ,stay tuned!轧钢厂高棒轧钢工岗位安全操作规程1.认真执行公司的环境/职业健康安全标准化方针,掌握并执行《高棒工艺技术规程》的相关内容;2.作业前应对使用工具进行检查,防止打滑造成摔伤;禁止戴手套使用大锤;3.执行电、氧焊操作时必须佩戴电焊手套、防护镜等;4.在换辊、换槽、换导卫时必须严格执行锁定程序,行车配合作业时应有专人指挥;5.任何计划检修或临时检修时必须与维修协调锁定好一次电源;6.使用手提砂轮机时必须佩戴防护镜,禁止在轧机旋入方向磨槽. 在线检查或调整进口导卫时严禁戴手套;7.开机之前要鸣笛,确保轧线人员处于安全区域后方可过钢(短笛为提示,长笛为开机);8.测试辊缝的铁丝只能是一端“7”形,另一端为椭圆形;测试接手端辊缝时必须站在轧辊旋出方向;9.禁止任何时刻跨域轧机,必须从安全桥上通过;10.在试轧小样时,脚下要站稳,身体不能向轧机方向倾斜;11.调整料型时应密切注意轧件走向,特别是轧件头部应主动避开,防止跑钢伤人;12.处理冷却水管时必须在停机状态下进行;13.进入轧机处理事故之前,必须和CS1联系确认后,将控制开关由集中拨至“关断”位置并锁定方可进行;14.处理事故时应待轧机停稳后进行,并执行锁定程序;15.检查飞剪或处理飞剪事故时,必须将飞剪机旁操作箱控制开关拨至”关断”后并锁定方可进行;16.检修或临时处理故障时,必须确认相关能源已经被安全锁定后方可作业;17.执行《轧钢厂员工通用安全操作规程》。
棒材厂低配室辊道电气系统控制与改进

棒材厂低配室辊道电气系统控制与改进
付朝高
【期刊名称】《江西冶金》
【年(卷),期】2004(024)006
【摘要】介绍了棒材厂低配室辊道电气设备的控制运行情况,通过设计切换备用装置,提高了设备的作业率.
【总页数】3页(P7-8,40)
【作者】付朝高
【作者单位】南昌钢铁有限责任公司,江西,南昌,330012
【正文语种】中文
【中图分类】TG333.11
【相关文献】
1.棒材冷床对齐辊道槽形的改进 [J], 郜莉;韩芸;兰小青
2.棒材厂冷床输入辊道装置改进 [J], 赵解来;孙一峰;扶志刚;喻颖
3.棒材厂二作业区中轧机前输送辊道的改造 [J], 王春林;余富春
4.棒材冷剪后辊道和移送链之间的移送设备的改进 [J], 田宏星
5.棒材冷床对齐辊道的改进与应用 [J], 郜莉; 韩芸; 兰小青
因版权原因,仅展示原文概要,查看原文内容请购买。
降低二十辊森吉米尔轧机轧钢油耗的探索
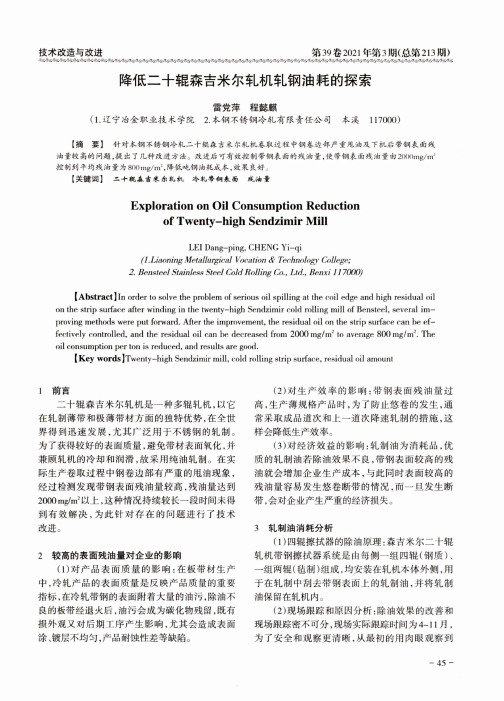
中 ,冷轧产品的表面质量是反映产品质量的重要 指 标 ,在冷轧带钢的表面附着大量的油污,除油不 良 的 板 带 经 退 火 后 ,油 污 会 成 为 碳 化 物 残 留 ,既有 损 外 观 又 对 后 期 工 序 产 生 影 响 ,尤其会造成表面 涂 、镀层不均匀,产品耐蚀性差等缺陷。
原 有 的 功 能 ,于是挑选了备用擦拭器中相对变形 设 定 具 体 还 要 操 作 人 员 根 据 除 油 的 效 果 换 ,安装时保证与擦拭器辊之 调 。压 力 会 有 一 个 细 微 的 调 整 范 围 ,在一定的范
间的松紧度。
围内正常都可保证良好的除油效果。
设备问题对除油的干扰。
度 会 造 成 带 钢 中 间 位 置 除 油 效 果 差 ,凸度增大会
(2)
新增压缩空气管路:为了保证空气吹扫系使 带 钢 边 部 的 除 油 效 果 变 差 ,说明凸度和压力之
统 介 质 的 供 应 ,在乳机传动侧新增了提供压缩空 间 存 在 一 定 的 平 衡 关 系 ,而不是压力越大除油效
回装。
—46 —
技术改造与改进
第 39卷 2021年第3期(总第213期〉
图 3 带 钢 边 部 会 有 3~8mm宽的纵向油条
5 实施后的效果 5.1 直观效果对比
从 目 前 现 场 带 钢 残 油 的 直 观 表 现 来 看 ,带钢 表 面 残 油 量 降 低 明 显 ,边 部 甩 油 问 题 也 基 本 解 决 。 从 近 三 个 月 的 残 油 检 测 结 果 上 看 ,残油数据趋于 稳 定 状 态 ,平 均 残 油 量 为 800mg/m 2。调整前后效 果见图4(a)~(b)。
沙钢5000mm宽厚板轧机轧辊降耗的改进措施
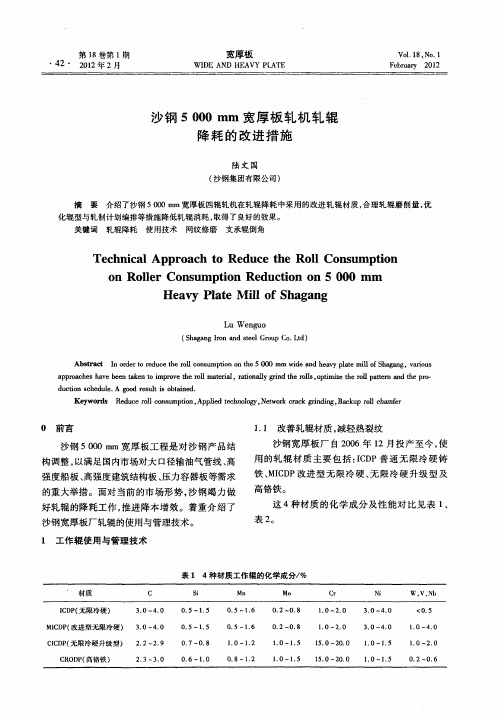
表1 4种材质工作辊的化学成分/ %
材质
ID ( C P 无限冷硬)
MI P 改 进 型无 限 冷硬 ) CD (
C
3 0~ . . 40
3 0~ . . 40
S i
0 5一1 5 . .
