第章液态金属凝固过程中的传热、传质及液体流动摘要
第二讲液态金属的流动与传热

5)表面张力 造型材料一般不被液态金属润湿,即润湿角θ>900。故液态
金属在铸型细薄部分的液面是凸起的,而由表面张力产生一个 指向液体内部的附加压力,阻碍对该部分的充填。所以,表面 张力对薄壁铸件、铸件的细薄部分和棱角的成形有影响。型腔 越细薄,棱角的曲率半径超小,表面张力的影响则越大。为克 服附加压力用阻碍,必须在正常的充型压力上增加一个附加压 头。
式中,
v为在静压头H作用下液态金属在型腔 中的平均流速;
t为液态金属自进入型腔到停止流动的 时间。
充型过程的物理模型
7
由流体力学原理可知 :
v 2gH
式中,H为液态金属的静压头;为流速系数。
关于流动时间的计算,液态金属不同的停止流动机理则有不 同的计算方法。
对于纯金属或共晶成分合金,凝固方式呈逐层凝固时,其停 止流动是由于液流末端之前的某处从型壁向中心生长的晶粒相 接触,通道被堵塞的结果。因此,对于这类液态金属的停止流 动时间t,可以近似地认为是试样从表面至中心的凝固时间,可 根据热平衡方程求出(凝固时间的计算)。
17
A1-Si合金的流动性,在共晶成分处并非最大值,而在过共 晶区里继续增加,是因为初生硅相块状晶体,有较小的机械强度, 不形成坚强的网络,结晶潜热得以发挥。硅相的结晶潜热比 α 相大三倍。
18
3)金属的比热、密度和导热系数
比热和密度较大的合金,因其本身含有较多的热量,流动性 好。导热系数小的合金,热量散失慢,保持流动的时间长;导 热系数小,在凝固期间液固并存的两相区小,流动阻力小,故 流动性好。
合金的结晶温度范围越宽,枝晶就 越发达,液流前端析出少量固相, 即在较短的时间,液态金属便停止 流动。在液态金属的前端析出 15~20%的固相量时,流动就停止。
第4章 液态金属凝固过程中的传热、传质及液体流动
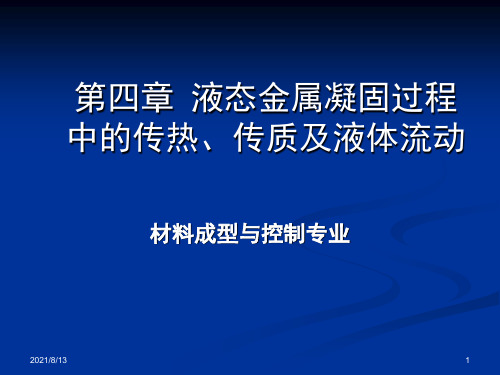
第四章 液态金属凝固过程 中的传热、传质及液体流动
铸件凝固时间:液态金属充满铸型的时刻到凝固完毕所 需要的时间。
凝固速度:单位时间凝固层增长的厚度。 铸件凝固时间的确定方法:试验法、数值模拟法、计算
法。 1、理论计算法
t2 b2 A 1V 11LC Ti1 TT 浇 2 0TS
计算温度场有些假设,算出的凝固时间是近似的。 应用较少。
2021/8/13
2021/8/13
8
3、影响铸件温度场的因素 (1)金属性质的影响 1)金属的导热系数
铸件凝固时表面的温度比中心要低。金属的导热系数大, 铸件内部的温度均匀化的能力就大,温度梯度就小,即断 面上的温度分布较平坦。
2)结晶潜热
金属的结晶潜热大,向铸型传热的时间长,铸型内表面被 加热的温度也越高,因此铸件断面上的温度梯度较小,铸 件冷却速度下降,温度场分布较平坦。
25
2021/8/13
26
在实际的生产中,通常不需计算出铸件的凝固时间,只 需通过比较它们的相对厚度或模数就可制定生产工艺。
铸件温度场及凝固时间的精确计算——计算机数值模拟
2021/8/13
27
第二节 凝固过程中的传质
2021/8/13
28
§4-2 凝固过程中的传质
传质控制方程:
菲克第一定律: JADddczADdcdxzA
(C*L-C*S)dfS=(1-fS)dC*L
第3章 凝固过程的传热[23页]
![第3章 凝固过程的传热[23页]](https://img.taocdn.com/s3/m/0059e3a9294ac850ad02de80d4d8d15abe2300f6.png)
Tw f (t)
第二类边界条件: 给出通过物体表面的比热流随
时间的变化关系
T qx, y, z, t
n
第三类边界条件: 给出物体周围介质温度以及物
体表面与周围介质的换热系数
T = n
Tw
Tf
纯金属在铸型中凝固传热模型
K-导热 C-对流 R-辐射 N-牛顿界面换热
“三传”
所谓“三传”,即金属的凝固过程是一个 同时包含动量传输、质量传输和热量传输 的三传耦合的三维传热物理过程,而在热 量传输过程中同时存在有导热、对流和辐 射传热这三种传热方式。
t x x y y z z
λ --导热系数;
T--热力学温度; q --单位体积物体单位时间内释放的热量; c--比热容;
q L f s
t
ρ--密度;
t--时间。
对具体热场用上述微分方程进行求解时,需要根 据具体问题给出导热体的初始条件与边界条件。
初始条件: 初始条件是指物体开始导热时
