英国ContourTools金刚石切削刀具
论述金刚石刀具超精密切削的机理丶条件和应用范围

金刚石刀具超精密切削的机理丶条件和应用范围
金刚石刀具是超精密切削中常用的刀具材料,其切削机理、条件和应用范围如下:
1.切削机理:
⏹金刚石刀具的切削刃非常锋利,在切削过程中能够实现“切入式切削”,
使切削力大大减小。
⏹金刚石的硬度极高,切削时不易被工件材料磨损,能够保持良好的切削刃
形状。
⏹金刚石的传热性能极佳,能够快速地将切削热量传递出去,从而降低切削
温度,减少热损伤。
1.切削条件:
⏹刀具刃口半径:为了实现超精密切削,需要将刀具的刃口半径减小到亚微
米级,以提高切削的精度和表面粗糙度。
⏹切削用量:为了减小切削力和热量,需要选择较小的切削深度和进给速度,
以提高切削效率。
⏹工件材料:金刚石刀具适用于加工各种硬材料,如淬火钢、硬质合金等。
但是,对于一些韧性较大的材料,需要进行预处理或选择其他刀具材料。
1.应用范围:
⏹金刚石刀具广泛应用于超精密切削领域,如光学零件、轴承、硬盘磁头、IC
芯片等高精度、高表面质量的零件加工。
⏹在加工过程中,金刚石刀具还可以用于制作各种微细结构,如微孔、微槽
等。
综上所述,金刚石刀具的超精密切削需要满足一定的条件,并具有广泛的应用范围。
精密车削过程中难点分析

精密车削过程中难点分析李金玉北京京煤集团三河综合厂个人简历精密车削过程中难点分析摘要:精密切削加工选用的背吃刀量极小(几微米甚至小于1微米),因此切削力及温度对加工精度的影响不容忽视。
关键词:精密机床进给量背吃刀量温度在长时间试切过程中,对于切削用量、刀具几何参数、工件材质等因素对表面粗糙度的影响较为重视,而往往忽视了切削力对表面粗糙度的二次影响。
因此,减小切削力对表面粗糙度的影响已成为精密切削领域一个亟待解决的重要问题。
其次,温度对加工也有不可忽视的影响。
一、引言经过近些年的不断发展,精密机床的加工性能已达到相当高的水平。
由于精密切削加工选用的背吃刀量极小(几微米甚至小于1微米),因此切削力对加工精度的影响不容忽视。
在精密切削中,由于金刚石刀具的切削刃具有钝圆半径,因此前刀面被分为平面和圆柱面两部分(圆柱面部分均为负前角)。
当选用不同的背吃刀量时,刀具前刀面的两个部分在切削过程中所起作用和所占比重也各不相同。
以前刀面圆弧部分为主要工作部分时,其单位切削面积所受切削力比以平面部分为主要工作部分时大得多,切削层越薄,单位面积所受切削力越大。
切削力对被加工工件的尺寸和形状精度、加工表面粗糙度、加工变质层和刀具耐用度等均具有直接或间接影响。
在长时间试切过程中,对于切削用量、刀具几何参数、工件材质等因素对表面粗糙度的影响较为重视,而往往忽视了切削力对表面粗糙度的二次影响。
因此,减小切削力对表面粗糙度的影响已成为精密切削领域一个亟待解决的重要问题。
其次,温度对加工也有不可忽视的影响。
本文通过精密车削,研究了各切削参数对切削力的影响规律。
二、精密车削条件1、精密机床拿HCM-I型精密车床来说,机床工作台由直流伺服电机驱动,进给分辨率0.01μm;采用空气静压主轴(回转精度±0.1μm);导轨部件采用可抗温度干扰的花岗岩材料,空气导轨直线度误差0.13μm/100mm;采用空气弹簧作为减振、隔振系统;机床固有频率:水平方向≤1.12Hz,垂直方向≤2Hz。
金刚石刀具在数控机床中的应用

