轴类零件加工工艺
轴类零件加工工艺
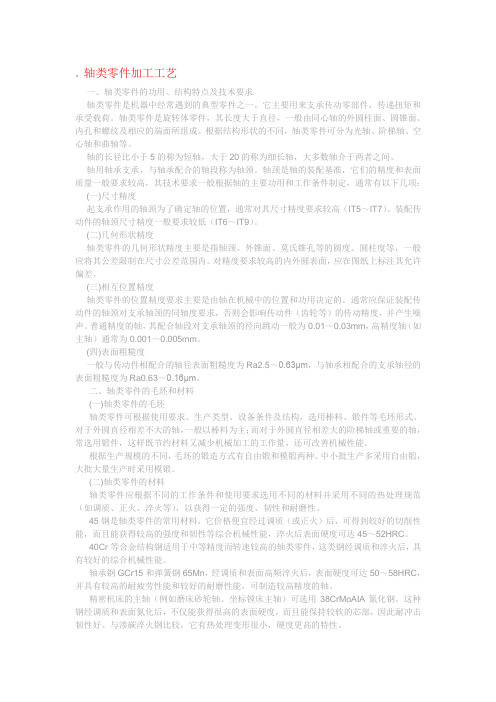
轴类零件加工工艺一、轴类零件的功用、结构特点及技术要求轴类零件是机器中经常遇到的典型零件之一。
它主要用来支承传动零部件,传递扭矩和承受载荷。
轴类零件是旋转体零件,其长度大于直径,一般由同心轴的外圆柱面、圆锥面、内孔和螺纹及相应的端面所组成。
根据结构形状的不同,轴类零件可分为光轴、阶梯轴、空心轴和曲轴等。
轴的长径比小于5的称为短轴,大于20的称为细长轴,大多数轴介于两者之间。
轴用轴承支承,与轴承配合的轴段称为轴颈。
轴颈是轴的装配基准,它们的精度和表面质量一般要求较高,其技术要求一般根据轴的主要功用和工作条件制定,通常有以下几项:(一)尺寸精度起支承作用的轴颈为了确定轴的位置,通常对其尺寸精度要求较高(IT5~IT7)。
装配传动件的轴颈尺寸精度一般要求较低(IT6~IT9)。
(二)几何形状精度轴类零件的几何形状精度主要是指轴颈、外锥面、莫氏锥孔等的圆度、圆柱度等,一般应将其公差限制在尺寸公差范围内。
对精度要求较高的内外圆表面,应在图纸上标注其允许偏差。
(三)相互位置精度轴类零件的位置精度要求主要是由轴在机械中的位置和功用决定的。
通常应保证装配传动件的轴颈对支承轴颈的同轴度要求,否则会影响传动件(齿轮等)的传动精度,并产生噪声。
普通精度的轴,其配合轴段对支承轴颈的径向跳动一般为0.01~0.03mm,高精度轴(如主轴)通常为0.001~0.005mm。
(四)表面粗糙度一般与传动件相配合的轴径表面粗糙度为Ra2.5~0.63μm,与轴承相配合的支承轴径的表面粗糙度为Ra0.63~0.16μm。
二、轴类零件的毛坯和材料(一)轴类零件的毛坯轴类零件可根据使用要求、生产类型、设备条件及结构,选用棒料、锻件等毛坯形式。
对于外圆直径相差不大的轴,一般以棒料为主;而对于外圆直径相差大的阶梯轴或重要的轴,常选用锻件,这样既节约材料又减少机械加工的工作量,还可改善机械性能。
根据生产规模的不同,毛坯的锻造方式有自由锻和模锻两种。
轴的加工工艺包括什么
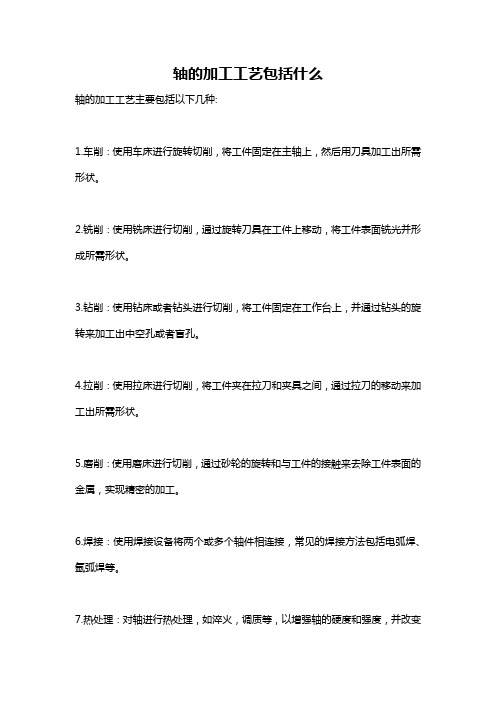
轴的加工工艺包括什么
轴的加工工艺主要包括以下几种:
1.车削:使用车床进行旋转切削,将工件固定在主轴上,然后用刀具加工出所需形状。
2.铣削:使用铣床进行切削,通过旋转刀具在工件上移动,将工件表面铣光并形成所需形状。
3.钻削:使用钻床或者钻头进行切削,将工件固定在工作台上,并通过钻头的旋转来加工出中空孔或者盲孔。
4.拉削:使用拉床进行切削,将工件夹在拉刀和夹具之间,通过拉刀的移动来加工出所需形状。
5.磨削:使用磨床进行切削,通过砂轮的旋转和与工件的接触来去除工件表面的金属,实现精密的加工。
6.焊接:使用焊接设备将两个或多个轴件相连接,常见的焊接方法包括电弧焊、氩弧焊等。
7.热处理:对轴进行热处理,如淬火,调质等,以增强轴的硬度和强度,并改变
其组织结构和性能。
8.抛光:对轴进行表面抛光处理,使其表面光滑,增加其美观性。
9.组装:将加工好的轴与其他配件一起进行组装,形成完整的机械设备。
轴类零件加工工艺

轴类零件加工工艺机床主轴机床主轴是典型的受扭转—弯曲复合作用的轴件,它受的应力不大(中等载荷),承担的冲击载荷也不大,假如使用滑动轴承,轴颈处要求耐磨。
因此大多采纳45钢制造,并进行调质处理,轴颈处由表面淬火来强化。
载荷较大时则用40Cr等低合金结构钢来制造。
车床主轴的选材结果如下:材料:45钢。
热处理:整体调质,轴颈及锥孔表面淬火。
性能要求:整体硬度NB220~HB240;轴颈及锥孔处硬度HRC52。
工艺路线:锻造→正火→粗加工→调质→精加工→表面淬火及低温回火→磨削。
该轴工作应力专门低,冲击载荷不大,45钢处理后屈服极限可达400MPa以上,完全可满足要求。
现在有部分机床主轴差不多能够用球墨铸铁制造。
拖拉机半轴汽车半轴是典型的受扭矩的轴件,但工作应力较大,且受相当大的冲击载荷,其结构如图5所示。
最大直径达50mm左右,用45钢制造时,即使水淬也只能使表面淬透深度为10%半径。
为了提高淬透性,并在油中淬火防止变形和开裂,中、小型汽车的半轴一样用40Cr制造,重型车用40CrMnMo等淬透性专门高的钢制造。
