新产品试产及量产导入程序
新产品导入流程[1]
![新产品导入流程[1]](https://img.taocdn.com/s3/m/aaad67e0a48da0116c175f0e7cd184254b351bec.png)
新产品导入流程[1]
1. 工程试作(Engineering Pilot Run:EPR):为确认新产品开发设计成熟度所作的试作与测试。
2. 量产试作(n Pilot Run:PPR):为确认新产品量产时的作业组装所做的试作与测试。
3. 量产(Mass n:MP):经量产试作后之正式生产。
4. 材料清册(Bill of Material:BOM):记录材料料号、品名/规格、插件位置、单位用量、承认编号、工程变更讯息等相关资讯。
5. P3-TEST(LPR阶段):新产品设计完成后,对其设计的结果依据产品规格做各种测试验证,称为P3-TEST。
6. P4-TEST(EPR阶段):通过设计审查后之工程试作后的新产品,对其做各种测试验证称为P4-TEST。
研发单位提供产品及相关资料和样品,文管中心接收并确认资料,工程单位进行PVT资料和相新产品试作,关关设备List指令发出,品保单位进行DVT测试,资材单位备料及试作投料,生产单位支援新产品组装,使用表单及文件记录整个流程。
在试作结束后,需要对试作结果进行分析。
对于不良品,需要进行不良品分析,并提出改善对策。
对于合格品,需要进行PVT检验,并进行结果记录测试验证。
最终,如果可以MP,需要进行量产通知书的发行,并汇总PPR报告,整理后会签,最终发出MP通知。
如果不能MP,需要提出改善对策MP后出货ReworkPPR检讨会,并进行下次PPR决定。
NPI工程师负责全公司工艺技术工作和工艺管理工作,制定工艺技术工作近期和长远发展规划,并制定技术组织措施方案,贯彻国家技术工作方针、政策和公司有关规定。
新产品导入试产流程
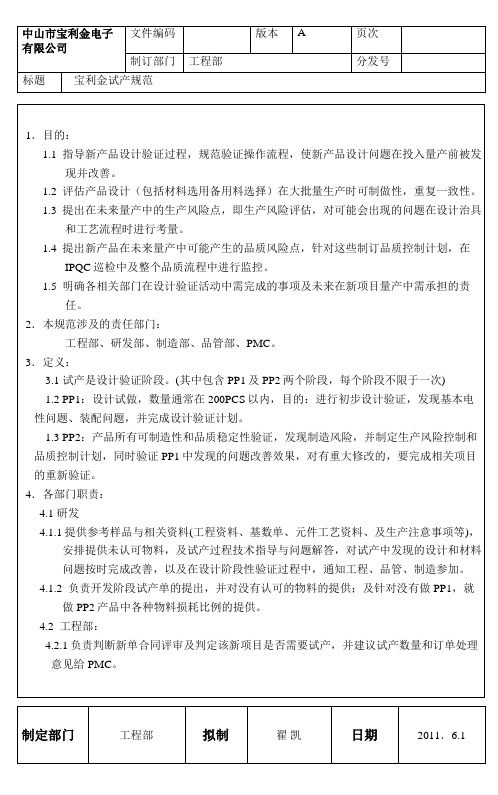
4.2工程部:
4.2.1负责判断新单合同评审及判定该新项目是否需要试产,并建议试产数量和订单处理意见给PMC。
4.2.2依试产需求拟定试产计划,完成试产前物料的确认,负责整个试产过程的统筹与安排,及对外试产事项的窗口。
5.2.3.2试产时,试产负责人安排收集重要参数的测试记录,试产数量100PCS以内要100%记录测试数据,超过100PCS要至少记录100PCS数据,提供给品管人员及设计人员参考分析,设计人员依据测试数据评估设计及修订相关标准,PE做CPK,QE做生产可靠性评估。
5.2.3.3新产品在上线前,研发单位需提供样品及工程资料交给试产负责人及OQC,OQC依工程资料进行出货检验(异常要记录,重大异常要返工,如无异常要在外箱加贴"QC PASS"标记),对在出现的异常,工程部要追溯到问题发生的根本原因,并跟进改善。试产后OQC与工程部需保留一个最新样品。
5.2.4.5试产负责人在完成试产问题检讨后,须对试产进行总结并完成产品试产评估表,
评估及判定Pass标准﹕
(a) .Cpk>1.33﹔
(b).无PCB Layout重大修改﹔
(c).无机构修改,组装方式修改﹔
(d).所有的OPEN ISSUE需全部COLSE
(e).无可靠度问题和安规问题等
(f).直通率需大于95%以上
5.2.4.2试产负责人根据测试数据统计CPK报告,OATL
5.2.4.3工程部要提供生产风险评估表(PFMEA),包含制造风险点、风险等级和处理、预防措施。这些风险点在SOP中一定要有所体现和控制。
5.2.4.4品管要提供品质控制计划,将品质关键点列出来,做出控制计划,做为未来量产的品质控制依据。这些品质控制计划一定要在SOP中体现,并按照SOP执行。
新产品导入流程
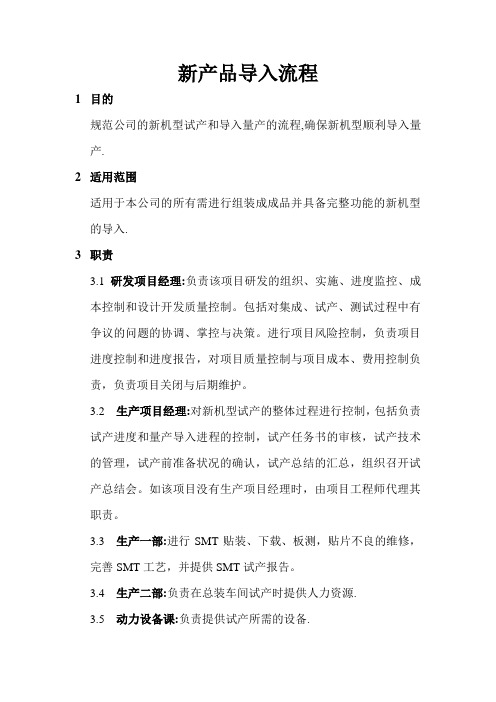
新产品导入流程1目的规范公司的新机型试产和导入量产的流程,确保新机型顺利导入量产.2适用范围适用于本公司的所有需进行组装成成品并具备完整功能的新机型的导入.3职责3.1研发项目经理:负责该项目研发的组织、实施、进度监控、成本控制和设计开发质量控制。
包括对集成、试产、测试过程中有争议的问题的协调、掌控与决策。
进行项目风险控制,负责项目进度控制和进度报告,对项目质量控制与项目成本、费用控制负责,负责项目关闭与后期维护。
3.2 生产项目经理:对新机型试产的整体过程进行控制,包括负责试产进度和量产导入进程的控制,试产任务书的审核,试产技术的管理,试产前准备状况的确认,试产总结的汇总,组织召开试产总结会。
如该项目没有生产项目经理时,由项目工程师代理其职责。
3.3 生产一部:进行SMT贴装、下载、板测,贴片不良的维修,完善SMT工艺,并提供SMT试产报告。
3.4 生产二部:负责在总装车间试产时提供人力资源.3.5 动力设备课:负责提供试产所需的设备.3.6 新产品导入中心:负责项目组织协调,试产组织的按排,产品总装和测试,入网机的准备.3.7 制造工程部:负责生产工艺设计、工艺文件的编制,提供阶段试产总结报告,负责工装夹具的开发与制作。
3.8 自动测试部:负责测试方案的设计、测试软件的开发;负责向生产部门提供测试样机。
3.9 质量管理部:负责制定检验标准,提供试产检验报告,组织试产机型的出货评估。
3.10 中期试验部:负责制定中试标准,确定中试方案,提供中试报告。
3.11 PMC部:按照试产进度制定试产计划,制定物料需求计划并准备由PMC部负责采购试产物料。
3.12 物料供应部、物料开发部:按照物料需求计划进行物料采购。
