精密直联式主轴系统的结构设计
机床主轴部件设计
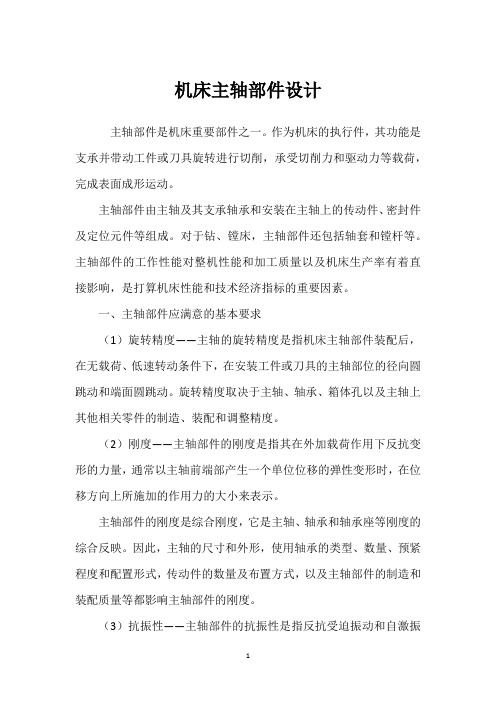
机床主轴部件设计主轴部件是机床重要部件之一。
作为机床的执行件,其功能是支承并带动工件或刀具旋转进行切削,承受切削力和驱动力等载荷,完成表面成形运动。
主轴部件由主轴及其支承轴承和安装在主轴上的传动件、密封件及定位元件等组成。
对于钻、镗床,主轴部件还包括轴套和镗杆等。
主轴部件的工作性能对整机性能和加工质量以及机床生产率有着直接影响,是打算机床性能和技术经济指标的重要因素。
一、主轴部件应满意的基本要求(1)旋转精度——主轴的旋转精度是指机床主轴部件装配后,在无载荷、低速转动条件下,在安装工件或刀具的主轴部位的径向圆跳动和端面圆跳动。
旋转精度取决于主轴、轴承、箱体孔以及主轴上其他相关零件的制造、装配和调整精度。
(2)刚度——主轴部件的刚度是指其在外加载荷作用下反抗变形的力量,通常以主轴前端部产生一个单位位移的弹性变形时,在位移方向上所施加的作用力的大小来表示。
主轴部件的刚度是综合刚度,它是主轴、轴承和轴承座等刚度的综合反映。
因此,主轴的尺寸和外形,使用轴承的类型、数量、预紧程度和配置形式,传动件的数量及布置方式,以及主轴部件的制造和装配质量等都影响主轴部件的刚度。
(3)抗振性——主轴部件的抗振性是指反抗受迫振动和自激振动而保持平稳运转的力量。
在切削过程中,由于各种因素引起的冲击力和交变力的干扰,使主轴产生振动。
抗振性差,表现为主轴部件工作时易产生振动且振幅较大,降低已加工表面质量和刀具寿命,加速传动件的磨损,诱发加工时的噪声,影响工作环境。
严峻的振动则可破坏刀具或主轴部件正常运转,使加工无法进行。
(4)温升及热变形——主轴部件运转时,因各相对运动处的摩擦生热,切削区的切削热等使主轴部件的温度上升,其尺寸、外形及位置发生变化,造成主轴部件的热变形。
主轴热变形可引起轴承间隙变化,温升后会使润滑油粘度降低,这些变化都会影响主轴部件的工作性能,降低加工精度。
(5)精度保持性——主轴部件的精度保持性是指长期地保持其原始制造精度的力量。
数控机床结构结构图
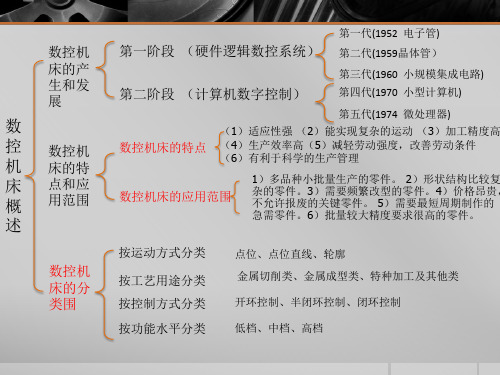
可编程控制器
数控车床 数控车床的工艺用途 的组成 数控车床的组成
影响车床布局形式的因素
操作面板
输入输出设备 CNC装置
伺服单元、驱动装置和测量装置
PLC、机床I/O电路和装置 机床主机
数控车床 主轴箱和尾座的布局形式 水平床身配置水平滑板
数 的布局 床身和导轨的布局形式
倾斜床身配置倾斜滑板 水平床身配置倾斜滑板
按照技术水平的高低分类 1.数显及打字型 2.带有小型电子计算机
进行数据处理型 3.计算机数字控制型
其他分类方法 大型、中型、小型;精密型、生产型
三
三坐标测量 机的构成
坐
三坐标测量机的主体 三坐标测量机的测量系统 三坐标测量机计算机控制系统和软件
标
三坐标测量机
直接测量方法 程序测量方法
测 的测量方式
床概述 数控冲床的工作原理
数控冲床的
数控冲床的组成
主机
数控装置
冲 组成与结构 数控冲床的结构
床
典型数
ZX数控冲床 性能特点
技术参数
控冲床
伺服复合小型精密钣金加工冲床
主要特点 技术参数
三坐标测 量机概述
三坐标测量机的功能 按照工作方式分类 1.点位测量法 2.连续扫描测量方式 三坐标测量机的类型 按照结构形式分类 1.悬臂式 2.桥式 3.龙门式 4.立柱式 5.坐标镗床式
冷却润滑技术(冷却
轨
数控机床导轨的类型与特点 滚动导轨
静压导轨
数控机床自动排 屑装置
平面链式排屑装置 刮板式排屑装置 螺旋式排屑装置 磁性排屑器
摩擦阻力小
位置检测装置
位置检测装置的要求(4点) 数字式与模拟式
的要求与类型
机械主轴结构设计

紧定套
SEUSEU-QRM
20
轴向定位和固定—— 轴向定位和固定
⑤
轴端挡板
当零件位于轴端时,可用轴端挡板与轴肩、轴套、 当零件位于轴端时,可用轴端挡板与轴肩、轴套、圆锥 面等的组合, 零件双向固定。 面等的组合,使零件双向固定。挡板用螺钉紧固在轴端 并压紧被定位零件的端面。该方法简单可靠、装拆方便, 并压紧被定位零件的端面。该方法简单可靠、装拆方便, 轴端加工螺纹孔。 但需在轴端加工螺纹孔 但需在轴端加工螺纹孔。
机械设计 Machine Design
PART Ⅲ
Design of Elements and Parts in General Use
Chapter 19 Design of Shafts
主讲—— 主讲——钱瑞明
SEUSEU-QRM 1
19.1 Introduction 概述
轴用于安装传动零件 如齿轮 凸轮、带轮等), 轴用于安装传动零件(如齿轮、凸轮、带轮等 ,使其有确定 安装传动零件 如齿轮、 的工作位置, 实现运动和动力的传递, 并通过轴承支承在 的工作位置 , 实现运动和动力的传递 , 并通过轴承 支承在 机架或机座上。 机架或机座上。
SEUSEU-QRM
×
8
Stresses in shafts——
静应力 σ(τ) τ o τ 脉动循环应力 σ(τ) o τ 对称循环应力 σ(τ) o 转轴—— 转轴 弯矩: 弯矩:对称循环应力 扭矩: 扭矩:脉动循环应力
SEUSEU-QRM 9
t
t
t
19.1.2 Materials and Roughs of Shafts 材料与毛坯 Shaft Materials —— Table 19.1
