光学加工工艺
光学冷加工工艺流程

光学冷加工工艺流程光学冷加工是一种利用激光技术进行加工的方法,它可以在材料表面形成微小的热效应区域,通过控制激光加热时间和能量密度,实现材料的冷加工。
光学冷加工广泛应用于精密加工、微纳加工和光学元件制备等领域,具有高效、高精度和无损伤等优点。
光学冷加工的工艺流程主要包括以下几个步骤:1. 材料准备:首先需要选择适合光学冷加工的材料,常见的材料有金属、陶瓷、玻璃等。
对于需要进行精密加工的材料,还需要进行表面处理,以消除材料的氧化层和污染物。
2. 激光加工参数设置:根据具体的加工要求,需要设置激光的加热时间和能量密度。
加热时间和能量密度的选择需要考虑材料的热导率、熔点和热膨胀系数等因素。
3. 激光加工设备调试:将激光加工设备进行调试,确保激光的功率和焦点等参数满足要求。
同时,还需要保证加工设备的稳定性和安全性,以防止意外事故的发生。
4. 加工操作:将待加工的材料放置在加工平台上,并通过光学系统将激光聚焦在材料表面。
激光加热后,材料会在短时间内形成微小的热效应区域。
在这个过程中,需要保持激光加工头与材料表面的距离恒定,并控制激光加热时间和能量密度,以控制热效应区域的形成和扩散。
5. 加工结果检验:完成加工后,需要对加工结果进行检验。
通常可以通过显微镜观察材料表面的形貌和微观结构变化,并使用精密测量仪器对加工尺寸进行测量。
如果加工结果符合要求,即可进行下一步的处理;如果加工结果不理想,可以调整加工参数进行再次加工。
光学冷加工工艺流程的关键在于控制激光加热时间和能量密度,以及保持激光加工头与材料表面的距离恒定。
这样可以控制材料的热效应区域,实现微小区域的冷加工。
同时,光学冷加工还可以利用光学系统的特性,实现对材料的精密加工和微纳加工。
光学冷加工具有高效、高精度和无损伤等优点,广泛应用于光学元件制备、微电子器件制备和材料表面处理等领域。
综上所述,光学冷加工工艺流程包括材料准备、激光加工参数设置、激光加工设备调试、加工操作和加工结果检验等步骤。
传统光学加工(第一章粗磨)

磁性装夹是利用电磁吸力将工件固定的一种装夹方 式。透镜的磁性装夹,是将工件先粘在具有一定平 行度要求的金属导磁圆盘上,然后把粘好零件的导 磁圆盘放到铣磨机的磁性工作盘上,并使二者对好 中心,接着,打开磁力开关,将粘有透镜的导磁圆 盘吸住。另外,采用磁性装夹铣磨球面时定中心较 困难,而且粘结上盘下盘和清洗等辅助工序又费工 时,因此,球面铣磨很少采用磁性装夹,它多用于 平面的铣磨中。
(二)粒度磨料的粒度是以颗粒的大小分类的 。我国的磨料粒度号规定,对用筛选法获得 的磨料,粒度号用一英寸长度上有多少个筛 孔数来命名的。
二、磨具 通常采用的磨具有两种,一种是普通磨料制 成的砂轮,另一种是用结合剂固着的金刚石 磨具。 (一)金刚石磨具的结构 1.金刚石层:它是金刚石磨具的工作部分,由 金刚石颗粒和结合剂组成。 2. 过渡层:只含有结合剂,对金刚石层和基体 之间起着连接固结作用。过渡层厚一般为1~ 2mm。
(二)真空装夹的夹具设计
真空装夹是利用真空吸附的作用力,将工件固定在 夹具上。 真空吸附装夹的优点是:操作方便,易于实现自动 化,不仅能单件加工,而且也适用于立式铣磨机上 成盘加工,生产效率高。其缺点是:对工件的直径 公差要求严格,一般要求直径公差在(-0.02)~(0.05 )mm。
(三)磁性装夹的夹具
过大的偏心量将增大磨边的磨削量,甚至造成零 件的报废。造成球面偏心的重要原因是夹具定位 面的偏心。因此在夹具制造中,要特别注意夹具 定位面d与口径D对工件回转袖线的同心度。
§1-7 球面铣磨夹具的设计
一、球面铣磨夹具的设计
在透镜铣磨中,所用的夹具通常有弹性装夹 、真空吸附装夹和磁性装夹。
无论设计和使用哪种夹具,都必须满足以下 要求: 1. 夹具装夹零件必须牢固可靠。如果装夹不 牢,加工零件会产生松劲,这不仅要影响加 工精度,甚至可能损坏零件,同时也容易造 成磨轮的磨损。
光学冷加工的工艺流程

光学冷加工的工艺流程光学冷加工是一种高精密度、高表面质量的精密加工技术。
它通过使用激光光束或电子束来对工件进行局部熔化或蒸发,然后再利用凝固后的残余热进行表面精密加工。
光学冷加工技术在微纳米加工领域具有广泛的应用,主要包括微纳米精密加工、微纳米表面处理和微纳米结构制备等方面。
光学冷加工的工艺流程可以分为以下几个步骤:首先是工件的装夹与定位。
在进行光学冷加工之前,需要将工件进行装夹,并对其进行精确定位,以保证加工的精度和稳定性。
其次是光源的选择和调节。
在光学冷加工中,通常会选择激光光束或电子束作为加工源,需要根据具体的加工任务选择合适的光源,并对其进行调节和优化。
接下来是能量传递和局部加热。
在光学冷加工中,光束或电子束会对工件表面进行局部加热,使其局部熔化或蒸发。
然后是凝固和形成残余热。
在加热后,工件表面会迅速凝固,形成残余热。
最后是残余热的利用和表面精密加工。
利用残余热对工件表面进行精密加工,例如去除表面残余材料、形成微纳米结构等。
总的来说,光学冷加工的工艺流程包括装夹定位、光源选择调节、能量传递局部加热、凝固形成残余热和残余热利用表面精密加工。
这个工艺流程是非常复杂的,需要对设备和工艺参数进行精确控制,以保证加工的精度和质量。
下面我们将从光学冷加工的原理、应用和发展趋势等几个方面对其进行更详细的介绍。
首先是光学冷加工的原理。
光学冷加工是基于光热效应的一种加工技术。
光热效应是指当光束或电子束照射到物体表面时,光能或电子能被吸收,导致局部温度的升高。
在光学冷加工中,光束或电子束通过对工件表面进行局部加热,使其局部熔化或蒸发,然后利用凝固后的残余热进行表面精密加工。
这种加工方式具有高精度、高表面质量和高加工效率的优点,特别适用于微纳米加工领域。
光学冷加工技术在微纳米加工领域具有广泛的应用。
它可以用于微纳米精密加工,例如微孔加工、微型器件加工等;还可以用于微纳米表面处理,例如表面改性、表面粗糙度调控等;还可以用于微纳米结构制备,例如微纳米结构的形成、微纳米光栅的制备等。
光学镜片生产工艺