例:铁牛45半轴材料:40Cr。
热处理:整体调质。
性能要求:杆部HRC37~HRC44;盘部外圆HRC24~HRC34。
工艺路线:下料→锻造→正火→机械加工→调质→盘部钻孔→磨花键。
机床齿轮机床齿轮工作条件较好,工作中受力不大,转速中等,工作平稳无强烈冲击,因此其齿面强度、心部强度和韧性的要求均不太高,一样用45钢制造,采纳高频淬火表面强化,齿面硬度可达HRC52左右,这对弯曲疲劳或表面疲劳是足够了。
齿轮调质后,心部可保证有HB220左右的硬度及大于4kg?m/cm2的冲击韧性,能满足工作要求。
关于一部分要求较高的齿轮,可用合金调质钢(如40Cr等)制造。
这时心部强度及韧性都有所提高,弯曲疲劳及表面疲劳抗力也都增大。
例:一般车床床头箱传动齿轮。
材料:45钢。
热处理:正火或调质,齿部高频淬火和低温回火。
《轴类零件加工工艺》课件
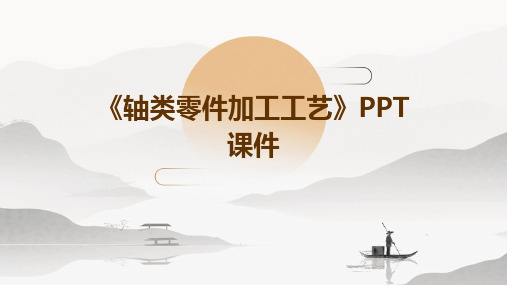
详细描述
轴类零件是各种机械设备中必不可少的组成部分,广泛 应用于汽车、机床、电机、船舶、航空航天等领域。例 如,在汽车中,轴类零件用于连接发动机和传动系统, 传递动力,驱动车辆行驶;在机床中,轴类零件用于支 撑旋转刀具或工件,实现切削加工;在电机中,轴类零 件用于传递扭矩,驱动发电机或电动机运转。因此,轴 类零件的性能和加工质量对机械设备的性能和使用寿命 具有重要影响。
直接测量法
通过直接测量工件尺寸、几何形 状等参数,与标准值进行比较, 判断是否符合要求。
比较测量法
使用标准量具与被测工件进行比 较,确定工件是否合格。
检测方法与工具
• 自动检测法:利用传感器、计算机等设备实现自动检测和 记录,提高检测效率和精度。
检测方法与工具
卡尺
用于测量长度、宽度、厚度等参数。
随着环保意识的提高,绿色制造技术成为未 来制造业的发展方向,轴类零件加工行业也 不例外。
详细描述
绿色制造技术包括节能减排、资源循环利用 、环保材料等,这些技术的应用能够降低轴 类零件加工过程中的能耗和排放,减少对环 境的污染,实现可持续发展。
新材料的应用与挑战
总结词
随着新材料技术的不断发展,新型材料在轴类零件加工中的应用越来越广泛,同时也带 来了一些挑战。
精加工
加工精度
精加工阶段需要进一步提高零件的加 工精度和表面质量。
余量控制
冷却方式
选择适当的冷却方式,如切削液、润 滑油等,以降低切削温度、减少刀具 磨损。
合理控制余量,避免过多或过少余量 导致的问题。
表面处理
表面粗糙度
轴类零件加工工艺
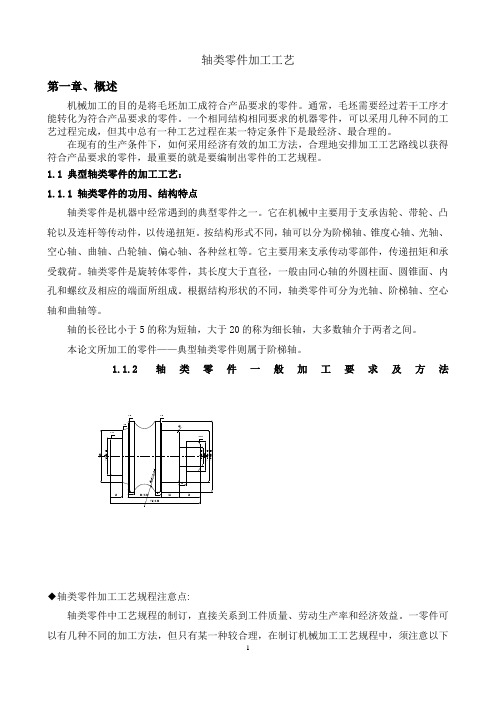
轴类零件加工工艺第一章、概述机械加工的目的是将毛坯加工成符合产品要求的零件。
通常,毛坯需要经过若干工序才能转化为符合产品要求的零件。
一个相同结构相同要求的机器零件,可以采用几种不同的工艺过程完成,但其中总有一种工艺过程在某一特定条件下是最经济、最合理的。
在现有的生产条件下,如何采用经济有效的加工方法,合理地安排加工工艺路线以获得符合产品要求的零件,最重要的就是要编制出零件的工艺规程。
1.1 典型轴类零件的加工工艺:1.1.1 轴类零件的功用、结构特点轴类零件是机器中经常遇到的典型零件之一。
它在机械中主要用于支承齿轮、带轮、凸轮以及连杆等传动件,以传递扭矩。
按结构形式不同,轴可以分为阶梯轴、锥度心轴、光轴、空心轴、曲轴、凸轮轴、偏心轴、各种丝杠等。
它主要用来支承传动零部件,传递扭矩和承受载荷。
轴类零件是旋转体零件,其长度大于直径,一般由同心轴的外圆柱面、圆锥面、内孔和螺纹及相应的端面所组成。
根据结构形状的不同,轴类零件可分为光轴、阶梯轴、空心轴和曲轴等。
轴的长径比小于5的称为短轴,大于20的称为细长轴,大多数轴介于两者之间。
本论文所加工的零件——典型轴类零件则属于阶梯轴。
1.1.2 轴类零件一般加工要求及方法◆轴类零件加工工艺规程注意点:轴类零件中工艺规程的制订,直接关系到工件质量、劳动生产率和经济效益。
一零件可以有几种不同的加工方法,但只有某一种较合理,在制订机械加工工艺规程中,须注意以下1几点。
1)粗基准选择:有非加工表面,应选非加工表面作为粗基准。
对所有表面都需加工的铸件轴,根据加工余量最小表面找正。
