放电等离子烧结技术的原理及应用
放电等离子体烧结

放电等离子体烧结
放电等离子体烧结是一种先进的材料加工技术,通过放电等离子体的高温、高能量作用,实现材料的烧结和熔融,从而制备出具有优异性能的复杂形状零件。
这种技术在金属、陶瓷、复合材料等领域都有着广泛的应用。
放电等离子体烧结技术的原理是利用高压电场使气体放电产生等离子体,等离子体在电场的作用下加热材料并使其烧结。
这种烧结方式具有高温、高能量、高速等特点,可以实现材料的快速烧结和熔融,从而大大提高材料的致密性和机械性能。
在金属材料加工中,放电等离子体烧结可以实现对金属粉末的高效烧结,制备出高强度、高硬度的金属零件。
同时,还可以实现对金属表面的改性处理,提高金属的耐磨性和耐腐蚀性。
在陶瓷材料加工中,放电等离子体烧结可以实现对陶瓷粉末的快速烧结,制备出高强度、高韧性的陶瓷制品。
在复合材料加工中,放电等离子体烧结可以实现对复合材料的烧结和熔融,制备出具有优异性能的复合材料制品。
放电等离子体烧结技术具有许多优点,如烧结速度快、烧结温度高、烧结效果好等。
与传统的烧结方法相比,放电等离子体烧结可以大大缩短加工周期,提高生产效率,降低生产成本。
此外,放电等离子体烧结还可以实现对材料的局部加热和局部烧结,实现对复杂形状零件的加工,提高材料的利用率和加工精度。
随着科技的不断进步,放电等离子体烧结技术在材料加工领域的应用将会越来越广泛。
通过不断的研究和创新,放电等离子体烧结技术将会为材料加工领域带来更多的突破和进步,为人类社会的发展做出更大的贡献。
相信在不久的将来,放电等离子体烧结技术将会成为材料加工领域的重要技术,为人类创造出更多的奇迹。
《放电等离子烧结制备MAX-cBN复合材料》

《放电等离子烧结制备MAX-cBN复合材料》篇一一、引言在当前的工业应用中,高性能的复合材料以其卓越的物理和化学性能受到广泛关注。
其中,MAX-cBN(由MAX相陶瓷和立方氮化硼(cBN)组成的复合材料)因其高硬度、高热导率和良好的化学稳定性,在机械加工、电子封装和热管理等领域具有广泛的应用前景。
本文将详细介绍放电等离子烧结技术在制备MAX-cBN复合材料中的应用及其优势。
二、放电等离子烧结技术概述放电等离子烧结(SPS)技术是一种利用脉冲电流进行加热的固相烧结方法。
它利用强大的电场产生高能量密度等离子体,将颗粒间隙内的空气排净,通过产生的焦耳热直接作用于颗粒,从而达到烧结目的。
这种方法能够有效地减小颗粒尺寸、增强材料性能、缩短制备周期。
三、MAX-cBN复合材料的制备(一)材料选择与配比在制备MAX-cBN复合材料时,选择合适的MAX相陶瓷和cBN粉末是关键。
MAX相陶瓷具有优异的力学性能和热稳定性,而cBN则以其高硬度、高热导率和良好的化学稳定性著称。
通过合理的配比,可以获得具有优异性能的MAX-cBN复合材料。
(二)放电等离子烧结过程在放电等离子烧结过程中,首先将MAX相陶瓷和cBN粉末混合均匀,然后放入模具中。
通过施加一定的压力和电压,利用脉冲电流产生的高能量密度等离子体进行烧结。
在烧结过程中,颗粒间的结合力逐渐增强,形成致密的复合材料。
四、放电等离子烧结技术的优势(一)高效率:放电等离子烧结技术能够在短时间内完成烧结过程,大大缩短了制备周期。
(二)低能耗:由于等离子体直接作用于颗粒,使得能量利用率高,降低了能耗。
(三)提高性能:放电等离子烧结技术可以减小颗粒尺寸,增强材料性能。
同时,高能量密度等离子体的作用使得颗粒间的结合力增强,有利于获得致密的复合材料。
五、实验结果与讨论通过放电等离子烧结技术制备的MAX-cBN复合材料具有优异的性能。
X射线衍射(XRD)分析表明,材料具有明显的MAX相和cBN相的特征峰;扫描电子显微镜(SEM)观察发现,材料具有致密的微观结构,颗粒间结合紧密;硬度测试表明,材料的硬度远高于单一MAX相陶瓷或cBN;热导率测试也显示出了良好的导热性能。
放电等离子体烧结技术课件
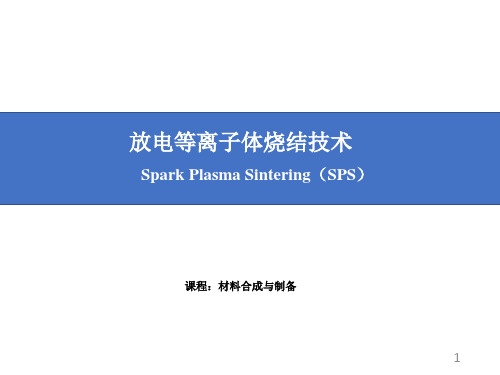
▪ 2000年6月武汉理工大学购置了国内首台SPS装置。 ▪ 随后上海硅酸盐研究所、清华大学、武汉大学等高校及科研机构也相继引进了
SPS装置, 用来进行相关的科学研究。
3
放电等离子体烧结(SPS)简介
由于其独特的烧结机理, SPS技术具有升温速度快、烧 结温度低、烧结时间短、节能环保等特点, SPS已广泛 应用于纳米材料、梯度功能材料、金属材料、磁性材料 、复合材料、陶瓷等材料的制备。
8
放电等离子烧结(SPS)的应用
将1700 C下用SPS分别烧结3 min和5 min的样品与常规方法在1500 C烧结 72 h的样品对比可以看出使用SPS方法得到的样品所用时间更短, 致密性更 好。
放电等离子体烧结技术
Spark Plasma Sintering(SPS)
课程:材料合成与制备
1
目录
1. 放电等离子烧结(SPS)简介 2. 放电等离子烧结(SPS)的基本原理 3. 放电等离子烧结(SPS)的优缺点 4. 放电等离子烧结(SPS)的应用
2
放电等离子体烧结(SPS)简介
SPS的发展
▪ 1930年, 美国科学家提出利用等离子体脉冲电流烧结原理, 直到1965年, 脉冲电流烧
结技术才在美、日等国得到应用。日本获得了SPS技术的专利, 但当时未能解决该 技术存在的生产效率低等问题, 因此SPS技术没有得到推广应用。
▪ SPS技术的推广应用是从上个世纪80年代末期开始的。 ▪ 1988年日本研制出第一台工业型SPS装置, 并在新材料研究领域内推广应用。 ▪ 由于SPS技术具有快速、低温、高效率等优点, 近几年国内外许多大学和科研机构
放电等离子烧结技术

放电等离子烧结技术概述放电等离子烧结技术是一种利用放电等离子体瞬间高温作用,将微米尺寸的粒子连结成块状材料的先进烧结工艺。
该技术可应用于金属、陶瓷和高分子材料的制备,广泛应用于航空航天、汽车工业、电子器件等领域。
原理放电等离子烧结技术主要依靠高能电子束、激光束或电弧产生的等离子体,对粉末进行加热、熔化、溶胶-凝胶相变及凝固等过程。
其主要步骤包括放电等离子体生成、能量传递、粉末加热和冷却固化。
1.放电等离子体生成:通过施加电弧、电子束或激光束,将电能转化为热能,形成高电离度的等离子体。
此过程会产生高温和高压的环境,使粉末表面瞬间熔化。
2.能量传递:放电等离子体中的高能电子、电荷、能量和动量会在粉末中传递。
高能电子的轰击使粉末中的原子、分子发生能级跃迁,从而引发化学反应、电子交换和原子结构的变化。
这些能量和动量的传递是改变粉末性质、形成块状材料的关键。
3.粉末加热:放电等离子体释放的能量使粉末中的粒子加热,粒子间的距离减小,表面融化形成胶体。
同时,粉末中的化学反应使胶体具有一定的粘结力,使粉末颗粒开始结合。
4.冷却固化:当放电停止时,粉末开始冷却。
冷却过程中,胶体迅速凝固,形成粒子间的连接。
这些连接在冷却固化后形成比较牢固的固结区,从而构成块状材料。
优点和应用放电等离子烧结技术具有以下优点:•高效性:放电等离子体的高能量传输和快速冷却固化过程,使得烧结时间大大缩短,提高了生产效率。
•成型性:该技术可实现复杂形状、高密度、均匀结合的材料制备,满足不同行业的需求。
•可控性:通过调整放电参数和粉末性质,可以控制物质的相变过程和烧结结构,达到所需的性能要求。
•应用广泛:放电等离子烧结技术可应用于制备各种材料,包括金属、陶瓷和高分子材料。
在航空航天、汽车工业、电子器件等领域有着广泛应用。
发展趋势放电等离子烧结技术在材料科学和工程领域的研究和应用仍在不断发展。
未来的发展趋势有:1.新材料研究:随着新材料的涌现,放电等离子烧结技术将继续为新材料的研发和制备提供有力的手段。
《放电等离子烧结制备MAX-cBN复合材料》范文

