汽车顶棚分析
汽车顶棚可行性研究报告

汽车顶棚可行性研究报告一、引言汽车顶棚是车辆的一个重要部件,不仅可以提供车辆的防护作用,还可以起到美观和功能性的作用。
随着人们对汽车个性化需求的不断提高,汽车顶棚的设计和材料选择也越来越受到关注。
本报告旨在对汽车顶棚的可行性进行研究,分析其对车辆性能和用户体验的影响,并提出改进建议。
二、汽车顶棚的作用汽车顶棚是车辆的一个重要部件,它主要有以下几个作用:1、防护作用:汽车顶棚可以有效防止外界雨水、阳光、尘土等对车辆内部的侵害,保护车内乘客和行李的安全。
2、提高车辆性能:合适的顶棚设计可以改善车辆的风阻系数,减少车辆的风阻,提高车辆的燃油经济性和操控性能。
3、美观作用:汽车顶棚是车辆外观设计的重要组成部分,设计精美的顶棚可以提升车辆的品牌形象和竞争力。
4、功能性作用:一些高级车型的顶棚还集成了天窗、天幕等功能,增加了车内的采光和通风效果,提高了乘坐舒适度。
综上所述,汽车顶棚不仅是车辆的一个重要部件,还具有重要的功能性和美观性作用。
三、影响汽车顶棚的因素汽车顶棚的设计和材料选择受到以下因素的影响:1、材料选择:汽车顶棚主要有钢制、铝制、玻璃、碳纤维等材料,不同材料的强度、重量和造价不同,对车辆性能和造型有不同影响。
2、设计风格:汽车顶棚的设计风格主要有硬顶、软顶、敞篷等,不同设计风格适用于不同类型的车型和用途。
3、安全性:汽车顶棚在车辆碰撞时需要保持结构完整性,能够有效抵御外力的侵害,保护车内乘客的安全。
4、用户体验:汽车顶棚的开启方式、遮阳效果、采光效果等都会影响用户的舒适感和使用体验。
以上因素都会对汽车顶棚的设计和选择产生影响,需要综合考虑和平衡。
四、汽车顶棚改进的建议针对汽车顶棚存在的一些问题和局限性,我们提出以下改进建议:1、采用轻质材料:选择轻质高强度的碳纤维等材料,可以减轻车辆重量,提高车辆的燃油经济性和性能。
2、增加多功能设计:将现代科技元素融入到顶棚设计中,如智能开闭系统、太阳能充电系统等,增加顶棚的功能性和智能化。
关于汽车顶棚生产工艺分析报告
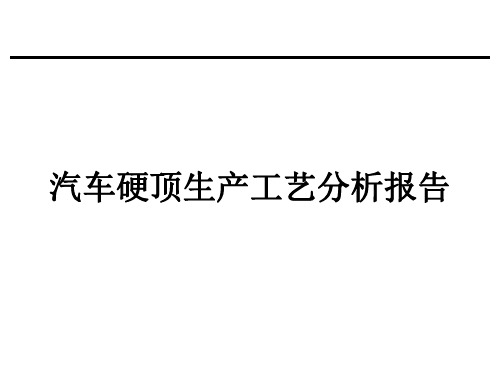
一、顶棚行业现状
随人民生活水平的提高,对汽车行业的要求也越来越高, 特别是在乘员仓内对气味和声学的要求足步在提高。因此, 对汽车内饰产品的材料和工艺要求越来越高。 随着要求的提高,特别是声学要求的提高,现有干法工 艺使用的批量生产的复合板材已经无法满足其性能要求。为 了满足更高的要求,更多的供应商选择采用湿法工艺,根据 自身的经验和技术实力,针对不同的要求自制基材从而达到 较高的声学等相关性能要求。 湿法工艺相对于干法工艺其优势主要体现在: 第一、可以满足翻边工艺的要求; 第二、可以根据对声学性能不同要求选择合适的原材料 因此,目前国内中高端车型基本上已经是湿法工艺的天 下,例如国内福特的所有车型均使用湿法工艺。 目前重庆地区能够生产湿法顶棚的供应商主要有安通林、 华博、长鹏、敏特4家。
涤纶经编面料是用相同旦数的低弹涤纶 ①、成型工艺:先将基材部分的材 丝织制或以不同旦数的低弹丝做原料交织 料组合好,再将无纺布和基材部分 而成。 湿法顶棚的 一起热模压制成型,成型完成后在 基材部分由 ②、无纺布+PU 优点:具有防潮、透气、无毒、耐腐蚀性、 基板上喷胶后将经编布复合面料和 纵向尺寸稳定性好、质感好,与针刺无纺 热固性的聚 泡沫+经编布 基材一起热模压制成型。 布相比耐久性、 耐清洁性能、耐磨损性 氨酯胶、催 ②、成型区域场地面积约100m2。 湿法PU复合 能好,较好的吸音性能。 化剂、玻纤、 ③、人员数量:15人 基材 缺点:成本较高。 PU板、牛皮 纸或无纺布 ①、成型工艺:先将基材部分的材 构成成、材 优点:具有防潮、透气、无毒、耐腐蚀性、 料组合好ห้องสมุดไป่ตู้再将无纺布和基材部分 料成本较低。 质感好,与针刺无纺布相比耐久性、耐清 一起热模压制成型,成型完成后在 ③、无纺布+PU 洁性能、耐磨损性能较好,有一定的吸音 基板上喷胶后将经编布复合面料和 泡沫+针织布 性能。 基材一起热模压制成型。 缺点:成本较高。 ②、成型区域场地面积约100m2。 ③、人员数量:15人 ①、成型工艺:先将基材部分的材 优点:具有防潮、价格低、耐腐蚀性,耐 料组合好,再将面料和基材部分一 ④、印花无纺布 清洁性能及耐磨损性能好等优点。 起热模具压制成型。 缺点:无纺布相比延伸率略差。 ②、成型区域场地面积约100m2。 ③、人员数量:9人
汽车顶棚系统工艺概述

二、顶棚分类及材料分析
1.顶棚分类
顶棚类型主要分软顶和硬顶两种: ⑴软顶 A.粘接式 这种形式将顶棚直接粘接在顶盖上,一般由面料和泡沫复合而成。面 层起装饰作用, 泡抹起绝热、吸音、隔热的作用。面层用机织布、编制布等织 物或人造革、 PVC 膜等材 料制造;泡抹层用聚氨脂 (PU) 或交联聚乙烯 (XPE) 泡抹制造;面层和泡抹曾用层压法, 或火焰发复合在一起。其特点是简单易行, 成本最低,但装饰效果和功能均不如其他两 种,故用于简易车或货车上。 B.吊装式 为了把外表面挂起来,采用棚杆结构。在饰面与顶盖之间设有隔热的 衬垫,衬垫一般是 粘在顶盖内侧的。吊挂的顶棚是在饰面上面缝制的布袋中穿 过棚杆,棚杆弯曲成与顶盖 的横断面相近似的曲线。棚杆多数为圆形端面,
汽车顶棚系统工艺概述
目录
一 概述 二 顶棚分类及材料分析 三 生产工艺介绍
一、概述
顶棚内饰是汽车整车内饰的重要组成部分,其主要作用是提高车内 的装饰性,同时 顶棚内饰还可提高与车外的隔热、绝热效果;降低车内 噪声,提高吸音效果;提高乘员 乘坐的舒适性和安全性。