0 5—1 5 . .
M n
0 5一16 . .
0 5—16 . .
M o
的风 险 。改进 型 ID C P和 高 铬 铁 材 质 轧 辊 , 由 则
来 越 多 , 磨量不 断加 大 , 接影 响生产 的正 常推 修 直
断提 高 , 而轧辊订 单 又相对 不足 , 辊 网纹现 象越 轧
例较高, 尤其是大批量推进管线钢的生产 , 无限冷
硬升级 型 材 质更 适 合 目前 的 生产 。而普 通 ID CP 型则 由 于硬度 的偏 低 , 磨性 相对 不足 , 耐 在轧 辊 的 过钢量 提 升后 , 利于板 型 的控制 , 不 且增 加 了剥落
陆文国: 沙钢5 0 m宽 0 0 m 厚板轧机轧辊降耗的改 进措施
。 3 4・
考虑 到 目前 市 场形 势 和生 产 趋 势 , 种 钢 比 品
20 年以前, 08 一直采用将轧辊网纹修磨干净 再上机使用。且 当ห้องสมุดไป่ตู้品种钢 比例相对不高 , 轧辊
基本 能满 足生产 需要 。后来 随着 品种 钢 比例 的不
摘
要 介绍 了沙钢 500mm宽厚板 四辊轧机在轧辊降耗 中采用 的改进轧辊材 质 , 0 合理轧辊磨 削量 , 优 使用技术 网纹修磨 支承辊倒角
化辊 型与轧制计划编排等措施降低轧 辊消耗 , 取得了 良好的效果 。
关键 词 轧辊 降耗
优化轧辊管理降低辊耗
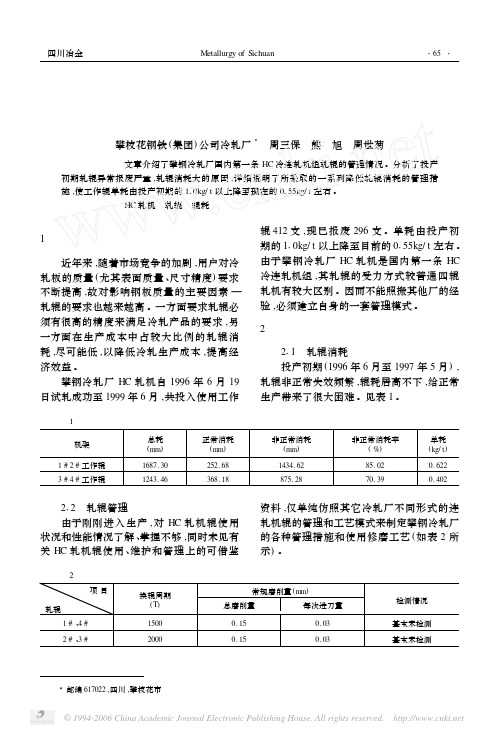
从实际生产反映的情况来看 ,现行的管 理制度能满足要求 ,对把轧辊消耗降低到目 前的 0157kg/ t (见表 7) 和杜绝爆辊起了重要 的作用 。
使用过的工作辊 ,磨工参照《轧辊质量信
息传递记录》并对应实际辊面情况 ,再根据 《工作辊磨下量》中相应的一项确定磨削量 ; 对因有缺陷而重磨的轧辊 ,磨工应根据重磨
辊的缺陷形式和大小以及探伤员的标注确定
磨削量 :当班磨过的每一根轧辊都应在相应 的记录本上做好记录 ,直径和辊号必须与辊 面所标注对应且准确无误 ;缺陷辊还应标注
·66 ·
1999 年第 5 期
上述措施缺乏针对性和科学性 ,从实际 生产中也发现存在许多问题 。
213 初期暴露的问题 (1) 换辊周期过长 ,磨削量过小 。HC 轧 机由于 中 间 辊 的 轴 向 移 动 以 及 弯 辊 力 的 使 用 ,轧辊受力状况明显区别于普通四辊轧机 , 工作辊辊面局部磨损严重 。其换辊周期相对 于普通轧机必应大大缩短 ,否则容易产生疲 劳裂纹或掉肉 ,且 0115mm 的常规磨削量根 本无法磨净工作辊每次上机轧制后的表面损 伤; (2) 对辊身表面缺陷及其危害的认识了 解不够 。冷轧辊绝大多数的表层剥落 (即爆 辊) 都不是自然产生的 ,而是在一定的时间内 发展形成的 ,通常是以辊身表面微裂纹为其 起点 ,在轧制持续的负荷作用下发展成疲劳 断裂 。所以轧辊表面裂纹的检测 ,在冷轧辊 管理工作中至关重要 ; (3) 轧辊信息传递缺乏严肃性且不畅通 。 在轧辊信息中有重要作用的“换辊单”经常没 有或所填产量 、长度与实际严重不符 ,造成管 理方对该辊的性能无法及时 、准确掌握 ;另磨 工和装配工之间没有轧辊信息的传递 ,磨工 磨辊处于盲目磨削的状态 ; (4) 磨削质量较差 。由于对轧辊不规范 磨削也会产生缺陷的认识不够 ,磨削中普遍 存在大进给量 、快速磨削 、磨削量极少的现 象 。以致磨完的轧辊一是其疲劳层没有除 去 ;二是即使下机的轧辊没有裂纹 ,也会因磨 削方法不当产生烧伤 、裂纹 ; (5) 轧辊的周转处于缺乏监管 、无序 、混
棒材轧钢的降本增效措施
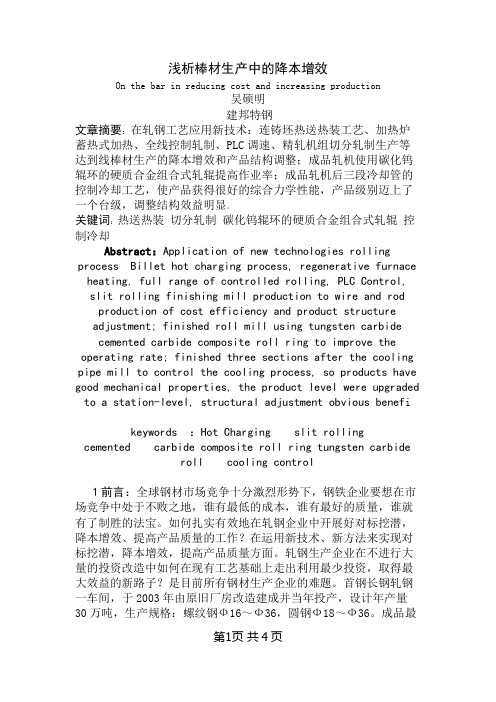
浅析棒材生产中的降本增效On the bar in reducing cost and increasing production吴硕明建邦特钢文章摘要:在轧钢工艺应用新技术:连铸坯热送热装工艺、加热炉蓄热式加热、全线控制轧制、PLC调速、精轧机组切分轧制生产等达到线棒材生产的降本增效和产品结构调整;成品轧机使用碳化钨辊环的硬质合金组合式轧辊提高作业率;成品轧机后三段冷却管的控制冷却工艺,使产品获得很好的综合力学性能,产品级别迈上了一个台级,调整结构效益明显。
关键词:热送热装切分轧制碳化钨辊环的硬质合金组合式轧辊控制冷却Abstract:Application of new technologies rolling process Billet hot charging process, regenerative furnace heating, full range of controlled rolling, PLC Control, slit rolling finishing mill production to wire and rodproduction of cost efficiency and product structureadjustment; finished roll mill using tungsten carbidecemented carbide composite roll ring to improve the operating rate; finished three sections after the cooling pipe mill to control the cooling process, so products have good mechanical properties, the product level were upgraded to a station-level, structural adjustment obvious benef ikeywords:Hot Charging slit rolling cemented carbide composite roll ring tungsten carbideroll cooling control1前言:全球钢材市场竞争十分激烈形势下,钢铁企业要想在市场竞争中处于不败之地,谁有最低的成本,谁有最好的质量,谁就有了制胜的法宝。
