保险杠注塑工艺总结
汽车注塑工作总结 (2)
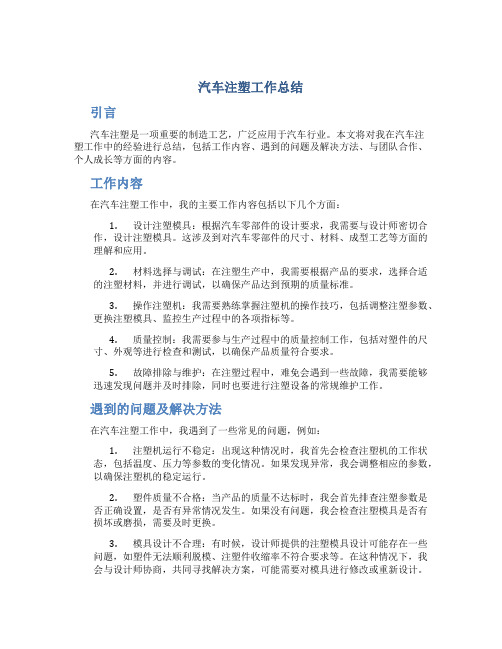
汽车注塑工作总结引言汽车注塑是一项重要的制造工艺,广泛应用于汽车行业。
本文将对我在汽车注塑工作中的经验进行总结,包括工作内容、遇到的问题及解决方法、与团队合作、个人成长等方面的内容。
工作内容在汽车注塑工作中,我的主要工作内容包括以下几个方面:1.设计注塑模具:根据汽车零部件的设计要求,我需要与设计师密切合作,设计注塑模具。
这涉及到对汽车零部件的尺寸、材料、成型工艺等方面的理解和应用。
2.材料选择与调试:在注塑生产中,我需要根据产品的要求,选择合适的注塑材料,并进行调试,以确保产品达到预期的质量标准。
3.操作注塑机:我需要熟练掌握注塑机的操作技巧,包括调整注塑参数、更换注塑模具、监控生产过程中的各项指标等。
4.质量控制:我需要参与生产过程中的质量控制工作,包括对塑件的尺寸、外观等进行检查和测试,以确保产品质量符合要求。
5.故障排除与维护:在注塑过程中,难免会遇到一些故障,我需要能够迅速发现问题并及时排除,同时也要进行注塑设备的常规维护工作。
遇到的问题及解决方法在汽车注塑工作中,我遇到了一些常见的问题,例如:1.注塑机运行不稳定:出现这种情况时,我首先会检查注塑机的工作状态,包括温度、压力等参数的变化情况。
如果发现异常,我会调整相应的参数,以确保注塑机的稳定运行。
2.塑件质量不合格:当产品的质量不达标时,我会首先排查注塑参数是否正确设置,是否有异常情况发生。
如果没有问题,我会检查注塑模具是否有损坏或磨损,需要及时更换。
3.模具设计不合理:有时候,设计师提供的注塑模具设计可能存在一些问题,如塑件无法顺利脱模、注塑件收缩率不符合要求等。
在这种情况下,我会与设计师协商,共同寻找解决方案,可能需要对模具进行修改或重新设计。
解决这些问题的方法主要是通过经验积累和与团队的合作。
我会积极参与与设计师、质检人员、供应商等的沟通,及时反馈问题,并共同探讨解决方案。
与团队合作在汽车注塑工作中,团队合作至关重要。
我与设计师、质检人员、操作工等紧密合作,共同推动项目的进展和完成。
保险杠注塑工艺流程

保险杠注塑工艺流程一、概述保险杠作为汽车外部的重要部件,其质量和外观直接关系到整车的安全性和美观性。
注塑工艺是目前制造保险杠的主要方法之一。
本文将介绍保险杠注塑的工艺流程。
二、模具设计保险杠注塑的第一步是进行模具设计。
模具的设计包括模具结构设计和模具零件设计。
模具结构设计要考虑到注塑过程中的材料流动、冷却等因素,以确保注塑产品的质量。
模具零件设计要根据保险杠的形状和尺寸确定,并考虑到模具的制造和使用方便性。
三、材料选择保险杠的注塑材料一般选择聚丙烯(PP)或聚碳酸酯(PC)等工程塑料。
材料的选择要考虑到保险杠的用途、耐磨性、抗冲击性以及成本等因素。
四、注塑工艺参数设置注塑工艺参数的设置对注塑产品的质量和成型效率有重要影响。
常见的注塑工艺参数包括注射压力、注射速度、保压时间、冷却时间等。
这些参数需要根据材料的特性和模具的设计来确定。
五、注塑成型在注塑成型过程中,首先将选定的塑料颗粒加热熔化,然后通过注射装置将熔融的塑料注入模具腔中。
待塑料冷却固化后,打开模具,取出成型的保险杠。
六、后处理注塑成型后,保险杠需要进行后处理。
后处理包括修整、去毛刺、穿孔等工艺,以使保险杠外观更加美观、符合设计要求。
七、质量检验保险杠注塑完成后,需要进行质量检验。
质量检验包括外观检查、尺寸测量、物理性能测试等。
通过质量检验,可以确保注塑产品的质量符合要求。
八、包装和出厂质量检验合格的保险杠将进行包装,以保护产品不受损伤。
然后,将包装好的保险杠出厂,交付给汽车制造商或汽车零部件供应商。
总结:保险杠注塑工艺流程包括模具设计、材料选择、注塑工艺参数设置、注塑成型、后处理、质量检验、包装和出厂等环节。
这些环节相互关联,缺一不可。
通过科学合理的工艺流程,可以生产出质量优良、外观美观的保险杠产品,满足市场需求。
同时,工艺流程的优化也可以提高生产效率,降低生产成本。
保险杠注塑工艺的发展将为汽车行业的发展提供更多可能。
保险杠模具设计总结
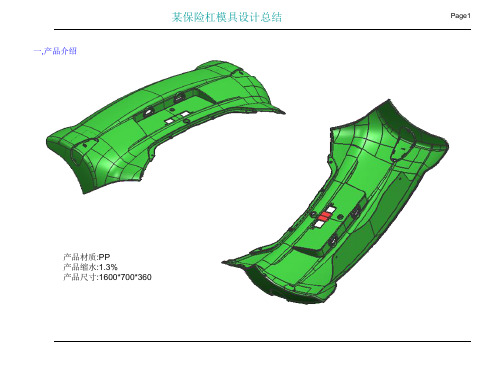
某保险杠模具设计总结
斜顶
顶块 此产品的顶出由6个斜顶+6个顶块组成.
Page11
六,温控系统
某保险杠模具设计总结
1,前模冷却系统
天侧
前模共6组运水
Page12
2,后模冷却系统
某保险杠模具设计总结
天侧
后模共6+6(其中包括斜顶,顶块运水)
Page13
3,斜顶,顶块冷却系统
某保险杠模具设计总结
Page14
A LIFTER 1 A B
C
LIFTER 6 D 行程22.1mm
D
行程9.43mm C
LIFTER 5
后模斜顶结构图PaLeabharlann e6LIFTER 4 25度
LIFTER 3
LIFTER1和LIFTER4,LIFTER2和LIFTER3为镜像关系,以下只描述其中一件. 模具顶出行程为180mm
某保险杠模具设计总结
三,模具结构
某保险杠模具设计总结
Page3
模具结构:4个滑块(两个前模滑块,两个后模滑块),六个斜顶,六个直顶块.
1,前模滑块
某保险杠模具设计总结
此滑块用油缸驱动,滑块行程36mm, 油缸行程需要104mm,实际定购油缸 行程为110mm.
