共晶金锡焊料焊接的处理和可靠性问题
共晶焊资料

共晶焊资料(转引)焊接2009-09-02 18:22:56 阅读593 评论0 字号:大中小2007-09-12 09:47:281 引言共晶焊技术在电子封装行业得到广泛应用,如芯片与基板的粘接、基板与管壳的粘接、管壳封帽等等。
与传统的环氧导电胶粘接相比(表1),共晶焊接具有热导率高、电阻小、传热快、可靠性强、粘接后剪切力大的优点,适用于高频、大功率器件中芯片与基板、基板与管壳的互联。
对于有较高散热要求的功率器件必须采用共晶焊接。
共晶焊是利用了共晶合金的特性来完成焊接工艺的。
共晶合金具有以下特性:(1)比纯组元熔点低,简化了熔化工艺;(2)共晶合金比纯金属有更好的流动性,在凝固中可防止阻碍液体流动的枝晶形成,从而改善了铸造性能;(3)恒温转变(无凝固温度范围)减少了铸造缺陷,如偏聚和缩孔;(4)共晶凝固可获得多种形态的显微组织,尤其是规则排列的层状或杆状共晶组织,可成为优异性能的原位复合材料(in-situ composite)。
共晶是指在相对较低的温度下共晶焊料发生共晶物熔合的现象,共晶合金直接从固态变到液态,而不经过塑性阶段。
其熔化温度称共晶温度。
"真空/可控气氛共晶炉"是国际上近几年推出的新设备,可实现器件的各种共晶工艺;共晶时无需使用助焊剂,并具有抽真空或充惰性气体的功能,在真空下共晶可以有效减少共晶空洞;如辅以专用的夹具,则能实现多芯片一次共晶。
我所根据新的工艺要求,研制出2种型号真空/可控气氛共晶炉,如图1所示。
GJL-2023B是PLC(可编程控制器)控制,在温控仪表上设定温度曲线,气体流量控制手动调节。
GJL-225是工控机控制,在液晶显示屏上设定工艺曲线及气体流量等工艺参数,由控制软件自动完成工艺过程。
2 真空/可控气氛共晶炉主要应用领域2.1 IC芯片焊接IC芯片与基板的焊接是共晶焊的主要应用方向。
通常使用金锡(AlaSn 80/20)、金硅(AuSi)、金锗(AuGe)等合金材料的焊片将芯片焊接到基板(载板)上,合金焊片放在IC与基板问的焊盘上。
共晶焊接工艺需考虑的因素
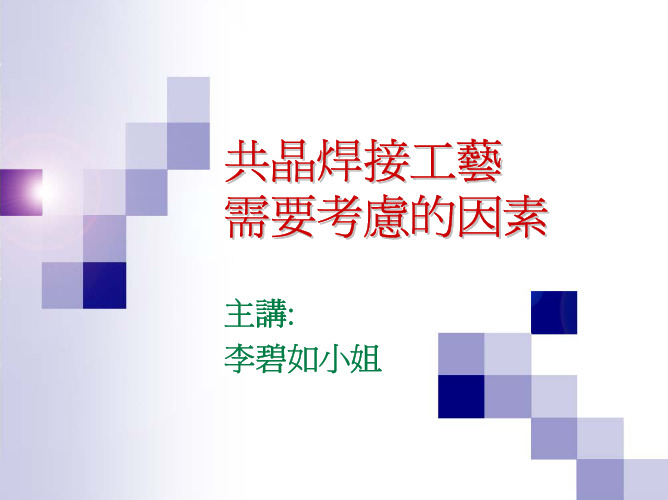
粗糙的表面
平滑的表面
選擇材料
晶片
共晶點 < 支架/陶瓷板 最高可承受的溫度
支架
塑膠材料 Tg > 共晶材料的共晶點 支架設計
堅固性
表面粗糙度 < 共晶材料的厚度
能力及挑戰
分享 1: 共晶
晶片: 底層鍍Sn 支架鍍銀; 塑膠材料 Tg ~281°C
找出塑膠材料的Tg
支架設計
支架設計
堅固性 ⇒ 晶片跟支架的接觸面
支架設計
固晶在不堅固的支架上, 晶片跟支架的接觸, 推力被影響
固晶在堅固的支架上, 良好的接觸提高推力
高推力
低推力
表面粗糙度
支架表面的粗糙度要比共晶材料的厚度還 要少, 否則共晶材料就不足夠填滿表面不平 的地方, 造成流動性差的情況
-3.s LSL 8
NOMINAL
7
6
5
4
3
2
1
0
0.10
0.15
0.20
0.25
0.30
0.35
0.40
0.45
+3.s
0.50
0.55
能力及挑戰
分享 2: 焊劑共晶
點印焊劑
LED 進回流爐之後
LED 在室溫固晶
LED 進回流爐之前
能力及挑戰
分享 2: 焊劑共晶
使用焊劑:
去除表面氧化物 幫助共晶材料 ( e.g. AuSn) 的流動
製程考慮
頂針痕深度
吸晶片力度及頂針速度 優化後吸晶/固晶力度
50g ± 5g
設定 1 2 3
吸晶/固晶力度 頂針速度 痕深度 (μm)
焊点可靠性之焊点寿命改善

焊点可靠性之焊点寿命改善提高SMT焊点可靠性的方法主要有以下四种:(1) 研制开发新型基板材料以减小陶瓷芯片载体与树脂基板之间的热膨胀系数差。
研究主要集中于印刷电路板材料,已经研制开发了42%Ni-Fe合金(CTE=5ppm/o C)、Cu-因瓦合金-Cu复合材料板(CTE=2.8~13ppm/o C)等新型基板材料,效果较好[41]。
但是由于新型材料制作工艺复杂、价格昂贵,其实用性受到很大限制,90年代起极少有此类研究见于文献。
(2) 提高软钎料合金自身的力学性能,向Sn-Pb共晶合金基体中加入微量合金元素以实现合金强化。
由于实际生产中需综合考虑成本、工艺性等多方面问题,对Sn-Pb基钎料合金而言,这方面的工作较少,主要是添加Ag[42]。
朱颖博士开发了Sn-Pb-RE系列钎料合金,不仅提高表面组装焊点热循环寿命2-3倍,而且在成本和工艺性方面均有很好的应用前景[43]。
近年来,随着环境保护呼声的日益提高,开发无铅钎料(Lead-Free Solder)成为了软钎焊材料研究的热点,HP公司的Glazer对此作了很好的综述[44],焦点在于新型无铅钎料合金在保证润湿性的前提下,其熔点要与现有工艺条件匹配且其力学性能要优于Sn-Pb共晶合金。
(3) 焊点形态优化设计。
作为承受载荷的结构件,不同的焊点形态将导致焊点内部不同的热应力-应变分布,从而导致不同的焊点热疲劳性能。
焊点形态优化设计包括两方面的内容:一是焊点形态预测,即在钎料量、焊点高度、焊盘几何、软钎焊规范等工艺参数确定的条件下,借助于焊点成型的数学物理模型计算出焊点的最终形态。
近年来提出了多种基于能量最小原理的焊点形态预测模型[45-47]。
二是优化设计,即何种焊点形态才具有最优的热疲劳性能。
优化判据的确定是一个涉及到焊点失效机制的理论问题,目前还远没有—1 —解决,现有的优化设计工作的优化判据均是不同形态焊点的热疲劳寿命试验数据[48]。
机械设计论文 金锡真空共晶焊仿真分析
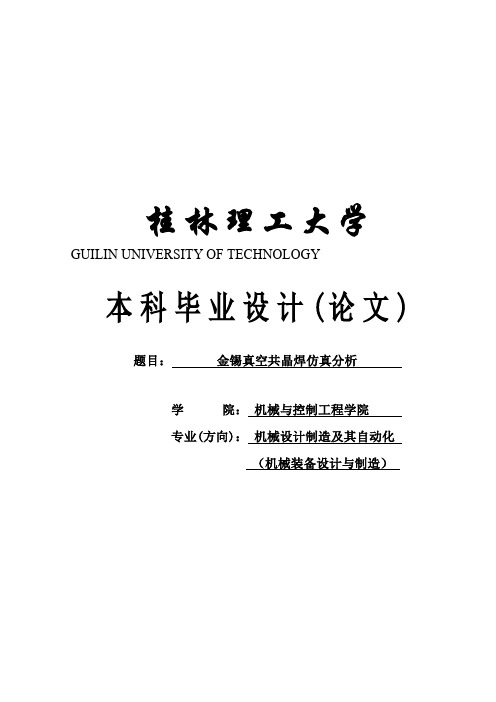
桂林理工大学GUILIN UNIVERSITY OF TECHNOLOGY本科毕业设计(论文) 题目:金锡真空共晶焊仿真分析学院:机械与控制工程学院专业(方向):机械设计制造及其自动化(机械装备设计与制造)摘要共晶焊是微电子组装技术中的一种重要焊接工艺,在混合集成电路中彰显出了较重要的地位。
芯片、焊片、基板共晶焊接后,由于芯片、焊片以及基板的热膨胀系数不相同而导致焊片内部产生热应力,甚至导致焊接失效,因此焊片焊接冷却后的应力分析是焊片可靠性预测的基础。
