冷镦成型工艺处理设计,螺栓
冷镦成型工艺

冷镦成型工艺 Document number:PBGCG-0857-BTDO-0089-PTT1998紧固件冷镦成型工艺紧固件成型工艺中,冷镦(挤)技术是一种主要加工工艺。
冷镦(挤)属于金属压力加工范畴。
在生产中,在常温状态下,对金属施加外力,使金属在预定的模具内成形,这种方法通常叫冷镦。
实际上,任何紧固件的成形,不单是冷镦一种变形方式能实现的,它在冷镦过程中,除了镦粗变形外,还伴随有正、反挤压、复合挤压、冲切、辗压等多种变形方式。
因此,生产中对冷镦的叫法,只是一种习惯性叫法,更确切地说,应该叫做冷镦(挤)。
冷镦(挤)的优点很多,它适用于紧固件的大批量生产。
它的主要优点概括为以下几个方面:a.钢材利用率高。
冷镦(挤)是一种少、无切削加工方法,如加工杆类的六角头螺栓、圆柱头内六角螺钉,采用切削加工方法,钢材利用率仅在25%~35%,而用冷镦(挤)方法,它的利用率可高达85%~95%,仅是料头、料尾及切六角头边的一些工艺消耗。
b.生产率高。
与通用的切削加工相比,冷镦(挤)成型效率要高出几十倍以上。
c.机械性能好。
冷镦(挤)方法加工的零件,由于金属纤维未被切断,因此强度要比切削加工的优越得多。
d.适于自动化生产。
适宜冷镦(挤)方法生产的紧固件(也含一部分异形件),基本属于对称性零件,适合采用高速自动冷镦机生产,也是大批量生产的主要方法。
总之,冷镦(挤)方法加工紧固件、异形件是一种综合经济效益相当高的加工方法,是紧固件行业中普遍采用的加工方法,也是一种在国内、外广为利用、很有发展的先进加工方法。
因此,如何充分利用、提高金属的塑性、掌握金属塑性变形的机理、研制出科学合理的紧固件冷镦(挤)加工工艺,是本章的目的和宗旨所在。
1 金属变形的基本概念1.1变形变形是指金属受力(外力、内力)时,在保持自己完整性的条件下,组成本身的细小微粒的相对位移的总和。
1.1.1 变形的种类a.弹性变形金属受外力作用发生了变形,当外力去掉后,恢复原来形状和尺寸的能力,这种变形称为弹性变形。
螺栓冷镦加工工艺及检测

0.75
2.8
5.6
0.8
5.6
11.2
0.75
三. 表 面 粗 糙 度
1.
符号
— — —
2.
用任何方法获得的表面。 用去除材料的方法获得的表面。 用不去除材料的方法获得的表面。
参数与其数值系列 参数: a)轮廓算术平均偏差 Y
Ra
X
L
定义:在取样长度 L 内轮廓偏距绝对值得算术平均值。
普通螺纹主坯直径 6 10 1 1.5 螺坯直径 d0 max do min d0 max do min 5.329 5.272 8.995 8.939 5.344 5.312 9.016 8.986 5.303 5.246 8.963 8.907 5.269 5.212 8.928 8.872 5.289 5.232 8.950 8
a)
二轮 a) b)
三轮
行呈式滚丝机
滚压外螺纹精度高可达 1.6mm 以上 一台机床上能加工多种规格的螺纹,如:M2~M42,还能加工锥管螺纹,梯形螺纹,螺杆 等。 3) 毛坯直径尺寸的确定
do=
tan(α/2) 3P
[3d2
’
max(d
´²
’ ² ´³ ’³ ’² ’² min-d 1 min)-2(d min-d1 min)]+1/2(d min+d1 min)
用于计算应 力的偏差
-108 -108 -130 -108 -108 -164 -146 -130 -108 -164 -130 -108 — — -115 -115 -140 -115 -115 -176 -153 -140 -115 -176 -140 -115 -140 -140 -108 -108 -130 -108 -108 -164 -146 -130 -108 -164 -130 -108 — —
冷镦成型工艺
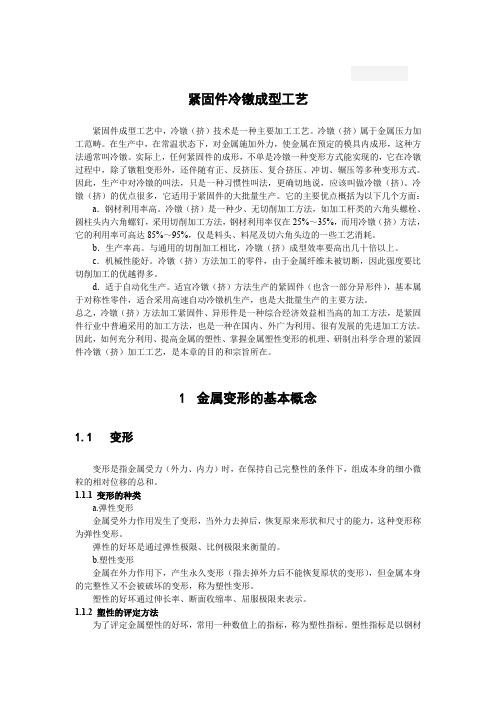
紧固件冷镦成型工艺紧固件成型工艺中,冷镦(挤)技术是一种主要加工工艺。
冷镦(挤)属于金属压力加工范畴。
在生产中,在常温状态下,对金属施加外力,使金属在预定的模具内成形,这种方法通常叫冷镦。
实际上,任何紧固件的成形,不单是冷镦一种变形方式能实现的,它在冷镦过程中,除了镦粗变形外,还伴随有正、反挤压、复合挤压、冲切、辗压等多种变形方式。
因此,生产中对冷镦的叫法,只是一种习惯性叫法,更确切地说,应该叫做冷镦(挤)。
冷镦(挤)的优点很多,它适用于紧固件的大批量生产。
它的主要优点概括为以下几个方面:a.钢材利用率高。
冷镦(挤)是一种少、无切削加工方法,如加工杆类的六角头螺栓、圆柱头内六角螺钉,采用切削加工方法,钢材利用率仅在25%~35%,而用冷镦(挤)方法,它的利用率可高达85%~95%,仅是料头、料尾及切六角头边的一些工艺消耗。
b.生产率高。
与通用的切削加工相比,冷镦(挤)成型效率要高出几十倍以上。
c.机械性能好。
冷镦(挤)方法加工的零件,由于金属纤维未被切断,因此强度要比切削加工的优越得多。
d.适于自动化生产。
适宜冷镦(挤)方法生产的紧固件(也含一部分异形件),基本属于对称性零件,适合采用高速自动冷镦机生产,也是大批量生产的主要方法。
