PCB可测试性设计技术要概述
PCB电路板测试检验及规范分析
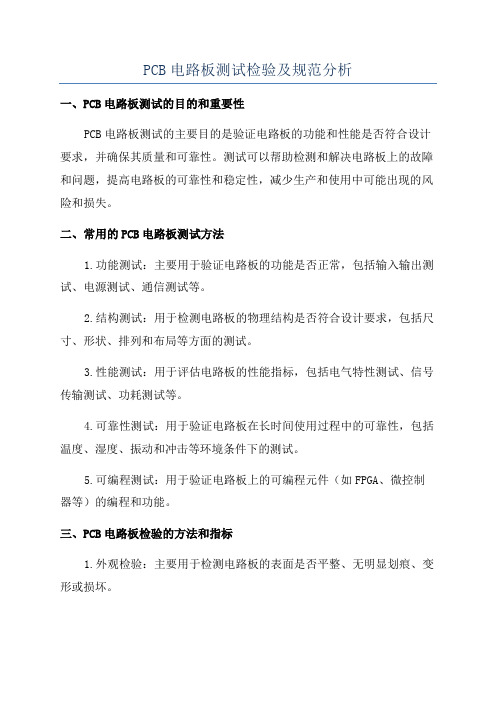
PCB电路板测试检验及规范分析一、PCB电路板测试的目的和重要性PCB电路板测试的主要目的是验证电路板的功能和性能是否符合设计要求,并确保其质量和可靠性。
测试可以帮助检测和解决电路板上的故障和问题,提高电路板的可靠性和稳定性,减少生产和使用中可能出现的风险和损失。
二、常用的PCB电路板测试方法1.功能测试:主要用于验证电路板的功能是否正常,包括输入输出测试、电源测试、通信测试等。
2.结构测试:用于检测电路板的物理结构是否符合设计要求,包括尺寸、形状、排列和布局等方面的测试。
3.性能测试:用于评估电路板的性能指标,包括电气特性测试、信号传输测试、功耗测试等。
4.可靠性测试:用于验证电路板在长时间使用过程中的可靠性,包括温度、湿度、振动和冲击等环境条件下的测试。
5.可编程测试:用于验证电路板上的可编程元件(如FPGA、微控制器等)的编程和功能。
三、PCB电路板检验的方法和指标1.外观检验:主要用于检测电路板的表面是否平整、无明显划痕、变形或损坏。
2.尺寸测量:用于验证电路板的尺寸和孔径是否符合设计要求,并通过光学测量或机械测量手段进行。
3.焊点质量检查:用于验证电路板上的焊点是否牢固、无焊接缺陷和冷焊等问题。
4.电气连通性测试:用于验证电路板上的导线、电阻、电容等电气元件的连通性和正常工作。
五、常用的PCB电路板质量控制标准1.IPC-A600H:电路板的外观和细节质量标准,包括外观缺陷、焊接缺陷和尺寸要求等。
2.IPC-6012D:刚性印制板的质量标准,包括材料、尺寸、硬度、结构、电气性能等方面的要求。
3.IPC-6013C:有机衬底印制电路板的质量标准,包括材料、尺寸、结构、可靠性等方面的要求。
4.IPC-2221B:印制板设计的通用规范,包括电气、机械、材料和可靠性等方面的要求和指导。
5.JEDEC标准:半导体器件和集成电路的质量控制标准,包括ESD测试、温度循环测试等。
总结:PCB电路板的测试、检验及规范分析对于确保电路板的质量和性能至关重要。
PCB技术简介
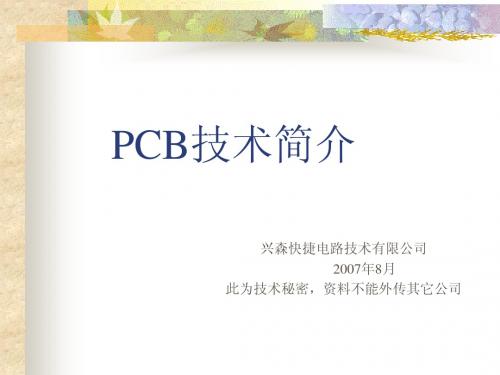
不同表面处理PCB制作工艺流程
PCB 表面处理方式分类
PCB 随着客户使用要求的不同,其相应的表面处理方 式也较多,一般可分为如下几种: 1、热风整平(HAL ) 2、化学镍金(沉金) 3、图镀镍金 4、全板镀硬金(厚金) 5、无铅喷锡 6、OSP 处理(广州快捷) 7、沉锡(广州快捷) 8、沉银
沉银板制作工艺
银厚度标准:0.1-0.3um ; 生产能力: 最小生产尺寸:任意一边大于100MM(最小单 边尺寸不小于50MM); 最大生产尺寸:22"*22"; 板厚度≤6.5MM 注意事项:
包装时用干净白纸或无硫纸隔开,然后真空包装,禁止放置防潮珠, 以避免因此造成银面发黄。(如果客户有特殊包装要求,请按客户要 求执行)
固化—字符→(二钻)→铣板→终检→沉银→电测试→终检→ 包装 如客户要求印刷黑色字符的,请按下述流程生产; 前工序→终检1→沉银→字符→电测试→(二钻、V-CUT)→铣板 →终检2→包装 对于有效交货尺寸有一边小于50MM板,改成PANEL沉银再铣 外形(生产用0.3-0.7mm FR4光板保护板面)
沉锡板制作工艺流程
工程设计---计划投料---开料---磨边---(钻LDI 孔)---内光 成像---内层蚀刻---AOI 检查(目检)---棕化(黑化)---层 压---钻孔(铣毛边)---去毛刺---沉铜---全板镀铜---外光成 像---QC 检查---图形电镀铜、锡---外层蚀刻(SES )---外 AOI 检查---丝印阻焊(塞孔)---阻焊成像---QC 检查---阻焊 固化—---丝印字符(固化)---外形---终检1→沉锡→字符→ 电测试→(二钻、V-CUT)→铣板→终检2→包装 如客户要求印刷黑色字符的,请按下述流程生产; 前工序→终检1→沉锡→字符→电测试→(二钻、V-CUT)→铣 板→终检2→包装 对于有效交货尺寸有一边小于50MM板,改成PANEL沉锡 再铣外 形(生产用0.3-0.7mm FR4光板保护板面)
PCB飞针测试技术概述

PCB飞针测试技术概述我国的PCB研制工作始于1956年,1963-1978年,逐步扩大形成PCB产业。
改革开放后20多年,由于引进国外先进技术和设备,单面板、双面板和多层板均获得快速发展,国内PCB产业由小到大逐步发展起来。
中国由于下游产业的集中及劳动力土地成本相对较低,成为发展势头最为强劲的区域。
2002年,成为第三大PCB产出国。
2003年,PCB产值和进出口额均超过60亿美元,首度超越美国,成为世界第二大PCB产出国,产值的比例也由2000年的8.54%提升到15.30%,提升了近1倍。
2006年中国已经取代日本,成为全球产值最大的PCB 生产基地和技术发展最活跃的国家。
我国PCB产业近年来保持着20%左右的高速增长,远远高于全球PCB行业的增长速度。
飞针测试是目前PCB测试一些主要问题的最新解决办法。
它用探针来取代针床,使用多个由马达驱动的、能够快速移动的电气探针同器件的引脚进行接触并进行电气测量。
这种仪器最初是为裸板而设计的,也需要复杂的软件和程序来支持;现在已经能够有效地进行模拟在线测试了。
飞针测试的出现已经改变了低产量与快速转换(quick-turn)装配产品的测试方法。
以前需要几周时间开发的测试现在几个小时就可以了,大大缩短产品设计周期和投入市场的时间。
1、飞针测试系统的结构特点飞针式测试仪是对传统针床在线测试仪的一种改进,它用探针来代替针床,在X-Y机构上装有可分别高速移动的4个头共8根测试探针,最小测试间隙为0.2mm。
工作时在测单元(UUT,unitundertest)通过皮带或者其它UUT传送系统输送到测试机内,然后固定测试机的探针接触测试焊盘(TESTpad)和通路孔(via),从而测试在测单元(UUT)的单个元件。
测试探针通过多路传输(multiplexing)系统连接到驱动器(信号发生器、电源供应等)和传感器(数字万用表、频率计数器等)来测试UUT上的元件。
当一个元件正在测试的时候,UUT上的其它元件通过探针器在电气上屏蔽以防止读数干扰。
ATE的可测试性设计

总结: 5. 总结:
PCBA的可测试性,涉及PCB布局设计,硬件设计和软件设计。每 一开发环节完成后,设计工程师都应该站在“可测试”的角度 查检设计是否满足测试的要求。 测试点的预留,PCB布局上的实现方式,软件的支持方式,都要 与ATE设计兼容。这对顺利快速地导入可靠的ATE测试,有非常 重要的意义。
ICT在线回路测试 1.2 ICT在线回路测试
ICT主要是针对待测试产品网络节点间的通断路,器件的焊接,器件的参 数性能。 通过数百毫伏电压和数十毫安以内电流对电子器件进行分立隔离测试,从 而精确地测出所装电阻、电感、电容、二极管、三极管、可控硅、场效应 管、集成块等通用和特殊元器件的漏装、错装、参数值偏差、焊点连焊、 线路板开短路等故障,并将故障是哪个元件或开短路位于哪个点准确告诉 用户。 除了传统意义上的测试,ICT还集成了用于处理器测试的Boundary Scan (边界扫描), Tree Chain(树链测试)等,集成了各种总线接口,方便地实现 板级芯片的在线烧录,把烧录整合到测试中,方便下一工站的功能测试。
测试实例2 4.2 测试实例2
2. 数字输入
