钻杆耐磨带焊缝凹槽缺陷的改进方法
石油钻杆磨损原因及应对措施

石油钻杆磨损原因及应对措施摘要::分析了石油钻杆工作原理,耐磨带性能影响因素性能特点与影响因素。
分析材料特性是影响耐磨带性能的核心因素,耐磨带特性的改变取决于堆焊材料成分、组织性能的变化以及配套堆焊工艺的严格实施。
关键词:钻杆磨损;耐磨带;性能分析1、耐磨带工作原理钻杆接头耐磨带实质上是一个沿接头圆周方向,具有一定宽度和一定厚度的隔离带。
通过这个隔离带,使钻杆接头外壁和套管壁或井壁隔离,避免钻杆接头与套管壁或井壁直接接触,以保护钻杆接头和套管免遭强烈磨损。
耐磨带的工况条件比较复杂,性能要求比较苛刻,应当具有良好的综合抗磨性能。
所谓综合抗磨性能,是指具有较高耐磨性的同时还必须具有适度的减磨性。
最佳的耐磨性与减磨性之间存在一定的匹配关系,上述技术指标之间以及与摩擦系数之间的函数关系的量化确立,可能对于耐磨带焊接材料性能的重大突破具有重要参考价值。
2、耐磨带性能影响因素接头耐磨带性能影响因素较多,总体上有三大因素:2.1载荷力的影响在钻井过程中,凡是增大钻杆接头与套管内壁(或井壁)接触力的因素,都会加剧磨损发生。
如在“狗腿”度大的井段,接头与套管内壁接触压力相对增大,此时无论是耐磨带还是套管内壁(或井壁),其磨损现象就会加剧。
2.2摩擦系数的影响在钻井过程中,凡是增大接头与套管内壁摩擦系数的因素,都会加剧磨损发生。
如润滑剂品种或加入量不合适、转盘转速增大以及温度过高或过低时,其磨损现象也会加剧。
2.3耐磨带与套管(或井壁)材料特性的影响根据摩擦学中的“吸附膜”理论,对于钻杆钢与岩石形成的摩擦副,两者之间很难形成吸附膜,摩擦系数主要取决于摩擦副材料的表面特性,而摩擦副其表面特性是稳定的,摩擦系数受载荷的影响较小。
对于钻杆与套管钢形成的摩擦副,两者之间比较容易形成吸附膜,当施加正压力时,随吸附膜逐渐被破坏,摩擦副表面特性对摩擦系数形成的贡献越来越大,摩擦系数受载荷的影响较大。
凡是增大摩擦系数的材料特性,都会加剧磨损发生。
焊接缺陷成因及消除方法
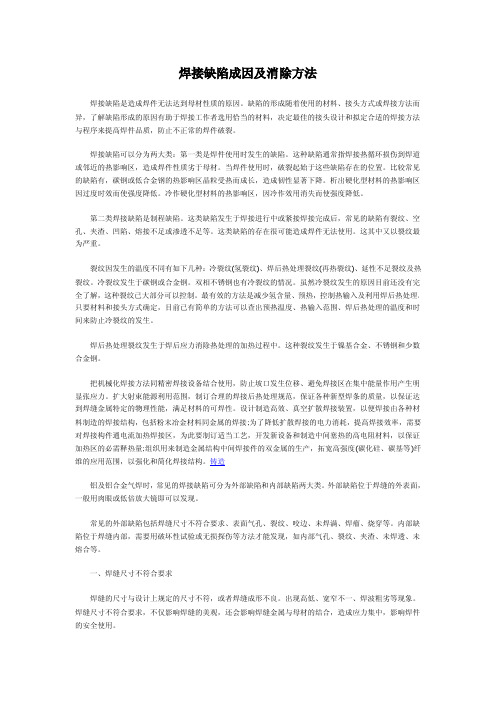
焊接缺陷成因及消除方法焊接缺陷是造成焊件无法达到母材性质的原因。
缺陷的形成随着使用的材料、接头方式或焊接方法而异,了解缺陷形成的原因有助于焊接工作者选用恰当的材料,决定最佳的接头设计和拟定合适的焊接方法与程序来提高焊件品质,防止不正常的焊件破裂。
焊接缺陷可以分为两大类:第一类是焊件使用时发生的缺陷。
这种缺陷通常指焊接热循环损伤到焊道或邻近的热影响区,造成焊件性质劣于母材。
当焊件使用时,破裂起始于这些缺陷存在的位置。
比较常见的缺陷有,碳钢或低合金钢的热影响区晶粒受热而成长,造成韧性显著下降。
析出硬化型材料的热影响区因过度时效而使强度降低。
冷作硬化型材料的热影响区,因冷作效用消失而使强度降低。
第二类焊接缺陷是制程缺陷。
这类缺陷发生于焊接进行中或紧接焊接完成后,常见的缺陷有裂纹、空孔、夹渣、凹陷、熔接不足或渗透不足等。
这类缺陷的存在很可能造成焊件无法使用。
这其中又以裂纹最为严重。
裂纹因发生的温度不同有如下几种:冷裂纹(氢裂纹)、焊后热处理裂纹(再热裂纹)、延性不足裂纹及热裂纹。
冷裂纹发生于碳钢或合金钢。
双相不锈钢也有冷裂纹的情况。
虽然冷裂纹发生的原因目前还没有完全了解,这种裂纹已大部分可以控制。
最有效的方法是减少氢含量、预热,控制热输入及利用焊后热处理。
只要材料和接头方式确定,目前已有简单的方法可以查出预热温度、热输入范围、焊后热处理的温度和时间来防止冷裂纹的发生。
焊后热处理裂纹发生于焊后应力消除热处理的加热过程中。
这种裂纹发生于镍基合金、不锈钢和少数合金钢。
把机械化焊接方法同精密焊接设备结合使用,防止坡口发生位移、避免焊接区在集中能量作用产生明显张应力。
扩大射束能源利用范围,制订合理的焊接后热处理规范,保证各种新型焊条的质量,以保证达到焊缝金属特定的物理性能,满足材料的可焊性。
设计制造高效、真空扩散焊接装置,以便焊接由各种材料制造的焊接结构,包括粉末冶金材料同金属的焊接;为了降低扩散焊接的电力消耗,提高焊接效率,需要对焊接构件通电流加热焊接区,为此要制订适当工艺,开发新设备和制造中间塞热的高电阻材料,以保证加热区的必需释热量;组织用来制造金属结构中间焊接件的双金属的生产,拓宽高强度(碳化硅、碳基等)纤维的应用范围,以强化和简化焊接结构。
消除焊接缺陷的方法和措施
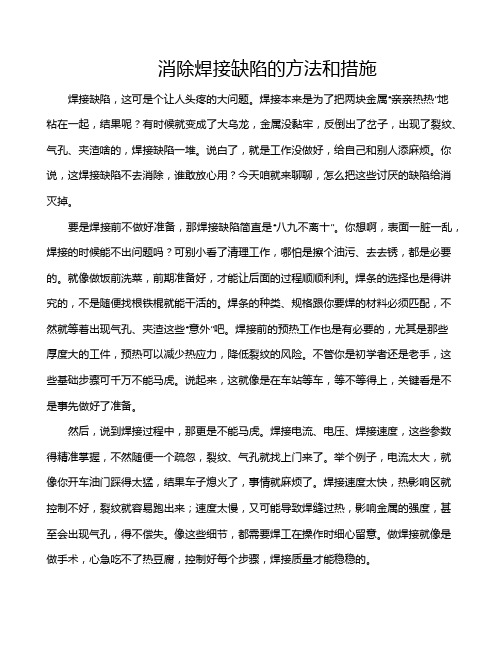
消除焊接缺陷的方法和措施焊接缺陷,这可是个让人头疼的大问题。
焊接本来是为了把两块金属“亲亲热热”地粘在一起,结果呢?有时候就变成了大乌龙,金属没黏牢,反倒出了岔子,出现了裂纹、气孔、夹渣啥的,焊接缺陷一堆。
说白了,就是工作没做好,给自己和别人添麻烦。
你说,这焊接缺陷不去消除,谁敢放心用?今天咱就来聊聊,怎么把这些讨厌的缺陷给消灭掉。
要是焊接前不做好准备,那焊接缺陷简直是“八九不离十”。
