带式输送机论文中英文资料外文翻译文献
普通带式输送机的毕业设计论文(含中英文翻译)[管理资料]
![普通带式输送机的毕业设计论文(含中英文翻译)[管理资料]](https://img.taocdn.com/s3/m/0bd709bbcf84b9d529ea7ac5.png)
毕业设计说明书普通带式输送机的设计作者: 学号:学院(系):专业:指导教师:评阅人:2006年6月普通带式输送机的设计摘要本文在参考常规下运带式输送机设计方法的基础上,分析了常见驱动方式和制动方式用于长运距、大运量下运带式输送机上的优缺点,提出该运输机可采用的驱动和制动方式;分析了常见软起动装置及其选型方法,归纳总结出长运距、大运量变坡输送下运带式输送机设计中的关键问题和可靠驱动方案和制动方式优化组合的可行方案;通过常规设计计算,提出了合理确定张紧位置、张紧方式及张紧力大小的方法;对驱动装置及各主要部件进行了选型并校核。
长距离变坡下运带式输送机运行工况复杂,在设计方面需考虑各种可能的工况,并计算最危险工况下输送机的各项参数,同时为保证运行过程中输送机各组成部分能适应载荷及工况的变化需将拉紧力统一,然后重新计算各工况下输送机参数,最终确定整机参数。
本论文对长运距、大运量变坡下运带式输送机,综合考虑各方面的因素,采用合理的驱动方案、制动方式和软启动装置组合,有效保证长运距、大运量变坡下运带式输送机的可靠运行。
关键词:带式输送机下运长距离变坡STUDY ON COMMON TRANSPORTING BELT-CONVEYER ABSTRACT Based on the design method for the conventional Downwards Transporting Belt-Conveyer (DTBC), the common used driving and braking devices were analyzed in the condition of long-distance and heavy-capacity. The driving and braking types were presented for this kind of conveyer. The soft-starting devices and their type-selection were analyzed. The key points were summarized for designing the long-distance, heavy-capacity DTBC used in varying slope environment. The reliable combined scheme of driving and braking units was put forward. The methods for determining the tensioning location, type and the amount of tensioning force based on the results of conventional calculations. The criterion was summarized for selecting driving device and the main components in the conveyer.Due to the complicated operational condition of long-distance and varying slope DTBC, it is necessary to consider every kind of possible working conditions during its design and calculate the parameters in the most dangerous condition. At the same time, it is necessary to uniform the tensioning force in order to suit the variations of the load and condition. Then the conveyer's parameters should be re-calculated under various conditions and the parameters should be determined finally.The research of this paper shows that by using reasonable combination of driving scheme, braking mode and soft-starting device and by determining the schemes for braking and soft-starting from the dynamical analysis and simulation, the reliable operation could be guaranteed for the long-distance, heavy-capacity and varying slope DTBC.Key word Belt-conveyer, Downwards transportation, long-distance, Varying slope目录1 绪论 (1) (2) (2) (2) (3) (3) (4) (4) (5) (5) (5) (6)、大运量下运带式输送机关键技术分析研究 (6)、制动方案的分析 (6)3长距离、大运量下运带式输送机关键技术的分析 (7) (7) (7) (8)4 长距离大运量下运带式输送机的设计 (11)带式输送机原始参数 (11)带式输送机的设计计算 (11)............................................................1 1 .....................................................................1 2 (12)................................................1 3 .....................................................................1 3 ............................................................1 3 ........................................................................1 4 .....................................................................1 5 ................................................1 6 最大发电状态下张力计算 (16)最大电动状态下张力计算 (19) (20)......................................................2 1 ............................................................2 4 滚筒的选择与减速器的选择 (24)...............................................................2 4 ..................................................................2 4 ........................................................................2 4 制动器装置的选择 (25)................................................2 5 (27) (27) (28)目前主要的软起动装置原理与性能 (28)软起动装置的选用 (31) (31).....................................................................3 2 .........................................................3 2 ........................................................................3 2 5 结论 (34)致谢 (35)参考文献 (36)外文文献原文译文1 绪论带式输送机的最新发展方向时一呈现长距离、大运量、高速度、集中控制等特点。
带式输送机英文文献翻译
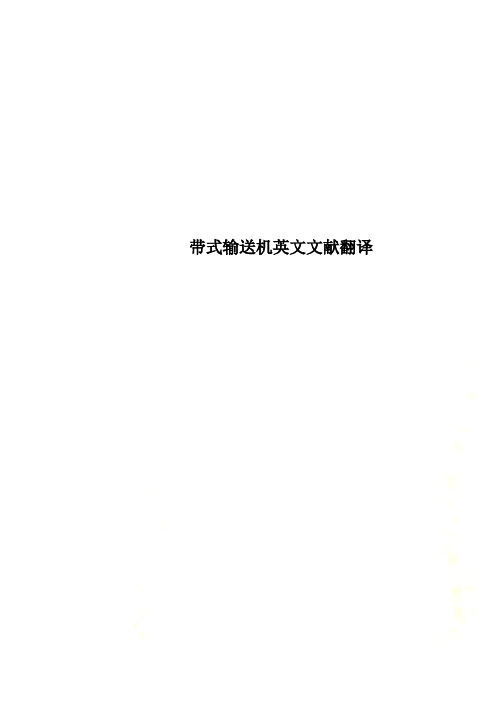
带式输送机英文文献翻译原文Transporting machine to press the operation way can is divided into:1:The leather belt type transports machine 2:Is spiral to transport machine 3:The Dou type promotes machine 4:The roller transports machine 5:Calculate to transport machine 6:The plank chain transports machine 7:The net takes to transport machine 8:The chain transports machine.1.ParameterIs general according to various condition of request, material shipping point that the material transports system, relevant of the production craft process and material of characteristic etc. to make sure each main parameter.①Transport ability:The ability oftransporting the transporting of machine means unit for time inside transport of material quantity.While transporting to spread a form material, with the quality or physical volume calculation that the per hour transports a material;At transport into a piece product, with the number of items calculation that the per hour transports.②Transport speed:The exaltation transports speed to improve the ability of transporting.When being making to lead a piece by belt conveyer and transporting length was more big, transport speed to gradually enlarge.But the take type of high-speed operation transports machine to need to notice vibration, Zao voice and start and make etc. problem.For use chain as lead a piece of transport machine,transporting the speed should not lead greatly, in order to prevent the aggrandizement power carry alotus.Carry on transporting of craft operation machine at the same time, transporting the speed should press to produce a craft to request an assurance.③Reach a size:Transport reaching of machine a size to include belt conveyer width, lath width and anticipate Dou capacity, piping diameter and container all of etc.s.These reach a sizes to all directly influence to transport machine of transport ability.④Transport length and QingCape:Transport circuit length and Qing Cape size to directly influence the total resistance of transporting the machine and need of power.2.Transport a machine the spot application wayConstitute to carry on explaining in detail from the take type machine system first:Leather belt's transporting machine is to spread a form material to transport and pack to unload an equipments most importantly, can extensively used for the mineral mountain, metallurgy, building materials, chemical engineering, electric power, industrial realms like food processing,etc, in the coal mine, metal mineral, the steel business enterprise, port, grounds like cement works,etc a great deal of application that can see skin machine, transporting the machine can not only complete to spread a transporting of form material, but also can transport into a piece material, butbasis use location, work environment, transport the dissimilarity of material category, will also have bigger difference in its design and the application;Modernization of transport the machine system has higher request to the dust palliative, is this, in each the device that transfer place and establish and sprinkle water and gather a dust, transport machine and follow line in the tape will establish and defend a breeze cover or block an aerofoil, system from list the machine constitute of, to work in the whole machine system of operate and fix to say, want and have a foothold and divide the single machine of the tube at oneself, and want to understand mutual contact between systems, list machine again is constitute to°from many partses,only work well the daily maintenance of each parts maintains and makes it is placed in good work status so as to ensure the safe movement of equipments;We generally will transport the use place, work environment of machine according to the take type, technique function and transport material category to wait various dissimilarity with satisfy various forms of homework work condition, in addition to in addition to transporting machine, the in general use leather belt of more adoption also various special kind tapes of new structure transport machine and have a mainly having of the representative among them:Big Qing Cape take type machine, deep slot take type machine and press take type machine, take care of the formtake type, the air cushion take type, the flat surface turn take type, the line friction type, wave-like in shape the belt conveyer type blocking a side transport machine etc. and carry on a thin method for turning and canning exist various classifications and make following introduction now:Press the use classification, there is in general use ambulation type, under the well choice type, the strip mine is used a fixed type, special kind structure type, can move a place type and transport machine, load machine appropriation redistribution function type, the big Qing Cape type transports machine etc., generally speaking transport machine inside the short distance factory can complete level, up the luck or bottomcarries, canning go against the wood grain type leather belt machine can be used for double to transport a material, hang arm machine usually install anticipate on board in the heap, and can turn round, line up the function of soil or cloth by realization, but Gao Jia Ji propped up by in the door usually match with other spread and anticipate and handle an equipments common use, for example give or get an electric shock and constuct a medium application in water, can install standard in the center frame, the machine's mounting places on the track Zhen, easy to move and place;Press the category of transporting the material to categorize, have the generally lax material is used of, the strong and tough material is used of and list piece theleather belt used in material transport machine etc. and press the rubber conveyance takes a loading segment of position to categorize, include a leather belt loading segment at top of and loading segment at underneath of and at the same time loading segment at up underneath of double to transport machine three, the use double can distinguish to transporting machine at up branch and bottom branch transport a material, but for keeping material contact noodles don't produce a change and need to bring in to go to the rubber to be periodically inside out.3.CategorizeTransporting machine generally and pressing already didn't lead piece to carry on a classification and had to lead a transporting of piece machine to generallyinclude to lead a piece, loading to reach a piece, drive device, bring to the stretch device and change to accept an etc. to the device and.Lead a piece to in order to deliver to lead dint, can adopt belt conveyer and lead chain or steel wire rope;The loading reaches a piece to in order to accept to put a material and has already anticipated Dou and bracket or mourns to have...etc.;Drive device to transport machine with the power, generally from electric motor, decelerate a machine and make machine(stop a machine) etc. to constitute;Bring to the stretch to equip to generally have the Luo pole the type and heavy hammer type 2 kind, can make to lead a piece to keep certain tension and hang a degree, transport machine by assurance normaloperation;Pay to accept a piece to in order to accept to give to lead piece or loading to reach a piece, can adopt to give Gun and roll an etc..Having the structure characteristics that lead the transporting of piece machine is:Be delivered a material and pack reaching with the loading leading a link together inside the piece, or directly pack in leading a piece(is like belt conveyer), led a piece to once round each roller or the chain round beginning and end and connect with each other, formation include and deliver a having of material carry branch and don't deliver a material of have never carried shutting of branch and match wreath road, make use of lead continuous sport of piece and transport a material.This type ofly transporting model is numerous,there is mainly a take type transporting a machine, plank type and transporting a machine, small car type and transporting machine, escalator, automatic sidewalk, paring off plank and transporting machine, covering up and paring off plank and transporting a machine, Dou type and transporting a machine, Dou type and promoting machine and hanging and transporting machine and build on stilts a cableway...etc..The structure that didn't lead transporting of piece machine constitutes each not same, use to the work of transporting the material to reach a piece as well not same.Their structure characteristicses are:Make use of a work to reach a revolving of piece to exercise or the back and forth exercise, or make useof lie quality to make the material transport forward in the fluxion in the piping.For example, the Gun son transports the work of machine to reach the piece as a series of Gun son, the Gun son makes to revolve sport to transport a material;Is spiral to transport the work of machine to reach a piece for spiral, helix at anticipate and make to revolve sport in the slot with follow anticipate slot to push to send a material;The vibration transports the work of machine to reach piece in order to anticipate slot, anticipate slot to make back and forth sport with transport Be placed to among them of material etc..Install(1)The fixed type transports machine should by rule gearing method gearing atfix of foundation up.The ambulation type transports machine formally before circulating and should live wheel with the wedge Xie or uses to make a machine to stop.So as not to take place to take a stroll in the work, there is the passage that many sets , between machine and machine, there shoulded be one meter between wall and machine while transporting a parallel homework of machine.(2)The beard checks an each operation part, tape to take to button up to equip with loading before using whether normal, whether protection equipments iswell-found.The tape rises a tight degree beard before starting the adjustment is to suitable extent.(3)Leather belt's transporting machine should get empty to carry a start.Waitingto revolve normal rear can go into to anticipate.Drive after forbiding to go into first to anticipate.(4)There are few set that when transport machine to establish to circulate should from unload to anticipate to carry a beginning, the sequence starts.After revolving as usual all, the square can go into to anticipate.(5)Appear in the movement when the tape runs to be partial to a phenomenon should park the car adjustment, can not force an use, so as not to wear away edge and increment burden.(6)Work environment and be sent material temperature not to must be higher than 50 ℃ and be lowerthan-10 ℃ .Can not transport the material of having sour alkaline oil andorganic melting agent composition.(7)Forbid pedestrian or multiply by a person on the belt conveyer.(8)Have to stop going into first to anticipate before parking the car, wait leather belt up save to anticipate to unload to the utmost a square can park the car.(9)Transporting the machine electric motor has to insulate good.The ambulation type transports machine electric cable to pull and drag along indiscriminately.The dynamoelectric confidential credibility connects ground.(10)The leather belt beats slippery strictly forbid to by hand pull leather belt, so as not to take place trouble.5.Adjust to try(1) Each equipments with meticulouscare adjusts to try to transport machine after installing and satisfies a drawing request.(2) Each deceleration machine exercises parts to add to note to correspond lubricant.(3) The gearing after transporting machine to attain to request each single set equipments carries on beginning to work to make run-in, and knot to put together to adjust to try to transport machine to satisfy an operative request. (4) Adjust to try the electricity part of transporting the machine.Include to connect adjusting of line and action to try to the normal regulations electricity, make the equipments have good function, attain the function and status of design.6.Transport machine to block knothole 2kinds of boring crafts(1)Blow up boring:The material after the irradiation of continuous laser and centrally forms one cave pit, then from and laser beam the coaxial oxygen flow to clean meltdown material and form one bore very quickly.The size of general bore is as thick relevant as plank, blow up to bore hole the average diameter as thick plank half, therefore blow up to bore hole bore path bigger to thicker plank, and not circle, should not in requesting higher spare parts use(if the petroleum Shai sews a tube), can be used for a waste up.In addition because of bore hole use of oxygen pressure with incise homology, splash a little bit greatly.(2)Pulse boring:The pulse laser that adopts high peak value power makes alittle amount material melt or vaporizes, in common use air or nitrogen spirit are to lend support to air and oxidize to make bore expand because of putting heat by decrease, the air pressure more incises of the oxygen pressure is small.The particle jet with small creation of each pulse laser gradually goes deep into, therefore slab boring time takes several seconds.Once bore hole completion, immediately change assistance air into oxygen to carry on incising.Boring hole diameter like this is smaller, its boring quality is better than to blow up boring.Not only should have higher exportation power for the laser machine used by this;The time and space characteristic that more important time ties, therefore the general crosscurrent carbon dioxide laser machine can notadapt to the request that the laser incises.In addition the pulse bores hole to also have the more dependable spirit road the control system to carry out cutting over of air category, air pressure and bore hole a horary control.译文:输送机按运作方式可以分为:1:皮带式输送机2:螺旋输送机3:斗式提升机4:滚筒输送机5:计量输送机6:板链输送机7:网带输送机8:链条输送机。
皮带输送机的驱动外文文献翻译、中英文翻译
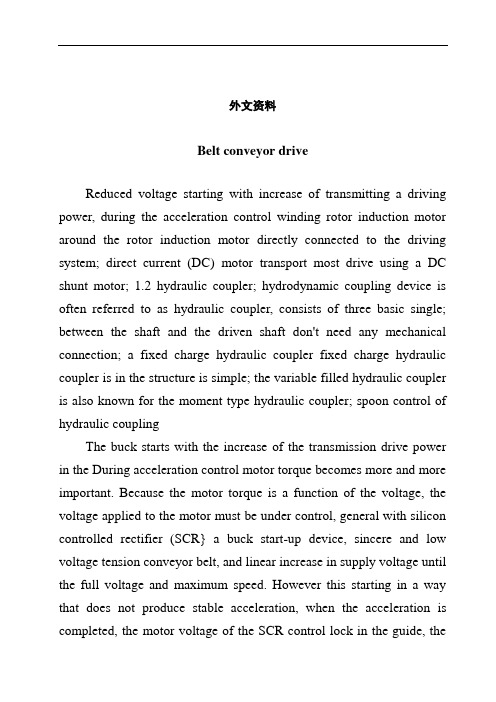
外文资料Belt conveyor driveReduced voltage starting with increase of transmitting a driving power, during the acceleration control winding rotor induction motor around the rotor induction motor directly connected to the driving system; direct current (DC) motor transport most drive using a DC shunt motor; 1.2 hydraulic coupler; hydrodynamic coupling device is often referred to as hydraulic coupler, consists of three basic single; between the shaft and the driven shaft don't need any mechanical connection; a fixed charge hydraulic coupler fixed charge hydraulic coupler is in the structure is simple; the variable filled hydraulic coupler is also known for the moment type hydraulic coupler; spoon control of hydraulic couplingThe buck starts with the increase of the transmission drive power in the During acceleration control motor torque becomes more and more important. Because the motor torque is a function of the voltage, the voltage applied to the motor must be under control, general with silicon controlled rectifier (SCR} a buck start-up device, sincere and low voltage tension conveyor belt, and linear increase in supply voltage until the full voltage and maximum speed. However this starting in a way that does not produce stable acceleration, when the acceleration is completed, the motor voltage of the SCR control lock in the guide, themotor provides full pressure. Such control power can reach 750kW.Wound rotor induction motor winding rotor induction motor directly connected to the drive system Reducer through in the rotor windings of the motor in series resistance torque control of motor. In at the start of a transmission device, the resistor in series in the rotor to generate a low torque, when the conveyor belt speed, the resistance is gradually reduced steadily increasing torque. In multi drive system, an additional slip resistance may will always be connected in series in the circuit of rotor winding to help load sharing. The motor system design is relatively simple, but the control system may very complex, because they are based on the computer control of the resistive switching. Nowadays, the majority control system is custom designed to meet the specifications of transmission system around the rotor motor is suitable for 400 KVV above the system.Drive direct current (DC) motor transport most use DC shunt motor, the motor armature in the external connection. Controlled DC drive technique is generally used for SCR device, which allows continuous variable speed operation of DC drive system in machinery is simple, but design of electronic circuits, monitoring and control the whole system, compared to other soft start system is expensive, but in torque, load sharing and transmission for the main consideration occasions, it is a reliable, saving the cost of the DC motor general use in larger power conveying device, including should play the conveying belt tension control of multi drive Dynamic systems and transmission devices that require a wide range of transmission.Hydrodynamic coupling is often referred to as the hydrauliccoupler, consists of three basic units: as the impeller of the centrifugal pump, promote hydraulic turbine and put into the shell of the two power components. Fluid from the impeller to the turbine, on the driven shaft torque. Torque and speed because of the circulating fluid in driving Shaft and the driven shaft does not need any mechanical connection. This connection power generated by the decision to hydraulic coupling of the filling quantity, the torque is proportional to the input speed. Because in the fluid coupling output speed less than the input rate, the difference therebetween said to slip, generally 1% - 3%. Transmission power of up to several thousand kilowatts.A fixed charge hydraulic coupler fixed charge hydraulic coupler is in relatively simple in structure and has only limited the bending part of the conveying device most commonly used soft start device, the structure is relatively simple and low cost, can provide excellent soft start effect on now use most of the conveyor.Variable filled hydraulic coupler, also known as torque hydraulic coupler limited. Coupling of the impeller installed in the AC motor, turbine is installed on the driven gear for high-speed shaft on, containing the operating components of the axle box is installed on the driving base. Coupling the rotating shell with an overflow outlet allow the liquid to continuously from the working chamber midstream Into a separate auxiliary chamber, oil from the auxiliary chamber through a heat exchanger pump to control electromagnetic valve of coupler filling liquid quantity. In order to control the starting torque of the single motor driving system must be monitoring of AC motor current to the solenoid valve control provide feedback. Variable filled hydraulic coupler can beused in power delivery system and the power can reach thousands of kilowatts the drive is very complex both in mechanical, or electrical driving system at moderate cost.Spoon pipe control hydraulic coupler is also known for the variable speed fluid couplings. This hydraulic coupler is also by three standard coupling unit form, i.e., an impeller, a turbine and a A housing containing loop. This hydraulic coupler need outside the working chamber setting catheter (also known as spoon pipe) and luminal and rely on adjusting device to change the spoon pipe opening (scoop tube and the top end of the rotation of the shell of spacing) artificially change the working cavity of the filling quantity, so as to realize the output speed regulation. This control provides a reasonably smooth acceleration, but the computer control system is very complex. Spoon pipe control hydraulic coupler can be used in single or multiple machine drive system, power range for 150kW-750kW.Variable frequency controlVariable frequency control is also a direct drive mode, it has a very unique high performance.VFC Device for induction motor with changes in the frequency and voltage, excellent starting torque and acceleration.VFC equipment is a power electronic controller, first of all, the AC is rectified into DC, then using the inverter, then transforms the DC frequency, driving voltage controllable AC. VFC adopts vector control or direct torque control (DTC) technology, can according to different load with different speed.VFC driving energy according to the given s curves start or stop, to achieve automatic tracking started or stopped curve.VFC drive for conveying belt started to provide excellentcontrol of speed and torque, also can for the multi machine drive system For load sharing.VFC controller can be easily installed on the conveyor drive power is small. Past when in high voltage, VFC device structure due to the power semiconductor devices rated voltage value restrictions become very complex, high voltage transmission often use low-voltage inverter, and then use the step-up transformer at the output, or using a plurality of low voltage inverter in series to solve. And simple device series connection of two level inverter system compared due to the series between devices easily pressure and output can be a better harmonic characteristics, three level voltage type PWI inverter system in several megawatts industrial transmission in recent years won 750kW/ system has been successfully installed in the belt conveyor drive system of the long 2 71m two in the coal mine of three 2.3kv VFC.Neutral point three level inverter using IGBTDue to tandem device voltage sharing easy, low device each time the switch of DV / dt and output good harmonic performance, the three-level voltage inverter in high power drive applications become more and more popular. V oltage IGBT (HV-IGBT) makes application of three-level neutral point box have a principle of high-voltage inverter design Greater scope of application. This inverter can now be achieved from 2. RV to 4. 16Kv full scope of application.HV-IGBT module series can be used in 3. RV and 4. 