测试设置:PLC必须被短接片短接至24V。 测试方法:默认时,DSP能识别X1-3电压为高;当单片机板拉低 X1-24是,DSP能识别到X1-3被置低。 可测试性设计:硬件要留有X1-24的测试点; 软件要能方便识别X1-3端子状态。
测试实例3 4.3 测试实例3
1.5 各种检测手段的比较
AOI检测侧重恰当的位置是否安装有恰当的器件。 不足:从外观的角度进行检测,不能检测错料,虚焊,器件极性反向,器件失 不足: 效等。 ICT静态检测电路的开短路故障;动态独立测试电子器件的功能,进行“器件级” 的功能测试。 不足: 不足:需要较多的测试点,实际应用中,往往通过降低测试覆盖率的方式来保 证产品信号的完整性和抗干扰能力。另外,能够有效地查找在SMT组装过程中发 生的各种缺陷和故障,但是它不能够评估整个线路板所组成的系统的总体性能。 FT从整板的角度验证待测试产品的“输入”和“输出”性能。 不足: 不足:由于是验证待测试产品的整体性能,测试留有盲区。比如:器件性能降 低,旁路电容未装,并联的数个电容中一个失效,连接器或跳线未安装。 人工目检主要是针对测试盲区,弥补前面测试中的漏洞。 不足:难于保证目检的规范,目检的效果。不能像自动测试一样可靠。 不足:
PCB四密度通用测试技术介绍

四密度通用测试技术介绍1 通用测试技术的起源和发展最早的PCB通用电性测试技术可追溯至七十年代末八十年代初, 由于当时的元器件均采用标准封装(Pitch为100mil), PCB亦只有THT(通孔技术)密度层次, 所以欧美测试机厂商就设计了一款标准网格的测试机, 只要PCB上的元件和布线是按照标准距离排布的,则每个测试点均会落在标准网格点上, 因为当时所有PCB都能通用, 故称为通用测试机。
由于半导体封装技术的发展, 元器件开始有了更小的封装及贴片(SMT)封装, 标准密度通用测试开始不再适用, 于是九十年代中期, 欧美的测试厂商又推出了双倍密度测试机, 并结合用一定的钢针斜率制造夹具以转换PCB测试点与机器网格连接, 随着HDI制程工艺的逐渐成熟, 双倍密度通用测试又不能完全满足测试的需求,于是在二000年左右, 欧洲测试机厂商又推出了四倍密度网格通用测试机。
图一为网格规格:(图一) 网格密度单密度双密度四密度2 通用测试的关键技术2·1开关元件要满足大部份HDI PCB的测试要求, 测试面积必须要足够大, 通常有以下标准尺寸: 9.6×12.8(inch)、16 X12.8(inch)、24×19.2(inch), 在双密度满网格(Full Grid)情况下, 上述三种尺寸测试点数分别是49512、81920、184320, 电子元件的数量高达数十万, 开关元件是保证测试稳定的一个核心元件, 要求其具有耐高压(>300V)、低漏电等性能, 同时电阻值等电气性能要均衡一致,所以这类元件一定要经过严格的筛选与检测, 通常以晶体管或场效应管作为开关元件,基本线路如图二所示:图(二):开关回路晶体三极管的优缺点:优点: 成本低,抗静电击穿能力强, 稳定性高;缺点: 电流驱动,电路比较复杂, 需隔离基流(Ib)影响, 功耗大场效应管的优缺点:优点: 电压驱动, 电路简单, 不受基流(Ib)影响,功耗小缺点: 成本高, 极易发生静电击穿, 需加静电保护措施, 稳定性不高, 所以会增加维修成本。
PCB四密度通用测试技术介绍(doc 6页)

PCB四密度通用测试技术介绍(doc6页)部门: xxx时间: xxx整理范文,仅供参考,可下载自行编辑四密度通用测试技术介绍1 通用测试技术的起源和发展最早的PCB通用电性测试技术可追溯至七十年代末八十年代初, 由于当时的元器件均采用标准封装(Pitch为100mil), PCB亦只有THT(通孔技术)密度层次, 所以欧美测试机厂商就设计了一款标准网格的测试机, 只要PCB上的元件和布线是按照标准距离排布的,则每个测试点均会落在标准网格点上, 因为当时所有PCB都能通用, 故称为通用测试机。
由于半导体封装技术的发展, 元器件开始有了更小的封装及贴片(SMT)封装, 标准密度通用测试开始不再适用, 于是九十年代中期, 欧美的测试厂商又推出了双倍密度测试机, 并结合用一定的钢针斜率制造夹具以转换PCB测试点与机器网格连接, 随着HDI制程工艺的逐渐成熟, 双倍密度通用测试又不能完全满足测试的需求,于是在二000年左右, 欧洲测试机厂商又推出了四倍密度网格通用测试机。
图一为网格规格:(图一) 网格密度单密度双密度四密度2 通用测试的关键技术2·1开关元件要满足大部份HDI PCB的测试要求, 测试面积必须要足够大, 通常有以下标准尺寸: 9.6×12.8(inch)、16 X12.8(inch)、24×19.2(inch), 在双密度满网格(Full Grid)情况下, 上述三种尺寸测试点数分别是49512、81920、184320, 电子元件的数量高达数十万, 开关元件是保证测试稳定的一个核心元件, 要求其具有耐高压(>300V)、低漏电等性能, 同时电阻值等电气性能要均衡一致,所以这类元件一定要经过严格的筛选与检测, 通常以晶体管或场效应管作为开关元件,基本线路如图二所示:图(二):开关回路晶体三极管的优缺点:优点: 成本低,抗静电击穿能力强, 稳定性高;缺点: 电流驱动,电路比较复杂, 需隔离基流(Ib)影响, 功耗大场效应管的优缺点:优点: 电压驱动, 电路简单, 不受基流(Ib)影响,功耗小缺点: 成本高, 极易发生静电击穿, 需加静电保护措施, 稳定性不高, 所以会增加维修成本。
PCB印制电路板设计技术要求
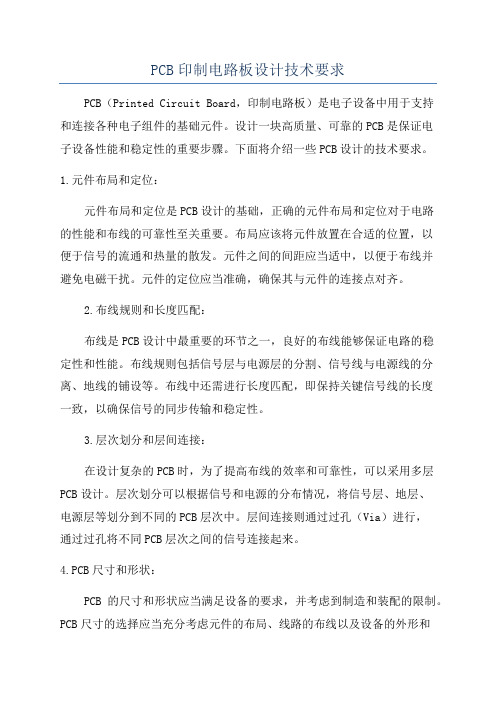
PCB印制电路板设计技术要求PCB(Printed Circuit Board,印制电路板)是电子设备中用于支持和连接各种电子组件的基础元件。
设计一块高质量、可靠的PCB是保证电子设备性能和稳定性的重要步骤。
下面将介绍一些PCB设计的技术要求。
1.元件布局和定位:元件布局和定位是PCB设计的基础,正确的元件布局和定位对于电路的性能和布线的可靠性至关重要。
布局应该将元件放置在合适的位置,以便于信号的流通和热量的散发。
元件之间的间距应当适中,以便于布线并避免电磁干扰。
元件的定位应当准确,确保其与元件的连接点对齐。
2.布线规则和长度匹配:布线是PCB设计中最重要的环节之一,良好的布线能够保证电路的稳定性和性能。
布线规则包括信号层与电源层的分割、信号线与电源线的分离、地线的铺设等。
布线中还需进行长度匹配,即保持关键信号线的长度一致,以确保信号的同步传输和稳定性。
3.层次划分和层间连接:在设计复杂的PCB时,为了提高布线的效率和可靠性,可以采用多层PCB设计。
层次划分可以根据信号和电源的分布情况,将信号层、地层、电源层等划分到不同的PCB层次中。
层间连接则通过过孔(Via)进行,通过过孔将不同PCB层次之间的信号连接起来。
4.PCB尺寸和形状:PCB的尺寸和形状应当满足设备的要求,并考虑到制造和装配的限制。
PCB尺寸的选择应当充分考虑元件的布局、线路的布线以及设备的外形和空间要求。
同时,不规则形状的PCB设计也会增加制造的复杂度和成本,因此应当尽可能选择规整的形状。
5.阻抗控制和信号完整性:在高速数字电路和射频电路设计中,阻抗控制和信号完整性非常重要。
在布线过程中,应当通过调整信号线的宽度和间距,以及信号层和地层的分布,来实现所需要的阻抗匹配。
同时,需要采取一些措施来减少或避免信号的串扰和噪声。
6.焊盘和焊接技术:在PCB设计中,焊盘和焊接技术的合理选择对于元件的连接和电路的稳定性至关重要。
焊盘的形状和尺寸应当根据元件的引脚形态和间距进行设计,以保证焊接的可靠性。
可测性设计
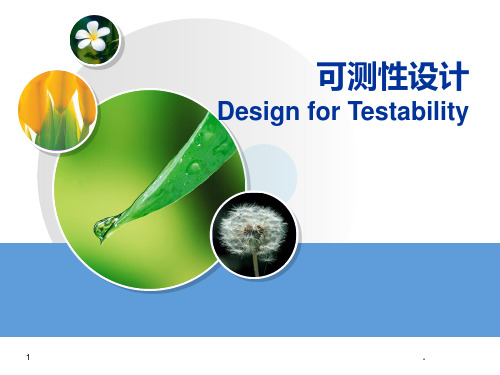
5
.
