FDS 工艺介绍
FDS技术介绍

可用螺纹长度b 取决于板厚S1 和 S2: b = S1 + 3 x S2 (无导向孔) b = S1 + 2 x S2 (有导向孔和)
FLOWFORM®技术资料
- 三层铝板接头截面: 1.0 mm + 2.0 mm + 2.0 mm - 有导向孔的连接
Source: Arnold Umformtechnik
● 生产在一个静态工作站自动进行
● 同样使用在 Audi TT, A4, A6L, A7, A8, S4, S5, R8
Thank you!
感谢下 载
高效率和控制成本。
钻尾螺钉即具有高螺纹负载比又具有较高的性价比
EJOT FDS® 螺钉
•
高螺纹负载比例
•
高装配安全性
•
高强度
•
动态安全性
•
适于多次重复装配
•
有无导向孔均可使用
•
成本优势
FDS® 螺钉的特征
能从内部或外部拧紧的螺钉头
负载螺纹
螺纹形成区 圆柱状区域 钻孔区域 螺钉尖端
在没有预冲孔和夹具作用的条件下FDS®螺钉装配的工艺过程
螺钉装配动图5
RSF20
螺钉装配动图6
RSF20
螺钉装配动图7
RSF20
螺钉装配动图8
RSF20
螺钉装配动图9
RSF20
螺钉装配动图10
RSF20
螺钉装配动图11
RSF20
螺钉装配动图12
RSF20
螺钉装配动图13
RSF20
螺钉装配动图14
RSF20
螺钉装配动图15
RSF20
螺钉装配动图16
= hold-down (clamp/device)
FDS技术介绍范文
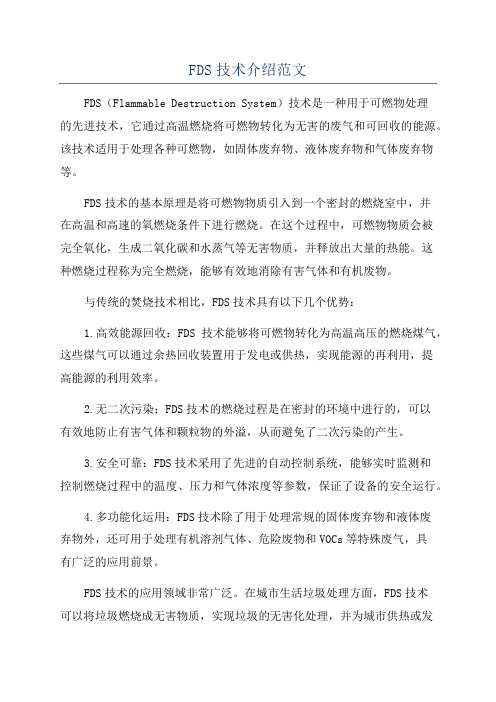
FDS技术介绍范文FDS(Flammable Destruction System)技术是一种用于可燃物处理的先进技术,它通过高温燃烧将可燃物转化为无害的废气和可回收的能源。
该技术适用于处理各种可燃物,如固体废弃物、液体废弃物和气体废弃物等。
FDS技术的基本原理是将可燃物物质引入到一个密封的燃烧室中,并在高温和高速的氧燃烧条件下进行燃烧。
在这个过程中,可燃物物质会被完全氧化,生成二氧化碳和水蒸气等无害物质,并释放出大量的热能。
这种燃烧过程称为完全燃烧,能够有效地消除有害气体和有机废物。
与传统的焚烧技术相比,FDS技术具有以下几个优势:1.高效能源回收:FDS技术能够将可燃物转化为高温高压的燃烧煤气,这些煤气可以通过余热回收装置用于发电或供热,实现能源的再利用,提高能源的利用效率。
2.无二次污染:FDS技术的燃烧过程是在密封的环境中进行的,可以有效地防止有害气体和颗粒物的外溢,从而避免了二次污染的产生。
3.安全可靠:FDS技术采用了先进的自动控制系统,能够实时监测和控制燃烧过程中的温度、压力和气体浓度等参数,保证了设备的安全运行。
4.多功能化运用:FDS技术除了用于处理常规的固体废弃物和液体废弃物外,还可用于处理有机溶剂气体、危险废物和VOCs等特殊废气,具有广泛的应用前景。
FDS技术的应用领域非常广泛。
在城市生活垃圾处理方面,FDS技术可以将垃圾燃烧成无害物质,实现垃圾的无害化处理,并为城市供热或发电提供可再生能源。
在危险废物处理方面,FDS技术可以将危险废物彻底转化为无害物质,避免了对环境和人体的污染。
在化工和制药行业中,FDS技术可以用于处理有机溶剂和VOCs废气,减少有机污染物的排放,保护环境和员工的健康。
尽管FDS技术在可燃物处理方面具有许多优势,但也存在一些挑战。
首先是设备的高成本和复杂性,需要投入较大的资金和技术支持。
其次,对于特殊的废气处理场景,FDS技术需要根据不同的情况进行定制设计,增加了工程的复杂性和难度。
FDS连接工艺在车身轻量化中的应用研究

种 超高 强 度钢 板 ,替 代 传统 钢 板构 件 或组 件 ,实现
某 种意 义 上讲 ,紧 固件 的 多样 性反 应 了一 套 紧
车身 框架结 构的轻 量化和高 强度 。
固件 系统的 成熟程度 及加工 能力 。
在 汽 车工 业 ,连 接铝 材 的 主要 方 式有 传 统 的机
通 过 对 多 种 不 同 形 状 规 格 的 热 融 自 攻 丝 钉
特 征 。同 时 ,FDS周 期 时间 短 ,材 料处 理少 ,所有 螺 钉头 、螺钉 头下 的 凹承 区 、钉杆 的承 力 螺 纹 区 、
的工 序都可 以集成 为简单 自动的过 程 。
