热处理应力及其影响
热处理工艺对金属结构件的应力和变形控制
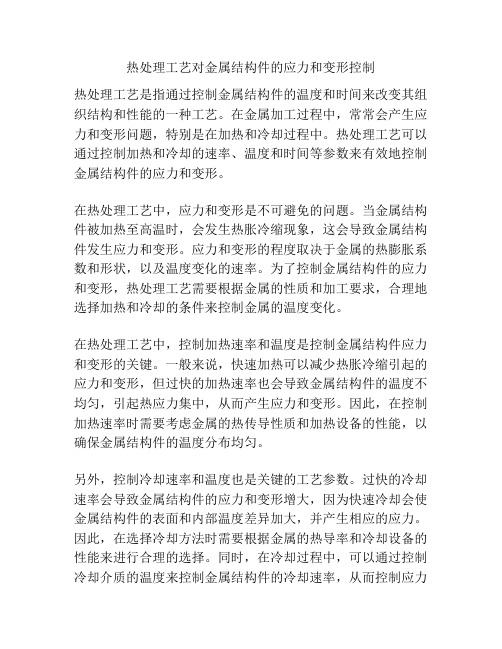
热处理工艺对金属结构件的应力和变形控制热处理工艺是指通过控制金属结构件的温度和时间来改变其组织结构和性能的一种工艺。
在金属加工过程中,常常会产生应力和变形问题,特别是在加热和冷却过程中。
热处理工艺可以通过控制加热和冷却的速率、温度和时间等参数来有效地控制金属结构件的应力和变形。
在热处理工艺中,应力和变形是不可避免的问题。
当金属结构件被加热至高温时,会发生热胀冷缩现象,这会导致金属结构件发生应力和变形。
应力和变形的程度取决于金属的热膨胀系数和形状,以及温度变化的速率。
为了控制金属结构件的应力和变形,热处理工艺需要根据金属的性质和加工要求,合理地选择加热和冷却的条件来控制金属的温度变化。
在热处理工艺中,控制加热速率和温度是控制金属结构件应力和变形的关键。
一般来说,快速加热可以减少热胀冷缩引起的应力和变形,但过快的加热速率也会导致金属结构件的温度不均匀,引起热应力集中,从而产生应力和变形。
因此,在控制加热速率时需要考虑金属的热传导性质和加热设备的性能,以确保金属结构件的温度分布均匀。
另外,控制冷却速率和温度也是关键的工艺参数。
过快的冷却速率会导致金属结构件的应力和变形增大,因为快速冷却会使金属结构件的表面和内部温度差异加大,并产生相应的应力。
因此,在选择冷却方法时需要根据金属的热导率和冷却设备的性能来进行合理的选择。
同时,在冷却过程中,可以通过控制冷却介质的温度来控制金属结构件的冷却速率,从而控制应力和变形。
热处理工艺对金属结构件的应力和变形控制具有重要意义。
首先,合理的热处理工艺可以降低金属结构件的应力和变形,提高其工作性能和使用寿命。
其次,热处理工艺可以改善金属结构件的内部组织结构,提高其强度、硬度和耐磨性等性能。
最后,热处理工艺可以实现金属结构件的尺寸精度控制,满足加工要求。
总之,热处理工艺对金属结构件的应力和变形控制具有重要意义。
通过合理选择加热和冷却的条件,可以降低金属的应力和变形,提高其性能和使用寿命。
热处理过程中材料的应力的变化
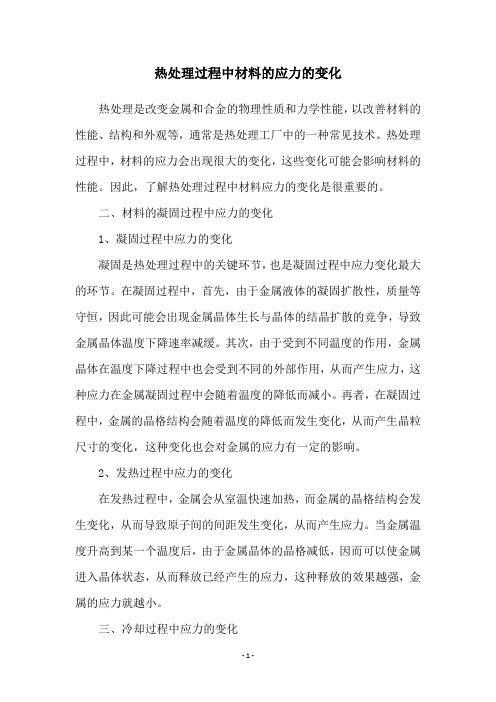
热处理过程中材料的应力的变化热处理是改变金属和合金的物理性质和力学性能,以改善材料的性能、结构和外观等,通常是热处理工厂中的一种常见技术。
热处理过程中,材料的应力会出现很大的变化,这些变化可能会影响材料的性能。
因此,了解热处理过程中材料应力的变化是很重要的。
二、材料的凝固过程中应力的变化1、凝固过程中应力的变化凝固是热处理过程中的关键环节,也是凝固过程中应力变化最大的环节。
在凝固过程中,首先,由于金属液体的凝固扩散性,质量等守恒,因此可能会出现金属晶体生长与晶体的结晶扩散的竞争,导致金属晶体温度下降速率减缓。
其次,由于受到不同温度的作用,金属晶体在温度下降过程中也会受到不同的外部作用,从而产生应力,这种应力在金属凝固过程中会随着温度的降低而减小。
再者,在凝固过程中,金属的晶格结构会随着温度的降低而发生变化,从而产生晶粒尺寸的变化,这种变化也会对金属的应力有一定的影响。
2、发热过程中应力的变化在发热过程中,金属会从室温快速加热,而金属的晶格结构会发生变化,从而导致原子间的间距发生变化,从而产生应力。
当金属温度升高到某一个温度后,由于金属晶体的晶格减低,因而可以使金属进入晶体状态,从而释放已经产生的应力,这种释放的效果越强,金属的应力就越小。
三、冷却过程中应力的变化在冷却过程中,金属的温度会逐渐降低,而金属的晶格结构也会随着温度的降低而变化,从而导致金属间隔的变化,进而产生应力。
随着温度的降低,金属的晶体结构也会随着温度的降低而发生变化,从而产生应力,这种应力会随着温度的降低而增加。
最后,当冷却到室温后,金属的晶体结构会停止变化,应力也会随之稳定,凝固而成的金属晶体结构也会得到稳定。
四、结论热处理过程中材料的应力是比较复杂的,它会随着温度的改变而发生变化,并且会随着热处理工艺的不同而有所不同。
凝固过程中应力的变化最为明显,应力会随着温度的下降而减小;在发热过程中,应力会随着温度的提升而增加;在冷却过程中,应力会随着温度的下降而增加,直到达到室温后稳定下来。
热处理对金属材料的应力松弛行为的影响分析
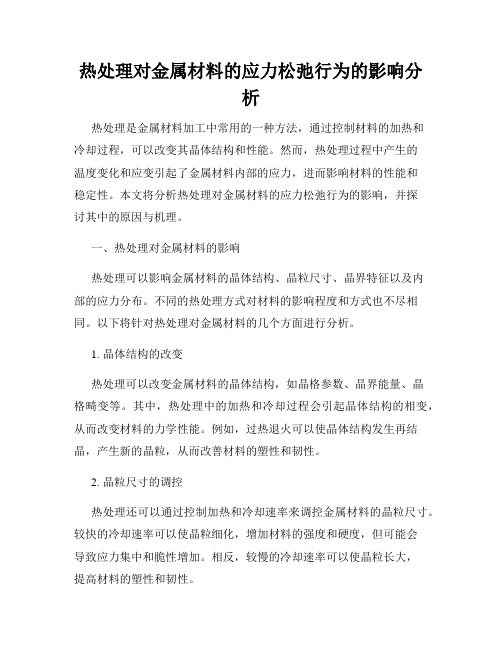
热处理对金属材料的应力松弛行为的影响分析热处理是金属材料加工中常用的一种方法,通过控制材料的加热和冷却过程,可以改变其晶体结构和性能。
然而,热处理过程中产生的温度变化和应变引起了金属材料内部的应力,进而影响材料的性能和稳定性。
本文将分析热处理对金属材料的应力松弛行为的影响,并探讨其中的原因与机理。
一、热处理对金属材料的影响热处理可以影响金属材料的晶体结构、晶粒尺寸、晶界特征以及内部的应力分布。
不同的热处理方式对材料的影响程度和方式也不尽相同。
以下将针对热处理对金属材料的几个方面进行分析。
1. 晶体结构的改变热处理可以改变金属材料的晶体结构,如晶格参数、晶界能量、晶格畸变等。
其中,热处理中的加热和冷却过程会引起晶体结构的相变,从而改变材料的力学性能。
例如,过热退火可以使晶体结构发生再结晶,产生新的晶粒,从而改善材料的塑性和韧性。
2. 晶粒尺寸的调控热处理还可以通过控制加热和冷却速率来调控金属材料的晶粒尺寸。
较快的冷却速率可以使晶粒细化,增加材料的强度和硬度,但可能会导致应力集中和脆性增加。
相反,较慢的冷却速率可以使晶粒长大,提高材料的塑性和韧性。
3. 晶界特征的变化热处理还可影响金属材料的晶界特征,如晶界产生与消灭、晶界迁移等。
具体来说,热处理可以通过消除晶界能量来减少材料中的晶界密度,从而改善材料的力学性能。
此外,热处理还可以通过材料的再结晶过程调整晶界特征,进一步提高材料的力学性能和抗蠕变性。
4. 应力分布的改变热处理过程中所产生的温度变化和冷却速率的不均匀性会导致金属材料内部产生应力。
这些应力存在于晶界和晶内,并可能引起应力松弛行为,即应力的持续缓慢释放。