你想啊,表面一脏一乱,焊接的时候能不出问题吗?可别小看了清理工作,哪怕是擦个油污、去去锈,都是必要的。
就像做饭前洗菜,前期准备好,才能让后面的过程顺顺利利。
焊条的选择也是得讲究的,不是随便找根铁棍就能干活的。
焊条的种类、规格跟你要焊的材料必须匹配,不然就等着出现气孔、夹渣这些“意外”吧。
焊接前的预热工作也是有必要的,尤其是那些厚度大的工件,预热可以减少热应力,降低裂纹的风险。
不管你是初学者还是老手,这些基础步骤可千万不能马虎。
说起来,这就像是在车站等车,等不等得上,关键看是不是事先做好了准备。
然后,说到焊接过程中,那更是不能马虎。
焊接电流、电压、焊接速度,这些参数得精准掌握,不然随便一个疏忽,裂纹、气孔就找上门来了。
举个例子,电流太大,就像你开车油门踩得太猛,结果车子熄火了,事情就麻烦了。
焊接速度太快,热影响区就控制不好,裂纹就容易跑出来;速度太慢,又可能导致焊缝过热,影响金属的强度,甚至会出现气孔,得不偿失。
像这些细节,都需要焊工在操作时细心留意。
做焊接就像是做手术,心急吃不了热豆腐,控制好每个步骤,焊接质量才能稳稳的。
不过,话说回来,焊接结束之后,你以为就完了?可别高兴太早。
焊接完之后,检验可是一个大问题。
如果不认真检查,难保焊接缺陷会悄悄地藏在焊缝里,到时候可真是后悔都来不及。
检测的方式也多种多样,像是目视检查,找找有没有裂纹、气孔、夹渣等缺陷;也可以用射线探伤、超声波探伤,反正就是得把缺陷找出来,不能让它有藏身之地。
石油钻杆耐磨带磨损原因及耐磨解决方法

石油钻杆耐磨带磨损原因及耐磨解决方法在钻井过程中,钻柱在井眼中与套管内壁发生接触产生摩擦,使得扭矩和摩擦增加,而钻杆接头对套管的磨损影响最大,因为钻杆接头的直径比钻杆本体大20%~30%,很容易与套管内壁接触并磨损套管。
当接触力足够大时,润滑膜的润滑作用完全消失,钻杆接头与套管内壁直接接触产生了干摩擦。
在摩擦过程中,钻杆接头的磨损非常严重,偶然的碰撞就可能使钻杆接头产生断裂;同时,钻杆接头的磨损也使得套管壁厚减薄,抗挤能力随之降低。
若对此估计不足,有可能因此导致钻井事故或油气井的早期报废,给油田造成巨大的损失。
有研究结果表明,钻柱不居中使钻杆接头在钻井施工中与套管内壁相互摩擦是造成套管磨损的主要原因,而钻柱不居中又是钻探过程中不可避免的。
因此,可见如何降低钻杆与套管之间的摩擦接触或摩擦系数是防磨的关键与核心。
钻杆接头耐磨带是以凸起的形式熔合在钻杆接头表面,用以代替钻杆接头来和套管摩擦的材料,对钻杆接头起到了保护作用。
由于耐磨带的硬度低于钻杆本身,因此,对套管起到了一定的保护作用。
而耐磨带在磨损掉一部分之后,可以进行重复堆焊使用。
钻杆耐磨带主要是采用耐磨带焊丝通过CO2气体保护焊的方式堆焊到钻杆接头部位的一种高合金耐磨材料。
目前,国产耐磨带焊丝以北京固本KB150最具代表性。
KB150是北京固本公司第三代产品,是一种高级无裂纹、套管友好耐磨带,继承了KB100和KB300的优点,耐磨带能力介于KB100和KB300之间,摩擦因数低,减摩能力高于KB300和KB100,其焊接简单且焊接过程产生很少的火花和烟尘,且保持一定的韧性可承受在大位移井、深井和水平井的严苛钻井条件下产生的大转矩和高温;能在多种外界环境下补焊,而不会产生裂纹和脱落,同时抗硫化氢腐蚀。
摩擦焊接钻杆焊缝断裂失效分析

摩擦焊接钻杆焊缝断裂失效分析运用金相显微镜、扫描电镜对摩擦焊接钻杆焊缝断裂失效进行了分析。
结果表明,碳化物分布不均匀导致调质处理后在钻杆接头中产生“带状组织”。
焊后不正确的热处理使焊缝组织中出现残存的条状分布的马氏体,此条状分布的马氏体使焊缝的强韧性下降,造成焊缝发生疲劳断裂失效。
改进热处理工艺后,消除了残存马氏体,提高了钻杆焊缝的强韧性,从而提高了钻杆的使用寿命。
石油钻杆是油田钻井机械的重要部件。
钻杆由钻杆接头和钻杆管体通过摩擦焊接而成,焊后进行正火或调质处理。
钻杆使用时承受很大的拉应力和扭矩,并经受强烈的震动和冲击。
合理的摩擦焊工艺和正确的焊后热处理可使焊缝力学性能满足行业标准[1]。
如果摩擦焊或焊后热处理工艺不当,钻杆使用时焊缝容易断裂,造成很大的经济损失。
现有现场使用断裂钻杆1根,需要进行失效分析,判定其失效原因,提出解决措施,以提高钻杆质量,避免断杆事故发生。
2 现场调研钻杆生产厂生产的钻杆采用的接头为外购件,材料为40CrMnMo钢,调质处理后硬度为285~319HB(30~35HRC)。
管体采用已使用过的钻杆切除已损坏的接头后的旧管体。
接头与管体采用摩擦压力25~30MPa和顶锻压力50~60MPa的摩擦焊进行焊接。
根据现场了解,摩擦焊工艺较稳定,一般情况下能保证焊接质量。
焊后钻杆经中频加热后冲去焊缝内翻边,然后用车床车去外翻边。
最终热处理工艺为:中频淬火+中频加热回火。
规定的淬火加热温度为920℃,回火温图2 钻杆接头母材的金相组织×400腐蚀剂:4%硝酸酒精根据化学成分分析结果可知,该接头的材料为40CrMnMo钢。
接头母材的金相显微组织为回火索氏体,晶粒度为7~8级,沿接头轴向呈带状分布,显微组织不均匀。