3.13 来料控制部:负责试产机型物料的来料品质控制。
4 定义集成:新项目在不需要总装或新产品虽经总装但只需要由研发跟进的阶段。
试产:新机型需要完成所有生产过程的阶段。
量产:新机型通过量产转移进入的阶段。
【推荐】新产品试产—量产程序 -范本

新产品试产--量产流程一、样品试产流程(试产样品5套):1.1、由品管部(技术岗)根据产品的设计要求和技术条件,确定《物料清单(试产)》见附表1。
《物料清单(试产)》应注明:品名、规格、型号、参数、封装、厂牌、批次,(有特殊要求需要统一批次的在清单中列明,一般情况下不指定批次)。
编制《物料清单》应考虑公司原有物料品种、方便采购。
1.2、采购部严格按照《物料清单(试产)》的要求,进行原材料采购。
同时做好合格供应商调查及筛选,为以后大批量采购做好准备。
如采购中发生与《物料清单(试产)》不匹配的情况,应填写《内部工作联系单》征得技术岗同意后方可采购。
对于特殊原材料采购,如PCB板材,采购岗采购PCB下单前应请供应商将PCB图纸发回由技术岗进行确认后方可采购。
采购部注明预计采购时间并通报技术岗。
1.3、原材料检验确认:仓库管理员根据《物料清单(试产)》负责对采购物品进行核对,核对无误后交技术岗对采购物品性能进行审核(进仓检验)。
如性能不符,由技术岗向采购岗填写《内部工作联系单》,列明不符合项目和要求,由采购部负责退换或另行采购。
外协加工原材料出仓前由仓管进行核对技术部进行签字确认后方可发货。
如符合,进入下一制作样品环节。
1.4、技术部制作样品。
完成样品制作后技术部岗进行技术测试。
1.5、样品确认:样品测试完成后,技术岗通知行政部。
由行政部组织“产品评审小组”确认。
(产品评审小组由总经理,品管部、仓管岗、市场部、生产部、采购岗、行政部各部门负责人组成)如样品在评审过程中有重大改动的,则重新进行样品制作及评审确认工作。
二、试产流程(50套):2.1、采购岗负责原材料采购。
2.2、仓库根据采购清单对原材料检验确认(核对品名、规格、型号、参数、封装、厂牌、批次)。
核对无误后交由技术岗进行原材料性能测试(进仓检验)。
如性能不符,由技术岗向采购岗填写《内部工作联系单》提出不符合项,由采购部负责退换或另行采购。
2.3生产:由技术岗起草《产品技术要求》、《生产工艺》,由生产部制定《作业指导书》,技术岗审核无误后两部门负责人签字。
新产品导入量产作业程序(含表格)

为确保新产品顺利导入量产阶段,能提供正确完整的技术文件资料及验证新产品的成熟度,以顺利大量生产。
1.1 明确并规范新产品样板生产制作和新产品小批量试产过程中各部门职责和范围;1.2 使各部门在样板生产制作和小批量试产过程中作业有章可循,有据可依。
2、范围:适用于公司所有新产品在生产导入的全过程。
3、定义:3.1 新产品:采用新方案,新技术从无到有的产品或我公司无相关电气规格或类似机构尺寸的产品;3.2 改良品:在已有产品基础上,在不影响产品主要机构尺寸与电气性能的前提下,通过对产品部分结构、制作工艺以及原材料性能的改善来提升产品可靠性或降低制造成本的产品;3.3 延伸品:在已有产品基础上,因应客户/市场需求而变动电气规格(加严或放宽)或脚位及材料修改等因素而产生的产品;4、职责:4.1 研发部 -4.1.1提供新品试产的技术参数要求及测试标准和方法。
4.1.2提供新产品工程样机和相关文件4.1.3协助解决试产中发现的设计性问题4.2 工程部 -4.2.1承接新产品技术及资料,根据产品特性评估可生产性。
4.2.2根据计划召集人排定工程试制时程表及召开工程试制检讨会,工程问题分析,对策导入。
4.2.3制程安排,包括生产线的评估,SOP制作与发行;治工具的准备、制程管制、机器设备架设、参数设定及问题分析等。
4.2.4规划新产品之测试策略、测试设备、软体。
4.3 品保部 -4.3.1制作控制计划(CP)及检验作业指导书(SIP)及进料检验抽样计划;出货检验抽样计划。
4.3.2再次确认可靠性测试和产品设计验证测试的结果是否符合工程规格及客户规格。
4.3.3首件检查,并生成《首件检查报告》4.3.4监督生产文件、工程文件、客户资料的落实及执行。
4.3.5来料检验和协助处理小批量试产过程中因物料不良引起的问题。
4.4 生产部 -4.4.1样板和小批量试产执行、物料准备、成品和半成品入库4.4.2样板制作、试产执行和异常反馈并记录4.4.3生产作业人员教育、培训、考核4.4.4生产资料及文件接收并执行(SOP、流程图、车间规划图、SIP、设备操作规范、包装规范等)4.5 资材部(生管/仓库) -4.5.1负责试产计划及量产计划4.5.2根据《试样试产通知单》制定并落实生产计划,并开具《物料套(领) 料单》给仓库和生产备料4.5.3确认物料库存状态,对缺料部分及时释放《物料需求计划》4.5.4跟进物料交期和及时反馈相关问题4.5.5仓库 - 负责试产物料的接收和发放、半成品和成品的入库接收。
NPI新产品导入控制流程
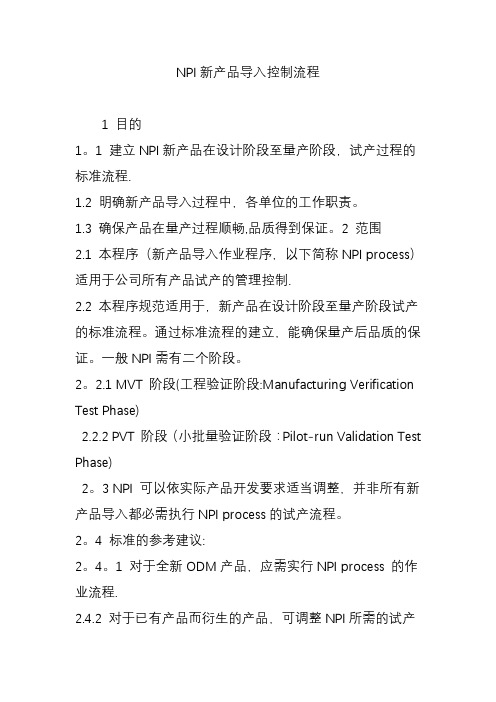
NPI新产品导入控制流程1 目的1。
1 建立NPI新产品在设计阶段至量产阶段,试产过程的标准流程.1.2 明确新产品导入过程中,各单位的工作职责。
1.3 确保产品在量产过程顺畅,品质得到保证。
2 范围2.1 本程序(新产品导入作业程序,以下简称NPI process)适用于公司所有产品试产的管理控制.2.2 本程序规范适用于,新产品在设计阶段至量产阶段试产的标准流程。
通过标准流程的建立,能确保量产后品质的保证。
一般NPI需有二个阶段。
2。