应力松弛可能导致材料的形变、组织结构的变化以及材料性能的退化。
二、应力松弛行为的原因与机理应力松弛是热处理过程中产生的应力释放现象,其影响因素主要有以下几个方面。
1. 温度变化引起的线热应变热处理过程中的温度变化会导致金属材料的线热应变,即由于温度变化引起的材料长度变化。
热处理应力及其影响

热处理应力及其影响热处理残余力就是指工件经热处理后最终残存下来得应力,对工件得形状, ;尺寸与性能都有极为重要得影响。
当它超过材料得屈服强度时, ;便引起工件得变形,超过材料得强度极限时就会使工件开裂,这就是它有害得一面,应当减少与消除。
但在一定条件下控制应力使之合理分布,就可以提高零件得机械性能与使用寿命,变有害为有利。
分析钢在热处理过程中应力得分布与变化规律,使之合理分布对提高产品质量有着深远得实际意义.例如关于表层残余压应力得合理分布对零件使用寿命得影响问题已经引起了人们得广泛重视。
一、钢得热处理应力工件在加热与冷却过程中,由于表层与心部得冷却速度与时间得不一致,形成温差,就会导致体积膨胀与收缩不均而产生应力,即热应力。
在热应力得作用下,由于表层开始温度低于心部,收缩也大于心部而使心部受拉,当冷却结束时,由于心部最后冷却体积收缩不能自由进行而使表层受压心部受拉。
即在热应力得作用下最终使工件表层受压而心部受拉。
这种现象受到冷却速度,材料成分与热处理工艺等因素得影响。
当冷却速度愈快,含碳量与合金成分愈高,冷却过程中在热应力作用下产生得不均匀塑性变形愈大,最后形成得残余应力就愈大。
另一方面钢在热处理过程中由于组织得变化即奥氏体向马氏体转变时,因比容得增大会伴随工件体积得膨胀,;工件各部位先后相变,造成体积长大不一致而产生组织应力。
组织应力变化得最终结果就是表层受拉应力,心部受压应力,恰好与热应力相反。
组织应力得大小与工件在马氏体相变区得冷却速度,形状,材料得化学成分等因素有关. 实践证明,任何工件在热处理过程中, ;只要有相变,热应力与组织应力都会发生. ;只不过热应力在组织转变以前就已经产生了,而组织应力则就是在组织转变过程中产生得,在整个冷却过程中,热应力与组织应力综合作用得结果, ;就就是工件中实际存在得应力。
这两种应力综合作用得结果就是十分复杂得,受着许多因素得影响,如成分、形状、热处理工艺等。
热处理中的材料变形与应力释放
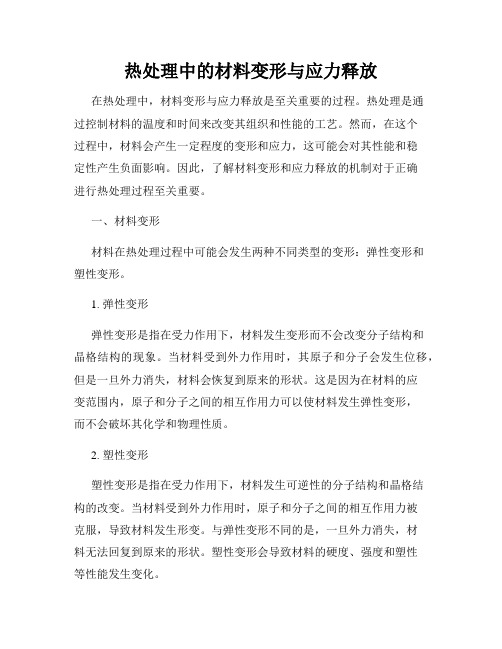
热处理中的材料变形与应力释放在热处理中,材料变形与应力释放是至关重要的过程。
热处理是通过控制材料的温度和时间来改变其组织和性能的工艺。
然而,在这个过程中,材料会产生一定程度的变形和应力,这可能会对其性能和稳定性产生负面影响。
因此,了解材料变形和应力释放的机制对于正确进行热处理过程至关重要。
一、材料变形材料在热处理过程中可能会发生两种不同类型的变形:弹性变形和塑性变形。
1. 弹性变形弹性变形是指在受力作用下,材料发生变形而不会改变分子结构和晶格结构的现象。
当材料受到外力作用时,其原子和分子会发生位移,但是一旦外力消失,材料会恢复到原来的形状。
这是因为在材料的应变范围内,原子和分子之间的相互作用力可以使材料发生弹性变形,而不会破坏其化学和物理性质。
2. 塑性变形塑性变形是指在受力作用下,材料发生可逆性的分子结构和晶格结构的改变。
当材料受到外力作用时,原子和分子之间的相互作用力被克服,导致材料发生形变。
与弹性变形不同的是,一旦外力消失,材料无法回复到原来的形状。
塑性变形会导致材料的硬度、强度和塑性等性能发生变化。
二、应力释放热处理过程中,材料会在高温下处理一段时间,这个过程会导致材料内部产生一定的应力。
要避免这些应力对材料性能造成不利影响,需要进行应力释放。
1. 冷却过程中的应力释放在热处理过程中,材料在高温处理后需要进行冷却。
在冷却过程中,由于材料的不均匀收缩,内部会产生应力。
为了释放这些应力,通常采取缓慢冷却的方法,使材料逐渐恢复到平衡状态。
这样可以减少材料的内部应力,提高其稳定性和可靠性。
2. 后热处理过程中的应力释放有一些材料,在经过热处理后还需要进行后热处理过程,以进一步调整其组织和性能。
在这个过程中,同样需要考虑到应力的释放。
通过适当的热处理工艺和参数设置,可以使材料内部的应力得到有效释放,从而提高材料的性能。
总结:在热处理过程中,材料变形与应力释放是不可避免的。
了解材料的变形类型和应力释放机制,可以帮助工程师和技术人员选择合适的热处理工艺和参数,以达到预期的材料性能和稳定性。
热处理 残余应力
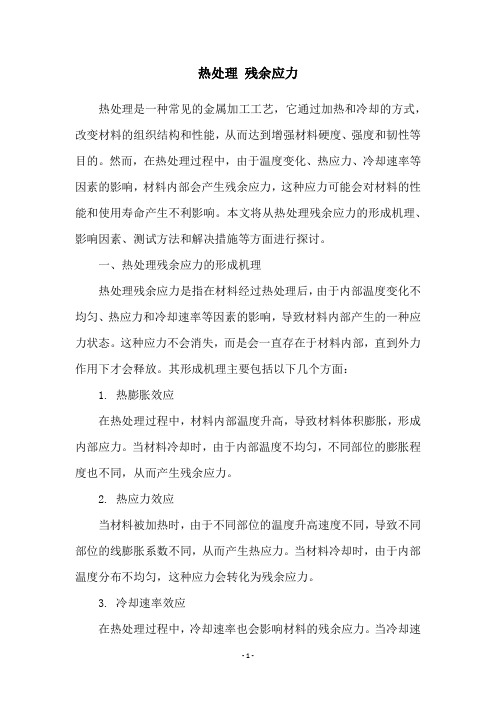
热处理残余应力热处理是一种常见的金属加工工艺,它通过加热和冷却的方式,改变材料的组织结构和性能,从而达到增强材料硬度、强度和韧性等目的。
然而,在热处理过程中,由于温度变化、热应力、冷却速率等因素的影响,材料内部会产生残余应力,这种应力可能会对材料的性能和使用寿命产生不利影响。
本文将从热处理残余应力的形成机理、影响因素、测试方法和解决措施等方面进行探讨。
一、热处理残余应力的形成机理热处理残余应力是指在材料经过热处理后,由于内部温度变化不均匀、热应力和冷却速率等因素的影响,导致材料内部产生的一种应力状态。
这种应力不会消失,而是会一直存在于材料内部,直到外力作用下才会释放。
其形成机理主要包括以下几个方面:1. 热膨胀效应在热处理过程中,材料内部温度升高,导致材料体积膨胀,形成内部应力。
当材料冷却时,由于内部温度不均匀,不同部位的膨胀程度也不同,从而产生残余应力。
2. 热应力效应当材料被加热时,由于不同部位的温度升高速度不同,导致不同部位的线膨胀系数不同,从而产生热应力。
当材料冷却时,由于内部温度分布不均匀,这种应力会转化为残余应力。
3. 冷却速率效应在热处理过程中,冷却速率也会影响材料的残余应力。
当冷却速率较快时,材料内部的热应力会更大,残余应力也会更大。
二、热处理残余应力的影响因素热处理残余应力的大小和分布情况受多种因素的影响,主要包括以下几个方面:1. 材料的性质不同材料的热膨胀系数、热导率、热容等性质不同,这些性质会影响材料在热处理过程中的温度分布和残余应力大小。