16Kv equipments2. A V each inverter switch only needs a HV-IGBT[2,3].Main power inverter circuitHigh voltage AC drive applications. Compared with a two-levelvoltage type inverter, three-level midpoint box voltage type inverter provides three voltage levels to the output terminal, for the same quality of output current, the switching frequency can be reduced to the original 1 / 4, the switching devices of rated voltage S2u s4u and S3u and S2u S1u trunk additional value can be reduced to the original 1 / 2, attached to the motor transient voltage stress may also be reduced to the original 1 / 2. Three level neutral point voltage type inverter switch state can be summarized in Table 1, u, V and W respectively represents three, P, N and G is a DC bus three points. For example, when the switch is closed, u are in a state of P (positive bus bar voltage), on the contrary, when the switch is closed, u are in a state of n (negative bus voltage). In the neutral case, the phase in the o state, then on the basis of the phase current polarity is positive or negative, or conduction or s In order to ensure that the neutral point voltage is balanced, the average current injected at the o point should be zero at 3U.As commonly used 12 pulse diode rectifier to the DC link capacitor charging, introduced at the input end of the harmonic is very small. If the input harmonic have higher requirements, using a 24 pulse diode rectifier as input converter. The need to have the ability to regenerate more advanced, you can use an active input converter instead of diode rectifier and then input rectifier and inverter output for the same structure.Inverter controlMotor controlled induction motor control can be used in rotor field oriented vector control Is implemented through the use of PWM modulator completed the constant torque and high speed in the fieldweakening region. Figure 2 shows the indirect vector control block diagram of figure in the flux command a psi R is function of velocity, velocity feedback and feedforward slip control signal Sichuan HMU. The addition results of frequency signal integration, although after generation unit vector (COS theta E and sinO theta E) and finally through the vector rotator generate voltage V 'angle theta control PWM modulator.Inverter. Its basic principle is that the three level PWM modulator uses two reference waves to recognize Ur1 and Ur2, but only use a triangular wave. It is determined in an optimized way every time Switch time.Switching frequency harmonics generated by as much as possible is small, the use is as low as possible to minimize the switching losses; the zero sequence components are added to each reference Tripoli to the relative position of the maximization of fundamental voltage. An additional degree of freedom as the reference wave and triangle wave can be changed, it can be for the current balance of DC link midpoint.Three level inverter 3V of three 750kW/ after Zhuang coal mine 2.7 km. Long belt conveyor drive system successfully installed, on the performance of the variable frequency drive system (VFC) were tested. The test results show that the control system using VFC belt The excellent characteristics of conveyor. Figure 3 for test results and waveforms. Shown by the figures, curve 1 shows controlled belt speed, belt speed with the S-shaped curve shape curve 2,3, respectively, which indicated that current and torque, curve 4 shows tension belt. From the figure can be found with the tension fluctuation range is small, all testresults show a belt conveyor drive system satisfactory characteristics.In recent years, conveyor drive control technology have been more reliable, consistent with the cost-effective and efficient driving drive system provides users with a choice. In these choices, variable frequency control (VFC) showing in the future long distance conveying belt conveyor Plays an important role. Using the midpoint of the high-pressure work GBT block three level inverter itself can provide high voltage power supply to the motor terminals, so that the inverter control application more simple. By Zhuang coal mine 2. 7 km long belt conveyor in the midpoint of the clamped three-level inverter VVVF (VFC) control system test results show that, using the midpoint of the BV-IGBT block three level inverter and rotor flux vector control strategy of induction motor variable frequency drive is used, the belt conveyor drive system has very good performance, showing a good application prospect.中文译文皮带输送机的驱动降压启动随着传送驱动功率的增加,在加速期间控制使绕线转子感应电机绕线转子感应电机直接连接到驱动系;直流(DC)电机大多数传送驱动使用DC并励电机,;1.2液力偶合器;流体动力偶合器通常被称为液力偶合器,由三个基本单;轴和从动轴之间不需要任何机械连接;固定充液液力偶合器固定充液液力偶合器是在结构较简;可变充液液力偶合器也称为限矩型液力偶合器;勺管控制液力偶合降压启动随着传送驱动功率的增加,在加速期间控制使用的电机扭矩变得越来越重要。
带式输送机中英文对照外文翻译文献
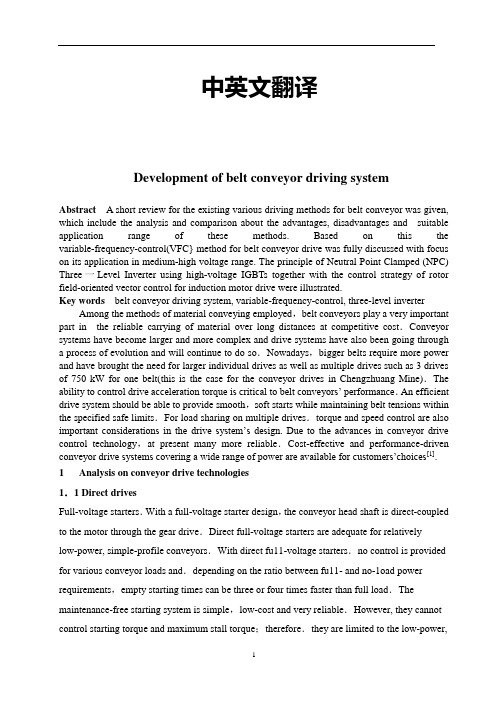
中英文翻译Development of belt conveyor driving systemAbstract A short review for the existing various driving methods for belt conveyor was given, which include the analysis and comparison about the advantages, disadvantages and suitable application range of these methods. Based on this the variable-frequency-control(VFC} method for belt conveyor drive was fully discussed with focus on its application in medium-high voltage range. The principle of Neutral Point Clamped (NPC) Three一Level Inverter using high-voltage IGBTs together with the control strategy of rotor field-oriented vector control for induction motor drive were illustrated.Key words belt conveyor driving system, variable-frequency-control, three-level inverter Among the methods of material conveying employed,belt conveyors play a very important part in the reliable carrying of material over long distances at competitive cost.Conveyor systems have become larger and more complex and drive systems have also been going through a process of evolution and will continue to do so.Nowadays,bigger belts require more power and have brought the need for larger individual drives as well as multiple drives such as 3 drives of 750 kW for one belt(this is the case for the conveyor drives in Chengzhuang Mine).The ability to control drive acceleration torque is critical to belt conveyors’ performance.An efficient drive system should be able to provide smooth,soft starts while maintaining belt tensions within the specified safe limits.For load sharing on multiple drives.torque and speed control are also important considerations in the drive system’s design. Due to the advances in conveyor drive control technology,at present many more reliable.Cost-effective and performance-driven conveyor driv e systems covering a wide range of power are available for customers’choices[1].1 Analysis on conveyor drive technologies1.1 Direct drivesFull-voltage starters.With a full-voltage starter design,the conveyor head shaft is direct-coupled to the motor through the gear drive.Direct full-voltage starters are adequate for relativelylow-power, simple-profile conveyors.With direct fu11-voltage starters.no control is provided for various conveyor loads and.depending on the ratio between fu11- and no-1oad power requirements,empty starting times can be three or four times faster than full load.The maintenance-free starting system is simple,low-cost and very reliable.However, they cannot control starting torque and maximum stall torque;therefore.they are limited to the low-power,simple-profile conveyor belt drives.Reduced-voltage starters.As conveyor power requirements increase,controlling the applied motor torque during the acceleration period becomes increasingly important.Because motor torque 1s a function of voltage,motor voltage must be controlled.This can be achieved through reduced-voltage starters by employing a silicon controlled rectifier(SCR).A common starting method with SCR reduced-voltage starters is to apply low voltage initially to take up conveyor belt slack.and then to apply a timed linear ramp up to full voltage and belt speed.However, this starting method will not produce constant conveyor belt acceleration.When acceleration is complete.the SCRs, which control the applied voltage to the electric motor.are locked in full conduction, providing fu11-line voltage to the motor.Motors with higher torque and pull—up torque,can provide better starting torque when combined with the SCR starters, which are available in sizes up to 750 KW.Wound rotor induction motors.Wound rotor induction motors are connected directly to the drive system reducer and are a modified configuration of a standard AC induction motor.By inserting resistance in series with the motor’s rotor windings.the modified motor control system controls motor torque.For conveyor starting,resistance is placed in series with the rotor for low initial torque.As the conveyor accelerates,the resistance is reduced slowly to maintain a constant acceleration torque.On multiple-drive systems.an external slip resistor may be left in series with the rotor windings to aid in load sharing.The motor systems have a relatively simple design.However, the control systems for these can be highly complex,because they are based on computer control of the resistance switching.Today,the majority of control systems are custom designed to meet a conveyor system’s particular specifications.Wound rotor motors are appropriate for systems requiring more than 400 kW .DC motor.DC motors.available from a fraction of thousands of kW ,are designed to deliver constant torque below base speed and constant kW above base speed to the maximum allowable revolutions per minute(r/min).with the majority of conveyor drives, a DC shunt wound motor is used.Wherein the motor’s rotating arma ture is connected externally.The most common technology for controlling DC drives is a SCR device.which allows for continual variable-speed operation.The DC drive system is mechanically simple, but can include complex custom-designed electronics to monitor and control the complete system.This system option is expensive in comparison to other soft-start systems.but it is a reliable, cost-effective drive inapplications in which torque,1oad sharing and variable speed are primary considerations.DC motors generally are used with higher-power conveyors,including complex profile conveyors with multiple-drive systems,booster tripper systems needing belt tension control and conveyors requiring a wide variable-speed range.1.2 Hydrokinetic couplingHydrokinetic couplings,commonly referred to as fluid couplings.are composed of three basic elements; the driven impeller, which acts as a centrifugal pump;the driving hydraulic turbine known as the runner and a casing that encloses the two power components.Hydraulic fluid is pumped from the driven impeller to the driving runner, producing torque at the driven shaft.Because circulating hydraulic fluid produces the torque and speed,no mechanical connection is required between the driving and driven shafts.The power produced by this coupling is based on the circulated fluid’s amount and density and the torque in proportion to input speed.Because the pumping action within the fluid coupling depends on centrifugal forces.the output speed is less than the input speed.Referred to as slip.this normally is between l% and 3%.Basic hydrokinetic couplings are available in configurations from fractional to several thousand kW .Fixed-fill fluid couplings.Fixed-fill fluid couplings are the most commonly used soft-start devices for conveyors with simpler belt profiles and limited convex/concave sections.They are relatively simple,1ow-cost,reliable,maintenance free devices that provide excellent soft starting results to the majority of belt conveyors in use today.Variable-fill drain couplings.Drainable-fluid couplings work on the same principle as fixed-fill couplings.The coupling’s impellers are mounted on the AC motor and the runners on the driven reducer high-speed shaft.Housing mounted to the drive base encloses the working circuit.The c oupling’s rotating casing contains bleed-off orifices that continually allow fluid to exit the working circuit into a separate hydraulic reservoir.Oil from the reservoir is pumped through a heat exchanger to a solenoid-operated hydraulic valve that controls the filling of the fluid coupling.To control the starting torque of a single-drive conveyor system,the AC motor current must be monitored to provide feedback to the solenoid control valve.Variable fill drain couplings are used in medium to high-kW conveyor systems and are available in sizes up to thousands of kW .The drives can be mechanically complex and depending on the control parameters.the system can be electronically intricate.The drive system cost is medium to high,depending upon size specified.Hydrokinetic scoop control drive.The scoop control fluid coupling consists of the three standard fluid coupling components:a driven impeller, a driving runner and a casing that encloses the working circuit.The casing is fitted with fixed orifices that bleed a predetermined amount of fluid into a reservoir.When the scoop tube is fully extended into the reservoir, the coupling is l00 percent filled.The scoop tube, extending outside the fluid coupling,is positioned using an electric actuator to engage the tube from the fully retracted to the fully engaged position.This control provides reasonably smooth acceleration rates.to but the computer-based control system is very complex.Scoop control couplings are applied on conveyors requiring single or multiple drives from l50 kW to 750 kW.1.3 Variable-frequency control(VFC)Variable frequency control is also one of the direct drive methods.The emphasizing discussion about it here is because that it has so unique characteristic and so good performance compared with other driving methods for belt conveyor.VFC devices Provide variable frequency and voltage to the induction motor, resulting in an excellent starting torque and acceleration rate for belt conveyor drives.VFC drives.available from fractional to several thousand(kW ), are electronic controllers that rectify AC line power to DC and,through an inverter, convert DC back to AC with frequency and voltage contro1.VFC drives adopt vector control or direct torque control(DTC)technology,and can adopt different operating speeds according to different loads.VFC drives can make starting or stalling according to any givenS-curves.realizing the automatic track for starting or stalling curves.VFC drives provide excellent speed and torque control for starting conveyor belts.and can also be designed to provide load sharing for multiple drives.easily VFC controllers are frequently installed on lower-powered conveyor drives,but when used at the range of medium-high voltage in the past.the structure of VFC controllers becomes very complicated due to the limitation of voltage rating of power semiconductor devices,the combination of medium-high voltage drives and variable speed is often solved with low-voltage inverters using step-up transformer at the output,or with multiple low-voltage inverters connected in series.Three-level voltage-fed PWM converter systems are recently showing increasing popularity for multi-megawatt industrial drive applications because of easy voltage sharing between the series devices and improved harmonic quality at the output compared to two-level converter systems With simple series connection ofdevices.This kind of VFC system with three 750 kW /2.3kV inverters has been successfully installed in ChengZhuang Mine for one 2.7-km long belt conveyor driving system in following the principle of three-level inverter will be discussed in detail.2 Neutral point clamped(NPC)three-level inverter using IGBTsThree-level voltage-fed inverters have recently become more and more popular for higher power drive applications because of their easy voltage sharing features.1ower dv/dt per switching for each of the devices,and superior harmonic quality at the output.The availability of HV-IGBTs has led to the design of a new range of medium-high voltage inverter usingthree-level NPC topology.This kind of inverter can realize a whole range with a voltage rating from 2.3 kV to 4.1 6 kV Series connection of HV-IGBT modules is used in the 3.3 kV and 4.1 6 kV devices.The 2.3 kV inverters need only one HV-IGBT per switch[2,3].2.1 Power sectionTo meet the demands for medium voltage applications.a three-level neutral point clamped inverter realizes the power section.In comparison to a two-level inverter.the NPC inverter offers the benefit that three voltage levels can be supplied to the output terminals,so for the same output current quality,only 1/4 of the switching frequency is necessary.Moreover the voltage ratings of the switches in NPC inverter topology will be reduced to 1/2.and the additional transient voltage stress on the motor can also be reduced to 1/2 compared to that of a two-level inverter.The switching states of a three-level inverter are summarized in Table 1.U.V and W denote each of the three phases respectively;P N and O are the dc bus points.The phase U,for example,is in state P(positive bus voltage)when the switches S1u and S2u are closed,whereas it is in state N (negative bus voltage) when the switches S3u and S4u are closed.At neutral point clamping,the phase is in O state when either S2u or S3u conducts depending on positive or negative phase current polarity,respectively.For neutral point voltage balancing,the average current injected at O should be zero.2.2 Line side converterFor standard applications.a l2-pulse diode rectifier feeds the divided DC-link capacitor.This topology introduces low harmonics on the line side.For even higher requirements a 24-pulse diode rectifier can be used as an input converter.For more advanced applications where regeneration capability is necessary, an active front.end converter can replace the dioderectifier, using the same structure as the inverter.2.3 Inverter controlMotor Contro1.Motor control of induction machines is realized by using a rotor flux.oriented vector controller.Fig.2 shows the block diagram of indirect vector controlled drive that incorporates both constant torque and high speed field-weakening regions where the PW M modulator was used.Inthis figure,the command flux is generated as function of speed.The feedback speed isadded with the feed forward slip command signal . the resulting frequency signal isintegrated and then the unit vector signals(cos and sin)are generated.The vector rotatorgenerates the voltage and angle commands for the PW M as shown.PWM Modulator.The demanded voltage vector is generated using an elaborate PWM modulator.The modulator extends the concepts of space-vector modulation to the three-level inverter.The operation can be explained by starting from a regularly sampled sine-triangle comparison from two-level inverter.Instead of using one set of reference waveforms and one triangle defining the switching frequency,the three-level modulator uses two sets of reference waveforms U r1 and U r2 and just one triangle.Thus, each switching transition is used in an optimal way so that several objectives are reached at the same time.Very low harmonics are generated.The switching frequency is low and thus switching losses are minimized.As in a two-level inverter, a zero-sequence component can be added to each set of reference waveform s in order to maximize the fundamental voltage component.As an additional degree of freedom,the position of the reference waveform s within the triangle can be changed.This can be used for current balance in the two halves of the DC-1ink.3 Testing resultsAfter Successful installation of three 750 kW /2.3 kV three-level inverters for one 2.7 km long belt conveyor driving system in Chengzhuang Mine.The performance of the whole VFC system was tested.Fig.3 is taken from the test,which shows the excellent characteristic of the belt conveyor driving system with VFC controller.Fig.3 includes four curves.The curve 1 shows the belt tension.From the curve it can be find that the fluctuation range of the belt tension is very smal1.Curve 2 and curve 3 indicate current and torque separately.Curve 4 shows the velocity of the controlled belt.The belt velocityhave the“s”shape characteristic.A1l the results of the test show a very satisfied characteristic for belt driving system.4 ConclusionsAdvances in conveyor drive control technology in recent years have resulted in many more reliable.Cost-effective and performance-driven conveyor drive system choices for users.Among these choices,the Variable frequency control (VFC) method shows promising use in the future for long distance belt conveyor drives due to its excellent performances.The NPC three-level inverter using high voltage IGBTs make the Variable frequency control in medium voltage applications become much more simple because the inverter itself can provide the medium voltage needed at the motor terminals,thus eliminating the step-up transformer in most applications in the past.The testing results taken from the VFC control system with NPC three.1evel inverters used in a 2.7 km long belt conveyor drives in Chengzhuang Mine indicates that the performance of NPC three-level inverter using HV-IGBTs together with the control strategy of rotor field-oriented vector control for induction motor drive is excellent for belt conveyor driving system.References[l] Jim Ehler. Conveyor drive technologies offer smooth, soft starts[J]. Motors& Drives, 2001(4): 28-35.[2] Sommer R, Mertens A. Medium voltage drive system with three-level NPC inverter using IGBTs[A]. IEE Colloquium on PWM Medium V oltage Drives[C]. Birmingham,2000[3] Mertens A, Sommer R, Brunotte C. Applications of medium voltage drives with IGBT three-level inverter[A]. IEE colloquium on PWM medium voltage drives[C]. Birmingham,2000中文译文:带式输送机及其牵引系统在运送大量的物料时,带式输送机在长距离的运输中起到了非常重要的竞争作用。
带式输送机英文文献翻译
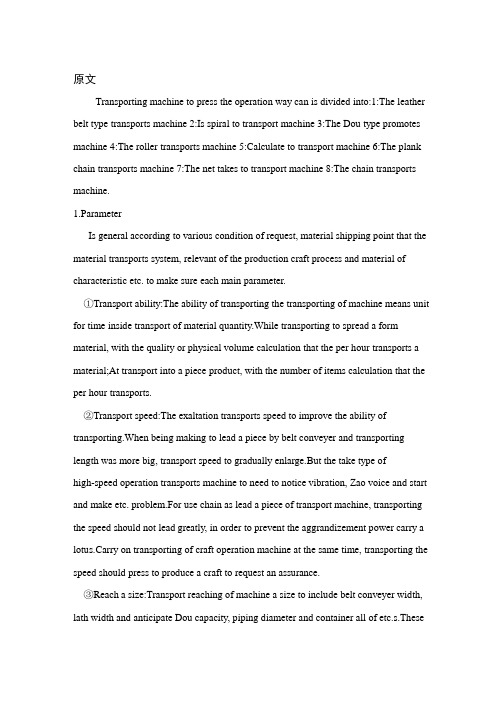
原文Transporting machine to press the operation way can is divided into:1:The leather belt type transports machine 2:Is spiral to transport machine 3:The Dou type promotes machine 4:The roller transports machine 5:Calculate to transport machine 6:The plank chain transports machine 7:The net takes to transport machine 8:The chain transports machine.1.ParameterIs general according to various condition of request, material shipping point that the material transports system, relevant of the production craft process and material of characteristic etc. to make sure each main parameter.①Transport ability:The ability of transporting the transporting of machine means unit for time inside transport of material quantity.While transporting to spread a form material, with the quality or physical volume calculation that the per hour transports a material;At transport into a piece product, with the number of items calculation that the per hour transports.②Transport speed:The exaltation transports speed to improve the ability of transporting.When being making to lead a piece by belt conveyer and transporting length was more big, transport speed to gradually enlarge.But the take type ofhigh-speed operation transports machine to need to notice vibration, Zao voice and start and make etc. problem.For use chain as lead a piece of transport machine, transporting the speed should not lead greatly, in order to prevent the aggrandizement power carry a lotus.Carry on transporting of craft operation machine at the same time, transporting the speed should press to produce a craft to request an assurance.③Reach a size:Transport reaching of machine a size to include belt conveyer width, lath width and anticipate Dou capacity, piping diameter and container all of etc.s.Thesereach a sizes to all directly influence to transport machine of transport ability.④Transport length and Qing Cape:Transport circuit length and Qing Cape size to directly influence the total resistance of transporting the machine and need of power. 