白色区间显微硬度为183~188HV,黑色区间显微硬度为216~223HV。
黑色区间内含有较多的白色碳化物颗粒,用HR-150型洛氏硬度计测定其洛氏硬度值为31~36HRC,平均值为34HRC。
浅谈旧加重钻杆耐磨带堆焊的必要性

加重钻杆耐磨带堆焊的必要性及其应用论文摘要:在深井超深井勘探过程中,由于径向力、涡动、横向振动等因素的存在,随着钻井时间的增长,钻柱作用于套管内壁的侧向力增大,导致套管和钻具接头磨损的问题越来越严重。
造成钻具耐磨带失效的主要原因有地层研磨性、钻杆的井下工况、耐磨材料选择与敷焊工艺的影响。
选择合理的耐磨材料与敷焊工艺对解决钻具耐磨带失效问题非常重要。
论文关键词:耐磨带钻具铁基合金粉焊丝一、加重钻杆的作用加重钻杆通常应用于水平井、定向井以及深井等难度较大的井位中,可以部分代替钻铤以提高钻机的钻深能力,由于它的弹性比普通钻铤高,在弯曲井眼中用它来代替钻铤时,可以降低旋转扭矩和提升负荷。
另外在弯曲井段用加重钻杆代替钻杆时,由于加重钻杆于井壁接触面积较小,能减少旋转扭矩和上提阻力以及压差卡钻的可能性。
更重要的是有利于保持定向井的方向。
二、钻井过程中的磨损种类在油气田勘探开发钻井中,尤其是在深井、大位移井、水平井、大斜度井中,钻杆和套管的磨损严重,给油气田带来重大损失。
因此,钻井过程中钻杆和套管的磨损及防磨问题,已引起钻井界的密切关注。
套管磨损———套管磨损的主要形式为偏磨,偏磨后的套管横截面呈月牙型。
一方面套管圆周上呈月牙型部位壁厚最薄,导致抗挤强度大大降低。
在高地层压力作用下,假如设计的套管安全系数没有足够大,轻易导致套管挤毁,造成钻井报废或局部井段报废。
另一方面,偏磨套管在抗挤强度降低的同时其抗内压强度也随着降低。
在井控及中途测试时,假如没有充分考虑到套管磨损的影响,可能造成严重后果,即气井完井井控和测试时,要么冒套管破裂地面窜气的风险,要么提前入套管或下套管后再测试。
这不仅造成重大经济损失,而且给加深钻井造成困难或钻不到设计深度。
钻杆磨损———由于钻杆接头的外径大于杆体的外径,因此钻杆的磨损主要表现在钻杆接头的磨损。
当井眼曲率较大时,钻杆杆体也会受到磨损。
在钻井过程中旋转的钻杆接头和井壁或套管壁不断地摩擦,造成接头的严重磨损,尤其在硬地层或研磨性地层,井段钻杆接头磨损加剧。
焊接质量缺陷原因分析及预防、治理措施
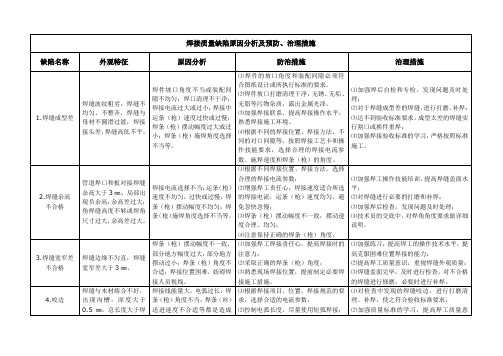
接高温时产生气体进入熔池; ⑸电弧过长, 氩弧焊时保护气 体流量过大或过小, 保护效果 不好等。 ⑴多层多道焊接时, 层间药皮 清理不干净; ⑵焊接线能量小,焊接速度 快; ⑶焊接操作手法不当; ⑷前一层焊缝表面不平或焊 件表面不符合要求。 产生表面裂纹的原因因为不 同的钢种、焊接方法、焊接环 境、预热要求、焊接接头中杂 质的含量、 装配及焊接应力的 大小等不同, 但产生表面裂纹 的根本原因是产生裂纹的内 部诱因和必须的应力有两点。 ⑴焊工责任心不强, 质量意识 差; ⑵焊接工器具准备不全或有 缺陷。 ⑴加强焊件表面打磨,多层多道焊时层 间药皮必须清理干净方可进行次层焊 ⑴严格按照规程和作业指导书的要求施焊; 接; ⑵对出现表面夹渣的焊缝,进行打磨清除, ⑵选择合理的焊接电流和焊接速度; 必要时进行补焊。 ⑶加强焊工练习,提高焊接操作水平。
⑴适当加大焊接电流,提高焊接线能 ⑴加强练习, 提高操作技术, 焊工责任心强; 量; ⑵针对不同的母材、焊材,制定处理不同位 ⑵焊接速度适当,不能过快; 置未熔合缺陷相应的措施并执行。 ⑶熟练操作技能,焊条(枪)角度正确。
17.管道焊口未 焊透
焊口焊接时,焊缝熔深 不够,未将母材焊透。
⑴对口间隙严格执行标准要求,最好间 隙不小于 2 ㎜。 ⑵对口坡口角度,按照壁厚和 DL/T869-2004 《火力发电厂焊接技术 规程》的要求,或者按照图纸的设计要 求。一般壁厚小于 20 ㎜的焊口采用 V 造成未焊透的主要原因是: 对 型坡口,单边角度不小于 30° ,不小于 口间隙过小、坡口角度偏小、 20 ㎜的焊口采用双 V 型或 U 型等综合 钝边厚、焊接线能量小、焊接 性坡口。 速度快、焊接操作手法不当。 ⑶钝边厚度一般在 1 ㎜左右,如果钝边 过厚,采用机械打磨的方式修整,对于 单 V 型坡口,可不留钝边。 ⑷根据自己的操作技能,选择合适的线 能量、焊接速度和操作手法。 ⑸使用短弧焊接,以增加熔透能力。 造成这些缺陷的原因是: 对口 间隙大,钝边薄、宽,熔池温 度过高, 熔池存在一个地方时 间过长, 对熔池的控制不当造 ⑴对口间隙符合标准要求,一般为 2~ 3 ㎜;对于对口间隙不均匀的焊口,用 机械打磨等方法设法修整到规定要求。 ⑵对于坡口钝边不符合要求的进行打
焊缝缺陷的原因和处理方法

焊缝缺陷的原因和处理方法
分类包含主要原因处理方法
裂纹热裂
纹
母材抗裂性能差、焊接材料质量不好、焊接工艺参数选择不当、焊接内应力过大等
在裂纹两端钻止裂孔或铲除裂纹处的焊缝金属,进