《放电等离子烧结制备MAX-cBN复合材料》篇一一、引言随着科技的发展,复合材料在众多领域中发挥着越来越重要的作用。
其中,MAX-cBN(MAX相与立方氮化硼)复合材料以其独特的物理和化学性质,在高温、高强度、高硬度等应用场景中表现出色。
本文将详细介绍放电等离子烧结技术在制备MAX-cBN复合材料中的应用,并探讨其制备过程、性能及潜在的应用前景。
二、放电等离子烧结技术概述放电等离子烧结(Spark Plasma Sintering, SPS)是一种新型的固相烧结技术。
其原理是在特定压力和真空或非氧化性气氛条件下,通过通电放电产生等离子体环境,实现快速烧结的目的。
此技术因其独特的高效性、环保性和适用性广泛等优点,已被广泛应用于金属、陶瓷等复合材料的制备中。
三、MAX-cBN复合材料的制备1. 材料选择与配比:选择合适的MAX相和cBN原料,根据所需的性能要求确定其配比。
2. 混合与预处理:将选定的原料进行充分混合,并采用适当的预处理方法如球磨、压制等,以改善原料的颗粒度和分散性。
3. 放电等离子烧结:将预处理后的原料放入SPS设备中,在特定压力和气氛条件下进行烧结。
通过控制烧结温度、时间和压力等参数,实现MAX相与cBN的紧密结合。
四、MAX-cBN复合材料的性能研究1. 微观结构分析:通过X射线衍射(XRD)、扫描电子显微镜(SEM)等手段,观察MAX-cBN复合材料的微观结构,分析其相组成和颗粒分布。
2. 力学性能测试:对制备的MAX-cBN复合材料进行硬度、抗弯强度等力学性能测试,评估其性能表现。
3. 热稳定性与化学稳定性分析:通过高温氧化实验、酸碱腐蚀实验等方法,研究MAX-cBN复合材料的热稳定性和化学稳定性。
五、应用前景与展望MAX-cBN复合材料因其独特的物理和化学性质,在高温、高强度、高硬度等应用场景中具有广阔的应用前景。
例如,可应用于航空航天、汽车制造、精密加工等领域。
未来,随着科技的发展和工艺的改进,放电等离子烧结技术将在制备MAX-cBN复合材料中发挥更大的作用,为各领域的应用提供更优质的材料。
赛琅泰克 放电等离子烧结
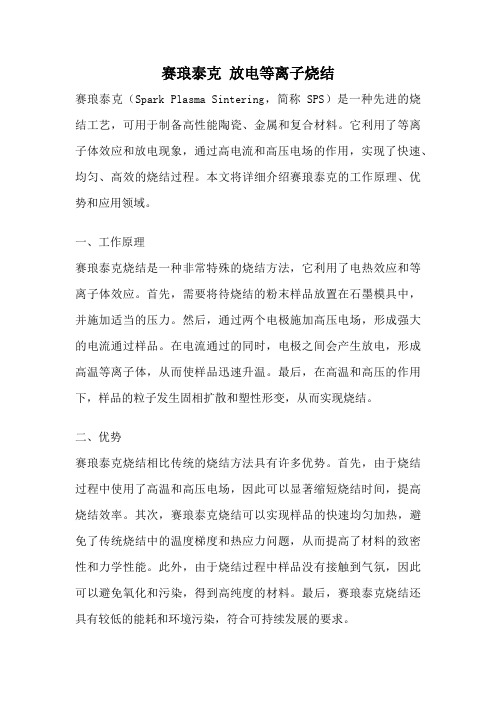
赛琅泰克放电等离子烧结赛琅泰克(Spark Plasma Sintering,简称SPS)是一种先进的烧结工艺,可用于制备高性能陶瓷、金属和复合材料。
它利用了等离子体效应和放电现象,通过高电流和高压电场的作用,实现了快速、均匀、高效的烧结过程。
本文将详细介绍赛琅泰克的工作原理、优势和应用领域。
一、工作原理赛琅泰克烧结是一种非常特殊的烧结方法,它利用了电热效应和等离子体效应。
首先,需要将待烧结的粉末样品放置在石墨模具中,并施加适当的压力。
然后,通过两个电极施加高压电场,形成强大的电流通过样品。
在电流通过的同时,电极之间会产生放电,形成高温等离子体,从而使样品迅速升温。
最后,在高温和高压的作用下,样品的粒子发生固相扩散和塑性形变,从而实现烧结。
二、优势赛琅泰克烧结相比传统的烧结方法具有许多优势。
首先,由于烧结过程中使用了高温和高压电场,因此可以显著缩短烧结时间,提高烧结效率。
其次,赛琅泰克烧结可以实现样品的快速均匀加热,避免了传统烧结中的温度梯度和热应力问题,从而提高了材料的致密性和力学性能。
此外,由于烧结过程中样品没有接触到气氛,因此可以避免氧化和污染,得到高纯度的材料。
最后,赛琅泰克烧结还具有较低的能耗和环境污染,符合可持续发展的要求。
三、应用领域赛琅泰克烧结在材料科学领域有着广泛的应用。
首先,它可以用于制备高性能的陶瓷材料,如氧化物陶瓷、碳化硅陶瓷和氮化硅陶瓷等。
这些陶瓷材料具有优异的耐热、耐磨和绝缘性能,广泛应用于航空航天、能源和电子等领域。
其次,赛琅泰克烧结还可以用于制备金属材料,如钛合金、镍基高温合金和不锈钢等。
这些金属材料具有高强度、高韧性和良好的耐腐蚀性能,广泛应用于汽车、船舶和医疗器械等领域。
此外,赛琅泰克烧结还可以制备复合材料,如陶瓷基复合材料和金属基复合材料等,用于制备高性能的结构材料和功能材料。
赛琅泰克烧结是一种先进的烧结工艺,通过电热效应和等离子体效应实现材料的快速、均匀、高效烧结。
《放电等离子烧结制备MAX-cBN复合材料》

《放电等离子烧结制备MAX-cBN复合材料》篇一一、引言随着科技的发展,复合材料在工业领域的应用越来越广泛。
其中,MAX-cBN(主要为碳化物与立方氮化硼)复合材料以其优异的物理、化学及机械性能,成为了一种重要的复合材料。
放电等离子烧结技术(SPS)以其独特的优势,如高能量密度、低热应力、精确的温度控制等,在制备MAX-cBN复合材料中展现出强大的潜力。
本文旨在深入探讨放电等离子烧结制备MAX-cBN 复合材料的工艺过程、性能特点及其应用前景。
二、放电等离子烧结技术概述放电等离子烧结(SPS)技术是一种新型的烧结技术,其基本原理是利用脉冲直流电场在粉末颗粒间产生放电现象,通过放电产生的热量和等离子体的作用,使粉末颗粒在短时间内达到烧结状态。
这种技术具有烧结温度低、烧结时间短、烧结体性能优异等优点。
三、MAX-cBN复合材料的制备1. 材料选择与预处理:选择高质量的MAX相和cBN粉末作为原料,进行充分的干燥和研磨处理,以提高其表面活性和均匀性。
2. 混合与成型:将预处理后的MAX相和cBN粉末按照一定比例混合,并通过压力成型为所需的形状。
3. 放电等离子烧结:将成型后的样品置于SPS设备中,设定合适的温度、压力和时间等参数,进行放电等离子烧结。
四、MAX-cBN复合材料的性能特点MAX-cBN复合材料具有优异的物理、化学及机械性能。
其硬度高、耐磨性好、热稳定性强,同时具有良好的导电性和导热性。
此外,其优异的抗腐蚀性能和高温性能也使其在许多领域具有广泛的应用前景。
五、应用前景MAX-cBN复合材料在机械制造、航空航天、电子信息等领域具有广泛的应用前景。
例如,可以用于制造高精度的切削工具、耐磨零件、高温结构件等。
此外,其优异的导电性和导热性也使其在电子封装、散热器件等领域具有潜在的应用价值。
六、结论放电等离子烧结技术为制备MAX-cBN复合材料提供了一种有效的途径。
通过优化工艺参数,可以获得具有优异性能的MAX-cBN复合材料。
放电等离子体烧结技术

1 放电等离子体烧结的工艺 1.1放电等离子体烧结的设备
一般放电等离子体烧结设备主要由三部分组成
产生单轴向压 力的装置和烧 结模具,压力 装置可根据烧 结材料的不同 施加不同的压 力;
脉冲电流发生 器,用来产生 等离子体对材 料进行活化处 理
电阻加热设备
材料合成与制备
SPS装置的结构示意图
图1 为其装置简图。图2 为SPS 的电压、电流及外加压力与烧结 时间的关系曲线。其电流曲线主要由三段组成: (1) 脉冲大电流; (2) 稳态小电流; (3) 停止放电间隙。在稳态电流阶段, 仅施加很小 的压力; 放电间隙阶段施加大压力。
分电流加热模具,使模具开始对试样传热,试样温度升高,
开始收缩,产生一定的密度,并随着温度的升高而增大,
直至达到烧结温度后收缩结束,致密度达到最大。
材料合成与制备
1.3 等离子体烧结工艺参数的控制
烧结气氛 烧结气氛对样品烧结的影响很大(真空烧结情况除外), 合适的气氛将有助于样品的致密化。
材料合成与制备
烧结温度 烧结温度的确定要考虑烧结体样品在高温下的相转变、
晶粒的生长速率、样品的质量要求以及样品的密度要求。一 般情况下,随着烧结温度的升高,试样致密度整体呈上升趋 势,这说明烧结温度对样品致密度程度有明显的影响,烧结 温度越高,烧结过程中物质传输速度越快,样品越容易密实。
但是,温度越高,晶粒的生长速率就越快,其力学性能就越差。而 温度太低,样品的致密度就很低,质量达不到要求。温度与晶粒大小 之间的矛盾在温度的选择上要求一个合适的参数。
业株式会社生产,SPS-1050)。
材料合成与制备
等离子体烧结技术的概念
等离子体 等离子体是宇宙中物质存在的一种状态,是除固、
《放电等离子烧结制备MAX-cBN复合材料》范文