降低1422热轧检修能耗的措施及效果

热轧 板厂关 于 检修 、 停 机期 间 , 对 相关 主线 设 备 以及辅 助设 施进 行 明确 的规 范和 制订 。但该 规 定是 主要 耗能 设 备 和 系统 停 役 的规 范 和 要 求 , 对 辅 助设备 、 零 散系统 需要 分厂 、 作业 区进 一步 细化 和 完善 , 如 3号 加 热 炉 排 烟 风 机 , 在 炉 温 降 低 到 9 8 0℃ 以下 时 , 烧 嘴需切 换 到常 规模 式 , 排 烟风 机
梅钢 1 4 2 2热 轧 的工 序 能 耗 近 几 年 来 呈 现 持 续 降低 的态势 , 热 轧 板 厂 按 照公 司节 能 降耗 的要
1 . 1 检 修 时间延 长
正常情 况 下 , 检 修包 括计划 定 修与工 艺停 机 , 其 时 间节点 均按 照设 备定 修期 和工 艺换 辊周期 确
1 . 2 停机 制度 需要 进一步 细化
浪费。 2 . 2 提 高停机 规范 执行 率 1 ) 明确停役 要 求 , 责 任 到人 。按 照能 源 体 系 推 进要求 , 各作 业 区进行 能耗 源辨识 , 纳 入到各 作 业 区 的岗位规 程 中 , 并 把具 体 设 备 的停启 控 制 要 求 划分 到责任 人 , 按 要求 执行 。 2 ) 建 立 并 完 善 用 能 检 查 机 制 。根 据 公 司 推 行的” 三 级用 能检查 责 任机 制 ” 的要 求 , 认 真组 织 厂 里 的二级 用 能 检查 , 即 厂级 和 作 业 区级 。各 作 业 区作 业 长 负 责 管 辖 区域 内 的 能 源 因素 进 行 排
2 0 1 3年第 2期
梅 山科技
ቤተ መጻሕፍቲ ባይዱ
伯恩斯港厂降低轧辊消耗量的措施

伯恩斯港厂降低轧辊消耗量的措施伯恩斯港厂降低轧辊消耗量的措施安赛乐米塔尔集团在全球共运营24 家碳钢热轧带钢厂(HSM),每座带钢厂都有自己特定的产品与用户。
由于每一个厂的历史和当地市场需求的差异,这些带钢厂处在技术的不同发展阶段。
无论发展差异如何,安赛乐米塔尔集团已具备为各种问题交流解决方案的知识与经验。
自2006 年以来,安赛乐米塔尔伯恩斯港厂在热轧带钢生产方面已经与美国国内与国外各厂交流了知识与经验。
随着这一过程进行,在欧洲、南美和北美的三个厂被看成这方面的标杆:Gent(比利时)、Tubarao(巴西)和Dofasco(加拿大),作为这一活动的结果,制定出“结对工程”。
这一对标过程对所有涉及到的热轧带钢厂都非常有益。
通过钢厂总经理和部门经理的研究讨论,进行了一些改进,从而优化轧机稳定性,最终提高了带钢质量。
2008 年,当检查分析伯恩斯港厂HSM 计划外的换辊数量时,发现该厂在轧辊更换方面绩效差。
2009 年内,经过方法论途径,使用源于团队会议、头脑风暴和统计分析产生的理念,改变了轧辊更换频率高的状况。
仅采用几项技术,在没有资本投入的情况下实现了良好结果。
这一结果是通过结构性试验、知识共享以及改善作业而实现的。
以下将具体介绍在2009 年使用的方法和采取的一些技术。
在10 个月的时间内,实现了质量改善与轧辊费用降低。
2010 年,安赛乐米塔尔集团努力维持在2009 年通过标准化和自动化所实施的工艺变更而赢得的利益。
轧辊车间采取系列措施,使轧辊研磨量降低,同时在轧机的最后机架采用耐磨性更好的轧辊,如在F5 用高Cr 轧辊,F4用高速钢复合(HSS-CPC)轧辊等。
1 伯恩斯港厂80 英寸热轧带钢生产线伯恩斯港厂是安赛乐米塔尔在美国最大的钢厂,是一座联合钢铁厂。
该厂有2 座高炉,具备年产500 万t 钢水的能力。
安赛乐米塔尔伯恩斯港厂前身为伯利恒钢厂。
伯恩斯港厂的主要用户为汽车工业,主要产品为热轧、冷轧和涂层薄板。
高棒轧制速度提升中故障分析

高棒轧制速度提升中故障分析裴旭苗① 邵忠文(首钢长治钢铁有限公司轧钢厂 山西长治036011)摘 要 高棒产线轧制φ12mm热轧带肋钢筋,随着轧制速度的提升,成品波浪弯缺陷及高速倍尺剪堆钢故障明显增加,造成倍尺剪的堆钢问题亟待解决,本文介绍了倍尺剪系统的控制原理和过程,对提速后遇到的故障进行了分析,并制定了预防措施,达到提速后稳定生产的目的。
关键词 提速 波浪弯 故障 解决措施中图法分类号 TG155.4 文献标识码 ADoi:10 3969/j issn 1001-1269 2023 Z2 0301 前言首钢长钢轧钢厂高速棒材项目于2018年9月投产,它是在原轧钢厂高线北线生产线系列中,从主生产跨通过分岔通道将原线引入精整跨,新增的设备:其中高速上钢系统(倍尺剪系统)为国产设备,由天津博技制造,产品为φ12~φ16mm圆钢/热轧带肋钢筋及φ18、φ20mm圆钢直条棒材,年产能55万吨,主要钢种为低合金钢,坯料尺寸150mm×150mm×12000mm。