由于太阳直射车顶,汽车顶部温度较高,因此顶棚内饰的耐热性和 耐候性指标要求较高。
⑴基材种类: PU 板基材、PS 板基材、FS 板基材、废纺毡基材、麻纤维板基材、瓦楞纸板等。 ⑵面饰材料: A.针织面饰:经编、纬编等,以经编为主; B. PVC 面饰; C.无纺布面饰:针刺无纺布、缝编无纺布、热轧无纺布等;
二、顶棚分类及材料分析
2.顶棚的材料类型
⑶几种常用的成型顶棚材料: A.热塑性基材
三、生产工艺介绍
零件加工工艺流程:以 PU 板作为骨架材料制作的顶棚Βιβλιοθήκη 其主要加 工工艺有干法和湿法两种:
某款轻客顶棚设计分析

2.7 顶棚主要性能试验 顶棚作为安全关键件,需要满足国家标准 GB8410-2006《汽
车内饰材料的燃烧特性》和 GB7258-2017《机动车运行安全技 术条件》的阻燃要求,燃烧速度≤ 70.0 mm/min。同时,顶棚 由于处于车身顶盖位置,受环境温度影响大,因此需要对饰材 与基材间粘结性能、挠度、耐热老化、低温存放、耐湿热、耐气 候交变、耐光色牢度、含水量变化率和耐低温冲击等性能进行 试验验证确认。
遮阳板安装底座与顶棚通常需要设定 1.0 mm 的干涉量,与 顶棚开口通常留有 5.0 mm 的压合量。遮阳板后端与顶棚留有 15.0 mm 的手指间隙,以保证翻折遮阳板的手部操作空间。顶棚
前端与前风挡玻璃的间隙应当设置为 4.0 mm 左右,前风挡玻璃 黑边须超出顶棚前端 10.0 mm。顶棚前端裁切位置应高于驾驶员 上视野线,以避免切边外漏(图 3)。
顶棚周边配合件较多,设计初期需要对各个搭接配合位置进 行断面分析,主要包括卡扣安装配合、立柱护板配合、门洞密封 条配合、室内顶灯配合、遮阳板安装点配合、挡风玻璃配合与车 身钣金搭接配合等。这需要逐一做断面进行匹配关系校核,确保 满足设计要求。下面通过该款顶棚与立柱护板及遮阳板安装点的 断面分析,阐释顶棚与周边件搭接匹配注意事项。 2.6.1 顶棚与立柱护板的配合
另外,顶棚作为车内大型裸露的复合材质装饰件,需要评估 乘员使用过程中抚摸、脏污等各种工况条件,因此需要进行耐摩 擦色牢度、耐水污染和抗微生物性能等试验,以进行验也需要对 气味性、甲醛含量、气雾冷凝值和有机物散发性能等进行试验验证。
3 总结
顶棚作为车内大型内饰件,设计阶段需要充分校核与周边件 的匹配关系,避免后期不必要的设计变更。同时,需要了解清楚 顶棚的法规要求,相关性能要求需要进行试验验证,以确保满足 车辆使用的各种工况。另外,因轻客车型的成本控制要求,通过 合理选用成型工艺、原材料及装配方式,以降低零部件成本,提 升市场竞争力。目前该款顶棚已实现批量生产。
某轿车内饰顶棚总成的结构设计优化及分析--z正文..--2011-5-12--

第1章绪论引言出于各种不同的目的和要求,汽车的品种越来越多,近年来,随着人们环保意识的增强,对汽车提出了更高要求。
最近,国际汽车界又制定了一项新标准,简称为NVH标准,即噪音(Noise)、震荡(Vibration)、平稳(Harshness)三项标准,通俗称为乘坐轿车的“舒适感”。
随着时代拓展专业化分工,整车制造企业已经逐渐将大部分零部件交给零部件生产企业来做。
盛行的“模块化”生产方式把汽车装配生产线上的部分装配劳动转移到装配生产线以外的地方去进行。
这样,零部件生产企业必然遇到NVH问题。
如今,NVH问题已经成为在车型开发过程中各大整车企业和零部件企业关注的主要问题之一。
国外公司的统计表明,整车约有1/3的故障问题是和车辆的NVH问题有关的。
而各大公司有近1/5的开发费用耗费在解决车辆的NVH问题上。
而国内现在的实际情况还只是关注车辆的安全性、燃油经济性等方面,消费者还没有重视车辆NVH的性能。
不过,国内现在已经有很多整车企业和零部件企业开始了这方面的技术储备.设计者要考虑的问题也不单纯是零部件的本身,而是零部件与零部件之间,零部件与整车之间的关系。
NVH特性的研究不仅仅适用于整个汽车新产品的开发过程,而且适用于改进现有车型乘坐舒适性的研究。
这时针对汽车的某一个系统或总成进行建模分析,找出对乘坐舒适性影响最大的因素,通过改善激励源振动状况(降幅或移频)或控制激励源振动噪声向车室内的传递来提高乘坐舒适性。
然而解决汽车汽车NVH的方法各异,特别是随着时间的推移和科学技术的迅速发展,设计经验和使用实践日益丰富,结构和材料上不断推陈出新,虽然它离不开结构的继承性,但是新老结构型式交织在一起,难以确切下定义和予以统一命名,往往容易混淆,这样就给人们分门别类去认识它和研究它带来一定的困难。
然而,根据问题产生的零部件来源又分外饰NVH和内饰NVH两种。
外饰件组成机构较多,内饰件亦有成百上千,在此无法一一做详细的介绍及分析。
车辆内饰顶棚设计方案

车辆内饰顶棚设计方案背景随着人们对车内舒适性和个性化需求的不断提高,车内饰设计成为一个越来越重要的考虑因素。
车辆内饰顶棚是车内饰的重要部分,它不仅关系到车内视觉效果和空间感受,还能为车内添置更多的功能和体验。
本文将探讨车辆内饰顶棚设计方案,帮助读者了解基本概念和设计方法。
定义车辆内饰顶棚是指车顶部位的内饰装饰,包括车顶板、遮光帘、灯具、音响、通风口等。
它不仅具有美观性,更能够影响车内光线清晰度、隔音效果、通风效果等方面的品质。
设计考虑因素色彩和材质为了满足个性化需求,顶棚的颜色和材质需要得到精心搭配和设计。
对于低端车型,一般采用较为简单的中性色彩和经济实惠的材质,而高档车型则会采用更为精致的皮革或柔软的天然材料。
光线清晰度和遮光效果车内顶棚的光线清晰度和遮光效果对于驾乘者的舒适感非常重要。
一般来说,夏季需要具备防晒隔热的遮阳功能,冬季则要考虑保温和防冻的需要。