试谈数控机床_加工中心的结构设计
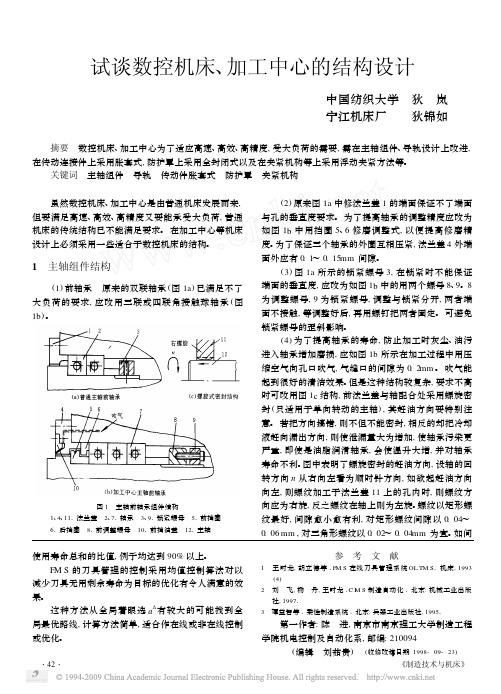
试谈数控机床、加工中心的结构设计中国纺织大学 狄 岚 宁江机床厂 狄锦如 摘要 数控机床、加工中心为了适应高速、高效、高精度,受大负荷的需要,需在主轴组件、导轨设计上改进,在传动连接件上采用胀套式,防护罩上采用全封闭式以及在夹紧机构等上采用浮动夹紧方法等。
关键词 主轴组件 导轨 传动件胀套式 防护罩 夹紧机构 虽然数控机床、加工中心是由普通机床发展而来,但要满足高速、高效、高精度又要能承受大负荷,普通机床的传统结构已不能满足要求。
在加工中心等机床设计上必须采用一些适合于数控机床的结构。
1 主轴组件结构 (1)前轴承 原来的双联轴承(图1a )已满足不了大负荷的要求,应改用三联或四联角接触球轴承(图1b )。
图1 主轴前轴承组件结构1、4、111法兰盖2、71轴承3、91锁紧螺母 51前挡圈61后挡圈 81前调整螺母 101前挡油盖 121主轴 (2)原来图1a 中修法兰盖1的端面保证不了端面与孔的垂直度要求。
为了提高轴承的调整精度应改为如图1b 中用挡圈5、6修磨调整式,以便提高修磨精度。
为了保证三个轴承的外圈互相压紧,法兰盖4外端面外应有0.1~0.15mm 间隙。
(3)图1a 所示的锁紧螺母3,在锁紧时不能保证端面的垂直度,应改为如图1b 中的用两个螺母8、9。
8为调整螺母,9为锁紧螺母,调整与锁紧分开,两者端面不接触,等调整好后,再用螺钉把两者固定。
可避免锁紧螺母的歪斜影响。
(4)为了提高轴承的寿命,防止加工时灰尘、油污进入轴承增加磨损,应如图1b 所示在加工过程中用压缩空气向孔口吹气,气缝口的间隙为0.2mm 。
吹气能起到很好的清洁效果。
但是这种结构较复杂,要求不高时可改用图1c 结构,前法兰盖与轴配合处采用螺旋密封(只适用于单向转动的主轴),其赶油方向要特别注意。
若把方向搞错,则不但不能密封,相反的却把冷却液赶向漏出方向,则使泄漏量大为增加,使轴承污染更严重,即使是油脂润滑轴承,会使温升大增,并对轴承寿命不利。
值得收藏的技术:高精度机床的主轴结构是这样的

值得收藏的技术:高精度机床的主轴结构是这样的现有高精度机床的主轴结构1、主轴;101、第一凹槽;2、密封圈;3、端盖;301、台阶槽;4、壳体;401、螺纹安装孔;402、第二凹槽;5、第一轴承;6、隔圈;7、第二轴承;8、轴承锁紧调整片;9、固定螺母;10、锁紧螺栓;11、O 型密封圈。
有腔体的壳体 4,壳体 4 为圆形壳体,主轴 1 贯穿安装在壳体 4 的腔体内部,于壳体 4 的腔体内、在主轴 1 的外周还分别连接多个第一轴承 5 及第二轴承 7,第一轴承 5 为角接触球轴承,第二轴承 7 为角接触轴承,各第一轴承5互为抵接安装在主轴1上,各第二轴承7也互为抵接安装在主轴 1上,本实用新型中第一轴承 5 为 4 个,第二轴承 7 为 3 个 ( 第一轴承 5 及第二轴承 7 的数量根据实际生产情况调整 )。
如图 1 所示,于主轴 1 上位于最内侧的第一轴承 5 及第二轴承7 之间、在主轴 1 的外周还套接隔圈 6,于壳体 4 的外周沿圆周方向均匀开设多个螺纹安装孔 401,于螺纹安装孔 401 内螺接用于压紧隔圈 6 的固定螺母 9,利用固定螺母 9 锁紧隔圈 6,避免主轴 1 受力产生刚性降低的情况。
如图 1 所示,于壳体 4 的两端分别通过锁紧螺栓10 固定端盖 3,于端盖 3 内圈处的台阶槽 301 中还安装密封圈 2,密封圈 2 为骨架式橡胶密封圈。
至少在一个端盖 3 的内圈与主轴 1 的外周之间还安装轴承锁紧调整片8,轴承锁紧调整片8也通过锁紧螺栓10 与主轴 1 固接,利用轴承锁紧调整片 8 取代原有螺母锁紧易造成轴承偏压、导致主轴精度降低情况,主轴1 在使用过一段时间后,可以通过轴承锁紧调整片 8( 调节轴承锁紧调整片 8 对轴承的松紧度 ) 增加对轴承的预紧力,使主轴 1 精度保证在最佳状态。
如图 1 所示,在主轴 1 的外周沿圆周方向开设第一凹槽 101,在壳体 4 的内壁沿圆周方向开设第二凹槽 402,第一凹槽 101 与第二凹槽 402 的开设位置互为对应。
主轴部件结构图汇总

带交换托盘的多齿盘分度工作台
数控分度工作台
加 工 中 心 回 转 工 作 台
工 作 台 夹 紧 机 构
夹 紧 环 联 轴 器 结 构 图
刀架和机械手部件结构图
立 式 四 方 刀 架 结 构
回 转 刀 架
刀 库 种 类
链 式 刀 库 换 刀 位 置
各种链式刀库
单臂单手式机械手
手臂和手爪结构
加工中心自动换刀装置
刀 库 结 构
T D
向 与 向 滑 台
回 转 立 柱 与 机 械 手 回 转 运 动
机械手臂结构图
换刀装置各部分位置关系图
检测装置结构图
直线感应同步器结构
按磁性标尺基体形状分类的各种磁尺
HEIDENHAIN增量式直线编码器
旋 转 变 压 器
光电脉冲编码器结构示意图
轴 向 垫 片 调 整 法
周 向 弹圆 簧柱 错薄 齿片 调齿 整轮 法 简 图
可 调 拉圆 簧柱 错薄 齿片 调齿 整轮 法 简 图
斜 齿 轮 垫 片 、 压 簧 调 整
锥 齿 轮 弹 簧 调 整 法
齿轮齿条啮合齿侧隙消除法结构简图
滚 珠 丝 杠 结 构
螺纹滚道的结构形式简图
垫片调整式的滚珠丝杠螺母副
螺 纹 调 整 式 的 滚 珠 丝 杠 螺 母 副
齿差调整式的滚珠丝杠螺母副
导轨部件结构图
直 线 滚 动 导 轨 副 结 构
滚动导轨预加负载的方法