光学镜片生产工艺光学镜片是一种广泛应用于眼镜、相机、显微镜等光学设备中的关键部件。
其生产工艺的精密性和复杂性对于镜片的质量和性能起着决定性的作用。
本文将介绍光学镜片的生产工艺,包括材料的选择、加工工艺以及常见的光学镜片制造方法。
一、材料的选择光学镜片的材料选择对于镜片的光学性能和使用寿命有着至关重要的影响。
常见的光学镜片材料包括玻璃和塑料。
玻璃材料具有较高的折射率和透过率,适用于高精度光学镜片的制造。
塑料材料则具有较低的成本和较高的抗冲击性能,适用于一些低成本的光学镜片。
二、加工工艺1. 切割:将材料切割成所需尺寸的坯料。
切割工艺的精确度和平整度直接影响到后续加工工艺的实施。
2. 磨削:通过磨削工艺将切割好的坯料进行修整和精加工。
磨削工艺的精度和表面质量对于光学镜片的成像质量有着重要的影响。
3. 抛光:在磨削工艺后,使用抛光工艺进一步提高镜片的表面光洁度和平整度。
抛光工艺通常采用机械抛光和化学抛光两种方法。
4. 镀膜:针对特定的光学要求,通过镀膜工艺在镜片表面镀上一层薄膜,以改善镜片的透过率、反射率等光学性能。
三、光学镜片制造方法1. 球面镜片制造方法:球面镜片是最常见的一种光学镜片,其制造方法相对简单。
首先,选择适当的材料进行切割成圆形坯料,然后进行磨削和抛光工艺,最后进行镀膜。
2.非球面镜片制造方法:非球面镜片是近年来发展起来的一种新型光学镜片,其表面形状不再是球面,而是根据特定的光学要求设计的。
非球面镜片的制造方法相对复杂,常见的方法有以下几种:(1) 数控加工:利用数控机床进行精密的加工,根据设计的非球面曲线进行切削和抛光。
(2) 压制法:将热塑性材料加热至软化状态,然后通过模具进行压制,使其形成非球面镜片的形状。
(3) 电解抛光:利用电解抛光的原理,在电解液中加工镜片,通过控制电解液的浓度和电流密度,实现非球面镜片的精密加工。
四、光学镜片的质量控制光学镜片的质量控制是生产过程中至关重要的一环。
光学加工工艺简述

一:光学冷加工工序
2)铣磨: 去除镜片表面凹凸不平 的气泡和杂质,起到成 型作用
一:光学冷加工工序
3)精磨: 将铣磨出来的镜片 的破坏层给消除掉, 固定R值
一:光学冷加工工序
4)抛光: 将精磨镜片在一次抛光,这道工序主要是把 外观做的更好,光洁度在这一步确定下来
一:光学冷加工工序
5)清洗:将抛光过后的镜片表面的抛光粉清 洗干净
1)光学样板: 第一次生产某种球面镜,需要生产它的光学样板及 对板,光学样板一定要保证非常高的精确度
光学样板允许误差 R A级误差 B级误差
0.5~5mm
5~10mm 10~35mm 35~350mm 1000~40000
0.5um
1um 2um 0.02% 0.003%
1um
3um 5um 0.03% 0.005%
8:涂墨或喷黑漆, 为防止镜片边缘反光在其外 圆或未抛光区域涂上一层黑墨,一般使用光 学专用无尘净化黑漆涂笔,但对于一些面积 较大区域则需要专用喷涂工具
一:光学冷加工工序
9:将2个R值相反的镜片用胶将其联合,此步 骤可在步骤8之前或之后作,多数情况下是 正负透镜胶合。一般采用光敏胶胶合。
二.光学冷加工的一些常识
光学加 此步骤一般由材料供应商完成,对于普通镜 片或圆形窗口,光学加工厂收到的一般是圆 柱料,圆柱直径比完工件直径大1~2mm, 光学工厂再对此圆柱进行切割,切成一个个 毛坯片,中心厚度也要比完工件大一些,具 体大多少视光洁度要求而定,此步骤造成的 材料浪费主要由刀口宽度决定
二.光学冷加工的一些常识
2)工装及成盘 第一次生产某种球面镜,除了光学样板,还 需要生产一整套工装,即在铣磨,精磨,抛 光每一步都需要的砣子,精度也越来越高, 在抛光过程用的工装精度最高,工件镶在这 样的工装上,不同R及外径的工件决定最终 成盘数量
光学产品超精密加工工艺
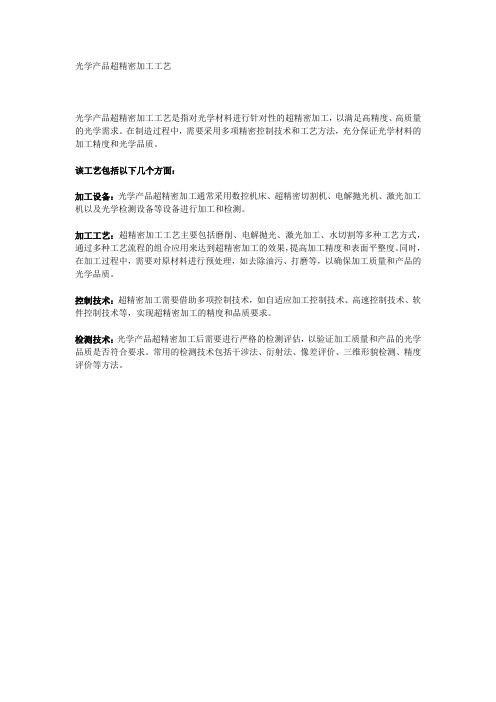
光学产品超精密加工工艺
光学产品超精密加工工艺是指对光学材料进行针对性的超精密加工,以满足高精度、高质量的光学需求。
在制造过程中,需要采用多项精密控制技术和工艺方法,充分保证光学材料的加工精度和光学品质。
该工艺包括以下几个方面:
加工设备:光学产品超精密加工通常采用数控机床、超精密切割机、电解抛光机、激光加工机以及光学检测设备等设备进行加工和检测。
加工工艺:超精密加工工艺主要包括磨削、电解抛光、激光加工、水切割等多种工艺方式,通过多种工艺流程的组合应用来达到超精密加工的效果,提高加工精度和表面平整度。
同时,在加工过程中,需要对原材料进行预处理,如去除油污、打磨等,以确保加工质量和产品的光学品质。
控制技术:超精密加工需要借助多项控制技术,如自适应加工控制技术、高速控制技术、软件控制技术等,实现超精密加工的精度和品质要求。
检测技术:光学产品超精密加工后需要进行严格的检测评估,以验证加工质量和产品的光学品质是否符合要求。
常用的检测技术包括干涉法、衍射法、像差评价、三维形貌检测、精度评价等方法。
光学零件基本加工工艺规程设计