金刚石刀具在数控机床中的应用随着科技的不断进步和发展,数控机床在工业领域中扮演着重要的角色。
数控机床的出现大大提高了生产效率和加工质量,而金刚石刀具作为一种高性能的切削工具,在数控机床中的应用也越来越广泛。
本文将探讨金刚石刀具在数控机床中的应用,并分析其优势和挑战。
一. 金刚石刀具的基本特性金刚石刀具由金刚石颗粒和金属粉末经压制、烧结等工艺制成,具有极高的硬度、耐磨性和热稳定性。
这些特性使得金刚石刀具在切削加工中具备以下优势:1. 高硬度:金刚石刀具的硬度仅次于金刚石,可用于切削超硬材料如陶瓷和高硬度合金等。
2. 耐磨性:金刚石刀具具有出色的耐磨性,可在切削过程中保持较长的使用寿命。
3. 热稳定性:金刚石刀具具有良好的热稳定性,可承受高温切削环境下的工作,不易变形。
二. 金刚石刀具在数控机床中的应用领域1. 切削加工金刚石刀具广泛应用于数控机床的切削加工领域,包括车削、铣削、钻削、磨削等。
由于金刚石刀具的高硬度和耐磨性,可用于加工硬度较高的材料,如钛合金、高速钢等。
同时,金刚石刀具还能够提供更高的加工精度和表面质量。
2. 精密加工在数控机床的精密加工中,金刚石刀具的应用更能体现出其独特的优势。
例如,在汽车零部件的精密加工过程中,采用金刚石刀具可以实现更高的加工精度和更好的表面质量。
3. 工具磨损监测由于金刚石刀具的耐磨性较高,因此可以通过监测金刚石刀具的磨损情况,准确地评估刀具的使用寿命。
这对机床的保养和刀具的及时更换具有重要意义,可降低生产成本,并提高生产效率。
三. 金刚石刀具在数控机床中的挑战虽然金刚石刀具在数控机床中有广泛的应用前景,但面临着一些挑战和限制:1. 成本高昂:金刚石刀具的制造成本较高,所以其售价也相对较高,这给广泛应用带来了一定的限制。
2. 技术要求高:金刚石刀具的加工工艺复杂,需要高精度和高温高压的条件,所以其生产过程要求较高的技术水平。
3. 刀具表面质量难以保证:由于金刚石刀具的硬度很高,常规的抛光或修整技术难以完成对其表面的加工,从而可能会影响到加工表面质量。
在单点金刚石机床上用刨削加工微槽的方法
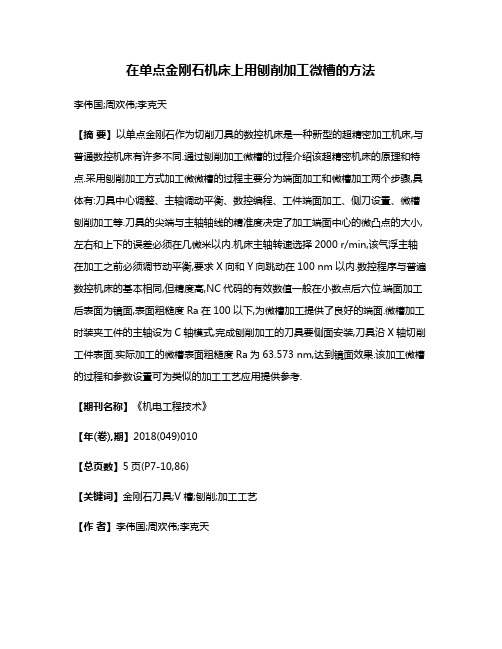
在单点金刚石机床上用刨削加工微槽的方法李伟国;周欢伟;李克天【摘要】以单点金刚石作为切削刀具的数控机床是一种新型的超精密加工机床,与普通数控机床有许多不同.通过刨削加工微槽的过程介绍该超精密机床的原理和特点.采用刨削加工方式加工微微槽的过程主要分为端面加工和微槽加工两个步骤,具体有:刀具中心调整、主轴调动平衡、数控编程、工件端面加工、侧刀设置、微槽刨削加工等.刀具的尖端与主轴轴线的精准度决定了加工端面中心的微凸点的大小,左右和上下的误差必须在几微米以内.机床主轴转速选择2000 r/min,该气浮主轴在加工之前必须调节动平衡,要求X向和Y向跳动在100 nm以内.数控程序与普遍数控机床的基本相同,但精度高,NC代码的有效数值一般在小数点后六位.端面加工后表面为镜面,表面粗糙度Ra在100以下,为微槽加工提供了良好的端面.微槽加工时装夹工件的主轴设为C轴模式,完成刨削加工的刀具要侧面安装,刀具沿X轴切削工件表面.实际加工的微槽表面粗糙度Ra为63.573 nm,达到镜面效果.该加工微槽的过程和参数设置可为类似的加工工艺应用提供参考.【期刊名称】《机电工程技术》【年(卷),期】2018(049)010【总页数】5页(P7-10,86)【关键词】金刚石刀具;V槽;刨削;加工工艺【作者】李伟国;周欢伟;李克天【作者单位】广东机械技师学院,广东广州 510450;广州铁路职业技术学院,广东广州 510430;广东工业大学,广东省微纳加工技术与装备重点实验室,广东广州510060【正文语种】中文【中图分类】TG55美国摩尔公司生产的NanoTech 350FG机床是一种超精密自由曲面加工机床,具有三条直线运动轴X、Y和Z以及两个旋转轴B和C。
可实现的加工方式有两轴车削、铣削、飞刀切削、刨削和磨削等,还可以实现快刀伺服和慢刀伺服加工。
用于加工球面、非球面以及自由曲面的光学镜面以及其他高精度机械零件,例如模具的模仁。
金刚石刀具知识点