本文首先对芯片、焊片、基板共晶焊接后,冷却的热应力进行了仿真分析,运用ANSYS有限元软件,分别分析焊片厚度、基板厚度、芯片厚度、对流系数和冷却温度对应力的影响;其次针对影响共晶焊接冷却应力的五个因素,建立了三水平五因子的正交试验表,共18个组合,并对各因素因子组合进行了仿真分析,得到了各因素对共晶焊接冷却应力影响的程度和顺序。
所得结果对焊片、基板、芯片厚度对共晶焊冷却应力的影响提供理论依据,对各工艺参数及尺寸参数的选择具有一定指导意义,具有一定的工程应用价值。
关键词:共晶焊;仿真分析;正交试验;应力Simulated analysis of vacuum AuSn eutectic solder weldingAbstract:Eutectic solder is an important welding process in microelectronics assembly technology, highlighted in the hybrid integrated circuit more important position. After soldering,because of chip, welding,substrate,thermal expansion coefficient’s different ,welding thermal stress is generated, and even lead to welding failure, so the stress of the weld after welding cooling analysis is the basis of the welding piece of reliability prediction.This paper research the chip, welding pieces, substrate eutectic after welding, the thermal stress of cooling simulation analysis, the finite element software ANSYS, respectively analyzing welding slice thickness, substrate thickness, chip thickness, convection coefficient and the cooling temperature effect on the stress; Secondly according to the five factors influencing the eutectic welding stress of cooling, the establishment of a three level five factor orthogonal test table, a total of 18 combinations, and factor combination of various factors on the simulation analysis, obtained the impact of various factors on the eutectic welding cooling stress degree and order. Results on welding , substrate, chip thickness of eutectic welding cooling stress provide theoretical basis for the influence of the various process parameters and the selection of size parameters have certain guiding significance, has certain engineering application value.Key words:eutectic;simulated analysis;orthogonal test table;stress目录摘要 (I)1绪论 (1)1.1研究的目的和意义 (1)1.2相关技术概述 (1)1.2.1金锡真空共晶焊简述 (1)1.2.2真空共晶设备 (2)1.3金锡真空共晶焊的研究现状 (3)1.4研究内容 (4)2 相关理论基础 (5)2.1 热传递的基本方式 (5)2.2 热应力理论 (6)2.3 正交试验法原理 (6)2.4 ANSYS14.5热分析的方法 (7)2.4.1 ANSYS的简介 (7)2.4.2 ANSYS14.5技术新特点 (8)2.4.3 ANSYS热分析原理 (8)2.4.4 瞬态热分析步骤 (8)3 金锡共晶焊应力仿真分析 (10)3.1 金锡共晶焊三维实体有限元模型的建立 (10)3.1.1 选择单元类型 (10)3.1.2 定义材料性能参数 (10)3.1.3 三维模型的建立与网格划分 (11)3.2 施加载荷 (12)3.3 求解与后处理 (12)3.4 共晶焊焊片的热应力耦合分析 (13)3.4.1 施加载荷与约束 (13)3.4.2 热应力耦合仿真结果 (13)4 基于正交试验的共晶焊应力分析 (15)4.1 共晶焊应力仿真的试验设计 (15)4.1.1 试验目的 (15)4.1.2 试验内容 (15)4.2 共晶焊片应力仿真的试验结果分析 (22)4.2.1 焊片厚度对焊片最大应力值影响 (22)4.2.2 基板厚度对焊片最大应力值影响 (22)4.2.3 芯片厚度对焊片最大应力值影响 (22)4.2.4 对流系数对焊片最大应力值影响 (22)4.2.5冷却温度对焊片最大应力值影响 (22)4.2.6各因素的影响顺序 (23)5 结论 (24)致谢 (25)参考文献 (26)1绪论1.1研究的目的和意义随着集成电路向着低成本方向发展,对芯片焊接要求具有高性能、高密度、高可靠性特点并且要小型化,基板或壳体与芯片互连,主要有共晶焊接和导电胶粘接两种方法。
金锡共晶温度曲线

金锡共晶,也称为AuSn20,是一种含有AuSn(δ)和Au5Sn(ζ)两相的低温共晶贵金属焊料。
当金的质量分数为80%,锡为20%时,其共晶反应温度较低,约为278℃,且在无需助焊剂的情况下即可与金层直接焊接。