且选择平整光滑表面,让开浇口处。
选牢固可靠表面为粗基准,同时,粗基准不可重复使用。
2)精基准选择:要符合基准重合原则,尽可能选设计基准或装配基准作为定位基准。
符合基准统一原则。
尽可能在多数工序中用同一个定位基准。
尽可能使定位基准与测量基准重合。
选择精度高、安装稳定可靠表面为精基准。
工艺规程制订得是否合理,直接影响工件的质量、劳动生产率和经济效益。
轴类零件的加工工艺及技术要求
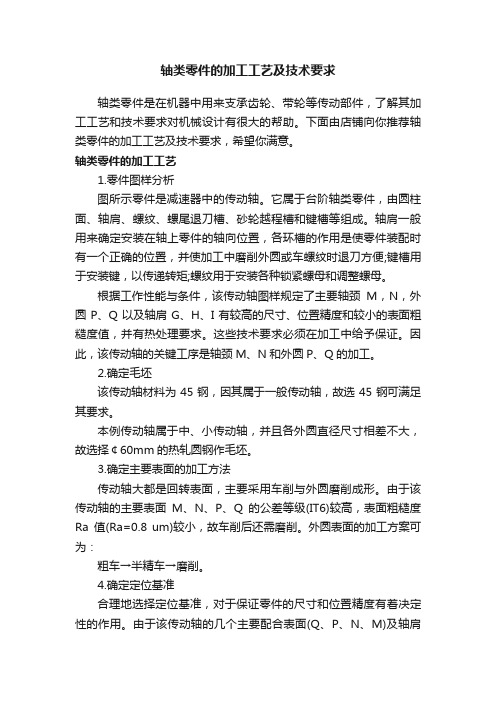
轴类零件的加工工艺及技术要求轴类零件是在机器中用来支承齿轮、带轮等传动部件,了解其加工工艺和技术要求对机械设计有很大的帮助。
下面由店铺向你推荐轴类零件的加工工艺及技术要求,希望你满意。
轴类零件的加工工艺1.零件图样分析图所示零件是减速器中的传动轴。
它属于台阶轴类零件,由圆柱面、轴肩、螺纹、螺尾退刀槽、砂轮越程槽和键槽等组成。
轴肩一般用来确定安装在轴上零件的轴向位置,各环槽的作用是使零件装配时有一个正确的位置,并使加工中磨削外圆或车螺纹时退刀方便;键槽用于安装键,以传递转矩;螺纹用于安装各种锁紧螺母和调整螺母。
根据工作性能与条件,该传动轴图样规定了主要轴颈M,N,外圆P、Q以及轴肩G、H、I有较高的尺寸、位置精度和较小的表面粗糙度值,并有热处理要求。
这些技术要求必须在加工中给予保证。
因此,该传动轴的关键工序是轴颈M、N和外圆P、Q的加工。
2.确定毛坯该传动轴材料为45钢,因其属于一般传动轴,故选45钢可满足其要求。
本例传动轴属于中、小传动轴,并且各外圆直径尺寸相差不大,故选择¢60mm的热轧圆钢作毛坯。
3.确定主要表面的加工方法传动轴大都是回转表面,主要采用车削与外圆磨削成形。
由于该传动轴的主要表面M、N、P、Q的公差等级(IT6)较高,表面粗糙度Ra值(Ra=0.8 um)较小,故车削后还需磨削。
外圆表面的加工方案可为:粗车→半精车→磨削。
4.确定定位基准合理地选择定位基准,对于保证零件的尺寸和位置精度有着决定性的作用。
由于该传动轴的几个主要配合表面(Q、P、N、M)及轴肩面(H、G)对基准轴线A-B均有径向圆跳动和端面圆跳动的要求,它又是实心轴,所以应选择两端中心孔为基准,采用双顶尖装夹方法,以保证零件的技术要求。
粗基准采用热轧圆钢的毛坯外圆。
中心孔加工采用三爪自定心卡盘装夹热轧圆钢的毛坯外圆,车端面、钻中心孔。
但必须注意,一般不能用毛坯外圆装夹两次钻两端中心孔,而应该以毛坯外圆作粗基准,先加工一个端面,钻中心孔,车出一端外圆;然后以已车过的外圆作基准,用三爪自定心卡盘装夹(有时在上工步已车外圆处搭中心架),车另一端面,钻中心孔。
轴类零件加工工艺
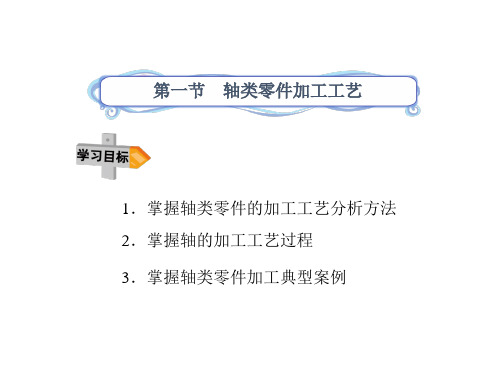
• 一、箱体零件的功用、结构及技术要求
1.功用、结构
功用:将机器中有关部件的轴、套、齿轮等相关零件连接成 一个整体,使这些零件保持正确的相对位置,并按一定的传动关 系协调地工作。
结构:形状复杂,壁薄且不均匀,内部呈腔形,既有精度要求 较高的孔系和平面,也有许多精度要求较低的紧固孔。
a)
b)
a)齿轮油泵箱体 b)齿轮减速箱箱体
Hale Waihona Puke 2.防止套类零件变形的工艺措施套类零件一般都存在壁较薄、径向刚度较差、容易变形等缺点。
套类零件变形的原因及工艺措施
导致变形的因素
工艺措施
夹紧力
(1)使夹紧力均匀分布,如图a所示 (2)变径向夹紧为轴向夹紧,如图b所示 (3)增加套筒毛坯的刚度,如图c所示
外力
切削力
重力 离心力
(1)增大刀具的主偏角 (2)内、外表面同时加工,如图c所示 (3)粗、精加工分开进行 增加辅助支承 配重
套类零件的毛坯类型与所用材料、结构形状和尺寸大小有关, 常采用型材、锻件或铸件。
毛坯内孔直径小于φ20mm时大多选用棒料,孔径较大、长度 较长的零件常用无缝钢管或带孔的铸、锻件。
• 三、套类零件的加工工艺分析
1.保证相互位置精度的工艺措施
轴承套毛坯采用“4件合一”的方 式加工:指棒料按四个轴承套零件尺 寸下料,四件同时加工
传动轴是轴类零件中使 用最多、结构最为典型的一 种阶梯轴,所示。该轴为小 批量生产,材料选择45钢, 淬火硬度40~45HRC。试分 析其加工工艺过程。