⾦刚⽯⼑具知识点⼑具基础知识⼀、⼑具材料应具备的性能;A,⾼的硬度和⾼耐磨性1.硬度是⼑具材料应具备的基本特性2.耐磨性是指材料抵抗磨损的能⼒。
B,⾜够的强度和韧性1.强度是⼑具材料抵抗破坏的能⼒2,韧性是指材料发⽣断裂时外界做功的⼤⼩。
3.⾼的耐热性和热传性4.良好的⼯艺性和经济性1)切削性能⽬前⼑具材料分四⼤类:⼯具钢、硬质合⾦、陶瓷及超硬⼑具材料等。
常⽤的⼑具材料⼀、⼯具钢1. 碳素⼯具钢碳素⼯具钢是含碳量为0.65%~1.3%的优质碳素钢。
常⽤的钢号有T7A、T8A等。
耐热温度:200℃~300℃。
2. 合⾦⼯具钢1868年,英国的穆舍特制成含钨的合⾦⼯具钢。
在碳素⼯具钢中加⼊适当的元素铬(Cr)、硅常⽤的合⾦⼯具钢有9CrSi,CrWMn等(Si)、锰(Mn)、钒(V)、钨(W)等炼成的。
耐热温度:325℃~400℃。
主要⽤于制造细长的或截⾯积⼤、刃形复杂的⼑具。
⼆,⾼速钢⾼速钢是⼀种富含钨(W)、铬(Cr)、钼(Mo)、钒(V)等元素的⾼合⾦⼯具钢。
美国的F.W.泰勒和M.怀特于1898年创制的。
含碳量⼀般在0.70~1.65%之间。
耐热温度:500℃~650℃。
⾼速钢的抗弯强度是硬质合⾦的3~5倍,冲击韧性是硬质合⾦的6~10倍1.普通⾼速钢(HSS)2.钨系⾼速钢:W18Cr4V (W18)3.具有较好的综合性能,可制造复杂刃型的⼑具。
但由于钨是稀有⾦属,现在很少使⽤。
4.钨钼系⾼速钢:W6Mo5Cr4V2 (M2)5.M2的碳化物颗粒⼩,分布均匀,具有较⾼的抗弯强度、塑性、韧性和耐磨性。
⼜因为钼的存在,使其热塑性⾮常好。
2. ⾼性能⾼速钢(HSS-E)⾼性能⾼速钢是在普通⾼速钢中增加⼀些碳、钒及添加钴(Co)、铝等元素的新钢种。
钴⾼速钢:W2Mo9Cr4VCo8 (M42)⼀种含钴的超硬⾼速钢,常温硬度67HRC-69HRC,具有良好的综合性能。
铝⾼速钢:W6Mo5Cr4V2Al在M2的基础上加Al、增C,提⾼了钢的耐热性和耐磨性。
单晶金刚石车刀在超精密单点切削中的磨损分析

单晶金刚石车刀在超精密单点切削中的磨损分析磨损分析是评估单晶金刚石车刀在超精密单点切削中使用过程中的性能退化情况。
磨损是由切削力和摩擦力引起的,而超精密单点切削要求较小的切削力和摩擦力。
因此,单晶金刚石车刀的磨损是非常重要的。
首先,单晶金刚石车刀的磨损主要有两种形式:刃口磨损和表面磨损。
刃口磨损会导致车刀的切削边缘变钝,从而降低切削效率和切削质量。
表面磨损主要是由刀具与工件表面接触时产生的摩擦引起的。
这些磨损形式都会导致单晶金刚石车刀的使用寿命减少。
其次,可以通过磨损分析来确定单晶金刚石车刀的磨损程度。
常用的磨损评估方法有:测量切削力和刀具表面形貌、观察工件表面质量等。
测量切削力可以间接评估刃口磨损程度,如果切削力增加,则说明刃口已经磨损。
观察工件表面质量也可以判断磨损情况,如果工件表面粗糙度增加,则说明刃口已经损坏。
最后,还可以通过磨损分析找出导致单晶金刚石车刀磨损的原因。
可能的原因包括:切削条件不合适、切削速度过高、切削液不合适等。
通过找出磨损原因,可以采取相应的措施来减少磨损,延长单晶金刚石车刀的使用寿命。
总之,单晶金刚石车刀在超精密单点切削中的磨损分析是评估其使用寿命和性能的重要手段。
通过磨损分析,可以确定磨损程度,找出导致磨损的原因,并采取相应的措施来延长车刀的使用寿命。
此外,单晶金刚石车刀磨损分析还可以提供对刀具寿命的预测和刀具性能的改进。
通过磨损分析,可以获取关于刀具磨损速率和刀具寿命的重要信息。
这些信息对于制定合理的刀具更换计划非常关键,以避免频繁更换刀具或过度使用磨损严重的刀具。
磨损分析还可以帮助改进单晶金刚石车刀的设计和制造工艺。
通过观察磨损形态和区域,可以了解刀具的磨损机制和影响因素。
这对于优化刀具的材料、几何形状和涂层等方面非常有价值。
例如,可以针对刀具的磨损情况进行改进,使其更耐磨、更耐用,并提高切削效率和切削质量。
此外,磨损分析还可以通过对比不同切削条件下的磨损情况,寻找最佳的切削参数组合。
知名切削刀具制造商网址(欧美篇)