钉 杆螺 纹 成型 区和 钉 杆 尾尖 ,其 中 ,尾尖 部 分形 成
挤 出环 颈 和衬 套特 征 ,螺纹 成 型 区部 分形 成 螺纹 ,
力产 生很 高 的热 量 ,会软 化 钣金 材料 ,使得 FDS螺 削膏的涂 抹是必 须的 。
钉可 以穿 透钣 金 ,获 得一 个 合理 的 紧 固力 。FDS是
FDS螺 钉 既 作 为 钻 头 又 可 以起 到而 来 ,可 以 形成 同 样类 型 的衬 套 用 ,FDS螺 钉特 征 主要可 以 分为 5个部 分 ,如 图2:
性 高 ,但 是 受限于 不能 连接 异种金 属 。这2种 工艺都
目前 FDS螺 钉 的 采 购 主 要 还 是 以 国 外 进 口为
要 求 双边 可达 ,这使 设计 受 限严 重 。FDS工艺 是可 主 ,这类 钉子 使 用特 殊 配 方的 硬质 合 金 材料 制 成 ,
以解决这 个双边 可达 问题 ,使 设计更 宽裕 。
械 紧 固SPR ̄EI电阻 点焊 RSW 。SPR是 一种 稳 健而 (FDS螺 钉 )夹 持装 置 的定 制 ,可 以选 用多 种 不 同
“流钻螺钉”(FDS)工艺
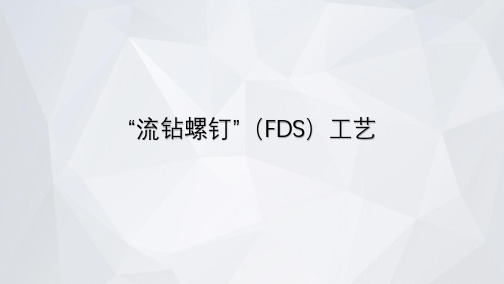
BMW 8 Series Coupe
Jaguar I-PACE
五、 FDS工艺的优、缺点
优点: 1、可连接的材料种类多,包括超高强钢、铝镁合金、复合材料在内 的异种材料; 2、单面操作,可用于封闭型腔结构、壁厚大或封闭腔体,无法使用 SPR或Clinching; 3、板件被加热,板件与螺钉接触好,连接强度大。 4、 螺钉可拆卸,回收方便,可使用公制螺栓进行返修。 5、工作环境清洁,无火花、碎屑,几乎无噪声。 缺点 1、设备系统成本远高于电阻点焊,铆钉成本高(单价 0.15 欧元) ; 2、单面施力,连接时需要高强度刚性支撑; 3、工艺完成后材料正反面均有较大凸起,同时大量使用会增加车身 自重(M5单个螺钉重4~5g,而SPR铆钉约0.3~0.8g) 4、CT时间长,约为2~6S(部分设备优化可达到1.5~3S,取决于板材 厚度)
六、FDS常见缺陷:
Hale Waihona Puke 缺失/位置错误螺栓断裂/破损
边距过小
头部间隙
FDS返修方法: 在缺陷螺钉附近重新打一个螺钉。
七、设备系统组成:
4.
2.
FDS两种标准枪
Standard Length
Reduced Length
二、 FDS工艺历史
FDS发明于1990年,1996年首次应用于莲花轿车车身框架的连接。由于当时采用的主 要是手持夹具进行装夹,整个装配过程的时间和精度不好控制,使得该工艺使用受到限 制。 20世纪90年代末,巍博(Weber)为EJOT公司开发了RSF20S螺钉驱动系统,此系 统的问世实现了FDS工艺的自动化生产,并可以增大连接的板材总厚度,于2000年首次 应用在奥迪A4后轮罩的连接上。
三、 FDS工艺的过程
FDS连接工艺过程包括六个阶段:旋转(加热)→穿透→通孔→攻螺纹→拧螺纹→紧固。
铝合金热熔自攻丝工艺与性能研究
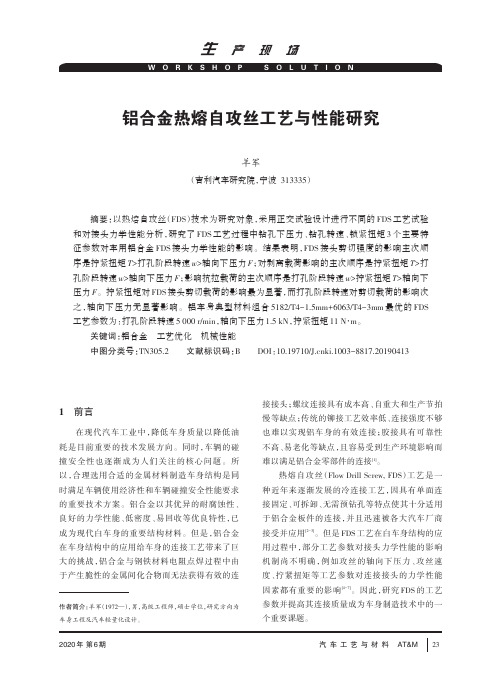
摘要:以热熔自攻丝(FDS )技术为研究对象,采用正交试验设计进行不同的FDS 工艺试验和对接头力学性能分析,研究了FDS 工艺过程中钻孔下压力、钻孔转速、锁紧扭矩3个主要特征参数对车用铝合金FDS 接头力学性能的影响。
结果表明,FDS 接头剪切强度的影响主次顺序是拧紧扭矩T >打孔阶段转速w >轴向下压力F ;对剥离载荷影响的主次顺序是拧紧扭矩T >打孔阶段转速w >轴向下压力F ;影响抗拉载荷的主次顺序是打孔阶段转速w >拧紧扭矩T >轴向下压力F 。
拧紧扭矩对FDS 接头剪切载荷的影响最为显著,而打孔阶段转速对剪切载荷的影响次之,轴向下压力无显著影响。
铝车身典型材料组合5182/T4-1.5mm+6063/T4-3mm 最优的FDS 工艺参数为:打孔阶段转速5000r/min ,轴向下压力1.5kN ,拧紧扭矩11N∙m 。
关键词:铝合金工艺优化机械性能中图分类号:TN305.2文献标识码:BDOI :10.19710/ki.1003-8817.20190413铝合金热熔自攻丝工艺与性能研究羊军(吉利汽车研究院,宁波313335)作者简介:羊军(1972—),男,高级工程师,硕士学位,研究方向为车身工程及汽车轻量化设计。
