典型轴类零件数控加工工艺设计
轴套类零件数控车削加工工艺01图

短锥面配合零件根据图1、图2所示的短锥面配合零件,制定数控车削加工工艺(单件小批量生产),所用机床为CK6136S数控车床(FANUC 0i-TD数控系统)。
图1短锥面配合件—锥面套、短锥轴图2短锥面配合件—组合体1.工艺分析该组合件由轴类和套类两个零件组成,由一根毛坯料通过切断的方式来加工。
组合件表面由内外圆柱面、内外圆锥面、圆弧及外螺纹等表面组成,其中多个直径尺寸与轴向尺寸有较高的尺寸精度和表面粗糙度要求。
零件图尺寸标注完整,符合数控加工尺寸标注要求;轮廓描述清楚完整;零件材料为45钢,切削加工性能较好,无热处理和硬度要求。
通过上述分析,采取以下几点工艺措施:1)零件图上带公差的尺寸,因公差值较小,故编程时不必取其平均值,而取基本尺寸即可(其公差尺寸的保证主要是通过修改刀具半径值的方法来完成)。
2)该轴类零件左、右端面均为多个尺寸的设计基准,相应工序加工前,应该先将轴类零件的左、右端面车出来。
3)两个零件在加工时需左右掉头各装夹一次。
2.确定加工装备选用浙江凯达机床股份有限公司生产的SK6136S数控车,配置系统为FANUC 0imate-TD系统,配置标准三爪卡盘及卡盘钥匙,如图3所示。
图3 加工装备3.确定装夹方案1)采用三爪自动定心卡盘夹紧。
先加工套类零件,用三爪卡盘夹持长毛坯零件的一端,加工另一端端面,钻底孔,车φ48外圆,切断该套类零件。
掉头用三爪卡盘夹套类零件的φ48外圆,车内孔及内锥。
2)在加工轴类零件时,用三爪卡盘夹持毛坯零件左端,加工右端端面,外圆锥及φ40、φ48外圆。
掉头用三爪卡盘夹持零件右端φ40外圆,加工出左端φ48外圆,螺纹外圆及圆弧尺寸。
4.确定加工顺序及走刀路线加工顺序的确定按由外到内、由粗到精、由近到远的原则确定,在一次装夹中尽可能加工出较多的工件表面。
由于该零件为单件生产,走刀路线设计不必考虑最短进给路线或最短空行程路线,编程时车削走刀路线沿零件轮廓顺序进行。
毕业设计:数控车削圆锥轴套配合件的加工工艺及仿真
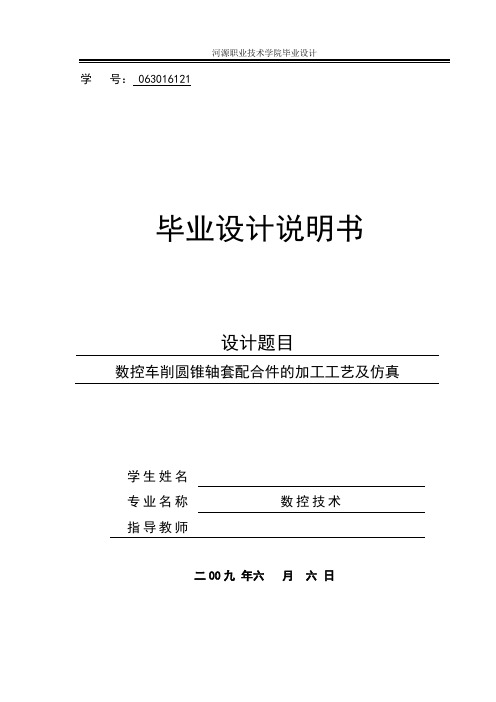
学号: 063016121毕业设计说明书设计题目数控车削圆锥轴套配合件的加工工艺及仿真学生姓名专业名称数控技术指导教师二00九年六月六日学号:063016121河源职业技术学院机电工程系毕业设计数控车削圆锥轴套配合件的加工工艺及仿真指导教师:专业名称:数控技术论文提交日期: 2009-6-1论文答辩日期: 2009-6-6论文评阅人:目录摘要 (1)ABSTRACT (2)第一章绪论 (3)第二章零件的结构分析 (4)2.1工件一的分析 (4)2.2工件二的分析 (5)2.3工件一与工件二装配分析 (6)2.4确定零件的公差等级 (6)2.4.1工件1的公差等级 (6)2.4.2工件2的公差等级 (7)第三章零件的工艺设计 (8)3.1加工设备的选定 (8)3.2零件材料和毛坯的选用 (8)3.3夹具的选用 (8)3.4刀具的选择 (8)3.4.1工件1选用的刀具 (9)3.4.2工件2选用的刀具 (9)3.5加工参数的选用 (9)3.5.1主轴转速的确定 (9)3.5.2进给速度的确定 (10)3.6.3背吃刀量确定 (10)第四章加工工艺方案 (11)4.1工件1工艺方案 (11)4.2工件2工艺方案 (11)第五章零件的加工编制 (13)5.1数控车床编程基础 (13)5.1.1数控车床编程特点 (13)5.1.2数控车床的坐标系和参考点 (13)5.2工件1加工程序 (14)5.3工件2加工程序 (15)总结 (16)参考文献 (17)结束语 (18)摘要轴类零件是机器中经常遇到的典型零件之一。
它主要用来支承传动零部件,传递扭矩和承受载荷。
轴类零件是旋转体零件,其长度大于直径,一般由同心轴的外圆柱面、圆锥面、内孔和螺纹及相应的端面所组成。
根据结构形状的不同,轴类零件可分为光轴、阶梯轴、空心轴和曲轴等。
本设计圆锥轴套配合件为典型的轴类零件,零件形状轨迹虽然并不复杂但是为了保证相互配合,必须右严格的尺寸要求,所以加工难度大。
轴类零件的数控加工工艺编制及分析
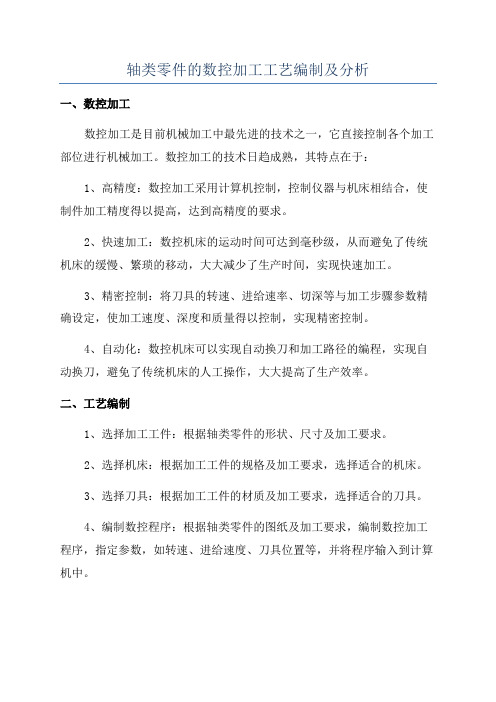
轴类零件的数控加工工艺编制及分析
一、数控加工
数控加工是目前机械加工中最先进的技术之一,它直接控制各个加工部位进行机械加工。
数控加工的技术日趋成熟,其特点在于:
1、高精度:数控加工采用计算机控制,控制仪器与机床相结合,使制件加工精度得以提高,达到高精度的要求。
2、快速加工:数控机床的运动时间可达到毫秒级,从而避免了传统机床的缓慢、繁琐的移动,大大减少了生产时间,实现快速加工。
3、精密控制:将刀具的转速、进给速率、切深等与加工步骤参数精确设定,使加工速度、深度和质量得以控制,实现精密控制。
4、自动化:数控机床可以实现自动换刀和加工路径的编程,实现自动换刀,避免了传统机床的人工操作,大大提高了生产效率。
二、工艺编制
1、选择加工工件:根据轴类零件的形状、尺寸及加工要求。
2、选择机床:根据加工工件的规格及加工要求,选择适合的机床。
3、选择刀具:根据加工工件的材质及加工要求,选择适合的刀具。
4、编制数控程序:根据轴类零件的图纸及加工要求,编制数控加工程序,指定参数,如转速、进给速度、刀具位置等,并将程序输入到计算机中。
轴类零件加工工艺过程【详解】

轴类零件加工工艺过程内容来源网络,由“深圳机械展(11万㎡,1100多家展商,超10万观众)”收集整理!更多cnc加工中心、车铣磨钻床、线切割、数控刀具工具、工业机器人、非标自动化、数字化无人工厂、精密测量、3D打印、激光切割、钣金冲压折弯、精密零件加工等展示,就在深圳机械展.轴类零件是常见的零件之一。
按轴类零件结构形式不同,一般可分为光轴、阶梯轴和异形轴三类;或分为实心轴、空心轴等。
它们在机器中用来支承齿轮、带轮等传动零件,以传递转矩或运动。
台阶轴的加工工艺较为典型,反映了轴类零件加工的大部分内容与基本规律。
下面就以减速箱中的传动轴为例,介绍一般台阶轴的加工工艺。
1.零件图样分析图A-1 传动轴图A-1所示零件是减速器中的传动轴。
它属于台阶轴类零件,由圆柱面、轴肩、螺纹、螺尾退刀槽、砂轮越程槽和键槽等组成。
轴肩一般用来安装在轴上零件的轴向位置,各环槽的作用是使零件装配时有一个正确的位置,并使加工中磨削外圆或车螺纹时退刀方便;键槽用于安装键,以传递转矩;螺纹用于安装各种锁紧螺母和调整螺母。