第3章 凝固过程的传热
主要内容
3.1 凝固过程的传热 3.2 凝固时间的计算 3.3 液态金属凝固温度场
3.1 凝固过程的传热
3.1.1 凝固过程的传热特点
金属凝固过程中,其传热特点可简要概括为: “一热、二迁、三传”。
“一热”,即在凝固过程中热量的传输是第 一位的,是最重要的,它是凝固过程能否进 行的驱动力。
(即 t = 0 时)的瞬时温度分布。
边界条件:边界条件是指导热体表面与周围
介质间的热交换情况。
“二迁”
所谓“二迁”,是指在金属凝固时存在着 两个界面,即固—液界面和金属—铸型界 面,而这两个界面随着凝固进程而发生动 态迁移,并使得界面上的传热现象变得极 为复杂。
液态金属凝固过程中的传热与传质
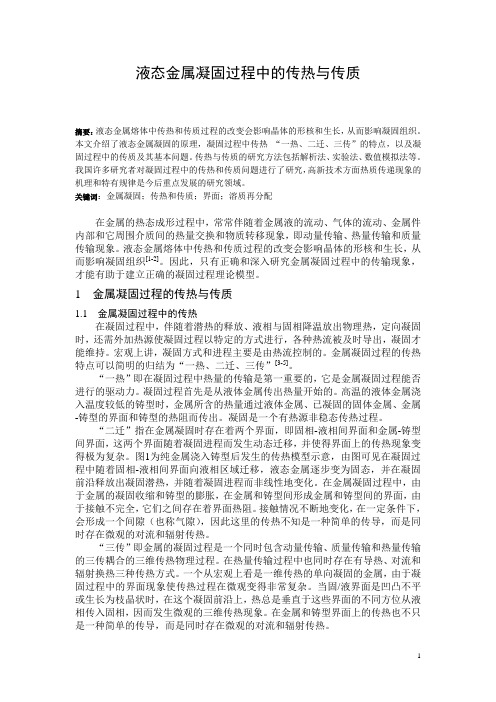
液态金属凝固过程中的传热与传质摘要:液态金属熔体中传热和传质过程的改变会影响晶体的形核和生长,从而影响凝固组织。
本文介绍了液态金属凝固的原理,凝固过程中传热“一热、二迁、三传”的特点,以及凝固过程中的传质及其基本问题。
传热与传质的研究方法包括解析法、实验法、数值模拟法等。
我国许多研究者对凝固过程中的传热和传质问题进行了研究,高新技术方面热质传递现象的机理和特有规律是今后重点发展的研究领域。
关键词:金属凝固;传热和传质;界面;溶质再分配在金属的热态成形过程中,常常伴随着金属液的流动、气体的流动、金属件内部和它周围介质间的热量交换和物质转移现象,即动量传输、热量传输和质量传输现象。
液态金属熔体中传热和传质过程的改变会影响晶体的形核和生长,从而影响凝固组织[1-2]。
因此,只有正确和深入研究金属凝固过程中的传输现象,才能有助于建立正确的凝固过程理论模型。
1 金属凝固过程的传热与传质1.1 金属凝固过程中的传热在凝固过程中,伴随着潜热的释放、液相与固相降温放出物理热,定向凝固时,还需外加热源使凝固过程以特定的方式进行,各种热流被及时导出,凝固才能维持。
宏观上讲,凝固方式和进程主要是由热流控制的。
金属凝固过程的传热特点可以简明的归结为“一热、二迁、三传”[3-5]。
“一热”即在凝固过程中热量的传输是第一重要的,它是金属凝固过程能否进行的驱动力。
凝固过程首先是从液体金属传出热量开始的。
高温的液体金属浇入温度较低的铸型时,金属所含的热量通过液体金属、已凝固的固体金属、金属-铸型的界面和铸型的热阻而传出。
凝固是一个有热源非稳态传热过程。
“二迁”指在金属凝固时存在着两个界面,即固相-液相间界面和金属-铸型间界面,这两个界面随着凝固进程而发生动态迁移,并使得界面上的传热现象变得极为复杂。
图1为纯金属浇入铸型后发生的传热模型示意,由图可见在凝固过程中随着固相-液相间界面向液相区域迁移,液态金属逐步变为固态,并在凝固前沿释放出凝固潜热,并随着凝固进程而非线性地变化。
第3章 凝固过程的传热(1)

液相向固相转变时还包含有弯曲固-液界面的形成(产生毛细作用)和热量的微观
熔体内形成了固体,产生一个面积为A的固-液界面,就要克服一个与之相对
运输,在合金凝固时还存在溶质的微观运输。 应的额外能量-界面能。因此,A/v值高的异质系统要比A/v值低的异质系统能量更 高,更不稳定。可以用平衡温度(熔点)来表达两相之间的相对稳定性。由毛细作 用引起的熔点温度变化(曲率过冷度)为, 其中,K是曲率, K
合金凝固组织特征不仅取决于冷却条件,而且取决于合金成分(见图1.8 所示的 Al-Cu系中Al和金属间化合物θ (Al2Cu)相之间的部分相图)。 理解不同的凝固组织如何受合金成分和凝固条件的影响非常重要。不 管凝固组织看来多么复杂,但都可以把问题简化为两种基本的凝固组织形 态,即树枝晶和共晶(包晶也以树枝状生长)。 一般情况下还会有两者的混合体。可以归 纳为: (a)纯物质:平面状或树枝状生长; (b)固溶体树枝晶 (不管有无枝晶间析出相); (c)树枝晶和枝晶间共晶; (d)共晶。 理解了这两种生长方式就可以解释几 乎所有合金的凝固组织。 铸造合金的设计前提就是获得所需的性 能和良好的铸造性(易充型、低缩孔和低热裂倾向)。
一些涉及凝固过程的重要生产环节有:铸造(连续铸造、模锭铸造、砂型铸
造、精密铸造、金属型铸造),焊接,锡焊/铜焊,快速成型过程,定向凝固等。 此外,纯物质的结晶也非常重要。例如,半导体及硅晶体制备是现代固体物
