注塑件 分型面的选择
模具设计分型面的选择及设计原则

模具设计分型面的选择及设计原则一、分型面的选择分型面的选择也是模具设计的第一步,它受到产品的形状,外观,壁厚,尺寸精度,模穴数等很多因素的影响。
一般的产品拿到手里,大分型面确定我相信大家对这个基本没什么问题。
可对于很多有侧抽芯,或者涉及到枕位,碰穿,插穿时。
这些就有争论了,怎么去选择有时候还真不是个简单的事,因此,咱们这里来聊聊如何去选择分型面。
一般来说分型面的选择都会遵循以下的几个原则:1:符合产品脱模要求分型面也就是为了产品能顺利取出模具的。
因此,分型面的位置应该选在产品断面尺寸最大的部位,这是一条最基本的原则。
2:方位的确定在决定产品在模具里面的方位时,分型面的选择应该尽量防止产品形成侧孔或者侧扣位,应避免采用复杂的模具结构。
3:分型面的形状一般的产品,常常采用一个与注塑机开模运动方向垂直的分型面,特殊情况下才采用其它形状的分型面。
分型面的形状以方便加工和脱模为原则。
像某此弯曲的产品,分型时就得根椐它弯曲的曲率来。
4:确保产品外观和质量分型面不要选择在产品光滑的'外表面。
外观面一般来说是不允许有夹线及其它影响美观的线条出现的;有些有同心度要求的产品,得把有同心度要求的部分全部放到同一侧,这样才能保证其同心度。
5:有利于脱模一般的模具的脱模机构都是在动模的,所以选择分型面时应尽可能的使开模后产品留在动模。
因此对于有些有可能粘住定模的地方,我们往往会加做定模辅助脱模机构。
6:考虑侧向开模距离一般的侧向机械式开模的距离都是比较小的。
因此选择分型面时应把抽芯距长的方向选择在前后模开合的方向上,将短的方向做为侧向分型。
7:锁模力的考虑模具的侧向锁模力相对来说比较小,所以对于投影面积较大的大型产品,应将投影面积大的方向放在前后模开合模方向上,而将侧投影面积较小的作为侧向分型。
8:利于排气当把分型面做为主要排气时,应该把分型面设计在塑料流动的末端,以利于排气。
9:模具零件易于加工选择分型面时,应把模具分割成易于加工的零件,减小机加工难度。
注塑模具分型面的选择
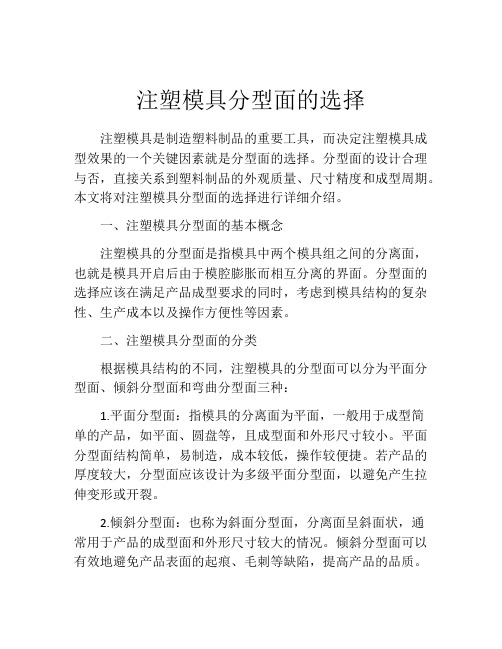
注塑模具分型面的选择注塑模具是制造塑料制品的重要工具,而决定注塑模具成型效果的一个关键因素就是分型面的选择。
分型面的设计合理与否,直接关系到塑料制品的外观质量、尺寸精度和成型周期。
本文将对注塑模具分型面的选择进行详细介绍。
一、注塑模具分型面的基本概念注塑模具的分型面是指模具中两个模具组之间的分离面,也就是模具开启后由于模腔膨胀而相互分离的界面。
分型面的选择应该在满足产品成型要求的同时,考虑到模具结构的复杂性、生产成本以及操作方便性等因素。
二、注塑模具分型面的分类根据模具结构的不同,注塑模具的分型面可以分为平面分型面、倾斜分型面和弯曲分型面三种:1.平面分型面:指模具的分离面为平面,一般用于成型简单的产品,如平面、圆盘等,且成型面和外形尺寸较小。
平面分型面结构简单,易制造,成本较低,操作较便捷。
若产品的厚度较大,分型面应该设计为多级平面分型面,以避免产生拉伸变形或开裂。
2.倾斜分型面:也称为斜面分型面,分离面呈斜面状,通常用于产品的成型面和外形尺寸较大的情况。
倾斜分型面可以有效地避免产品表面的起痕、毛刺等缺陷,提高产品的品质。
不过倾斜分型面制造难度较大,同时增加了模具的成本和加工难度。
3.弯曲分型面:也称为曲面分型面,在分离面呈曲面状的情况下,它可以用来制造外形复杂且不规则的产品。
弯曲分型面制造难度和成本都比平面分型面和倾斜分型面高,但能够制造更高精度的产品。
三、注塑模具分型面的选择原则1.分型面尽可能选择简单,以降低制造成本及操作难度,同时提高模具的寿命。
2.分型面应该尽量避免在成型面上留下痕迹和印记。
对于防止痕迹和印记的问题,可以选择倾斜分型面或弯曲分型面。
3.考虑产品的工艺特点和成型要求。
例如,对于薄壁弱结构的产品,分型面应该选择为多级平面分型面。
对于大型产品,可以选择倾斜分型面或弯曲分型面来保证产品的成型精度。
4.尽量选择产品表面朝上的分型面,以方便后续产品加工和涂装。
5.考虑成型周期和生产效率,尽可能选择简单的分型面结构,降低模具的制造和开发周期,提高生产效率。
注塑模具结构中的分型面设计

图 3 分 型 面 选 择 应便 于脱 模
4
f
r
( ) 合 分 型 面 e瓣 ( )双 分 型 面 f
实 际的模具 结构基 本上 有 3种情 况 : 型腔 ①
完 全 在 动 模 一 侧 ; 型 腔 完 全 在 定 模 一 侧 ; 型 腔 ② ③
收稿 日期 : 0 0 0 —2 2 1 7 4
1 .定 模
2 .动 模
3、.瓣 合模 块 4
图 1 分 型 面 的 形 式
分 别在 动 、 定模 中。分 型 面 不仅 关 系 到 塑件 的 正常 成形 和脱 模 , 而且涉及 到模具 制造 成本 。
第 一作 者 简介 :郭继 祥 ,男 ,18 9 4年 生 ,硕 士 研 究生 。
设 计 ・ 究 研 分 型 面选 择 总的原则 为 : 证 塑件质 量 , 于脱 保 便