1前言在现代汽车工业中,降低车身质量以降低油耗是目前重要的技术发展方向。
同时,车辆的碰撞安全性也逐渐成为人们关注的核心问题。
所以,合理选用合适的金属材料制造车身结构是同时满足车辆使用经济性和车辆碰撞安全性能要求的重要技术方案。
铝合金以其优异的耐腐蚀性、良好的力学性能、低密度、易回收等优良特性,已成为现代白车身的重要结构材料。
但是,铝合金在车身结构中的应用给车身的连接工艺带来了巨大的挑战,铝合金与钢铁材料电阻点焊过程中由于产生脆性的金属间化合物而无法获得有效的连接接头;螺纹连接具有成本高、自重大和生产节拍慢等缺点;传统的铆接工艺效率低、连接强度不够也难以实现铝车身的有效连接;胶接具有可靠性不高、易老化等缺点,且容易受到生产环境影响而难以满足铝合金零部件的连接[1]。
白车身FDS连接技术浅谈
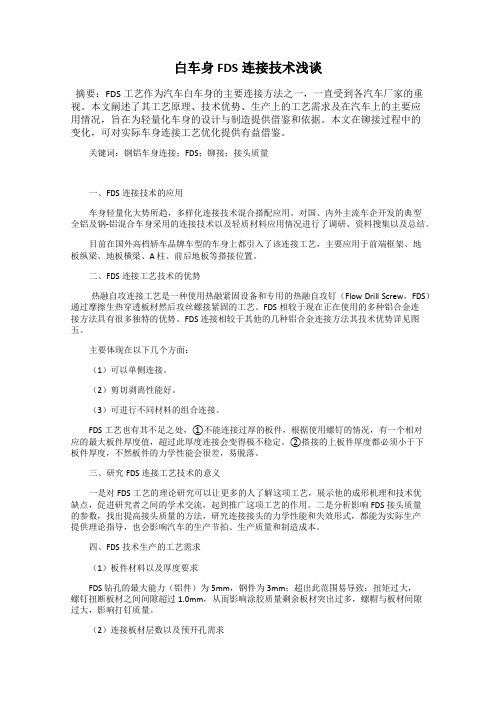
白车身FDS连接技术浅谈摘要:FDS工艺作为汽车白车身的主要连接方法之一,一直受到各汽车厂家的重视。
本文阐述了其工艺原理、技术优势、生产上的工艺需求及在汽车上的主要应用情况,旨在为轻量化车身的设计与制造提供借鉴和依据。
本文在铆接过程中的变化,可对实际车身连接工艺优化提供有益借鉴。
关键词:钢铝车身连接;FDS;铆接;接头质量一、FDS连接技术的应用车身轻量化大势所趋,多样化连接技术混合搭配应用。
对国、内外主流车企开发的典型全铝及钢-铝混合车身采用的连接技术以及轻质材料应用情况进行了调研、资料搜集以及总结。
目前在国外高档轿车品牌车型的车身上都引入了该连接工艺,主要应用于前端框架、地板纵梁、地板横梁、A 柱、前后地板等搭接位置。
二、FDS连接工艺技术的优势热融自攻连接工艺是一种使用热融紧固设备和专用的热融自攻钉(Flow Drill Screw,FDS)通过摩擦生热穿透板材然后攻丝螺接紧固的工艺。
FDS相较于现在正在使用的多种铝合金连接方法具有很多独特的优势。
FDS连接相较于其他的几种铝合金连接方法其技术优势详见图五。
主要体现在以下几个方面:(1)可以单侧连接。
(2)剪切剥离性能好。
(3)可进行不同材料的组合连接。
FDS工艺也有其不足之处,①不能连接过厚的板件,根据使用螺钉的情况,有一个相对应的最大板件厚度值,超过此厚度连接会变得极不稳定。
②搭接的上板件厚度都必须小于下板件厚度,不然板件的力学性能会很差,易脱落。
三、研究FDS连接工艺技术的意义一是对FDS工艺的理论研究可以让更多的人了解这项工艺,展示他的成形机理和技术优缺点,促进研究者之间的学术交流,起到推广这项工艺的作用。
二是分析影响FDS接头质量的参数,找出提高接头质量的方法,研究连接接头的力学性能和失效形式,都能为实际生产提供理论指导,也会影响汽车的生产节拍、生产质量和制造成本。
四、FDS技术生产的工艺需求(1)板件材料以及厚度要求FDS 钻孔的最大能力(铝件)为5mm,钢件为3mm;超出此范围易导致:扭矩过大,螺钉扭断板材之间间隙超过1.0mm,从而影响涂胶质量剩余板材突出过多,螺帽与板材间隙过大,影响打钉质量。
fds工艺技术要求

fds工艺技术要求FDS (Flexible Display System) 是一种新型显示技术,其具备柔性和可弯曲的特点,可以广泛应用于智能手机、平板电脑、电子书等电子产品中。
FDS 技术要求具体包括以下几点:1. 基质技术要求:FDS 的基质是柔性的,需要能够长时间保持其形状和弯曲性,在弯曲过程中不产生损伤。
基质材料的选择应具备高弯曲性能、高耐疲劳性、稳定的机械性能以及良好的耐高温性,以确保显示屏的可靠性和耐用性。
2. 线路设计要求:FDS 的线路是采用柔性基板上的导线连接显示模块,需要考虑线路的柔性和导电性能。
线路设计应合理布局,确保其能够适应显示屏的弯曲和摺叠,防止线路脱落和短路等问题的发生。
此外,线路材料也应具备良好的绝缘性能和抗氧化性,以提高线路的可靠性和稳定性。
3. 电子元器件要求:FDS 中的电子元器件需要具备柔性和可靠性。
传统硬性组件在FDS中一般需要进行转化,例如使用柔性电路板替代刚性电路板,使用柔性电解质电容器替代刚性电解质电容器等。