光学零件基本加工工艺规程设计一、材料选择在设计光学零件基本加工工艺规程之前,首先需要根据光学零件的要求和使用环境选择合适的材料。
一般情况下,光学零件常用的材料包括玻璃、晶体和塑料等。
不同的材料有不同的特性和加工难度,在选择材料时需要考虑光学性能、物理性能和耐久性等因素,并权衡其加工难度和成本等因素。
二、加工流程规划1.光学零件的加工主要分为粗加工和精加工两个阶段。
粗加工阶段主要是通过切削、研磨和抛光等工艺对原材料进行形状和尺寸的加工,以获得近似尺寸和粗糙度要求的加工零件。
精加工阶段主要是通过抛光、研磨和涂膜等工艺对粗加工后的零件进行微调和处理,以获得最终的光学性能和表面质量。
2.在粗加工阶段,常用的加工工艺包括切削、磨削、抛光和研磨等。
切削是指通过刀具对材料进行切削来获得所需形状和尺寸的工艺,常用的切削工具有铣刀、车刀和钻头等。
磨削是指通过磨轮对材料进行磨削来获得粗加工目标,常用的磨削工具有砂轮、磨粒和金刚石等。
抛光和研磨则是通过对材料表面进行机械处理来获得较好的表面质量,常用的工具有抛光布、研磨液和涂膜等。
3.在精加工阶段,主要采用的工艺有抛光、研磨和涂膜等。
抛光是通过抛光布和涂膏等工具对零件表面进行抛光处理,以提高表面质量和光学性能。
研磨是通过研磨片和涂膏等工具对零件进行平面研磨和修整,以达到更高的尺寸精度和表面光洁度。
涂膜是在零件表面涂覆一层光学膜以改善其光学性能和耐磨性,常用的涂膜有反射膜、透明膜和滤光膜等。
三、加工参数确定在光学零件基本加工工艺规程设计中,还需要确定加工参数,以保证加工精度和表面质量。
加工参数包括切削力、磨削速度、抛光布压力和涂膜厚度等。
这些参数的选择和调整需要根据加工材料的硬度、光学要求和设备性能等因素进行综合考虑。
一般情况下,需要通过试验和实践来不断调整和优化加工参数,以获得最佳的加工效果。
综上所述,光学零件基本加工工艺规程设计是基于光学要求和加工难度等因素来选择合适的材料、规划加工流程和确定加工参数等,以获得满足光学性能和表面质量的最终加工零件。
光学研磨加工工艺流程
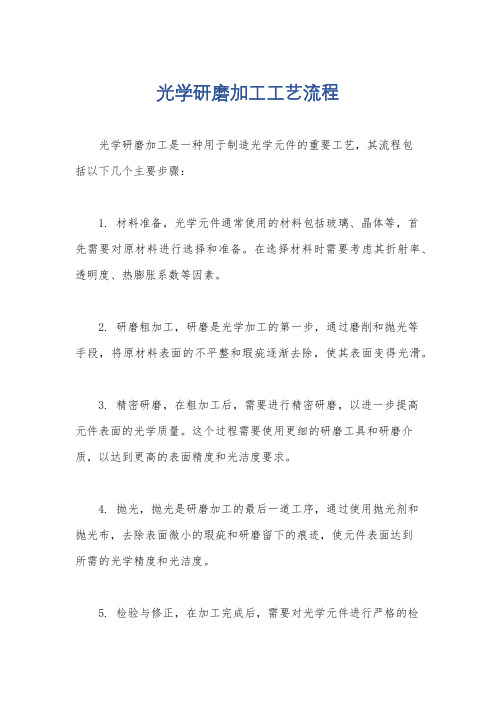
光学研磨加工工艺流程
光学研磨加工是一种用于制造光学元件的重要工艺,其流程包
括以下几个主要步骤:
1. 材料准备,光学元件通常使用的材料包括玻璃、晶体等,首
先需要对原材料进行选择和准备。
在选择材料时需要考虑其折射率、透明度、热膨胀系数等因素。
2. 研磨粗加工,研磨是光学加工的第一步,通过磨削和抛光等
手段,将原材料表面的不平整和瑕疵逐渐去除,使其表面变得光滑。
3. 精密研磨,在粗加工后,需要进行精密研磨,以进一步提高
元件表面的光学质量。
这个过程需要使用更细的研磨工具和研磨介质,以达到更高的表面精度和光洁度要求。
4. 抛光,抛光是研磨加工的最后一道工序,通过使用抛光剂和
抛光布,去除表面微小的瑕疵和研磨留下的痕迹,使元件表面达到
所需的光学精度和光洁度。
5. 检验与修正,在加工完成后,需要对光学元件进行严格的检
验,包括表面粗糙度、平整度、曲率等参数的测量,以及光学性能
的测试。
如果发现问题,还需要进行修正和再加工,直至达到要求
的标准。
总的来说,光学研磨加工工艺流程包括材料准备、研磨粗加工、精密研磨、抛光和检验修正等多个环节,每个环节都需要严格控制
和精细操作,以确保最终制造出符合要求的光学元件。
光学元件加工工艺流程
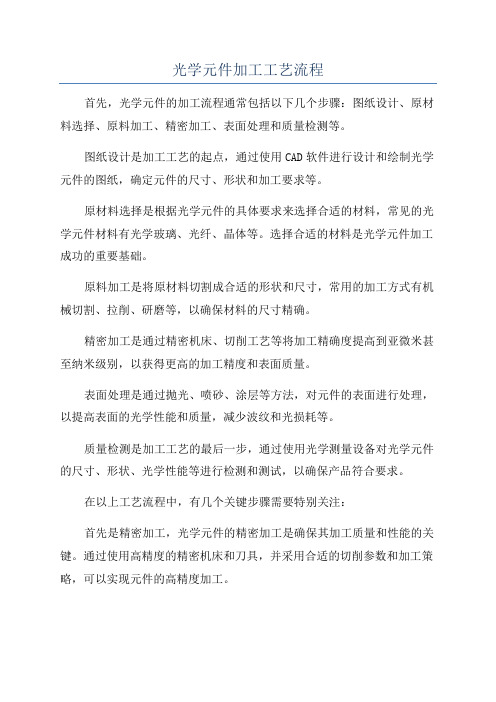
光学元件加工工艺流程首先,光学元件的加工流程通常包括以下几个步骤:图纸设计、原材料选择、原料加工、精密加工、表面处理和质量检测等。
图纸设计是加工工艺的起点,通过使用CAD软件进行设计和绘制光学元件的图纸,确定元件的尺寸、形状和加工要求等。
原材料选择是根据光学元件的具体要求来选择合适的材料,常见的光学元件材料有光学玻璃、光纤、晶体等。
选择合适的材料是光学元件加工成功的重要基础。
原料加工是将原材料切割成合适的形状和尺寸,常用的加工方式有机械切割、拉削、研磨等,以确保材料的尺寸精确。
精密加工是通过精密机床、切削工艺等将加工精确度提高到亚微米甚至纳米级别,以获得更高的加工精度和表面质量。
表面处理是通过抛光、喷砂、涂层等方法,对元件的表面进行处理,以提高表面的光学性能和质量,减少波纹和光损耗等。
质量检测是加工工艺的最后一步,通过使用光学测量设备对光学元件的尺寸、形状、光学性能等进行检测和测试,以确保产品符合要求。
在以上工艺流程中,有几个关键步骤需要特别关注:首先是精密加工,光学元件的精密加工是确保其加工质量和性能的关键。
通过使用高精度的精密机床和刀具,并采用合适的切削参数和加工策略,可以实现元件的高精度加工。
其次是表面处理,光学元件的表面处理是确保其光学性能和表面质量的重要环节。
通过采用不同的表面处理方法,如抛光、喷砂和涂层等,可以消除表面缺陷,提高元件的光学性能和质量。
最后是质量检测,光学元件的质量检测是评估产品质量的重要手段。
通过使用精密的光学测量设备和检测方法,对元件进行尺寸、形状和光学性能等多方面的检测和测试,可以确保产品的质量符合要求。
总结:光学元件加工工艺流程包括图纸设计、原材料选择、原料加工、精密加工、表面处理和质量检测等多个步骤。
其中精密加工、表面处理和质量检测是确保产品质量和性能的关键步骤。
通过合理的加工工艺和精密的加工设备,可以提高元件的加工精度和表面质量,从而满足光学元件在光学系统中的要求。
光学加工工艺流程