根据工作性能与条件,该传动轴图样(图A-1)规定了主要轴颈M,N,外圆P、Q以及轴肩G、H、I有较高的尺寸、位置精度和较小的表面粗糙度值,并有热处理要求。
这些技术要求必须在加工中给予得到确保。
因此,该传动轴的关键工序是轴颈M、N和外圆P、Q的加工。
2.确定毛坯该传动轴材料为45钢,因其属于一般传动轴,故选45钢可满足其要求。
本例传动轴属于中、小传动轴,并且各外圆直径尺寸相差不大,故选择¢60mm的热轧圆钢作毛坯。
3.确定主要表面的加工方法传动轴大都是回转表面,主要采用车削与外圆磨削成形。
由于该传动轴的主要表面M、N、P、Q的公差等级(IT6)较高,表面粗糙度Ra值(Ra=0.8 um)较小,故车削后还需磨削。
外圆表面的加工方案(参考表A-3)可为:粗车→半精车→磨削。
4.定位基准合理地选择定位基准,对于零件的尺寸和位置精度有着决定性的作用。
轴类零件的数控加工工艺和程序编制

轴类零件的数控加工工艺和程序编制轴类零件是机械制造中常见的零件类型,其外观形态特征是一条导向的长轴,其与其他机械部件的连接必须要求较高的配合精度和表面质量。
数控加工是一种精度高、效率高、重复性好的加工方式,因此在轴类零件的加工中应用十分广泛。
本文将就轴类零件的数控加工工艺和程序编制进行详细介绍。
一、零件设计和加工前准备在加工轴类零件之前,必须对零件进行设计,包括轴的直径、长度以及与其他机械部件之间的连接方式等。
同时还要对原材料进行选取和检验,保证原材料的质量符合要求。
根据零件图纸,制作加工工艺流程图,并确定加工工序、工具的选择和切削参数等。
为保证加工质量和生产效率,选择合适的加工中心、夹具和辅助装置来进行加工准备。
二、数控编程数控编程是数控加工的核心,其目的是根据零件图纸和加工工艺流程图,编出机床能够识别的G代码和M 代码,控制数控机床按照预定的加工路径和工艺参数进行加工。
在轴类零件的数控编程过程中,需要注意以下几点:1.合理选择加工方式:轴类零件表面质量要求高,因此需采用多道次切削的方式,以减小一次切削的切削量,提高表面光洁度和精度。
2.合理选择切削工具:根据轴类零件的材质和加工工艺,选择合适的切削工具,包括刀具形状、切削刃数和硬度等.3.合理选择切入和切出方式:切削前后,机床的运动速度要慢,以免对工件表面形成切削痕迹。
4.合理选择切削参数:根据轴类零件的材质、切削类型和工艺要求等,合理选取切削速度、进给量、切深等切削参数。
5.确保程序正确性:数控编程完成后,需要进行程序检查和验证,以确保程序的正确性和可行性。
在加工过程中,还需进行数控系统的监测和调整,以保证加工的准确性和稳定性。
三、数控加工过程数控加工过程是指根据数控编程的G代码和M代码,控制数控机床进行加工的过程。
在轴类零件的数控加工过程中,应注意以下几点:1.保持加工平稳:轴类零件加工时需要注意加工平稳,尽量减少零件表面划痕和毛刺等缺陷,以提高表面质量和精度。
轴类零件数控加工工艺
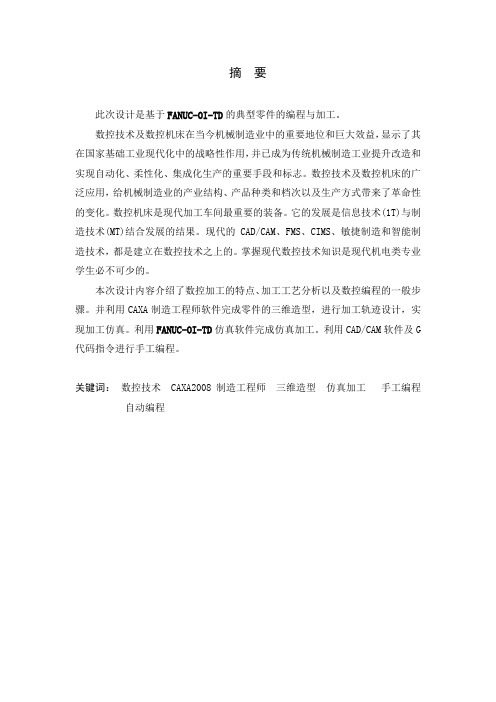
摘要此次设计是基于FANUC-OI-TD的典型零件的编程与加工。
数控技术及数控机床在当今机械制造业中的重要地位和巨大效益,显示了其在国家基础工业现代化中的战略性作用,并已成为传统机械制造工业提升改造和实现自动化、柔性化、集成化生产的重要手段和标志。
数控技术及数控机床的广泛应用,给机械制造业的产业结构、产品种类和档次以及生产方式带来了革命性的变化。
数控机床是现代加工车间最重要的装备。
它的发展是信息技术(1T)与制造技术(MT)结合发展的结果。
现代的CAD/CAM、FMS、CIMS、敏捷制造和智能制造技术,都是建立在数控技术之上的。
掌握现代数控技术知识是现代机电类专业学生必不可少的。
本次设计内容介绍了数控加工的特点、加工工艺分析以及数控编程的一般步骤。
并利用CAXA制造工程师软件完成零件的三维造型,进行加工轨迹设计,实现加工仿真。
利用FANUC-OI-TD仿真软件完成仿真加工。
利用CAD/CAM软件及G 代码指令进行手工编程。
关键词:数控技术CAXA2008制造工程师三维造型仿真加工手工编程自动编程AbstractThe tax system of real estate is a powerful leverage to keep the market’s fair competition and realize the macro adjustment and control on real estate. The design is based on the typical components FANUC-OI-TD programming and processing.CNC technology and CNC machine tools in today's machinery manufacturing industry in the important position and great efficiency, showing its presence in the national infrastructure in the strategic role of industrial modernization, and has become the traditional mechanical manufacturing industry to enhance the transformation and realization of automation, flexible, integrated an important means of production and logo. CNC technology and CNC machine tool widely used for industrial machinery manufacturing industry, product type and grade as well as the mode of production has brought a revolutionary change. CNC machine tool is the most important modern processing plant equipment. Its development of information technology (1T) and Manufacturing