该焊料的特点是钎焊温度适中、高强度、低粘滞性,因此在电子封装中常用作芯片的焊接材料,也可用于高可靠气密封装中。
温度是影响金锡合金焊料共晶形貌的重要因素。
随着温度的升高,金锡合金焊料的共晶结构会变得更加致密,晶粒细化,共晶面积增加,共晶比例增大,且枝晶的生长速度也随之加快。
此外,合金中存在的纳米晶也会影响共晶形貌。
在实际应用中,金锡合金的熔点在共晶温度附近对成分非常敏感。
当金的重量比大于80%时,随着金的增加,熔点会急剧提高。
在焊接过程中,镀金层的金可能会侵入焊料,导致熔点变化。
因此,焊接参数需要优化。
通常情况下,AuSn (80:20)合金焊料在焊接时所施加的温度应使焊料有足够的流动性和润湿性,真空共晶回流炉的峰值温度通常选在约350℃,焊接时间为2-4分钟,成品率可达98%以上。
锡焊过程中遇到的问题及解决方法
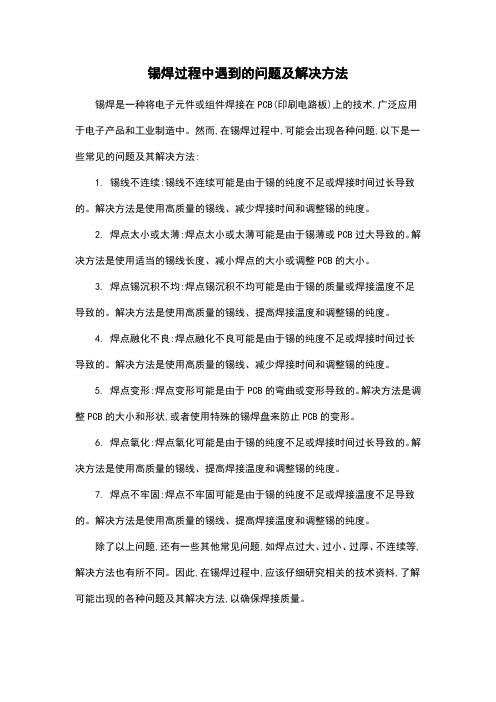
锡焊过程中遇到的问题及解决方法
锡焊是一种将电子元件或组件焊接在PCB(印刷电路板)上的技术,广泛应用于电子产品和工业制造中。
然而,在锡焊过程中,可能会出现各种问题,以下是一些常见的问题及其解决方法:
1. 锡线不连续:锡线不连续可能是由于锡的纯度不足或焊接时间过长导致的。
解决方法是使用高质量的锡线、减少焊接时间和调整锡的纯度。
2. 焊点太小或太薄:焊点太小或太薄可能是由于锡薄或PCB过大导致的。
解决方法是使用适当的锡线长度、减小焊点的大小或调整PCB的大小。
3. 焊点锡沉积不均:焊点锡沉积不均可能是由于锡的质量或焊接温度不足导致的。
解决方法是使用高质量的锡线、提高焊接温度和调整锡的纯度。
4. 焊点融化不良:焊点融化不良可能是由于锡的纯度不足或焊接时间过长导致的。
解决方法是使用高质量的锡线、减少焊接时间和调整锡的纯度。
5. 焊点变形:焊点变形可能是由于PCB的弯曲或变形导致的。
解决方法是调整PCB的大小和形状,或者使用特殊的锡焊盘来防止PCB的变形。
6. 焊点氧化:焊点氧化可能是由于锡的纯度不足或焊接时间过长导致的。
解决方法是使用高质量的锡线、提高焊接温度和调整锡的纯度。
7. 焊点不牢固:焊点不牢固可能是由于锡的纯度不足或焊接温度不足导致的。
解决方法是使用高质量的锡线、提高焊接温度和调整锡的纯度。
除了以上问题,还有一些其他常见问题,如焊点过大、过小、过厚、不连续等,解决方法也有所不同。
因此,在锡焊过程中,应该仔细研究相关的技术资料,了解可能出现的各种问题及其解决方法,以确保焊接质量。
共晶焊接工艺
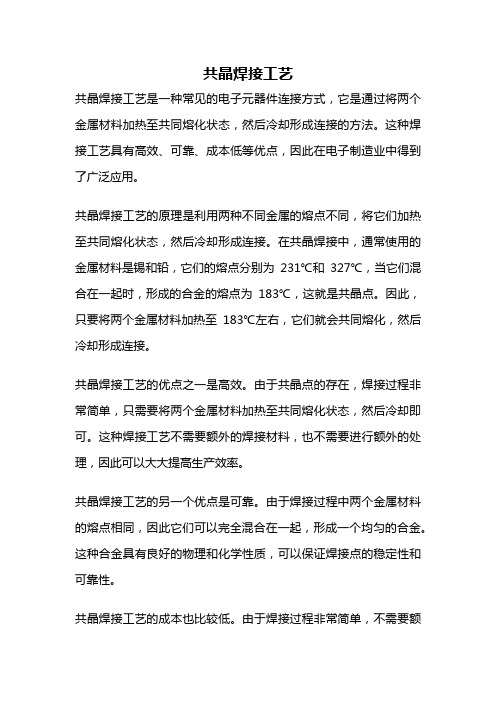
共晶焊接工艺共晶焊接工艺是一种常见的电子元器件连接方式,它是通过将两个金属材料加热至共同熔化状态,然后冷却形成连接的方法。
这种焊接工艺具有高效、可靠、成本低等优点,因此在电子制造业中得到了广泛应用。
共晶焊接工艺的原理是利用两种不同金属的熔点不同,将它们加热至共同熔化状态,然后冷却形成连接。
在共晶焊接中,通常使用的金属材料是锡和铅,它们的熔点分别为231℃和327℃,当它们混合在一起时,形成的合金的熔点为183℃,这就是共晶点。
因此,只要将两个金属材料加热至183℃左右,它们就会共同熔化,然后冷却形成连接。
共晶焊接工艺的优点之一是高效。
由于共晶点的存在,焊接过程非常简单,只需要将两个金属材料加热至共同熔化状态,然后冷却即可。
这种焊接工艺不需要额外的焊接材料,也不需要进行额外的处理,因此可以大大提高生产效率。
共晶焊接工艺的另一个优点是可靠。
由于焊接过程中两个金属材料的熔点相同,因此它们可以完全混合在一起,形成一个均匀的合金。
这种合金具有良好的物理和化学性质,可以保证焊接点的稳定性和可靠性。
共晶焊接工艺的成本也比较低。
由于焊接过程非常简单,不需要额外的焊接材料和处理,因此成本相对较低。
此外,共晶焊接工艺可以在较低的温度下进行,这可以减少能源消耗和生产成本。
尽管共晶焊接工艺具有许多优点,但它也存在一些缺点。
首先,由于焊接过程中使用的金属材料是锡和铅,这两种金属都是有毒的。
因此,在焊接过程中需要采取一些措施,以确保工人的安全和环境的保护。
其次,共晶焊接工艺只适用于某些特定的金属材料,对于其他材料可能不适用。
总的来说,共晶焊接工艺是一种高效、可靠、成本低的电子元器件连接方式。
它的原理是利用两种不同金属的熔点不同,将它们加热至共同熔化状态,然后冷却形成连接。
尽管它存在一些缺点,但在电子制造业中仍然得到了广泛应用。
共晶金锡焊料焊接的处理和可靠性问题

共晶金锡焊料焊接的处理和可靠性问题摘要:因为传统铅锡焊料和无铅焊料强度不足、砍蠕变能力差以及其他的本身缺陷,共晶金锡焊料已经替代它们广泛用于高可靠和高功率电路中,包括使用在混合电路、MEM、光电开关、LEDs、激光二极管和无线电装置。
金锡焊料焊接中可以避免使用组焊剂,尤其可以减少污染和焊盘的腐蚀。
虽然使用金锡焊料有很多优点,但材料的性能和焊接工艺工程仍需研究。
前言:由于共晶金锡焊料具有优良的机械和热传导性能(特别是强度和抗蠕变性)以及不需组焊剂可以很好的再流的特性,共晶AuSn被广泛应用于高温和高可靠性的电路中。
与之对比其他无铅和传统的铅锡共晶焊料却有着大量的问题:焊接时需要的组焊剂造成了焊接焊盘的腐蚀,同时残杂也会危害EMES、光电电路和密封封装(组焊剂一般在密封电路中被禁止使用)。
在光学电路中焊料的过度蠕变或应力松弛的积累会导致阵列的退化。
低强度低热传导率(尽管这个问题被夸大了,事实上热传导率还需要考虑大焊接焊料的厚度)共晶金锡焊料已经得到了广泛应用:如MEMS光开关等微电子和光电子学中使用的倒装芯片;光纤附件; GaAs和InP激光二极管;密封包装;和射频器件等。
AuSn的焊接已证明可靠性可以达到30多年,是因为其焊接中再流过程可以产生重复、无空洞以及无缺陷的焊接。
本文回答了很多公司关于焊接设计、焊接材料组合以及再流焊技术发展等问题。
相图我们可以从金锡焊料的二元相图去认识很多共晶金锡焊料焊接的关键问题,如图1所示,焊料中富金时,液相线下降非常迅速,在常温下有大量的“线性”化合物。
当使用金锡焊料焊接镀金层时,焊接温度必须超过280摄氏度,因为只有达到这个焊接问题,镀层里的金元素才可以扩散或融入到焊料中。