光学加工工艺流程下载温馨提示:该文档是我店铺精心编制而成,希望大家下载以后,能够帮助大家解决实际的问题。
文档下载后可定制随意修改,请根据实际需要进行相应的调整和使用,谢谢!并且,本店铺为大家提供各种各样类型的实用资料,如教育随笔、日记赏析、句子摘抄、古诗大全、经典美文、话题作文、工作总结、词语解析、文案摘录、其他资料等等,如想了解不同资料格式和写法,敬请关注!Download tips: This document is carefully compiled by theeditor. I hope that after you download them,they can help yousolve practical problems. The document can be customized andmodified after downloading,please adjust and use it according toactual needs, thank you!In addition, our shop provides you with various types ofpractical materials,such as educational essays, diaryappreciation,sentence excerpts,ancient poems,classic articles,topic composition,work summary,word parsing,copy excerpts,other materials and so on,want to know different data formats andwriting methods,please pay attention!光学加工工艺流程一、准备工作阶段。
在进行光学加工之前,需要做好充分的准备。
光学加工工艺流程

光学加工工艺流程嘿,朋友们!今天咱就来聊聊光学加工工艺流程这档子事儿。
你想想看啊,那一片片亮晶晶的镜片,从最初的原材料到最后变成我们能使用的完美光学器件,这中间得经历多少奇妙的过程呀!首先就是毛坯制作啦。
就好像盖房子得先有块地一样,这毛坯就是光学加工的基础。
得挑选合适的材料,精心打造出一个大致的形状来。
这可不是随随便便就能搞定的事儿,得有经验、有技术才行。
然后呢,就是研磨啦!这就好比是给毛坯做一次精心的打磨,把那些粗糙的地方一点点地磨平,让它逐渐变得光滑细腻。
这可不是轻松的活儿,得一遍又一遍地耐心打磨,就跟雕琢一件艺术品似的。
接着就是抛光啦!哎呀呀,这可真是个神奇的步骤。
经过抛光,那镜片就像是被施了魔法一样,变得光亮照人。
你能想象吗,原本还有些模糊的表面,一下子就变得清晰透明啦!再往后就是镀膜啦!这就像是给镜片穿上一件漂亮的外衣。
这层膜可不简单,它能让镜片有各种各样神奇的功能,比如防反射呀、增加透光率呀等等。
这镀膜的技术那也是相当讲究的,厚了薄了都不行。
最后就是检验啦!这可是把关的重要环节。
得仔细检查每一个镜片,看看有没有瑕疵,有没有达到要求。
要是有一点问题,那可就前功尽弃啦!你说这光学加工工艺流程是不是很有意思?就像一个艺术家在精心创作一幅伟大的作品一样。
每一个步骤都那么重要,都需要精心对待。
想想我们生活中的那些光学器件,从眼镜到相机镜头,从望远镜到显微镜,哪一个不是经过这样一道道复杂的工艺流程才诞生的呀!它们让我们能看清这个美丽的世界,能捕捉到那些珍贵的瞬间。
所以啊,可别小看了这光学加工工艺流程。
它就像是一个神奇的魔法,把普通的材料变成了能给我们带来便利和惊喜的宝贝。
下次当你拿起一副眼镜或者对着相机拍照的时候,可别忘了这背后有着这么多不为人知的故事和努力呀!这就是光学加工工艺流程的魅力所在,它让我们的生活变得更加丰富多彩!。
光学配件加工工艺

光学配件加工工艺
光学配件加工是指对光学元件或光学系统中的配件进行加工和制造的过程。
下面是一般光学配件加工的常见工艺步骤:
1. 零件设计:根据光学要求和需求,对光学配件进行设计,并确定材料、尺寸和形状等参数。
2. 材料准备:选择适合的材料,如光学玻璃、晶体、金属或塑料等,并进行必要的材料预处理,如切割、研磨或抛光等。
3. 加工工艺选择:根据设计要求和材料特性,选择合适的加工工艺,如机械加工、磨削、抛光、薄膜镀膜等。
4. 机械加工:采用数控机床或传统机械设备进行加工,包括铣削、车削、钻孔、切割等步骤,以获得所需的形状和尺寸。
5. 精密磨削:使用磨床或磨削机进行精密磨削,以提高光学配件的表面质量和精度。
6. 抛光和润饰:通过手工或自动化的抛光过程,对光学配件进行表面处理,以获得更高的光学品质和光滑度。
7. 清洗和检验:对加工后的光学配件进行清洗和检验,确保其符合设计要求和质量标准。
8. 镀膜和涂层:根据需要,在光学配件表面进行薄膜镀膜或其他涂层处理,以改善光学性能或增加耐磨性等特性。
9. 组装和调试:将光学配件组装到光学系统中,并进行必要的调试和测试,以确保其正常工作和性能稳定。
以上是一般光学配件加工的基本步骤,具体的加工工艺和步骤可
能会因不同的光学元件和需求而有所变化。
光学配件加工需要严格的质量控制和专业的技术人员进行操作,以保证最终产品的光学性能和质量。
光学元件加工工艺流程

光学元件加工工艺流程光学元件加工工艺流程是指将光学材料加工成符合特定要求的光学元件的过程。
光学元件广泛应用于光学系统中,包括光学仪器、光学通信、激光加工等领域。
下面将介绍一般的光学元件加工工艺流程。
一、原材料准备需要准备光学材料,如玻璃、晶体等。
这些材料要求具有良好的光学性能和机械性能,以保证最终加工出的光学元件具有高质量和稳定性。
在原材料准备过程中,需要检查材料的纯度、均匀性和无瑕疵情况。
二、材料切割在光学元件加工过程中,首先需要将原材料切割成合适的尺寸和形状。
切割过程中需要使用切割工具和切割液,以避免材料的损伤和变形。
切割后的材料需要进行清洗和检查,以确保表面的平整度和无污染。
三、粗磨和细磨切割后的光学元件表面粗糙,需要进行粗磨和细磨来改善表面质量。
粗磨是利用磨料对材料表面进行磨削,以去除表面的瑕疵和不均匀性。
细磨是在粗磨的基础上进一步提高表面的平整度和光洁度。
粗磨和细磨需要使用不同颗粒大小和不同硬度的磨料,并配合合适的磨剂和磨具。
四、抛光抛光是在细磨的基础上进一步改善光学元件表面质量的工艺。
抛光是利用特殊的抛光液和抛光机械设备对元件表面进行处理,以去除微小的瑕疵和提高表面的平整度和光洁度。
抛光过程需要控制抛光液的浓度、温度和时间,以避免对元件的损伤和变形。
五、镀膜在光学元件加工过程中,为了改善元件的光学性能和耐磨性,常常需要进行镀膜处理。
镀膜是将一层或多层薄膜沉积在元件表面的过程。
常见的镀膜方法有真空蒸镀、离子镀、溅射镀等。
镀膜可以提高元件的反射率、透过率和耐腐蚀性。
六、检测和质量控制在光学元件加工过程中,需要对加工后的元件进行严格的检测和质量控制,以确保元件的性能和质量符合要求。
常用的检测方法有光学显微镜、干涉仪、激光干涉仪等。
检测内容包括表面形貌、平整度、光学性能等。
七、组装和封装在光学元件加工完成后,需要根据具体的应用需求进行组装和封装。
组装是将多个光学元件按照一定的位置和方向组合在一起,以构成光学系统。
光学元件加工工艺流程