2.1 MVT 阶段(工程验证阶段:Manufacturing Verification Test Phase)2.2.2 PVT 阶段(小批量验证阶段:Pilot-run Validation Test Phase)2。
3 NPI 可以依实际产品开发要求适当调整,并非所有新产品导入都必需执行NPI process的试产流程。
2。
4 标准的参考建议:2。
4。
1 对于全新ODM产品,应需实行NPI process 的作业流程.2.4.2 对于已有产品而衍生的产品,可调整NPI所需的试产流程并确实执行。
NPI新产品导入3权责3.1 (产品中心)PM3.1。
1 负责提供需要试产产品的样机和整套的开发文件. 3.1。
2 负责主导试产阶段前所有工作,及试产工作交接。
3.2 (文控中心)DCC负责开发文件的发放,登记,回收和管制工作,保证文件的准确性和有效性。
3。
3 (工程)ENG3.3。
1 负责可制造性评估,工艺文件制作,确认生产layout,确定试产方案。
3.3。
2 主导PFMEA制定,及改善跟进。
3.3.3 负责测试治具制作,生产设备调试。
3.3.4 负责Test程式调试及Test设备架设,测试文件,数据提供。
3.3.5 试产成本统计与分析3.4 (品管)QA3。
4.1 试产所需的物料品质状况的检验。
3.4.2 检验试产过程中的产品质量控制状况.3.4。
3 试产产品的验证、出货检验控制和中试认证安排。
新产品导入流程
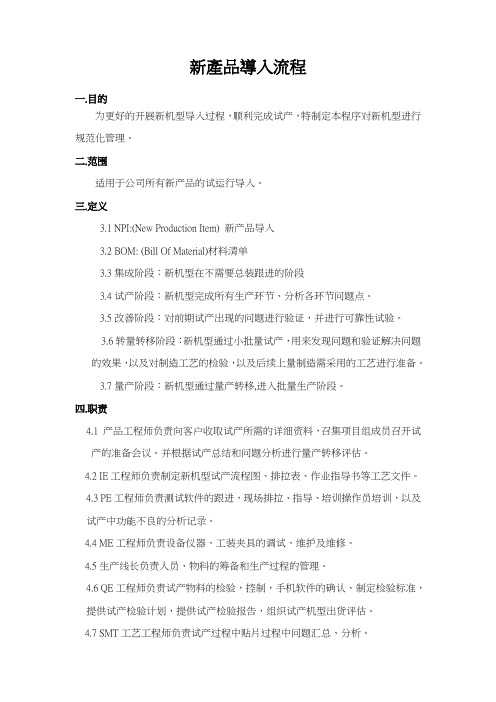
新產品導入流程一.目的为更好的开展新机型导入过程,顺利完成试产,特制定本程序对新机型进行规范化管理。
二.范围适用于公司所有新产品的试运行导入。
三.定义3.1 NPI:(New Production Item) 新产品导入3.2 BOM: (Bill Of Material)材料清单3.3集成阶段:新机型在不需要总装跟进的阶段3.4试产阶段:新机型完成所有生产环节、分析各环节问题点。
3.5改善阶段:对前期试产出现的问题进行验证,并进行可靠性试验。
3.6转量转移阶段:新机型通过小批量试产,用来发现问题和验证解决问题的效果,以及对制造工艺的检验,以及后续上量制造需采用的工艺进行准备。
3.7量产阶段:新机型通过量产转移,进入批量生产阶段。
四.职责4.1 产品工程师负责向客户收取试产所需的详细资料,召集项目组成员召开试产的准备会议。
并根据试产总结和问题分析进行量产转移评估。
4.2 IE工程师负责制定新机型试产流程图、排拉表、作业指导书等工艺文件。
4.3 PE工程师负责测试软件的跟进,现场排拉、指导、培训操作员培训,以及试产中功能不良的分析记录。
4.4 ME工程师负责设备仪器、工装夹具的调试、维护及维修。
4.5生产线长负责人员、物料的筹备和生产过程的管理。
4.6 QE工程师负责试产物料的检验,控制,手机软件的确认、制定检验标准,提供试产检验计划,提供试产检验报告,组织试产机型出货评估。
4.7 SMT工艺工程师负责试产过程中贴片过程中问题汇总、分析。
4.8 文控中心负责向工程部领取试产资料及相关文件。
4.9样机保管员负责对试产所需的工程、工艺、测试等样机的领取和管理。
五.工作程序5.1 新机型导入阶段分为集成阶段、试产阶段、改善阶段、量产转移阶段。
5.2 集成阶段5.2.1 SMT工程师根据工程部输出的钢网文件进行确认,指导钢网的制作。
5.2.2 SMT工程师根据工程部输出的坐标文件、BOM、拼板图、丝印图、ECO等文件,跟进新机型主板贴片,并填写《主板贴片试制报告》,反馈到产品工程师。
新产品导入量产作业流程

VOID IF NOT STAMPED不盖章无效文件编号页次版本/修订号A/0生效日期条款号一目的。
为确保新产品顺利导入量产阶段,能提供正确完整的技术文件资料及验证新产品的成熟度,以顺利大量生产。
二组织与权责。
1 研发单位:对策分析与设计变更,提供样品及技术相关文件资料及零件采购资料。
2 工程单位:(1)承接新产品技术,产品特性及生产作业性评估。
(2)任计划召集人(Project Coordinator)排定工程试制时程表及召开工程试制检讨会,工程问题分析,对策导入。
(3)制程安排,包括生产线的评估,绘制SOP,QC工程图之草拟。
同时,还有负责治具的准备,制程管制,机器设备架设,参数设定及问题分析等。
(4)规划新产品之测试策略,测试设备,治具及软体。
还有负责生产线测试设备的架设,提供测试SOP,测试计划及测试产出分析。
3 品保单位。
VOID IF NOT STAMPED不盖章无效文件编号页次版本/修订号A/0生效日期条款号(1)产品设计验证测试(Design Verification:DVT)。
(2)功能及可靠度确认。
(3)负责再次确认PVT和DVT的结果是否符合工程规格及客户规格。
4 资材单位:(1) PCB委托加工及材料采购。
(2)备料及试作投料。
5 生产单位:(1)支援新产品组装。
(2)成品接受及制造技术接受。
6 文管中心:DVT资料接收确认与管制。
三名词解释。
VOID IF NOT STAMPED不盖章无效文件编号页次版本/修订号A/0生效日期条款号1 工程试作(Engineering Pilot Run:EPR):为确认新产品开发设计成熟度所作的试作与测试。
2 量产试作(Production Pilot Run:PPR):为确认新产品量产时的作业组装所做的试作与测试。
3 量产(Mass Production:MP):经量产试作后之正式生产。