其中φ12mm热轧带肋钢筋最大设计速度35m/s,投产后实际轧制速度仅28m/s,设备能力未充分发挥,为提高高棒产能,长钢轧钢厂开始对高棒产线轧制速度进行提速。
随着轧制速度的提升,成品波浪弯缺陷及高速倍尺剪堆钢故障明显增加,φ12mm热轧带肋钢筋提速过程中出现的波浪弯、倍尺头尾部弯曲造成的切损大及剪切点不稳定、后摆杆卡阻、短尾钢堆钢问题亟待解决,提高高棒产线轧制速度技术研究迫在眉睫。
轧钢厂高速棒材提速过程中故障主要集中在高速上钢系统,经统计,高棒区1-9月工艺故障累计426次,其中高速区故障323次,占总故障的76%,高速上钢系统月平均故障率35 89次。
因此重点从高速上钢系统着手进行研究分析。
2 高速上钢系统的介绍2.1 高速上钢系统的组成高速上钢系统由剪前夹送辊、前伺服摆杆、高速飞剪、后摆杆、剪后(夹送)制动辊、转毂等设备组成。
提高20辊轧机高牌号无取向硅钢产品轧制稳定性的操作方法
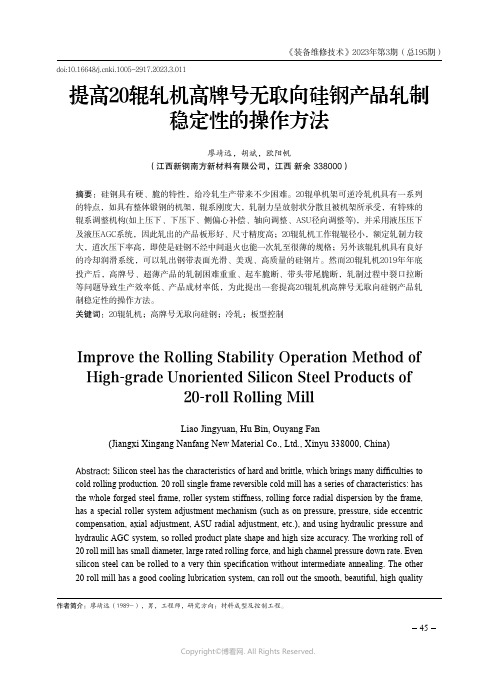
稳定性的操作方法廖靖远,胡斌,欧阳帆(江西新钢南方新材料有限公司,江西 新余 338000)摘要:硅钢具有硬、脆的特性,给冷轧生产带来不少困难。
20辊单机架可逆冷轧机具有一系列的特点,如具有整体锻钢的机架,辊系刚度大,轧制力呈放射状分散且被机架所承受,有特殊的辊系调整机构(如上压下、下压下、侧偏心补偿、轴向调整、ASU径向调整等),并采用液压压下及液压AGC系统,因此轧出的产品板形好、尺寸精度高;20辊轧机工作辊辊径小,额定轧制力较大,道次压下率高,即使是硅钢不经中间退火也能一次轧至很薄的规格;另外该辊轧机具有良好的冷却润滑系统,可以轧出钢带表面光滑、美观、高质量的硅钢片。
然而20辊轧机2019年年底投产后,高牌号、超薄产品的轧制困难重重、起车脆断、带头带尾脆断,轧制过程中裂口拉断等问题导致生产效率低、产品成材率低,为此提出一套提高20辊轧机高牌号无取向硅钢产品轧制稳定性的操作方法。
关键词:20辊轧机;高牌号无取向硅钢;冷轧;板型控制Improve the Rolling Stability Operation Method of High-grade Unoriented Silicon Steel Products of20-roll Rolling MillLiao Jingyuan, Hu Bin, Ouyang Fan(Jiangxi Xingang Nanfang New Material Co�, Ltd�, Xinyu 338000, China) Abstract: Silicon steel has the characteristics of hard and brittle, which brings many difficulties to cold rolling production� 20 roll single frame reversible cold mill has a series of characteristics: has the whole forged steel frame, roller system stiffness, rolling force radial dispersion by the frame, has a special roller system adjustment mechanism (such as on pressure, pressure, side eccentric compensation, axial adjustment, ASU radial adjustment, etc�), and using hydraulic pressure and hydraulic AGC system, so rolled product plate shape and high size accuracy� The working roll of20 roll mill has small diameter, large rated rolling force, and high channel pressure down rate� Evensilicon steel can be rolled to a very thin specification without intermediate annealing. The other20 roll mill has a good cooling lubrication system, can roll out the smooth, beautiful, high quality 作者简介:廖靖远(1989-),男,工程师,研究方向:材料成型及控制工程。
棒材轧制中降低工艺故障提高作业率的方法和措施
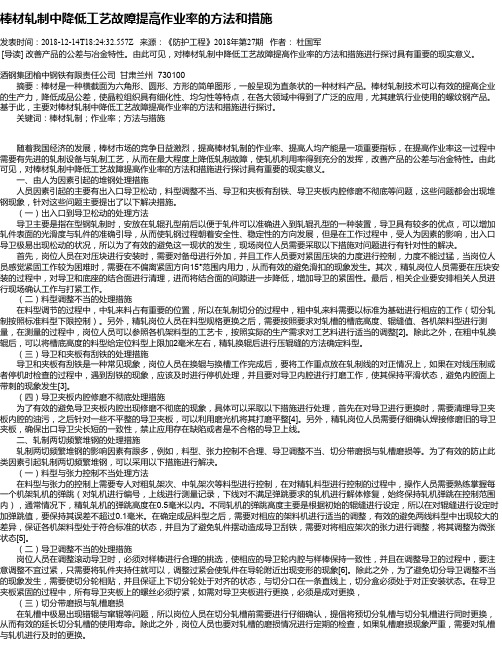
棒材轧制中降低工艺故障提高作业率的方法和措施发表时间:2018-12-14T18:24:32.557Z 来源:《防护工程》2018年第27期作者:杜国军[导读] 改善产品的公差与冶金特性。
由此可见,对棒材轧制中降低工艺故障提高作业率的方法和措施进行探讨具有重要的现实意义。
酒钢集团榆中钢铁有限责任公司甘肃兰州 730100 摘要:棒材是一种横截面为六角形、圆形、方形的简单图形,一般呈现为直条状的一种材料产品。
棒材轧制技术可以有效的提高企业的生产力,降低成品公差,使晶粒组织具有细化性、均匀性等特点,在各大领域中得到了广泛的应用,尤其建筑行业使用的螺纹钢产品。