《放电等离子烧结制备MAX-cBN复合材料》篇一一、引言随着科技的发展,复合材料在工业领域的应用越来越广泛。
其中,MAX-cBN(以MAX相和立方氮化硼为主要成分的复合材料)因其独特的物理和化学性质,在切削工具、耐磨材料、高温超导等领域具有广泛的应用前景。
本文将详细介绍放电等离子烧结技术在制备MAX-cBN复合材料中的应用及其优越性。
二、放电等离子烧结技术放电等离子烧结(Spark Plasma Sintering, SPS)是一种新型的烧结技术,其原理是利用脉冲电流在颗粒间产生放电等离子体,从而实现材料的快速致密化。
SPS技术具有烧结温度低、烧结时间短、材料致密性好等优点,因此在制备复合材料方面具有广泛的应用。
三、MAX-cBN复合材料的制备MAX-cBN复合材料的制备主要采用放电等离子烧结技术。
首先,将MAX相和cBN粉末按照一定比例混合,然后在一定的温度和压力下进行烧结。
在烧结过程中,通过控制电流的大小和频率,使颗粒间产生放电等离子体,从而实现材料的快速致密化。
四、MAX-cBN复合材料的性能MAX-cBN复合材料具有优异的物理和化学性能。
其硬度高、耐磨性好、热稳定性强,且具有良好的导电性和导热性。
此外,MAX-cBN复合材料还具有优异的力学性能,如高强度、高韧性等。
这些性能使得MAX-cBN复合材料在切削工具、耐磨材料、高温超导等领域具有广泛的应用前景。
五、放电等离子烧结技术的优势放电等离子烧结技术制备MAX-cBN复合材料具有以下优势:1. 烧结温度低:相比传统烧结技术,SPS技术可以在较低的温度下实现材料的致密化,有利于保护材料的性能。
2. 烧结时间短:SPS技术可以在短时间内完成烧结过程,提高了生产效率。
3. 材料致密性好:SPS技术通过脉冲电流在颗粒间产生放电等离子体,使材料实现快速致密化,提高了材料的致密性和性能。
4. 易于控制:SPS技术的电流和频率等参数易于控制,可以实现材料的精确制备。
放电等离子烧结技术的发展和应用

放电等离子烧结技术的发展和应用放电等离子烧结技术是一种先进的粉末冶金加工技术,已经在多个领域得到广泛应用。
该技术利用高能电子束通过等离子激发粉末颗粒,使其迅速熔化并相互凝结成块状材料。
以下将对其发展历程和应用进行叙述。
放电等离子烧结技术最早出现在20世纪60年代,起初用于制备高纯度金属材料。
随着计算机技术的发展和先进的机械设备的应用,该技术逐渐被引入到其他领域。
在20世纪80年代,放电等离子烧结技术得到了快速发展,相关装备的性能和稳定性得到了大幅提升。
放电等离子烧结技术的应用非常广泛。
首先,它在粉末冶金领域的应用非常成功。
通过控制放电参数和材料组分,可以获得粉末冶金材料的高密度、均匀性和良好的力学性能。
这种材料广泛应用于汽车、航空航天和船舶等领域的零部件制造。
其次,放电等离子烧结技术在纳米材料制备方面表现出了巨大的潜力。
通过精确控制放电参数和材料组分,可以制备出尺寸均一、结晶度高的纳米材料。
这些纳米材料具有独特的物理和化学性质,广泛应用于电子器件、生物传感器和催化剂等领域。
此外,放电等离子烧结技术在材料修复和再制造领域也有重要的应用。
例如,通过控制放电过程中的温度和压力,可以在材料表面修复裂纹和划痕。
此外,该技术还可以用于金属材料的再制造,将废旧材料和废品转化为可用的新材料。
尽管放电等离子烧结技术有许多优点,但也存在一些挑战。
首先,该技术在大规模生产上仍面临困难,因为设备成本高昂。
其次,放电过程中产生的高温和高压环境对设备的稳定性和耐用性要求较高。
总的来说,放电等离子烧结技术的发展和应用为材料制备和加工领域带来了巨大的潜力。
随着相关技术的进一步改进和成熟,相信这一技术将能够在更多领域发挥重要作用,为社会经济的发展做出重要贡献。
放电等离子烧结技术是一种基于等离子态物理过程的先进加工技术,具有高速、高能量和高密度等优点,被广泛应用于粉末冶金、纳米材料制备、材料修复和再制造等领域。
随着科学技术的不断进步和人们对高性能材料需求的增加,放电等离子烧结技术也在不断发展和创新。
等离子体烧结
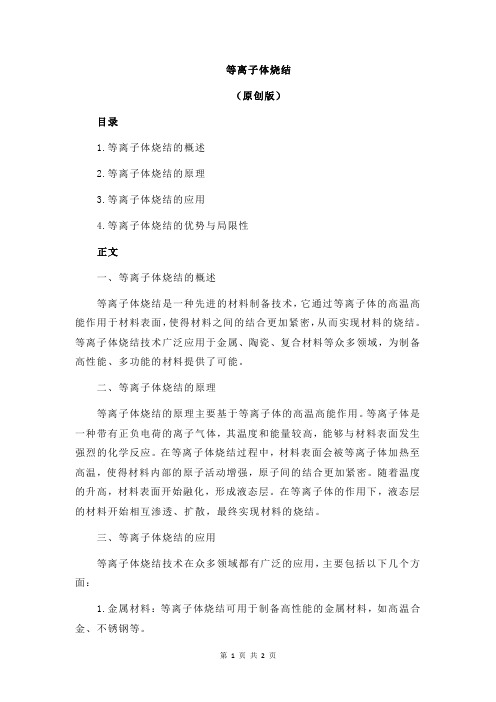
等离子体烧结(原创版)目录1.等离子体烧结的概述2.等离子体烧结的原理3.等离子体烧结的应用4.等离子体烧结的优势与局限性正文一、等离子体烧结的概述等离子体烧结是一种先进的材料制备技术,它通过等离子体的高温高能作用于材料表面,使得材料之间的结合更加紧密,从而实现材料的烧结。
等离子体烧结技术广泛应用于金属、陶瓷、复合材料等众多领域,为制备高性能、多功能的材料提供了可能。
二、等离子体烧结的原理等离子体烧结的原理主要基于等离子体的高温高能作用。
等离子体是一种带有正负电荷的离子气体,其温度和能量较高,能够与材料表面发生强烈的化学反应。
在等离子体烧结过程中,材料表面会被等离子体加热至高温,使得材料内部的原子活动增强,原子间的结合更加紧密。
随着温度的升高,材料表面开始融化,形成液态层。
在等离子体的作用下,液态层的材料开始相互渗透、扩散,最终实现材料的烧结。
三、等离子体烧结的应用等离子体烧结技术在众多领域都有广泛的应用,主要包括以下几个方面:1.金属材料:等离子体烧结可用于制备高性能的金属材料,如高温合金、不锈钢等。
2.陶瓷材料:等离子体烧结可用于制备各种陶瓷材料,如氧化锆、氧化铝等。
3.复合材料:等离子体烧结可用于制备复合材料,如金属基复合材料、陶瓷基复合材料等。
4.功能材料:等离子体烧结还可用于制备具有特定功能的材料,如超导材料、光电材料等。
四、等离子体烧结的优势与局限性等离子体烧结技术具有许多优势,如烧结温度低、能耗小、制备过程环保等。
同时,等离子体烧结还能够实现材料的快速烧结,提高生产效率。
然而,等离子体烧结技术也存在一定的局限性,如设备成本较高、对材料表面的要求较高等。
此外,等离子体烧结过程中可能产生的等离子体损伤也需要关注。
综上所述,等离子体烧结技术是一种具有广泛应用前景的材料制备技术。
放电等离子体烧结

放电等离子体烧结
放电等离子体烧结是一种新兴的材料加工技术,通过高温等离子体的作用,可以将粉末材料烧结成坚固的材料。
这种技术具有高效、环保、节能等优点,被广泛应用于金属、陶瓷、复合材料等领域。
放电等离子体烧结的原理是利用放电等离子体在高温下的高能量状态,使粉末颗粒表面迅速熔化并结合成致密的材料。
在这个过程中,放电等离子体不仅提供了高温和高压的条件,还能够激发粉末颗粒之间的化学反应,加速烧结速度,提高材料的密度和强度。
放电等离子体烧结技术的优势在于可以实现快速烧结、高密度、高强度和高温稳定性的材料制备。
与传统烧结方法相比,放电等离子体烧结可以大大缩短烧结时间,降低能耗,减少材料损耗,提高生产效率和材料质量。
在金属材料加工领域,放电等离子体烧结技术被广泛应用于制备高性能的工具钢、不锈钢、合金等材料。
通过这种技术,可以实现金属材料的高密度、高强度、高硬度和高耐磨性,满足各种工业领域对材料性能的要求。
在陶瓷材料加工领域,放电等离子体烧结技术也有着重要的应用。
通过这种技术,可以制备高密度、高强度、高耐磨性和高抗压性的陶瓷材料,广泛应用于电子、光学、航空航天等领域。
在复合材料领域,放电等离子体烧结技术的应用也日益广泛。
通过
这种技术,可以实现复合材料的高密度、高强度、高硬度和高耐磨性,满足汽车、航空航天、船舶等领域对复合材料性能的要求。
总的来说,放电等离子体烧结技术是一种高效、环保、节能的材料加工技术,具有广阔的应用前景。
随着材料科学技术的不断发展,相信放电等离子体烧结技术将在各个领域发挥重要作用,为人类社会的发展做出贡献。
《放电等离子烧结制备高纯Ti3AlC2及固溶强化》范文

《放电等离子烧结制备高纯Ti3AlC2及固溶强化》篇一一、引言随着现代材料科学的飞速发展,高纯度的金属陶瓷复合材料成为了众多领域研究的热点。
Ti3AlC2作为一种典型的MAX相陶瓷材料,具有优异的力学性能、良好的导电性和高温稳定性,在航空航天、生物医疗、能源等领域具有广泛的应用前景。
本文将详细介绍放电等离子烧结(SPS)制备高纯Ti3AlC2及其固溶强化的方法,并分析其工艺特点、性能优势以及实际应用。
二、放电等离子烧结技术放电等离子烧结(SPS)是一种新型的烧结技术,其原理是利用脉冲电流在烧结过程中产生的等离子体放电效应,使粉末颗粒在高温高压下快速烧结成致密的材料。
该技术具有烧结温度低、烧结时间短、能量利用率高等优点,因此在金属、陶瓷及复合材料的制备中得到了广泛应用。
三、制备高纯Ti3AlC21. 材料选择与预处理:选择高纯度的Ti、Al和C的金属粉末作为原料,通过机械混合和球磨等方法进行预处理,以获得均匀的混合粉末。
2. 制备工艺:将预处理后的混合粉末放入SPS设备中,通过设定适当的温度、压力和电流等参数,进行放电等离子烧结。
在烧结过程中,通过控制烧结温度和时间,使粉末颗粒在高温高压下发生固相反应,生成Ti3AlC2。
3. 产物纯度与性能:通过SPS技术制备的Ti3AlC2具有高纯度、高致密度和良好的力学性能。
通过X射线衍射(XRD)和扫描电子显微镜(SEM)等手段对产物进行表征,验证其物相组成和微观结构。
四、固溶强化为了进一步提高Ti3AlC2的性能,采用固溶强化的方法。
在Ti3AlC2中引入其他元素,使其固溶于基体中,形成固溶体,从而提高材料的力学性能和耐腐蚀性能。
具体方法是在SPS制备过程中,将其他元素以一定比例与Ti、Al和C的混合粉末一起进行烧结。
通过控制烧结过程中的温度和时间,使其他元素固溶于Ti3AlC2基体中。
五、性能分析1. 力学性能:通过对制备的高纯Ti3AlC2及固溶强化后的材料进行硬度、抗弯强度等力学性能测试,分析其性能变化规律。
放电等离子烧结技术

