个人总结的铝合金压铸件结构设计方法
压铸模具结构及设计剖析
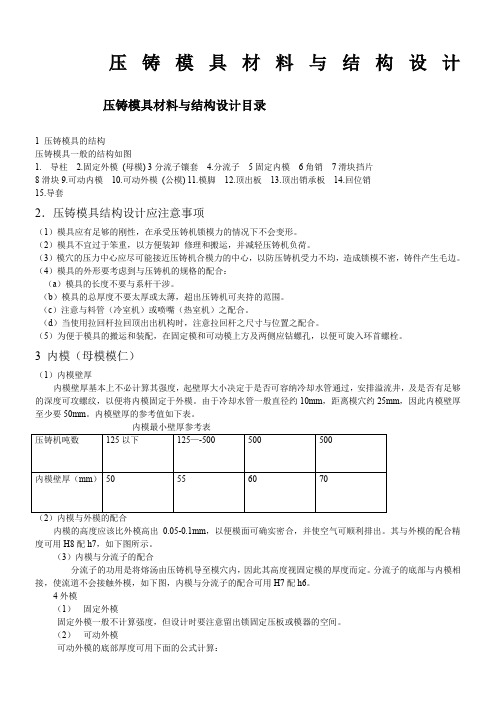
压铸模具材料与结构设计压铸模具材料与结构设计目录1 压铸模具的结构压铸模具一般的结构如图1.导柱2.固定外模(母模) 3分流子镶套 4.分流子5固定内模6角销7滑块挡片8滑块9.可动内模10.可动外模(公模) 11.模脚12.顶出板13.顶出销承板14.回位销15.导套2.压铸模具结构设计应注意事项(1)模具应有足够的刚性,在承受压铸机锁模力的情况下不会变形。
(2)模具不宜过于笨重,以方便装卸修理和搬运,并减轻压铸机负荷。
(3)模穴的压力中心应尽可能接近压铸机合模力的中心,以防压铸机受力不均,造成锁模不密,铸件产生毛边。
(4)模具的外形要考虑到与压铸机的规格的配合:(a)模具的长度不要与系杆干涉。
(b)模具的总厚度不要太厚或太薄,超出压铸机可夹持的范围。
(c)注意与料管(冷室机)或喷嘴(热室机)之配合。
(d)当使用拉回杆拉回顶出出机构时,注意拉回杆之尺寸与位置之配合。
(5)为便于模具的搬运和装配,在固定模和可动模上方及两侧应钻螺孔,以便可旋入环首螺栓。
3 内模(母模模仁)(1)内模壁厚内模壁厚基本上不必计算其强度,起壁厚大小决定于是否可容纳冷却水管通过,安排溢流井,及是否有足够的深度可攻螺纹,以便将内模固定于外模。
由于冷却水管一般直径约10mm,距离模穴约25mm,因此内模壁厚至少要50mm。
内模壁厚的参考值如下表。
(2)内模与外模的配合内模的高度应该比外模高出0.05-0.1mm,以便模面可确实密合,并使空气可顺利排出。
其与外模的配合精度可用H8配h7,如下图所示。
(3)内模与分流子的配合分流子的功用是将熔汤由压铸机导至模穴内,因此其高度视固定模的厚度而定。
分流子的底部与内模相接,使流道不会接触外模,如下图,内模与分流子的配合可用H7配h6。
4外模(1)固定外模固定外模一般不计算强度,但设计时要注意留出锁固定压板或模器的空间。
(2)可动外模可动外模的底部厚度可用下面的公式计算:其中:h:外模底部之厚度(mm)p:铸造压力(kg/cm2)L:模脚之间距(mm)a:成品之长度(mm)b:成品之宽度(mm)B:外模之宽度(mm)E:钢的杨氏模数=2.1×106kg/cm2d:外模在开模方向的最大变形量(mm),一般取d≤0.05mm.例:某铸件长300mm,宽250mm,铸造压力选定280(kg/cm2),外模之宽度560(mm),模脚之间距360(mm),最大变形量取0.05(mm)。
铝合金压铸工艺中的模具设计
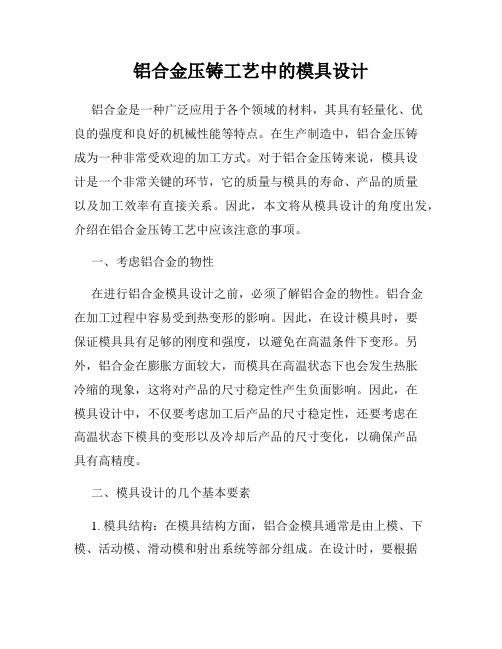
铝合金压铸工艺中的模具设计铝合金是一种广泛应用于各个领域的材料,其具有轻量化、优良的强度和良好的机械性能等特点。
在生产制造中,铝合金压铸成为一种非常受欢迎的加工方式。
对于铝合金压铸来说,模具设计是一个非常关键的环节,它的质量与模具的寿命、产品的质量以及加工效率有直接关系。
因此,本文将从模具设计的角度出发,介绍在铝合金压铸工艺中应该注意的事项。
一、考虑铝合金的物性在进行铝合金模具设计之前,必须了解铝合金的物性。
铝合金在加工过程中容易受到热变形的影响。
因此,在设计模具时,要保证模具具有足够的刚度和强度,以避免在高温条件下变形。
另外,铝合金在膨胀方面较大,而模具在高温状态下也会发生热胀冷缩的现象,这将对产品的尺寸稳定性产生负面影响。
因此,在模具设计中,不仅要考虑加工后产品的尺寸稳定性,还要考虑在高温状态下模具的变形以及冷却后产品的尺寸变化,以确保产品具有高精度。
二、模具设计的几个基本要素1. 模具结构:在模具结构方面,铝合金模具通常是由上模、下模、活动模、滑动模和射出系统等部分组成。
在设计时,要根据铝合金的物性和加工要求来确定模具结构和形状,以达到高效生产的目的。
2. 模具材料:在模具材料的选择方面,应根据铝合金的物性进行选择。
通常,适合用于铝合金模具的材料应具有高强度、高耐磨性和高温耐受性等特点。
目前,常用的模具材料有SKD61、H13和CRM等。
3. 考虑注塑工艺:在进行模具设计时,必须考虑到注塑工艺。
这意味着必须根据注塑工艺的参数来设计模具。
例如,应根据化学成分和温度参数来确定注塑机的射出系统和出口形状,以确保正常的注塑过程。
三、注塑机的选择在进行铝合金压铸加工时,注塑机的选择是非常关键的环节。
不同的注塑机具有不同的投影面积和射程,这会对产品的尺寸稳定性、成型速度和加工效率产生直接影响。
因此,在选择注塑机时,不仅要考虑加工数量和生产周期,还要考虑产品的几何形状、尺寸和质量要求。
四、模具维护模具在长期使用过程中,需要进行定期维护和保养。
压铸件结构设计及影响

2.5
1.2
2.5
1.0
1.8
1.8
3.0
1.8
3.0
1.5
2.2
2.5
3.5
2.5
3.5
2.0
2.5
压铸件壁厚同浇注温度的关系
浇注温度越高,溶解空气越多,难以析出,直接影响塑性;含铁量也随着温度 的升高而升高,含铁量高导致流动性差,结晶粗大,性能恶化;溶液氧化加剧, 氧化夹渣增多,产生缺陷;温度高易产生紊流,饱气等。