此外,为了增加车内空气流通和舒适性,顶棚上通常会设置一些通风口。
音响和灯光装置车内顶棚还可以作为装载音响和灯光的场所。
高端车型通常会搭载更加高效和柔和的灯光和音响系统,提供更加全面和优质的驾乘体验。
设计方案简约风格简约风格的顶棚设计强调整体的简洁性和清晰性。
颜色一般选用中性色,如白色、黑色、深灰色等。
材质一般采用环保耐用的塑料或者钢板等经济材料,减少材料进行垃圾回收和环保处理的成本。
通风口、遮光帘、灯光等装置均采用最简单的原则实现,使整个车内的设计具有一定的流畅性和稳定性。
运动风格运动风格的顶棚设计强调层次感和动感。
除了常规的颜色外,顶棚上的图案、装饰和线条都会采用钢制、铝制等金属材质和华丽艺术的贴花,为车内增添更多的运动元素。
此外,搭载更强效的音响系统和灯光设备,能够提供更有动感的驾乘体验。
豪华风格豪华风格的顶棚设计强调高端与奢华感。
材质经常采用柔软的天然皮革、高档檀木、进口羊绒等,让车内充满温馨而又奢华的氛围,在提高车内整体质感的同时,也提高了生活品质的体验。
汽车顶棚的模态分析

汽车顶棚的有限元模态分析与比较
郑文,翁建生
(南京航空航天大学车辆工程系,南京
210016)
Modal Analysis and Comparison of Vehicle Ceiling with Finite Element Method
ZHENG Wen , WENG Jian-sheng (Department of Vehicle Engineering , Nanjing University of Aeronautics and Astronautics , Nanjing 210016 , China) Abstract: Vehicle ceiling modal has important influence 0日 the low-frequency noise in the cab. In this paper , ANSYS is utilized to analyze the modal of convex surface ceiling and arc ceiling. Then the effects of the length , height and number of convex surface and the height of arc 0 日 ceiling modal are discussed. The results show that the ceiling 口 atural frequencies increase with the increase of these factors and the strengthened mode shape keeps invariant with convex surface ceiling but different with arc ceiling. By comparing these two methods , it is fou日 d that the improving of ceiling 口 atural frequencies by the arc structure is better than by the convex surface structure. Key words: vehicle ceiling; modal; natural frequency; finite element
车辆内饰顶棚设计方案

车辆内饰顶棚设计方案车辆内饰设计对整车外观的重要性越来越受到人们的关注,其中车辆内饰顶棚设计更是不可忽视的一部分。
一个精心设计的车辆内饰顶棚不仅可以提高驾乘者的舒适性和美观度,还可以体现出车辆设计者的品味和创意。
那么如何设计出一个令人满意的车辆内饰顶棚呢?以下是一些常见的设计方案供参考。
1. 簇绒式车内顶棚簇绒式车内顶棚是一种较为传统的设计方案,通过在车内顶棚上添加簇绒材料制成,可以起到保暖、减噪、防晒等作用,并且具有较好的视觉效果,提升驾驶者的舒适感。
不过缺点是在颜色和样式方面的选择较为有限,很难达到太多的创意。
2. 多彩加灯效装饰这种设计不仅可以使整车内部充满时尚感和艺术气息,还可以创造出独特的视觉效果,提高车内室内的空气质量与气味,是一种跳脱传统设计的方案。
多彩加灯效装饰的方式也很灵活,有的是在顶棚上添加LED灯条,在其低端保留一定空间,这样可以创造出车内空间更宽敞的错觉。
与此同时,可以根据驾驶者个性偏好,添加不同颜色的LED灯条,十分自由和个性化。
当然,缺点就是成本相对较高,对于少数消费者而言,还是显得过于奢侈。
3. 玄关效果玄关效果设计是一种常见的车辆内饰顶棚设计方案,通常采用玄关墙面设计的类似原理。
这种设计方法主要依靠车顶板将前后两处顶棚穿插搭接,并在搭接处设置装饰和照明,形成一块中央突出的“棚顶”,制造“天窗”效果,塑造出豪华和高端的内饰体验。
此外这种方式还可以在顶棚上添加适当的彩绘或图案,更加盛装面积。
4. 皮质车内顶棚皮质车内顶棚是一种豪华、高品质的顶棚设计方案,选用顶级牛皮和PU人造皮等优质材料,不仅能体现车主品味,还拥有比较好的触感、漂亮的外观和舒适的体验。
此外,因为皮质车内顶棚采用了人工制皮工艺,所以颜色、样式、款式都有较大的多样性。
5. 黑天鹅绒顶棚黑天鹅绒顶棚主要是一种高端豪华车型所具备的顶棚设计方案,该工艺需要投入高端原材料、提供精湛的制作工艺和专业技术才能完成。
黑天鹅绒顶棚从柔软度、密度和光泽度等方面都要比簇绒式顶棚提升,高端豪华车型中的一些高级版本通常会采用这种顶棚设计方案。
顶棚基材分析