Technology (MT) integrated development results. Modern CAD / CAM, FMS, CIMS, agile manufacturing and intelligent manufacturing technology, are based on numerical control technology on top of. To master modern CNC technology, modern machinery and electronic knowledge is essential for students.The design of the content presented the characteristics of CNC machining, processing technology analysis, and numerical control programming general steps. And take advantage of CAXA 2008Manufacturing Engineer to complete part of the three-dimensional modeling software, for processing trajectory design, implementation process simulation. Complete the simulation using simulation software FANUC processing. The u se of CAD / CAM software and G code instructions manua l programming.Keywords:CNC Technology CAXA2008 Manufacturing Engineer Three-dimensional modeling Simulation processing Manualprogramming Automatic Programming目录第一章:概述1.1数控加工的特 (9)1.2数控机床 (10)1.3数控加工 (15)1.4数控编程系 (16)1.5CAD/CAM系统 (17)第二章:数控机床的分类2. 1按加工工艺方法分 (19)2.1.1金属切削类数控机床 (19)2.1.2特种加工类数控机床 (20)2.1.3板材加工数控机床 (20)2. 2按控制控制运动轨迹分类 (20)2.2. 1点位控制数控机床 (20)2.2. 2直线控制数控机床 (21)2.2. 3轮廓控制数控机床 (19)2. 3按驱动装置的特点分类 (20)2.3. 1开环控制数控机床 (20)2.3. 2闭环控制数控机床 (23)2.2. 3半闭环控制数控机床 (23)2.2.4混合控制数控机床 (24)第三章数控车的工艺与工装3.1. 合理选择切削用量 (25)3.2合理选择刀具 (26)3.3合理选择夹具 (27)3.4确定加工路线 (27)3.5 加工路线与加工余量的联系 (27)3.6夹具安装要点 (27)第四章数控车轴类零件加工4.1轴类零件数控加工工艺设计 (28)4.1.1零件图工艺分析 (28)4.2数控走刀路线图:(用CAXA数控车2008生成) (29)4.2.1粗车外形走刀路线图:(用CAXA数控车2008生成)..29 4.2.2精车外形走刀路线图:(用CAXA数控车2008生成)..30 4.2.3切槽走刀路线图:(用CAXA数控车2008生成) (31)4.2.4切螺纹走刀路线图:(用CAXA数控车2008生成) (32)4.2.5工件调头装夹以后的加工路线图 (33)4.2.6精加工调头后的外形刀路线图:(用CAXA数控车2008生成) (34)4.2.7 工艺措施 (34)4.2.8选择设备 (35)4.2.9确定零件的定位基准和装夹方式 (35)4.2.10刀具选择与参数 (36)4.2.11.表1 数控加工刀具卡片 (40)4.2.12合理选择切削用量 (41)4.2.13典型轴类零件数控加工工艺卡片 (42)4.2.14零件粗精加工程序(FAUNC─TD系统;主轴是无极调速) (43)(1)粗加工外形 (43)(2)精加工外形尺寸 (48)(3)加工螺纹退刀槽 (50)(4)加工外螺纹 (52)(5)利用装有正爪的卡盘的数控车床装夹加工 (54)(5.1)粗加工外形 (54)(5.2)精加工外形 (57)4.2.15实际加工程序:(整合后) (59)4.2.16程序传输 (68)4.2.17孔加工专用夹具 (71)4.2.18.直径6mm的孔的加工 (83)第五章程序首句妙用与控制尺寸精度的技巧5.1程序首句妙用G00的技巧 (85)5.2控制尺寸精度的技巧 (86)5.2.1修改刀补值保证尺寸精度 (87)5.2.2半精加工消除丝杆间隙影响保证尺寸精度 (87)5.2.3程序编制保证尺寸精度 (87)5.2.4修改程序和刀补控制尺寸 (88)第六章数控电气技术6.1数控机床电气控制系统综述 (89)6.2数控机床运动坐标的电气控制 (92)结束语 (95)致谢 (96)参考文献 (97)第一章概述1.1 数控加工的特点数控加工,也称之为NC(Numerical Control)加工,是以数值与符号构成的信息,控制机床实现自动运转。
轴类零件加工工艺设计毕业论文

图上几个精度要求较高的尺寸,因其公差值较小,所以编程时没有取平均值,而取其基本尺寸。
在轮廓线上,有个锥度10度坐标P1、和一处圆弧切点P2,在编程时要求出其坐标,P1(,75)P2(35,)。
通过以上数据分析,考虑加工的效率和加工的经济性,最理想的加工方式为车削,考虑该零件为大批量加工,故加工设备采用数控车床。
确定切削用量
数控编程时,编程人员必须确定每道工序的切削用量,并以指令的形式写人程序中。切削用量包括主轴转速、背吃刀量及进给速度等。对于不同的加工方法,需要选用不同的切削用量。切削用量的选择原则是:保证零件加工精度和表面粗糙度,充分发挥刀具切削性能,保证合理的刀具耐用度,并充分发挥机床的性能,最大限度提高生产率,降低成本。
设置刀点和换刀点