行补焊
冷裂
纹
焊接结构设计不合理、焊缝布置不当、焊接工艺措施不合理,焊前未预热、焊后冷却
快等
孔穴气孔
焊条药皮损坏严重、焊条和焊剂未烘烤、母材有油污或锈和氧化物、焊接电流过小、
弧长过长,焊接速度太快等
铲去气孔处的焊缝金属,然后补焊
弧坑
缩孔
焊接电流太大且焊接速度太快、熄弧太快,未反复向熄弧处补充金属等在弧坑处补焊
固体杂质夹渣
焊接材料质量不好、焊接电流太小、焊接速度太快、熔渣密度太小、阻焊熔渣上浮、
多层焊时熔渣未清除干净等
铲除夹渣处的焊缝金属,然后焊补夹钨氩弧焊时钨极与熔池金属接触挖去夹钨处缺陷金属,重新补焊
未熔
合
焊接电流太小、焊接速度太快、坡口角度间隙太小、操作技术不佳等。
铲除未熔合处的焊缝金属好补焊;
未焊透对开敞性好的结构的单面未焊透,可在焊缝背面直接补焊。
对于不能直接焊补的重要焊件,应铲去未焊透的焊缝金属,重新焊接。
形状缺陷咬边
焊接工艺参数选择不当,如电流过大、电弧过长;操作技术不正确,如焊枪角度不对,
运条不当等;焊条药皮端部的电弧偏吹;焊接零件的位置安放不当等。
轻微的、浅的咬边可用机械方法修锉,使其平滑过
渡;严重的、深的咬边应进行补焊。
焊瘤焊接工艺参数选择不正确、操作技术不佳、焊件位置安放不当等铲、锉、磨等手工或机械方法除去多余的堆积金属。
下塌、根部收缩、错边
其它电弧擦伤、飞溅、表面撕裂等。
焊接常见的质量缺陷及防治措施

焊接常见的质量缺陷及防治措施焊接工程上存在的质量缺陷主要包括以下几个方面:•凡是肉眼或低倍放大镜能看到的且位于焊缝表面的缺陷,如咬边(咬肉)、焊瘤、弧坑、表面气孔、夹渣、表面裂纹、焊缝位置不合理等称为外部缺陷•而必须用破坏性试验或专门的无损检测方法才能发现的内部气孔、夹渣、内部裂纹、未焊透、未溶合等称为内部缺陷。
•但常见的多是焊后不清理焊渣和飞溅物以及不清理的焊疤。
凡是肉眼或低倍放大镜能看到的且位于焊缝表面的缺陷,如咬边(咬肉)、焊瘤、弧坑、表面气孔、夹渣、表面裂纹、焊缝位置不合理等称为外部缺陷而必须用破坏性试验或专门的无损检测方法才能发现的内部气孔、夹渣、内部裂纹、未焊透、未溶合等称为内部缺陷。
但常见的多是焊后不清理焊渣和飞溅物以及不清理的焊疤。
焊缝尺寸不符规范要求现象:焊缝在检查中焊缝的高度过大或过小;或焊缝的宽度太宽或太窄,以及焊缝和母材之间的过渡部位不平滑、表面粗糙、焊缝纵、横向不整齐,还有在角焊缝部位焊缝的下凹量过大。
展开剩余94%原因:•焊缝坡口加工的平直度较差,坡口的角度不当或装配间隙大小不均等而引起的。
•焊接中电流过大,使焊条熔化过快,控制焊缝成形困难,电流过小,在焊接引弧时会使焊条产生“粘合现象”,造成焊不透或焊瘤。
•焊工操作熟练程不够,运条方法不当,如过快或过慢,以及焊条角度不正确。
•埋弧自动焊过程,焊接工艺参数选择不当。
焊缝坡口加工的平直度较差,坡口的角度不当或装配间隙大小不均等而引起的。
焊接中电流过大,使焊条熔化过快,控制焊缝成形困难,电流过小,在焊接引弧时会使焊条产生“粘合现象”,造成焊不透或焊瘤。
焊工操作熟练程不够,运条方法不当,如过快或过慢,以及焊条角度不正确。
埋弧自动焊过程,焊接工艺参数选择不当。
防治措施:•按设计要求和焊接规范的规定加工焊缝坡口,尽量选用机械加工以使坡口角度和坡口边缘的直线度和坡口边缘的直线度达到要求,避免用人工气割、手工铲削加工坡口。
在组对时,保证焊缝间隙的均匀一致,为保证焊接质量打下基础。
降低钻杆耐磨带过度磨损 提高钻杆使用寿命

2791 概述钻杆是钻柱的基本组成部分,主要用于传递扭矩、输送钻井液,以及在钻井过程中不断连接钻杆,以达到不断加深井眼的目的。
钻杆使用寿命的长短,与钻杆失效数量成正比。
某管具服务站使用量最大、最频繁的是5"G105钻杆。
本文就5"G105钻杆失效数量及原因进行统计分析,找出影响5"G105钻杆使用寿命的主要原因,从而提出相应对策,提高钻杆使用寿命。
本文中的使用寿命指正常使用周期内的使用寿命,即钻杆正常使用寿命周期内因失效而影响的使用寿命。
2 5"G105钻杆使用情况分析某管具服务站近三年5"G105钻杆周转总量116286根次,停用总量为1995根,其中报废总量493根(报废指因使用后损坏而无法修复的钻杆,不包括技术淘汰)。
从量上的分析来看,因接头损坏导致停用的钻杆占74.02%,是影响钻杆使用寿命的主要因素。
以上的分析图表表明,非正常停用的钻杆中,接头外径过小、管体腐蚀严重、管体刺穿是影响钻杆使用寿命的三大主要因素。
在诸多因素中,直接引发钻杆报废的因素包括管体的腐蚀、刺穿、咬扁、过度弯曲等,与钻杆的使用、泥浆性能等相关,从该服务站层来看,视为不可抗因素,本文不做分析。
引发钻杆停用的因素主要是接头的损坏,包括偏磨、长度不够、外径过小、耐磨带掉块等。
分析表明,接头外径过小是接头损坏的主要原因。
接头外径过度磨损、偏磨这二项之和超过总数的98%。
而钻杆的结构形式决定了此二项均发生在接头耐磨带过度磨损之后。
所以,应该把预防耐磨带过度磨损作为提高钻杆使用寿命的主要手段。