汽车顶棚基材的交流编制人:汽车顶棚是现代汽车包括轿车、客车、卡车、工程车等不可缺少的内饰件之一,包括两类,分别是成型顶棚和异型顶棚。
汽车顶棚是用不同种类的非金属材料复合模压制成,具有良好的隔热、隔音性能和独特的装饰效果,能够满足汽车在装配线上快速装配的需要,世界各国都十分重视它的研究和开发,并且在汽车生产上大量应用。
汽车顶棚的基材研究一直是世界各国汽车业关注的重要内容之一。
轻量化、无污染、可回收、低成本是研究的主要课题。
国内汽车顶棚制造业的专家认为:经过20多年的技术引进和吸收开发,在技术方面同国外差距已经不大。
降低顶棚成本已成为研究开发工作中的重点内容,以适应越来越激烈的竞争需求。
本文就成型顶棚的基材进行了论述,着重介绍“TRAMIVEX”成型顶棚的性能特点以及生产方式,以供大家参考。
一、国内外现状成型顶棚在国外,特别是在汽车工业发达的国家,如美国、德国、英国、法国、日本、瑞典、意大利等已大量生产和应用,其材料结构设计。
制造工艺、技术装备五花八门,各具特色,至今各国仍在这个领域中投入较大的人力物力进行更新的材料结构和生产工艺、技术装备的研究开发,不断扩大在汽车上的应用,为了满足现代汽车多品种、大批量生产需要,所有的汽车生产大国均建立了相当规模,装备先进的转移生产工厂,在汽车生产比较集中的西欧更为突出,以德国的EMP工厂为例,成型顶棚年产量达100万辆份,销往许多国家的汽车厂,国内的上海桑塔纳轿车、北京切诺基吉普车、一汽奥迪100型轿车、一汽大众的高尔夫、捷达轿车、南汽依维柯轻型车、二汽EQ153平头卡车、东联公司的中巴客车、天客TJ622小客车、天汽TJ1041轻型车、洛拖菲亚特80-90DT拖拉机等均采用不同基材的成型顶棚作为顶盖内部装饰,国内成型顶棚的生产尚在起步进行阶段,公主岭市汽车装饰材料厂在89和91年分别研制出了再生纤维/树脂基和塑料粉板基的成型顶棚。
北京地毯三厂研制出了玻璃纤维/树脂基的成型顶棚,由于工艺装备等条件所限,产品水平和生产效率与国外相比,还有一定差距,因此国内汽车应用的成型顶棚大部分仍靠进口。
汽车内饰顶棚DFMEA分析范例

车身工程中心编制人:新严重度新频度新探测度新风险顺序数Line No.Item/FunctionPotential Effect(s)Of Failure SEV ClassPotential Cause(s)/Mechanism(s)of FailureOCCCurrent Prevention Control DET RPNRecommend Action(s)Responsible DepartmentTarge Completi -on DateNew SEV New OCC New DETNew RPN1无法通过认证,不能销售10对材料特性认识不足,设计前未进行遮阳板材料分析2设计时进行材料燃烧特性分析240增加检验频次2不能销售10未进行内部凸出物圆角分析2设计时进行内部凸出物圆角分析240增加检验频次3影响销售4顶棚拉伸深度型面设计不合理2按供应商工艺同步意见书检查数模2164客户抱怨5顶棚材料或者顶棚隔音隔热附件不符合NVH定义3对材料进行NVH分析23054顶棚立柱搭接面差间隙设计不合理3按照GD&T方案书要求检查数模22464顶棚设计时未考虑零件加工误差,及实物随外面气候原因变形3按照设计方案检查数模448试验验证7生产效率低维修困难6顶棚安装孔定位与基准设计不合理,误差累积造成顶棚孔位不准安装困难3按GD&T方案书要求检查数模236顶棚:汽车顶盖装饰件,对汽车内部起装饰、隔热吸音等作用Part No.Department 设计潜在失效模式及后果分析(D-FMEA)Design Failure Mode and Effects Analysis (D-FMEA)供应商/顾客:零件名称:顶棚零件号:责任部门:FMEA 编号:Model(s)Key DateVerificationCompiled ByNo.车型号/车辆类型:PM 关键日期:审核:Supplier/Customer Part Name :建议措施责任部门核心小组成员:日期(编制):日期(修改):FMEA Team MembersCompile DateAmend Date成型不到位或面料褶皱、破损,外观质量差软件数模分析措施结果/Action Results采取的措施Potential Failure ModeCurrent Detection ControlActions Taken现行预防控制探测度风险顺序数不满足燃烧特性,内饰(顶棚)材料在测试时燃烧速度大于100mm/min 试验验证内饰(顶棚)内部凸出物圆角小于5mm软件数模分析影响销售顶棚立柱搭接处出现较大间隙面差,外观质量差软件数模分析顶棚安装困难试验验证现行探测控制NVH试验不合格,噪声大试验验证潜在失效原因潜在失效模式试验验证序号项目/功能潜在失效后果严重度级别发生频度责任目标完成日期。
顶棚产品知识报告

顶棚生产工艺流程
12
顶棚湿法生产工艺流程
顶棚生产工艺流程
13
顶棚后工序附件组装
顶棚生产工艺流程
14
顶棚后工序附件组装
顶棚生产工艺流程
15
顶棚检具功能展示
顶棚生产工艺流程
16
顶棚生产工艺流程
顶棚干湿法性能对比
1、单位面积质量:以同一款车型顶棚为例,满足顶棚性能要求的同时,与干法顶棚相比, 湿法顶棚单位面积质量可降低约28.5% (湿法优)
2、目前,汽车顶棚主要由基材+装饰层一体成型,利用大型成套生产设备,用热塑法或热固 法将他们复合成一个整体,成为具有一定刚性和立体形状的内饰件,基材通常采用麻纤维板, PP玻纤板,PU板等,目前PU板处于主流地位,装饰层主要采用PET、织物面料+PU+PET、 PVC皮、麂皮等。