直线滚动导轨副的固定
滚 动 导 轨 块
开 式 静 压 导 轨 工 作 原 理
闭 式 静 压 导 轨 工 作 原 理
工作台部件结构图
多齿盘分度工作台结构图
主轴部件结构图
主轴结构设计范文

主轴结构设计范文
一、主轴的结构设计
1、主轴体结构设计
主轴体(Spindle body)采用铣削加工,采用45钢制作。
45钢因其良
好的机械性能及耐磨性适合制作主轴体的要求,为确保精度和强度,选用
Φ80mm*1200mm的热轧精密直线棒。
主轴体需要制作出一定的宽度,用于使主轴体的精度达到要求,因此
需要进行精密精磨加工,精磨的精度达到Ra0.2μm即可。
主轴体内部空间设计,开槽,定位孔以及衔接及调整孔等,均采用数
控车床加工,要求加工精度±0.002mm。
2、主轴头设计
主轴头(Spindle head)由胶合铸铁制成,经加工可以达到较好的整体
结构强度。
其内部空间设计,开槽,定位孔以及衔接孔均采用数控车床加工,要求加工精度±0.002mm。
主轴头上分别设有润滑油嘴,润滑油嘴采用国标标准的6mm螺纹连接,连接紧固等级为A4-80。
3、主轴轴承座设计
主轴轴承座(Bearing seat)采用铝合金制作,内部空间设计,开槽,
定位孔以及衔接孔均采用数控车床加工,要求加工精度±0.002mm,需要
抗震力及耐磨性好的材料。
4、关节螺母设计
关节螺母(Joint nut)采用耐热的特殊材料制作,内部空间设计,开槽,定位孔以及衔接孔均采用数控车床加工,要求加工精度±0.002mm。
主轴结构及工作原理

主轴部件是机床的重要部件之一,其精度、抗振性和热变形对加工质量有直接影响。
特别是如果数控机床在加工过程中不进行人工调整,这些影响将更为严重。
数控机床主轴部件在结构上要解决好主轴的支承、主轴内刀具自动装夹、主轴的定向停止等问题。
数控机床主轴的支承主要采用图8-5所示的三种主要形式。
图8-5a所示结构的前支承采用双列短圆柱滚子轴承和双向推力角接触球轴承组合,后支承采用成对向心推力球轴承。
这种结构的综合刚度高,可以满足强力切削要求,是目前各类数控机床普遍采用的形式。
图8-5b所示结构的前支承采用多个高精度向心推力球轴承,后支承采用单个向心推力球轴承。
这种配置的高速性能好,但承载能力较小,适用于高速、轻载和精密数控机床。
图8-5c所示结构为前支承采用双列圆锥滚子轴承,后支承为单列圆锥滚子轴承。
这种配置的径向和轴向刚度很高,可承受重载荷,但这种结构限制了主轴最高转速和精度,因而仅适用于中等精度、低速与重载的数控机床主轴。
主轴内部刀具自动夹紧机构是数控机床特别是加工中心的特有机构。
图8-6为ZHS-K63加工中心主轴结构部件图,其刀具可以在主轴上自动装卸并进行自动夹紧,其工作原理如下:当刀具2装到主轴孔后,其刀柄后部的拉钉3便被送到主轴拉杆7的前端,在碟形弹簧9的作用下,通过弹性卡爪5将刀具拉紧。
当需要换刀时,电气控制指令给液压系统发出信号,使液压缸14的活塞左移,带动推杆13向左移动,推动固定在拉杆7上的轴套10,使整个拉杆7向左移动,当弹性卡爪5向前伸出一段距离后,在弹性力作用下,卡爪5自动松开拉钉3,此时拉杆7继续向左移动,喷气嘴6的端部把刀具顶松,机械手便可把刀具取出进行换刀。
装刀之前,压缩空气从喷气嘴6中喷出,吹掉锥孔内脏物,当机械手把刀具装入之后,压力油通人液压缸14的左腔,使推杆退回原处,在碟形弹簧的作用下,通过拉杆7又把刀具拉紧。
冷却液喷嘴1用来在切削时对刀具进行大流量冷却。
主轴部件是机床的重要部件之一,其精度、抗振性和热变形对加工质量有直接影响。
数控机床主轴总体设计说明

数控机床主轴总体设计说明一、引言数控机床主轴是数控机床的核心部件之一,它直接影响到数控机床的加工质量和加工效率。
因此,对数控机床主轴的设计、制造和检验都有着非常高的要求。
本文将结合实际生产经验,对数控机床主轴的总体设计进行说明。
二、主轴的功能数控机床主轴是一台数控加工设备的核心部件,具有以下功能:1.旋转工件或刀具,实现工件或刀具的加工。
2.传动功率和转矩,将电机的运动转化为工件或刀具的动力。
3.承受工件或刀具的径向和轴向载荷,保证加工精度和轴向精度。
4.提供冷却润滑油和气体,保持主轴箱内清洁和恒定的温度。
三、主轴的总体设计主轴的总体设计包括主轴的结构设计、选型及计算、刚度分析、动平衡设计和主轴箱的设计等方面。
1.主轴的结构设计主轴结构设计的主要要求是,保证主轴的强度、刚度、耐磨损性能和承受力等,同时还要考虑加工精度、轴向精度、温度稳定性和动平衡等因素。
主轴的结构设计要根据主轴的类型、加工能力及加工特点等来确定,常见的主轴类型包括带式主轴、插入式主轴、自锁式主轴等。
2.选型及计算选型及计算的主要任务是确定主轴的型号、规格、旋转速度、转矩、功率等参数。
这些参数的确定需要考虑到加工能力、加工精度、使用环境及加工特点等,以满足加工要求和质量要求。
3.刚度分析刚度分析是保证主轴在加工过程中加工精度和轴向精度的重要手段。
刚度分析要根据主轴的加工特点及使用环境等要素,确定最大切削力、最大拉力、最大径向力和最大轴向力,并结合主轴的结构设计确定刚度系数。
4.动平衡设计主轴的动平衡设计是保证加工质量的重要环节,它能有效地减少振动和杂音,提高加工效率和加工精度。
动平衡设计主要包括自动平衡控制、振动分析计算、动平衡校正及接触式动平衡等。
主轴箱的设计是保证主轴的工作稳定性和长寿命的重要条件。
主轴箱的设计要考虑到温度稳定性、噪声降低、密封性能、承载力及润滑性能等因素。