3 耐磨带过度磨损原因分析下面结合该管具服务站管理现状以及所服务站的井队的实现情况,对耐磨带过度磨损的原因进行分析。
3.1 修复不及时造成耐磨带磨损后修复不及时的主要原因有:3.1.1 服务站巡井原因该服务站主要负责47支钻井队的管具保障服务。
井队数量多、分布广、距离远、用车量大等因素直接导致巡井力度不够。
目前大部分巡检工作主要依靠服务站上井作业人员上井查看后反馈信息。
石油钻杆耐磨带焊接裂纹缺陷的改进方法

石油钻杆耐磨带焊接改进方法在实际生产过程中,带有锲形的4145H钢在喷焊KB300耐磨带焊丝后,耐磨带上出现了大量不合格的裂纹。
焊后耐磨带机械性能不符合《北京固本科技有限公司KB300耐磨带焊丝》焊接标准要求,需要对焊接工艺进行改进。
一、耐磨带焊接改进后的结果及分析针对耐磨带焊接出现裂纹问题,北京固本对耐磨带焊接工艺进行改进。
在焊接前,将管体预热温度由原来的150℃逐步提高到330℃;焊后,对焊接部分进行保温,保温时间由原来的4 h逐步提高到6 h。
1、焊接裂纹将焊接前预热温度逐步提高到330℃,焊接后立即对焊接部分进行保温,随着保温时间的延长,裂纹逐步减少,等保温时间达到6 h时,裂纹消失,此时,焊接效果达到最佳形态。
图2工艺改进后的焊接效果耐磨带焊接裂纹消除。
这主要是因为随着预热温度的提高,管体透热深度增加,管体表面温度接近于焊接时焊丝扩散温度,在焊接过程中减少了因管体内外温差造成的热应力,从而减少了焊接裂纹的形成。
但预热温度太高,会导致喷焊带流动,造成焊接不合格。
焊接后,立即进行保温,随着保温时间的延长,焊接应力减小,裂纹逐步消除,但保温时间太长会影响生产效率的提高。
因此,选择保温6 h为最佳工艺。
2力学性能表1 不同工艺焊接后的力学性能在保温时间一定的情况下,随着预热温度的提高抗拉强度逐步升高;在预热温度一致的情况下,随着保温时间的延长,抗拉强度逐步升高,但当预热温度升高到400℃时,抗拉强度开始出现下降趋势;硬度值的变化规律与抗拉强度一致。
这主要是因为预热温度上升,基体表面温度升高,温差减小,有利于焊接时组织均匀化,提高抗拉强度,但当温度太高焊接层出现熔化现象,使组织破坏,强度下降;保温时间延长,有利于焊接组织均匀化,从而提高性能,但预热温度超过330℃时,焊接部分开始出现熔化现象.为此,预热温度选择300℃为佳:保温时间达到6 h后,抗拉强度几乎不再变化,从生产效益方面考虑,选择保温6 h为宜。
焊缝中常见的缺陷分析及其防止措施
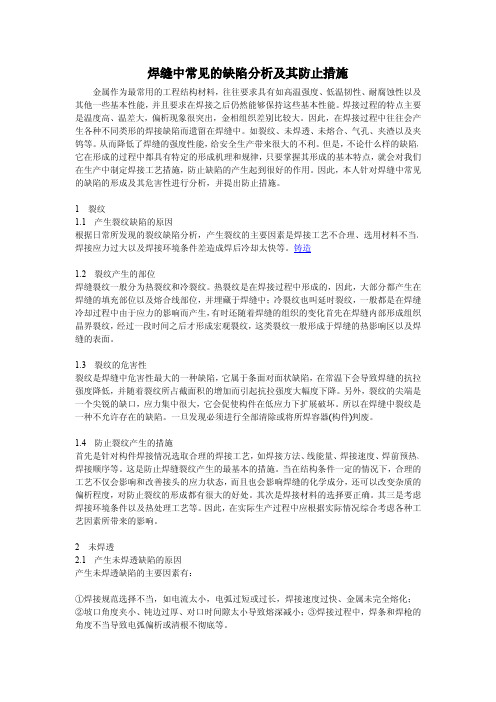
焊缝中常见的缺陷分析及其防止措施金属作为最常用的工程结构材料,往往要求具有如高温强度、低温韧性、耐腐蚀性以及其他一些基本性能,并且要求在焊接之后仍然能够保持这些基本性能。
焊接过程的特点主要是温度高、温差大,偏析现象很突出,金相组织差别比较大。
因此,在焊接过程中往往会产生各种不同类形的焊接缺陷而遗留在焊缝中。
如裂纹、未焊透、未熔合、气孔、夹渣以及夹钨等。
从而降低了焊缝的强度性能,给安全生产带来很大的不利。
但是,不论什么样的缺陷,它在形成的过程中都具有特定的形成机理和规律,只要掌握其形成的基本特点,就会对我们在生产中制定焊接工艺措施,防止缺陷的产生起到很好的作用。
因此,本人针对焊缝中常见的缺陷的形成及其危害性进行分析,并提出防止措施。
1裂纹1.1产生裂纹缺陷的原因根据日常所发现的裂纹缺陷分析,产生裂纹的主要因素是焊接工艺不合理、选用材料不当、焊接应力过大以及焊接环境条件差造成焊后冷却太快等。
铸造1.2裂纹产生的部位焊缝裂纹一般分为热裂纹和冷裂纹。
热裂纹是在焊接过程中形成的,因此,大部分都产生在焊缝的填充部位以及熔合线部位,并埋藏于焊缝中;冷裂纹也叫延时裂纹,一般都是在焊缝冷却过程中由于应力的影响而产生,有时还随着焊缝的组织的变化首先在焊缝内部形成组织晶界裂纹,经过一段时间之后才形成宏观裂纹,这类裂纹一般形成于焊缝的热影响区以及焊缝的表面。
1.3裂纹的危害性裂纹是焊缝中危害性最大的一种缺陷,它属于条面对面状缺陷,在常温下会导致焊缝的抗拉强度降低,并随着裂纹所占截面积的增加而引起抗拉强度大幅度下降。
另外,裂纹的尖端是一个尖锐的缺口,应力集中很大,它会促使构件在低应力下扩展破坏。
所以在焊缝中裂纹是一种不允许存在的缺陷。
一旦发现必须进行全部清除或将所焊容器(构件)判废。
1.4防止裂纹产生的措施首先是针对构件焊接情况选取合理的焊接工艺,如焊接方法、线能量、焊接速度、焊前预热、焊接顺序等。
这是防止焊缝裂纹产生的最基本的措施。
50钻杆偏磨的原因及处理措施

50钻杆偏磨的原因及处理措施摘要:对50钻杆的使用情况进行了力学与运动学分析,并对钻杆接头及耐磨带进行了研究.发现导致钻杆接头偏磨的根本原因并非是钻杆柱的公转引起,而是耐磨带失效所引起。
据此,阐述了50钻杆偏磨产生过程和形成机理,以及对钻杆疲劳寿命的影响,提出了减少偏磨的措施。
关键词:50钻杆;耐磨带;疲劳寿命;偏磨在钻井过程中.钻杆在任何部位的失效。
都会造成严重的后果,甚至造成油(气)井报废。