电子元器件的选择应考虑到其对柔性显示屏的适应性和稳定性,以确保显示屏的正常工作。
4. 生产工艺要求:FDS 的生产工艺需要具备高精度和高效率。
生产工艺要求包括基质制备、线路制备、元器件安装和封装等环节。
基质制备需要采用适合的材料和加工工艺,确保基质的柔性和稳定性。
线路制备需要采用精确的工艺和设备,确保线路的质量和稳定性。
元器件安装和封装要求快速、准确、可靠,以提高生产效率和产品质量。
5. 质量控制要求:FDS 的质量控制需要严格把控各个环节的质量,包括原材料的质量评估、制造过程的质量控制和成品的质量检测。
原材料的质量评估需从供应商处获取相关认证和检测报告。
制造过程的质量控制需要建立完善的生产控制流程和质量检测手段,确保生产过程的稳定性和产品的一致性。
成品的质量检测需要采用多种手段,包括外观检测、电性能测试、可靠性测试等,以确保产品符合相关规范和标准。
“流钻螺钉”(FDS)工艺

流钻螺钉 (FDS) 工艺1. 引言流钻螺钉(FDS)工艺是一种常见的金属加工技术,用于在螺钉中切削连续螺纹,并提供更好的连接强度和密封性能。
FDS工艺通常应用于制造高质量的螺钉,用于各种工业和建筑领域。
本文将介绍流钻螺钉工艺的基本原理、材料要求以及其应用。
2. 工艺原理流钻螺钉(FDS) 工艺是一种通过将积极切削工具(如钻头)移动到螺纹表面上,使用旋转运动来切削或修整金属材料的金属加工方法。
该工艺适用于所有类型的螺纹设计,包括粗螺纹、细螺纹和特殊螺纹。
FDS工艺的最大优势是切削过程中无需预先开孔,从而提高了生产效率。
切削过程中,金属材料被制造螺纹的工具逐渐削除,直到形成所需的螺纹形状和规格。
3. 材料要求在流钻螺钉 (FDS) 工艺中,选择适当的材料对于最终产品的质量和性能至关重要。
一般来说,常用的螺钉材料包括碳钢、不锈钢、黄铜和铝。
材料选择时需考虑以下几个因素: - 强度和刚度:确保螺钉足够强度和刚性,能够承受所需的负荷。
- 耐腐蚀性:根据使用环境选择合适的耐腐蚀性能,以保证产品的使用寿命。
- 加工性能:选择易于加工而且能够满足切削要求的材料。
- 美观性:如果螺钉需要暴露在外部,外观方面也需要考虑。
4. FDS工艺步骤FDS工艺的步骤如下:1. 准备材料:选择适当的螺钉材料,并切割成合适的长度。
2. 加工设备准备:安装切削工具并调整其位置和角度。
确保工具能够准确地切削所需的螺纹尺寸。
3. 加工过程:将螺钉放置在夹具中,开始加工。
慢慢将切削工具移到螺纹表面上,旋转工具以切削金属,并逐渐形成螺纹。
4. 检验和修整:检查加工后的螺钉是否符合要求。
如有需要,可以使用其他工具进行修整,以确保螺纹质量。
5. 清洁和包装:清洁并包装好加工后的螺钉,准备发货或存储。
5. 应用领域FDS工艺广泛应用于各个领域,例如: - 建筑和施工:用于连接结构和构件,提供安全可靠的连接性能。
- 汽车工业:用于制造汽车零部件,如引擎、底盘和座椅。
FDS技术介绍
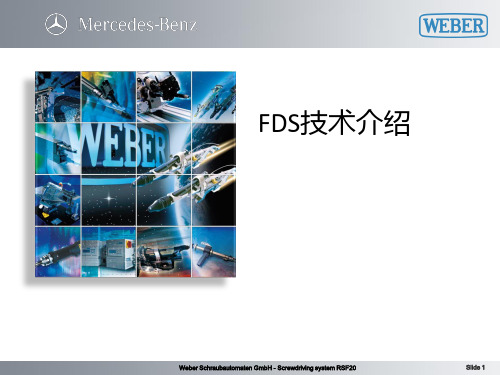
Slide 41
FDS对机器人的要求
通过改变适配器与螺钉装配系统的连接进行优化 :
- 螺钉装配系统通过这样的连接避免机器人的5 轴受到扭矩
- 不会发生滑脱:
轴不会受到加工力 造成的扭矩影响
F = 加工力
- 缺点: 限制了活动范围
Weber Schraubautomaten GmbH - Screwdriving system RSF20
Weber Schraubautomaten GmbH - Screwdriving system RSF20
Slide 14
对接系统的机器人接口
Weber Schraubautomaten GmbH - Screwdriving system RSF20
Slide 15
Weber Schraubautomaten GmbH - Screwdriving system RSF20
Slide 2
概述
• 薄板金属材料的连接技术 • FDS® 螺钉装配的工艺过程 • FDS 自动装配过程的控制 • 对机器人的要求 • 应用范例
Weber Schraubautomaten GmbH - Screwdriving system RSF20
Slide 3
什么是FDS呢?