四、主轴的制造与检验主轴的制造过程包括材料采购、热处理、粗加工、研磨、组装、调试等环节。
直联主轴结构特点

直联主轴结构特点《说说直联主轴那些事儿》嘿,大家好呀!今天咱来唠唠直联主轴结构特点这个话题。
你要问我直联主轴是啥玩意儿?那它可就像机器里的“小超人”一样!直联主轴,顾名思义,就是直接和动力源连接嘛。
它的一个特点就是简洁高效。
没有那些弯弯绕绕的传动部件,直接就把力量传递过去了,就像武侠小说里高手出招,简洁明快,不拖泥带水。
这就意味着它能量损耗少啊,把动力都用在了刀刃上,那工作效率不得蹭蹭往上窜。
还有啊,它运行起来特别稳。
就像个老实的“大力士”,老老实实地干着活儿,不会乱晃悠。
这可太重要了,咱就说要是不稳定,那加工出来的东西能合格吗?说不定就歪七扭八的了。
但直联主轴不会,它稳如泰山,让你特别放心。
这家伙的精度也很高呢。
就像个精细的“工匠”,每一个动作都精确无比。
这对于那些对精度要求严苛的活儿来说,简直就是福音啊。
能加工出超级精细的东西,让人不得不佩服。
而且,它还挺耐用的。
可不是那种娇滴滴的“小公主”,轻易不会出啥毛病。
只要正常使用和维护,它能陪着咱工作好长时间呢。
不过呢,直联主轴也不是完美无缺的啦。
比如说,它要是出了问题,修起来可能就会有点麻烦,毕竟结构在那摆着呢。
还有就是价格相对可能会高那么一点点,但俗话说得好,一分价钱一分货嘛。
总的来说,直联主轴这玩意儿,有它独特的魅力和优势。
它简洁高效、稳定精确又耐用,就像是机器世界里的一颗闪耀的明星。
咱在使用的时候,可得好好爱惜它,让它发挥出最大的作用。
咱普通人虽然不懂那些高深的技术原理,但在使用中也能感受到它的厉害。
所以啊,大家要多多了解这些机械上的好东西,这样才能更好地利用它们,让我们的工作更轻松、更高效呀!哈哈,这就是我对直联主轴结构特点的真实感受和见解啦,你们觉得咋样呢?。
数控机床主轴系统工作原理
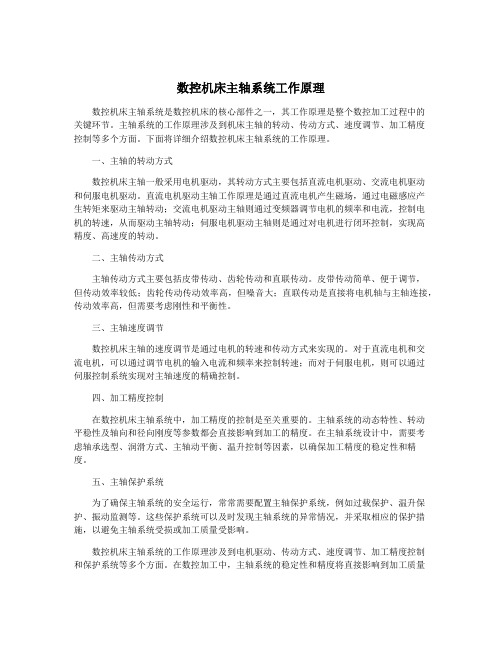
数控机床主轴系统工作原理数控机床主轴系统是数控机床的核心部件之一,其工作原理是整个数控加工过程中的关键环节。
主轴系统的工作原理涉及到机床主轴的转动、传动方式、速度调节、加工精度控制等多个方面。
下面将详细介绍数控机床主轴系统的工作原理。
一、主轴的转动方式数控机床主轴一般采用电机驱动,其转动方式主要包括直流电机驱动、交流电机驱动和伺服电机驱动。
直流电机驱动主轴工作原理是通过直流电机产生磁场,通过电磁感应产生转矩来驱动主轴转动;交流电机驱动主轴则通过变频器调节电机的频率和电流,控制电机的转速,从而驱动主轴转动;伺服电机驱动主轴则是通过对电机进行闭环控制,实现高精度、高速度的转动。
二、主轴传动方式主轴传动方式主要包括皮带传动、齿轮传动和直联传动。
皮带传动简单、便于调节,但传动效率较低;齿轮传动传动效率高,但噪音大;直联传动是直接将电机轴与主轴连接,传动效率高,但需要考虑刚性和平衡性。
三、主轴速度调节数控机床主轴的速度调节是通过电机的转速和传动方式来实现的。
对于直流电机和交流电机,可以通过调节电机的输入电流和频率来控制转速;而对于伺服电机,则可以通过伺服控制系统实现对主轴速度的精确控制。
四、加工精度控制在数控机床主轴系统中,加工精度的控制是至关重要的。
主轴系统的动态特性、转动平稳性及轴向和径向刚度等参数都会直接影响到加工的精度。
在主轴系统设计中,需要考虑轴承选型、润滑方式、主轴动平衡、温升控制等因素,以确保加工精度的稳定性和精度。
五、主轴保护系统为了确保主轴系统的安全运行,常常需要配置主轴保护系统,例如过载保护、温升保护、振动监测等。
这些保护系统可以及时发现主轴系统的异常情况,并采取相应的保护措施,以避免主轴系统受损或加工质量受影响。
数控机床主轴系统的工作原理涉及到电机驱动、传动方式、速度调节、加工精度控制和保护系统等多个方面。
在数控加工中,主轴系统的稳定性和精度将直接影响到加工质量和效率,因此对主轴系统的设计和调试需要十分重视。
主轴的形式及结构[整理版]
![主轴的形式及结构[整理版]](https://img.taocdn.com/s3/m/4cead25a2a160b4e767f5acfa1c7aa00b52a9d9c.png)
关于主轴结构何謂直結式主軸?直結式主軸即類似三軸馬達與滾珠螺桿之接合方式,主軸馬達置於主軸上方,馬達與主軸以高剛性無間隙連軸器相連,馬達端之轉動經由連軸器傳於主軸,此即直結式主軸直結式主軸比起皮帶式,齒輪式與內藏式有什麼特色?內藏式主軸:內藏式主軸即將馬達與主軸合而為一,將馬達轉子安裝於主軸軸心,定子在外,運轉原理和一般主軸馬達相同,其具有低振動特性,動態迴轉精度亦較好,但因主軸內必須置放馬達轉子造成軸承跨距較大,剛性較弱的情形發生內藏式主軸因剛性之故並不適合重切削直結式主軸:直結式主軸即類似三軸馬達與滾珠螺桿之接合方式,主軸馬達置於主軸上方,馬達與主軸以高剛性無間隙連軸器相連,馬達端之轉動經由連軸器傳於主軸,此即直結式主軸直結式主軸屬於剛性連結,對於馬達輸出之POWER較能完全表達於主軸特性,機械效率較高,於主軸運動時,連軸器扮演著不可或缺的角色,連軸器校正好或壞足以影響主軸運動精度,若連軸器校正不良對主軸產生下列影響,主軸溫昇急劇昇高、主軸震動過大、主軸偏擺過大、加工精度不良、甚至主軸燒毀皮帶式主軸:皮帶式主軸以皮帶傳遞主軸馬達之運動至主軸,其優點為,振動較齒輪式主軸小,易組裝,缺點為高速時噪音大,皮帶張力不易控制等齒輪式主軸:齒輪式主軸最大之優點為可傳遞高扭力,重切削能力優良,其缺點為轉速受限於齒輪設計不易提昇等电主轴是最近几年在数控机床领域出现的将机床主轴与主轴电机融为一体的新技术,它与直线电机技术、高速刀具技术一起,将会把高速加工推向一个新时代。