知名切削刀具制造商网址(欧美篇)2011-01-29 18:57(法国EPB)山高旗下世界上首屈一指的刀柄系统及镗刀制造商,以其一流的产品性能和完美的技术服务著称于世。
(法国塞菲提)成立于1932年,欧洲汽车制造厂商眼中的最佳刀具供应商,现隶属山特维克集团。
www.outiltec.fr(法国无敌泰克)IMC旗下著名刀具公司,擅长于钻头、铰刀、成型刀具,特别是枪钻的非标制作。
(意大利丹德瑞)著名的镗刀及平旋盘制造厂商。
(意大利Fiudi)成立于1959年,主要从事CBN,PCD和天然金刚石各类刀具产品的生产制造。
(西班牙JMC)生产丝锥与铰刀60余年。
(西班牙克耐乐)知名可转位刀具供应商。
www.palbit.pt(葡萄牙帕比特)欧洲老牌硬质合金工具厂。
(瑞士迪哈特)拥有世界闻名的高精度铰刀,也是PCD刀具业的领导者,隶属于高迈特集团。
(瑞士弗雷萨)世界著名刀具生产厂商之一,特色产品高速切削铣刀。
(瑞士好优利)发明出了第一把用于去毛刺的刀具。
(瑞士凯撒)知名的工具系统品牌,日本大昭和的技术提携者。
mina-tech.ch(瑞士拉米那)瑞士最先进的硬质合金刀具制造厂,开发出了万用材质刀片。
(瑞士斯特拉姆)有80年制造硬质合金刀具历史,现隶属美国ATI 冶联,擅长加工难加工金属材料。
www.urma.ch(瑞士钨马)国际知名的专业模块式镗刀的生产厂家,在世界上拥有众多的用户,孔加工刀具的领先者。
/cn(瑞典山特维克)经过140余年的发展,在制造工艺方面已经发展成为全球的领导者。
(瑞典山高)世界上硬质合金刀具的主要制造商。
(丹麦尤尼莫克)是一个国际化的刀具优化解决方案制造商和供应商,2011年被京瓷公司收购。
(荷兰嘉伯乐)山高旗下知名整体式铣刀品牌。
(北爱尔兰欧霸)是全世界生产铣刀和槽钻最大制造商之一。
(奥地利梅克斯特)欧洲知名旋转刀具制造商。
(奥地利贝瑞特)蓝帜旗下专业提供切削材料和硬质合金材料的制造商。
《金刚石涂层刀具》课件

优点:可以提高刀具的使用寿 命,降低加工成本,提高加工
精度和效率
原料准备:金刚石粉、粘结剂、溶剂等 混合搅拌:将金刚石粉与粘结剂、溶剂混合均匀 涂覆:将混合好的金刚石粉涂覆在刀具表面 固化:将涂覆好的刀具放入固化炉中,加热固化 打磨抛光:对固化后的刀具进行打磨抛光,提高刀具的表面质量 检测:对刀具进行性能检测,确保其符合使用要求
PPT,a click to unlimited possibilities
汇报人:PPT
CONTENTS
PART ONE
PART TWO
特性:耐磨性高、耐热性好、 硬度高、化学稳定性好
金刚石涂层刀具是一种在刀具 表面涂覆一层金刚石颗粒的刀 具
应用领域:广泛应用于机械加 工、航空航天、汽车制造等领
挑战:金刚石涂层刀具的制造 过程中,需要解决金刚石涂层 的加工精度和表面粗糙度问题
解决方案:采用先进的加工技 术和设备,提高金刚石涂层刀 具的加工精度和表面粗糙度
挑战:金刚石涂层刀具在加工过程中容易磨损 解决方案:采用先进的涂层技术,提高刀具的耐磨性 挑战:金刚石涂层刀具在加工过程中容易产生热量 解决方案:采用冷却技术,降低刀具的温度,提高加工精度 挑战:金刚石涂层刀具在加工过程中容易产生振动 解决方案:采用先进的加工工艺,降低刀具的振动,提高加工
在汽车、航空航天、电子等领 域,金刚石涂层刀具被广泛用 于磨削和研磨加工
金刚石涂层刀具在磨削和研磨 中的应用广泛,可以提高加工 效率和精度
金刚石涂层刀具在磨削和研磨 加工中具有耐磨、耐热、耐腐
蚀等优点
金刚石涂层刀具在磨削和研磨 加工中可以实现高精度、高效
率的加工效果
医疗领域:用于制造手术刀、 牙科钻头等医疗器械
金刚石刀具

金刚石的刀具发展与技术侯文文0840202211摘要:本文主要对金刚石刀具的分类、加工方法、金刚石刀具的发展现状及应用领域作了简单的介绍,对聚晶金刚石刀具的刃磨技术作了详细的研究分析。
1、引言:随着现代加工制造业对高速切削加工的要求不断提高,对于各种难切削复合材料、工程陶瓷材料等,传统的切削加工刀具已不能满足高速切削的需要,而超硬切削刀具是解决以上问题的有效手段,其中,金刚石刀具的应用较为广泛。
金刚石具有极高的硬度、良好的耐磨性和导热性、低摩擦系数和热膨胀系数,在现代切削加工中体现出难以替代的优越性,被誉为当代提高生产率最有希望的刀具材料之一。
目前,金刚石刀具在机械加工中的应用日渐普及,已成为现代材料加工中不可或缺的重要工具。
2、金刚石刀具的基本介绍2.1 天然金刚石(ND)刀具为天然金刚石拉蔓峰谱,具有以下特征:(1)1332尖锋处显示存在金刚石。
(2)波型幅度(FWHM)为4.1cm-1显示为纯金刚石。
ND是目前已知矿物中最硬的物质,主要用于制备刀具车刀。
天然金刚石刀具精细研磨后刃口半径可达0.01~0.002µm。
其中天然单晶金刚石(Single Crystalline Diamond,SCD)刀具切削刃部位经高倍放大1500倍仍然观察到刀刃光滑。
SCD车削铝制活塞时Ra可达到4µm,而在同样切削条件下用PCD 刀具加工时的表面粗糙时的Ra为15~50µm。
故采用SCD刀具配合精密车床进行精密和超精密加工,可获得镜面表面。
2.2 聚晶金刚石(PCD)刀具PCD是高温超高压条件下通过钴等金属结合剂将金刚石微粉聚集烧结合成的多晶体材料,又称烧结金刚石。
聚晶金刚石刀具整体烧结成铣刀,用于铣削加工,PCD晶粒呈无序排列状态,属各向同性,硬度均匀,石墨化温度为550℃。
刀具具有高硬度、高导热性、低热胀系数、高弹性模量和低摩擦系数。
刀刃非常锋利等特点。
超精密切削与金刚石刀具