理和技术的重要部分。集成电路是所有新型电子器件(无线电、手表、计算机 等)的基础单元,制造集成电路需要大尺寸、低缺陷的单晶,而这种单晶的制 备则需要对掺杂元素的量和均匀性进行严格控制。到目前为止,这种单晶还只 能从熔体中生长。半导体物理方面的需求极大促进了凝固理论和技术的进步。 虽然铜制品的铸造可以追溯到公元前4000年。公元前1600年,中国也出现
【精品课件】液态成形中的流动与传热

液态金属停止流动机理与充型能力
充型能力强
前端析出15~20%的固相量 时,流动就停止。
纯金属、共晶成分合金及结晶温度 很窄的合金停止流动机理示意图
宽结晶温度合金停止 流动机理示意图
一、金属性质方面的因素
2、结晶潜热 • 结晶潜热约占液态金属热含量的85-90%,但是,它对不同
类型合金的流动性影响是不同的。
本节重点内容
1、充型能力的基本概念
2、影响充型能力的因素及提高充型能力的措施
2.1.1 流动性与充型能力的基本概念
• 液态金属充满铸型型腔,获得形状完整、轮廓清晰的铸 件的能力,即液态金属充填铸型的能力,简称液态金属 的充型能力。
• 实验证明,同一种金属用不同的铸造方法,所能铸造的 铸件最小壁厚不同。同样的铸造方法,由于金属不同, 所能得到的最小壁厚也不同,如表所示。
• 纯金属和共晶成分的合金在固定温度下凝固,在一般的浇注 条件下,结晶潜热的作用能够发挥,是估计流动性的一个重 要因素。凝固过程中释放的潜热越多,则凝固进行得越缓慢, 流动性就越好。其流动性与结晶潜热相对应:Pb的流动性最 差,Al的流动性最好,Zn、Sb、Cd、Sn依次居于中间。
• 对于结晶温度范围较宽的合金,散失一部分(约20%)潜热后, 晶粒就连成网络而阻塞流动,大部分结晶潜热的作用不能发 挥,所以对流动性影响不大。
5表面张力 造型材料一般不被液态金属润湿,即润湿角>90°。
故液态金属在铸型细簿部分的液面是凸起的,而由表面张力 产生一个指向液体内部的附加压力,阻碍对该部分的充填。 所以,表面张力对薄壁铸件、铸件的细簿部分和棱角的成形 有影响。型腔越细薄,棱角的曲率半径越小,表面张力的影 响则越大。为克服附加压力的阻碍,必须在正常的充型压头 上增加一个附加压头h。
凝固原理讲义-凝固过程中的流动-

溶质边界层
28
旋转圆盘下的浓度边界层厚度为
dc 1.61D1/3 1/61/ 2
D为溶质扩散系数,为运动粘滞系数, 为旋转圆盘的转速
温度边界层
29
T z
(Tb
Tm ) / dT
热扩散传热
dT 1/ 2
主要对流传热
温度边界层
30
晶体旋转对流体中的速度边界层、溶质边界层和温度边界层
36
两板之间的液体产生自然对流, 对流的速度vx分布曲线为正弦波形
作用于液体单元上的粘滞力示意图
作用于单元底面积上的剪切力
液态金属中自然对流的驱动力
37
液体单元上的粘滞力为:
y
dy
dxdz
dxdz
y
dxdydz
单位体积上的粘滞力为:
F粘
y
另外,根据牛顿粘滞定律
vx
y
F粘
y
vx y
2vx y 2
设在一个长度为L的圆柱体内,有很多半径为R的微小孔道, 每个小孔道是直而光滑的,我们关注的是每个管道内的流速大小
枝晶间液态金属的流动
43
每个圆管中的横截面上任一点的轴向切应力可以表示为以下两种形式:
r
vx r
黏度系数,沿管道轴向上的流动速度
r
p0 pL L
r 2
进,出口处的压力, 管道长度,指定点的半径
联立以上两式得
44
dvx
p0 pL
2L
rdr
积分,得
vx
p0 pL
4L
r 2
C
边界条件, r R时,vx 0,
当r=0时,
得
C
p0 pL
液态金属的传热与凝固方式
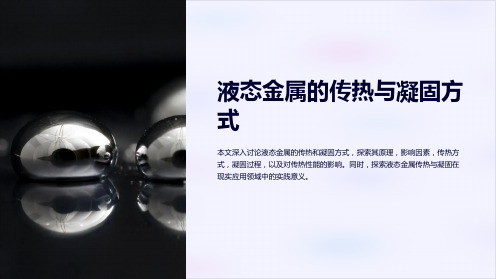
本文深入讨论液态金属的传热和凝固方式,探索其原理,影响因素,传热方 式,凝固过程,以及对传热性能的影响。同时,探索液态金属传热与凝固在 现实应用领域中的实践意义。
液态金属的传热原理
液态金属的传热原理是基于热传导机制,其中,热量通过金属中的自由电子 传播。这种电子传导机制使液态金属具有出色的导热性能。
液态金属的凝固过程
液态金属的凝固过程是指金属从液态向固态的相变过程。这个过程是由温度 和时间共同作用下的原子重新排列所导致。
凝固式对传热性能的影响
不同的凝固方式会对液态金属的传热性能产生不同影响,包括凝固结构的有 序性、晶粒尺寸和形态等。理解这些影响可以更好地优化传热性能。
液态金属传热与凝固的应用领域
液态金属传热的影响因素
液态金属传热的影响因素包括金属的物理特性、温度差、传热介质等。理解 这些因素对传热效果的影响能够优化液态金属的传热性能。
液态金属的传热方式