刀具究竟从什么位置开始移动到指定的位置呢?所以在程序执行的一开始,必须确定刀具在工件坐标系下开始运动的位置,这一位置即为程序执行时刀具相对于工件运动的起点,所以称程序起始点或起刀点。此起始点一般通过对刀来确定,所以,该点又称对刀点。在编制程序时,要正确选择对刀点的位置。对刀点设置原则是:便于数值处理和简化程序编制。易于找正并在加工过程中便于检查,引起的加工误差小。对刀点可以设置在加工零件上,也可以设置在夹具上或机床上,为了提高零件的加工精度,对刀点应尽量设置在零件的设计基准或工艺基谁上。实际操作机床时,可通过手工对刀操作把刀具的刀位点放到对刀点上,即“刀位点”与“对刀点”的重合。所谓“刀位点”是指刀具的定位基准点,车刀的刀位点为刀尖或刀尖圆弧中心。平底立铣刀是刀具轴线与刀具底面的交点。球头铣刀是球头的球心,钻头是钻尖等。用手动对刀操作,对刀精度较低,且效率低。而有些工厂采用光学对刀镜、对刀仪、自动对刀装置等,以减少对刀时间,提高对刀精度。加工过程中需要换刀时,应规定换刀点。所谓“换刀点”是指刀架转动换刀时的位置,换刀点应设在工件或夹具的外部,以换刀时不碰工件及其它部件为准。
轴类零件的数控加工工艺分析
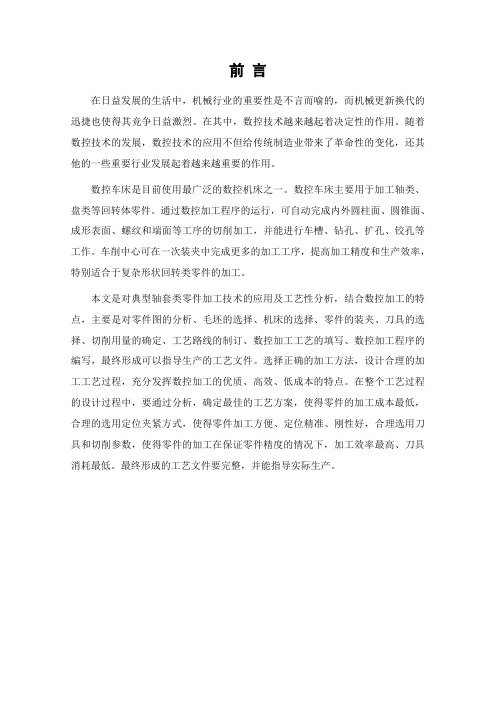
前言在日益发展的生活中,机械行业的重要性是不言而喻的,而机械更新换代的迅捷也使得其竞争日益激烈。
在其中,数控技术越来越起着决定性的作用。
随着数控技术的发展,数控技术的应用不但给传统制造业带来了革命性的变化,还其他的一些重要行业发展起着越来越重要的作用。
数控车床是目前使用最广泛的数控机床之一。
数控车床主要用于加工轴类、盘类等回转体零件。
通过数控加工程序的运行,可自动完成内外圆柱面、圆锥面、成形表面、螺纹和端面等工序的切削加工,并能进行车槽、钻孔、扩孔、铰孔等工作。
车削中心可在一次装夹中完成更多的加工工序,提高加工精度和生产效率,特别适合于复杂形状回转类零件的加工。
本文是对典型轴套类零件加工技术的应用及工艺性分析,结合数控加工的特点,主要是对零件图的分析、毛坯的选择、机床的选择、零件的装夹、刀具的选择、切削用量的确定、工艺路线的制订、数控加工工艺的填写、数控加工程序的编写,最终形成可以指导生产的工艺文件。
选择正确的加工方法,设计合理的加工工艺过程,充分发挥数控加工的优质、高效、低成本的特点。
在整个工艺过程的设计过程中,要通过分析,确定最佳的工艺方案,使得零件的加工成本最低,合理的选用定位夹紧方式,使得零件加工方便、定位精准、刚性好,合理选用刀具和切削参数,使得零件的加工在保证零件精度的情况下,加工效率最高、刀具消耗最低。
最终形成的工艺文件要完整,并能指导实际生产。
目录前言------------------------------------------------------------2 摘要------------------------------------------------------------5 第一章零件加工工艺分析1.1零件图的工艺分析------------------------------------------71.2零件图纸中的尺寸标注分析----------------------------------81.3 零件的结构工艺性分析-------------------------------------8 1.4零件毛坯的选择--------------------------------------------91.5确定零件的定位基准和装夹方式-----------------------------101.5.1粗基准选择原则1.5.2精基准选择原则1.5.3定位基准1.5.4装夹方式第二章数控加工工艺方案的制定2.1加工方法的选择------------------------------------------11 2.2加工方案的确定--------------------------------------------122.3工序与工歩的划分----------------------------------------123.3.1按工序划分3.3.2按工歩的划分2.4确定加工顺序及进给路线----------------------------------133.4.1零件加工必须遵守的安排原则3.4.2进给路线2.5加工机床的选择------------------------------------------142.6刀具的选择----------------------------------------------14 2.7量具的选择----------------------------------------------16 2.8冷却液的选择--------------------------------------------17 第三章切削用量的选择3.1切削用量的选择原则--------------------------------------18 3.2背吃刀量的选择------------------------------------------19 3.3主轴转速的选择------------------------------------------19 3.4进给量或进给速度的选择----------------------------------20 3.5编程误差及其控制------------------------------------------------------------213.5.1编程误差3.5.2误差控制第四章 SIEMENS 802C常用编程指令4.1常用G指令代码功能表 -----------------------------------224.2常用M指令代码功能表------------------------------------23 第五章数控加工工艺过程卡片5.1数控车削加工工艺过程卡片--------------------------------24 5.2 数控车削加工零件工序卡片-------------------------------25 5.3数控车加工刀具卡片--------------------------------------26 第六章程序编制及模拟运行6.1编写数控加工程序-----------------------------------------276.2程序的模拟运行-------------------------------------------296.3零件的加工---------------------------------------------29 