3、顶棚主要的功能是装饰。正常使用时,虽不承受自重以外的其他应力,但因跨度较大,所 以需要一定的刚度。另外,由于面积大,对车内隔声、隔热效果起着重要作用,因此具有重量 轻、比强度高、导热系数低等优点的泡沫塑料、蜂窝结构基材将成为发展方向。
模具里面进行成型 干法和湿法的主要区别:两者的胶粘剂区别非常大,湿法顶棚所用的胶为聚氨酯热固型胶 ,生产的过程中需要洒水,聚氨酯豫聚体通过与水发生化学反应,产生粘接效果,反应方 程式如下:
2RNCO+H2O=RNHCONHR+CO2
干法顶棚材料结构
湿法顶棚材料结构
8
顶棚生产工艺流程
PU发泡原理简介
2、耐高温尺寸稳定性:干法顶棚在100度高温下,经过16h,尺寸变化率≤2.5%,而湿法 顶棚在同等条件下的尺寸变化率≤0.5%(湿法优)
3、NVH性能:湿法顶棚的隔声量在1000HZ以下,吸声量在1600HZ以上均优于干法顶棚 (湿法优)
汽车顶棚生产与工艺改进措施的分析
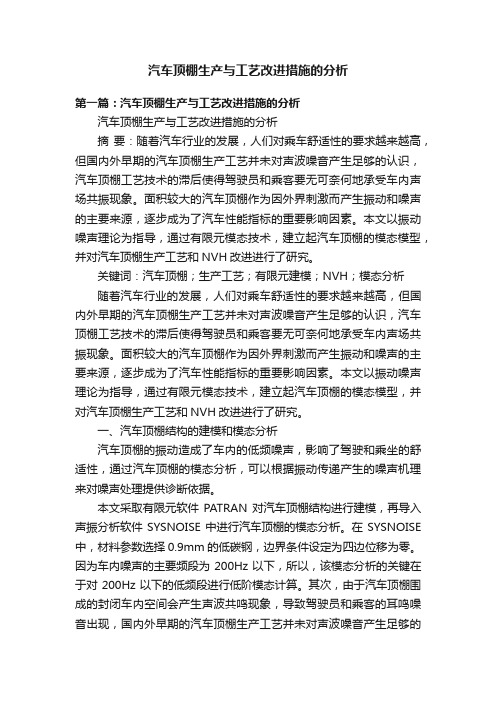
汽车顶棚生产与工艺改进措施的分析第一篇:汽车顶棚生产与工艺改进措施的分析汽车顶棚生产与工艺改进措施的分析摘要:随着汽车行业的发展,人们对乘车舒适性的要求越来越高,但国内外早期的汽车顶棚生产工艺并未对声波噪音产生足够的认识,汽车顶棚工艺技术的滞后使得驾驶员和乘客要无可奈何地承受车内声场共振现象。
面积较大的汽车顶棚作为因外界刺激而产生振动和噪声的主要来源,逐步成为了汽车性能指标的重要影响因素。
本文以振动噪声理论为指导,通过有限元模态技术,建立起汽车顶棚的模态模型,并对汽车顶棚生产工艺和NVH改进进行了研究。
关键词:汽车顶棚;生产工艺;有限元建模;NVH;模态分析随着汽车行业的发展,人们对乘车舒适性的要求越来越高,但国内外早期的汽车顶棚生产工艺并未对声波噪音产生足够的认识,汽车顶棚工艺技术的滞后使得驾驶员和乘客要无可奈何地承受车内声场共振现象。
面积较大的汽车顶棚作为因外界刺激而产生振动和噪声的主要来源,逐步成为了汽车性能指标的重要影响因素。
本文以振动噪声理论为指导,通过有限元模态技术,建立起汽车顶棚的模态模型,并对汽车顶棚生产工艺和NVH改进进行了研究。
一、汽车顶棚结构的建模和模态分析汽车顶棚的振动造成了车内的低频噪声,影响了驾驶和乘坐的舒适性,通过汽车顶棚的模态分析,可以根据振动传递产生的噪声机理来对噪声处理提供诊断依据。
本文采取有限元软件PATRAN对汽车顶棚结构进行建模,再导入声振分析软件SYSNOISE中进行汽车顶棚的模态分析。
在SYSNOISE 中,材料参数选择0.9mm的低碳钢,边界条件设定为四边位移为零。
因为车内噪声的主要频段为200Hz以下,所以,该模态分析的关键在于对200Hz以下的低频段进行低阶模态计算。
其次,由于汽车顶棚围成的封闭车内空间会产生声波共鸣现象,导致驾驶员和乘客的耳鸣噪音出现,国内外早期的汽车顶棚生产工艺并未对声波噪音产生足够的认识,汽车顶棚工艺技术的滞后使得驾驶员和乘客要无可奈何地承受车内声场共振现象。
汽车顶棚制造工艺及相关故障解析

114AUTO TIMEMANUFACTURING AND PROCESS | 制造与工艺汽车顶棚制造工艺及相关故障解析1 引言客户在与产品直接接触后会对产品质量有主观感性的认知,这种认知虽然以人的主观感受为基础,却反映了人的真实感受,这种对产品质量感性的认识叫做感知质量[1]。
消费者对于汽车顶棚的感知质量体现就十分明显,触摸柔软度,舒适感等等。
产品的感知质量是客户获得的关于产品设计及制造质量的第一手信息,是最直观真实的感受,它的好坏直接影响着客户对产品的购买决定,决定了使用满意度以及产品的质量口碑[2]。
2 汽车顶棚简介在目前市场当中,我们将汽车顶棚分为硬顶与软顶两个种类。
2.1 软顶软顶一般由面料与泡沫通过层压法进行复合形成,因为目前在市场使用较少,本文不详细介绍。
2.2 硬顶硬顶一般由无纺布、玻纤、PU 层、胶经过干法或湿法工艺复合得到,具有固定顶棚特征形状,通过周边固定装置(遮阳板底座、卡扣等)与白车身进行配合。
3 顶棚制造工艺简介目前汽车顶棚制造工艺分为干法工艺与湿法工艺两种,其主要步骤如下:原材料符合模压成型水切割检验包装入库。
3.1 干法制造工艺顶棚干法制造工艺一般采用冷模压方式进行,具体工艺步骤如下:(以下数据仅针对普通工艺研究使用)将无纺布、热熔胶粉、玻璃纤维制得复合材料基材。
谢建东 吴红广 余李辉上汽通用五菱汽车股份有限公司重庆分公司 重庆市 401120摘 要: 随着汽车市场的日渐饱和,消费者对于汽车质量(安全性、舒适性、可靠性)要求逐步提高,为满足客户日益增长的要求,汽车生产厂家必须不断提升自身产品质量,才能在激烈的市场竞争中占有一席之地。
内外饰作为汽车的重要构成部分之一,汽车顶棚的质量很大程度上代表了汽车内外饰的质量,是汽车生产厂家与消费者重点关注的地方,行业内称为感知质量,因此,汽车顶棚制造工艺与相关的故障研究就显得尤为重要。