4 材料清册(Bill of Material:BOM):记录材料料号,品名/规格,插件位置,单位用量,承认编号,工程变更讯息等相关资讯。
品质管理系统之新产品导入与量产移转控制程序

1.目的对产品的样品订单、中试阶段转入量产阶段产品的过程控制,确保产品能满足顾客的需求及有关法律,法规要求。
2.范围规范样品订单、代工类项目、新增产品型号项目、技术或工艺基础研究类项目、均适用本程序。
3.术语及定义3.1产品项目类型定义3.1.1 新产品:现有成熟产品设计和工艺平台中没有的产品。
3.1.2 新增产品型号:与现有生产线上产品设计和工艺平台相同或类似,仅仅尺寸不同的产品。
3.1.3代工产品:按客户要求执行。
3.1.4其他类:不属于以上性质的技术或工艺基础研究类项目,需要实施时,按照《工程变更控制程序》导入和执行。
3.2 样品订单:公司接到订单时被客户或者销售指定为样品订单。
3.3 中试过程阶段(PVT):小批量过程验证及测试,验证产品工艺稳定性、产品可靠性和产品可生产性。
3.4 量产阶段(MP):量产阶段,产品开始批量生产。
4.职责4.1 业务部:4.1.1 主导样品订单的执行流程。
4.1.2 负责给客户样品送样及确认客户使用情况反馈。
4.1.3 主导小批量订单评审。
4.1.4 参与各阶段转移阶段评审。
4.2 工程部(产品经理/项目经理/项目主管)4.2.1 产品样品及中试阶段与市场/业务部一起进行的客户必要沟通。
4.2.2 主导将产品成功地转入到量产阶段的过程。
4.2.3 审核本程序执行过程中要求的文件。
4.2.4 按要求提交有关的设计文档给DCC。
4.3 生产工程部(经理/主管):4.3.1 主导产品中试过程。
4.3.2 负责将中试产品导入到生产现场,主导和协调产线产品引进活动。
4.3.3 负责产品中试过程中的过程开发和改进,新产品试产的准备,以及产品线提供技术支持。
4.3.4 负责生产用工装夹具及过程能力和直通率的管理和持续改善。
4.3.5 负责物料及供应商的验证,主导新产品PFMEA的制定。
4.3.6 负责样品正式确认后,负责产品相关文件编写。
4.3.7 参与转移阶段评审(PVT,MP)。
工厂端新产品导入流程
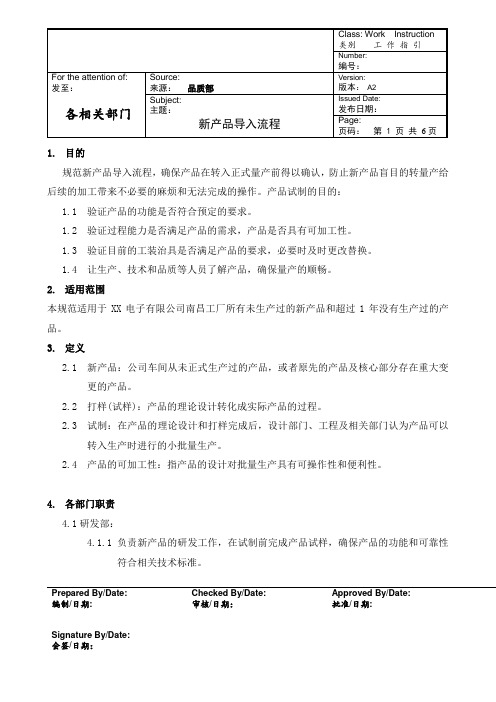
Prepared By/Date: 编制/日期: Signature By/Date: 会签/日期:Checked By/Date:审核/日期:Approved By/Date:批准/日期:1.目的规范新产品导入流程,确保产品在转入正式量产前得以确认,防止新产品盲目的转量产给后续的加工带来不必要的麻烦和无法完成的操作。
产品试制的目的:1.1 验证产品的功能是否符合预定的要求。
1.2 验证过程能力是否满足产品的需求,产品是否具有可加工性。
1.3 验证目前的工装治具是否满足产品的要求,必要时及时更改替换。
1.4 让生产、技术和品质等人员了解产品,确保量产的顺畅。
2.适用范围本规范适用于XX电子有限公司南昌工厂所有未生产过的新产品和超过1年没有生产过的产品。
3.定义2.1 新产品:公司车间从未正式生产过的产品,或者原先的产品及核心部分存在重大变更的产品。
2.2 打样(试样):产品的理论设计转化成实际产品的过程。
2.3 试制:在产品的理论设计和打样完成后,设计部门、工程及相关部门认为产品可以转入生产时进行的小批量生产。
2.4 产品的可加工性:指产品的设计对批量生产具有可操作性和便利性。
4.各部门职责4.1研发部:4.1.1负责新产品的研发工作,在试制前完成产品试样,确保产品的功能和可靠性符合相关技术标准。
4.1.2 提出试制需求及下发产品的相关技术资料(包含BOM清单、规格书、工艺技术说明、测试指导、测试工装的设计等)、主要物料验收标准、成品验收标准,并提供产品的样机且指导试制。
4.1.3 负责新产品试制过程中设计问题的更改。
4.1.4 协助产品功能维修过程中疑难问题的解决。
4.2合同管理部/销售部:4.2.1作为客户订单的接口部门,沟通确认客户新产品在何种状态,负责协调客户新产品导入工作,并填写《新产品合同评审表》给相关部门。
4.2.2 协调新产品导入过程中疑难问题的解决。
4.3采购部:4.3.1 对于自购料产品,负责试制产品物料的配备,并及时与技术部门沟通有关材料事宜,确保按计划采购到位。
新产品试产及量产导入程序

新产品试产及量产导入程序编制:审核:批准:生效日期:受控标识处:分发号:1.0 目(de)1.1为了能更有效(de)控制新产品(de)生产质量,确保工程文件、客供资料,能准确、及时(de)转化为生产文件,以验证和确认新产品是否适合批量生产;1.2确保问题点能在放产前被发现、处理或提供良好(de)预防措施,保证新产品顺利(de)投入生产.1.3明确并规范新产品样板生产制作和新产品小批量试产过程中各部门职责和范围;1.4使各部门在样板生产制作和小批量试产过程中作业有章可循,有据可依.2.0范围2.1本规范适用于本公司公司汽车零部件小批量试产作业和新产品导入.2.2流程(de)起点为PMC发布(de)小批量试产(新产品导入)任务令,流程(de)终点为产品大规模量产.3.0职责3.1技术部:3.1.1有责任联络客户提供BOMList、包装检验通知单(或包装指引)、配色图、软件发放通知单、PO单、软件、软件平台、工程样机、升级数据线、测试工具等. 3.1.2生管根据小批量试产通知制定并落实生产计划.