30°
20°
Page4
行程示意图
行程示意图
2,后模滑块
一,产品介绍
某保险杠模具设计总结
Page1
产品材质:PP 产品缩水:1.3% 产品尺寸:1600*700*360
二,热流道系统
某保险杠模具设计总结
流道调节镶件
Page2
此产品采用四点开放式胶口, 利用流道调整镶件调节产品 熔接线,经moldflow和T1试模 验证,基本可以满足客户外观 要求及成型周期(60s)要求.
保险杠注塑工艺小结

保险杠注塑工艺小结保险杠作为汽车外部构件之一,其重要性不言而喻。
为了保证其质量和外观,先进高效的注塑工艺得到广泛应用。
本文介绍保险杠注塑工艺的七大要素,包括材料选择、模具设计、注塑机选择、注塑参数调整、模具保养维护、注塑成型管理和质量控制。
一、材料选择保险杠的材料选择非常重要,需要根据使用环境、结构要求和装配要求等多方面综合考虑。
目前常用的材料有PP材料、ABS材料和PC材料等。
PP材料是一种性价比很高的材料,具有良好的耐热、耐腐蚀和强度;ABS材料具有优良的防冲击性、热稳定性和机械性能,尤其适用于车身外壳;PC材料是一种高强度、高温耐受、高透明度的材料,适用于汽车前后照明器、进气口、天窗等外饰件。
二、模具设计模具设计是注塑工艺中最重要的一个环节,其合理性和先进性直接影响着注塑产品的质量。
在进行模具设计时,需要根据保险杠的结构、尺寸、要求等多方面因素进行考虑,选用适合的模具类型和结构,以确保注塑生产过程中的良好性能。
三、注塑机选择注塑机是注塑工艺的核心设备,其性能和靠谱性直接影响着注塑产品的质量。
在选择注塑机时,需要考虑材料特性、模具结构、注塑产品要求等因素,选用适合注塑生产的注塑机,以确保产品生产的稳定性和质量。
四、注塑参数调整注塑过程的机器参数调整非常重要,需要根据材料特性、模具结构、产品特性和生产环境等因素,对注塑机各个参数进行调整,以保证注塑产品的尺寸、密度、表面质量等合理性。
五、模具保养维护模具保养维护是注塑工艺过程中最重要的一个环节,其重要性不亚于注塑机的运行。
在进行注塑生产过程中,需要对模具进行定期的维护保养,包括清洗、涂抹抗锈剂、定期检查等内容,以保证模具的正常运行和延长使用寿命。
六、注塑成型管理注塑生产的管理非常重要,需要对注塑生产过程进行全面管理,包括原料采购、库房管理、注塑生产计划、生产过程控制等方面内容,以保证注塑产品的生产质量和稳定性。
七、质量控制注塑产品的质量控制是整个注塑工艺中最重要的一个环节,关系到注塑产品的质量和成本。
注塑行业工作总结范文(3篇)

第1篇一、前言随着我国经济的快速发展,注塑行业作为制造业的重要分支,发挥着越来越重要的作用。
在过去的一年里,我作为一名注塑行业的从业者,经历了许多挑战与机遇。
在此,我将对过去一年的工作进行总结,并对未来的工作方向进行展望。
一、工作回顾1. 生产管理(1)优化生产流程:通过对生产线的梳理和优化,提高了生产效率,降低了生产成本。
在保证产品质量的前提下,实现了产能的提升。
(2)设备维护与保养:加强设备维护保养工作,确保生产设备正常运行,降低设备故障率,提高设备使用寿命。
(3)人员培训:定期组织员工进行技术培训,提高员工技能水平,增强团队凝聚力。
2. 产品质量(1)严格控制原材料质量:从源头把关,确保原材料符合国家标准,为生产优质产品奠定基础。
(2)加强生产过程控制:严格执行生产工艺,对生产过程中的关键环节进行监控,确保产品质量稳定。
(3)完善品管体系:建立健全品管制度,对不合格品进行追溯,提高产品合格率。
3. 成本控制(1)优化采购流程:通过集中采购、谈判议价等方式,降低采购成本。
(2)合理控制生产成本:通过提高生产效率、降低能源消耗等措施,降低生产成本。
(3)加强库存管理:合理安排库存,降低库存成本。
4. 市场拓展(1)积极开拓新市场:参加行业展会,与客户建立良好的合作关系,扩大市场份额。
(2)提升品牌形象:加强品牌宣传,提高品牌知名度。
(3)优化客户服务:提高客户满意度,增强客户忠诚度。
二、工作亮点1. 产能提升:通过优化生产流程、提高设备利用率,实现了产能的提升,满足了客户需求。
2. 产品质量稳定:通过加强生产过程控制、完善品管体系,使产品质量得到了有效保障。
3. 成本降低:通过优化采购流程、合理控制生产成本、加强库存管理,实现了成本的有效控制。
4. 市场拓展成效显著:通过参加行业展会、加强品牌宣传,成功开拓了新市场,提升了品牌知名度。
三、不足与反思1. 人员素质有待提高:部分员工对新技术、新工艺掌握不足,影响生产效率。
工作总结注塑

工作总结注塑
经过一段时间的努力工作,我对注塑行业的工作有了一定的了解和经验,现在
我来总结一下这段时间的工作。
首先,注塑工作需要具备一定的技术水平和操作经验。
在这段时间里,我不断
学习和提升自己的技能,熟练掌握了注塑机的操作流程和技术要点,能够独立完成产品的注塑加工工作。
同时,我也加强了对注塑机的维护保养,确保设备的正常运转,提高了生产效率和产品质量。
其次,注塑工作需要具备良好的团队合作精神。
在工作中,我和同事们密切合作,互相协助,共同完成生产任务。
通过团队合作,我们能够更快更好地完成工作,提高了生产效率,同时也增强了团队的凝聚力和战斗力。
再次,注塑工作需要具备严谨的质量意识。
在生产过程中,我始终把质量放在
首位,严格按照工艺要求操作,确保产品的质量稳定可靠。
同时,我也积极参与质量管理工作,及时发现和解决生产中的质量问题,不断提升产品质量,满足客户的需求。
最后,注塑工作需要具备不断进取的精神。
在这段时间里,我不断学习和积累
经验,不断改进工作方法,提高工作效率,满足客户需求。
同时,我也积极参与技术培训和学习,不断提升自己的技术水平和专业素养。
总的来说,注塑工作是一项需要技术、团队、质量和进取精神的工作。
通过这
段时间的工作总结,我更加明确了自己的工作方向和目标,也更加坚定了自己在注塑行业的发展信心。
我会继续努力学习和提升自己,为注塑行业的发展贡献自己的力量。
汽车保险杠注射工艺分析及注射模设计

汽车保险杠注射工艺分析及注射模设计摘要:随着经济的快速发展,人们生活水平得到提高,物质生活越来越好,汽车几乎成为了人们出行必备的交通工具。