2. 热处理工艺参数热处理工艺参数,如加热温度、保温时间、冷却速率等,会影响材料的温度分布和残余应力大小。
3. 加工工艺材料在加工过程中可能会产生残余应力,这些应力可能会在热处理过程中被激发,从而增加热处理残余应力的大小。
4. 热处理设备热处理设备的性能和精度也会影响热处理残余应力的大小和分布情况。
三、热处理残余应力的测试方法热处理残余应力的测试方法主要包括以下几种:1. X射线衍射法X射线衍射法可以通过测量材料中的晶格应变来计算残余应力大小和分布情况。
淬火热应力
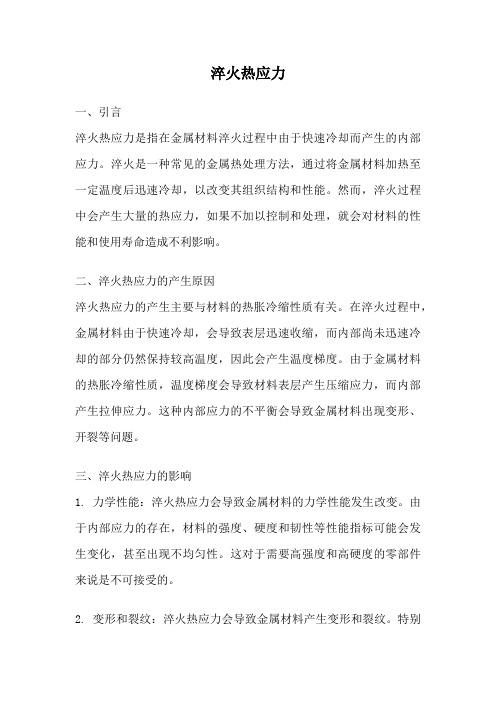
淬火热应力一、引言淬火热应力是指在金属材料淬火过程中由于快速冷却而产生的内部应力。
淬火是一种常见的金属热处理方法,通过将金属材料加热至一定温度后迅速冷却,以改变其组织结构和性能。
然而,淬火过程中会产生大量的热应力,如果不加以控制和处理,就会对材料的性能和使用寿命造成不利影响。
二、淬火热应力的产生原因淬火热应力的产生主要与材料的热胀冷缩性质有关。
在淬火过程中,金属材料由于快速冷却,会导致表层迅速收缩,而内部尚未迅速冷却的部分仍然保持较高温度,因此会产生温度梯度。
由于金属材料的热胀冷缩性质,温度梯度会导致材料表层产生压缩应力,而内部产生拉伸应力。
这种内部应力的不平衡会导致金属材料出现变形、开裂等问题。
三、淬火热应力的影响1. 力学性能:淬火热应力会导致金属材料的力学性能发生改变。
由于内部应力的存在,材料的强度、硬度和韧性等性能指标可能会发生变化,甚至出现不均匀性。
这对于需要高强度和高硬度的零部件来说是不可接受的。
2. 变形和裂纹:淬火热应力会导致金属材料产生变形和裂纹。
特别是对于大尺寸和复杂形状的零部件来说,由于热应力的不均匀分布,会导致局部应力集中,从而引起裂纹的产生。
这会降低零部件的强度和使用寿命,甚至导致零部件失效。
3. 内部组织和性能:淬火热应力还会对金属材料的内部组织和性能产生影响。
由于受到应力的影响,材料的晶粒尺寸、晶界形态和相变行为等都可能发生改变。
这可能导致材料的硬度、韧性、疲劳寿命等性能指标发生不利变化。
四、淬火热应力的控制方法为了有效控制淬火热应力,保证材料的性能和使用寿命,可以采取以下几种方法:1. 适当选择冷却介质:不同的冷却介质具有不同的冷却速率,可以通过选择合适的冷却介质来控制淬火过程中的冷却速率,从而减小热应力的产生。
2. 采用预淬火处理:预淬火处理是在正式淬火之前,先进行一次较为缓慢的冷却处理。
这可以减小淬火过程中的温度梯度,减少热应力的产生。
3. 采用温度梯度控制淬火:通过控制淬火过程中的温度梯度分布,可以减小热应力的产生。
热处理淬火应力及其分布的影响因素

工件淬火时,热应力和组织应力都将在同一工件中发生,绝大多数情况下还同时发生。
例如普通钢件淬火时,从加热温度冷却至Ms点以前产生热应力,继续冷却时,热应力继续发生变化;但与此同时,由于发生奥氏体向马氏体转变,则还产生组织应力,因此,在实际工件上产生的应力应为热应力与组织应力这二者叠加的结果。
而热应力与组织应力二者的变化规律恰好相反,因此如何恰当利用其彼此相反的特性,以减少变形、开裂,是很重要的。
影响淬火应力的因素:1、含碳量的影响钢中含碳量增加,马氏体比体积增大,淬火后组织应力应增加。
但钢中(溶入奥氏体中)含碳量增加,使Ms下降,淬火后残余奥氏体量增加,因而组织应力下降。
综合这两方面的相反作用效果,随着含碳量增加,热应力作用逐渐减弱,组织应力逐渐增强。
随着含碳量的增加,表面压应力值逐渐减小,拉应力值逐渐增大,而且拉应力值的位置越来越靠近表面。
此外,随着含碳量的增加,孪晶型马氏体数量增多,马氏体生长过程中有裂纹存在,这些均将导致增大高碳钢淬裂倾向性。
2、合金元素的影响钢中加入合金元素后,其热导率下降,导致热应力和组织应力增加。
多数合金元素使Ms下降,这使热应力作用增强。
凡增加钢的淬透性的合金元素,在工件没有完全淬透的情况下,有增强组织应力的作用。
3、工件尺寸的影响工件尺寸大小对内应力分布的影响,有以下两种情况。
(1)完全淬透的情况。
工件尺寸大小主要影响淬火冷却过程中截面的温差,特别是在高温区工件表面与淬火介质温度差大,冷却快,而工件尺寸越大中心部位热量向表面的传导越慢,因而工件尺寸越大对高温区的温差影响越大。
因此可以推知,当工件直径较小时,温差较小,热应力作用较小,应力特征主要为组织应力型;而直径较大时,使高温区的温差影响突出,热应力作用增强,因而工件淬火应力变成热应力型。
(2)不完全淬透情况。
在工件没有完全淬透的情况下,除了前述的热应力和组织应力外,尚因表面淬硬部位是马氏体,未淬硬部位是非马氏体而产生组织不同情况。
热处理对金属材料的应力松弛的影响

热处理对金属材料的应力松弛的影响热处理是金属材料加工中常用的一种方法,通过对材料进行加热和冷却来改变其物理和化学性质,以达到所需的性能和微观结构。
然而,热处理过程可能引起金属材料的应力松弛,这对材料性能和使用寿命产生重要影响。
本文将讨论热处理对金属材料应力松弛的影响及其原因。
一、应力松弛的定义应力松弛是指金属材料在受力作用下,在一段时间内减小或消失内部残余应力的过程。
热处理后,材料的内部结构会发生改变,原有的残余应力会发生重新分布或消失,从而减小了材料的内部应力。
二、热处理对应力松弛的影响1. 温度变化引起的热应力在热处理过程中,材料经历了加热和冷却两个过程,温度的快速变化会导致材料内部出现热应力。
这种应力会增大材料的内部应力,从而导致应力松弛的增加。
2. 相变引起的残余应力平衡热处理过程中,材料的晶体结构可能发生相变,如经过固溶体化处理后再经过淬火等冷却过程。
这些相变会引起材料内部的残余应力,而这些残余应力会通过应力松弛来重新平衡。
3. 冷却速率与晶粒大小的影响热处理中的冷却速率对金属材料的晶粒尺寸有重要的影响。
快速冷却可以得到较小的晶粒,而慢速冷却则会得到较大的晶粒。
较小的晶粒内部的应力比较均匀,容易松弛,而较大的晶粒则容易形成应力集中点,导致应力松弛困难。