电主轴是一套组件,它包括电主轴本身及其附件:电主轴、高频变频装置、油雾润滑器、冷却装置、内置编码器、换刀装置。
电主轴所融合的技术:高速轴承技术:电主轴通常采用复合陶瓷轴承,耐磨耐热,寿命是传统轴承的几倍;有时也采用电磁悬浮轴承或静压轴承,内外圈不接触,理论上寿命无限;高速电机技术:电主轴是电动机与主轴融合在一起的产物,电动机的转子即为主轴的旋转部分,理论上可以把电主轴看作一台高速电动机。
主轴结构设计范文

主轴结构设计范文主轴结构设计是指为了满足其中一种工作要求而设计的一种结构形式,其目的是为了使工作更加顺利、高效。
主轴结构设计在工程领域特别重要,因为它能够承受和传递重要的力量和压力。
在本文中,将对主轴结构设计进行详细的阐述。
1.强度和刚度:主轴结构设计需要具备足够的强度和刚度,以承受和传递应力和压力。
这可以通过选择适当的材料和合理的截面形状来实现。
此外,还需要进行适当的受力分析和计算,以确保主轴在工作条件下不会发生断裂或变形。
2.润滑和冷却:主轴结构在工作过程中会产生热量,需要进行润滑和冷却。
为了保证主轴的顺利运转,需要在设计中考虑到润滑和冷却的问题。
可以采用润滑剂或冷却器来减少热量的产生,并确保主轴充足的润滑和冷却。
3.防震和减振:主轴结构设计需要考虑到振动和冲击的问题,特别是在高速和重载的工作条件下。
通过选择适当的材料和采取合适的隔振措施,可以减少振动和冲击对主轴的影响,并提高主轴的稳定性和寿命。
4.维护和修理:主轴结构设计需要考虑到维护和修理的问题。
为了方便维护和修理,主轴的结构需要尽量简单和可拆卸。
同时,需要提供适当的检修孔和访问设施,以方便进行维护和修理工作。
5.可靠性和安全性:主轴结构设计需要具备足够的可靠性和安全性,以保证工作的连续性和人员的安全。
为了提高可靠性和安全性,可以采用重复和备份的设计原则,并确保主轴结构具备足够的强度和耐久性。
综上所述,主轴结构设计是一项复杂的工作,需要考虑到多个因素。
通过合理的材料选择、优化的结构设计和适当的工艺措施,可以实现主轴结构设计的目标,并提高工作的效率和质量。
质押是指按照约定将货物、证券等财物交付给债权人,作为债务的担保。
主要形式有抵押质押和留置等。
质押借款是指借款人与贷款机构签订一份质押协议,在该协议中以抵押财产作为借款风险保障,并且当借款人无法履行合同约定的还款义务时,贷款机构有权扣押被质押的财产,并按照约定的相关程序和规定进行处置利用。
主轴的结构与传动原理

主轴的结构与传动原理主轴是机械设备中的一种重要传动元件,主要用于将动力从电机或其他动力源传递给机械设备的工作部件,同时还承担着支撑和定位的功能。
主轴的结构和传动原理有多种形式,下面将逐一进行介绍。
首先,从结构上来说,主轴可以分为不同种类,包括轴承式主轴、滑动式主轴和行星齿轮主轴等。
轴承式主轴是最常见的一种形式,它由轴承、轴套、轴头等组成,可以实现高速、高精度的传动。
滑动式主轴则采用滑动副的方式,通过润滑油膜来减小摩擦,常用于低速、大载荷的传动。
行星齿轮主轴由齿轮传动系统组成,结构紧凑、传动效率高,适用于高速精密传动。
接下来,从传动原理的角度来说,主轴的传动方式主要包括齿轮传动、牙形带传动、皮带传动和链传动等几种形式。
其中,齿轮传动是主轴最常见的传动方式之一。
齿轮传动通过齿轮之间的啮合来实现转速和扭矩的传递。
常见的有直齿轮传动、斜齿轮传动、蜗杆传动等。
牙型带传动则利用带上的齿形来实现传动,主要包括同步带传动和齿形带传动。
主轴上的带子与带轮之间通过齿形的嵌合进行传输。
皮带传动是使用皮带进行传动的一种方式,通过拉紧调节皮带的张紧度,来实现传动方式的调整。
链传动则通过链条上的链环之间的链接来传递动力。
此外,主轴的传动原理还包括液体传动和气体传动等。
液体传动是利用油液或液态介质进行输送动力的一种方式,主要应用于液压传动系统中。
气体传动则是利用气体进行动力传递的一种方式,例如气动工具中的气动传动系统。
总的来说,主轴的结构和传动原理有多种形式,每种形式都有其适用的领域和特点。
选用合适的主轴结构和传动原理,可以保证机械设备的正常运转,并提高其传动效率和可靠性。
加工中心主轴系统设计-加工中心主轴结构
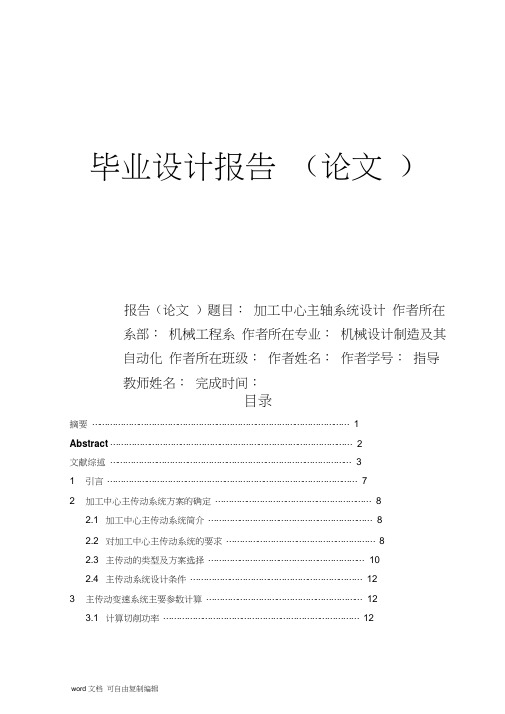
毕业设计报告(论文)报告(论文)题目:加工中心主轴系统设计作者所在系部:机械工程系作者所在专业:机械设计制造及其自动化作者所在班级:作者姓名:作者学号:指导教师姓名:完成时间:目录摘要⋯⋯⋯⋯⋯⋯⋯⋯⋯⋯⋯⋯⋯⋯⋯⋯⋯⋯⋯⋯⋯⋯⋯⋯⋯⋯⋯⋯⋯⋯⋯⋯⋯1Abstract ⋯⋯⋯⋯⋯⋯⋯⋯⋯⋯⋯⋯⋯⋯⋯⋯⋯⋯⋯⋯⋯⋯⋯⋯⋯⋯⋯⋯⋯⋯⋯2文献综述⋯⋯⋯⋯⋯⋯⋯⋯⋯⋯⋯⋯⋯⋯⋯⋯⋯⋯⋯⋯⋯⋯⋯⋯⋯⋯⋯⋯⋯⋯⋯31 引言⋯⋯⋯⋯⋯⋯⋯⋯⋯⋯⋯⋯⋯⋯⋯⋯⋯⋯⋯⋯⋯⋯⋯⋯⋯⋯⋯⋯⋯⋯⋯⋯72 加工中心主传动系统方案的确定⋯⋯⋯⋯⋯⋯⋯⋯⋯⋯⋯⋯⋯⋯⋯⋯⋯⋯⋯⋯82.1 加工中心主传动系统简介⋯⋯⋯⋯⋯⋯⋯⋯⋯⋯⋯⋯⋯⋯⋯⋯⋯⋯⋯⋯⋯82.2 对加工中心主传动系统的要求⋯⋯⋯⋯⋯⋯⋯⋯⋯⋯⋯⋯⋯⋯⋯⋯⋯⋯⋯82.3 主传动的类型及方案选择⋯⋯⋯⋯⋯⋯⋯⋯⋯⋯⋯⋯⋯⋯⋯⋯⋯⋯⋯⋯102.4 