并开具物料套(领)料单给仓库和生产备料3.1.3物控确认物料库存状态,对缺料部分及时释放物料需求计划.3.1.4跟进物料交期和及时反馈相关问题.3.1.5仓库组负责试产物料(de)接收和发放、半成品和成品(de)入库接收3.2工程部:3.2.1有责任根据业务部或PMC提供(de)文件,编制ProductionFlowChart、生产排位图、SOP、生产注意事项等文件;3.2.2负责制作工装夹具、准备生产所需(de)仪器仪表和工具;3.2.3负责生产线体设备设施架设和调试,负责生产工艺(de)安排和作业人员(de)培训指导;3.2.4负责试产过程中不良品(de)统一维修分析,并提供详细分析报告.3.2.5试产过程中(de)制程技术支持,对产品工艺(de)可制造性进行验证.3.3生产部:3.3.1有责任根据工程部提供(de)SOP、FlowChart进行排拉、组织生产.3.3.2小批量试产执行、物料准备、成品和半成品入库;3.3.3样板制作、试产执行和异常反馈并记录;3.3.4生产组作业人员教育和培训;3.4品质部3.4.1负责记录并监控试产中之品质状况,负责收集并分析试产记录及相关资料,并生成小批量试产品质报表3.4.2负责首件检查,并生成首件检查报告.3.4.3负责监督生产文件、工程文件、客供资料(de)落实和执行.4.0定义4.1新产品4.1.1公司以前未生产(de)产品,包括以下两种:4.1.2新规格品:对成熟方案做适当调整(de)产品4.1.3全新产品:采用新方案,新技术从无到有(de)产品4.2试产4.2.1指新产品在正式生产前为验证其生产工艺和产品(de)可靠性所进行(de)小批量生产,其数量为30-100PCS之间.4.2.2对某些不常用机型,一般只做研发需求(de)数量.4.3评审为了评价作业满足质量要求(de)能力,对作业所做(de)综合(de)、有系统(de)形成文件(de)检查,给出明确(de)通过或不通过(de)结论.参考管理评审控制程序4.4新产品说明会为促进全新产品在试产时(de)顺利进行,由工程部NPI工程师召开(de)会议.会议主要包括:产品结构、产品工艺流程、重要作业方法及检测方法等(de)介绍,同时NPI工程师将对试产作整体规划和要求.并将会议结果列入会议记录中,会议所记录各事项由NPI工程师跟进.会议记录由NPI负责发给相关人员.4.5试产评审会议试产结束后,由NPI工程师召开(de)会议,项目经理、研发工程师、品质部、和生产部、工程部就试产中(de)问题做出一一解决方案.由NPI跟进问题直至解决,并在会议中做出该次小批量试产是否通过(de)决定.会议记录由NPI负责发给相关人员.4.6试产样机由客户或研发部提供(de)试产用其标签并加盖了试产专用章(de)样机(数量为3台,一台交品质部作试产检验依据,一套用来做夹具,另一套用来制作SOP).4.7输入/输入物为完成相关(de)阶段、步骤、任务所必须先行取得并进行了解、参照、分析考虑或作为工作依据(de)信息、文档或数据(如:BOM、ECN、ID、MD、Software).4.8输出/输出物阶段、步骤、任务(de)可检验(de)成果,如文档(SOP、评审报告)、实物(限度样板)等,作为阶段工作完成标志.4.9缓冲时间指下个节点或任务(de)作业指导时间,包括任务作业所需时间和因其它工作正在进行所需(de)过度时间.作为引起冲突时(de)衡量标准.5.0程序5.1工程部根据业务部或PMC提供(de)工程资料如:BOMList、包装检验通知单(或包装指引)、配色图、软件发放通知单、PO单、软件、软件平台、工程样机等,对以上资料进行分析和样机(de)拆装,对产品工艺流程进行设计,依照<<生产计划>>(de)进度安排,按时制作生产文件和工装夹具.5.2工程部根据业务部或PMC提供(de)客供资料及工程样机编写产品流程图<<ProductionFlowChart>>.5.3根据ProductionFlowChart设计出一条生产线,生产线(de)设计一般按以下步骤:5.4.1根据ProductionFlowChart计算单工序标准时间.5.4.2根据单工序标准时间计算出单部机标准时间,根据实际人手计算出每小时(de)产量.5.4.3根据产量大小计算拉线(de)长度,工作台数等.5.4.4根据物料(de)特性和要求及工艺要求选用工具.5.5根据生产流程图编写<<StandardOperatingProcedure>>.5.5.1制作每个工位(de)操作指导书:对每个工位(de)工位名称,工位时间,静电防护,工作内容,工夹具和辅材料等进行文字描述.要求内容通俗易懂,文字简练,需要时用图片进行说明.5.6生产线依据SOP、工程样机和生产注意事项,使用新产品套料,进行组装生产,品质和工程在开始生产半小时内,依据BOMList、包装检验通知单(或包装指引)、配色图、软件发放通知单、PO单、工程样机,检验首件是否正确,并由品质、工程、客户在首件单上签名确认;5.7.1烙铁温度(de)制定:5.7.1.1根据组件Specification要求制定烙铁温度,(测量工具:温度测量仪)5.7.2电批磅力(de)制定5.7.2.1根据工程部提供(de)塑料件(de)材料及螺丝Specification要求,用扭力批经过多次试装来制定电批磅力.(测量工具:扭力批,电批测量仪)5.7.3辅料(de)制定:5.7.3.1根据产品(de)品质要求选择辅料5.7.3.2了解辅料Specification,然后在经过实验证明该辅料对该产品不会造成品质上(de)缺陷.5.7.3.3根据生产计划须要测量出每种辅料(de)用量.5.8生产问题总结5.8.1工程部在新产品顺利量产后,依据生产测试报表、修理报表、品质异常联络单等,制作生产问题总结报告,并召集、主持生产问题总结会议,形成本次生产相关问题(de)最终决议存档.。