的推 板脱模 机构 便可使 塑件 脱模 。
() a
一 - -
( ) b
图 5 分 型 面对 制 品精 度 的 影 响
( ) 型面 选择 应 有 利 于排 气 。注 塑模 的排 气 4分
是 模 具 设 计 中不 可 忽 视 的 一 个 问 题 , 别 是 快 速 注 特
塑成 形工艺 的发 展对 注塑 模 排气 的要 求就 更 严 格 。
() 梯 分 型 面 c容 。分型 面选 择 合 理 , 具结 构 简 模
单 ,塑 件 易成形 , 塑件 质 量 高。若 分 型 面选 择不 且 合理 , 则模 具结 构变 得 复 杂 , 塑件 成 形 困难 , 塑 件 且
质 量 差
《 电加工与模具}00年第 6 21 期
设 计 ・ 究 研
注塑模具之分型面的选择

注塑模具之分型面的选择分型面的选择分型面为动模与定模的分界面,是取出塑件或者浇注系统凝料的面.它的合理选择是塑件能完好成型的条件,不仅关系到塑件的脱模,而且涉及摸具结构与制造成本. 合理的分型面不但能满足制品各方面的性能要求 ,而且使模具结构简单,成本亦会令人满意.选择分型面时有下面一些原则能够遵循:.分型面应选择在塑件的最大截面处(圖二),否则给脱模与加工带来困难(圖一).此点可说是选择的首要原则.图一(無法脫模)图二(順利脫模).尽可能地将塑件留在公模侧,因在公模侧设置脱模机构简便易行..在安排制件在型腔中方位时,尽量避免侧向分型或者抽芯以利于简化模具结构.结合以上原则还要综合考虑塑件的尺寸精度、外观质量、使用要求及是否有利于浇注系统特别是浇口的合理安排, 是否有利于排气。
所设计的模具的塑件电话机的上面板(图示),由图能够看出,不能将侧面作为分型面,由于那将导致不合理的模具高度与模腔深度。
关于这一模具,分型面没有太多的选择。
它的侧边是有斜度的,下端面为最大截面,可考虑将整个外观面作为分型面。
电话机的上面板外观表面质量的要求很高,顶杆不能在外观面侧顶出,否则顶出痕迹会影响表面质量,因此外观面最好在母模侧成产品外观图型。
在结构方面,(如图所示)内侧面有很多小直径的BOSS,这些结构宜用顶管(套筒顶针)成型且便于脱模。
那么,这一部分应在公模侧。
如此布置,党制品冷却时,会因收缩作用而包覆在公模仁上,有利于制品滞留在公模一側。
根据以上分析,分型面的选择为整个外观面,内部结构在公模侧成型,外观面成型与母模侧(与图二相似)。
这样易于脱模,使模具结构相对简化,且分型面有一靠破处可设置浇口亦利于浇注系统的安内部结构图靠破 BOSS排。
综上,此选择可行。
型腔数目的确定注射模可设计成一模一腔也可设计成一模多腔。
其数目的确定要从下列几个方面考虑:.注塑产品的尺寸及结构的复杂性.塑件的尺寸精度—型腔越多,精度也相对降低。
注塑模具分型面的选择原则
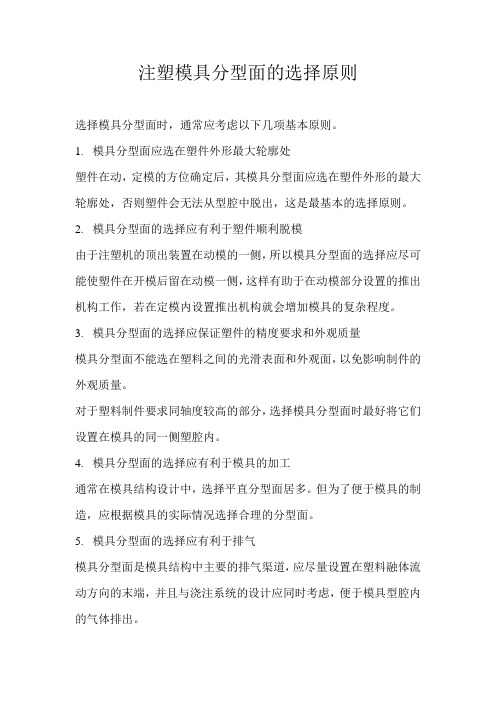
注塑模具分型面的选择原则
选择模具分型面时,通常应考虑以下几项基本原则。
1. 模具分型面应选在塑件外形最大轮廓处
塑件在动,定模的方位确定后,其模具分型面应选在塑件外形的最大轮廓处,否则塑件会无法从型腔中脱出,这是最基本的选择原则。
2. 模具分型面的选择应有利于塑件顺利脱模
由于注塑机的顶出装置在动模的一侧,所以模具分型面的选择应尽可能使塑件在开模后留在动模一侧,这样有助于在动模部分设置的推出机构工作,若在定模内设置推出机构就会增加模具的复杂程度。
3. 模具分型面的选择应保证塑件的精度要求和外观质量
模具分型面不能选在塑料之间的光滑表面和外观面,以免影响制件的外观质量。
对于塑料制件要求同轴度较高的部分,选择模具分型面时最好将它们设置在模具的同一侧塑腔内。
4. 模具分型面的选择应有利于模具的加工
通常在模具结构设计中,选择平直分型面居多。
但为了便于模具的制造,应根据模具的实际情况选择合理的分型面。
5. 模具分型面的选择应有利于排气
模具分型面是模具结构中主要的排气渠道,应尽量设置在塑料融体流动方向的末端,并且与浇注系统的设计应同时考虑,便于模具型腔内的气体排出。
6. 模具分型面的选择应考虑模具的侧向抽芯
为了保证侧向抽芯的放置容易和抽芯机构的动作顺利,选择模具分型面时,应以浅的侧向凹孔或短的侧向凸台作为抽芯方向,将较深的凹孔或较高的凸台放置于合模的方向,并尽量把侧向抽芯机构放置在动模一侧。
以上信息由:金马泰模具厂提供。
注塑模具设计规范
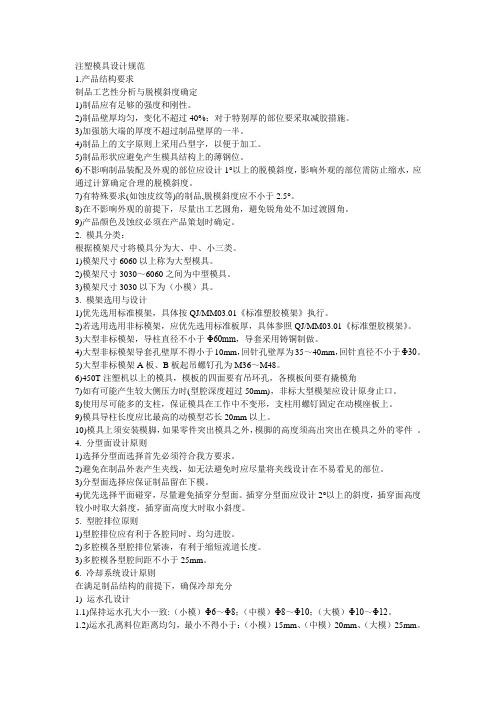
注塑模具设计规范1.产品结构要求制品工艺性分析与脱模斜度确定1)制品应有足够的强度和刚性。
2)制品壁厚均匀,变化不超过40%;对于特别厚的部位要采取减胶措施。
3)加强筋大端的厚度不超过制品壁厚的一半。
4)制品上的文字原则上采用凸型字,以便于加工。
5)制品形状应避免产生模具结构上的薄钢位。
6)不影响制品装配及外观的部位应设计1°以上的脱模斜度,影响外观的部位需防止缩水,应通过计算确定合理的脱模斜度。
7)有特殊要求(如蚀皮纹等)的制品,脱模斜度应不小于2.5°。