基于此,主要对棒材轧制中降低工艺故障提高作业率的方法和措施进行探讨。
关键词:棒材轧制;作业率;方法与措施随着我国经济的发展,棒材市场的竞争日益激烈,提高棒材轧制的作业率、提高人均产能是一项重要指标,在提高作业率这一过程中需要有先进的轧制设备与轧制工艺,从而在最大程度上降低轧制故障,使轧机利用率得到充分的发挥,改善产品的公差与冶金特性。
由此可见,对棒材轧制中降低工艺故障提高作业率的方法和措施进行探讨具有重要的现实意义。
一、由人为因素引起的堆钢处理措施人员因素引起的主要有出入口导卫松动,料型调整不当、导卫和夹板有刮铁、导卫夹板内腔修磨不彻底等问题,这些问题都会出现堆钢现象,针对这些问题主要提出了以下解决措施。
(一)出入口到导卫松动的处理方法导卫主要是指在型钢轧制时,安放在轧辊孔型前后以便于轧件可以准确进入到轧辊孔型的一种装置,导卫具有较多的优点,可以增加轧件表面的光滑度与轧件的准确引导,从而使轧钢过程朝着安全性、稳定性的方向发展,但是在工作过程中,受人为因素的影响,出入口导卫极易出现松动的状况,所以为了有效的避免这一现状的发生,现场岗位人员需要采取以下措施对问题进行有针对性的解决。
首先,岗位人员在对压块进行安装时,需要对备母进行外加,并且工作人员要对紧固压块的力度进行控制,力度不能过猛,当岗位人员感觉紧固工作较为困难时,需要在不偏离紧固方向15°范围内用力,从而有效的避免滑扣的现象发生。
32-4马钢一钢轧总厂——降低硅钢轧辊消耗
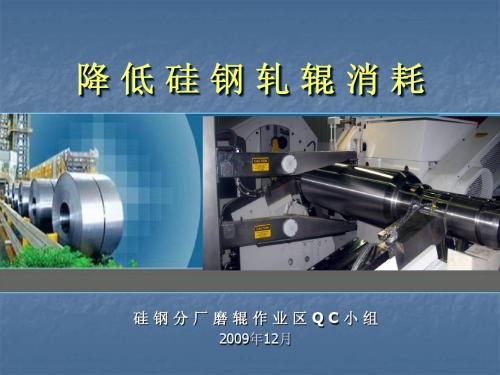
确认结果
“生产中牌号”是非要因 生产中牌号” 生产中牌号
要因确认
确认6 确认6
轧制张力与轧制速度均衡设定
硅钢轧 机 为可 逆式 轧 制 , 其 轧制 张力 与轧 制 速度 相互制 约 , 当 轧 制速 度 > 800MPM MPM时 轧制张力MAX 10T 轧制速度<800MPM 轧制张力MAX 15T MAX为 MPM, MAX为 800MPM时,轧制张力MAX为10T, 轧制速度<800MPM,轧制张力MAX为15T。一卷带钢 整个多道次轧制过程需保持张力均衡稳定,不可波动过频过大, 整个多道次轧制过程需保持张力均衡稳定 , 不可波动过频过大, 否则易发生断带等 生产异常情况,小组对08 08年下半年因轧制张力波动造成的 生产异常情况 , 小组对08年下半年因轧制张力波动造成的异常生产 情况做一分析 调查,并据此做以下轧辊消耗情况表。 调查,并据此做以下轧辊消耗情况表。
制表日期:2009年 制表日期:2009年2月20日 20日
71 62.6 68.7
确认结果
“轧制张力与轧制速度均衡设定”是要因 轧制张力与轧制速度均衡设定” 轧制张力与轧制速度均衡设定
要因确认
确认7 确认7
轧制压下率的分配
硅钢轧机轧制道次较多,特别在一、二道次高压下量轧制时对轧辊磨损较大, 硅钢轧机轧制道次较多,特别在一、二道次高压下量轧制时对轧辊磨损较大,故在 的分配需均衡, 小组对1 每个道次的压下率的分配需均衡,以保证轧制正常,小组对1月份轧制压下率分配 情况做一分析调查如下: 情况做一分析调查如下:
确认结果
“入口压板台易磨损”是非要因 入口压板台易磨损” 入口压板台易磨损
要因确认
确认3 确认3
圆盘剪堵边次数多 圆盘剪堵边次数多 堵边次数
6、鄂钢棒材《实施新冷却技术,降低轧辊导卫消耗,提高生产率》[1]
![6、鄂钢棒材《实施新冷却技术,降低轧辊导卫消耗,提高生产率》[1]](https://img.taocdn.com/s3/m/d19617fe770bf78a652954b2.png)
武钢集团鄂钢公司棒材厂《实施新冷却技术降低轧辊导卫消耗,提高生产率》简介原棒材厂二车间轧辊、导卫及精轧活套器旋转辊的冷却管网布置、冷却结构件的设计以及冷却水质量等诸多方面都存在缺陷,造成生产过程中,导致轧辊缺水断辊、轧槽烧损不耐磨、旋转辊粘铁、备件消耗大以及圆钢成品表面出现麻点、凹坑等质量问题。
围绕以上问题,对冷却管网、冷却结构件等进行重新设计和改造,实施新冷却技术,达到了杜绝轧辊缺水断辊、轧槽耐磨损、旋转辊不粘铁、备件消耗降低以及圆钢成品表面质量满足国家标准的良好效果。
武汉钢铁(集团)公司合理化建议“金点子”申报材料鄂钢公司棒材厂《实施新冷却技术,降低轧辊导卫消耗,提高生产率》武钢集团鄂钢公司二O一O年五月目录1、《实施新冷却技术,降低轧辊导卫消耗,提高生产率》合理化建议书2、《实施新冷却技术,降低轧辊导卫消耗,提高生产率》审查论证意见3、《实施新冷却技术,降低轧辊导卫消耗,提高生产率》立项计划4、《实施新冷却技术,降低轧辊导卫消耗,提高生产率》实施情况报告5、《实施新冷却技术,降低轧辊导卫消耗,提高生产率》效益分析报告6、鄂钢公司《关于表彰2009年度合理化建议“金点子”和优秀组织单位的决定》7、武汉钢铁(集团)合理化建议“金点子”申报表《实施新冷却技术降低轧辊导卫消耗,提高生产率》合理化建议书武钢集团鄂钢公司棒材厂尹志香、王汉林二OO九年六月一、建议产生的背景:鄂钢棒材厂二车间是2003年12 月26日投产的一条连轧生产线。
年设计产量为50万吨。
该车间1#750轧机至18#350轧机机架是由哈东伟提供的短应力轧机,通过悬挂式横梁输送浊循环水冷却轧辊和导卫。
由于初始设计缺陷,冷却方式和效果明显不满足生产现场需要:粗轧孔型烧损、掉块及断辊现象频繁;中精轧孔型磨损不均、龟裂、发黑现象严重。
,致使换辊换孔型频繁、成品材尺寸和质量不合格,严重制约了棒材厂生产的正常进行。