1.结构分析
主要结构要素有内外圆柱面、螺纹、键槽等,该轴为典型的 阶梯轴结构,有两个支承轴颈。
2.技术要求
两端轴颈的尺寸精度为IT7,表面粗糙度Ra值为0.8μm; 用于安装齿轮的轴颈的尺寸精度主IT7,表面粗糙度Ra值为 1.6μm; 右端轴颈外圆上规定了圆柱度为0.02mm; 左端轴颈外圆上规定了圆柱度为0.02mm; 轴上各配合面对两端轴颈的公共轴线的径向跳动为0.02mm, 可保证齿轮平稳传动。
轴类零件加工工艺方案设计说明书

本单元 小结
零件工艺性分析方法
采集分析信息的关键:
应用分析方法分析特定零件
与实际加工联系 对应的技术准备
轴类零件制造工艺特点
毛坯
棒料
锻件
加工方法
车(粗、半精)
磨 (精车)
安装
一端夹持
对顶
一夹一顶
工序尺寸
多为第一类,轴向尺寸、键槽为第二类
教学 单元
零件工艺设计原则
零件毛坯选择
添加标题
2
主题
添加标题
3
加工前应做的技术准备
添加标题
4
教学目标
添加标题
5
熟练进行零件工艺性分析
添加标题
6
二、轴类零件图纸的工艺性分析
支承传动件 传递运动、扭矩
添加标题
1
轴类零件在机器中的作用:
添加标题
2
结构特点:
添加标题
3
回转体、由各种回转面 组成
添加标题
4
主要技术要求:
添加标题
5
轴的直径精度,圆度、圆柱度、同轴度、垂直度等
工艺设计前的决策内容
本单元 小结
上教学 单元回顾
毛坯确定
1、
工艺设计步骤与方法
2、
工序尺寸计算方法
3、
工艺文件种类选择与填写
4、
2、复杂轴的工艺设计
1、简单轴的工艺设计
本教学 单元主题
接工艺过程卡
1、结构特点:回转面
轴类零件 加工小结
1、加工特点:以车为主,磨做精加工
1、毛坯选择:棒料
工艺计算
2、
工艺分析
2、
202X
轴类零件加工工艺过程
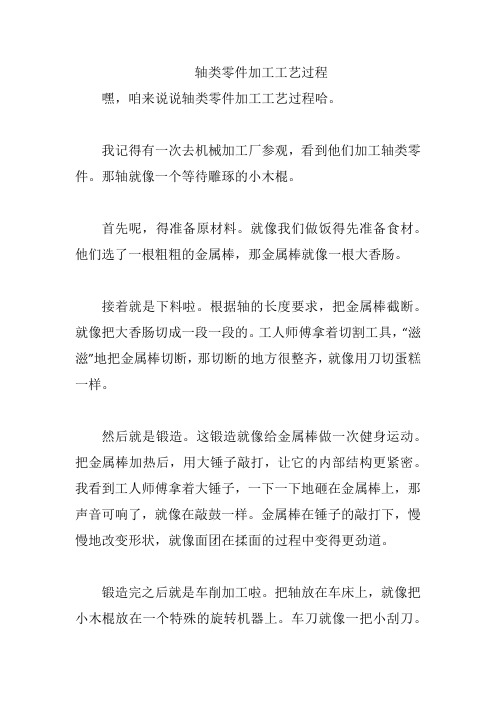
轴类零件加工工艺过程嘿,咱来说说轴类零件加工工艺过程哈。
我记得有一次去机械加工厂参观,看到他们加工轴类零件。
那轴就像一个等待雕琢的小木棍。
首先呢,得准备原材料。
就像我们做饭得先准备食材。
他们选了一根粗粗的金属棒,那金属棒就像一根大香肠。
接着就是下料啦。
根据轴的长度要求,把金属棒截断。
就像把大香肠切成一段一段的。
工人师傅拿着切割工具,“滋滋”地把金属棒切断,那切断的地方很整齐,就像用刀切蛋糕一样。
然后就是锻造。
这锻造就像给金属棒做一次健身运动。
把金属棒加热后,用大锤子敲打,让它的内部结构更紧密。
我看到工人师傅拿着大锤子,一下一下地砸在金属棒上,那声音可响了,就像在敲鼓一样。
金属棒在锤子的敲打下,慢慢地改变形状,就像面团在揉面的过程中变得更劲道。
锻造完之后就是车削加工啦。
把轴放在车床上,就像把小木棍放在一个特殊的旋转机器上。
车刀就像一把小刮刀。
车床开始转动,轴也跟着转起来,车刀慢慢地靠近轴,把多余的部分削掉。
我看到车削下来的金属屑就像小卷卷的面条一样掉下来。
就像我们削铅笔,把外面的木头削掉,露出尖尖的笔芯。
车削完了还要进行铣削。
铣削就像给轴做一些小装饰。
在轴上铣出一些键槽之类的。
铣刀在轴上快速地转动,就像一个小雕刻刀在雕刻。
我记得有一次,在铣削一个键槽的时候,工人师傅特别小心,要确保键槽的尺寸和位置都很精确,就像在雕刻一个精细的图案。
接着是磨削加工。
这磨削就像给轴做一次美容。
用砂轮把轴的表面磨得更光滑。
砂轮和轴接触的时候,发出“沙沙”的声音,就像在给轴擦脸。
我在机械加工厂看到从下料到最后的磨削,每一步都很关键。
所以说,轴类零件加工工艺过程就是下料、锻造、车削、铣削、磨削等。
就像他们加工轴类零件那样,这样就能做出一个合格的轴啦。
轴类零件从毛坯到成品的完整加工流程

轴类零件从毛坯到成品的完整加工流程下载温馨提示:该文档是我店铺精心编制而成,希望大家下载以后,能够帮助大家解决实际的问题。