8)在不影响外观的前提下,尽量出工艺圆角,避免锐角处不加过渡圆角。
9)产品颜色及蚀纹必须在产品策划时确定。
2. 模具分类:根据模架尺寸将模具分为大、中、小三类。
1)模架尺寸6060以上称为大型模具。
2)模架尺寸3030~6060之间为中型模具。
3)模架尺寸3030以下为(小模)具。
3. 模架选用与设计1)优先选用标准模架,具体按QJ/MM03.01《标准塑胶模架》执行。
2)若选用选用非标模架,应优先选用标准板厚,具体参照QJ/MM03.01《标准塑胶模架》。
3)大型非标模架,导柱直径不小于Φ60mm,导套采用铸铜制做。
4)大型非标模架导套孔壁厚不得小于10mm,回针孔壁厚为35~40mm,回针直径不小于Φ30。
5)大型非标模架A板、B板起吊螺钉孔为M36~M48。
6)450T注塑机以上的模具,模板的四面要有吊环孔,各模板间要有撬模角7)如有可能产生较大侧压力时(型腔深度超过50mm),非标大型模架应设计原身止口。
8)使用尽可能多的支柱,保证模具在工作中不变形,支柱用螺钉固定在动模座板上。
9)模具导柱长度应比最高的动模型芯长20mm以上。
10)模具上须安装模脚,如果零件突出模具之外,模脚的高度须高出突出在模具之外的零件。
4. 分型面设计原则1)选择分型面选择首先必须符合我方要求。
2)避免在制品外表产生夹线,如无法避免时应尽量将夹线设计在不易看见的部位。
UG注塑模具设计智慧树知到答案章节测试2023年日照职业技术学院
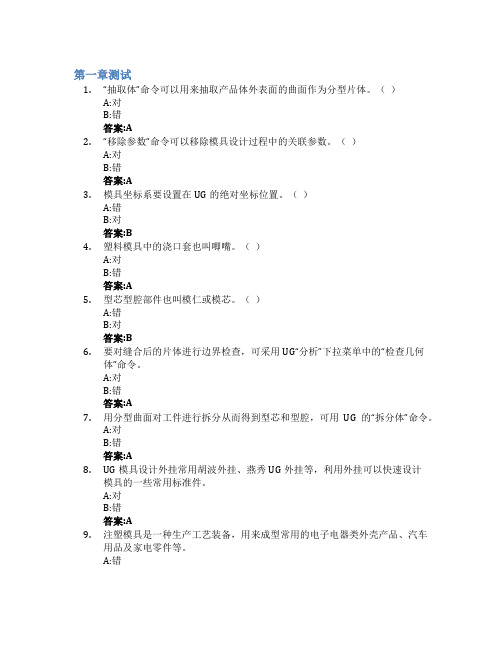
第一章测试1.“抽取体”命令可以用来抽取产品体外表面的曲面作为分型片体。
()A:对B:错答案:A2.“移除参数”命令可以移除模具设计过程中的关联参数。
()A:对B:错答案:A3.模具坐标系要设置在UG的绝对坐标位置。
()A:错B:对答案:B4.塑料模具中的浇口套也叫唧嘴。
()A:对B:错答案:A5.型芯型腔部件也叫模仁或模芯。
()A:错B:对答案:B6.要对缝合后的片体进行边界检查,可采用UG“分析”下拉菜单中的“检查几何体”命令。
A:对B:错答案:A7.用分型曲面对工件进行拆分从而得到型芯和型腔,可用UG的“拆分体”命令。
A:对B:错答案:A8.UG模具设计外挂常用胡波外挂、燕秀UG外挂等,利用外挂可以快速设计模具的一些常用标准件。
A:对B:错答案:A9.注塑模具是一种生产工艺装备,用来成型常用的电子电器类外壳产品、汽车用品及家电零件等。
A:错B:对答案:B10.塑料是由合成树脂及添加剂组成。
A:错B:对答案:B第二章测试1.UG产品斜率分析的目的有()。
A:对直身面增加拔模B:找出分型面位置C:得到前模面和后模面的拔模角度答案:ABC2.UG“塑模部件验证” 命令在模具分模中的主要作用是()。
A:获得分型线B:区分前后模颜色面C:修补破孔答案:B3.对于小件产品(<100mm),产品边到模仁边的距离一般取25~30 mm;产品最高位置到前模仁(型腔)顶面的距离一般取25~30 mm。
()A:对B:错答案:A4.创建分型面时,产品R角处一般不用拉伸命令来创建片体。
()A:错B:对答案:B5.分模前要设置产品的收缩率,UG中常用“缩放体”命令设置产品收缩率。
()A:错B:对答案:B6.分型面的选择原则是:开设在产品投影轮廓最大处。
A:错B:对答案:B7.分型面是指分开模具取出塑件和浇注系统凝料可分离接触的表面。
A:错B:对答案:B8.UG在抽取多个产品外观面时,可结合“颜色过滤器”进行快速抽取。
注塑模具分型面的设计原则

注塑模具分型面的设计原则注塑模具的分型面,这个词一听就让人觉得高大上,实际上就是决定我们能不能顺利取出塑料件的一个关键因素。
咱们今天就来聊聊这个话题,看看在设计分型面时,咱们得注意些什么。
1. 分型面的基本概念1.1 什么是分型面?首先,分型面就是模具的两个部分相接的地方,通俗点说,就是模具合在一起的“门”,这个“门”一开,咱们的产品才能顺利出来。
想象一下,如果这个“门”设计得不合适,那出来的产品就像个坏苹果,难看得很,不仅浪费了材料,还得重来,真是让人心疼啊。
1.2 分型面的功能这个“门”可不是说开就开的,它有很多重要的功能。
比如,确保模具的对接精度,防止漏料;还要便于操作,方便工人打开模具取出产品。
要是这“门”设计得好,大家工作起来就轻松多了,真是事半功倍。
2. 分型面设计的原则2.1 简单易行的设计说到设计原则,首先要说的就是“简单”!别把事情搞复杂,设计越简单,出错的概率就越低。
想象一下,你设计个复杂得像迷宫一样的分型面,结果工人进进出出都找不到方向,最后累得像只狗,这可就得不偿失了。
2.2 符合产品的形状再来就是,要根据你要做的产品形状来设计分型面。
比如,如果你的产品是个球形的东西,那你可不能给它设计个方形的分型面,这样不仅取不出来,还得给它找个“新家”!所以,分型面的设计一定要与产品形状“珠联璧合”,才能顺利取出。
2.3 考虑排气和冷却还有一点,千万别忽略了排气和冷却的问题。