这是一项全新的技术,被世界上很多大 型汽车公司应用于白车身的组装,可提
Slide 30
RSF20 螺钉装配动图12
Weber Schraubautomaten GmbH - Screwdriving system RSF20
Slide 31
RSF20 螺钉装配动图13
Weber Schraubautomaten GmbH - Screwdriving system RSF20
FDS膨胀纤维抗裂防水剂综合施工标准工艺

FDS膨胀纤维抗裂防水剂施工工艺技术特点FDS膨胀纤维抗裂防水剂1、FDS膨胀纤维抗裂防水剂是由聚丙烯纤维,无机硅粉和添加多种改性复合而成旳多功能外加剂,产品具有微膨胀性能和阻裂纤维旳共同长处,同步尚有高抗裂,高抗渗旳超叠加效应,是一种机理完善,性能卓越旳复合材料。
2、技术特点(1)双重保护、双重功能:FDS膨胀纤维抗裂防水剂可从物理和化学两方面提高混凝土旳抗裂能力,为混凝土提供双重保护,一方面,数量众多旳合成纤维产生微细配筋及网状承托旳作用,克制了混凝土旳开裂进程;另一方面,膨胀组分与水泥水化产物发生化学反映并产生适度膨胀,可避免混凝土收缩开裂;(2)阶段抗裂、层次抗裂:微膨胀剂重要在混凝土硬化过程发生作用,而聚丙烯纤维则重要在混凝土塑性阶段发挥作用。
FDS膨胀纤维抗裂防水剂将两者复合体现了“阶段抗裂、层次抗裂”科学理念,可达到全程抗裂旳目旳,它们从不同层面,以不同方式,在不同步段对混凝土作出最有效旳奉献;(3)膨胀纤维抗裂防水剂产品掺入混凝土中后,依托纤维在混凝土中巨大数量旳均匀分布,在混凝土内部构成一种均匀旳乱向支撑体系,从而产生一种有效旳二级加强效果,并有助于削减混凝土塑性收缩及冻缩及冻融时旳应力。
收缩旳能量被分散到每立方米上千万条具有高抗拉强度而弹性模量相对较低旳纤维单丝上,从而有效增强了混凝土旳韧性,克制了微细裂缝旳产生和发展。
同步,无数纤维单丝旳加入可有效阻碍骨料旳离析,保证了混凝土初期旳均匀泌水性,从而阻碍了沉降裂纹旳形成。
实践证明,掺入该产品旳混凝土与一般混凝土相比较,其抗裂能力提高75%;(4)大大提高混凝土旳抗渗防水性能。
掺入大量微细纤维可以有效地克制混凝土初期干缩微裂及离析裂纹旳产生及发展,极大减少了混凝土旳收缩裂缝,特别是有效克制了连通裂缝旳产生。
均匀分布在混凝土中彼此相粘连旳大量纤维起了“承托”骨料旳作用,这样有效减少了混凝土表面旳析水与集料旳离析,从而使混凝土中直径为50~100纳米和不小于100纳米旳孔隙旳含量大大减少,可以极大地提高抗渗能力,与一般混凝土相比较,抗渗能力提高60%~75%;(5)增强抗冲击及抗震能力。
FDS热融自攻丝铆接系统

热融自攻丝FDS铆接系统Stoger 7501 FSF系统外观图热融自攻丝FDS铆接系统(Flow drill screw, FDS)发明于1990年,1996年首次应用于莲花轿车车身框架的连接。
由于采用手持夹具进行装夹,整个装配过程的时间和精度不好控制,使得该工艺使用受到限制。
20世纪90年代末,Weber Schraubautomaten为EJOT公司开发了RSF20S螺钉驱动系统,RSF20S的问世实现了FDS工艺的自动化生产,并增大了可连接板材的厚度,于2000年首次用于Audi A4后轮罩连接。
在过去五年中,许多欧洲汽车厂商开始使用FDS技术,如捷豹XK和X150,奥迪R8, A8, TT Coupe,A6等,其中新奥迪A8上有多达740个流钻螺钉。
欧洲的尼桑、路虎、保时捷、宝马等众多汽车品牌也都引入了流钻螺钉连接工艺。
目前全球已经有德国、意大利、英国、丹麦、匈牙利、波兰六个国家在汽车中使用了该技术。
如图所示,FDS工艺通过螺钉的高速旋转软化待连接板材,并在巨大的轴向压力作用下挤压并旋入待连接板材,最终在板材与螺钉之间形成螺纹连接,而中心孔处的母材则被挤出并在下层板的底部形成一个环状套管。
其优点是:①因为螺钉不需要变形,因此可以用来连接包括超高强钢、铝镁合金、复合材料在内的任何材料及异种材料;②螺钉高速旋转可以软化金属,因此可在较小变形的情况下实现单边连接,使得连接更加方便;③铆钉可以拆卸,回收方便。
但是该方法也有其明显的缺点:①因为下层板要钻穿,因此接头的防腐蚀能力会降低;②工艺结束后螺钉前端必须露出于挤出套管之外,加上尖头的过渡部分,使得螺钉尺寸较长,如果大量使用会增加车身自重,同时过长的露出部分也会对车身的设计与制造产生影响。
除WEBER外,又一世界重量级装配连接系统专家-STOGER推出重量级FDS产品7501 FSF 系统:德国STOGER热融自攻丝铆接系统铆头FSF系统的控制单元各种各样的热融自攻丝紧固件。
FDS线槽技术在现代建筑中的应用

FDS线槽技术在现代建筑中的应用摘要:地面线槽布线专门为现代化建筑物布线复杂、出线口位置变化不定推出的一种新型的布线方式,本文根据施工经验和现场的环境,给出了一种快速、有效的地面线槽的设计施工方法,供现代建筑设计施工参考。