可测性设计的重要概念
❖ 可测性 Testability = Controllable + Observable ➢ Controllable 可控性
➢ 有支持边界扫描测试功能的软件系统(用于建立边界扫描 测试所需要的各种文件和执行边界扫描测试,比如ASSET InterTech公司的ScanWorks 和法国Temento公司的 DiaTem )
14
.
边界扫描技术
❖ 选择集成电路 ➢ 在设计数字电路板时,应尽可能选择支持IEEE1149.1标
指能够对电路中每个内部节点进行复位和置位的能力 ➢ Observable 可观性
指不论用直接还是间接的方式都能观察到电路中任一个 内部节点状态的能力
6
.
可测性设计的重要概念
❖ 测试矢量与测试码自动生成(ATPG) (Automatic Test Pattern Generation)
➢ 测试矢量是每个时钟周期应用于管脚的用于测试或者操作 的逻辑1和逻辑0的数据
有三类方法:a、Ad hoc 测试
b、基于扫描的方法
c、BIST(Built in Self Test)
➢ Ad hoc 测试:即专项测试,按功能基本要求设计电路, 采取一些比较简单易行的措施,使他们的可测性得到提高
➢ SCAN扫描测试:Full Scan、 Boundary Scan 和 Partial Scan
.
边界扫描技术
❖ 数字电路板使用边界扫描测试方法有三个前提条件:
➢ 电路板上使用的集成电路(IC)支持边界扫描标准 IEEE1149.1(目前ALTERA、XILINX和 LATTICE的主要系 列的大规模可编程逻辑集成电路都支持IEEE1149.1 )
PCB设计规范-生产可测试性要求-模板

1.0目的用于研发中心硬件部PCB制作过程中,对于产品大批量的生产,需要进行在线测试和功能测试,在线测试以及研制生产测试设备的可行性与方便性。
2.0范围本规范适用于公司硬件部所有PCB制作。
3.0职责及权限文件编写标准文件制定单位为研发中心硬件部,修改需要通知相关部门,其他任何单位和个人不得随意更改。
4.0检查事项4.1 基本定义4.1.1在线测试也称内电路测试,也就是在单板上对器件进行测试的一种方法。
通过在线测试仪在被测试单板上的测试点上施加测试探针来测试器件,网络电气特性的一种测试方法。
4.1.2功能测试通过功能测试仪模拟被测试单板实际运行的环境来确认单板所有的功能的一种测试方法。
4.2 基本要求1)、总体方案确定的子系统、模块或单板应有通讯接口。
2)、为子模块和单板所确定的软件和硬件接口应尽量统一和标准。
3)、应尽量采用具有自检和自环等自测试功能的元器件。
4)、在总体方案中为子模块和单板的自测试功能分配或预留一定的命令编码。
5)、为使在线测试可行和方便,单板上的元器件(特别是SMT器件)应设计测试点,或者采用具有边界扫描测试(BST)功能的IC。
4.3在线测试对印制电路板设计的要求(预留)主要采用针床式在线测试仪进行单板的在线测试工作,以下测试点尺寸和密度的要求也是针对针床式在线测试仪提出来的。
4.3.1测试点的设置准则1)、如果一个节点网络中有一个节点是连接到贯穿的器件上,那么不必设置测试点。
2)、如果一个节点网络中连接的所有元件都是边界扫描器件(都是数字器件),那么此网络不必设计测试点。
3)、除了上述两种情况及本标准3.4所描述的情况以外,每个布线网络都应当设置一个测试点,在单板电源和地走线上,每2A 电流至少有一个测试点。
测试点尽量集中在焊接面,且要求均匀分布在单板上。
4)、测试点的密度不超过30个/inch2。
4.3.2测试点的尺寸要求 4.3.2.1测试点的自身尺寸要求a ) 尽量使元器件装在A 面(Top side ),B 面(Bottom side )器件高度应尽量避免超过150mil ;b ) 采用金属化通孔,通孔大小为Φ外≥0.9 mm (36 mil ), Φ内≤0.5 mm (20 mil );c ) 或采用单面测试焊盘,焊盘大小Φ≥0.9 mm (36 mil );d )相邻测试点的中心间距,优先选用d ≥1.8 mm (70 mil ),可以选用d ≥1.25 mm (50 mil );e )测试点是必须可以过锡的(打开防焊层)。
pcb板设计及参数技术要求

PCB使用技巧1、元器件标号自动产生或已有的元器件标号取消重来2、单面板设置:3、自动布线前设定好电源线加粗4、PCB封装更新,只要在原封装上右键弹出窗口内的footprint改为新的封装号5、100mil=2.54mm;1mil=1/1000英寸7、定位孔的放置8、设置图纸参数10、元件旋转:X键:使元件左右对调(水平面); Y键:使元件上下对调(垂直面)11、元件属性:12、生成元件列表(即元器件清单)Reports|Bill of Material13、原理图电气法则测试(Electrical Rules Check)即ERCTools工具|ERC…电气规则检查Multiple net names on net:检测“同一网络命名多个网络名称”的错误Unconnected net labels:“未实际连接的网络标号”的警告性检查Unconnected power objects:“未实际连接的电源图件”的警告性检查Duplicate sheet mnmbets:检测“电路图编号重号”Duplicate component de signator:“元件编号重号”bus label format errors:“总线标号格式错误”Floating input pins:“输入引脚浮接”Suppress warnings:“检测项将忽略所有的警告性检测项,不会显示具有警告性错误的测试报告”Create report file:“执行完测试后程序是否自动将测试结果存在报告文件中”Add error markers:是否会自动在错误位置放置错误符号15、PCB布线的原则如下16、工作层面类型说明布线工程师谈PCB设计作者:本站来源:本站整理发布时间:2006-3-2 11:56:27 发布人:51c51减小字体增大字体PCB布线技术---一个布线工程师谈PCB设计的经验!LBSALE[10]LBSALE今天刚到这里注册,看到不少弟兄的帖子,感觉没有对PCB有一个系统的、合理的设计流程.就随便写点,请高手指教.一般PCB基本设计流程如下:前期准备->PCB结构设计->PCB布局->布线->布线优化和丝印->网络和DRC检查和结构检查->制版.第一:前期准备.这包括准备元件库和原理图.“工欲善其事,必先利其器”,要做出一块好的板子,除了要设计好原理之外,还要画得好.在进行PCB设计之前,首先要准备好原理图SCH的元件库和PCB的元件库.元件库可以用peotel 自带的库,但一般情况下很难找到合适的,最好是自己根据所选器件的标准尺寸资料自己做元件库.原则上先做PCB的元件库,再做SCH的元件库.PCB的元件库要求较高,它直接影响板子的安装;SCH的元件库要求相对比较松,只要注意定义好管脚属性和与PCB元件的对应关系就行.PS:注意标准库中的隐藏管脚.之后就是原理图的设计,做好后就准备开始做PCB设计了.第二:PCB结构设计.这一步根据已经确定的电路板尺寸和各项机械定位,在PCB 设计环境下绘制PCB板面,并按定位要求放置所需的接插件、按键/开关、螺丝孔、装配孔等等.并充分考虑和确定布线区域和非布线区域(如螺丝孔周围多大范围属于非布线区域).第三:PCB布局.布局说白了就是在板子上放器件.这时如果前面讲到的准备工作都做好的话,就可以在原理图上生成网络表(Design-> Create Netlist),之后在PCB图上导入网络表(Design->Load Nets).就看见器件哗啦啦的全堆上去了,各管脚之间还有飞线提示连接.然后就可以对器件布局了.一般布局按如下原则进行:①.按电气性能合理分区,一般分为:数字电路区(即怕干扰、又产生干扰)、模拟电路区(怕干扰)、功率驱动区(干扰源);②.完成同一功能的电路,应尽量靠近放置,并调整各元器件以保证连线最为简洁;同时,调整各功能块间的相对位置使功能块间的连线最简洁;③.对于质量大的元器件应考虑安装位置和安装强度;发热元件应与温度敏感元件分开放置,必要时还应考虑热对流措施;④.I/O驱动器件尽量靠近印刷板的边、靠近引出接插件;⑤.时钟产生器(如:晶振或钟振)要尽量靠近用到该时钟的器件;⑥.在每个集成电路的电源输入脚和地之间,需加一个去耦电容(一般采用高频性能好的独石电容);电路板空间较密时,也可在几个集成电路周围加一个钽电容.⑦.