总之,冷镦(挤)方法加工紧固件、异形件是一种综合经济效益相当高的加工方法,是紧固件行业中普遍采用的加工方法,也是一种在国内、外广为利用、很有发展的先进加工方法。
因此,如何充分利用、提高金属的塑性、掌握金属塑性变形的机理、研制出科学合理的紧固件冷镦(挤)加工工艺,是本章的目的和宗旨所在。
1 金属变形的基本概念1.1变形变形是指金属受力(外力、内力)时,在保持自己完整性的条件下,组成本身的细小微粒的相对位移的总和。
1.1.1 变形的种类a.弹性变形金属受外力作用发生了变形,当外力去掉后,恢复原来形状和尺寸的能力,这种变形称为弹性变形。
弹性的好坏是通过弹性极限、比例极限来衡量的。
冷镦锻工艺与模具设计

以GB5786-M8六角头螺栓为例来说明。
..冷镦锻工艺是一种少无切削金属压力加工工艺。
它是一种利用金属在外力作用下所产生的塑性变形,并借助于模具,使金属体积作重新分布及转移,从而形成所需要的零件或毛坯的加工方法。
冷镦锻工艺的特点:1.冷镦然是在常温条件进行的.冷镦锻可使金属零件的机械性能得到改善.2.冷镦锻工艺可以提高材料利率。
它是以塑性变形为基础的压力加工方法,可实现少切削或者无切削加工。
一般材料利用率都在85%以上,最高可达99%以上.3.可提高生产效率.金属产品变形的时间和过程都比较短,特别是在多工位成形机上加工零件,可大大提高生产率.4.冷镦锻工艺能提高产品表面粗糙度、保证产品精度。
二、冷镦锻工艺对原材料的要求1.原材料的化学成份及机械性能应符合相关标准.2.原材料必须进行球化退火处理,其材料金相组织为球状珠光体4—6级。
3.原材料的硬度,为了尽可能减少材料的开裂倾向,提高模具使用寿命还要求冷拔料有尽可能低的硬度,以提高塑性.一般要求原材料的硬度在HB110~170(HRB62—88)。
4.冷拔料的尽寸精度一般应根据产品的具体要求及工艺情况而定,一般来说,对于缩径和强缩尺寸精度要求低一些。
5.冷拔料的表面质量要求有润滑薄膜呈无光泽的暗色,同时表面不得有划痕、折叠、裂纹、拉毛、锈蚀、氧化皮及凹坑麻点等缺陷。
6.要求冷拔料半径方向脱碳层总厚度不超过原材料直径的1-1。
5%(具体情况随各制造厂家的要求而定)。
7.为了保证冷成形时的切断质量,要求冷拔料具有表面较硬,而心部较软的状态。
8.冷拔料应进行冷顶锻试验,同时要求材料对冷作硬化的敏感性越低越好,以减少变形过程中,由于冷作硬化使变形抗力增加.三、紧固件加工工艺简述紧固件主要分两大粪:一类是螺纹类紧固件;另一类是非螺纹类紧固件或联接件。
这里仅针对螺纹类紧固件进行简述。
1. 螺纹类紧固件加工流程一般都是由剪断、冷镦、或者冷挤压、切削、螺纹加工、热处理、表面处理等生产工序组成的.材料改制工艺流程一般为:酸洗→拉丝→退火→磷化皂化→拉丝→(球化磷化)螺纹类紧固件冷加工艺流程订要有以下几种情况:8。
冷镦成型工艺设计
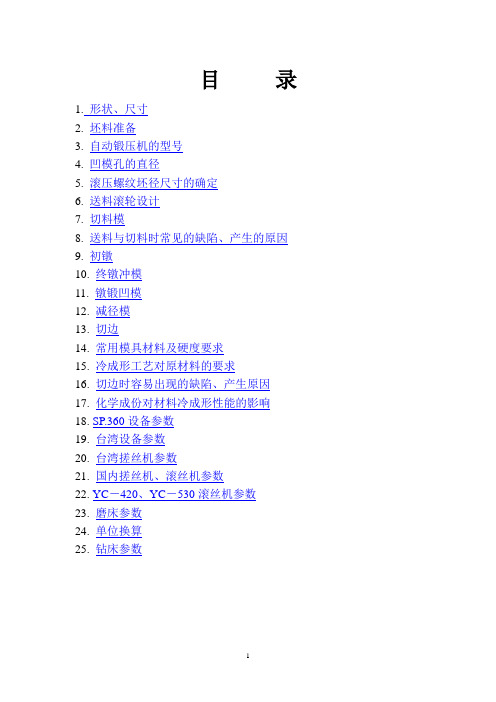
目录1.形状、尺寸2. 坯料准备3. 自动锻压机的型号4. 凹模孔的直径5. 滚压螺纹坯径尺寸的确定6. 送料滚轮设计7. 切料模8. 送料与切料时常见的缺陷、产生的原因9. 初镦10. 终镦冲模11. 镦锻凹模12. 减径模13. 切边14. 常用模具材料及硬度要求15. 冷成形工艺对原材料的要求16. 切边时容易出现的缺陷、产生原因17. 化学成份对材料冷成形性能的影响18. SP.360设备参数19. 台湾设备参数20. 台湾搓丝机参数21. 国内搓丝机、滚丝机参数22. YC-420、YC-530滚丝机参数23. 磨床参数24. 单位换算25. 钻床参数形状、尺寸:1.圆角半径――取直径的1/20~1/5。
冷锻时圆角过大反而难锻造。
2.镦粗头部和法兰部尺寸――头部或法兰部体积V在2D3(D为坯料直径)以下时用单击镦锻机,3.5D3以下时可用双击镦锻机加工,而不会产生纵向弯曲。
如V为4.7D3必须经三道镦粗工序。
这部分的直径D1,(镦粗后直径)对于C<0.2%的碳素钢,不经中间退火能够镦粗到2.5D。
超过上述范围必须中间退火。
侧面尺寸由于难以控制,公差要尽可能放宽。
3.镦粗部分的形状――头部或头下部的高度比直径大时,侧壁上向上和向下设置2°左右的锥度,使材料填充良好。
球形头部顶上允许设计成小平面。
4.挤压件坯料和挤出部分断面积之比A0/A1,即挤压比R,对S10C、BSW1的实心、空心正挤压件,如在5~10以下,对反挤压杯形件,如在1.3~4间,能够一次成形。
自由挤压件的R如在1.25~1.4以下,能经一道工序加工。
杯形件反挤压时的冲头压力,当R约为1.7时最小。
5.挤压件断面变化部分的锥度如图1,但对于变形抗力高的材料,从模具强度上考虑,α(度)要取较大值。
挤压比制件形状1.25 2 4 50棒、管正挤压件反挤压杯形件10~2060~9030~4560~9045~6075~9075~9075~906.反挤压杯形件的侧壁高度――侧壁高度H和冲头直径d的比H/d,对S10C、BSW1如在2~3以下,对更硬的材料如在1~2以下,均可一次成形。
紧固件冷镦成型工艺,一文搞懂!