2.Transport a machine the spot application wayConstitute to carry on explaining in detail from the take type machine system first:Leather belt's transporting machine is to spread a form material to transport and pack to unload an equipments most importantly, can extensively used for the mineral mountain, metallurgy, building materials, chemical engineering, electric power, industrial realms like food processing,etc, in the coal mine, metal mineral, the steel business enterprise, port, grounds like cement works,etc a great deal of application that can see skin machine, transporting the machine can not only complete to spread a transporting of form material, but also can transport into a piece material, but basis use location, work environment, transport the dissimilarity of material category, will also have bigger difference in its design and the application;Modernization of transport the machine system has higher request to the dust palliative, is this, in each the device that transfer place and establish and sprinkle water and gather a dust, transport machine and follow line in the tape will establish and defend a breeze cover or block an aerofoil, system from list the machine constitute of, to work in the whole machine system of operate and fix to say, want and have a foothold and divide the single machine of the tube at oneself, and want to understand mutual contact between systems, list machine again is constitute to°from many partses, only work well the daily maintenance of each parts maintains and makes it is placed in good work status so as to ensure the safe movement of equipments;We generally will transport the use place, work environment of machine according to the take type, technique function and transport material category to wait variousdissimilarity with satisfy various forms of homework work condition, in addition to in addition to transporting machine, the in general use leather belt of more adoption also various special kind tapes of new structure transport machine and have a mainly having of the representative among them:Big Qing Cape take type machine, deep slot take type machine and press take type machine, take care of the form take type, the air cushion take type, the flat surface turn take type, the line friction type, wave-like in shape the belt conveyer type blocking a side transport machine etc. and carry on a thin method for turning and canning exist various classifications and make following introduction now: Press the use classification, there is in general use ambulation type, under the well choice type, the strip mine is used a fixed type, special kind structure type, can move a place type and transport machine, load machine appropriation redistribution function type, the big Qing Cape type transports machine etc., generally speaking transport machine inside the short distance factory can complete level, up the luck or bottom carries, canning go against the wood grain type leather belt machine can be used for double to transport a material, hang arm machine usually install anticipate on board in the heap, and can turn round, line up the function of soil or cloth by realization, but Gao Jia Ji propped up by in the door usually match with other spread and anticipate and handle an equipments common use, for example give or get an electric shock and constuct a medium application in water, can install standard in the center frame, the machine's mounting places on the track Zhen, easy to move and place;Press the category of transporting the material to categorize, have the generally lax material is used of, the strong and tough material is used of and list piece the leather belt used in material transport machine etc. and press the rubber conveyance takes a loading segment of position to categorize, include a leather belt loading segment at top of and loading segment at underneath of and at the same time loading segment at upunderneath of double to transport machine three, the use double can distinguish to transporting machine at up branch and bottom branch transport a material, but for keeping material contact noodles don't produce a change and need to bring in to go to the rubber to be periodically inside out.3.CategorizeTransporting machine generally and pressing already didn't lead piece to carry on a classification and had to lead a transporting of piece machine to generally include to lead a piece, loading to reach a piece, drive device, bring to the stretch device and change to accept an etc. to the device and.Lead a piece to in order to deliver to lead dint, can adopt belt conveyer and lead chain or steel wire rope;The loading reaches a piece to in order to accept to put a material and has already anticipated Dou and bracket or mourns to have...etc.;Drive device to transport machine with the power, generally from electric motor, decelerate a machine and make machine(stop a machine) etc. to constitute;Bring to the stretch to equip to generally have the Luo pole the type and heavy hammer type 2 kind, can make to lead a piece to keep certain tension and hang a degree, transport machine by assurance normal operation;Pay to accept a piece to in order to accept to give to lead piece or loading to reach a piece, can adopt to give Gun and roll an etc..Having the structure characteristics that lead the transporting of piece machine is:Be delivered a material and pack reaching with the loading leading a link together inside the piece, or directly pack in leading a piece(is like belt conveyer), led a piece to once round each roller or the chain round beginning and end and connect with each other, formation include and deliver a having of material carry branch and don't deliver a material of have never carried shutting of branch and match wreath road, make use of lead continuous sport of piece and transport a material.This type ofly transporting model is numerous, there is mainly a take type transporting a machine, plank type andtransporting a machine, small car type and transporting machine, escalator, automatic sidewalk, paring off plank and transporting machine, covering up and paring off plank and transporting a machine, Dou type and transporting a machine, Dou type and promoting machine and hanging and transporting machine and build on stilts a cableway...etc..The structure that didn't lead transporting of piece machine constitutes each not same, use to the work of transporting the material to reach a piece as well not same.Their structure characteristicses are:Make use of a work to reach a revolving of piece to exercise or the back and forth exercise, or make use of lie quality to make the material transport forward in the fluxion in the piping.For example, the Gun son transports the work of machine to reach the piece as a series of Gun son, the Gun son makes to revolve sport to transport a material;Is spiral to transport the work of machine to reach a piece for spiral, helix at anticipate and make to revolve sport in the slot with follow anticipate slot to push to send a material;The vibration transports the work of machine to reach piece in order to anticipate slot, anticipate slot to make back and forth sport with transport Be placed to among them of material etc..Install(1)The fixed type transports machine should by rule gearing method gearing at fix of foundation up.The ambulation type transports machine formally before circulating and should live wheel with the wedge Xie or uses to make a machine to stop.So as not to take place to take a stroll in the work, there is the passage that many sets , between machine and machine, there shoulded be one meter between wall and machine while transporting a parallel homework of machine.(2)The beard checks an each operation part, tape to take to button up to equip with loading before using whether normal, whether protection equipments is well-found.Thetape rises a tight degree beard before starting the adjustment is to suitable extent.(3)Leather belt's transporting machine should get empty to carry a start.Waiting to revolve normal rear can go into to anticipate.Drive after forbiding to go into first to anticipate.(4)There are few set that when transport machine to establish to circulate should from unload to anticipate to carry a beginning, the sequence starts.After revolving as usual all, the square can go into to anticipate.(5)Appear in the movement when the tape runs to be partial to a phenomenon should park the car adjustment, can not force an use, so as not to wear away edge and increment burden.(6)Work environment and be sent material temperature not to must be higher than50 ℃ and be lower than-10 ℃ .Can not transport the material of having sour alkaline oil and organic melting agent composition.(7)Forbid pedestrian or multiply by a person on the belt conveyer.(8)Have to stop going into first to anticipate before parking the car, wait leather belt up save to anticipate to unload to the utmost a square can park the car.(9)Transporting the machine electric motor has to insulate good.The ambulation type transports machine electric cable to pull and drag along indiscriminately.The dynamoelectric confidential credibility connects ground.(10)The leather belt beats slippery strictly forbid to by hand pull leather belt, so as not to take place trouble.5.Adjust to try(1) Each equipments with meticulous care adjusts to try to transport machine after installing and satisfies a drawing request.(2) Each deceleration machine exercises parts to add to note to correspond lubricant.(3) The gearing after transporting machine to attain to request each single set equipments carries on beginning to work to make run-in, and knot to put together to adjust to try to transport machine to satisfy an operative request.(4) Adjust to try the electricity part of transporting the machine.Include to connect adjusting of line and action to try to the normal regulations electricity, make the equipments have good function, attain the function and status of design.6.Transport machine to block knothole 2 kinds of boring crafts(1)Blow up boring:The material after the irradiation of continuous laser and centrally forms one cave pit, then from and laser beam the coaxial oxygen flow to clean meltdown material and form one bore very quickly.The size of general bore is as thick relevant as plank, blow up to bore hole the average diameter as thick plank half, therefore blow up to bore hole bore path bigger to thicker plank, and not circle, should not in requesting higher spare parts use(if the petroleum Shai sews a tube), can be used for a waste up.In addition because of bore hole use of oxygen pressure with incise homology, splash a little bit greatly.(2)Pulse boring:The pulse laser that adopts high peak value power makes a little amount material melt or vaporizes, in common use air or nitrogen spirit are to lend support to air and oxidize to make bore expand because of putting heat by decrease, the air pressure more incises of the oxygen pressure is small.The particle jet with small creation of each pulse laser gradually goes deep into, therefore slab boring time takes several seconds.Once bore hole completion, immediately change assistance air into oxygen to carry on incising.Boring hole diameter like this is smaller, its boring quality is better than to blow up boring.Not only should have higher exportation power for the laser machine used by this;The time and space characteristic that more important time ties, therefore the general crosscurrent carbon dioxide laser machine can not adapt to therequest that the laser incises.In addition the pulse bores hole to also have the more dependable spirit road the control system to carry out cutting over of air category, air pressure and bore hole a horary control.译文:输送机按运作方式可以分为:1:皮带式输送机2:螺旋输送机3:斗式提升机4:滚筒输送机5:计量输送机6:板链输送机7:网带输送机8:链条输送机。
带式输送机英文和翻译

带式输送机自动维护系统方法Prof.dr.ir. Gabriel LodewijksDeIft荷兰理工大学概要本文论述了带式输送机系统维修自动化,特别是托辊。
自动维护是一种很有前途的护方法,这种维护方法能够大大提高维护的效率,维护精度,并能够降低维护成本。
为了更有效优化自动维护工作,维修供电的台车,能够在一个自主带式输送机的结构是作为维护系统平台调整。
在这台上安装振动分析的数据采集设备,台车可以通过自动维修系统,在台车上或者电脑中央板收集数据。
最优化维修方法是视逻辑模拟模型而定,模拟模型是带式输送机设计布局的本身。
通过模拟模型也能得出带式输送机其他组成部件精确的剩余寿命信息。
引言现在,越来越多公司为了平衡预算,通过长期接收训练有素经验丰富的人员,减少长期外包维修专业工作人员人数。
但现实上难以实现,很多公司与外部企业没有足够的维修经验。
一般来说,在皮带输送系统的维修,可分为条件检查或整个系统的监测和更换和/或赔偿(简称服务的组成部分)。
与外包维修工程遇到检查或状况的系统检测大多问题一样。
这些问题不是不值得探讨,有时移动带式输送机组件的状态。
有同样经验的人应该进行定期检查机器,以避免同样问题出现。
为了克服由外包维修人员经验不足所造成的运作问题,对带式输送机组件可以自动检查。
这样的知识,例如磨损率和更换的时间表可以建立在数据基础制度。
外包维修人员则可以用来代替消减组件。
另外,也可以自动更换组件。
本文讨论的皮带输送系统自动维护的方法和技巧。
第2部分是智能维修的概念,第3部分是研究现有应用于智能维修系统的检查系统,第4部分讨论评估带式输送机旋转部件基于振动的检测概念的地位,第5部分提出一个研究案例,第6部分是结论和建议。
智能维修带式输送系统的维修,可分为条件和整个系统及其组成部分的监测服务。
状态监测的定义是连续或定期测量和解释数据显示组件的条件,以决定是否需要更换或维修,因此,检测状态处理获得(数据采集或从传感器采集)的数据,同时解释该数据,并采取纠正行动,从而防住系统故障的发展和普及。
带式输送机外文文献翻译、中英文翻译
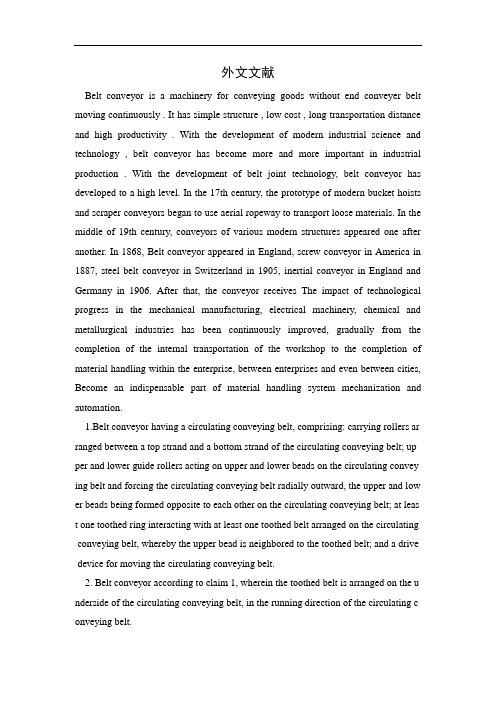
外文文献Belt conveyor is a machinery for conveying goods without end conveyer belt moving continuously . It has simple structure , low cost , long transportation distance and high productivity . With the development of modern industrial science and technology , belt conveyor has become more and more important in industrial production . With the development of belt joint technology, belt conveyor has developed to a high level. In the 17th century, the prototype of modern bucket hoists and scraper conveyors began to use aerial ropeway to transport loose materials. In the middle of 19th century, conveyors of various modern structures appeared one after another. In 1868, Belt conveyor appeared in England, screw conveyor in America in 1887, steel belt conveyor in Switzerland in 1905, inertial conveyor in England and Germany in 1906. After that, the conveyor receives The impact of technological progress in the mechanical manufacturing, electrical machinery, chemical and metallurgical industries has been continuously improved, gradually from the completion of the internal transportation of the workshop to the completion of material handling within the enterprise, between enterprises and even between cities, Become an indispensable part of material handling system mechanization and automation.1.Belt conveyor having a circulating conveying belt, comprising: carrying rollers ar ranged between a top strand and a bottom strand of the circulating conveying belt; up per and lower guide rollers acting on upper and lower beads on the circulating convey ing belt and forcing the circulating conveying belt radially outward, the upper and low er beads being formed opposite to each other on the circulating conveying belt; at leas t one toothed ring interacting with at least one toothed belt arranged on the circulating conveying belt, whereby the upper bead is neighbored to the toothed belt; and a drive device for moving the circulating conveying belt.2. Belt conveyor according to claim 1, wherein the toothed belt is arranged on the u nderside of the circulating conveying belt, in the running direction of the circulating c onveying belt.3. Belt conveyor according to claim 2, wherein the toothed ring is arranged at the e nd of the carrying rollers, and wherein projecting from the end of a first carrying rolle r is a journal for the connection of the drive device.4. Belt conveyor according to claim 3, wherein the toothed belt extends in the regio n of the side border of the circulating conveying belt.5. Belt conveyor according to claim 1, wherein the toothed belt and the toothed ring have multisplining.6. Belt conveyor according to claim 1, wherein Kevlar filaments are incorporated i n the toothed belt.7. Belt conveyor according to claim 1, wherein the toothed belt is attached on the c irculating conveying belt via one of welding, vulcanizing, and adhesively bonding the reto.8. Belt conveyor having a circulating conveying belt, comprising: carrying rollers a rranged between a top strand and a bottom strand of the circulating conveying belt; an d a drive device and a force-transmission device for moving the conveying belt, where in a pair of elements which interact with one another with a form fit is provided for fo rce-transmission purposes, one of said elements being assigned to the force-transmissi on device and the other of said elements being assigned to the conveying belt, wherei n the force-transmission device comprises at least one toothed ring, and wherein the ci rculating conveying belt has at least one toothed belt, the toothed ring and toothed belt interacting with a form fit, wherein the toothed belt is a constituent part of a toothed-belt component which is of essentially U-shaped design in the transverse direction of t he toothed belt and engages around the side-border region of the conveying belt.9. Belt conveyor according to claim 8, wherein the toothed ring is assigned at least t o a first belt-conveyor carrying roller, which is operatively connected to the drive devi ce.10. Belt conveyor according to claim 8, further comprising a counterpressure devic e, which acts on that region of the toothed-belt component which extends on the top si de of the circulating conveying belt.11. Belt conveyor according to claim 8, wherein the free ends of the essentially U-shaped toothed-belt component are designed as a bead.12. Belt conveyor according to claim 8, further comprising guide rollers, which act on one of the toothed belt and the toothed-belt component.13. Belt conveyor having a circulating conveying belt, comprising: carrying rollers arranged between a top strand and a bottom strand of the circulating conveying belt; u pper and lower guide rollers acting on upper and lower beads on the circulating conve ying belt and forcing the circulating conveying belt radially outward, the upper and lo wer beads being formed opposite to each other on the circulating conveying belt; at le ast one toothed ring interacting with at least one toothed belt formed on the circulating conveying belt, whereby the upper bead is neighbored to the toothed belt; and a drive device for moving the circulating conveying belt, wherein a pair of said guide rollers are arranged on angled retaining arms such that the guide rollers act on one of the toot hed belt and the upper and lower beads, by way of inclined running surfaces.14. Belt conveyor according to claim 12, wherein in each case one pair of guide rol lers on the top strand and on the bottom strand of the circulating conveying belt act on one of the toothed belt and the toothed-belt component, extending over the entire bor der region of the circulating conveying belt.15. Belt conveyor according to claim 1, wherein the carrying rollers are of conical configuration and form a belt curve, and wherein the toothed ring undergoes a form-fi tting connection in relation to the circulating conveying belt at the larger-diameter end of the respective carrying roller on the outer radius of the belt curve.16. The belt driving device of claim 1, wherein one of said toothed ring and said to othed belt is releasably fixed to the carrying rollers.Belt conveyor according to claim 16, wherein one of said toothed ring and said toot hed belt is releasably fixed to the force-transmission device by one of.The present invention relates to a belt conveyor having a circulating conveying belt , having carrying rollers, which are arranged between the top strand and the bottom str and of the conveying belt, and having a drive device and a force-transmission device f or moving the conveying belt.BACKGROUND OF THE INVENTIONIt is known from practice for force to be transmitted from the drive device to the co nveying belt of a belt conveyor via friction fitting. The friction between a driven carry ing roller and the conveying belt, for example, may even be sufficient for this purpose . The rest of the carrying rollers are mounted in a movable manner and rotate along. DE 42 44 170 C2Discloses a belt conveyor having an endless conveying belt, the latter being driven by means of a force-transmission device which is present in the form of a friction whe el. A drive shaft extends beneath the bottom strand of the conveying belt. On the inner radius of the belt curve, a motor is connected as a drive device to the drive shaft and, in the region of the outer radius, a friction wheel is seated on the drive shaft and is in c ontact with the outer surface of the conveying belt. In this case, the friction wheel inte racts with a carrying roller functioning as counterpressure roller. The drive shaft is mo unted such that it can be moved at an angle both in the region of the outer radius and i n the region of the inner radius of the belt curve.Theangle mounting of the drive shaft allows adaptation of the exent towhich the friction movablewheel is pressed against the conveying belt in proportion t o the actual load. In this way, the wear is reduced if, in part-load operation, the conve ying belt is only subjected to the contact-pressure force which is necessary for this pur pose.Although the belt conveyor known from DE 42 44 170 C2 reduces the wear of the c onveying belt, it cannot rule it out altogether. The task of conveying foodstuffs or othe r goods which are to be kept clean involves, in addition to the mechanical damage to t he conveying belt, the aspect of hygiene and of keeping goods clean. The abraded surf ace particles of the conveying belt could have a considerable adverse effect on the qua lity of the goods which are to be conveyed. Moreover, the known belt conveyor requir es an extremely high level of structural outlay as far as the movable mounting of the s eparate drive shaft is concerned.Taking as departure point the belt conveyor known from DE 42 44 170 C2, the obje ct of the invention is to specify a belt conveyor of the type in question which largely r ules out any adverse effect to the surface of the coconveying belt of the belt conveyorby the force-transmission device. According to a particularly preferred configuration, the belt conveyor is intended to require just a low level of structural outlay.The above object is achieved by the features of Patent claim 1. According to the latt er, a belt conveyor of the type in question is configured such that a pair of elements w hich interact with one another with a form fit is provided for force-transmission purpo ses, and that one element is assigned to the force-transmission device and the other ele ment is assigned to the conveying belt. According to the invention, it has been found t hat the surface of the conveying belt is not adversely affected as a result of the action of the force-transmission device if a separate pair of elements is provided in order to r ealize force transmission. It has also been found that the use of a pair of movement-co nverting elements which are known per se and interact with one another with a form fi t largely eliminates the disadvantages which are known in the case of friction-fitting movement conversion, in particular wear and abrasion.According to a preferred exemplary embodiment of the belt conveyor according to t he invention, the pair of elements could be present as toothed ring and toothed belt, th e tooth flanks of the toothed ring and of the toothed belt interacting with one another. It would be possible for the toothed ring to be assigned to the force-transmission devic e and for the toothed belt to be assigned to the conveying belt.As far as a particularly low level of structural outlay is concerned, a preferred confi guration of the abovementioned exemplary embodiment provides that the toothed ring is assigned to a carrying roller, and the latter thus simultaneously assumes the role of the force-transmission device. Via a journal projecting from the carrying roller, the dri ve takes place by means of a motor. The toothed ring could be plugged onto the carryi ng roller and fixed releasably—for example via a shaft/hubconnection or a feather key —to the same.In the case of a plugged-on toothed ring, it isadvantageous that it is possible to use carrying rollers which are already present. It is particularly advantageous for each carr ying roller to be assigned at least one toothed ring. Over the entire running path of the conveying belt, it would then be the case that the toothed belt and the toothed rings int erengage and move the conveying belt in a dimensionally stable manner. Corresponding to the toothed ring or rings which is/are arranged between the top and bottom stran ds and belongs/belong to the preferred configuration mentioned above, the toothed bel t is arranged on the underside of the conveying belt, and extends in the running directi on of the same. Arranging the toothed belt on the underside of the conveying belt onc e again ensures that the top side of the conveying belt, which is charged if appropriate with goods which are to be kept clean, is not subject to any force transmission, mecha nical damage or production of abrasion particles or other contaminants.An expedient development of the preferred configuration of the belt conveyor acco rding to the invention makes provision for the toothed ring to be arranged at the end o f the carrying roller. As a result, on the one hand, straightforward maintenance of the f orce-transmission device is made possible and, on the other hand, this arrangement is also more cost-effective than a, for example, central arrangement. Direct force transmi ssion over a short distance is achieved by a journal for the connection of the drive dev ice projecting from that end of the carrying roller which is provided with the toothed r ing.It is particularly advantageous if the toothed belt extends in the region of the side b order of the conveying belt. As a result, on the one hand, straightforward production o f the conveying belt with the toothed belt is made possible by the direct relationship to the border region and, on the other hand, a role is also played here by the accessibilit y to the pair of elements for maintenance purposes and, of course, by the coordination between the toothed belt and the arrangement of the toothed ring.In addition to toothed belts and toothed rings with normal toothing, it would also b e possible to realize multisplining. This further reduces undesired sliding and thus we ar, heating and noise development. In order to absorb high tensile forces, it would be possible for Kevlar filaments to be incorporated in the toothed belt, which usually con sists of plastic. It would be possible for the conveying belt to be produced with the too thed belt by welding, vulcanizing or adhesive bonding. According to a particularly pre ferred configuration, it would be possible for the toothed belt to be a constituent part o f a toothed- belt component which is of essentially U-shaped design in the transverse direction of the toothed belt.The U-shape makes it possible for the toothed- belt component simply to be plugge d onto the border of the conveying belt until the border region has come into contact with the base part between the U-legs. The inner surface of the toothed- belt compone nt may have been provided with adhesive beforehand. As a result of its shaping and of being produced in this way, the toothed- belt component engages around the side-bor der region of the conveying belt.While the toothed belt of the conveying belt is subjected to compressive force by th e toothed ring, and this largely rules out detachment of the toothed- belt component o n the underside of the conveying belt, a counterpressure device could be provided in o rder to secure that region of the toothed- belt component which extends on the top sid e of the conveying belt. In design terms, the leg of the counterpressure device could b e present in the form of an arm which acts on the U-toothed- belt component on the to p side and thus constantly presses the same onto the top side of the conveying belt. As far as reliable guidance is concerned, it would be possible for the toothed belt or the toothed- belt component containing the toothed belt to form a bead. A bead ridge is thus produced over the length of the conveying belt. In the case of a U-shaped tooth ed- belt component, the bead ridge extends in each case at the free ends of the U-legs, at a distance from the border of the conveying belt, the distance depending essentially on the width of the