放电等离子烧结技术一、技术概述放电等离子烧结技术是一种利用高温等离子体烧结陶瓷材料的方法。
该技术通过放电产生高温等离子体,使陶瓷粉末在高温下熔融并形成致密的块体,从而达到烧结的目的。
二、工艺流程1.原料制备:将陶瓷粉末按一定比例混合,并加入必要的助剂。
2.成型:将混合好的陶瓷粉末通过压制或注塑成型。
3.预处理:对成型后的坯体进行去除水分和有机物等预处理。
4.放电等离子体处理:将坯体置于放电等离子体发生器中,通过放电产生高温等离子体,使陶瓷粉末在高温下熔融并形成致密的块体。
5.后处理:对放电等离子体处理后得到的块体进行去除残余气孔和表面加工。
三、优点1.能够制备出具有优异性能的陶瓷材料,如高强度、高硬度、耐腐蚀性好等。
2.制备过程中无需添加任何外部热源,能够节约能源。
3.制备的陶瓷材料致密度高、气孔率低,具有较好的抗压强度和耐磨性。
四、缺点1.设备成本高,需要专门的放电等离子体发生器。
2.制备过程中需要控制放电等离子体的温度和时间等参数,技术难度较大。
3.制备出的陶瓷材料存在一定的残余应力,容易导致裂纹和断裂。
五、应用领域放电等离子烧结技术主要应用于制备高强度、高硬度、耐腐蚀性好的陶瓷材料。
目前已广泛应用于航空航天、汽车工业、机械加工等领域。
例如,利用该技术可制备出具有优异性能的氧化锆陶瓷刀具,在机械加工领域得到广泛应用。
六、发展趋势随着科学技术的不断进步和人们对高性能材料需求的增加,放电等离子烧结技术将会得到更广泛的应用。
未来该技术将会更加成熟,设备成本也将会逐渐降低,同时制备出的陶瓷材料也将会具有更优异的性能。
放电等离子烧结技术及其在钛基复合材料制备中的应用

放电等离子烧结技术及其在钛基复合材料制备中的应用下载温馨提示:该文档是我店铺精心编制而成,希望大家下载以后,能够帮助大家解决实际的问题。
文档下载后可定制随意修改,请根据实际需要进行相应的调整和使用,谢谢!并且,本店铺为大家提供各种各样类型的实用资料,如教育随笔、日记赏析、句子摘抄、古诗大全、经典美文、话题作文、工作总结、词语解析、文案摘录、其他资料等等,如想了解不同资料格式和写法,敬请关注!Download tips: This document is carefully compiled by the editor. I hope that after you download them, they can help you solve practical problems. The document can be customized and modified after downloading, please adjust and use it according to actual needs, thank you!In addition, our shop provides you with various types of practical materials, such as educational essays, diary appreciation, sentence excerpts, ancient poems, classic articles, topic composition, work summary, word parsing, copy excerpts, other materials and so on, want to know different data formats and writing methods, please pay attention!放电等离子烧结技术及其在钛基复合材料制备中的应用1. 引言放电等离子烧结技术是一种先进的材料加工方法,通过电子的加速和热能的释放,将材料粉末烧结成块状。
《放电等离子烧结制备MAX-cBN复合材料》
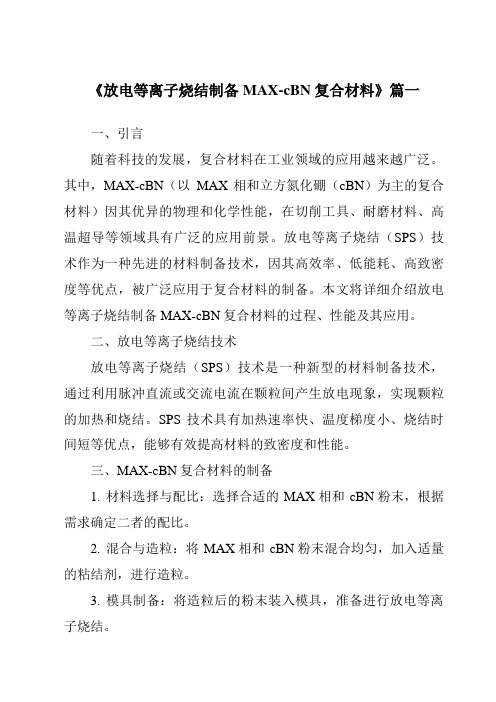
《放电等离子烧结制备MAX-cBN复合材料》篇一一、引言随着科技的发展,复合材料在工业领域的应用越来越广泛。
其中,MAX-cBN(以MAX相和立方氮化硼(cBN)为主的复合材料)因其优异的物理和化学性能,在切削工具、耐磨材料、高温超导等领域具有广泛的应用前景。
放电等离子烧结(SPS)技术作为一种先进的材料制备技术,因其高效率、低能耗、高致密度等优点,被广泛应用于复合材料的制备。
本文将详细介绍放电等离子烧结制备MAX-cBN复合材料的过程、性能及其应用。
二、放电等离子烧结技术放电等离子烧结(SPS)技术是一种新型的材料制备技术,通过利用脉冲直流或交流电流在颗粒间产生放电现象,实现颗粒的加热和烧结。
SPS技术具有加热速率快、温度梯度小、烧结时间短等优点,能够有效提高材料的致密度和性能。
三、MAX-cBN复合材料的制备1. 材料选择与配比:选择合适的MAX相和cBN粉末,根据需求确定二者的配比。
2. 混合与造粒:将MAX相和cBN粉末混合均匀,加入适量的粘结剂,进行造粒。
3. 模具制备:将造粒后的粉末装入模具,准备进行放电等离子烧结。
4. SPS烧结:将模具置于SPS设备中,设置合适的烧结温度、压力和时间,进行放电等离子烧结。
四、MAX-cBN复合材料的性能通过放电等离子烧结制备的MAX-cBN复合材料具有以下优点:1. 高致密度:SPS技术能够有效提高材料的致密度,使材料具有较高的力学性能。
2. 优良的物理和化学性能:MAX相和cBN的优异性能使复合材料具有优良的物理和化学性能。
3. 良好的加工性能:复合材料具有良好的加工性能,便于进行后续的加工和成型。
五、MAX-cBN复合材料的应用MAX-cBN复合材料在切削工具、耐磨材料、高温超导等领域具有广泛的应用前景。
例如,在切削工具中,MAX-cBN复合材料具有较高的硬度和耐磨性,能够有效提高切削效率和工具寿命;在耐磨材料中,复合材料具有优异的耐磨性能和抗疲劳性能,能够满足高负荷、高速度的工作环境;在高温超导领域,复合材料的高温超导性能使其成为研究热点。
放电等离子烧结技术的原理及应用_冯海波