压铸件最小脱模斜度
配合面最小斜度
非配合面最小斜度
B
合金种类
外表面A 内表面B 内表面A 内表面B
铝、镁合金 0˚15΄
0˚30΄
0˚30́
1˚
A
锌合金
0˚10΄
0˚15΄
0˚15΄
0˚45΄
•说明: •由此斜度而引起的铸件尺寸偏差,不计入尺寸公差值内。 •表中数值仅适用型腔深度或型芯高度≤50mm,表面粗糙度在Ra0.1,大端 与小端 •尺寸的单面差的最小值为0.03mm。当深度或高度>50mm,或表面粗糙 度超过 Ra0.1时,则脱模斜度可适当增加。 •高熔点的合金大于低熔点合金; •壁厚厚的大于薄壁的; •内侧的大于外侧的; •形状复杂的大于形状简单的。
压铸件圆角参数的选择一
压铸件圆角参数的选择二
压铸件圆角参数的选择三
压铸件圆角与应力集中的关系
圆角过小导致模具龟裂、掉块
压铸加强筋的设计
h1 h2
h
结构尺寸
说明
a
b=1~1.4h h1≤5h
b——筋的根部宽度 h——铸件的壁厚
h2≥0.8mm
h1——筋的高度
r1=(0.5bcosahsina) h2——筋端离筋端的高度
铝合金压铸件的结构设计经验
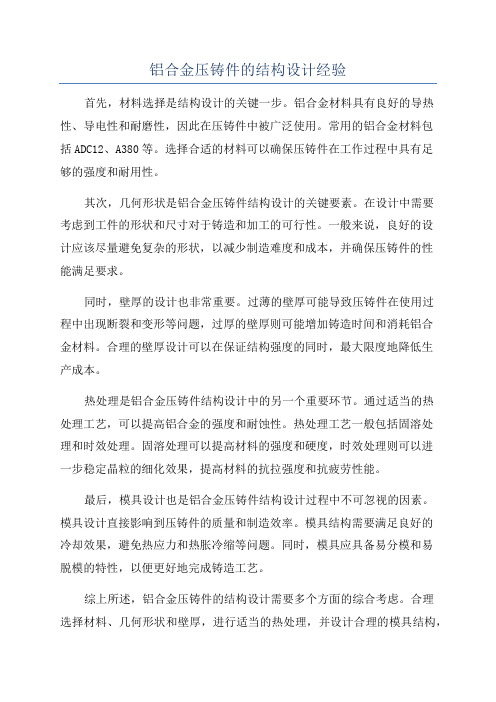
铝合金压铸件的结构设计经验首先,材料选择是结构设计的关键一步。
铝合金材料具有良好的导热性、导电性和耐磨性,因此在压铸件中被广泛使用。
常用的铝合金材料包括ADC12、A380等。
选择合适的材料可以确保压铸件在工作过程中具有足够的强度和耐用性。
其次,几何形状是铝合金压铸件结构设计的关键要素。
在设计中需要考虑到工件的形状和尺寸对于铸造和加工的可行性。
一般来说,良好的设计应该尽量避免复杂的形状,以减少制造难度和成本,并确保压铸件的性能满足要求。
同时,壁厚的设计也非常重要。
过薄的壁厚可能导致压铸件在使用过程中出现断裂和变形等问题,过厚的壁厚则可能增加铸造时间和消耗铝合金材料。
合理的壁厚设计可以在保证结构强度的同时,最大限度地降低生产成本。
热处理是铝合金压铸件结构设计中的另一个重要环节。
通过适当的热处理工艺,可以提高铝合金的强度和耐蚀性。
热处理工艺一般包括固溶处理和时效处理。
固溶处理可以提高材料的强度和硬度,时效处理则可以进一步稳定晶粒的细化效果,提高材料的抗拉强度和抗疲劳性能。
最后,模具设计也是铝合金压铸件结构设计过程中不可忽视的因素。
模具设计直接影响到压铸件的质量和制造效率。
模具结构需要满足良好的冷却效果,避免热应力和热胀冷缩等问题。
同时,模具应具备易分模和易脱模的特性,以便更好地完成铸造工艺。
综上所述,铝合金压铸件的结构设计需要多个方面的综合考虑。
合理选择材料、几何形状和壁厚,进行适当的热处理,并设计合理的模具结构,可以确保铝合金压铸件具有优良的性能和稳定的质量,满足不同工程领域的需求。
五金、铝合金压铸件的结构设计、生产工艺和相关模具

五金、铝合金压铸件的结构设计、生产工艺和相关模具一、铝合金压铸件的结构设计作为五金制品的一种,铝合金压铸件在工业生产中具有很重要的作用,它广泛应用于汽车零部件、摩托车零部件、自行车零部件、电工设备、航空航天领域等。
铝合金压铸件的结构设计是非常重要的,它直接影响到产品的质量和使用性能。
1.结构设计原则(1)设计合理性:要求产品设计合理,能够满足产品的使用要求和生产工艺要求。
(2)易于加工:要求产品的结构设计能够方便加工和生产,减少生产成本。
(3)适应性强:要求产品的结构设计能够适应不同的工艺要求和使用环境。
2.结构设计要点(1)壁厚:对于铝合金压铸件来说,壁厚的设计是非常重要的,壁厚太厚容易造成收缩不均匀、气泡、裂纹等问题,壁厚太薄则会影响产品的强度和稳定性。
(2)加工余量:在设计铝合金压铸件时需要考虑到加工余量,保证产品在结束后进行加工时不会出现问题。
(3)结构形式:产品的结构形式要具有设计的合理性和美学性,能够顺应现代的审美观念。
(4)浇口设计:浇口的设计直接影响到产品的成型质量,需要设计合理的浇口位置和形式。
3.结构设计方法(1)CAD设计:利用CAD软件进行产品的三维设计和分析,可以有效地减少设计过程中的错误和成本。
(2)模具设计:根据产品的结构设计进行模具的设计,保证产品的生产质量和效率。
二、铝合金压铸件的生产工艺铝合金压铸件的生产工艺是一个复杂的过程,需要结合材料特性和模具设计才能完成。
生产工艺的质量直接关系到产品的质量和性能。
1.型腔填充铝合金压铸件的成型过程是通过将铝合金在一定的温度下充入模具中,并施加一定的压力来完成的。
型腔填充是成型过程中的关键一步,需要确保模具内的铝合金能够充分填满型腔,避免气泡和缩松等问题的产生。
2.固化冷却在型腔充填完成后,需要将模具进行固化冷却,使铝合金在模具中凝固成型。
固化冷却过程中需要控制温度和时间,保证产品的成型质量。
3.反压和除渣在成型后的铝合金压铸件表面可能会出现一些氧化物和杂质,需要进行反压和除渣处理,保证产品的表面质量。
铝合金压铸件设计要点