塑料在注塑时,气体会被压进去,这可得有个地方让它们“透透气”。
设计合理的排气孔,能有效减少气泡,确保产品的质量。
冷却也是个关键,模具里温度一高,产品就容易变形,大家想要的可不是变形金刚。
3. 分型面的优化技巧3.1 选对材料说到优化,材料的选择也不能小觑。
不同材料对分型面的影响是巨大的,比如,硬度、耐磨性、导热性,这些都得考虑。
要是用错材料,分型面可能很快就磨损了,那可就麻烦了。
3.2 模具结构的调整最后,模具的结构调整也是提升分型面设计的好方法。
注塑模成型部分(模仁)设计原则

注塑模--成型部分(模仁)设计原则我是以一个产品结构设计者的角度来介绍,而非专业模具设计者,所论述的知识内容只为产品结构设计工作服务。
上面有讲到注塑模中的标准模架部分,现在来讲成型部分的一些基本原则,也就是模仁设计的注意事项。
一,拔模1,拔模的必要性拔模并非模具工作者的口头术语,我们做结构的也经常讲这个东西,它关乎塑件制品能否顺利脱模,关乎制品的成型难度、顶出难度、表面质量等,是我们在设计产品时时时刻刻要考虑到的问题。
有人说只要在关键位置给出拔模角度就好了,其他的就叫模具设计者们去自己弄吧,我并不赞同这个说法,拔模在产品结构设计环节就该被完成,为何要拖到下个工序呢,对于一个产品,任何一个面都要考虑拔模问题,并在结构设计环节做出来,这是咱的职业操守。
拔模的定义:为了能够使产品能够顺利脱模,我们把产品的侧壁设置一定角度的做法就叫做拔模,这个角度就叫拔模角度,为什么设置拔模角度:热塑性塑料在冷却过程中会收缩,从而紧贴在模仁上,很难被顶出。
(如下图)从图中可以看出开模以后,产品从定模脱出,贴在后模上面,此时顶出装置开始把塑件从动模上顶出,但塑件却被卡在了后模上面,当然塑料肯定很有钢铁强,最终会被顶出,可强行顶出会使塑件变形或被破坏。
这就是拔模方向错误导致的。
2,拔模角度的选择拔模会改变原定产品的尺寸,会使直面变成斜面,这是不可避免的。
但我们也可以换一个角度来想,只有拔好模的产品外观尺寸才是正确的,未拔模的是错的,那我们就不用去纠结拔模后会改变尺寸的问题了。
当然,在保证顺利脱模的情况下,拔模角度越小越好,那么我们从哪些角度来考虑拔模角度的大小呢?之前在产品结构设计基本原则中就有说过,如下:(1),在不影响产品外观和功能下,拔模角尽量大。
(2),尺寸大的产品,拔模角尽量小。
(3),产品结构复杂不易拔模的,采用较大斜度。
(4),塑胶材料收缩率大的,拔模斜度也要大。
(5),增强塑料选大斜度,自润滑塑料选较小斜度。
模具分型面选择原则
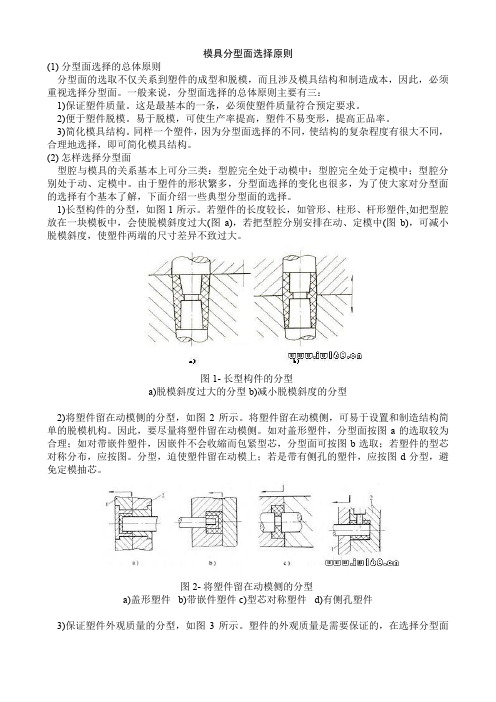
模具分型面选择原则(1) 分型面选择的总体原则分型面的选取不仅关系到塑件的成型和脱模,而且涉及模具结构和制造成本,因此,必须重视选择分型面。
一般来说,分型面选择的总体原则主要有三:1)保证塑件质量。
这是最基本的一条,必须使塑件质量符合预定要求。
2)便于塑件脱模。
易于脱模,可使生产率提高,塑件不易变形,提高正品率。
3)简化模具结构。
同样一个塑件,因为分型面选择的不同,使结构的复杂程度有很大不同,合理地选择,即可简化模具结构。
(2) 怎样选择分型面型腔与模具的关系基本上可分三类:型腔完全处于动模中;型腔完全处于定模中;型腔分别处于动、定模中。
由于塑件的形状繁多,分型面选择的变化也很多,为了使大家对分型面的选择有个基本了解,下面介绍一些典型分型面的选择。
1)长型构件的分型,如图1所示。
若塑件的长度较长,如管形、柱形、杆形塑件,如把型腔放在一块模板中,会使脱模斜度过大(图a),若把型腔分别安排在动、定模中(图b),可减小脱模斜度,使塑件两端的尺寸差异不致过大。
图1- 长型构件的分型a)脱模斜度过大的分型 b)减小脱模斜度的分型2)将塑件留在动模侧的分型,如图2所示。
将塑件留在动模侧,可易于设置和制造结构简单的脱模机构。
因此,要尽量将塑件留在动模侧。
如对盖形塑件,分型面按图a的选取较为合理;如对带嵌件塑件,因嵌件不会收縮而包紧型芯,分型面可按图b选取;若塑件的型芯对称分布,应按图。
分型,迫使塑件留在动模上;若是带有侧孔的塑件,应按图d分型,避免定模抽芯。
图2- 将塑件留在动模侧的分型a)盖形塑件 b)带嵌件塑件 c)型芯对称塑件 d)有侧孔塑件3)保证塑件外观质量的分型,如图3所示。
塑件的外观质量是需要保证的,在选择分型面时认真考虑,如在平滑的表面或圆弧曲面上应尽量不设置分型面.图a是保持曲面光滑的分型,图b是可减少飞边的分型,图c是可减少溢料的分型。
图3- 保证塑件外观质量的分型a)使曲面光滑的分型 b)减少飞边的分型 c)减少溢料的分型4)有利于排气的分型,如图4所示。
模具设计习题与答案

模具设计习题与答案模具设计习题与答案模具是用来成型物品的工具,这种工具由各种零件构成,不同的模具由不同的零件构成。
下面是店铺整理的模具设计习题与答案,欢迎大家参考。
填空1. 分型面的形状有平面、斜面、阶梯面、曲面。
2. 分型面选择时为便于侧分型和抽芯,若塑件有侧孔或侧凹时,宜将侧型芯设置在垂直开模方向上,除液压抽芯机构外,一般应将抽芯或分型距较大的放在开模方向上。