关键词:汽车质量 内外饰 顶棚制造 故障解析 感知质量Automobile Ceiling Manufacturing Process and Related Fault AnalysisXie Jiandong ,Wu Hongguang ,Yu LihuiAbstract : W ith the increasing saturation of automobile market, consumers' requirements for automobile quality (safety, comfort, reliability) are gradually improving. To meet the requirements of customer's growing, car manufacturers must continually improve quality of their products, to place in the fierce market competition. Internal and external decoration as one of the important part of automobile, and the quality of the car roof largely representing the quality of the car inside and outside are the focus of car manufacturers and consumers, which is called perceived quality in the industry. Therefore, it is very important to study the manufacturing technology of automobile roof and related fault.Key words : a utomobile quality, interior and exterior decoration, ceiling manufacturing, fault analysis, perceived quality 图1 软顶图示简介面料泡沫PU层热熔胶粉热熔胶粉无纺布无纺布玻璃纤维玻璃纤维PU图2 硬顶截面图简介AUTO TIME115MANUFACTURING AND PROCESS | 制造与工艺 时代汽车 将制得基材进行升温(基材成型温度:上表面200±10℃、下表面180±10℃)。
汽车内饰顶棚天窗口包边结构设计分析
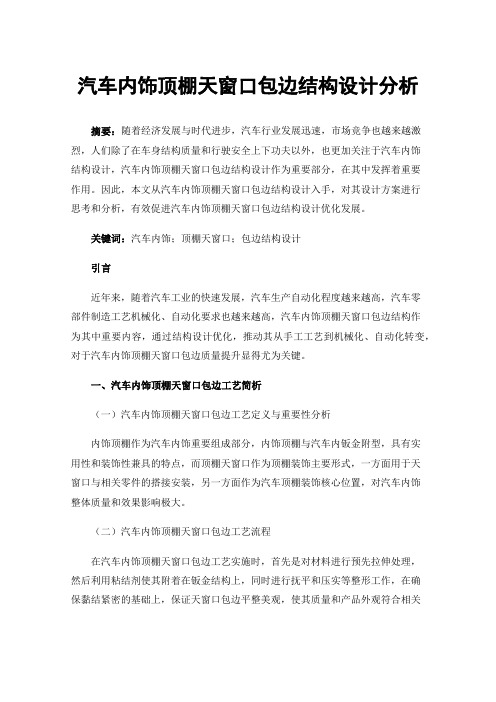
汽车内饰顶棚天窗口包边结构设计分析摘要:随着经济发展与时代进步,汽车行业发展迅速,市场竞争也越来越激烈,人们除了在车身结构质量和行驶安全上下功夫以外,也更加关注于汽车内饰结构设计,汽车内饰顶棚天窗口包边结构设计作为重要部分,在其中发挥着重要作用。
因此,本文从汽车内饰顶棚天窗口包边结构设计入手,对其设计方案进行思考和分析,有效促进汽车内饰顶棚天窗口包边结构设计优化发展。
关键词:汽车内饰;顶棚天窗口;包边结构设计引言近年来,随着汽车工业的快速发展,汽车生产自动化程度越来越高,汽车零部件制造工艺机械化、自动化要求也越来越高,汽车内饰顶棚天窗口包边结构作为其中重要内容,通过结构设计优化,推动其从手工工艺到机械化、自动化转变,对于汽车内饰顶棚天窗口包边质量提升显得尤为关键。
一、汽车内饰顶棚天窗口包边工艺简析(一)汽车内饰顶棚天窗口包边工艺定义与重要性分析内饰顶棚作为汽车内饰重要组成部分,内饰顶棚与汽车内钣金附型,具有实用性和装饰性兼具的特点,而顶棚天窗口作为顶棚装饰主要形式,一方面用于天窗口与相关零件的搭接安装,另一方面作为汽车顶棚装饰核心位置,对汽车内饰整体质量和效果影响极大。
(二)汽车内饰顶棚天窗口包边工艺流程在汽车内饰顶棚天窗口包边工艺实施时,首先是对材料进行预先拉伸处理,然后利用粘结剂使其附着在钣金结构上,同时进行抚平和压实等整形工作,在确保黏结紧密的基础上,保证天窗口包边平整美观,使其质量和产品外观符合相关要求,最后呈现图1的效果。
所以,汽车内饰顶棚天窗口包边工艺可以分为四个方面,包括:面料夹持、机构平推、下压包边、预包边后整形等内容。
图1:汽车顶棚天窗口包边后结构二、汽车内饰顶棚天窗口包边结构优化设计思路分析(一)科学合理处理顶棚状态在汽车内饰顶棚天窗口包边工艺实施时,顶棚状态的预先科学处理是极为关键的,不仅可以为后续包边工艺实施打下良好基础,还可以有效提升包边工艺的质量和美观度,对于汽车内饰顶棚天窗口包边结构优化设计尤为关键。
汽车顶蓬、地毯设计知识介绍

1.2 顶蓬的功能
由于太阳直射车顶, 汽车顶部温度较高,因 此顶篷内饰的耐热性和 耐候性指标要求较严。
提高安全和舒适性
2.顶蓬的材料介绍
2.1 顶蓬的材料分类
按材料分为:硬质的和软质的 硬质的一般是玻璃钢材料再喷涂上面漆而成,或
PVC板材吸塑成型。这类顶蓬一般隔热、隔音效果较差, 但强度、刚性较好。
5、麻纤维板: 由麻纤维和PP纤维组成
2.1 顶蓬的材料分类
饰面和纬编面料, 面料
面料
(针织物:至少一组纱线系统形成线圈,彼此相互串套而形成的一类织 物总成。
经编针织物:纱线沿经向喂入编制形成线圈的针织物; 纬编针织物:纱线沿纬向喂入编制形成线圈的针织物) 经编面料:由表层为经编织物,中层为聚氨酯泡沫材料,底层为机织或 针织或无纺布或其他材料复合而成的面料。 纬编面料:由表层为纬编织物,中层为聚氨酯泡沫材料,底层为机织或 针织或无纺布或其他材料复合而成的面料。
5.顶蓬相关标准
GB/T 4669 纺织品 机织物 单位长度质量和单位面积质 量的测定-克重测定
2.1-2顶蓬基材特性
a、自带胶层可避免在制造过程中使用其它复合胶水。 b、使用一步法模压工艺可减少制造周期。(原有麻纤板 基材为两步模压成型,基材压型完成后进行喷胶处理,然 后与面料一起热压成型)。 c、克重范围广(600-2000g/m²)。 d、低挥发物含量(水溶剂生产工艺,VOC接近0),环保 可回收。