工 业 技 术102科技资讯 SCIENCE & TECHNOLOGY INFORMATION①作者简介:项文杰(1987—),男,浙江绍兴人,本科,助理工程师,从事产品结构设计工作。
DOI:10.16661/ki.1672-3791.2017.27.102铝合金压铸件设计要点①项文杰 佟志国(浙江宇视科技有限公司 浙江杭州 310051)摘 要:一位优秀的压铸件设计人员,应熟悉压铸型的制造工艺和压铸件的生产工艺,以便使设计的压铸件符合制型最简单、生产操作最方便的要求。
压铸件设计是保证压铸件质量的最根本环节,其结构设计和工艺的合理性直接决定模具制作、产品尺寸精度、压铸工艺参数、生产安装效率等高低难易程度。
文章通过归纳铝合金压铸件在设计过程中的注意要点来提高压铸件设计质量,为更多结构设计师提供一定的参考依据。
关键词:压铸 结构设计 模具 缺陷中图分类号:TG249.2 文献标识码:A 文章编号:1672-3791(2017)09(c)-0102-03Abstract : An excellent die casting designer should be familiar with the die casting process and the production process of die casting, so that the design of die casting conform to the most simple production and the most convenient production operation requirements. Die casting design is the most fundamental link to ensure the quality of die casting, the structural design and the rationality of the process directly determine the mold production, product size accuracy, die casting process parameters, production and installation efficiency and other high and low degree of ease. In this paper, the main points of attention in the design process of aluminum alloy die casting are summarized to improve the quality of die casting design, and provide a reference for more structural designers.Key Words : Casting; Structure design; Pattern; Defect铝压铸件具有生产效率高、加工成本低、生产过程中易实现机械自动化、铸件尺寸精度高、表面质量好、整体力学性能好等优点;但在铸造成型过程中易产生气孔、流痕、擦伤、凹陷、裂纹、欠铸等缺陷,这些缺陷使得压铸件外观质量和机械性能下降。
铝合金压铸模具结构剖析

铝合金压铸模具结构剖析
铝合金压铸模具结构剖析
铝合金压铸模具,是如何设计的?如题,产品图如下,有很多的薄片小筋板,分型面是平整的;学习参考就来下载图纸吧。
模具设计思路:
1.压铸模具设计,铝合金压铸模产品的三维外观,平面较于规则,对于新手模具设计师来说,都可以搞定模具设计;
2.压铸模具图纸产品后模侧的结构会有凸起特征,分型面直接用坐标拆分即可;
3.压铸模具设计-拔模检测,以正负0.5为分析值,其符合开模要求;
4.压铸模具图纸-内厚分析,两端有装配结构孔,其结构较厚,上面有装配的螺丝孔;
5.压铸模具图纸,其模具的外观整体结构,压铸模具不带工字板,要开码模槽;
6压铸模具图纸,滑块位置结构剖面线,其铲基原身留,斜导柱尽量做到16;
7.压铸模具图纸,分流锥剖面图,整体来说,压铸模具结构相对于简单,分流锥图解流道不好设计;
8.压铸模具设计教程,前模仁平面有凸起台阶,流道的对面是渣包,用UG拆分体一次可以把分型面设计好,渣包要拉伸、拔模、倒R 角;
9.压铸模具设计,后模结构设计,一般设计压铸模具,都需要用模流分析软件跑一跑,然后再画进胶流道,流道是压铸模具设计的一大难点;
10.压铸模具设计,滑块入子原身结构设计,侧孔用滑块抽芯,双螺丝固定在行位座上。
压铸件结构设计规范方案

压铸件的结构设计压铸件的结构设计是压铸工作的第一步。
设计的合理性和工艺的适应性会影响后续工作的顺利进行,如分型面的选择、浇口的开度、顶出机构的布置、模具和制造难度,合金凝固和收缩规律,铸造精度的保证,缺陷的检测。
种类等,都会以压铸件本身的优劣为前提。
1 、压铸件设计预检说明(1)压铸件的设计涉及四个方面:a、即压力铸造对零件的形状和结构的要求;乙。
压铸件的工艺性能;丙。
压铸件的尺寸精度和外观要求;d .压铸件的分型面确定;压铸件的设计是压铸生产技术的重要组成部分。