金刚石刀具的性能特点
➢ 极高的硬度和耐磨性:硬度达HV10000,是自然界最硬的物质, 具有极高的耐磨性,天然金刚石耐磨性为硬质合金80-120倍,人 造金刚石耐磨性为硬质合金60-80倍。
➢ 各向异性能:单晶金刚石晶体不同晶面及晶向的硬度、耐磨性能 、微观强度、研磨加工的难易程度以及与工件材料之间的摩擦系 数等相差很大,因此,设计和制造单晶金刚石刀具时,必须进展 晶体定向。
普通刀具前刀面磨损
普通刀具前刀面的破损
普通刀具后刀面磨损
普通刀具粘结磨损
超精细切削刀具磨损与寿命
第三节 超精细切削刀时积屑瘤的生成规律
,
法应力
=s 剪应力,=
O
A
B
刀具
OA—粘结区〔内摩擦区〕:摩擦系数是变化的 AB—滑动区〔外摩擦区〕:摩擦系数是常数 影响前刀面摩擦系数的主要因素 工件材料,切削厚度,切削速度,刀具前角
✓ 天然单晶金刚石有一系列优点,如:硬度高、导热 系数大、摩擦系数低、刀刃能磨得锋利,虽然价格 昂贵,但仍被一致公认为理想、不可替代的超精细 切削刀具。
金刚石刀具
金刚石刀具
天然单晶金刚石刀具 单晶金刚石刀具
人造单晶金刚石刀具
PCD刀具 多晶金刚石刀具
CVD金刚石薄膜涂层刀具
CVD金刚石刀具
金刚石厚度膜焊接刀具
超精细切削与金刚石刀具
本课件PPT仅供大家学习使用 学习完请自行删除,谢谢! 本课件PPT仅供大家学习使用 学习完请自行删除,谢谢! 本课件PPT仅供大家学习使用 学习完请自行删除,谢谢! 本课件PPT仅供大家学习使用 学习完请自行删除,谢谢!
传统切削加工方式
车刀和车削
钻头和钻削
铣刀与铣削
铣刀与铣削
金刚石刀具标准

金刚石刀具标准金刚石刀具的标准主要包括对其物理性能、制造工艺、几何参数、使用性能等方面的详细规定。
以下是一些关于金刚石刀具标准的信息:1.物理性能标准:硬度:金刚石刀具的硬度极高,约为HV10000(维氏硬度)。
导热性:PCD(聚晶金刚石)刀具的导热系数非常高,约700W/mK,有利于散热和延长刀具使用寿命。
热膨胀系数:PCD的热膨胀系数远低于硬质合金,使得在高温加工条件下仍能保持良好的尺寸稳定性,有助于提高加工精度。
2.制造工艺标准:金刚石颗粒大小:根据用途和精度要求,金刚石刀具的金刚石颗粒度可分为粗粒度、中粒度和细粒度三个级别,分别对应不同的加工应用和切削性能。
结合剂成分与含量:金刚石刀具性能受到金刚石晶粒与结合剂(如钴)含量的影响,标准会规定合适的配方比例以保证刀具的强度和耐磨性。
3.几何参数标准:刀具的前角、后角、主偏角、副偏角、刃倾角等几何参数都有严格的公差范围,以满足不同材料和加工方式的需求。
4.使用性能标准:刀具寿命:金刚石刀具因其优异的耐磨性和耐热性,其寿命普遍远高于硬质合金刀具,具体标准可能涉及到连续切削长度或切削次数等指标。
加工精度:根据国家或行业标准,金刚石刀具在使用过程中应能达到规定的加工精度和表面粗糙度要求。
5.国内标准:国内对于金刚石刀具的质量和生产有专门的国家标准,例如提到的“燕矶标准”是中国国家金刚石刀具生产标准的一部分,由国家和地方技术监督部门联合制定,以确保产品质量和一致性。
要了解具体的金刚石刀具标准,可以查阅相关国家标准,如GB/T系列标准,以及行业标准等官方发布的详细文档。
此外,国际上也有一些ISO标准对金刚石刀具的生产和检测进行了规定。
金刚石刀具切削加工课件
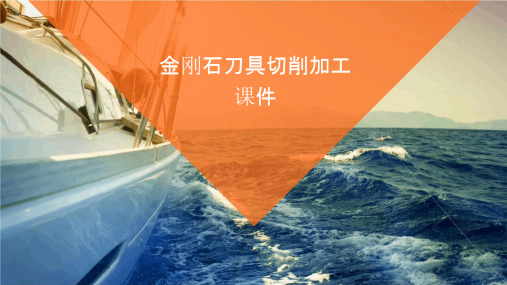
1.谢谢聆 听
03
降低成本和提高经济效益
随着金刚石刀具材料的发展和新型切削工艺的应用,金刚 石刀具在难加工材料切削加工中的应用将会降低成本和提 高经济效益。
金刚石刀具切削加工案例分析
06
案例一
要点一
总结词
高效、高精度、高可靠性
要点二
详细描述
金刚石刀具在汽车零件切削加工中表现出高效、高精度和 高可靠性的优势。通过优化切削参数和刀具设计,能够实 现高效加工,提高生产效率。同时,金刚石刀具具有高硬 度和高耐磨性,可保证加工精度和延长刀具使用寿命。此 外,金刚石刀具切削过程中产生的热量较少,可减少工件 热变形和加工误差。
素有关。
通过合理的选择刀具材料和几何 参数,可以降低切削力,提高加
工效率。
金刚石刀具的切削热
金刚石刀具的切削热主要来自于切削刃与工件之间的摩擦和冲击。
切削热会导致刀具温度升高,从而影响刀具的硬度和耐磨性,甚至引起工件变形和 产生表面缺陷。
通过使用冷却润滑剂和选择合适的刀具材料和几何参数,可以降低切削热的影响。
特点
硬度高、耐磨性好、热稳定性优 异、抗粘结性好、导热性好、化 学稳定性好。
金刚石刀具切削加工的应用范围
01
难加工材料
如硬质合金、陶瓷、玻璃等硬脆材料。
02
高精度加工
如超精密切削、微细加工等。
03
高效率加工
如粗加工、重型切削等。
金刚石刀具切削加工的历史与发展
历史
金刚石刀具的发展可以追溯到20世纪初,当时人们开始利用天然金刚石进行手 工切削。随着科技的发展,人造金刚石的出现进一步推动了金刚石刀具的发展。
智能化控制
随着人工智能技术的发展,智能化控制技术在金刚石刀具切削加工中得到了广泛应用,通 过智能化控制技术,能够对切削过程进行实时监控和调整,从而提高加工精度和效率。
Seco Tools公司推出可加工硬质钢材的硬质合金立铣刀