toothed belt. As an alternative to a bead ridge, it would be possible for the toothed- belt component or for the straightforward toothed belt also to have at least one beveled free end. The guidance measure taken on the toothed belt or on the s pecific toothed- belt component is provided in order that a guide roller or a pair of gui de rollers acts on the beveled surface or on the bead or bead ridge. The guidance meas ure explained above could be taken equally well in the case of belt curves and straight belt lines and of belt S-shapes bridging different heights.In the case of belt curves, the force acting on the conveying belt is directed toward the inner radius of the belt curve, with the result that the guide rollers, in an advantage ous manner which is known per se, could have inclined running surfaces. Correspondi ngly angled retaining arms as a constituent part of retaining structures for the guide ro llers could be arranged in each case in the region of a carrying roller. The guide rollers could be arranged in pairs on the top strand and on the bottom strand of the conveyi ng belt.It should be emphasized at this point that, with the abovementioned configuration o f the belt conveyor according to the invention having the bead or beveled free ends, t wo functions are combined in the pair of form-fitting elements. Not only the force tra nsmission, but also the guidance of the conveying belt, takes place. The dimensional s tability of the conveying belt isadvantageously increased by the pair of form-fitting el ements with the specific configuration of the toothed belt or of the toothed- belt comp onent for action of the guide rollers thereon.In the case of the already cited design of the belt conveyor in the form of a belt curv e, the carrying rollers are of conical design and the toothed ring is arranged at the larg er-diameter end of the respective carrying roller, that is to say on the outer radius of th e belt curve. The drive device is present as a motor and is assigned to the first carrying roller of the belt curve. The form-fitting interengagement of the toothed wheel and to othed belt takes place in the region of each carrying roller, the form fit, in relation to t he first, motor-driven carrying roller, serving for force-transmission purposes and, in r elation to the rest of the rollers, serving for guiding the conveying belt.The previously explained principle of force transmission via a pair of elements w hich interact with one another with a form fit could also be used in the case of a straig ht belt line or in the case of a height-changing belt S-shape. Here, the carrying rollers are of a cylindrical design and the force transmission takes place—as with the belt cur ve—at a first carrying roller, while the followingcarrying rollers, likewise equipped w ith the pair of form-fitting elements, serve for guiding the conveying belt. In contrast t o the belt curve, however, it would be possible, in the case of the straight belt line or i n the case of the belt S-shape, for the pair of elements to be arranged at the two free e nds of the respective carrying roller and on the two border regions of the conveying b elt. It would thus be possible specifically for the two border regions of the conveying belt to have a toothed belt or a toothed- belt component which interacts with the tooth ed rings at the two free ends ofeac carrying roller. Furthermore, it would also be possible, with these types of construction of the belt conveyor according to the invention, to provide guide rollers.A further advantage of the preferred embodiment of the belt conveyor according to th e invention, the toothed ring and toothed belt interacting, consists in the improved cap acity for controlling the belt speed in accordance with the current loading. It would be possible to provide a control device which senses a change in the speed by correspon ding measuring sensors and adjusts the power of the drive device in line with the safet y regulations.In comparison with the force transmission realized by friction fitting, the belt con veyor according to the invention not only has the advantage of better capacity for cont rol, but also has the advantage that the conveying belt has a high level of dimensional stability as a result of the guidance by means of the pair of form-fitting elements and b y means of the pairs of guide rollers and can be subjected to higher torques. Overall, it is possible to achieve an increased level of drive power during start-up. In the case of the belt conveyor according to the invention being designed in the form of a belt curv e with an inner radius of 400 mm, the carrying rollers rotate at 230 rpm at a maximum speed of 1.5 m/sec.There are various possibilities then, of advantageously configuring and developin g the teaching of the present invention. For this purpose, reference is made, on the one hand, to the claims subordinate to Patent claim 1 and, on the other hand, to the follow ing explanation of an exemplary embodiment of the invention with reference to the dr awing. In conjunction with the explanation of the cited exemplary embodiment of the invention, generally preferred configurations anddevelopments of the teaching are also explained.中文译文带式输送机是连续运动的无端输送带输送货物的机械。
带式输送机技术的最新发展外文文献翻译、中英文翻译、外文翻译

附录Ⅰ英文文献翻译附录A带式输送机技术的最新发展M. A. AlspaughOverland Conveyor Co., Inc.MINExpo 2004拉斯维加斯, 内华达州,美国,2004.9.27摘要粒状材料运输要求带式输送机具有更远的输送距离、更复杂的输送路线和更大的输送量。
为了适应社会的发展,输送机需要在系统设计、系统分析、数值仿真领域向更高层次发展。
传统水平曲线和现代中间驱动的应用改变和扩大了带式输送机发展的可能性。
本文回顾了为保证输送机的可靠性和可用性而运用数字工具的一些复杂带式输送机。
前言虽然这篇文章的标题表明在皮带输送机技术中将提出“新”发展,但是提到的大多思想和方法都已存在很长时间了。
我们不怀疑被提出一些部件或想法将是“新”的对你们大部分人来说。
所谓的“新”就是利用成熟的技术和部件组成特别的、复杂的系统;“新”就是利用系统设计工具和方法,汇集一些部件组成独特的输送机系统,并解决大量粒状原料的装卸问题;“新”就是在第一次系统试验(委任)之前利用日益成熟的计算机技术进行准确节能计算机模拟。
同样,本文的重点是特定复杂系统设计及满足长距离输送的要求。
这四个具体课题将覆盖:1、托辊阻力2、节能3、动力分散4、分析与仿真节能减小设备整体电力消费是所有项目的一个重要方面,皮带输送机是也不例外。
虽然与其他运输方法比较皮带输送机总是运输大吨位高效率的手段,但是减少带式输送机的功率消耗的方法还是很多的。
皮带输送机的主要阻力组成部分有:a.托辊阻力b.托辊与皮带的摩擦力c.材料或输送带弯曲下垂引起的阻力这些阻力加上一些混杂阻力组成输送材料所需的力。
1在一台输送长度400米的典型短距离输送机中,力可以分为如图1所示的几个部分,图中可以看出提升力所占比例最大,而阻力还是占绝大部分。
图1在高倾斜输送带中如矿用露天倾斜输送带,所受力可分解为图2所示的几个部分,其中提升力仍占巨大比例。
由于重力是无法避免的,因此没有好的方法减少倾斜式输送机所受力。
皮带机输送机中英文对照外文翻译文献

皮带机输送机中英文对照外文翻译文献中英文资料翻译中文:带式输送机及其牵引系统在运送大量的物料时,带式输送机在长距离的运输中起到了非常重要的竞争作用。
输送系统将会变得更大、更复杂,而驱动系统也己经历了一个演变过程,并将继续这样下去。
如今,较大的输送带和多驱动系统需耍更大的功率,比如3驱动系统需耍给输送带750KW(成庄煤矿输送机驱动系统的要求)。
控制驱动力和加速度扭矩是输送机的关键。
一个高效的驱动系统应该能顺利的运行,同时保持输送带张紧力在指定的安全极限负荷内。
为了负载分配在多个驱动上,扭矩和速度控制在驱动系统的设计中也是很重要的因素。
由于输送机驱动系统控制技术的进步,目前更多可靠的低成本和高效驱动的驱动系统可供顾客选择[1]1带式输送机驱动1. 1带式输送机驱动方式全电压启动在全电压启动设计中,带式输送机驱动轴通过齿轮传动直接连接到电机。
直接全压驱动没有为变化的传送负载提供任何控制,根据满载和空载功率需求的比率,空载启动时比满载可能快3-4倍。
此种方式的优点是:免维护,启动系统简单,低成本,可靠性高。
但是,不能控制启动扭矩和最大停止扭矩。
因此,这种方式只用于低功率,结构简单的传送驱动中。
降压启动随着传送驱动功率的增加,在加速期间控制使用的电机扭矩变得越来越重要。
由于电机扭矩是电压的函数,电机电压必须得到控制,一般用可控硅整流器(SCR}构成的降压启动装置,先施加低电压拉紧输送带,然后线性的增加供电电压直到全电压和最大带速。
但是,这种启动方式不会产生稳定的加速度,当加速完成时,控制电机电压的SCR 锁定在全导通,为电机提供全压。
此种控制方式功率可达到750kW。
绕线转子感应电机绕线转子感应电机直接连接到驱动系统减速机上,通过在电机转子绕组中串联电阻控制电机转矩。
在传送装置启动时,把电阻串联进转子产生较低的转矩,当传送带加速时,电阻逐渐减少保持稳定增加转矩。
在多驱动系统中,一个外加的滑差电阻可能将总是串联在转子绕组回路中以帮助均分负载。
机械毕业设计英文外文翻译94带式输送机及其牵引系统

外文翻译英文原文Belt Conveying Systems Development of driving systemAmong the methods of material conveying employed,belt conveyors playa very important part in the reliable carrying of material over longdistances at competitive cost.Conveyor systems have become larger and more complex and drive systems have also been going through a process of evolution and will continue to do so.Nowadays,bigger belts require more power and have brought the need for larger individual drives as well as multiple drives such as 3 drives of 750 kW for one belt(this is the case for the conveyor drives in Chengzhuang Mine).The ability to control drive acceleration torque is critical to belt conveyors’performance.An efficient drive system should be able to provide smooth,soft starts while maintaining belt tensions within the specified safe limits.For load sharing on multiple drives.torque and speed control are also important considerations in the drive system’s design.Due to the advances in conveyor drive control technology,at present many more reliable.Cost-effective and performance-driven conveyor drive systems covering a wide range of power are available for customers’ choices[1].1 Analysis on conveyor drive technologies1.1 Direct drivesFull-voltage starters.With a full-voltage starter design,the conveyor head shaft is direct-coupled to the motor through the gear drive.Direct full-voltage starters are adequate for relatively low-power, simple-profile conveyors.With direct fu11-voltage starters.no control is provided for various conveyor loads and.depending on the ratio between fu11-and no-1oad power requirements,empty starting times can be three or four times faster than full load.The maintenance-free starting system is simple,low-cost and very reliable.However, they cannot control starting torque and maximum stall torque;therefore.they arelimited to the low-power, simple-profile conveyor belt drives.Reduced-voltage starters.As conveyor power requirements increase,controlling the applied motor torque during the acceleration period becomes increasingly important.Because motor torque 1s a function of voltage,motor voltage must be controlled.This can be achieved through reduced-voltage starters by employing a silicon controlled rectifier(SCR).A common starting method with SCR reduced-voltage starters is to apply low voltage initially to take up conveyor belt slack.and then to apply a timed linear ramp up to full voltage and belt speed.However, this starting method will not produce constant conveyor belt acceleration.When acceleration is complete.the SCRs, which control the applied voltage to the electric motor. are locked in full conduction, providing fu11-line voltage to the motor.Motors with higher torque and pull—up torque,can provide better starting torque when combined with the SCR starters, which are available in sizes up to 750 KW.Wound rotor induction motors.Wound rotor induction motors are connected directly to the drive system reducer and are a modified configuration of a standard AC induction motor.By inserting resistance in series with the motor’s rotor windings.the modified motor control system controls motor torque.For conveyor starting,resistance is placed in series with the rotor for low initial torque.As the conveyor accelerates,the resistance is reduced slowly to maintain a constant acceleration torque.On multiple-drive systems.an external slip resistor may be left in series with the rotor windings to aid in load sharing.The motor systems have a relatively simple design.However, the control systems for these can be highly complex,because they are based on computer control of the resistance switching.Today,the majority of control systems are custom designed to meet a conveyor system’s particular specifications.Wound rotor motors are appropriate for systems requiring more than 400 kW .DC motor.DC motors.available from a fraction of thousands of kW ,are designed to deliver constant torque below base speed and constant kW above base speed to the maximum allowable revolutions per minute(r/min).with the majority of conveyor drives, a DC shunt wound motor is used.Wherein the motor’s rotating armatureis connected externally.The most common technology for controlling DC drives is a SCR device. which allows for continual variable-speed operation.The DC drive system is mechanically simple, but can include complex custom-designed electronics to monitor and control the complete system.This system option is expensive in comparison to other soft-start systems.but it is a reliable, cost-effective drive in applications in which torque,1oad sharing and variable speed are primary considerations.DC motors generally are used with higher-power conveyors,including complex profile conveyors with multiple-drive systems,booster tripper systems needing belt tension control and conveyors requiring a wide variable-speed range.1.2 Hydrokinetic couplingHydrokinetic couplings,commonly referred to as fluid couplings.are composed of three basic elements; the driven impeller, which acts as a centrifugal pump;the driving hydraulic turbine known as the runner and a casing that encloses the two power components.Hydraulic fluid is pumped from the driven impeller to the driving runner, producing torque at the driven shaft.Because circulating hydraulic fluid produces the torque and speed,no mechanical connection is required between the driving and driven shafts.The power produced by this coupling is based on the circulated fluid’s amount and density and the torque in proportion to input speed.Because the pumping action within the fluid coupling depends on centrifugal forces.the output speed is less than the input speed.Referred to as slip.this normally is between l% and 3%.Basic hydrokinetic couplings are available in configurations from fractional to several thousand kW .Fixed-fill fluid couplings.Fixed-fill fluid couplings are the most commonly used soft-start devices for conveyors with simpler belt profiles and limited convex/concave sections.They arerelatively simple,1ow-cost,reliable,maintenance free devices that provide excellent soft starting results to the majority of belt conveyors in use today.Variable-fill drain couplings.Drainable-fluid couplings work on the same principle as fixed-fill couplings.The coupling’s impellers are mounted on the AC motor and the runners on the driven reducer high-speed shaft.Housing mounted to the drive base encloses the working circuit.The coupling’s rotating casingcontains bleed-off orifices that continually allow fluid to exit the working circuit into a separate hydraulic reservoir.Oil from the reservoir is pumped through a heat exchanger to a solenoid-operated hydraulic valve that controls the filling of the fluid coupling.To control the starting torque of a single-drive conveyor system,the AC motor current must be monitored to provide feedback to the solenoid control valve.Variable fill drain couplings are used in medium to high-kW conveyor systems and are available in sizes up to thousands of kW .The drives can be mechanically complex and depending on the control parameters.the system can be electronically intricate.The drive system cost is medium to high, depending upon size specified.Hydrokinetic scoop control drive.The scoop control fluid coupling consists of the three standard fluid coupling components:a driven impeller, a driving runner and a casing that encloses the working circuit.The casing is fitted with fixed orifices that bleed a predetermined amount of fluid into a reservoir.When the scoop tube is fully extended into the reservoir, the coupling is l00 percent filled.The scoop tube, extending outside the fluid coupling,is positioned using an electric actuator to engage the tube from the fully retracted to the fully engaged position.This control provides reasonably smooth acceleration rates.to but the computer-based control system is very complex.Scoop control couplings are applied on conveyors requiring single or multiple drives from l50 kW to 750 kW.1.3 Variable-frequency control(VFC)Variable frequency control is also one of the direct drive methods.The emphasizing discussion about it here is because that it has so unique characteristic and so good performance compared with other driving methods for belt conveyor. VFC devices Provide variable frequency and voltage to the induction motor, resulting in an excellent starting torque and acceleration rate for belt conveyor drives.VFC drives.available from fractional to several thousand(kW ), are electronic controllers that rectify AC line power to DC and,through an inverter, convert DC back to AC with frequency and voltage contro1.VFC drives adopt vector control or direct torque control(DTC)technology,and can adopt different operatingspeeds according to different loads.VFC drives can make starting or stalling according to any given S-curves.realizing the automatic track for starting or stalling curves.VFC drives provide excellent speed and torque control for starting conveyor belts.and can also be designed to provide load sharing for multiple drives.easily VFC controllers are frequently installed on lower-powered conveyor drives,but when used at the range of medium-high voltage in the past.the structure of VFC controllers becomes very complicated due to the limitation of voltage rating of power semiconductor devices,the combination of medium-high voltage drives and variable speed is often solved with low-voltage inverters using step-up transformer at the output,or with multiple low-voltage inverters connected in series.Three-level voltage-fed PWM converter systems are recently showing increasing popularity for multi-megawatt industrial drive applications because of easy voltage sharing between the series devices and improved harmonic quality at the output compared to two-level converter systems With simple series connection of devices.This kind of VFC system with three 750 kW /2.3kV inverters has been successfully installed in ChengZhuang Mine for one 2.7-km long belt conveyor driving system in following the principle of three-level inverter will be discussed in detail.2 Neutral point clamped(NPC)three-level inverter using IGBTsThree-level voltage-fed inverters have recently become more and more popular for higher power drive applications because of their easy voltage sharing features.1ower dv/dt per switching for each of the devices,and superior harmonic quality at the output.The availability of HV-IGBTs has led to the design of a new range of medium-high voltage inverter using three-level NPC topology.This kind of inverter can realize a whole range with a voltage rating from 2.3 kV to 4.1 6 kV Series connection of HV-IGBT modules is used in the 3.3 kV and 4.1 6 kV devices.The 2.3 kV inverters need only one HV-IGBT per switch[2,3].2.1 Power sectionTo meet the demands for medium voltage applications.a three-level neutral point clamped inverter realizes the power section.In comparison to a two-level inverter.the NPC inverter offers the benefit that three voltage levels can besupplied to the output terminals,so for the same output current quality,only 1/4 of the switching frequency is necessary.Moreover the voltage ratings of the switches in NPC inverter topology will be reduced to 1/2.and the additional transient voltage stress on the motor can also be reduced to 1/2 compared to that of a two-level inverter.The switching states of a three-level inverter are summarized in Table 1.U.V and W denote each of the three phases respectively;P N and O are the dc bus points.The phase U,for example,is in state P(positive bus voltage)when theswitches S1u and S2uare closed,whereas it is in state N (negative bus voltage)when the switches S3u and S4uare closed.At neutral point clamping,the phase isin O state when either S2u or S3uconducts depending on positive or negative phasecurrent polarity,respectively.For neutral point voltage balancing,the average current injected at O should be zero.2.2 Line side converterFor standard applications.a l2-pulse diode rectifier feeds the divided DC-link capacitor.This topology introduces low harmonics on the line side.For even higher requirements a 24-pulse diode rectifier can be used as an input converter.For more advanced applications where regeneration capability is necessary, an active front.end converter can replace the diode rectifier, using the same structure as the inverter.2.3 Inverter controlMotor Contro1.Motor control of induction machines is realized by using a rotor flux.oriented vector controller.Fig.2 shows the block diagram of indirect vector controlled drive that incorporates both constant torque and high speed field-weakening regions where the PW M modulator was used.In this figure,the command flux is generated as function of speed.The feedback speed is added with the feed forward slip command signal . the resulting frequency signal is integrated and then the unit vectorsignals(cos and sin )are generated.The vector rotator generates the voltage and angle commands for the PW M as shown.PWM Modulator.The demanded voltage vector is generated using an elaborate PWM modulator.The modulator extends the concepts of space-vector modulation to the three-level inverter.The operation can be explained by starting from a regularly sampled sine-triangle comparison from two-level inverter.Instead of using one set of reference waveforms and one triangle defining the switching frequency, the three-level modulator uses two sets of reference waveforms Uandr1and just one triangle.Thus, each switching transition is used in an optimal Ur2way so that several objectives are reached at the same time.Very low harmonics are generated.The switching frequency is low and thus switching losses are minimized.As in a two-level inverter, a zero-sequence component can be added to each set of reference waveform s in order to maximize the fundamental voltage component.As an additional degree of freedom,the position of the reference waveform s within the triangle can be changed.This can be used for current balance in the two halves of the DC-1ink.3 Testing resultsAfter Successful installation of three 750 kW /2.3 kV three-level inverters for one 2.7 km long belt conveyor driving system in Chengzhuang Mine.The performance of the whole VFC system was tested.Fig.3 is taken from the test,which shows the excellent characteristic of the belt conveyor driving system with VFC controller.Fig.3 includes four curves.The curve 1 shows the belt tension.From the curve it can be find that the fluctuation range of the belt tension is very smal1.Curve 2 and curve 3 indicate current and torque separately.Curve 4 shows the velocity of the controlled belt.The belt velocity have the“s”shape characteristic.A1l the results of the test show a very satisfied characteristic for belt driving system.4 ConclusionsAdvances in conveyor drive control technology in recent years have resulted in many more reliable.Cost-effective and performance-driven conveyor drive system choices for users.Among these choices,the Variable frequency control (VFC) method shows promising use in the future for long distance belt conveyor drives due toits excellent performances.The NPC three-level inverter using high voltage IGBTs make the Variable frequency control in medium voltage applications become much more simple because the inverter itself can provide the medium voltage needed at the motor terminals,thus eliminating the step-up transformer in most applications in the past.The testing results taken from the VFC control system with NPC three.1evel inverters used in a 2.7 km long belt conveyor drives in Chengzhuang Mine indicates that the performance of NPC three-level inverter using HV-IGBTs together with the control strategy of rotor field-oriented vector control for induction motor drive is excellent for belt conveyor driving system.中文译文:带式输送机及其牵引系统在运送大量的物料时,带式输送机在长距离的运输中起到了非常重要的竞争作用。
带式输送机英文翻译

毕业设计(论文)外文资料翻译学院:机械电子工程学院专业:机械设计制造及其自动化姓名:孟庆林学号: Z080501734外文出处: Applied Energy 87 (2010) 1929–1937 (用外文写)附件: 1.外文资料翻译译文;2.外文原文。
指导教师评语:签名:年月日带式输送机系统的运作效率的最优控制摘要:带式输送机系统的能源效率的提高可以通过设备和操作水平实现。
文献中提到的开关控制和可变速控制可以改善皮带输送机的能源效率。
目前的应用主要集中在较低的水平控制循环或不在系统级别操作顾虑的个别皮带输送机。
在本文中,最优开关控制和基于最优控制的变速驱动(VSD)可以提高皮带输送机系统在操作水平过程中的的能源效率,使用时间的效率,斜坡带速和其他率制度约束的也会被考虑到。
把燃煤电厂煤碳输送系统作为一个案例研究,通过这两个最优控制策略实现了能源的巨大节约。
此外,案例研究也证明,基于最优控制的VSD也实现了相当客观的的能源节约。
关键字:皮带输送系统运作效率最有开关控制基于变速驱动器的最优控制1.说明皮带输送机广泛用于处理散装材料的中长距离输送,因为它有比其他输送方式较高的运输效率。
能源成本决定了很大一部分皮带输送机的运营成本(高达40%根据[1])。
作为一个整体,材料处理消耗了大部分的能源供应,例如,在南非消耗材料处理部门消耗了电力供应的10%[2]。
因此,为了减少能源消耗或者材料处理的能源成本,这对提高带式输送机的能源效率是非常重要的,这也是带式输送机技术主要发展之一[3]。
带式输送机是典型的从电气能转换为机械能的能源转换系统,其能源效率可分为四个部分:性能效率,操作效率,设备效率和技术效率。
对于大多数的能源系统,能源效率的提高可以很容易的实施于操作效率和设备效率。
这确实适用于带式输送机。
同时它还指出设备效率和操作效率决定执行效率,执行效率通常由各种外部指标反映,比如能源消耗、能源成本或温室气体的排放。
煤矿带式输送机中英文对照外文翻译文献