设计中必须考虑以下问题:模具分型面的选择、浇口的开度、顶出器位置的选择、铸件的收缩率、铸件尺寸精度的保证、铸件局部缺陷的预防、铸件孔的相关要求、铸件的相关要求收缩变形,加工余量大小;(2)压铸件的设计如下:a、正确选择压铸材料;乙。
合理确定压铸件的尺寸精度;丙。
尽量使壁厚分布均匀;d .在每个角落添加工艺角以防止尖角。
(3)压铸件的分类按使用要求可分为两类,一类是承受较大载荷或具有较高相对运动速度的零件。
检验项目包括尺寸、表面质量、化学成分、力学性能[抗拉强度、伸长率]、硬度];另一类是其他零件,检验项目包括尺寸、外观质量和化学成分。
在设计压铸件时,还应注意零件应符合压铸的工艺要求。
压铸件的可制造性从分型面的位置、顶面顶杆的位置、铸孔的相关要求、收缩变形的相关要求、加工余量的大小等方面考虑。
合理确定压铸面的分型面,既可以简化压铸模具的结构,又可以保证铸件的质量。
⑷、压铸结构的可制造性:1)尽量消除铸件咬边,使模具结构简单。
2)使铸件的壁厚尽可能均匀,利用加强筋减少壁厚,减少铸件的气孔、缩孔、变形等缺陷。
3)尽量消除铸件上的深孔和深腔。
由于小芯子容易折弯折断,深腔的充排气差。
4)设计的铸件应易于脱模和抽芯。
5 ] 肉厚的均匀性是必要的。
6 ] 防止尖角。
7 ] 注意拔模斜度。
8 ] 注意产品公差标记。
9 ] 太厚太薄都不合适。
10 ]防止死角倒角(可以尽量少)。
压铸铝工艺及结构

压铸铝工艺是一种制造铝制品的方法,它涉及将铝液注入模具中,然后冷却固化形成所需的形状。
这种工艺可以生产出高强度、精度高、表面光滑的铝制品,广泛应用于汽车、电子、建筑等行业。
压铸铝结构是指用压铸铝工艺制造的铝制品的结构。
这种结构通常具有以下特点:
1. 高强度:压铸铝工艺可以生产出高强度的铝制品,其强度可以与钢材相媲美。
2. 精度高:压铸铝工艺可以保证铝制品的尺寸精度,满足各种精密设备的装配要求。
3. 表面光滑:压铸铝工艺可以生产出表面光滑的铝制品,减少了后续加工的需要。
4. 耐腐蚀:铝本身具有良好的耐腐蚀性能,经过压铸铝工艺处理后,其耐腐蚀性能进一步提高。
5. 易于回收:铝具有很高的回收价值,废弃的压铸铝制品可以方便地回收再利用。
总之,压铸铝工艺及结构具有许多优点,广泛应用于各个行业。
压铸模设计压铸件结构设计及压铸工艺

压铸模设计、压铸件结构设计及压铸工艺引言压铸是一种常用的金属零件制造方法,其通过将熔化的金属注入到预先加工好的模具中,通过压力将金属冷却固化成型。
在压铸过程中,压铸模具的设计、压铸件结构的设计以及压铸工艺的选择都是至关重要的。
本文将分别介绍压铸模设计的相关要点、压铸件结构设计的原则以及压铸工艺的选择。
压铸模设计要点压铸模具是进行压铸加工的关键工具,其设计的合理与否直接影响到产品质量和生产效率。
下面是一些压铸模设计的要点:1.模具材料选择:常见的模具材料有钢、铝合金等,根据压铸件的要求和使用场景选择合适的模具材料,以确保模具具有足够的强度和耐磨性。
2.结构设计:模具的结构要合理,与压铸件的形状相匹配,避免出现脱模困难、变形等问题。
同时,要考虑到模具的拆卸和维护,方便进行清理和更换模具零部件。
3.冷却系统设计:在模具中设置合适的冷却系统,以提高压铸件的凝固速度并避免产生缺陷。
冷却系统的设计要考虑到冷却介质的流动性、冷却效果以及与压铸件形状的匹配等因素。
4.压铸模表面处理:对模具表面进行适当的处理,如喷涂涂层、表面硬化等,以延长模具的使用寿命和提高模具的抗腐蚀性能。
压铸件结构设计原则压铸件结构设计的目标是在满足产品功能和外观要求的前提下,尽量减少结构复杂性和提高生产效率。
以下是一些常用的压铸件结构设计原则:1.壁厚均匀:保持压铸件的壁厚均匀,避免厚度过大或过薄导致不均匀收缩和应力集中。
2.避免尖角和过度薄壁结构:减少压铸件中的尖角和过度薄壁结构,因为这些部分容易引起变形和缺陷。
3.引导放料设计:在压铸件结构中设置合适的引导放料设计,以确保熔融金属能够充分填充整个模腔,并避免产生气孔和冷却不均。
4.滑动方向和出料设计:考虑到模具的拆卸和压铸件的出料,结构中应合理设置滑动方向和出料设计,以方便模具的安装和压铸件的脱模。
压铸工艺选择在确定了压铸模具设计和压铸件结构设计后,还需要选择适合的压铸工艺。
以下是一些常用的压铸工艺选择要点:1.压铸机选择:根据压铸件的尺寸和形状,选择合适的压铸机型号和规格。
详解压铸零件结构设计-精

压铸件设计规范目录铸圆脱铸缘压铸压铸内压铸压铸级压铸压铸一、壁厚1、压铸件的壁厚对铸件质量有很大的影响。
以铝合金为例,薄壁比厚壁具有更高的强度和良好的致密性。
因此,在保证铸件有足够的强度和刚性的条件下,应尽可能减少其壁厚,并保持壁厚均匀一致。
2、铸件壁太薄时,使金属熔接不好,影响铸件的强度,同时给成型带来困难;壁厚过大或严重不均匀则易产生缩瘪及裂纹。
厚壁压铸件,其壁中心层的晶粒粗大,易产生缩孔、缩松等缺陷,同样降低铸件的强度。
3、压铸件的壁厚一般以2.5~4mm为宜,同一压铸件内昀大壁厚与昀小壁厚之比不要大于3∶1,壁厚超过6mm的零件不宜采用压铸。