关键词:现代建筑;地面布线系统;建筑电气安装0 引言FDS(Floor disposal system)地面布线系统是由线槽、分线盒、插座(出线)箱、各种连接件组成的,为现代化建筑物综合布线系统提供电路交通桥、出口和维修站。
地面线槽是一种封闭的、直接隐蔽于地板砖或大理石面的金属槽,可以灵活方便地提供电源、电话、电视、计算机、话筒等线缆传输电能和信号接口。
使用者可以随时打开盖板,接通所需的电源和信息,不用时关上盖板与地面平齐,不影响室内办公设施的布置和人员的通道。
在自动化办公场所、会议室、计算机机房等大空间且隔断多、用电设备移动性大、敷设多功能线路的场所有很好的应用。
1、工程概况某地高新区创业大厦项目,建筑高度133米,为高层一类公共建筑。
其中地下两层建筑面积37187.4㎡,局部设夹层,地上30层建筑面积112144.5㎡,总建筑面积149331.9㎡,是该区的标志性建筑。
首层、二层为政务大厅、多功能厅、报告厅会议及办公,三到三十层为会议及办公室。
该工程多为办公会议室,要求空间分割灵活,信息点引出方便,尽量避免长距离临时拉线,且安装项目工期较短、工种多、任务重。
办公场所使用设备和最大容纳的人数已定,但设施摆放的具体位置没有确定。
在保证项目工期尽快完成前提下,建设单位要求设计、土建、安装、装饰协调,用一合适的布线系统完成该情况下施工任务。
2、通用地面线槽设计及敷设简介图1地面线槽示意图地面线槽采用优质钢板加工成型的,由槽盖和槽底组成的全封闭高强度矩形钢管,其示意图如图1所示。
地面线槽的设计要满足建筑物设备近期和发展需要,根据所需回路的穿线根数、横截面积和工艺要求确定线槽的规格及槽数。
FDS技术在钢铝混合车身上的应用
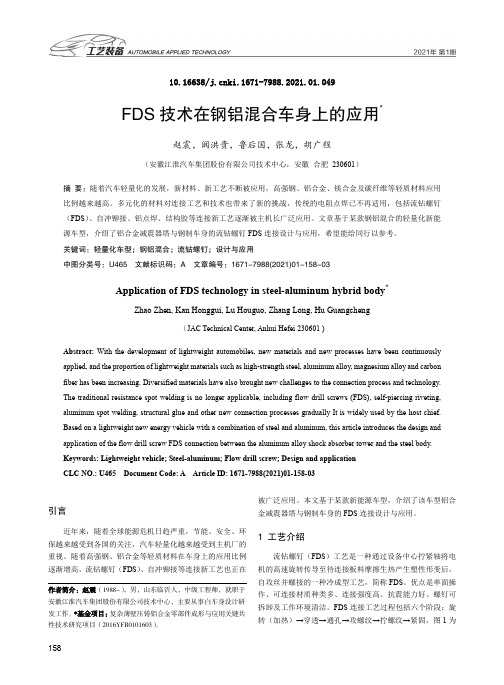
10.16638/ki.1671-7988.2021.01.049FDS技术在钢铝混合车身上的应用*赵震,阚洪贵,鲁后国,张龙,胡广程(安徽江淮汽车集团股份有限公司技术中心,安徽合肥230601)摘要:随着汽车轻量化的发展,新材料、新工艺不断被应用,高强钢、铝合金、镁合金及碳纤维等轻质材料应用比例越来越高。
多元化的材料对连接工艺和技术也带来了新的挑战,传统的电阻点焊已不再适用,包括流钻螺钉(FDS)、自冲铆接、铝点焊、结构胶等连接新工艺逐渐被主机长广泛应用。
文章基于某款钢铝混合的轻量化新能源车型,介绍了铝合金减震器塔与钢制车身的流钻螺钉FDS连接设计与应用,希望能给同行以参考。
关键词:轻量化车型;钢铝混合;流钻螺钉;设计与应用中图分类号:U465 文献标识码:A 文章编号:1671-7988(2021)01-158-03Application of FDS technology in steel-aluminum hybrid body*Zhao Zhen, Kan Honggui, Lu Houguo, Zhang Long, Hu Guangcheng(JAC Technical Center, Anhui Hefei 230601 )Abstract:With the development of lightweight automobiles, new materials and new processes have been continuously applied, and the proportion of lightweight materials such as high-strength steel, aluminum alloy, magnesium alloy and carbon fiber has been increasing. Diversified materials have also brought new challenges to the connection process and technology. The traditional resistance spot welding is no longer applicable, including flow drill screws (FDS), self-piercing riveting, aluminum spot welding, structural glue and other new connection processes gradually It is widely used by the host chief. Based on a lightweight new energy vehicle with a combination of steel and aluminum, this article introduces the design and application of the flow drill screw FDS connection between the aluminum alloy shock absorber tower and the steel body. Keywords: Lightweight vehicle; Steel-aluminum; Flow drill screw; Design and applicationCLC NO.: U465 Document Code: A Article ID: 1671-7988(2021)01-158-03引言近年来,随着全球能源危机日趋严重,节能、安全、环保越来越受到各国的关注,汽车轻量化越来越受到主机厂的重视。