继电器线圈处要加放电二极管(1N4148即可);⑧.布局要求要均衡,疏密有序,不能头重脚轻或一头沉——需要特别注意,在放置元器件时,一定要考虑元器件的实际尺寸大小(所占面积和高度)、元器件之间的相对位置,以保证电路板的电气性能和生产安装的可行性和便利性同时,应该在保证上面原则能够体现的前提下,适当修改器件的摆放,使之整齐美观,如同样的器件要摆放整齐、方向一致,不能摆得“错落有致” .这个步骤关系到板子整体形象和下一步布线的难易程度,所以一点要花大力气去考虑.布局时,对不太肯定的地方可以先作初步布线,充分考虑.第四:布线.布线是整个PCB设计中最重要的工序.这将直接影响着PCB板的性能好坏.在PCB的设计过程中,布线一般有这么三种境界的划分:首先是布通,这时PCB设计时的最基本的要求.如果线路都没布通,搞得到处是飞线,那将是一块不合格的板子,可以说还没入门.其次是电器性能的满足.这是衡量一块印刷电路板是否合格的标准.这是在布通之后,认真调整布线,使其能达到最佳的电器性能.接着是美观.假如你的布线布通了,也没有什么影响电器性能的地方,但是一眼看过去杂乱无章的,加上五彩缤纷、花花绿绿的,那就算你的电器性能怎么好,在别人眼里还是垃圾一块.这样给测试和维修带来极大的不便.布线要整齐划一,不能纵横交错毫无章法.这些都要在保证电器性能和满足其他个别要求的情况下实现,否则就是舍本逐末了.布线时主要按以下原则进行:①.一般情况下,首先应对电源线和地线进行布线,以保证电路板的电气性能.在条件允许的范围内,尽量加宽电源、地线宽度,最好是地线比电源线宽,它们的关系是:地线>电源线>信号线,通常信号线宽为:0.2~0.3mm,最细宽度可达0.05~0.07mm,电源线一般为1.2~2.5mm.对数字电路的PCB可用宽的地导线组成一个回路, 即构成一个地网来使用(模拟电路的地则不能这样使用)②.预先对要求比较严格的线(如高频线)进行布线,输入端与输出端的边线应避免相邻平行,以免产生反射干扰.必要时应加地线隔离,两相邻层的布线要互相垂直,平行容易产生寄生耦合.③.振荡器外壳接地,时钟线要尽量短,且不能引得到处都是.时钟振荡电路下面、特殊高速逻辑电路部分要加大地的面积,而不应该走其它信号线,以使周围电场趋近于零;④.尽可能采用45o的折线布线,不可使用90o折线,以减小高频信号的辐射;(要求高的线还要用双弧线)⑤.任何信号线都不要形成环路,如不可避免,环路应尽量小;信号线的过孔要尽量少;⑥.关键的线尽量短而粗,并在两边加上保护地.⑦.通过扁平电缆传送敏感信号和噪声场带信号时,要用“地线-信号-地线”的方式引出.⑧.关键信号应预留测试点,以方便生产和维修检测用⑨.原理图布线完成后,应对布线进行优化;同时,经初步网络检查和DRC检查无误后,对未布线区域进行地线填充,用大面积铜层作地线用,在印制板上把没被用上的地方都与地相连接作为地线用.或是做成多层板,电源,地线各占用一层.——PCB布线工艺要求①.线一般情况下,信号线宽为0.3mm(12mil),电源线宽为0.77mm(30mil)或1.27mm(50mil);线与线之间和线与焊盘之间的距离大于等于0.33mm(13mil),实际应用中,条件允许时应考虑加大距离;布线密度较高时,可考虑(但不建议)采用IC脚间走两根线,线的宽度为0.254mm(10mil),线间距不小于0.254mm(10mil).特殊情况下,当器件管脚较密,宽度较窄时,可按适当减小线宽和线间距.②.焊盘(PAD)焊盘(PAD)与过渡孔(VIA)的基本要求是:盘的直径比孔的直径要大于0.6mm;例如,通用插脚式电阻、电容和集成电路等,采用盘/孔尺寸1.6mm/0.8mm(63mil/32mil),插座、插针和二极管1N4007等,采用1.8mm/1.0mm(71mil/39mil).实际应用中,应根据实际元件的尺寸来定,有条件时,可适当加大焊盘尺寸;PCB板上设计的元件安装孔径应比元件管脚的实际尺寸大0.2~0.4mm左右.③.过孔(VIA)一般为1.27mm/0.7mm(50mil/28mil);当布线密度较高时,过孔尺寸可适当减小,但不宜过小,可考虑采用1.0mm/0.6mm(40mil/24mil).④.焊盘、线、过孔的间距要求PAD and VIA : ≥ 0.3mm(12mil)PAD and PAD : ≥ 0.3mm(12mil)PAD and TRACK : ≥ 0.3mm(12mil)TRACK and TRACK : ≥ 0.3mm(12mil)密度较高时:PAD and VIA : ≥ 0.254mm(10mil)PAD and PAD : ≥ 0.254mm(10mil)PAD and TRACK : ≥ 0.254mm(10mil)TRACK and TRACK : ≥ 0.254mm(10mil)第五:布线优化和丝印.“没有最好的,只有更好的”!不管你怎么挖空心思的去设计,等你画完之后,再去看一看,还是会觉得很多地方可以修改的.一般设计的经验是:优化布线的时间是初次布线的时间的两倍.感觉没什么地方需要修改之后,就可以铺铜了(Place->polygon Plane).铺铜一般铺地线(注意模拟地和数字地的分离),多层板时还可能需要铺电源.时对于丝印,要注意不能被器件挡住或被过孔和焊盘去掉.同时,设计时正视元件面,底层的字应做镜像处理,以免混淆层面.第六:网络和DRC检查和结构检查.首先,在确定电路原理图设计无误的前提下,将所生成的PCB网络文件与原理图网络文件进行物理连接关系的网络检查(NETCHECK),并根据输出文件结果及时对设计进行修正,以保证布线连接关系的正确性;网络检查正确通过后,对PCB设计进行DRC检查,并根据输出文件结果及时对设计进行修正,以保证PCB布线的电气性能.最后需进一步对PCB的机械安装结构进行检查和确认.第七:制版.在此之前,最好还要有一个审核的过程.PCB设计是一个考心思的工作,谁的心思密,经验高,设计出来的板子就好.所以设计时要极其细心,充分考虑各方面的因数(比如说便于维修和检查这一项很多人就不去考虑),精益求精,就一定能设计出一个好板子.印制线路板设计经验点滴对于电子产品来说,印制线路板设计是其从电原理图变成一个具体产品必经的一道设计工序,其设计的合理性与产品生产及产品质量紧密相关,而对于许多刚从事电子设计的人员来说,在这方面经验较少,虽然已学会了印制线路板设计软件,但设计出的印制线路板常有这样那样的问题,而许多电子刊物上少有这方面文章介绍,笔者曾多年从事印制线路板设计的工作,在此将印制线路板设计的点滴经验与大家分享,希望能起到抛砖引玉的作用.笔者的印制线路板设计软件早几年是TANGO,现在则使用PROTEL2.7 F OR WINDOWS.板的布局:印制线路板上的元器件放置的通常顺序:放置与结构有紧密配合的固定位置的元器件,如电源插座、指示灯、开关、连接件之类,这些器件放置好后用软件的LOCK功能将其锁定,使之以后不会被误移动;放置线路上的特殊元件和大的元器件,如发热元件、变压器、IC等;放置小器件.元器件离板边缘的距离:可能的话所有的元器件均放置在离板的边缘3mm以内或至少大于板厚,这是由于在大批量生产的流水线插件和进行波峰焊时,要提供给导轨槽使用,同时也为了防止由于外形加工引起边缘部分的缺损,如果印制线路板上元器件过多,不得已要超出3mm范围时,可以在板的边缘加上3mm的辅边,辅边开V形槽,在生产时用手掰断即可.高低压之间的隔离:在许多印制线路板上同时有高压电路和低压电路,高压电路部分的元器件与低压部分要分隔开放置,隔离距离与要承受的耐压有关,通常情况下在2000kV时板上要距离2mm,在此之上以比例算还要加大,例如若要承受3000V的耐压测试,则高低压线路之间的距离应在3.5mm以上,许多情况下为避免爬电,还在印制线路板上的高低压之间开槽.印制线路板的走线:印制导线的布设应尽可能的短,在高频回路中更应如此;印制导线的拐弯应成圆角,而直角或尖角在高频电路和布线密度高的情况下会影响电气性能;当两面板布线时,两面的导线宜相互垂直、斜交、或弯曲走线,避免相互平行,以减小寄生耦合;作为电路的输入及输出用的印制导线应尽量避免相邻平行,以免发生回授,在这些导线之间最好加接地线.