二、建议提出:2006年5月,棒材厂就二车间轧辊和导卫水冷却存在的问题,组织轧钢、准备等相关管理人员召开专题讨论会,成立以“二车间轧辊和导卫水冷却操作”的专题攻关小组。
QC成果降低棒二分厂连轧区域电气故障率精品资料

标准 化
下步 打算
√
饼图显示接触针折断维修合计7次,占空过辊道故障维修总量的百分比 =7÷25×100%=28%,超出了≤20%的标准。
选题 理由
现场 调查
目标
原因 分析
要因 确认
制定 对策
对策 实施
效果 检查
标准 化
下步 打算
×
如果航空连接触点进水,会造成航空连接触点短路,影响电气信号正 常使用,出现故障。现场调查连轧线航空盒连接触点进水情况:
组长
张卫春
辅导员 王静 活动次数 16次
小组成员
姓名
工龄
文化程度 职 务
组内职务
张卫春
19
专科 点检员
组长
康合合
5
本科 助理工程师
组员
张伟峰
22
专科 点检员
组员
杨伟清
23
本科 工程师
组员
宋增贵
5
本科 点检员
组员
2007年7月宝 钢特材条钢厂从 国外引进了一条 高温合金棒材连 轧生产线,连轧 机形式为16连轧, 机架成45度角布 置,重点生产军 工产品。
效果 检查
标准 化
下步 打算
4.实施后效果检查
该对策要求完成的时间是5月31日,小组于28日前,完成了现场的 所有改进工作,完全达到了对策表中的强、弱电信号间距≥100mm的要 求,任务完成。
选题 理由
现场 调查
目标
原因 分析
要因 确认
制定 对策
对策 实施
效果 检查
标准 化
下步 打算
检查一:棒二分厂2011年1月至2011年12月设备引起停机次数
课题背景
从2011年开始, 由于市场需求,公 司产品结构调整等 因素,棒二分厂普 通钢种的生产比例 加大。军品主要为 无水轧制,普通钢 种为有水轧制,造 成现场的空气湿度 会明显增加。
浅谈如何降低950轧线的工序能耗

浅谈如何降低950轧线的工序能耗发布时间:2022-06-13T01:41:21.691Z 来源:《建筑实践》2022年第4期作者:侯建民[导读] 当前钢铁形势,钢铁企业面临巨大压力,受国家政策影响,产能受到限制侯建民山东泰山钢铁集团有限公司热轧部摘要:当前钢铁形势,钢铁企业面临巨大压力,受国家政策影响,产能受到限制,钢铁企业成本增加,因此,降低工序能耗,深挖内潜,节支降耗,已经成为钢铁企业的主要攻关课题。
关键词:热轧带钢;工序能耗;成本前言节支降耗,提高效益成为当前钢铁企业的主要任务。
950轧钢加热工序主要包括板坯接收、推钢、加热、出钢四个过程,如何提高加热炉的板坯加热质量,减少煤气消耗,是我们一直攻关的课题,加热工序的节能攻关,带钢的成材率攻关对降低整个轧钢系统的能耗有着重要意义。
本文侧重以轧钢加热炉节能改造、成材率攻关为分析对象,介绍加热炉对成材率、煤气消耗的影响,提出950轧线提高成材率、降低加热炉能耗的措施和方法。
1 950热轧中宽带生产线各工序概述加热工序是将连铸机生产出的合格钢坯输送至入炉辊道,根据生产计划钢坯入炉(双蓄热步进梁式加热炉)加热,按照工艺要求温度出炉准备轧制的过程。
轧制工序是将按工艺温度出炉的钢坯通过粗轧高压水除鳞、E1除鳞点、E1立辊轧制、粗轧可逆轧机5道次轧制、热卷箱、飞剪、精轧除鳞箱、精轧机的轧制过程,是将钢坯轧制成一定宽度和厚度的带钢的过程。
卷取工序是将通过层流冷却系统的带钢卷成具有外在良好卷形,是热轧带钢生产过程中的最后一道工序。
(950轧钢生产线工艺流程见图1所示)2 950加热工序能耗影响因素分析加热工序能耗占轧钢综合能耗的70%~80%,影响加热工序能耗的因素也是影响整个轧线总能耗的决定性因素,由于煤气消耗直接影响加热工序节能效率,所以分析加热炉煤气消耗影响因素,从中找出主要控制因素,便可以有效地提高此工序的节能效率。
而影响加热炉煤气能耗的因素很多,下面主要从设备、板坯、人员等方面进行了分析。
降低四辊燃料破碎机辊耗的措施

( 1 )下 辊 表 面硬 度不 足 。上 辊 和下 辊 表面
由于设备结构 、制造 、操作等原 因,经常出现 辊面崩边 、环形楔松动 、辊子窜动等状况 ,导
致 破 碎后 燃 料 粒 度 超 标 ,造 成 烧 结 工 序 能耗 升
硬度 ( H R C )值 均为 5 3 。上 辊 进 行 粗 破 , 主 、 被 动辊 间隙控 制在 7 mm 以内 ,作 业 中碰 辊 相对 较 少 ,使用 中损 耗 不大 。下 辊 对燃 料 进行 细 破 ,
高 ,增加了检修频次和维修费用 。为此 ,烧 结
厂 开 展攻 关 ,可 望 提 高 四辊 破 碎 机 辊 子使 用 寿 命 。本文 进行 总结 。
主 、被动辊 间隙为 3 m m,且工艺要求破碎后燃
料 粒度 小 于 3 m m 的 比例 ≥7 5 %,所 以下辊 碰 辊
较 多 ,易 出现 不 同程 度 的崩 边 、脱 块 。 因此 下 辊 的表面 硬度要 求更 高 。 ( 2 ) 辊 皮 安 装 不 合 理 。 辊 子 由辊 皮 、轮 毂 、锥 面环 形 楔 、紧 固螺 栓 与 主轴 构 成 ,辊 皮
作者 :舒 良良,大学学历 ,助理 工程 师 ,现 主要
碎 辊 工作 状 态 下 辊 子受 到 反 复 冲击 和 挤 压 ,一 旦 紧 固螺 栓 因 疲 劳失 效 而 产 生 塑 性 变 形 后 被 拉 长 ,环 形 楔 无 法 定 位 造成 辊 皮 松 脱 ,如 未 能 及 时 发 现 ,辊 子 在 失 衡 的情 况 下 继 续 运 行 ,将 导 致 辊皮 损 坏 、环 形 楔 损坏 、轴 承 损 坏 等 ,被 迫