这样可以产生两个优点:在这个温度下第二次再流不会损坏到焊料;更高的温度也可以产生更大的抗蠕变性。
然而,焊接后中间的焊料很难再次起到焊接作用,因为即使两个焊接界面可以分开,残留下焊接时形成的金属间化合物都会阻止再流。
锡焊过程中遇到的问题及解决方法
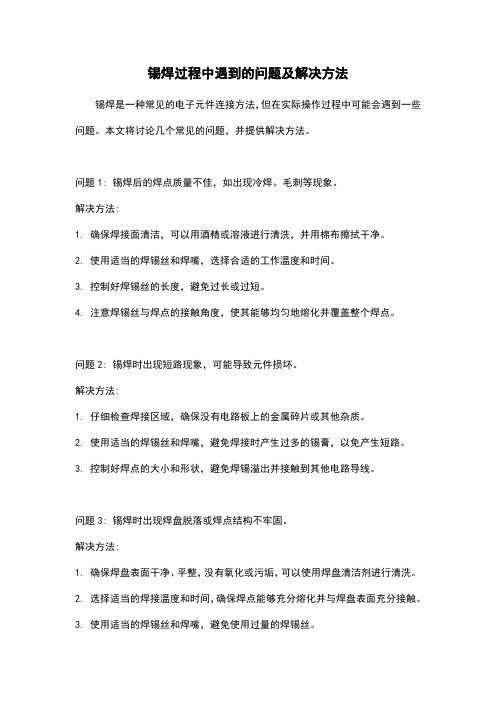
锡焊过程中遇到的问题及解决方法锡焊是一种常见的电子元件连接方法,但在实际操作过程中可能会遇到一些问题。
本文将讨论几个常见的问题,并提供解决方法。
问题1: 锡焊后的焊点质量不佳,如出现冷焊、毛刺等现象。
解决方法:1. 确保焊接面清洁,可以用酒精或溶液进行清洗,并用棉布擦拭干净。
2. 使用适当的焊锡丝和焊嘴,选择合适的工作温度和时间。
3. 控制好焊锡丝的长度,避免过长或过短。
4. 注意焊锡丝与焊点的接触角度,使其能够均匀地熔化并覆盖整个焊点。
问题2: 锡焊时出现短路现象,可能导致元件损坏。
解决方法:1. 仔细检查焊接区域,确保没有电路板上的金属碎片或其他杂质。
2. 使用适当的焊锡丝和焊嘴,避免焊接时产生过多的锡膏,以免产生短路。
3. 控制好焊点的大小和形状,避免焊锡溢出并接触到其他电路导线。
问题3: 锡焊时出现焊盘脱落或焊点结构不牢固。
解决方法:1. 确保焊盘表面干净、平整,没有氧化或污垢,可以使用焊盘清洁剂进行清洗。
2. 选择适当的焊接温度和时间,确保焊点能够充分熔化并与焊盘表面充分接触。
3. 使用适当的焊锡丝和焊嘴,避免使用过量的焊锡丝。
4. 控制好焊接压力和速度,确保焊点能够均匀地涂覆在焊盘上。
问题4: 锡焊时出现焊接位置不准确或焊点位置偏移。
解决方法:1. 在焊接前进行焊点位置的标记,可以使用标尺或模板等工具。
2. 确保焊点周围没有杂物或障碍物,以免影响焊接的准确性。
3. 控制好焊锡丝的长度和形状,避免过长或过短。
4. 在焊接过程中保持手的稳定性,使用辅助工具如放大镜或显微镜等,以确保焊点的准确性。
总结起来,锡焊过程中遇到的问题主要包括焊点质量不佳、短路现象、焊盘脱落和焊点位置偏移等。
通过保持焊接面的清洁、选择适当的焊锡丝和焊嘴、控制好焊接温度和时间、调整焊点大小和形状等方法,可以解决这些问题,提高焊接质量。
焊锡问题点解决方案

锡焊工程的不良原因分析及改善对策(一)1.短路(SHORT)焊接设计不当,可由圆型焊垫改为椭圆形。
加大点与点之间的距离。
零件方向设计不当,如S0IC的脚如与锡波平行,便易短路,修改零件方向,使其与锡波垂直.自动插件弯脚所致,由于PCB规定线脚的长度在2mm以下(无短路危险时)及担心弯脚角度太大时零件会掉,故因此造成短路,需将焊点离开线路2mm以上.基板孔太大.钖与孔中穿透至基板的上侧而造成短路,故需缩小孔径至下影响零件装插的程度。
自动插件时,残留的零件脚太长,需限制在2mm以下.锡炉温度太低。
钖无法迅速滴回锡槽,需调高锅炉温度.轴送带速度太慢,锡无法快速滴回,需调快轴送带速度.板面的可焊性不佳,将板面清洁。
基板中玻璃材料溢出,在焊接前检查板面是否有玻璃物突出.阻焊膜失效,检查适当的阻焊膜和使用方式.板面污染,将板面清洁。
2.针孔及气孔(PINHOLES AND BLOwHOLES)外表上,针孔及气孔的不同在于针孔的直径较小,现于表面.可看到底部。
针孔及气孔都表现为焊点中有气泡.只是尚未变大王表层,大部分都发生在基板底郎,当底部的气泡完全扩散爆开前已冷凝时,即形成了针孔或气孔。
形成的原因如下:基板或零件的线脚上沾有有机污染物.此类污染材料来自自动插件面,零件存放及贮存不良因素。
用普通的溶剂即可轻易的去除此类污染物,但遇sILICOK0II类似含有SILICON的产品则较困难。
如发现问题的造成是因为SILICON OIL,则须考虑改变润滑油或脱膜剂的来源。
基板含有电铍溶液和,类似材料所产生之水气,如果基板使用较廉价的材料,则有可能吸入此类水气,焊锡时产生足够的热,将溶液气化而造成气孔装配前将基板在烤箱中烘烤,可以改善此间题。
基板储存太多或包装不当,吸收附近环境的水氟,故装配前需先烘烤。
助焊剂活性不够,助焊剂润湿不良.也会造成针孔及氧孔.助焊剂槽中含有水份,需定期更换助焊剂。
助焊剂水份过多,也是造成针孔及气孔的原因,应更换助焊剂.发泡及空压机压缩中含有过多的水份,需加装滤水器,并定期排水.预热温度过低,无法蒸发水氟或溶剂,基板一旦进入锡炉,瞬间与高温接解,而产生爆裂,故需调高预热温度.3.吃锡不良(POOR WETTING)现象为线路板的表面有部分未沾到锡,原因为:表面附有油脂、杂质氧化等,可以溶解洗净。
金锡合金钎料
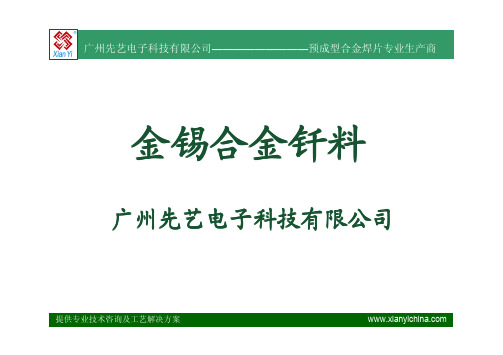
一、行业背景随着电-光之间相互转化器件的大规模推广,尤其是基于电致发光的大功率LED和高功率激光器,以及基于光通信原理的Intel光脑技术,都要求光电子封装材料和工艺进行变革。
两方面的特殊要求使得AuSn20成为光电子封装关注的焦点。
首先,针对大功率光电器件的高导热需要,AuSn20共晶的热导率是57w/m·K,热导率为焊料中最高。
其次,可靠性和微区加工的需要,AuSn20 共晶中金含量80wt%,共晶点为280℃,无疑它的可靠性极佳。
这些特性使得它在大功率LED,电劢汽车和激光器等微电子领域,以及光通信和光电器件的戓略领域中得到广泛应用。
提供专业技术咨询及工艺解决方案预成型铸造拉拨轧制法叠层冷轧复合法预合金化法铸造拉拨轧制法需要添加第三组元Pd或Pt,影响了金锡合金的纯度,焊接性能也会受到影响难以控制金和锡的反应量,未合金化的金和锡都会对焊料产生不良影响不用添加第三组元,成分均匀,焊接性能良好提供专业技术咨询及工艺解决方案提供专业技术咨询及工艺解决方案Au-Sn二元合金相图1、高强度焊料的焊接强度可以直接决定焊接质量。
高的焊接强度能达到高的可靠性,相反焊接强度不够,则可靠性比较差。
AuSn20作为共晶合金,有着共晶合金的普遍特征:细小均匀的晶格,从而有着很高的强度。
提供专业技术咨询及工艺解决方案2、良好的漫流性漫流性是一种焊料在熔化后的流动能力大小的表征,良好的漫流性必须有着较小的熔化范围以及在焊接温度时较小的黏度,只有这样,焊料在焊接时才能迅速完全熔化为液态,在焊盘表面铺展开来。