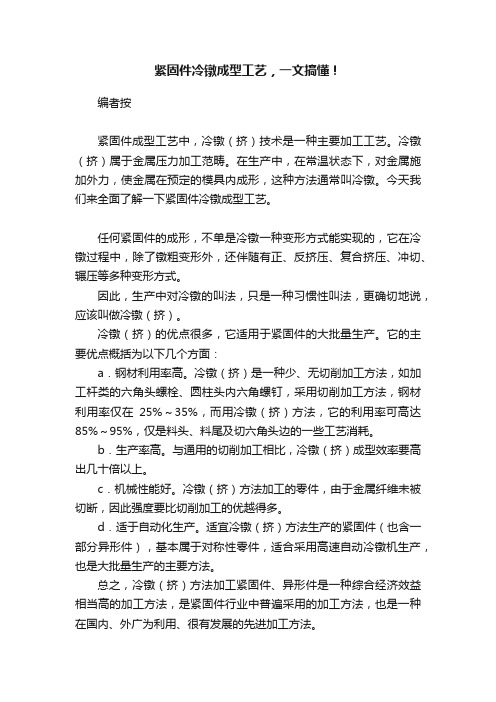
紧固件冷镦成型工艺,一文搞懂!编者按紧固件成型工艺中,冷镦(挤)技术是一种主要加工工艺。
冷镦(挤)属于金属压力加工范畴。
在生产中,在常温状态下,对金属施加外力,使金属在预定的模具内成形,这种方法通常叫冷镦。
今天我们来全面了解一下紧固件冷镦成型工艺。
任何紧固件的成形,不单是冷镦一种变形方式能实现的,它在冷镦过程中,除了镦粗变形外,还伴随有正、反挤压、复合挤压、冲切、辗压等多种变形方式。
因此,生产中对冷镦的叫法,只是一种习惯性叫法,更确切地说,应该叫做冷镦(挤)。
冷镦(挤)的优点很多,它适用于紧固件的大批量生产。
它的主要优点概括为以下几个方面:a.钢材利用率高。
冷镦(挤)是一种少、无切削加工方法,如加工杆类的六角头螺栓、圆柱头内六角螺钉,采用切削加工方法,钢材利用率仅在25%~35%,而用冷镦(挤)方法,它的利用率可高达85%~95%,仅是料头、料尾及切六角头边的一些工艺消耗。
b.生产率高。
与通用的切削加工相比,冷镦(挤)成型效率要高出几十倍以上。
c.机械性能好。
冷镦(挤)方法加工的零件,由于金属纤维未被切断,因此强度要比切削加工的优越得多。
d.适于自动化生产。
适宜冷镦(挤)方法生产的紧固件(也含一部分异形件),基本属于对称性零件,适合采用高速自动冷镦机生产,也是大批量生产的主要方法。
总之,冷镦(挤)方法加工紧固件、异形件是一种综合经济效益相当高的加工方法,是紧固件行业中普遍采用的加工方法,也是一种在国内、外广为利用、很有发展的先进加工方法。
因此,如何充分利用、提高金属的塑性、掌握金属塑性变形的机理、研制出科学合理的紧固件冷镦(挤)加工工艺,是研究的目的和宗旨所在。
一、金属变形的基本概念变形变形是指金属受力(外力、内力)时,在保持自己完整性的条件下,组成本身的细小微粒的相对位移的总和。
1 变形的种类a.弹性变形金属受外力作用发生了变形,当外力去掉后,恢复原来形状和尺寸的能力,这种变形称为弹性变形。
弹性的好坏是通过弹性极限、比例极限来衡量的。
冷镦知识和工艺讲解
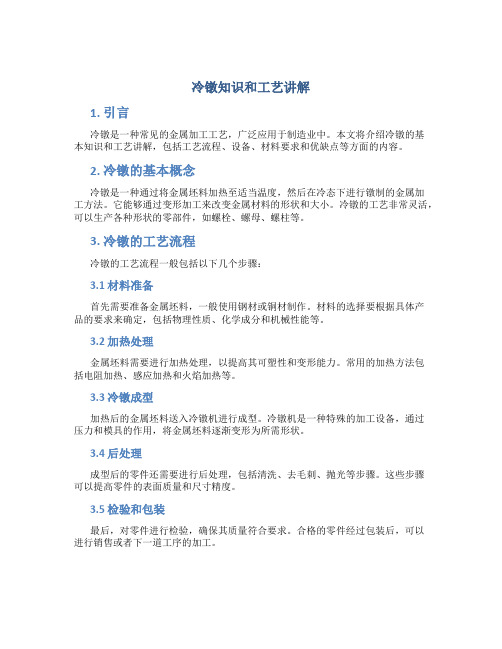
冷镦知识和工艺讲解1. 引言冷镦是一种常见的金属加工工艺,广泛应用于制造业中。
本文将介绍冷镦的基本知识和工艺讲解,包括工艺流程、设备、材料要求和优缺点等方面的内容。
2. 冷镦的基本概念冷镦是一种通过将金属坯料加热至适当温度,然后在冷态下进行镦制的金属加工方法。
它能够通过变形加工来改变金属材料的形状和大小。
冷镦的工艺非常灵活,可以生产各种形状的零部件,如螺栓、螺母、螺柱等。
3. 冷镦的工艺流程冷镦的工艺流程一般包括以下几个步骤:3.1 材料准备首先需要准备金属坯料,一般使用钢材或铜材制作。
材料的选择要根据具体产品的要求来确定,包括物理性质、化学成分和机械性能等。
3.2 加热处理金属坯料需要进行加热处理,以提高其可塑性和变形能力。
常用的加热方法包括电阻加热、感应加热和火焰加热等。
3.3 冷镦成型加热后的金属坯料送入冷镦机进行成型。
冷镦机是一种特殊的加工设备,通过压力和模具的作用,将金属坯料逐渐变形为所需形状。
3.4 后处理成型后的零件还需要进行后处理,包括清洗、去毛刺、抛光等步骤。
这些步骤可以提高零件的表面质量和尺寸精度。
3.5 检验和包装最后,对零件进行检验,确保其质量符合要求。
合格的零件经过包装后,可以进行销售或者下一道工序的加工。
4. 冷镦的设备冷镦机是冷镦过程中最重要的设备,它通常由下列部分组成:•送料装置:用于将金属坯料送入冷镦机,保持均匀的进料速度。
•压力机构:通过压力使金属坯料变形,完成冷镦过程。
•模具:冷镦模具决定了最终产品的形状和尺寸精度。
•冷却装置:用于冷却金属零件,防止变形和表面质量不良。
5. 冷镦材料的要求冷镦的材料要求主要包括以下几个方面:5.1 可镦性金属材料的可镦性是指其在冷态下的变形能力。
优秀的可镦性意味着材料容易变形,而不容易断裂。
一般来说,钢材的可镦性比较好,常用于冷镦加工。
5.2 易切削性金属材料的易切削性是指其在冷镦过程中,容易切断和形成所需形状。
易切削性好的材料在加工过程中能够减少切削力和模具磨损,提高生产效率和产品的质量。
紧固件冷镦工艺详解

冷镦:就是利用金属的塑性,采用冷态力学进行施压或冷拔,达到金属固态变形的目的。
(基本定义)在室温下把棒材或线材的顶部加粗的锻造成形方法。
冷镦主要用於制造螺栓、螺母、铁钉、铆钉和钢球等零件。
锻坯材料可以是铜、铝、碳钢、合金钢、不锈钢和钛合金等,材料利用率可达80~90%。
冷镦多在专用的冷镦机上进行,便於实现连续、多工位、自动化生产。
在冷镦机上能顺序完成切料、镦头、聚积、成形、倒角、搓丝、缩径和切边等工序。
生产效率高,可达300件/分以上,最大冷镦工件的直径为48毫米。
冷镦螺栓工序示意图为冷镦螺栓的典型工序。
多工位螺母自动冷镦机为多工位螺母自动冷镦机。
棒料由送料机构自动送进一定长度,切断机构将其切断成坯料,然后由夹钳传送机构依次送至聚积压形和冲孔工位进行成形。
冷镦是指原材料在常温下进行冲压,热镦是指原材料在经过加温后进行冲压,具体的用途没有特别的要求,一般情况下都要求用冷镦,因为这样的表面光洁度,材料的组织成份会比较紧密些,还有就是较大的工件常采用热镦加工。
锻造头部,也叫热墩,把头部加热烧红,挤压成型;螺丝的六角头是墩出来的吗?绝大多数是墩出来的,因为这样可以节省材料。
根据墩锻机吨位大小和螺栓直径,可以采用冷墩或热墩工艺。
小批量的专用或特殊螺栓的六角头是车削后铣成的。