两步法: 基材成型后再和面料粘接成型工艺,它主要热塑性材料作为基材 ,通过模具140°左右的温度热压成型,然后由喷涂好粘接剂的表 皮沾接在成型基材上,再通过80°-100°模温热压合成成型。如 果整车配置带有天窗,那么顶蓬需要经过天窗包边加工装饰,满 足整车设计配置要求。
汽车顶棚内饰设计解析
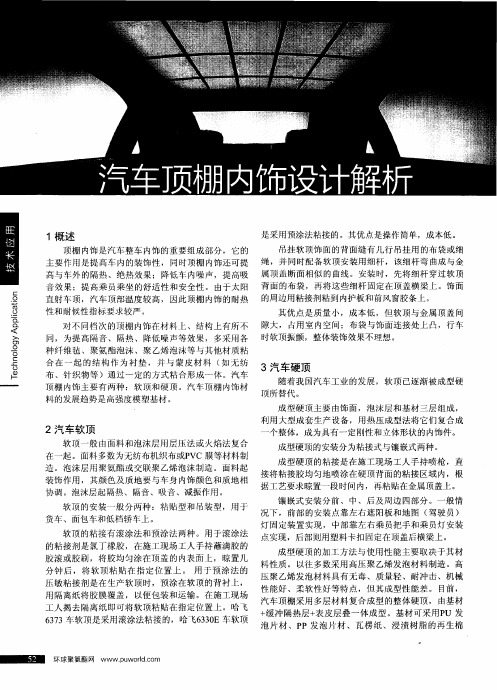
低 、成型 自由度高 。但其 隔音 效果差 ,且热 变形温度 味 。
较低。另外PS泡沫体 内残余物在加热过程 中生成 的气
填料 :天麻纤维 、木纤维 、回收的棉纤维 与回收
体可聚集于HIPS下,形成气泡 ,造成 次品。
的化学纤维等 。
由于PS受多种溶剂溶解 ,因此不利于使用溶剂型
其优 点是形状稳 定 ,耐热性好 ,强度高 ,又可 以
下面介绍几种常用的硬顶材料 。
3)材 料 耐热 性 LLABS/PVC 好 ,使用 温 度可 达
3.1热 塑 性 基材
130℃ 。
此材料经烤箱 加热软化 后 ,在常温模 具 中受压冷
41耐候性 、耐老化性好 。
却后成 型,面料可在成 型前与基材复合 好,也可在成
5)有利于材料 回收利用 。
性 能好 、柔 软性好等特 点,但其 成型性能差 。 目前 , 用隔离纸将胶 膜覆盖 ,以便包装 和运输 。在施工现场
汽车顶棚采用 多层材料复合成 型的整体硬顶 ,由基材 工人揭 去隔离纸 即可将软顶粘 贴在指定位置上 。哈 飞
+缓冲 隔热层+表皮层 叠一体成型 。基材可采用PU 发 6373车软 顶是采用滚涂法粘接 的,哈飞6330E车软顶
型 时复合面料 。
3.2热 固性基材
3.1.1聚苯 乙烯材料
是 以酚醛树脂 为基材 ,其 成型为热模压 型 ,即将
聚苯 乙烯泡 沫板材 两面 各复合 上一 层HIPS后 , 酚醛树脂 、填料 按 比例混合 后,放入高温模 具 中,交
得到 的有较高刚度的复合材料。PS基材质量轻 、成本 联固化成型 。热 压成型 时能耗 较大 ,而 且有较 刺激气
粘接剂与表皮 面料粘接 ,它 的较 低软化温度 也不利于 回收利 用 。但它 的价格太高 ,专业投资大 ,成 形周期
- 1、下载文档前请自行甄别文档内容的完整性,平台不提供额外的编辑、内容补充、找答案等附加服务。
- 2、"仅部分预览"的文档,不可在线预览部分如存在完整性等问题,可反馈申请退款(可完整预览的文档不适用该条件!)。
- 3、如文档侵犯您的权益,请联系客服反馈,我们会尽快为您处理(人工客服工作时间:9:00-18:30)。
表皮材料主要采用织物或PVC 膜。
聚氨酯发泡
废纺毡
二、常用汽车顶棚安装工艺
1、软顶的安装:
软顶主要用于货车、面包车和低档轿车上。 一般分两种:粘贴型和吊装型。 软顶的粘接有滚涂法和预涂法两种。其优点是操作简单, 成本低。缺点是整体装饰效果不理想,隔音隔热效果差。
耐高低温性:根据Q/FTA011规定顶盖内护面在-30 C~80 C范围内正常使用,不得有开裂、变形、剥离等现象。
•其它主要性能要求 主要指顶棚内饰材料的抗静电性、抗污染性、阻燃性、 耐水性、气味性以及面饰与基材的剥离强度等。
1)抗静电性非常重要,顶棚内饰必须进行防静电处 理,把静电减少到最低标准,要求在使用过程中,不 得产生静电作用,不允许产生起毛、起球、吸灰等现 象。 2)抗污染性是指在使用过程中遇油、水的污染时, 不易扩散。 3)耐水性能是指顶盖内护面经耐水试验后,不得有 剥离、脱壳现象。 4)阻燃性:GB 8410所规定的条件下符合要求; 5)气味性: 参照Q/FTA147试验方法及评价标准,在 要求≤3级为符合要求(有明显气味,但无干扰性气味)。
4、顶棚模块化现状:
顶棚模块化是国内顶棚领域顶尖组装技术。由于成本高,对 车身精度以及单个产品质量要求高,因此没有广泛应用。 对于像奥迪、宝来、速腾、迈腾等系列小型顶棚都已实现模 块化。
目前国内汽车内饰顶棚产品中附件最多,模块化最复杂的车 型是福建东南汽车的克莱斯勒大捷龙车型,该车型顶棚不同 于上述小型顶棚,该顶棚尺寸较大(2640×1350mm),每款 顶棚的分件包含了空调器总成、大灯总成、扶手总成、衣钩 总成、线束、隔音垫等,有近30种、50余个,整个顶棚加附件 能达到30多公斤,顶棚自身重量不足3公斤。
镶嵌式:安装分前、中、后及周边四部分。对于乘用车
来说一般情况下,前部的安装点靠左右遮阳板和阅读灯 固定装置实现,中部靠左右乘员扶手和乘员灯安装点实 现,后部用塑料卡扣固定在顶盖后横梁上,在顶棚与横 梁间加缓冲垫进行减震设计 。一般采用此安装工艺。
三、成型硬顶棚介绍 1、成型硬顶主要性能要求 由于太阳直射车顶,汽车顶部温度较高,因此顶棚内饰 的耐高低温性和耐候性指标要求较严。
1、设计过程中: 单一顶棚设计时,由于顶盖附件固定在车身钣金上,顶 棚上开安装过孔,顶棚与顶盖附件之间无直接装配关系; 模块化设计时:1)要求顶棚和这些相关附件装配牢固, 顶棚相对较软,因此要在顶棚背面设计支架,将顶盖附 件固定在支架上。
2)顶棚总成与车身钣金的装配方式主要采用卡扣连接
(铁卡扣,固定在附件支架上,增强安装可靠性,安装方便,但 要求位置准确)、粘链粘接(安装方便,位置精度要求不高, 安装牢固性稍差于铁卡扣,一般在金属件以及刚性好的顶棚上粘 接牢固)
3、实现模块化将带来一定的优缺点。 优点: 对整车厂:产品管理方便、简化装配工艺,减少工序, 生产节拍加快,提高生产效率; 对于配件厂:在项目控制、设备设计、质量控制、商务 管理能力方面均会有大幅提高。