Seco Tools公司推出可加工硬质钢材的硬质合金立铣刀无
【期刊名称】《模具工程》
【年(卷),期】2009(000)008
【摘要】SecoTools公司通过采用Jabro5HF180MEGA-64系列硬质合金金立铣刀,正在继续成功地开发高进给铣削方案(HFM),从而可加工硬度为48—
62HRC的硬质钢材。
JHF180铣刀尤其适用于模具,其寿命比变通硬质合金立铣刀多出400%。
【总页数】1页(P40)
【作者】无
【作者单位】无
【正文语种】中文
【中图分类】TG71
【相关文献】
1.Monster Tool公司推出多用途硬质合金旋转锉 [J], 无
2.肯纳推出加工碳纤维增强复合材料的整体硬质合金立铣刀系列 [J],
3.山高推出小颈硬质合金立铣刀 [J],
4.伊斯卡推出EPN-F整体硬质合金立铣刀 [J], 田付新
5.山高推出应用更广的硬质合金立铣刀 [J],
因版权原因,仅展示原文概要,查看原文内容请购买。
金刚石涂层刀具综述

涂层金刚石刀具综述1引言随着汽车、航空和航天等工业的发展,有色金属及合金、纤维增强塑料、纤维增强金属以及石墨、陶瓷等新型先进材料越来越多的应用到这些工业产品中,这对机械加工提出了高效率,高精度等要求,普通刀具已经不能满足需求,而迫切需要一种耐磨性更高、能稳定实现高精、高效、寿命更长的超硬刀具。
金刚石涂层刀具因其具有十分接近天然金刚石的硬度和耐磨性、高的弹性模量、极高的热导率、良好的自润滑性和化学稳定性等优异性能,成为加工难加工材料的理想刀具。
化学气相沉积(CVD)金刚石问世于20世纪80年代初[1],1987年美国的Crystallume公司率先在CZ硬质合金刀片上沉积金刚石涂层。
1995年瑞士的Sandvik公司与美国的Balzers AG公司合作建立了一条金刚石涂层生产线。
1997年日本的刀具公司在北京展出了他们的金刚石涂层刀具。
目前,国外已有金刚石涂层的丝锥、钻头、绞刀、立铣刀及可转位刀片等产品出售[2],很多公司推出了自己的金刚石涂层产品,并且一些产品已进入了商品化阶段,如美国的Norton 公司、SP3公司,欧洲的Balzers公司、Cemen Cone公司、Sandivik公司、美国诺顿公司等。
图1.1为国外生产的金刚石涂层刀具。
(a) 德国 Emuge Franken 公司产品 (b) 瑞士 Balzers 公司产品图 1.1 国外公司生产的 CVD 金刚石涂层刀具CVD金刚石涂层刀具是利用化学气相沉积的方法在韧性好,强度高的硬质合金基体上沉积一定厚度的金刚石薄膜制造而成的。
目前金刚石涂层刀具常用的基体材料为与金刚石的热膨胀系数较为接近的Si3N4系陶瓷和WC系硬质合金。
其中Si3N4系陶瓷具有较高的硬度、耐磨性和热稳定性,与金刚石的热膨胀系数最为接近,因此一直被认为是CVD金刚石涂层较为理想的基体材料。
但是,由于Si3N4陶瓷本身脆性大,抗冲击性能差,一般认为,Si3N4基金刚石涂层刀具仅宜用于精加工,而不宜进行冲击切削加工。
超硬刀具金刚石刀具介绍