丝又是怎样制出的?单件小批量可以用板牙套丝、车床挑丝、旋风铣铣制等方法。
大批量生产中常采用搓丝机搓丝、滚丝机滚丝的方法,效率很高。
因为螺栓杆成形方法有冷拔和缩径,所以这种螺栓的没有螺纹的部分直径不一定略小。
采用冷拔时,略小;采用缩径时,可以与螺纹等径或稍大。
螺栓整个是压铸造的吗?如果螺栓材料为铝合金、锌合金、铜合金等低熔点的合金或金属,也可以采用压铸成型的方法。
钢制的不采用压铸制造。
螺栓的六角头的成形不能一概而论,有冷墩的、有热墩的、有镦后直接出成品的,也有镦后再机加工的,也有全部机加工的。
镦制的螺栓头部是有加工痕迹的,在根部有模具的夹具痕迹。
冷镦锻工艺与模具设计

以GB5786-M8六角头螺栓为例来说明。
..冷镦锻工艺是一种少无切削金属压力加工工艺。
它是一种利用金属在外力作用下所产生的塑性变形,并借助于模具,使金属体积作重新分布及转移,从而形成所需要的零件或毛坯的加工方法。
冷镦锻工艺的特点:1.冷镦然是在常温条件进行的.冷镦锻可使金属零件的机械性能得到改善.2.冷镦锻工艺可以提高材料利率。
它是以塑性变形为基础的压力加工方法,可实现少切削或者无切削加工。
一般材料利用率都在85%以上,最高可达99%以上.3.可提高生产效率.金属产品变形的时间和过程都比较短,特别是在多工位成形机上加工零件,可大大提高生产率.4.冷镦锻工艺能提高产品表面粗糙度、保证产品精度。
二、冷镦锻工艺对原材料的要求1.原材料的化学成份及机械性能应符合相关标准.2.原材料必须进行球化退火处理,其材料金相组织为球状珠光体4—6级。
3.原材料的硬度,为了尽可能减少材料的开裂倾向,提高模具使用寿命还要求冷拔料有尽可能低的硬度,以提高塑性.一般要求原材料的硬度在HB110~170(HRB62—88)。
4.冷拔料的尽寸精度一般应根据产品的具体要求及工艺情况而定,一般来说,对于缩径和强缩尺寸精度要求低一些。
5.冷拔料的表面质量要求有润滑薄膜呈无光泽的暗色,同时表面不得有划痕、折叠、裂纹、拉毛、锈蚀、氧化皮及凹坑麻点等缺陷。
6.要求冷拔料半径方向脱碳层总厚度不超过原材料直径的1-1。
5%(具体情况随各制造厂家的要求而定)。
7.为了保证冷成形时的切断质量,要求冷拔料具有表面较硬,而心部较软的状态。
8.冷拔料应进行冷顶锻试验,同时要求材料对冷作硬化的敏感性越低越好,以减少变形过程中,由于冷作硬化使变形抗力增加.三、紧固件加工工艺简述紧固件主要分两大粪:一类是螺纹类紧固件;另一类是非螺纹类紧固件或联接件。
这里仅针对螺纹类紧固件进行简述。
1. 螺纹类紧固件加工流程一般都是由剪断、冷镦、或者冷挤压、切削、螺纹加工、热处理、表面处理等生产工序组成的.材料改制工艺流程一般为:酸洗→拉丝→退火→磷化皂化→拉丝→(球化磷化)螺纹类紧固件冷加工艺流程订要有以下几种情况:8。
螺丝冷镦工艺流程

螺丝冷镦工艺流程
螺丝冷镦工艺流程如下:
1.选择合适的原材料:一般螺丝的原材料是金属丝材,常用的材料包括碳钢、不锈钢等。
2.切割:将选定的原材料根据螺丝的长度要求进行切割。
3.镦头:将切割好的金属丝材的一端加热至高温,然后用压力将其压成预定的形状,形成螺丝的头部。
4.冷镦成型:将加热镦头后的金属丝材放入冷镦机中进行冷镦成型。
冷镦机通过冷挤压的方式,将金属材料逐渐塑性变形成螺纹状。
5.剪断:将冷镦成型后的金属材料切割成螺丝的长度。
6.清洗和去毛刺:清洗螺丝并去除表面的毛刺,确保产品质量。
7.表面处理:根据需要对螺丝进行镀锌、镀镍等表面处理,提高其耐腐蚀性能。
8.检验和包装:对螺丝进行质量检验,包装成成品。
冷镦锻工艺与模具设计

以GB5786-M8六角头螺栓为例来说明...冷镦锻工艺是一种少无切削金属压力加工工艺。
它是一种利用金属在外力作用下所产生的塑性变形,并借助于模具,使金属体积作重新分布及转移,从而形成所需要的零件或毛坯的加工方法。
冷镦锻工艺的特点:1.冷镦然是在常温条件进行的。
冷镦锻可使金属零件的机械性能得到改善。
2.冷镦锻工艺可以提高材料利率。
它是以塑性变形为基础的压力加工方法,可实现少切削或者无切削加工。
一般材料利用率都在85%以上,最高可达99%以上。
3.可提高生产效率。
金属产品变形的时间和过程都比较短,特别是在多工位成形机上加工零件,可大大提高生产率。
4.冷镦锻工艺能提高产品表面粗糙度、保证产品精度。
二、冷镦锻工艺对原材料的要求1.原材料的化学成份及机械性能应符合相关标准。
2.原材料必须进行球化退火处理,其材料金相组织为球状珠光体4-6级。
3.原材料的硬度,为了尽可能减少材料的开裂倾向,提高模具使用寿命还要求冷拔料有尽可能低的硬度,以提高塑性。
一般要求原材料的硬度在HB110~170(HRB62-88)。
4.冷拔料的尽寸精度一般应根据产品的具体要求及工艺情况而定,一般来说,对于缩径和强缩尺寸精度要求低一些。
5.冷拔料的表面质量要求有润滑薄膜呈无光泽的暗色,同时表面不得有划痕、折叠、裂纹、拉毛、锈蚀、氧化皮及凹坑麻点等缺陷。
6.要求冷拔料半径方向脱碳层总厚度不超过原材料直径的1-1.5%(具体情况随各制造厂家的要求而定)。
7.为了保证冷成形时的切断质量,要求冷拔料具有表面较硬,而心部较软的状态。
8.冷拔料应进行冷顶锻试验,同时要求材料对冷作硬化的敏感性越低越好,以减少变形过程中,由于冷作硬化使变形抗力增加。
三、紧固件加工工艺简述紧固件主要分两大粪:一类是螺纹类紧固件;另一类是非螺纹类紧固件或联接件。
这里仅针对螺纹类紧固件进行简述。
1. 螺纹类紧固件加工流程一般都是由剪断、冷镦、或者冷挤压、切削、螺纹加工、热处理、表面处理等生产工序组成的。