第11卷 第3期2003年9月 材 料 科 学 与 工 艺MATERIALS SCIENCE &TECHNOLOGYVol .11No .3Sep .,2003放电等离子烧结技术的原理及应用冯海波,周 玉,贾德昌(哈尔滨工业大学材料科学与工程学院,黑龙江哈尔滨150001,E -mail :fenghb @hit .edu .cn )摘 要:放电等离子烧结(SPS )是一种用于材料烧结致密化的新技术,为深入研究和探讨其技术优势,介绍了SPS 的基本原理和系统的组成,讨论了SPS 技术在纳米材料的制备、梯度功能材料的烧结和高致密度、细晶粒陶瓷制备等方面的应用,并对其研究和应用前景予以展望.关键词:放电等离子烧结;机理;纳米材料;梯度功能材料;陶瓷中图分类号:T F 124文献标识码:A文章编号:1005-0299(2003)03-0327-05Principle and application of spark plasma sintering technologyFENG Hai -bo ,ZHOU Yu ,JIA De -chang(School of Materials Science and Engineering ,Harb in Institute of Technology ,Harbin 150001,China ,E -mail :fenghb @hit .edu .cn )A bstract :The basic principles ,system c onstituents and typical sintering technique of spark plasma sintering (SPS ),anew advanc ed sintering tec hnique used for materials consolidation .SPS were discussed to further study its advantages .Nano -materials synthesis ,functional gradient materials (FGMs )and high density fine grain ceramic sintered by SPS were disc ussed .The future research and applic ation of SPS were reviewed as well .Key words :spark plasma sintering ;principle ;nano -materials ;functional gradient materials ;c eramic 收稿日期:2002-08-23.作者简介:冯海波(1971-),男,博士生;周 玉(1955-),男,博士,教授,博士生导师;贾德昌(1969-),男,博士,教授,博士生导师. 放电等离子烧结(SPS )是近年来发展起来的一种新型的快速烧结技术.由于等离子活化烧结技术融等离子活化、热压、电阻加热为一体,因而具有升温速度快、烧结时间短、晶粒均匀、有利于控制烧结体的细微结构、获得的材料致密度高、性能好等特点.该技术利用脉冲能、放电脉冲压力和焦耳热产生的瞬时高温场来实现烧结过程,对于实现优质高效、低耗低成本的材料制备具有重要意义,在纳米材料、复合材料等的制备中显示了极大的优越性,现已应用于金属、陶瓷、复合材料以及功能材料的制备[1,2].目前国内外许多大学和科研机构利用SPS 进行新材料的研究与开发,并对其烧结机理与特点进行深入研究与探索,尤其是其快速升温的特点,可作为制备纳米块体材料的有效手段,因而引起材料学界的特别关注[3~5].但目前关于SPS 的烧结机理还存在争议,尤其是烧结的中间过程还有待于深入研究,为此,本文将对SPS 技术有关的机理和应用予以介绍和讨论.1 SPS 系统的结构日本住友石炭矿业株式会社制造的SPS 系统主要由3部分组成(图1)[5,6]:①产生单轴向压力的装置和烧结模,压力装置可根据烧结材料的不同施加不同的压力;②脉冲电流发生器,用来产生等离子体对材料进行活化处理;③电阻加热设备.SPS 与热压(HP )烧结有相似之处,但加热方式完全不同,它是利用直流脉冲电流直接通电烧结的加压烧结方法,通过调节脉冲直流电的大小控制升温速率和烧结温度.整个烧结过程可在真空环境下进行,也可在保护气氛中进行.烧结过程中,脉冲电流直接通过上下压头和烧结粉体或石墨模具,因此加热系统的热容很小,升温和传热速度快,从而使快速升温烧结成为可能.SPS 系统可用于短时间、低温、高压(500~1000MPa )烧结,也可用于低压(20~30MPa )、高温(1000~2000℃)烧结,因此广泛应用于金属、陶瓷和各种复合材料的烧结,包括一些用通常方法难以烧结的材料,如表面容易生成硬的氧化层的金属钛和铝用SPS 技术可在短时间内烧结到90%~100%致密[1,2,5].图1 放电等离子烧结系统示意图[5,6]Fig .1 Schematic diag ram of SPS system [5,6]2 放电等离子烧结机理SPS 作为一种新颖而有效的快速烧结技术,已应用于各种材料的研制和开发,但SPS 的烧结机理目前还没有达成较为统一的认识[1,4,5,7].一般认为:SPS 过程除具有热压烧结的焦耳热和加压造成的塑性变形促进烧结过程外,还在粉末颗粒间产生直流脉冲电压,并有效利用了粉体颗粒间放电产生的自发热作用,因而产生了一些SPS 过程特有的现象,如图2所示[5,8].SPS 的烧结有两个非常重要的步骤,首先由特殊电源产生的直流脉冲电压,在粉体的空隙产生放电等离子,由放电产生的高能粒子撞击颗粒间的接触部分,使物质产生蒸发作用而起到净化和活化作用,电能贮存在颗粒团的介电层中,介电层发生间歇式快速放电,如图3所示[9].等离子体的产生可以净化金属颗粒表面,提高烧结活性,降低金属原子的扩散自由能,有助于加速原子的扩散.当脉冲电压达到一定值时,粉体间的绝缘层被击穿而放电,使粉体颗粒产生自发热,进而使其高速升温.粉体颗粒高速升温后,晶粒间结合处通过扩散迅速冷却,电场的作用因离子高速迁移而高速扩散,通过重复施加开关电压,放电点在压实颗粒间移动而布满整个粉体.使脉冲集中在晶粒结合处是SPS 过程的一个特点.颗粒之间放电时会产生局部高温,在颗粒表面引起蒸发和熔化,在颗粒接触点形成颈部,由于热量立即从发热中心传递到颗粒表面和向四周扩散,颈部快速冷却而使蒸气压低于其他部位.气相物质凝聚在颈部形成高于普通烧结方法的蒸发-凝固传递是SPS 过程的另一个重要特点.晶粒受脉冲电流加热和垂直单向压力的作用,体扩散、晶界扩散都得到加强,加速了烧结致密化过程,因此用较低的温度和比较短的时间可得到高质量的烧结体[5,8,10].图2施加直流开关脉冲电流的作用[5,8]Fig .2 Effect of O N -OF F DC pulse energizing [5,8]图3 放电过程中粉末粒子对的模型[9]Fig .3 M odel of par ticle -pair in discharg e process [9] 虽然目前尚未对脉冲电流对烧结致密化的影响有统一的认识,但研究表明对于块体金属材料,大电流脉冲的作用对物质的结晶过程有重要的影响.脉冲电流作用下的结晶过程,当无序介质中有脉冲电流作用时,成核率可表为I =A ′D ′exp {-(W c +W 0)[k (T 0+T c (t ))]-1}.式中:W 0为未加脉冲时的热力学势垒,W c 为电脉冲引起的势垒改变,T 0为初始温度,T c 为焦耳热引起的温升,D ′为载流介质的扩散系数,A ′为不依赖于温度的常数,k 为Boltzman 常数.在形核初期,核所占体积可以忽略,因金属热导率高,故可忽略其内部的温度不均匀,则T c 和电流密度(j )的关系为T c =j 2t (σ0ρλ)-1.式中:σ0为无序介质的电导率,ρ为密度,λ为比·328·材 料 科 学 与 工 艺 第11卷 热,t为通电时间,满足0<t<τp,τp为脉冲宽度.电流引起的成核势垒改变为W c= c-21[j0(r)j0(r′)-j n(r)j n(r′)]d r d r′/2|r-r′|.式中:j0和j n分别为形核前后的电流密度分布, r和r′为空间坐标,c1为常数.当一脉冲作用后,将形成许多球形小晶核,镶嵌于无序背景中,推导得W c=K1j2ζV.式中:K1为与材料有关的常数,j为电流密度分布,V为晶核的体积,ζ=(σ0-σn)(σn+ 2σ0)-1(式中σn为形核后的电导率),则脉冲电流作用下的形核公式为I=A′D′exp{-(W0+K1j2ζV)×[k T+kj2t(σ0ρλ)-1]-1}.当脉冲宽度很窄时,τ K1|ζ|Vσ0ρλk-1,则I=A′D′exp[-(W0+K1j2ξV)×(k T0)-1],若σn>σ0,则ζ<0,相应于结晶过程.此时W c <0,I>I0(I0为未加脉冲时的形核率),这表明脉冲电流可以通过减小成核势垒来增大成核率.根据Av rami方程,成核率增大将引起晶粒细化.脉冲电流的驰豫时间极短,因此在超短脉冲电流的作用下,有可能获得大块纳米晶材料[11].因此,在理论上SPS过程可提高成核率,从而获得较为细小的组织,这也是SPS方法引起广泛关注的主要原因.但SPS快速烧结的机理还存在争议,其烧结的中间过程还有待于进一步深入的研究.有关等离子体的产生尚缺乏具有说服力的证据,尤其是对于非导电性粉体,电流不能通过,通常认为其烧结致密化是由模具和上下压头充当发热体,热量传递快捷,同时由于大电流的采用,使非导电性粉体快速通过低温区直接进入高温区,是SPS 能够实现快速烧结的主要原因.3 放电等离子烧结的应用3.1 纳米材料的制备纳米材料以其独特的性能特点,引起材料学界的关注,但纳米晶块体材料的较为有效和实用的制备方法目前还在研究探索之中.SPS技术由于烧结时间大大缩短,可以抑制晶粒的长大,因此有望获得致密的纳米材料.尤其是机械合金化等非平衡方法获得的粉末,晶粒细化的同时引入的大量缺陷和亚结构,无法在传统的热压或热等静压烧结过程中得以保留和体现,而SPS技术作为一种快速烧结方法则可能使这些特点在烧结后的块体材料中得以保留.Yong等用机械合金化方法制备平均晶粒尺寸10~15nm的复合粉末,900℃/60MPa/5min放电等离子烧结获得了致密度大于95%、晶粒尺寸小于30nm的Fe-Co块体材料[12].研究表明:由于外加电压对扩散的促进作用,活化能比无压烧结略有降低,脉冲电流使晶粒表面活化,在SPS过程中晶粒生长极快,只是由于烧结时间极短而且烧结温度远低于热压等传统方法才能够获得较小的晶粒尺寸[13,14],因此很难制备晶粒尺寸小于100nm 的Y-TZP材料[15].WO3、Mg和C粉末,通过机械合金化的方法制备纳米复合粉末,经1963K/19.2 -38.2MPa/5min真空SPS烧结可获得致密的WC和WC-18%MgO纳米复合材料[16].采用SPS 法已成功制备了MgO/BaTiO3[17]、TiAl-X和Ti3Al -X[18]、WC-10Co[19]、Nd2Ti2O7/Al2O3[20]等多种纳米复合材料.此外,对Mo[21]、NiTi[22]、Nb-Al-N和Nb-Al-Mo[23]、TiAl/Ti2AlC[24]等多种体系的复合材料,采用SPS方法制备均能够获得较高性能的块体材料.因此,用机械合金化制备纳米或非晶的复合粉末,采用非平衡的SPS快速烧结技术有望成为制备多种纳米复合材料或大块非晶合金的有效方法.3.2 梯度功能材料的烧结梯度功能材料(FGMs)是一种组成在某个方向上梯度分布的复合材料,在金属和陶瓷粘合时由于二者烧结致密的温度相差较大,且界面的膨胀系数不同而产生热应力,给材料的制备带来困难,而应用SPS方法可以很好的克服这一难点,实现烧结温度的梯度分布.日本学者采用SPS系统制备了致密的ZrO2(3Y)/Ni、ZrO2(3Y)/不锈钢和聚酯亚胺/Al等梯度功能材料[5,25].将不同组成的混合ZrO2/Ni粉体(95%/90%/85%/ 80%/75%/70%/60%/50%/30%ZrO2(体积分数)依次分层放入如图4所示的石墨模具中进行放电等离子烧结,在样品的两端形成温度梯度,从而使梯度分布的粉末一次烧结致密,其密度远高于普通烧结方法.通过调整模具的形状可以改变和控制模具内的温度分布,使复杂形状试样的制备成为可能.而采用导电复合粉末制备层状梯度复合材料时,可以通过调整复合粉末成分形成可设计的电阻值,从而在脉冲电流通过时形成温度梯度或温度变化.Shen还采用SPS法分别制备了交替层叠和梯度分布的TiN/Al2O3复合材料[26].采用SPS不仅能够制作轴向层状梯度材料,而且还能制作径向圆筒状梯度材料[3].随着SPS技术的广泛使用新型梯度功能材料正不断问世[27].·329·第3期冯海波,等:放电等离子烧结技术的原理及应用图4 石墨梯度模具F ig.4G radient g raphite die3.3 高致密度、细晶粒陶瓷在SPS过程中,每一个粉末及其相互间的孔隙都是发热源,因此烧结时传热时间极短,可以忽略不计,烧结温度也大为降低,而且如前所述,还可通过增大形核率来降低晶粒尺寸,因此可获得高致密的细晶或纳米晶陶瓷材料.Kim采用球磨制得晶粒尺寸25nm的Al2O3/Cu粉末,在50MPa压力,1250℃烧结5min,获得晶粒尺寸200~500nm的陶瓷材料,其相对密度达97%以上,断裂韧性为4.51MPa·m1/2[28].Yoshimura利用化学方法制得的小于10nm的10%Al2O3/ZrO2粉末,在1300℃烧结,获得晶粒尺寸小于100nm,相对密度高于98%的陶瓷材料[29].Nishimura用SPS方法制备α-Si3N4和β-Si3N4陶瓷,烧结温度1500~1 600℃,时间5~7min,达到理论密度的98%以上,晶粒尺寸150~200nm[30].