中英文对照外文翻译A Comparison of Soft Start Mechanisms forMining Belt Conveyors1800 Washington Road Pittsburgh, PA 15241 Belt Conveyors are an important method for transportation of bulk materials in the mining industry. The control of the application of the starting torque from the belt drive system to the belt fabric affects the performance, life cost, and reliability of the conveyor. This paper examines applications of each starting method within the coal mining industry.INTRODUCTIONThe force required to move a belt conveyor must be transmitted by the drive pulley via friction between the drive pulley and the belt fabric. In order to transmit power there must be a difference in the belt tension as it approaches and leaves the drive pulley. These conditions are true for steady state running, starting, and stopping. Traditionally, belt designs are based on static calculations of running forces. Since starting and stopping are not examined in detail, safety factors are applied to static loadings (Harrison, 1987). This paper will primarily address the starting or acceleration duty of the conveyor. The belt designer must control starting acceleration to prevent excessive tension in the belt fabric and forces in the belt drive system (Suttees, 1986). High acceleration forces can adversely affect the belt fabric, belt splices, drive pulleys, idler pulleys, shafts, bearings, speed reducers, and couplings. Uncontrolled acceleration forces cancause belt conveyor system performance problems with vertical curves, excessive belt take-up movement, loss of drive pulley friction, spillage of materials, and festooning of the belt fabric. The belt designer is confronted with two problems, The belt drive system must produce a minimum torque powerful enough to start the conveyor, and controlled such that the acceleration forces are within safe limits. Smooth starting of the conveyor can be accomplished by the use of drive torque control equipment, either mechanical or electrical, or a combination of the two (CEM, 1979).SOFT START MECHANISM EVALUATION CRITERIONWhat is the best belt conveyor drive system? The answer depends on many variables. The best system is one that provides acceptable control for starting, running, and stopping at a reasonable cost and with high reliability (Lewdly and Sugarcane, 1978). Belt Drive System For the purposes of this paper we will assume that belt conveyors are almost always driven by electrical prime movers (Goodyear Tire and Rubber, 1982). The belt "drive system" shall consist of multiple components including the electrical prime mover, the electrical motor starter with control system, the motor coupling, the speed reducer, the low speed coupling, the belt drive pulley, and the pulley brake or hold back (Cur, 1986). It is important that the belt designer examine the applicability of each system component to the particular application. For the purpose of this paper, we will assume that all drive system components are located in the fresh air, non-permissible, areas of the mine, or in non-hazardous, National Electrical Code, Article 500 explosion-proof, areas of the surface of the mine.Belt Drive Component Attributes Size.Certain drive components are available and practical in different size ranges. For this discussion, we will assume that belt drive systems range from fractional horsepower to multiples of thousands of horsepower. Small drive systems are often below 50 horsepower. Medium systems range from 50 to 1000 horsepower. Large systems can be considered above 1000 horsepower. Divisionof sizes into these groups is entirely arbitrary. Care must be taken to resist the temptation to over motor or under motor a belt flight to enhance standardization. An over motored drive results in poor efficiency and the potential for high torques, while an under motored drive could result in destructive overspending on regeneration, or overheating with shortened motor life (Lords, et al., 1978). Torque Control.Belt designers try to limit the starting torque to no more than 150% of the running torque (CEMA, 1979; Goodyear, 1982). The limit on the applied starting torque is often the limit of rating of the belt carcass, belt splice, pulley lagging, or shaft deflections. On larger belts and belts with optimized sized components, torque limits of 110% through 125% are common (Elberton, 1986). In addition to a torque limit, the belt starter may be required to limit torque increments that would stretch belting and cause traveling waves. An ideal starting control system would apply a pretension torque to the belt at rest up to the point of breakaway, or movement of the entire belt, then a torque equal to the movement requirements of the belt with load plus a constant torque to accelerate the inertia of the system components from rest to final running speed. This would minimize system transient forces and belt stretch (Shultz, 1992). Different drive systems exhibit varying ability to control the application of torques to the belt at rest and at different speeds. Also, the conveyor itself exhibits two extremes of loading. An empty belt normally presents the smallest required torque for breakaway and acceleration, while a fully loaded belt presents the highest required torque. A mining drive system must be capable of scaling the applied torque from a 2/1 ratio for a horizontal simple belt arrangement, to a 10/1 ranges for an inclined or complex belt profile.Thermal Rating.During starting and running, each drive system may dissipate waste heat. The waste heat may be liberated in the electrical motor, the electrical controls,, the couplings, the speed reducer, or the belt braking system. The thermal load ofeach start Is dependent on the amount of belt load and the duration of the start. The designer must fulfill the application requirements for repeated starts after running the conveyor at full load. Typical mining belt starting duties vary from 3 to 10 starts per hour equally spaced, or 2 to 4 starts in succession. Repeated starting may require the dreading or over sizing of system components. There is a direct relationship between thermal rating for repeated starts and costs. Variable Speed. Some belt drive systems are suitable for controlling the starting torque and speed, but only run at constant speed. Some belt applications would require a drive system capable of running for extended periods at less than full speed. This is useful when the drive load must be shared with other drives, the belt is used as a process feeder for rate control of the conveyed material, the belt speed is optimized for the haulage rate, the belt is used at slower speeds to transport men or materials, or the belt is run a slow inspection or inching speed for maintenance purposes (Hager, 1991). The variable speed belt drive will require a control system based on some algorithm to regulate operating speed. Regeneration or Overhauling Load. Some belt profiles present the potential for overhauling loads where the belt system supplies energy to the drive system. Not all drive systems have the ability to accept regenerated energy from the load. Some drives can accept energy from the load and return it to the power line for use by other loads. Other drives accept energy from the load and dissipate it into designated dynamic or mechanical braking elements. Some belt profiles switch from motoring to regeneration during operation. Can the drive system accept regenerated energy of a certain magnitude for the application? Does the drive system have to control or modulate the amount of retarding force during overhauling? Does the overhauling occur when running and starting? Maintenance and Supporting Systems. Each drive system will require periodic preventative maintenance. Replaceable items would include motor brushes, bearings, brake pads, dissipation resistors, oils, and cooling water. If the drive system is conservatively engineered and operated, the lower stress onconsumables will result in lower maintenance costs. Some drives require supporting systems such as circulating oil for lubrication, cooling air or water, environmental dust filtering, or computer instrumentation. The maintenance of the supporting systems can affect the reliability of the drive system.Cost.The drive designer will examine the cost of each drive system. The total cost is the sum of the first capital cost to acquire the drive, the cost to install and commission the drive, the cost to operate the drive, and the cost to maintain the drive. The cost for power to operate the drive may vary widely with different locations. The designer strives to meet all system performance requirements at lowest total cost. Often more than one drive system may satisfy all system performance criterions at competitive costs.Complexity.The preferred drive arrangement is the simplest, such as a single motor driving through a single head pulley. However, mechanical, economic, and functional requirements often necessitate the use of complex drives. The belt designer must balance the need for sophistication against the problems that accompany complex systems. Complex systems require additional design engineering for successful deployment. An often-overlooked cost in a complex system is the cost of training onsite personnel, or the cost of downtime as a result of insufficient training.SOFT START DRIVE CONTROL LOGICEach drive system will require a control system to regulate the starting mechanism. The most common type of control used on smaller to medium sized drives with simple profiles is termed "Open Loop Acceleration Control". In open loop, the control system is previously configured to sequence the starting mechanism in a prescribed manner, usually based on time. In open loop control, drive-operating parameters such as current, torque, or speed do not influence sequence operation. This method presumes that the control designer hasadequately modeled drive system performance on the conveyor. For larger or more complex belts, "Closed Loop" or "Feedback" control may he utilized. In closed loop control, during starting, the control system monitors via sensors drive operating parameters such as current level of the motor, speed of the belt, or force on the belt, and modifies the starting sequence to control, limit, or optimize one or wore parameters. Closed loop control systems modify the starting applied force between an empty and fully loaded conveyor. The constants in the mathematical model related to the measured variable versus the system drive response are termed the tuning constants. These constants must be properly adjusted for successful application to each conveyor. The most common schemes for closed loop control of conveyor starts are tachometer feedback for speed control and load cell force or drive force feedback for torque control. On some complex systems, It is desirable to have the closed loop control system adjust itself for various encountered conveyor conditions. This is termed "Adaptive Control". These extremes can involve vast variations in loadings, temperature of the belting, location of the loading on the profile, or multiple drive options on the conveyor. There are three common adaptive methods. The first involves decisions made before the start, or 'Restart Conditioning'. If the control system could know that the belt is empty, it would reduce initial force and lengthen the application of acceleration force to full speed. If the belt is loaded, the control system would apply pretension forces under stall for less time and supply sufficient torque to adequately accelerate the belt in a timely manner. Since the belt only became loaded during previous running by loading the drive, the average drive current can be sampled when running and retained in a first-in-first-out buffer memory that reflects the belt conveyance time. Then at shutdown the FIFO average may be use4 to precondition some open loop and closed loop set points for the next start. The second method involves decisions that are based on drive observations that occur during initial starting or "Motion Proving'. This usually involves acomparison In time of the drive current or force versus the belt speed. if the drive current or force required early in the sequence is low and motion is initiated, the belt must be unloaded. If the drive current or force required is high and motion is slow in starting, the conveyor must be loaded. This decision can be divided in zones and used to modify the middle and finish of the starsequence control. The third method involves a comparison of the belt speed versus time for this start against historical limits of belt acceleration, or'Acceleration Envelope Monitoring'. At start, the belt speed is measured versus time. This is compared with two limiting belt speed curves that are retained in control system memory. The first curve profiles the empty belt when accelerated, and the second one the fully loaded belt. Thus, if the current speed versus time is lower than the loaded profile, it may indicate that the belt is overloaded, impeded, or drive malfunction. If the current speed versus time is higher than the empty profile, it may indicate a broken belt, coupling, or drive malfunction.In either case, the current start is aborted and an alarm issued. CONCLUSIONThe best belt starting system is one that provides acceptable performance under all belt load Conditions at a reasonable cost with high reliability. No one starting system meets all needs. The belt designer must define the starting system attributes that are required for each belt. In general, the AC induction motor with full voltage starting is confined to small belts with simple profiles. The AC induction motor with reduced voltage SCR starting is the base case mining starter for underground belts from small to medium sizes. With recent improvements, the AC motor with fixed fill fluid couplings is the base case for medium to large conveyors with simple profiles. The Wound Rotor Induction Motor drive is the traditional choice for medium to large belts with repeated starting duty or complex profiles that require precise torque control. The DC motor drive, Variable Fill Hydrokinetic drive, and the Variable Mechanical Transmission drive compete for application on belts with extreme profiles orvariable speed at running requirements. The choice is dependent on location environment, competitive price, operating energy losses, speed response, and user familiarity. AC Variable Frequency drive and Brush less DC applications are limited to small to medium sized belts that require precise speed control due to higher present costs and complexity. However, with continuing competitive and technical improvements, the use of synthesized waveform electronic drives will expand.煤矿业带式输送机几种软起动方式的比较1800 年华盛顿路匹兹堡, PA 15241带式运送机是采矿工业运输大批原料的重要方法。
高速带式输送机的设计_外文翻译(可编辑)
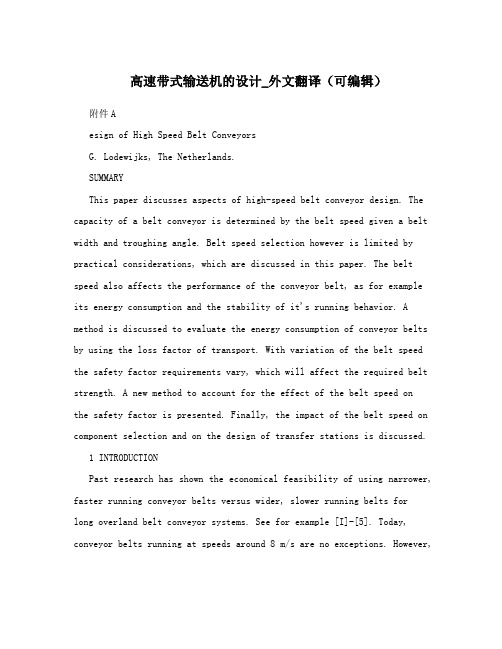
高速带式输送机的设计_外文翻译(可编辑)附件Aesign of High Speed Belt ConveyorsG. Lodewijks, The Netherlands.SUMMARYThis paper discusses aspects of high-speed belt conveyor design. The capacity of a belt conveyor is determined by the belt speed given a belt width and troughing angle. Belt speed selection however is limited by practical considerations, which are discussed in this paper. The belt speed also affects the performance of the conveyor belt, as for exampleits energy consumption and the stability of it's running behavior. A method is discussed to evaluate the energy consumption of conveyor belts by using the loss factor of transport. With variation of the belt speed the safety factor requirements vary, which will affect the required belt strength. A new method to account for the effect of the belt speed onthe safety factor is presented. Finally, the impact of the belt speed on component selection and on the design of transfer stations is discussed.1 INTRODUCTIONPast research has shown the economical feasibility of using narrower, faster running conveyor belts versus wider, slower running belts forlong overland belt conveyor systems. See for example [I]-[5]. Today, conveyor belts running at speeds around 8 m/s are no exceptions. However,velocities over 10 m/s up to 20 m/s are technically dynamically feasible and may also be economically feasible. In this paper belt speeds between the 10 and 20 m/s are classified as high. Belt speeds below the 10 m/s are classified as low.Using high belt speeds should never be a goal in itself. If using high belt speeds is not economically beneficial or if a safe andreliable operation is not ensured at a high belt speed then a lower belt speed should be selected.Selection of the belt speed is part of the total design process. The optimum belt conveyor design is determined by static or steady state design methods. In these methods the belt is assumed to be a rigid, inelastic body. This enables quantification of the steady-state operation of the belt conveyor and determination of the size of conveyor components. The specification of the steady-state operation includes a quantification of the steady-state running belt tensions and power consumption for all material loading and relevant ambient conditions. It should be realized that finding the optimum design is not a one-time effort but an iterative process [6].Design fine-tuning, determination of the optimum starting and stopping procedures, including determination of the required control algorithms, and determination of the settings and sizes of conveyor components such as drives, brakes and flywheels, are determined by dynamicdesign methods. In these design methods, also referred to as dynamic analyses, the belt is assumed to be a three-dimensional visco- elastic body. A three dimensional wave theory should be used to study time dependent transmission of large local force and displacement disturbances along the belt [7]. In this theory the belt is divided into a series of finite elements. The finite elements incorporate visco- elastic springs and masses. The constitutive characteristics of thefinite elements must represent the rheological characteristics of the belt. Dynamic analysis produces the belt tension and power consumption during non-stationary operation, like starting and stopping, of the belt conveyor.This paper discusses the design of high belt-speed conveyors, in particular the impact of using high belt speeds on the performance of the conveyor belt in terms of energy consumption and safety factor requirements. Using high belt speeds also requires high reliability of conveyor components such as idlers to achieve an acceptable component life. Another important aspect of high-speed belt conveyor design is the design of efficient feeding and discharge arrangements. These aspects will be discussed briefly.2 BELTSPEED2.1 BELT SPEED SELECTIONThe lowest overall belt conveyor cost occur in the range of belt widthsof 0.6 to 1.0 m [2]. The required conveying capacity can be reached by selection of a belt width in this range and selecting whatever belt speed is required to achieve the required flow rate. Figure 1 shows an example of combinations of belt speed and belt width to achieve Specific conveyor capacities. In this example it is assumed that the bulk density is 850 kg/m3 coal and that the trough angle and the surcharge angle are 35' and 20' respectively.Figure 1: Belt width versus belt speed for different capacities.Belt speed selection is however limited by practical considerations.A first aspect is the troughability of the belt. In Figure 1 there is no relation with the required belt strength rating , which partly depends on the conveyor length and elevation. The combination of belt width and strength must be chosen such that good troughability of the belt is ensured. If the troughability is not sufficient then the belt will not track properly. This will result in unstable running behavior of the belt, in particular at high belt speeds, which is not acceptable. Normally, belt manufacturers expect a sufficiently straight run if approximately 40% of the belt width when running empty, makes contact with the carrying idlers. Approximately 10% should make tangential contact with the center idler roll.A second aspect is the speed of the air relative to the speed of the bulk solid material on the belt relative airspeed . If the relative airspeed exceeds certain limits then dust will develop. This is in particular a potential problem in mine shafts where a downward airflowis maintained for ventilation purposes. The limit in relative airspeed depends on ambient conditions and bulk material characteristics.A third aspect is the noise generated by the belt conveyor system. Noise levels generally increase with increasing belt speed. In residential areas noise levels are restricted to for example 65 dB. Although noise levels are greatly affected by the design of the conveyor support structure and conveyor covers, this may be a limiting factor in selecting the belt speed.2.2 BELT SPEED VARIATIONThe energy consumption of belt conveyor systems varies withvariation of the belt speed, as will be shown in Section 3. The belt velocity can be adjusted with bulk material flow supplied at the loading point to save energy. If the belt is operating at full tonnage then it should run at the high design belt speed. The belt speed can be adjusted decreased to the actual material volume flow supplied at the loading point. This will maintain a constant filling of the belt trough and a constant bulk material load on the belt. A constant filling of the belt trough yields an optimum loading-ratio, and lower energy consumption per unit of conveyed material may be expected. The reduction in energy consumption will be at least 10% for systems where the belt speed is varied comparedto systems where the belt speed is kept constant [8].Varying the belt speed with supplied bulk material flow has the following advantages:Less belt wear at the loading areasLower noise emissionImproved operating behavior as a result of better belt alignment and the avoidance of belt lifting in concave curve by reducing belt tensions Drawbacks include:Investment cost for controllability of the drive and brake systems Variation of discharge parabola with belt speed variationControl system required for controlling individual conveyors in a conveyor systemConstant high belt pre-tensionConstant high bulk material load on the idler rollsAn analysis should be made of the expected energy savings to determine whether it is worth the effort of installing a more expensive, more complex conveyor system.3 ENERGY CONSUMPTIONClients may request a specification of the energy consumption of a conveyor system, for example quantified in terms of imum kW-hr/ton/km,to transport the bulk solid material at the design specifications over the projected route. For long overland systems, the energy consumption is mainly determined by the work done to overcome the indentation rolling resistance [9]. This is the resistance that the belt experiences due to the visco-elastic time delayed response of the rubber belt cover to the indentation of the idler roll. For in-plant belt conveyors, work done to overcome side resistances that occur mainly in the loading areaalso affects the energy consumption. Side resistances include the resistance due to friction on the side walls of the chute and resistance that occurs due to acceleration of the material at the loading point.The required drive power of a belt conveyor is determined by the sum of the total frictional resistances and the total material lift. The frictional resistances include hysteresis losses, which can be considered as viscous velocity dependent friction components. It doesnot suffice to look just at the imum required drive power to evaluate whether or not the energy consumption of a conveyor system is reasonable. The best method to compare the energy consumption of different transport systems is to compare their transport efficiencies.3.1 TRANSPORT EFFICIENCYThere are a number of methods to compare transport efficiencies. The first and most widely applied method is to compare equivalent friction factors such as the DIN f factor. An advantage of using an equivalent friction factor is that it can also be determined for an empty belt. A drawback of using an equivalent friction factor is that it is not a'pure'efficiency number. It takes into account the mass of the belt, reduced mass of the rollers and the mass of the transported material. In a pure efficiency number, only the mass of the transported material is taken into account.The second method is to compare transportation cost, either in kW-hr/ton/km or in $/ton/km. The advantage of using the transportation costis that this number is widely used for management purposes. The disadvantage of using the transportation cost is that it does not directly reflect the efficiency of a system.The third and most "pure" method is to compare the loss factor of transport [10]. The loss factor of transport is the ratio between the drive power required to overcome frictional losses neglecting drive efficiency and power loss/gain required to raise/lower the bulk material and the transport work. The transport work is defined as the multiplication of the total transported quantity of bulk material and the average transport velocity. The advantage of using loss factors of transport is that they can be compared to loss factors of transport of other means of transport, like trucks and trains. The disadvantage is that the loss factor of transport depends on the transported quantity of material, which implies that it can not be determined for an empty belt conveyor.The following are loss factors of transport for a number oftransportsystems to illustrate the concept:Continuous transport:Slurry transport around 0.01Belt conveyors between 0.01 and 0.1Vibratory feeders between 0.1 and 1Pneumatic conveyors around 1 0Discontinuous transport:Ship between 0.001 and 0.01Train around 0.01Truck between 0.05 and 0.13.2 INDENTATION ROLLING RESISTANCEFor long overland systems, the energy consumption is mainly determined by the work done to overcome the indentation rolling resistance. Idler rolls are made of a relatively hard material likesteel or aluminum whereas conveyor belt covers are made of much softer materials like rubber or PVC. The rolls therefore indent the belt's bottom-cover when the belt moves over the idler rolls, due to the weight of the belt and bulk material on the belt. The recovery of the compressed parts of the belt's bottom cover will take some time due to its visco-elastic time dependent properties. The time delay in the recovery of the belt's bottom cover results in an asymmetrical stress distribution between the belt and the rolls, see Figure 2. This yields a resultant resistance force called theindentation rolling resistance force. The magnitude of this force depends on the visco-elastic properties of the cover material, the radius of the idler roll, the vertical force due to the weight of the belt and the bulk solid material, and the radius of curvature of thebelt in curves in the vertical plane.Figure 2: Asymmetric stress distribution between belt and roll [7].It is important to know how the indentation rolling resistance depends on the belt velocity to enable selection of a proper belt velocity, [11].Figure 3: Loss factor tanb of typical cover rubber [7]Firstly, the indentation rolling resistance depends on the vertical load on the belt, which is the sum of the belt and the bulk material weight. If the vertical load on the belt decreases with a factor 2 then the indentation rolling resistance decreases with a factor 2.52 2 ^4/3 . The bulk load decreases with increasing belt speed assuming a constant capacity. Therefore, the indentation rolling resistance decreases more than proportionally with increasing belt speed.Secondly, the indentation rolling resistance depends on the size of the idler rolls. If the roll diameter increases with a factor 2 then the indentation rolling resistance decreases with a factor 1.58 2 ^2/3 . In general the idler roll diameter increases with increasing