冷镦螺栓缩径模具内孔孔型设计
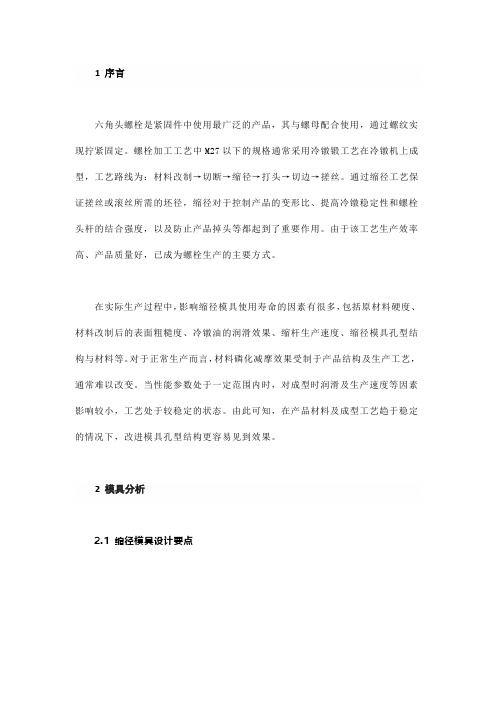
1 序言六角头螺栓是紧固件中使用最广泛的产品,其与螺母配合使用,通过螺纹实现拧紧固定。
螺栓加工工艺中M27以下的规格通常采用冷镦锻工艺在冷镦机上成型,工艺路线为:材料改制→切断→缩径→打头→切边→搓丝。
通过缩径工艺保证搓丝或滚丝所需的坯径,缩径对于控制产品的变形比、提高冷镦稳定性和螺栓头杆的结合强度,以及防止产品掉头等都起到了重要作用。
由于该工艺生产效率高、产品质量好,已成为螺栓生产的主要方式。
在实际生产过程中,影响缩径模具使用寿命的因素有很多,包括原材料硬度、材料改制后的表面粗糙度、冷镦油的润滑效果、缩杆生产速度、缩径模具孔型结构与材料等。
对于正常生产而言,材料磷化减摩效果受制于产品结构及生产工艺,通常难以改变。
当性能参数处于一定范围内时,对成型时润滑及生产速度等因素影响较小,工艺处于较稳定的状态。
由此可知,在产品材料及成型工艺趋于稳定的情况下,改进模具孔型结构更容易见到效果。
2 模具分析2.1 缩径模具设计要点缩径模具采用预应力组合结构,以保证其整体强度;外部模套采用H13碳钢材料,芯部为硬质合金KG5,硬度1250~1340HV模套加热至400℃以上,以过盈配合将模芯压入。
缩径模具孔型结构中最重要的参数是工作带导向角度α和定径带长度L。
工作带导向角度α直接影响缩径力的大小,α过大或过小都会引起缩径力的增加;定径带长度L决定了模具使用寿命的长短,L过长或过短都会降低模具的使用寿命[1]。
定径带后面的孔径与定径带直径之差以0.05~0.07mm为宜,避免工件与模具接触使得摩擦力增加,确保缩径的顺利进行[2]。
2.2 缩径模具孔型结构缩径模具主要结构及参数如图1所示。
工作带是对材料进行挤压缩径的区域,图中α表示工作带导向角度(°);定径带保证缩径后坯料的尺寸精度,d为定径带直径(mm);L为定径带长度(mm)。
图1缩径模具主要结构及参数2.3 缩径变形量ψ缩径变形量为缩径前后线材横截面积的变化,缩径变形程度是缩径工艺设计及计算的重要参数,也是影响缩径模具寿命最重要的因素。
不锈钢螺栓制造工艺

不锈钢螺栓制造工艺一、引言不锈钢螺栓在工业生产中扮演着重要的角色,它们被广泛应用于建筑、机械、航空航天等领域。
不锈钢螺栓具有耐腐蚀、耐高温、强度高等特点,因此备受青睐。
本文将介绍不锈钢螺栓的制造工艺。
二、原材料选择不锈钢螺栓的制造首先要选择合适的原材料。
常见的不锈钢材料有304、316、321等。
根据螺栓的使用环境和要求,选择合适的不锈钢材料非常重要。
三、冷镦成型不锈钢螺栓的制造过程通常从冷镦成型开始。
冷镦成型是指将钢材通过模具加工成所需形状的工艺。
在冷镦成型过程中,将经过预处理的不锈钢原料锤击压制,使其逐渐变形成螺栓的形状。
四、热处理冷镦成型后的不锈钢螺栓需要进行热处理。
热处理是通过加热和冷却的方式改变材料的组织结构和性能。
这一步的目的是增加螺栓的硬度和强度,提高其耐腐蚀性。
五、车削加工经过热处理的不锈钢螺栓需要进行车削加工。
车削是通过旋转工件并使用刀具切削的工艺。
通过车削加工,可以使螺栓的直径、长度和螺纹尺寸达到标准要求。
六、螺纹加工螺纹是不锈钢螺栓的重要组成部分,它能够让螺栓与螺母紧密连接。
螺纹加工是将螺栓表面进行切割或滚动,形成螺纹纹理的过程。
螺纹加工需要精确的控制参数,以确保螺纹质量达到要求。
七、表面处理不锈钢螺栓的表面处理非常重要,可以提高其耐腐蚀性和美观度。
常见的表面处理方法有镀锌、电镀和喷涂等。
镀锌可以在螺栓表面形成一层锌层,提供耐腐蚀的保护。
电镀可以在螺栓表面形成一层金属镀层,提高其外观和耐腐蚀性能。
喷涂是将特殊的涂料喷涂在螺栓表面,提供良好的防腐蚀性能。
八、质量检验制造完成的不锈钢螺栓需要进行质量检验。
质量检验包括外观检查、尺寸检验和性能检验等。
外观检查主要是检查螺栓的表面是否有缺陷和污染物。
尺寸检验包括测量螺栓的直径、长度和螺纹尺寸是否符合标准要求。
性能检验主要是测试螺栓的强度和耐腐蚀性能是否达到要求。
九、包装和运输经过质量检验合格的不锈钢螺栓需要进行包装和运输。
包装通常采用纸箱、木箱或塑料袋等包装材料,以保护螺栓免受损坏。
螺栓工艺流程
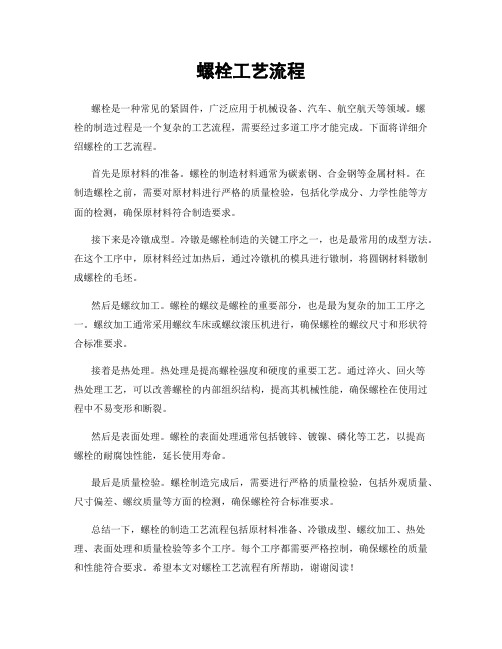
螺栓工艺流程
螺栓是一种常见的紧固件,广泛应用于机械设备、汽车、航空航天等领域。
螺
栓的制造过程是一个复杂的工艺流程,需要经过多道工序才能完成。
下面将详细介绍螺栓的工艺流程。
首先是原材料的准备。
螺栓的制造材料通常为碳素钢、合金钢等金属材料。
在
制造螺栓之前,需要对原材料进行严格的质量检验,包括化学成分、力学性能等方面的检测,确保原材料符合制造要求。
接下来是冷镦成型。
冷镦是螺栓制造的关键工序之一,也是最常用的成型方法。
在这个工序中,原材料经过加热后,通过冷镦机的模具进行镦制,将圆钢材料镦制成螺栓的毛坯。
然后是螺纹加工。
螺栓的螺纹是螺栓的重要部分,也是最为复杂的加工工序之一。
螺纹加工通常采用螺纹车床或螺纹滚压机进行,确保螺栓的螺纹尺寸和形状符合标准要求。
接着是热处理。
热处理是提高螺栓强度和硬度的重要工艺。
通过淬火、回火等
热处理工艺,可以改善螺栓的内部组织结构,提高其机械性能,确保螺栓在使用过程中不易变形和断裂。
然后是表面处理。
螺栓的表面处理通常包括镀锌、镀镍、磷化等工艺,以提高
螺栓的耐腐蚀性能,延长使用寿命。
最后是质量检验。