白车身新材料连接工艺介绍
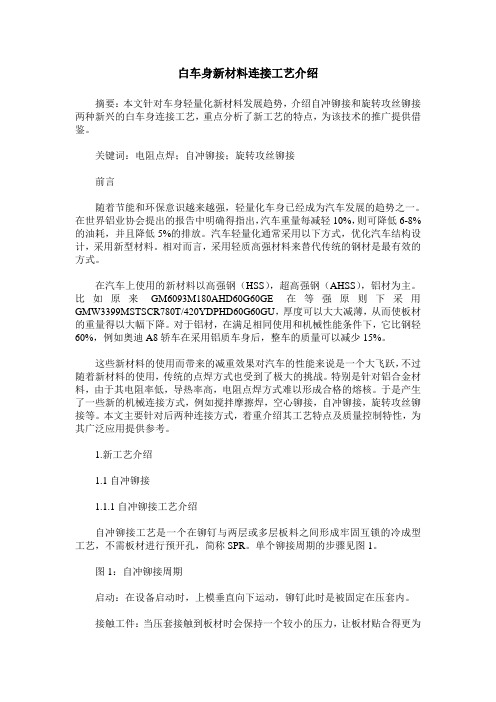
白车身新材料连接工艺介绍摘要:本文针对车身轻量化新材料发展趋势,介绍自冲铆接和旋转攻丝铆接两种新兴的白车身连接工艺,重点分析了新工艺的特点,为该技术的推广提供借鉴。
关键词:电阻点焊;自冲铆接;旋转攻丝铆接前言随着节能和环保意识越来越强,轻量化车身已经成为汽车发展的趋势之一。
在世界铝业协会提出的报告中明确得指出,汽车重量每减轻10%,则可降低6-8%的油耗,并且降低5%的排放。
汽车轻量化通常采用以下方式,优化汽车结构设计,采用新型材料。
相对而言,采用轻质高强材料来替代传统的钢材是最有效的方式。
在汽车上使用的新材料以高强钢(HSS),超高强钢(AHSS),铝材为主。
比如原来GM6093M180AHD60G60GE在等强原则下采用GMW3399MSTSCR780T/420YDPHD60G60GU,厚度可以大大减薄,从而使板材的重量得以大幅下降。
对于铝材,在满足相同使用和机械性能条件下,它比钢轻60%,例如奥迪A8轿车在采用铝质车身后,整车的质量可以减少15%。
这些新材料的使用而带来的减重效果对汽车的性能来说是一个大飞跃,不过随着新材料的使用,传统的点焊方式也受到了极大的挑战。
特别是针对铝合金材料,由于其电阻率低,导热率高,电阻点焊方式难以形成合格的熔核。
于是产生了一些新的机械连接方式,例如搅拌摩擦焊,空心铆接,自冲铆接,旋转攻丝铆接等。
本文主要针对后两种连接方式,着重介绍其工艺特点及质量控制特性,为其广泛应用提供参考。
1.新工艺介绍1.1自冲铆接1.1.1自冲铆接工艺介绍自冲铆接工艺是一个在铆钉与两层或多层板料之间形成牢固互锁的冷成型工艺,不需板材进行预开孔,简称SPR。
单个铆接周期的步骤见图1。
图1:自冲铆接周期启动:在设备启动时,上模垂直向下运动,铆钉此时是被固定在压套内。
接触工件:当压套接触到板材时会保持一个较小的压力,让板材贴合得更为紧密,同时压套内铆钉在冲头的推动下,位置开始发生变化。
铆接前半周期:板材和铆钉在冲头的推动下,依照下模内腔的轮廓逐渐形成接头。
fds工艺在电池包壳体连接中的应用研究
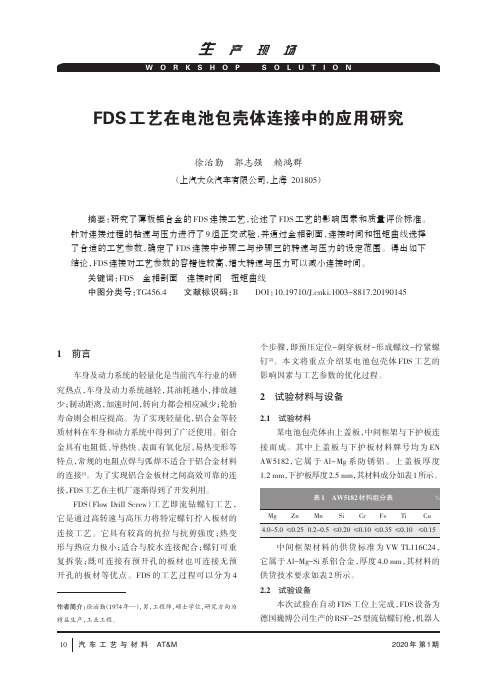
摘要:研究了薄板铝合金的FDS 连接工艺,论述了FDS 工艺的影响因素和质量评价标准。
针对连接过程的钻速与压力进行了9组正交试验,并通过金相剖面,连接时间和扭矩曲线选择了合适的工艺参数,确定了FDS 连接中步骤二与步骤三的转速与压力的设定范围。
得出如下结论,FDS 连接对工艺参数的容错性较高,增大转速与压力可以减小连接时间。
关键词:FDS金相剖面连接时间扭矩曲线中图分类号:TG456.4文献标识码:BDOI :10.19710/ki.1003-8817.20190145FDS 工艺在电池包壳体连接中的应用研究徐治勤郭志强赖鸿群(上汽大众汽车有限公司,上海201805)作者简介:徐治勤(1974年—),男,工程师,硕士学位,研究方向为精益生产,工业工程。
1前言车身及动力系统的轻量化是当前汽车行业的研究热点,车身及动力系统越轻,其油耗越小,排放越少;制动距离,加速时间,转向力都会相应减少;轮胎寿命则会相应提高。
为了实现轻量化,铝合金等轻质材料在车身和动力系统中得到了广泛使用。
铝合金具有电阻低、导热快、表面有氧化层,易热变形等特点,常规的电阻点焊与弧焊不适合于铝合金材料的连接[1]。
为了实现铝合金板材之间高效可靠的连接,FDS 工艺在主机厂逐渐得到了开发利用。
FDS (Flow Drill Screw )工艺即流钻螺钉工艺,它是通过高转速与高压力将特定螺钉拧入板材的连接工艺。
它具有较高的抗拉与抗剪强度;热变形与热应力极小;适合与胶水连接配合;螺钉可重复拆装;既可连接有预开孔的板材也可连接无预开孔的板材等优点。
FDS 的工艺过程可以分为4个步骤,即预压定位-刺穿板材-形成螺纹-拧紧螺钉[2]。
本文将重点介绍某电池包壳体FDS 工艺的影响因素与工艺参数的优化过程。
2试验材料与设备2.1试验材料某电池包壳体由上盖板,中间框架与下护板连接而成。
其中上盖板与下护板材料牌号均为EN AW5182,它属于Al-Mg 系防锈铝。
FDS工艺介绍

FDS工艺介绍FDS(Front End Schedule,前端排期)工艺是一种项目管理工艺,主要用于计划和控制项目的前期工作。
该工艺在项目开始前制定项目计划、交付物、资源需求和时间表,并根据实际进展情况进行调整和更新。
本文将详细介绍FDS工艺的原理、流程和应用。
FDS工艺的原理是在项目开始前的前期规划阶段,通过制定详细的计划和时间表,确保项目能够按时交付,并减少不必要的风险。