印制导线的宽度:导线宽度应以能满足电气性能要求而又便于生产为宜,它的最小值以承受的电流大小而定,但最小不宜小于0.2mm,在高密度、高精度的印制线路中,导线宽度和间距一般可取0.3mm;导线宽度在大电流情况下还要考虑其温升,单面板实验表明,当铜箔厚度为50μm、导线宽度1~1.5mm、通过电流2A时,温升很小,因此,一般选用1~1.5mm宽度导线就可能满足设计要求而不致引起温升;印制导线的公共地线应尽可能地粗,可能的话,使用大于2~3mm的线条,这点在带有微处理器的电路中尤为重要,因为当地线过细时,由于流过的电流的变化,地电位变动,微处理器定时信号的电平不稳,会使噪声容限劣化;在DIP封装的IC脚间走线,可应用10-10与12-12原则,即当两脚间通过2根线时,焊盘直径可设为50mil、线宽与线距都为10mil,当两脚间只通过1根线时,焊盘直径可设为64mil、线宽与线距都为12mil.印制导线的间距:相邻导线间距必须能满足电气安全要求,而且为了便于操作和生产,间距也应尽量宽些.最小间距至少要能适合承受的电压.这个电压一般包括工作电压、附加波动电压以及其它原因引起的峰值电压.如果有关技术条件允许导线之间存在某种程度的金属残粒,则其间距就会减小.因此设计者在考虑电压时应把这种因素考虑进去.在布线密度较低时,信号线的间距可适当地加大,对高、低电平悬殊的信号线应尽可能地短且加大间距.印制导线的屏蔽与接地:印制导线的公共地线,应尽量布置在印制线路板的边缘部分.在印制线路板上应尽可能多地保留铜箔做地线,这样得到的屏蔽效果,比一长条地线要好,传输线特性和屏蔽作用将得到改善,另外起到了减小分布电容的作用.印制导线的公共地线最好形成环路或网状,这是因为当在同一块板上有许多集成电路,特别是有耗电多的元件时,由于图形上的限制产生了接地电位差,从而引起噪声容限的降低,当做成回路时,接地电位差减小.另外,接地和电源的图形尽可能要与数据的流动方向平行,这是抑制噪声能力增强的秘诀;多层印制线路板可采取其中若干层作屏蔽层,电源层、地线层均可视为屏蔽层,一般地线层和电源层设计在多层印制线路板的内层,信号线设计在内层和外层.焊盘:焊盘的直径和内孔尺寸:焊盘的内孔尺寸必须从元件引线直径和公差尺寸以及搪锡层厚度、孔径公差、孔金属化电镀层厚度等方面考虑,焊盘的内孔一般不小于0.6mm,因为小于0.6mm的孔开模冲孔时不易加工,通常情况下以金属引脚直径值加上0.2mm作为焊盘内孔直径,如电阻的金属评论(1)阅读(1870)[整理] 有源晶振和无源晶振的作用分别是什么?2007-09-11 13:56:41 字号:大中小1.无源晶振是有2个引脚的无极性元件,需要借助于时钟电路才能产生振荡信号,自身无法振荡起来2.有源晶振有4只引脚,是一个完整的振荡器,其中除了石英晶体外,还有晶体管和阻容元件主要看你应用到的电路,如果有时钟电路,就用无源,否则就用有源无源晶体需要用DSP片内的振荡器,无源晶体没有电压的问题,信号电平是可变的,也就是说是根据起振电路来决定的,同样的晶体可以适用于多种电压,可用于多种不同时钟信号电压要求的DSP,而且价格通常也较低,因此对于一般的应用如果条件许可建议用晶体,这尤其适合于产品线丰富批量大的生产者.评论(1)阅读(825)[转载] 芯片封装技术知多少2007-09-11 13:38:51 字号:大中小自从美国Intel公司1971年设计制造出4位微处a理器芯片以来,在20多年时间内,CPU从Intel4004、80286、80386、80486发展到Pentium和PentiumⅡ,数位从4位、8位、16位、32位发展到64位;主频从几兆到今天的400MHz以上,接近GHz;CPU芯片里集成的晶体管数由2000个跃升到500万个以上;半导体制造技术的规模由SSI、MSI、LSI、VLSI达到ULSI.封装的输入/输出(I/O)引脚从几十根,逐渐增加到几百根,下世纪初可能达2千根.这一切真是一个翻天覆地的变化.对于CPU,读者已经很熟悉了,286、386、486、Pentium、Pentium Ⅱ、Celeron、K6、K6-2 ……相信您可以如数家珍似地列出一长串.但谈到CPU和其他大规模集成电路的封装,知道的人未必很多.所谓封装是指安装半导体集成电路芯片用的外壳,它不仅起着安放、固定、密封、保护芯片和增强电热性能的作用,而且还是沟通芯片内部世界与外部电路的桥梁——芯片上的接点用导线连接到封装外壳的引脚上,这些引脚又通过印制板上的导线与其他器件建立连接.因此,封装对CPU和其他LSI集成电路都起着重要的作用.新一代CPU的出现常常伴随着新的封装形式的使用. 芯片的封装技术已经历了好几代的变迁,从DIP、QFP、PGA、BGA到CSP再到MCM,技术指标一代比一代先进,包括芯片面积与封装面积之比越来越接近于1,适用频率越来越高,耐温性能越来越好,引脚数增多,引脚间距减小,重量减小,可靠性提高,使用更加方便等等.下面将对具体的封装形式作详细说明.一、DIP封装70年代流行的是双列直插封装,简称DIP(Dual In-line Package).DIP封装结构具有以下特点:1.适合PCB的穿孔安装;2.比TO型封装(图1)易于对PCB布线;3.操作方便.DIP封装结构形式有:多层陶瓷双列直插式DIP,单层陶瓷双列直插式DIP,引线框架式DIP(含玻璃陶瓷封接式,塑料包封结构式,陶瓷低熔玻璃封装式),如图2所示.衡量一个芯片封装技术先进与否的重要指标是芯片面积与封装面积之比,这个比值越接近1越好.以采用40根I/O引脚塑料包封双列直插式封装(PDIP)的CPU为例,其芯片面积/封装面积=3×3/15.24×50=1:86,离1相差很远.不难看出,这种封装尺寸远比芯片大,说明封装效率很低,占去了很多有效安装面积.Intel公司这期间的CPU如8086、80286都采用PDIP封装.二、芯片载体封装80年代出现了芯片载体封装,其中有陶瓷无引线芯片载体LCCC(Leadless Ceramic Chip Carrier)、塑料有引线芯片载体PLCC(Plastic Leaded Chip Carrier)、小尺寸封装SOP(Small Outline Package)、塑料四边引出扁平封装PQFP(PlasticQuad Flat Package),封装结构形式如图3、图4和图5所示.以0.5mm焊区中心距,208根I/O引脚的QFP封装的CPU为例,外形尺寸28×28mm,芯片尺寸10×10mm,则芯片面积/封装面积=10×10/28×28=1:7.8,由此可见QFP比DIP的封装尺寸大大减小.QFP的特点是:1.适合用SMT表面安装技术在PCB上安装布线;2.封装外形尺寸小,寄生参数减小,适合高频应用;3.操作方便;4.可靠性高.在这期间,Intel公司的CPU,如Intel 80386就采用塑料四边引出扁平封装PQFP.三、BGA封装90年代随着集成技术的进步、设备的改进和深亚微米技术的使用,LSI、VLSI、ULSI相继出现,硅单芯片集成度不断提高,对集成电路封装要求更加严格,I/O引脚数急剧增加,功耗也随之增大.为满足发展的需要,在原有封装品种基础上,又增添了新的品种——球栅阵列封装,简称BGA(Ball Grid Array Package).如图6所示.BGA一出现便成为CPU、南北桥等VLSI芯片的高密度、高性能、多功能及高I/O引脚封装的最佳选择.其特点有:1.I/O引脚数虽然增多,但引脚间距远大于QFP,从而提高了组装成品率;2.虽然它的功耗增加,但BGA能用可控塌陷芯片法焊接,简称C4焊接,从而可以改善它的电热性能:3.厚度比QFP减少1/2以上,重量减轻3/4以上;4.寄生参数减小,信号传输延迟小,使用频率大大提高;5.组装可用共面焊接,可靠性高;6.BGA封装仍与QFP、PGA一样,占用基板面积过大;Intel公司对这种集成度很高(单芯片里达300万只以上晶体管),功耗很大的CPU芯片,如Pentium、Pentium Pro、Pentium Ⅱ采用陶瓷针栅阵列封装CPGA和陶瓷球栅阵列封装CBGA,并在外壳上安装微型排风扇散热,从而达到电路的稳定可靠工作.四、面向未来的新的封装技术BGA封装比QFP先进,更比PGA好,但它的芯片面积/封装面积的比值仍很低.Tessera公司在BGA基础上做了改进,研制出另一种称为μBGA的封装技术,按0.5mm焊区中心距,芯片面积/封装面积的比为1:4,比BGA前进了一大步.1994年9月日本三菱电气研究出一种芯片面积/封装面积=1:1.1的封装结构,其封装外形尺寸只比裸芯片大一点点.也就是说,单个IC芯片有多大,封装尺寸就有多大,从而诞生了一种新的封装形式,命名为芯片尺寸封装,简称CSP(Chip SizePackage或Chip Scale Package).CSP封装具有以下特点:1.满足了LSI芯片引出脚不断增加的需要;2.解决了IC裸芯片不能进行交流参数测试和老化筛选的问题;3.封装面积缩小到BGA的1/4至1/10,延迟时间缩小到极短.曾有人想,当单芯片一时还达不到多种芯片的集成度时,能否将高集成度、高性能、高可靠的CSP芯片(用LSI或IC)和专用集成电路芯片(ASIC)在高密度多层互联基板上用表面安装技术(SMT)组装成为多种多样电子组件、子系统或系统.由这种想法产生出多芯片组件MCM(Multi Chip Model).它将对现代化的计算机、自动化、通讯业等领域产生重大影响.MCM的特。