belt speed to limit the bearing rpm's to maintain acceptable idler life. In that case the indentation rolling resistance decreases with increasing belt speed.Thirdly, the indentation rolling resistance depends on the visco-elastic properties of the belt's cover material. These properties depend on the deformation rate, see Figure 3. The deformation rate in its turn depends on the size of the deformation area in the belt's bottom cover depending on belt and bulk load and on the belt speed. In general the indentation rolling resistance increases with increasing deformationrate and thus belt speed , but only to a relatively small account.Fourthly, the indentation rolling resistance depends on the belt's bottom cover thickness. If the bottom cover thickness increases with a factor 2 then the indentation rolling resistance increases with a factor 1.26 2 ^1/3 . if a bottom cover is increased to account for an increase in belt wear with increasing belt speed, then the indentation rolling resistance increases as well.It should be realized that the indentation rolling resistance, although important, is not the only velocity dependent resistance. The rolling resistance of the idler rolls for example depends on thevertical load as well as on their rotational speed. The effect of the vertical load, which directly depends on the belt speed, is large. The effect of the rotational speed is much smaller. Another resistance occurs due to acceleration of the bulk solid material at the loading point. This resistance increases quadratically with an increase in belt speed assuming that the bulk material falls straight onto the belt. This willaffect smaller, in plant belt conveyors in particular.EXAMPLETo illustrate the concept discussed above lets consider a 6 km long conveyor belt with a capacity of 5000 TPH. The trough angle, the surcharge angle and the bulk density are again taken 35', 20' and 850kg/m^3 respectively. Figure 4 shows the required belt speed as afunction of the belt width to achieve the required capacity of 5000 TPH. This figure is somewhat similar to Figure 1.Figure 4The figures 5 and 6 show the required belt strength and the required drive power as a function of the belt speed. The required belt strength decreases and the required drive power slowly increases with increasing belt speed as can be seen in those figures. Figure 7 shows the loss factor of transport and the DIN f factor versus belt speed. The loss factor of transport is always higher than the DIN f factor because the DIN f factor takes the mass of the belt into account in the denominator whereas the loss factor of transport only accounts for the mass of the bulk solid material. Intuitively, it may be expected that there will be an economically optimum belt speed in the high belt speed range. The determination of the optimum belt speed however, requires more information and is beyond the scope of this paper.Figure 5Figure 6Figure 7 3.3 RUBBER COMPOUNDSThe indentation rolling resistance depends on the visco-elastic properties of the belt's bottom cover as discussed in the preceding section. This implies that the rolling resistance can be decreased by selecting a special low indentation rolling resistance rubber compound that is available on the market today. A small premium has to be paidfor this special compound, but costs can be limited by applying it for the bottom cover only and using a normal wear-resistant compound for thecarrying top cover. In that case turnovers are required to fully use the energy saving function of the bottom compound.A Quantitative indication of the level of indentation rolling resistance is the indentation rolling resistance indicator tan/E ^1/3, where tan is the loss angle and E' the storage modulus of the compound. Compounds with a reasonable indentation rolling resistance performance have indicators below 0.1. Figure 8 shows these indicators for typical medium to good performing rubbers. As can be seen in that figure, the choice for a specific rubber compound affects the energy consumption of the belt conveyor, in particular as a function of the ambient temperature.One comment warning must be made. A special belt with lowindentation rolling resistance compound should never be selected if only one conveyor belt manufacturer offers it. In that case the conveyor systemcan only perform in accordance with its design specifications when that specific belt is used. It is much better, also cost wise, to specify the upper limit of the resistance indicator as given above that can be met by more than one conveyor belt manufacturer.Figure 8: Indentation rolling resistance indicators forfour?different rubbers as a function of temperature.4. SAFETY FACTOR REQUIREMENTSFor design purposes, standards like DIN 22101, ISO 5048 and CEMA provide safety factors SF that limit the permissible belt loads. Twotypes of safety factors can be distinguished: safety factors on the steady-state running tensions and safety factors on the non-stationary tensions. In general the safety factor on the steady-state running tension is based on:1 Stationary full and empty, summer and winter andnon-stationary belt tensions2 Belt tensions from extra resistances and deformations inhorizontal and vertical curves, troughing transitions, belt turnovers, on pulleys etc.3 Belt conveyor system maintenance4 Belt conveyor system operational data including hours per day, days per year and years of service5 Belt splice design and fatigue characteristics including those of thebelt tensile carrying member steel cords or fabric and the rubber6 Splice kit storage and handling.All these six items should be taken into account when determiningthe safety factor.standards like the DIN standard base the recommended safety factoron reduction factors. DIN 22101 uses three reduction factors. The first r0 generally accounts for the reduction of the strength of the belt splices due to fatigue. The second r1 accounts for the extra forces that act on the belt in transition zones and on pulleys etc. The third r2 accounts for the extra dynamic stresses in the belt during starting andstopping. The required minimum safety factor can be calculated as follows:SF 1/ 1- r0+r1+r2 1The DIN standard also gives values for the three reduction factors. For example, for a steel cord conveyor belt under "normal" operational conditions the values are as follows: r0 0.665, r1 0.15, r2 0.06, which yields a safety factor SF 8.Although much can be said about the applicability of the safety factor determined with the DIN standard for the design of long belt conveyor systems, the major drawback, keeping the belt speed selection in mind, is that the conveyor system's operational data and the real fatigue properties of the belt are not taken into account.It is possible to account for these factors and to achieve a tailor-made safety factor by taking the belt's operational data into account. The reduction factors r1 and r2 are independent of the fatigue properties of the belt and thus constant with increasing number of load cycles. Let's assume that the reduction factor r0 varies linearly with the log1O of the number of load cycles revolution of the belt through the total belt conveyor from 0 to 0.665 at 10,000 load cycles approximation of DIN standard :r0 0.166 log10 N N 10.000 2where N is the number of load cycles. After 10,000 load cycles r0 hardly increases. Now let's assume that the conveyor under design has a length of 10,000 m, a life expectation of 5 years at 5000 operationalhours per year. The total number of load cycles can be calculated with the following equation:N [ 3600 V / 2L ]HY 3where V is the belt speed, L the conveyor length, H the number of operational hours per year and Y the number of expected years of operation. Equation 3 is visualized in Figure 9.Figure 9: Number of load cycles versus belt speed for given example.The value of the reduction factor ro can be determined with equation 2 and the number of load cycles as given in Figure 9. The result is shown in Figure 10.Figure 10: DIN 22101 reduction factor r0 for given exampleThe safety factor as a function of the belt speed then can be determined with equation 1 and Figure 10. The result is shown in Figure 11.Figure 11: Minimum required safety factor for given exampleFrom Figure 11 it can be learned that for the belt under design the required minimum safety factor on the steady-state running tensions is about 7.5 if the belt is running at 2 m/s, and about 10 in case the belt is running at 20 m/s. Taking the belt speed into account during safety factor determination thus prevents overrating of the belt at low speeds and underrating at high speeds also depends on the length of the conveyor system .The above given figures and numbers are to illustrate the procedure only. This procedure can be fine tuned by taking measured fatigueproperties of the belt tensile-carrying member steel cords or fabric and the rubber into account, as well as the actual load cycle of the belt empty, fully loaded, steady state running, starting and stopping, summer, and winter conditions etc. .5 BELT CONVEYOR DYNAMICSIn essence the dynamics of a belt conveyor does not change with the belt speed. However, with increasing belt speed the rate of changes increases, which will result in a decreasing running stability of the belt.This paper is not intended to fully discuss belt conveyor dynamics.It is referred to [7] where this topic is extensively discussed. However, a number of notes on the dynamics of high belt speed conveyors can be made.When a belt between two idlers is exited by an idler roll in or near a natural frequency of transverse vibration of the belt span, resonance phenomena occur. The amplitude of transverse vibration increases considerably when resonance occurs yielding increased roll/ bearing wear and an increased power consumption of the belt. This increase invibration amplitude, also referred to as belt flap, must be avoided. In high-speed belt systems the effect of resonance on the structure is very destructive, as observed with lower speed belts that resonate anddestroy idler bearings. Care should therefore be taken to design a belt conveyor so that the possibility of resonance in the belt is avoided andat the same time best use is made of current static design methods so that the economics of the design are saved.Belt tracking must be excellent at high speeds. If the belt does not track properly then run off may be expected since, with increasing belt speed, side displacements and the rate of side displacement increase. The combination of belt width and strength must be chosen such that good troughability is ensured, see Section 2.1. Also imum effort must be made by the belt manufacturer to make straight belts and to construct true belt splices. In addition, longer manufactured belt lengths reduce the numberof splices and thus increase the chance of straightness.A similar comment can be made for the design of horizontal belt curves. The position of the belt on the idlers changes with a change in belt tension mainly due to a change in loading degree. The belt will move sideward in particular during large tension variations as occur during aborted starting and emergency stopping. The change in belt tension during starting and stopping will increase with increasing belt speed. For low belt speed conveyors static design methods may be sufficient to determine the imum side displacement. For high belt speed conveyors however, dynamic design methods are required to predict the side displacement to a sufficient level of accuracy.Normal operational starting and stopping procedures will not change for high belt speed conveyors, except that starting and stopping will take more time. The nature of emergency stop procedures however willchange. In general emergency stop procedures are designed to stop the belt in a short period of time without the use of the drive system and so that the belt conveyor is not damaged. A typical emergency stop time f。
带式输送机外文文献翻译、中英文翻译
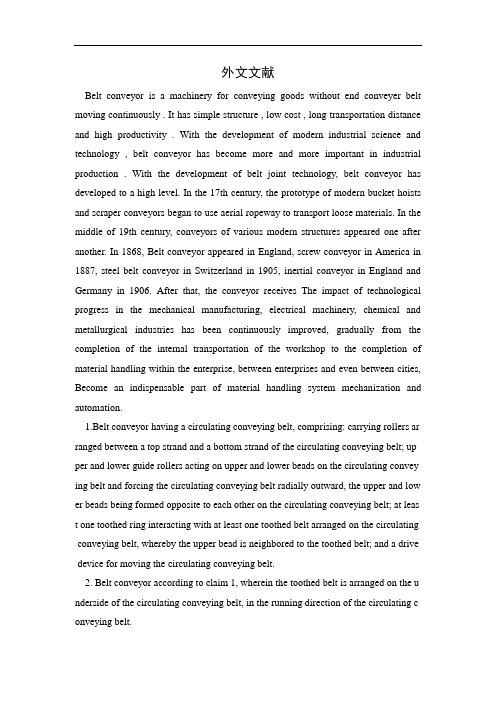
外文文献Belt conveyor is a machinery for conveying goods without end conveyer belt moving continuously . It has simple structure , low cost , long transportation distance and high productivity . With the development of modern industrial science and technology , belt conveyor has become more and more important in industrial production . With the development of belt joint technology, belt conveyor has developed to a high level. In the 17th century, the prototype of modern bucket hoists and scraper conveyors began to use aerial ropeway to transport loose materials. In the middle of 19th century, conveyors of various modern structures appeared one after another. In 1868, Belt conveyor appeared in England, screw conveyor in America in 1887, steel belt conveyor in Switzerland in 1905, inertial conveyor in England and Germany in 1906. After that, the conveyor receives The impact of technological progress in the mechanical manufacturing, electrical machinery, chemical and metallurgical industries has been continuously improved, gradually from the completion of the internal transportation of the workshop to the completion of material handling within the enterprise, between enterprises and even between cities, Become an indispensable part of material handling system mechanization and automation.1.Belt conveyor having a circulating conveying belt, comprising: carrying rollers ar ranged between a top strand and a bottom strand of the circulating conveying belt; up per and lower guide rollers acting on upper and lower beads on the circulating convey ing belt and forcing the circulating conveying belt radially outward, the upper and low er beads being formed opposite to each other on the circulating conveying belt; at leas t one toothed ring interacting with at least one toothed belt arranged on the circulating conveying belt, whereby the upper bead is neighbored to the toothed belt; and a drive device for moving the circulating conveying belt.2. Belt conveyor according to claim 1, wherein the toothed belt is arranged on the u nderside of the circulating conveying belt, in the running direction of the circulating c onveying belt.3. Belt conveyor according to claim 2, wherein the toothed ring is arranged at the e nd of the carrying rollers, and wherein projecting from the end of a first carrying rolle r is a journal for the connection of the drive device.4. Belt conveyor according to claim 3, wherein the toothed belt extends in the regio n of the side border of the circulating conveying belt.5. Belt conveyor according to claim 1, wherein the toothed belt and the toothed ring have multisplining.6. Belt conveyor according to claim 1, wherein Kevlar filaments are incorporated i n the toothed belt.7. Belt conveyor according to claim 1, wherein the toothed belt is attached on the c irculating conveying belt via one of welding, vulcanizing, and adhesively bonding the reto.8. Belt conveyor having a circulating conveying belt, comprising: carrying rollers a rranged between a top strand and a bottom strand of the circulating conveying belt; an d a drive device and a force-transmission device for moving the conveying belt, where in a pair of elements which interact with one another with a form fit is provided for fo rce-transmission purposes, one of said elements being assigned to the force-transmissi on device and the other of said elements being assigned to the conveying belt, wherei n the force-transmission device comprises at least one toothed ring, and wherein the ci rculating conveying belt has at least one toothed belt, the toothed ring and toothed belt interacting with a form fit, wherein the toothed belt is a constituent part of a toothed-belt component which is of essentially U-shaped design in the transverse direction of t he toothed belt and engages around the side-border region of the conveying belt.9. Belt conveyor according to claim 8, wherein the toothed ring is assigned at least t o a first belt-conveyor carrying roller, which is operatively connected to the drive devi ce.10. Belt conveyor according to claim 8, further comprising a counterpressure devic e, which acts on that region of the toothed-belt component which extends on the top si de of the circulating conveying belt.11. Belt conveyor according to claim 8, wherein the free ends of the essentially U-shaped toothed-belt component are designed as a bead.12. Belt conveyor according to claim 8, further comprising guide rollers, which act on one of the toothed belt and the toothed-belt component.13. Belt conveyor having a circulating conveying belt, comprising: carrying rollers arranged between a top strand and a bottom strand of the circulating conveying belt; u pper and lower guide rollers acting on upper and lower beads on the circulating conve ying belt and forcing the circulating conveying belt radially outward, the upper and lo wer beads being formed opposite to each other on the circulating conveying belt; at le ast one toothed ring interacting with at least one toothed belt formed on the circulating conveying belt, whereby the upper bead is neighbored to the toothed belt; and a drive device for moving the circulating conveying belt, wherein a pair of said guide rollers are arranged on angled retaining arms such that the guide rollers act on one of the toot hed belt and the upper and lower beads, by way of inclined running surfaces.14. Belt conveyor according to claim 12, wherein in each case one pair of guide rol lers on the top strand and on the bottom strand of the circulating conveying belt act on one of the toothed belt and the toothed-belt component, extending over the entire bor der region of the circulating conveying belt.15. Belt conveyor according to claim 1, wherein the carrying rollers are of conical configuration and form a belt curve, and wherein the toothed ring undergoes a form-fi tting connection in relation to the circulating conveying belt at the larger-diameter end of the respective carrying roller on the outer radius of the belt curve.16. The belt driving device of claim 1, wherein one of said toothed ring and said to othed belt is releasably fixed to the carrying rollers.Belt conveyor according to claim 16, wherein one of said toothed ring and said toot hed belt is releasably fixed to the force-transmission device by one of.The present invention relates to a belt conveyor having a circulating conveying belt , having carrying rollers, which are arranged between the top strand and the bottom str and of the conveying belt, and having a drive device and a force-transmission device f or moving the conveying belt.BACKGROUND OF THE INVENTIONIt is known from practice for force to be transmitted from the drive device to the co nveying belt of a belt conveyor via friction fitting. The friction between a driven carry ing roller and the conveying belt, for example, may even be sufficient for this purpose . The rest of the carrying rollers are mounted in a movable manner and rotate along. DE 42 44 170 C2Discloses a belt conveyor having an endless conveying belt, the latter being driven by means of a force-transmission device which is present in the form of a friction whe el. A drive shaft extends beneath the bottom strand of the conveying belt. On the inner radius of the belt curve, a motor is connected as a drive device to the drive shaft and, in the region of the outer radius, a friction wheel is seated on the drive shaft and is in c ontact with the outer surface of the conveying belt. In this case, the friction wheel inte racts with a carrying roller functioning as counterpressure roller. The drive shaft is mo unted such that it can be moved at an angle both in the region of the outer radius and i n the region of the inner radius of the belt curve.Theangle mounting of the drive shaft allows adaptation of the exent towhich the friction movablewheel is pressed against the conveying belt in proportion t o the actual load. In this way, the wear is reduced if, in part-load operation, the conve ying belt is only subjected to the contact-pressure force which is necessary for this pur pose.Although the belt conveyor known from DE 42 44 170 C2 reduces the wear of the c onveying belt, it cannot rule it out altogether. The task of conveying foodstuffs or othe r goods which are to be kept clean involves, in addition to the mechanical damage to t he conveying belt, the aspect of hygiene and of keeping goods clean. The abraded surf ace particles of the conveying belt could have a considerable adverse effect on the qua lity of the goods which are to be conveyed. Moreover, the known belt conveyor requir es an extremely high level of structural outlay as far as the movable mounting of the s eparate drive shaft is concerned.Taking as departure point the belt conveyor known from DE 42 44 170 C2, the obje ct of the invention is to specify a belt conveyor of the type in question which largely r ules out any adverse effect to the surface of the coconveying belt of the belt conveyorby the force-transmission device. According to a particularly preferred configuration, the belt conveyor is intended to require just a low level of structural outlay.The above object is achieved by the features of Patent claim 1. According to the latt er, a belt conveyor of the type in question is configured such that a pair of elements w hich interact with one another with a form fit is provided for force-transmission purpo ses, and that one element is assigned to the force-transmission device and the other ele ment is assigned to the conveying belt. According to the invention, it has been found t hat the surface of the conveying belt is not adversely affected as a result of the action of the force-transmission device if a separate pair of elements is provided in order to r ealize force transmission. It has also been found that the use of a pair of movement-co nverting elements which are known per se and interact with one another with a form fi t largely eliminates the disadvantages which are known in the case of friction-fitting movement conversion, in particular wear and abrasion.According to a preferred exemplary embodiment of the belt conveyor according to t he invention, the pair of elements could be present as toothed ring and toothed belt, th e tooth flanks of the toothed ring and of the toothed belt interacting with one another. It would be possible for the toothed ring to be assigned to the force-transmission devic e and for the toothed belt to be assigned to the conveying belt.As far as a particularly low level of structural outlay is concerned, a preferred confi guration of the abovementioned exemplary embodiment provides that the toothed ring is assigned to a carrying roller, and the latter thus simultaneously assumes the role of the force-transmission device. Via a journal projecting from the carrying roller, the dri ve takes place by means of a motor. The toothed ring could be plugged onto the carryi ng roller and fixed releasably—for example via a shaft/hubconnection or a feather key —to the same.In the case of a plugged-on toothed ring, it isadvantageous that it is possible to use carrying rollers which are already present. It is particularly advantageous for each carr ying roller to be assigned at least one toothed ring. Over the entire running path of the conveying belt, it would then be the case that the toothed belt and the toothed rings int erengage and move the conveying belt in a dimensionally stable manner. Corresponding to the toothed ring or rings which is/are arranged between the top and bottom stran ds and belongs/belong to the preferred configuration mentioned above, the toothed bel t is arranged on the underside of the conveying belt, and extends in the running directi on of the same. Arranging the toothed belt on the underside of the conveying belt onc e again ensures that the top side of the conveying belt, which is charged if appropriate with goods which are to be kept clean, is not subject to any force transmission, mecha nical damage or production of abrasion particles or other contaminants.An expedient development of the preferred configuration of the belt conveyor acco rding to the invention makes provision for the toothed ring to be arranged at the end o f the carrying roller. As a result, on the one hand, straightforward maintenance of the f orce-transmission device is made possible and, on the other hand, this arrangement is also more cost-effective than a, for example, central arrangement. Direct force transmi ssion over a short distance is achieved by a journal for the connection of the drive dev ice projecting from that end of the carrying roller which is provided with the toothed r ing.It is particularly advantageous if the toothed belt extends in the region of the side b order of the conveying belt. As a result, on the one hand, straightforward production o f the conveying belt with the toothed belt is made possible by the direct relationship to the border region and, on the other hand, a role is also played here by the accessibilit y to the pair of elements for maintenance purposes and, of course, by the coordination between the toothed belt and the arrangement of the toothed ring.In addition to toothed belts and toothed rings with normal toothing, it would also b e possible to realize multisplining. This further reduces undesired sliding and thus we ar, heating and noise development. In order to absorb high tensile forces, it would be possible for Kevlar filaments to be incorporated in the toothed belt, which usually con sists of plastic. It would be possible for the conveying belt to be produced with the too thed belt by welding, vulcanizing or adhesive bonding. According to a particularly pre ferred configuration, it would be possible for the toothed belt to be a constituent part o f a toothed- belt component which is of essentially U-shaped design in the transverse direction