推荐值见表1。
我司的铝压铸件,按如下要求选取壁厚:散热齿一般取2.0~2.5mm,(自然散热)间距取10~12mm,(强迫风冷)间距取8~10mm.其余壁厚取4.5~5.0mm;螺纹孔为M3的PCB支撑柱,直径取6.5~7.5mm;接地螺纹孔处的壁厚取:M4 9.5~10.5mm, M5 10.5~11mm。
表1 压铸件的最小壁厚和正常壁厚二、铸造圆角和脱模斜度1、铸造圆角压铸件各部分相交应有圆角(分型面处除外),使金属填充时流动平稳,气体容易排出,并可避免因锐角而产生裂纹。
对于需要进行电镀和涂饰的压铸件,圆角可以均匀镀层,防止尖角处涂料堆积。
压铸件的圆角半径R一般不宜小于1mm,最小圆角半径为0.5 mm,见表2。
铸造圆角半径的计算见表3。
我司铝压铸件的圆角一般取R1.0mm,无配合处最小取R3.0mm(有外观要求的除外)。
表2 压铸件的最小圆角半径(mm)①、对锌合金铸件,K=1/4;对铝、镁合金铸件, K=1/2。
②、计算后的最小圆角应符合表2的要求。
表3 铸造圆角半径的计算(mm)2、脱模斜度设计压铸件时,就应在结构上留有脱模斜度,无脱模斜度时,在需要之处,必须有脱模的工艺斜度。
斜度的方向,必须与铸件的脱模方向一致。
推荐的脱模斜度见表4。
我司现采用的脱模斜度一般取前模1.5°,后模1.0°。
压铸件结构设计规范

压铸件结构设计压铸件结构设计是压铸工作的第一步。
设计的合理性和工艺适应性将会影响到后续工作的顺利进行,如分型面选择、内浇口开设、推出机构布置、模具结构及制造难易、合金凝固收缩规律、铸件精度保证、缺陷的种类等,都会以压铸件本身工艺性的优劣为前提。
1、压铸件零件设计的注意事项⑴、压铸件的设计涉及四个方面的内容:a、即压力铸造对零件形状结构的要求;b、压铸件的工艺性能;c、压铸件的尺寸精度及表面要求;d、压铸件分型面的确定;压铸件的零件设计是压铸生产技术中的重要部分,设计时必须考虑以下问题:模具分型面的选择、浇口的开设、顶杆位置的选择、铸件的收缩、铸件的尺寸精度保证、铸件内部缺陷的防范、铸孔的有关要求、收缩变形的有关要求以及加工余量的大小等方面;⑵、压铸件的设计原则是:a、正确选择压铸件的材料;b、合理确定压铸件的尺寸精度;c、尽量使壁厚分布均匀;d、各转角处增加工艺园角,避免尖角。
⑶、压铸件分类按使用要求可分为两大类,一类承受较大载荷的零件或有较高相对运动速度的零件,检查的项目有尺寸、表面质量、化学成分、力学性能(抗拉强度、伸长率、硬度);另一类为其它零件,检查的项目有尺寸、表面质量及化学成分。
在设计压铸件时,还应该注意零件应满足压铸的工艺要求。
压铸的工艺性从分型面的位置、顶面推杆的位置、铸孔的有关要求、收缩变形的有关要求以及加工余量的大小等方面考虑。
合理确定压铸面的分型面,不但能简化压铸型的结构,还能保证铸件的质量。
⑷、压铸件结构的工艺性:1)尽量消除铸件内部侧凹,使模具结构简单。
2)尽量使铸件壁厚均匀,可利用筋减少壁厚,减少铸件气孔、缩孔、变形等缺陷。
3)尽量消除铸件上深孔、深腔。
因为细小型芯易弯曲、折断,深腔处充填和排气不良。
4)设计的铸件要便于脱模、抽芯。
5)肉厚的均一性是必要的。
6)避免尖角。
7)注意拔模角度。
8)注意产品之公差标注。
9)太厚太薄皆不宜。
10)避免死角倒角(能少则少)。
11)考虑后加工的难易度。
铝合金压铸件产品结构设计要点

铝合金压铸件的结构设计要点简介为了提升铝合金铸件产品研发的合格率,在结构设计、开发时应注意以下几方面的内容:铸件壁厚相差不能过大,厚度的差距过大会对填充带来影响,且一般浇口部分的肉厚要大于零件的平均肉厚,目的是减少多铝液的压力损失;脱模问题,这点在压铸过程中非常重要,现实中脱模往往容易出现问题,这比注塑脱模麻烦多了,所以拔模斜度的设置和动定模脱模力的计算要注意些,一般拔模斜度为1°~3°,通常考虑到脱模的顺利性,外拔模要比内拔模的斜度要小些,外拔模1°,而内拔模要2°~3°左右。
设计时考虑到模具设计的问题,如果有多个位置的抽芯位,尽量放两边,最好不要放在下位抽芯,这样时间长了下抽芯会容易出问题;有些压铸件外观可能会有特殊的要求,如喷油、喷粉等,这时就要使结构上避开重要外观位置,便于设置浇口溢流槽;在结构上尽量的避免出现导致模具结构复杂的情况出现,如不得不使用多个抽芯或螺旋抽芯等。
对于需进行表面加工的零件,在零件设计时给适合的加工留量,不能太多,会把里面的气孔都暴露出来的;不能太少,否则粗精定位一加工,黑皮还没加工掉,你就等再在模具上打火花了,留量最好不要大于0.8mm,这样加工出来的面基本看不到气孔的,因为有硬质层的保护。
选料应注意选用ADC12还是A380等,但同时也要看具体的要求——销往法国的铝压铸件,如果有FDA的要求,就不能用ADC-12,须用ADC-3T代替;铝合金没有弹性,要做扣位只有和塑料配合。
一般不能做深孔,在开模具时只做点孔,然后在后加工;如果是薄壁件,不能太薄,而且一定要用加强肋,增加抗弯能力。