PCB设计中的射频检测技术
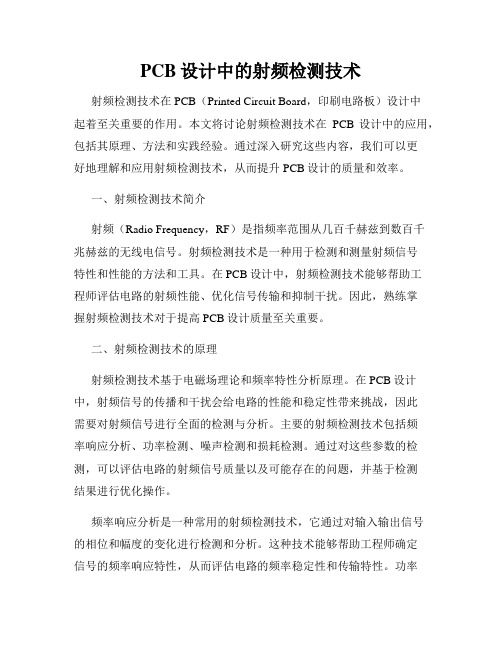
PCB设计中的射频检测技术射频检测技术在PCB(Printed Circuit Board,印刷电路板)设计中起着至关重要的作用。
本文将讨论射频检测技术在PCB设计中的应用,包括其原理、方法和实践经验。
通过深入研究这些内容,我们可以更好地理解和应用射频检测技术,从而提升PCB设计的质量和效率。
一、射频检测技术简介射频(Radio Frequency,RF)是指频率范围从几百千赫兹到数百千兆赫兹的无线电信号。
射频检测技术是一种用于检测和测量射频信号特性和性能的方法和工具。
在PCB设计中,射频检测技术能够帮助工程师评估电路的射频性能、优化信号传输和抑制干扰。
因此,熟练掌握射频检测技术对于提高PCB设计质量至关重要。
二、射频检测技术的原理射频检测技术基于电磁场理论和频率特性分析原理。
在PCB设计中,射频信号的传播和干扰会给电路的性能和稳定性带来挑战,因此需要对射频信号进行全面的检测与分析。
主要的射频检测技术包括频率响应分析、功率检测、噪声检测和损耗检测。
通过对这些参数的检测,可以评估电路的射频信号质量以及可能存在的问题,并基于检测结果进行优化操作。
频率响应分析是一种常用的射频检测技术,它通过对输入输出信号的相位和幅度的变化进行检测和分析。
这种技术能够帮助工程师确定信号的频率响应特性,从而评估电路的频率稳定性和传输特性。
功率检测是另一种重要的射频检测技术,它用于测量信号的功率,以确保电路在正常工作状态下具有适当的功率水平。
噪声检测和损耗检测则主要用于评估电路中可能存在的噪声和损耗情况,以便进行相应的优化和改进措施。
三、射频检测技术的方法在PCB设计中,射频检测技术可以通过多种方法来实施。
以下是几种常见的射频检测方法:1. 传统仪器检测:传统的射频检测方法通常使用专业的测试仪器,如频谱分析仪、网络分析仪等。
这些仪器能够提供准确的信号分析和参数测量,但价格昂贵且需要专业操作技能。
2. 软件仿真检测:近年来,随着计算机软件的不断发展,软件仿真检测成为一种越来越受欢迎的射频检测方法。
PCB测试工艺及技术方法详解
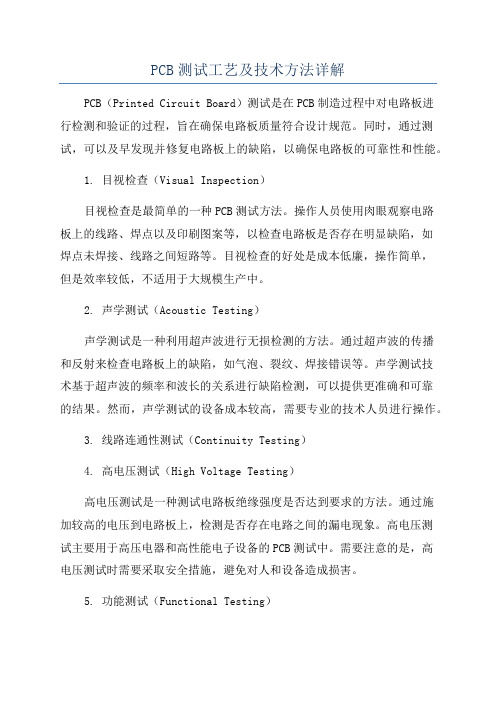
PCB测试工艺及技术方法详解PCB(Printed Circuit Board)测试是在PCB制造过程中对电路板进行检测和验证的过程,旨在确保电路板质量符合设计规范。
同时,通过测试,可以及早发现并修复电路板上的缺陷,以确保电路板的可靠性和性能。
1. 目视检查(Visual Inspection)目视检查是最简单的一种PCB测试方法。
操作人员使用肉眼观察电路板上的线路、焊点以及印刷图案等,以检查电路板是否存在明显缺陷,如焊点未焊接、线路之间短路等。
目视检查的好处是成本低廉,操作简单,但是效率较低,不适用于大规模生产中。
2. 声学测试(Acoustic Testing)声学测试是一种利用超声波进行无损检测的方法。
通过超声波的传播和反射来检查电路板上的缺陷,如气泡、裂纹、焊接错误等。
声学测试技术基于超声波的频率和波长的关系进行缺陷检测,可以提供更准确和可靠的结果。
然而,声学测试的设备成本较高,需要专业的技术人员进行操作。
3. 线路连通性测试(Continuity Testing)4. 高电压测试(High Voltage Testing)高电压测试是一种测试电路板绝缘强度是否达到要求的方法。
通过施加较高的电压到电路板上,检测是否存在电路之间的漏电现象。
高电压测试主要用于高压电器和高性能电子设备的PCB测试中。
需要注意的是,高电压测试时需要采取安全措施,避免对人和设备造成损害。
5. 功能测试(Functional Testing)功能测试是一种对电路板进行正常工作情况下的整体功能验证的方法。
通过将电路板连接到相应的电源和设备上,进行各种操作和测试,来检查电路板是否符合设计要求和功能规范。
功能测试可以模拟实际使用场景,测试电路板的性能、稳定性和可靠性。
功能测试一般需要使用专业的测试设备和软件,并且需要根据具体产品的功能要求进行定制。
除了以上介绍的PCB测试方法外,还有一些其他的测试方法,如热冲击测试、震动测试、环境适应性测试等。
电路板pcb技术要求

电路板pcb技术要求电路板(PCB)技术是现代电子产品制造中不可或缺的一部分。
PCB 是一种用于支持和连接电子元件的基础组件。
它由一个绝缘材料的基板上覆盖着导电材料形成的线路与孔位构成。
PCB技术的要求涵盖了多个方面,包括设计、制造、组装和测试等环节。
PCB设计是整个电路板制造过程的起点。
在设计阶段,需要考虑电路的功能需求、布局规划、信号完整性、电源和地线分离、EMC(电磁兼容性)等因素。
设计人员需要根据产品的要求和限制,选择适当的材料、线宽和间距,并合理安排元件的布局,以确保电路板的性能和可靠性。
PCB制造是将设计图转化为实际电路板的过程。
制造过程包括图形化的电路板制作、化学沉积、光刻、蚀刻、钻孔、金属化、印刷和涂覆等步骤。
制造人员需要严格执行制造标准,确保电路板的质量和一致性。
同时,制造过程中需要注意防止氧化和腐蚀等问题,以保证电路板的可靠性和长寿命。
然后,PCB组装是将元件焊接到电路板上的过程。
在组装过程中,需要根据设计要求和元件规格,选择适当的焊接方法,如表面贴装技术(SMT)或插件焊接技术。
组装人员需要熟悉焊接工艺和设备操作,确保焊接的可靠性和质量。
此外,组装过程还需要进行充分的测试和质量控制,以确保产品的性能和可靠性。
PCB测试是验证电路板功能和性能的过程。
在测试过程中,需要使用专业的测试设备和技术,对电路板进行电气测试、信号完整性测试、功能测试和可靠性测试等。
测试人员需要熟悉测试方法和仪器操作,准确判断测试结果,并及时处理测试中发现的问题。
通过测试,可以确保电路板的质量和性能达到设计要求。
PCB技术要求涉及到设计、制造、组装和测试等多个环节。
在每个环节中,需要专业的人员和设备,严格执行标准和规范,以确保电路板的质量和可靠性。
随着电子产品的发展和需求的增加,PCB技术也在不断创新和进步,以满足更高的要求和挑战。
PCB测试工艺技术

PCB测试工艺技术随着电子行业的迅速发展,PCB板的应用越来越广泛。
为了保证产品品质和稳定性,在生产过程中需要进行PCB测试工艺技术。
本文将介绍PCB测试工艺技术的原理、方法和流程,以及相关的测试仪器设备和常见的测试问题及其解决办法。
一. PCB测试工艺技术的原理和方法PCB测试工艺技术是指在电子产品的生产过程中,通过一系列的测试工序对生产出的PCB板进行测试,以检测PCB板的功能是否符合要求。
其原理是通过测试PCB板的电气性能来判断PCB板的质量。
主要包括以下方法:1.电路连通性测试电路连通性测试是一项起始测试,它可以检测PCB板电路的连通情况,比如是否有开路、短路等问题。
测试方法主要有针式测试和机器式测试两种。
针式测试需要用到专用的测试针,将它们插入PCB板上的测试点进行测试。
机器式测试则需要用到自动测试仪器,它可以快速地测试PCB板上大量的测试点。
2.点数测试点数测试可以检测PCB板上有多少电路,而这些电路是通过测试的。
这一测试方法可以帮助检测出任何未能测试过的区域,以便进行必要的修改和改进。
3.板面外观检查板面外观检查是指检查PCB板在制造过程中是否晶体尺寸、线宽和孔径符合规格要求。
此外,维修和维护人员也可以用它来检查PCB板是否已受到某些损害,如触电或电子计算机。
二. PCB测试工艺技术的流程PCB测试的流程主要包括以下步骤:1.确定测试项目。
在进行PCB测试之前,需要确定测试的项目,即确定测试的类型和范围。
2.准备测试样品。
准备好要测试的PCB板和相应的测试仪器。
同时确保测试样品在一定条件下,如温度、湿度、电源等情况下的测试。
3.进行测试。
根据测试项目进行测试。
4.记录测试结果。
根据测试结果建立PCB板的测试报告。
5.总结和改进。
总结测试结果,确定下一步工作的方向,并改进测试方法和测试参数等。