通过FDS工艺,项目管理人员可以清楚地了解项目的范围、目标和关键路径,在充分了解项目需求的基础上,合理分配资源和制定项目进度计划。
1.编制项目计划和时间表:项目管理人员在项目开始前会根据项目的需求和目标,制定详细的项目计划和时间表。
这些计划和时间表包括项目的范围、进度、资源需求等信息,以确保项目能够按时交付。
2.制定交付物和阶段性目标:在项目计划中,项目管理人员会明确项目的交付物和阶段性目标。
通过清晰地定义这些目标,可以使项目团队更好地明确工作内容和优先级,并有效地推进项目进展。
3.分配资源和人力:根据项目的需求和计划,项目管理人员会适当分配和调整项目所需的资源和人力。
这包括分配专门的项目经理和团队成员,确保项目进展顺利。
4.监控和调整进度:在项目实施过程中,项目管理人员会根据实际进展情况,不断监控和调整项目的进度。
通过及时更新项目时间表,并采取必要的措施,确保项目能够按时完成。
5.风险管理:FDS工艺中,风险管理是一个重要的环节。
项目管理人员需要对项目可能面临的风险进行评估,并制定相应的风险应对措施。
这样能够在项目实施过程中及时应对风险,减少不确定性对项目进度的影响。
FDS工艺在项目管理中应用广泛,特别适用于复杂和大型项目。
它能够帮助项目管理人员全面了解项目需求和目标,制定详细的计划和时间表,并根据实际情况进行调整和更新。
通过FDS工艺,项目管理人员可以更好地控制项目进度,减少风险,并确保项目能够按时交付。
总之,FDS工艺是一种非常重要的项目管理工艺。
- 1、下载文档前请自行甄别文档内容的完整性,平台不提供额外的编辑、内容补充、找答案等附加服务。
- 2、"仅部分预览"的文档,不可在线预览部分如存在完整性等问题,可反馈申请退款(可完整预览的文档不适用该条件!)。
- 3、如文档侵犯您的权益,请联系客服反馈,我们会尽快为您处理(人工客服工作时间:9:00-18:30)。
设备易损件寿命
Screw Driver拧紧头约 1万次
Collet Jaw 夹紧头约 1万次
Sleeve铜衬套约 1万次
FDS Matrix—设备
设备采购
价格: 约80万/System (FDS GUN + AUTO Feeder + Controller)
采购周期: 18周 (含运输)
FDS Matrix—标准
缺点:FDS工艺的局限性
1. 连接点处需要高的刚性支撑 2. Cycle Time时间长,约为5-8秒 3. 铆钉成本的piece cost 0.15Euro/Rivet
4. 设备系统成本远高于电阻点焊 800K人民币/system 5. 工艺完成后铆钉正反面均有较大凸起保留 6. 正面铆接方向需要留出大的进枪空间 7. 铆钉选用、工艺参数跟铆接材料、铆接姿态相关性强
工艺要求MR材料、厚度匹配要求
1. 接头不能含脆性材料(如玻璃、脆性塑料) 2. 底层材料(die侧)通常是1.5mm-3.5mm的铝型材或者 3mm左右的铸铝件 3. 上层板材可以7mm的prehole引导孔或者没有引导孔 4. 没有引导孔时,不同材质铆接原则: 软材质铆向硬材质 薄材质铆向厚材质
工艺要求铆钉选择要求
工艺要求MR接头设计要求
工艺参数
工艺参数
n: 转速
F: 压紧力
M: 扭矩
设备系统组成
4.
2.
设备FDS两种标准枪
Standard Length
Reduced Length
设备FDS枪组成结构
设备送钉方式
设备应用方式
Robotic System Prefer
质量标准 推荐标准
在线依靠自动监控系统100%反馈质量,外观检查,扭矩检查 破检,拉伸试验
FDS Matrix—标准返修 Nhomakorabea法1. 邻近位置FDS 2. 原位置用公制螺纹螺栓返修 3. 邻近位置拉铆
The END !
Pedestal System Prefer
设备应用柔性、互换性
FDS跟其他应用的互换: Gripper,FDS Tool Changer:Walther,Staubli 不同铆钉可以通过Magazine Fill系统填充 换枪盘上装不同规格送钉管,不同送钉器
设备接口标准、公用动力要求:无特别要求
Normal Rivet
Special Design Rivet
优点:FDS是单面自攻螺纹连接
1. 单面连接工艺(使型材、小孔洞连接成为可能) 2. 可以有预开孔或者没有预开孔 3. 可以连接不同材料 4. 因为连接过程中的旋转摩擦生热使得攻丝旋转扭矩低 5. 因为大的螺纹接触面而产生大的旋紧扭矩 6. 很高的松开扭矩 7. 气密性水密性好 8. 动态承载性好 9. 攻丝的螺纹可以重复旋紧 10. 可以使用公制螺丝返修
Flow Drill Screw 旋转攻丝铆接
FDS Matrix
简介:旋转攻丝铆接工艺是通过高速旋转使板料热变形后攻丝铆接的冷成型工艺。
铆钉:通过特殊的感应加热高频淬火工艺– EJOT (M5,M6系列)
铆钉表面硬度从HV320提高到HV450-HV600
铆钉:通过特殊的感应加热高频淬火工艺– EJOT (M5,M6系列)