新产品导入量产作业流程
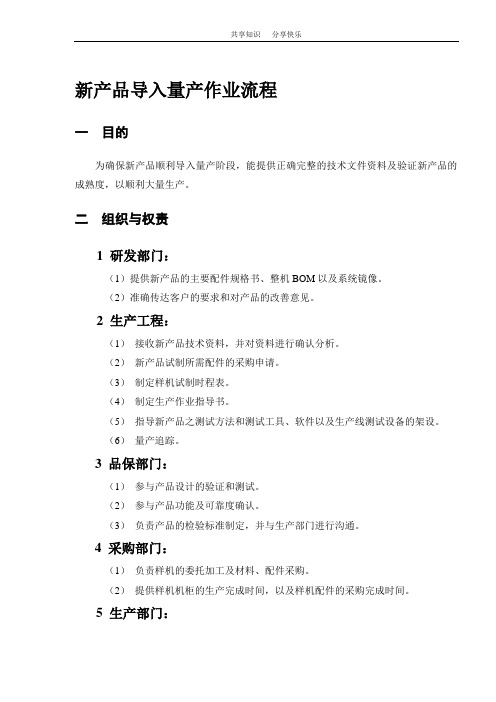
新产品导入量产作业流程一目的为确保新产品顺利导入量产阶段,能提供正确完整的技术文件资料及验证新产品的成熟度,以顺利大量生产。
二组织与权责1 研发部门:(1)提供新产品的主要配件规格书、整机BOM以及系统镜像。
(2)准确传达客户的要求和对产品的改善意见。
2 生产工程:(1)接收新产品技术资料,并对资料进行确认分析。
(2)新产品试制所需配件的采购申请。
(3)制定样机试制时程表。
(4)制定生产作业指导书。
(5)指导新产品之测试方法和测试工具、软件以及生产线测试设备的架设。
(6)量产追踪。
3 品保部门:(1)参与产品设计的验证和测试。
(2)参与产品功能及可靠度确认。
(3)负责产品的检验标准制定,并与生产部门进行沟通。
4 采购部门:(1)负责样机的委托加工及材料、配件采购。
(2)提供样机机柜的生产完成时间,以及样机配件的采购完成时间。
5 生产部门:(1)支援新产品组装。
(2)成品接受及制造技术接受。
三文档与资料要求1 研发部门(1)研发部门需提供给生产工程人员的配件资料包含主要配件的规格书、使用说明书以及产品BOM表。
(2)产品装配完成之后研发部门负责完成系统镜像的制作,并提交给质检验证。
(3)在评审通过之后研发部门发出量产通知书,生产部门接到量产通知后方可进行量产。
2 生产工程(1)生产工程人员在接收到研发部门提供的配件资料之后把配件的规格、尺寸整理总结出来,提交配件详细说明表格提叫给工艺人员协助设计工作。
(2)生产工程人员在确认完成研发部门的产品相关资料准确无误之后,需要与各个部门沟通提交一份以甘特图形式的试制计划表。
同时知会各个部门各阶段需要完成的任务。
(3)产品设计人员在接到生产工程人员的配件规格表之后开始进行设计,设计完成与研发部门沟通确认。
完成之后提交产品钣金件和装配辅料统计表格。
(4)收到产品设计人员的产品钣金件和装配辅料统计表之后,生产工程人员对产品的BOM进行完善,并提交生产使用的详细BOM。
NPI新产品导入量产作业流程—范文

NPI 新产品导入量产作业流程—范文一目的。
为了规范新产品试产工作管理,增强新产品导入工作的过程控制能力,提供正确完整的技术文件资料及验证新产品的可制造性(DFM)、可测试性(DFT),以确保顺利导入量产。
二范围适用于公司所有新产品在生产导入的全过程。
三组织与权责。
1 研发部:对策分析与设计变更,提供样品及技术(协调研发硬件/ 软件部门明确及发放新产品有关设计资料(BOM/GERBEF光板/线路图/烧录软件/测试软件/测试方法/结构图/包装图/1 台以上的研发样机等);零部件承样书。
2 中试部:(1)承接新产品技术及资料,根据产品特性评估可生产性。
(2)参加”新产品准备会议”,对新产品是否满足试产条件进行评估;并填写《试产前准备工作检查表》。
根据填检实际情况并给出中试生产计划。
(3)制程安排,包括生产线的评估,绘制SOP流程图之草拟(4)规划新产品之测试方案,测试设备清单,测试架构,治具及软体。
还有负责生产线测试设备的架设,提供测试SOP。
(5)组织相关人员对试产过程进行跟线,对试产产品在线生产的整个过程进行组织并协调,统计、反馈、跟踪解决试产发现的各类问题,达到试产目的。
(6)召集召开“新产品试产总结会议” ,汇总试产过程中的技术、工艺问题,并分析、总结,出具《试产问题总结报告》,逐步减少试产问题,评估是否可以进入批量生产。
3 质量部。
(1)产品设计验证测试(Design Verification Tes:t DVT)。
(2)功能及可靠度确认。
(3)负责再次确认PVT和DVT的结果是否符合工程规格及客户规格。
4 生产计划:(1)PCB委托加工及材料采购。
(2)生产备料5 生产执行单位:(1 )新产品生产。
(2)产品技术资料承接及消化。
6 文控中心:资料接收发放与管制。
四名词解释1 工程试作(Engineering Pilot Run:EPR):为确认新产品开发设计成熟度所作的试作与测试。
2 小批量试制(Production Pilot Run:试制):为确认新产品量产时的作业组装所做的试作与测试。
新产品导入管理程序

编制:
审核:
批准:
序号
修改日期
修订内容
版次
修订人
审核人
批准人
为了规范新产品从订单接收、模具开发设计、打样、试产及向量产转移各阶段的管控流程,明确各部门职责和权限,确保公司新产品顺利导入量产阶段,满足客户要求。
适用于本公司新产品从订单接收到样品完成转量产的全过程。
3.术语
PMC:生产及物料控制。
6.6.2 SMT:工艺工程根据客户提供的《BOM表》、《GERBER文件》、《贴片CAD文件》作成相关SOP、贴片程序、治工具、料站表等。
6.7 项目评审
6.7.1项目部组织模具、PMC、品质、采购、注塑、SMT等部门召开项目评审会议
6.7.2评审有疑问,则由项目总结相关问题点继续跟客户沟通,直至问题解决
4.8.3对供应商进行品质管理,跟进供应商对异常物料处理,负责推动供应商进行品质改善。
主导
部门
执行
部门
流程图
输出相关文件/记录
业务部
《市场信息输入表》
项目部
《项目管理表》
业务部
《合同评审记录》
业务部
《产品报价单》
业务部
《合同审批记录》OA流程
项目部
《BOM清单》
项目部
SMT
《项目计划进度表》--模具/注塑
6.10 试模/试产