文档下载后可定制随意修改,请根据实际需要进行相应的调整和使用,谢谢!并且,本店铺为大家提供各种各样类型的实用资料,如教育随笔、日记赏析、句子摘抄、古诗大全、经典美文、话题作文、工作总结、词语解析、文案摘录、其他资料等等,如想了解不同资料格式和写法,敬请关注!Download tips: This document is carefully compiled by the editor. I hope that after you download them, they can help you solve practical problems. The document can be customized and modified after downloading, please adjust and use it according to actual needs, thank you!In addition, our shop provides you with various types of practical materials, such as educational essays, diary appreciation, sentence excerpts, ancient poems, classic articles, topic composition, work summary, word parsing, copy excerpts, other materials and so on, want to know different data formats and writing methods, please pay attention!轴类零件从毛坯到成品的完整加工流程随着工业的不断发展,轴类零件在各种机械设备中扮演着重要的角色。
轴类零件的加工工艺

轴类零件的加工工艺
1. 零件分析:对轴类零件的图纸加工进行分析,包括尺寸、精度、材料等方面,确定加工工艺路线。
2. 材料准备:根据轴类零件的材料要求,选择符合要求的原材料进行加工前的准备。
3. 车削加工:轴类零件的加工主要采用车削的方式进行,通过车床加工,将材料逐步加工成符合要求的零件形状和尺寸。
4. 磨削加工:对于需要达到精度要求较高的轴类零件,可以通过磨削的方式进行加工,如内外圆磨削、表面磨削等。
5. 热处理:对于一些需要改变材料性质的轴类零件,可以通过热处理的方式进行加工,如淬火、回火等。
6. 装配:根据轴类零件的要求,可以进行装配,使得零件能够正常地使用。
7. 检验:对加工完成的轴类零件进行检验,包括尺寸、精度、硬度等方面的检验,确保零件质量符合要求。
轴类零件加工工艺毕业设计

轴类零件加工工艺毕业设计轴类零件加工工艺毕业设计在机械制造领域中,轴类零件是一种常见且重要的零件类型。
轴类零件的加工工艺对于产品的质量和性能有着直接的影响。
因此,对轴类零件的加工工艺进行深入研究和设计是非常有必要的。
本文将从加工工艺的选定、工艺流程的设计以及加工设备的选择等方面,探讨轴类零件加工工艺的毕业设计。
一、加工工艺选定轴类零件的加工工艺选定是毕业设计的核心部分。
在进行加工工艺选定时,需要考虑到零件的材料、形状、尺寸以及产品要求等因素。
首先,对于不同材料的轴类零件,其加工工艺会有所不同。
例如,对于钢材轴类零件,常见的加工工艺包括车削、铣削、钻削等;而对于铝合金轴类零件,则可以采用铣削、钻削、镗削等加工工艺。
其次,零件的形状和尺寸也会对加工工艺的选定产生影响。
对于较为复杂的形状和大尺寸的轴类零件,可能需要采用多道工序进行加工。
最后,根据产品要求,还需要考虑到表面光洁度、精度要求等因素,选择适合的加工工艺。
二、工艺流程设计在确定加工工艺选定后,需要进行工艺流程的设计。
工艺流程设计是将加工工艺按照一定的顺序组合起来,形成一条完整的加工流程。
在进行工艺流程设计时,需要考虑到加工工艺之间的先后关系、工艺之间的依赖关系以及工艺之间的协调性。
例如,对于一个轴类零件的加工工艺流程,可能包括车削、铣削、钻削等多个工艺。
在进行工艺流程设计时,需要确保各个工艺之间的顺序正确,避免出现工艺之间的冲突和矛盾。
此外,还需要考虑到工艺之间的依赖关系,确保前一道工艺的加工结果能够满足后一道工艺的要求。
最后,还需要考虑到工艺之间的协调性,确保整个加工流程的高效和稳定。
三、加工设备选择加工设备的选择是轴类零件加工工艺设计的重要环节。
在进行加工设备选择时,需要根据零件的形状、尺寸以及加工工艺的要求来确定合适的设备。