6.4加工结果检测-------------------------------------------29第七章设备简介7.1西门子802C数控系统简介----------------------------------307.2 CK6141数控车床简介------------------------------------31 毕业设计总结-------------------------------------------------33 参考文献-----------------------------------------------------34 致谢---------------------------------------------------------35摘要本文是对典型轴类零件加工技术的应用及数控加工的工艺性分析,主要是对零件图的分析、毛坯的选择、定位基准的选择、零件的装夹、工艺路线的制订、刀具的选择、切削用量的确定、数控加工工艺卡片的填写、数控加工程序的编写。
数控车---简单轴类零件的编程与加工.
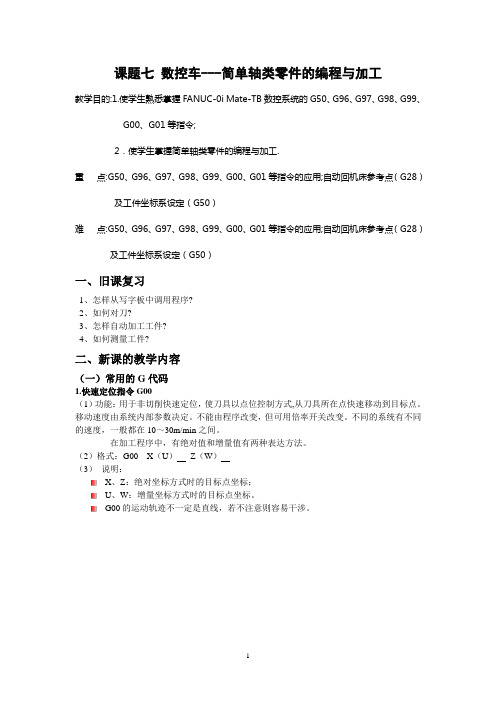
课题七数控车---简单轴类零件的编程与加工教学目的:1.使学生熟悉掌握FANUC-0i Mate-TB数控系统的G50、G96、G97、G98、G99、G00、G01等指令;2.使学生掌握简单轴类零件的编程与加工.重点:G50、G96、G97、G98、G99、G00、G01等指令的应用;自动回机床参考点(G28)及工件坐标系设定(G50)难点:G50、G96、G97、G98、G99、G00、G01等指令的应用;自动回机床参考点(G28)及工件坐标系设定(G50)一、旧课复习1、怎样从写字板中调用程序?2、如何对刀?3、怎样自动加工工件?4、如何测量工件?二、新课的教学内容(一)常用的G代码1.快速定位指令G00(1)功能:用于非切削快速定位,使刀具以点位控制方式,从刀具所在点快速移动到目标点。
移动速度由系统内部参数决定。
不能由程序改变,但可用倍率开关改变。
不同的系统有不同的速度,一般都在10~30m/min之间。
在加工程序中,有绝对值和增量值有两种表达方法。
(2)格式:G00 X(U)Z(W)(3)说明:X、Z:绝对坐标方式时的目标点坐标;U、W:增量坐标方式时的目标点坐标。
G00的运动轨迹不一定是直线,若不注意则容易干涉。
图7-1 采用绝对坐标G00X37Z30 图7-2 采用相对坐标G00U25W202 . 直线插补G01(1)功能:使刀具以给定的进给速度,从所在点出发,直线移动到目标点。
(2)格式:G01 X(U)Z(W) F(3)说明:X、Z: 绝对坐标方式时的目标点坐标;U、W: 增量坐标方式时的目标点坐标。
F是进给速度。
3 . 暂停指令(G04)(1)功能:该指令可使刀具做短时间的停顿, 即刀具作短时的无进给运动(2)格式:G04 X(U)G04 P(3)说明:X、U指定时间,允许带小数点;秒P指定时间,不允许带小数点,毫秒(4)应用场合:车削沟槽或钻孔时,为使槽底或孔底得到准确的尺寸精度及光滑的加工表面,在加工到槽底或孔底时,应暂停适当时间;使用G96车削工件轮廓后,改成G97车削螺纹时,可暂停适当时间,使主轴转速稳定后再执行车螺纹,以保证螺距加工精度要求。
毕业设计——轴套的加工工艺分析
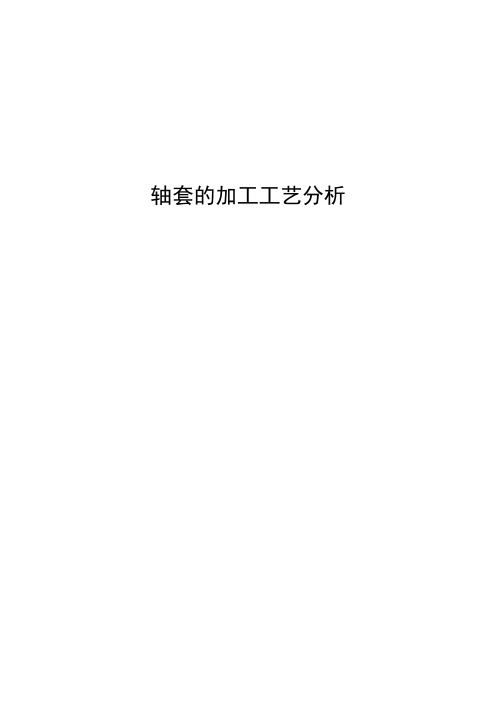
轴套的加工工艺分析【摘要】轴套类零件是机器中经常遇到的典型零件之一。
它主要用来支承传动零部件,传递扭矩和承受载荷。
轴套类零件是旋转体零件,其长度大于直径,一般由同心轴的外圆柱面、圆锥面、内孔和螺纹及相应的端面所组成。
本文是对典型轴套类零件加工技术的应用及数控加工的工艺性分析。
【关键词】:工艺分析,加工程序,切削用量,公差目录引言 (1)一、零件工艺分析 (1)(一)零件的分析 (1)二、毛坯的选择 (3)(一)毛坯的种类 (3)(二)选择毛坯的原则 (3)三、数控加工工艺分析 (4)(一)定位基准的确定 (4)(二)工艺路线的拟订 (5)(三)机床设备与工艺装备的选择 (6)(四)加工阶段的划分 (7)(五)工序的划分 (8)(六)工序顺序的安排 (8)总结 (12)参考文献 (22)谢辞....................................................................................................................错误!未定义书签。
引言毕业设计是专业教学工作的重要组成部分和教学过程中的重要实际性环节。
毕业设计的目的是:通过设计,培养我们综合运用所学的基础理论知识,专业理论知识和一些相关软件的学习,去分析和解决本专业范围内的一般工程技术问题的能力,培养我们建立正确的工艺设计思维,学会查找工具书,掌握数控工艺设计的一般程序,规范和方法。
本次设计选择的课题为轴套零件的车削加工工艺设计及其数控加工程序编制(如图1)。
这次毕业设计让我们对机械制图的基础知识有了进一步的了解,同时也为我们从事绘图工作奠定了一个良好的基础。
并锻炼了自己的动手能力,达到了学以致用的目的。
它是一次专业技能的重要训练和知识水平的一次全面体验,是学生毕业资格认定的重要依据,同时也为我们将来走向工作岗位奠定了必要的理论基础和实践经验。
轴类零件机械加工工艺规程设计

1.零件图的分析
设计说明书
由零件图可知,该零件属于轴类回转体零件,零件表面有圆弧,切槽,倒角,简 单螺纹,锥体,锥孔部分,是一个结构复杂的细长轴零件,零件的主体尺寸长度为 145mm,最大位置直径为Φ53mm,最右端有一段长 22mm 公称直径为Φ33mm 的普通 螺纹,并有 2×45º倒角,但零件中没有退刀槽,这就给零件的加工增加了一定的难度, 再是一段由直径为Φ35mm 和Φ44mm 之间连接的半径为 R24mm 的圆弧,要计算出交 点尺寸才可以编程,左端的孔加工也有一定的难度,最小直径部分要计算出尺寸,加 工时要保证孔的锥度和表面粗糙度,中间要有大量的计算。给整个设计带来了一定的 挑战。
因: VC=∏dn/1000
F= f×n
故主轴转速:n=(1000×110)/(3.14×60)=584r/min
进给速度:F= f×n=0.3×584=175 mm/min
考虑到刀具强度、机床刚度等实际情况,选择 n=600r/min F=200 mm/min