汽车后保险杠是汽车最重要的外观件之一,早期的汽车后保险杠采用金属制造,但现代的汽车后保险杠都采用塑料,由模具注射成型。
塑料保险杠不但成本大大降低,缓冲性能好,比金属更具有弹性,更能吸收撞击力,而且可以自动回弹和自动修复。
后保险杠外形尺寸大,结构复杂,外观要求很高,所以模具设计难度也非常高。
关键词:汽车保险杠;注射工艺;注射模设计汽车保险杠的质量是汽车安全问题中重要的一环。
汽车在发生轻微碰撞后,保险杠可以吸收碰撞能量,即使汽车发生严重碰撞,冲击力也会通过保险杠系统合理地分配给整个车身,避免造成过大的局部变形,从而保护乘客的安全,因此,汽车保险杠对于材料的要求十分严格。
1汽车保险杆的发展情况1896年卡尔本茨发明了第一辆汽车(三轮汽车),当时的汽车没有保险杠,只有一个安装喇叭和车灯用的金属横梁,后来为了达到美观的效果,增加了装饰用的前盖板,这就是最初的保险杆原型。
随着交通事故的频繁发生,人们逐渐意识到保险杠对车辆及行人的保护作用,有人考虑在前盖板上增加保护功能,具体采用与前横梁留有一定间隙的保险杠盖板,后来进一步发展成在保险杠盖板与横梁之间增加能吸能缓冲的橡胶构件,这样做能够很大程度降低汽车对行人的冲击,这种结构最终演变成后来的金属保险杠总成。
随后汽车保险杠又出现了由外板、缓冲材料和横梁三部分组成的保险杠结构。
近些年随着各行各业技术的大力发展,新型的保险杠结构也不断涌现,如液压吸能式、带气腔式等。
另外,出于保护行人的要求,现在国外也在研究安全气囊式保险杠。
2成型保险杠模具结构介绍以普通整车车身作为参考,保险杠长1.5~2.5m,宽0.5~1m,纵深深度0.5~1m。
假设某一保险杠外形尺寸为1720mm×940mm×540mm,按此塑件外形尺寸设计的注射模尺寸大概在2500mm×1200mm×2000mm。
PP材料保险杠的注塑工艺的制作技术
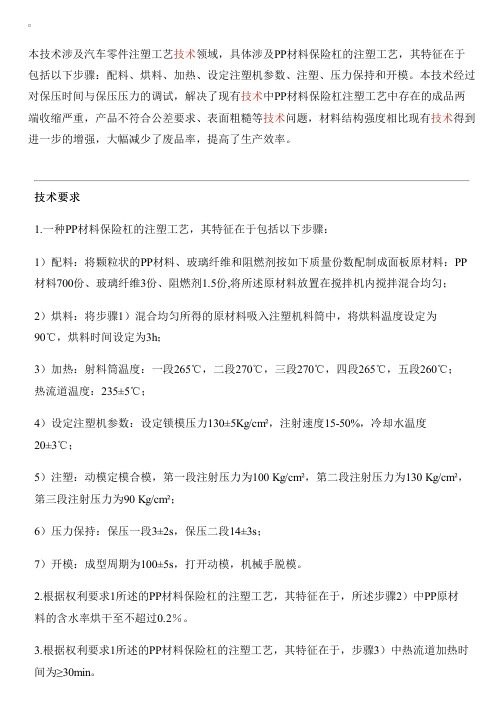
本技术涉及汽车零件注塑工艺技术领域,具体涉及PP材料保险杠的注塑工艺,其特征在于包括以下步骤:配料、烘料、加热、设定注塑机参数、注塑、压力保持和开模。
本技术经过对保压时间与保压压力的调试,解决了现有技术中PP材料保险杠注塑工艺中存在的成品两端收缩严重,产品不符合公差要求、表面粗糙等技术问题,材料结构强度相比现有技术得到进一步的增强,大幅减少了废品率,提高了生产效率。
技术要求1.一种PP材料保险杠的注塑工艺,其特征在于包括以下步骤:1)配料:将颗粒状的PP材料、玻璃纤维和阻燃剂按如下质量份数配制成面板原材料:PP 材料700份、玻璃纤维3份、阻燃剂1.5份,将所述原材料放置在搅拌机内搅拌混合均匀;2)烘料:将步骤1)混合均匀所得的原材料吸入注塑机料筒中,将烘料温度设定为90℃,烘料时间设定为3h;3)加热:射料筒温度:一段265℃,二段270℃,三段270℃,四段265℃,五段260℃;热流道温度:235±5℃;4)设定注塑机参数:设定锁模压力130±5Kg/cm²,注射速度15-50%,冷却水温度20±3℃;5)注塑:动模定模合模,第一段注射压力为100 Kg/cm²,第二段注射压力为130 Kg/cm²,第三段注射压力为90 Kg/cm²;6)压力保持:保压一段3±2s,保压二段14±3s;7)开模:成型周期为100±5s,打开动模,机械手脱模。
2.根据权利要求1所述的PP材料保险杠的注塑工艺,其特征在于,所述步骤2)中PP原材料的含水率烘干至不超过0.2%。
3.根据权利要求1所述的PP材料保险杠的注塑工艺,其特征在于,步骤3)中热流道加热时间为≥30min。
4.根据权利要求1所述的PP材料保险杠的注塑工艺,其特征在于,步骤6)中保压一段压力为70 Kg/cm²,保压二段压力为50 Kg/cm²。
注塑车间工艺年度总结(3篇)
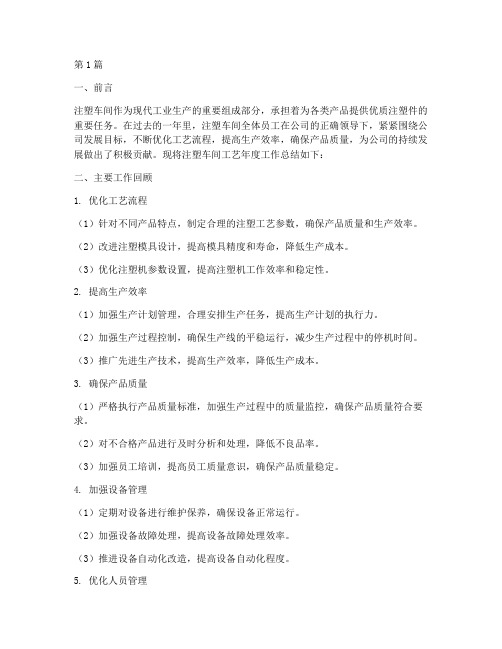
第1篇一、前言注塑车间作为现代工业生产的重要组成部分,承担着为各类产品提供优质注塑件的重要任务。
在过去的一年里,注塑车间全体员工在公司的正确领导下,紧紧围绕公司发展目标,不断优化工艺流程,提高生产效率,确保产品质量,为公司的持续发展做出了积极贡献。
现将注塑车间工艺年度工作总结如下:二、主要工作回顾1. 优化工艺流程(1)针对不同产品特点,制定合理的注塑工艺参数,确保产品质量和生产效率。
(2)改进注塑模具设计,提高模具精度和寿命,降低生产成本。
(3)优化注塑机参数设置,提高注塑机工作效率和稳定性。
2. 提高生产效率(1)加强生产计划管理,合理安排生产任务,提高生产计划的执行力。
(2)加强生产过程控制,确保生产线的平稳运行,减少生产过程中的停机时间。
(3)推广先进生产技术,提高生产效率,降低生产成本。
3. 确保产品质量(1)严格执行产品质量标准,加强生产过程中的质量监控,确保产品质量符合要求。
(2)对不合格产品进行及时分析和处理,降低不良品率。
(3)加强员工培训,提高员工质量意识,确保产品质量稳定。
4. 加强设备管理(1)定期对设备进行维护保养,确保设备正常运行。
(2)加强设备故障处理,提高设备故障处理效率。
(3)推进设备自动化改造,提高设备自动化程度。
5. 优化人员管理(1)加强员工培训,提高员工技能水平。
(2)完善绩效考核体系,激发员工工作积极性。
(3)加强团队建设,提高团队协作能力。
三、存在问题及改进措施1. 存在问题(1)部分员工对工艺流程的理解不够深入,导致生产过程中出现偏差。
(2)设备故障处理速度有待提高。
(3)生产计划执行力度不够。
2. 改进措施(1)加强员工培训,提高员工对工艺流程的理解和应用能力。
(2)优化设备故障处理流程,提高故障处理速度。
(3)加强生产计划管理,提高生产计划的执行力。
四、展望在新的一年里,注塑车间将继续秉承“质量第一、客户至上”的原则,不断优化工艺流程,提高生产效率,确保产品质量,为公司的发展贡献力量。
保险杠工艺参数

PP+EPDM-TD10的成型工艺参数前提考虑:汽车保险杠应为“注塑成型”。