由于铝铸件的温度要在800摄氏度左右,模具寿命一般比较短,如电机外壳一般只有80K左右;压铸件的设计与塑胶件的设计比较相似,塑胶件的一些设计常规也适用于压铸件,压铸模具一般是不允许靠破的。
对于铝合金,模具所受温度和压力比塑胶的大很多,对设计的正确性要求特严,即使很好的模具材料,一旦有焊接,模具就几乎无寿命可言,锌合金跟塑胶差不多,模具寿命较好;不能有凹的尖角,避免模具崩角。
五金、铝合金压铸件的结构设计、生产工艺和相关模具

五金、铝合金压铸件的结构设计、生产工艺和相关模具一、引言五金铝合金压铸件是指通过金属模具将铝合金熔融液压铸成制品的一种工艺,是工业制造领域中常见的金属加工方式。
本文将从结构设计、生产工艺和相关模具三个方面对五金铝合金压铸件进行分析介绍。
二、结构设计1.设计原则五金铝合金压铸件的结构设计需要遵循以下原则:(1)合理布局:根据零部件的功能需求和受力情况,合理布局零部件的结构和连接方式。
(2)加工便利:尽量减少零部件的复杂性,尤其是薄壁结构和内部空腔,以便于后续的加工和热处理。
(3)配件一体化:尽量将多个零部件设计成一个整体,减少连接件和焊接,提高零部件的整体性能。
2.设计要素(1)壁厚设计:根据零部件的受力情况和铝合金的流动能力,确定良好的壁厚设计,避免产生疏松和变形。
(2)浇口和排气系统:合理设计浇口和排气系统,保证熔融铝合金填充整个模腔并排除气泡,避免缺陷。
(3)加工余量:考虑到热处理和精加工的需要,留有一定的加工余量,以确保零件的尺寸精度和表面质量。
三、生产工艺1.原料准备铝合金压铸件的原料主要是铝合金锭,通常采用A380、A383或ADC12等合金型号。
原材料应经过严格的质量检验和配料混合,以确保合金成分的稳定和质量的一致性。
2.模具制造铝合金压铸的模具通常由下模和上模组成。
模具的材质需具有优良的强度、硬度和热稳定性。
在模具的设计制造过程中,需充分考虑热胀冷缩、压铸工艺及零件的收缩率等因素。
3.压铸工艺(1)设备选择:选择适合铝合金压铸件生产的压铸设备,确保设备的稳定性和高效性。
(2)熔炼铝合金:将原料锭放入熔炉中熔化成熔体,同时进行合金成分的调节和温度的控制。
(3)模具铸造:将熔融的铝合金浇注至模具腔内,经过一定时间的凝固后,取出成型的铝合金压铸件。
四、相关模具1.压铸模具铝合金压铸件的模具是整个生产过程中至关重要的部分。
压铸模具主要由模腔、浇口系统、冷却系统和排气系统等组成,其结构和精度对制品的质量和成型率有直接影响。
铝合金压铸结构设计规范

铝合金压铸结构设计规范
其次,在设计铝合金压铸结构件时,需要考虑结构的合理性和可靠性。
这包括确定结构的几何形状、壁厚、孔径、配重、连接方式等。
同时,需
要根据零件的使用环境和所需功能来制定合适的设计要求。
例如,对于承
受高温的结构件,需要考虑材料的热膨胀系数和热稳定性。
此外,铝合金压铸结构件的设计应尽量简单易行。
减少零件数量和结
构复杂性可以有效降低制造成本,提高生产效率。
特别是对于大量批量生
产的结构件,设计简化是非常重要的。
另外,铝合金压铸结构件在设计时还需要考虑材料的力学性能和耐久
性能。
材料的力学性能包括强度、刚度、韧性等,应满足零件在使用过程
中的力学要求。
耐久性能包括抗腐蚀性能、抗疲劳性能等,这些性能会直
接影响到零件的使用寿命。
最后,铝合金压铸结构件的设计还需要与生产工艺相结合。
设计要考
虑到生产过程中的可操作性、可靠性和经济性。
设计师需要充分了解铝合
金压铸工艺的特点和要求,合理设计结构以提高制造工艺的效率和质量。
总之,铝合金压铸结构设计规范包括了多个方面的要求,从材料选择
到几何设计、力学性能和耐久性能等方面都需要考虑。
设计师需要根据具
体的应用场景和设计要求,综合考虑各个因素,在满足功能和安全的前提下,设计出性能优良、制造工艺可行的铝合金压铸结构件。
铝合金压铸零件设计

对组件E1的外壳模具设计指导老师:熊伟组长:高科文组员:任伯韬韩钊王建康马晓骁王定刚赵造标贺泽成吴昌军班级:成型112班2014 年 6 月 10 日一前言及分组 (2)二E1组件形状及尺寸 (3)三E1组件外壳对组件的保护和美观 (4)四外壳的初步设计 (4)1 结构密封分析 (5)2 E1件固定与上下板连接分析 (5)3 散热分析 (6)4 外壳材料的选择 (6)5 E1组件外壳厚度的设计 (7)五外壳成型零件设计形状及分析 (8)1压铸件结构设计的工艺性 (10)2外壳技术要求 (11)2加工余量 (12)4铸造和圆角 (13)5起模斜度 (14)七压铸成型设计 (14)1压铸机的选用及相关 (14)2压铸模具基本结构 (15)3压铸成型过程 (16)4分型面的设计 (17)5浇注系统的设计 (18)浇注系统的结构与分类 (18)内浇口的设计 (19)横浇道的设计 (19)直浇道的设计 (20)6排溢系统的设计 (21)7模架的设计 (22)对组件E1的外壳模具设计一、前言及分工关于这次对E1组件的外形设计我想每个人拿着都有一种自己心目中的外形,但这次老师的分组设计,在我们第二组九个人必须且只能有一种方案。