ap=3mm; (2)精车外圆时,选取 VC=130m/min ap=0.2mm f=0.1mm.
选取刀具时,要使刀具的尺寸与被加工工件的表面尺寸和形状相适应。根据零件 的分析所选择的刀具有:主偏角分别为 75º、30º的外圆车刀,宽度为 3.5mm 的切槽刀, 刀片材料为标准的 60º螺纹车刀。标准直径为Φ24 的麻花钻,内圆车刀。刀片材料为 YT15 或 YT30。 2.4 机床的选用
根据现有数控机床和零件的加工工艺可选用。华中数控系统(HNC-21),机床型 号为华中世纪星 21TCK1640 数控车床,功率:4KW,可选用的加工的工件毛坯为Φ60 ×150,高速档为:250~2500r/min,低速档为:75~790r/min。机床精度为 0.001,机床 辅住夹具有顶尖、尾座。
轴类零件数控加工工艺及编程
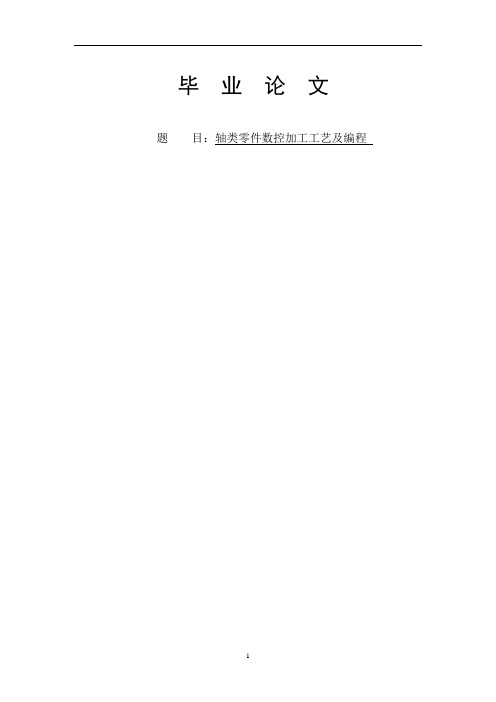
毕业论文题目:轴类零件数控加工工艺及编程轴类零件数控加工工艺及编程摘要:数控机床加工工艺与普通机床加工工艺在原则上基本相同,但数控加工的整个过程是自动进行的。
数控加工的工序内容比普通机床的加工的工序内容复杂,这是因为数控机床价格昂贵,若只加工简单的工序,在经济上不合算,所以在数控机床上通常安排较复杂的工序,甚至是在通用机床上难以完成的那些工序。
数控机床加工程序的编制比普通机床工艺规程编制复杂,这是因为在普通机床的加工工艺中不必考虑的问题,如工序内工步的安排、对刀点、换刀点及走刀路线的确定等问题,在数控加工时,这一切都无例外地都变成了固定的程序内容。
正由于这个特点,促使对加工程序的正确性和合理性要求极高,不能有丝毫的差错,否则加工不出合格的零件。
关键词:轴类零件数控车削工艺设计一、零件加工工艺分析1.零件图分析如图1.1所示该零件从结构上来看包括内﹑外表面:内表面主要是孔,外表面由圆柱、圆锥、顺圆弧、逆圆弧及螺纹等表面组成,其中多个直径以及宽度尺寸有较严格的尺寸精度和表面粗糙度要求,适合数控车削加工;球面Sφ48㎜的尺寸公差还兼有控制该球面形状(线轮廓)误差的作用;零件材料为45钢,该材料具有较高的强度以及较好的韧性﹑塑性;无热处理和硬度要求。
图1.12.工艺分析(1)如图1.1所示内孔直径φ28,圆柱尺寸φ35﹑φ42和φ52,宽度尺寸4和3,取中值作为编程的尺寸依据。
其他尺寸皆取基本尺寸作为编程尺寸依据。
(2)φ52的圆柱与φ28的孔有较高的同轴度要求,加工时必须以同一个定位基准进行加工。
(3)φ28的公差等级为IT8表面粗糙度Ra为1.6,宜采用钻→扩→铰进行加工以保证尺寸和表面粗糙度的要求。
(4)在轮廓曲线上,有三处为圆弧,其中两处为既过象限又改变进给方向的轮廓曲线,因此在加工时应进行机械间隙补偿,以保证轮廓曲线的准确性。
(5)零件中有比较大的圆弧需要进行加工,为了不使加工过程中出现过切现象选择较大副偏角的车刀进行加工。
复合轴类零件的数控加工工艺分析及夹具设计

第1章 绪论
1.1 概述
数控加工,就是泛指在数控机床上进行零件加工的工艺过程。数控机床是一种用计算机来控制的机床,用来控制机床的计算机,不管是专用计算机、还是通用计算机都统称为数控系统。数控机床的运动和辅助动作均受控于数控系统发出的指令[1]。而数控系统的指令是由程序员根据工件的材质、加工要求、机床的特性和系统所规定的指令格式(数控语言或符号)编制的。数控系统根据程序指令向伺服装置和其它功能部件发出运行或终断信息来控制机床的各种运动。利用数控机床加工,其加工产品的质量一致性好,加工精度和效率高,尤其是在复杂的曲线或曲面、多工艺复合化加工和高精度要求的产品加工时,其优点是传统机床无法相比的[2]。
关键词:轴类配合零件;夹具设计;工艺分析;数控仿真
Abstract
NC machining process the design focuses on the composite shaft parts and NC programming. The main task of NC machining process design is to make the process of NC machine tool, but also the preparatory work before. CNC machining program not only process includes the parts, but also including the cutting parameters, tool path, cutting tool size and machining process. The design of NC machining process design and procedures for typical shaft with parts of the. Process design from the beginning of the part drawing, choose CNC equipment, parts of positioning and clamping mode is determined, the reasonable processing plan, dividing the NC machining process, determine the processing procedures, the reasonable selection of tool and tool, fixture design a processing steps, the final determination of machining allowance, finally draw process card, complete process card, and preparation of complete program. Using simulation software to verify the correctness of the program, write the graduation design summary.
典型零件的加工工艺

图4-1
二、轴类零件的材料、毛坯和热处理