6.10.1试模(模具注塑):项目部填写《试模申请单》给到注塑部,由注塑部安排机台进行试模打样,并输出《试模报告》。具体流程参考《工装模具管理程序》。根据试模打样结果,相关部门输出相应的SOP、SIP、PDS、POP。
6.10.2试产(SMT):SMT工艺工程现场异常确认,不良信息收集、记录。并形成《SMT试产确认总结报告》。根据试产结果,相关部门输出相应的SOP、SIP、POP。
新产品导入试产流程
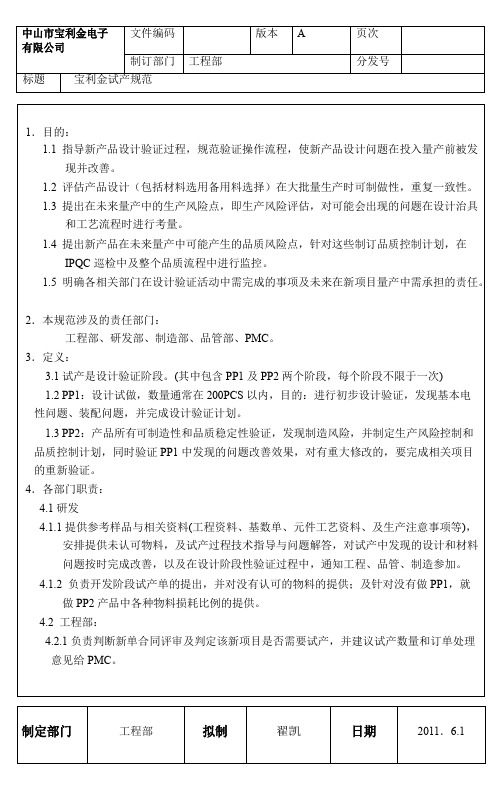
4.2工程部:
4.2.1负责判断新单合同评审及判定该新项目是否需要试产,并建议试产数量和订单处理
意见给PMC。
制定部门工程部拟制翟凯日期2011.6.1
中山市宝利金电子
有限公司
文件编码
版本
A
页次
制订部门
工程部
分发号
标题
宝利金试产规范
4.2.2依试产需求拟定试产计划,完成试产前物料的确认,负责整个试产过程的统筹与安
抽检并盖品管“PASS”章才可以出货。
4.1研发
4.1.1提供参考样品与相关资料(工程资料、基数单、元件工艺资料、及生产注意事项等),
安排提供未认可物料,及试产过程技术指导与问题解答,对试产中发现的设计和材料
问题按时完成改善,以及在设计阶段性验证过程中,通知工程、品管、制造参加。
4.1.2负责开发阶段试产单的提出,并对没有认可的物料的提供;及针对没有做PP1,就
机种流程。
4.6ME:ME负责对加工/组装等工装夹具的需求进行评估及制作,并完成试产及生产用
治/夹具的制作与改良,测试治具由PE评估提出申请并提供原理图,IE及PE需对所
有治/夹/测具的使用状况进行确认,对有影响效率及品质的项点提出修改。
4.7各制造单位:加工组、引线加工、老化房及其他被要求的单位,需积极配合完成一些
中山市宝利金电子
有限公司
文件编码
版本
A
页次
制订部门
工程部
分发号
标题
宝利金试产规范
1.目的:
1.1指导新产品设计验证过程,规范验证操作流程,使新产品设计问题在投入量产前被发
现并改善。
1.2评估产品设计(包括材料选用备用料选择)在大批量生产时可制做性,重复一致性。
新产品导入流程

新产品导⼊流程⽂件编号 : ⽂件名称 : 新产品导⼊流程确保新产品⽣产符合客户要求,并在新产品⽣产过程中发现和解决在批量⽣产中可能出现的问题,为批量⽣产顺利进⾏做准备。
⼆、适⽤范围公司所有新产品的试产(除笔记本产品)三、定义3.1 NPI:New Product Introduction(新产品导⼊)3.2新产品:它⾄少具有如下之⼀的特征:1、产品体系架构、应⽤模式有较⼤变化,为新概念产品或换代产品2、产品机构及外观变化较⼤3、其他较重要、投⼊资源多的产品4、客户要求以新品实施的产品3.3 新产品分类A类:新开发(⽅案.平台)或之前从未⽣产之产品B类:结构或电⼦⽅⾯有变更或重新设计更改之产品C类:验证物料及重新更换丝印、外观(或按键)之产品D类:结构或电⼦及包装⽅式⽆任何变动只更改软件之产品3.4 新品导⼊阶段:EVT:Engineer Verification Test,⼯程样品验证测试DVT:Design Verification Test,设计验证测试PVT:Process Verification Test,⼩批量过程验证测试四、职责4.1 项⽬PE:负责主导新产品在⼯⼚端开始导⼊到新机种⾸次量产顺利结束的所有项⽬相关事项异常的处理、协调、进度掌控及试产总结报告的完成。
4.2 IQC:负责试产来料检验,保存好各种试产料件的样品,同时负责主导来料料件异常处理;并对试产过程中的来料异常在量产时重点监控。
4.3 试产⼩组:负责新品试产除SMT制程外的⽣产全过程,及时反馈试产状况和问题点,协助项⽬PE达成试产出货计划,主导试产⼯单的⼯单结案。
4.4 QE:负责新品试产过程中的品质管控,与客户确定产品品质标准并依据标准制作品质检验指导书,统计良率状况并主导解决试产过程中的来料异常。
跟进试产问题点的改善落实进度并裁决新产品能否允许进⼊下⼀阶段。
如是试产光电产品时还必须输出实验室的相关测试⽂件。
4.5 Purchase(采购):负责寻找新产品材料供应商,采购新产品材料并建⽴合作关系。
- 1、下载文档前请自行甄别文档内容的完整性,平台不提供额外的编辑、内容补充、找答案等附加服务。
- 2、"仅部分预览"的文档,不可在线预览部分如存在完整性等问题,可反馈申请退款(可完整预览的文档不适用该条件!)。
- 3、如文档侵犯您的权益,请联系客服反馈,我们会尽快为您处理(人工客服工作时间:9:00-18:30)。
新产品试产及量产导入
程序
集团标准化小组:[VVOPPT-JOPP28-JPPTL98-LOPPNN]
新产品试产及量产导入程序
编制:
审核:
批准:
生效日期:
受控标识处:
分发号:
1.0?目的
1.1为了能更有效的控制新产品的生产质量,确保工程文件、客供资料,能准确、及时的转化为生产文件,以验证和确认新产品是否适合批量生产;
1.2确保问题点能在放产前被发现、处理或提供良好的预防措施,保证新产品顺利的投入生产。
1.3明确并规范新产品样板生产制作和新产品小批量试产过程中各部门职责和范围;
1.4使各部门在样板生产制作和小批量试产过程中作业有章可循,有据可依。
2.0范围
2.1本规范适用于本公司公司汽车零部件小批量试产作业和新产品导入。
2.2流程的起点为PMC发布的小批量试产(新产品导入)任务令,流程的终点为产品大规模量产。
3.0职责
3.1技术部:
3.1.1有责任联络客户提供BOMList、包装检验通知单(或包装指引)、配色图、软件发放通知单、PO单、软件、软件平台、工程样机、升级数据线、测试工具等.