液态金属的传热方式包括对流传热、辐射传热和传热管传热等。不同的传热方式在不同的情况下有不同 的适用性和效果。了解这些方式可以为液态金属传热的设计和应用提供指导。
液态金属传热与凝固在众多领域都有广泛应用,包括航天、工业制造、能源等。这些应用为我们提供了 更高效、更可靠的传热技术。
结论和实践意义
深入理解液态金属的传热与凝固方式对于优化传热性能、改进工艺以及实现创新应用具有重要意义。这 将不仅推动液态金属传热技术的发展,也助力相关领域的进步与创新。
金属凝固理论 第4章 液态金属凝固过程中的传热、传质及液体流动

金属的凝固温度越高,在凝固过程中铸件表面和铸型内表 面的温度越高,铸型内外表面的温差就越大,致使铸件断 面温度场出现较大的梯度。如有色金属与钢铁相比,其温 度场较平坦。
2020/10/15
11/56
(2)铸型性质的影响 1)铸型的蓄热系数
铸型的蓄热系数越大,对铸件的冷却能力就越大, 铸件内的温度梯度就越大。铸型的导热系数越大, 能把铸型内表面吸收的热迅速传至外表面,使铸 型内表面保持强的吸热能力,铸件内的温度梯度 也就大。
向中心推进时,把铸型加热到更高温度,所以铸 件内温度场较平坦。
2)铸件的形状 铸件的棱角和弯曲表面,与平面的散热条件不同。
向外凸出的部分,散出的热量被较大体积的铸型 所吸收,铸件的冷速较大,如果铸件内凹的表面, 则相反。
2020/10/15
13/56
三、铸件的凝固方式及影响因素
TL
TS
L
S+L S
第四章 液态金属凝固过程 中的传热、传质及液体流动
2020/10/15
1/56
第一节 凝固过程中的传热
在材料成形过程中,液态金属的过热热量和 凝固潜热主要是通过传导而释放的。
2020/10/15
2/56
一、凝固过程中的热传导及傅里叶方程
温度场基本概念: 稳定温度场: 不随时间而变的温度场(即温度只是坐标的函 数),其表达式为:
2020/10/15
T n
Tw Tf
4/56
凝固过程中,热量传递有三种形式:传导、辐射、 对流。
以热传导为主。 热传导过程取决于温度的分布——温度场:温度
随空间和时间的变化。 T = f(x,y,z,t) Fourier热传导方程:
【材料成型原理--铸造】第4章 液态金属凝固过程中的传热与传质
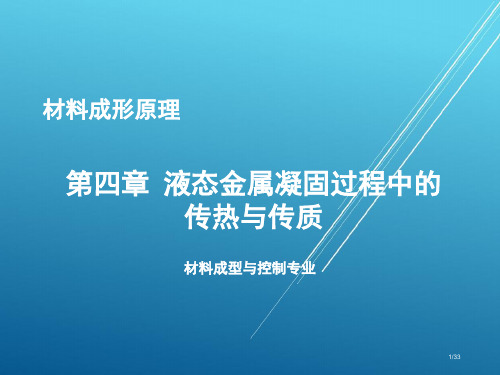
• 2、模型建立
• 温度TL时,开始凝固: • 固 度k相0C:0。百分数dfS;溶质浓
• 液相:溶质浓度几乎不变, 为C0。 • 温度降到T*时,
• 固 数f相S;:溶质浓度C*S;百分
•
液相:溶质浓 数fL。
度
C*L;百
分
28/33
• 当dfSf)S界,溶面这质处些浓固溶度相质增增将加加均d百C匀*L分扩,量散则为到:d整fS个时液,相排中出,溶使质剩量余为液(相C*(L-C1*S-) • (C*L-C*S)dfS=(1-fS)dC*L
30/33
31/33
32/33
33/33
34/33
35/33
• (二)固相无扩散,液相只有有限扩散(无对流或搅拌) 的溶质再分配
• 1、假设: • (1)合金单相凝固; • (2)固相无扩散(接近实际情况); • (3)液相有限扩散(无对流、搅拌); • (4)固液相线为直线,k0为常数; • (5)试样很长,单向放热,平面推进。
• 该两式为平衡凝固时溶质再分配的数学模型。
19/33
CS
1
C0k0 f S (1 k0 )
CL
k0
C0 f L (1 k0 )
• 3、验证 (1)开始凝固时 • 初始条件:fS0,fL1 • 则:CS=k0C0;CL=C0 (2)凝固结束时 • 初始条件:fS1,fL0 • 则:CS=C0;CL=C0/k0
凝固时间与凝固层厚度的平方成正比。
计算结果与实际接近。
适合大平板和结晶间隔小的铸件。
14/33
• 3、“折算厚度”法则
R2 t
K2
R V1 为铸件折算厚度或铸件模数。
A1
液态金属凝固过程中的传热与传质

液态金属凝固过程中的传热与传质摘要:液态金属熔体中传热和传质过程的改变会影响晶体的形核和生长,从而影响凝固组织。
本文介绍了液态金属凝固的原理,凝固过程中传热“一热、二迁、三传”的特点,以及凝固过程中的传质及其基本问题。
传热与传质的研究方法包括解析法、实验法、数值模拟法等。
我国许多研究者对凝固过程中的传热和传质问题进行了研究,高新技术方面热质传递现象的机理和特有规律是今后重点发展的研究领域。
会形成一个间隙(也称气隙),因此这里的传热不知是一种简单的传导,而是同时存在微观的对流和辐射传热。