光学元件加工工艺流程光学元件是指用于控制和调节光的传输和传播的装置,广泛应用于光学仪器、激光器、通信设备等领域。
光学元件的加工工艺流程是指将光学元件的原材料经过一系列的加工工艺,最终制成符合要求的光学元件的过程。
下面将详细介绍光学元件加工工艺流程的主要步骤。
1. 材料选择光学元件的材料选择非常重要,通常根据光学元件的具体用途和要求来选择合适的材料。
常用的光学元件材料包括玻璃、晶体、塑料等。
不同的材料具有不同的光学性质和机械性能,因此需要根据具体要求进行选择。
2. 切割切割是将原材料切割成适当尺寸的工艺步骤。
切割通常使用钻孔、锯片、激光等工具进行。
在切割过程中,需要注意控制切割尺寸的精度和表面质量。
3. 粗磨粗磨是将切割好的材料进行粗加工的过程。
粗磨通常使用砂轮或研磨机进行,目的是将材料的表面进行初步修整,去除切割时产生的毛刺和不平整。
4. 细磨细磨是在粗磨的基础上进一步提高材料表面的光洁度和平整度的工艺步骤。
细磨通常使用细砂轮、研磨液等工具进行,通过不断的磨削和抛光,使材料的表面达到所需的光学要求。
5. 抛光抛光是在细磨的基础上进一步提高材料表面质量的工艺步骤。
抛光通常使用抛光机或抛光液进行,通过不断的摩擦和磨削,使材料的表面变得光滑、亮度提高。
6. 镀膜镀膜是为了改善光学元件的光学性能而进行的工艺步骤。
镀膜通常使用真空蒸发、溅射等技术进行,通过在光学元件表面镀上一层特定的薄膜,来实现对光的反射、透射等特性的调控。
7. 检测与测试在光学元件加工的每个环节中,都需要进行相应的检测和测试,以确保加工质量符合要求。
常用的检测手段包括平面度检测、表面粗糙度检测、光学性能测试等。
只有通过严格的检测和测试,才能保证光学元件的质量和性能。
8. 清洗与包装在光学元件加工完成后,需要进行清洗和包装,以确保光学元件的表面干净无尘,避免污染和损坏。
清洗通常使用特殊的清洗液和设备进行,包装则需要采用防震、防潮等适当的包装材料,以保护光学元件的完整性和安全性。
光学机械加工工艺流程

光学机械加工工艺流程一、引言光学机械加工是指利用机械设备对光学元件进行加工和加工过程中的检测和测量的一系列工艺流程。
光学机械加工工艺流程的正确操作对于保证光学元件的质量和性能至关重要。
本文将介绍光学机械加工的一般工艺流程,以及每个环节的主要步骤和注意事项。
二、加工前的准备1. 材料准备:选择合适的光学材料,如玻璃、晶体等,并对材料进行检查,确保没有明显的缺陷和污染。
2. 设备准备:确保加工设备的正常运行,如研磨机、抛光机、切割机等,并根据加工要求进行调试和校准。
3. 工艺准备:根据光学元件的形状和要求,确定适当的加工工艺,如研磨、抛光、切割等,并准备相应的磨料、液体和工具。
三、研磨加工1. 研磨前的表面处理:清洗光学元件表面,去除污垢和油脂,以确保研磨效果。
2. 研磨操作:将光学元件放置在研磨机上,选用适当的研磨盘和磨料进行研磨。
按照预定的研磨时间和力度进行操作,注意保持合适的温度和湿度。
3. 研磨后的检查:对研磨后的光学元件进行检查,观察表面是否平整、光滑,并进行粗略测量,以确保研磨工艺的准确性。
四、抛光加工1. 抛光前的清洗:清洗研磨后的光学元件,去除残留的研磨剂和杂质,以确保抛光效果。
2. 抛光操作:将光学元件放置在抛光机上,选用适当的抛光盘和抛光液进行抛光。
根据预定的抛光时间和力度进行操作,注意保持合适的温度和湿度,并定期更换抛光盘和抛光液。
3. 抛光后的检查:对抛光后的光学元件进行检查,观察表面是否光洁、均匀,并进行精细测量,以确保抛光工艺的准确性。
五、切割加工1. 切割前的定位:根据加工要求,在光学元件上进行定位,标记切割线或切割点,以确保切割的准确性。
2. 切割操作:使用适当的切割工具,如切割机、钻孔机等,进行切割。
根据预定的切割线或切割点进行操作,注意控制切割速度和压力,避免产生裂纹或碎裂。
3. 切割后的检查:对切割后的光学元件进行检查,观察切割面是否平整、无裂纹,并进行精确测量,以确保切割工艺的准确性。
光学冷加工工艺
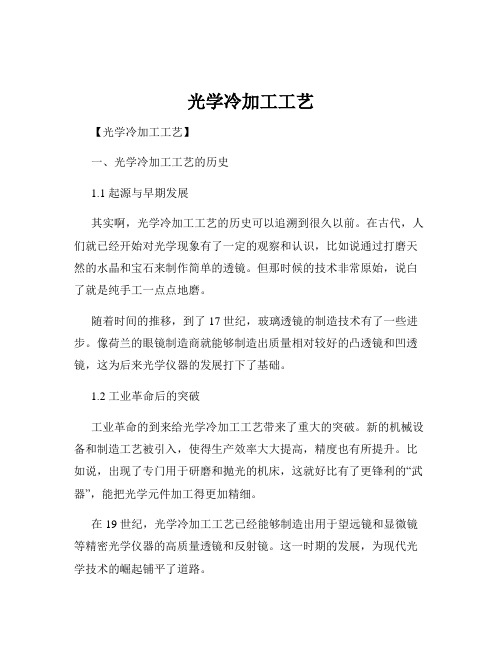
光学冷加工工艺【光学冷加工工艺】一、光学冷加工工艺的历史1.1 起源与早期发展其实啊,光学冷加工工艺的历史可以追溯到很久以前。
在古代,人们就已经开始对光学现象有了一定的观察和认识,比如说通过打磨天然的水晶和宝石来制作简单的透镜。
但那时候的技术非常原始,说白了就是纯手工一点点地磨。
随着时间的推移,到了 17 世纪,玻璃透镜的制造技术有了一些进步。
像荷兰的眼镜制造商就能够制造出质量相对较好的凸透镜和凹透镜,这为后来光学仪器的发展打下了基础。
1.2 工业革命后的突破工业革命的到来给光学冷加工工艺带来了重大的突破。
新的机械设备和制造工艺被引入,使得生产效率大大提高,精度也有所提升。
比如说,出现了专门用于研磨和抛光的机床,这就好比有了更锋利的“武器”,能把光学元件加工得更加精细。
在 19 世纪,光学冷加工工艺已经能够制造出用于望远镜和显微镜等精密光学仪器的高质量透镜和反射镜。
这一时期的发展,为现代光学技术的崛起铺平了道路。
二、光学冷加工工艺的制作过程2.1 毛坯制备首先得有个材料的毛坯,这就像盖房子得先有块地一样。
通常会选用光学玻璃或者晶体材料,然后通过切割、铸型等方法,得到一个初步具有形状的毛坯。
2.2 粗磨接下来就是粗磨啦,这一步就是把毛坯表面的粗糙部分去掉,让它大致接近最终的形状。
就好比雕刻一个石像,先把大体的轮廓给弄出来。
2.3 精磨粗磨完了,就得精磨。
精磨会让表面更加光滑、形状更加精确。
这个过程就需要更精细的磨料和更精密的设备。
2.4 抛光抛光是关键的一步,就像给脸蛋化妆一样,让表面变得光亮如镜。
通过使用特殊的抛光剂和工具,把微小的瑕疵和不平整的地方都处理掉,使光学元件具有良好的光学性能。
三、光学冷加工工艺的特点3.1 高精度要求光学冷加工工艺的一个显著特点就是对精度的要求极高。
说白了,一点点微小的误差都可能导致光学性能的大幅下降。
比如说,一个透镜表面的平整度偏差一点点,成像可能就会变得模糊不清,就像我们拍照时手抖了一样。
光学仪器加工工艺