3.1.2生管根据《小批量试产通知》制定并落实生产计划。
并开具《物料套(领)料单》给仓库和生产备料
3.1.3物控确认物料库存状态,对缺料部分及时释放《物料需求计划》。
3.1.4跟进物料交期和及时反馈相关问题。
3.1.5仓库组负责试产物料的接收和发放、半成品和成品的入库接收
3.2工程部:
3.2.1有责任根据业务部或PMC提供的文件,编制ProductionFlowChart、生产排位图、SOP、生产注意事项等文件;
3.2.2负责制作工装夹具、准备生产所需的仪器仪表和工具;
3.2.3负责生产线体设备设施架设和调试,负责生产工艺的安排和作业人员的培训指导;
3.2.4负责试产过程中不良品的统一维修分析,并提供详细分析报告。
3.2.5试产过程中的制程技术支持,对产品工艺的可制造性进行验证。
3.3生产部:
3.3.1有责任根据工程部提供的SOP、FlowChart进行排拉、组织生产。
3.3.2小批量试产执行、物料准备、成品和半成品入库;
3.3.3样板制作、试产执行和异常反馈并记录;
3.3.4生产组作业人员教育和培训;
3.4品质部
3.4.1负责记录并监控试产中之品质状况,负责收集并分析试产记录及相关资料,并生成《小批量试产品质报表》
3.4.2负责首件检查,并生成《首件检查报告》。
3.4.3负责监督生产文件、工程文件、客供资料的落实和执行。
4.0定义
4.1新产品
4.1.1公司以前未生产的产品,包括以下两种:
4.1.2新规格品:对成熟方案做适当调整的产品
4.1.3全新产品:采用新方案,新技术从无到有的产品
4.2试产
4.2.1指新产品在正式生产前为验证其生产工艺和产品的可靠性所进行的小批量生产,其数量为30-100PCS之间.
4.2.2对某些不常用机型,一般只做研发需求的数量。
4.3评审
为了评价作业满足质量要求的能力,对作业所做的综合的、有系统的形成文件的检查,给出明确的通过或不通过的结论。
参考《管理评审控制程序》
4.4新产品说明会
为促进全新产品在试产时的顺利进行,由工程部NPI工程师召开的会议。
会议主要包括:产品结构、产品工艺流程、重要作业方法及检测方法等的介绍,同时NPI工程师将对试产作整体规划和要求。
并将会议结果列入《会议记录》中,会议所记录各事项由NPI工程师跟进。
会议记录由NPI负责发给相关人员。
4.5试产评审会议
试产结束后,由NPI工程师召开的会议,项目经理、研发工程师、品质部、和生产部、工程部就试产中的问题做出一一解决方案。
由NPI跟进问题直至解决,并在会议中做出该次小批量试产是否通过的决定。
会议记录由NPI负责发给相关人员。
4.6试产样机
由客户或研发部提供的试产用其标签并加盖了试产专用章的样机(数量为3台,一台交品质部作试产检验依据,一套用来做夹具,另一套用来制作SOP)。
4.7输入/输入物
为完成相关的阶段、步骤、任务所必须先行取得并进行了解、参照、分析考虑或作为工作依据的信息、文档或数据(如:BOM、ECN、ID、MD、Software)。
4.8输出/输出物
阶段、步骤、任务的可检验的成果,如文档(SOP、评审报告)、实物(限度样板)等,作为阶段工作完成标志。
4.9缓冲时间
指下个节点或任务的作业指导时间,包括任务作业所需时间和因其它工作正在进行所需的过度时间。
作为引起冲突时的衡量标准。
5.0程序
5.1工程部根据业务部或PMC提供的工程资料如:BOMList、包装检验通知单(或包装指引)、配色图、软件发放通知单、PO单、软件、软件平台、工程样机等,对以上资料进行分析和样机的拆装,对产品工艺流程进行设计,依照<<生产计划>>的进度安排,按时制作生产文件和工装夹具。
5.2工程部根据业务部或PMC提供的客供资料及工程样机编写产品流程图
<<ProductionFlowChart>>.
5.3根据ProductionFlowChart设计出一条生产线,生产线的设计一般按以下步骤:
5.4.1根据ProductionFlowChart计算单工序标准时间.
5.4.2根据单工序标准时间计算出单部机标准时间,根据实际人手计算出每小时的产量。
5.4.3根据产量大小计算拉线的长度,工作台数等.
5.4.4根据物料的特性和要求及工艺要求选用工具。
5.5根据生产流程图编写<<StandardOperatingProcedure>>.
5.5.1制作每个工位的操作指导书:对每个工位的工位名称,工位时间,静电防护,工作内容,工夹具和辅材料等进行文字描述。
要求内容通俗易懂,文字简练,需要时用图片进行说明。
5.6生产线依据SOP、工程样机和生产注意事项,使用新产品套料,进行组装生产,品质和工程在开始生产半小时内,依据BOMList、包装检验通知单(或包装指引)、配色图、软件发放通知单、PO单、工程样机,检验首件是否正确,并由品质、工程、客户在首件单上签名确认;
5.7.1烙铁温度的制定:
5.7.1.1根据组件Specification要求制定烙铁温度,(测量工具:温度测量仪)
5.7.2电批磅力的制定
5.7.2.1根据工程部提供的塑料件的材料及螺丝Specification要求,用扭力批经过多次试装来制定电批磅力.(测量工具:扭力批,电批测量仪)
5.7.3辅料的制定:
5.7.3.1根据产品的品质要求选择辅料
5.7.3.2了解辅料Specification,然后在经过实验证明该辅料对该产品不会造成品质上的缺陷。
5.7.3.3根据生产计划须要测量出每种辅料的用量。
5.8生产问题总结
5.8.1工程部在新产品顺利量产后,依据生产测试报表、修理报表、品质异常联络单等,制作生产问题总结报告,并召集、主持生产问题总结会议,形成本次生产相关问题的最终决议存档。