例如,对于较为复杂的形状和大尺寸的轴类零件,可能需要选择五轴联动加工中心或者数控车床等高精度加工设备。
而对于形状简单且尺寸较小的轴类零件,则可以选择普通车床或者铣床等设备。
轴类零件加工工艺介绍
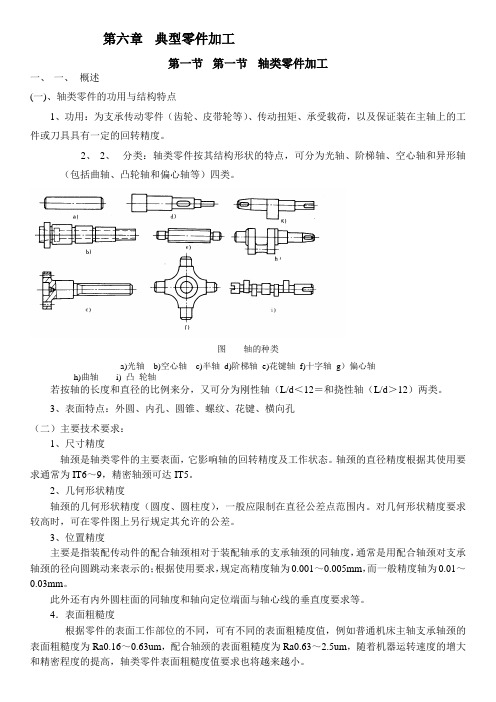
第六章典型零件加工第一节第一节轴类零件加工一、一、概述(一)、轴类零件的功用与结构特点1、功用:为支承传动零件(齿轮、皮带轮等)、传动扭矩、承受载荷,以及保证装在主轴上的工件或刀具具有一定的回转精度。
2、2、分类:轴类零件按其结构形状的特点,可分为光轴、阶梯轴、空心轴和异形轴(包括曲轴、凸轮轴和偏心轴等)四类。
图轴的种类a)光轴b)空心轴c)半轴d)阶梯轴e)花键轴f)十字轴g)偏心轴h)曲轴i) 凸轮轴若按轴的长度和直径的比例来分,又可分为刚性轴(L/d<12=和挠性轴(L/d>12)两类。
3、表面特点:外圆、内孔、圆锥、螺纹、花键、横向孔(二)主要技术要求:1、尺寸精度轴颈是轴类零件的主要表面,它影响轴的回转精度及工作状态。
轴颈的直径精度根据其使用要求通常为IT6~9,精密轴颈可达IT5。
2、几何形状精度轴颈的几何形状精度(圆度、圆柱度),一般应限制在直径公差点范围内。
对几何形状精度要求较高时,可在零件图上另行规定其允许的公差。
3、位置精度主要是指装配传动件的配合轴颈相对于装配轴承的支承轴颈的同轴度,通常是用配合轴颈对支承轴颈的径向圆跳动来表示的;根据使用要求,规定高精度轴为0.001~0.005mm,而一般精度轴为0.01~0.03mm。
此外还有内外圆柱面的同轴度和轴向定位端面与轴心线的垂直度要求等。
4.表面粗糙度根据零件的表面工作部位的不同,可有不同的表面粗糙度值,例如普通机床主轴支承轴颈的表面粗糙度为Ra0.16~0.63um,配合轴颈的表面粗糙度为Ra0.63~2.5um,随着机器运转速度的增大和精密程度的提高,轴类零件表面粗糙度值要求也将越来越小。
(三)、轴类零件的材料和毛坯合理选用材料和规定热处理的技术要求,对提高轴类零件的强度和使用寿命有重要意义,同时,对轴的加工过程有极大的影响。
1、轴类零件的材料一般轴类零件常用45钢,根据不同的工作条件采用不同的热处理规范(如正火、调质、淬火等),以获得一定的强度、韧性和耐磨性。
轴类零件加工工艺过程
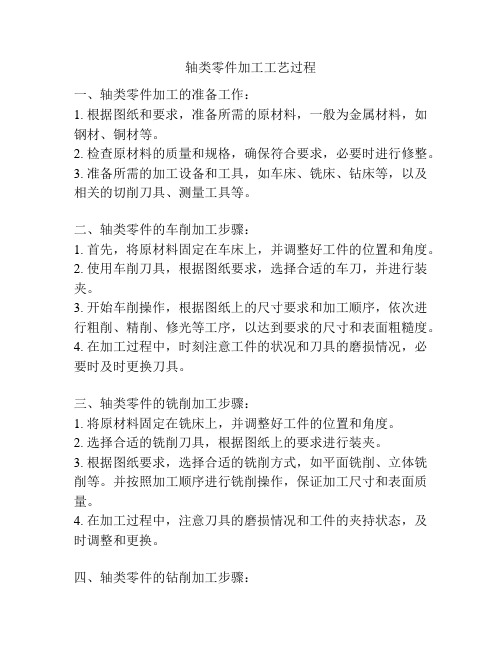
轴类零件加工工艺过程一、轴类零件加工的准备工作:1. 根据图纸和要求,准备所需的原材料,一般为金属材料,如钢材、铜材等。
2. 检查原材料的质量和规格,确保符合要求,必要时进行修整。
3. 准备所需的加工设备和工具,如车床、铣床、钻床等,以及相关的切削刀具、测量工具等。
二、轴类零件的车削加工步骤:1. 首先,将原材料固定在车床上,并调整好工件的位置和角度。
2. 使用车削刀具,根据图纸要求,选择合适的车刀,并进行装夹。
3. 开始车削操作,根据图纸上的尺寸要求和加工顺序,依次进行粗削、精削、修光等工序,以达到要求的尺寸和表面粗糙度。
4. 在加工过程中,时刻注意工件的状况和刀具的磨损情况,必要时及时更换刀具。
三、轴类零件的铣削加工步骤:1. 将原材料固定在铣床上,并调整好工件的位置和角度。
2. 选择合适的铣削刀具,根据图纸上的要求进行装夹。
3. 根据图纸要求,选择合适的铣削方式,如平面铣削、立体铣削等。
并按照加工顺序进行铣削操作,保证加工尺寸和表面质量。
4. 在加工过程中,注意刀具的磨损情况和工件的夹持状态,及时调整和更换。
四、轴类零件的钻削加工步骤:1. 将原材料固定在钻床上,并调整好工件的位置和角度。
2. 选择合适的钻孔刀具,根据图纸要求进行装夹。
3. 根据图纸上的孔径要求,选择合适的钻头,并进行设定,调整钻头的速度和进给量。
4. 开始钻削操作,根据图纸上的孔径位置进行钻孔,保证加工尺寸和孔壁的质量。
5. 在加工过程中,注意刀具的磨损情况和冷却液的使用,及时调整和更换。
五、轴类零件加工的后续工序:1. 进行工件的检验,包括尺寸测量、表面质量等,确保符合要求。
2. 进行必要的热处理、表面处理等工艺,以提高工件的性能和耐用度。
3. 进行最后的整理和打磨工作,使工件达到最终的要求。
4. 进行产品的包装和出库。