超硬刀具金刚石刀具介绍PCD聚晶金刚石刀具;CVD金刚石膜刀具(物理涂层)PVD物理涂层金刚石刀具PCBN聚晶立方氮化硼刀具;一、概述超硬刀具材料是指比陶瓷材料更硬的刀具材料。
包括:单晶金刚石、聚晶金刚石(PCD)、聚晶立方氮化硼(PCBN)和CVD金刚石等。
超硬刀具主要是以金刚石和立方氮化硼为材料制作的刀具,其中以人造金刚石复合片(PCD)刀具及立方氮化硼复合片(PCBN)刀具占主导地位。
许多切削加工概念,如绿色加工、以车代磨、以铣代磨、硬态加工、高速切削、干式切削等都因超硬刀具的应用而起,故超硬刀具已成为切削加工中不可缺少的重要手段。
随着科技的进步,制造业的高速发展,CNC 加工技术的迅猛发展以及数控机床的普遍使用,超硬刀具的生产及应用也越来越广泛。
PCD和PCBN刀具已广泛应用于机械加工的各个行业,如汽车零部件的切削加工,强化木地板的加工等,极大地促进了切削加工及先进制造技术的飞速发展。
二、切削材料及超硬材料发展史3、金刚石、超硬材料的特性与作用众所周知,金刚石材料的成分是碳,金刚石与铁系有亲和力,切削过程中,金刚石的导热性优越,散热快,但是要注意切削热不宜高于700度,否则会发生石墨化现象,工具会很快磨损。
因为金刚石在高温下和W、Ta、Ti、Zr、Fe、Ni、Co、Mn、Cr、Pt等会发生反应,与黑色金属(铁碳合金)在加工中会发生化学磨损,所以,金刚石不能用于加工黑色金属只能用在有色金属和非金属材料上,而CBN即使在1000oC的高温下,切削黑色金属也完全能胜任。
已成为未来难加工材料的主要切削工具材料。
一般超硬材料指的是人造金刚石、人造CBN。
这两种材料的同时存在,起到了互补的作用、可以覆盖当前与今后发展的各种新型材料的加工,对整个切削加工领域极为有利。
1.PCD金刚石烧结体(PCD)的出现,在许多方面代替了天然单晶金刚石。
PCD与天然金刚石比较,价格便宜,且刃磨远比天然金刚石方便,所以其应用、推广特别迅速。
金刚石涂层刀具

金刚石涂层刀具为迎合用户对提高生产效率、减轻产品重量提出的要求,在机械加工中,正更多地使用各种先进材料。
很多企业在汽车零件和飞机结构件中大量使用非铁材料,如硅铝合金、金属基和碳复合材料、玻璃纤维加强塑料等。
虽然这些材料重量较轻,但在材料中添加了硬质耐磨颗粒作为强化剂,这无疑加添了这些材料的加工难度,这些硬质颗粒会造成刀具过早磨损和产生大量切削热。
刀具磨损重要是由硬颗粒的摩擦磨损和酸腐蚀的化学磨损所致。
因此,多数刀具用户认为,金刚石涂层刀具是加工耐磨的非铁金属和非金属复合材料的理想刀具。
在各种刀具涂层中,用金刚石涂层刀具加工难加工材料能很好地保护切削刃,且无化学磨损。
金刚石涂层与其它涂层的对比金刚石涂层是用化学气相沉积(CVD)方法沉积在可转位刀片或旋转刀具的表面上,CVD方法只适用于整体硬质合金刀具,不适合钎焊的硬质合金刀片和高速钢刀具,由于过高的沉积温度(1400F)会损坏钎焊的硬质合金刀片和高速钢刀具。
用物理气相沉积(PVD)的金属氮化物(如TiAlN涂层)的显微硬度只相当于金刚石涂层的1/3,虽然一些PVD碳涂层称为“类金刚石涂层”,但它们并不具备金刚石涂层的硬度性能,这些无定形碳涂层的最高显微硬度仅仅是金刚石涂层的50%。
金刚石涂层的硬质合金刀具的优点是综合了天然金刚石的硬度和硬质合金的强度及断裂韧性,所以金刚石涂层完全可用于具有多而杂形状切削刃的旋转刀具以及具有多而杂断屑槽形的多刃刀具。
金刚石涂层刀具在加工非金属复合材料和塑料时,刀具寿命可比不涂层的硬质合金刀具提高10~20倍或更高,而且在加工非铁金属和复合材料时提高了材料切除率。
对于加工表面干净度要求高、抗磨粒磨损和抗腐蚀磨损的切削加工,最适合采纳金刚石涂层刀具,而采纳未涂层的硬质合金刀具进行加工很难达到上述要求。
金刚石涂层应用于特种刀具的进展趋势与九十时代PVD涂层应用于加工刀具后显著提高了切削性能相像佛,使刀具品牌上了一个新台阶。
可与单晶金刚石刀具媲美的PCD刀具