从 事技 术管理工作。
2 0 1 5 年第 5 期
停 机检 修 处理 。
宣钢热带生产线辊耗偏高原因分析及对策
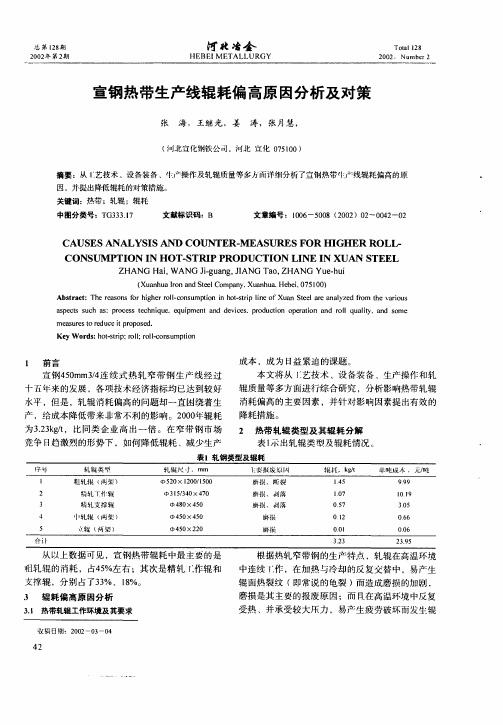
ap cs s c s rc s e h iu .e up n d d vc s rd cin o eain a d rl q ai nd sme s e t u h a -po es tc nq e q ime ta e ie.po u t p rt o l u l n o o n  ̄.a o
总第 l8 2 期 20 年 第2 02 期
河 北 冶 4- " -
HEBE E lM TALLURGY
To a 28 t Il 2 0 0 2, N Ulb r2 I e l
宣钢 热带生产线辊耗偏 高原 因分析及对策
张 海 ,王继 光 ,姜 涛 , 张月慧 ,
(iJ宣 化 钢铁 公 司 , ̄ - 宣 化 0 50  ̄ L , l ,I ,L I 7 10)
支撑辊 ,分 别 占了3 % 、l%。 3 8 3 辊耗偏 高原 因分析
31 热带轧辊工作环境 及其要求 .
收稿 日期 :2 0 -0 -0 02 3 4 42
磨损 是其 主要 的报 废 原 因 ;而 1在高 温环境 中反复 7 ,
受热 、并 承受 较大 压力 ,易产生 疲 劳破 坏而 发生 辊
(1 )原料 条件 不理 想 。宣 钢 热 带使 用 的原 料
为 l0 mm ×l0 m, l 0 m × m ×2 5 7m 2 mm矩 形 连 铸 坯 。 要 轧 成 成 品带 钢
( 3) ̄ 4 J 备 差 ,加 l 量 和加 l 度 L gm l 设 质 精 差 。轧辊加 l 质量 埘 于精 轧 l 辊 和 支撑 辊尤 为重 : 作
降耗措 施 。 2 热带 轧辊 类型 及其 辊耗 分解 表 l 出轧辊 类 犁及 辊耗情 况 。 示
水平 ,但是 ,轧 辊 消耗偏 高 的问题 却一 直 凼绕着生 产 ,给 成本降低 带来 _常 不利 的影 响 。2 0 年辊 耗 _ J 00 为32 k ,比 同类 企业 高 出 一倍 。在 窄 带 钢 市场 .3 ̄t 竞争 日趋激烈 的形势 下 ,如何 降低 辊耗 、减 少生产
- 1、下载文档前请自行甄别文档内容的完整性,平台不提供额外的编辑、内容补充、找答案等附加服务。
- 2、"仅部分预览"的文档,不可在线预览部分如存在完整性等问题,可反馈申请退款(可完整预览的文档不适用该条件!)。
- 3、如文档侵犯您的权益,请联系客服反馈,我们会尽快为您处理(人工客服工作时间:9:00-18:30)。
活动 个人综合能力 质量意识
前 4 3
后 5
自信心
5
个人综合能力 5 4 3 2 1 0
质量意识
QC知识
团队精神 自信心
制图人:岳培培
3
4 3
4
5 5
团队精神
活动前 活动后
QC知识
2018年3月21日
下步计划
通过本次活动小组成员提高了运用QC工具分析问题、解决问题的能力,增
加了对QC工具的了解,增强了团队的凝聚力。本次QC活动之后,我们小组计
对策实施
对策实施一:安装轴承时,应垫以铜棒或木棒,然后锤击 实施方法:安装轴承时,应垫以铜棒或木棒,然后锤击,严禁用榔头直击轴承, 严禁用榔头直击轴承
对轴承所施加的压力平均分布在轴承的内圈(装轴)和外圈(装孔)上,切勿 单方向施加压力,以防轴承倾斜挤压坏配合表面。 对策实施后,对轴承内圈和外圈压力进行测量,结果如下: 轧机 内圈 压力
外圈 压力
1 21
21
2 22
22
3 23
22
4 23
23
5 20
20
6 24
24
7 21
21
8 23
23
9 22
23
对策实施后,轴承内外圈压力差小于2MPa,符合标准。
对策实施
对策实施二:轴承在安装前要进行打压实验,并更换破损 的油管和分配器
实施方法:轴承在安装前要进行打压实验,油管破损漏油、分配器不过油,要 进行更换。轴承在安装前要抹上润滑脂,防止刚上线的轧机轴承无润滑,上线 运转的轧机也定期为轴承加油。
2018.2
2018.3
为计划进度
为实际进度
制表人:岳培培
时间:2017年12月8日
选题理由
公司要求
2018年根据钢铁市场形势,降本增效,为公司创造利润。
结合我厂实际要求,轧钢准备作业区降低轧机维修成本。 10
2017年每月烧辊频次统计
厂部要求
现
状
5
7
1月 2月
6
3月
8
7
4月 5月
8
8
9 5
4
9月
降低棒材轧辊烧辊频次
案 例
发布人:高秋喜 单位:轧钢准备作业区
概况
要因确认 对策制定 对策实施
目录
PAGE DIRECTORY
小组简介
选题理由
现状调查
效果验证
巩固措施 下步计划
设定目标
原因分析
概况 Introduction
烧辊是制约棒材产能提升的重大问题,发 生烧辊事故后需停车更换新辊,不但制约生 产,而且增加维修成本,影响作业区产量。
60% 6 6
40%
20%
0%
100%
时间:2017年12月20日
制图/表人:岳培培 结论
由图可知,造成轧机烧辊的主要原因是接触疲劳和磨 损,占83.3%。
目标设定
本次活动 目标
棒材作业去每月烧辊次数≤2次
6 6
4
2 2
0
现状
制图人:岳培培
目标
2017年12月20日
原因分析
我们对“头脑风暴法”的因素进行分层、归纳和整理,做出树图如 下:
确认过程
人员
成绩
高秋喜 刘洪斌 马建国
92 89 88
杨辉
86
确认标准 确认方法
实操考试成绩≥75分 检查培训记录 确认人