of the toothed belt.The U-shape makes it possible for the toothed- belt component simply to be plugge d onto the border of the conveying belt until the border region has come into contact with the base part between the U-legs. The inner surface of the toothed- belt compone nt may have been provided with adhesive beforehand. As a result of its shaping and of being produced in this way, the toothed- belt component engages around the side-bor der region of the conveying belt.While the toothed belt of the conveying belt is subjected to compressive force by th e toothed ring, and this largely rules out detachment of the toothed- belt component o n the underside of the conveying belt, a counterpressure device could be provided in o rder to secure that region of the toothed- belt component which extends on the top sid e of the conveying belt. In design terms, the leg of the counterpressure device could b e present in the form of an arm which acts on the U-toothed- belt component on the to p side and thus constantly presses the same onto the top side of the conveying belt. As far as reliable guidance is concerned, it would be possible for the toothed belt or the toothed- belt component containing the toothed belt to form a bead. A bead ridge is thus produced over the length of the conveying belt. In the case of a U-shaped tooth ed- belt component, the bead ridge extends in each case at the free ends of the U-legs, at a distance from the border of the conveying belt, the distance depending essentially on the width of the toothed belt. As an alternative to a bead ridge, it would be possible for the toothed- belt component or for the straightforward toothed belt also to have at least one beveled free end. The guidance measure taken on the toothed belt or on the s pecific toothed- belt component is provided in order that a guide roller or a pair of gui de rollers acts on the beveled surface or on the bead or bead ridge. The guidance meas ure explained above could be taken equally well in the case of belt curves and straight belt lines and of belt S-shapes bridging different heights.In the case of belt curves, the force acting on the conveying belt is directed toward the inner radius of the belt curve, with the result that the guide rollers, in an advantage ous manner which is known per se, could have inclined running surfaces. Correspondi ngly angled retaining arms as a constituent part of retaining structures for the guide ro llers could be arranged in each case in the region of a carrying roller. The guide rollers could be arranged in pairs on the top strand and on the bottom strand of the conveyi ng belt.It should be emphasized at this point that, with the abovementioned configuration o f the belt conveyor according to the invention having the bead or beveled free ends, t wo functions are combined in the pair of form-fitting elements. Not only the force tra nsmission, but also the guidance of the conveying belt, takes place. The dimensional s tability of the conveying belt isadvantageously increased by the pair of form-fitting el ements with the specific configuration of the toothed belt or of the toothed- belt comp onent for action of the guide rollers thereon.In the case of the already cited design of the belt conveyor in the form of a belt curv e, the carrying rollers are of conical design and the toothed ring is arranged at the larg er-diameter end of the respective carrying roller, that is to say on the outer radius of th e belt curve. The drive device is present as a motor and is assigned to the first carrying roller of the belt curve. The form-fitting interengagement of the toothed wheel and to othed belt takes place in the region of each carrying roller, the form fit, in relation to t he first, motor-driven carrying roller, serving for force-transmission purposes and, in r elation to the rest of the rollers, serving for guiding the conveying belt.The previously explained principle of force transmission via a pair of elements w hich interact with one another with a form fit could also be used in the case of a straig ht belt line or in the case of a height-changing belt S-shape. Here, the carrying rollers are of a cylindrical design and the force transmission takes place—as with the belt cur ve—at a first carrying roller, while the followingcarrying rollers, likewise equipped w ith the pair of form-fitting elements, serve for guiding the conveying belt. In contrast t o the belt curve, however, it would be possible, in the case of the straight belt line or i n the case of the belt S-shape, for the pair of elements to be arranged at the two free e nds of the respective carrying roller and on the two border regions of the conveying b elt. It would thus be possible specifically for the two border regions of the conveying belt to have a toothed belt or a toothed- belt component which interacts with the tooth ed rings at the two free ends ofeac carrying roller. Furthermore, it would also be possible, with these types of construction of the belt conveyor according to the invention, to provide guide rollers.A further advantage of the preferred embodiment of the belt conveyor according to th e invention, the toothed ring and toothed belt interacting, consists in the improved cap acity for controlling the belt speed in accordance with the current loading. It would be possible to provide a control device which senses a change in the speed by correspon ding measuring sensors and adjusts the power of the drive device in line with the safet y regulations.In comparison with the force transmission realized by friction fitting, the belt con veyor according to the invention not only has the advantage of better capacity for cont rol, but also has the advantage that the conveying belt has a high level of dimensional stability as a result of the guidance by means of the pair of form-fitting elements and b y means of the pairs of guide rollers and can be subjected to higher torques. Overall, it is possible to achieve an increased level of drive power during start-up. In the case of the belt conveyor according to the invention being designed in the form of a belt curv e with an inner radius of 400 mm, the carrying rollers rotate at 230 rpm at a maximum speed of 1.5 m/sec.There are various possibilities then, of advantageously configuring and developin g the teaching of the present invention. For this purpose, reference is made, on the one hand, to the claims subordinate to Patent claim 1 and, on the other hand, to the follow ing explanation of an exemplary embodiment of the invention with reference to the dr awing. In conjunction with the explanation of the cited exemplary embodiment of the invention, generally preferred configurations anddevelopments of the teaching are also explained.中文译文带式输送机是连续运动的无端输送带输送货物的机械。
带式输送机论文中英文资料外文翻译文献

带式输送机论文中英文资料外文翻译文献中英文资料外文翻译文献A Comparison of Drive Starting Mechanisms forAggregate Belt ConveyorsAbstractThe purpose of this paper is to describe the torque/speed characteristics,during starting conditions,of the most common drives used on belt conveyors today. Requirements of a Belt Conveyor DriveA belt conveyor is considered to be a constant torque device. In other words,the required driving torque is approximately constant at varying speeds (see figure l).other applications,such as a pump drive,have variable torque requirements(see figure2).However,to increase the speed of a conveyor additional torque must be added until the desired speed is obtained. Newton’s Second Law of Motion governs this relationship.∑=F m aThe most straightforward example would be a constant acceleration torque(see figure3).In reality the acceleration torque is rarely constant. However,static calculation models as outlined in the Conveyor Equipment Manufacturers Association handbook (CEMA) make this assumption. When using static models the average acceleration torque is estimated over the entire acceleration time and assumed to be linear. Dynamic models,which are beyond the scope of this paper,allow acceleration torque values to vary in magnitude during the acceleration(or deceleration)Period.It should be noted that,given a constant load,a larger acceleration torque results in a faster acceleration time and also higher Peak belt tensions. Conversely,a smalleracceleration torque results in a longer start time and smaller Peak belt tensions. Across-The-Line AC Motor StartTechnically this is the simplest type of drive used on a belt conveyor. In this drive type an AC squirrel cage induction motor is started by simply throwing the contactor and energizing the motor. The resulting output torque,assuming that rated voltage is maintained,is strictly a function of the motor design. NEMA has Provided design standards that define the output torque characteristics of the most commonly used 3 Phase motors up to approximately 250 hp(figure4).In sizes larger than 250 hp manufacturers generally use the NEMA design codes in a relative manner(i.e.,NEMA C has a greater locked rotor torque than a NEMA B motor).The most critical locations on the AC motor speed/torque curve have been named for definition purposes. These common names are provided in figure 5.The most rigorous method of determining average acceleration torque,for staticcalculations,is to break the curve into several verticalsections,then sum the individual areas under the curve and finally divide by the number of sections.The more common way is to apply the following simplified equation:These static approximation methods work for most belt conveyors but can get the designer into trouble from time to time,especially on long and/or steep and/or fast conveyors. One item that needs to be examined is breakaway torque. Just because the drive provides enough average torque to accelerate the load doesn’t mean that it provides enough torque to break it away from zero speed and get it moving.CEMA defines breakaway torque as twice the torque required to overcome the total friction plus the torque required to lift the load vertically. Locked rotor torque (LRT) needs to be greater than breakaway torque! A good static Program makes this check.In addition to examining the effect that average torque has on the conveyor components the belt designer needs to determine the effect of peak torque. It is not uncommon for the breakdown torque (BDT) of a NEMA C motor to be greater than2.5 times full load torque (FLT).Generally the belting and Pulley manufacturers allowa transient overload of 1.5 times full load operating load. An across-the-line start can easily cause tensions to exceed these maximums. These higher than normal loads can be designed into the conveyor if they are known up front.Considering only average starting torque can cause the conveyor designer to undersize the take-up weight. It is notuncommon for conveyors with across-the-line starters to experience intermittent drive slip. This generally happens when Peak torque (BDT) is input by the drive and the take-up has been sized for average torque but not peak torque. The result can be devastating. When the drive pulley slips during thiscondition,the tension on the Tl and T2 sides (high and low)of the drive Pulley tries to equalize. This can subject a low tension bend or take-up pulley,just behind the drive pulley,to tensions that approach Tl tension. These Pulleys are rarely,if ever,designed for this load condition and the result is low tension Pulley failure. This condition is easily demonstrated with dynamic analysis.Another common Problem with across-the-line starts is caused by voltage dips during starting. If the power distribution system is not stiff enough to handle the huge inrush currents of an across-the-1ine start,the starting torque of the motors can be reduced to a Point that the conveyor will not start. This is due to the fact that the output torque of an AC squirrel cage induction motor is reduced by the square of the applied voltage. In other words,a voltage drop of 10%would equate to a torque reduction of 19%. Reduced Voltage StartingThe reduced voltage starting of an AC squirrel cage induction motor is done for two basic reasons:1 .To reduce the inrush current that naturally occurs when a motor is Startedacross-the-1ine. A typical current/speed graph is shown in figure 6.It is not uncommon for the inrush current to be 6 times or more than it is at full load torque. As stated above high inrush currents cause the voltage in a power distribution system to sag. The cost of electrical power distribution equipment can becomevery high if it needs to be designed to handle the high inrush currents.2 . To reduce Peak motor torque during starting conditions,which subsequentlyincreases acceleration time. By reducing the Peak torques the conveyor components can be designed for lower tension loads. This primarily includes belting,Pulleys and external support structure. This can result in significant cost savings.Two common types of reduced voltage starters are the Current Limiting and the Constant Torque devices.Graphs are included above(figures 7 through 8) that depict the same motor/conveyorapplication with an Across-The-Line,a limitd Curren, and a constant Torque start. After studying the graphs it becomes apparent that the best use of the limited torque start is to protect the power distribution system from high inrush currents. The constant torque start reduces the high torque Peaks and Protects the conveyor’s mechanical components. In both cases the Start time is increased because the over all magnitude of acceleratingtorque is reduced. However,neither method will make it easier to start a“hard-to-start conveyor.”Correcting a hard starting conveyor is not a reason to use a reduced voltage starter!翻译带式输送机驱动方式比较摘要本文的目的是描述最常见的机用输送皮带起动时的扭矩/转速特性。
带式输送机及其牵引系统机械外文文献翻译、中英文翻译、外文翻译
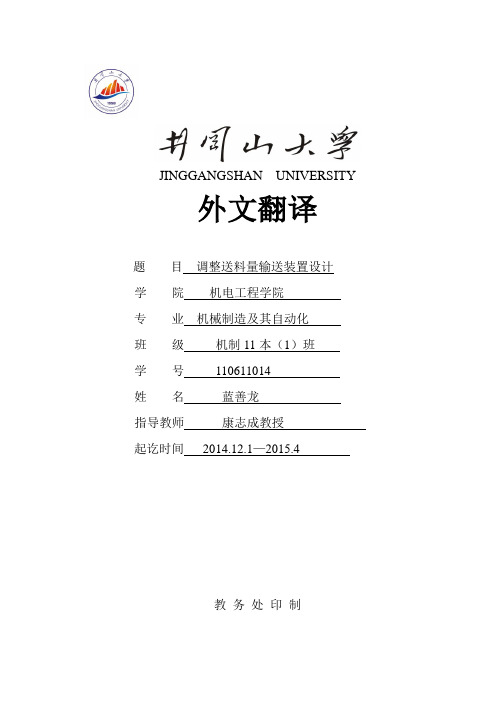
JINGGANGSHAN UNIVERSITY外文翻译题目调整送料量输送装置设计学院机电工程学院专业机械制造及其自动化班级机制11本(1)班学号110611014姓名蓝善龙指导教师康志成教授起讫时间2014.12.1—2015.4教务处印制AbstractBulk material transportation requirements have continued to press the belt conveyor indu stry to carry higher tonnages over longer distances and more diverse routes. In order keep up, si gnificant technology advances have been required in the field of system design, analysis and nu merical simulation. The application of traditional components in non-traditional applications re quiring horizontal curves and intermediate drives have changed and expanded belt conveyor po ssibilities. Examples of complex conveying applications along with the numerical tools require d to insure reliability and availability will be reviewed.Belt Conveying Systems Development of driving system Among the methods of material conveying emploved, belt conveyors play a very imporient part in the reliable carrying of material over long distances at competitive cost. Conveyor systems have become larger and more complex and drive systems have a l so been going through a process of evolution and will continue to do so. Nowadays, bigger belts require more power and have brought the need for larger individual drives as well as multiple drives such as 3 drives of 750 kW for one belt(this is the case for the conveyor drives in Chengzhuang Mine). The ability to control drive acceleration torque is critical to belt conveyors' performance. A efficient drive system should be able to provide smooth, soft starts while maintaining belt tensions within the specified safe limits. For load sharing on multiple drives. torque and speed control are also considerations in the drive system's design. Due to the advances in conveyor drive control technology, at present many more reliable. Cost-effective and performance- driven conveyor drive systems covering a wide range of power are available for customers' choices[1]. 1 Analysis on conveyor drive technologies1. 1 Direct drives Full-voltage starters.With a full-voltage starter design, the conveyor head shaft is direct-coupled to the motor through the gear drive. Direct 8 full-voltage starters are adequate for relatively low-power, simple- Profile conveyors. With direct full-voltage starters. no control is provided for various conveyor loads and. depending on the ratio between full- and no-load power requirements, empty starting times can be three or our times faster than full load. The maintenance-free starting system is simple, low-cost and very reliable. However, they cannot control starting torque and maximum stall torque; therefore. they are limited to the low-power, simple-profile conveyor belt drives.Reduced-voltage starters. As conveyor power requirements increase,controlling theapplied motor torque during the acceleration period becomes increasingly important. Because motor torque is a function of voltage, motor voltage must be controlled. This can be achieved throughreduced-voltage starters by employing a silicon controlled rectifier (SCR). A common starting method with SCR reduced-voltage starters is to apply low voltage initially to take up conveyor belt slack. and then to apply a timed linear ramp up to full voltage and belt speed. However, this starting method will not produce constant conveyor belt acceleration. When acceleration is complete. the SCRs, which control the applied voltage to the electric motor. are locked in full conduction, providing full-line voltage to the motor. Motors with higher torque and pull -vp torque, can providebetterstarting torque when combined with the SCR starters, which are available in sizesup to 750 KW.Wound rotor induction motors. Wound rotor induction motors are 9 connected directly to the drive system reducer and are a modified onfiguration of a standard AC induction motor. By inserting resistance in series with the motor's rotor windings. the modified motor control System controls motor torque. For conveyor starting, resistance is placed in series with the rotor for low initial torque. As the conveyor accelerates,the resistance is reduced slowly to maintain a constant acceleration torque. On multiple-drive systems. an external slip resistor may be left in series with the rotor windings to aid in load sharing .the motor systems have a relatively simple a design.However,the control systems for these can be highly complex, because they are based on computer control of the resistance switching. Today, the majority of control systems are custom designed to meet a conveyor system's particular specifications. Wound rotor motors are appropriate for systems requiring more than 400KW.DC motor. DC motors. available from a fraction of thousands of KW,are designed to deliver constant torque below base speed and constant KW above base speed to themaximum allowable revolutions per minute (r/min). with the majority of conveyor drives, a .DC shunt wound motor is used. Wherein the motor's rotating armature is connected externally. The most common technology for controlling DC drives is a SCR device. which allows for continual variable-speed operation. The DC drive system is mechanically simple, but can include complex custom-designed electronics to monitor and control the complete system. this system option is expensive in comparison to othersoft-start systems. but it is a reliable, cost-effective drive in applications in which torque,load sharing and variable speed are primary considerations. DC motors generally are used with higher-power conveyors, 10 including complex profile conveyors with multiple-drive systems, booster tripper systems needing belt tension control and conveyors requiring a wide variable-speed range.1. 2 Hydrokinetic coupling2.Hydrokinetic couplings, commonly referred to as fluid couplings. are composed of threebasic elements; the driven impeller, which acts as a centrifugal pump; the driving hydraulic turbine known as the runner and a casing that encloses the two power components.Hydraulic fluid is pumped from the driven impeller to the driving runner, producing torqueat the driven shaft. Because circulating hydraulic fluid produces the torque and speed, no mechanical connection is required between the driving and driver shafts.The power produced by this coupling is based on the circulated fluid's amount and density and the torque in proportion to input speed. Because the pumping action within the fluid coupling depends on centrifugal forces. the output speed is less than the input speed. Referred to as slip. this normally is between 1% and 3%. Basic hydrokinetic couplings are available in configurations from fractional to several thousand KW.Fixed-fill fluid couplings. Fixed-fill fluid couplings are the most commonly usedsoft-start devices for conveyors with simpler belt profiles and limited convex/concave sections. They are relatively simple,low-cost,reliable,maintenance free devices that provide excellent soft starting results to the majority of belt conveyors in use today.Variable-fill drain couplings. Drainable-fluidcouplings work on the same principle as fixed-fill couplings. The coupling's 11 impellersare mounted on the AC motor and therunners on the driven reducer high-speed shaft. Housing mounted to the drive base encloses the working circuit. The coupling's rotating casing contains bleed-off orifices that continually allow fluid to exit the working circuit into a separate hydraulic reservoir. Oil from the reservoir is pumped through a heat exchanger to a solenoid-operated hydraulic valve that controls the filling of the fluid coupling. To control the starting torque of a single-drive conveyor system, the AC motor current must be monitored to provide feedback to the solenoid control valve. Variable fill drain couplings are used in medium to high-kw conveyor systems and are available in sizes up to thousands of kw.The drives can be mechanically complex and depending on the control parameters. the system can be electronically intricate. The drive system cost is medium to high,depending upon size specified.Hydrokinetic scoop control drive. The scoop control fluid coupling consists of the three standard fluid coupling cmponents: a driven impeller, a driving runner and a casing that encloses the working circuit. The casing is fitted with fixed orifices that bleed a predetermined amount of fluid into a reservoir. When the scoop tube is fully extended into the reservoir, the coupling is 100 percent filled. The scoop tube, extending outside the fluid coupling, is positioned using an electric actuator to engage the tube from the fully retracted to the fully engaged position. This control provides reasonably smooth acceleration rates. to but the computer-based control system is very complex. Scoop control couplings areVariable-frequency control(VFC) Variable frequency control is also one of the direct drive methods. the emphasizing discussion about it here is because that it has so unique characteristic and so good performance compared with other driving methods for belt conveyor. VFC devices Provide variable frequency and voltage to the induction motor, resulting in anexcellent starting torque and acceleration rate for belt conveyor drives. VFC drives. available from fractional to several thousand (kW),are electronic controllers that rectify AC line power to DC and, through an inverter, convert DC back to AC with frequency and voltage control. VFC drives adopt vector control or direct torquecontrol(DTC)technology, and can adopt different operating speeds according to different loads. VFC drives can make starting or stalling according to any given S-curves realizing the automatic track for starting or stalling curves. VFC drives provide excellent speed and torque control for starting conveyor belts. and can also be designed to provide load sharing for multiple drives. easily VFC controllers are frequently installed on lower-powered convey- or drives, but when used at the range of medium-high voltage in the past. the structure of VFC controllers becomes very complicated due to the limitation of voltage rating of power semiconductor devices, the combination of medium-high voltage drives and variable speed is often solved with low-voltage inverters using step-up transformer at the output, or with multiple low-voltage inverters connected in series. Three-level voltage-fed PWM converter systems are recently showing increasing popularity for multi-megawatt industrial drive applications because of easy voltage sharing between the series devices and iroved 13 harmonic quality at the outputcompared to two-level converter systems With simple series connection of devices. This kind of VFC system with three 750 kW /2. A V inverters has been successfully installed in ChengZhuang Mine for one 2. 7-km long belt conveyor driving system in following the principle of three-level inverter will be discussed in detail. 2 Neutral point clamped(NPC)three-level inverter using IGBTs Three-level voltage-fed inverters have recently become more and more popular for higher power drive applications because of their easy voltage sharing features. lower dv/dt per switching for each of the devices, and superiorharmonic quality at the output. The availability of NV-IGBTs has led to the design of a new range of medium-high voltage inverter using three-level NPC topology. This kind of inverter can realize a whole range with a voltage rating from 2. 3 kV to 4. 16kV Series connection of IIV-IGBT modules is used in the 3. 3 kV and 4. 1 6kV devices. The 2. 3 kV inverters need only one HV-IGBT per switch[2,3].2. 