3. 为了保证塑件质量,分型面选择时,对有同轴度要求的塑件,将有同轴度要求的部分设在同一模板内。
4. 为了便于排气,一般选择分型面与熔体流动的末端相重合。
5. 为了便于塑件的脱模,在一般情况下,使塑件在开模时留在动模或下模上。
6. 注射模分流道设计时,从传热面积考虑,热固性塑料宜用梯形截面和半圆形截面分流道;热塑性塑料宜用圆形分流道。
从压力损失考虑,圆形截面分流道最好:从加工方便考虑用梯形、U形或矩形分流道。
7. 在多型腔模具中,型腔和分流道的排列有平衡式和非平衡式两种。
8. 当型腔数较多,爱模具尺寸限制时,通常采用非平衡布置。
由于各分流道长度不同,可采用将浇口设计成不同的截面尺寸来实现均衡进料,这种方法需经多次试模和整修才能实现。
9. 浇口的类型可分点浇口、侧浇口、直接浇口、中心浇口、潜伏式浇口、护耳浇口六类。
10. 浇口截面形状常见的有矩形和圆形。
一般浇口截面积与分流道截面之比为3%~9%,浇口表面粗糙度值不低于为0.4um。
设计时浇口可先选取偏小尺寸,通过试模逐步增大。
11. 注射模的排气方式有开设排气槽排气和利用模具分型面可模具零件的配合间隙自然排气。
排气槽通常开设在型腔最后被填充的部位。
最好开在分型面上,并在凹模一侧,这样即使在排气槽内产生飞边,也容易随塑件脱出。
12. 排气是塑件成型的需要,引气是塑件脱模的需要。
13. 常见的引气方式有镶拼式侧隙引气和气阀式引气两种。
判断1. 侧浇口包括扇形浇口和薄片式浇口,扇形浇口常用来成型宽度较大薄片状塑件;薄片式浇口常用来成型大面积薄板塑件(√)2. 成型零件的磨损是因为塑件与成型零件在脱模过程中的相对摩擦及熔体冲模过程中的冲刷。
《塑料注塑模结构设计》7成型零部件设计7
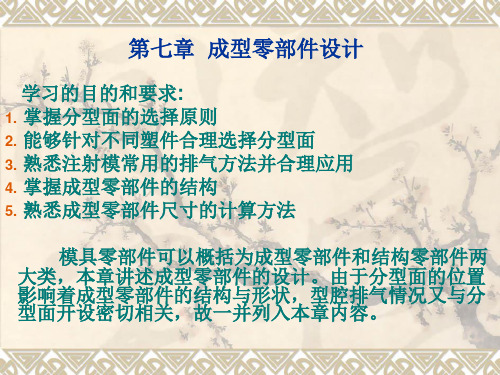
5 瓣合式凹模(镶拼式凹模) 镶拼式凹模)
组成凹模的每一个镶块都是活动的, 组成凹模的每一个镶块都是活动的,它们被模套或其他锁合装置 箍合在一起 适用: 适用:有侧凹或侧孔的制品 当瓣合模块数量等于2时 可将他们组成的凹模成为哈夫凹模。 当瓣合模块数量等于 时,可将他们组成的凹模成为哈夫凹模。
瓣合式凹模结构示意图
二 设计要点
排气槽(或孔 位置和大小的选定 主要依靠经验, 排气槽 或孔)位置和大小的选定,主要依靠经验,经过试模 或孔 位置和大小的选定, 后再修改或增加。 后再修改或增加。 基本的设计要点可归纳如下: 基本的设计要点可归纳如下: 1.排气要保证迅速、完全,排气速度要与充模速度相适应; .排气要保证迅速、完全,排气速度要与充模速度相适应; 2.排气槽(孔)尽量设在塑件较厚的成型部位 2.排气槽(孔)尽量设在塑件较厚的成型部位; 尽量设在塑件较厚的成型部位; 3.排气槽应尽量设在分型面上,但排气槽溢料产生的毛边应不 .排气槽应尽量设在分型面上, 妨碍塑件脱模; 妨碍塑件脱模; 4.排气槽应尽量设在料流的终点,如流道、冷料井的尽端; .排气槽应尽量设在料流的终点,如流道、冷料井的尽端; 5.为了模具制造和清模的方便,排气槽应尽量设在凹模的一面; .为了模具制造和清模的方便,排气槽应尽量设在凹模的一面; 6.排气槽排气方向不应朝向操作面,防止注射时漏料烫伤人; .排气槽排气方向不应朝向操作面,防止注射时漏料烫伤人; 7.排气槽 孔)不应有死角,防止积存冷料; 不应有死角, .排气槽(孔 不应有死角 防止积存冷料;
一 凹模结构设计
凹模是成型塑件外表面的成型零件。 凹模是成型塑件外表面的成型零件。 凹模的基本结构:整体式、整体嵌入式和组合式、镶拼式。 凹模的基本结构:整体式、整体嵌入式和组合式、镶拼式。
常州注塑模具分型面的设计规范

转角处用扫描面或网格面平滑接顺尽量减少台阶和尖角的出现以便提高分型面加工工艺性。
*曲面比较陡时可在模肉四个角位做原身管位定位,合模时起定位和防滑作用。
<五>、分型面中枕位的设计:
枕位不易过长,会增加加工时间和FIT模难度。
枕位设计原则:
<一>、枕位延伸段长度:大模20~30mm,小模8~10mm即可。(见图五)
主要分型面与开模方向不垂直时,分型面沿斜面延伸一段后在分型面两端做平位,以利于加工定位及Fit模。(见图二)
延伸段长度:大模L=20~30mm,小模L=10mm即可。
*斜面比较陡时可在模肉四个角位做原身管位定位(也可考虑用圆型分型面管位块),合模时起定位和防滑作用。
<三>、主要分型面为单曲面的情况:
二、分型面在不同情况下的设计要求:
<一>、主要分型面为平面的情况:
主要分型面与开模方向垂直时,分型面可直接拉伸而成。(见图一)
*对于这种分型面用UG自动分模时常会在一些转角位有一些微小的起伏(高度方向几个丝的变化),对制作Fit模有一定的影响,应注意用平面替换,以利于磨床磨出。
<二>、主要分型面为斜面的情况:
在注塑模具的设计中,分型面的设计很关键,其设计的结果将直接影响到模具结构、模具加工难度和模具设计制造费用;由于分型面的设计对于同一产品具有不同的结果,所以分型面的设计确定有一定的难度。