以上就是轴类零件加工的基本工艺过程,通过严格按照要求进行加工操作,可以确保加工出高质量的轴类零件。
加工过程中需要密切关注工件的状况和刀具的磨损情况,及时调整和更换,以保证加工质量和工艺效率。
机械制造及工艺——轴类零件加工工艺
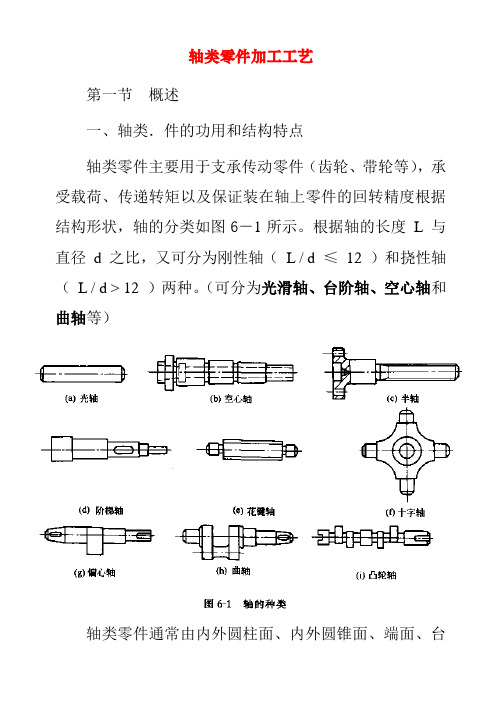
轴类零件加工工艺第一节概述一、轴类.件的功用和结构特点轴类零件主要用于支承传动零件(齿轮、带轮等),承受载荷、传递转矩以及保证装在轴上零件的回转精度根据结构形状,轴的分类如图6-1所示。
根据轴的长度L 与直径d 之比,又可分为刚性轴(L / d≤12 )和挠性轴(L / d > 12 )两种。
(可分为光滑轴、台阶轴、空心轴和曲轴等)轴类零件通常由内外圆柱面、内外圆锥面、端面、台阶面、螺纹、键槽、花键、横向孔及沟槽等组成。
二、轴类零件的技术要求、材料和毛坯装轴承的轴颈和装传动零件的轴头处表面,一般是轴类零件的重要表面,其尺寸精度、形状精度(圆度、圆柱度等)、位置精度(同轴度、与端面的垂直度等)及表面粗糙度要求均较高,是在制订轴类零件机械加工工艺规程时,应着重考虑的因素。
一般轴类零件常选用45#钢;对于中等精度而转速较高的轴可用40cr ;对于高速、重载荷等条件下工作的轴可选用20Cr 和20CrMnTi 等低碳合金钢进行渗碳淬火,或用3sCrMoAIA 氮化钢进行氮化处理。
轴类零件的毛坯最常用的是圆棒料和锻件,只有某些大型的、结构复杂的轴才采用铸件(铸钢或球墨铸铁)。
第二节外圆表面的加工方法和加工方案外圆表面是轴类零件的主要表面因此要合理地制订轴类零件的机械加工工艺规程,首先应了解外圆表面的各种加工方法和加工方案。
本章主要介绍常用的几种外圆加工方法和常用的外圆加工方案。
一、外圆表面的车削加工根据毛坯的制造精度和工件最终加工要求,外圆车削一般可分为粗车、半精车、精车、精细车。
粗车的目的是切去毛坯硬皮和大部分余量。
加工后工件尺寸精度IT11-IT13 ,表面粗糙度Ra50~12.5μm 。
半精车的尺寸精度可达IT8~IT11 ,表面粗糙度角Ra6.3~3.2μm 。
半精车可作为中等精度表面的终加工,也可作为磨削或精加工的预加工。
精车后的尺寸精度可达IT7~IT8 ,表面粗糙度Ra1.6~0.8μm 。
- 1、下载文档前请自行甄别文档内容的完整性,平台不提供额外的编辑、内容补充、找答案等附加服务。
- 2、"仅部分预览"的文档,不可在线预览部分如存在完整性等问题,可反馈申请退款(可完整预览的文档不适用该条件!)。
- 3、如文档侵犯您的权益,请联系客服反馈,我们会尽快为您处理(人工客服工作时间:9:00-18:30)。
以下为六角车床/转塔车床加工短轴的典型工艺: 1)送料,夹紧;2)粗车外圆;3)精车外圆,倒角;4)钻中心孔; 5)钻孔;6)铰孔;7)切槽,倒角;8)套外螺纹;9)滚花;10) 切断;11)车端面。
3、套筒类零件
4、盘类零件
对于毛坯为棒料或无缝钢管的盘类零件,都选用外圆表面作粗定 位基准。对于毛坯为锻件或铸件的盘类零件,其粗基准选择是:如果有 不加工表面,则以该表面为粗基准.如无这样的表面,则优先选择内孔 作为粗基准.或设划线工序,使零件加工余量合理分配。
在选择精基准时,通常采用互为基准的原则,视具体情况选择圆 或内孔,外圆与端面的组合或内孔与端面的组合等定位方式。精加工, 若要保证圆柱表面轴线与端面的垂直度,应以端面为基准;若要保证外 圆和内孔间的同轴度,则以外圆为基准;齿轮淬火后修磨内孔,应以齿 轮分度圆为基准。
(3)长轴类零件的轴径表面常见工艺路线
渗碳轴类零件: 备料—锻造—正火—钻中心孔—粗车—半精车、精车—渗碳(或碳氮共渗)—淬
火、低温回火—粗磨—次要表面加工—精磨。 一般精密调质钢轴类零件:
备料—锻造—正火(退火)—钻中心孔—粗车—调质—半精车、精车—表面淬 火、回火—粗磨—次要表面加工—精磨。 精密氮化钢轴类零件:
一端用中心孔定位。 对中心通孔的长轴,在内孔半精加工后,利用工件的内锥孔或内
孔的两端加工出带锥度的工艺孔,加上锥形堵塞或锥套心轴加工。内 孔精加工前不要将锥堵或锥套拆下,以避免因重新安装带耒的同轴度 误差。
(2)加工路线的安排 1)划分加工阶段