螺栓制造完成后,需要进行严格的质量检验,包括外观质量、尺寸偏差、螺纹质量等方面的检测,确保螺栓符合标准要求。
总结一下,螺栓的制造工艺流程包括原材料准备、冷镦成型、螺纹加工、热处理、表面处理和质量检验等多个工序。
每个工序都需要严格控制,确保螺栓的质量和性能符合要求。
希望本文对螺栓工艺流程有所帮助,谢谢阅读!。
冷镦锻工艺与模具设计

冷镦锻工艺与模具设计冷镦锻工艺是一种利用冷变形原理,通过冲击力使材料表面产生塑性变形,通过模具来塑造材料形状的工艺。
冷镦锻工艺主要应用于金属制品的生产中,如螺丝、螺母、铆钉等。
本文将重点介绍冷镦锻工艺的基本原理以及模具设计的要点。
1.材料准备:选择合适的材料进行冷镦锻加工。
通常选择易于塑性变形的材料,如碳钢、合金钢等。
2.材料切割:将材料按照需要的长度进行切割。
切割过程需要注意保持材料的质量和精度。
3.镦头设计:根据产品的需求和形状设计镦头。
镦头是冷镦锻的关键部件,它决定了最终产品的形状和质量。
4.冷镦锻加工:将切割的材料放入冷镦机床中,通过冲击力和挤压力使材料发生塑性变形。
冷镦机床通常由强制进料装置、冷锻头和后处理装置等组成。
5.后处理:对冷镦锻加工后的产品进行去毛刺、清洗、校直等处理。
这些处理过程可以提高产品的表面质量和精度。
1.模具材料选择:模具需要选择耐磨、耐冲击和耐高温的材料,如合金钢、硬质合金等。
2.模具结构设计:模具结构需要合理,能够实现产品的形状要求,并且易于装卸和调整。
模具结构通常包括模具座、模具芯、模具套等组件。
3.模具热处理:模具需要进行适当的热处理,以增加其硬度和耐磨性。
4.模具表面处理:模具表面需要进行适当的涂层处理,以减少摩擦和磨损。
5.模具维护:模具需要定期进行维护和保养,以延长其使用寿命和保持良好的工作状态。
综上所述,冷镦锻工艺与模具设计密不可分。
只有合理选择冷镦锻工艺并设计优化的模具,才能保证产品的质量和生产效率。
冷镦成型工艺设计螺栓

冷镦成型工艺设计螺栓冷镦成型工艺设计是现代机械加工领域的一种重要技术,主要用于生产螺栓。
螺栓是一种常用的紧固件,广泛应用于机械、建筑、电力等行业。
在进行冷镦成型工艺设计时,需要考虑材料的选择、设备的选择、形状的设计等因素,以确保螺栓的质量和生产效率。
首先,冷镦成型工艺设计需要选择合适的材料。
螺栓一般采用碳素钢、合金钢等材料制造,需要根据具体情况选择合适的材料。
材料的选择要考虑到其强度、塑性、韧性等性能指标,并且要保证材料的可加工性和经济性。
其次,冷镦成型工艺设计需要选择合适的设备。
螺栓的冷镦成型工艺需要使用专用的冷镦机进行加工。
冷镦机的选择要考虑到其规格、型号、性能等因素。
一般而言,冷镦机需要具备足够的压力和速度,以确保金属材料在加工过程中的塑性变形。
然后,冷镦成型工艺设计需要进行螺栓形状的设计。
螺栓的形状设计主要包括螺纹的设计、头部的设计等。
螺纹的设计要考虑到螺纹的牙型、螺距、深度等要素,以确保螺栓能够与螺母完全配合。
头部的设计要考虑到头部的形状、孔径等要素,以确保螺栓能够方便地进行装拆。
此外,冷镦成型工艺设计还需要考虑到加工过程中的工艺参数。
例如,冷镦成型的工艺参数包括镦击次数、镦击力度、冷镦机的压力和速度等。
这些工艺参数直接影响到螺栓的质量和生产效率。
通过合理地调整这些工艺参数,可以提高螺栓的传动性能和抗疲劳性能。
另外,冷镦成型工艺设计还需要进行工艺试验和优化。
工艺试验可以通过制作样品螺栓,采用不同的工艺参数进行冷镦成型,然后对比样品螺栓的传动性能、强度等指标,找出最优的工艺参数。
在优化工艺参数时,需要考虑到生产成本、生产效率等因素,以实现螺栓的高质量、高效率生产。
综上所述,冷镦成型工艺设计是一项复杂的技术工作,涉及到材料的选择、设备的选择、形状的设计、工艺参数的调整等多个方面。
只有在各个环节都进行合理的设计和优化,才能够生产出质量可靠、性能优良的螺栓。
外六角头冷镦螺栓不切边工艺流程

外六角头冷镦螺栓不切边工艺流程下载提示:该文档是本店铺精心编制而成的,希望大家下载后,能够帮助大家解决实际问题。
文档下载后可定制修改,请根据实际需要进行调整和使用,谢谢!本店铺为大家提供各种类型的实用资料,如教育随笔、日记赏析、句子摘抄、古诗大全、经典美文、话题作文、工作总结、词语解析、文案摘录、其他资料等等,想了解不同资料格式和写法,敬请关注!Download tips: This document is carefully compiled by this editor. I hope that after you download it, it can help you solve practical problems. The document can be customized and modified after downloading, please adjust and use it according to actual needs, thank you! In addition, this shop provides you with various types of practical materials, such as educational essays, diary appreciation, sentence excerpts, ancient poems, classic articles, topic composition, work summary, word parsing, copy excerpts, other materials and so on, want to know different data formats and writing methods, please pay attention!1. 简介在螺栓生产工艺中,外六角头冷镦螺栓是一种常见的产品类型。