缺点: 1)对车身要求提高:由于顶棚总成以卡扣与车身相连, 精度提高,因此需要车身上安装孔位置精确。 2)这种供货模式要求各种产品的偏差严格,生产质量稳 定,否则会因为一个小附件实物质量的问题导致整个总成 不合格; 3)顶棚上支架增多,附件工装制作复杂,附件装配工艺 复杂,因此产品价格增加接近一倍。 4)顶棚总成的状态相对增加,对操作工人水平要求提高; 5)附件维修更换不方便如:线束。
常用汽车顶棚有两种:软顶和硬顶
1、软顶:一般由面料和泡沫层用层压法或火焰法复合在
一起。泡沫层用聚氨酯或交联聚乙烯泡沫(XPE)制造,起 隔热、隔音、吸音、减振作用。面料多数为无纺布机织布 或PVC 膜等材料制造,起装饰作用,其颜色及质地要与车 身内饰颜色和质地相协调。
2、硬顶:是具有一定刚性和立体形状的内饰件。 采用多层材料复合成型的整体硬顶,由基材+缓冲隔热层 +表皮层叠一体成型。基材可采用PU 发泡片材、PP 发泡 片材、瓦楞纸、玻璃纤维等
对于顶棚结构相同的总成,只需制作一套工装。
4)整车装配: a、顶棚总成在整车装配时,先取下前端定位卡扣的固定卡 片,安装定位卡扣,从前向后进行装配,最后端三个固定孔 设有相对较大偏差量。 b、累积偏差到最后端三个固定点上,因此在最后端三个固 定卡扣上粘有薄毛毡,防止卡扣与车身间相对活动产生噪音。 c、由于卡扣在顶棚背面,装配工人需清楚固定卡扣的数量 以及位置。
2、成型硬顶棚开发需注意问题 1)、制定设计方案阶段需考虑: 顶棚与周边配合件的搭接关系、干涉量以及自身固定点的 数量及位置、定位孔的确定。
2)、做数模阶段需注意:
a、将相关边界装配全,与顶盖线束间留出足够的间隙,否 则装车时会出现干涉现象。一般线束直径及线束安装卡扣 尺寸数模都会小于实物;数模上线束走向都是规则的,但 实际装车过程中,线束走向一般不规则。
Байду номын сангаас 吊挂软顶:优点是质量小,成本低;缺点:软顶与金属顶 盖间隙大,占用室内空间;布袋与饰面连接处上凸,行车 时软顶振颤,整体装饰效果不理想。
2、成型硬顶的安装: 分为粘接式与镶嵌式两种。
粘接式:成型硬顶的粘接是在施工现场工人手持喷枪,直 接将粘接胶均匀地喷涂在硬顶背面的粘接区域内,根据工 艺要求晾置一段时间后,再粘贴在金属顶盖上 。应用比较 少。
3、成型硬顶模块化分析 一般成型硬顶是单一件供 货,在有些高档车型已实 现模块化:在顶棚厂进行 顶盖附件装配(包括线束、 阅读灯、乘客扶手、缓冲 垫块等),再以总成状态 提供到整车厂进行装配。
顶棚模块化,对顶盖上各附件的安装结构有一定的要求。 以NFC-SONATA顶棚为例,分析从设计到生产装配过程 中需注意的问题:
3)、顶棚首轮样件需注意: 首轮样件提供时要关注顶棚上的相关支架位置是否 准确,与周边配合处的厚度是否合适(尤其对于压 缩量小的无纺布)。 一般在首模件阶段顶棚支架为手工粘接,没有定位 工装,会出现粘接偏差。那么安装在支架上的附件 位置就会有偏差。 与相关附件配合处的厚度也很重要,一般在装附件 处顶棚局部压薄,厚度是否准确,将直接影响与附 件的装配效果。 确定顶棚自身质量后才可分析装配过程中出现问题 的原因。
汽车顶棚
07.4.8
目录:
一、常用汽车顶棚形式、
加工工艺及材料 二、常用汽车顶棚安装工艺
三、成型硬顶棚介绍
一、常用汽车顶棚形式、加工工艺及材料 顶棚内饰是汽车整车内饰的重要组成部分,它的主要作用 是提高车内的装饰性,同时顶棚内饰还可提高与车外的隔 热、绝热效果;降低车内噪声,提高吸音效果;提高乘员 乘坐的舒适性和安全性。
3)对于顶棚背面的粘接支架以及粘接的附件,高度应 低于顶棚的凸出面,可防止运输过程中附件受损坏。
4)顶棚上一些加强件的设计:由于安装附件后,顶 棚总成重量增加,搬运过程中会产生顶棚变形,因 此需要设计顶棚加强件,主要用于刚性相对较差的 聚氨酯基材顶棚上。
5)为避免顶棚附件与钣金件硬接触产生噪音,在顶 棚附件周围设计缓冲块,整车装配后与钣金贴合,消 除噪音。主要使用软发泡材料以及不同密度的XPE材 料。同时可在运输过程中对顶盖附件起到防护作用。
3)顶棚总成装配工艺:先把铁卡扣、支架放在工装定位孔 内,再将顶棚放在工装上,在支架上打胶,放入顶棚内护面, 螺接固定附件。
工装上顶棚内护板定位孔为前端两定位孔以及中间顶灯开口。 正面装配完后,将顶棚翻转,按照顶棚上附件位置的压痕, 粘接背面附件。
对于前端两定位孔处的塑料卡扣,为防止在运输过程中 晃动,在卡扣处加垫片。整车装配过程中取下垫片。
b、数模厚度表示基材还是包含面料,这决定了与周 边配合件预留干涉量值。
C、与护板干涉量规定有偏差范围,但设计数模时 一定要将与同一个件的干涉量作一致,如与B柱上 护板干涉量一般规定为1~1.5mm,那么在设计数模 时定为一个确定值1mm,否则在装配中会出现干涉 量不一致的现象:干涉量大的地方先接触,干涉量 小的地方会留有间隙的情况。尤其是无纺布面料效 果明显。
C、装配好的顶棚总成是通过卡扣与车身相连接, 因此要求卡扣卡接强度高,选用金属卡扣固定,而 不是塑料卡扣。
2、生产装配过程中:
1)对位置精度要求不严格的附件采用粘接方式:在 顶棚本体上压出附件粘接范围,用于附件粘接定位。 如:顶盖线束、线束插接件、以及一些缓冲块、支架 等。
2)、对于位置精度要求严格的附件安装: 对于扶手、顶灯、卡扣等位置精度要求高的附件, 需要设计安装定位工装
6)支架、胶、卡扣的选用:
a、顶棚自身重量不足3公斤,整个顶棚加附件装配后 能达到十几公斤,因此对顶棚的刚性要求很严,在刚 性差的部位使用金属支架加强,如天窗周围,在刚性 相对差的部位使用塑料支架加强。
b、安装附件会使用大量胶,胶会散发一定的气味, 因此在选择胶的型号时,既要考虑粘接牢固性,还应 考虑整车气味性的要求,本顶棚采用的胶为热熔胶。 材料牌号:国民淀粉BM-7213。