1 Power section To meet the demands for medium voltage applications. a three-level neutral point clamped inverter realizes the power section. In comparison to a two-level inverter. the NPC inverter offers the benefit that three voltage levels can be supplied to the output terminals, so for the same output current quality, only 1/4 of the switching frequency is necessary. Moreover the voltage ratings of the switches in NPC inverter topology will be reduced to 1/2. and the additional transient voltage stress on themotor 14 can also be reduced to 1/2 compared to that of a two-level inverter.The switching states of a three-level inverter are summarized in Table 1. U. V and W denote each of the three phases respectively; P N and 0 are the do bus points. The phase U, for example, is in state P (positive bus voltage)when theswitches S1uand S2u are closed, whereas it is in state N (negative bus voltage) when the switches S3u and S4u, are closed. At neutral point clamping, the phase is in 0 state when either S2u.or S3u, conducts depending on positive or negative phase current polarity, respectively. For neutral point voltage balancing, the average current injected at 0 should be zero.2. 2 Line side converter For standard applications. a 12-pulse diode rectifier feeds the divided DC-link capacitor. This topology introduces low harmonics on. the line side. For even higher requirements a 24-pulse diode rectifier can be used as an input converter. For more advanced applications where regeneration. capability is necessary, an active front. end converter can replace the diode rectifier, using the same structure as the inverter.2. 3 Inverter control Motor Control. Motor control of induction machinesis realized by using a rotor flux. oriented vector controller. Fig. 2 shows the block diagram of indirect vector controlled drive that incorporates both constant torque and high speed field-weakening regions where the PW M modulator was used. In this figure, the command fluxψ.is generated as function of speed. The feedback speed is added with the feed 15 forward slip command signalψ,the resulting frequency signal is integrated and then the unit vector signals(cosθe and sinθ e)are generated. The vector rotator generates the voltage Vs and Angle θe commands for the PW M as shown.PWM Modulator. The demanded voltage vector is generated using an elaborate PWM modulator. The modulator extends the concepts of space-vector modulation to the three-level inverter. The operation can be explained by starting from a regularly sampled sine-triangle comparison from two-level inverter. Instead of using one set of reference waveforms and one triangle defining the switching frequency, three-level Modulator uses two sets of reference waveforms Uand U and just one triangle. Thus, each switching transition is used in an optimal way so that several objectives are reached at the same time. Very low harmonics are generated. The switching frequency is low and thusswitching losses are minimized. A in a two-level inverter, a zero-sequencecomponent can be added to each set of reference waveform s in order to maximize the fundamental voltage component. As an additional degree of freedom, the position of the reference waveform s within the triangle can be changed. This can be used for current balance in the two halves of the DC-link. 3 Testing results After Successful installation of three 750 kW /2. 3 kV three-level inverters for one 2. 7 km long belt conveyor driving system in Cheng zhuang Mine. The performance of the whole VFC system was tested. Fig. 3 is 16 taken from the test, which shows the excellent characteristic of the belt conveyor driving system with VFC controller. Fig. 3 includes four curves. The curve 1 shows the belt tension . From the curve it can be find that the fluctuation range of the belt tension is very small. Curve 2 and curve 3 indicate current and torque separately. Curve 4 shows the velocity of the controlled belt. The belt velocity have the "s" shape characteristic. All the results of the test show a very satisfied characteristic for belt driving system. 4 Conclusions Advances in conveyor drive control technology in recent years have resulted in many morereliable. Cost-effective and performance-driven conveyor drive system choices forusers.Among these choices,theVariable frequency control (VFC) method shows promising use in the future for long distance belt conveyor drives due to its excellent performances. The NPC three-level inverter using high voltage TGBTs make the Variable frequency control in medium voltage applications become much more simple because the inverter itself can provide the medium voltage needed at the motor terminals, thus eliminating the step-up transformer in most applications in the past. The testing results taken from the VFC control system with NTC three. level inverters used in a 2. 7 km long belt conveyor drives in Chengzhuang Mine indicates that the performance of NPC three-level inverter usingHV-TGBTs together with the control strategy of rotor field-oriented vector control for induction motor drive is excellent for belt conveyor driving system.References:[1]Kung, Walter, “The Henderson Coarse Ore Conveying System-A Review of Commissioning, Start-up, and Operation”, Bulk Material Handling by Belt Conveyor 5, Society for Mining, Metallurgy and Exploration , Inc., 2004 ;[2]Alspaugh, Mark, “The Evolution of Intermediate Driven Belt Conveyor Technology”, Bulk Solids Handli ng”, Vol. 23 (2003) No.3;[3]Goodnough, Ryne, “In-Pit Conveying at the Wyodak Mine- Gillette, Wyoming” , Bulk Material Handling by Belt Conveyor 5, Society for Mining, Metallurgy and Exploration, Inc., 2004 ;[4]Dewicki, Grzegorz, “Bulk Material Handling and Processing- Numerical Techniques and Simulation of G ranular Material”, Bulk Solids Handling”, V ol. 23 (2003) No.2.摘要粒状材料运输要求带式输送机具有更远的输送距离、更复杂的输送路线和更大的输送量。
带式输送机的设计与制作毕业设计(含外文翻译)
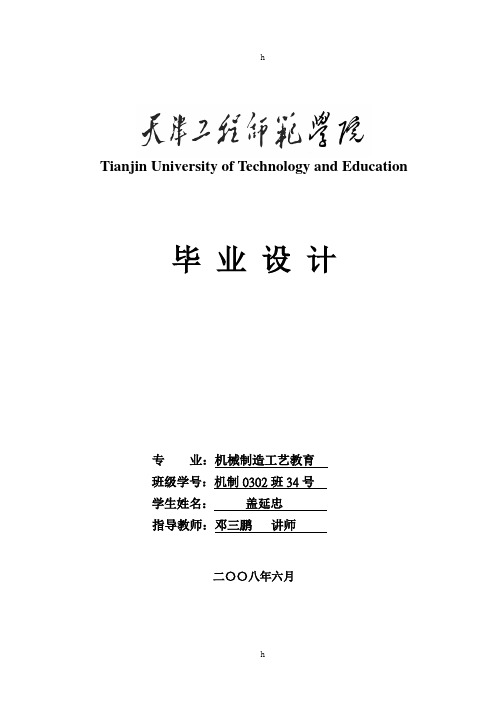
Tianjin University of Technology and Education 毕业设计专业:机械制造工艺教育班级学号:机制0302班34号学生姓名:盖延忠指导教师:邓三鹏讲师二〇〇八年六月天津工程师范学院本科生毕业设计带式输送机的设计与制作Study on Automatic Feeding Device of Polyacrylamine ——Design and Manufacture of Belt Conveyors专业班级:机械制造工艺教育学生姓名:盖延忠指导教师:邓三鹏讲师系别:机械工程学院2008年6摘要带式输送机是以输送带作为牵引和承载构件,通过承载物料的输送带运动进行物料输送的连续输送设备,它不仅应用于企业内部的运输,也拓展到企业外部的输送,广泛应用于冶金、矿山、港口、粮食和化工等领域。
随着工业的发展,对带式输送机的需求越来越大。
首先分析了国内外带式输送机的现状与发展。
通过工况的分析和各种输送机的优缺点的比较,确定了普通带式输送机为基本结构,改进输送带形状,改向滚筒等的设计方案。
通过计算输送带的张力,确定了电机功率;根据料袋的大小确定了输送带的宽度;根据负载情况确定了滚筒和托辊的参数,并分别进行了校核;根据作业空间确定了倾角,由于倾角达到了30°,属大倾角传动,为防止打滑改进了输送带和改向滚筒,并选用了较低的传送速度。
设计了输送带的张紧装置和上袋限位装置。
最后分析了带式输送机跑偏的原因并提出了纠正措施;并对固定带式输送机安装及试运转方法进行了详细的说明。
完成了整个带式输送机的制作,运行结果表明:所设计的带式输送机运行平稳可靠,达到在小空间实现大倾角送料而不打滑的目的,很好的完成了预定任务。
关键词:输送带;滚筒;托辊ABSTRACTThe belt conveyer is takes the hauling and the carrying piece by the conveyor belt, carries on material handling's stream handling equipment through the load bearing material's conveyor belt movement, it not only applies in the enterprise internal transportation, also develops the enterprise exterior transportation, widely applies in domains and so on metallurgy, mine, harbor, grain and chemical industry. Along with the industry development, the needing is getting bigger and bigger to the belt conveyer's demand.First it has analyzed the domestic and foreign belt conveyer's present situation and the development. Through the operating mode analysis and each kind of belt conveyer's good and bad points' comparison, it had determined the ordinary belt conveyer is the basic structure, improves the conveyor belt shape, changes to the drum and so on design proposal. Through calculates conveyor belt's tensity, it has determined the electrical machinery power; Has determined conveyor belt's width according to feed bag's size; Had determined according to the load situation the drum and supporting roller's parameter, and has carried on the examination separately; Has determined the inclination angle according to the working space, because the inclination angle has achieved 30°, is the great inclination angle transmission, to prevent to slip improved the conveyor belt and changes to the drum, and has selected the low transfer rate. Has designed conveyor belt's stretching device and the previous bag stop block. The ultimate analysis belt type conveyer has run the leaning reason and proposed the correction measure; And it has carried on the detailed explanation to the fixed belt conveyer installment and the test run method.Completing the entire belt conveyer's manufacture, the movement result had indicated: Designs belt conveyer movement steady reliable, achieves realizes the goal which in the small space the great inclination angle feeding does not slip, very good has completed the task.Key words: Belt conveyer;Roller;Pulley目录1绪论 (1)1.1项目研究的背景 (1)1.2国内外带式输送机的发展概况 (2)1.3设计的主要任务 (5)2设计方案的选择 (6)2.1方案1普通带式输送机 (6)2.2方案2移动式带式输送机 (7)2.3方案分析比较及方案的选择 (9)3带式输送机的设计及制作 (11)3.1带式输送机的系统设计 (11)3.1.1输送机布置方案的确定 (11)3.1.2带式输送机设计的原始资料和工作条件 (12)3.2输送带的结构与选择 (12)3.2.1输送机对输送带的要求 (12)3.2.2输送机的带速和宽度的确定 (13)3.2.3输送带的磨损形式 (15)3.3带式输送机托辊的设计 (15)3.3.1托辊的性能及托辊直径的选择 (15)3.3.2托辊间距的确定 (16)3.3.3托辊的加工工艺 (17)3.4滚筒的设计 (18)3.5设计过程中的相关计算 (20)3.5.1由带速、带宽验算输送能力 (21)3.5.2驱动辊筒有效张力的计算和传动方案的设计 (21)3.5.3输送带张力的计算 (23)3.5.4校核托辊载荷 (25)3.6张紧装置选择 (28)3.7带式输送机的加工安装和试运行 (29)3.7.1带式输送机跑偏的原因及纠正 (29)3.7.2固定带式输送机安装及试运转方案 (30)3.7.3大倾角输送机的解决方案 (31)3.7.4物料的限位机构 (32)3.8输送机的电气控制设计 (32)结论 (34)致谢 (35)参考文献 (36)外文翻译 (37)1绪论1.1项目研究的背景聚丙烯酰胺(polyacrylamids)简称PAM,是一种线型高分子聚合物,是水溶性高分子化合物中应用最为广泛的品种之一,聚丙烯酰胺和它的衍生物可以用作有效的絮凝剂,增稠剂,纸张增强剂,以及液体的减阻剂等,广泛应用于水处理、造纸、石油、煤矿、矿冶、地质、轻纺,建筑等工业部门。
带式输送机的的特点与应用外文翻译、中英文翻译、外文文献翻译

翻译部分英文原文1.1 The take type transports the characteristics and the application of the machineThe take type transports machine since 1795 was disheveled hair and clear,through the development of more than twocenturies,already drive electric power、metallurgy、coal、chemical engineering、mineral mountain、portetc.every trade adopts extensively.Especially the Industrial Revolution brings material,lately technical adoption for the third time lately and makes the take type transport the development of the machine to follow a new era.In now days ,whether appraise from carry、length、economy-effectiveness and so on.It can be the same train,automobile transport to match the situation as it stands,and become the first to the development of industries.1.1.1 The take type transports the characteristics of the machine:(1) The structure is simple.Followed by belt conveyor drive pully to one drum,or idlerroller components、drives、conveyors several large components.Only a dozen or morecomponents,production can be standardized and may require portfolio assembly,thestructure is very simple;(2) Transport the material scope extensively.Conveyor belt with wear,corrosionresistance ,oil resistance,such as fire-retardant properties,and high-resistance,lowtemperature,may be required to produce,which will transport all kinds of stuff,blockmaterials,chemicals,the Health clinker and concrete;capacity.Volumeolume per hour from a few kilograms to several(3) Transport to have great capacity.Vthousands of tons,but is uninterrupted deliveryThis is the train,the automobile conveyance is too far behind to catch up;(4) The luck is apart from to grow.Single length of up to 10 kilometers an abroad,is verypopular,in the middle reproduced without any points.Cross-countrily the take type transports machine to often use to rub to drive a way inthe center,making to transport the restriction that the length is free from the beltconveyer strength.(5) It is strong to the circuit adaptability.Modern belt conveyor in layingcross-country,from the trough to tube-shaped,it can be horizontal and vertical planetumed breaking the mold conveyor or not bend the restrictions,which will rely onmountain water,and walk along the terrain,can save a lot of a tunnel,bridgeinfrastructure investment;(6) Pack to unload very convenient.Under the belt conveyor process needs,may at anypoint on the equipment and dump;Pipe conveyor as well.Can also pack,unload to anticipate on the return journey segment ,carry on anti-toconveyance;(7) The credibility is high .As simple structure,moving parts light weight ,as long as thebelt is not torn,with a life span of 10 years,metal components,as long as antirustgood,for the past several decades is not a bad idea;(8) The operation fee is cheap.Wear parts belt conveyor idlers and only roller,conveyorlongevity,a high degree of automation,use of the staff is small,per km on average lessthan one,the consumption of oil and electricity rarely;(9) Can consume low,the efficiency is high.Since moving parts as light weight,low voidshipped in all non-continuous and continuous transport,Belt conveyor energyminimum,maximum efficiency;(10) Maintain a fee little .Belt conveyor is the only moving parts and idler pulley,belt wearis very.Compare under,the train,automobile wears away a parts to want many,and replace towear away a piece also more multifarious;On the other say,the take type transports the superiority of the machine already veryobviously,it is the key equipments of the indispensability in the nationaleconomy .Moreover,Internet the realization has been greatly shortened the beltconveyor design,development,manufacture,sales cycles,make it more competitive.1.2 The take type transports the present condition and the development of the machineTake type’s transporting machine is the coal mine is the most ideal to transport an equipments efficiently and continuously,compared with other conveyance equipmentses have distance of transport long,the carrying capacity is big and continue to transport etc.advantage,and circulate credibility,be easy to the realization automation and concentrate to turn a control,particularly to high produce efficiently the mineral well,the take type transports the key equipments that the machine has become coal to mine the machine electricity integral whole to turn a technique and equips.Along with the our country is high to produe of mineral well efficiently now,the take type that is originally possessed’s transporting machine is a regardless main parameter to still circulate functions and all have already can’t satisfy a request,have to the long pull,high take soon,big carrying capacity,big power of large turn the direction development,and want improve and raise to circulate function, insure safe credibility.The take type that the our country production make transports the species,type of the machine moreFive--Y ear Plan”period,the national oneone--stop “Nissan 10,000 tons .In the”Enghth Fivemore.In-greatly improved,and mine withhas-greatlyfully mechanized equipment”projects,conveyor technology hashigh power .The key to long-distance belt conveyor technology research and development of new products ,LU has made considerable progress.Such as the big cape long pull take type transport machine to become a set an equipments,high produce to work efficiently noodles fluently slot the flexible take type transport machine ,etc.all filled up local bland ,and transport machine to turn down the key technique to the take type and it main dollar the parts carried on the theories research and the product development,develop successfully variety soft start and make to move equip and take PLC as core of the programmable electricity control device,driving the system adoption to adjust soon type the liquid dint matches the machine and the planet wheel gear to decelerate a machine accidentally.The coal mine take type transports technical development trend of machine .The equipments is large to turn,the exaltation transport an ability:For adapt high produce efficiently intensive turn the demand of the production,the take type transports machine to transport an ability to want enlargement.Long-distance,high belt speed,large-capacity,high-power future is the inecitable trend of development,as well as transport for the high-technology development direction.Transport quantity and raise to the 3000-4000 ts/h in the 10 as of aftertime also raise to the 4-6ms/s soon,transport length to transport to the flexible take type confidential attain a 3000ms.For strength steel belt conveyor take longer to 5,000 m above single-driven power demandreached 1,000~1,500 kw,conveyor tensile strength reached 6,000 N/mm (steel cord)and 2500 N/mm (steel cord).By the coal mine well to descend agreeable slot particularly flexible transport a technical development,along with high produce efficiently continuously develop of the emergence and the coal science and technology of work the noodles,the original flexible take type transports machine,is a regardless main parameter,still circulate functions all hard adapt high produce efficiently a request of work the noodles,the coal mine needs main parameter urgently on the scene greater ,the technique is more advanced,function more dependable long pull ,big carrying capacity 、big power fluently slot the flexible take type transport machine ,transporting technical design level of machine by the exaltation our country take type,filling up local bland,near to and catch up the technique level of the international advanced industrial country.It contains seven of the key technologies:(1) belt conveyor dynamic analysis and controltechnology;(2)soft start with the power balance technology;(3)Intermediate Driver;(4)automatic tensioning technology .(5)new lifetime high technology high-speed roller;(6)rapid shift from the tail;(7)with efficient storage technology.Raise 1 dollar parts function and credibicity :The equipments switch on rate of high and low mainly be decided by the function and the credibility of 1 dollar parts.In addition to further improving and enhancing the existing yuan parts of the performance and reliability,we will continue to research and development of new technologies and metadata components,such as high-performance technical controllable soft start,Dynamic Analysis and Monitoring Technology,and efficient storage devices with rapid shift from the tail,high-speed roller,belt conveyor so that the performance can be further raised.Extend function ,a machine uses to turn much:Expan a luck a person,carry to anticipate or double to conveyance etc.function,attain a machine to use much,make it the exertive and biddest economic performance.Develop a special type a take type to transport machine,if the flection take type transports the machine,big cape or perpend cularity to promote to transport machine etc.The big cape take type transports the extreme limit that the machine broke the last luck cape 25°25°s,expand,mine s,expand,mine for the coal mine and the main and inclined well transported an equipments to choose a type to develop a new path,also transporting the equipments that the system changed an extension to provide economy efficiently for the current inclined well,to raise a yield and decline low cost have important meaning.The level take type transports machine to have amplitude in the our country mineral mountain the production of applied foregroune,especially in the coal mine.My more inclind seam,16~25°seam,16~25° tilt seam exist in large numbers. tilt seam exist in large numbers.The take type transports the function success to used for the bottom of the well,since can reduce tunnel to expand the quantity and equipments.中文译文1.1带式输送机的的特点与应用带式输送机自1795年被发明以来,经过两个多世纪的发展,已被电力、冶金、煤炭、化工、化工、矿山、港口等各行各业广泛采用,矿山、港口等各行各业广泛采用,矿山、港口等各行各业广泛采用,特别是第三次工业革命带来了新材料、新技术的采特别是第三次工业革命带来了新材料、新技术的采用使带式输送机的发展步入了一个新纪元。
- 1、下载文档前请自行甄别文档内容的完整性,平台不提供额外的编辑、内容补充、找答案等附加服务。
- 2、"仅部分预览"的文档,不可在线预览部分如存在完整性等问题,可反馈申请退款(可完整预览的文档不适用该条件!)。
- 3、如文档侵犯您的权益,请联系客服反馈,我们会尽快为您处理(人工客服工作时间:9:00-18:30)。
中英文资料外文翻译文献A Comparison of Drive Starting Mechanisms forAggregate Belt ConveyorsAbstractThe purpose of this paper is to describe the torque/speed characteristics,during starting conditions,of the most common drives used on belt conveyors today. Requirements of a Belt Conveyor DriveA belt conveyor is considered to be a constant torque device. In other words,the required driving torque is approximately constant at varying speeds (see figure l).other applications,such as a pump drive,have variable torque requirements(see figure2).However,to increase the speed of a conveyor additional torque must be added until the desired speed is obtained. Newton’s Second Law of Motion governs this relationship.∑F ma=The most straightforward example would be a constant acceleration torque(see figure3).In reality the acceleration torque is rarely constant. However,static calculation models as outlined in the Conveyor Equipment Manufacturers Association handbook (CEMA) make this assumption. When using static models the average acceleration torque is estimated over the entire acceleration time and assumed to be linear. Dynamic models,which are beyond the scope of this paper,allow acceleration torque values to vary in magnitude during the acceleration(or deceleration)Period.It should be noted that,given a constant load,a larger acceleration torque results in a faster acceleration time and also higher Peak belt tensions. Conversely,a smalleracceleration torque results in a longer start time and smaller Peak belt tensions. Across-The-Line AC Motor StartTechnically this is the simplest type of drive used on a belt conveyor. In this drive type an AC squirrel cage induction motor is started by simply throwing the contactor and energizing the motor. The resulting output torque,assuming that rated voltage is maintained,is strictly a function of the motor design. NEMA has Provided design standards that define the output torque characteristics of the most commonly used 3 Phase motors up to approximately 250 hp(figure4).In sizes larger than 250 hp manufacturers generally use the NEMA design codes in a relative manner(i.e.,NEMA C has a greater locked rotor torque than a NEMA B motor).The most critical locations on the AC motor speed/torque curve have been named for definition purposes. These common names are provided in figure 5.The most rigorous method of determining average acceleration torque,for staticcalculations,is to break the curve into several vertical sections,then sum the individual areas under the curve and finally divide by the number of sections.The more common way is to apply the following simplified equation:These static approximation methods work for most belt conveyors but can get the designer into trouble from time to time,especially on long and/or steep and/or fast conveyors. One item that needs to be examined is breakaway torque. Just because the drive provides enough average torque to accelerate the load doesn’t mean that it provides enough torque to break it away from zero speed and get it moving.CEMA defines breakaway torque as twice the torque required to overcome the total friction plus the torque required to lift the load vertically. Locked rotor torque (LRT) needs to be greater than breakaway torque! A good static Program makes this check.In addition to examining the effect that average torque has on the conveyor components the belt designer needs to determine the effect of peak torque. It is not uncommon for the breakdown torque (BDT) of a NEMA C motor to be greater than2.5 times full load torque (FLT).Generally the belting and Pulley manufacturers allowa transient overload of 1.5 times full load operating load. An across-the-line start can easily cause tensions to exceed these maximums. These higher than normal loads can be designed into the conveyor if they are known up front.Considering only average starting torque can cause the conveyor designer to undersize the take-up weight. It is not uncommon for conveyors with across-the-line starters to experience intermittent drive slip. This generally happens when Peak torque (BDT) is input by the drive and the take-up has been sized for average torque but not peak torque. The result can be devastating. When the drive pulley slips during thiscondition,the tension on the Tl and T2 sides (high and low)of the drive Pulley tries to equalize. This can subject a low tension bend or take-up pulley,just behind the drive pulley,to tensions that approach Tl tension. These Pulleys are rarely,if ever,designed for this load condition and the result is low tension Pulley failure. This condition is easily demonstrated with dynamic analysis.Another common Problem with across-the-line starts is caused by voltage dips during starting. If the power distribution system is not stiff enough to handle the huge inrush currents of an across-the-1ine start,the starting torque of the motors can be reduced to a Point that the conveyor will not start. This is due to the fact that the output torque of an AC squirrel cage induction motor is reduced by the square of the applied voltage. In other words,a voltage drop of 10%would equate to a torque reduction of 19%. Reduced Voltage StartingThe reduced voltage starting of an AC squirrel cage induction motor is done for two basic reasons:1 .To reduce the inrush current that naturally occurs when a motor is Startedacross-the-1ine. A typical current/speed graph is shown in figure 6.It is not uncommon for the inrush current to be 6 times or more than it is at full load torque. As stated above high inrush currents cause the voltage in a power distribution system to sag. The cost of electrical power distribution equipment can become very high if it needs to be designed to handle the high inrush currents.2 . To reduce Peak motor torque during starting conditions,which subsequentlyincreases acceleration time. By reducing the Peak torques the conveyor components can be designed for lower tension loads. This primarily includes belting,Pulleys and external support structure. This can result in significant cost savings.Two common types of reduced voltage starters are the Current Limiting and the Constant Torque devices.Graphs are included above(figures 7 through 8) that depict the same motor/conveyorapplication with an Across-The-Line,a limitd Curren, and a constant Torque start. After studying the graphs it becomes apparent that the best use of the limited torque start is to protect the power distribution system from high inrush currents. The constant torque start reduces the high torque Peaks and Protects the conveyor’s mechanical components. In both cases the Start time is increased because the over all magnitude of accelerating torque is reduced. However,neither method will make it easier to start a“hard-to-start conveyor.”Correcting a hard starting conveyor is not a reason to use a reduced voltage starter!翻译带式输送机驱动方式比较摘要本文的目的是描述最常见的机用输送皮带起动时的扭矩/转速特性。