近年来国产钻杆在油(气)井钻探中越来越多的被采用,取得了良好的效果。
同时防止钻杆失效.延长钻杆的使用寿命就成为一个大家所关注的课题。
50钻杆偏磨可引起钻杆螺纹失效,形成糖葫芦或造成全角变化率扩大,甚至脱靶,导致钻杆管体疲劳断裂.降低钻杆的使用寿命等后果。
有学者指出,井下钻杆旋转时存在着自转、公转、自转和公转共存等3种运动形式。
自转引起钻杆的均匀磨损.公转引起钻杆的偏磨。
笔者通过钻杆的使用情况跟踪。
对偏磨的现象与原因进行了观察与分析,发现是钻杆接头的耐磨带失效引起了钻杆的偏磨。
严重偏磨使钻杆的疲劳寿命大幅降低。
据此,本文对50钻杆井下运动特征,偏磨的形成过程及对钻杆疲劳寿命的影响进行了探讨。
1钻柱的井下力学与运动学特征钻柱的井下力学与运动学特征主要有:其一,为获得合理的钻压,钻柱大部分(钻杆)重量加载于游车大钩,另一部分(钻铤)重量施加于钻头上。
其拉应力()沿钻柱的分布情况如图1所示。
钻杆振动时叠加交变正压力或弯曲应力。
另外,泥浆压力使50钻杆产生径向拉应力:其二.钻柱受方补心驱动力与井下摩阻、钻阻产生扭矩形成切应力;其三,钻柱在井下钻进时(忽略纵向振动),如图1所示,主转动为角速度Ω2。
由于井径大于钻杆外径,相对图1:50钻杆“涡动”示意细长的50钻杆柱,就有了产生横向摆动的自由度。
同时受井壁与钻井液的摩阻,钻杆产生沿井身中心O1的角速度Ω1运动。
Ω1与Ω2叠加构成了钻杆的“涡动”。
因此A点的线速度V A=Ω2R2—Ω1R1>0,那么“涡动”基本上就成为钻杆柱的基本运动形:其四,在钻进时,钻杆会附加纵向振动和横向振动。
4.焊缝缺欠、缺陷产生原因及防止方法

14 2013-7-7
15 2013-7-7
从图1看出。对接接头的焊缝,其焊趾(焊 缝表面与母材的交界处)处的应力最大。应 力集中系数的大小取决于焊缝余高h、焊趾 处夹角θ和转角半径r。焊缝余高h增加.则 θ角增加,r值减小,会使应力集中系数增 大。从图还可得出对接接头几何尺寸与应 力集中系数K 的关系式为: K =σmax/σ0 焊缝的余高愈大,应力集中程度愈严重, 焊接接头的强度反而会降低。焊后削平余 高。只要不低于母材,减少应力集中,有 时反而可以提高焊接接头的强度。焊缝的 16 转角半径愈小,应力集中的程度则愈大; 2013-7-7
18 2013-7-7
焊接区中的气体来源: 大气的侵入,溶解于母 材、焊丝和焊芯中的气体,受潮药皮或焊剂 熔化时产生的气体,焊丝或母材上的油污和 铁锈等在受热后分解所释放出的气体,焊接 过程中冶金化学反应产生的气体。熔焊过程 中形成气孔的气体主要有:氢气、一氧化碳 和氮气。 氢气孔:多数情况下出现在焊缝表面上,断 面形状多呈螺钉状,从焊缝表面上看呈圆喇 叭口形,气孔四周内壁光滑。个别情况下也 以小圆球形状存在于焊缝内部。 氮气孔:多数以成堆的蜂窝状出现在焊缝表 面上。 一氧化碳气孔:多数情况下产生在焊缝内部, 19 沿结晶方向分布,有些象条虫状,表面光滑。 2013-7-7
形成原因 操作不当或焊接规范选择不当。如
焊接电流过小,而立焊、横焊、仰焊时电流
过大,焊接速度太慢,电弧过长,运条摆动
不正确。
防止措施 调整合适的焊接电流和焊接速度,
7 2013-7-7
采用短弧操作,掌握正确的运条手法。
凹坑
焊后在焊缝表面或背面形成低于母材表面
的局部低洼缺陷。
未焊满 由于填充金属不足,在焊缝表面
焊接缺陷成因及消除方法

焊接缺陷成因及消除方法一、焊接缺陷的成因:1.焊剂质量不好:焊剂的质量不佳,包括焊剂的性能和施焊条件不满足要求,会导致焊接质量不高,出现缺陷。
2.焊接参数不合理:焊接过程中,当焊接电流、焊接电压、焊枪速度等参数不合理,就会导致焊接缺陷。
3.温度不均匀:焊接过程中,如果温度分布不均匀,会导致焊接缺陷。
4.焊接工艺不当:焊接工艺不当,焊接方法不正确,会导致焊接缺陷。
5.材料质量不良:焊接材料的质量不良,会导致焊接缺陷。
6.污染不洁:焊接缝口处有污物、水珠、油污或其他杂质,会导致焊接缺陷。
二、消除焊接缺陷的方法:1.保证焊接条件合理:在焊接过程中,要确保焊接电流、焊接电压、焊枪速度等参数合理,以达到最佳的焊接质量。
2.保证焊接质量:在焊接过程中,要使用合格的焊剂,并且要确保焊剂能够满足焊接要求,以达到最佳的焊接质量。
3.保证温度均匀:在焊接过程中,要保证焊缝的温度分布均匀,以达到最佳的焊接质量。
4.保证焊接工艺:在焊接过程中,要使用合理的焊接工艺,以达到最佳的焊接质量。
5.保证材料质量:在焊接过程中,要使用合格的材料,确保材料的质量,以达到最佳的焊接质量。
6.保证焊接环境干净:在焊接过程中,要保证焊接环境干净,不要有污物、水珠、油污或其他杂质,以达到最佳的焊接质量。
7.保证焊缝的外观:在焊接过程中,要保证焊缝的外观,确保焊缝的光滑度、宽度、厚度等,以达到最佳的焊接质量。
8.加强检查:在焊接完成后,要对焊缝进行全面的检查,注意检查焊缝的外观、强度、承载能力等,以确保焊接质量。