确认结果 高秋喜
实操考试成绩≥80分 确认时间 2018.1.2
要因确认
确认二
轴承封闭不严
对更换下的烧损的轧辊轴承内部进行检查:
确认结论
非要因
确认过程
确认标准 确认方法
轴承内无水迹 现场检测 确认人
刘洪斌
马建国 杨辉
2018.1.5
2018..10 2018.1.15
装配过盈量大 装配压力分配 不均 油管破损漏油、 分配器不过油
5
现场检测
组装后试压20MPa不能漏油
高秋喜
2018.1.20
制表/图:岳培培 时间:2017/12/28
要因确认
确认一
培训少
确认结论
非要因
对2017年12月对轧钢准备作业区职工装配轧辊的操作技能进行考查,考查情况如下:
确认结果 刘洪斌
轴承内无水迹,符合标准 确认时间 2018.1.5
要因确认
确认三
装配过盈量大
确认结论
非要因
对装配的轴承内圈和轧辊轴径之差进行测量:
确认过程
轧机 1 差值 0.5
2 0.4
3 0.3
4 0.4
5 0.5
6 0.4
7 0.4
8 0.5
9 0.4
确认标准 确认方法
轴承内圈和轧辊轴径之差 不大于0.6mm 现场测量 确认人
序号 1 末端原因 培训少 轴承封闭不严 确认方法 检查培训记 录 确认标准 理论培训学时大于16学时/半年, 实作考试成绩≥75分 确认人 高秋喜 确认时间 2018.1.2
2
3 4
现场检测
现场测量 现场检测
轴承内无水迹
轴承内圈和轧辊轴径之差不大于 0.6mm 安装轴承时,分布在轴承的内圈 (装轴)和外圈(装孔)上压力 相差不大于2MPa
对策实施后,上线使用的轧辊润滑正常,符合标准。
综合效果检查
各措施实施后,小组成员对作业区烧辊频次进行跟踪记录,结果如下:
6
4
2
6 2
0 活动前
制图人:岳培培
活动后
2018年3月21日
烧辊频次已由平均每月6次降低到平均每月2次,达到预期目标。
效益计算
经 济 效 益
无 形 效 益
维修一架烧辊的成本是2000元。每年降低烧辊48次,节约成本 96000元,其中:吨钢效益:350元/吨;机时产量:150吨/小时。 更换轧辊时间10分钟,每月节约时间创效: Q=10/60*48*350*150=42万元 总创效约为51.6万元。
5W1H 序号 要因
原则 对策 目标
1
2
措施 负责人 地点 完成时间 安装轴承时, 使车刀前 应垫以铜棒 查询合理 装配压力 间隙角在 或木棒,然 轧钢准备 2018.1.2 高秋喜 的装配方 分步不均 8--10° 后锤击,严 作业区 8 法 范围内 禁用榔头直 击轴承 轴承在安装 油管破损 前要进行打 保证油管、 漏油、分 全长齿错 压实验,并 轧钢准备 2018.1.2 杨辉 分配器完 ≤2mm 更换破损的 作业区 配器不过 8 好 油 油管和分配 器 制表人:岳培培 时间:2018年1月21日
*
存在的问题
通过本次自主管理活动,小组成员成功利用了QC的理论和方法,分工协作,成功的降 低了棒材轧辊烧辊频次,提高了我们解决工作中实际问题的能力,提高了小组成员的综合 素质,将对我们分析解决其他问题大有帮助。 此外,小组各成员从质量意识、自信心、团队精神等方面进行了自我评价,感受到了 自身综合能力的提升。
人 岗位工操作 水平参差不 齐 培训少 轴承封闭不 严 轴承磨损 烧辊 机 轴承裂纹 轴承配合表 面被破坏 润滑失效 装配过盈量 大 压力分配不 均
油管破损漏 油、分配器 不过油
法
末端因素统计 培训少
培训少
轴承封闭 不严
末端 因素
装配过盈 量大
装配压力 分配不均
油管破损 漏油、分 配器不过 油
针对末端因素,制定了要因确认计划 表:
小组简介
课题名称
小组名称 小组类型
降低棒材轧辊烧辊频次
成立日期
2017.12
轧钢准备作业区轧机组 现场型 组长 高秋喜
小组成员
活动日期
5人
QC教育时间
2017.12—2018.3
12学时
活动频次
4次/月,出勤率100%
制表:岳培培 时间:2017年12月5日
小组成员概况
姓 名 高秋喜 刘洪斌 年龄 48 44 学 历 初中 中技 职称 技师 技师 组内职务 组长 组员 组内分工 对外沟通 原因分析
现状调查
现状调查二
对造成烧辊的原因进行分析并按原因分类统计: 频次 36 24 6 6 比例
调 83.3% 查 91.7% 表
40 35 30 25 20 15 10 5 0 36 100% 120%
原因 接触疲劳 磨损 裂纹 其它
50%
24 83.30%
50%
91.70%
100%
80%
排 列 图
6
2
10月
4
11月
4
12月
0
6月
7月
8月
选择课题
降低棒材轧辊烧辊频次
现状调查
现状调查一
小组成员对作业区2017年各月份烧辊频次进行统 计:
2017年每月烧辊频次统计
10
7
5
8
6
7
8
8
9
5 4 2
9月
6 4 4
0 1月 2月 3月 4月 5月 6月 7月 8月 10月 11月 12月
结论
由图可知,2017年10月烧辊次数最少,共2次,平均烧辊次数 是每月6次。
经过本次自主管理活动,作业区烧辊次数显著减少,非计划停车时 间显著减少,为企业带来了经济效益,提高了企业的整体管理水 平,有利于树立良好的公司形象。
巩固措施 将自主管理活动中采取的一系列措施加入到日常管理中,对各项要求进行 了检查监督考核,同时将有效的措施统一到规程中,督促职工按标准化作 业,形成系统有效的降低成本体系。
确认结果 马建国
轴承内圈和轧辊轴径之差在 0.3-0.5mm范围内,符合标准 确认时间 2018.1.10