1.数据:1)PP(聚丙烯)螺杆式注射成型的数据:[1]喷嘴温度:170~190℃料筒温度:前段:180~200℃中段:200~220℃后段:160~170℃模具温度:40~80℃注射压力:70~120MPa保压压力:50~60MPa注射时间:0~5s保压时间:20~60s冷却时间:15~50s成型周期:40~120s2)EPDM(三元乙丙橡胶)热固性塑料3)TD10(10%滑石粉)在聚丙烯的改性体系中,加入超细滑石粉母料不但能够显著的提高聚丙烯制品的刚性、表面硬度、耐热蠕变性、电绝缘性、尺寸稳定性,还可以提高聚丙烯的冲击强度。
在聚丙烯中添加少量的滑石粉还能起到成核剂的作用,提高聚丙烯的结晶性,从而使聚丙烯各项机械性能提高,又由于提高结晶性,细化晶粒,亦能提高聚丙烯的透明性。
填充20%和40%超细目滑石粉的聚丙烯复合材料,不论是在室温和高温下,都能够显著提高聚丙烯的刚性和高温下的耐蠕变性能。
例如:添加40%的超细目滑石粉母料的聚丙烯抗弯曲模量可从16100kg/cm2提高到42000kg/cm2,热变形温度从62℃(1.82Mpa力)提高到88℃或从121℃(0.45Mpa力)提高到147℃。
2.所得结论:1)在加入滑石粉后,聚丙烯的热变形温度升高;热变形力降低,故推测其融化温度升高,所需注塑压力降低。
2)三元乙丙橡胶为热固性塑料,不溶不熔。
推测其分解温度低于PP的熔融温度,故在温度方面不予以考虑。
粘度方面应大于PP-TD10,故注射压力应略大于PP-TD10的注射压力。
3)因为加入滑石粉后PP的结晶度升高,故推测本材料结晶度较高,故保压压力宜等于注射压力。
4)时间方面应与纯PP相似3.工艺参数:1)温度料筒温度:前段:200~220℃中段:220~240℃后段:190~200℃喷嘴温度:190~210℃模具温度:50~70℃2)压力注射压力:90~100MPa注射压力:20~30MPa保压压力:90~100MPa3)注塑时间:5s保压时间:25s摸内冷却时间:50s4.参考资料[1] 塑料成型工艺与模具设计P56注射成型的工艺参数,表4-1。
注塑工作总结范文7篇
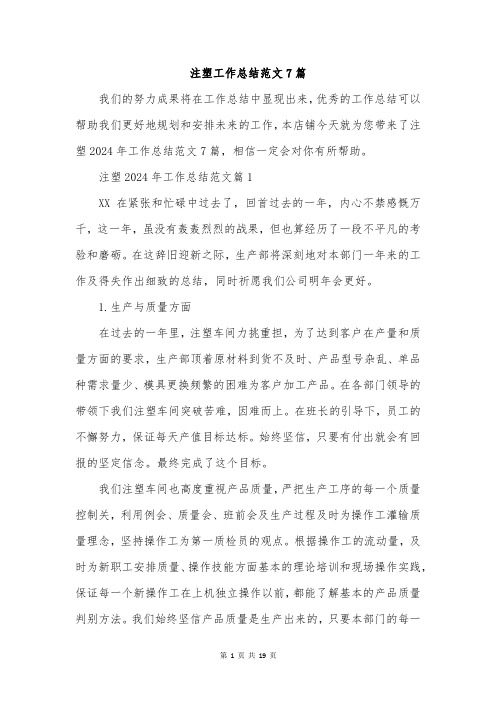
注塑工作总结范文7篇我们的努力成果将在工作总结中显现出来,优秀的工作总结可以帮助我们更好地规划和安排未来的工作,本店铺今天就为您带来了注塑2024年工作总结范文7篇,相信一定会对你有所帮助。
注塑2024年工作总结范文篇1XX在紧张和忙碌中过去了,回首过去的一年,内心不禁感慨万千,这一年,虽没有轰轰烈烈的战果,但也算经历了一段不平凡的考验和磨砺。
在这辞旧迎新之际,生产部将深刻地对本部门一年来的工作及得失作出细致的总结,同时祈愿我们公司明年会更好。
1.生产与质量方面在过去的一年里,注塑车间力挑重担,为了达到客户在产量和质量方面的要求,生产部顶着原材料到货不及时、产品型号杂乱、单品种需求量少、模具更换频繁的困难为客户加工产品。
在各部门领导的带领下我们注塑车间突破苦难,因难而上。
在班长的引导下,员工的不懈努力,保证每天产值目标达标。
始终坚信,只要有付出就会有回报的坚定信念。
最终完成了这个目标。
我们注塑车间也高度重视产品质量,严把生产工序的每一个质量控制关,利用例会、质量会、班前会及生产过程及时为操作工灌输质量理念,坚持操作工为第一质检员的观点。
根据操作工的流动量,及时为新职工安排质量、操作技能方面基本的理论培训和现场操作实践,保证每一个新操作工在上机独立操作以前,都能了解基本的产品质量判别方法。
我们始终坚信产品质量是生产出来的,只要本部门的每一个员工都有高度的质量意识,并付诸于生产操作的每一环节中,产品质量将会稳步提高,以达到满足客户质量要求的目标。
2.人员管理方面因公司生产任务的急剧增加,产品型号的多样化,公司新招聘员工很多,共有很多批次的新员工进入到车间的各生产岗位,且流动量很大,各岗位人员极不稳定,给生产各方面管理带来极大压力,就在这样的压力推动下,本车间还是坚定地对各岗位进行岗前岗中的简单培训,保证新进员工的顺利进入岗位角色,做到在班长及各级领导的正确引导下,基本胜任各自的岗位工作。
3.安全生产方面在过去的一年里,基于行业的特殊性,我们注塑车间将安全生产纳入了日常的管理工作之中,能够经常对各岗位员工进行安全知识的教育,培训操作工正确操作生产设备,发现问题及时处理。
注塑工艺年终总结及计划

注塑工艺年终总结及计划注塑工艺年终总结及计划一、引言注塑工艺是现代工业发展中非常重要的工艺技术之一,它广泛应用于家电、汽车、医疗器械、日用品等各个行业。
本篇年终总结及计划将回顾过去一年的工作情况,并制定明年的规划和目标,旨在提高注塑工艺的质量和效率。
二、工作回顾1. 注塑模具设计优化通过与设计部门密切合作,我们成功进行了多款模具的设计优化工作。
通过模具结构的改进和材料的选择,显著提高了注塑过程中的成型质量和生产效率。
下一步,我们将继续研究新的设计理念,并将其应用到实际生产中,以进一步提高模具的效能。
2. 注塑工艺参数优化我们对注塑机的参数进行了仔细的调整和优化。
通过合适的温度、速度和压力的组合,我们最大限度地减少了废品和缺陷的产生。
注塑工艺参数的优化是一个持续的过程,明年我们将继续关注新的研究成果,并对参数进行进一步的改进。
3. 检测设备升级我们购置了先进的注塑工艺检测设备,包括压力传感器、温度计和流量计等。
这些设备的使用为我们提供了更准确、更可靠的数据,有助于我们更好地控制注塑过程中的各个环节。
明年我们将进一步完善检测设备的使用方法,并加强员工的培训,以提高检测数据的准确性和可靠性。
4. 员工培训与技术交流我们注重员工的技能培训和分享经验的机会,组织了一系列的培训课程和技术交流活动。
员工通过参与这些活动,不仅提高了自身的技术水平,还加强了团队合作和沟通能力。
明年我们将继续加强员工培训工作,推动技术团队的建设和发展。
三、明年计划根据过去一年的工作回顾和总结,我们计划在明年的工作中有以下几个重点:1. 模具设计和材料研究我们将持续与设计部门合作,优化模具的设计和选择适合的材料。
通过引入新的设计理念和先进的材料,提高模具的效能和寿命,减少成型过程中的缺陷和废品。