总之,要想消除焊接缺陷,就要从焊接条件、焊剂质量、温度均匀性、焊接工艺、材料质量、焊接环境干净、焊缝外观、检查等多方面入手,全面把关,以确保最终的焊接质量。
焊缝缺陷的产生原因及解决措施
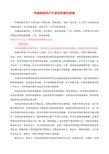
焊接缺陷的产生原因和解决措施焊缝质量有四个方面形成:焊接结构、焊接规范、母材、电焊条。
以上四个方面来形成焊缝质量好、符合质量要求,或是不好、不符合质量要求。
焊缝质量指的是:力学性能、化学成分、裂纹或裂缝、气孔、咬肉等。
在焊接当中有时焊缝出现裂纹或裂缝、气孔、咬肉等缺陷。
焊接当中产生这三种缺陷的原因和解决办法:一、焊缝开裂:裂纹裂缝都是焊缝开裂。
一般的说法是肉眼勉强看出的称为裂纹;明显看出的称为裂缝。
焊缝在焊接当中开裂有以下原因:应力、拘束力、刚性、化学成分、焊缝予留的间隙、电流、焊道、母材清洁等。
这些因素都可能是造成焊缝开裂的原因。
虽然造成焊缝开裂原因很多,但在某种场合是多种原因造成的,也有两种或三种因素造成的。
但不管几个易素,其中必有一个主要因素。
也有各种条件都没有什么影响,只受一种因素造成焊缝开裂。
因此出现焊缝开裂必须首先正确地分析出开裂的主要因素及次要因素,根据造成开裂的主要、次要因素采取相应措施进行解决。
焊接过程形成的焊缝是焊条和母材两者经过电流高温熔化后形成焊缝,是焊条和母材由固体变成液体,高温液体是热胀,冷却变成固体是收缩。
由于热胀冷缩,自然使被焊接结构产生应力。
有些焊接结构本身就存有拘束力和刚性。
焊接过程是由固体变成液体,也就是固态转变成液态(通常说铁水),再由液态变成固态,也就形成焊缝。
液态转变成固态(也就是铁水开始凝固),也就是铁水转变成晶粒。
铁水转变成晶粒的过程就是结晶过程。
母材温度低的位置先开始结晶,逐渐向焊缝中间位置伸展,焊缝中间最后结晶。
由于热胀冷缩的作用,焊接结构受应力或拘束力或刚性的影响,使被焊母材晶粒连接不到一起,轻者在焊缝中间出现小裂纹,重者在焊缝中间出明显的裂缝。
即使母材和电焊条的化学成分都好,受焊接结构的拘束力、刚性和焊接过程产生的应力影响,也会出现裂纹或裂缝。
如果母材和电焊条的化学成分不好(碳、硫、磷等偏高);或是焊缝予留的间隙太大,母材在焊缝边缘杂质过多,或电流过大,并且焊接速度过快、过慢、焊道过宽等因素会使焊缝开裂情况更要加重。
焊缝中的常见缺陷及其防止措施

焊缝中的常见缺陷及其防止措施
焊缝中常见的缺陷包括以下几种:
1. 焊缝气孔:气孔是由于焊接过程中未完全排出的气体形成的小孔。
它可以降低焊缝的强度和密封性能。
防止措施包括:
- 保持焊接区域的干燥和清洁,避免有水分、油污等杂质进入焊缝。
- 选用合适的焊接材料,控制焊接电流和电压,以减少气体的产生。
- 确保焊接操作符合标准和规范,如正确使用焊接电源和焊枪等设备,控制焊接速度和角度。
2. 焊缝夹渣:夹渣是由于焊接过程中未完全排除的焊渣和沉淀物残留在焊缝中形成的。
它会降低焊缝的密封性和强度。
防止措施包括:
- 清理焊接区域,确保焊接前的基材表面清洁。
- 选择合适的焊接工艺,如使用足够的焊接电流和填充材料,以便焊渣和沉淀物可以顺利排除。
- 在焊接过程中定期对焊缝进行清理,及时清除夹渣。
3. 焊缝裂纹:焊缝裂纹可分为冷裂纹、热裂纹和应力裂纹等。
它们可能会导致焊缝的破裂和失效。
防止措施包括:
- 控制焊接过程中的预热和降温速度,以避免温度梯度过大引起冷裂纹。
- 选择合适的焊接工艺和填充材料,以避免热裂纹的生成。
- 避免过量的残余应力,如通过预加应力退火来改善应力裂纹的情况。
4. 焊缝凹陷和错边:焊缝的凹陷和错边可能会导致焊缝的强度下降和不均匀厚度。
防止措施包括:
- 控制好焊接的速度和焊枪的运动轨迹,以确保焊缝的均匀填充。
- 使用适当的焊缝形状和角度,以减少焊缝的凹陷和错边。
以上是常见焊缝的缺陷及其防止措施。
实际操作中,也应根据不同的焊接材料和工艺选择合适的防控方法。
- 1、下载文档前请自行甄别文档内容的完整性,平台不提供额外的编辑、内容补充、找答案等附加服务。
- 2、"仅部分预览"的文档,不可在线预览部分如存在完整性等问题,可反馈申请退款(可完整预览的文档不适用该条件!)。
- 3、如文档侵犯您的权益,请联系客服反馈,我们会尽快为您处理(人工客服工作时间:9:00-18:30)。
周完成信号 , 向P C发送 , L 并 L P C接到
1 )后 ,根据编码开关有效位对应的输入 0
同的 工艺 调定 不 同的延 迟时 间 ,这 样才
能满 足 实 际需 要 。
管体在一定宽度 内快速往复运动 ,当管体 完成 3 0 6 度旋转 后焊 机产生一个管体旋转
一
二 、 改 造 方 案
改造 工作主要 有两个 内容 ,PLC的
端 口 ( . 9 .3 .5 的编码状态 , 0 0 、1 1 、1 1 ) 在 P 程 序中插入相应的延时程序段 。 LC 根据
一
D I1 .9 9 ji n 1 0 - 9 2 2 1 . 1 0 6 O : 0 3 6 / . s . 0 1 8 7 .0 0 2 .6 s