• 轴类零件的毛坯常用棒料和锻件。光滑轴、直径相差不大 的非重要阶梯轴宜选用棒料,一般比较重要的轴大都采用 锻件作为毛坯,只有某些大型的、结构复杂的轴采用铸件。 • 根据生产规模的不同,毛坯的锻造方式有自由锻和模锻两 种。中小批生产多采用自由锻,大批大量生产时通常采用 模锻。 • 45钢是轴类零件的常用材料,它价格便宜,经过调质(或 正火)后,可得到较好的切削性能,而且能够获得较高的 强度和韧性,淬火后表面硬度可达45~52HRC。 • 40Cr等合金结构钢适用于中等精度而转速较高的轴类零 件。这类钢经调质和淬火,具有较好的综合力学性能。
3.主轴的检验
• 主轴的最终检验要按一定顺序进 行,先检验各个外圆的尺寸精度、 素线平行度和圆度,再用外观比 较法检验各表面的粗糙度和表面 缺陷,最后再用专用检具检验各 表面之间的位置精度,这样可以 判明和排除不同性质误差之间对 测量精度的干扰。 • 检验前、后支承轴径对公共基准 的同轴度误差,通常采用如图4-6 所示的方法。 • C6150型车床主轴上其他各表面 相对于支承轴径位置精度的检验 常在图4-7所示的专用检具上进行。
6加工方法和加工设备的选择
More to learn
定位基准选择
(1)精基准的选择 精基准选择时应尽量符合“基准重合” 和“基准统一”原则,保证主要加工表面(主要轴径的支 承孔)的加工余量均匀,同时定位基面应形状简单、加工 方便,以保证定位质量和夹紧可靠。此外,精基准的选择 还与生产批量的大小有关。箱体零件典型的定位方案有两 种:
图4-11
(2)粗基准的选择 箱体零件加工面较多,粗基准选择时 主要考虑各加工面能否分配到合理的加工余量,以及加工 面与非加工面之间是否具有准确的相互位置关系。箱体零 件上一般有一个(或几个)主要的大孔,为了保证孔加工 的余量均匀,应以该毛坯孔作为粗基准。箱体零件上的不 加工面以内腔为主,它和加工面之间有一定的相互位置关 系。箱体中往往装有齿轮等传动件,它们与不加工的内壁 之间只有不大的间隙,如果加工出的轴承孔与内腔壁之间 的误差太大,就有可能使齿轮安装时与箱体壁相碰。从这 一要求出发,应选内壁为粗基准,但这将使夹具结构十分 复杂。考虑到铸造时内壁与主要孔都是由同一个泥芯浇铸 的,因此实际生产中常以孔为主要粗基准,限制4个自由 度,而辅之以内腔或其他毛坯孔为次要基准面,以实现完 全定位。
- 1、下载文档前请自行甄别文档内容的完整性,平台不提供额外的编辑、内容补充、找答案等附加服务。
- 2、"仅部分预览"的文档,不可在线预览部分如存在完整性等问题,可反馈申请退款(可完整预览的文档不适用该条件!)。
- 3、如文档侵犯您的权益,请联系客服反馈,我们会尽快为您处理(人工客服工作时间:9:00-18:30)。
目录摘要 (3)绪论 (5)一、选择本课题的目的及意义 (5)二、数控机床及数控技术的应用与发展 (5)(一)数控机床的应用与发展 (5)(二)数控技术的应用与发展 (6)三、对课题任务的阐述 (6)第二章工艺方案分析 (7)2.2零件图分析及毛坯的选择 (7)2.3设备的选择 (8)2.5确定加工方法 (10)2.6确定加工方案 (10)第三章确定零件的定位基准和装夹方式 (12)1.粗基准选择原则 (12)2.精基准选择原则 (12)3.定位基准 (12)4.装夹方式 (12)第四章工艺过程 (13)1.工序与工步的划分 (13)2.工步的划分 (13)第五章确定加工顺序及进给路线 (14)1.零件加工必须遵守的安排原则 (14)2.进给路线 (14)第六章刀具及切削用量的选择 (14)6.1选择数控刀具的原则 (14)6.2选择数控车削用刀具 (15)6.3设置刀点和换刀点 (16)6.4切削用量的选择 (16)1.背吃刀量的选择 (16)选择背吃刀量: (16)2.主轴转速的选择 (17)3.进给量的选取 (17)4.进给速度的选取 (17)7.1轴类零件加工工艺分析 (18)7.2典型轴类零件加工工艺 (20)7.3加工坐标系设置 (21)7.4手工编程 (22)第八章结束语 (25)第九章致谢词 (26)参考文献 (27)摘要数控技术是用数字信息对机械运动和工作过程进行控制的技术,数控装备是以数控技术为代表的新技术对传统制造产业和新兴制造的渗透形成的机电一体化产品,即所谓的数字化装备,数控技术的应用不但给传统制造业带来了革命性的变化,使制造业成为工业化的象征,而且随着数控技术的不断发展和应用领域的扩大,对国计民生的一些重要行业(IT、汽车、医疗、轻工等)的发展起着越来越重要的作用,因为这些行业所需要装备的数字化已是现代发展的大趋势。
而数控加工技术是随着数控机床的产生、发展而逐步完善起来的一种应用技术,是机械制造业人员长期从事数控加工时间的经验总结。
数控加工技术就是用数控机床加工零件的方法。
在数控加工中,利用工件的旋转运动和刀具的直线运动或者曲线运动来改变毛坯的尺寸和形状,把毛坯加工成符合精度要求的零件。
数控车削加工是利用工件相对于刀具的旋转运动对工件进行切削加工的方法。
车削适合加工回转类零件、内外圆锥面、端面、圆弧面、沟槽、螺纹和回转成形面等,所用的刀具主要是车刀。
数控车削加工是现代制造技术的典型代表,在制造业的各个领域得到广泛的应用如航天、汽车、精密机械等。
总之,它是从零件图纸到获得数控加工程序的全过程。
已经成为这些行业不可或缺的加工手段。
关键词:数控技术;车削加工;数控加工工艺;数控编程Abstractnumerical control technology is to use digital information to mechanical motion and working process control technology, numerical control equipment in the numerical control technology, as a representative of the new technology to the traditional manufacturing industry and emerging manufacturing the penetration of the formation of the electromechanical integration products, the so-called digital equipment, not only the numerical control technology application for the traditional manufacturing industry has brought the revolutionary change, make the