2. 注塑工艺参数优化我们将进一步研究注塑工艺参数的优化方法,并将其应用到实际生产中。
通过优化参数,降低产品的缺陷率和废品率,提高生产效率。
汽车注塑工作总结报告
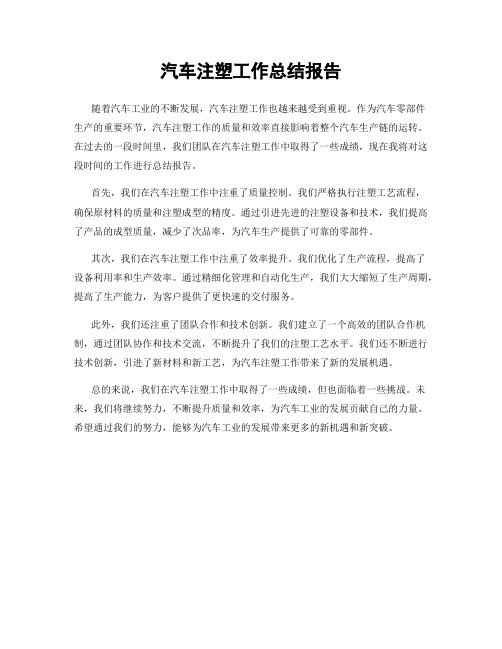
汽车注塑工作总结报告
随着汽车工业的不断发展,汽车注塑工作也越来越受到重视。
作为汽车零部件
生产的重要环节,汽车注塑工作的质量和效率直接影响着整个汽车生产链的运转。
在过去的一段时间里,我们团队在汽车注塑工作中取得了一些成绩,现在我将对这段时间的工作进行总结报告。
首先,我们在汽车注塑工作中注重了质量控制。
我们严格执行注塑工艺流程,
确保原材料的质量和注塑成型的精度。
通过引进先进的注塑设备和技术,我们提高了产品的成型质量,减少了次品率,为汽车生产提供了可靠的零部件。
其次,我们在汽车注塑工作中注重了效率提升。
我们优化了生产流程,提高了
设备利用率和生产效率。
通过精细化管理和自动化生产,我们大大缩短了生产周期,提高了生产能力,为客户提供了更快速的交付服务。
此外,我们还注重了团队合作和技术创新。
我们建立了一个高效的团队合作机制,通过团队协作和技术交流,不断提升了我们的注塑工艺水平。
我们还不断进行技术创新,引进了新材料和新工艺,为汽车注塑工作带来了新的发展机遇。
总的来说,我们在汽车注塑工作中取得了一些成绩,但也面临着一些挑战。
未来,我们将继续努力,不断提升质量和效率,为汽车工业的发展贡献自己的力量。
希望通过我们的努力,能够为汽车工业的发展带来更多的新机遇和新突破。
注塑工艺的年终总结
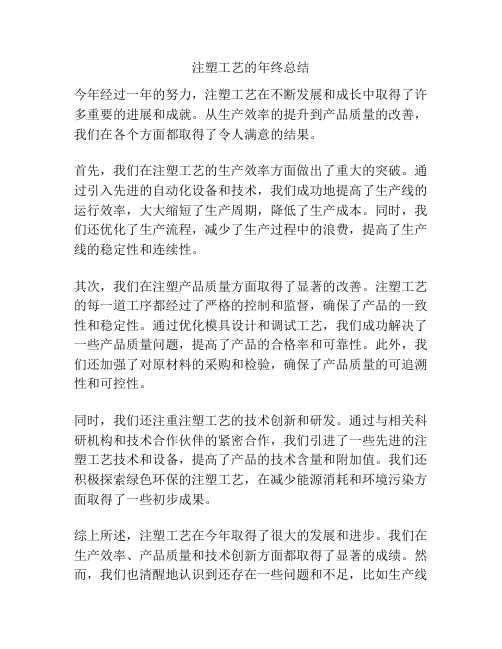
注塑工艺的年终总结
今年经过一年的努力,注塑工艺在不断发展和成长中取得了许多重要的进展和成就。
从生产效率的提升到产品质量的改善,我们在各个方面都取得了令人满意的结果。
首先,我们在注塑工艺的生产效率方面做出了重大的突破。
通过引入先进的自动化设备和技术,我们成功地提高了生产线的运行效率,大大缩短了生产周期,降低了生产成本。
同时,我们还优化了生产流程,减少了生产过程中的浪费,提高了生产线的稳定性和连续性。
其次,我们在注塑产品质量方面取得了显著的改善。
注塑工艺的每一道工序都经过了严格的控制和监督,确保了产品的一致性和稳定性。
通过优化模具设计和调试工艺,我们成功解决了一些产品质量问题,提高了产品的合格率和可靠性。
此外,我们还加强了对原材料的采购和检验,确保了产品质量的可追溯性和可控性。
同时,我们还注重注塑工艺的技术创新和研发。
通过与相关科研机构和技术合作伙伴的紧密合作,我们引进了一些先进的注塑工艺技术和设备,提高了产品的技术含量和附加值。
我们还积极探索绿色环保的注塑工艺,在减少能源消耗和环境污染方面取得了一些初步成果。
综上所述,注塑工艺在今年取得了很大的发展和进步。
我们在生产效率、产品质量和技术创新方面都取得了显著的成绩。
然而,我们也清醒地认识到还存在一些问题和不足,比如生产线
的设备老化和维护不及时等。
因此,明年我们将继续加大投入,在注塑工艺的改进和优化上不断努力,为客户提供更优质的产品和服务。
注塑工艺年度总结报告(3篇)

第1篇一、前言随着我国制造业的快速发展,注塑工艺作为现代工业生产中不可或缺的一部分,其技术水平和工艺流程的优化对于提高产品质量和生产效率具有重要意义。
在过去的一年里,我作为注塑工艺的从业者,积极参与到生产实践中,以下是对本年度工作的总结。
二、工作回顾1. 技术培训与提升本年度,我参加了公司组织的多场注塑工艺培训,学习了最新的注塑技术、设备操作和维护知识。
通过培训,我对注塑工艺有了更深入的了解,为今后的工作打下了坚实的基础。
2. 生产过程优化在注塑生产过程中,我注重对工艺参数的调整和优化,通过不断试验和实践,成功降低了产品的不良率,提高了生产效率。
以下是具体措施:(1)优化模具设计:针对不同产品特点,对模具结构进行改进,提高产品尺寸精度和表面光洁度。
(2)调整工艺参数:通过调整注射压力、温度、速度等参数,使产品成型更加稳定,减少缺陷。
(3)优化生产线布局:对生产线进行合理布局,提高生产效率,降低生产成本。
3. 设备维护与保养本年度,我认真负责地完成了设备维护与保养工作,确保了生产线的正常运行。
具体措施如下:(1)定期检查设备:对注塑机、模具、辅机等设备进行定期检查,发现问题及时解决。
(2)做好设备清洁:保持设备清洁,防止异物进入,影响生产。
(3)做好设备润滑:对设备进行定期润滑,减少磨损,延长设备使用寿命。
4. 团队协作与沟通在工作中,我注重与同事的沟通与协作,共同解决生产过程中的问题。
通过团队协作,提高了工作效率,确保了生产任务的顺利完成。
三、存在的问题与不足1. 对注塑工艺的理论知识掌握不够深入,需要加强学习。
2. 在生产过程中,对某些工艺参数的调整不够灵活,导致生产效率有待提高。
3. 对设备维护与保养的重视程度不够,有时存在侥幸心理。
四、来年工作计划1. 加强注塑工艺理论的学习,提高自身技术水平。
2. 优化生产过程,提高生产效率,降低不良率。
3. 严格做好设备维护与保养工作,确保生产线正常运行。
保险杠注塑工艺总结

保险杠注塑工艺小结(提纲)第一部分:概述一、原材料1.材料组成以及材料性能保险杠等外饰零件主要采用的材料是PP+EPDM以及滑石粉的改性产品。
PP是一种结晶性,具有一定的收缩性,其收缩性受模具温度影响,提供保险杠产品一定的强度。
EPDM是一种橡胶,可起到一定的吸收撞击能量的作用,与PP共混,改善材料的拉伸性能和弯曲性能。
添加滑石粉使材料的强度增加,以达到一定的性能要求。
同时在材料中还添加了其它助剂,起到改善材料的反应机理和调整收缩率的作用。
在注塑工程中部分助剂还可起到一定的交联作用,提高EPDM 与PP之间的相互的结合,进一步提高产品的机械性能。
2.材料的干燥和成型条件PP+EPDM的吸水性较弱,干燥要求为80℃-100℃,干燥时间2-4小时。
成型的工艺范围较宽,通常的塑化温度为210℃-260℃之间,注塑压力在50-100Kgf/cm2左右。