由于金锡合金焊料一般都是共晶成分,在280℃熔点附近很小的一个范围内完全熔化成流动性很好的液态,因而具有很小的粘滞性,能够很迅速的铺展开来,漫流性很好。
提供专业技术咨询及工艺解决方案3、抗热疲劳由于金锡合金焊料是共晶成分,组织细小,焊料强度较高,在接近熔点的时候依然保持有一定的强度,同时此种焊料抗裂纹扩展能力也很强,所以金锡共晶合金的抗蠕变性能和抗疲劳性能也很优良。
经典:锡焊原理与焊点可靠性分析-经典

波峰焊——波峰焊时,由于表面张力与润湿力的方向 相反,因此表面张力是不利于润湿的因素之一。
•SMD波峰焊时表面张力造成阴影效应
粘度与表面张力
• 熔融合金的粘度与表面张力是焊料的重要性能。 • 优良的焊料熔融时应具有低的粘度和表面张力,以增 加焊料的流动性及被焊金属之间的润湿性。 • 锡铅合金的粘度和表面张力与合金的成分密切相关。
锡焊过程锡焊过程焊接过程是焊接金属表面助焊剂焊接过程是焊接金属表面助焊剂熔融焊料和空气等之间相互作用的复杂过程熔融焊料和空气等之间相互作用的复杂过程表面清洁焊件加热熔锡润湿扩散结合层冷却后形成焊点物理学物理学润湿黏度毛细管现象热传导扩散溶解化学化学助焊剂分解氧化还原电极电位助焊剂分解氧化还原电极电位冶金学冶金学合金合金层金相老化现象合金合金层金相老化现象电学电学电阻热电动势电阻热电动势材料力学材料力学强度拉力剥离疲劳应力集中强度拉力剥离疲劳应力集中焊接过程中焊接金属表面母材焊接过程中焊接金属表面母材以以cucu为例助焊剂熔融焊料之间相互作用助焊剂熔融焊料之间相互作用助焊剂与母材的反应助焊剂与母材的反应11松香去除氧化膜松香去除氧化膜松香的主要成分是松香酸松香的主要成分是松香酸融点为7474
由于液体内部分子受到四周分子的作用力是对 称的,作用彼此抵消,合力=0。但是液体表面分子 受到液体内分子的引力大于大气分子对它的引力, 因此液体表面都有自动缩成最小的趋势。
熔融焊料在金属表面也有表面张力现象。
大大气
液体表面分子受液体内分子的引力>大气分子引力
液体内部分子受力合力=0
表面张力与润湿力
放大1,000倍的QFP引脚焊点横截面图
三. 焊点可靠性分析
影响焊点强度的主要因素: (1)金属间合金层(金属间结合层)质量与厚度 (2)焊接材料的质量 (3)焊料量 (4)PCB设计
共晶锡锌合金焊料的性能及焊接特性

共晶锡锌合金焊料的性能及焊接特性J.Villain,U.Corradi,Chr.Weippert奥格斯堡应用技术大学德国奥格斯堡86161,Baumgartnerstr.16Villain@lrz.Ui3.i一=uenchen.de摘要:通过共晶锡锌合金的张力与蠕变性能测试,我们能够得出这种焊料与锡银合金及SAC合金(SAC--锡,银,铜合金)在机械性能方面的不同。
试验显示,锡锌焊料的强度大于含铅焊料及其他在研究范围之内的无铅焊料-其抗蠕变性也优于锡铅合金。
微1纳米硬度测量结果解释了共晶锡锌台金具备高强度的原因。
在回流焊特别是波峰焊过程中.高温是获得可湿性及高可靠性焊点的必要因素。
焊接过程结束后,锡锌焊料合金会表现出消光加工的特性,焊点也将具备较高的强度,但温度循环后其强度减少幅度会大于其他测试合金,不过其临界强度总是大干临界值。
抗腐蚀性测试取得了较为满意的结果。
根据金相剖面图可以看出这种台金与其他无铅焊料合金在结构上的不同。
有时铝层未完全溶解于焊料。
如果可靠性测试取得较好的效果.则锡锌焊料合金可被用于电子学领域。
关键词:无铅焊料合金,共晶锡锌焊料,可靠性,回流焊接,波峰焊接,纳米硬度介绍目前人们已开发出了数种无铅焊料,这些材料可在不同的产品及工作温度条件下取代含铅焊料。
研究人员己对锡银、锡银铜以及锡锌合金及其可靠性进行了深入的研究。
研究结果显示.无铅焊料在通常情况下总是具有较高的熔点和中等可湿性。
添加其他元素(如金和镍)会使无铅焊料的溶解性优于含铅焊料。
我们将锡锌台金研究取得的所有结果与SNAG3.5、Sn63Pb37以及SnA93.5Cu0.7Bi2焊料合金进行了对比。
锡锌合金焊料表1列出了某些锡锌二元及三元焊料合金【1】,图1是锡锌合金相团2】。
上述大多数合金都与其共晶合金结构相近。
焊料中的铋能够降低台金熔点,但与铅混合后(如为电子元件镀敷金属)将形成低熔点共晶结构,从而大幅度削弱焊点可靠性。
金锡钎料

金锡焊料及其在微电子封装中的应用张春杨(西安电子科技大学微电子学院140712班)摘要:在功率放大器微电子器件制造工艺中,硅芯片在工作中会产生大量的热,故其结构需要一个良好的散热通道。
金基钎料比锡基或铅基钎料有较优良的热导性和较高的熔点,同时具有较高的抗热疲劳性能,因此,金基钎料是性能优良的微电子器件封装用材料。
AuSn20 钎料除可用于芯片与电路基材的连接外,还可广泛用于多种高可靠电路气密封装。
本文介绍了Au80%Sn20%焊料的基本物理性能。
同时介绍这种焊料在微电子、光电子封装中的应用。
关键词:金锡合金;钎料;微电子封装;光电子封装Abstract:In the power amplifier manufacturing process during microelectronics devices, the silicon chip will generate a lot of heat in the work, so the structure needs a good cooling channel. Gold-based solder has a better thermal conductivity and high melting point than tin-based solder or lead-based solder,and at the same time it has a high thermal fatigue resistance,therefore, gold-based solder is excellent microelectronics device packaging material.AuSn20 solder can be used to connect chips and circuit substrates, it can also be used in a variety of high-reliability circuit hermetic package.This article describes the physical properties of eutectic Au/Sn Solder alloy and its applications for rnicroelectronics and optoelectronis packagings.Key words:Au Sn Solder alloy;Solder;Microelectronics Packaging;Optoelectronic Packaging 1.前言钎焊是组装电子产品的一项重要技术。