三. PCB测试工艺技术的测试仪器设备常见的PCB测试工艺测试仪器设备有:1.万用表2.直流电源和交流源3.频率计和波形发生器4.示波器5.网络分析仪6.自动测试仪7.参数测试仪等。
PCB设计技术手册

PCB设计技术手册在电子产品的基础电路板(PCB)上,电子元器件被布置在导电轨道上,形成电路连接。
因此,PCB设计的质量和效率会直接影响到电子产品的性能和生产周期。
这篇文章将介绍一些基本的PCB设计技术,这些技术可以帮助PCB工程师设计出更好的电路板。
一、PCB设计的基本流程PCB设计的基本流程包括:需求分析,电路原理图设计,PCB布线设计,PCB布局设计,PCB生产及测试等步骤。
在PCB设计之前,工程师需要了解产品的功能,要求和规格,并确定PCB板的大小和形状。
在电路原理图设计阶段,设计师需要将产品的电路原理转换为电路原理图,而电路原理图是一种图形化的表示电路关系的工具,其中电路元器件和电路连接以特定的符号表示。
在PCB布线设计阶段,PCB上的导线被布置在电路原理图中指定的位置上,以完成电路连接。
此外,PCB布局设计阶段和PCB生产及测试阶段也非常重要,并且需要设计师在设计之前考虑好这些方面。
二、PCB设计的基本技术1. PCB布局PCB布局是PCB设计工作中的重要阶段,它决定了电子产品的性能、可靠性和成本。
在PCB布局设计时,需要考虑电路布局的紧凑度,信号传输长度、路径、轨迹和EMI/EMC等因素。
为了减少跨越和信号传输的影响,不同的信号线应该被隔离开来,且在布局过程中应该避免出现盲孔位于主通路上的情况。
2. PCB布线PCB布线是在PCB上连接电子元件的导线布置,它直接影响到电子产品的性能和可靠性。
我们应该总是尝试使用最短的布线路径,可以通过使用角度线,曲线线,或在曲线线的拐角处放置过渡电容器等方式来增加信号的干扰抑制能力。
此外,还要注意控制PCB布线的噪声特性,以减少附加噪声和降低EMI和EMC。
3. PCB制造和测试为了确保PCB设计的质量和可靠性,在PCB制造过程中应注意一些细节问题,如PCB板厚度,铜箔厚度等。
测试是评价PCB设计的效果的重要工具,可以测试PCB的关键电参数,以确定设计的可靠性和准确性。
电路板pcb技术要求

电路板pcb技术要求电路板(PCB)是现代电子设备中不可或缺的一部分,它承载着电子元件的连接和支持功能。
在设计和制造电路板时,有一些技术要求需要遵循,以确保电路板的质量和可靠性。
电路板的尺寸和层数是设计时需要考虑的重要因素。
尺寸应根据设备的要求进行合理规划,同时要考虑到制造工艺的可行性。
层数则取决于电路板上的电子元件数量和复杂度。
一般来说,双面电路板已经能满足大多数应用的需求,但在一些特殊情况下,多层电路板可能更适合。
电路板的材料选择也是至关重要的。
常见的电路板材料包括FR-4玻璃纤维覆铜板和铝基板。
FR-4材料具有良好的绝缘性能和机械强度,适用于大多数一般性应用。
而铝基板则具有优异的散热性能,适用于高功率和高温应用。
在选择材料时,需要考虑到电路板的工作环境和要求。
电路板的布线和布局也需要注意。
布线是指电路板上导线和元件之间的连接方式,而布局则是指元件在电路板上的位置安排。
合理的布线和布局可以减少电路板的噪声和干扰,提高电路的性能和稳定性。
布线时需要注意信号和电源线的分离,避免相互干扰。
同时,布局时要考虑到元件之间的相互作用和散热需求,以保证电路板的正常工作。
电路板的焊接和组装也是关键步骤。
焊接是将电子元件固定在电路板上的过程,可分为手工焊接和机器焊接两种方式。
手工焊接需要经验丰富的技术人员进行,而机器焊接则可以提高生产效率和焊接质量。
组装是将电路板与其他设备连接起来的过程,需要确保连接可靠和接触良好。
电路板的测试和质量控制也是不可忽视的。
在制造过程中,需要进行各种测试,如电气测试、连通性测试和可靠性测试,以确保电路板的功能和性能符合设计要求。
同时,质量控制是指对电路板制造过程中的每个环节进行严格控制,以减少缺陷和故障率。
电路板(PCB)技术要求是确保电路板质量和可靠性的重要保证。
从尺寸和层数的选择到材料的选用,再到布线布局、焊接组装和测试质量控制,每个环节都需要严格遵循技术要求。
只有这样,才能制造出高质量的电路板,满足各种应用需求。
PCB可靠性测试方法则要

PCB可靠性测试方法则要PCB(Printed Circuit Board,印刷电路板)是电子设备中重要的组成部分,其可靠性对整个系统的稳定运行和寿命有着重要影响。
为了确保PCB的可靠性,需要进行一系列的测试方法,以下将介绍几种常用的PCB可靠性测试方法。
1.焊接可靠性测试:焊接是PCB组装中的重要工艺,焊接可靠性测试主要目的是评估焊接质量和连接稳定性。
常用的焊接可靠性测试方法包括环境测试、热冲击测试、振动测试和冲击测试等。
环境测试将PCB置于高温、低温、高湿和低湿等不同环境条件下进行测试,以模拟实际使用环境;热冲击测试则是在极端温度变化下测试焊点的稳定性;振动测试和冲击测试则是评估焊点的机械强度和耐久性。
2.电气性能测试:电气性能测试是评估PCB的工作稳定性和可靠性的重要手段。
常用的电气性能测试方法包括耐压测试、绝缘电阻测试、接触电阻测试和信号传输测试等。
耐压测试通过对PCB内部电路的导电材料和结构的耐压能力进行测试,以确保PCB能够在工作电压范围内正常运行;绝缘电阻测试评估PCB的绝缘性能,确保电路之间不发生意外电流引起的故障;接触电阻测试用于评估焊接点和连接器的接触质量等;信号传输测试则是测试PCB上各个信号线路的传输性能,以保证数据的准确性和可靠性。
3.环境适应性测试:环境适应性测试是评估PCB在特定环境条件下的可靠性。
这些环境条件包括温度、湿度、气压、气氛和介质等。
环境适应性测试方法主要包括高温老化测试、低温冷冻测试、湿热循环测试和腐蚀性气体测试等。
高温老化测试用于评估PCB在高温下的稳定性和耐久性;低温冷冻测试用于评估PCB在低温下的性能和可靠性;湿热循环测试则是在高温高湿条件下测试PCB的可靠性;腐蚀性气体测试则是评估PCB对环境中腐蚀气体的抵抗能力。
4.动态电热测试:动态电热测试是评估PCB在实际工作条件下的电热特性和可靠性。
这种测试方法主要是通过在PCB上施加实际工作负载,并在不同工况下测试PCB的温度分布、热传导性能和散热能力等。
- 1、下载文档前请自行甄别文档内容的完整性,平台不提供额外的编辑、内容补充、找答案等附加服务。
- 2、"仅部分预览"的文档,不可在线预览部分如存在完整性等问题,可反馈申请退款(可完整预览的文档不适用该条件!)。
- 3、如文档侵犯您的权益,请联系客服反馈,我们会尽快为您处理(人工客服工作时间:9:00-18:30)。
PCB可测试性设计技术要概述随着技术进入超大规模集成(VLSI)时代,VLSI电路的高度复杂性及多层印制板、表面封装(SMT)、圆片规模集成(WSI)和多模块(MCM)技术在电路系统中的运用,都使得电路节点的物理可访问性正逐步削弱以至于消失,电路和系统的可测试性急剧下降,测试成本在电路和系统总成本中所占的比例不断上升,常规测试方法正面临着日趋严重的测试困难。
PCB可测试性设计技术要概述在电路的逻辑设计完成后,通常是以手工的方式来加入可测试性(Testability)设计。
激烈的市场竞争要求更短的设计开发周期,这样的可测试性设计方法已成为严重的设计瓶颈。
随着设计进入了以综合为基础的阶段,将测试与综合结合起来,以自动化的方式来实现可测试性设计已成为必须的趋势。
1.PCB可测试性的关键技术PCB可测试性的关键技术包括:可测试性的度量、可测试性机制的设计与优化和测试信息的处理与故障诊断。
提高印制板的可测试性,首先就要对PCB的可测试性水平进行度量,一般包括精确性和简单性两个方面。
精确性是指可测试性的度量方法能准确地预计产品测试程序生成的困难,并且定位到产品某一部位,从而便于产品设计进行可测试性更改。
简单性是指度量可测试性的计算量应小于测试程序生成的计算量。
PCB的可测试性设计过程实际上就是将某种能够方便测试进行的可测试性机制引入到PCB中,提供获取被测对象内部测试信息的信息通道。
因此,合理有效的设计可测试性机制是成功地提高PCB可测试性水平的保障。
现有的可测试性机制的设计方法包括LFSR方法、IDDQ技术、电平灵敏度设计以及边界扫描机制等。
可测试性机制的引入一方面会提高系统的可测试性水平,从而降低产品的全寿命周期费用,但另一方面也在一定程度上提高了产品的初始成本。
进行可测试性机制设计优化就是要综合权衡各种可测试性机制的性能和费用,采用性能费用比最佳的设计机制。
提高产品质量和可靠性,降低产品全寿命周期费用,要求可测试性设计技术能够方便快捷地获取测试时的反馈信息,能够很容易地根据反馈信息做出故障诊断。