3.材料对油漆和装配性能的影响PP+EPDM的油漆性能在很大程度上取决与材料本身的性质。
由于PP本身的极性很弱,因此主要的油漆结合力取决于EPDM的分布情况,要求EPDM均匀地分布在产品表面,保证各个表面的油漆结合力一致。
工艺中,要求在流体的流动过程中形成适当的剪切力,通过PP和EPDM在流动速度上的差异,将EPDM 留在产品的外表面来达到油漆要求。
但在实际的工艺控制中由于要求兼顾其它方面的产品质量,这方面比较容易被忽略。
PP+EPDM对于产品尺寸上的影响主要是由于材料的模具收缩率引起。
EPDM 作为橡胶体,在压力的作用下存在一定的可收缩性,因此在注塑压力的作用下,EPDM有一定的收缩,而开模后产品又存在一定的弹性释放。
而PP作为结晶材料,在不同的温度下,结晶的速度不同,会造成收缩率存在变化。
在油漆过程中,二次烘烤会引起PP的再结晶,因此对产品的尺寸而言,存在的变数比较多。
4.材料主要性能对产品质量的影响熔融指数:熔融指数考察的是材料的流动性,熔融指数低,材料流动困难不但会造成产品的表面的诸多缺陷,还会形成局部的尺寸偏小等问题。
注塑工作总结及范文(3篇)

第1篇一、前言注塑行业作为我国制造业的重要组成部分,近年来发展迅速。
在过去的一年里,我所在的公司在注塑领域取得了显著的成果。
在此,我对过去一年的注塑工作进行总结,以期为今后工作提供借鉴。
二、工作总结1. 生产方面(1)产量:在过去的一年里,公司注塑产量稳步提升,同比增长15%。
主要得益于设备升级、工艺优化和人员培训。
(2)质量:通过加强品控管理,注塑产品质量得到明显提高。
合格率达到了98%,较去年同期提升2个百分点。
(3)成本:通过优化原材料采购、降低能耗和合理利用边角料,注塑产品成本降低5%。
2. 设备方面(1)设备升级:购置了多台高性能注塑机,提高了生产效率。
(2)设备维护:严格执行设备保养制度,确保设备正常运行。
3. 人员方面(1)培训:组织开展了多次技能培训,提高了员工综合素质。
(2)团队建设:加强团队协作,提高团队凝聚力。
4. 市场方面(1)拓展新客户:成功开拓了5家新客户,提高了市场份额。
(2)维护老客户:加强与老客户的沟通与合作,巩固合作关系。
三、工作亮点1. 优化生产流程,提高生产效率。
2. 加强品控管理,提升产品质量。
3. 降低生产成本,提高企业竞争力。
4. 加强团队建设,提高员工综合素质。
四、不足与改进1. 生产过程中,部分产品出现不良品,需加强品控环节。
2. 设备维护方面,部分设备存在老化现象,需加大设备更新力度。
3. 员工培训方面,需进一步拓宽培训内容,提高培训质量。
五、范文尊敬的领导、同事们:时光荏苒,转眼间一年过去了。
在过去的一年里,我所在的公司在注塑领域取得了丰硕的成果。
在此,我向大家汇报一下过去一年的工作总结。
一、生产方面1. 产量:同比增长15%,主要得益于设备升级和工艺优化。
2. 质量:合格率达到98%,较去年同期提升2个百分点。
3. 成本:降低5%,主要得益于原材料采购优化和能耗降低。
二、设备方面1. 设备升级:购置多台高性能注塑机,提高生产效率。
2. 设备维护:严格执行设备保养制度,确保设备正常运行。
注塑月总结报告范文

一、前言在过去的一个月中,我作为一名注塑工艺学徒,在公司的严格管理和师傅的悉心指导下,认真学习注塑工艺流程,积极参与生产实践,努力提高自己的专业技能。
现将本月的总结报告如下:二、工作内容1. 注塑工艺理论学习:本月我重点学习了注塑工艺的基本原理、工艺流程、设备操作及常见问题处理等方面的知识,为实际操作打下了坚实的基础。
2. 设备操作与维护:在师傅的带领下,我熟悉了注塑机、模具、加热器等设备的操作规程,并学会了设备的基本维护和保养方法。
3. 生产实践:在注塑生产过程中,我积极参与各项操作,包括原料准备、模具安装、加热、注塑、脱模、产品检验等环节,积累了丰富的实践经验。
4. 问题解决:在遇到生产过程中出现的问题时,我能够根据所学知识和实践经验,分析问题原因,提出解决方案,并协助师傅进行问题处理。
三、工作成绩1. 提高生产效率:通过不断学习和实践,我逐渐掌握了注塑工艺的各个环节,使生产效率得到了一定程度的提升。
2. 降低不良品率:在注塑生产过程中,我注重产品质量,严格执行操作规程,使得不良品率有所下降。
3. 优化工艺参数:通过对生产数据的分析,我提出了优化工艺参数的建议,得到了师傅和领导的认可。
四、不足与改进1. 理论知识掌握不全面:在注塑工艺理论学习方面,我还有待进一步提高,需要加强对专业书籍和资料的阅读。
2. 实践经验不足:在生产实践中,我还需要积累更多的实践经验,提高自己的操作技能。
3. 团队协作能力有待提高:在团队协作方面,我还需要加强与同事之间的沟通与交流,提高自己的团队协作能力。
五、下月工作计划1. 深入学习注塑工艺理论知识,提高自己的专业素养。
2. 积极参与生产实践,积累更多的实践经验,提高自己的操作技能。
3. 加强与同事之间的沟通与交流,提高团队协作能力。
4. 关注生产过程中的问题,提出合理化建议,为生产优化贡献自己的力量。
总之,在过去的一个月中,我在注塑工艺方面取得了一定的成绩,但也存在不足。
保险杠注塑工艺小结
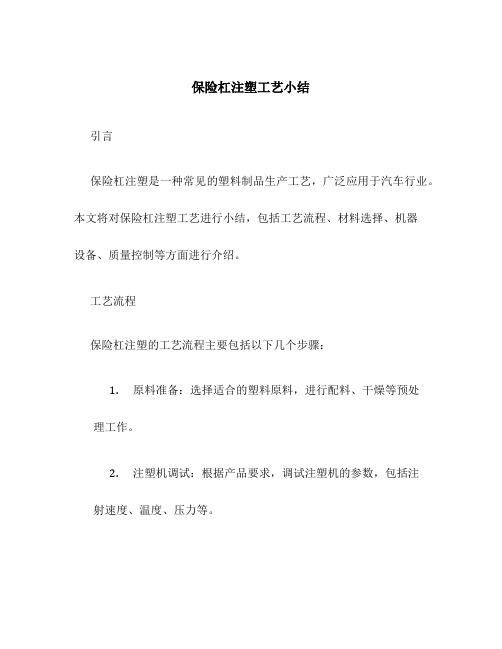
保险杠注塑工艺小结引言保险杠注塑是一种常见的塑料制品生产工艺,广泛应用于汽车行业。
本文将对保险杠注塑工艺进行小结,包括工艺流程、材料选择、机器设备、质量控制等方面进行介绍。
工艺流程保险杠注塑的工艺流程主要包括以下几个步骤:1.原料准备:选择适合的塑料原料,进行配料、干燥等预处理工作。
2.注塑机调试:根据产品要求,调试注塑机的参数,包括注射速度、温度、压力等。
3.模具安装:安装注塑机上的模具,确保其与注塑机配合良好。
4.开始注塑:将预热好的塑料原料通过注塑机的加热筒加热至熔化状态,然后通过射嘴注入到模具腔中。
5.冷却和模具开启:注塑成型后,利用冷却系统对模具进行冷却,使塑料快速凝固。
冷却完毕后,将模具开启,取出成品。
6.去除余料:将成品中的余料去除,以便进行后续加工。