光学仪器加工工艺一、光学材料选择光学材料是光学仪器制造的基础,其选择直接影响到仪器的性能和使用寿命。
在选择光学材料时,需要考虑材料的折射率、硬度、韧性、耐热性、抗磨损性、抗老化性等物理和化学性能。
常用的光学材料包括玻璃、石英、塑料等。
二、光学设计光学设计是根据仪器的功能和性能要求,确定光学系统的结构、光学元件的形状和尺寸,以及镜片和透镜的组合方式。
设计过程中需要考虑光线的传播路径、光线的聚焦和扩散、光学元件的精度和稳定性等因素。
三、光学元件加工光学元件加工是将光学材料加工成所需形状和尺寸的镜片或透镜的过程。
加工过程中需要保证镜片或透镜的精度和表面质量,同时还需要考虑材料的硬度和韧性等因素。
常用的加工方法包括机械加工、化学加工和激光加工等。
四、光学装配与调整光学装配是将加工好的光学元件按照设计要求组装在一起的过程。
在装配过程中,需要保证各个元件之间的相对位置和精度,同时还需要对元件进行调试和校准。
装配完成后需要进行精度检测和调整,以确保仪器的性能和使用寿命。
五、镀膜工艺镀膜工艺是在光学元件表面涂覆一层或多层薄膜,以提高元件的反射率、透射率、抗磨损性等性能的过程。
常用的镀膜材料包括金属薄膜、介质薄膜等。
镀膜工艺需要保证膜层的均匀性和稳定性,同时还需要考虑镀膜材料的物理和化学性能。
六、检验与测试检验与测试是对制造完成的仪器进行性能检测和评估的过程。
检验与测试的内容包括光学系统的精度检测、光学元件的表面质量检测、仪器的功能测试等。
通过检验与测试可以确保仪器的性能和使用寿命符合设计要求。
七、清洁与保养清洁与保养是保持仪器性能和使用寿命的重要措施。
清洁主要是去除仪器表面的污垢和尘埃,保养则包括定期对仪器进行检查和维护,以及更换磨损严重的元件等。
八、包装与运输包装与运输是确保仪器在运输过程中不受损坏的重要措施。
包装材料需要具有良好的抗震性和防潮性,同时还需要根据仪器的尺寸和重量选择合适的包装方式。
在运输过程中需要采取防震措施,避免仪器受到冲击和振动。
光学零件基本加工工艺规程设计

光学零件基本加工工艺规程设计1. 引言光学零件是光学系统中不可或缺的组成部分,其加工工艺的好坏直接影响到光学器件的性能和质量。
为了确保光学零件的精度和稳定性,需要制定一套科学合理的加工工艺规程。
本文将对光学零件基本加工工艺规程进行设计,以保证光学零件的制造质量。
2. 加工工艺流程设计光学零件的加工工艺流程主要包括以下几个步骤: - 设计和确定加工方案 - 材料准备 - 加工前检验 - 粗加工 - 热处理(如有需要) - 精加工 - 检验和测量 - 清洗和包装3. 加工方案设计在加工零件前,需要制定合适的加工方案,包括选择合适的加工设备、工艺参数和加工顺序等。
根据光学零件的材料和几何形状,可以确定具体的加工方案。
4. 材料准备材料准备是加工过程中的重要环节,主要包括材料的选用和预处理。
光学零件要求使用优质的光学材料,如光学玻璃、单晶硅等。
在使用前,需要进行清洗和去除表面污染物的处理。
5. 加工前检验在进行加工前,需对材料进行检验,确保其符合零件要求。
检验内容包括材料的化学成分、力学性能和几何尺寸等。
6. 粗加工粗加工是将初始材料加工成近似形状的过程,其目的是为了减少后续加工量,提高加工效率。
粗加工方法可以采用切削、研磨等方式,根据不同材料和零件形状选择合适的工艺。
7. 热处理某些光学零件需要进行热处理,以改善其性能和结构组织。
热处理方式包括退火、淬火和回火等,根据不同零件的要求选择合适的热处理方式。
8. 精加工精加工是将经过粗加工的零件加工至最终形状和精度的过程。
精加工方法包括抛光、研磨、切削等,根据零件的要求和加工难度选择合适的工艺方法。
9. 检验和测量加工完成后,需要对光学零件进行检验和测量,以保证其质量和精度。
常用的检验方法包括光学透射率测量、平面度测量和表面粗糙度测量等。
根据零件的要求和检验标准,选择合适的检验方法和检测设备。
10. 清洗和包装最后,将加工完成的光学零件进行清洗和包装工作。
光学加工工艺简介

光学加⼯⼯艺简介光学零件的加⼯,分为热加⼯、冷加⼯和特种加⼯,热加⼯⽬前多采⽤于光学零件的坯料备制;冷加⼯是以散粒磨料或固着磨料进⾏锯切、粗磨、精磨、抛光和定⼼磨边。
特种加⼯仅改变抛光表⾯的性能,⽽不改变光学零件的形状和尺⼨,它包括镀膜、刻度、照相和胶合等。
冷加⼯各⼯序的主要任务是:粗磨(切削)⼯序:是使零件具有基本准确的⼏何形状和尺⼨。
精磨(粗磨)⼯序:是使零件加⼯到规定的尺⼨和要求,作好抛光准备。
抛光(精磨)⼯序:是使零件表⾯光亮并达到要求的光学精度。
定⼼⼯序:是相对于光轴加⼯透镜的外圆。
胶合⼯序:是将不同的光学零件胶合在⼀起,使其达到光轴重合或按⼀定⽅向转折。
球⾯光学零件现⾏加⼯技术三⼤基本⼯序为:1、范成法原理的铣磨(切削)2、压⼒转移原理的⾼速粗磨3、压⼒转移原理的⾼速抛光。
范成法原理的铣磨(切削),虽然加⼯效率较⾼,但其影响误差的因素较多,达到较⾼精度和较粗糙度较困难。
压⼒转移原理的准球⼼⾼速粗磨和⾼速抛光,零件受⼒较均匀,加⼯效率也较⾼,但必须预先准确修整磨(模)具的⾯形,才能保证零件的⾯形精度。
准确修整⾯形精度需要操作者的经验和技巧,⽽且需反复修整。
⼀、传统研磨与⾼速研磨特点1.传统研磨传统研磨也叫古典研磨,它是⼀种历史悠久的加⼯⽅法其主要特点是:(1)采⽤普通研磨机床或⼿⼯操作;(2)要求⼈员技术⽔平较⾼;(3)研磨材料多采⽤散砂(研磨砂)抛光沥青(4)抛光剂是⽤氧化铈或氧化铁;(5)压⼒⽤加荷重⽅法实现虽然这种⽅法效率低, 但加⼯精度较⾼所以,⽬前仍被采⽤。
2.⾼速研磨抛光⼀般是指准球⼼法(或称弧线摆动法)。
其主要特点是:(1)采⽤⾼速、⾼压和更有效的利⽤抛光模,⼤⼤提⾼了抛光效率(2)压⼒头围绕球⼼做弧线摆动,⼯作压⼒始终指向球⼼,也是靠球模成型的。
3.范成法准球⼼法对机床的精度要求较低,加⼯⽅法和传统法相近,易于实现,⽤的较⼴;范成法对机床精度及调整要求较⾼,⽬前很少采⽤。
光学加工工艺