2.PCB可测试性技术的发展可测试性技术自出现以来,得到了迅速的发展,按测试机制的特点及出现时间,大体分为3个发展阶段:特定目标可测试性设计阶段、基于扫描设计的结构化测试性设计阶段和基于边界扫描机制的标准化可测试性设计阶段。
(1)特定目标可测试性设计技术特定目标可测试性设计技术(Ad-hocDFT)是第一代可测试性设计技术,它以外部测试和特定目标可测试性设计方法为基础。
这种设计方法是针对特定功能和结构的PCB进行可测试性预测,判断其是否符合可测试性要求,若不能满足,则通过改善电路设计方案来提高其河测试性水平,直到满足要求。
它主要采用外部测试方法,测试向量的输入和响应的输出均通过被测对象的输入输出端口进行操作,对被测对象的内部结点的控制和观测则采用以针床为基础的在线测试技术。
这种方法的主要缺点是,复杂系统的设计难度大、周期长;难以实现时序电路的测试;需要专用的测试针床和仪器,因此成本高,且测试时可能会损坏被测电路。
随着PCB的规模越来越大、芯片管脚间距越来越小、表面封装技术和MCM技术的发展,采用无力接触的针床测试方法越来越难以满足要求。
回此,目前除一些分离元件较多、复杂程度较低的电路的可测试性设计以外,特定目标可测试性设计技术已逐步被其他设计方法所取代。
(2)基于扫描设计的结构化设计结构化可测试性设计是第二代的DFT方法,其主要思想是从可测试性观点出发,对电路结构提出一定的设计规则以使所设计的电路便于测试。
这种方法通常采用扫描设计,通常采用扫描设计,包括电平敏感扫描设计、扫描通路和扫描位置等。
这种设计方法克服了特定目标可测试性设计的缺点,但它同时也有不少缺点。
这些缺点包括:设计过程仍较为复杂,设计周期长,因主要采用外部测试的方法,所以自动化程度不够,成本较高;不同厂家的产品采用不同的设计方法,使得产品之间互不兼容,产品的可维修性差。
(3)基于边界扫描机制的标准化设计基于边界扫描机制的标准化设计方法是针对结构化可测试性设计方法的缺点而开发出的一种更为简单、标准化的可测试性设计方法,是第三代的DFT,是IEEE和JTAG(JointTestActionGroup)于1990年共同推出的IEEE1149.1边界扫描标准。
该标准定义了标准的边界扫描结构及其测试接口,其主要思想是通过在芯片管脚和芯片内部逻辑电路之间(即芯片的边界上)增加边界扫描单元,实现对芯片管脚状态的串行设定和读取,从而提供芯片级、板级、系统级的标准测试框架。
这个标准的规范使得不同厂家的芯片用到同一系统中时,不仅能提供统一的施加测试信号的功能,而且也能支持所有的测试情况(芯片测试、组件测试、PCB测试、PCB上芯片的测试、MCM测试、模块测试以及系统诊断等)。
边界扫描机制提供了一种完整的、标准化的可测试性设计方法。
自从边界扫描标准出现以来,市场上支持边界扫描机制的芯片及设计开发软件与日俱增,其应用越来越广泛。
11.2.4几种可测试性设计技术1.Ad-hoc测试技术如前所述,特定目标可测试性设计技术(Ad-hoc)是一种早期的DFT技术,它是针对一个已经成型的印制电路设计中的测试问题。
这种技术的主要基本思想是:通过添加选择器来访问内部电路,以增强其可控性和可观测性;添加逻辑门电路来控制内总电路以增加其可控性;在需要的地主增加观测点。
这种技术有如下3种方法:(1)分块法基于测试生成和故障模拟的复杂程度正比于电路逻辑门数的3次方,因此,如果将电路分成若干独立的子块进行测试,就可以大大简化测试。
分块法正是基于这点而提出的,这种方法在技术实现上又有3种方式:机械式分割、跳线式和选通门式。
机械分割式是将电路一分为二,跳线式则引入大量的I/O端口,选通门式需要大量额外的输入/输出和选题模块。
(2)添加测试点这是提高电路可测试性最直接的方法。
其基本的思想是将电路内部难于测试的节点直接引出作为测试点,在测试时由原始输入端直接控制并可由原始输出端直接观察。
当测试点作为PCB的原始输入端时,可以提高电路的可控性;当测试点作为用作电路的原始输出时,则可以提高电路的可观测性。
(3)利用总线结构法总线结构类似于分块法,可用在专用PCB 的可测试性中。
它将电路分成若干个功能,然后与总线相连,从而可以通过总线测试各个功能模块,改善了各个功能块的可测试性。
但是,这种方法的一个缺点是功能检测总线自身的故障。
Ad-hoc测试法的优点是直接有效,可以尽可能地减少额外的面积消耗,不会对原始电路的设计产生限制,对于少量需要特别考虑的点比较适用。
但是由于它需要添加新的测试点和管脚,而且这无法自动完成,需要设计人员对电路的深入了解后提出,从而测试成本较高;在某些情况下功能测试可能需要耗费大量的输入输出引脚;必须构造错误的激励达到测试目的。
基于以上原因,这种测试方法正逐渐被扫描测试和内建自测试技术(BIST)所取代。
2.扫描技术印制电路中一般都包括了时序逻辑和组合逻辑两部分。
组合逻辑使现有测试技术能较好地测试生成;而时序逻辑电路的测试生成,由于时序电路往往很复杂,因此很难获得足够令人满意的测试程序。
扫描结合测试向量自动生成技术,通过将电路中难以测试的时序元件转化为可串行输入和输出的可扫面单元,从而从可测试性的角度来看增加了许多可控制点和观测点,极大地提高了整个PCB的可观测性。
扫描设计是当今流行的测试方法。
根据扫描测试包含的触发器数量,它可分为全面扫描测试和部分扫描测试及边界扫描测试。
全面扫描测试技术易于实现,测试覆盖率高,但消耗资源也多,所占面积大,有可能会对原始电路设计产生不良影响;部分扫描技术实现相对全面扫描来说较难,测试覆盖率不高,但其消耗的资源也较少,占用面积较小,对原始设计的影响也不大。
边界扫描测试作为一种特殊的扫描方式和测试标准,它提供了一整套完整的测试方案,且在实际的测试中不需要借助复杂和昂贵的测试设备。
基于JTAC的边界扫测试技术是目前的主流测试技术,得到了广泛的应用,并得到了世界上绝大多数集成电路制造商和设备测试商的支持,如Intel80386-EX和Intel80486以上处理器、Motorola公司的68040微处理器,Xilinx公司的XC3001以上系列FPGA、TexasInstruction公司的C40系列DSP芯片、DEC的Alpha21164系列Risc芯片等,都支持JTAG1149.1规范。
下面将对其体系结构进行简要介绍。
为实现边界扫描,每个被测芯片都必须在芯片引脚和该引脚所连接的芯片电路之间包含称为边界扫描单元的测试扫描电路。
除与封装引脚的芯片的工作逻辑相连外,边界扫描单元也进行互连,在集成电路周围形成移位寄存器通路。
在正常的芯片操作过程中,数据在芯片引脚和芯片的内部逻辑之间流动,如同扫描单元不存在一样。
但在测试方式下,测试程序引导扫描单元沿移位寄存器传送数据,后者可归类于多芯片和芯片部件。
装入测试单元的数据可取代流入或流出芯片引脚的数据。
这样,除外部芯片与芯片间的连接外,也允许进行芯片内部逻辑的测试。
边界扫描结构使器件的I/O端口具有可控制性、可观察性,从而改善器件和系统的可测试性。
边界扫描结构如图6-2所示。
它通过附加的TAP (TestAccessPort,测试访问口),可以将测试激励信号移位置入芯片的边界扫描单元或将测试响应信号从边界扫描单元读出。
这样,通过扫描机制由TAP控制器、TAP测试存取端口及若干寄存器组成,全部设计在组件内。
图11-2边界扫描体系结构图6-3所示为数据寄存器(DataRegister,DR)连接图。
IEEE1149.1所定义的DR至少应包括两个寄存器,即一测试边界扫描寄存器(BoundaryScanRegister,BSR)和旁路寄存器(BypassRegister,BR)。
图6-3中的其他寄存器是IEEE1149.1协议的可选寄存器,分别是设备标识寄存器(DeviceIdentificationRegister,DIR)和测试数据寄存器(TestDataRegister,TDR)。
从图6-2、图6-3可以看出,边界扫描寄存器是一个移位寄存器通路,它含有与组件所有输入和输出引脚连接的边界扫描单元,即它的长度等于测试对象中的被测引脚。
对BSR的操作,如捕获引脚信号、移位等,不会影响芯片的正常操作。
在扫描测试过程中,BSR输出的信号可经TDO移出,而新的数据又可以从TDI移入。
图11-3数据寄存器连接示意图3.内建自测技术(BIST)内建自测设计技术的基本思想是不需要外产来施加测试向量,由电路自己生成测试向量,依靠自身来决定获得的测试结果是否正确。
这种方法通过PCB内部集成少量的逻辑电路来实现对集成电路的测试。