7.检验和包装:对成品进行检验,判断其是否符合质量要求。
合格的产品进行包装,准备出库。
材料选择在保险杠注塑工艺中,常用的塑料材料包括聚丙烯(PP)、聚苯乙烯(PS)、聚碳酸酯(PC)等。
选择合适的材料对于产品的性能和外观至关重要。
1.聚丙烯(PP):具有良好的可加工性和耐候性,是保险杠注塑材料的首选。
其具有耐高温、耐酸碱、抗冲击等特性,适用于汽车保险杠等外部零件。
2.聚苯乙烯(PS):透明、韧性好,耐热性和耐寒性较差。
常用于内饰件等低要求的零部件。
3.聚碳酸酯(PC):具有优异的强度、刚度和耐冲击性,同时具备良好的透明度。
适用于要求较高的车身外部零部件。
材料选择需要考虑产品的使用环境、功能需求和成本等因素。
机器设备在保险杠注塑工艺中,主要使用的机器设备包括注塑机、模具和辅助设备。
1.注塑机:选择适合产品要求的注塑机,注重其注射量、锁模力、射出速度等参数的匹配。
2.模具:根据产品设计要求,选择合适的模具。
模具的材质和制造工艺对成品质量有着重要影响。
3.辅助设备:包括干燥机、冷却系统、温控设备等,用于提高生产效率和产品质量。
机器设备的选择需要考虑产品规格、生产能力和成本等因素。
- 1、下载文档前请自行甄别文档内容的完整性,平台不提供额外的编辑、内容补充、找答案等附加服务。
- 2、"仅部分预览"的文档,不可在线预览部分如存在完整性等问题,可反馈申请退款(可完整预览的文档不适用该条件!)。
- 3、如文档侵犯您的权益,请联系客服反馈,我们会尽快为您处理(人工客服工作时间:9:00-18:30)。
保险杠注塑工艺小结(提纲)第一部分:概述一、原材料1.材料组成以及材料性能保险杠等外饰零件主要采用的材料是PP+EPDM以及滑石粉的改性产品。
PP是一种结晶性,具有一定的收缩性,其收缩性受模具温度影响,提供保险杠产品一定的强度。
EPDM是一种橡胶,可起到一定的吸收撞击能量的作用,与PP共混,改善材料的拉伸性能和弯曲性能。
添加滑石粉使材料的强度增加,以达到一定的性能要求。
同时在材料中还添加了其它助剂,起到改善材料的反应机理和调整收缩率的作用。
在注塑工程中部分助剂还可起到一定的交联作用,提高EPDM 与PP之间的相互的结合,进一步提高产品的机械性能。
2.材料的干燥和成型条件PP+EPDM的吸水性较弱,干燥要求为80℃-100℃,干燥时间2-4小时。
成型的工艺范围较宽,通常的塑化温度为210℃-260℃之间,注塑压力在50-100Kgf/cm2左右。
3.材料对油漆和装配性能的影响PP+EPDM的油漆性能在很大程度上取决与材料本身的性质。
由于PP本身的极性很弱,因此主要的油漆结合力取决于EPDM的分布情况,要求EPDM均匀地分布在产品表面,保证各个表面的油漆结合力一致。
工艺中,要求在流体的流动过程中形成适当的剪切力,通过PP和EPDM在流动速度上的差异,将EPDM 留在产品的外表面来达到油漆要求。
但在实际的工艺控制中由于要求兼顾其它方面的产品质量,这方面比较容易被忽略。
PP+EPDM对于产品尺寸上的影响主要是由于材料的模具收缩率引起。
EPDM 作为橡胶体,在压力的作用下存在一定的可收缩性,因此在注塑压力的作用下,EPDM有一定的收缩,而开模后产品又存在一定的弹性释放。
而PP作为结晶材料,在不同的温度下,结晶的速度不同,会造成收缩率存在变化。
在油漆过程中,二次烘烤会引起PP的再结晶,因此对产品的尺寸而言,存在的变数比较多。
4.材料主要性能对产品质量的影响熔融指数:熔融指数考察的是材料的流动性,熔融指数低,材料流动困难不但会造成产品的表面的诸多缺陷,还会形成局部的尺寸偏小等问题。
而熔融指数过高,流动性过好,会使一定的压力下,型腔内熔体的量对注塑和保压压力十分敏感,用于控制尺寸的工艺的稳定性变差。
材料收缩率:材料收缩率的偏差必然导致产品的尺寸不良。
对于PP+EPDM而言除了材料本身的性质外,收缩率还取决于产品形状、模具结构、注塑速度、压力和温度。
通常材料供应商提供的材料收缩率是一个范围,如果是某个定值是指对于某个形状的产品而言,有较大工艺窗口的模具收缩率参考值。
EPDM的含量:由于EPDM的流动性较差,会引起表面和尺寸上的缺陷。
EPDM可被压缩,会造成局部的应力集中,过多的EPDM含量会造成工艺上控制的困难。
滑石粉含量:滑石粉同样会起到降低流动性的作用,主要会对产品表面造成不利影响,同时如果滑石粉如果共混不均匀,还会对降低产品的油漆性能。
虽然,一般而言材料供应商不会提供材料的各种成分含量。
但是从材料的部分其它性能上可以进行判断。
断裂伸长率的大小,相当部分取决于材料中EPDM的含量,含量越高,延伸率越大。
同时,滑石粉含量越高,强度也越高。
因此,在同等的材料性能下,还需要考虑材料的工艺性能。
通常理想的材料选择,应该考虑工艺窗口尽量变宽。
随着目前对产品尺寸要求的提高,相对会采用收缩率比较高的材料,因为收缩高,工艺上的变动使产品尺寸的影响也会变小。
二、设备1.注塑机a.注塑机各工艺参数设定介绍以下就UBE注塑机的各项参数设定值进行如下简述:注塑速度:注塑速度共分 段控制,输入值为最大注塑速度的百分比值。
注塑切换位置:各段注塑速度的切换位置注塑压力:注塑过程中所需注塑压力的上限值。
注塑机根据系统压力的反馈情况,对最高注塑压力进行限制。
如果注塑压力可以满足产品注塑的速度要求,注塑过程以速度控制为主,如果注塑压力低于注塑的速度所要求的注塑压力,余下的注塑过程以设定的注塑压力控制,直至补缩切换点。
此时,速度控制失效。
因此,在某些注塑过程中会出现提高注塑压力可以降低产品的现象。
补缩和保压压力:注塑机可设定一段补缩压力和 段保压压力。
补缩和保压时间:补缩和保压过程所需的时间。
V-P转换:即速度控制和压力控制转换点,注塑阶段以速度控制为主,补缩和保压阶段以压力控制为主。
V-P转换点是注塑和补缩、保压的转换点。
V-P转换压力:V-P转换压力的定义如下,当实际所需的注塑压力大于转换压力时,注塑过程正常在V-P转换点切换为补缩和保压。
如果没有达到转换压力,注塑过程继续进行,直至压力达到V-P转换压力进行切换。