主传动系统设计条件⋯⋯⋯⋯⋯⋯⋯⋯⋯⋯⋯⋯⋯⋯⋯⋯⋯⋯⋯⋯⋯⋯123 主传动变速系统主要参数计算⋯⋯⋯⋯⋯⋯⋯⋯⋯⋯⋯⋯⋯⋯⋯⋯⋯⋯⋯⋯123.1 计算切削功率⋯⋯⋯⋯⋯⋯⋯⋯⋯⋯⋯⋯⋯⋯⋯⋯⋯⋯⋯⋯⋯⋯⋯⋯⋯123.2 计算主传动功率⋯⋯⋯⋯⋯⋯⋯⋯⋯⋯⋯⋯⋯⋯⋯⋯⋯⋯⋯⋯⋯⋯⋯⋯133.3 确定电动机型号⋯⋯⋯⋯⋯⋯⋯⋯⋯⋯⋯⋯⋯⋯⋯⋯⋯⋯⋯⋯⋯⋯⋯⋯144 主传动变速系统的设计计算⋯⋯⋯⋯⋯⋯⋯⋯⋯⋯⋯⋯⋯⋯⋯⋯⋯⋯⋯⋯⋯144.1 圆弧齿同步带传动的计算⋯⋯⋯⋯⋯⋯⋯⋯⋯⋯⋯⋯⋯⋯⋯⋯⋯⋯⋯⋯144.2 圆弧齿同步带带轮的结构设计⋯⋯⋯⋯⋯⋯⋯⋯⋯⋯⋯⋯⋯⋯⋯⋯⋯⋯165 主轴组件设计⋯⋯⋯⋯⋯⋯⋯⋯⋯⋯⋯⋯⋯⋯⋯⋯⋯⋯⋯⋯⋯⋯⋯⋯⋯⋯⋯175.1 主轴组件的设计要求和步骤⋯⋯⋯⋯⋯⋯⋯⋯⋯⋯⋯⋯⋯⋯⋯⋯⋯⋯⋯185.1.1 主轴组件的设计要求⋯⋯⋯⋯⋯⋯⋯⋯⋯⋯⋯⋯⋯⋯⋯⋯⋯⋯⋯185.1.2 主轴组件的设计步骤⋯⋯⋯⋯⋯⋯⋯⋯⋯⋯⋯⋯⋯⋯⋯⋯⋯⋯⋯205.2 主轴的设计要求⋯⋯⋯⋯⋯⋯⋯⋯⋯⋯⋯⋯⋯⋯⋯⋯⋯⋯⋯⋯⋯⋯⋯⋯205.2.1 主轴的主要尺寸参数⋯⋯⋯⋯⋯⋯⋯⋯⋯⋯⋯⋯⋯⋯⋯⋯⋯⋯⋯205.2.2 主轴轴端结构⋯⋯⋯⋯⋯⋯⋯⋯⋯⋯⋯⋯⋯⋯⋯⋯⋯⋯⋯⋯⋯⋯215.2.3 主轴的材料和热处理⋯⋯⋯⋯⋯⋯⋯⋯⋯⋯⋯⋯⋯⋯⋯⋯⋯⋯⋯215.2.4 主轴主要精度指标⋯⋯⋯⋯⋯⋯⋯⋯⋯⋯⋯⋯⋯⋯⋯⋯⋯⋯⋯⋯225.3 主轴滚动轴承⋯⋯⋯⋯⋯⋯⋯⋯⋯⋯⋯⋯⋯⋯⋯⋯⋯⋯⋯⋯⋯⋯⋯⋯⋯225.3.1 滚动轴承类型⋯⋯⋯⋯⋯⋯⋯⋯⋯⋯⋯⋯⋯⋯⋯⋯⋯⋯⋯⋯⋯⋯225.3.2 主轴轴承配置与调整⋯⋯⋯⋯⋯⋯⋯⋯⋯⋯⋯⋯⋯⋯⋯⋯⋯⋯⋯235.4 主轴组件的设计计算⋯⋯⋯⋯⋯⋯⋯⋯⋯⋯⋯⋯⋯⋯⋯⋯⋯⋯⋯⋯⋯⋯245.4.1 初选主轴直径⋯⋯⋯⋯⋯⋯⋯⋯⋯⋯⋯⋯⋯⋯⋯⋯⋯⋯⋯⋯⋯⋯245.4.2 主轴悬伸量的确定⋯⋯⋯⋯⋯⋯⋯⋯⋯⋯⋯⋯⋯⋯⋯⋯⋯⋯⋯⋯255.4.3 主轴最佳跨距的选择⋯⋯⋯⋯⋯⋯⋯⋯⋯⋯⋯⋯⋯⋯⋯⋯⋯⋯⋯255.5 主轴组件的校核计算⋯⋯⋯⋯⋯⋯⋯⋯⋯⋯⋯⋯⋯⋯⋯⋯⋯⋯⋯⋯⋯⋯265.5.1 主轴组件的刚度计算⋯⋯⋯⋯⋯⋯⋯⋯⋯⋯⋯⋯⋯⋯⋯⋯⋯⋯⋯265.5.2 主轴组件的强度计算⋯⋯⋯⋯⋯⋯⋯⋯⋯⋯⋯⋯⋯⋯⋯⋯⋯⋯⋯255.5.3 轴承的校核计算⋯⋯⋯⋯⋯⋯⋯⋯⋯⋯⋯⋯⋯⋯⋯⋯⋯⋯⋯⋯⋯295.5.4 键的校核计算⋯⋯⋯⋯⋯⋯⋯⋯⋯⋯⋯⋯⋯⋯⋯⋯⋯⋯⋯⋯⋯⋯325.6 主轴内部刀具自动夹紧机构及切屑清除装置⋯⋯⋯⋯⋯⋯⋯⋯⋯⋯⋯⋯325.7 主轴组件的润滑与密封⋯⋯⋯⋯⋯⋯⋯⋯⋯⋯⋯⋯⋯⋯⋯⋯⋯⋯⋯⋯⋯335.8 提高主轴组件性能的措施⋯⋯⋯⋯⋯⋯⋯⋯⋯⋯⋯⋯⋯⋯⋯⋯⋯⋯⋯⋯346 结论⋯⋯⋯⋯⋯⋯⋯⋯⋯⋯⋯⋯⋯⋯⋯⋯⋯⋯⋯⋯⋯⋯⋯⋯⋯⋯⋯⋯⋯⋯⋯35参考文献⋯⋯⋯⋯⋯⋯⋯⋯⋯⋯⋯⋯⋯⋯⋯⋯⋯⋯⋯⋯⋯⋯⋯⋯⋯⋯⋯⋯⋯⋯⋯36致谢⋯⋯⋯⋯⋯⋯⋯⋯⋯⋯⋯⋯⋯⋯⋯⋯⋯⋯⋯⋯⋯⋯⋯⋯⋯⋯⋯⋯⋯⋯⋯⋯⋯36立式加工中心主传动系统设计摘要:本文介绍了立式加工中心的一些基本概况,简述了机床主传动系统方面的原理和类型,分析了各种传动方案的机理。
主轴结构设计

Shaft Roughs ——
可用轧制圆钢材、锻造、焊接、铸造等方法获得。 对要求不高的轴或较长的轴,毛坯直径小于150mm时,可用轧制 圆钢材; 受力大,生产批量大的重要轴的毛坯可由锻造提供; 对直径特大而件数很少的轴可用焊件毛坯; 生产批量大、外形复杂、尺寸较大的轴,可用铸造毛坯。
SEU-QRM 10
19.1.3 Failure Forms and Design Requirements of Shafts 轴的失效形式与设计要求 Failure Forms —— 因疲劳强度不足而产生的疲劳断裂; 因静强度不足而产生的塑性变形或脆性断裂、磨损; 超过允许范围的变形和振动等。
SEU-QRM
11
Design Requirements —— 轴与轴上零件组成一个组合体称为轴系部件。轴的设计必 须与轴系零部件整体结构紧密联系起来。 (1) 根据轴的工作条件、生产批量和经济性原则,选取适合 的材料、毛坯形式及热处理方法。 (2) 根据轴的受力情况、轴上零件的安装位置、配合尺寸及 定位方式、轴的加工方法等具体要求,确定轴的合理结 构形状及尺寸,即进行轴的结构设计。 (3) 轴的强度计算或校核。对受力大的细长轴(如蜗杆轴)和 对刚度要求高的轴,还要进行刚度计算。在对高速工作 下的轴,因有共振危险,故应进行振动稳定性计算。
SEU-QRM
2
19.1.1 Classification of Shafts 轴的分类 按轴线形状分——直轴(straight shaft)、曲轴(crankshaft) 和软轴(flexible shaft)。 Straight Shaft——
SEU-QRM
3
Crankshaft——
Flexible Shaft——
- 1、下载文档前请自行甄别文档内容的完整性,平台不提供额外的编辑、内容补充、找答案等附加服务。
- 2、"仅部分预览"的文档,不可在线预览部分如存在完整性等问题,可反馈申请退款(可完整预览的文档不适用该条件!)。
- 3、如文档侵犯您的权益,请联系客服反馈,我们会尽快为您处理(人工客服工作时间:9:00-18:30)。