精度及表面粗糙度要求较高的重要表面(轴颈、基准内孔等)为粗加 工---半精加工---精加工三个阶段,对要求更高的表面还应有光整加工阶段; 其余表面加工分为粗加工一半精加工两个阶段进行或一次加工完毕。
备料—锻造—正火(退火)—钻中心孔—粗车—调质——半精车、精车—低温时 效—粗磨—氮化处理—次要表面加工—精磨—光磨。 整体淬火轴类零件:
备料—锻造—正火(退火)—钻中心孔—粗车—调质——半精车、精车—次要 表面加工—整体淬火—粗磨—低温时效—精磨。
2、短轴类零件
(1)定位基准的选择 短轴刚性大,一般以外圆柱面定位,用三爪卡盘夹紧后呈悬伸状切削。 径向力大时,用一端是工件外圆,一端中心孔定位。
二、轴类零件的材料、毛坯及热处理
1 材料 一般采用45钢。中等精度而转速较高的轴可采用40Cr等合金结构结构钢。精度较 高的轴可采用GCr15和65Mn等材料。高速、重载的轴选用20CrMnTi,20Mn2B,20Cr 等。
2 毛坯 一般采用圆棒料和锻件。某些大型结构复杂的用铸件。
3 热处理 锻造毛坯在机械加工前,需正火或退火热处理。 需局部表面淬火提高耐磨的轴,在淬火前安排调质处理,调质处理安排在粗车后, 半精车前。表面淬火安排在精加工前。 对精度较高的的轴,在局部淬火后或粗磨后,为控制尺寸稳定,需低温时效处理。 对氮化钢,需在氮化前进行调质和低温时效处理。 总之,轴的精度越高,对材料及热处理要求越高,热处理次数越多。机床主 轴,尤其紧密机床主轴,要求严格。
(1)定位基准的选择 对尺寸较小的套类零件,一般以外圆为定位基准,用三爪卡盘夹紧后呈 悬伸状切削.对内孔尺寸较大的套类零件,一般以外圆/内孔互为定位基准。 对长套筒类零件,加工外圆时,用双顶尖:加工内孔时,采用夹一头, 另一头用中心架托外圆。
(2)加工路线的拟定 一般套筒主要表面加工分在几次装夹中进行。划分出粗、半精、精加工 阶段。可先加工孔,然后以孔为精基准最终加工外圆,这种方法所用夹 具结构简单,定心精度高,能保证较高的位置精度,应用较广泛。也可 先加工外圆,然后以外圆为精基准最终加工孔,用此法工件装夹可靠, 但加工精度低,为得到较高的同轴度,采用定心精度高的夹具,如弹性 膜片卡盘、液性塑料夹具等。
2)热处理工序的安排 热处理工序一般安排在各个加工阶段之间。 毛坯在锻造或铸造后,一般须安排正火或退火处理,以便消除应力,细化 晶粒,改善切削性能。淬火,表面淬火,渗碳和氮化等热处理,安排在半精 加工之后,精磨前。 对精度很高的长轴,在淬火后精磨前,安排低温实效处理。 3)确定加工顺序 基准先行/先外后内/先大后小/断面宜后(指键槽、花键、横向孔)。
5、异形类零件
三、轴类零件的加工工艺过程
轴类零件的形状各种各样,其工艺过程也有所不同。 1.长轴类零件 2.短轴类零件 3.套筒类零件 4.盘类零件 5.异形轴类
1、长轴类零件
(1)定位基准的选择 一般长轴以中心孔为精基准,易实现基准统一,这也满足基准
重合原则。 粗加工时,为传递较大的扭矩和提高工件的刚性,一端用外圆,
(3)防止加工中套筒变形 套筒零件属薄壁件,加工中常因夹紧力、切削力、残余 应力和切削热等因素的影响而产生变形。故应采取如下防 止变形措施: 粗、精加工分阶段举行,并将热处理工序安排在粗、精 加工阶段之间,使粗加工产生的变形及热处理变形在精加 工中得到纠正。 对于精度要求较高精密套筒(孔圆度0.0015mm):任何 微小径向变形,都有可能引起失败,故应将径向夹紧改为 轴向夹紧;对于普通精度的套筒,如需径向夹紧时:也应 尽可能使径向夹紧力均匀,使用过渡套或弹簧套夹紧工件 或作出工艺凸边及工艺螺纹。
轴类零Байду номын сангаас加工工艺规程设计
一、轴类零件的分类、特点和技术要求
光滑轴;阶梯轴;空心轴;异形轴(曲轴、齿 轮轴、偏心轴、十字轴、凸轮轴、花键轴)
作用:起支承传动件和传递转矩。 形状:长度大于直径;加工表面为内外圆柱面、圆锥面、螺纹、 花键、沟槽等; 主要技术要求: 1)尺寸精度—轴径及内孔等配合有一定的尺寸精度要求.一般 为IT6-IT9轴向精度较低。 2)几何形状精度—轴径、基准内孔等重要表面有圆度或圆柱 度要求。 3)位置精度—重要圆柱表面有同轴度、径向圆跳动、轴心线 与基准面的垂直度、端面全跳动度要求。 4)表面粗糙度—重要表面粗糙度值为Ra0.1—0.6。