manufacturing industry to become the symbol of industrialization, and along with numerical control technology unceasing development and application domain expansion, and the people's livelihood of some important industry (IT, automobile, medical, light industry, the development of playing a more and more important role, because these industry need to equip the digitization already is the modern development trends. And the numerical control processing technology is with the generation and development of numerical control machine and improved step by step up an application of the technology, is the mechanical manufacturing personnel engaged in the numerical control processing time of experience. Nc machining technology is to use the method of numerical control machine tool processing components. In the numerical control processing, the use of the rotary motion of the straight-line movement and the cutting tool or curve motion to change the size and shape of the blank, the blank processing in compliance with the requirement of accuracy parts. The numerical control turning processing is to use the rotary motion of the cutting tool relative to the workpiece cutting processing method. Turning back for machining parts, internal and external cone surface and face, circular arc surface, groove, thread and rotary shape face, the use of the cutting tools is mainly lathe tool. The numerical control turning processing is the typical representative of modern manufacturing technology, manufacturing in every field of the widely application such as aerospace, automotive, precision machinery, etc. In short, it is from drawings to get the whole process of nc machining process. The industry has become an indispensable processing method.Key words: the numerical control technology; Turning processing; Numerical control processing technology; CNC programming绪论一、选择本课题的目的及意义目的:通过这次设计可以使我们学会对相关学科中的基本理论、基本知识进行综合运用,同时使对本专业有较完整的、系统的认识,从而达到巩固、扩大、深化所学知识的目的,培养和提高综合分析问题和解决问题的能力,以及培养科学的研究和创造能力。
意义:随着社会经济的快速发展,人们对生活用品的要求也越来越高,企业对生产效率也有相应的提高。
数控机床的出现实现了广大人们的这一愿望。
数控车削加工工艺是实现产品设计、保证产品的质量、保证零件的精度,节约能源、降低消耗的重要手段。
是企业进行生产准备、计划调度、加工操作、安全生产、技术检测和健全劳动组织的重要依据。
也是企业对高品质、高品种、高水平,加速产品更新,提高经济效益的技术保证。
这不但满足了广大消费者的目的,即实现了产品多样化、产品高质量、更新速度快的要求,同时推动了企业的快速发展,提高了企业的生产效率。
机械工业是国民经济各部门的装备军,而数控加工在机械行业占有领头羊的地位,因此国民经济各部门的生产技术水平和所取得的经济效益,在很大程度上取决于机械行业和数控行业中所能提供的机械装备的技术性能、指令和可靠性。
因此数控加工技术水平和生产规模是衡量一个国家科技水平和经济实力的重要标志。
数控工艺规程的编制是直接指导产品或零件制造工艺过程和操作方法的工艺文件,它将直接影响企业产品质量、效益、竞争能力。
本文通过对典型轴类零件数控加工工艺的分析,对零件进行编程加工,给出了对于典型零件数控加工工艺分析的方法,对于提高制造质量、实际生产具有一定的意义。
二、数控机床及数控技术的应用与发展(一)数控机床的应用与发展随着电子信息技术的发展世界机床已经进入了以数字化制造技术为核心的机电一体化时代,其中数控机床就是其代表机床之一。
数控机床是制造业的加工母机和国民经济的重要基础。
随着科学技术不断发展,数控机床的发展也越来越快,数控机床也正朝着高性能、高精度、高速度、高柔性化和模块化方向发展。
我国近几年数控机床虽然发展较快,但与国际先进水平还存在一定的差距,主要表现在:可靠性差,外观质量差,产品开发周期长,应变能力差。