“三传”即金属的凝固过程是一个同时包含动量传输、质量传输和热量传输的三传耦合的三维传热物理过程。
在热量传输过程中也同时存在有导热、对流和辐射换热三种传热方式。
一个从宏观上看是一维传热的单向凝固的金属,由于凝固过程中的界面现象使传热过程在微观变得非常复杂。
当固/液界面是凹凸不平或生长为枝晶状时,在这个凝固前沿上,热总是垂直于这些界面的不同方位从液相传入固相,因而发生微观的三维传热现象。
在金属和铸型界面上的传热也不只是一种简单的传导,而是同时存在微观的对流和辐射传热。
图1 纯金属在铸型中凝固时的传热模型K-导热,C-对流,R-辐射,N-牛顿界面换热1.2金属凝固过程中的传质金属液凝固时出现的固相成分常与液相成分不同,引起固相、液相内成分分布的不均匀,于是在金属凝固时固相层增厚的同时出现了组分的迁移过程,即传质。
凝固过程的溶质传输决定着凝固组织中的成分分布,并影响到凝固组织结构。
金属的凝固过程,其传质问题直接和金属的凝固方式相关联,主要研究几种基本传质问题:①金属凝固过程中整个凝固体系内溶质的变化;②金属以平界面方式凝固时凝固过程的溶质变化;③金属以枝晶方式凝固时凝固过程的溶质变化。
平界面凝固过程中的传质与溶质再分配是最基本的传质问题,对许多复杂传质问题的研究是在此基础上进行的。
主要包括:(1)平衡凝固条件下的溶质再分配;(2)固相无扩散而液相均匀混合的溶质再分配;(3)固相无扩散,液相中有扩散而无对流的溶质再分配;(4)液相中部分混合(对流)的溶质再分配。
液体金属处理中的传热传质研究

液体金属处理中的传热传质研究摘要液体金属处理是金属材料加工和制造的重要工艺之一,其熔融状态下的物理和化学性质具有独特性,但其特殊的性质也带来了复杂的传热和传质过程。
本文对液体金属处理过程中的传热传质研究进行了综述,包括自然对流、强迫对流、辐射传热、多相传热、相变传热以及传质过程等方面,阐述了各种传热传质模型和相应的研究方法,为液体金属处理过程的优化提供了理论依据。
关键词:液体金属处理、传热传质、传热模型、传质模型、优化第一章绪论液体金属处理是指把金属在高温下熔融,进行浇注、铸造、锻造、轧制、挤压、拉伸等多种加工方法的工艺。
在液体金属处理过程中,热量的传递和物质的传输是必不可少的环节,因此传热传质研究是液体金属处理技术的基础之一。
传热传质研究不仅能够改善液体金属处理的工艺技术,还有助于提高加工工件的质量和生产效率。
第二章传热传质模型传热传质模型是对液体金属处理过程中热量和物质传递现象的描述和分析。
液体金属的传热传质过程复杂多样,存在自然对流、强迫对流、辐射传热、多相传热、相变传热等多种传热传质方式。
2.1 自然对流传热模型自然对流是指在温度差的作用下,由于热量的不均匀分布而形成的一种流动状态。
液体金属处理中的自然对流,通常伴随着温度场的非线性变化和较强的非线性耦合。
自然对流传热模型建立的核心是流体运动的动量传递方程和热传递方程。
2.2 强迫对流传热模型强迫对流是指机械或热力学作用下引起的流体运动。
液体金属处理中的强迫对流主要有气流或液流对液体金属表面的冷却、加热和搅拌等作用。
强迫对流传热模型建立的核心是Navier-Stokes方程和能量方程。
2.3 辐射传热模型辐射传热是指热量通过辐射作用而传递的物理过程。
液体金属处理过程中的辐射传热,实际上是由液体金属产生的热量向周围空气和固体传递的过程。
辐射传热模型的建立需要涉及真实物理场的射线互相作用方程和辐射传热方程。
2.4 多相传热模型多相传热是指液体金属处理过程中含有两种或两种以上的相的传热现象。
4 凝固过程的液体金属流动和传热.ppt
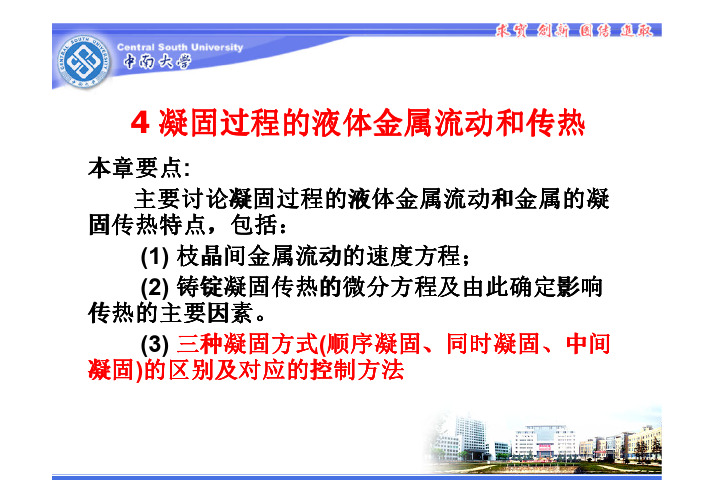
本章要点:主要讨论凝固过程的液体金属流动和金属的凝固传热特点固传热特点,,包括包括::4 凝固过程的液体金属流动和传热1(1) 枝晶间金属流动的速度方程枝晶间金属流动的速度方程;;(2) 铸锭凝固传热的微分方程及由此确定影响传热的主要因素传热的主要因素。
(3) 三种凝固方式(顺序凝固顺序凝固、、同时凝固同时凝固、、中间凝固)的区别及对应的控制方法在浇筑和凝固过程中在浇筑和凝固过程中,,液体金属时刻在流动 包括对流和枝晶间的黏性流动液体金属流动是一种动量传输过程液体金属流动是一种动量传输过程,,是铸锭成型是铸锭成型、、传热传热、、传质的必要条件浇筑和凝固过程中的特性1 凝固过程液体金属的流动是一种动量传输过程是一种动量传输过程。