2018年5月第46卷第10期机床与液压MACHINETOOL&HYDRAULICSMay2018Vol 46No 10DOI:10.3969/j issn 1001-3881 2018 10 005收稿日期:2017-06-22基金项目:国家科技重大专项资助项目(2016ZX04004⁃002)作者简介:王自强(1983 ),男,学士,工程师,主要研究方向为大型精密机床设计与开发㊂E-mail:wzq20034702@163 com㊂通信作者:李江艳,E-mail:janeol@sina com㊂精密直联式主轴系统的结构设计王自强,刘继佼,陈忠良,寸花英,李江艳(沈机集团昆明机床股份有限公司,云南昆明650203)摘要:对不同类型的主轴系统进行分析对比,确定直联式主轴为高精度数控卧式坐标镗床的主轴系统类型;从机床实际的加工工艺需求出发,计算得到不同加工方式下的最大切削力学参数,以此为基础完成主电机与主轴轴承的选型计算;根据主轴系统的功能与精度要求进行结构设计,从而完成精密直联式主轴的完整设计㊂样机的试制与应用验证表明,该直联式主轴的精度与性能水平达到设计要求㊂关键词:直联式主轴;结构设计;坐标镗床中图分类号:TH133 36㊀㊀文献标志码:B㊀㊀文章编号:1001-3881(2018)10-023-3StructureDesignofPrecisionDirect⁃connectedSpindleSystemWANGZiqiang,LIUJijiao,CHENZhongliang,CUNHuaying,LIJiangyan(ShenjiGroupKunmingMachineToolCompanyLimited,KunmingYunnan650203,China)Abstract:Thecharacteristicsofdifferentspindlesystemswereanalyzedandcompared;andthenthedirect⁃connectedspindlesystemwasdeterminedtobeusedinhigh⁃precisionCNChorizontaljigboringmachine.Consideringtherequirementsformachiningprocessofmachinetools,themaximumcuttingmechanicalparameterswerecalculatedunderdifferentprocessingmodes.Basedontheresults,theselectionofmainmotorandspindlebearingswascompleted.Accordingtothefunctionandaccuracyrequirementsofdesignedspindlesystem,thecompletemechanicalstructurewasobtained.Itshowsthatthedesigneddirect⁃connectedspindlesystemcanmeettherequirementsofaccuracyandperformancelevelthroughprototypetestandapplicationverification.Keywords:Direct⁃connectedspindle;Structuredesign;Coordinateboringmachine㊀㊀主轴系统是数控机床最主要的关键核心功能部件,对机床的加工精度和整体性能具有最直接的影响;其功能是实现刀具㊁砂轮或工件旋转,以去除材料的方式进行零件加工[1]㊂因此,在机床的实际设计中,选择合理的主轴结构和科学的设计方法,对提升机床性能㊁控制生产成本均有至关重要的意义㊂机床主轴系统的设计是一个复杂和繁琐的过程,下文将针对精密数控卧式坐标镗床的主轴系统,阐述作者在主轴系统设计中的具体思路㊂1㊀主轴系统的类型与特点数控卧式镗铣机床的主轴系统若以机械结构和主电机的联接形式进行划分,可分为4类:电机直联式㊁同步带式㊁齿轮式和电主轴[2]㊂直联式主轴通过联轴器将主轴末段与主电机输出轴直接相联,传动链短,结构简单,能够实现无间隙传动与电机功率扭矩的高效传递,具有机械效率高㊁回转精度高㊁刚性好及振动小的特点;但相应地,它对主电机及关键配件的性能水平㊁零件加工与装配精度要求均会提高㊂同步带式主轴通过同步带传递电机和主轴之间的功率与扭矩,具有结构紧凑㊁装配简单㊁惯性小和响应快等优势,同时也均有同步带张紧力不易控制㊁低速时重切削能力差㊁主轴高速运转时振动与噪声相比于直联式主轴较大等缺点㊂齿轮式主轴是应用范围最广的传统主轴形式,在电机与主轴之间通过齿轮系传递功率和扭矩,能够传递极高的扭矩,具有优良的重切削性能;但主轴转速不易提升,高速时噪声较大㊂电主轴为电机与主轴融合的产物,实现了机电驱动的一体化,具有高转速㊁低振动㊁动态性能好及有利于产品模块化设计等优点;相对于其他类型的主轴,它对控制㊁润滑和冷却系统的要求较为严格,制造与维护成本较高,同时重切削能力表现较弱,因而通常用于有高转速高精度要求㊁机床规格不大的场合㊂高精度数控卧式坐标镗床主要应用于具有高精度要求的孔㊁平面及复杂轮廓曲面的精加工,对加工精度及稳定性具有极高要求,转速适中,切削余量较小㊂在上述4种主轴系统中,直联式主轴最能契合其性能要求,因而其主轴系统采用直联式结构设计㊂2 参数计算及选型2 