对于我们的设计思路,我先这是一个很重要的问题,最开始我们大家很茫然,没有清楚我们对E1件外壳应该从那些方面着手,我也在想老师经常提及用现代模具设计的方法,现代模具设计我想应该是结合CAD和CAE软件去完成这次作业,但是对软件,确实不是那样的熟悉,也就只能用我们自己的方式去表达这次设计内容。
对于这次设计,并不是重要的不是这次设计的结果,应该是这次设计过程中设计本专业的知识要点和原理分析,这次设计突出的要点,着重在E1外壳的压铸件设计,分型面设计,浇注排溢系统上。
分组讨论合作第一组:任伯韬韩钊马晓骁王定刚共同完成组件外壳设计主要1、尺寸分析;2、材料选择;3、壳体的密封;4、壳体的链接;5、功能分析;6、UG作图。
压铸件结构设计及压铸工艺解读

压铸件基本结构的设计
? 铸造圆角
在压铸零件 壁面与壁面连接处 ,不论是直角、 锐角或钝角, 都应设计成圆角 ,只有当预计选定 为分型面的部位 上才不采用圆角 链接。
1. 铸造圆角有助于金属液的流动 ,减少涡流, 气体容易排出,有利于成形;
2. 铸造圆角可避免在尖角处产生的 应力集中而 产生的裂;
影响外观。
3
从简化模具结构、延长模具使用寿命考虑
? 避免模具局部过薄
1. 避免因孔边距离凸缘距离过小,使模具镶块在 a处断裂; 2. 在孔与 边缘处保证a≥3mm 。
4
从简化模具结构、延长模具使用寿命考虑
? 避免压铸件上互相交叉的不通孔
1. 交叉的不通孔设计需要使用公差配合较高的互相交叉的型 芯,这既增加了模具的加工量,又要求严格控制的抽芯次 序,一旦金属液进入交叉的间隙中,便会使抽芯困难;
?从液态金属充填型腔到内浇道完全凝固时,继续 在压射冲头下的持续时间称为 持压时间 。持压的 作用是使压力传递给未凝固的金属,保证铸件在 压力下结晶,以 获得致密的组织 。
?一般原则: ?持压时间的长短取决于铸件的 材质和壁厚 ; ? 对熔点高、结晶范围大和厚壁 的铸件,持压时 间要 长些。 ? 持压时间不足,易造成 疏松,如铸件内浇道处 的金属尚未完全凝固,由于压射冲头的退回, 金属被抽出,铸件内形成空洞; ? 对结晶范围小而壁又薄的铸件 ,持压时间可 短 些。
?因此,在压铸模温度过高时,应 采取冷却措施 。 通常用压缩空气、水或其他液体进行冷却。
26
? 压铸模工作温度一般可按下式计算: 1
t型 ? 3 t浇 ? ? t
t型---铸模工作温度;t浇---液体金属浇注温度;Δt---温度控制公差(一般取25)
一种可阳极氧化压铸铝合金材料的制备方法及压铸方法
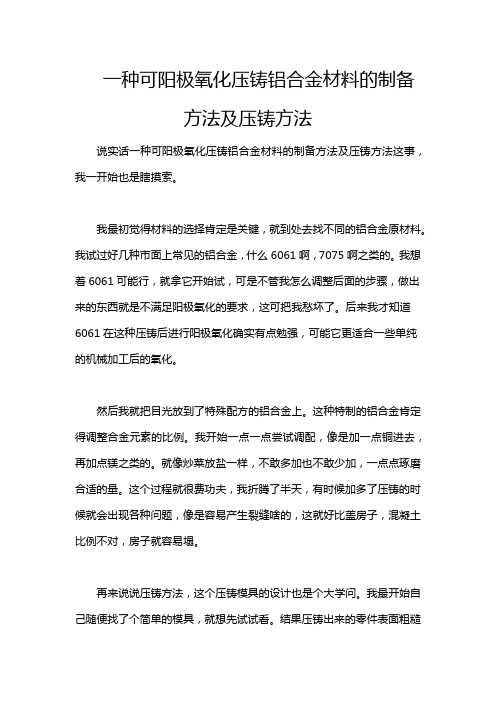
一种可阳极氧化压铸铝合金材料的制备方法及压铸方法说实话一种可阳极氧化压铸铝合金材料的制备方法及压铸方法这事,我一开始也是瞎摸索。
我最初觉得材料的选择肯定是关键,就到处去找不同的铝合金原材料。
我试过好几种市面上常见的铝合金,什么6061啊,7075啊之类的。
我想着6061可能行,就拿它开始试,可是不管我怎么调整后面的步骤,做出来的东西就是不满足阳极氧化的要求,这可把我愁坏了。
后来我才知道6061在这种压铸后进行阳极氧化确实有点勉强,可能它更适合一些单纯的机械加工后的氧化。
然后我就把目光放到了特殊配方的铝合金上。
这种特制的铝合金肯定得调整合金元素的比例。
我开始一点一点尝试调配,像是加一点铜进去,再加点镁之类的。
就像炒菜放盐一样,不敢多加也不敢少加,一点点琢磨合适的量。
这个过程就很费功夫,我折腾了半天,有时候加多了压铸的时候就会出现各种问题,像是容易产生裂缝啥的,这就好比盖房子,混凝土比例不对,房子就容易塌。
再来说说压铸方法,这个压铸模具的设计也是个大学问。
我最开始自己随便找了个简单的模具,就想先试试看。
结果压铸出来的零件表面粗糙度很差,根本没法进行后面的阳极氧化。
我才意识到模具要有特定的形状和纹理,这样冷却的速度和金属流动的方向才能合适。
后来我找专业人士设计了一套模具,那压铸出来的效果真就不一样了。
对于压铸的温度和压力,这也是一门需要反复尝试的技术。
我开始老想高温高压肯定能把铝合金乖乖压铸成型。
可是情况不是这么简单,有时候温度太高,铝合金虽然成型了,但是里面的结构可能就被破坏了,而且会影响后面的阳极氧化效果。
就像烤面包,温度高了烤糊了,低了又没烤熟一样。
压力也是,过大可能会损坏模具,过小又无法让铝合金充满整个模腔。
还有一些预处理步骤。
在压铸之前,我原来都不重视铝合金表面的清洁啊干燥啊这些事儿。
结果压铸出来的东西,氧化出来的色泽很不均匀。
后来我每次压铸之前都确保铝合金原料干干净净的,才得到了比较满意的结果。
- 1、下载文档前请自行甄别文档内容的完整性,平台不提供额外的编辑、内容补充、找答案等附加服务。
- 2、"仅部分预览"的文档,不可在线预览部分如存在完整性等问题,可反馈申请退款(可完整预览的文档不适用该条件!)。
- 3、如文档侵犯您的权益,请联系客服反馈,我们会尽快为您处理(人工客服工作时间:9:00-18:30)。
铝合金压铸件的结构设计经验
钢铁零件在含有磷酸溶液中进行化学处理,使钢铁表面生成一层难溶于水的保护膜的过程,叫做磷化处理!