可与单晶金刚石刀具媲美的PCD刀具单晶(天然)金刚石刀具广泛应用于精密零件(如光学镜片)的切削加工,因为这种刀具能加工出超精细的表面光洁度,并能达到极高的廓形精度。
然而,单晶金刚石的成本较高,为其他刀具材料(如烧结PCD和硬质合金)的2-5倍。
用化学气相沉积法(CVD)在刀具(如钴含量小于6%的硬质合金刀具)上沉积厚度为2-500μm的聚晶金刚石(称为CVD金刚石或PCVD)薄膜已经有几十年的历史。
近20年前,Norton金刚石薄膜公司(当时还是圣戈班磨料磨具公司的业务部门之一,现在其业务已被合并到圣戈班的其他部门)成为率先制备出厚度约1mm 的CVD金刚石厚膜的企业之一。
如下表所示,CVD金刚石的硬度和强度高于烧结PCD、硬质合金(Co含量6%)、氮化硅和碳化硅等硬质材料,与天然金刚石不相上下。
然而,由于制备CVD金刚石厚膜和刀具焊接的成本较高,技术的突破并没有转化为市场的成功。
表 CVD金刚石与其他硬质材料的力学性能对比金刚石切削的诀窍在于:用金刚石刀具的硬晶面和硬晶向去切削工件材料的软晶面和软晶向。
为了提高刀具的切削能力,CVD金刚石厚膜的硬晶面与软晶面一起生长,使其具有更好的强度。
但是,将CVD金刚石厚膜复合片精确磨削成所需要的形状大大增加了加工难度和成本。
由于过去几年来天然金刚石价格的快速攀升,刀具制造商开始寻求经济实用的CVD金刚石厚膜制备和刀具焊接技术。
强劲的行业需求催生出了新一代的直流电弧等离子体反应炉(见图),这种设备能以较好的成本效益沉积出直径达100mm、厚度达2mm的CVD金刚石厚膜。
图直流电弧等离子体反应炉从材料的化学成分来看,CVD金刚石为99.999%的纯碳,其纯度甚至超过了天然金刚石,因为CVD金刚石是在严格控制环境条件的实验室中制成的。
因此,用实验室沉积的CVD金刚石通常可以制成品质更高的切削刀具。
然而,由于CVD金刚石生长速度较快,因此在其内部往往存在很高的内应力。
英国Contour Tools金刚石切削刀具

英国Contour Tools金刚石切削刀具
总部位于英国的康图公司(Contour Fine Tooling)是国际著名的金刚石刀具制造商,已有20多年的历史,致力于为客户提供超精密、高质量的刀具,在单点金刚石切削领域享有极高的荣誉。
其生产的刀具广泛应用于超精密加工和光学领域。
包角在不超过120°时,精选天然金刚石作为刀头,具有好的耐磨性和前后角范围,刃磨后的刀刃非常耐用。
康图公司不仅提供金刚石车刀,而且也提供超精密金刚石铣刀。
康图金刚石刀具特点:
1、可选择控制波纹度刀具和非控制波纹度刀具
2、可选圆锥控制后刀面和圆柱控制后刀面
3、刃口在800倍Nomarski显微镜下观察无缺陷
4、刀具使用寿命长
5、精选金刚石颗粒,制作精度高,一致性好
刀具几何参数:
1、刀尖圆弧半径R:0.02-100mm
2、圆弧轮廓精度:<1.0um-<0.05um
3、刀具前角:-25°-5°
4、刀具后角:5°-15°
5、包角大小:100°或者120°120°以上需用合成单晶金刚石。
- 1、下载文档前请自行甄别文档内容的完整性,平台不提供额外的编辑、内容补充、找答案等附加服务。
- 2、"仅部分预览"的文档,不可在线预览部分如存在完整性等问题,可反馈申请退款(可完整预览的文档不适用该条件!)。
- 3、如文档侵犯您的权益,请联系客服反馈,我们会尽快为您处理(人工客服工作时间:9:00-18:30)。
英国Contour Tools金刚石切削刀具
总部位于英国的康图公司(Contour Fine Tooling)是国际著名的金刚石刀具制造商,已有20多年的历史,致力于为客户提供超精密、高质量的刀具,在单点金刚石切削领域享有极高的荣誉。
其生产的刀具广泛应用于超精密加工和光学领域。
包角在不超过120°时,精选天然金刚石作为刀头,具有好的耐磨性和前后角范围,刃磨后的刀刃非常耐用。
康图公司不仅提供金刚石车刀,而且也提供超精密金刚石铣刀。
康图金刚石刀具特点:
1、可选择控制波纹度刀具和非控制波纹度刀具
2、可选圆锥控制后刀面和圆柱控制后刀面
3、刃口在800倍Nomarski显微镜下观察无缺陷
4、刀具使用寿命长
5、精选金刚石颗粒,制作精度高,一致性好
刀具几何参数:
1、刀尖圆弧半径R:0.02-100mm
2、圆弧轮廓精度:<1.0um-<0.05um
3、刀具前角:-25°-5°
4、刀具后角:5°-15°
5、包角大小:100°或者120°120°以上需用合成单晶金刚石。