- 1、下载文档前请自行甄别文档内容的完整性,平台不提供额外的编辑、内容补充、找答案等附加服务。
- 2、"仅部分预览"的文档,不可在线预览部分如存在完整性等问题,可反馈申请退款(可完整预览的文档不适用该条件!)。
- 3、如文档侵犯您的权益,请联系客服反馈,我们会尽快为您处理(人工客服工作时间:9:00-18:30)。
目录1.形状、尺寸2. 坯料准备3. 自动锻压机的型号4. 凹模孔的直径5. 滚压螺纹坯径尺寸的确定6. 送料滚轮设计7. 切料模8. 送料与切料时常见的缺陷、产生的原因9. 初镦10. 终镦冲模11. 镦锻凹模12. 减径模13. 切边14. 常用模具材料及硬度要求15. 冷成形工艺对原材料的要求16. 切边时容易出现的缺陷、产生原因17. 化学成份对材料冷成形性能的影响18. SP.360设备参数19. 台湾设备参数20. 台湾搓丝机参数21. 国内搓丝机、滚丝机参数22. YC-420、YC-530滚丝机参数23. 磨床参数24. 单位换算25. 钻床参数形状、尺寸:1.圆角半径――取直径的1/20~1/5。
冷锻时圆角过大反而难锻造。
2.镦粗头部和法兰部尺寸――头部或法兰部体积V在2D3(D为坯料直径)以下时用单击镦锻机,3.5D3以下时可用双击镦锻机加工,而不会产生纵向弯曲。
如V为4.7D3必须经三道镦粗工序。
这部分的直径D1,(镦粗后直径)对于C<0.2%的碳素钢,不经中间退火能够镦粗到2.5D。
超过上述范围必须中间退火。
侧面尺寸由于难以控制,公差要尽可能放宽。
3.镦粗部分的形状――头部或头下部的高度比直径大时,侧壁上向上和向下设置2°左右的锥度,使材料填充良好。
球形头部顶上允许设计成小平面。
4.挤压件坯料和挤出部分断面积之比A0/A1,即挤压比R,对S10C、BSW1的实心、空心正挤压件,如在5~10以下,对反挤压杯形件,如在1.3~4间,能够一次成形。
自由挤压件的R如在1.25~1.4以下,能经一道工序加工。
杯形件反挤压时的冲头压力,当R 约为1.7时最小。
5.挤压件断面变化部分的锥度如图1,但对于变形抗力高的材料,从模具强度上考虑,α(度)要取较大值。
挤压比制件形状1.25 2 4 50棒、管正挤压件反挤压杯形件10~2060~9030~4560~9045~6075~9075~9075~906.反挤压杯形件的侧壁高度――侧壁高度H和冲头直径d的比H/d,对S10C、BSW1如在2~3以下,对更硬的材料如在1~2以下,均可一次成形。
7.凹穴的尺寸和位置――在材料的集中部分附加的凹穴深度取小于直径,只有一个凹穴时,必须布置在制件的对称中心。
8.底、法兰、幅板的厚度――厚度和直径之比T/D对S10C、BSW1如在1/10以上,可一次加工成形。
比上述界限薄时,沿材料流动方向设置3°~5°斜度使厚度逐渐增加。
9.尺寸公差――虽尽可能松些为好,如需标注,选取与一般能够得到的精度相符合的公差。
10.一次缩径的极限变形为0.36,凹模导入角为2a≤30°,多次缩径时,总极限压缩为0.96~1.36。
第一次和第二次缩径的极限压缩为0.29~0.35,第三次和第四次可提高到0.36~0.40。
(ε=(D2-d2)/D2),D-材料直径;d-缩径后直径。
11.Φ22搓花t=1.5可增大0.44mm。
12.如果一序凹模圆角半径大而二序凹模圆角半径小,会造成根部折叠;13.减径挤压时,由于断面减缩率较小,此时中心层金属的流动速度反而慢于表层金属,中心层产生附加拉应力,可能会造成内部裂纹;14.减径挤压时,凹模工作带厚度不均匀会造成杆部弯曲;15.由于摩擦的影响而导致附加应力和残余应力,当它们的值超过挤压材料的许可值时,就可能产生环形鱼鳞状裂纹;(材料润滑不良)16.头部的文字对头部变形有影响(受力不均产生);17.冷挤压零件的结构工艺性1.对称性:最好是轴对称旋转体,其次是对称的非旋转体;2.断面积差:在零件不同断面上,特别是在相邻断面上的断面积差设计的越小越有利;3.断面过渡及圆角过渡:冷挤压件断面有差别时,应设计从一个断面缓慢的过渡到另一个断面,避免急剧变化。
可用锥形面或中间台阶来逐步过渡,且过渡处要有足够大的圆角。
4.断面形状:锥形问题,锥形件冷挤压会产生一个有害的水平分力,故应先冷挤加工成圆筒形,然后单独镦出外部锥体或车削加工出内锥体。
18.19.各种镦粗方式的加工界限;20.在上下固定的凹模间隙内,将材料镦出凸缘的加工界限;21.反挤压杯形件时,形状畸变的形式主要有孔口断面坡口和底棱缺肉;如果要获得口端平整的杯形件,可以先在毛坯上预成形一个凹窝,使凹窝的深度大于出现坡口时的深度,然后对端面实行封闭,将端面挤平;22.杆长100mm及以下螺栓采用搓丝工艺。
23.圆头不切边零件的三序上模外圆尺寸要比零件头部外圆尺寸大0.4mm左右,因为外圆充不满。
坯料准备A.热处理球化退火――钢材,特别是含碳量0.3%以上的钢材,需作珠光体细球化处理(珠光体4~6级)。
预先经过冷加工(拉拔、镦粗)的材料,珠光体球化最容易。
热轧材料的球化,要预先经正火或淬火-回火处理。
(使钢中碳化物球状化而进行的退火工艺。
1.完全退火――用于含碳量0.2%以下的钢及非铁金属。
2.正火――为使钢材组织均匀化、晶粒细化而进行正火。
可作为退火的前处理,低碳钢只要作此处理就可锻造。