三、应力松弛的机制1. 塑性应变释放热处理后,材料内部的塑性应变会通过晶格或晶间滑移的方式逐渐释放出来,从而减小应力松弛。
2. 晶界滑移和晶界转动材料在热处理过程中,晶界的滑移和转动可以减小晶界的能量,从而释放内部应力。
3. 再结晶过程热处理过程中,材料内部可能会发生再结晶现象,这个过程可以使材料内部的局部应变得到释放,减小材料的应力。
四、应力松弛对材料性能的影响1. 综合力学性能应力松弛对金属材料的机械性能具有重要影响,包括材料的强度、延伸性和韧性等。
2. 耐蚀性能应力松弛会导致材料内部的残余应力减小,从而降低材料的应力腐蚀敏感性。
3. 疲劳寿命应力松弛对金属材料的疲劳寿命产生显著影响,合理的热处理过程可以有效延长材料的疲劳寿命。
钢材热处理工艺对材料应力和变形的影响研究
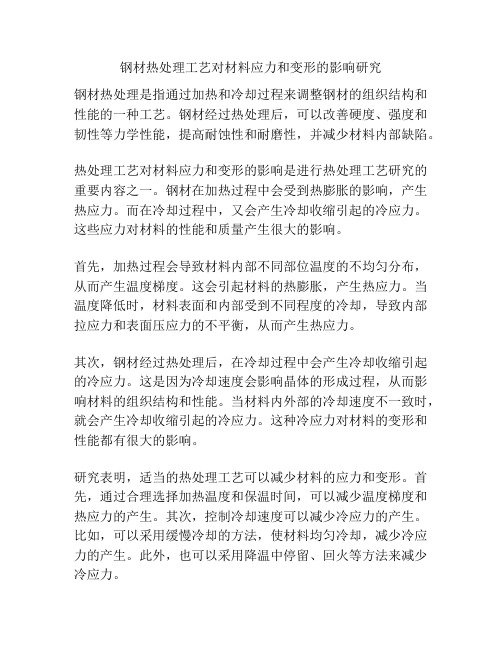
钢材热处理工艺对材料应力和变形的影响研究钢材热处理是指通过加热和冷却过程来调整钢材的组织结构和性能的一种工艺。
钢材经过热处理后,可以改善硬度、强度和韧性等力学性能,提高耐蚀性和耐磨性,并减少材料内部缺陷。
热处理工艺对材料应力和变形的影响是进行热处理工艺研究的重要内容之一。
钢材在加热过程中会受到热膨胀的影响,产生热应力。
而在冷却过程中,又会产生冷却收缩引起的冷应力。
这些应力对材料的性能和质量产生很大的影响。
首先,加热过程会导致材料内部不同部位温度的不均匀分布,从而产生温度梯度。
这会引起材料的热膨胀,产生热应力。
当温度降低时,材料表面和内部受到不同程度的冷却,导致内部拉应力和表面压应力的不平衡,从而产生热应力。
其次,钢材经过热处理后,在冷却过程中会产生冷却收缩引起的冷应力。
这是因为冷却速度会影响晶体的形成过程,从而影响材料的组织结构和性能。
当材料内外部的冷却速度不一致时,就会产生冷却收缩引起的冷应力。
这种冷应力对材料的变形和性能都有很大的影响。
研究表明,适当的热处理工艺可以减少材料的应力和变形。
首先,通过合理选择加热温度和保温时间,可以减少温度梯度和热应力的产生。
其次,控制冷却速度可以减少冷应力的产生。
比如,可以采用缓慢冷却的方法,使材料均匀冷却,减少冷应力的产生。
此外,也可以采用降温中停留、回火等方法来减少冷应力。
除了热处理工艺本身的影响外,材料的组织结构和化学成分也会对应力和变形产生影响。
比如,合适的加热温度可以促使材料发生相变,从而改变其组织结构,减少应力和变形。
此外,合适的化学成分可以改变材料的热膨胀系数和热导率,从而减少应力和变形的产生。
综上所述,钢材热处理工艺对材料应力和变形的影响是一个复杂的物理过程。
合理选择热处理工艺、控制温度、时间和冷却速度等因素,可以有效地减少应力和变形的产生,提高材料的性能和质量。
研究钢材热处理工艺对材料应力和变形的影响,对于优化热处理工艺,提高钢材的综合性能和质量具有重要意义。
焊接后热处理对焊接残余应力的影响

焊接后热处理对焊接残余应力的影响摘要:焊接作为一个不均匀性的加热过程,在焊接结构的局部发生塑性变形问题,经过冷却之后,工件内部就会残留部分应力。
如果发生焊接残余应力,不仅对工件的机械强度造成影响,也可能引发工件的开裂、变形,降低尺寸的精确度。
本文结合焊接后热处理技术要点,对焊接残余应力的影响因素、危害以及消除策略等进行分析与探讨。
关键词:焊接;热处理;残余应力;影响1影响焊接残余应力的主要因素1.1焊接原材料的影响随着原材料的熔化温度变化,焊接的残余应力也会相应发生变化。
其温度越高、残余应力就越大。
同时,对残余应力大小的影响因素还包括:线膨胀系数、屈服强度、弹性模量等。
原材料的种类不同,由此产生的变化也有所区别。
当膨胀系数处于高温条件下,其温度就会持续上升,此时为线性增加状态;屈服强度、弹性模量等都会随着原材料类型的不同而表现出不同的反应。
1.2焊接参数的影响在相对正常的焊接条件下,若想确保焊接电流不产生任何变化,则需要提高焊接效率,此时将延长焊接的温度场,同时增加了焊接的梯度,此时焊接残余应力就会加大。
若想确保焊接的速度不发生改变,则提高焊接电流强度,此时焊接的温度场就会变宽、加长,增加温度梯度,焊接的残余应力也相应加大。
1.3焊接热源的影响在结构焊接过程中,一般只采取局部加热方法,但是热源中心的温度一般较高,由于焊缝与焊件不同点之间的距离存在差异,因此在加热的瞬间,各点温度会产生变化,温度场也可能有所改变。
由于加热并不是均匀进行,焊件的温度梯度有所增加,对焊接残余应力大小造成影响。
如果在自然条件下完成焊件的冷却,此时温度由800℃降低到500℃,无论是焊接的残余应力还是应变力大小,都会受到影响,需加强重视。
1.4焊接比容的影响当钢材结构经过加热或者冷却之后,就会产生相变作用,由此变化也会引发比容、性能等改变。
一般情况下,如果温度已经上升到700℃以上,那么钢材就会由奥氏体转变为铁素体,但是对残余应力的影响可以忽略不计。
热处理过程中材料的应力的变化

热处理过程中材料的应力的变化
热处理是金属材料加工过程中重要的一环,可为材料赋予所需的力
学性质和组织结构。
然而,在热处理过程中,材料内部会发生诸多变化。
其中,应力的变化是十分重要的,以下是应力变化的主要表现:
1. 相变应力
在金属材料热处理过程中,如果晶格结构发生相变,就会产生相变应力。
相变引起的内部压力会随着材料温度的变化而发生变化,导致材
料产生应力。
2. 残余应力
金属材料经过热处理后,内部组织结构和化学成分发生了变化,残余
应力的形成也就在所难免了。
当热处理结束后,材料的温度迅速降低,由于材料内部各处的热膨胀系数不同,就会产生残余应力。
3. 弹性变形应力
弹性变形应力,也被称为弹性残留应力,在热处理过程中的形成主要
源于材料的分解过程。
当材料受到一定的挤压或拉伸时,会产生一定
程度的弹性变形,而这一变形的应力就是弹性变形应力。
4. 加工应力
加工应力是材料加工过程中的一种内部应力,主要产生于金属材料的塑性变形过程中。
当材料受到加工而变形时,就会产生一定程度的加工应力,这种应力会在热处理过程中得到释放。
总之,在金属材料热处理过程中,应力变化具有多种表现形式。