中科院上海硅酸盐研究所的研究者用SPS方法制备了Al2O3等氧化物[31]、SiC-Al2O3[32]、SiC-ZrO2-Al2O3复相陶瓷[33,34]和纳米3Y-TZP[13]等多种材料,并通过对其力学性能和显微结构的研究,认为SPS方法制备的陶瓷复合材料与普通烧结方法相比,在降低烧结温度提高致密度的同时,强度和韧性均有所提高[35~37].在研究Sialon陶瓷时发现,采用SPS制备方法1600℃烧结,当加热速率为200℃/min时,发生各向异性的Ostwald长大(动态长大),不需添加晶种即可以使晶粒各向异性长大,获得由长棒状晶粒构成的韧性互锁显微组织,从而提高其断裂韧性.对于其他体系的陶瓷也可通过液相烧结的动态长大机制改善显微组织结构提高力学性能[38,39].此外,SPS方法逐步应用于金属间化合物、金属基复合材料、超导材料、磁性材料和压电陶瓷以及铁电和热电材料等制备与研究,并获得了较为优异的性能.随着SPS技术的发展,其在材料科学研究领域中的应用也在不断扩展.4 结语SPS方法是一种新颖的烧结方法,升温速度快、时间短、烧结效率高,可获得高致密度的产品,其独特的等离子体活化和快速烧结作用,抑制了晶粒长大,较好地保持了原始颗粒的微观结构,从而在本质上提高了材料性能,并为纳米晶材料和新性能材料的制备提供了可能.SPS技术可以通过控制模具的形状等因素来改变和控制温度场分布,有望获得形状复杂的梯度功能材料.尽管目前关于SPS的烧结机理还存在争议,尤其是烧结的中间过程和现象还有待于深入研究,但众多的实验已表明,SPS这一快速有效的制备技术在材料科学领域有着更为广阔的应用前景.参考文献:[1]王士维,陈立东,平井敏雄,等.脉冲电流烧结机理的研究进展[J].无机材料学报,2001,6(16):1055-1061.[2]陈立冬,王士维.脉冲电流烧结的现状与展望[J].陶瓷学报,2001,3(22):204~207.[3]罗锡裕.放电等离子烧结材料的最新进展[J].粉末冶金工业,2001,6(11):7-16.[4]张久兴,刘科高,周美玲.放电等离子烧结技术的发展与应用[J].粉末冶金技术,2002,3(20):129-134. [5]高 濂,宫本大树.放电等离子烧结技术[J].无机材料学报,1997,2(14):129-133.[6]JU NG Y G,HA C G,SHIN J H,et al.Fabrica tio n offunctionally g raded Z rO2/NiCrAlY composites by plasmaactiv ated sintering using tape casting and it's thermalbarrier proper ty[J].M aterials Science and Eng ineering,2002(A323):110-118.[7]张利波,彭金辉,张世敏.等离子体活化烧结在材料制备中的新应用[J].稀有金属,2000,6(24):445-449.[8]张东明,傅正义.放电等离子加压烧结技术特点及应用[J].武汉工业大学学报,1999,21(6):15-17. [9]彭金辉,张利波,张世敏.等离子活化烧结技术新进展[J].云南冶金,2000,29(3):42-44.[10]李汶霞,鲁燕萍,果世驹.等离子烧结与等离子活化烧结[J].真空电子技术,1998,1:17-23. [11]周本濂.材料制备中的非平衡过程[J].材料研究学报,1997,11(6):576-585.[12]K IM Y D,CHU NG J Y,K IM J,et al.Fo rma tio n ofnanocrystalline Fe-Co pow ders produced by mechani-cal alloying[J].M aterials Science and Eng ineering,2000(A291):17-21.[13]李 蔚,高 濂,郭景坤.放电等离子快速烧结纳米3Y-TZP材料[J].无机材料学报,1999,6(14):·330·材 料 科 学 与 工 艺 第11卷 985-988.[14]N YG REN M,SHEN Z J.On the preparatio n of bio-,nano-and structural ceramics and composites by sparkplasma sintering[J].Solid State Sciences,2003(5):125-131.[15]L I W,G AO L.Rapid sintering of nanocrystalline ZrO2(3Y)by spark plasma sintering[J].J of the EuropeanCeramic Socie ty,2000(20):2441-2445.[16]SHERIF EL-ESKAN DARAN Y M.Fabrica tio n ofnanocrystalline WC and nanocomposite WC-M gO re-fractory materials at room temperature[J].J of A lloysand Compounds,2000(296):175-182.[17]HWANG H J,NAG AI T,SA NDO M,et al.Fabrica-tion of piezoelectric particle-dispersed ceramic nano com-posite[J].J of the European Ceramic Society,1999(19):993-997.[18]CALD ERON H A,GA RIBAY-FEBL ES V,UM EM-OT O M,et al.M echanical properties of nanocry s-talline T i-Al-X alloy s[J].M aterials Science andEngineering,2002(A329-331):196-205.[19]CHA S I,HONG S H,K IM B K.Spark plasma sin-tering behavior of nanocrystalline WC-10Co cementedcarbide powders[J].M aterials Science and Engineer-ing,2003(A351):31-38.[20]ZHAN G D,KUN TZ J,W AN J,et al.Alumina-basednanocomp osites consol idated by s park plasma s intering[J].Scripta Material ia,2002(47):737-741.[21]张久兴,刘科高,王金淑,等.放电等离子烧结钼的组织和性能[J].中国有色金属学报,2001,11(5):796-800.[22]Y E L L,LI U Z G,RAV IP RASAD K,et al.Conso li-dation of MA amorphous N iT i pow ders by spark plas-ma sintering[J].M aterials Science and Engineering,1998(A241):290-293.[23]M U RAKA M I T,KOM A TS U M,K AWAHA RA A,et al.M echanical proper ties of spark plasma sinteredN b-Al compacts strengthened by dispersion of Nb2Nphase and additions of M o and W[J].Intermetallics,1999(7):731-739.[24]M EI B,M I YAM O TO Y.Inv estigation of TiAl/Ti2AlC composites prepared by spark plasma sintering[J].M aterials Chemistry and Physics,2002(75):291-295.[25]OM O RI M.Sintering,Consolidation,reaction andcrystal g rowth by the spark plasma sy stem[J].M ateri-al Science and Engineering,2000(A287):183-188.[26]SHEN Z J,JOHNSSO N M,NYG REN M.TiN/Al2O3composites and graded laminates thereof conso li-dated by spark plasma sintering[J].J of the EuropeanCeramic Socie ty,2003(23):1061-1068.[27]LU O Y M,PAN W,LI S Q,et al.A novel functio n-ally g raded material in the T i-Si-C system[J].M a-terials Science and Engineering,2003(A345):99-105.[28]KI M Y D,OH S T,M IN K H,et al.Synthesis of Cudispersed Al2O3nanocompo sites by high energy ballmilling and pulse electric current sintering[J].ScriptaM aterilia,2001(44):293-297.[29]N ISHIM U RA T,M IT I MO M,HI RO T SU RU H,etal.Fabrica tio n of silicon nitride nano-ceramics byspark plasma sintering[J].J of M aterials Science Let-ter,1995(14):1046-1047.[30]YOSHI M U RA M,OHJI T,SA NDO M,et al.Sy n-thesis of nanog rained Z rO2-based composites by chemi-cal processing and pulse electric cur rent sintering[J].M aterials Letters,1999(38)18-21.[31]高 濂,洪金生,宫本大树.放电等离子快速烧结氧化物陶瓷[J].无机材料学报,1998,1(13):18-22.[32]高 濂,王宏志,洪金生,等.放电等离子快速烧结SiC-Al2O3纳米复相陶瓷[J].无机材料学报,1999,1(14):55-60.[33]高 濂,王宏志,洪金生,等.SiC-ZrO2-Al2O3纳米复相陶瓷的力学性能和显微结构[J].无机材料学报,1999,14(5):795-799.[34]GA O L,WAN G H Z,HON G J S,et al.SiC-ZrO2(3Y)-Al2O3nanocomposites superfast densified byspark plasma sintering[J].N anoStructured M aterials,1999,11(1):43-49.[35]高 濂,洪金生,宫本大树.放电等离子快速烧结氧化铝力学性能和显微结构研究[J].无机材料学报,1998,6(13):904-908.[36]GA O L,HON G J S,M iy amo toh,et al.Bendingstrength and microstructure of Al2O3ceramics densifiedby spark plasma sintering[J].J of the Euro pean Ce-ramics Society,2000(20):2149-2152.[37]GA O L,JIN X H,KAWAO KA H,et al.Microstruc-ture and mechanical proper ties of SiC-mullite nano com-posite prepared by spark plasma sintering[J].Ma terialsScience and Engineering,2002(A334):262-266. [38]SHEN Z J,ZHAO Z,PENG H,et al.F ormation oftough interlocking micro structure in silicon nitride ce-ramics by dynamic ripening[J].Nature,2002,4(16): 266-269.[39]SHEN Z J,N YG REN M.Implications o f kineticallupromoted formation of metastableα-Sialon phases[J].Jof the European Ceramic Society,2001(21):611-615.(编辑 吕雪梅)·331·第3期冯海波,等:放电等离子烧结技术的原理及应用。
放电等离子烧结工艺方法