一、分型面的设计原则:
<一>、保证产品的外观质量和精度。
<二>、保证模具零件成型时的刚性。
<三>、分型面应该有利于侧向抽芯。
<四>、分型面应该有利于塑件脱模。
分型面
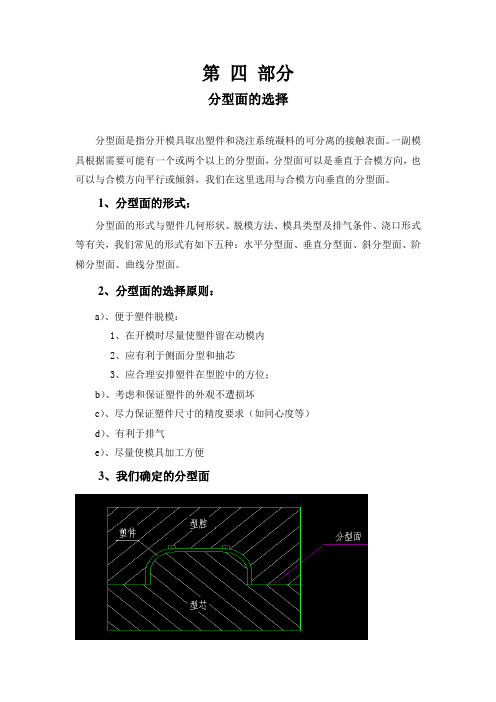
第四部分分型面的选择分型面是指分开模具取出塑件和浇注系统凝料的可分离的接触表面。
一副模具根据需要可能有一个或两个以上的分型面,分型面可以是垂直于合模方向,也可以与合模方向平行或倾斜,我们在这里选用与合模方向垂直的分型面。
1、分型面的形式:分型面的形式与塑件几何形状、脱模方法、模具类型及排气条件、浇口形式等有关,我们常见的形式有如下五种:水平分型面、垂直分型面、斜分型面、阶梯分型面、曲线分型面。
2、分型面的选择原则:a)、便于塑件脱模:1、在开模时尽量使塑件留在动模内2、应有利于侧面分型和抽芯3、应合理安排塑件在型腔中的方位;b)、考虑和保证塑件的外观不遭损坏c)、尽力保证塑件尺寸的精度要求(如同心度等)d)、有利于排气e)、尽量使模具加工方便3、我们确定的分型面经过仔细的审核和逐步的推敲,我们最终把分型面确定在了这里因为在此,它不会影响到制件表面的质量,也不会影响到塑件的脱模,而且成型零件便于加工,可以节约制造成本。
浇注系统的设计1、浇注系统的组成所谓注塑模的浇注系统是指从主流道的始端到型腔之间的熔体流动通道。
其作用是使塑件熔体平稳而有序地充填到型腔中,以获得组织致密、外形轮廓清晰的塑件。
因此,浇注系统十分重要。
而浇注系统一般可分为普通浇注系统和无流道浇注系统两类。
我们在这里选用普通浇注系统,它一般是由主流道、分流道、浇口和冷料穴四部分组成,如图四所示:图四2、浇注系统各部分的设计A、主流道设计:主流道是连接注射机喷嘴与分流道的一段通道,通常和注射机喷嘴在同一轴线上,断面为圆形,带有一定的锥度,其主要设计点为:⑴主流道圆锥角α=2o~6o,对流动性差的塑件可取3 o~8o,内壁粗糙度为Ra0.63μm 。
⑵主流道大端呈圆角过渡,半径r=1~3mm ,以减小料流转向过渡时的阻力。
⑶在模具结构允许的情况下,主流道应尽可能短,一般小于60mm ,过长则会影响熔体的顺利充型。
⑷对小型模具可将主流道衬套与定位圈设计成整体式。
注塑模具之分型面的选择(doc 7页)
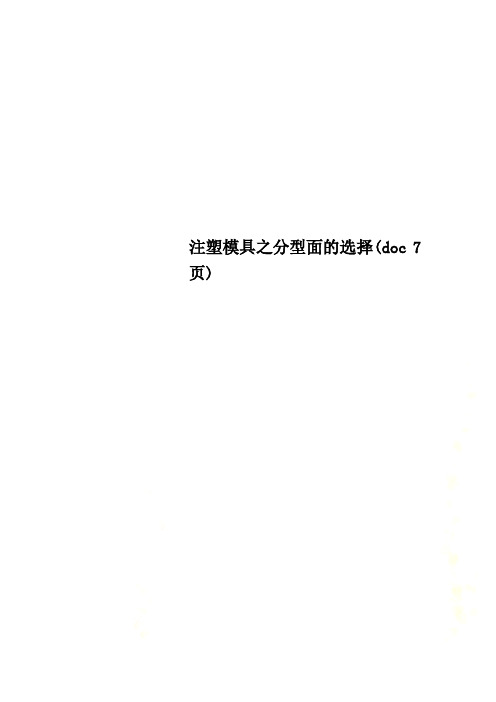
注塑模具之分型面的选择(doc 7页)分型面的选择分型面为动模与定模的分界面,是取出塑件或浇注系统凝料的面.它的合理选择是塑件能完好成型的条件,不仅关系到塑件的脱模,而且涉及摸具结构与制造成本. 合理的分型面不但能满足制品各方面的性能要求 ,而且使模具结构简单,成本亦会令人满意.选择分型面时有下面一些原则可以遵循:.分型面应选择在塑件的最大截面处(圖二),否则给脱模和加工带来困难(圖一).此点可说是选择的首要原则.图一(無法脫模)图二(順利脫模).尽可能地将塑件留在公模侧,因在公模侧设置脱模机构简便易行..在安排制件在型腔中方位时,尽量避免侧向分型或抽芯以利于简化模具结构.结合以上原则还要综合考虑塑件的尺寸精度、外观质量、使用要求及是否有利于浇注系统特别是浇口的合理安排, 是否有利于排气。
所设计的模具的塑件电话机的上面板(图示),由图可以看出,不能将侧面作为分型面,因为那将导致不合理的模具高度和模腔深度。
对于这一模具,分型面没有太多的选择。
它的侧边是有斜度的,下端面为最大截面,可考虑将整个外观面作为分型面。
电话机的上面板外观表面质量的要求很高,顶杆不能在外观面侧顶出,否则顶出痕迹会影响表面质量,所以外观面最好在母模侧成产品外观图型。
在结构方面,(如图所示)内侧面有很多小直径的BOSS,这些结构宜用顶管(套筒顶针)成型且便于脱模。
那么,这一部分应在公模侧。
如此布置,党制品冷却时,会因收缩作用而包覆在公模仁上,有利于制品滞留在公模一側。
根据以上分析,分型面的选择为整个外观面,内部结构在公模侧成型,外观面成型与母模侧(与图二相似)。
这样易于脱模,使模具结构相对简化,且分型面有一靠破处可设置浇口亦利于浇注系统的安内部结构图靠破 BOSS排。
综上,此选择可行。
型腔数目的确定注射模可设计成一模一腔也可设计成一模多腔。
其数目的确定要从以下几个方面考虑:.注塑产品的尺寸及结构的复杂性.塑件的尺寸精度—型腔越多,精度也相对降低。
- 1、下载文档前请自行甄别文档内容的完整性,平台不提供额外的编辑、内容补充、找答案等附加服务。
- 2、"仅部分预览"的文档,不可在线预览部分如存在完整性等问题,可反馈申请退款(可完整预览的文档不适用该条件!)。
- 3、如文档侵犯您的权益,请联系客服反馈,我们会尽快为您处理(人工客服工作时间:9:00-18:30)。