了解这些应力变化和其产生的原因,对于制定金属材料的热处理工艺和保证材料性质是十分重要的。
焊接后热处理技术及焊接残余应力的影响分析
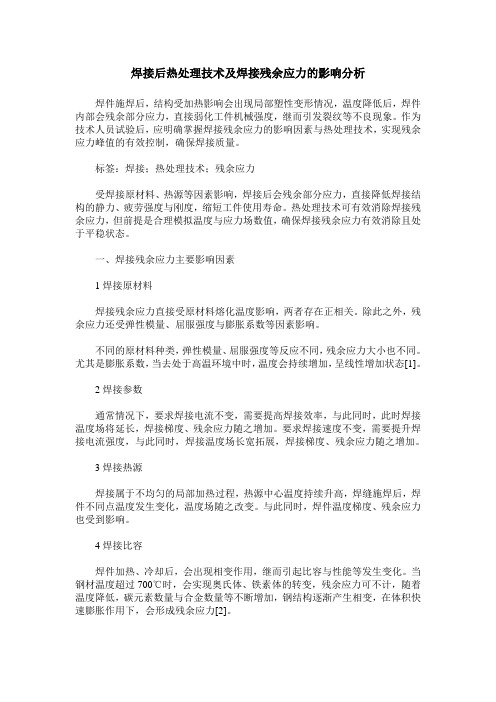
焊接后热处理技术及焊接残余应力的影响分析焊件施焊后,结构受加热影响会出现局部塑性变形情况,温度降低后,焊件内部会残余部分应力,直接弱化工件机械强度,继而引发裂纹等不良现象。
作为技术人员试验后,应明确掌握焊接残余应力的影响因素与热处理技术,实现残余应力峰值的有效控制,确保焊接质量。
标签:焊接;热处理技术;残余应力受焊接原材料、热源等因素影响,焊接后会残余部分应力,直接降低焊接结构的静力、疲劳强度与刚度,缩短工件使用寿命。
热处理技术可有效消除焊接残余应力,但前提是合理模拟温度与应力场数值,确保焊接残余应力有效消除且处于平稳状态。
一、焊接残余应力主要影响因素1焊接原材料焊接残余应力直接受原材料熔化温度影响,两者存在正相关。
除此之外,残余应力还受弹性模量、屈服强度与膨胀系数等因素影响。
不同的原材料种类,弹性模量、屈服强度等反应不同,残余应力大小也不同。
尤其是膨胀系数,当去处于高温环境中时,温度会持续增加,呈线性增加状态[1]。
2焊接参数通常情况下,要求焊接电流不变,需要提高焊接效率,与此同时,此时焊接温度场将延长,焊接梯度、残余应力随之增加。
要求焊接速度不变,需要提升焊接电流强度,与此同时,焊接温度场长宽拓展,焊接梯度、残余应力随之增加。
3焊接热源焊接属于不均匀的局部加热过程,热源中心温度持续升高,焊缝施焊后,焊件不同点温度发生变化,温度场随之改变。
与此同时,焊件温度梯度、残余应力也受到影响。
4焊接比容焊件加热、冷却后,会出现相变作用,继而引起比容与性能等发生变化。
当钢材温度超过700℃时,会实现奥氏体、铁素体的转变,残余应力可不计,随着温度降低,碳元素数量与合金数量等不断增加,钢结构逐渐产生相变,在体积快速膨胀作用下,会形成残余应力[2]。
二、焊接残余应力对构件的危害1焊件静力强度下降焊件结构在承载力影响下,会产生一定的塑性变形能力。
屈服强度区域应力随者荷载力的增加而加大,不在屈服强度的区域应力也随之改变,此时,静力强度不受焊接残余应力影响。
热处理对降低金属材料内应力的效果

热处理对降低金属材料内应力的效果热处理是一种常用的金属加工方法,通过对金属材料进行加热和冷却的过程,可以改善其力学性能和物理性质。
在这个过程中,热处理对降低金属材料内应力起着重要的作用。
本文将探讨热处理对降低金属材料内应力的效果。
首先,热处理能够通过减轻或消除金属材料内部的应力,提高其机械性能和耐腐蚀性。
在金属材料的加工和制造过程中,可能会产生各种应力,如冷变形、残余应力等。
这些应力会对金属材料的性能和寿命产生负面影响。
而通过热处理,可以对金属材料进行再结晶退火、回火处理等,从而使其内部的应力得以释放和消除,避免应力集聚和脆性断裂的发生,大大提高金属材料的可靠性和使用寿命。
其次,热处理还可以对金属材料进行强化和调质,改善其内部结构和晶粒大小,从而减小内应力的生成。
通过热处理的加热和冷却过程,可以改变材料的晶体结构和组织形态,提高其强度和硬度。
通过合理的热处理工艺,可以使材料的晶粒尺寸减小,晶界增多,从而减小材料的内部应力。
同时,在热处理过程中,还可以通过固溶、析出等相变过程调控金属材料的组织状态,降低内应力的产生。
这些措施有助于提高金属材料的耐用性和抗疲劳性能,减轻应力集中和塑性变形,降低金属材料内应力的生成。
此外,热处理还可以改变金属材料的化学成分和组织结构,减少内应力的积累。
在某些情况下,金属材料的内应力可能来自于化学成分的不均匀或晶体结构的非平衡状态。
通过热处理可以调整金属材料的成分和组织结构,消除杂质和间隙原子等缺陷,使其达到热平衡状态,从而减少内应力的积累。
例如,热处理中的回火过程可以通过沉淀硬化作用消除析出物,改善材料的均匀性和稳定性,从而减小内应力。
综上所述,热处理对降低金属材料内应力具有显著的效果。
它可以通过减轻和消除材料内部的应力,提高材料的力学性能和耐腐蚀性;通过强化和调质的方式改善内部结构和晶粒大小,减小内应力的生成;同时,通过调控材料的成分和组织结构,减少内应力的积累。
因此,在金属材料的加工和制造过程中,合理应用热处理技术,可以有效降低金属材料的内应力,提高其可靠性和使用寿命。
残余应力对热处理的影响
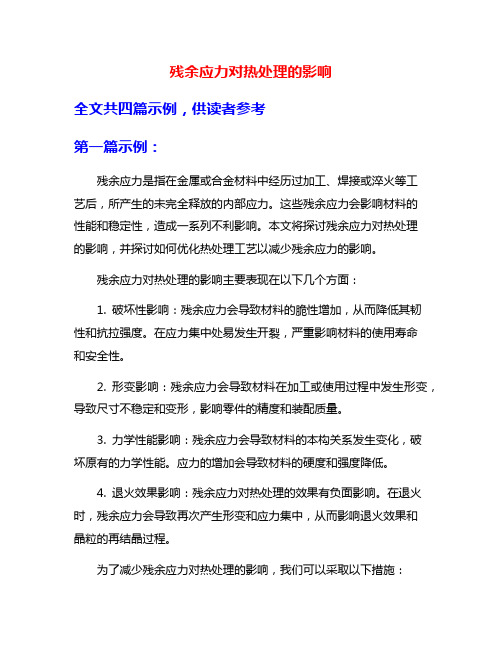
残余应力对热处理的影响全文共四篇示例,供读者参考第一篇示例:残余应力是指在金属或合金材料中经历过加工、焊接或淬火等工艺后,所产生的未完全释放的内部应力。
这些残余应力会影响材料的性能和稳定性,造成一系列不利影响。
本文将探讨残余应力对热处理的影响,并探讨如何优化热处理工艺以减少残余应力的影响。
残余应力对热处理的影响主要表现在以下几个方面:1. 破坏性影响:残余应力会导致材料的脆性增加,从而降低其韧性和抗拉强度。
在应力集中处易发生开裂,严重影响材料的使用寿命和安全性。
2. 形变影响:残余应力会导致材料在加工或使用过程中发生形变,导致尺寸不稳定和变形,影响零件的精度和装配质量。
3. 力学性能影响:残余应力会导致材料的本构关系发生变化,破坏原有的力学性能。
应力的增加会导致材料的硬度和强度降低。
4. 退火效果影响:残余应力对热处理的效果有负面影响。
在退火时,残余应力会导致再次产生形变和应力集中,从而影响退火效果和晶粒的再结晶过程。
为了减少残余应力对热处理的影响,我们可以采取以下措施:1. 合理控制加工工艺:在加工过程中,应合理控制温度、速度和应力等参数,避免产生过大的残余应力。
2. 适当退火处理:在材料加工后进行适当的退火处理,可减少残余应力的影响,恢复材料的力学性能和结构稳定性。
3. 采用热处理工艺:在产品设计和制造过程中,合理选择热处理工艺,如淬火、回火或正火等,可以减少残余应力的产生,提高材料的性能和稳定性。
4. 精确控制温度和时间:在热处理过程中,应精确控制温度和时间,避免过热或过冷,以减小残余应力的产生。