光学加工工艺我一直觉得光学加工工艺就像是一场神奇的魔法之旅。
你看啊,咱们身边到处都是光学的影子,从眼镜到显微镜,从望远镜到手机摄像头,每一个光学元件的背后都有着光学加工工艺的精心雕琢。
我有个朋友叫小李,他就在一家光学加工厂工作。
有一次我去他那儿参观,简直就像进入了一个微观的奇妙世界。
一进门,我就看到各种各样的镜片毛坯,它们看起来普普通通的,就像还没被发掘的璞玉。
小李笑着跟我说:“你可别小看这些啊,这就是光学奇迹开始的地方。
”光学加工的第一步往往是切割。
那些大块的光学材料,就像一块大蛋糕一样,得按照精确的尺寸切割开来。
这个过程可不像咱们切蛋糕那么随意,差之毫厘就可能谬以千里。
工人们就像技艺高超的厨师,操作着精密的切割设备,小心翼翼地把材料切成合适的小块。
我当时就忍不住问小李:“这得需要多高的精度啊?”小李回答说:“精度那可是得用微米来计算的,稍微偏差一点,后面做出来的光学元件可能就成废品了。
”接着就是研磨了。
这研磨的过程就像是一场缓慢而细致的舞蹈。
研磨机就像舞者的舞伴,和镜片毛坯亲密接触。
工人们把镜片固定在研磨机上,然后撒上研磨粉。
这研磨粉就像是魔法的粉末,在研磨机的旋转下,一点一点地把镜片打磨成需要的形状。
我看着那些在研磨机上旋转的镜片,不禁感叹:“这得花多少时间和耐心啊!”小李告诉我:“可不是嘛,有时候一个镜片得研磨好几个小时甚至好几天呢,就像养育一个孩子,得慢慢雕琢。
”在研磨之后就是抛光了。
抛光这个环节可不得了,它能让镜片变得像镜子一样光滑。
抛光的工具就像一把神奇的刷子,轻轻地在镜片表面拂过,把那些微小的瑕疵都给去除掉。
我好奇地问小李:“这抛光是怎么做到让镜片这么光滑的呢?”小李解释说:“这抛光工具上有特殊的材料,再加上合适的压力和速度,就像给镜片做了一场温柔的按摩,把它的表面变得无比光滑。
”还有镀膜这一环节呢。
镀膜就像是给镜片穿上一层华丽的外衣。
通过镀膜,可以增加镜片的透光率、减少反射等。
- 1、下载文档前请自行甄别文档内容的完整性,平台不提供额外的编辑、内容补充、找答案等附加服务。
- 2、"仅部分预览"的文档,不可在线预览部分如存在完整性等问题,可反馈申请退款(可完整预览的文档不适用该条件!)。
- 3、如文档侵犯您的权益,请联系客服反馈,我们会尽快为您处理(人工客服工作时间:9:00-18:30)。
2.计算机数控单点金刚石车削技术
计算机数控单点金刚石车削技术,是由美国国防科研机构于60年代率先开发、80年代得以推广应用的非球面光学零件加工技术。它是在超精密数控车床上,采用天然单晶金刚石刀具,在对机床和加工环境进行精确控制条件下,直接利用金刚石刀具单点车削加工出符合光学质量要求的非球面光学零件。该技术主要用于加工中小尺寸、中等批量的红外晶体和金属材料的光学零件,其特点是生产效率高、加工精度高、重复性好、适合批量生产、加工成本比传统的加工技术明显降低。采用该项金刚石车削技术加工出来的直径120mm以下的光学零件,面形精度达l/2~1l,表面粗糙度的均方根值为0.02~0.06mm。
国外光学加工技术的发展现状
1.引言
如今我们不难发现,军用武器系统中几乎都装备有各种各样的光电传感器件,而在这些光电传感器件中,或多或少都采用了各种样式的光学零件。从美国陆军所作的一项调查报告的材料中我们知道,1980~1990年美国军用激光和红外热成像产品所需要的各种光学零件就有114.77万块,其中球面光学零件为63.59万块,非球面光学零件为23.46万块,平面光学零件为18.1万块,多面体扫瞄镜为9.62万块。拿M1坦克为例,其大约使用了90块透镜、30块棱镜以及各种反射镜、窗口和激光元件。又如一具小小的AN/AVS-6飞行员夜视眼镜就采用了9块非球面光学零件和2块球面光学零件。
(1)莫尔M-18非球面加工机
莫尔M-18非球面加工机是一种3轴计算机数控超精密加工系统,可以使用单点金刚石刀具车削,也可以使用磨轮磨削,既能加工各种高精度平面、球面和非球面光学零件,又能加工模具表面和其它表面。金刚石车削和磨轮磨削相结合,扩大了机床的加工能力。例如加工精密模具,在一台这样的金刚石车床就能将其加工完成。首先使用磨轮在模具基体上加工出公差一致的面形,然后镀制无电镍,最后使用单点金刚石刀具,车削无电镍表面,完成模具的精加工。该加工机床采用了Allen-Bradley 7320型、8200型或通用电器公司2000型计算机数控系统,车床的位置控制采用了Newlett-Packard 5501A型激光传感器系统。莫尔M-18机床的主要技术性能指标如下:
X轴行程410mm;Z轴行程230mm;空气轴承主轴中心到工作台面的距离为292mm ,到旋转工作台面的距离为178mm;X轴和Z轴在全部行程上的直线性为0.5mm;X轴和Z轴在全部行程上的垂直度为1µrad;X轴Z轴在全部行程上的偏向角为0.5µrad s;X轴Z轴全部行程上的定位精度1.5mm;X轴和Z轴每25.4mm行程的定位精度为0.5mm;B轴旋转360°时的角度偏差为±3µrad s;X轴和Z轴的读数精度为5mm;B轴的读数精度为1.3µrad s;主轴的轴向误差为0.05mm ,径向误差为0.2mrad;机床的体积(高´长´宽)为1778´2032´1800mm。
计算机数控单点金刚石车削技术除了可以用来直接加工球面、非球面光学零件外,还可以用来加工各种光学零件的成型模具和光学零件机体,例如加工玻璃模压成型模具、复制模具、光学塑料注射成型模具和加工复制环氧树脂光学零件用的机体等。该技术与离子束抛光技术相结合,可以加工高精度非球面光学零件;与镀硬碳膜工艺和环氧树脂复制技术相结合,可生产较为便宜的精密非球面反射镜和透镜。假若在金刚石车床上增加磨削附件或采用陶瓷刀具、安装精密夹具和采用在-100°C低温进行金刚石切削等措施,此项技术的应用范围将可进一步扩大。目前,美国亚里桑那大学光学中心已经使用该技术取代了传统的手工加工工艺,但加工玻璃光学零件时,还不能直接磨削成符合质量要求的光学镜面,仍然需要进行柔性抛光。
目前批量生产的模压成型非球面光学零件的直径为2~50mm,直径公差为±0.01mm;厚度为0.4~25mm,厚度公差为±0.01mm;曲率半径可达5mm;面形精度为1.5λ,表面粗糙度符合美国军标为80-50;折射率可控制到±5×10-4mm,折射均匀性可以控制到< 5×10-6mm;双折射小于0.01λ/cm。
(2)普奈莫MSG-325型金刚石车床