分型面的选择分型面为动模与定模的分界面,是取出塑件或浇注系统凝料的面.它的合理选择是塑件能完好成型的条件,不仅关系到塑件的脱模,而且涉及摸具结构与制造成本. 合理的分型面不但能满足制品各方面的性能要求 ,而且使模具结构简单,成本亦会令人满意.选择分型面时有下面一些原则可以遵循:.分型面应选择在塑件的最大截面处(圖二),否则给脱模和加工带来困难(圖一).此点可说是选择的首要原则.图一(無法脫模)图二(順利脫模).尽可能地将塑件留在公模侧,因在公模侧设置脱模机构简便易行..在安排制件在型腔中方位时,尽量避免侧向分型或抽芯以利于简化模具结构.结合以上原则还要综合考虑塑件的尺寸精度、外观质量、使用要求及是否有利于浇注系统特别是浇口的合理安排, 是否有利于排气。
所设计的模具的塑件电话机的上面板(图示),由图可以看出,不能将侧面作为分型面,因为那将导致不合理的模具高度和模腔深度。
对于这一模具,分型面没有太多的选择。
它的侧边是有斜度的,下端面为最大截面,可考虑将整个外观面作为分型面。
电话机的上面板外观表面质量的要求很高,顶杆不能在外观面侧顶出,否则顶出痕迹会影响表面质量,所以外观面最好在母模侧成产品外观图型。
在结构方面,(如图所示)内侧面有很多小直径的BOSS,这些结构宜用顶管(套筒顶针)成型且便于脱模。
那么,这一部分应在公模侧。
如此布置,党制品冷却时,会因收缩作用而包覆在公模仁上,有利于制品滞留在公模一側。
根据以上分析,分型面的选择为整个外观面,内部结构在公模侧成型,外观面成型与母模侧(与图二相似)。
这样易于脱模,使模具结构相对简化,且分型面有一靠破处可设置浇口亦利于浇注系统的安内部结构图靠破 BOSS排。
综上,此选择可行。
型腔数目的确定注射模可设计成一模一腔也可设计成一模多腔。
其数目的确定要从以下几个方面考虑:.注塑产品的尺寸及结构的复杂性.塑件的尺寸精度—型腔越多,精度也相对降低。
这不仅由于型腔加工精度产差,也由于熔体在模具内流动不均所致。
.制造难度—多腔模比单腔模的难度大。
.制造成本—多腔模高于单腔模,但不是简单的倍数关系。
从塑单件成本中所占的费用比例来看比单腔模低。
.注塑成型的生产效益。
从表面上看,多腔模比单腔模高的多,单多腔模所使用的注射极大,每一注射循环期长而维持费用高。
根据以上几方面,一般小尺寸及结构简单的模具适合一模多腔。
针对本次所设计的模具,其塑件的外型尺寸为271×217×40(mm)为中型且结构复杂,我选择一模一腔。
注射機的選擇浇注系统。
浇注系统指塑料熔体从注射机喷嘴喷出来后达到模腔之前在模具中所流经的信道,其作用是将熔体从喷嘴平稳快速地引进模腔并在熔体充模和固化定型过程中将注射压力和保压压力充分传递到模腔各部它的设计合理与否直接对制品成型起到决定作用,设计浇系统,应从以下几个方面考虑:①保证塑料熔体流动平稳;②流程尽量短,尽量平直,以减小注射压力和熔体热量的损失,并缩短充模时间;③防止冲击型芯和崁件;④防止制品变形翘曲,减轻浇口附近残余应力集中现象;⑤应与塑料品种相适应;尽量减少塑料消耗,尽量设置平衡七、側面分型與抽芯機構的設計当塑件上具有於開模方向不同的凸起、凹槽和孔時,模具必須有側向分型或抽芯機構。
側抽機構必須在塑件脫模之前完成抽芯動作,還必須在核模過程中讓機構負位。
我所設計的模具有三處需要設置側抽機構。
側抽機構的種類很多,一般分為機動、液動(氣動)以及手動等三大類型。
機動式分型與抽芯機構利用注射機的開模運動,並對其方向進行變換後,可將模具側向分型或把側向型芯從製品中抽出。
這類機構雖然結構比較複雜,但操作方便,生產效率高,生產中應用最多。
液動(氣動)以液壓力或壓縮空氣為動力,適於抽拔側向長型芯,其抽拔力大、抽拔距長,多用於管狀結構抽芯,但液動或氣動裝置成本較高。
鴻準公司大多采用機動式。
我所設計的模具結構中均采用機動式側抽機構。
下面分別介紹。
(一)插破側抽機構此插破處附近有三個小型的BOSS ,由於他們所在位置的限制,不能在公模側設置斜銷。
這種情況適於采用側抽芯機構,而型芯在母模側,在公母模分模之前必須將其抽出,否則將破壞型芯之上的成品部分,這一點公模滑塊是辦不到的。
因為三板模在脫料板和母模板之間要進行第一次分模,可利用這一相對運動將側芯型抽出,我考慮用母模滑塊來實現。
將驅動桿固圖7.1.1定在上固定板上,這樣在脫料板與母模板分離時使滑塊於驅動桿發生相對運動,將側芯抽出。
開始考慮采用較常用的斜撐銷作為驅動桿,但脫料板與母模板分模行程較長且脫料板也有8mm的行程,所設置的驅動軋桿在完成抽芯任務後還要不妨碍分模的繼續進行,與斜撐銷相干涉的模板部分必須逃空(如圖7.1.2示),這樣不僅破壞了模板的強度,而且是斜銷處在較差的受力狀態,另外,由於還必須設置楔緊塊以防止注射是滑塊因受型腔內熔體壓力發生位移及幫圖7.1.2 圖7.1.3 助滑塊負位,在原設定的模板寬度下難以設置,所以斜撐銷不可取。
改為較適用於這種情況的撥桿作為驅動桿,其形狀如圖 7.1.3 所示。
那麼,此側抽機構由撥桿、滑塊、壓板、固定裝置及定位裝置組成。
1.撥桿的設計撥桿的抽拔距S側向型芯從成型位置到不妨碍塑件頂出的脫模位置的距離為抽拔距。
為安全起見,抽拔距應比側孔或側凹的深度大1.5~3mm。