共晶焊技术
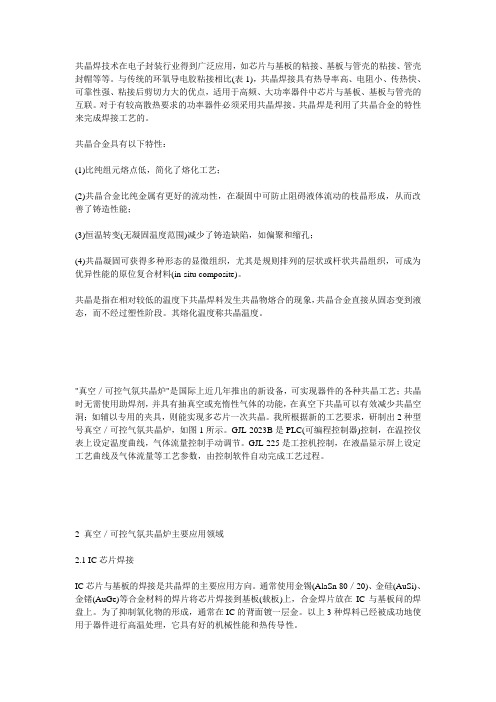
共晶焊技术在电子封装行业得到广泛应用,如芯片与基板的粘接、基板与管壳的粘接、管壳封帽等等。
与传统的环氧导电胶粘接相比(表1),共晶焊接具有热导率高、电阻小、传热快、可靠性强、粘接后剪切力大的优点,适用于高频、大功率器件中芯片与基板、基板与管壳的互联。
对于有较高散热要求的功率器件必须采用共晶焊接。
共晶焊是利用了共晶合金的特性来完成焊接工艺的。
共晶合金具有以下特性:(1)比纯组元熔点低,简化了熔化工艺;(2)共晶合金比纯金属有更好的流动性,在凝固中可防止阻碍液体流动的枝晶形成,从而改善了铸造性能;(3)恒温转变(无凝固温度范围)减少了铸造缺陷,如偏聚和缩孔;(4)共晶凝固可获得多种形态的显微组织,尤其是规则排列的层状或杆状共晶组织,可成为优异性能的原位复合材料(in-situ composite)。
共晶是指在相对较低的温度下共晶焊料发生共晶物熔合的现象,共晶合金直接从固态变到液态,而不经过塑性阶段。
其熔化温度称共晶温度。
"真空/可控气氛共晶炉"是国际上近几年推出的新设备,可实现器件的各种共晶工艺;共晶时无需使用助焊剂,并具有抽真空或充惰性气体的功能,在真空下共晶可以有效减少共晶空洞;如辅以专用的夹具,则能实现多芯片一次共晶。
我所根据新的工艺要求,研制出2种型号真空/可控气氛共晶炉,如图1所示。
GJL-2023B是PLC(可编程控制器)控制,在温控仪表上设定温度曲线,气体流量控制手动调节。
GJL-225是工控机控制,在液晶显示屏上设定工艺曲线及气体流量等工艺参数,由控制软件自动完成工艺过程。
2 真空/可控气氛共晶炉主要应用领域2.1 IC芯片焊接IC芯片与基板的焊接是共晶焊的主要应用方向。
通常使用金锡(AlaSn 80/20)、金硅(AuSi)、金锗(AuGe)等合金材料的焊片将芯片焊接到基板(载板)上,合金焊片放在IC与基板问的焊盘上。
为了抑制氧化物的形成,通常在IC的背面镀一层金。
金锡共晶焊接

金锡共晶焊接金锡共晶焊接是一种常见的电子元器件连接技术,它的历史可以追溯到20世纪60年代。
下面将从金锡共晶焊接的起源、发展、应用和未来展望四个方面进行阐述。
一、起源金锡共晶焊接最早起源于美国,当时电子工业正在快速发展,需要一种高效、可靠的元器件连接技术。
20世纪60年代初,美国贝尔实验室的研究人员发现,在金和锡的共晶点(即金和锡的混合物)中,金和锡的比例为80:20时,具有很好的焊接性能。
于是,他们开始研究金锡共晶焊接技术,并在1969年获得了专利。
二、发展金锡共晶焊接技术在20世纪70年代得到了广泛应用,特别是在电子工业中。
它的优点是焊点强度高、导电性好、耐腐蚀、不易氧化等。
同时,金锡共晶焊接技术也不断改进和发展。
例如,为了提高焊点的可靠性,研究人员开始添加其他元素,如银、铜、镍等,形成了多种共晶焊料。
此外,还出现了一些新的焊接方式,如反向焊接、双面焊接等。
三、应用金锡共晶焊接技术在电子工业中得到了广泛应用。
它可以用于连接各种电子元器件,如集成电路、电容器、电阻器等。
此外,金锡共晶焊接技术还可以用于连接电路板和电子设备外壳等。
在汽车、航空航天、医疗器械等领域,金锡共晶焊接技术也有着重要的应用。
四、未来展望随着电子工业的不断发展,金锡共晶焊接技术也在不断改进和完善。
未来,金锡共晶焊接技术将更加智能化、自动化、绿色化。
例如,研究人员正在研发新型共晶焊料,以提高焊点的可靠性和耐用性。
同时,智能化的焊接设备也将更加普及,以提高生产效率和质量。
此外,绿色化的焊接技术也将受到更多关注,以减少对环境的影响。
总之,金锡共晶焊接技术是一种重要的电子元器件连接技术,它的发展历程充满了创新和进步。
未来,随着电子工业的不断发展,金锡共晶焊接技术也将不断完善和发展。
金锡焊料焊接工艺

金锡焊料焊接工艺
金锡焊料焊接工艺是一种常用的电子元器件连接方式,常见于电路板的焊接过程中。
金锡焊料是由金、锡和独特配方的助焊剂组成的,具有良好的焊接性能和电气导通性能。
金锡焊料的焊接工艺一般包括以下几个步骤:
1. 准备工作:首先需要清洁焊接表面,去除灰尘、油污等杂质,以确保焊接的可靠性。
同时,还需要准备好合适的焊锡丝和焊接工具。
2. 预热:将焊接的部件加热至一定温度,通常是150-300摄氏
度之间。
预热可以提高焊锡的流动性和润湿性,有助于焊接的质量。
3. 上锡:将预先剪好的焊锡丝放在焊接点上,然后使用加热工具(如电烙铁)加热焊接点和焊锡丝。
焊锡会熔化并润湿焊接表面,形成焊接点。
4. 焊接:在焊接点上保持一定的加热时间,使焊锡充分润湿和填充焊接表面的微观缺陷。
焊接时间通常控制在几秒到十几秒之间。
5. 冷却:焊接完成后,需要等待焊接点冷却固结。
如果立即移动或受力,可能会导致焊点断裂或焊接不牢固。
虽然金锡焊料的焊接工艺相对简单,但在实际操作中仍需注意
以下几点:
1. 控制焊接温度:过高的温度会引起焊接点熔化过大或烧坏周围元器件,而过低的温度则可能导致焊点不牢固。
2. 控制焊接时间:焊接时间太短会导致焊锡没有充分润湿并填充焊接表面的微观缺陷,而时间过长则可能烧坏周围元器件。
3. 确保焊接点质量:焊接完成后,需要对焊接点进行检查,确保焊点形状完整、焊锡光亮、无虚焊、冷焊等质量问题。
需要提醒的是,金锡焊料的使用需要注意安全,避免对人体和环境造成伤害。
在使用金锡焊料时,应戴上防护手套、护目镜等防护用具,确保工作环境通风良好。
半导体封装工艺中金锡共晶焊料性质和制备方法研究

1 金锡共晶焊料性质 金锡共晶焊料属于无铅硬焊料,其组分为 :Au80wt.%
SHI Chao