残余应力对热处理有着不可忽视的影响,我们需要重视残余应力的形成和影响机制,并采取合适的措施减少其影响。
通过合理的工艺优化和热处理处理,我们可以有效减少残余应力的产生,提高材料的性能和稳定性,确保产品质量和安全性。
【字数达到要求,2000字】。
第二篇示例:残余应力是指在零应力下发生形变后,当去掉外加的载荷或变温后,材料内部所保留的应力。
热处理对金属材料的残余应力和变形行为的影响分析
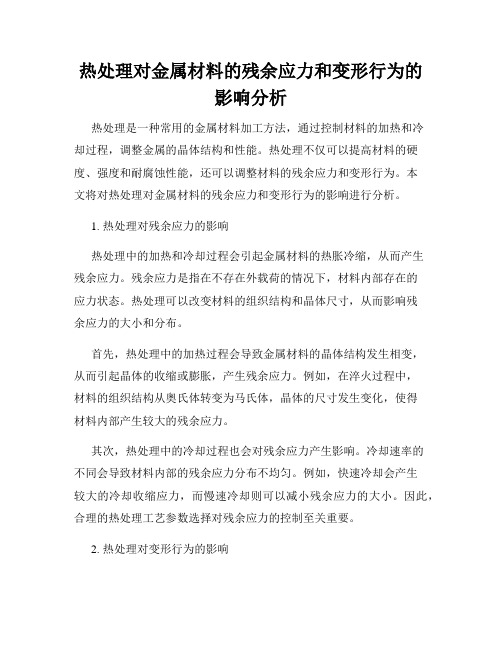
热处理对金属材料的残余应力和变形行为的影响分析热处理是一种常用的金属材料加工方法,通过控制材料的加热和冷却过程,调整金属的晶体结构和性能。
热处理不仅可以提高材料的硬度、强度和耐腐蚀性能,还可以调整材料的残余应力和变形行为。
本文将对热处理对金属材料的残余应力和变形行为的影响进行分析。
1. 热处理对残余应力的影响热处理中的加热和冷却过程会引起金属材料的热胀冷缩,从而产生残余应力。
残余应力是指在不存在外载荷的情况下,材料内部存在的应力状态。
热处理可以改变材料的组织结构和晶体尺寸,从而影响残余应力的大小和分布。
首先,热处理中的加热过程会导致金属材料的晶体结构发生相变,从而引起晶体的收缩或膨胀,产生残余应力。
例如,在淬火过程中,材料的组织结构从奥氏体转变为马氏体,晶体的尺寸发生变化,使得材料内部产生较大的残余应力。
其次,热处理中的冷却过程也会对残余应力产生影响。
冷却速率的不同会导致材料内部的残余应力分布不均匀。
例如,快速冷却会产生较大的冷却收缩应力,而慢速冷却则可以减小残余应力的大小。
因此,合理的热处理工艺参数选择对残余应力的控制至关重要。
2. 热处理对变形行为的影响除了对残余应力的影响外,热处理还可以调整金属材料的变形行为,包括塑性变形和弹性变形。
首先,热处理可以提高金属材料的塑性变形能力。
在热处理过程中,晶体结构的调整可以使材料的晶界和位错运动更加容易,从而提高材料的塑性变形能力。
例如,在退火处理中,材料的晶粒得到了细化,晶界的移动路径减小,增加了材料在塑性变形过程中的滞后与吸收应变的能力。
其次,热处理还可以调整材料的弹性变形行为。
材料经过热处理后,其弹性模量、屈服强度等力学性能会发生变化。
例如,时效处理可以提高合金材料的强度和硬度,使材料具有较高的弹性变形能力。
另外,热处理还可以改善金属材料的应力松弛行为。
材料在热处理后,残余应力会通过应力松弛的方式逐渐减小。
应力松弛是指材料在存在残余应力的情况下,由于位错在晶体中的滑动和扩散,使得部分应力得以释放。
残余应力对热处理的影响-概述说明以及解释

残余应力对热处理的影响-概述说明以及解释1.引言1.1 概述残余应力是指在材料内部存在的一种留存状态的应力,它可以在热处理过程中产生或减小。
残余应力的存在对材料的性能和稳定性有着重要的影响,因此研究残余应力与热处理的关系具有重要的理论和实际意义。
本文将首先介绍残余应力的概念以及其在材料中的形成机制,然后探讨热处理在材料加工过程中的作用,最后分析残余应力对热处理过程产生的影响。
通过深入探讨残余应力与热处理之间的关系,有助于更好地理解材料的行为,提高材料的性能和延长材料的使用寿命。
1.2 文章结构文章结构部分应包括对整篇文章的内容安排和组织方式进行详细说明,以引导读者对文章的整体结构有清晰的认识。
在这篇关于残余应力对热处理的影响的文章中,文章结构应该包括引言、正文和结论三个主要部分。
引言部分应该简要介绍文章的主题并概述文章的目的和重要性。
正文部分将详细阐述残余应力的概念、热处理的作用以及残余应力对热处理的影响。
最后结论部分将对文章的主要内容进行总结,并探讨残余应力与热处理之间的关系,实际应用中的意义,以及未来研究方向。
通过清晰的文章结构安排,读者可以快速了解整篇文章的内容,并更好地理解作者的观点和论述。
1.3 目的:本文旨在探讨残余应力对热处理的影响,探讨残余应力与热处理之间的相互关系。
我们将深入剖析残余应力的概念、热处理的作用以及残余应力对热处理的具体影响,以期为相关领域的研究和实践提供理论支撑和参考依据。
通过本文的研究,我们希望能够更好地理解残余应力与热处理之间的关系,为工程领域的实际生产提供一定的指导和帮助,促进相关领域的发展和进步。
2.正文2.1 残余应力的概念残余应力是指在材料内部的应力状态,在材料形成过程中产生或者在外部加载消失后保留在材料内部的应力。
在材料经历了各种加工过程,如焊接、锻造、冷却等后,内部会出现不均匀的温度和应变分布,导致产生残余应力。
这种应力不会通过外力作用而发生变化,会一直存在于材料内部,直到被外部力量释放。
热处理对金属材料的应力松弛行为的影响

热处理对金属材料的应力松弛行为的影响热处理是一种常见的金属加工方法,通过控制材料的温度和时间来改善其物理和化学性能。
在热处理的过程中,材料会受到热应力的影响,而这些热应力可能会引起材料的应力松弛行为。
本文将探讨热处理对金属材料的应力松弛行为的影响,并分析其中的原因。
一、热处理对金属材料的应力松弛行为有着显著的影响。
在热处理过程中,材料的晶体结构会发生改变,晶界的形态和尺寸也会发生变化。
这些变化会导致材料内部的应力重新分布,从而引起应力松弛。
首先,热处理会改变材料的晶体结构。
例如,通过固溶处理,金属材料中的固溶体相可能会发生一定程度的溶解和析出,从而改变了晶体的结构。
这种晶体结构的改变可能会引起晶界的移动和变形,导致应力的释放和松弛。
其次,热处理还会改变材料的晶界形态和尺寸。
在热处理过程中,晶界的移动和再结晶现象会发生,从而改变了晶界的形态和尺寸。
这种晶界的形态和尺寸的改变会导致材料内部的位错和晶片重新组合,从而引起应力的释放和松弛。
最后,热处理还会改变材料的化学成分和相变行为。
在热处理过程中,金属材料的化学成分可能会发生变化,例如,发生固溶、析出或相变等现象。
这种化学成分的变化会引起金属材料内部的晶粒和相的重新排列,从而导致应力的释放和松弛。
二、热处理对金属材料的应力松弛行为的原因分析热处理对金属材料的应力松弛行为的影响可以通过以下几个方面进行原因分析。
首先,热处理改变了材料的晶体结构,导致晶体中的位错重新排列。