放电等离子烧结工艺方法放电等离子烧结工艺方法是一种常用的粉末冶金制备材料的技术方法。
该方法通过将粉末材料置于高温高压等离子体中,利用等离子体的能量和冲击力使粉末颗粒结合成块状材料。
放电等离子烧结工艺方法具有制备高密度、高强度材料的优势,广泛应用于金属、陶瓷等材料的制备过程中。
放电等离子烧结工艺方法的基本原理是利用高能电子束或激光束对粉末进行加热,使其迅速熔化并与周围颗粒结合。
在放电等离子体中,电子束或激光束的高能量可以使粉末颗粒表面瞬间熔化,形成液态金属或陶瓷。
同时,等离子体中的冲击力也可以促使颗粒之间的结合,增加材料的致密度和强度。
放电等离子烧结工艺方法可以分为两个步骤:预压和烧结。
在预压阶段,粉末材料被填充到模具中,并施加一定的压力,使颗粒之间的接触面积增大。
这有助于在后续的烧结过程中形成更好的结合。
在烧结阶段,加热源通过电子束或激光束对材料进行加热,并使其瞬间熔化。
在高温下,液态金属或陶瓷颗粒之间产生扩散效应,使颗粒结合更加紧密。
随着烧结时间的增加,材料逐渐冷却并固化,最终形成块状材料。
放电等离子烧结工艺方法具有许多优点。
首先,它可以制备高密度、高强度的材料。
由于等离子体的高能量和冲击力,粉末颗粒之间的结合更加紧密,颗粒内部的缺陷和孔隙减少,从而提高了材料的密度和强度。
其次,放电等离子烧结工艺方法具有较高的制备效率。
由于加热源的高能量,材料的烧结速度较快,可以在较短的时间内完成制备过程。
此外,该方法还可以制备复杂形状的材料。
通过合理设计模具结构,可以制备出具有复杂形状和内部结构的材料,满足不同应用领域的需求。
然而,放电等离子烧结工艺方法也存在一些局限性。
首先,该方法对原材料的要求较高。
粉末颗粒的尺寸、形状、成分等都会对最终材料的性能产生影响,因此需要精确控制原材料的质量。
其次,放电等离子烧结工艺方法对设备要求较高。
高能电子束或激光束的加热源需要具备较高的功率和精度,以确保材料能够均匀加热和烧结。
放电等离子烧结技术的发展和应用
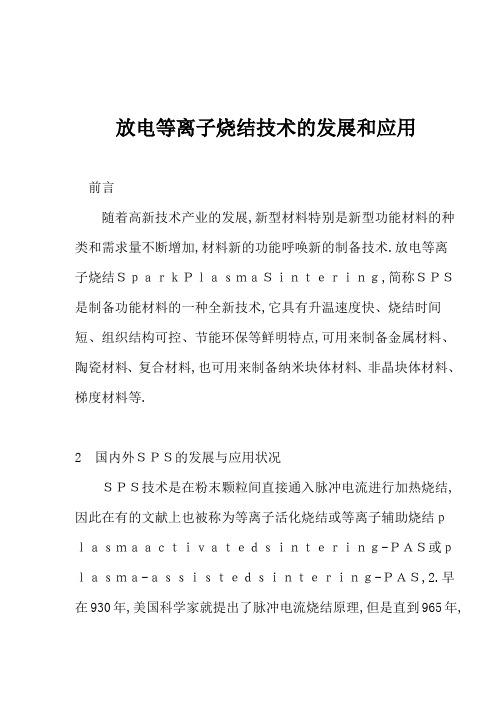
放电等离子烧结技术的发展和应用前言随着高新技术产业的发展,新型材料特别是新型功能材料的种类和需求量不断增加,材料新的功能呼唤新的制备技术.放电等离子烧结SparkPlasmaSintering,简称SPS是制备功能材料的一种全新技术,它具有升温速度快、烧结时间短、组织结构可控、节能环保等鲜明特点,可用来制备金属材料、陶瓷材料、复合材料,也可用来制备纳米块体材料、非晶块体材料、梯度材料等.2 国内外SPS的发展与应用状况SPS技术是在粉末颗粒间直接通入脉冲电流进行加热烧结,因此在有的文献上也被称为等离子活化烧结或等离子辅助烧结plasmaactivatedsintering-PAS或plasma-assistedsintering-PAS,2.早在930年,美国科学家就提出了脉冲电流烧结原理,但是直到965年,脉冲电流烧结技术才在美、日等国得到应用.日本获得了SPS技术的专利,但当时未能解决该技术存在的生产效率低等问题,因此SPS技术没有得到推广应用.988年日本研制出第一台工业型SPS装置,并在新材料研究领域内推广应用.990年以后,日本推出了可用于工业生产的SPS第三代产品,具有0~00t的烧结压力和脉冲电流5000~8000A.最近又研制出压力达500t,脉冲电流为25000A的大型SPS装置.由于SPS技术具有快速、低温、高效率等优点,近几年国外许多大学和科研机构都相继配备了SPS烧结系统,并利用SPS进行新材料的研究和开发3.998年瑞典购进SPS烧结系统,对碳化物、氧化物、生物陶瓷等材料进行了较多的研究工作4.国内近三年也开展了用SPS技术制备新材料的研究工作,3,引进了数台SPS烧结系统,主要用来烧结纳米材料和陶瓷材料5~8.SPS作为一种材料制备的全新技术,已引起了国内外的广泛重视.3 SPS的烧结原理3 等离子体和等离子加工技术9,0SPS是利用放电等离子体进行烧结的.等离子体是物质在高温或特定激励下的一种物质状态,是除固态、液态和气态以外,物质的第四种状态.等离子体是电离气体,由大量正负带电粒子和中性粒子组成,并表现出集体行为的一种准中性气体.等离子体是解离的高温导电气体,可提供反应活性高的状态.等离子体温度4000~0999℃,其气态分子和原子处在高度活化状态,而且等离子气体内离子化程度很高,这些性质使得等离子体成为一种非常重要的材料制备和加工技术.等离子体加工技术已得到较多的应用,例如等离子体CVD、低温等离子体PVD以及等离子体和离子束刻蚀等.目前等离子体多用于氧化物涂层、等离子刻蚀方面,在制备高纯碳化物和氮化物粉体上也有一定应用.而等离子体的另一个很有潜力的应用领域是在陶瓷材料的烧结方面.产生等离子体的方法包括加热、放电和光激励等.放电产生的等离子体包括直流放电、射频放电和微波放电等离子体.SPS利用的是直流放电等离子体.32 SPS装置和烧结基本原理SPS装置主要包括以下几个部分:轴向压力装置;水冷冲头电极;真空腔体;气氛控制系统真空、氩气;直流脉冲电源及冷却水、位移测量、温度测量和安全等控制单元.SPS的基本结构如图所示.SPS与热压HP有相似之处,但加热方式完全不同,它是一种利用通-断直流脉冲电流直接通电烧结的加压烧结法.通-断式直流脉冲电流的主要作用是产生放电等离子体、放电冲击压力、焦耳热和电场扩散作用.SPS烧结时脉冲电流通过粉末颗粒如图2所示.在SPS烧结过程中,电极通入直流脉冲电流时瞬间产生的放电等离子体,使烧结体内部各个颗粒均匀地自身产生焦耳热并使颗粒表面活化.与自身加热反应合成法SHS和微波烧结法类似,SPS是有效利用粉末内部的自身发热作用而进行烧结的.这种放电直接加热法,热效率极高,放电点的弥散分布能够实现均匀加热,因而容易制备出均质、致密、高质量的烧结体.SPS烧结过程可以看作是颗粒放电、导电加热和加压综合作用的结果.除加热和加压这两个促进烧结的因素外,在SPS技术中,颗粒间的有效放电可产生局部高温,可以使表面局部熔化、表面物质剥落;高温等离子的溅射和放电冲击清除了粉末颗粒表面杂质如去除表层氧化物等和吸附的气体.电场的作用是加快扩散过程,9,2.4 SPS的工艺优势SPS的工艺优势十分明显:加热均匀,升温速度快,烧结温度低,烧结时间短,生产效率高,产品组织细小均匀,能保持原材料的自然状态,可以得到高致密度的材料,可以烧结梯度材料以及复杂工件等3,.与HP和HIP相比,SPS装置操作简单、不需要专门的熟练技术.文献报道,生产一块直径00mm、厚7mm的ZrO23Y/不锈钢梯度材料FGM用的总时间是58min,其中升温时间28min、保温时间5min和冷却时间25min.与HP相比,SPS技术的烧结温度可降低00~200℃3.5 SPS在材料制备中的应用目前在国外,尤其在日本开展了较多用SPS制备新材料的研究,部分产品已投入生产.SPS可加工的材料种类如表所示.除了制备材料外,SPS还可进行材料连接,如连接MoSi2与石墨4,ZrO2/Cermet/Ni等5.近几年,国内外用SPS制备新材料的研究主要集中在:陶瓷、金属陶瓷、金属间化合物,复合材料纳米材料和功能材料等方面.其中研究最多的是功能材料,它包括热电材料6、磁性材料7,功能梯度材料8,复合功能材料9和纳米功能材料20等.对SPS制备非晶合金、形状记忆合金2、金刚石等也作了尝试,取得了较好的结果.5 功能梯度材料功能梯度材料FGM的成分是梯度变化的,各层的烧结温度不同,利用传统的烧结方法难以一次烧成.利用CVD、PVD等方法制备梯度材料,成本很高,也很难实现工业化.采用阶梯状的石墨模具,由于模具上、下两端的电流密度不同,因此可以产生温度梯度.利用SPS在石墨模具中产生的梯度温度场,只需要几分钟就可烧结好成分配比不同的梯度材料.目前SPS成功制备的梯度材料有:不锈钢/ZrO2;Ni/ZrO2;Al/高聚物;Al/植物纤维;PSZ/Ti等梯度材料.在自蔓延燃烧合成SHS中,电场具有较大激活效应和作用,特别是场激活效应可以使以前不能合成的材料也能成功合成,扩大了成分范围,并能控制相的成分,不过得到的是多孔材料,还需要进一步加工提高致密度.利用类似于SHS电场激活作用的SPS技术,对陶瓷、复合材料和梯度材料的合成和致密化同时进行,可得到65nm的纳米晶,比SHS少了一道致密化工序22.利用SPS可制备大尺寸的FGM,目前SPS制备的尺寸较大的FGM体系是ZrO23Y/不锈钢圆盘,尺寸已达到00mm×7mm23.用普通烧结和热压WC粉末时必须加入添加剂,而SPS使烧结纯WC成为可能.用SPS制备的WC/Mo梯度材料的维氏硬度HV和断裂韧度分别达到了24GPa和6MPa·m/2,大大减轻由于WC和Mo的热膨胀不匹配而导致热应力引起的开裂24.52 热电材料由于热电转换的高可靠性、无污染等特点,最近热电转换器引起了人们极大的兴趣,并研究了许多热电转换材料.经文献检索发现,在SPS制备功能材料的研究中,对热电材料的研究较多.热电材料的成分梯度化是目前提高热电效率的有效途径之一.例如,成分梯度的βFeSi2就是一种比较有前途的热电材料,可用于200~900℃之间进行热电转换.βFeSi2没有毒性,在空气中有很好的抗氧化性,并且有较高的电导率和热电功率.热电材料的品质因数越高Z=α2/kρ,其中Z是品质因数,α为Seebeck系数,k为导热系数,ρ为材料的电阻率,其热电转换效率也越高.实验表明,采用SPS制备的成分梯度的βFeSixSi含量可变,比βFeSi2的热电性能大为提高25.这方面的例子还有Cu/Al2O3/Cu26,MgFeSi227,βZn4Sb328,钨硅化物29等.2用于热电致冷的传统半导体材料不仅强度和耐久性差,而且主要采用单向生长法制备,生产周期长、成本高.近年来有些厂家为了解决这个问题,采用烧结法生产半导体致冷材料,虽改善了机械强度和提高了材料使用率,但是热电性能远远达不到单晶半导体的性能.现在采用SPS生产半导体致冷材料,在几分钟内就可制备出完整的半导体材料,而晶体生长法却要十几个小时.SPS制备半导体热电材料的优点是,可直接加工成圆片,不需要单向生长法那样的切割加工,节约了材料,提高了生产效率.热压和冷压-烧结的半导体性能低于晶体生长法制备的性能.现用于热电致冷的半导体材料的主要成分是Bi,Sb,Te和Se,目前最高的Z值为30×0-3/K,而用SPS制备的热电半导体的Z值已达到29~30×0-3/K,几乎等于单晶半导体的性能30.表2是SPS和其它方法生产BiTe材料的比较.53 铁电材料用SPS烧结铁电陶瓷PbTiO3时,在900℃~000℃下烧结~3min,烧结后平均颗粒尺寸<μm,相对密度超过98%.由于陶瓷中孔洞较少3,因此在0~06Hz之间介电常数基本不随频率而变化.用SPS制备铁电材料Bi4Ti3O2陶瓷时,在烧结体晶粒伸长和粗化的同时,陶瓷迅速致密化.用SPS容易得到晶粒取向度好的试样,可观察到晶粒择优取向的Bi4Ti3O2陶瓷的电性能有强烈的各向异性32.用SPS在900℃烧结制备的BaTiO3陶瓷,其晶粒尺寸接近200nm33.用SPS制备铁电Li置换IIVI半导体ZnO陶瓷,使铁电相变温度Tc提高到470K,而以前冷压烧结陶瓷只有330K34.54 磁性材料用SPS烧结NdFeB磁性合金,若在较高温度下烧结,可以得到高的致密度,但烧结温度过高会导致出现α相和晶粒长大,磁性能恶化.若在较低温度下烧结,虽能保持良好的磁性能,但粉末却不能被完全压实,因此要详细研究密度与性能的关系35.SPS在烧结磁性材料时具有烧结温度低、保温时间短的工艺优点.NdFeCoVB在650℃下保温5min,即可烧结成接近完全密实的块状磁体,没有发现晶粒长大36.用SPS制备的865Fe6Si4Al35Ni和MgFe2O4的复合材料850℃,30MPa,具有高的饱和磁化强度Bs=2T和高的电阻率ρ=×0-2Ω·m37.以前用快速凝固法制备的软磁合金薄带,虽已达到几十纳米的细小晶粒组织,但是不能制备成合金块体,应用受到限制.而现在采用SPS制备的块体磁性合金的磁性能已达到非晶和纳米晶组织带材的软磁性能3. 55 纳米材料致密纳米材料的制备越来越受到重视.利用传统的热压烧结和热等静压烧结等方法来制备纳米材料时,很难保证能同时达到纳米尺寸的晶粒和完全致密的要求.利用SPS技术,由于加热速度快,烧结时间短,可显着抑制晶粒粗化.例如:用平均粒度为5μm的TiN粉经SPS烧结963K,96~382MPa,烧结5min,可得到平均晶粒65nm的TiN密实体3.文献3中引用有关实例说明了SPS烧结中晶粒长大受到最大限度的抑制,所制得烧结体无疏松和明显的晶粒长大. SPS烧结时,虽然所加压力较小,但是除了压力的作用会导致活化能Q降低外,由于存在放电的作用,也会使晶粒得到活化而使Q值进一步减小,从而会促进晶粒长大,因此从这方面来说,用SPS烧结制备纳米材料有一定的困难. 但是实际上已有成功制备平均晶粒度为65nm的TiN密实体的实例.在文献38中,非晶粉末用SPS烧结制备出20~30nm的Fe90Zr7B3纳米磁性材料.另外,还已发现晶粒随SPS烧结温度变化比较缓慢7,因此SPS制备纳米材料的机理和对晶粒长大的影响还需要作进一步的研究.56 非晶合金的制备在非晶合金的制备中,要选择合金成分以保证合金具有极低的非晶形成临界冷却速度,从而获得极高的非晶形成能力.在制备工艺方面主要有金属模浇铸法和水淬法,其关键是快速冷却和控制非均匀形核.由于制备非晶合金粉末的技术相对成熟,因此多年来,采用非晶粉末在低于其晶化温度下进行温挤压、温轧、冲击爆炸固化和等静压烧结等方法来制备大块非晶合金,但存在不少技术难题,如非晶粉末的硬度总高于晶态粉末,因而压制性能欠佳,其综合性能与旋淬法制备的非晶薄带相近,难以作为高强度结构材料使用39.可见用普通粉末冶金法制备大块非晶材料存在不少技术难题. SPS作为新一代烧结技术有望在这方面取得进展,文献40中利用SPS烧结由机械合金化制取的非晶Al基粉末得到了块状圆片试样0mm×2mm,此非晶合金是在375MPa下503K时保温20min制备的,含有非晶相和结晶相以及残余的Sn相.其非晶相的结晶温度是533K.文献4中用脉冲电流在423K和500MPa下制备了Mg80Ni0Y5B5块状非晶合金,经分析其中主要是非晶相.非晶Mg合金比A29D合金和纯镁有较高的腐蚀电位和较低的腐蚀电流密度,非晶化改善了镁合金的抗腐蚀抗力.从实践来看,可以采用SPS烧结法制备块状非晶合金.因此利用先进的SPS技术进行大块非晶合金的制备研究很有必要. 6 总结与展望放电等离子烧结SPS是一种低温、短时的快速烧结法,可用来制备金属、陶瓷、纳米材料、非晶材料、复合材料、梯度材料等.SPS的推广应用将在新材料的研究和生产领域中发挥重要作用. SPS的基础理论目前尚不完全清楚,需要进行大量实践与理论研究来完善;SPS需要增加设备的多功能性和脉冲电流的容量,以便做尺寸更大的产品;特别需要发展全自动化的SPS生产系统,以满足复杂形状、高性能的产品和三维梯度功能材料的生产需要42. 对实际生产来说,需要发展适合SPS技术的粉末材料;也需要研制比目前使用的模具材料石墨强度更高、重复使用率更好的新型模具材料,以提高模具的承载能力和降低模具费用.在工艺方面,需要建立模具温度和工件实际温度的温差关系,以便更好地控制产品质量.在SPS产品的性能测试方面,需要建立与之相适应的标准和方法.。
放电等离子体烧结