(China Electronic Technology Group Corporation thirteenth Institute,Shijiazhuang 050051,China)
Abstract :The eutectic gold–tin soldering material (Au80wt.%/Sn20wt%) which exhibits long-term reliability, high soldering strength, low erosion effects and suitable for step-soldering applicatons is widely received attention for packaging diode lasers. This paper described the characteristics and the composing state with gold–tin phase diagram. The different features and using fields of the important preparation methods including vaporization and electroplate were detailed summarized. It is recommended that the noticeable progress of forming gold–tin eutectic was made by cetc-13 which may favorable for the reliable packaging. Keywords: Semiconductor package;gold–tin soldering material;vaporization;electroplate
金锡焊料形态介绍
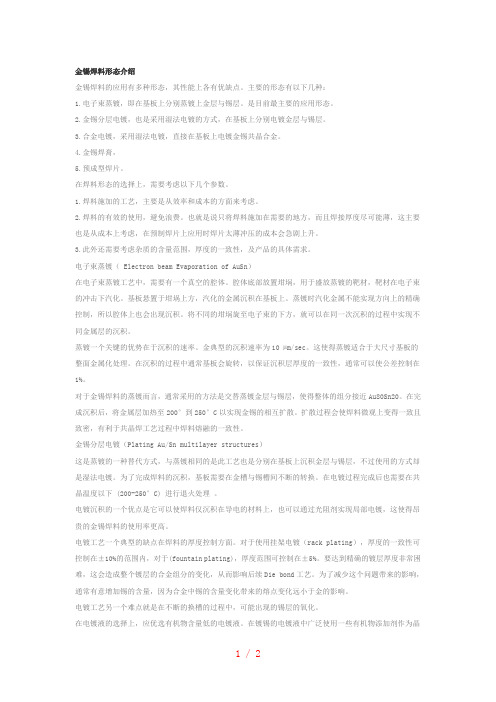
金锡焊料形态介绍金锡焊料的应用有多种形态,其性能上各有优缺点。
主要的形态有以下几种:1.电子束蒸镀,即在基板上分别蒸镀上金层与锡层。
是目前最主要的应用形态。
2.金锡分层电镀,也是采用湿法电镀的方式,在基板上分别电镀金层与锡层。
3.合金电镀,采用湿法电镀,直接在基板上电镀金锡共晶合金。
4.金锡焊膏,5.预成型焊片。
在焊料形态的选择上,需要考虑以下几个参数。
1.焊料施加的工艺,主要是从效率和成本的方面来考虑。
2.焊料的有效的使用,避免浪费。
也就是说只将焊料施加在需要的地方,而且焊接厚度尽可能薄,这主要也是从成本上考虑,在预制焊片上应用时焊片太薄冲压的成本会急剧上升。
3.此外还需要考虑杂质的含量范围,厚度的一致性,及产品的具体需求。
电子束蒸镀( Electron beam Evaporation of AuSn)在电子束蒸镀工艺中,需要有一个真空的腔体。
腔体底部放置坩埚,用于盛放蒸镀的靶材,靶材在电子束的冲击下汽化。
基板悬置于坩埚上方,汽化的金属沉积在基板上。
蒸镀时汽化金属不能实现方向上的精确控制,所以腔体上也会出现沉积。
将不同的坩埚旋至电子束的下方,就可以在同一次沉积的过程中实现不同金属层的沉积。
蒸镀一个关键的优势在于沉积的速率。
金典型的沉积速率为10 µm/sec。
这使得蒸镀适合于大尺寸基板的整面金属化处理。
在沉积的过程中通常基板会旋转,以保证沉积层厚度的一致性,通常可以使公差控制在1%。
对于金锡焊料的蒸镀而言,通常采用的方法是交替蒸镀金层与锡层,使得整体的组分接近Au80Sn20。
在完成沉积后,将金属层加热至200°到250°C以实现金锡的相互扩散。
扩散过程会使焊料微观上变得一致且致密,有利于共晶焊工艺过程中焊料熔融的一致性。
金锡分层电镀(Plating Au/Sn multilayer structures)这是蒸镀的一种替代方式,与蒸镀相同的是此工艺也是分别在基板上沉积金层与锡层,不过使用的方式却是湿法电镀。
金锡共晶焊接工艺
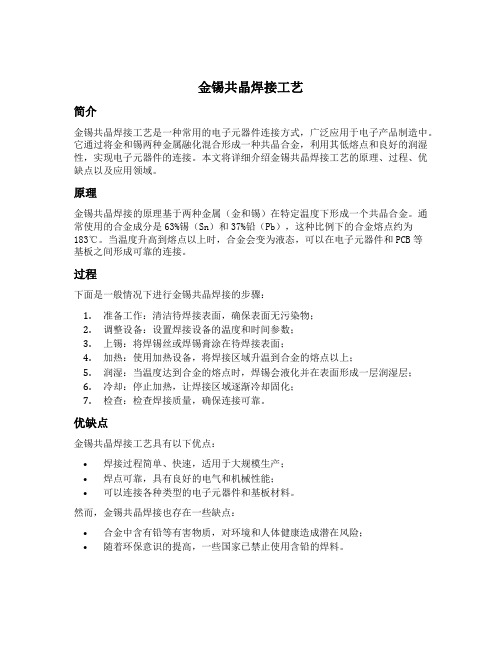
金锡共晶焊接工艺简介金锡共晶焊接工艺是一种常用的电子元器件连接方式,广泛应用于电子产品制造中。
它通过将金和锡两种金属融化混合形成一种共晶合金,利用其低熔点和良好的润湿性,实现电子元器件的连接。
本文将详细介绍金锡共晶焊接工艺的原理、过程、优缺点以及应用领域。
原理金锡共晶焊接的原理基于两种金属(金和锡)在特定温度下形成一个共晶合金。
通常使用的合金成分是63%锡(Sn)和37%铅(Pb),这种比例下的合金熔点约为183℃。
当温度升高到熔点以上时,合金会变为液态,可以在电子元器件和PCB等基板之间形成可靠的连接。
过程下面是一般情况下进行金锡共晶焊接的步骤:1.准备工作:清洁待焊接表面,确保表面无污染物;2.调整设备:设置焊接设备的温度和时间参数;3.上锡:将焊锡丝或焊锡膏涂在待焊接表面;4.加热:使用加热设备,将焊接区域升温到合金的熔点以上;5.润湿:当温度达到合金的熔点时,焊锡会液化并在表面形成一层润湿层;6.冷却:停止加热,让焊接区域逐渐冷却固化;7.检查:检查焊接质量,确保连接可靠。
优缺点金锡共晶焊接工艺具有以下优点:•焊接过程简单、快速,适用于大规模生产;•焊点可靠,具有良好的电气和机械性能;•可以连接各种类型的电子元器件和基板材料。
然而,金锡共晶焊接也存在一些缺点:•合金中含有铅等有害物质,对环境和人体健康造成潜在风险;•随着环保意识的提高,一些国家已禁止使用含铅的焊料。
应用领域金锡共晶焊接工艺广泛应用于电子产品制造中,包括但不限于以下领域:1.电子通信:手机、电脑、通信设备等;2.汽车电子:汽车控制系统、仪表板、导航装置等;3.家用电器:电视机、洗衣机、冰箱等;4.工业自动化:工控设备、机器人等。
结论金锡共晶焊接工艺是一种常用的电子元器件连接方式,具有简单快速、可靠性强的优点。
然而,由于合金中含有铅等有害物质,对环境和人体健康造成潜在风险,随着环保意识的提高,一些国家已禁止使用含铅的焊料。
因此,在实际应用中需要选择合适的焊接材料,并遵循相关环保法规。
- 1、下载文档前请自行甄别文档内容的完整性,平台不提供额外的编辑、内容补充、找答案等附加服务。