浇注时流柱冲击引起的动量对流动量对流。
金属液内温度和浓度不均引起的1.1 液体金属的对流对流成因:3自然对流自然对流。
电磁场或机械搅拌及振动引起的强制对流。
对于连续铸锭对于连续铸锭,,由于浇注和凝固同时进行由于浇注和凝固同时进行,,动量对流会连续不断地影响金属液的凝固过程属液的凝固过程,,如不采取适当措施均布液流不采取适当措施均布液流,,过热金属液就会冲入液穴的下部。
动量对流强烈时动量对流强烈时,,易卷入大量气体易卷入大量气体,,增加金属的二次氧化增加金属的二次氧化,,不利于夹渣的上浮,应尽量避免应尽量避免。
立式半连续铸锭过程中立式半连续铸锭过程中,,在金属液面下垂直导入液流时在金属液面下垂直导入液流时,,其落点周围会形成一个循环流动的区域成一个循环流动的区域,,称为涡流区。
特征是在落点中心产生向下的流股的流股,,在落点周围则引起一向上的流股的流股,,从而造成上下循环的轴向循环对流。
流注冲击引起的对流4影响流注穿透深度因素影响流注穿透深度因素:: 浇筑速度 浇筑温度流注在液穴中的穿透深度:沿液穴轴向对流往下延伸的距离 流注落下高度 结晶器尺寸注管直径流注穿透深度随其下落高度的增加而减小流注下落高度增加,其散乱程度增大,卷入的气体多,气泡浮力对流注的阻碍作用增强浇筑速度增大浇筑速度增大,,流注穿透深度增加结晶器断面尺寸减小结晶器断面尺寸减小,,气泡上浮区域减小气泡上浮区域减小,,存留在流注点下方气泡数量相应增加量相应增加,,对流注阻碍作用增强对流注阻碍作用增强,,流注穿透深度减小结晶器断面尺寸减小结晶器断面尺寸减小,,流注落点周围的涡流增强流注落点周围的涡流增强,,流注轴向速度降低流注轴向速度降低,,穿透深度减小6轴向循环对流轴向循环对流,,还会引起结晶器内金属液面产生水平对流,其方向决定着夹渣的聚集地点其方向决定着夹渣的聚集地点。
2液态成形中的流动与传热

T10
铸型 λ2 c2 ρ2
铸件 λ1 c1 ρ1
Ti
铸型
已凝固铸件
剩余 液相
x T2 Ti Ti T20 erf 2 a t 2
T20
0 图2-3无限大平板铸件凝固温度场分布
x
推导过程
假 设:
(1)凝固过程的初始状态为: 铸件与铸型内部分别为均温,铸件起始温度为浇铸温 度 ,铸型的起始温度为环境温度或铸型预热温度 ; (2)铸件金属的凝固温度区间很小,可忽略不计; (3)不考虑凝固过程中结晶潜热的释放;
c
;
2 —— 拉普拉斯运算符号。
二维传热:
2T T 2T a x 2 y 2 t
一维传热:
T 2T a t x 2
对具体热场用上述微分方程进行求解时,需要根据具体问
题给出导热体的初始条件与边界条件。
初始条件: 初始条件是指物体开始导热时(即 t
第二节 铸件凝固温度场的解析解法
一、半无限大平板铸件凝固过程的
一维不稳定温度场
二、铸件凝固时间计算 三、界面热阻与实际凝固温度场
四、铸件凝固方式及其影响因素
一、半无限大平板铸件凝固过程的 一维不稳定温度场
T
x T1 Ti T10 Ti erf 2 a t 1
某法线方向的温度变化率。温度梯度越大,图形
上反映为等温面(或等温线)越密集。
二、热传导过程的偏微分方程
三维傅里叶热传导微分方程为:
T t c 2T 2T 2T x 2 y 2 z 2
a
a 2T
式中:
a
—— 导温系数,
液态金属合金凝固热力学和动力学
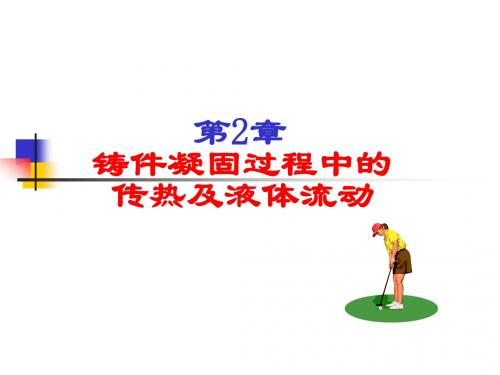
数学解析法主要是应用传热学的理论,建立一 个描述铸件凝固过程传热特征的各物理量之间的 方程式,也就是建立一个铸件和铸型的温度场数 学模型并进行求解。
金属液在铸型中凝固和冷却: 是一个不稳定的传热过程; 铸件的形状多种多样,其中大部分为三维的传 热问题; 铸件在凝固过程中又不断地释放出结晶潜热, 其断面上存在着已凝固完毕的固态外壳、液固态 并存的凝固区和液态区; 铸型和铸件的热物理参数一般都随温度而变化。
逐层凝固方式 体积凝固方式(或糊状凝固方式) 中间凝固方式
(1)逐层凝固 纯金属、共晶体在凝固过程中不存在液固并存
的两相区,断面上液体与 固体之间由一条界线清楚 分开,随温度下降而加厚, 液层减少直至中心。如灰 口铸铁、铝硅合金、黄铜 等。
小,铸件断面上的温度梯度也就越小。
3.浇注条件的影响
浇注温度 T浇
G
浇注温度越高则过热量越大,增加过热实际
上提高了铸件凝固时铸型的温度,冷却能力变
小,使铸件断面温度梯度减小。砂型铸造时尤
为明显。在金属型铸造时,浇注温度的影响不十
分明显。