普奈莫MSG-325型金刚石车床是计算机数控型双轴金刚石车床。机床采用一个重6t的花岗岩底座,花岗岩底座装在压缩空气垫上用于隔离振动,使振动减小到2Hz。X和Z溜板都安装在花岗岩底座上,两个溜板相互垂直安装,在整个行程上的垂直精度在0.76mm以内。X溜板上装有一个可以互换的刀架,Z溜板上装有一个空气轴承主轴。两个溜板的运动的精确位置用一个激光传感器系统测定,精度为0.025mm。
金刚石车床的价格十分昂贵,而且还不断提高。以MSG 325型车床为例,在80年代初每台价为30~40万美元,而到了90年代初每台价已升高到将近100万美元。这个价格对用户来说是一个不小的经济负担,推广普及应用有一定难度。因此,目前各国正在积极研究开发低成本的金刚石车削机床。下面介绍几种目前正在推广应用的金刚石车削机床.
(3) ULG-100A(H)型超精密非球面金刚石车床
该机床是日本东芝机械公司90年代产品,从1992年6月开始,每月生产2台,每台机床售价5000万日元。机床主轴采用高刚性超精密空气静轴承,机床数控装置具有反馈功能。它可加工各种光学零件和非球面透镜模压成型用金属模具。加工精度可达0.01mm。模压成型金属模具利用金刚石刀具和磨轮进行车削和研磨加工,能达到镜面质量。机床的主要技术性能指标如下:
该机床可以加工红外和可见光波段应用的各种球面和非球面透镜、菲涅耳透镜、反射镜、偏轴圆锥截面镜、多面体反射镜以及精密录像镜头等光学零件。在光学零件加工过程中,可采用激光干涉仪对加工件进行面形非接触测量。机床的主要技术性能指标如下:
机床的主轴采用空气轴承,在1000转/min时,在前端测量,其径向和轴向跳动均为0.1mm;驱动马达为1/3HP 100~2400转/min直流伺伏服马达;采用空气轴承的X溜板的名义尺寸为609´762mm,最大行程为304mm ,最大移动速度20cm/min ,水平方向运动误差0.5mm ,垂直方向运动误差1.27mm ,精密丝杠驱动马达1HP 0~2500转/min;Z溜板最大行程为203mm ,其它性能指标均与X溜板的相同;加工工件的直径,正常机床结构的为356mm ,大孔径机床结构的为560mm;加工工件的最大加工深度204mm;工件直径为150mm时,加工工件的面形精度可达l/2。
现在,世界上已掌握这项先进玻璃光学零件制造技术的著名公司和厂家有美国的柯达、康宁公司,日本的大原、保谷、欧林巴斯、松下公司,德国的蔡司公司和荷兰的菲利浦公司等。
玻璃光学零件模压成型技术是一项综合技术,需要设计专用的模压机床,采用高质量的模具和选用合理的工艺参数。成型的方法,玻璃的种类和毛坯,模具材料与模具制作,都是玻璃模压成型中的关键技术。
3.光学玻璃透镜模压成型技术
光学玻璃透镜模压成型技术是一种高精度光学元件加工技术,它是把软化的玻璃放入高精度的模具中,在加温加压和无氧的条件下,一次性直接模压成型出达到使用要求的光学零件。这项技术自80年代中期开发成功至今已有十几年的历史了,现在已成为国际上最先进的光学零件制造技术方法之一,在许多国家已进入生产实用阶段。这项技术的普及推广应用是光学行业在光学玻璃零件加工方面的重大革命。由于此项技术能够直接压制成型精密的非球面光学零件,从此便开创了光学仪器可以广泛采用非球面玻璃光学零件的时代。因此,也给光电仪器的光学系统设计带来了新的变化和发展,不仅使光学仪器缩小了体积、减少了重量、节省了材料、减少了光学零件镀膜和工件装配的工作量、降低了成本,而且还改善了光学仪器的性能,提高了光学成像的质量。
单点金刚石车削光学零件技术经济效果非常明显,例如加工一个直径100mm的90°离轴抛物面镜,若用传统的研磨抛光工艺方法加工,面形精度最高达到3mm(5l),加工时间需要12个月,每一个抛物面镜的加工成本为5万美元。而采用金刚石车削方法,3个星期就能完成,加工成本只有0.4万美元,面形精度可达0.6µm(1λ)。美国霍尼韦尔公司就用这种技术加工AN/AAD-5红外侦察装置的4面体扫描转镜。转镜的每一面尺寸为88.9´203.2mm,每面的平直度要求为l/2,角精度为90°±4²。用一台车床,15个月就加工出了124个扫描旋转反射镜,质量均达到了设计技术要求。每个旋转反射镜比用传统的加工方法加工节约费用2770美元。霍尼韦尔公司用这种工艺生产了200个4面体旋转镜,共计节约近90万美元。而且还为AN/AAD-5红外侦察装置加工了10万个平面反射镜,节约费用1千多万美元。在1980~1990年这10年间,平面(50´50mm)、多面体(直径90mm)、球面(直径100mm)、非球面(直径125mm)等4种军用光学零件的加工费用,按保守的经济效果计算,美国防部就总计节省约4亿美元。
从70年代开始,以红外热成像和高能激光为代表的军用光学技术迅速发展。军用光学系统不但要求成像质量好,而且要求体积小、重量轻、结构简单。这对光学加工行业是一个严峻考验。为了跟上时代发展的步伐,设计和制作出质地优良的光学成像系统,光学零件加工行业于70年代开展了大规模技术革命和创新活动,研究开发出许多新的光学零件加工方法,如非球面光学零件的加工法。近10多年来,新的光学零件加工技术得到进一步地推广和普及。目前,国外较为普遍采用的光学零件加工技术主要有:计算机数控单点金刚石车削技术、光学玻璃透镜模压成型技术、光学塑料成型技术、计算机数控研磨和抛光技术、环氧树脂复制技术、电铸成型技术……以及传统的研磨抛光技术
目前,采用金刚石车削技术可以加工的材料有:有色金属、锗、塑料、红外光学晶体(碲镉汞、锑化镉、多晶硅、硫化锌、硒化锌、氯化纳、氯化钾、氯化锶、氟化镁、氟化钙、铌酸锂、KDK晶体)无电镍、铍铜、锗基硫族化合物玻璃等。上述材料均可直接达到光学表面质量要求。此技术还可加工玻璃、钛、钨等材料,但是目前还不能直接达到光学表面质量要艺的关键技术,没有金刚石车削机床,就不可能实现金刚石车削加工光学零件新工艺。金刚石车削机床属于高精密机床,机床的主轴精度和溜板运动精度比一般的机床要高出几个数量级,主轴轴承和溜板导轨通常采用空气轴承和油压静力支承结构,机床运动部件的相对位置采用激光位移测量装置测定。在工件加工的整个过程中,采用激光干涉仪测量工件的面形误差。车床上装有反馈装置,可以补偿运动误差。金刚石车床的主要生产厂家是美国的莫尔精密机床公司和普奈莫精密公司。进入90年代后,日本东芝机械公司也开始生产这种车床。莫尔精密机床公司生产销售的主要产品是Moore M-18、-40非球面加工机,Moore T型床身机床,Moore光学平面加工机,Moore M -18油淋非球面加工机等。普奈莫精密公司生产出售的产品主要有MSG-325型、ASG-2500型、Nanoform 600型、Ultra 2000型等金刚石车床。日本东芝机械公司生产出售产品是ULG-100A(H)金刚石车床。