- 2、"仅部分预览"的文档,不可在线预览部分如存在完整性等问题,可反馈申请退款(可完整预览的文档不适用该条件!)。
- 3、如文档侵犯您的权益,请联系客服反馈,我们会尽快为您处理(人工客服工作时间:9:00-18:30)。
低强度
低热传导率(尽管这个问题被夸大了,事实上热传导率还需要考虑大焊接 焊料的厚度)共晶金锡焊料已经得到了广泛应用:
如MEMS光开关等微电子和光电子学中使用的倒装芯片;光纤附件;GaAs和InP激光二极管;密封包装;和射频器件等。
AuSn的焊接已证明可靠性可以达到30多年,是因为其焊接中再流过程可 以产生重复、无空洞以及无缺陷的焊接。本文回答了很多公司关于焊接设计、 焊接材料组合以及再流焊技术发展等问题。
很多领域使用到金锡焊料。表一列出了典型的基板和金属化的厚度。一般 的,TIW/Au和Ti/Pt/Au(互联层/阻挡层/保护层)用于半导体器件和陶瓷基板的焊 接,Ni/Au用在金属的连接。
Ni一般用电解电镀或化学电镀,但后者成本更低更多的使用。扩散阻挡层
一般选用Ni、Pt和Pd,或在TIW层上沉积NiSn和AuSn的金属间化合物。
焊接后,我们期盼构成n,£和泛的连续的界面。一般来说,瞬间液相 (TLP连接使用的更多而不是共晶连接。瞬间液相(TLP连接的优点的是连 接温度处于Sn液相点和共晶液相间之间。但是,此种焊接时加热时间和冷却时 间都需要更长,而且如果在这个过程里反应没
有完全,则以后长时间里微结构的演变都会继续。通过多层薄的焊料可以 减少这些缺陷,因为薄层可以减少扩散距离,也减少产生金属间化合物的时 间。
合适的焊接界面
扩散阻挡层
保护层
合适的焊接界面是使电子元器件焊接到陶瓷基板上的必备界面,因为大部 分的金属材料不可以直接互联到共价材料上;而对于金属基板是不需要焊接界 面。扩散阻挡层必须既要和焊接层互联良好,而且和锡(内在)不反应或足够 的厚以阻止再流和后面焊接形成的金属化合物的扩散。保护层是兼容纯金材料 和金锡焊料的必备材料,可以保护表面在再流焊接前的氧化。
相图
我们可以从金锡焊料的二元相图去认识很多共晶金锡焊料焊接的关键问
题,如图1所示,焊料中富金时,液相线下降非常迅速,在常温下有大量的“线
ห้องสมุดไป่ตู้性”化合物。
当使用金锡焊料焊接镀金层时,焊接温度必须超过280摄氏度,因为只有 达到这个焊接问题,镀层里的金元素才可以扩散或融入到焊料中。这样可以产 生两个优点:
在这个温度下第二次再流不会损坏到焊料;更高的温度也可以产生更大的 抗蠕变性。然而,焊接后中间的焊料很难再次起到焊接作用,因为即使两个焊 接界面可以分开,残留下焊接时形成的金属间化合物都会阻止再流。而且,焊 接中的 “凝固”现象也会使浸湿不充分导致焊接不完全而使强度下降。
这些缺点可以通过增加焊料中锡成分成为富锡焊料,这样,共晶成分中金 完全平均分散的。
但在使用金锡焊膏时候,这种方法也是有一定缺陷的,因为焊膏的成分是 可变的,这也是为什么使用蒸发、溅射或电镀方法来沉积焊膏。
对于共晶焊接,我们应该关注冷却时如下的过程:
L +3宀£一般来说,焊接后E和E构成了焊接的主要组成,其中E是 焊接后形成的金属间化合物。
缺点:
需要阻焊剂(微机电系统,倒装芯片和光电子学除发光二极管外);组分控 制;焊接气氛导致的孔洞率
溅射膜:
优点:
成分控制
缺点:
残留Ar杂质和空洞;中等和小批量的使用,成本和过程控制;沉积速度慢
蒸发膜“
优点:
成分控制
缺点:
不均匀以及污染,中等和小批量的使用,成本和过程控制;沉积速度慢 电镀膜:
优点:
成分控制,大批量使用,沉积速度快,
焊料的种类和种类
本文研究的焊料种类包括焊片、焊膏和沉积膜。沉积膜的技术包括溅射成 膜、蒸发成膜以及电镀成膜,膜可以是单层或多层的。它们的缺点和优点如下 介绍:
焊片:
优点:
单独使用;不依靠焊料的流淌来达到覆盖总个焊盘
缺点:
组成的一致性;氧化性;定位问题;低容量
焊膏:
优点:
大批量使用,包括使用光刻胶做网印刷
前言:
由于共晶金锡焊料具有优良的机械和热传导性能(特别是强度和抗蠕变 性)以及不需组焊剂可以很好的再流的特性,共晶AuSn被广泛应用于高温和高 可靠性的电路中。与之对比其他无铅和传统的铅锡共晶焊料却有着大量的问 题:
焊接时需要的组焊剂造成了焊接焊盘的腐蚀,同时残杂也会危害EMES光
电电路和密封封装(组焊剂一般在密封电路中被禁止使用)。
和Sn发生反应的阻挡层,扩散的速率和以下的因素有关系:
焊料互联的厚度
焊料液相点的峰值温度
焊接的时间
形成物的形貌和阻挡层上的残余应力
如图2所示,Song等人已使用一个特殊的例子详细阐述了阻隔层的损耗问 题。这两篇文章对比了金锡焊料焊接时,纯铜焊盘以及其上有Ni隔离层的差 别。金属间化合物Au-Ni-Sn和CuSn的生长速度成平方根的比例,这是个一个典 型的扩散速度,尽管Ni的耗散速度因为焊接峰值温度的影响变得更低。
缺点:
过程的敏感度
一般而言,单层共晶成分电镀层或多层次Au5Sn(E)'和AuSn(S)电镀
膜被认为适合于批量生产。但对于小批量的是使用,焊片、溅射或蒸发都可以 使用。
这个相图有利于我们认识焊料的机械性能。锡富一方形成的金属间化合物 方图是 “线”形化合物,具有极其有限的溶解度。这些化合物一般有着高强度和 良好的抗蠕变性,但展延性减少。
但在下文中我们将讨论到,具备中等延性和优良的抗蠕变性的金锡焊料形
成的金属间化合物却远比CuSn化合物有更好的展延性。
金属化层
选择合适的金属化层是共晶焊接的关键之一。一般的要符合如下的要求:
共晶
摘要:
因为传统铅锡焊料和无铅焊料强度不足、砍蠕变能力差以及其他的本身缺 陷,共晶金锡焊料已经替代它们广泛用于高可靠和高功率电路中,包括使用在 混合电路、MEM、光电开关、LEDs激光二极管和无线电装置。金锡焊料焊接 中可以避免使用组焊剂,尤其可以减少污染和焊盘的腐蚀。虽然使用金锡焊料 有很多优点,但材料的性能和焊接工艺工程仍需研究。
而扩散阻隔层W材料和Sn不发生反应,尤其再覆镀上NiSn或AuSn的金 属间化合物,更可以有效地减少阻隔层的金属损耗。
即使是生成物、再流焊温度以及时间等相似时,扩散速度也会不同。因为 阻隔物材料颗粒的减少会增加本身材料的扩散速度,就会导致阻隔层材料损速 度的增加。焊接各个阶段产生残余应力不仅增加扩散率,而且会产生新的增加 甚至开裂。