3.淬火――除可用来作为球化处理的前处理外,为使SUS27等奥氏体不锈钢软化,可加热到约1100℃再水冷。
4.软化退火――用来作为冷锻工序的中间退火处理。
B.润滑处理1.磷酸盐被膜处理――脱脂-水洗-酸洗-水洗-中和-水洗-薄膜处理-水洗-中和-水洗-润滑处理被膜处理过的坯料,一般用被膜润滑剂润滑。
被膜润滑剂是以脂肪酸钠肥皂为主要成分,和磷酸盐起反应会产生金属皂而起润滑效果。
精压印时,被膜处理后,薄薄地涂上一层低粘度的动植物油(蓖麻油、羊毛脂、棕榈油)。
在长行程的正挤压和齿形挤压时,用被膜润滑剂大多不能满足要求,这时可按要求的二硫化钼和石墨的微粒粉末厚度计算出能涂敷的量,将其溶于四铅化碳、酒精等挥发性溶剂中,用滚筒涂敷,可以获得良好的结果。
C.坯料制备1.坯料切断法――锯断、剪断、冲裁。
2.坯料的体积、尺寸、形状――坯料体积的计算,以制件体积为基础。
再加上由于锻后的切边、冲裁、切削加工等引起损失的体积(5~50%)。
锻造后即使不再加工,也要考虑因中间退火、酸洗造成的损失。
而且,还需考虑坯料体积的误差,要求即使在最小体积的情况下也不产生缺肉,必须预留体积余量。
多余的体积由横向或纵向挤出或形成飞边来调节。
但是,特别是出现横向飞边时,飞边大小会引起变形力的变化,从而使制件本身产生尺寸误差,因此体积公差,一般希望在0.5%左右。
采用不同直径的坯料能够制造同样的制件。
选取坯料直径的原则是,所选直径使在完成终锻件前材料的移动量或变形量、加工工序数尽量少,制件内部的变形分布尽量均一。
考虑坯料装入模具时,比模具内径过小的坯料定心困难,另一方面,和模具内径过于接近的坯料装入时,不仅特别是自动装入困难,而且还担心坯料的润滑坯膜被擦落。
因此,坯料直径一般比模具内径小0.1~0.2mm。
3.整形――坯料切断时产生的毛刺,是制件出现缺陷、工具磨损的原因,应利用滚筒清理等除去。
并且,即使没有毛刺,尖角也是锻造时产生折叠或引起润滑膜中断的原因,因此,要尽可能取大圆角或进行倒角。
为制作深杯形件用带压出凹穴的坯料,用模具预成形中心孔,可防止冲头偏心。
自动锻压机的型号Z47-12BZ――自动镦压机类4――多工位自动冷镦机7――多工位螺栓联合自动冷镦机12――主要参数:最大镦制规格12mmB――结构改进次序-第二次改进自动镦锻机别组划分表。
.带搓丝的叫螺栓联合自动冷镦机。
螺栓联合自动冷镦机能完成线材的送进、切断、初镦、缩径或挤压、终镦、切边、倒角、搓丝等工序。
凹模孔的直径为了使切下的毛坯能顺利进入凹模孔内,要求线材直径与凹模孔径之间有一定的间隙,此时所需要的最小间隙(单边)为0.01~0.10mm ,这个数值的大小与线材直径、与线材进入凹模的长度成正比,即线材直径越大,则所需要的最小间隙也越大。
制造全螺纹用的凹模孔的直径,可以根据滚丝或搓丝前所要的螺坯的最小尺寸来确定。
制造粗杆半螺纹用的模孔直径,根据产品光杆直径的最小尺寸来确定。
前者凹模孔的最小尺寸应当等于或略小于螺坯最小尺寸,后者的模孔最小尺寸应当等于或略小于光杆部分的最小尺寸。
对于全螺纹用的线材尺寸要求比半螺纹用的线材尺寸公差小;长杆工件用线材直径公差较短杆工件要小些。
滚压螺纹坯径尺寸的确定坯径的公差为0.02~0.03mm 。
理论滚轧直径:(日本)滚压螺纹的精度基本上取决于螺坯尺寸及其表面粗糙度。
二级精度(老标准) d 坯min =d 2min+T/3mmd 坯max =d 2min+3T/4mm (d 2min+4T/5mm ) d 坯min =d 2min+0.3Tmm纹内侧牙顶宽度。
外螺纹牙根宽度或内螺螺纹牙型半角;螺距;内螺纹内径;外螺纹内径(底径)或径(底径);外螺纹外径或内螺纹外;;;式中:=====-=--==+--=W p R R R R c R R R R b R a p W R bc W p a p R αα21212221212122'2223}tan 2)({312d坯max=d2min+0.7Tmm式中d2min――二级精度螺纹中径最小值T――二级精度螺纹中径公差值mm对于电镀螺纹,d2min为该螺纹电镀前中径最小值,即d2min -4δδ――电镀层厚度的最小值mm。
送料滚轮设计切料模切料模的直径d1=d0max+(0.1~0.25)mm,式中d0max为线材的最大直径。
切料模孔的工作部分长度L=(2.5~3)d1,引入孔的直径d2≥1.2d1,压装镶块的过盈量为0.08~0.10mm。
切断凹模与割料刀之间间隙的大小,对切断的质量是有影响的。
如果刀板与切断凹模的间隙太小,则上下裂缝不会相遇而产生新的裂缝,这样切料端面就会有缺陷,如果间隙太大,就有很大的压缩并有毛刺。
最合理的间隙和毛坯直径d0有关,一般间隙z=(5~15%)d0。
刀板上的刃口直径d的尺寸,是以线材的最大直径作公送料与切料时常见的缺陷、产生的原因:1.拉毛:由于刀板刃口中心与割料模中心不重合而产生摩擦;原材料不直,原材料直径大,模孔不光,原材料本身有条痕等。
2.毛刺:由于割料模与刀板的刃口不锋利或料软而产生的,有时刀板与割料模之间间隙太大也会产生毛刺。
3.压印大:切刀刃口不锋利或刃口已磨损产生的。
4.铁屑:由于线材端面与刀板摩擦或刀板不锋利造成的。
初镦对坯料的自由端进行镦锻时,镦锻质量及所需要的镦锻次数与坯料自由端的长径比有很大的关系,当长径比小于2.25时,一次可把头部镦成所需要的形状,当超过这个数值以后,就应进行预镦或初镦,把坯料先镦成圆锥形,然后进行第二次或更多次数的镦锻,其目的是要避免杆部金属产生纵向弯曲。
初冲模的设计1.初冲模具的设计原则:要求初冲有尽可能大的变形比,其次要避免金属纤维纵向弯曲。