位错是金属材料中的一种晶格缺陷,位错的运动和重新组合可能会引起材料内部的应力分布重新调整,导致应力的释放和松弛。
其次,热处理改变了材料的晶界形态和尺寸,导致晶界的移动和再结晶现象发生。
晶界是晶体中不同晶粒之间的边界,晶界的形态和尺寸对应力的分布和释放有着重要影响。
当晶界发生移动和再结晶现象时,材料内部的位错和晶片会重新组合,从而导致应力的释放和松弛。
最后,热处理改变了材料的化学成分和相变行为,导致晶粒和相的重新排列。
热处理过程中材料的应力的变化
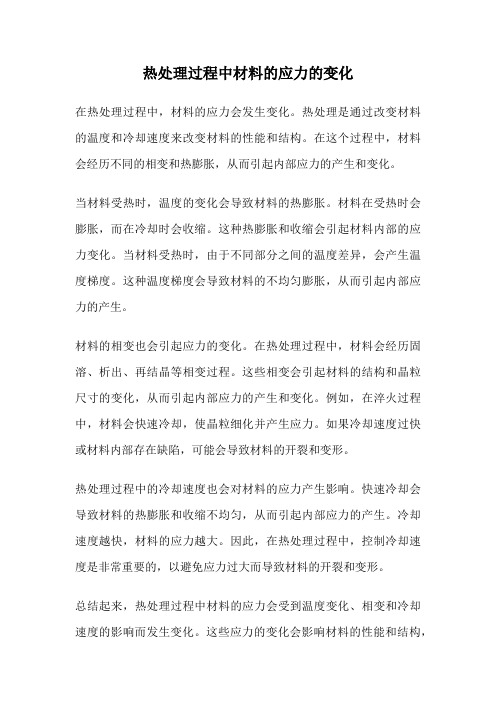
热处理过程中材料的应力的变化
在热处理过程中,材料的应力会发生变化。
热处理是通过改变材料的温度和冷却速度来改变材料的性能和结构。
在这个过程中,材料会经历不同的相变和热膨胀,从而引起内部应力的产生和变化。
当材料受热时,温度的变化会导致材料的热膨胀。
材料在受热时会膨胀,而在冷却时会收缩。
这种热膨胀和收缩会引起材料内部的应力变化。
当材料受热时,由于不同部分之间的温度差异,会产生温度梯度。
这种温度梯度会导致材料的不均匀膨胀,从而引起内部应力的产生。
材料的相变也会引起应力的变化。
在热处理过程中,材料会经历固溶、析出、再结晶等相变过程。
这些相变会引起材料的结构和晶粒尺寸的变化,从而引起内部应力的产生和变化。
例如,在淬火过程中,材料会快速冷却,使晶粒细化并产生应力。
如果冷却速度过快或材料内部存在缺陷,可能会导致材料的开裂和变形。
热处理过程中的冷却速度也会对材料的应力产生影响。
快速冷却会导致材料的热膨胀和收缩不均匀,从而引起内部应力的产生。
冷却速度越快,材料的应力越大。
因此,在热处理过程中,控制冷却速度是非常重要的,以避免应力过大而导致材料的开裂和变形。
总结起来,热处理过程中材料的应力会受到温度变化、相变和冷却速度的影响而发生变化。
这些应力的变化会影响材料的性能和结构,
因此在热处理过程中需要注意控制温度和冷却速度,以避免应力过大而导致材料的开裂和变形。
在实际应用中,根据不同材料的特性和要求,可以选择合适的热处理方法和工艺参数,以达到预期的效果。
- 1、下载文档前请自行甄别文档内容的完整性,平台不提供额外的编辑、内容补充、找答案等附加服务。
- 2、"仅部分预览"的文档,不可在线预览部分如存在完整性等问题,可反馈申请退款(可完整预览的文档不适用该条件!)。
- 3、如文档侵犯您的权益,请联系客服反馈,我们会尽快为您处理(人工客服工作时间:9:00-18:30)。
热处理应力及其影响热处理残余力是指工件经热处理后最终残存下来的应力,对工件的形状,;尺寸和性能都有极为重要的影响。
当它超过材料的屈服强度时,;便引起工件的变形,超过材料的强度极限时就会使工件开裂,这是它有害的一面,应当减少和消除。
但在一定条件下控制应力使之合理分布,就可以提高零件的机械性能和使用寿命,变有害为有利。
分析钢在热处理过程中应力的分布和变化规律,使之合理分布对提高产品质量有着深远的实际意义。
例如关于表层残余压应力的合理分布对零件使用寿命的影响问题已经引起了人们的广泛重视。
一、钢的热处理应力工件在加热和冷却过程中,由于表层和心部的冷却速度和时间的不一致,形成温差,就会导致体积膨胀和收缩不均而产生应力,即热应力。
在热应力的作用下,由于表层开始温度低于心部,收缩也大于心部而使心部受拉,当冷却结束时,由于心部最后冷却体积收缩不能自由进行而使表层受压心部受拉。
即在热应力的作用下最终使工件表层受压而心部受拉。
这种现象受到冷却速度,材料成分和热处理工艺等因素的影响。
当冷却速度愈快,含碳量和合金成分愈高,冷却过程中在热应力作用下产生的不均匀塑性变形愈大,最后形成的残余应力就愈大。
另一方面钢在热处理过程中由于组织的变化即奥氏体向马氏体转变时,因比容的增大会伴随工件体积的膨胀,;工件各部位先后相变,造成体积长大不一致而产生组织应力。
组织应力变化的最终结果是表层受拉应力,心部受压应力,恰好与热应力相反。
组织应力的大小与工件在马氏体相变区的冷却速度,形状,材料的化学成分等因素有关。
实践证明,任何工件在热处理过程中,;只要有相变,热应力和组织应力都会发生。
;只不过热应力在组织转变以前就已经产生了,而组织应力则是在组织转变过程中产生的,在整个冷却过程中,热应力与组织应力综合作用的结果,;就是工件中实际存在的应力。
这两种应力综合作用的结果是十分复杂的,受着许多因素的影响,如成分、形状、热处理工艺等。
就其发展过程来说只有两种类型,即热应力和组织应力,作用方向相反时二者抵消,作用方向相同时二者相互迭加。
不管是相互抵消还是相互迭加,两个应力应有一个占主导因素,热应力占主导地位时的作用结果是工件心部受拉,表面受压。
;组织应力占主导地位时的作用结果是工件心部受压表面受拉。
二、热处理应力对淬火裂纹的影响存在于淬火件不同部位上能引起应力集中的因素(包括冶金缺陷在内),对淬火裂纹的产生都有促进作用,但只有在拉应力场内(;尤其是在最大拉应力下)才会表现出来,;若在压应力场内并无促裂作用。
淬火冷却速度是一个能影响淬火质量并决定残余应力的重要因素,也是一个能对淬火裂纹赋于重要乃至决定性影响的因素。
为了达到淬火的目的,通常必须加速零件在高温段内的冷却速度,并使之超过钢的临界淬火冷却速度才能得到马氏体组织。
就残余应力而论,这样做由于能增加抵消组织应力作用的热应力值,故能减少工件表面上的拉应力而达到抑制纵裂的目的。
其效果将随高温冷却速度的加快而增大。
而且,在能淬透的情况下,截面尺寸越大的工件,虽然实际冷却速度更缓,开裂的危险性却反而愈大。
这一切都是由于这类钢的热应力随尺寸的增大实际冷却速度减慢,热应力减小,;组织应力随尺寸的增大而增加,最后形成以组织应力为主的拉应力作用在工件表面的作用特点造成的。
并与冷却愈慢应力愈小的传统观念大相径庭。
对这类钢件而言,在正常条件下淬火的高淬透性钢件中只能形成纵裂。
避免淬裂的可靠原则是设法尽量减小截面内外马氏体转变的不等时性。
仅仅实行马氏体转变区内的缓冷却不足以预防纵裂的形成。