4.铸件结构的影响 1)铸件的壁厚 壁厚 G 厚壁铸件比薄壁铸件含有更多的热量,当凝固
其值大小与材料的几何形状无关,主要取决于组
成材料的成分、内部结构、温度、压力。
2.1.2数学解析法
研究温度场方法有数学解析法、数值模拟法及 测温法等。
根据铸件温度场随时间的变化,能够预测铸件 凝固过程中其断面上各时刻的凝固区域大小及变 化,凝固前沿向中心推进的速度、缩孔和缩松的 位置,凝固时间等重要问题。
4.非金属铸件在金属型中凝固
常见于金属快速凝固过程,或非金属铸件在金 属型中冷却。这时热阻主要 存在于凝固层中,界面热阻 与金属型的热阻可以忽略不 计,传热过程主要取决于铸 件本身的热物理性能,温度 降主要发生在铸件一侧。
金属液态成型第二章 液态金属的流动与传热
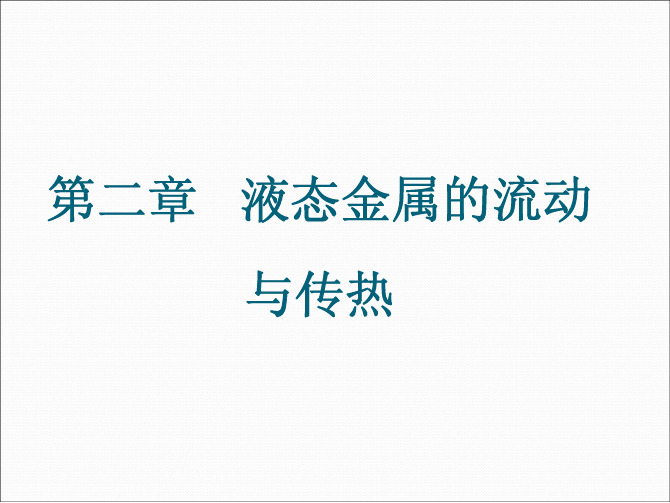
一维空间流动速度与压力场之间的关系
三维空间流动速度与压力场之间的关系-达西(Darcy)定律:
三、界面张力引起的流动
在一特定的系统中,界面张力受温度与溶质浓度的影响:
Marangoni数 当温度或浓度梯度垂直于凹曲的液面,此时势必产生一 个界面张力梯度,当达到Marangoni数的临界值时,将引起 流动,这种流动也称之为Marangoni对流。
逐层凝固方式示意图
糊状(体积)凝固方式示意图
恒温下结晶
结晶温度范围很小 或断面温度梯度很大
铸件断面温度场 较平坦
结晶温度 范围很宽
3. 铸件的凝固方式的影响因素
合金的结晶温度范围Δt; 温度梯度δt。 Δt/ δt依据: Δt/ δt << 1 趋于逐层凝固方式;Δt/ δt > 1 趋于体积凝固方 式。
2. 铸型性质方面的因素 1)铸型的蓄热系数 蓄热系数含义:表示铸型从其中的金属中 吸取并储存于本身中热量的能力; 蓄热系数越大,铸型的激冷能力就越强。
2)铸型的温度 预热铸型能减小金属与铸型的温差,从 而提高其充型能力。例如,在金属型中浇注 铝合金铸件,将铸型温度由340℃提高到 520℃,在相同的浇注温度(760℃)下,螺 旋线长度则由525mm增加到950mm。在熔 模铸造中,为得到清晰的铸件轮廓,可将型 壳焙烧到800℃以上进行浇注。
金属型 砂型
体积凝固
中间或层状凝固
砂型中:
低碳钢:层状凝固 中碳钢:中间凝固 高碳钢:体积凝固
2.1.6 凝固时间
1. 理论推导 (无限大平板)
很大局限性,仅作为近似计算,实际应用较少
2. 平方根定律
应用:大平板类零件比较准确
3. 折算厚度法则(模数法)
- 1、下载文档前请自行甄别文档内容的完整性,平台不提供额外的编辑、内容补充、找答案等附加服务。
- 2、"仅部分预览"的文档,不可在线预览部分如存在完整性等问题,可反馈申请退款(可完整预览的文档不适用该条件!)。
- 3、如文档侵犯您的权益,请联系客服反馈,我们会尽快为您处理(人工客服工作时间:9:00-18:30)。
2020/9/19
8
3、影响铸件温度场的因素 (1)金属性质的影响 1)金属的导热系数
铸件凝固时表面的温度比中心要低。金属的导热系数大, 铸件内部的温度均匀化的能力就大,温度梯度就小,即断 面上的温度分布较平坦。
2)结晶潜热
金属的结晶潜热大,向铸型传热的时间长,铸型内表面被 加热的温度也越高,因此铸件断面上的温度梯度较小,铸 件冷却速度下降,温度场分布较平坦。
2)铸型的预热温度
铸型预热温度越高,对铸件的冷却作用就越小, 铸件断面上的温度梯度也就越小。
2020/9/19
10
(3)浇注条件的影响 过热热量加热了铸型,所以过热度越大,相当于
铸型预热温度越高。铸件内的温度场越平坦。
(4)铸件结构的影响 1)铸件的壁厚 厚壁铸件比薄壁铸件含有更多的热量,当凝固层
S
TL
T
TS
S S+L S
逐层凝固
糊状凝固
2020/9/19
中间凝固
12
凝固时各区域组成:(1)固相区:全部固体 (2)凝固区:液体+固体 (3)液相区:全部液体
2020/9/19
金属或合金凝固分区示意图
13
1)逐层凝固方式
纯金属、共晶合 金或结晶温度范围很 小的合金,铸件断面 温度梯度很大,导致 铸件凝固区很小或没 有。这种凝固方式叫 逐层凝固方式。
2020/9/19
14
2)体积凝固方式
合金结晶温度 范围大或铸件断面 温度梯度小,铸件 凝固范围很大。这 种凝固方式叫体积 凝固方式。
2020/9/19
15
3)中间凝固方式
铸件凝固范围介于逐层凝固方式和体积 凝固方式之间。这种凝固方式叫中间凝 固方式。
2020/9/19