放电等离子体烧结
放电等离子体烧结
1.简介
放电等离子体烧结是一种利用等离子体特性进行烧结的方法。
它具有原料利用率高、烧结速度快、能耗低、烧结结构紧密等优点,它可以烧结金属、非金属和金属材料的复合材料。
放电等离子体烧结是一种强大的烧结工艺,它可以用来制造金属陶瓷、金属陶瓷复合材料,以及金属的高性能表面涂层等。
2.工艺原理
放电等离子体烧结是将低压电流以较高温度连续加热至原料表面,使原料快速熔液,利用等离子体的特性实现烧结的一种新的烧结方法。
放电等离子体烧结的原理包括电导热、电磁热、电离子热等。
在放电等离子体烧结过程中,热源可以是电流,或者是等离子体内热量产生的热源,当等离子体产生后,由于等离子体内的热量产生和原料表面电导热的作用,使得原料表面快速加热。
3.主要优点
放电等离子体烧结的主要优点有:
(1)烧结速度快,可以进行快速烧结。
(2)熔液区域较小,烧结过程中熔液的发生范围较小,烧结效果好。
(3)原料利用率高,烧结过程中不会出现损耗,原料利用率高。
(4)烧结均匀,烧结表面的晶粒细小均匀,且烧结结构紧密,
抗拉强度和耐磨性好。
(5)烧结温度低,烧结温度低,因而无需进行退火处理,烧结效率高。
(6)能耗低,由于烧结时采用的是低压电流,因此能耗低。