一般情况下只能产生在非淬透性件中的弧裂,虽以整体快速冷却为必要的形成条件,可是它的真正形成原因,却不在快速冷却(包括马氏体转变区内)本身,而是淬火件局部位置(由几何结构决定),在高温临界温度区内的冷却速度显著减缓,因而没有淬硬所致;。
产生在大型非淬透性件中的横断和纵劈,是由以热应力为主要成份的残余拉应力作用在淬火件中心;,而在淬火件末淬硬的截面中心处,首先形成裂纹并由内往外扩展而造成的。
为了避免这类裂纹产生,往往使用水--油双液淬火工艺。
在此工艺中实施高温段内的快速冷却,目的仅仅在于确保外层金属得到马氏体组织,;而从内应力的角度来看,这时快冷有害无益。
其次,冷却后期缓冷的目的,主要不是为了降低马氏体相变的膨胀速度和组织应力值,而在于尽量减小截面温差和截面中心部位金属的收缩速度,从而达到减小应力值和最终抑制淬裂的目的。
三、残余压应力对工件的影响渗碳表面强化作为提高工件的疲劳强度的方法应用得很广泛的原因。
一方面是由于它能有效的增加工件表面的强度和硬度,提高工件的耐磨性,另一方面是渗碳能有效的改善工件的应力分布,在工件表面层获得较大的残余压应力,;提高工件的疲劳强度。
如果在渗碳后再进行等温淬火将会增加表层残余压应力,使疲劳强度得到进一步的提高。
有人对35SiMn2MoV钢渗碳后进行等温淬火与渗碳后淬火低温回火的残余应力进行过测试其热处理工艺残余应力值(kg/mm2)渗碳后880-900度盐浴加热,260度等温40分钟-65渗碳后880-900度盐浴加热淬火,260度等温90分钟-18渗碳后880-900度盐浴加热,260度等温40分钟,260度回火9 0分钟-38表1.35SiMn2MoV钢渗碳等温淬火与渗碳低温回火后的残余应力值从表1的测试结果可以看出等温淬火比通常的淬火低温回火工艺具有更高的表面残余压应力。
等温淬火后即使进行低温回火,其表面残余压应力,也比淬火后低温回火高。
因此可以得出这样一个结论,即渗碳后等温淬火比通常的渗碳淬火低温回火获得的表面残余压应力更高,从表面层残余压应力对疲劳抗力的有利影响的观点来看,渗碳等温淬火工艺是提高渗碳件疲劳强度的有效方法。
渗碳淬火工艺为什么能获得表层残余压应力?渗碳等温淬火为什么能获得更大的表层残余压应力?其主要原因有两个:一个原因是表层高碳马氏体比容比心部低碳马氏体的比容大,淬火后表层体积膨胀大,而心部低碳马氏体体积膨胀小,制约了表层的自由膨胀,;造成表层受压心部受拉的应力状态。
而另一个更重要的原因是高碳过冷奥氏体向马氏体转变的开始转变温度(Ms),比心部含碳量低的过冷奥氏体向马氏体转变的开始温度(Ms)低。
这就是说在淬火过程中往往是心部首先产生马氏体转变引起心部体积膨胀,并获得强化,而表面还末冷却到其对应的马氏体开始转变点(Ms),故仍处于过冷奥氏体状态,;具有良好的塑性,不会对心部马氏体转变的体积膨胀起严重的压制作用。
随着淬火冷却温度的不断下降使表层温度降到该处的(Ms)点以下,表层产生马氏体转变,引起表层体积的膨胀。
但心部此时早已转变为马氏体而强化,所以心部对表层的体积膨胀将会起很大的压制作用,使表层获得残余压应力。
;而在渗碳后进行等温淬火时,当等温温度在渗碳层的马氏体开始转变温度(Ms)以上,心部的马氏体开始转变温度(;Ms)点以下的适当温度等温淬火,比连续冷却淬火更能保证这种转变的先后顺序的特点(;即保证表层马氏体转变仅仅产生于等温后的冷却过程中)。
;当然渗碳后等温淬火的等温温度和等温时间对表层残余应力的大小有很大的影响。
有人对35SiMn2MoV钢试样渗碳后在260℃和320℃等温40;分钟后的表面残余应力进行过测试,其结果如表2。
由表2可知在260℃行动等温比在320℃等温的表面残余应力要高出一倍多可见表面残余应力状态对渗碳等温淬火的等温温度是很敏感的。
不仅等温温度对表面残余压应力状态有影响,而且等温时间也有一定的影响。
有人对35SiMn2V钢在310℃等温2分钟,10分钟, 90分钟的残余应力进行过测试。
2分钟后残余压应力为-20kg/m m,10分钟后为-60kg/mm,60分钟后为-80kg/mm,60分钟后再延长等温时间残余应力变化不大。
从上面的讨论表明,渗碳层与心部马氏体转变的先后顺序对表层残余应力的大小有重要影响。
渗碳后的等温淬火对进一步提高零件的疲劳寿命具有普遍意义。
此外能降低表层马氏体开始转变温度(Ms)点的表面化学热处理如渗碳、氮化、氰化等都为造成表层残余压应力提供了条件,如高碳钢的氮化--淬火工艺,由于表层,;氮含量的提高而降低了表层马氏体开始转变点(Ms),淬火后获得了较高的表层残余压应力使疲劳寿命得到提高。
又如氰化工艺往往比渗碳具有更高的疲劳强度和使用寿命,也是因氮含量的增加可获得比渗碳更高的表面残余压应力之故。
此外,;从获得表层残余压应力的合理分布的观点来看,单一的表面强化工艺不容易获得理想的表层残余压应力分布,而复合的表面强化工艺则可以有效的改善表层残余应力的分布。
如渗碳淬火的残余应力一般在表面压应力较低,最大压应力则出现在离表面一定深度处,而且残余压力层较厚。
氮化后的表面残余压应力很高,但残余压应力层很溥,往里急剧下降。
如果采用渗碳--;氮化复合强化工艺,则可获得更合理的应力分布状态。
;因此表面复合强化工艺,如渗碳--氮化,渗碳--;高频淬火等,都是值得重视的方向。
根据上述讨论可得出以下结论;1、热处理过程中产生的应力是不可避免的,而且往往是有害的;。
但我们可以控制热处理工艺尽量使应力分布合理,就可将其有害程度降低到最低限度,甚至变有害为有利。
2、当热应力占主导地位时应力分布为心部受拉表面受压,当组织应力占主导地时应力分布为心部受压表面受拉。
3、在高淬透性钢件中易形成纵裂,在非淬透性工件中往往形成弧裂,在大型非淬透工件中容易形成横断和纵劈。
4、渗碳使表层马氏体开始转变温度(Ms)点下降,可导至淬火时马氏体转变顺序颠倒,心部首先发生马氏体转变而后才波及到表面,可获得表层残余压应力而提高抗疲劳强度。
5、渗碳后进行等温淬火可保证心部马氏体转变充分进行以后,表层组织转变才进行。
;使工件获得比直接淬火更大的表层残余压应力,可进一步提高渗碳件的疲劳强度。
6、复合表面强化工艺可使表层残余压应力分布更合理,可明显提高工件的疲劳强度。