它主要有以下特点:
1、磷化膜表面呈灰色或暗灰色。
2、磷化膜经填充、上油或涂漆处理,在大气条件下具有较好的抗腐蚀能力。
3、膜层的吸附能力强,常作为涂料的底层。
4、磷化膜具有较高的电绝缘性。
5、经磷化处理后,原金属的机械性能、强度、磁性等基本不变。
6、磷化膜有很好的润滑性能。
7、渗氮零件表面可以用磷化膜保护。
8、磷化膜的最大特点是能在钢铁的内表面及形状复杂的钢铁表面上获得保护膜。
9、膜层硬度和机械强度底,有一定的脆性。
钝化一般是指:为了提高镀锌层的防护性能和装饰性能,将镀件防入溶液中处理,使其表面形成一层化学稳定性较高的膜。
经钝化处理后能提高镀锌层的防护性能和表面光泽。
氧化一般分为:铝、铝合金和钢铁零件的氧化,只是所能达到的目的和所使用的溶液不同
1。
考虑壁厚的问题,厚度的差距过大会对填充带来影响——一般浇口部分的肉厚要大于零件的平均肉厚,目的是减少多铝液的压力损失。
7。
再有就是注意选料了,是用ADC12还是A380等,要看具体的要求了——销往法国的铝压铸件,如果有FDA的要求,就不能用ADC-12,须用ADC-3T代替。
在模具方面,压铸模具一般是不允许靠破的。
再补充点
如果有字模具或雕刻内容。
需要远离浇口,防止过早冲刷磨损。
对多出需要去毛边的零件,特别是内框型,需要加开一道五金冲裁模具冲毛边。
1。
考虑壁厚的问题,厚度的差距过大会对填充带来影响
2。
考虑脱模问题,这点在压铸实际中非常重要,现实中往往回出现这样的问题,这比注塑脱模讨厌多了,所以拔模斜度的设置和动定模脱模力的计算要注意些,一般拔模斜度为1到3度,通常考虑到脱模的顺利性,外拔模要比内拔模的斜度要小些,外拔模也就1度,而内拔模要2~3度左右
3。
设计时考虑到模具设计的问题,如果有多个位置的抽心位,尽量的放两边,最好不要放在下位抽心,这样时间长了下抽心会容易出问题
4。
有些压铸件外观可能会有特殊的要求,如喷油、喷粉等,这时就要时结构避开重要外观位置便于设置浇口溢流槽
5。
在结构上尽量的避免出现导致模具结构复杂的结构出现,如,不得不使用多个抽心或螺旋抽心等
6。
对于需进行表面加工的零件,注意,需要在零件设计时给适合的加工留量,不能太多,否则加工人员会骂你的,而且会把里面的气孔都暴露出来的,不能太少,否则粗精定位一加工,得,黑皮还没干掉,你就等再在模具上打火花了,那给多少呢,留量最好不要大于0。
8mm,这样加工出来的面基本看不到气孔的,因为有硬质层的保护。
7。
再有就是注意选料了,是用ADC12还是A380等,要看具体的要求了
8。
铝合金没有弹性,要做扣位只有和塑料配合。
9。
一般不能做深孔!在开模具时只做点孔,然后在后加工!
10。
如果是薄壁零件与不能太薄,而且一定要用加强肋,增加抗弯能力!由于铝铸件的温度要在800摄氏度左右!模具寿命一般比较短一般做如电机外壳的话只有80K左右就再见了!
1.压铸件的设计与塑胶件的设计比较相似,塑胶件的一些设计常规也适用于压铸件。
2.对于铝合金,模具所受温度和压力比塑胶的大很多,对设计的正确性要求特严。
即使很好的模具材料,一旦有焊接,模具就几乎无寿命可言。
锌合金跟塑胶差不多,模具寿命较好。
3.不能有凹的尖角,避免模具崩角。
4.压铸件的精度虽然比较高,但比塑胶差,而且拔模力比塑胶大,通常结构不能太复杂,必要时应将复杂的零件分解成两件或多件。
5.铝合金的螺孔通常模具只做锥坑,采用后加工。
对于要求严的配合部位通常留 0.3mm的后加工量。
6.铝合金压铸易产生气孔,在外观上需加以考虑。
铝合金压铸件(含硅)表面做阳极氧化很难的,一般时间稍长回出现黑色。
铝合金压铸件不能做阳极氧化,可用喷油或喷塑。
常用的合金铝6061、7075,铸铝A356着色效果都不错的。
压铸件和阳极氧化之间没有必然的联系。
铸铝的种类很多,不一定要选硅铝合金(铸铝分Al-Si系、AL-Cu系、AL-Mg系、AL-Zn系等,还有参杂稀土元素的)。
即使选用硅铝合金,阳极氧化也并非不可行。
一般来说,合金铝中多多少少都含硅元素,比如6061含硅0.4~0.8%,7075含硅0.4%,这样的含硅量对合金阳极化影响是很小的(顺便说一句,铜含量对铝合金阳极氧化影响不大,但在硬质氧化、瓷质氧化时,铜、锰影响很大)。
但当合金中硅含量很大(>7%)时,对合金的阳极氧化就会有影响。
主要体现在氧化耗时较长,膜层显得灰暗等,这些问题通过工艺可以解决(比如不用直流、而用脉冲电流氧化),这就需要表面处理厂家有一定的技术能力。
所以,铸铝≠硅铝合金≠不能阳极氧化。
另外再说说着色的问题。
铝合金的阳极氧化和着色是两个不同的工序,这与钢铁的发蓝不同。
钢铁发蓝是氧化膜本身呈蓝色,而着色是在阳极氧化后立即进行,氧化膜本身是无色透明的。
铝合金用硫酸阳极化得到的氧化膜最适宜染色,现在比较多的使用有机染料着色,着色后再对氧化膜进行封闭处理。
另外也有用重金属盐电解着色的,但要按楼主的要求染成红色比较困难!。