钻杆耐磨带焊 缝 凹槽缺 陷的改进方法
王云梁 冯启杰 1西安 石 油 大 学机 械 工 程 学 院; . 西 北 方 风 雷 工 业 集 团 公 司 . 2山
进行修 改, 通过这些措 施对该型耐磨带焊
机进 行 了改造 , 好 地 解 决 了凹槽 缺 陷问 很
题 。
耐 磨 带 ;PC改 造 ;钻杆 L
ARC 8 P耐磨带焊机 是从美 国 ARC
公司进 1的敷焊石油钻具产品耐磨带 专用 : 3
设备 , 该设备主要用于加重钻杆 和钻 杆以 及其 它井 下工具 表面耐磨 带的 自动敷焊 , 耐磨带的作用是增加钻杆耐磨强度和提升 使用 寿命 。该 型耐磨 带焊 机 的 自动化程 度较高 , 采用 P C控制技术 , OMRON L 以 公司 C M1 P 系列 P C作为核心控制单元 , L 因此可知该型焊机采用 了比较常 见的P LC 产品组成控制系统 , 这为我们的改造 工作 提供 了有利的基础。该型焊机在石油 钻具 生产领域 应用的较 多 , 希望 本文能给遇 到
槽 对耐 磨带 的性 能和 外观 都有 影 响 ,本
备, 早期 的焊机在敷焊过程 中耐磨带环接
文讨论的重点就是如何通过改造耐磨带焊 机 的 PL C控制 系统 ,改 善钻杆耐 磨带 的
凹槽 缺 陷 。
口处存 在 凹楷 缺陷 ,本文通过 增设部 分
P e 围控 制 电路 , 时对 焊 机 的 PC 序 L外 同 L程
现场调试情况 ,编码开关的 8 种编码并没 有与延迟时 间均 匀对应 ,为 了达到最佳使 用效果 ,进行 了实际工艺测定调试 ,最终 采用的对应结果是 :0 0 .s 0 ~0 0 ~0 O 、0 1 .
5 , 01 s 0~ 1 5 、 0 1 2 O 、 1 0~ 2. s .s l ~ .s 0 5、
焊 延迟 。
P C程序修 改使用 OMRON 公司提 L 供 的 C P o rmme 软件完成 , X— rg a r 该软件 是 OMR0N公 司免费向用户提供的 P C L 开 发软 件 ,对于 CP M1 P C该软件 支 型 L 持 的 非 常 完善 ,通过 该 软 件 可 以读 出、 写 入P 控 制程序 , LC 本文读 出后进行修改
成 一 个 凹槽 ,如 图 l ( a)所 示 。该 凹
A c8 型耐磨带焊机是对加重钻杆和钻杆 R P
等石 油 钻 具产 品进 行耐 磨 带 自动敷 焊 的设
而是 先停 止管 体旋 转 ,焊枪 继续 做往 复 敷焊 动作 ,根 据 外部延 时设 定开 关的状 态 ,进行 相应 的延 时操 作 ,经过 设定 延 时后再继续 跳转 到下一 条耐磨带或停止焊 机 工作 。
三 、 方 案 实 施
通过研究P C控制电路中的I O接 口 L / 部分 ,找到 了3个空闲数字输 入点 ,它们
的接 口地址分别为0 0 、 . 3 1 1 。 .9 1 1 、 .5 利用 这3 个输入点可定 义8 o g 状态 , 通过查找备 件库 , 有现 成的4 位编码开关可以利用 , 使 用 中仅使用其 中的 3 即可 , 位 用它的bt 、 i2
旋转 ,然 后在 耐 磨带 环的 接缝处 多堆 积
一
对应关系设定 为:编码开 关的状态 0 0 0~
0 对应 P C中0 档延时 , L ~7 延时时间在 些焊 丝。具体 方法是在 PL C收到管 体 0 7 . ~4 O 间分布 , 0 时P C 不进行敷 00 L 将 旋 转 一周 完成 信号 后 ,并 不马 上跳 转到 0 0 .s
il bt 0 L .9 1 1 、 .5 图 1钻杆上 耐磨带焊缝处的凹槽改造前 bt 、 i 来 对 应 P C的 0 0 、 .3 1 1 三个输 人接 口, i2 bt 、bt 位 的编码 bt 、 il i 0 后对 比 解决 凹槽 缺 陷的指 导 思想是 :当钻 组 合按 照二进 制顺 序编码 的方 式进 行编 状 0至 0 , 杆等 管体 完成 旋转 一 周后 ,让 管体 停 止 码 , 态从0 0 0 7 与敷焊 延时时 间的
下一条耐磨 带敷焊位 置或 马上停敷焊动 作结 束敷 焊 ,而是 让 管体 停止旋 转 ,然
后经过 一段时间延迟后再进行跳转或停止 堆焊 工作 。增 加 延时 时 间 ,又 带来 一个 新 问题 ,不 同种类 的 钻具 产品 的耐磨 带 敷 焊 工艺 不同 ,对 单 条耐磨 带宽 度 的要 求不 同 ,不 同的耐 磨带 宽 度对延 迟时 间 要 求也 不 同 ,因此 在进 行该 项改 造设 计 时 要考 虑敷 焊 延迟时 间的调 节 ,对 于不
同样问题的该产 品用户提供一 定的帮助 。
一
、
问题 分 析及 解 决 方 法 的提
焊机 的 工作过 程大 致可 描述 为 :焊
出
机开 始工作时加重钻杆或钻杆等石油钻具
产 品的管体 匀速旋转 ,焊枪启弧后垂直于
的是焊机 P C中的梯形图程序。 L 在梯形 图 中修改 的主要 内容 ,如图 2 所示 ,具体就 是在收到钻 杆杆体旋 转一周完成信号 ( . 1