16
凝固方式对铸件质量的影响
2020/9/19
体积凝固方式的缩松
18
影响凝固方式的因素
1)合金的化学成分 纯金属和共晶合金,凝固温度区间(液相线和固相线
温度差)为零,为逐层凝固方式。 当合金凝固温度区间很大时,凝固范围宽,为体积凝
固方式。
2)铸件断面温度梯度 温度梯度小,易产生
体积凝固方式。
2020/9/19
19
三、铸件凝固时间计算
随空间和时间的变化。
T = f(x,y,z,t) Fourier热传导方程:
Tt c(x2T2 y2T2 2 zT2)
a c
α为导热系数,λ为热导率,c为比热容,ρ为密度。
2020/9/19
3
凝固导热属非稳态导热;
导热微分方程的解较复杂;
形状简单的物体:大平板、长圆柱、球 体——可得解析解;
向中心推进时,把铸型加热到更高温度,所以铸 件内温度场较平坦。
2)铸件的形状 铸件的棱角和弯曲表面,与平面的散热条件不同。
向外凸出的部分,散出的热量被较大体积的铸型 所吸收,铸件的冷速较大,如果铸件内凹的表面, 则相反。
2020/9/19
11
三、铸件的凝固方式及影响因素
TL
TS
L
S+L S
T S+L
1)逐层凝固方式: ① 易补缩,不易产生缩松,组织致密,性能好。 ② 能在最后凝固部位形成集中缩孔。 ③ 裂纹能愈合,热裂倾向小。 ④ 充型能力好。 2)体积凝固方式: ① 不易补缩,易产生缩松。件性能差。 ② 热裂倾向大。 ③ 充型能力差。
2020/9/19
17
逐层凝固过程
体积凝固过程
逐层凝固缩孔特点
3) 金属的凝固温度
金属的凝固温度越高,在凝固过程中铸件表面和铸型内表 面的温度越高,铸型内外表面的温差就越大,致使铸件断 面温度场出现较大的梯度。如有色金属与钢铁相比,其温 度场较平坦。
2020/9/19
9
(2)铸型性质的影响 1)铸型的蓄热系数
铸型的蓄热系数越大,对铸件的冷却能力就越大, 铸件内的温度梯度就越大。铸型的导热系数越大, 能把铸型内表面吸收的热迅速传至外表面,使铸 型内表面保持强的吸热能力,铸件内的温度梯度 也就大。
第四章 液态金属凝固过程 中的传热、传质及液体流动
材料成型与控制专业
2020/9/19
1
第一节 凝固过程中的传热
在材料成形过程中,液态金属的过热热量和凝固潜 热主要是通过传导而释放的。
2020/9/19
2
一、凝固过程中的热传导及傅里叶方程
凝固过程中,热量传递有三种形式:传导、辐射、 对流。
以热传导为主。 热传导过程取决于温度的分布——温度场:温度
复杂件的凝固问题:采用计算机数值模拟。
2020/9/19
4
二、铸件凝固温度场
1、铸件凝固过程中热作用的特点
பைடு நூலகம்
(1)金属的流动特点影响热交换。 充型时——紊流——温度均匀。
(2)随温度下降——开始凝固— —凝固壳从冷却表面产生、长大。
(3)热量从最热的中心流经凝固 层,传给铸型。
(4)凝固过程温度分布:铸件中 心温度最高,远离铸件/铸型界面 的铸型温度最低。
20
铸型吸收的热量=铸件放出的热量
铸型吸收的热量的求法:
qt22(T i 2 T t20 )b2(TitT20 )
2020/9/19
6
◎实测法 a.温度场测量 b.凝固动态曲线
2020/9/19
7
◎ 数值模拟法 数值模拟法:把所研究的物体从时间和位置上分割成许多
小单元,对这些小单元用差分方程式近似代替微分方程式, 给出初始条件和边界条件,然后逐个计算各单元温度。 即使铸件形状很复杂,也只是计算式和程序烦杂而已,原 则上都是可以计算的。 实测法直观、可靠性好,但不方便;解析法适宜简单件, 有许多假设,误差大。 数值模拟法比其它方法准确性高,当单元选得足够小时, 差分方程的离散误差趋于零。 数值模拟法有多种方法,有限差分法应用较多。
凝固过程中铸件与铸型 的温度分布
2020/9/19
5
2、铸件凝固温度场
2、凝固传热研究方法
◎解析法:假设一维导热
T 2T
t x2
通解 TcDer(f x ) 2 t
对铸件:边界条件
初始条件
对铸型:边界条件
初始条件
T1Ti (Ti T10)er(f2x1t) T2Ti (T20Ti)er(f2x2t)
铸件凝固时间:液态金属充满铸型的时刻到凝固完毕所 需要的时间。
凝固速度:单位时间凝固层增长的厚度。 铸件凝固时间的确定方法:试验法、数值模拟法、计算
法。 1、理论计算法
t2 b2 A 1V 11LC Ti1 TT 浇 2 0TS
计算温度场有些假设,算出的凝固时间是近似的。 应用较少。
2020/9/19