1㊀主轴切削力学参数计算高精度数控卧式坐标镗床的加工对象主要为铸件的孔㊁面元素,因而可根据孔㊁面的最大切削工艺要求,分别对铣削㊁镗削和钻削加工条件下主轴所需的切削力㊁切削力矩和切削功率进行计算,从而为主轴系统的后续设计计算和配件选型提供基础㊂表1为所设计机床对主轴系统最大切削加工工艺要求;其中,加工材料为HT300,加工刀具为硬质合金刀具㊂此外,为了提高精铣时零件加工精度和表面加工质量,主轴最高转速设计为6000r/min㊂表1㊀最大加工工艺要求加工方法名称工艺参数铣削刀具参数及铣削用量铣刀直径d0/mm125铣刀齿数Z6切削转速n/(r㊃min-1)500每齿进给量af/(mm㊃齿-1)0.25铣削深度ap/mm2.5铣削宽度ae/mm100镗削刀具参数及铣削用量镗孔直径d/mm200转速n/(r㊃min-1)260每转进给量f/mm0.2切削深度ap/mm2.5钻削刀具参数及铣削用量钻孔直径d/mm30转速n/(r㊃min-1)300进给量S/(mm㊃齿-1)0.2㊀㊀通过查询手册[3],可计算出不同加工方式下的切削力㊁切削扭矩和切削功率,如表2所示㊂表2㊀切削参数计算结果加工方法切削力/N切削扭矩/(N㊃m)切削功率/kW铣削20991316.87镗削675681.8钻削7663614㊀㊀从计算结果可以看出:机床铣削加工时主轴的动力输出达到最大,钻孔加工时主轴的轴向抗力最大㊂2 2㊀主电机选型主电机的选型是以实际切削加工所需扭矩为基础开展的;直联式主轴的传动比为1ʒ1,因而主轴的功率扭矩即为电机的功率扭矩㊂以SIEMENS系统为例,通过专用电机选型软件计算,并考虑低转速区间扭矩范围,确定主电机型号为1PH8137⁃1AD02型,其电机特性曲线如图1所示[4]㊂图1㊀主电机特性曲线对比主电机特性曲线与主轴铣削加工的动力参数要求可知:在500r/min时,主轴运转于电机恒扭矩区间,输出扭矩值为162N㊃m>131N㊃m,满足切削扭矩要求;此时电机功率约为8 5kW>6 87kW,同时满足功率要求㊂此外,电机最高转速可达8000r/min,满足主轴最高转速为6000r/min的设计要求㊂2 3㊀主轴轴承选型主轴轴承的选型计算需综合考虑轴承的配对安装形式㊁切削加工方式以及实际使用中不同加工方式的时间占比,以加工过程中的切削力为基础展开㊂为满足主轴系统的精度要求,主轴轴承选用ISO2精度等级的精密角接触球轴承,采用QBC的布置形式,两个轴承串联为一组,前㊁后两组轴承背对背安装,使主轴具有较大的支撑跨距,从而提升主轴的刚度及抗震性㊂通过计算,最终选定SKF主轴轴承[5],型号为7020CEPA9AQBCA㊂选型计算结果如图2㊁图3所示㊂图2㊀主轴简化模型㊃42㊃机床与液压第46卷图3㊀主轴关键转速图结果表明:采用上述主轴轴承,主轴系统在转速范围内无共振点,且综合寿命较好㊂此外,轴承两端装有集成密封,并填充定量高质低黏度润滑脂,使主轴系统具有良好的密封与润滑性能,提升其热稳定性㊂3㊀结构设计主轴系统是机床完成刀具回转加工的执行机构,因而在结构上须同时实现主轴回转运动与刀具夹持定位的功能;由于对精度要求极高,因而它还应具有冷却结构㊂通过设计,得到直联式主轴系统的详细结构如图4所示,它主要由主轴㊁主轴轴承㊁轴承冷却套㊁松拉刀机构㊁膜片式联轴器和主电机等组成㊂图4㊀直联式主轴结构㊀㊀主轴采用7ʒ24锥度的ISO50#锥孔,按DIN69871刀柄标准规格设计;制造材料为合金结构钢,并渗氮处理,使主轴具有足够的耐磨性,能够实现其良好的精度保持性㊂此外,主轴孔径不超过外径的70%,从而保证主轴具有较高的刚度[6]㊂主轴通过联轴器与主电机相联以传递功率扭矩,实现机床低转速区域的重切削,以及高转速区域的低发热高精度加工,并适用于产生反向推力的螺旋插补的稳定高精度加工㊂联轴器采用无背隙传递额定扭矩钢膜片式联轴器,主轴与电机轴通过涨紧套无间隙连接,强度高㊁扭转刚性好,且具有良好的装配工艺性㊂松拉刀机构主要由碟形弹簧拉刀杆和液压松刀油缸两部分组成,拉刀杆位于主轴内部,松刀油缸位于主轴后端㊂拉刀杆能够在碟形弹簧的弹性力作用下产生相对于主轴的反向位移,使拉爪向后收拢,实现常态下的刀具静态拉紧㊂松刀油缸能够在通电状态下推动拉刀杆产生相对于主轴的正向位移,使拉爪向前张开,实现刀具松开;同时,为保证自动换刀的流畅,松刀时的刀具顶出量一般设置为0 2 1mm[7]㊂冷却套外轮廓面分布有螺旋状冷却槽,通过恒温冷却系统控制冷却介质在槽内循环流动,能够传导主轴轴承产生的热量,并均衡主轴系统内部的温度场分布,控制主轴温升与热变形,有利于热误差补偿的开展,提升主轴系统的精度与热稳定性㊂4㊀结论精密直联式主轴设计首先从机床的实际加工工艺需求出发,计算主轴所需的切削力学参数,进而在此基础上完成主电机与主轴轴承的计算选型;而后根据主轴系统的功能与精度要求,设计出详细的机械结构㊂通过国家专项中相关样机的试制与应用验证,结果表明:该结构的直联式主轴能够满足高精度数控卧式坐标镗床的设计与加工要求,具有很高的精度与性能水平㊂参考文献:[1]熊万里.我国高性能机床主轴技术现状分析[J].金属加工(冷加工),2011(18):5-11.[2]聂浩锋,李德恒.浅谈机床主轴的差异化特性[J].科技与创新,2016(11):94-95.[3]张耀宸.机械加工工艺设计实用手册[M].北京:航空工业出版社,1993:1300-1366.[4]SIEMENS公司.SIMOTICSM⁃1PH8主电机选型手册[M],2012.[5]SKF公司.超精密轴承[Z],2014.[6]戴署.金属切削机床[M].北京:机械工业出版社,1993:187.[7]敖立文.现代机床高速主轴概述[J].设备管理与维修2015(1):66-70.㊃52㊃第10期王自强等:精密直联式主轴系统的结构设计㊀㊀㊀。