此處側孔的深度為5.75 mm,所以抽拔距S=5.75+(1.5~3)=7.25~8.75 mm撥桿的傾角α撥桿與開模方向的傾角α是決定撥桿側抽機構工作效率的重要參數,它的大小對撥桿有效工作長度、抽拔距及撥桿的受力情況有決定性的影響。
由圖7.1.4 可以看出L=S/sinαH=S*ctgα其中L—撥桿有效工作長度圖7.1.4H—與L對應的有效抽拔高度從上可以得出,α值越大,L、H值越小,有利於減小注射模的尺寸。
α角的大小不僅影響L、H,還與抽芯時撥桿所受的彎曲力、脫模力有關(如圖7.1.5 )F w=F t/cosαF k=Ft*tgα其中F w—撥桿所受的彎曲力F t—所需的脫模力F k—所需的開模力從以上公式可以看出,α值增大,F w、F k值都隨之增大,對撥桿和塑模的強度與剛度不利。
圖7.1.5 由於注射機可提供的開模力都比較大,所以綜合考慮,一般為了減小撥桿的受力取α=10°~20°,為了使撥桿處於良好的受力狀態α最高不超過15°。
此處因抽拔距為7.25~8.75 mm,初取α為12°。
根據以上分析,可知撥桿的尺寸由抽拔距S、傾角α及有效工作長度L決定。
若初選S=8 mm,因撥桿與滑塊之間有0.5 mm的間隙,所以要取S=8.5mm,由公式H=S*ctgα=8*ctg12°=39.989mm 取H=40 mmL=H/cos12°=40/cos12°=40.89 mm???初定撥桿的截面尺寸為24×18撥桿的固定因注射過程中注射壓力很大,必須使撥桿牢固定位,否則會因撥桿的位移甚至變形導致製品的不合格,所以撥桿與和滑塊相接觸的兩塊耐模板之間為緊配合。
這樣使撥桿處與良好的受力狀態也使其更好的定位。
為方便裝配,在接觸部位撥桿有2°~3°的斜角,此斜角也起到合模複位時的導角作用。
另外為減小摩擦使運動過程順暢,在脫料板和母模板上均逃料。
而且,為減小應力集中在撥桿的有效抽拔的根部須倒圓角。
2.滑塊和導滑槽滑塊的設計滑塊是側抽芯機構中重要的零部件,注射成型和側抽芯的可靠性都需要它的運動精度保證。
它上面裝有側向型芯或成型鑲板,它的結構形狀根據具體製品模具結構設計,可以與型芯作成一個整體,也可采用組合裝配結構。
整體式在型芯較小、形狀簡單的情況下比較適用,此處型芯的截面為13.66mm×13.16mm,且較長,所以我采用有加工、修理方便等優點的組合式滑塊。
組合式結構把型芯與滑塊分開加工,然後裝配在一起,采用此結構還可以節省優質鋼材(型芯用鋼比滑塊用鋼要求多)。
此處設計的滑塊由滑塊座和側向型芯組成。
設計過程重要注意滑塊的整體高度H不能大於導滑長度L,否則在側抽過程中會產生過大的傾側力距,使導滑面過早磨損。
另外,為避免沖擊在滑塊座與撥桿接觸的端部倒圓角R=2mm。
此處及撥桿上的圓角影向了抽拔距,要對實際的抽拔距進行較核。
如圖7.1.6示,實際抽拔距為7.52mm ,在7.25~8.75 mm之間,符合要求。
圖7.1.6導滑槽的設計側向抽芯過程中,滑塊必須在滑槽內運動,並要求運動平穩且有一定的精度。
滑槽有幾種常見的形式,我選擇圖示的這一種,由兩塊壓板組成,此種形式其導滑部分易磨削且精度易保證,另外裝配也比較方便。
圖7.1.7 定位裝置為保證合模時滑塊與撥桿之間能夠順利復位,須采用滑塊定位裝置以限定滑塊的滑動位置。
采用設置一定位銷(M6的螺釘)使其定位,如圖7.1.6所示,在滑塊上端部開一槽,距離定位銷為7.52 mm,其具體尺寸見零件圖H011S003。
???彈簧的設置抽芯力的計算由於塑膠在模具冷卻後,會產生收縮現象,對模仁及型芯產生包緊力,從而產抽芯的阻力。
根據文獻一,可如此計算F t=A×F(μcosβ–sinβ)(N)式中F t—抽芯力—單位面積包緊力,一般可取7.85~11.77MPAFA—型芯被包緊部分的表面積μ—塑料對鋼的摩擦系數,一般取0.2左右β—脫模斜度.此處A=62.98+62.98+78.5+20.58=225.04m㎡, F取11.77 MPA得 F t=225.04×11.77×0.2 (由於β較小,故cosβ=1,sinβ=0)=529.744N撥桿的截面尺寸校核撥桿在與滑塊相對運動的過程中,由於包緊力所產生的抽芯阻力使得撥感受到跟達德彎曲力作用,有必要對其強度進行校核。
計算如下F w= F t/cosα=529.744/cos12°=541.58NM= F w*L/2=541.58×20.445=11072.6NmmW=bh /6=182×24/6=1296mmM/W=11072.6/1296=8.54N/mm ≦[σ]=13.7KN/cm其中M—撥桿承受最大彎距W—抗彎截面係數[σ]—許用彎曲應力(對碳鋼可取13.7KN/cm )從以上結果可以看出,撥桿的將度足夠。
(二) 斜銷的設計在製品上圖示的位置有一深度僅為1.21mm的卡勾,這一結構能夠成型並順利脫模必須采用側向成型或抽芯的裝置。
從卡勾所在位置可以看出,若仍采用滑塊進行側抽芯,由於卡勾的下面有成品部分無法設置滑塊,那麼側芯必須伸出很長,設計與加工都很麻煩。
像這樣的結構較適合用斜銷(成型斜頂桿)來成型。
斜銷比滑塊所占的體積小,有利於減小模具的體積。