设备油压顶出系统:1300T以上的设备有4组抽芯系统,动定模各2组,设定如下:Core open: 在合模之前的动作为“Set”,开模完成后动作为“Pull”Core Closed: 和模后的动作为“Set”,开模之前动作为“Pull”。
Core move:合模过程中动作为“Set“,开模过程动作为“Pull”,其中动作的位置可以设定。
此外,有2种状态可供选择:“Comb”:动作过程时,合模或开模过程不停止“Stop”:动作过程时,合模或开模过程停止,在抽芯动作完成后,开合模继续。
抽芯动作到位与否,可以用“LS”(限位开关)和“Time”(时间)两种方式控制。
LS-限位开关被触动后,表示动作到位。
Time-抽芯动作持续一段时间(设定值),设备自动给出到位信号。
此外,还设计顶出液压系统,顶出系统必须在抽芯“Pull”动作完成后进行(如果有抽芯动作)。
同时,顶出系统必须使用“LS”方式,否则将无法进行连续生产。
2.模温机a.外饰系统厂模温机现状在每台注塑机周边,均配备 台模温机,其中 台控制动模, 台控制定模。
可使用循环水和冷却水。
目前外饰系统厂的模温可控制范围狭窄,夏季实际控制温度范围在20-40℃,冬季在10-35℃之间。
在这样的条件下,相对缩小了工艺窗口。
3.干燥及集中供料系统a.干燥和集中供料系统工作情况外饰系统厂采用热风干燥设备,干燥容量有单位时间的材料耗用量而定。
材料干燥后,通过真空管通到集中供料系统的控制台上,在控制台上可以将管路连接到注塑机上。
注塑机上料斗的感应器,在料斗中的原料不足时向集中供料系统的控制单元发出信号,控制单元打开真空泵通过控制台,从干燥机送至注塑机上。
同时为了降低原材料的占地面积,在供料区域还设置了Silo。
作为未干燥粒子的缓冲贮存。
干燥料桶,从Silo或直接吸入塑料粒子,进行干燥。
吸入设备还可以通过吸料时间的差异控制从不同的管路吸入不同材料的比例,以进行原材料或者回用料配比。
b.干燥和集中供料系统对产品质量的影响主要对产品产生的影响包括以下几个方面:材料含水率过高:含水率过高,将影响产品的表面质量,出现排气不良现象。
同时会影响塑料熔体的流动性和模具收缩率,产生产品尺寸的偏差。
但是,由于PP+EPDM 的吸水性不高,对产品的影响较小。
三、模具1.模具结构a.模具结构与产品结构模具结构在很大程度上取决与产品结构和产品质量要求:模具顶出系统要求:根据对产品分型线位置的要求,在设计模具顶出系统时,必须进行考虑。
如果对分型线的位置没有特殊要求,可以采用模具开模到位后顶出。
通常在这种情况下,产品的分型线在可见表面上,该分型线无法消除,同时要求有一定的修边和打磨工作量。
另一种要求隐藏分型线,且在可见表面不允许有可见滑块痕迹,这种产品设计要求在大众设计的产品中比较多见。
这时要求开模同时顶出与开模同步,开模时利用滑块将产品顶住型腔。
同时产品向内收缩,在产品两侧完全与定模分开后,将模具彻底打开。
为方便取件,有时也采用第二级顶出。
为保证模具的安全性和操作性,通常在模具上设计有安全销,以保证在设备液压系统工作不正常时,通过安全销拉动模具顶板,保证模具定模型腔的安全。
合模过程之前,顶板不回退,依靠回顶将顶板回退到位。
为防止误操作,模具油缸的回退杆不与模具顶板连接,这样在注塑设备上始终保证无法使用手动方式退回顶板。
在模具由于在开模过程中,产品有一定程度的变形,任何设计或加工不理想,都可能产生产品损伤,产品设计时在两侧边缘尽量避免强度较低的部分和锐角。
流道系统:由于PP+EPDM对压力比较敏感,同时存在较大可压缩性,浇口如果直接进入产品通常会产生应力集中。
因此浇口应在冷流道中有足够的缓冲,或将浇口设置在不可见区域。
如采用多浇口结构,应该考虑产品的熔结痕问题。
尽量减少浇口数量。
采用Valve Gate技术,可以消除熔结痕,但是由于V/G浇口不是同时打开,容易引起冷料的问题。
在模具设置时必须充分考虑,冷料的去向,适当加大冷料井的容量。
如果采用Valve Gate侧浇口,前一个浇口熔体可能进入,后一个浇口的冷流道中,在这种情况下,冷流道中气体可能受困,应该考虑排气问题。
此外浇口的设置,还要求考虑门板和门槛等产品与车身的匹配关系。
在敏感区域不能设置浇口。
从尺寸稳定性方面考虑,通常增加浇口数量,有利于产品尺寸的稳定,和尺寸调整的方便。
但同时也会带来表面质量的不稳定因素,和换模效率模具成本增加等问题。
模具抛光要求:模具的光洁度与产品设计工艺有很大联系。
通常对于电镀产品而言,模具光洁度要求最高。
而模具光洁度提高,也有利于对熔体的流动进行控制。
但是,如果模具光泽度过高可能影响产品四、机械手取件1.机械手的功能介绍取件机械手的主要功能是将产品从模具中取出,并转移到工作台上。
延锋UBE 2200T 及3150T的注塑机采用的机械手可以进行3轴转动,但是1300T的机械手的转动方向至可以进行2轴转动。
每台机械手配有1路真空回路,用于使用吸盘吸取制件,另配有3路气路,保证机械手进行动作。
这3路气路有先后动作次序依次为“UnderCut1”、“Undercut 2”、“Clamp”,可根据需要选择是否使用。
此外还有一路单向气路提供剪切浇口,在1300T设备上增加汽缸,也可作为另一个轴方向的旋转功能使用。
2.机械手对质量的影响机械手对产品质量的影响主要表现在:1、吸盘吸力过大,容易导致产品表面凸起。
2、感应开关可能碰伤产品表面。
3、取件夹子可能碰伤产品。
4、吸盘位置发生相对移动,划伤产品。
5、取件周期过长,导致生产周期偏长。
6、产品碰撞设备,产品损伤。
7、吸盘或抓手位置在产品某些部位产生痕迹,造成缺陷无法判断。
第二部分:注塑工艺一、干燥使用热风干燥机对原材料进行干燥,通常要求注塑用的PP+EPDM的粒子含水率低于0.03%。
造成含水率无法满足这个指标的可能性,在于干燥温度或干燥时间无法满足要求。
除去设备故障因素外,可能造成的原因在于:干燥设备的容量无法满足生产的要求,随着生产的延续,干燥时间越来约少,干燥温度越来越低。
这样容易造成的产品缺陷主要为产品表面容易出现气泡、银纹、缩瘪等缺陷。
干燥不足还会引起,产品的机械性能下降。